LMI Technologies Gocator 1100 Series User manual

USER MANUAL Gocator 1100 & 1300 Series
Version 3.6.5.15 Revision: C

2Gocator 1100 & 1300 Series
Copyright © 2014 by LMI Technologies, Inc. All rights reserved.
Proprietary
This document, submitted in condence, contains proprietary information which shall not be
reproduced or transferred to other documents or disclosed to others or used for manufacturing or any
other purpose without prior written permission of LMI Technologies Inc.
No part of this publication may be copied, photocopied, reproduced, transmitted, transcribed, or
reduced to any electronic medium or machine readable form without prior written consent of
LMI Technologies, Inc.
Trademarks and Restrictions
Gocator™ is a registered trademark of LMI Technologies, Inc. Any other company or product names
mentioned herein may be trademarks of their respective owners.
Information contained within this manual is subject to change.
This product is designated for use solely as a component and as such it does not comply with the
standards relating to laser products specied in U.S. FDA CFR Title 21 Part 1040.
Contact Information
For more information, please contact LMI Technologies.
LMI Technologies, Inc.
1673 Cliveden Ave.
Delta, BC V3M 6V5
Canada
Telephone: +1 604 636 1011
Facsimile: +1 604 516 8368
www.lmi3D.com

3Gocator 1100 & 1300 Series
Introduction
The Gocator 1100 and 1300 series of laser displacement sensors are designed for 3D measurement
and control applications. Gocator sensors are congured using a web browser and can be connected to
a variety of input and output devices. This guide describes the installation and use of Gocator sensors.
Notational Conventions
This guide uses the following notational conventions:
!Warning Follow these safety guidelines to avoid potential injury or property damage.
Note Consider this information in order to make best use of the product.

4Gocator 1100 & 1300 Series
Introduction 3
Table of Contents 4
Safety and Maintenance 8
Laser Safety 8
Laser Classes 9
Precautions and Responsibilities 10
Class 3B Responsibilities 10
Systems Sold or Used in the USA 11
Electrical Safety 12
Environment and Lighting 13
Sensor Maintenance 13
Getting Started 15
System Overview 15
Standalone System 15
Dual-Sensor System 16
Multi-Sensor System 17
Hardware Overview 18
Side Mount Package 18
Top Mount Package 19
Master 100 20
Master 400/800 21
Master 1200/2400 22
Gocator Cordsets 23
Calibration Targets 24
Installation 25
Grounding - Gocator 25
Grounding - Master 400/800/1200/2400 25
Mounting (Side Mount Package) 26
Mounting (Top Mount Package) 28
Orientations 30
Network Setup 32
Client Setup 32
Gocator Setup 34
Running a Standalone Sensor System 34
Running a Dual Sensor System 35
Next Steps 40
Theory of Operation 41
3D Acquisition 41
Principle of 3D Acquisition 41
Resolution and Accuracy 42
Table of Contents
Z Resolution 42
Z Linearity 42
Range Output 43
Coordinate Systems 43
Gocator Web Interface 45
User Interface Overview 45
Common Elements 46
Toolbar 46
Metrics Panel 52
Data Viewer 53
Connection and Maintenance 54
Connection Page Overview 54
System Panel 55
Network Settings 55
Sensor Autostart 56
Overheat Temperature Protection 56
Available Sensor Panel 57
Buddy Assignment 57
Security Panel 58
Files Panel 58
Maintenance Panel 60
Sensor Backups and Factory Reset 60
Firmware Upgrade 61
Setup and Calibration 63
Setup Page Overview 63
Operation Mode Panel 65
Trigger Panel 65
Examples 68
Settings 70
Sensor Panel 71
Active Area 71
Exposure 72
Transformations 75
Layout Panel 75
Dual Sensor System Layout 75
Calibration 77
Data Viewer 84
Video Mode 84
Range Mode 85
Region Denition 86
Data Viewer Controls 86
Intensity Output 87
Measurement 88
Measurement Page Overview 88
Tools Panel 89
Adding and Removing Measurements 89
Measurement Management 90

5Gocator 1100 & 1300 Series
Changing the Measurement Name 90
Measurement ID 91
Range Sources 91
Common Measurement Parameters 92
Decisions 92
Output Filters 93
Range Measurement 94
Tools and Measurements 94
Script Measurement 97
Built-in Functions 98
Output 102
Ouput Page Overview 102
Ethernet Control and Output 102
Digital Outputs 107
Analog Output 110
Serial Output 112
Dashboard 114
Dashboard Page Overview 114
State and Health Information 115
Measurement Statistics 116
Gocator Device Files 117
Conguration Files 117
Setup 117
Trigger 117
Layout 118
Calibration 119
Sensors / Sensor 119
Sensors / Sensor / Proling 119
Range 121
Measurements / RangePositionZ 121
Measurements / RangeDierence 121
Measurements / Script 122
Output 123
Ethernet 123
Serial 124
Analog 124
DigitalOutput 125
Calibration File 127
SysCal 127
Entries 127
Protocols 129
Gocator Protocol 129
Concepts 129
Discovery 129
Command Channels 130
Result Channels 130
Modes 130
Buddy Communication Channels 130
States 131
Versions and Upgrades 131
Data Types 131
Range Sources 132
Status Codes 132
Command and Reply Formats 132
Result Format 134
Discovery Commands 134
Get Address 134
Set Address 136
Upgrade Commands 136
Get Protocol Version 136
Start Upgrade 137
Get Upgrade Status 137
Get Upgrade Log 137
Control Commands 138
Get Protocol Version 138
Get System Info 138
Log In/Out 139
Change Password 140
Change Buddy 140
Get File List 140
Copy File 141
Read File 141
Write File 142
Delete File 142
Get Default File 142
Set Default File 143
Get Loaded File 143
Get Mode 144
Set Mode 144
Get Time 144
Get Encoder 145
Start 145
Scheduled Start 145
Stop 146
Trigger 146
Scheduled Digital Output 146
Scheduled Analog Output 147
Ping 147
Reset 148
Backup 148
Restore 148
Restore Factory 149
Set Connection Type 149
Get Connection Type 149
Clear Calibration 150
Data Results 150
Video 151
Range 151
Range Intensity 151
Alignment Calibration 152
Travel Calibration 152

6Gocator 1100 & 1300 Series
Exposure Calibration 152
Measurement 153
Health Results 153
ModBus TCP Protocol 155
Concepts 155
Messages 156
Registers 158
Control Registers 158
Output Registers 159
Measurement Registers 161
EtherNet/IP Protocol 161
Concept 161
Basic Object 163
Identity Object (Class 0x01) 163
TCP/IP Object (Class 0xF5) 163
Ethernet Link Object (Class 0xF6) 164
Assembly Object (Class 0x04) 165
Command Object 165
Sensor State Assembly Object 166
Sample State Assembly 167
Extended Sample State Assembly 168
ASCII Protocol 169
Ethernet Communication 169
Asynchronous and Polling Operation 169
Serial Communication 170
Command and Reply Format 170
Special Characters 170
Standard Result Format 171
Custom Result Format 171
Control Commands 172
Start 172
Stop 172
Trigger 172
Load Conguration 173
Stamp 173
Alignment Calibration 174
Travel Calibration 174
Clear Calibration 174
Data Commands 175
Get Result 175
Get Value 175
Get Decision 176
Health Commands 177
Get Health 177
Selcom Serial Protocol 178
Connection Settings 178
Message Format 178
Software Development Kit 179
Tools 180
Sensor Recovery Tool 180
Troubleshooting 181
Mechanical/Environmental 181
Connection 181
Laser Ranging 181
Performance 182
Specications 183
Gocator 1100 Series 183
Gocator 1300 Series 184
Gocator 1120/1320 (Side Mount Package) 186
Gocator 1120/1320 (Top Mount Package) 188
Gocator 1125/1325 (Side Mount Package) 190
Gocator 1125/1325 (Top Mount Package) 192
Gocator 1150/1350 (Side Mount Package) 194
Gocator 1150/1350 (Top Mount Package) 197
Gocator 1160/1360 (Side Mount Package) 200
Gocator 1160/1360 (Top Mount Package) 203
Gocator 1165/1365 (Side Mount Package) 206
Gocator 1165/1365 (Top Mount Package) 209
Gocator 1170/1370 (Side Mount Package) 212
Gocator 1170/1370 (Top Mount Package) 215
Gocator 1190/1390 (Side Mount Package) 218
Gocator 1190/1390 (Top Mount Package) 221
Gocator 1100/1300 Power/LAN Connector 224
Grounding Shield 224
Power 224
Laser Safety Input 225
Gocator 1100 and 1300 I/O Connector 226
Grounding Shield 226
Digital Outputs 227
Digital Inputs 228
Encoder Input 228
Serial Output 229
Selcom Serial Output 230
Analog Output 231
Master 100 232
Master 100 Dimensions 233
Master 400/800 234
Master 400/800 Electrical Specications 235
Master 400/800 Dimensions 236
Master 1200/2400 237

8Gocator 1100 & 1300 Series
Safety and Maintenance
Laser Safety
Gocator sensors contain semiconductor lasers that emit visible
light and are designated as Class 2M, Class 3R, or Class 3B,
depending on the chosen laser option.
Gocator sensors are referred to as components, indicating that
they are sold only to qualied customers for incorporation into
their own equipment. These sensors do not incorporate safety
items that the customer may be required to provide in their own
equipment (e.g. remote interlocks, key control. Refer to references
for detail information). As such, these sensors do not fully comply
with the standards relating to laser products specied in IEC
60825-1 and FDA CFR Title 21 Part 1040.
!Use of controls or adjustments or performance of procedures other than those specied herein may
result in hazardous radiation exposure.
References
1. International standard IEC 60825-1 (2001-08) consolidated edition, Safety of laser products – Part 1:
Equipment classication, requirements and user’s guide.
2. Technical report 60825-10, Safety of laser products – Part 10. Application guidelines and
explanatory notes to IEC 60825-1.
3. Laser Notice No. 50, FDA and CDRH http://www.fda.gov/cdrh/rad-health.html
LASER
SENSOR
WARNING: DO NOT LOOK DIRECTLY
INTO THE LASER BEAM
LASER

Safety and Maintenance • 9Gocator 1100 & 1300 Series
Laser Classes
Class 2M laser components
Class 2M laser components would not cause permanent
damage to the eye under reasonably foreseeable
conditions of operation, provided that any exposure
can be terminated by the blink reex (assumed to take
0.25 seconds). Because classication assumes the blink
reex, the wavelength of light must be in the visible
range (400 nm to 700 nm). The Maximum Permissible
Exposure (MPE) for visible radiation for 0.25 seconds is
25 watts per square meter, which is equivalent to 1 mW
entering an aperture of 7 mm diameter (the assumed
size of the pupil).
IEC 60825-1:2007
LASER RADIATION
DO NOT STARE INTO THE BEAM
OR VIEW DIRECTLY WITH OPTICAL
INSTRUMENTS OR MAGNIFIERS
CLASS 2M LASER PRODUCT
PEAK POWER:
EMITTED WAVELENGTH:
This product is designated for use solely as a
component and as such it does not fully comply
with the standards relating to laser products
specified in U.S. FDA CFR Title 21 part 1040
and IEC 60825-1
1 mW
660 nm
Class3Rlasercomponents
Class 3R laser products emit radiation where direct
intrabeam viewing is potentially hazardous, but the
risk is lower with 3R lasers than for 3B lasers. Fewer
manufacturing requirements and control measures for
3R laser users apply than for 3B lasers. IEC 60825-1:2007
LASER RADIATION
AVOID DIRECT EYE EXPOSURE
CLASS 3R LASER PRODUCT
PEAK POWER:
EMITTED WAVELENGTH:
This product is designated for use solely as a
component and as such it does not fully comply
with the standards relating to laser products
specified in U.S. FDA CFR Title 21 part 1040
and IEC 60825-1
5 mW
660 nm
Class3Blasercomponents
Class 3B components are unsafe for eye exposure.
Usually only ocular protection will be required. Diuse
reections are safe if viewed for less than 10 seconds.
IEC 60825-1:2007
LASER RADIATION
AVOID EXPOSURE TO THE BEAM
CLASS 3B LASER PRODUCT
PEAK POWER:
EMITTED WAVELENGTH:
This product is designated for use solely as a
component and as such it does not fully comply
with the standards relating to laser products
specified in U.S. FDA CFR Title 21 part 1040
and IEC 60825-1
130 mW
660 nm
Labels reprinted here are examples only. For accurate specications, refer to the label on your sensor.

Safety and Maintenance • 10Gocator 1100 & 1300 Series
Precautions and Responsibilities
Precautions specied in IEC 60825-1 and FDA CFR Title 21 Part 1040 are as follows:
Requirement Class 2M Class3R Class3B
Remote interlock Not required Not required Required*
Key control Not required Not required Required – cannot remove
key when in use*
Power-on delays Not required Not required Required*
Beam attenuator Not required Not required Required*
Emission indicator Not required Not required Required*
Warning signs Not required Not required Required*
Beam path Not required Terminate beam at useful
length
Terminate beam at useful
length
Specular reection Not required Prevent unintentional
reections
Prevent unintentional
reections
Eye protection Not required Not required Required under special
conditions
Laser safety ocer Not required Not required Required
Training Not required Required for operator and
maintenance personnel
Required for operator and
maintenance personnel
*LMI Class 3B laser components do not incorporate these laser safety items. These items must be added and completed by the customer in
their system design.
Class3BResponsibilities
LMI Technologies has led reports with the FDA to assist customers in achieving certication of laser
products. These reports can be referenced by an accession number, provided upon request. Detailed
descriptions of the safety items that must be added to the system design are listed below.
Remote Interlock
A remote interlock connection must be present in Class 3B laser systems. This permits remote switches
to be attached in serial with the keylock switch on the controls. The deactivation of any remote switches
must prevent power from being supplied to any lasers.
Key Control
A key operated master control to the lasers is required that prevents any power from being supplied to
the lasers while in the OFF position. The key can be removed in the OFF position but the switch must not
allow the key to be removed from the lock while in the ON position.
Power-On Delays
A delay circuit is required that illuminates warning indicators for a short period of time prior to supplying
power to the lasers.
BeamAttenuators
A permanently attached method of preventing human access to laser radiation other than switches,
power connectors or key control must be employed. On some LMI laser sensors, the beam attenuator is
supplied with the sensor as an integrated mechanical shutter.

Safety and Maintenance • 11Gocator 1100 & 1300 Series
Emission Indicator
It is required that the controls that operate the sensors incorporate a visible or audible indicator when
power is applied and the lasers are operating. If the distance between the sensor and controls is more
than 2 meters, or mounting of sensors intervenes with observation of these indicators, then a second
power-on indicator should be mounted at some readily-observable position. When mounting the
warning indicators, it is important not to mount them in a location that would require human exposure
to the laser emissions. User must ensure that the emission indicator, if supplied by OEM, is visible when
viewed through protective eyewear.
Warning Signs
Laser warning signs must be located in the vicinity of the sensor such that they will be readily observed.
Examples of laser warning signs are as follows:
PEAK POWER
WAVELENGTH
100mW
600-780nm
CLASS IIIb LASER PRODUCT
INVISIBLE AND/OR VISIBLE LASER RADIATION
AVOID DIRECT EXPOSURE TO BEAM
DANGER
FDA warning sign example
IEC 60825-1:2007
CAUTION
AVOID EXPOSURE
TO THE BEAM
CLASS 3B LASER LIGHT
IEC warning sign example
Systems Sold or Used in the USA
Systems that incorporate laser components or laser products manufactured by LMI Technologies
require certication by the FDA.
Customers are responsible for achieving and maintaining this certication.
Customers are advised to obtain the information booklet Regulations for the Administration and
Enforcement of the Radiation Control for Health and Safety Act of 1968: HHS Publication FDA 88-8035.
This publication, containing the full details of laser safety requirements, can be obtained directly from
the FDA, or downloaded from their web site at http://www.fda.gov/cdrh.

Safety and Maintenance • 12Gocator 1100 & 1300 Series
Electrical Safety
Sensors should be connected to earth ground
All sensors should be connected to earth ground through their housing. All sensors should be mounted
on an earth grounded frame using electrically conductive hardware to ensure the housing of the sensor
is connected to earth ground. Use a multi-meter to check the continuity between the sensor connector
and earth ground to ensure a proper connection.
Minimize voltage potential between system ground and sensor ground
Care should be taken to minimize the voltage potential between system ground (ground reference for
I/O signals) and sensor ground. This voltage potential can be determined by measuring the voltage
between Analog_out- and system ground. The maximum permissible voltage potential is 12 V but should
be kept below 10 V to avoid damage to the serial and encoder connections. Refer to Gocator 1100 and
1300 I/O Connector (page 226) for a description of connector pins.
Use a suitable power supply
The +24 to +48 VDC power supply used with Gocator sensors should be an isolated supply with inrush
current protection or be able to handle a high capacitive load.
Use care when handling powered devices
Wires connecting to the sensor should not be handled while the sensor is powered. Doing so may cause
electrical shock to the user or damage to the equipment.
!
Failure to adhere to the guidelines described in this section may result in electrical shock or equipment
damage.

Safety and Maintenance • 13Gocator 1100 & 1300 Series
Environment and Lighting
Avoid strong ambient light sources
The imager used in this product is highly sensitive to ambient light hence stray light may have adverse
eects on measurement. Do not operate this device near windows or lighting xtures that could
inuence measurement. If the unit must be installed in an environment with high ambient light levels, a
lighting shield or similar device may need to be installed to prevent light from aecting measurement.
Avoid installing sensors in hazardous environments
To ensure reliable operation and to prevent damage to Gocator sensors, avoid installing the sensor in
locations;
• that are humid, dusty, or poorly ventilated
• with a high temperature, such as places exposed to direct sunlight
• where there are ammable or corrosive gases
• where the unit may be directly subjected to harsh vibration or impact
• where water, oil, or chemicals may splash onto the unit
• where static electricity is easily generated
Ensurethatambientconditionsarewithinspecications
Gocator sensors are suitable for operation between 0 – 50 °C and 25 – 85% relative humidity (non-
condensing). Measurement error due to temperature is limited to 0.015% of full scale per degree C.
The Master 100/400/800/1200/2400 is similarly rated for operation between 0 – 50 °C.
The storage temperature is -30 – 70 °C.
!
It is critical that the sensor is heat sunk through the frame it is mounted to. When a sensor is properly
heat sunk, the dierence between ambient temperature and the temperature reported in the sensor's
health channel is less than 15 °C.
Gocator sensors are high accuracy devices. It is critical that the temperature of all of its components are
in equilibrium. When the sensor is powered up, a warm-up time of at least one hour is required in order
to reach a consistent spread of temperature within the sensor.
Sensor Maintenance
Keep sensor windows clean
Gocator sensors are high-precision optical instruments. To ensure the highest accuracy is achieved in all
measurements, the windows on the front of the sensor should be kept clean and clear of debris.
Use care when cleaning sensor windows
Use dry, clean air to remove dust or other dirt particles. If dirt remains, clean the windows carefully with
a soft, lint-free cloth and non-streaking glass cleaner or isopropyl alcohol. Ensure that no residue is left
on the windows after cleaning.
Turnolaserswhennotinuse
LMI Technologies uses semiconductor lasers in 3D measurement sensors. To maximize the lifespan of
the sensor, turn o the laser when not in use.

Safety and Maintenance • 14Gocator 1100 & 1300 Series
Avoidexcessivemodicationstolesstoredonthesensor
Settings for Gocator sensors are stored in ash memory inside the sensor. Flash memory has an
expected lifetime of 100,000 writes. To maximize lifetime, avoid frequent or unnecessary le save
operations.

15Gocator 1100 & 1300 Series
System Overview
Gocator sensors can be installed and used in a variety of scenarios. Sensors can be connected as
standalone devices, dual-sensor systems, or multi-sensor systems.
Standalone System
Standalone systems are typically used when only a single Gocator sensor is required. The sensor can
be connected to a computer’s Ethernet port for setup and can also be connected to devices such as
encoders, photocells, or PLCs.
GOCATOR
POWER AND ETHERNET
CORDSET
GOCATOR I/O
CORDSET
GOCATOR
IN - ENCODER / TRIGGER / SAFETY
OUT - SERIAL / ANALOG / DIGITAL
USER PC
(can be disconnected after setup)
Getting Started

Getting Started • 16Gocator 1100 & 1300 Series
Dual-Sensor System
In a dual-sensor system, two Gocator sensors work together to perform ranging and output the
combined results. The controlling sensor is referred to as the Main sensor, and the helper is referred
to as the Buddy sensor. Gocator’s software recognizes three installation orientations – None (Isolated),
Opposite and Wide.
A Master 400/800/1200/2400 must be used to connect two sensors in a Dual-Sensor system. Gocator
Master cordsets are used to connect sensors to the Master.
GOCATOR
POWER AND ETHERNET
CORDSET
GOCATOR
I/O
CORDSET
MAIN
GOCATOR BUDDY
GOCATOR
POWER, LASER SAFETY,
TRIGGER INPUTS, ENCODER
GIGABIT ETHERNET SWITCH
MASTER 400/800/1200/2400

Getting Started • 17Gocator 1100 & 1300 Series
Multi-Sensor System
Master 400/800/1200/2400 networking hardware can be used to connect two or more sensors into
a Multi-sensor system. Gocator Master cordsets are used to connect the sensors to a Master. The
Master provides a single point of connection for power, safety, encoder and digital inputs. A Master
400/800/1200/2400 can be used to ensure that the scan timing is precisely synchronized across
sensors. Sensors and client computers communicate via an Ethernet switch (minimum 100 Mbit/s).
GOCATOR
POWER AND ETHERNET
TO MASTER CORDSET
USER PC
GIGABIT ETHERNET SWITCH
CAT5E ETHERNET CABLE
MASTER 400/800/1200/2400
POWER, LASER SAFETY,
TRIGGER INPUTS, ENCODER
GOCATOR

Getting Started • 18Gocator 1100 & 1300 Series
Hardware Overview
The Gocator 1100 and 1300 sensors are available in either the Top Mount Package or the Side Mount
Package. Side Mount Package is designed for side mounting and the Top Mount Package is designed for
top mounting.
Side Mount Package
CAMERA
LASER EMITTER
I/O CONNECTOR
POWER/LAN CONNECTOR
SERIAL NUMBER
POWER, RANGE AND LASER
INDICATOR
Item Description
Camera Observes laser light reected from target surfaces.
Laser Emitter Emits structured light for laser ranging.
I/O Connector Accepts input and output signals.
Power / LAN Connector Accepts power and laser safety signals and connects to 1000 Mbit/s Ethernet network.
Power Indicator Illuminates when power is applied (blue).
Range Indicator Illuminates when camera detects laser light and is within the target range (green).
Laser Indicator Illuminates when laser safety input is active (amber).
Serial Number Unique sensor serial number.

Getting Started • 19Gocator 1100 & 1300 Series
Top Mount Package
CAMERA
LASER EMITTER
LAN CONNECTOR
I/O CONNECTOR
POWER/LAN CONNECTOR
SERIAL NUMBER
POWER, RANGE, LASER
INDICATORS
Item Description
Camera Observes laser light reected from target surfaces.
Laser Emitter Emits structured light for laser ranging.
I/O Connector Accepts input and output signals.
Power / LAN Connector Accepts power and laser safety signals and connects to 1000 Mbit/s Ethernet network.
Power Indicator Illuminates when power is applied (blue).
Range Indicator Illuminates when camera detects laser light and is within the target range (green).
Laser Indicator Illuminates when laser safety input is active (amber).
Serial Number Unique sensor serial number.

Getting Started • 20Gocator 1100 & 1300 Series
Master 100
The Master 100 is used by the Gocator 1100 and 1300 series for standalone system setup.
Sensor IO Port
3
Master Host Port
Master Power Port
Encoder/Output Port
Master Ethernet Port
48V Power Supply*
(Pin 1)
(Pin 1)
Item Description
Master Ethernet Port Connects to the RJ45 connector labeled Ethernet on the Power/LAN to Master cordset.
Master Power Port Connects to the RJ45 connector labeled Power/Sync on the Power/LAN to Master
cordset. Provides power and laser safety to the Gocator.
Sensor I/O Port Connects to the Gocator I/O cordset.
Master Host Port Connects to the host PC's Ethernet port.
Power Accepts power (+48 V).
Power Switch Toggles sensor power.
Laser Safety Switch Toggles laser safety signal provided to the sensors [O= laser o, I= laser on].
Trigger Signals a digital input trigger to the Gocator.
Encoder Accepts encoder A, B and Z signals.
Digital Output Provides digital output.
Refer to Master 100 (page 232) for pinout details.
This manual suits for next models
15
Table of contents
Other LMI Technologies Laser Level manuals
Popular Laser Level manuals by other brands

Clas Ohlson
Clas Ohlson 40-7531 instructions
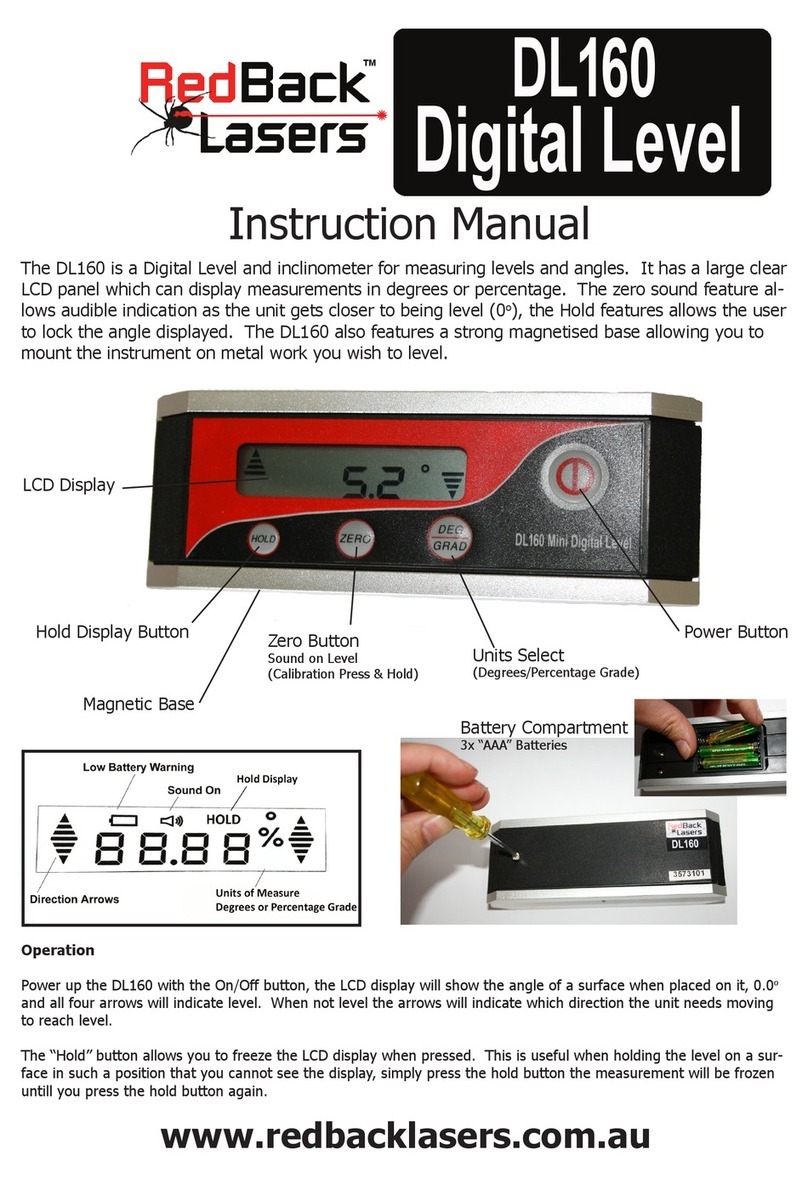
RedBack Laser
RedBack Laser DL 160 instruction manual

geo-FENNEL
geo-FENNEL 360 LinerPoint HP user manual
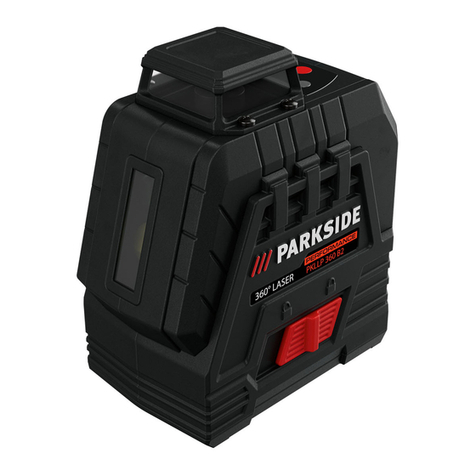
Parkside Performance
Parkside Performance PKLLP 360 B2 Operation and safety notes
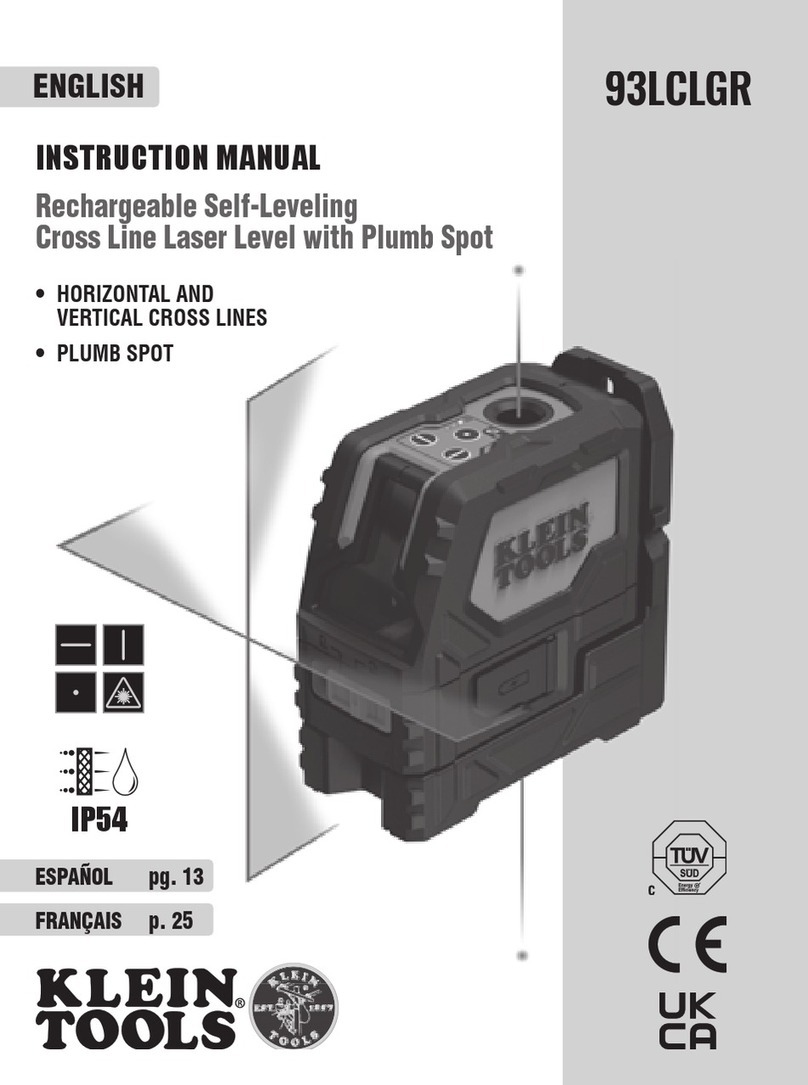
Klein Tools
Klein Tools 93LCLGR instruction manual
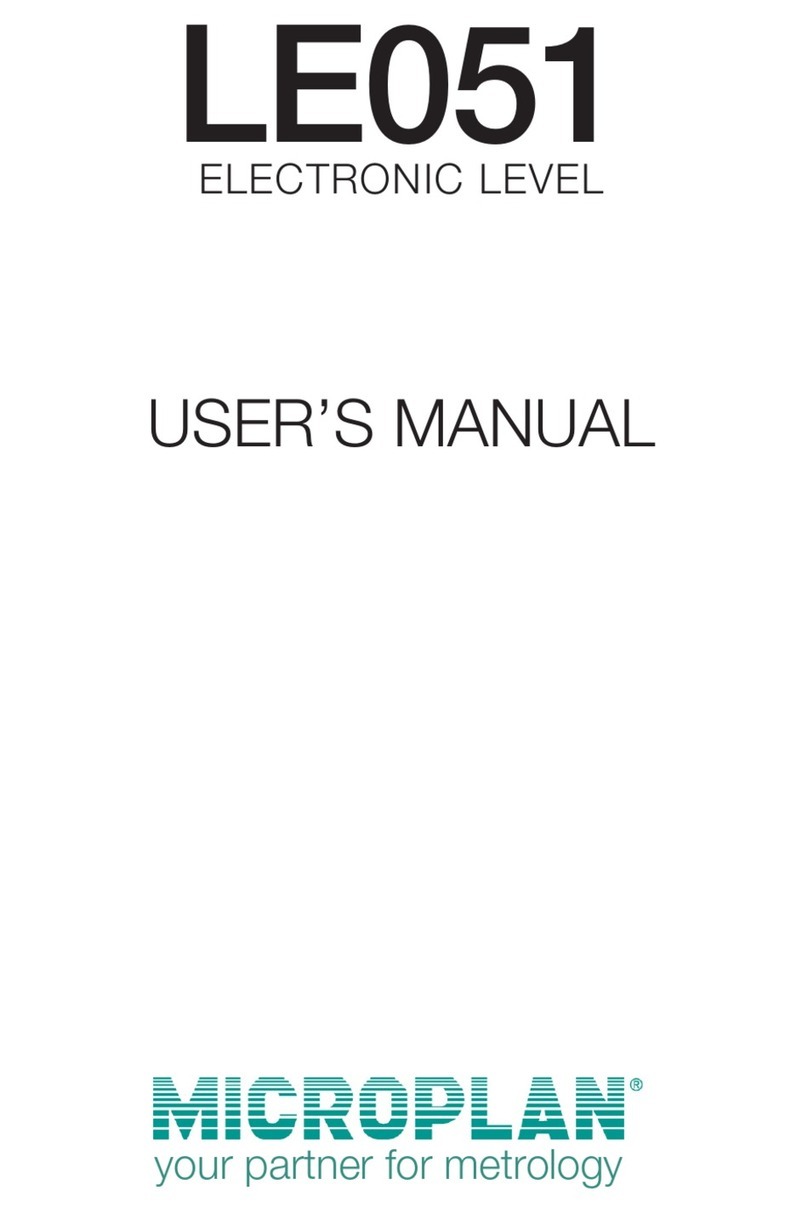
Microplan
Microplan LE051 user manual