Johnson Controls EasyIO FW Series User manual

EasyIO FW Series
Modbus Subordinate User Guide
LIT-12013785

Disclaimer
Confidentiality Notice
The information contained in this document is confidential information of Johnson Controls (S) Pte Ltd. Such
information and the software described herein, is furnished under a license agreement and may be used
only in accordance with that agreement.
The information contained in this document is provided solely for use by Johnson Controls (S) Pte Ltd employees,
licensees, and system owners; and, except as permitted under the below copyright notice, is not to be released to,
or reproduced for, anyone else.
While every effort has been made to assure the accuracy of this document, Johnson Controls (S) Pte Ltd is not
responsible for damages of any kind, including without limitation consequential damages, arising from the
application of the information contained herein. Information and specifications published here are current as of the
date of this publication and are subject to change without notice. The latest product specifications can be found by
contacting our corporate headquarters or support channel.
Trademark Notice
EasyIO logos are registered trademarks of Johnson Controls (S) Pte Ltd.
BACnet and ASHRAE are registered trademarks of American Society of Heating, Refrigerating and Air-
Conditioning Engineers. All other product names and services, mentioned in this publication, that are
known to be trademarks, registered trademarks, or service marks are the property of their respective
owners.
Freeboard is an open source real time Dashboard builder.
Copyright and Patent Notice
This document may not, in whole or in part, be copied, photocopied, reproduced, translated, or reduced
to any electronic medium or machine-readable form without prior written consent from Johnson Controls (S) Pte
Ltd
Copyright © 2019 Johnson Controls (S) Pte Ltd. All rights reserved
Disclaimer
The material in this manual is for information purposes only. The contents and the product it
describes are subject to change without notice. Johnson Controls (S) Pte Ltd makes no
representations or warranties with respect to this manual. In no event shall Johnson Controls (S) Pte Ltd be liable for
any damages, direct or incidental, arising out of or related to the use of this manual.
Johnson Controls (S) Pte Ltd
31, International Business Park,
#03-02, Singapore 609921
Singapore 609921

United States
Canada
Industry Canada Statement(s)
The term IC before the certification/registration number only signifies that the Industry Canada technical specifications
were met.
ISED Radio Frequency (RF) Exposure: This equipment complies with FCC and ISED Canada radiation exposure limits
set forth for an uncontrolled environment. The user should avoid prolonged exposure within 20 cm of the antenna, which
may exceed the FCC or RSS-102 radio frequency exposure limits.
Exposition aux fréquences radio (RF) de la ISDE : Cet équipement se conforme aux limites d'exposition aux radiations
de la FCC et de ISDE Canada, établies pour un environnement non contrôlé. L'utilisateur doit éviter une exposition
prolongée à moins de 20 cm de l'antenne, qui peut dépasser les limites d'exposition aux fréquences radio FCC ou RSS-
102.
This device has been designed to operate with an antenna having a maximum gain of 2 dB. Antenna having a higher
gain is strictly prohibited per regulations of Industry Canada. The required antenna impedance is 50 ohms.
To reduce potential radio interference to other users, the antenna type and its gain should be so chosen that the
Equivalent Isotropically Radiated Power (EIRP) is not more than that required for successful communication.
Le terme « IC » précédant le numéro d'accréditation/inscription signifie simplement que le produit est conforme aux
spécifications techniques d'Industry Canada.
Cet appareil a été conçu pour fonctionner avec une antenne d'un gain maximum de 2 dBi. En application des
réglementations d'Industry Canada, l'utilisation d'une antenne de gain supérieur est strictement interdite.
L'impédance d'antenne requise est de 50 ohms.
Pour réduire les interférences radio potentielles avec les dispositifs d'autres utilisateurs, le type d'antenne et son gain
doivent être choisis de façon à ce que la Puissance Isotrope Rayonnée Équivalente (PIRE) ne soit pas supérieure à la
puissance nécessaire pour une bonne communication.
Compliance Statement (Part 15.19)
This device complies with Part 15 of the FCC Rules. Operation is subject to the following two conditions:
1.
This device may not cause harmful interference, and
2.
This device must accept any interference received, including interference that may cause undesired
operation.
Warning (Part 15.21)
Changes or modifications not expressly approved by the party responsible for compliance could void the user’s authority to
operate the equipment.
RF Exposure
To comply with FCC RF exposure requirements for mobile transmitting devices, this transmitter should only be used or
installed at locations where there is at least 20 cm separation distance between the antenna and all persons.

Table of Contents
Introduction ................................................................................................................................................................... 5
Prerequisites .................................................................................................................................................................. 5
Device software configuration limitations..................................................................................................................... 6
Configuring the Modbus serial network ........................................................................................................................ 6
Configuring the Modbus TCP subordinate network ...................................................................................................... 9
Technical support......................................................................................................................................................... 12

Introduction
The EasyIO® FW series supports use of a Modbus subordinate through the Modbus subordinate driver. The series
facilitates the following Modbus subordinate protocols:
•Modbus RTU subordinate
•Modbus TCP Subordinate
The minimum firmware requirement for best performance of the BACnet protocol is v1.0b17a or later for the V1
series and v2.0b17a or later for the V2 series. If you enable the BACnet MSTP client or BACnet MSTP server, you
disable the Modbus serial master and Modbus serial subordinate. However, the BACnet IP server and Modbus TCP
subordinate are still available.
Primary protocol in use
Other available protocols
BACnet Client (IP +
MSTP)
BACnet IP Client
BACnet
MSTP Server
BACnet IP Server
Modbus Serial Master
Modbus TCP Master
Modbus Serial
Subordinate
Modbus TCP
Subordinate
BACnet Client (IP + MSTP)
✓
✓
✓
✓
BACnet MSTP Server
✓
✓
✓
✓
BACnet IP Server
✓
✓
✓
✓
✓
BACnet IP Server
✓
✓
✓
✓
✓
Modbus Serial Master
✓
✓
✓
✓
Modbus TCP Master
✓
✓
✓
✓
Modbus Serial Subordinate
✓
✓
✓
✓
Modbus TCP Subordinate
✓
✓
✓
✓
✓
Modbus TCP Subordinate
✓
✓
✓
✓
✓
Note: You can only choose BACnet MS/TP Server or Modbus serial. However, BACnet IP server and Modbus TCP
Subordinate are always enabled
Prerequisites
•CPT Tool dated 28th May 2020 or later.
•FW Series with firmware v1.0b17, v2.0b17 or later.

Device software configuration limitations
There are the following limitations for the Modbus RTU subordinate/Modbus TCP subordinate:
Max network allowed
1 (of both drivers)
Max discrete points allowed
200 register addresses (total)
Max coil output allowed
200 register addresses (total)
Max input register allowed
200 register addresses, depending on data type.
Integer data type occupies 1 register address
Float data type occupies 2 register addresses
Long data type occupies 2 register addresses
Max holding register allowed
200 register addresses, depending on data type.
Integer data type occupies 1 register address
Float data type occupies 2 registers addresses
Long data type occupies 2 registers addresses
The FW series can have the Modbus subordinate RTU and Modbus subordinate TCP networks on the same device.
However, there are register addressing limitations that you must observe when both network drivers are on the
same device. For example, the RTU and TCP networks share the coil address space in the FW series. If you use a
coil address in the RTU network, you cannot use the same address in the TCP network. For example, if you create
an RTU network and use a 0 coil address, the TCP network cannot create a new 0 coil address. However, you can
share the value from the RTU network coil address. If you require a new individual coil address, the network, RTU
or TCP, must employ the next available consecutive unused device coil address, irrespective of the network type.
Configuring the Modbus serial network
The architecture of the driver is deployed, as per the below procedure. You can drop the network object anywhere
in the Sedona app tree. It is best practice to create a separate folder for each network.
Network
Points
Note: To configure the Modbus subordinate driver, you must install the following kits as a minimum requirement:
•easyioFWMbSlave, 1.0.45.17.1 or higher
•easyioFWDriver, 1.0.45.17.1 or higher
To install the kits, complete the following steps:
1. Connect to the controller with CPT Tools and the following default logon credentials:
•IP address: 192.168.10.30
•Username: admin
•Password: < no password >
2. Add the kits to the controller using kit management and install easyioFWMbSlaveand easyioFWDriver.

3. Select easyioFWMbSlave from the Sedona palette and drag ModbusSlaveSerialNetwork to your app. You
can drag the object to the EasyIO folder or create a new folder for the serial network object. In the
following example, the object is in a new folder with a Modbus label.
4. Double-click the object to view the property sheet and configure the RTU network parameters, such as
baud rate, parity, setting the device address on the serial network, and so on.
5. Enable the network, ensure that you use the D terminal for the serial network connection, and observe
the correct polarity.
6. Drag the Modbus serial register type object to the Network object.
Note: The register object must be a child of the Network object. You can create folders below the Network
Object to facilitate logical management of the register objects. Modbus registers support register
addresses in a decimal format. By default, all registers are set to the disabled mode of enable = false. You
must enable each register object in the application, so that other systems, such as the Modbus master,
can discover the register.

There are a maximum of 200 input registers and holding registers. The FW series Modbus serial subordinate
network supports three data types including the Integer, Float, and Long data types. If you export a 16 bit register,
the first point is address 0 and the second point is address 1. If you export as 32 bit register, such as a float or long
data type, you use two registers. For example, if the first point is 32 bit, you use address 0. For the second point,
you use address 2 because the first point uses address 0 and address 1.
Input/
Holding
Registers
Data Type
Precision
Remarks
Word
16 bit
16 bit Signed Integer Standard
Long
32 bit
32 Bit Signed Integer Standard
Float
32 bit
32 Bit Float Standard

Name Register Type
-------------------- --------------
Set Point (Float type) floating point (2 registers)
Duration (Long type) 32-bit data (2 registers)
Count (Integer) 16-bit data (1 register)
Delay (Signed Integer) 16-bit data (1 register)
The Modbus register does not export any value. You must manually link a valid value to the Modbus register. For
example, in the following figure, you can export a temp value as a Modbus register.
Configuring the Modbus TCP subordinate network
The architecture of the driver is deployed, as per the below procedure. You can drop the network object anywhere
in the Sedona app tree. It is best practice to create a separate folder for each network.
Network
Points
Note: To configure the Modbus subordinate driver, you must install the following kits as a minimum requirement:
•easyioFWMbSlave, 1.0.45.17.1 or higher
•easyioFWDriver, 1.0.45.17.1 or higher
To install the kits, complete the following steps:
1. Connect to the controller with CPT Tools and the following default logon credentials:
•IP address: 192.168.10.30
•Username: admin
•Password: < no password >
2. Add the kits to the controller using kit management and install easyioFWMbSlave and easyioFWDriver on
your controller.
3. Select easyioFWMbSlave from the Sedona Palette and drag ModbusSlaveTCPNetwork to your app. You can
drag the object to the EasyIO folder or create a new folder for the Serial Network Object. In the following
example, the object is in a new folder with a Modbus label.

4. Double-click the object to view the property sheet and enable the network.
5. Drag the Modbus register type object to the Network object. The register object must be a child of the
Network object. Modbus registers support register addresses in a decimal format. By default, all registers
are set to the disabled mode. You must enable each register object in the application, so that other
systems can discover the register.

Input/
Holding
Registers
Data Type
Precision
Remarks
Word
16 bit
16 bit Signed Integer Standard
Long
32 bit
32 Bit Signed Integer Standard
Float
32 bit
32 Bit Float Standard

Technical support
For technical issues, contact one of the following regional support channels:
•Worldwide and Asia Pacific Support: [email protected]
•Americas Support: [email protected]
•Europe Support: [email protected]
Important: Use this FW series controller only as an operating control. Where failure or malfunction
of the FW could lead to personal injury or property damage to the controlled equipment or
other property, additional precautions must be designed into the control system. Incorporate and
maintain other devices, such as supervisory or alarm systems or safety or limit controls, intended to
warn of or protect against failure or malfunction of the FW.
Important: Utiliser ce FW controller uniquement en tant que dispositif de contrôle de
fonctionnement. Lorsqu'une défaillance ou un dysfonctionnement du FW risque de provoquer
des blessures ou d'endommager l'équipement contrôlé ou un autre équipement, la conception
du système de contrôle doit intégrer des dispositifs de protection supplémentaires. Veiller dans ce
cas à intégrer de façon permanente d'autres dispositifs, tels que des systèmes de supervision ou
d'alarme, ou des dispositifs de sécurité ou de limitation, ayant une fonction d'avertissement ou de
protection en cas de défaillance ou de dysfonctionnement du FW.
Product warranty
This product is covered by a limited warranty, details of which can be found at
www.johnsoncontrols.com/buildingswarranty.
Single point of contact
APAC
Europe
NA/SA
JOHNSON CONTROLS
C/O CONTROLS PRODUCT MANAGEMENT
NO. 32 CHANGJ
IJANG RD NEW DISTRICT
WUXI JIANGSU PROVINCE 214028
CHINA
JOHNSON CONTROLS
WESTENDHOF 3
45143 ESSEN
GERMANY
JOHNSON CONTROLS
507 E MICHIGAN ST
MILWAUKEE WI 53202
USA
Contact information
Contact your local branch office: www.johnsoncontrols.com/locations
Contact Johnson Controls: www.johnsoncontrols.com/contact-us
Table of contents
Other Johnson Controls Network Hardware manuals
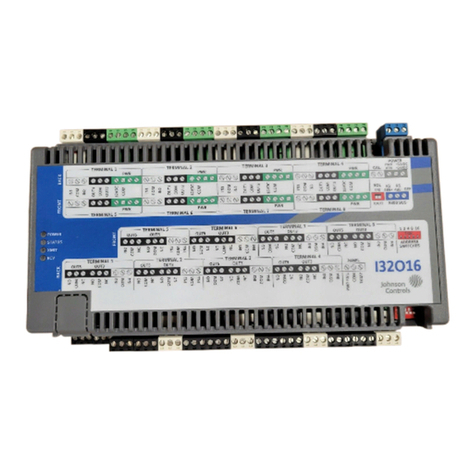
Johnson Controls
Johnson Controls S300 Series Manual
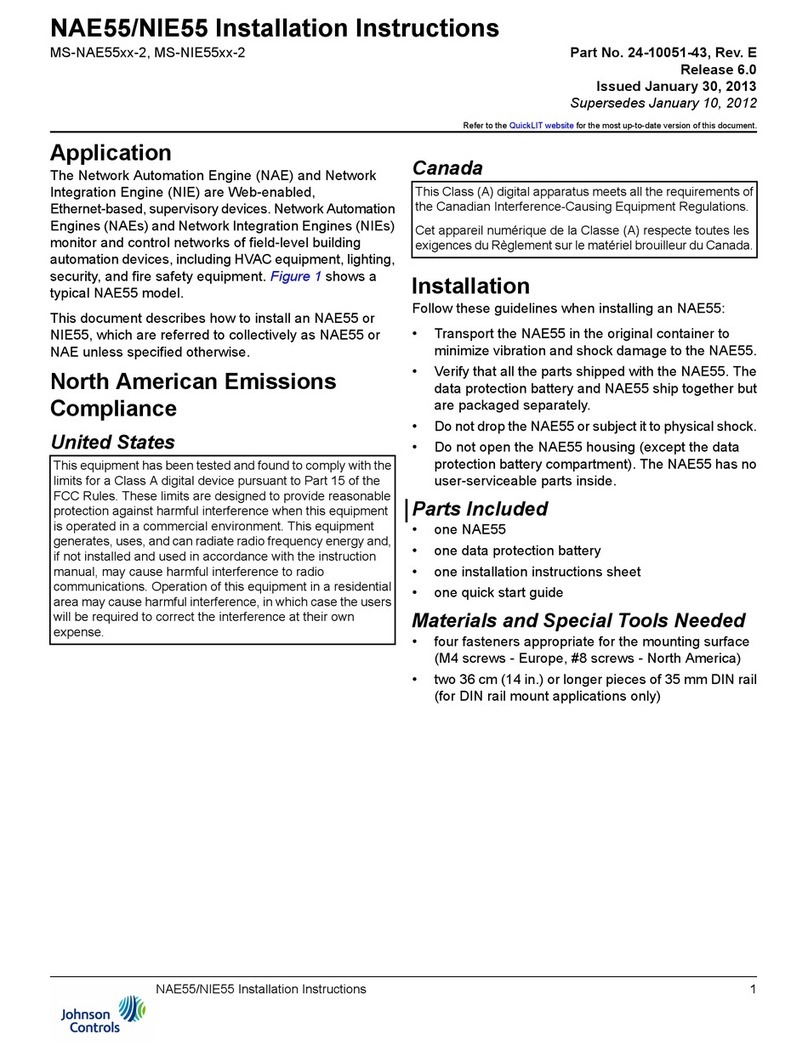
Johnson Controls
Johnson Controls NIE55 Series User manual
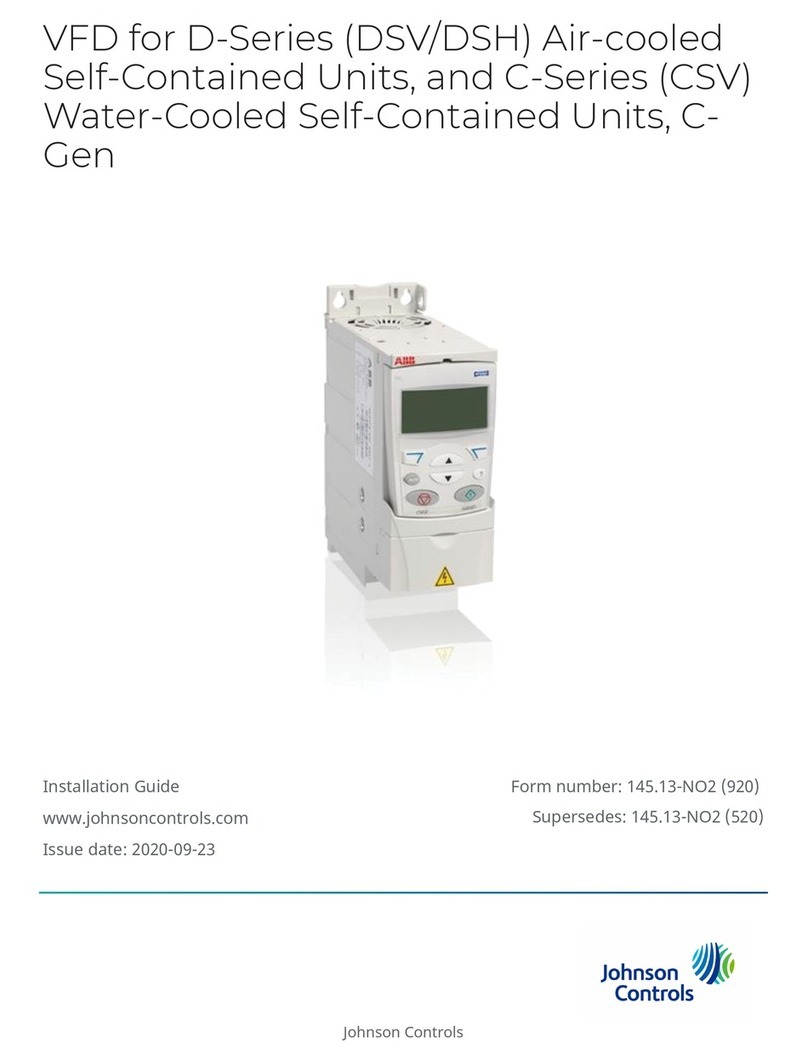
Johnson Controls
Johnson Controls D Series User manual
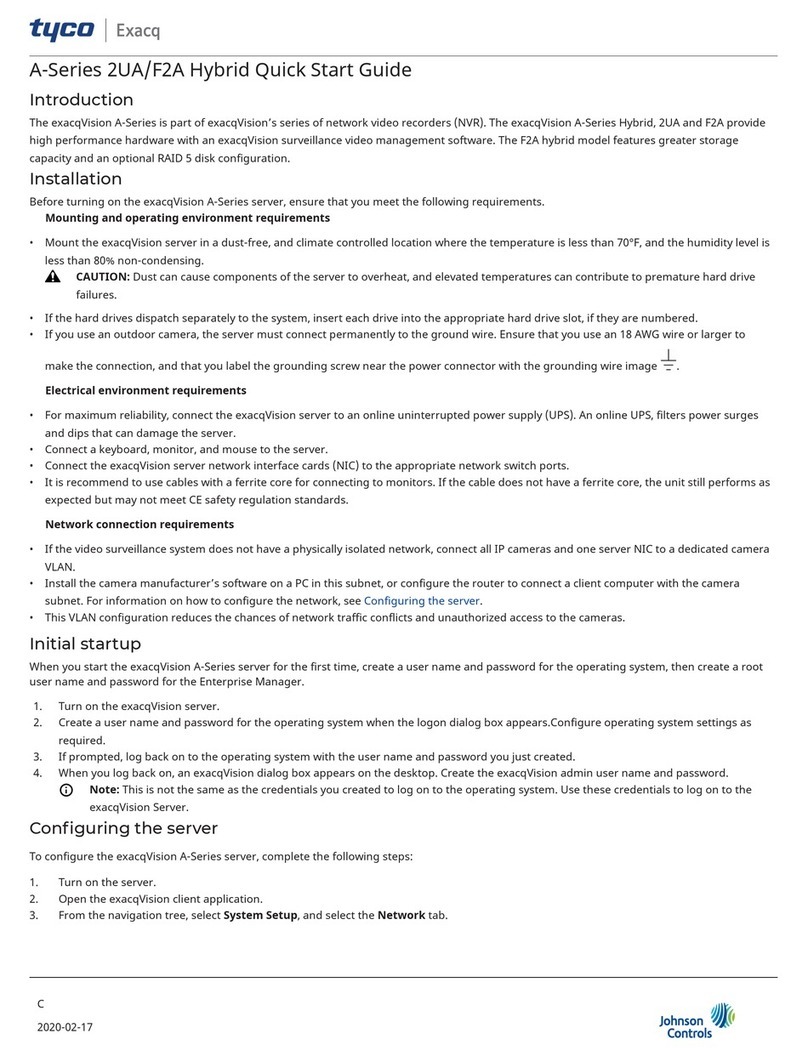
Johnson Controls
Johnson Controls Tyco exacqVision 2UA User manual
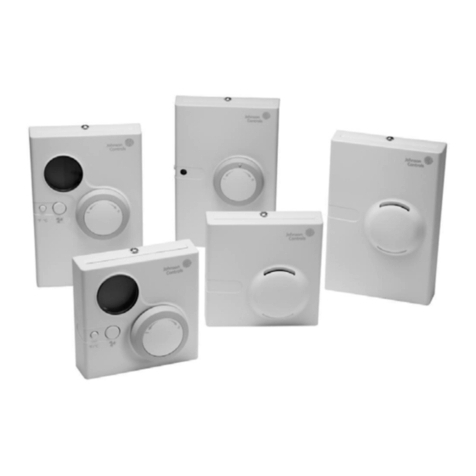
Johnson Controls
Johnson Controls Facility Explorer Service manual

Johnson Controls
Johnson Controls XP-910x User manual
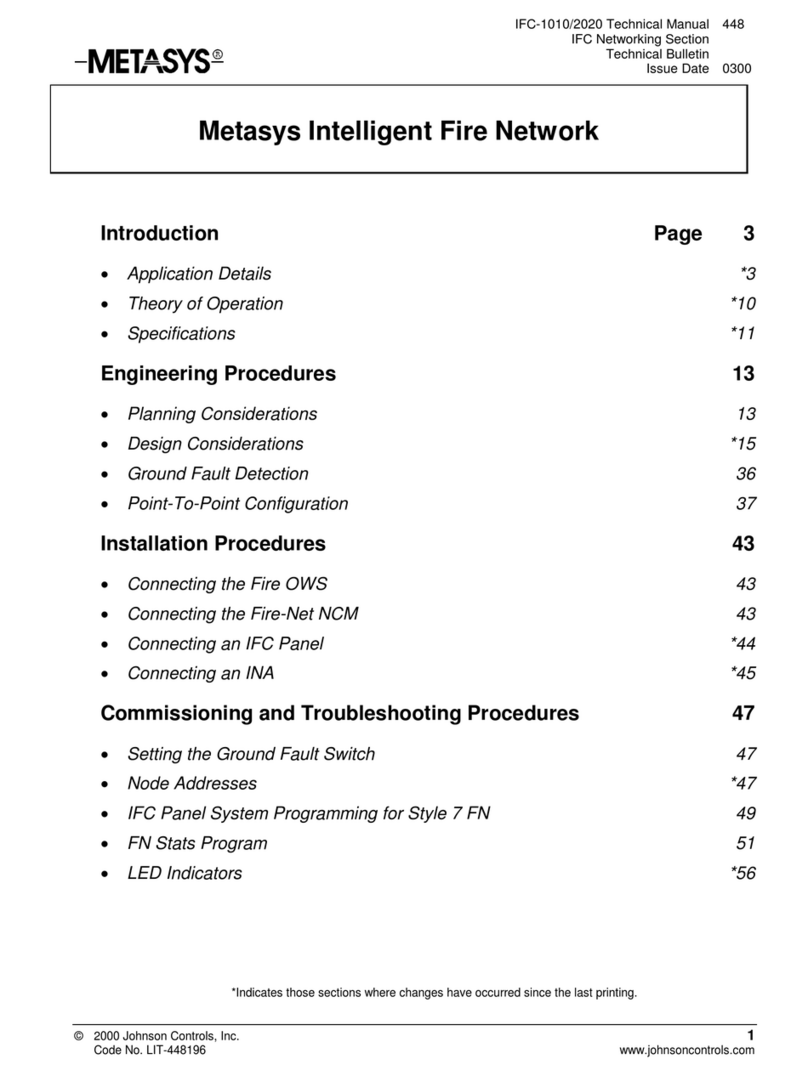
Johnson Controls
Johnson Controls Metasys Intelligent Fire Network User manual
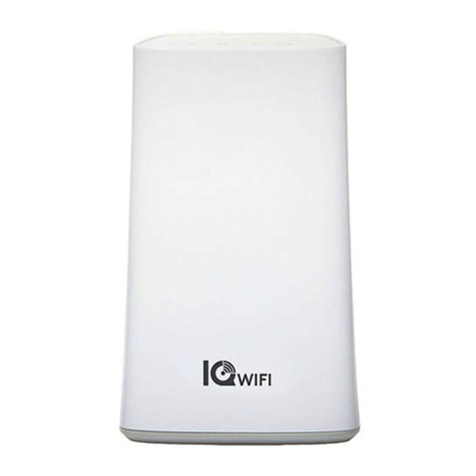
Johnson Controls
Johnson Controls IQ WIFI User manual

Johnson Controls
Johnson Controls Metasys NAE55 User manual
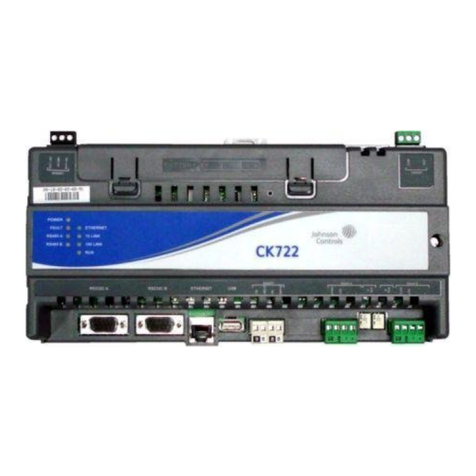
Johnson Controls
Johnson Controls CK722 User manual