KELCO F60 MK3 Assembly instructions

KELCO F60 MK3
DIGITAL PUMP CONTROLLER
INSTALLATION & PROGRAMMING
MANUAL
KELCO Engineering Pty Ltd
Sydney Australia
www.kelco.com.au

2
ELECTRICAL AND MECHANICAL LIMITS OF THIS CONTROLLER
DO NOT EXCEED THESE LIMITS UNDER ANY CIRCUMSTANCES
Ambient temperature T50 (0°C ~50°C)
Ingress Protection IP64
Feature of automatic action Type 1.B
Number of automatic cycles (A) for
each automatic action
5,000 cycles
Type of terminal Screw terminal block, type Y attachment
Load Termination Function
Input Input 1 HD /A /N AC 220-240V, 50Hz/60Hz
Input 2 A /N AC 220-240V, 50Hz/60Hz
Input 3 LV/N AC18-24V, 50Hz/60Hz; DC18-24V
Input 4 RMT1 /RMT2 Remote inputs sourced from LV terminal
Output Relay 1 (SPDT
pump control relay)
R1NO/R1COM/
R1NC VDE
40015012
NO contacts, AC240V, 50Hz, 10A
NC contacts AC240V,50Hz 3.5A
Duty factor, 5s ON, 5s OFF
Ralay 2 (SPST
alarm relay)
R1NO/R2COM
VDE 40015012
AC240V, 50Hz/60Hz; 3.5A
Duty factor, 5s ON, 5s OFF
Motor load Single phase motors (Single phase pump motors up to 2.4kW
maximum)
Three phase motor Via a suitable interposing contactor
IMPORTANT: Input 1 or 2 shall not be connected while the input 3 or
4 are connected
TEMPERATURE LIMITS
This F60 MK3 Pump Controller is designed to operate in an ambient
temperature range 1°C to 50°C. Process liquid temperature must not
exceed 60°C. Operation of this pump controller outside these temperature
limits may damage the controller and void any warranty on the product.
PRESSURE LIMITS
This F60 MK3 Pump Controller is designed to operate in the pressure
range 0 to 2000kPa, 0 to 20 Bars, 0 to 290 psi. It must never be exposed
to static or dynamic pressures in excess of 20 bars, 290 psi. The F60 MK3
must never be exposed to negative pressure. Never install the F60 MK3
on the suction pipe work of a pump. Operation outside the stated pressure
limits may damage this product and void any warranty,

3
IMPORTANT: READ THIS FIRST
DO NOT EXPOSE THE F60 MK3 TO VIBRATION. INSTALL ONLY IN
PIPEWORK THAT DOES NOT VIBRATE. Vibration will damage the
electronics within the F60 MK3 and will void your product warranty.
This F60 MK3 pump controller has been fully tested and calibrated. It is set
to mode 1 and it has its start-up and run-on timers both set to 5 seconds. All
other functions are turned o. On start up the F60 MK3 will run the pump
using its start-up timer. If it nds ow in the pipe system it will continue
to run the pump. If ow stops the pump will continue to run for 5 seconds,
held on by the F60 MK3’s run-on timer. If ow fails to return, the pump
will be shut down after the run-on period. Pressing and releasing the (R)
button on the F60 MK3 will repeat this basic process.
THE BUTTONS
The F60 MK3 is controlled and congured using 4 onboard buttons.
(R) Reset button. Stops the pump(s) and restarts the F60 MK3 when
released.
(˄) Up arrow button. For increasing program settings.
(˅) Down arrow button. For decreasing program settings.
(P) Programming button. For stepping through the menu and entering
settings into memory.
THE LIGHTS
The F60 MK3 includes 4 multicolour lights to indicate activity.
Flow: This light is GREEN when the F60 MK3 detects ow and RED when
no ow is detected.
Pump: This light is GREEN when a pump is running and RED when the
pump is stopped.
Timer: This light may be GREEN or RED when a timer or special function
is running.
Remote: This light is BLUE when remote input No. 1 is closed and o
when the remote is open. The light is RED when remote input No. 2 is
closed and o when the remote is open. This light is PURPLE when both
remote inputs 1 & 2 are closed.

4
LCD SCREEN BACKLIGHT
The LCD backlight can be turned on or o.
To turn the light o press and hold down the (˅) button. Press and release
the (R) button. Release the (˅) button. Repeat to turn the light on. The
light remembers the state it was last left in if power is turned o. The light
can be left permanently on or o as required.
TEMPERATURE
The F60 MK3 monitors its internal temperature when running. Pressing the
(˅) button while the controller is powered up displays the current internal
temperature of the F60 MK3.
PRESS (and release) THE (P) BUTTON
When the F60 MK3 is powered up, pressing the (P) button, holding it down
for 1 second and releasing it takes you to the top of the menu. Pressing
and releasing the (P) button loads whatever the screen is displaying into
the F60 MK3’s memory. The memory is non-volatile and settings are
retained when power is o. You can exit the menu at any time by pressing
and releasing the (R) button. Any settings you have made up to that point
will be retained. There is no need to step all the way through the menu
when making a change to a setting.
INSTALLING THE F60 MK3
1) Do not install the F60 MK3 in a fully exposed outdoor location. The
F60 MK3 is weatherproof, however, to ensure a long reliable life from
it we recommend it be protected from direct exposure to the sun and
rain. A skull cap is provided with the F60 MK3 and we recommend it
be used to protect the F60 MK3 when direct observation of the LCD
screen is not required.
2) Do not expose the F60 MK3 to freezing. If the pipework in which
the F60 MK3 is installed freezes, the pressure sensor in the controller
may fail. If the F60 MK3 is to be used in areas where low temperatures
will be encountered, always lag the pipework for several metres either
side of the F60 MK3. Also lag the base of the F60 MK3 to prevent the
unit and any adjacent pipework from freezing.
3) Do not use this controller in hot water applications. The F60 MK3
is not designed to be used in water hotter than 60ºC.

5
4) Never expose the F60 MK3 to static or dynamic pressures greater
than 20 Bars, 290 psi.
5) Do not install the F60 MK3 in a section of pipe that is subject to
vibration. Vibration will cause premature failure of the electronic
components within the F60 MK3.
6) Never install the F60 MK3 in the suction pipe of the pump or in any
location where it may be subject to partial vacuum conditions.

6
LOCATION
The F60 MK3 should be installed in a straight section of pipe preferably with
5 diameters of straight pipe either side of the paddle. The F60 MK3 can
be installed in a suitable pipe socket, tapping saddle or pipe tee. The F60
MK3 should be installed in the discharge pipework of the pumping system,
either before or after the system’s air cell. If the system does include an
air cell a decision must be made as to which side of the air cell to locate
the F60 MK3. The fundamental way the system operates will depend on
this decision. The F60 MK3 should not be installed in the suction pipe
of a pump as it requires positive pressure to operate properly. The F60
MK3 can be installed in either horizontal or vertical pipe. If it is installed in
vertical pipe the ow should preferably be in an upward direction. Do not
install the F60 MK3 on the underside of horizontal pipework.
WARNING: Never install the F60 MK3 in the suction pipe of the
pump or in any location where it may be subject to partial vacuum
conditions.

7
BEFORE THE AIR CELL
If the F60 MK3 is installed before the air cell in the system it will only start
the pump on pressure since the initial ow will be supplied from the air cell.
The only change in state the controller will see will be the falling pressure.
Choose this arrangement if you want to keep pump starts to a minimum
and you are prepared to accept the delay in starting associated with the
slow pressure fall from the air cell.

8
AFTER THE AIR CELL
If you install the F60 MK3 in the pipework after the air cell it will start the
pump each time ow pushes its paddle forward or each time pressure falls
to whatever pressure you have set the controller to start at. Choose this
arrangement if you want the system to deliver a steady pressure and to
start each time ow is sensed.

9
INSTALLATION
The F60 MK3 pump controller is supplied as two separate assemblies, the
paddle assembly and the electrical housing. The paddle assembly should
be installed in the pipework rst.

10
VERY IMPORTANT SAFETY NOTE :
A pressure relief valve should be tted to any system that can exceed the
pressure rating of any component on that system. Alternately, always
conrm that the pressure safety limits of individual items are compatible
and not compromised without the tting of appropriate safety devices, i.e.
a Pressure Relief Valve (PRV). A PRV should be tted to every system to
ensure the system can not run against a shuto head. A correctly set PRV
will ensure the system can’t overheat the pump in the event of this F60
MK3 or any other part of the system locking the pump on.

11
TRIMMING THE PADDLE
The paddle of the F60 MK3 can be cut down to suit the specic pipe size
and intended application. Cut the paddle using a hacksaw or tin snips so
it clears the sides of the pipe socket and protrudes approximately half to
two thirds of the way across the pipe when the controller is screwed into
the pipework. If the ow rate will only ever be fairly low, the paddle should
be cut longer, perhaps until it only clears the bottom of the pipe by 3 to
5mm. If you are unsure as to what length the paddle should be, a paddle
trimming calculator is available at.
https://www.kelco.com.au/paddle-trimming-calculator/
If you know what the expected ow rate is the calculator allows you to enter
your pipe diameter and paddle dimensions. It will then determine if the
selected paddle dimensions are adequate for the application. Spare
paddles to suit the F60 MK3 are available from Kelco or from your distributor.
To t the paddle assembly into the pipework, apply Teon tape or thread
sealing compound to the thread and use a suitable spanner and the
spanner ats provided on the paddle assembly (directly above the process
connection thread). Under no circumstances should the electrical housing
be twisted or used to screw the paddle assembly into the pipework, or to
align the controller with the axis of the pipework. To do so will irreparably
damage the controller and void its warranty. When correctly installed there
should be a minimum 4mm gap between the top of the pipe socket and the
top of the thread on the F60 MK3. Never apply water pressure to the F60
MK3 unless the electrical head is tted and the M4 locking screw is in place
and fully tightened. The F60 MK3 can be installed in either vertical or
horizontal pipe. When installed in vertical pipework ow should preferably
be in an upward direction past the controller’s paddle. The F60 MK3 has
a 1” BSP process connection. A matching female threaded socket, pipe
saddle or pipe tee must be provided to t the controller into pipework.
ATTACHING THE ELECTRICAL HOUSING
Once the paddle assembly has been installed, t the electrical housing
onto the spigot on top of the paddle assembly. Take care that the sealing
O-ring is on the top stem of the paddle assembly is in location and in good
order.

12
There is a at keying face on the cylindrical body of the paddle assembly
that keys the electrical housing onto the paddle assembly and aligns it
correctly. It is critical that the keying at is on the downstream side and at
90 degrees to the axis of the pipework. To secure the electrical housing
onto the paddle assembly, an Allen head cap screw is supplied. The
controller must be square to the axis of the pipework with the direction of
ow arrow pointing in the direction of ow.
With the electrical housing located on the spigot and in position, press
down with the at of your hand on the top face of the electrical enclosure.
While pressing down, screw the 4mm Allen screw fully through the housing
using the 3mm Allen Key (supplied). Tighten the screw and then release
your hand from the top of the housing.
DETACHING THE ELECTRICAL HOUSING
WARNING: Always switch o the power and fully de-pressurise the
pipe system before attempting to remove the electrical housing.
To allow easy access to the controller’s paddle, the electrical housing of
the F60 MK3 can be detached from the paddle assembly. Removing the
electrical housing allows access to the paddle without the need to disconnect
wiring. To remove the electrical assembly undo and completely remove
the M4 Allen head locking screw. Once the locking screw is removed, lift
the electrical housing straight o, do not twist it when doing this. Once the
electrical housing has been removed, the paddle assembly can be
unscrewed from the pipework using the spanner ats on the body of the
paddle housing. Simply reverse this procedure to ret the electrical housing
to the controller, taking care to ensure the O-ring on the top of the paddle
assembly is in place and is clean and in good condition.
SENSITIVITY ADJUSTMENT
Under the end of the electrical housing on the F60 MK3 is a red hexagonal
dust cap. If you remove this dust cap you gain access to an adjustment
screw that allows the paddle preload to be reduced. As supplied the
sensitivity adjustment screw is wound fully in. In this position, the paddle
is at its least sensitive. In this position, it takes a substantial force from the
moving water to move the paddle.

13
If you wind the sensitivity adjustment screw anti-clockwise (outward) the
force against the paddle that resists ow will be reduced. The paddle will
become increasingly more sensitive and will respond to progressively
lower ows the further out you wind the adjusting screw. The total
adjustment range is 10 turns of the screw. If you wind the adjustment
screw out beyond 10 turns there will not be enough residual force to return
the paddle to the o position when ow stops.
The range of sensitivity adjustment will also be aected by the orientation
of the controller. In horizontal pipework with the F60 MK3 mounted vertically
the useable range of adjustment is approximately 8 turns. In vertical
pipework with the F60 MK3 installed horizontally the full 10 turn range can
be utilised.
DUAL PUMP CONTROL Mode 5
The F60 MK3 is capable of controlling 2 pumps simultaneously. The pumps
can be of any required size and can be congured as a duty and standby
set or as a dual alternating set. The starting and stopping pressures for
both pumps can be set independently of each other in any required
conguration within the overall pressure limits of the F60 MK3. The F60
MK3 detects ow at one location in the pipework. This will normally dictate
the location of the F60 MK3 in the overall system. For example, when
used alone the F60 MK3 would normally be mounted in the systems
common discharge manifold. When set up this way the F60 MK3 will not
oer loss of ow protection to the individual pumps, only to the overall
system. A far better arrangement is to monitor ow from each pump
independently. To give each pump individual loss of ow protection the
F60 MK3 should be installed in the discharge pipe of one pump and a basic
ow switch installed in the discharge pipe of the second pump.
Dual ow sensing can then be implemented by connecting the remote
mounted ow switch into the remote input terminal No1 of the F60 MK3.
When congured this way, The F60 MK3 can monitor ow at the two
locations simultaneously. Loss of ow from either or both pumps will shut
the pumps down if ow is lost.

14
TYPICAL DUAL PUMP SET
A typical dual pump set is depicted in the accompanying sketch. The F60
MK3 and the F Series paddle ow switch are installed in the discharge
pipes from the pumps prior to their entry into the common discharge
manifold.
The remote ow switch can be a paddle switch, as illustrated, or an in line
ow switch. It must have normally open voltage free contacts.
Kelco F Series
Flow Switch

15
All electrical work associated with the F60 MK3 must
be carried out by qualied electrical personnel and all
electrical work must conform to AS/NZ standards and
to local wiring rules.
WARNING
ELECTRICAL INSTALLATION
A means for disconnection of the F60 MK3 must be incorporated in the
xed wiring in accordance with the wiring rules. External preliminary
protection is required under all circumstances. We suggest a maximum
C10 Amp breaker be used for the supply isolation.
INTRODUCTION
When used with its HD terminal link in place, the F60 MK3 can directly
control single-phase pump motors up to 2.4kW via Relay 1 normally open
contacts. No interposing contactor is required for such applications. The
F60 MK3 can also be used to control 3 phase pump motors of any size via
an appropriate interposing contactor.
WARNING: The contactor control circuit must never exceed 240VAC.
Never connect the F60 MK3 and contactor coil directly across 2
phases of a 3 phase supply.
The F60 MK3 requires a stable 220V to 240V AC 50Hz supply when
operated from the mains. It can also be operated from an 18 to 24V AC or
DC supply by utilising the low voltage active terminal LV and neutral
terminal N (see the included wiring diagrams). When operated from a low
voltage DC supply the terminals LV and neutral N are not polarity sensitive.
Pay attention to cable sizes and ensure cables are adequate for the specic
pump motor load. This is particularly important where long cable runs are
to be used in the installation. If the voltage drop associated with the starting
of the pump motor is excessive the F60 MK3 may repeatedly reset and not
operate properly.

16
THE HD (Heavy Duty) TERMINAL
The F60 MK3 pump controller contains a solid-state switch (HD Heavy
Duty drive) that can be used to protect the normally open contacts of Relay
1 by eliminating the destructive arcing caused by the starting and stopping
of motors. The solid-state switch is accessible from the HD terminal on the
terminal block. We recommend the HD terminal be used whenever the
controller is used to directly control a single phase motor. The HD terminal
should not be used when the F60 MK3 is connected to a contactor, external
timer, low wattage relay or to any other external device where voltage free
contacts are required. It is strictly intended for the direct control of highly
inductive AC motor loads. The HD terminal and the controller’s built in
relays must never be directly connected to a DC motor under any
circumstances.
When the HD terminal is linked to the normally open terminal of Relay 1,
the HD drive parallels a 42 Amp solid state switch across the relay’s
Normally Open contacts. This increases the momentary current carrying
capacity of the relay’s contacts to over 60 Amps. The solid-state HD drive
is only activated for a brief period when the motor starts and stops. It
eectively handles the high inrush current associated with the motor
starting, and it provides a current path for the destructive back EMF
associated with the motor stopping.
To use the HD drive, place a heavy link wire between the HD terminal
and the Normally Open terminal of Relay 1.
WARNING
The HD terminal must be left unused or only ever linked to Relay 1
Normally Open. It must never be used for any other purpose and it
must never be connected to any external device. Under no circumstances
connect the HD terminal to the terminals of Relay 2. The HD terminal
must be regarded as live at all times and at full mains potential.

17
BROWNOUT OR BLACKOUT
If a blackout or brownout occurs the F60 MK3 will not retain any memory
of where in its run or stop cycle it may have been, it will simply shut down
the pump. When power resumes, the F60 MK3 will attempt to reboot,
restart and run any timer settings from the beginning. A manual reboot
may be required if the supply is unstable on startup and and can be done
at any time by pressing and releasing the F60 MK3’s reset button.
CABLES
The F60 MK3 has 3 X M20 cable glands. As supplied, the cable glands
are blanked o with rubber plugs. To use the glands rst remove one
of the rubber plugs and assemble the (supplied) cable gland bush and
backing washer into the cable port. The cable glands can accept cable
from 7 to 9mm diameter. See sketch below for assembling the cable gland
components.
The F60 MK3 is supplied with a set of steel crimp rings. The crimp rings
are to provide strain relief for the controller’s cables. To use the crimps,
place one on the cable approximately 3 to 4mm below the end of the cables
outer sheathing. Crimp the two ears of the ring at using bull nosed pliers.
Pull the cable back through the cable gland until the crimp ring’s ears are
fully located into the slots in the cable gland housing. Always leave unused
cable glands sealed o using the (supplied) rubber plugs.
Rubber Plug
Backing Washer
M20 Gland Nut
Plug unused cable glands
using the rubber plugs
(supplied). Fully tighten
the gland nut to seal the
unused cable port.
Crimp the ears of the
strain relief ring onto the
cable and pull the cable
back into the slots in the
gland housing.
Cable 7mm to 9mm diameter
Controller Housing
Rubber Grommet Backing Washer
4mm

18
SUPPLY VOLTAGE LIMITS
VOLTAGE LIMITS ON TERMINALS LV & N
Maximum Supply Voltage 25VAC 50Hz or 25VDC
Minimum Supply Voltage 18VAC 50Hz or 18VDC
VOLTAGE LIMITS ON TERMINALS A & N
Maximum Supply Voltage 260VAC 50Hz
Minimum Supply Voltage 110VAC 50Hz
RELAYS
The F60 MK3 houses 2 relays. Relay 1 has S.P.D.T contacts. Relay 2 has
S.P.S.T Normally Open contacts. Relay 1 is normally regarded as the
pump control relay and relay 2 is normally regarded as the alarm relay.
When operating the F60 MK3 as a dual pump controller, relay 2 can be
used to control the second pump via a suitable interposing contactor.
With the HD terminal linked to the Normally Open terminal of Relay 1,
the F60 MK3 can directly control a single phase motor up to 2.4kW.
Without the HD link in place the relay 1 Normally Open contacts can
be used to control a pump motor via a suitable contactor. Both relays
can control motors of any required size via interposing contactors.
CONTACT RATINGS FOR RELAYS 1 & 2
Relay 1 normally open contacts
10A at 240VAC
Resistive Load PF > 0.9
Relay 1 normally closed contacts
3.5A at 240VAC
Resistive Load PF > 0.9
Relay 2 normally open contacts
3.5A at 240VAC
Resistive Load PF > 0.9
50mA at 5VDC Minimum Load both relays
IMPORTANT: When directly controlling a pump motor through relay 1,
always link the HD terminal to relay 1 Normally Open terminal and make
sure the maximum steady state motor current never exceeds 10 Amps. On
a pump motor P1 must not exceed 2.4kW.

19
POWERING THE F60 MK3
IMPORTANT
A means for disconnection of the F60 MK3 must be incorporated in the
xed wiring in accordance with the wiring rules. External preliminary
protection is required under all circumstances. We suggest a maximum
C10 Amp breaker be used for the supply isolation.
The power required to drive the F60 MK3 depends on the supply, AC or DC
and on temperature. The table below gives the maximum power required
from various supplies at 25°C. The measurements expressed represent
the maximum power required with the LCD backlight and all indicator lights
on.
POWER REQUIRED TO DRIVE THE STANDARD F60 MK3
24VDC Supply to LV & N Maximum 68mA 1.63Watts
24VAC 50Hz Supply to the LV & N
Terminals
Maximum 108mA 2.34Watts
220VAC 50Hz Supply to A & N Maximum 87mA 2.00Watts
240VAC 50Hz Supply to A & N Maximum 94mA 2.54Watts
POWER REQUIRED TO DRIVE THE 12VDC F60 MK3-12
With Both Relays Closed Maximum 68mA 0.81Watts
With One Relay Closed Maximum 52mA 0.62Watts
Quiescent State (relays open) Maximum 25mA 0.30Watts

20
REMOTE INPUTS
WARNING: The low voltage source available at the LV terminal is
non-isolated and must be regarded as operating at full mains potential
whenever the F60 MK3 is powered from the mains. Relative to earth
the LV terminal is at full mains potential. All remote wiring and remote
devices connected to the LV terminal must be mains voltage rated.
The F60 MK3 has two remote inputs marked RMT1 and RMT2. Remote
input 1 can be congured to operate in various ways in the program such
as start and stop for connection to tank level switches or for connection to
a remote ow switch in dual pump mode. Remote input 2 has a xed
function, it replicates the main reset button on the F60 MK3. A normally
open remote reset switch can be used to reboot the F60 MK3 by connecting
it to RMT2.
An external switch with voltage free contacts such as a tank level switch or
a set of external relay contacts can be used to control the F60 MK3. The
supply to the external switch must be taken from the LV terminal on the
F60 MK3 when the controller is powered from the mains or from a 24VAC
source. The F60 MK3 must always be powered from the same source as
the supply to the external switch. The supply to the remote switch on the
F60 MK3-12 (low voltage DC model) must be taken from the supply positive
terminal. In all cases the external switch return wire must be connected to
the correct remote input terminal on the F60 MK3. Relative to neutral, the
supply to the external switch will range from 12 to 24 VDC or from 20 to
35V AC depending on the supply voltage.
WARNING: Never connect an external power source of any kind to
the F60 MK3’s remote input terminals.
The remote switch can be installed some distance from the F60 MK3. The
maximum distance is limited by cable resistance and capacitance. The
total cable resistance must not exceed 5K Ohms with the remote switch
closed. The total capacitance of the cable must not exceed 25nF with the
remote switch open. Wires to the remote switch should be run separately
from power carrying cables. Do not run the remote switch wires in a conduit
that also contains power cables.
This manual suits for next models
1
Table of contents
Other KELCO Controllers manuals
Popular Controllers manuals by other brands
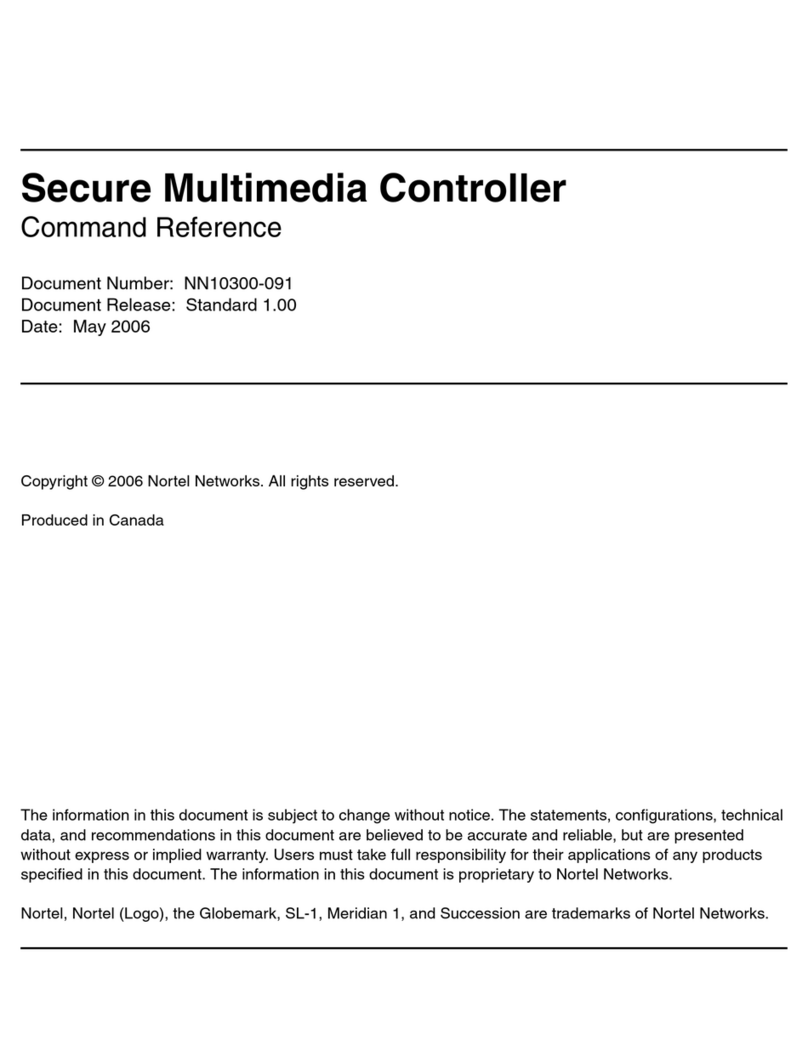
Nortel
Nortel SMC 2450 Command reference guide

YASKAWA
YASKAWA mp2500 user manual

IAI
IAI RCP5 First step guide
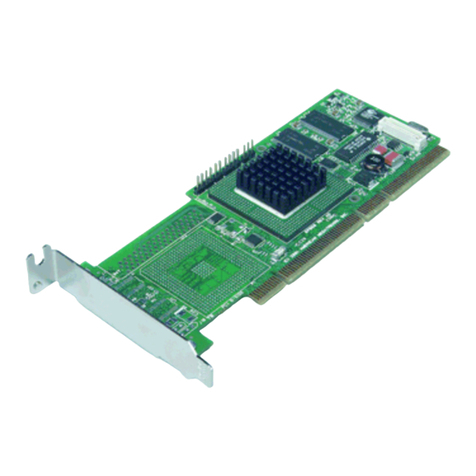
LSI
LSI MegaRAID SCSI 320-0 Zero-Channel RAID Controller Series... Quick Hardware Setup Guide
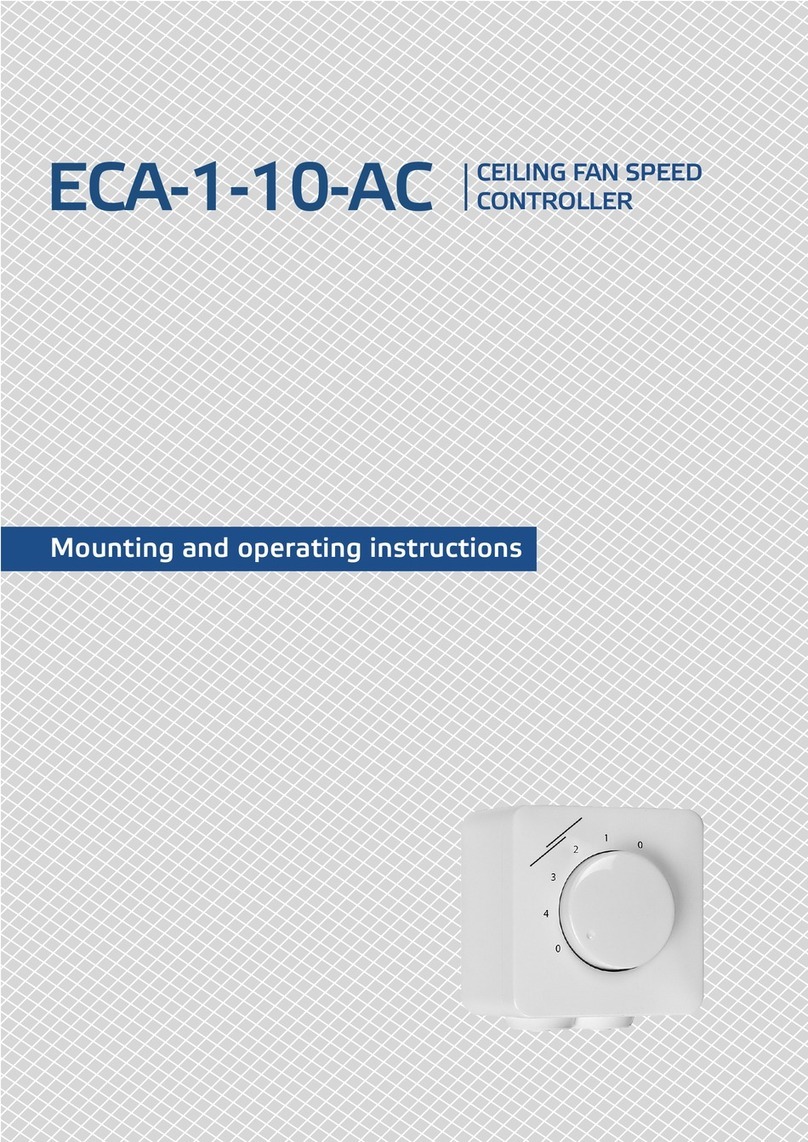
Sentera Controls
Sentera Controls ECA-1-10-AC Mounting and operating instructions
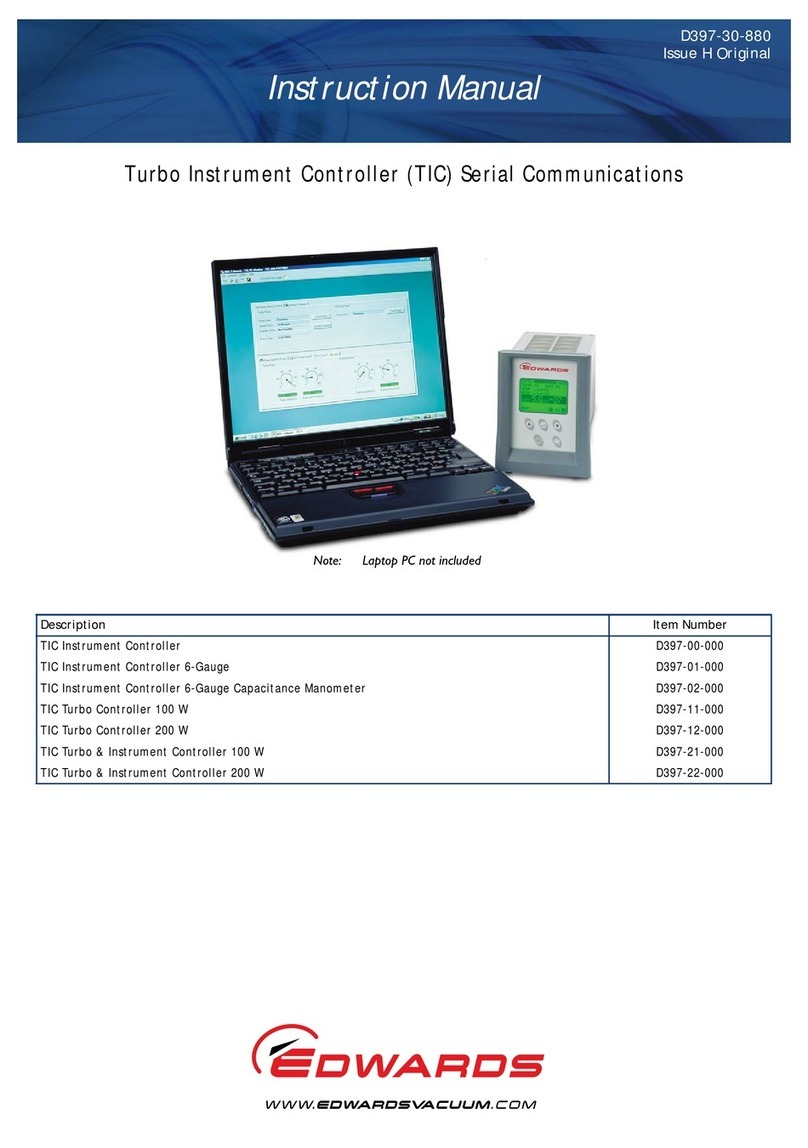
Edwards
Edwards D397-00-000 instruction manual