Jackco 66300C Assembly instructions

*This hydraulic jack conforms to all "ANSI / ASME" safety standards.
Visit our website at: http://www.jackco.com
66300C - 3 Ton Rapid Floor Jack
WARNING
Owners’s Manual & Safety Instructions
www.jackco.com
!
Read this material before using this product. Failure to do so can result in serious injury. SAVE THIS MANUAL.
This product may contain chemicals know
to the State of California to cause cancer,
birth defects, or other reproductive harm.
Prop. 65 Warning
for California Residents
!

For Your Safety
Specifications
Prior to Operation
Read these safety instructions carefully and keep this manual in an easy to find place as you may need
to use it again.
Non-compliance with these rules may result in injury or damage to the jack or vehicle.
Do not modify the jack in any way.
Never exceed the rated capacity of the jack.
This jack is a lifting device only and should never be used to move the vehicle.
The jack should be supported on a solid and level ground. Never use the jack in a surface where it may
sink into the ground.
Ensure that there are no persons inside the vehicle to be lifted. Switch off the engine and apply the
brake.
Position the jack under the manufacturer’s recommended lifting point for the vehicle. Off-centered loads
can slip and accidents may result.
During raising and lowering of the load, precautions should be taken to avoid movement of the vehicle.
Traffic may cause the raised vehicle to rock during roadside use of the jack.
Never work under a raised vehicle without supporting it with mechanical/jack stands.
Never position any part of your body near the movable parts of the jack.
Ensure that there are no persons or obstructions underneath the vehicle prior to lowering.
Do not adjust the overload bypass valve under any circumstance.
Air may become trapped in the hydraulic system during transit
To Purge Air
1. Insert the handle into the socket and secure it with the set screw provided.
2. Turn the handle counterclockwise until release valve is open, pump the jack several times to purge the
accumulated air in the system .
3. Turn the handle clockwise to close the release valve. The jack is now ready to use.
Use wheel chocks appropriately.
Capacity: 3 ton Saddle Diameter : 4.7 in
Min Height : 4.3 in Strokes to Max Height: 4
Max Height : 20.25 in Net Weight :
Dimension: 29.75 in (L) x 14.2 in (W)

Assembly
Operating Instructions
Air may become trapped in the hydraulic system during transit
To Purge Air
1. Insert the handle into the socket and secure it with the set screw provided.
2. Turn the handle counterclockwise until release valve is open, pump the jack several times to purge the
accumulated air in the system .
3. Turn the handle clockwise to close the release valve. The jack is now ready to use.
Please refer to the exploded view drawing in this manual in order to identify parts:
1. Assemble the two handle halves together by depressing the spring-loaded button on the knurled handle
section (#7) and inserting the upper handle section into the lower section (#8). The spring-loaded button
should engage with the hole in the lower handle section.
2. Grease the inside of the handle yoke (#11) and remove the handle set screw (#10).
3. Install the handle assembly in the handle yoke until the bottom of the handle engages with the universal
joint assembly (#13).
4. Reinstall the handle set screw in the handle yoke making sure the screw secures the handle to the
handle yoke. Tighten the screw.
5. Air may become trapped in the hydraulic system during shipping and handling. Trapped air will affect
the pumping performance of the jack. If this occurs, follow the air pumping procedure below:
a) Remove the four screws that secure the cover plate (A) to the jack frame (B) so the oil filler screw
(#37) can be removed from the hydraulic power unit reservoir tube (#38).
b) With the lift arm (C) in its down position, look inside the oil fill screw hole. You should be able to see
the top of the power unit’s cylinder (#35). The hydraulic fluid level should be no higher than the top of
the cylinder. Correct the fluid level if it is not at the proper height.
c) Pump the jack against a load that is at least 500 lbs. (225 Kgs).
After the load is raised, slightly turn the lift handle in a counterclockwise rotation so the load is very
slowly lowered. While the lift arm is lowering, quickly pump the lift handle 5 or 6 full incremental
pump strokes. After pumping, lower the lift arm to its full rest position.
d) Install the oil fill screw (#37). Rotate the handle in a clockwise rotation until tight and pump the lift arm
to maximum height.
If the pumping condition has improved, repeat steps "a" through "d" until all of the air has been purged from the system.
d) Install the cover plate (A) with the four screws.
To Lift a Vehicle:
To Lower a Vehicle:
Turn the handle clockwise.
Move the handle up and down.
Use the full stroke of the piston for greater speed
Support the vehicle with appropriate jack stands.
Lift the vehicle to remove the jack stands, ensuring that there are no
persons or obstructions under the vehicle.
Turn the handle counter-clockwise

Maintenance
Important: Both the maintenance and repair of the jack may only be performed by qualified persons,
who have suffcient knowledge of the hydraulic system used in these jacks.
Regularly lubricate the moving parts in the wheels, arms, handle and
pump roller pin.
• Only original replacement parts should be used.
Extremely Important: never use brake fluid.
• When the jack is not in use, make sure the lifting arm is fully retracted to avoid corrosion.
• Keep the jack in a clean, dry place and out of children’s reach.
• Replace the hydraulic fluid in the reservoir at least once a year. To check the hydraulic fluid level, lower
the lifting arm completely.
• The hydraulic fluid level should be just below the filler plug. Replenish if necessary, and reinstall the
rubber filler plug. Excessive hydraulic oil may render the jack inoperative.
• Inspect the jack before each use. Take corrective action or remove the jack from service if any of the
following problems are found:
• Keep warning labels and instructional decals clean and readable. You may use a mild soap solution to
wash external surfaces of the jack.
a. Cracked or damaged frame d. Loose hardware
b. Leaking hydraulic fluid e. Modified equipment
c. Scored, damaged piston rod

Troubleshooting
Caution: To prevent personal injury, all inspection, maintenance, and repair procedures must be performed
when the jack is free of load.
Trouble Solution
Jack will not lift load or leaks down
excessively
Jack will not lift to its full height
Return spring is broken or linkages are binding.
Replace spring if broken. Grease pivot shaft and
all lift arm linkages.
The hydraulic system has trapped air. Follow Step
5 of the “ASSEMBLY” procedure on page 3.
Discharge ball is not sealing hydraulic system
and oil may be dirty. Manually flush hydraulic
system. Open the release valve, as required, to
raise and lower the lift arm. Manually raise and
lower lift arm.
Jack will not lower completely
Jack will not lift smoothly or jack feels
spongy
Jack will not hold load or handle rises
1. The release valve is not closed. Turn the valve
clockwise tightly. If this does not work, remove
handle, lubricate handle receptacle and handle
end, then retry.
2. The hydraulic system has trapped air. Follow
Step 5 of the “ASSEMBLY” procedure on
page 3.
3. Pump seals or back-up ring may be defective.
Clean hydraulic fluid passages, replace seals
and refill hydraulic fluid. (Must be serviced by
qualified service center)
2. Low on hydraulic fluid. Follow Step 5 of the
“ASSEMBLY” procedure on page 3.
1. Low on hydraulic fluid. Follow Step 5 of the
“ASSEMBLY” procedure on page 3.

Parts List
Part No. Description Q’ty
1 Self Locking Retaining Ring 20mm 2
2 Washer 20mm 2
3 Front Wheel 2
4 Washer 24mm 2
5 Hex Nut M24 2
6 Washer M12 4
7 Hex Bolt M12x20 4
8 Rear Caster Assembly 2
9 Washer 16mm 2
10 Hext Nut M16 2
11 Washer 18mm 2
12 Yoke Retaining Bolt 2
13 Steel Rod (Brace) 2
14 Washer 8mm 4
15 Hext Bolt M8x20 4
16 Spring Load Lock Pin 1
17 Hand Lever (Upper) 1
18 Handle Lever (Lower) 1
Part No. Description Q’ty
19 Handle Bumper 1
20 Set Screw (Handle) 1
21 Handle Yoke 1
22 Universal Joint Assembly 1
23 Power Unit Assembly 1
24 Spring 2
25 Block Linkage 1
26 Lift Axle 1
27 Grease Fitting 1
28 Lifting Arm 1
29 Linkage Arm 2
30 Saddle 1
31 Saddle Screw 1
32 C-Clip 16 2
33 C-Clip 25 2
34 C-Clip 12 2
35 Rubber Saddle Pad 1

Model 66300C Power Unit
*Part numbers are for your reference only, not all parts are available separately.
Note: Default unit of measurement is metric, in mm.
Part No. Description Q’ty
1 Gasket 1
2 Reservoir 1
3 Gasket 1
4 O-Ring 29.6x3.5 1
5 Cylinder Nut 1
6 Ram 1
7 Retaining Ring 30mm 1
8 Ram Bearing 1
9 Cup Seal 1
10 O-Ring 31x4.6 1
11 Cylinder 1
12 Brass Cylinder Seal 1
13 Hydraulic Block 1
14 Bearing 1
15 Valve Seat 1
16 Relief Valve Spring 1
17 Relief Valve Screw (Small Pump) 1
18 O-Ring 7.1x1.8 2
19 Relief Valve Bolt 2
20 Bearing Ø5 1
21 Brass Washer 1
22 Small Pump Cylinder 1
Part No. Description Q’ty
23 O-Ring 10.2x2.65 2
24 Backup Washer 2
25 Small Pump Piston 1
26 Small Pump Spring 1
27 Dust Cover (Small) 1
28 Small Spring Cap 1
29 Retaining Ring 15 1
30 Universal Joint Assembly 1
31 Bearing Ø6 1
32 Hex Bolt M6 1
33 Bearing Ø7.5 1
34 Relief Valve Spring 1
35 Bearing Ø8 1
36 Relief Valve Screw (Large Pump) 1
37 Brass Washer 1
38 Large Pump Cylinder 1
39 O-Ring 26x2.65 2
40 Large Pump Piston 1
41 Large Pump Spring 1
42 Dust Cover (Large) 1
43 Large Spring Cap 1
44 Retaining Ring 31 1

Limited One Year Warranty
Jackco Transnational Inc. (Jackco) warrants all Jackco equipment and tools to the original purchaser against any
manufacturing defect in material or workmanship for a period of one (1) year from the original date of purchase. If the
defective equipment or tool is determined to be covered under this warranty, it shall be repaired or replaced at
manufacturer's discretion without charge, provided that the equipment or tool must be returned with proof of
purchase to the dealer and freight prepaid, if returned to the manufacturer. This warranty shall not apply to damage
due to accident, negligent use, lack of maintenance, abuse or applications other than the specific function the
equipment or tool is designed for.
No other warranties, expressed or implied, including those of merchantability or fitness for particular purpose shall
be applicable to Jackco except as specifically stated herein. In no event shall Jackco be liable to any party for any
special, direct, indirect, consequential, punitive damage of any nature caused by the sale or use of the equipment or
tool.
Note: This warranty gives the original purchaser specific legal rights which may very from state to state.
Visit our website at: http://www.jackco.com
Table of contents
Other Jackco Jack manuals
Popular Jack manuals by other brands

Hilman
Hilman Deluxe Toe Jack instruction manual

Cattini Oleopneumatica
Cattini Oleopneumatica YAK 215/N Operating and maintenance manual
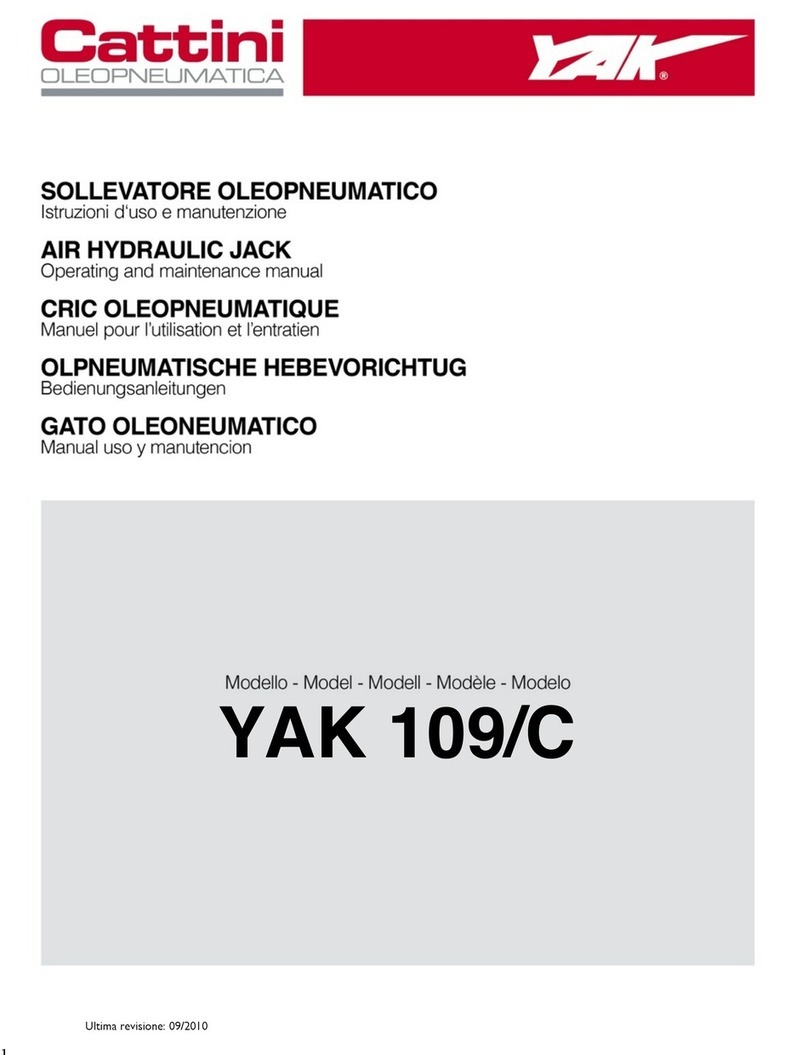
Cattini
Cattini YAK 109/C Operating and maintenance manual

Ranger Products
Ranger Products RFJ-10TL Installation and operation manual
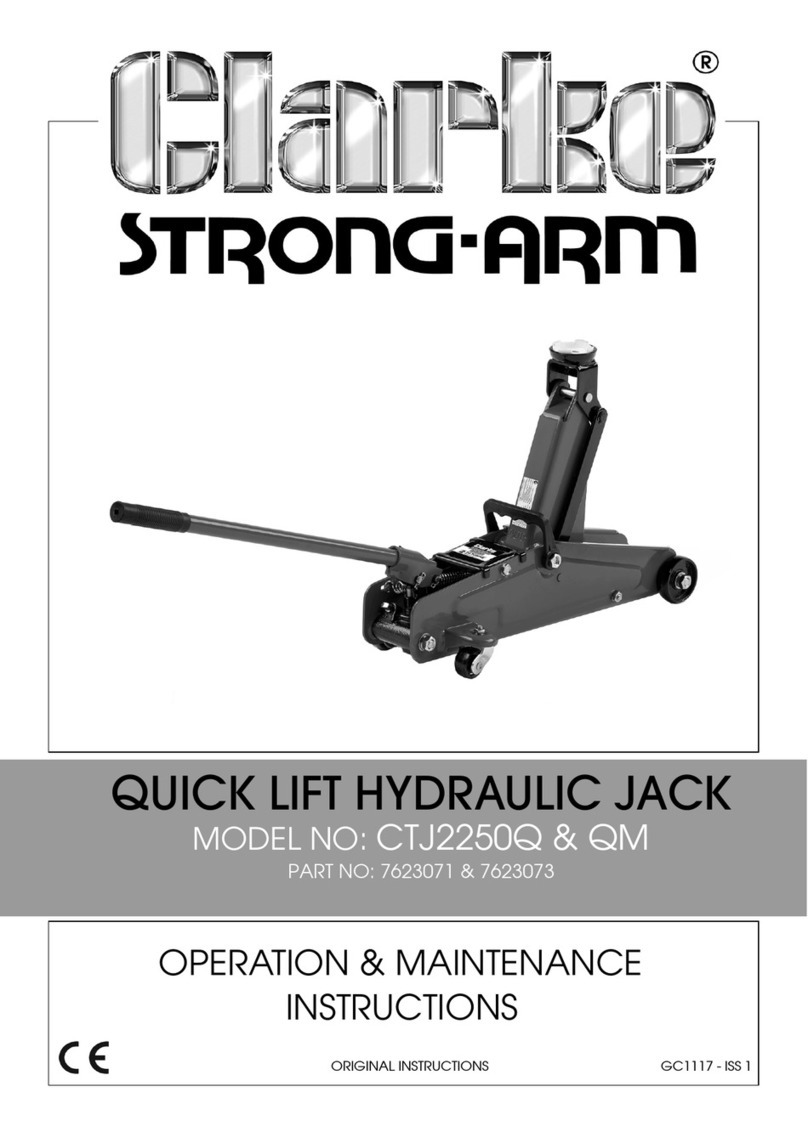
Clarke
Clarke Strong-Arm CTJ2250Q Operation & maintenance instructions
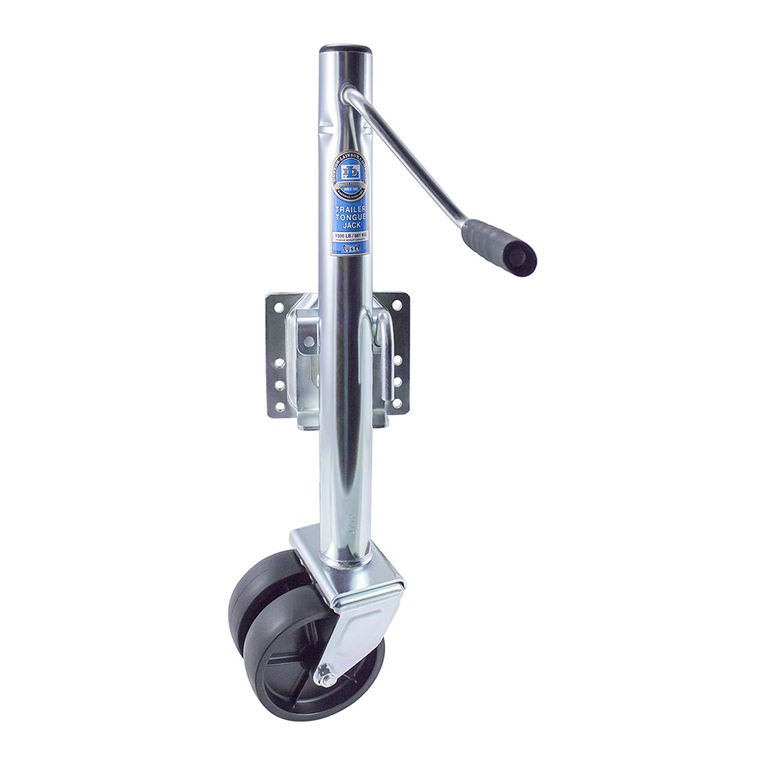
Dutton-Lainson
Dutton-Lainson 6800 Series quick start guide