Jetter JetMove 208-480 User manual

User Manual
JM-208-480 - Digital Servo Amplifier
60870619
We automate your success.

Introduction
2Jetter AG
Item no. 60870619
Revision 2.20
April 2020 / Printed in Germany
Translation of the original manual in German language.
Jetter AG reserves the right to make alterations to its products in the interest of
technical progress. These alterations need not be documented in every single case.
This user manual and the information contained herein have been compiled with due
diligence. Jetter AG shall not be liable for printing or general errors contained herein
or for damages arising from such errors.
The brand names and product names used in this document are trademarks or
registered trademarks of the respective title owner.

JetMove 208-480 Introduction
Jetter AG 3
How to Contact us:
Jetter AG
Graeterstrasse 2
71642 Ludwigsburg
Germany
Phone - Switchboard: ++49 7141/2550-0
Phone - Sales: ++49 7141/2550-433
Phone - Technical Hotline: ++49 7141/2550-444
Telefax: ++49 7141/2550-484
Internet Address: http://www.jetter.de
This User Manual is an Integral Part of
the JetMove 208-480:
To be entered by the customer:
Model:
Serial no.:
Year of construction:
Order no.:
Inventory no.:
Place of operation:

Introduction
4Jetter AG
Significance of this User Manual
This user manual is an integral part of the digital servo amplifier JetMove 208-480.
• Therefore it must be kept in a way that it is always at hand until the digital servo
amplifier JetMove 208-480 will be disposed of.
• Pass this user manual on if the JetMove 208-480 is sold or loaned/leased out.
In any case you encounter difficulties to clearly understand this user manual, please
contact the manufacturer.
We would appreciate any suggestions and contributions on your part and would ask
you to contact us. This will help us to produce manuals that are more user-friendly
and to address your wishes and requirements.
From the servo amplifier JetMove 208-480 module may result unavoidable residual
risks to persons and property. For this reason, any person who has to deal with the
transport, installation, operation, maintenance, and repair of the digital servo
amplifier JetMove 208-480 must have been familiarised with it and must be aware of
these dangers.
Therefore, this person must carefully read, understand and observe this manual, and
especially the safety instructions.
Missing or inadequate knowledge of the manual results in the loss of any claim of
liability on part of Jetter AG. Therefore, the operating company is recommended to
have the instruction of the persons concerned confirmed in writing.
History
Edition Meaning
1.00 Original issue
1.01 Modifications, see Appendix A of user manual rev. 1.01
2.00 Modifications, see Appendix A of user manual rev. 2.00
2.01 Style and orthography have been corrected
2.10 Modifications, see Appendix A of user manual rev. 2.10
2.11 Modifications, see Appendix A of user manual rev. 2.11
2.20 Modifications, see Appendix A of user manual rev. 2.20

JetMove 208-480 Introduction
Jetter AG 5
Description of Symbols
DANGER
This sign is to indicate a possible impending danger of serious physical damage
or death.
CAUTION
This sign is to indicate a possible impending danger of light physical damage.
This sign is also to warn you of material damage.
This sign indicates hazard of life due to electric shock caused by a high operating
voltage.
This sign is to indicate hazard of serious physical damage or death due to
accidentally touching dangerous parts of the device.
This sign indicates that you must wear goggles. Failure to comply may lead to
injuries.
This sign is to warn you of material damage due to applying hard blows or shocks
to the motor flange and shaft.
NOTICE
This sign is to indicate a possible impending situation which might bring damage
to the product or to its surroundings.
It also identifies requirements necessary to ensure faultless operation.

Introduction
6Jetter AG
INFO
You will be informed of various possible applications and will receive further
useful suggestions.
It also gives you words of advice on how to efficiently use hardware and software
in order to avoid unnecessary efforts.
· / - Enumerations are marked by full stops, strokes or scores.
Operating instructions are marked by this arrow.
Automatically running processes or results to be achieved are marked by this
arrow.
PC and user interface keys.
This symbol informs you of additional references (data sheets, literature, etc.)
associated with the given subject, product, etc. It also helps you to find your way
around this manual.

JetMove 208-480 Table of Contents
Jetter AG 7
Table of Contents
1 Safety Instructions 11
1.1 General Information 11
1.1.1 Usage to the Intended Purpose 11
1.1.2 Non-Intended Use 11
1.1.3 Qualified Personnel 12
1.1.4 Modifications and Alterations to the Module 12
1.1.5 Servicing and Repairs 12
1.1.6 Disposal 13
1.2 Ensure Your Own Safety 13
1.2.1 Malfunctions 13
1.2.2 Information Signs and Labels 14
1.2.3 Earthing Procedure 14
1.3 Residual Dangers 16
1.3.1 Hazards During Operation 16
1.3.2 Hazards after POWER has been Turned OFF 18
1.4 Instructions on EMI 18
2 Installing the JetMove 208-480 23
2.1 Scope of Delivery 23
2.2 Mechanical Installation 24
2.3 Electrical Installation 26
2.4 Checking the Installation 27
2.5 Notes on Safety as Regards the Installation 27
2.6 Safety Instructions for Commissioning 28
2.7 Notes on decommissioning 28
3 Operating Conditions 29
4 Physical Dimensions 35
5 Technical Data 37
5.1 Electrical Specification 37
5.2 Motor Protection 41
5.2.1 Built-In Thermal Sensor 41
5.2.2 I²t Calculation 42
5.2.3 Motor Overload Protection to UL 44
6 Drive Controller Structure 45
7 Description of Connections 47
7.1 Connection of the Power Supply 47

Table of Contents
8Jetter AG
7.2 Motor Connection 48
7.2.1 General Information 48
7.2.2 Assignment and Specifications 49
7.2.3 Motor Power Cable with Mating Connector SC 50
7.2.4 Motor Power Cable with Mating Connector SM 53
7.2.5 Connection Assignment of Terminal Box 56
7.3 Resolver Connection 57
7.3.1 Specifications 57
7.3.2 Resolver Cable with Mating Connector 57
7.4 HIPERFACE® Connection 59
7.4.1 Specifications 59
7.4.2 HIPERFACE® Cable with Mating Connector 59
7.5 Sin-Cos Encoder Connection 62
7.5.1 Adapter 62
7.5.2 Specifications 62
7.5.3 Connection Diagram 63
7.6 External Ballast Resistor and DC Link Connection 66
7.7 Digital Inputs, Logic Power Supply 72
7.8 Connection Details for Digital Outputs 74
7.9 Jx2 System Bus 75
7.9.1 Specification of the Jx2 System Bus Cable 75
8 Status Monitoring 77
9 Diagnostics 79
9.1 Fault Messages 79
9.2 Alarms 84
10 Connection Diagrams 85
11 Analog Input (Option) 89
11.1 Description 89
11.2 Technical Data 89
11.3 Description of Connections 90
12 Ethernet Interface (Option) 91
12.1 Description 91
12.2 Description of Connections 91
12.2.1 Connection between the JetMove 208-480...-OEM
and a PC or JetControl 92
12.2.2 Connection between the JetMove 208-480...-OEM
and a PC or JetControl through a Switch 92

JetMove 208-480 Table of Contents
Jetter AG 9
12.3 Logic Circuit LEDs, Mode Selector 93
12.3.1 LEDs 93
12.3.2 The DIP Switches 94
12.4 Setting the IP Address 94
12.4.1 Default IP Address 94
12.4.2 IP Address Taken out of the Configuration Store 94
12.4.3 IP Address Taken out of the Switch Position 96
13 Safe Torque OFF (STO) (Option -S1) 97
14 Counting Input (Option) 99
14.1 Description 99
14.2 EnDat 2.2 99
14.2.1 Technical Data 99
14.2.2 Description of Connections 100
14.2.3 EnDat Cable with Mating Connector 100
14.2.4 Voltage Supply of the Encoder 102
14.3 Synchronous Serial Interface (SSI) 103
14.3.1 Technical Data 103
14.3.2 Description of Connections 103
14.3.3 SSI Cable 104
14.4 Incremental Encoder 105
14.4.1 Technical Data 105
14.4.2 Description of Connections 105
14.4.3 Incremental Encoder Cable 106
15 Ordering Information 107
15.1 List of Documentation 107
15.2 Options 107
Appendix A: List of Illustrations 109
List of appendices
Appendix A: Recent Revisions 113
Appendix B: Glossary 115
Appendix C: List of Abbreviations 117
Appendix D: Index 118

Table of Contents
10 Jetter AG

JetMove 208-480 1.1 General Information
Jetter AG 11
TableofContents 1 Safety Instructions
1.1 General Information
The digital servo amplifier JetMove 208-480 fulfils the accepted safety regulations
and standards. Special emphasis was given to the safety of the users.
The following additional regulations apply to the user:
• Pertinent accident prevention regulations;
• Accepted safety rules;
• EC guidelines and other country-specific regulations.
1.1.1 Usage to the Intended Purpose
Usage to the intended purpose includes operation in accordance with this user
manual.
The digital servo amplifier JetMove 208-480 may only be operated in the closed
control cabinet and within the range of the set values.
Do not apply a voltage to the digital servo amplifier JetMove 208-480 that is
higher than the prescribed operating voltage.
Each of the three phases of the digital servo amplifier JetMove 208-480 has got an
operating voltage ranging between AC 340 V and AC 530 V. Thus, the digital servo
amplifier JetMove 208-480 comes under the EG Low Voltage Directive.
It is the explicit purpose of the digital servo controller JetMove 208-480 to
torque-, speed- and/or position-control, and to drive brushless synchronous
servo motors, asynchronous motors and three-phase stepper motors. The
rated voltage of the motors must be higher than, or at least equal to, the DC
link voltage supplied by the servo amplifier.
The digital servo amplifier JetMove 208-480 is used to drive machinery, such as
conveyors, production machines, and handling machines.
1.1.2 Non-Intended Use
The digital servo amplifier JetMove 208-480 must not be used in technical
systems which to a high degree have to be fail-save, e. g. ropeways and
aeroplanes.
Please do not use the integrated braking circuit in applications, where safety
hazards can occur.
The JetMove 204-480 is no safety-related part as per Machinery Directive 2006/
42/EC. This servo amplifier is not qualified for safety-relevant applications and
must, therefore, NOT be used to protect persons.
An exception to this rule is the STO function of devices with the -S1 option, see
chapter 13 "Safe Torque OFF (STO) (Option)", page 97.

1 Safety Instructions
12 Jetter AG
1.1.3 Qualified Personnel
Depending on individual phases of the product life cycle, there are different demands
on the personnel being involved. These demands have to be met, in order to grant
safety in handling the JetMove 208-480 at each phase of the product life cycle.
1.1.4 Modifications and Alterations to the
Module
Due to safety reasons, neither opening the digital servo amplifier
JetMove 208-480, nor carrying out any modifications or alterations to the
device and its functions is allowed.
Any modifications to the servo amplifier JetMove 208-480 not expressly authorized
by the manufacturer will result in a loss of any liability claims to Jetter AG.
The original parts are specifically designed for the servo amplifier JetMove
208-480. Parts and equipment of other manufacturers are not tested on our
part, and are, therefore, not released by us.
The installation of such parts may impair the safety and the proper functioning of the
digital servo amplifier JetMove 208-480.
Any liability on the part of Jetter AG for any damages resulting from the use of non
original parts and equipment is excluded.
1.1.5 Servicing and Repairs
Repairs at the digital servo amplifier JetMove 208-480 must not be carried out by the
operator. The digital servo amplifier JetMove 208-480 does not contain any parts to
be repaired by the operator.
For being repaired, the servo amplifier JetMove 208-480 must be sent to Jetter AG.
Phase of the Product
Life Cycle
Minimum Demands on the Personnel
Transport / Storage: Only properly trained and instructed personnel with
knowledge of correctly handling electrostatically
sensitive components.
Mounting /
Installation:
Trained personnel specified in electrical automotive
engineering, such as industrial electronics engineers.
Commissioning /
Programming:
Trained and instructed specialist personnel having got
broad knowledge and experience in electrical
engineering / motion systems, such as industrial
electronics engineers of automation engineering.
Operation: Only trained, instructed and authorized personnel with
knowledge of correctly handling electronic devices.
Decommissioning: Trained personnel specialized in electrical automotive
engineering, such as industrial electronics engineers.

JetMove 208-480 1.2 Ensure Your Own Safety
Jetter AG 13
The digital servo amplifier JetMove 208-480 is maintenance-free. Therefore,
absolutely no inspection or maintenance works are required for the operation of the
module.
1.1.6 Disposal
In case of obvious damage or erratic behavior, the servo amplifier must not be used
any more.
The environmental regulations for the respective country apply to disposing of the
digital servo JetMove 208-480 amplifier on the operating company’s premises.
You can disassemble the digital servo amplifier JetMove 208-480 into its main
components by unscrewing it (aluminium heat sink and side plate, steel casing cover,
electronic boards).
1.2 Ensure Your Own Safety
1.2.1 Malfunctions
DANGER
Isolate the digital servo amplifier JetMove 208-480 from the mains, if
maintenance works have to be carried out. By doing so, you will prevent
accidents resulting from electric voltage and moving parts.
Please follow the information given in chapter 1.3 "Residual Dangers",
page 16.
Safety and protective devices, e.g. the barrier and cover of the terminal
box must never be shunted or by-passed.
Dismantled protective equipment, such as the fuses and the thermal motor
circuit-breakers, must be reattached prior to commissioning and checked
for proper functioning.
Before commissioning, the machine manufacturer must carry out a danger
analysis of the respective machine and take adequate measures so that
inadvertent motions will not lead to personal injury and to material
damage.
In the case of malfunctions or other faults, please immediately
separate the digital servo amplifier JetMove 208-480 from the mains.
Please follow the information given in chapter 1.3 "Residual Dangers",
page 16.
Malfunctions or other damages are to be reported to a responsible person
at once.
Secure the digital servo amplifier JetMove 208-480 against misuse or
accidental use.

1 Safety Instructions
14 Jetter AG
1.2.2 Information Signs and Labels
1.2.3 Earthing Procedure
Markings, information signs, and labels always have to be observed and
kept readable.
Damaged or unreadable information signs and labels have to be replaced.
Screw the enclosure of the digital servo amplifier JetMove 208-480 onto a
highly conducting, earthed panel.
Do only use the digital servo amplifier JetMove 208-480 at the three-
phase, earthed industrial network (TN network, TT network with earthed
neutral, 5,000 A max, symmetric rated current at 400 / 480 V + 10 %).
The digital servo amplifier must not be operated when connected to
unearthed networks and to unsymmetrically earthed networks.
The leakage current is greater than 3.5 mA. In order to avoid electric
shocks, a second protective earth conductor is required.
For proper earthing, take the following measures:
• Connect the protective earth bus to the PE (GND) bolt (1) located on the
top side of the rack as well as to the PE (GND) terminal X1 (2) (please
refer to fig. 1).
The cross-sectional area of the two earthing conductors must be equal
to, or greater than, the cross-sectional area of the supply lines
(1.5 mm²/ AWG 16 min.).
• Provide a durable connection with the power supply of the digital servo
amplifier JetMove 208-480.
• The PE (GND) bus must be wired according to the connection diagram
(cf. chapter 10 "Connection Diagrams", page 85).
NOTICE
Follow the installation instruction below for the tightening torque of the PE bolt (1)
so that it does not become loose or even break off:
Do not overtighten the nut of the PE bolt (1). The maximum tightening
torque is 3 Nm!

JetMove 208-480 1.2 Ensure Your Own Safety
Jetter AG 15
Fig.: 1: Double earthing
12
NOTICE
Do not install an earth-leakage current breaker in the mains power
supply circuit.
If this advice is disregarded and an ELCB is installed, it will switch off the
servo amplifier although there is no error.
When an ELCB needs to be installed, an isolating transformer must be used.

1 Safety Instructions
16 Jetter AG
1.3 Residual Dangers
1.3.1 Hazards During Operation
WARNING
Hazard caused by high operating voltage!
Extremely hazardous voltages of up to 850 V may occur!
These voltages lead to muscle cramps, burns, unconsciousness, respiratory
standstill, and death.
During operation, all coverings and control cabinet doors must be kept
closed.
Do not open the device.
Do by no means disconnect the electric connections of the digital servo
amplifier JetMove 208-480 when it is live.
WARNING
Do not touch the terminals X1, X62, and X63 while the servo amplifier
is running.
In the given context, the terminals have the following meaning:
X1: AC 400/480 V voltage supply
X62: DC motor voltage up to 850 V
X63: DC link voltage up to 850 V
WARNING
Hot Surfaces!
During operation, the surfaces, respectively the heat sinks of the digital servo
amplifier JetMove 208-480 can heat up. The internal heat sink can reach
temperatures of up to 85 °C.
Do by no means touch the enclosure of the digital servo amplifier
JetMove 208-480 near the internal heat sink during operation and
during the cooling-off period after switching off the device.
Ensure that no temperature sensitive parts are attached to the digital servo
amplifier JetMove 208-480

JetMove 208-480 1.3 Residual Dangers
Jetter AG 17
WARNING
Danger in a potentially explosive atmosphere!
Do not operate the digital servo amplifier JetMove 208-480 in a
potentially explosive atmosphere.
CAUTION
Danger of injuries caused by mechanic force!
The digital servo amplifier JetMove 208-480 runs a servo motor. This servo
motor moves mechanic parts or sharp edges. Therefore, failure or malfunctioning
of the digital servo amplifier JetMove 208-480 can be dangerous for man or
damage the manufacturing plant to an amount depending on the respective kind
of plant. This should be prevented by installing additional safety devices.
• One safety precaution is to install a second set of limit switches to interrupt the
power supply of the motor.
• Another safety precaution would be installing a guard.
Make sure that hazards to persons are precluded even when the drive is
moving unintentionally.
WARNING
Do not remove any guards.
Do not wear gloves, lest they could get caught in the rotating shaft.
Never touch a rotating drive shaft.

1 Safety Instructions
18 Jetter AG
1.3.2 Hazards after POWER has been
Turned OFF
1.4 Instructions on EMI
The digital servo amplifier JetMove 208-480 is intended for use in industrial
surroundings. This module can cause radio interferences in residential areas. This
module is operated at the operator's own risk.
The noise immunity of a system depends on the weakest component of the system.
For this reason, correct wiring and shielding of cables is of paramount importance.
WARNING
Danger resulting from electric shock!
Up to 7 minutes after switching off the operating voltages, capacitors still carry
hazardous residual voltages.
As a precaution, measure the voltage in the DC link circuit (amplifier
terminal) and wait until it has fallen below DC 40 V.
Always wait at least 7 minutes after switching off the device, before
separating it from the mains or loosening the connections.
Always wait at least 10 minutes after switching off the device before taking
the following actions:
– Touching the screws of the terminals X1, X62 and X63;
– Disconnecting the terminals and touching the contacts.
NOTICE
Measures for increasing immunity to interference:
Earth the device adequately according to chapter 1.2.3 "Earthing
Procedure", page 14.
Connect all grounding terminals of the JetMove 208-480. A double
grounding terminal is required!
– Connect the protective earth terminal located on the enclosure.
– Connect the protective earth to terminal X1.
Please refer to fig. 1 on page 15.
The distance between the optional line filters and the digital servo amplifier
JetMove 208-480 must be as short as possible.

JetMove 208-480 1.4 Instructions on EMI
Jetter AG 19
When of a motor cable with included brake lines is used, these brake lines
must be shielded separately .
Follow the instructions given in Application Note 016 "EMC-Compatible
Installation of the Electric Cabinet" published by Jetter AG.
The following instructions are excerpts from Application Note 016:
On principle, physical separation should be maintained between signal
and power lines. We recommend spacings greater than 20 cm. Cables and
lines should cross each other at an angle of 90°.
Shielded cables must be used for the following lines:
Analog lines, data lines, motor cables coming from inverter drives (servo
output stage, frequency converter), lines between components and
interference suppressor filter, if the suppressor filter has not been placed
at the component directly.
Shield cables at both ends.
Unshielded wire ends of shielded cables should be as short as possible.
The entire shield must be drawn behind the isolation, its greatest possible
service area being clamped under a flat grounded strain relief.
When male connectors are used:
The shield must, in its entire perimeter, be drawn behind the shielding
clamp of the metallised connector housing, respectively of the EMC gland
bushing, its greatest possible surface area being clamped under a strain
relief.
Only use metallised connectors, e.g. SUB-D with metallised housing.
Make sure that the strain relief is directly connected with the housing here
as well (see fig. 2).

1 Safety Instructions
20 Jetter AG
Fig.: 2: Shielding of SUB-D connectors in conformity with the EMC standards
This manual suits for next models
1
Table of contents
Other Jetter Amplifier manuals
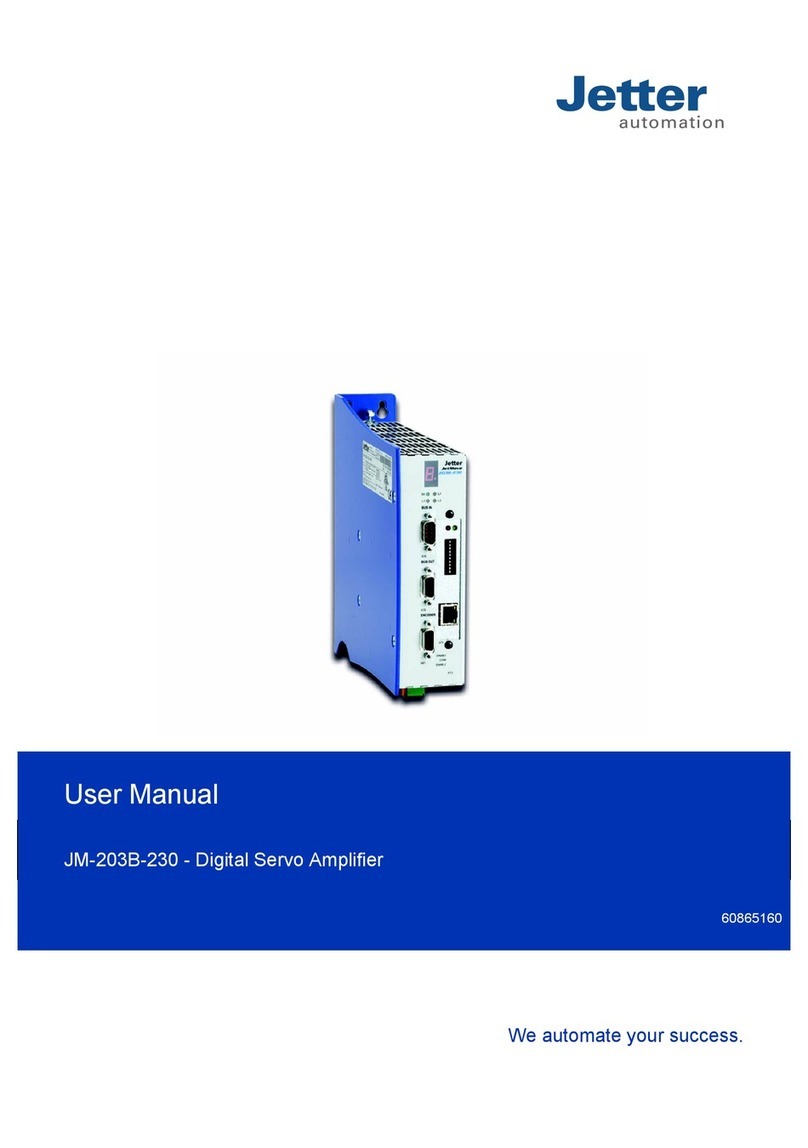
Jetter
Jetter JM-203B-230 User manual
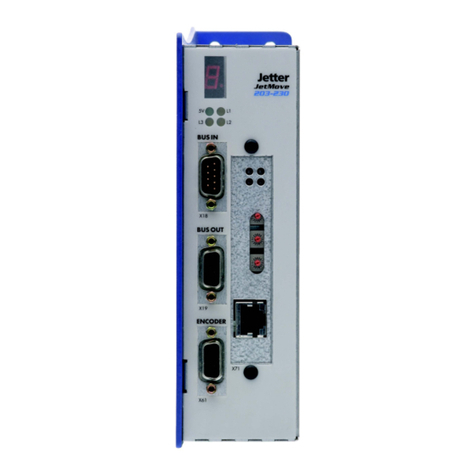
Jetter
Jetter JetWeb JetMove 203-230 User manual

Jetter
Jetter JM-208-480-OEM User manual
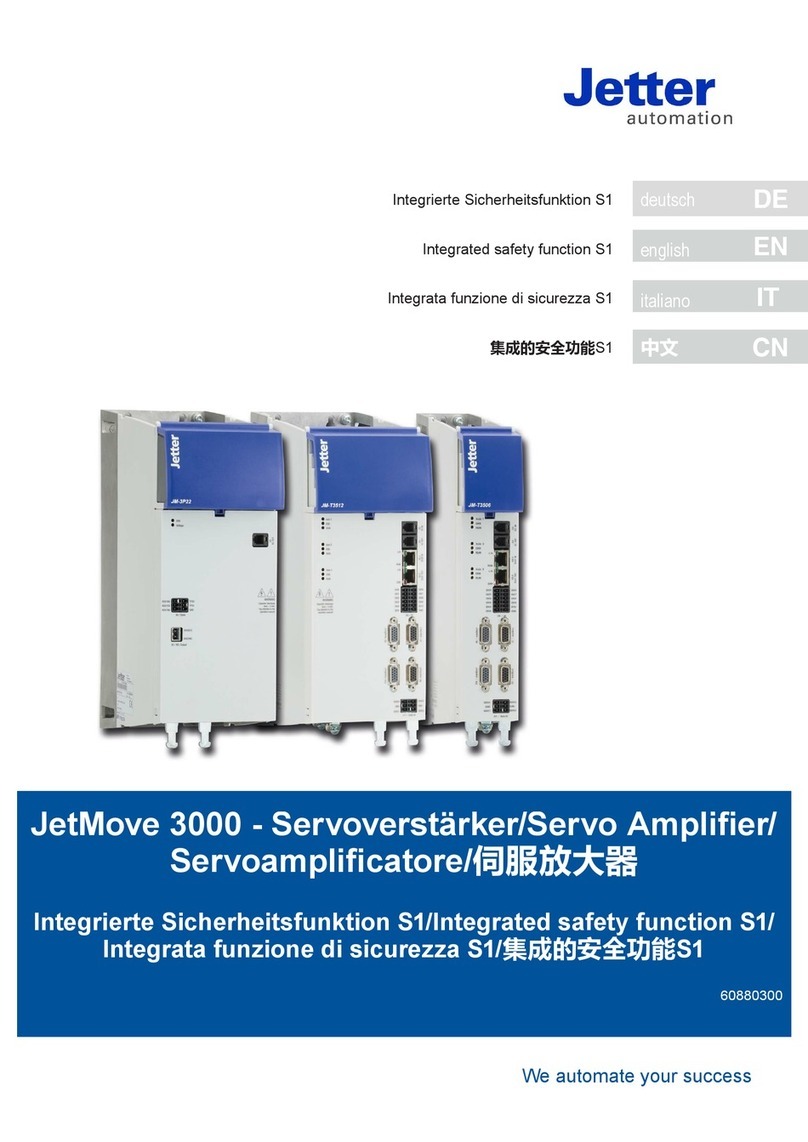
Jetter
Jetter JM-35 S1 Series User manual
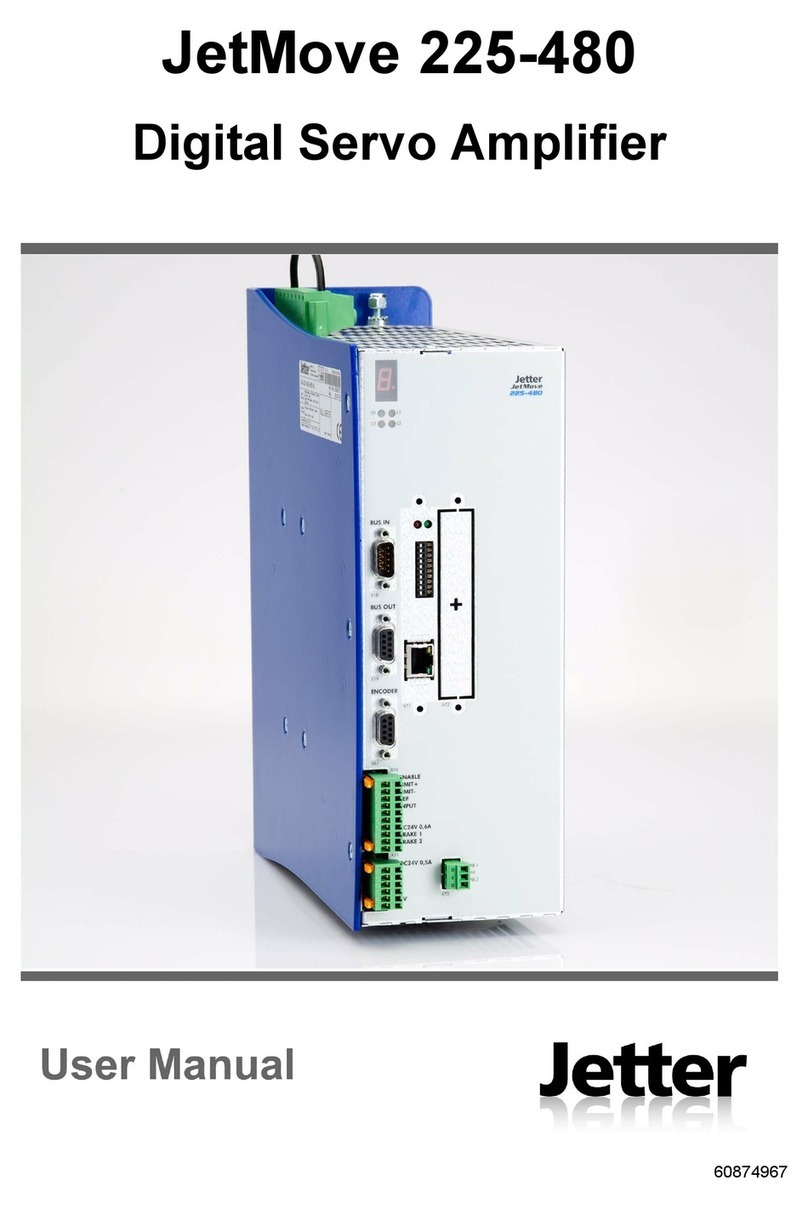
Jetter
Jetter JetMove 225-480 User manual

Jetter
Jetter JM-108 User manual
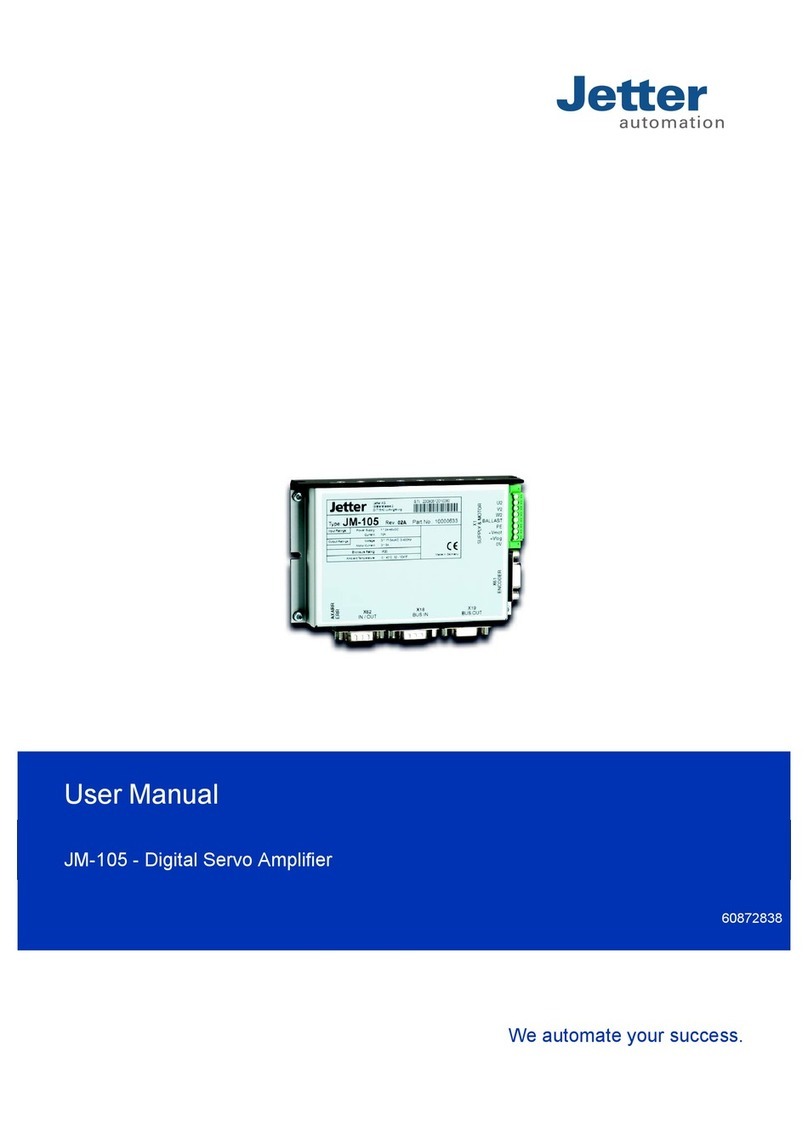
Jetter
Jetter JM-105 User manual
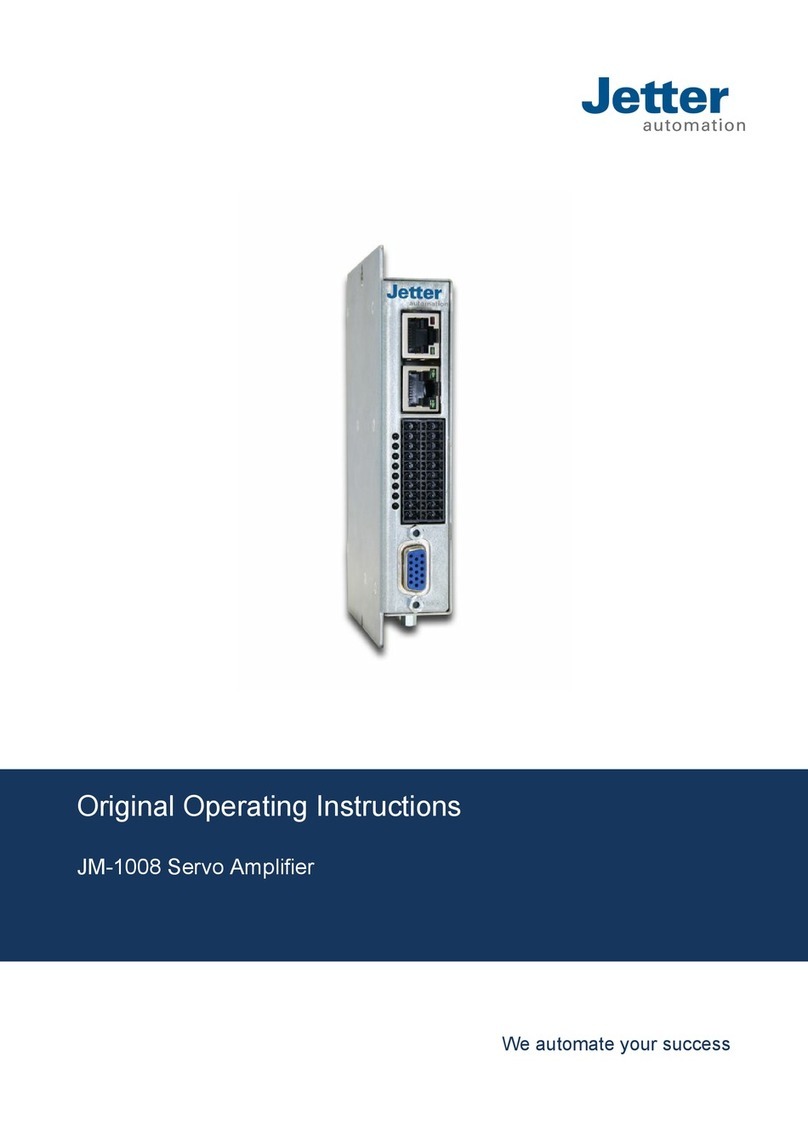
Jetter
Jetter JM-1008 User manual
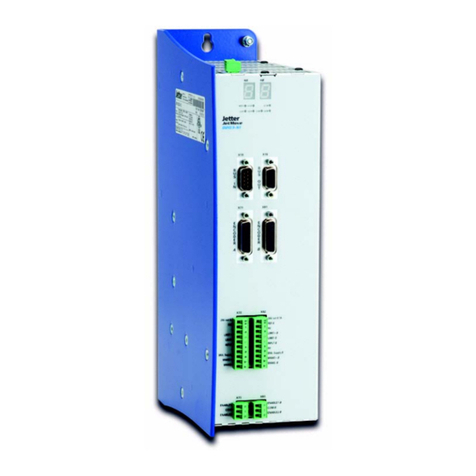
Jetter
Jetter JetMove D203 User manual
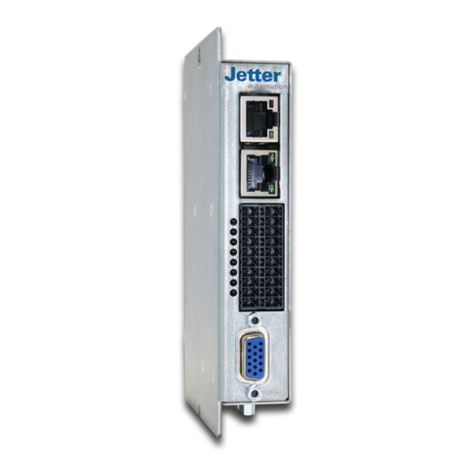
Jetter
Jetter JetMove JM-100 S1 Series User manual