Johnson Controls S300 Series Manual

24-10489-19 Revision B
December 2017
S300
Series
S300-DIN-RDR8S
and S300-DIN-I32O16
hardware
installation

Copyright 2017
Johnson Controls
All Rights Reserved
No part of this document may be reproduced without the prior permission of Johnson Controls.
If this document is translated from the original English version by Johnson Controls, all reasonable
endeavors will be used to ensure the accuracy of translation. Johnson Controls shall not be liable
for any translation errors contained herein or for incidental or consequential damages in connection
with the furnishing or use of this translated material.
Due to continuous development of our products, the information in this document is subject to
change without notice. Johnson Controls shall not be liable for errors contained herein or for
incidental or consequential damages in connection with furnishing or use of this material. Contents
of this publication may be preliminary and/or may be changed at any time without any obligation to
notify anyone of such revision or change, and shall not be regarded as a warranty.
Other Manufacturers’ Documentation
Johnson Controls does not duplicate documentation of other equipment manufacturers. When
necessary, Johnson Controls provides documentation that supplements that of other manufacturers.
When unpacking equipment, keep all original manufacturer documentation for future reference.
Technical Support
For factory technical support, Johnson Controls authorized field technicians or authorized dealer
representatives can contact Global Security Solutions Technical Support by phone at
can also call the Field Support Center at (800) 524-1330 or (414) 524-5000 and use options 6, 1, 7.
End users and customers should contact their local Johnson Controls branch or authorized dealer
for any of their support needs (technical support, maintenance contracts, on-site field support,
P2000 Software Service Agreements, Service Partnerships, and so on). Visit
http://www.johnsoncontrols.com/location-finder to find your local Johnson Controls office.
For material returns contact the branch if the material was purchased through a Johnson Controls
branch or through the Product Sales Operations Team, if ordered through the Advanced Order
Management System (AOMS) and follow the RMA process; or contact the authorized dealer
representative where the material was purchased directly.
Acknowledgments
Metasys® and Johnson Controls® are trademarks of Johnson Controls. All other company and
product names are trademarks or registered trademarks of their respective owners.

Declaration of Conformity
United States: This equipment has been tested and found to comply with the limits for a Class B
digital device, pursuant to Part 15 of the FCC rules. These limits are designed to provide
reasonable protection against harmful interference in a residential installation. This equipment
generates, uses and can radiate radio frequency energy and, if not installed and used in accordance
with the instructions, may cause harmful interference to radio communications. However, there is
no guarantee that interference will not occur in a particular installation. If this equipment does
cause harmful interference to radio or television reception, which can be determined by turning the
equipment off and on, the user is encouraged to try to correct the interference by one or more of the
following measures:
• Reorient or relocate the receiving antenna.
• Increase the separation between the equipment and receiver.
• Connect the equipment into an outlet on a circuit different from that to which the receiver is
connected.
• Consult the dealer or an experienced radio/TV technician for help.
The user is cautioned that changes and modifications made to the equipment without approval of
the manufacturer could void the user's authority to operate this equipment.
Canada: CAN ICES-3 (B)/NMB-3(B)
European Union: This product complies with the requirements of the EMC Directive.
This equipment must not be modified for any reason and it must be installed as stated in the
Manufacturer’s instructions. If this shipment (or any part thereof) is supplied as second-hand
equipment, equipment for sale outside the European Economic Area or as spare parts for either a
single unit or system, it is not covered by the Directives.

UNDERWRITERS LABORATORIES COMPLIANCE VERIFICATION SHEET
The following model numbers are listed under Underwriters Laboratories Inc. ® (UL) 1076 for
Proprietary Burglar Alarm Units and Systems, UL 294 for Access Control Systems Units and
Underwriters Laboratories of Canada ULC/ORD-C1076-86.
S300-DIN-RDR8S
S300-DIN-I32O16
When installed at the site the following requirements must be met to comply with these standards.
1. The S300-DIN-RDR8S and/or S300-DIN-I32O16 shall be mounted in subassembly
S300-DIN-L.
2. The S300-DIN-RDR8S and/or S300-DIN-I32O16 in combination with the S300-DIN-L must
be connected to a UL Listed Uninterruptible Power Supply that provides a minimum of 24
hours of AC emergency power.
3. The tamper switch must be enabled at all times.
4. Transient protection devices that are installed must not be removed or defeated.
5. Do not connect equipment to an AC power source that is controlled by a switch.
6. For a UL 294 Listed system the following Listed readers may be used.
7. UL 294 Performance Levels
Destructive Attack Level I
Endurance Level IV
Line Security Level I
Standby Power Level I
Manufacturer Model
HID Corp. 30387, 31503, 31815, 31880, 32005, 32788, 32985, 5355, 5365,
5395, 5405, 5455, 6005. All models may be followed by
additional suffixes.
13.56 MHZ Models - iCLASS Models R10, R15, R40, RP10,
RP15, RP40, RK40, RPK40. All models may be followed by
additional suffixes.
OSDP Models - iCLASS SE Models R10E, R15E, R30E, R40E,
RP10E, RP15E, RP30E, RP40E, RK40E, RPK40E. May be
followed by “XXX”, may be further followed by “NN”. Suffix
explanation X1=Reader Colors: K = Black, G = Gray, X2=
Wiring, N = Pigtail, T =Terminal, X3 = “R” or “N”. The suffix
“R” = Reader Employed with RS485 Module, “N” = No RS485
Module present.
pivCLASS Models – pivCLASS reader models R10E, R15E,
R30E, R40E, RP10E, RP15E, RP30E, RP40E, RPK40E and
RK40E, RPKCL40E, RKCL40E may be followed by “XXX”.
Suffix explanation X1 = Reader Colors: K = Black, G = Gray,
X2 = Wiring, N = Pigtail, T = Terminal, X3 = “R” or “N”. For use
with the model pivCLASS authentication module (PAM) M2000.
May be connected directly to S300-DIN-RDR8S Data 0/Data1
Wiegand interface.
Mercury Security Corp. MR-5

RDR8S and I32O16 Hardware Installation Introduction
24-10489-19 Rev. B
1
HARDWARE INSTALLATION
This document provides hardware installation instructions for the S300-DIN-
RDR8S and the S300-DIN-I32O16.
INTRODUCTION
The S300-DIN-RDR8S and S300-DIN-I32O16 modules provide interface
control for access and security devices associated with up to eight doors.
NOTE: Throughout this manual the S300-DIN-RDR8S module is also referred to
as the RDR8S, while the S300-DIN-I32O16 module is referred to as
the I32O16.
Figure 1: S300-DIN-RDR8S

RDR8S and I32O16 Hardware Installation Key Features
24-10489-19 Rev. B
2
Figure 2: S300-DIN-I32O16
KEY FEATURES
The key features of the RDR8S include:
• Wide range nominal voltage for power source (+12 to 24VDC)
• Support for S300 bus communications at 9600 or 19200 (Auto baud rate
detection 9600/19200 baud)
• Eight-door access control input/output interface, each door’s interface
consisting of:
– Supervised door sensor input, normally open or normally closed,
based on wired configuration
– Supervised “request to exit” switch input, normally open
– Supervised tamper and spare inputs
– Device interface (Wiegand Data0/Data1 or RS485)
– Door strike relay, SPDT (Single Pole Double Throw)
– Alarm shunt relay, SPDT
– Red lamp driver and green lamp driver (open collectors)
– +12VDC 250mA per reader power supply

RDR8S and I32O16 Hardware Installation Key Features
24-10489-19 Rev. B
3
• The OSDP Reader feature supports the use of HID OSDP Keypad Readers
type and HID OSDP Reader type (no keypad). The OSDP Reader feature:
– Adds Open Supervised Device Protocol (OSDP) v1.1 reader device
support.
Figure 1-1: OSDP System Diagram
– The OSDP reader implementation supports unencrypted
communications between the RDR8S and OSDP device. (OSDP
Standard version 2 SCF Encrypted Communications is not
supported.)
The following inputs are shared by all interfaces (one per unit):
• Calibration resistor input
• Supervised panel tamper and power fail inputs
The key features of the I32O16 include:
• Wide range nominal voltage for power source (+12 to 24VDC)
• Support for S300 bus communications at 9600 or 19200 (Auto baud rate
detection 9600/19200 baud)
• 32 input/output interface consisting of 8 terminals, each terminal including:
– 4 supervised inputs
– 2 relay outputs
– 2 open collector outputs (OUT1 and OUT2)
RDR8S
(PS-218)
E F G H
A B C D
CK721-A Controller
A B
Wiegand
reader
OSDP
reader
RDR2S-A
(PS-217)
A B
OSDP
reader
OSDP
reader Wiegand
reader

RDR8S and I32O16 Hardware Installation Application
24-10489-19 Rev. B
4
The following inputs are shared by all interfaces (one per unit):
• Calibration resistor input
• Supervised panel tamper and power fail inputs
APPLICATION
The RDR8S module supports up to eight doors per unit. The I32O16 module
supports 32 inputs, 16 relay outputs, and 16 open collector outputs per unit.
Both RDR8S and I32O16 use standard S300 bus (RS-485) communications
and can interface with the following controllers:
• CK722
• CK721-A version 3.0 and higher
The RDR8S provides the ability to configure supervised 4-state inputs and
unsupervised 2-state inputs. Any points not used for the door can be configured
as general purpose input/output (I/O) points, possibly eliminating the need to
purchase additional I/O modules for certain installations. The RDR8S provides
power for the card reader hardware. It does not provide power for door locking
hardware.
The I32O16 provides the ability to configure supervised 4-state inputs,
unsupervised 2-state inputs, and relay outputs. Additionally, 2 open collector
outputs per terminal are available.

RDR8S and I32O16 Hardware Installation Installation
24-10489-19 Rev. B
5
INSTALLATION
Unpacking the Equipment
Carefully inspect the shipping containers as soon as you receive them (with the
delivery agent present). Some shipping companies want to have an agent
present when a damaged container is opened. If a container is damaged, open it
immediately, inspect the contents, and have the agent make note on the
shipping document. Check the purchase order against the packing slips to
ensure the order is complete. If the contents of a container are damaged in any
way, notify the carrier and your Johnson Controls representative immediately.
Report any discrepancies to your Johnson Controls representative. Save the
packing materials for possible return shipments.
Package Contents
• S300-DIN-RDR8S or S300-DIN-I32O16 module
• Connectors set
•This manual
Tools Needed
Small, straight-blade screwdriver for securing wires in the terminal blocks.
MOUNTING
The module (RDR8S or I32O16) can be mounted on a flat surface, DIN rail, or
in a Johnson Controls’ approved enclosure, such as the S300-DIN-L.
For information on mounting the module in an enclosure, refer to the manual
provided with the enclosure.
DIN Rail Mounting
To mount an RDR8S or I32O16 module on a DIN rail:
1. Fully extend the white clips located on the bottom of the module.
2. Hook the module on top of the rail.
3. Push in the clips.

RDR8S and I32O16 Hardware Installation Mounting
24-10489-19 Rev. B
6
To remove a module from the DIN rail:
1. Pull down the clips at the bottom of the module.
2. Pull the bottom of the module out and lift it up.
Flat Surface Mounting
To mount an RDR8S or I32O16 module on a flat surface:
1. Make sure no connectors obstruct access to the clips on the bottom of
the module. If necessary, remove the connectors.
2. Fully extend the bottom clips.
3. Mount the module to the surface with mounting screws.
4. Replace the connectors, if previously removed.
Power Source
See the following table for power requirements.
Line Voltage Information
If the facility is located in an area where power lines are subject to frequent
lightning strikes, verify with the electric company that the building transformer
is equipped with surge protectors. These, as well as a “crowbar” type of
protection, can be installed at the main service entrance if the building
transformer is not equipped with lightning protection.
While lightning is one cause of power line transients, others can be internal or
external to the building environment. The general application of transient surge
suppression is low-cost insurance to ensure long life of the equipment being
installed.
Parameter Value
Input voltage +12 to 24VDC
Input current 2A at 24V, 4A at 12V
Power 48W

RDR8S and I32O16 Hardware Installation Description of Signals
24-10489-19 Rev. B
8
The following figures show the details of the terminal blocks.
Figure 2: RDR8S Door Interface and I32O16 Terminal Interface
REX Input
Red LED Output
Green LED Output
Device Interface
Door Sensor Input
D1
D0
COM
12VDC
GREEN
COM
RED
REX
COM
DS
DOOR 1 PWR/COMMLEDS
READER
Shunt Output
Tamper Input
Strike Output
NC
COM
NO
NC
COM
NO
STRIKE SHUNT
READER
SPARE
COM
TAMP
INPUTS
Spare Input
RDR8S DOOR INTERFACE:
ONE OF 8 READERS
IN2 Input
OUT1 Open Collector Output
OUT2 Open Collector Output
IN1 Input
COM
12VDC
OUT2
COM
OUT1
IN2
COM
IN1
PWR
TERMINAL
OUT3 Relay Output
IN3 Input
OUT5 Relay Output
NC
COM
NO
NC
COM
NO
OUT5 OUT3
TERMINAL
IN4
COM
IN3
IN4 Input
I32O16 TERMINAL INTERFACE:
ONE OF 8 TERMINALS

RDR8S and I32O16 Hardware Installation Description of Signals
24-10489-19 Rev. B
9
Figure 3: RDR8S and I32O16 Interface: Calibration Resistor
Figure 4: RDR8S and I32O16 Interface: Power Supply
RDR8S Input/Output Points
Device Interface Lines DATA0/RS485- and DATA1/RS485-
Description of Signals – With Wiegand readers, DATA0 and DATA1
are inputs from each reader, complying with the Wiegand interface
specification. In Wiegand configuration, these signals are pulled up to
5VDC by internal 3.92 K Ohm resistors.
In RS485 configuration, RS485- and RS485+ are bidirectional
communication lines. The signal lines are terminated to form one end
of a RS485 bus. The lines are NOT pulled up to 5VDC by internal
resistors.
Reference – These signals are referenced to logic ground (COM).
Protection – Each signal has a 6 V transient voltage suppressor
between it and COM.
CAUTION: These open collector outputs can be damaged with the use of
alternating current (AC) potentials as low as 1VAC. The LED outputs can
only be connected to direct current (DC) loads up to 12VDC.
Calibration Resistor
CAL.
POWER
PWR
RTN
+12VDC
+24VDC
To the power supply

RDR8S and I32O16 Hardware Installation Description of Signals
24-10489-19 Rev. B
10
Input Points
Description of Signals – The following are internally pulled up inputs:
– Reader 1: Door Sensor, REX, Tamper, Spare
– Reader 2: Door Sensor, REX, Tamper, Spare
– Reader 3: Door Sensor, REX, Tamper, Spare
– Reader 4: Door Sensor, REX, Tamper, Spare
– Reader 5: Door Sensor, REX, Tamper, Spare
– Reader 6: Door Sensor, REX, Tamper, Spare
– Reader 7: Door Sensor, REX, Tamper, Spare
– Reader 8: Door Sensor, REX, Tamper, Spare
– Panel Power Fail
– Panel Tamper
Reference – These signals are referenced to their associated COM input.
Protection – Each signal is protected with series resistors and dual
clamping diodes.
External Circuits – Two external resistors and switch circuit connected
between an input point and COM is required for 4-state operation. An
external switch connected between an input point and COM is required
for 2-state operation. For wiring details see “Wiring Input Devices” on
page 19.
Open Collector Output Points
Description of Signals – The following are open collector outputs:
– Reader 1: Red LED, Green LED
– Reader 2: Red LED, Green LED
– Reader 3: Red LED, Green LED
– Reader 4: Red LED, Green LED
– Reader 5: Red LED, Green LED
– Reader 6: Red LED, Green LED
– Reader 7: Red LED, Green LED
– Reader 8: Red LED, Green LED
The allowable voltage range for these signals is 0-12VDC, limited to
100mA. The connectors are shown in Figure 2.

RDR8S and I32O16 Hardware Installation Description of Signals
24-10489-19 Rev. B
11
Reference – These signals are referenced to logic ground (COM).
Protection – Each signal has a 30V transient voltage suppressor between it
and system ground.
Relay Output Points
Description of Signals – NC, NO, and COM are the three connections to a
single pole, double throw relay.
The following are the relay outputs:
– Reader 1: Strike, Shunt
– Reader 2: Strike, Shunt
– Reader 3: Strike, Shunt
– Reader 4: Strike, Shunt
– Reader 5: Strike, Shunt
– Reader 6: Strike, Shunt
– Reader 7: Strike, Shunt
– Reader 8: Strike, Shunt
Reference – The relay is a dry contact relay rated at 1A at 24VDC, 25VA
maximum.
RDR8S Reader Power
Description of Signals – 250mA at 12VDC is provided for each reader.
Protection – There is a 750mA PTC (Positive Temperature Coefficient)
re-settable fuse.
I32O16 Input/Output Points
Input Points
Description of Signals – The following are internally pulled up inputs:
– Terminal 1: IN1, IN2, IN3, IN4
– Terminal 2: IN1, IN2, IN3, IN4
– Terminal 3: IN1, IN2, IN3, IN4
– Terminal 4: IN1, IN2, IN3, IN4
– Terminal 5: IN1, IN2, IN3, IN4
– Terminal 6: IN1, IN2, IN3, IN4

RDR8S and I32O16 Hardware Installation Description of Signals
24-10489-19 Rev. B
12
– Terminal 7: IN1, IN2, IN3, IN4
– Terminal 8: IN1, IN2, IN3, IN4
– Panel Power Fail
– Panel Tamper
The allowable voltage range for these signals is 0-12VDC.
Reference – These signals are referenced to their associated COM input.
Protection – Each signal is protected with series resistors and dual
clamping diodes.
External Circuits – Two external resistors and switch circuit connected
between an input point and COM is required for 4-state operation. An
external switch connected between an input point and COM is required
for 2-state operation. For wiring details see “Wiring Input Devices” on
page 19.
Open Collector Output Points
Description of Signals – The following are open collector outputs:
– Terminal 1: OUT1, OUT2
– Terminal 2: OUT1, OUT2
– Terminal 3: OUT1, OUT2
– Terminal 4: OUT1, OUT2
– Terminal 5: OUT1, OUT2
– Terminal 6: OUT1, OUT2
– Terminal 7: OUT1, OUT2
– Terminal 8: OUT1, OUT2
The allowable voltage range for these signals is 0-12VDC, limited to
100mA. The connectors are shown in Figure 2.
CAUTION: These open collector outputs can be damaged with the use of
alternating current (AC) potentials as low as 1VAC. The LED outputs can
only be connected to direct current (DC) loads up to 12VDC.
Reference – These signals are referenced to logic ground (COM).
Protection – Each signal has a 30V transient voltage suppressor between
it and system ground.

RDR8S and I32O16 Hardware Installation Description of Signals
24-10489-19 Rev. B
13
Relay Output Points
Description of Signals – NC, NO, and COM are the three connections to a
single pole, double throw relay.
The following are the relay outputs:
– Terminal 1: OUT5, OUT3
– Terminal 2: OUT5, OUT3
– Terminal 3: OUT5, OUT3
– Terminal 4: OUT5, OUT3
– Terminal 5: OUT5, OUT3
– Terminal 6: OUT5, OUT3
– Terminal 7: OUT5, OUT3
– Terminal 8: OUT5, OUT3
Reference – The relay is a dry contact relay rated at 1A at 24VDC, 25VA
maximum.

RDR8S and I32O16 Hardware Installation Description of Signals
24-10489-19 Rev. B
14
Cable Requirements
Description Recommended Cable Type Maximum Segment
Length
RDR8S or I32O16 to
Power Supply1
Listed, 18 AWG, hook-up wire Wire should fit within the
enclosure.
RDR8S or I32O16 to
Controller
Listed, 18 AWG, 1 twisted pair 4000 feet (1219 m)
maximum. All RDR8S and
I32O16 modules
connected to a single
controller must be within
4000 feet of the controller.
RDR8S or I32O16 to
RDR2S-A
Listed, 18 AWG, 1 twisted pair 4000 feet (1219 m)
maximum
Door Sensor Belden 8442, 1 twisted,
unshielded pair, 22 AWG
500 ft. (152 m)
Door Strike and
Shunt
Belden 9740, 1 twisted,
unshielded pair, 18 AWG
Depends on power
requirements of the door
strike. Voltage to the strike
must not be reduced more
than 10% over the 18 AWG
wire, measured when
energized.
Request to Exit Belden 8442, 1 twisted,
unshielded pair, 22 AWG
500 feet (152 m)
Reader Power2
(I32O16 has +12
supplied)
Belden 9740, 1 twisted,
unshielded pair, 18 AWG
Refer to reader
manufacturer’s
specification for power
requirements.
Reader Data0/Data12
(RDR8S only)
Belden 9744, 2 twisted,
unshielded pair, 22 AWG
500 ft. (152 m). Refer to
reader manufacturer’s
specification for data
requirements.
Reader RS485 -/+2
(RDR8S only)
Listed, 18 AWG, 1 twisted pair 4000 feet (1219 m)
maximum. Refer to
manufacturer’s
specification for
requirements.

RDR8S and I32O16 Hardware Installation Description of Signals
24-10489-19 Rev. B
15
Cable Routing
The cables should run in grounded conduit or at least two feet from AC
power, fluorescent lights, or other high energy sources.
CAUTION: All data cables should be physically separated from power
lines. If conduit is used, do not run data cables in the same conduit as
power cables or certain door strike cables, e.g. strike voltage greater that
42V or Magnetic door locks without EMI suppression.
All cables must conform with the following regulations:
– National Electrical Code
–NFPA 70
– Local electrical codes
– Canadian Electric Code C22.1 (installations in Canada)
– BSI Standard BS7671, latest edition (installations in Great Britain)
Cabling should be made using good wiring practices and should be long
enough to allow service loops at their terminations in the enclosure.
General Purpose
Input
Belden 8442, 1 twisted,
unshielded pair, 22 AWG to
each detector
500 feet (152 m)
General Purpose
Output
Belden 9740, 1 twisted,
unshielded pair, 18 AWG to
each relay
Depends on load.
1 When wiring more than one RDR8S or I32O16, use the same type of hook-up wire and communications
wire to connect subsequent modules.
2 Refer to reader manufacturer’s recommendations when using UL-listed readers. In the absence of other
recommendations, consider these cable specifications taking into account the number of conductors that
will actually be needed for installation.
Description Recommended Cable Type Maximum Segment
Length

RDR8S and I32O16 Hardware Installation Description of Signals
24-10489-19 Rev. B
16
Power Supply
For power wiring with the enclosure, use the cable assembly shown in the
following figure. For more information refer to the manual provided with
the enclosure.
Figure 5: Cable Assembly for Power Wiring
CAUTION: Do not connect the power cable to the RDR8S or I32O16 until
all wiring is complete.
When connecting multiple RDR8S or I32O16 modules, wire the modules
in parallel following the “daisy chain” pattern as shown in the following
figures.
Figure 6: “Daisy Chain” Wiring Pattern
Connector (3-pole, gray) for
RDR8S or I32O16 module COM
(PWR return)
+24VDC
connector
black
red
Note: Chassis ground is not used.
To the next
RDR8S or
I32O16
module
1st RDR8S
or I32O16
2nd RDR8S
or I32O16
3rd RDR8S
or I32O16
RS-485 cable
connecting to
S300 bus
Other manuals for S300 Series
6
This manual suits for next models
2
Table of contents
Other Johnson Controls Network Hardware manuals
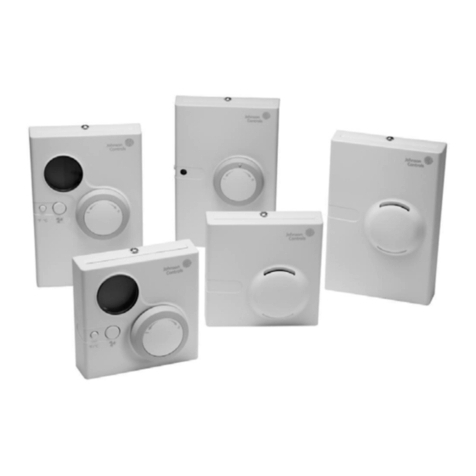
Johnson Controls
Johnson Controls Facility Explorer Service manual
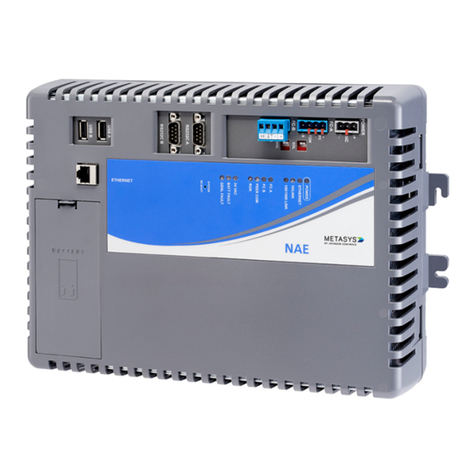
Johnson Controls
Johnson Controls NAE55 Series User manual
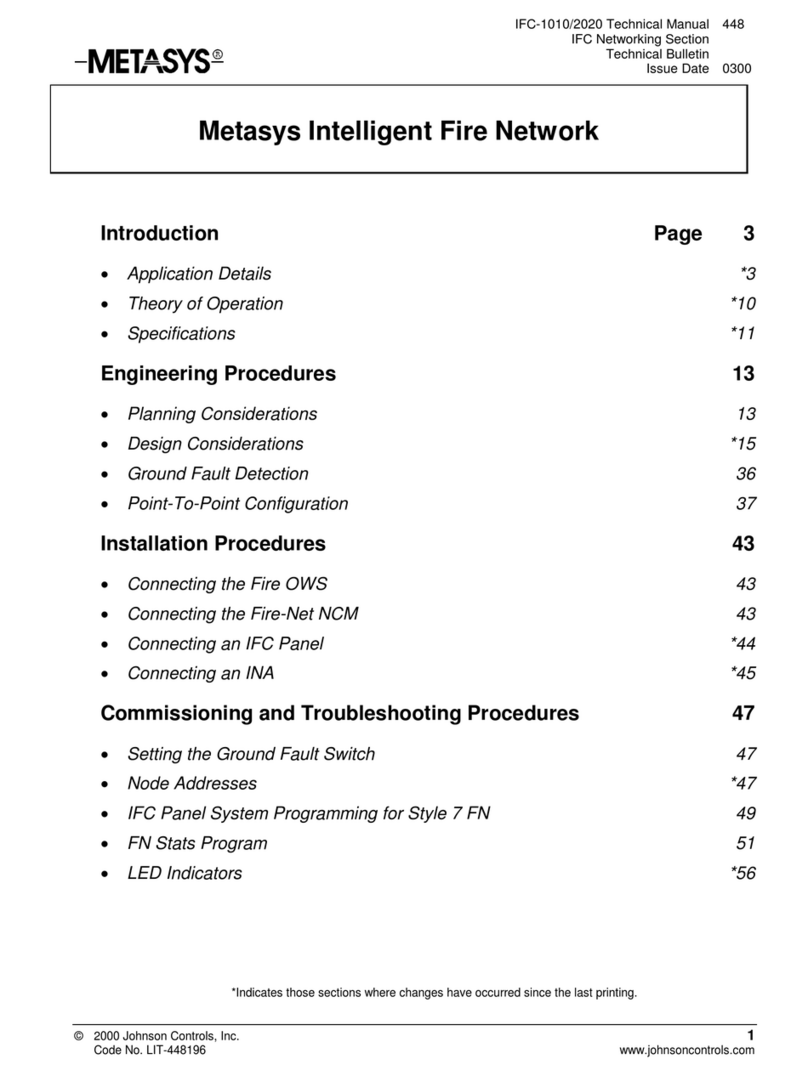
Johnson Controls
Johnson Controls Metasys Intelligent Fire Network User manual

Johnson Controls
Johnson Controls Metasys NAE55 User manual
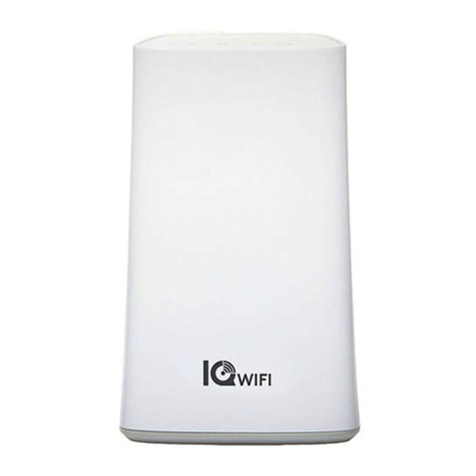
Johnson Controls
Johnson Controls IQ WIFI User manual
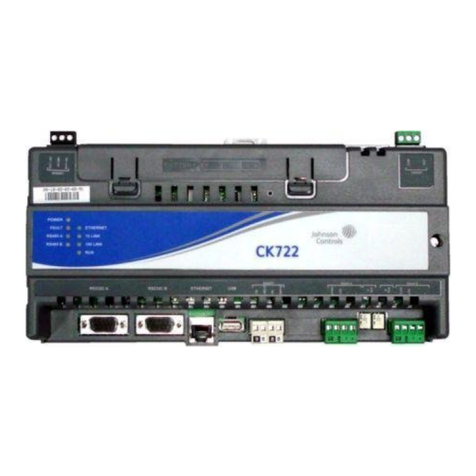
Johnson Controls
Johnson Controls CK722 User manual
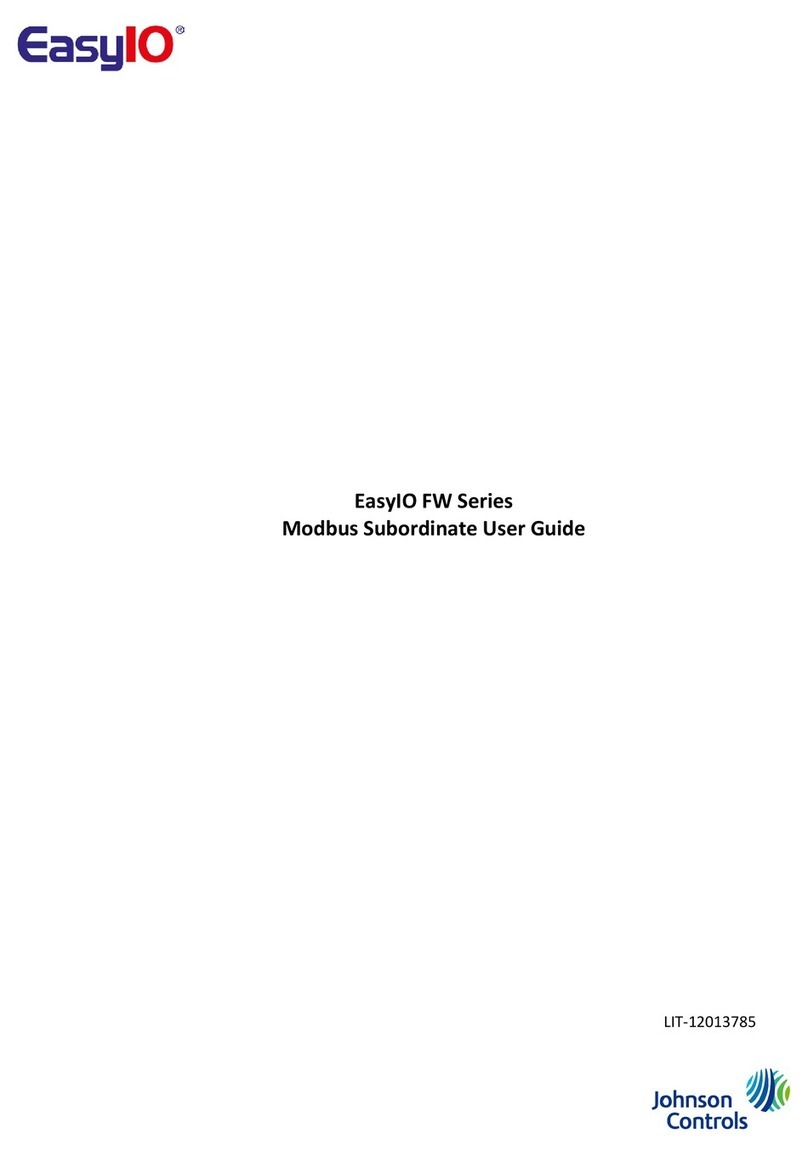
Johnson Controls
Johnson Controls EasyIO FW Series User manual
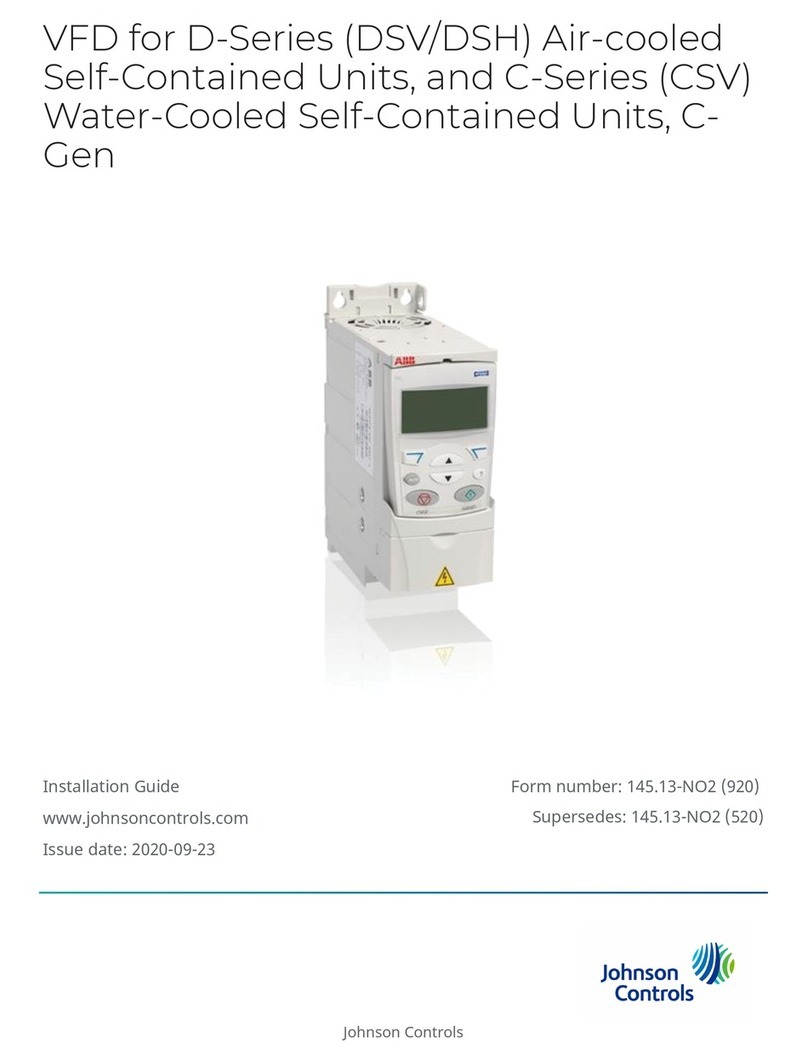
Johnson Controls
Johnson Controls D Series User manual
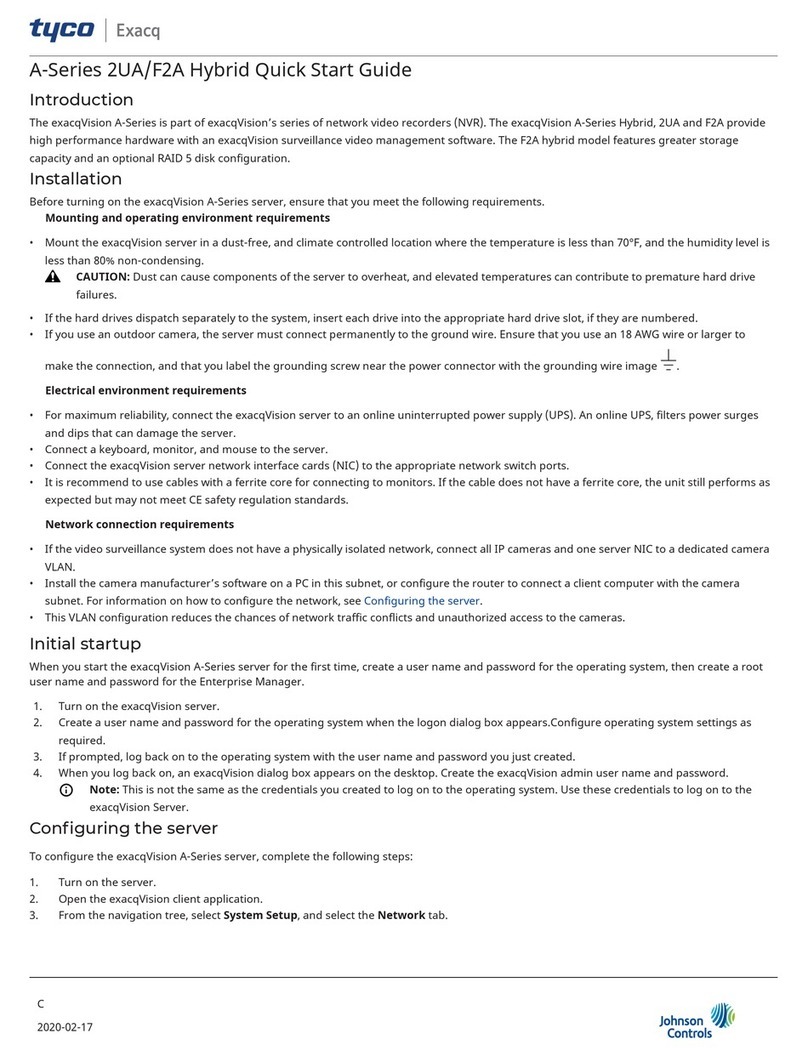
Johnson Controls
Johnson Controls Tyco exacqVision 2UA User manual
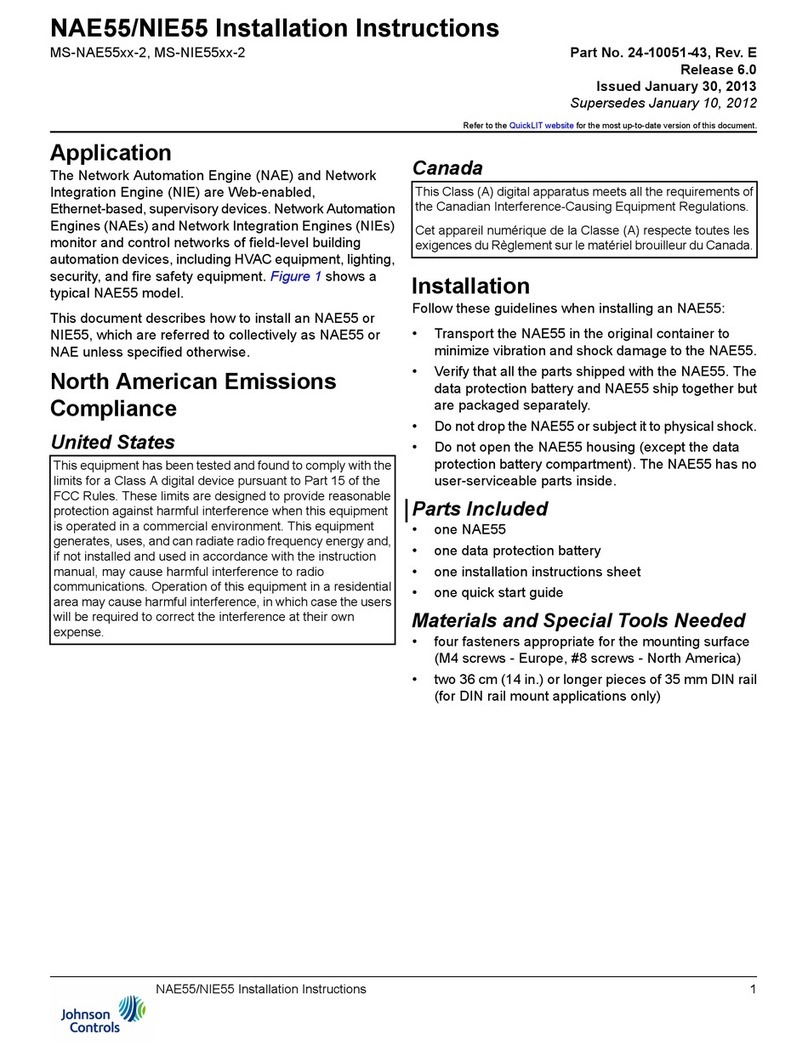
Johnson Controls
Johnson Controls NIE55 Series User manual