MAULE MX-7-420 TURBO-PROP User manual

Rev. A
FOR
MAULE MX-7-420
TURBO-PROP

MAULE AEROSPACE TECHNOLOGY, INC.
MAINTENANCE MANUAL
FOR M-7-420A
Rev. A
i
FOREWORD
Ahead of you are many hours of flying pleasure. The more you fly your new M-7 the
more you will realize that flying this aircraft is a stimulating new sensation that will never grow
old.
The Maule M-7 is designed and built to give you the airplane you have always
wanted. It is fast, comfortable, and easy to fly, yet no light airplane is safer than the Maule
M-7. Its sturdy construction means you will not have to pamper it to enjoy long years of
trouble-free service.
Our dealers and distributors are anxious to serve you and will gladly furnish advice as
to proper servicing methods. You may also address requests for information on any items
not covered in this manual to Maule Parts-Service Department of Maule Air, Inc. (Telephone
912-985-2045, Ext. 239). In correspondence, please be certain to give complete information
on serial number, engine make and model, etc.
WARRANTY
Maule Air, Inc. warrants each new airplane manufactured by it to be free from defects
in material and workmanship under normal use and service, provided, however, that this war-
ranty is limited to making good at the Maule factory any part or parts thereof which shall,
within ninety (90) days after delivery of such airplane to the original purchaser, be returned to
Maule with transportation charges prepaid, and which upon Maule's examination shall dis-
close to its satisfaction to have been thus defective; this warranty being expressly in lieu of
all other warranties expressed or implied and all other obligations or liabilities on the part of
Maule, and Maule neither assumes nor authorizes any other person to assume for it any
other liability in connection with the sale of its airplane.
This warranty shall not apply to any airplane which shall have been repaired or al-
tered outside Maule's factory in any way so as, in Maule's judgment, to affect the airplane’s
stability or reliability, or which airplane has been subject to misuse, negligence or accident.
Certain items of equipment are warranted separately by their manufacturer. The en-
gine and accessories are warranted by Allison Gas Turbine Division, General Motors Corpo-
ration, Indianapolis, Indiana. The Hartzell Propeller is warranted by Hartzell Propeller, Inc.,
Piqua, OH. Avionics items are warranted by their manufacturers. Manufacturers of sepa-
rately warranted items of equipment request that warranty claims be made through your
nearest authorized Distributor or authorized Service Center. Maule Air will be glad to help
you find that facility nearest to you.

MAULE AEROSPACE TECHNOLOGY, INC.
MAINTENANCE MANUAL
FOR M-7-420A
Rev. A
ii
TABLE OF CONTENTS
ITEM PAGE
Foreword...................................................................….…..
i
Warranty...............…................................................………
i
Table of Contents…............................….............................
ii
Log of Revisions…..................................…….....................
iii
SECTION I - GENERAL DATA
General Description......................................……................
1
Design Specification..........................................……...........
1
Fluid Capacities and Specification..........................……......
2
SECTION II - GENERAL MAINTENANCE
Cleaning and Care of Aircraft.....……..........................….…
4
Inspection Guides............................…….............................
6
Rigging Procedures..............................……........................
16
Lubrication.................................................…….......……….
18
Fabric Repairs………………………………………………….
19
SECTION III - MAJOR COMPONENT PARTS
Wings.....................................................……...................…
20
Lift Struts.....................................................……..............…
20
Fuselage...........................................................…....…....…
20
Surfaces and Controls................................……………..…..
21
Landing Gear, Wheels and Brakes......……....................….
22
Tailwheel………………………………………….……………..
24
Figure One………………………………………….…………..
26
Power Plant System........…..............................……...…..…
27
Fuel System....................….............................……….….…
28
Electrical System................…...................................………
29
Electrical Schematic………….......……………………….…..
32
Door Latch Adjustment Procedure....………..........……...…
35

MAULE AEROSPACE TECHNOLOGY, INC.
MAINTENANCE MANUAL
FOR MX-7-420
1
Rev. A
LOG OF REVISIONS
Rev. To
Page(s) Description Date
A 3, 19,
23, 24 Added oleo strut oil API GL-4 or GL-5 85W-140 gear oil for
new oleo spring P/N 4161B. 04/16/16

MAULE AEROSPACE TECHNOLOGY, INC.
MAINTENANCE MANUAL
FOR MX-7-420
2
Rev. A
SECTION I
GENERAL DATA
GENERAL DESCRIPTION:
Type: Four/five place high wing cabin monoplane.
Engine Installation: Single tractor engine in nose of fuselage.
Wing: Strut braced, two spar, metal covered, modified USA 35-B airfoil. Fiberglass
wing tips.
Fuselage: Welded steel tube structure.
Fuselage and tail group covered with Ceconite synthetic fabric. Fiberglass
engine cowl. Aluminum skin on forward fuselage and doors.
Landing Gear: Main gear split axle type, spring-oil oleo shock absorber. Hydraulic
Brakes. Steerable tailwheel (Automatic locking).
Control Systems: Dual controls wheels, rudder pedals and brakes. All controls direct-
ly cable driven. Fuel control/shut off valve is at the left lower side
panel. Mechanical flap and trim controls are at the center on the
floor. All other controls, switches, etc., are instrument panel
mounted.
DESIGN SPECIFICATIONS:
Wing Span 30 feet 10 inches
Length 24 feet 5 inches
Height 6 feet 4 inches
Gross Weight 2500 lbs.
Empty Weight Approx. 1440 lbs.
Wing Loading 15.8 lbs./sq. ft.
Power Loading 6.8 lbs./BHP
Useful Load Approx. 1060 lbs.
Seats Four/five
Flaps Neg. 7°, 0°, 24°, 40°
Baggage Allowance 250 lb. Structural Limit
Baggage Compartment Dimensions 35
½
H x 30W x 21L
Wings: a. Airfoil Modified USA 35-B
b. Chord 63 inches
c. Incidence +30 minutes
d. Dihedral 1.2 degrees
e. Sweepback None

MAULE AEROSPACE TECHNOLOGY, INC.
MAINTENANCE MANUAL
FOR MX-7-420
3
Rev. A
Areas:
a. Wing, Aileron and Flaps 157.9 sq.ft.
b. Ailerons (total) 12.6 sq.ft.
c. Flaps (total) 24.8 sq.ft.
d. Horizontal Stabilizer 18.1 sq. ft.
e. Elevators (including tab) 14.1 sq. ft.
f. Vertical Stabilizer 13.1 sq. ft.
g. Rudder 6.2 sq. ft.
h. Elevator Trim tab 1.03 sq. ft.
i. Rudder Tab .34 sq. ft.
FLUID CAPACITIES AND SPECIFICATIONS:
a. Main Fuel Tanks – (Jet A – wing leading edge inboard)
Right Main Tank 21.5 or 23.8 gallons
Left Main Tank 21.5 or 23.8 gallons
(Main fuel tanks considered one tank.)
b. Auxiliary Fuel Tanks – (Jet A – wing leading edge outboard)
Right Auxiliary Tank 15.0 gallons
Left Auxiliary Tank 15.0 gallons
c. Engine Oil (Mil-L-7808 and later and Mil-23699 and later) 10 quart max.
d. Brakes (Texaco Aircraft Hydraulic Oil 15, MIL-H-5606E or equiv.) 1 pint
e. Landing Gear - For P/N 4015B oleo spring, use New Holland No.134
hydraulic oil or Ford Tractor No. ESN-M2C134-D. 10W30 engine oil
may also be used. For P/N 4161B oleo spring use API GL-4 or GL-5
85W-140 gear oil
ENGINE FUEL SPECIFICATIONS
Primary MIL -T-5624L, grade JP-4 and JP-5
MIL-T-83133A, grade JP-8
ASTM D-1655, Jet B
ASTM D-1655, Jet A or A1
JP-1 fuel conforming to ASTM D-1655, Jet A
Arctic Diesel Fuel DF-A(VV-F-800B) conforming to ASTM D-1655, Jet A or A1
Diesel #1 fuel conforming to ASTM D-1655, Jet A
CAUTION Not all No. 1 diesel fuels or JP-1 fuels meet the primary fuel specifications. It is
the responsibility of the operator and supplier to determine whether a given fuel
meets these specifications.

MAULE AEROSPACE TECHNOLOGY, INC.
MAINTENANCE MANUAL
FOR MX-7-420
4
Rev. A
Emergency Mil-G-5572F, Aviation Gasoline, all grades (aircraft boost pump on; maximum
of 6 hours operation per overhaul period of turbine through an engine operat-
ing range of idle to 90% maximum SHP.)
CAUTION: MIL-G-5572 fuel containing tricresylphosphate (TCP) additive shall NOT be used.
Cold Weather To assure consistent starts below 4°C (40°F), the following fuels may be
necessary: MIL-T-5624, grade JP-4 ASTM D-1655, Jet B AVGAS/Jet A, Jet
A1, or JP-5 mixture (Refer to Cold Weather Fuels, para 2-48, of Allison 250-
B17 Engine Series Operation and Maintenance Manual for mixing/use of
cold weather fuel.)
NOTE Jet A, A1, JP-8 or JP-5 fuels are not restricted from use at ambient temperatures be-
low 0°F (-18°C); however, special provisions for starting must be made. (Refer to the Aircraft
Flight Manual.) Prolonged and uninterrupted operation with only AVGAS mixture will induce
lead buildup on turbine parts. This lead buildup can cause a gradual power reduction; con-
sequently, this AVGAS mixture should be used only for cold weather operation. During op-
eration with normal Jet A type fuel, the lead will slowly dissipate.
ENGINE OIL SPECIFICATION
The 250 Series engines are qualified and certified for use with MIL-L-7808 and subsequent,
and MIL-L-23699 series lubricating oils. The vendor brands of MIL-L-7808 and MIL-L-23699
series lubricating oils, which have been engine tested and accepted for use in the Model 250
engine, are listed in the Approved Oils paragraph of Allison 250-BI7 Engine Series Operation
& Maintenance Manual. Refer to para 1-73, Cold Weather Lubrication for the type of oil rec-
ommended at specific ambient temperatures.
NOTE Because of availability, reduced coking and better lubricating qualities at higher tem-
peratures, MIL-L-23699 oils are preferred for use in Model 250 engines. (Except for extreme-
ly cold weather operation, as indicated below).
Cold Weather Lubrication. The types of oil recommended at specific ambient temperatures
are as follows:
Ambient Temperature. Oil Type
0°C (32°F) and above MIL-L-23699, preferred
0°C (32°F) to -40°(-40°F) NM-L-23699 or MIL-L-7808G
-40°C (-40°F) and below MIL-L-7808G only
Approved Oils: Mixing of approved oils in 250 series engines is permitted only within a given
group number. An oil may be mixed with any other oil in its group. For example, an oil in
Group 23 may be mixed with another brand of oil in Group 23. Refer to the latest revision of
Allison 250-BI7 Engine Operations and Maintenance Manual (Publication 11W2) for ap-
proved oils, paragraph 1-74.
WARNING: Mixing of oils within an oil series but not in the same group is permitted only in
an emergency. Use of mixed oils (oils not in the same group) in an engine is limited to five

MAULE AEROSPACE TECHNOLOGY, INC.
MAINTENANCE MANUAL
FOR MX-7-420
5
Rev. A
hours total running time. Adequate maintenance records must be maintained to ensure that
the five-hour limit is not exceeded. Mixing of oils from different series is not permitted. Fail-
ure to comply with oil mixing restrictions can result in engine failure.
SECTION II
GENERAL MAINTENANCE
CLEANING AND CARE OF AIRCRAFT
Keeping the performance, speed and durability that was built into your aircraft at the
factory requires more than casual attention. The accumulation of dirt and oil on the outside
and debris inside does affect these factors and can be a fire hazard as well. The first step to
proper maintenance is a clean aircraft.
EXTERIOR
Frequent washing is good for your aircraft finish, especially during the first few
months. Use any quality car wash with a soft cloth or sponge and plenty of clean water-do
not use dishwashing detergent. Drying should be done with a chamois. Accumulation of oil,
grease and exhaust carbon deposits should be removed frequently by using a soft cloth
soaked in mineral spirits or other neutral cleaner.
For general polishing, apply a good quality car polish or wax according to instruc-
tions. Clean Plexiglas with plenty of soap and water using grit free soft cloth, chamois or
sponge. Use of a dry cloth on Plexiglas will not only cause scratches but will also build up an
electrostatic field which will attract dust to the surface. Blotting with a clean damp chamois
will remove the charge and the dust. After cleaning, polishing with a good Plexiglas cleaning
product such as "Mirror Glaze" will keep the glass clean and help polish out minor scratches.
Experience has shown that airplanes based at coastal airports or where there is an
otherwise corrosive atmosphere require special treatment to prevent corrosion, specifically
"electrolyte corrosion". Salt water and chemicals act as an electrolyte between dissimilar
metals and can start a strong corrosive action over a short period of time. Maule makes
every effort to separate dissimilar metals with primers and coatings during manufacture, but
there are some locations (such as rivets in wing skins) where this is impossible. To combat
corrosion it is important that the external painted surfaces be kept clean and well waxed.
Wash the airplane with fresh water frequently to remove any salt or chemical film. Periodi-
cally, coat the wings, flaps and ailerons internally with a quality corrosion preventative, sev-
eral of which are available. Floatplanes require more extensive preservation techniques
which are well known in the field.
INTERIOR
Floorboards should be vacuumed frequently and can be cleaned with any good rug
cleaner.

MAULE AEROSPACE TECHNOLOGY, INC.
MAINTENANCE MANUAL
FOR MX-7-420
6
Rev. A
Care should be taken in the disposal of candy wrappers, paper scraps, cigarette
butts, etc. These can work their way under the floorboards and become a fire hazard and
moisture trap.
NOTE: While washing the aircraft, ascertain that all drain holes are open. Clean out
any debris blocking them. Accumulated water can be dangerous, so check behind the bag-
gage compartment frequently.
Textile upholstery may be cleaned using a vacuum cleaner. Grease and oil spots on
the upholstery should be treated with a spot remover or dry cleaning fluid. Do not use soap
and water on textile materials.
Vinyl upholstery may be cleaned using soft whisk broom or suds of any mild soap
(castile or olive oil base) in lukewarm water. Use water sparingly as the upholstery otherwise
requires a long time to dry if water trickles through the seam stitches.
For best results, stains, especially those caused by grease or paint, should be re-
moved from upholstery as soon as possible or they may become “set”" and hard or impossi-
ble to remove. "Set" stains should be removed carefully with a clean cloth dampened in de-
natured alcohol. Stains caused by shoe polish can best be removed with turpentine. How-
ever, such cleaning agents are liable to affect the dust-repellent finish of the vinyl if used in
excess of the actual requirements. Never use volatile solvents such as lacquer thinner, ace-
tone, etc. on upholstery.
The cleaning should be completed by wiping the surface of the vinyl dry with a clean
cloth, particularly in the seam. No attempt should be made to apply preservatives such as
wax, polish, or varnishes, as these will not be absorbed by vinyl, but will merely collect dust.
There are protective treatments made especially for vinyl which are commercially available
and quite satisfactory.
Leather upholstery should be cleaned by leather cleaning methods using leather-
cleaning products.

MAULE AEROSPACE TECHNOLOGY, INC.
MAINTENANCE MANUAL
FOR MX-7-420
7
Rev. A
INSPECTION GUIDES
AIRFRAME INSPECTION
At 25 Hour Total Time, perform 50 Hour Inspection as described below:
At 50 Hour Total Time and every 50 hours thereafter:
1. Check battery for general condition and electrolyte level.
2. Check all main electrical connections.
3. Check fluid level in brake reservoirs.
4. Check the entire fuselage, tail surfaces and wing skins for cracks, security of fair-
ings and general condition.
CAUTION: If airplane is subject to excessive stress, i.e., heavy loads, adverse wind
conditions, rough landings, etc., take special care in examining wing skins for any
cracks. If any are found, repair before further flight in accordance with AC 43:13 and
factory drawings. (Do not replace any countersunk rivets with buttonhead rivets in wing
because it is not approved.)
5. Check aileron and flap skins for cracks.
6. Check the security, operation and general condition of all control surfaces.
7. Check main landing gear for condition and brakes for leakage and wear.
8. Check main landing gear oleo struts for oil leaks.
9. Check general condition of tailwheel, leaf springs and spring attachment. Leaf
springs should have 45°angle with no weight on the wheel. Check all bolts and
nuts holding the tail springs to the fuselage. Tighten nuts, if needed, so that there
is no play or side movement in the springs or their attachment.
10. Check tires for inflation and cuts.
11. Drain sumps of fuel tanks, checking for contamination and water.
At 100 Hours Total Time and every 100 Hours thereafter, perform the 50 hour inspection
plus the following:
1. Remove right and left kick panels in cockpit, windshield side post covers and panels
below seat fronts. Examine protective rudder cable guide tubes, (located behind
kick panels), if installed and attaching clamps, bolts and nuts for security and gen-
eral condition.

MAULE AEROSPACE TECHNOLOGY, INC.
MAINTENANCE MANUAL
FOR MX-7-420
8
Rev. A
2. Examine all front cockpit electrical connections and wires, fuel lines and fittings,
control cables attachments and pulleys for security, leaks, chafing, etc.
3. Remove rear seat, rear floorboard and panel behind baggage compartment.
4. Inspect all structure, all control cables, pulleys, fairings and electrical connections
and wires for security, chafing and corrosion.
5. Open zippers in headliner and inspect all control cables, pulleys, fairleads and elec-
trical connections and wires for security and chafing.
6. Remove wing root fairings and inspect control cables, fairleads, fuel lines and con-
nections, and electrical wires and connections for security, chafing and leaks. In-
spect wing attach points for security and corrosion.
7. Remove wing strut fairings, top and bottom, and inspect attaching fittings and bolts
for security, corrosion and cracks. Carefully inspect both sides of lift struts for ab-
rasion, corrosion, pin holes and punctures. Any paint loss or minor corrosion
should be sanded down to bare metal with fine sandpaper and metal primer should
be applied. After the primer is dried, a finish coat of the desired color may be add-
ed. Powder coating is recommended if complete strut is being refinished.
WARNING: Any unrepairable dents or punctures in strut are cause for replacement of
the strut.
CAUTION: This aircraft was equipped with sealed struts when manufactured, however,
if these struts were replaced in field with unsealed struts, comply with Maule Service
Bulletin No. 11 (AD# 98-15-18) as required. (New sealed struts are identified by two
weld spots located at upper end. Removal of the upper cuff is needed to locate the
weld spots).
CAUTION: Item (a)(4) of AD# 98-15-18 is very misleading as Maule never drills holes
in struts to attach cuffs, door clips or any hardware and it is illegal to do so since there
are no approved holes in the wing struts under the TC data. If aircraft has a modifica-
tion added requiring a drilled hole in strut under a #337, refer to AD for inspection re-
quirements at the 24-month intervals. Also, inspect the area around the holes(s) fre-
quently for corrosion or cracking (ref. SL#58).
8. Remove wheels and inspect wheels, tires, brake disc, bearings, brake lines and
brake pad for wear, cuts, chafing, leaks and general condition. Repack wheel bear-
ings.
9. Remove landing gear top fairings and inspect attaching fittings and bolts for securi-
ty, corrosion and cracks and inspect brake hose for security, chafing and leaks.
10. Remove all inspection covers/plates and inspect all visible control cables, pulleys,
bellcranks, electrical wires and connections, fuel lines and fittings, nuts, bolts, etc.
for security, chafing, leaks, etc.

MAULE AEROSPACE TECHNOLOGY, INC.
MAINTENANCE MANUAL
FOR MX-7-420
9
Rev. A
(CAUTION: If a wing has been removed and reinstalled, or a new wing installed, visual-
ly inspect the routing of aileron cables through the inspection hole cover located on un-
derside of wing, aft of rear spar and outboard of wing strut attach brackets. Ascertain
that cables are not routed over the strut attach brackets and are properly routed
through the fairleads and around pulleys. Ref. Maule Service Bulletin No. 12.)
11. CAUTION: At inspection hole in tail, visually check the pivoting action at the control
cable attachment points over the full range of rudder and elevator travel. This ac-
tion should be such that there are no bending loads imparted to the turnbuckles
(which are designed for straight tension load only). Any binding, which causes
bending of the turnbuckles, should be removed. Any cable attachment parts, which
display appreciable corrosion, must be replaced before further flight. NOTE: Pivot
points must be cleaned and lubricated with any lightweight lubricating oil. Following
lubrication, the cable attachments, including the turnbuckles, must be heavily
coated with a good preservative such as :
Black Bear Paralketone Preventative LPS 3, Heavy Duty Rust Inhibitor
Black Bear Co. (preferred) LPS Laboratories, Inc.
Long Island City, NY Tucker, GA
NOTE: Maule Service Bulletin No. 9 covers corrosive resistant parts replacement and is
particularly recommended for airplanes operating in a potentially corrosive environment.
Compliance to this SB provides for larger stainless steel turnbuckles and corrosion re-
sistant steel fasteners and attachment details for the elevator cables.
12. CAUTION: Special attention should be given to the horizontal stabilizer strut lower
attach tubes which are welded to the lower longerons. The seal on the inside of the
lower strut attach stub tubes can deteriorate with age which could cause corrosion
on the interior of the attach stub tubes, especially on floatplane models. It is rec-
ommended that the stabilizer struts be removed to inspect attach stub tubes at
each annual. If there is visible external corrosion around the attach stub tubes, or
the internal seal appears loose or cracked, remove the seal, clean the inside of the
tube and visually inspect the inside for corrosion. If corrosion is found, repair in ac-
cordance with AC 43.13-1B. After repair, or if no corrosion is found, fill entire tube
with silicone rubber to seal tube from moisture. Inspect the struts for dents, corro-
sion, or punctures and replace if necessary. Reinstall struts with new hardware and
document in aircraft records.
13. Lubricate all chains and points of rotation on sprockets, pulleys and bellcranks.
14. Inspect and lubricate all control surface hinges and control horn connections.
15. Lubricate door hinges and latches and seat tracks.
CAUTION: Carefully inspect all door hinge bolts and nuts for condition and security. If
using elastic nuts on door hinges, they must be replaced with castle nuts and cotter
pins. Refer to Maule Service Letter No. 61.

MAULE AEROSPACE TECHNOLOGY, INC.
MAINTENANCE MANUAL
FOR MX-7-420
10
Rev. A
16. Lubricate rudder pedals and rudder bar points of rotation.
17. Check control rigging and cable tensions.
18. Check and clean vacuum system regulator valve filter and intake filter.
19. Check the pitot static system for leaks.
20. Ensure that all applicable Airworthiness Directives and Maule Service Letters and
Bulletins that are mandatory have been complied with.
ENGINE INSPECTION
Scheduled Engine Inspection
CAUTION: Before undertaking any inspection or maintenance action, consult the referenced
paragraphs of the Allison Operation and Maintenance Manual. Failure to do so could result
in equipment damage or destruction, possibly resulting in personnel death or injury.
100 HOUR INSPECTION
Item Reference Inspection/Maintenance Action
1 N/A
Inspect the engine for loose or missing bolts, broken or
loose connections, security of mounting accessories and
broken or missing lock wire. Check accessible areas for ob-
vious damage and evidence of fuel or oil leakage.
2 N/A
Check mounting and support bolts to be sure they are tight,
lockwired and in good condition. Check security of screws
and rivets. Remove all foreign materials which might be
drawn into the compressor inlet.
3 N/A Check accessible fuel system components, lines, and con-
nections for security, damage or leakage. Accomplish with
the boost pump on.
4 3-134
Check fuel and propeller system control linkage for freedom
of operation, full travel and proper rigging. Check for exces-
sively high throttle forces and security of linkage. Also
check for loose or worn linkage and linkage bolts.
5 N/A Inspect compressor inlet guide vanes and visible blades and
vanes for foreign object damage.
6 3-37 Clean compressor with chemical wash solution if operating
in a smoggy area (as required).

MAULE AEROSPACE TECHNOLOGY, INC.
MAINTENANCE MANUAL
FOR MX-7-420
11
Rev. A
7 N/A Inspect the compressor scroll for cracks or breaks at the
anti-ice valve and customer bleed ports. If cracks or breaks
are detected, check engine for possible vibration causes.
8 N/A Inspect for discharge air tube inserts that are cocked or
backing out of the scroll. If cocked or loose inserts are de-
tected, check engine for possible vibration causes.
9 3-193 Check anti-icing valve for security, worn parts and proper
operation. Valve need not be removed or disassembled un-
less a problem is detected.
10 3-237, 3-238 Inspect compressor mount inserts for looseness or oil lea-
kage. Replace if loose and check engine for possible vibra-
tion causes.
11 3-221
Inspect the turbine support assemblies and engine exhaust
ducts for condition of welded joints, for cracks and buckling.
Check exhaust duct clamps for proper installation, condition
and torque.
12 3-235
Wet spline starter-generator gearshafts (new production or
those replaced in accordance with the Allison Commercial
Engine Bulletin (250-B17TP CEB-1056) do not need period-
ic inspection and lubrication. Clean and inspect any other
starter-generator gearshaft. Clean the female splines of the
starter-generator with mineral spirits and a soft brush. In-
spect splines in accordance with para 3-236, Starter-
Generator Gearshaft Female Spline Inspection.
Lubricate acceptable splines with grease (Aeroshell No.22,
or equivalent). Before reinstallation of the starter-generator,
make sure torsional damper members of the starter-
generator driveshaft are in hard contact with each other.
NOTE: Inspect the starter-generator brushes for wear in ac-
cordance with the Aircraft Manual at the same time the
spline inspection is made.
13 Item 5, Table III-10 Inspect and clean the turbine pressure oil system check
valve.
14 Item 4, Table III-10 Inspect and clean pressure oil tube screen assembly.
15 3-178 Measure oil flow from the scavenge passage or external
sump of the power turbine support.
16 Item 7, Table III-10 Inspect, clean and check magnetic drain plugs.
17 3-230 Inspect the outer combustion case for condition. Inspect the
weld joints of cases that do not have the brazed screen rein-
forcement in the armpit area.

MAULE AEROSPACE TECHNOLOGY, INC.
MAINTENANCE MANUAL
FOR MX-7-420
12
Rev. A
18 3-232 Clean the burner drain valve.
19 3-185 Inspect the ignition lead for burning, chafing, or cracking of
conduit and loose connectors and broken lock wire.
20 N/A Review engine records for compliance with all mandatory
bulletins, inspections and airworthiness directives.
21 N/A Review engine records for time or cycle limited parts, com-
ponents, accessories or modules.
22 N/A Enter component changes, inspection compliance, etc., in
logbook as required.
200 Hour Inspection
ln addition to the l00 hour inspection items, perform the following:
23
Item 1, Table III-103-
168; Item 2, Table III-
10 3-163, 3-172; Item
7, Table III-I0
Drain oil system and refill; remove, clean and reinstall the oil
filter and magnetic drain plugs.
300 Hour Inspection
In addition to the 100 hour and appropriate 200 hour inspection items, perform the fol-
lowing:
24 3-83 Inspect the compressor case when operating in an erosive
environment.
25 3-117
If the aircraft is equipped with an engine fuel filter differential
pressure warning system, replace the throw-away filter only
when an indication of contamination is obtained or every 300
hours, whichever comes first. If the aircraft is not equipped
with a differential pressure warning system, replace the fuel
filter every 300 hours unless operating experience demon-
strates that smaller time increments are advisable.
CAUTION: When there is evidence that the fuel pump filter
has been bypassed, the gas producer fuel control filter as-
sembly must be cleaned. (Refer to Cleaning the Gas Produc-
er Fuel Control Fuel Strainer, para 3-113.)
26 3-121 Perform a fuel pump bypass valve operational check whenev-
er a fuel filter is replaced.
27 3-105 Purge air from the filter bowl area of the single element pump.

MAULE AEROSPACE TECHNOLOGY, INC.
MAINTENANCE MANUAL
FOR MX-7-420
13
Rev. A
28 3-108 Inspect and clean the fuel nozzle.
29 Item 8, Table III-10 Inspect and clean the No. 1 bearing oil pressure reducer.
30 Item 11, Table III-10 Visually inspect external sump. Clean internal carbonaceous
deposits from sump.
31 3-166 Item 10,
Table III-10 Inspect the power turbine support scavenge strut. Clean in-
ternal carbonaceous deposits from sump.
Other Scheduled Inspections
Interval Reference Inspection/Maintenance Action
500HR/1 YR
250-B 17
CSL-1030
Inspect uncoated and coated power turbine outer coupling nuts
for corrosion. Compliance with bulletins removes this require-
ment.
500 HR 3-120 Check the fuel pump driveshaft on Sundstrand single element
pumps for spline wear. NOTE: This inspection not required on
TRW pumps.
600 HR 3-89 Make an installation rotating balance of the engine and propel-
ler at intervals not to exceed 600 hours.
1500 HR 3-128 Replace fuel control strainer assembly.
1750 HR 3-83
Inspect the compressor case. Inspection frequency shall be
made as necessary by operating environment. In erosive envi-
ronment, inspect case at least every 300 hours. In any envi-
ronment, do not exceed 1750 hours without case inspection.
1750 HR 3-212A Inspect the compressor splined adapter internal splines and the
spur adapter gearshaft splines (forward and aft) for wear.
En ine Oil System Scheduled Maintenance
(Table III-10 from Allison Operations & Maintenance Manual)
No. Item Action Time Period Notes
1 Engine
lube oil Change oil
200 hr max,
or six months,
whichever
comes first
Follow procedures in Oil
Change, para 3-163. (Refer
to Approved Oils, para 1-
74.)
2 Engine oil
filter
Inspect and clean filter
element using ultrasonic
cleaner with perchloroe-
thylene.
100 hr max. Follow procedures in Oil Fil-
ter, para 3-168.

MAULE AEROSPACE TECHNOLOGY, INC.
MAINTENANCE MANUAL
FOR MX-7-420
14
Rev. A
3 Engine
lube oil
When changing from
MIL-L-7808 to MIL-L-
23699 or vice versa As necessary Refer to Approved Oils, para
1-74.
4
Pressure
oil tube
screen as-
sembly
Inspect and clean screen
using mineral spirits 100 hr max.
Refer to applicable part of
Cleaning the Power Turbine
Support Pressure Oil Noz-
zle, para -3-177.
5
Turbine
pressure
Oil System
Check
Valve
Inspect and clean 100 hr max. Oil system check valve para
3-170.
6
Oil flow
from P.T.
scavenge
passage or
external
sump and
G.P sca-
venge pas-
sage
Measure oil flow 100 hr max. Follow procedures in Oil
Flow Measurement, para 3-
178.
7 Magnetic
drain plugs Inspect and clean 100 hr max. Follow procedures in Mag-
netic Plug, para1-172.
8 No. 1 bear-
ing oil
pressure Inspect and clean 300 hr max. Follow procedures in Oil
Change, para 3-163
9
No. 6-7
and No. 8
bearing
pressure
oil nozzle
Inspect, clean internal
carbonaceous deposits.
When neces-
sary, as di-
rected by the
oil flow mea-
surement
Refer to oil flow measure-
ment, para 3-178. If an oil
flow of less than 90 cc is ob-
served from the P.T. sca-
venge passage or 75 cc
from the G.P. scavenge
passage, follow procedures
in Gas Producer and Power
Turbine Pressure Oil Mani-
fold, para 3-165 and inspec-
tion and Cleaning of Power
Turbine Support Scavenge
Oil Strut, para 3.166.
10
Power tur-
bine sup
port
scavenge
oil strut
Inspect and clean inter-
nal carbonaceous depo-
sits. 300 hr max.
Follow procedures in Inspec-
tion and Cleaning of Power
Turbine Support Scavenge
Oil Strut, para 3-166.

MAULE AEROSPACE TECHNOLOGY, INC.
MAINTENANCE MANUAL
FOR MX-7-420
15
Rev. A
11 External
sump
Visually inspect for inter-
nal carbonaceous depo-
sits. 300 hr max. Clean or replace sump as
required.
SPECIAL ENGINE INSPECTIONS
Special inspections are required when the engine has been subjected to abnormal operating
conditions, when engine damage is suspected, or when associated parts are removed from
the engine. The special occurrence, the component or system to be inspected, and the na-
ture of the inspection are given in Table III-11, Allison Operating and Maintenance Manual.
SUDDEN STOPPAGE INSPECTION
The following inspections must be satisfactorily completed whenever the propeller strikes a
moving or stationary object.
NOTE: Sudden stoppage is the momentary or complete interruption in the rotation of the
aircraft propeller and engine drive system when the aircraft propeller comes in contact with
the ground, water, trees, or other obstacles.
The shock felt by the drive system requires that the engine be inspected and/or overhauled
by a designated overhaul facility as a result of possible damage.
If the aircraft propeller strikes an object causing damage to the propeller which can be cor-
rected by light grinding or filing and normal blending of the blades (nicks, gouges, scratches,
etc.) in accordance with applicable propeller service instructions, complete the following in-
spection:
a Inspect the engine inlet for foreign objects.
b Inspect the compressor blades and vanes for foreign object damage.
c Inspect the compressor case for evidence of blade tip rub.
d Inspect all magnetic plugs for metal accumulation. (Refer to Magnetic Plug, pa-
ra 3-172 and Table III-14.)
eRotate the propeller by hand and check for unusual noise.
f Motor the engine and check for unusual noise.
g Operate the engine for 30 minutes on the ground then check the magnetic plugs
for metal accumulation.
h Check balance the propeller.

MAULE AEROSPACE TECHNOLOGY, INC.
MAINTENANCE MANUAL
FOR MX-7-420
16
Rev. A
If the aircraft propeller strikes an object causing damage to the propeller blades requiring
blade replacement and overhaul of the propeller assembly, remove the engine and send it to
a designated overhaul facility for inspection.
a Refer to the appropriate propeller Service Instructions and Overhaul Manual.
b Refer to the Special Inspections required after propeller strike and/or crash in
the engine Overhaul Manual.
HARD LANDING LIMITS.
Make a visual inspection of the installed engine for external damage from airframe compo-
nents after any hard landing. Engines that have sustained landing forces exceeding 10g
shall be sent to an overhaul facility.
COMPRESSOR INLET AIR BLOCKAGE.
Replace the compressor assembly if the engine has been operated with inlet air restricted
due to foreign objects or materials which have become lodged in the compressor inlets. Tag
the replaced compressor to show that the cause of removal was inlet air blockage. Condi-
tions which constitute blockage are as follows:
a
Foreign objects or materials found in the inlet during inspection of the aircraft
when not in operation. If it can be determined that the blockage was not there
during the last operation of the engine, remove the foreign object or material
and leave the compressor in service.
b
Power loss encountered following a restriction at the compressor inlet area
while the engine is in operation. Blockage in flight can usually be verified by
inspection after landing (blockage still exists). However, some blockage may
be followed by ingestion before inspection can take place. Objects or mate-
rials which were large enough to have stopped at the inlet guide vanes before
ingestion, or which cause a noticeable raise in TOT, can be considered to have
caused compressor inlet blockage.

MAULE AEROSPACE TECHNOLOGY, INC.
MAINTENANCE MANUAL
FOR MX-7-420
17
Rev. A
RIGGING PROCEDURES
1. LEVELING:
Laterally: The airplane can be accurately leveled laterally using the front spar attach
bolts. Turn these two bolts so that a flat on the head is "up". Fabricate two
equal length spacers (1½ inch minimum length) which can be placed on the
bolt heads. Place a 48 inch level across the two spacers and block under the
landing gear to center the bubble.
Longitudinally: Using a level thirty-six (36) inches long or longer, place it on the leveling
lug and leveling mark thirty-one (31) inches to the rear of the leveling lug
on the bottom of the right wing root. Raise the tail to bring bubble to cen-
ter.
2. DIHEDRAL ANGLE:
To check dihedral angle at the front spar, remove both top wing root fairings to ex-
pose the front spar attach bolts. Stretch a string along the top of the wing above the
front spar, from wingtip to wingtip, and draw it tight. The end of the string can be at-
tached to tie down fittings underneath the wing to hold tautness. Be careful to protect the
edges of the wingtips from string chafing.
Find the row of flush rivets on the top of each wing from wingtip to wingtip at the front
spar location. Measure from the forward wing to fuselage attach bolt centerline, for both
left and right wings, outboard 127.5 inches along the top of each front wing spar. Using
masking tape or equivalent, tape the string down on the rivet centerline at this point.
At the inboard end of the front spar, measure the distance from the top rear edge of
the spar cap to the string on both wings. Adjust the front wing struts so as to have a
measurement of 2 3/4 inches on each wing (plus or minus 1/8 inch) at this location. It is
recommended that the rear struts be removed while adjusting dihedral. The wing must
be supported while the front strut is being adjusted. For rear strut adjustment, see sec-
tion on Washout.
CAUTION: Be sure that the strut fork is not extended more than 1 inch of threads from
the strut end to the end of the fork threads (not including the jam nut). There must be at
least 1 3/8 inch of thread engagement into the strut.
3. WASHOUT:
To adjust the washout in the wings, proceed as follows:
Put a leveling protractor chordwise on the underside of the wing root and adjust it to
a zero degree reading. Now put the protractor chordwise just inboard of the wing tip
and adjust the rear strut to give ½°trailing edge up, difference from the wing root angle.
Table of contents
Other MAULE Tools manuals
Popular Tools manuals by other brands
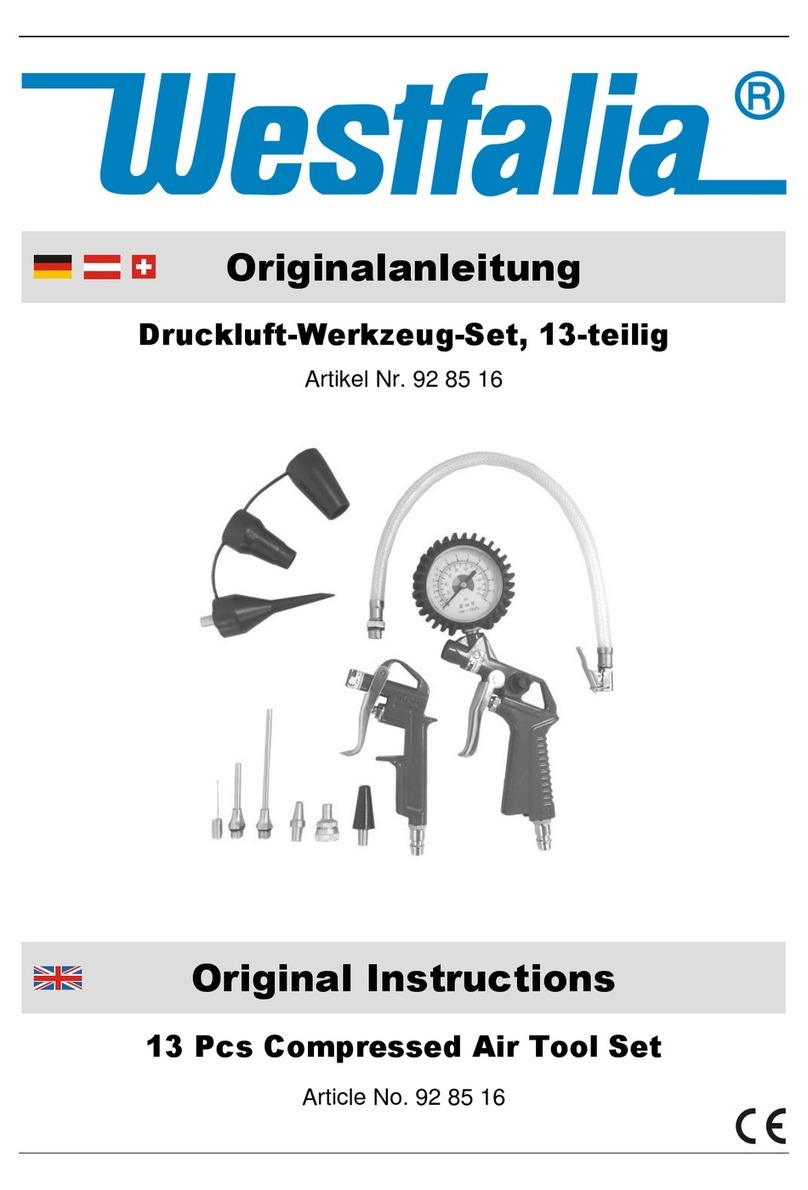
Westfalia
Westfalia 85 92 78 Original instructions
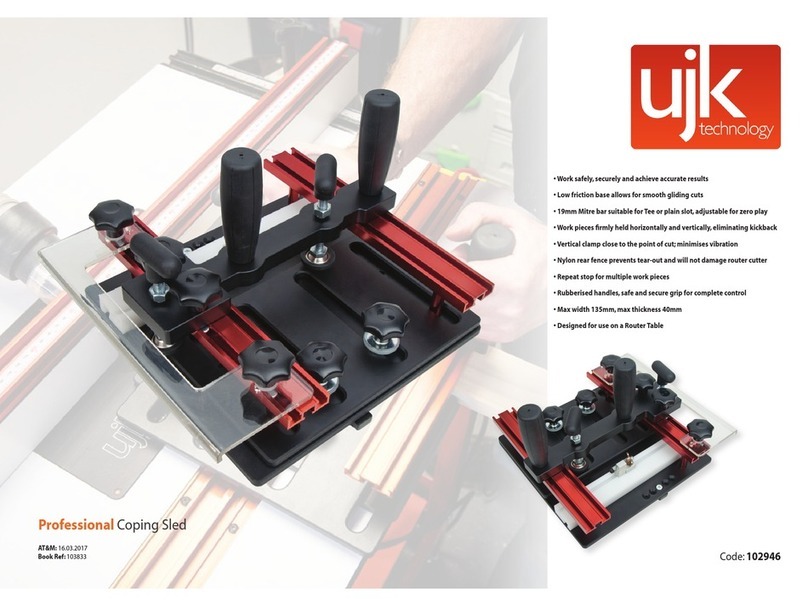
ujk technology
ujk technology 102946 manual

BIAX
BIAX RO 1785 Translation of the original operating manual
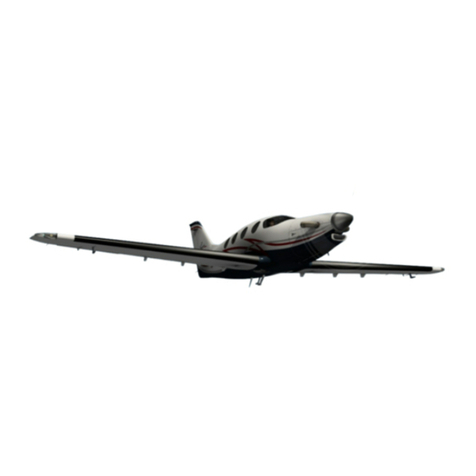
AEROBASK
AEROBASK EPIC E1000 owner's manual
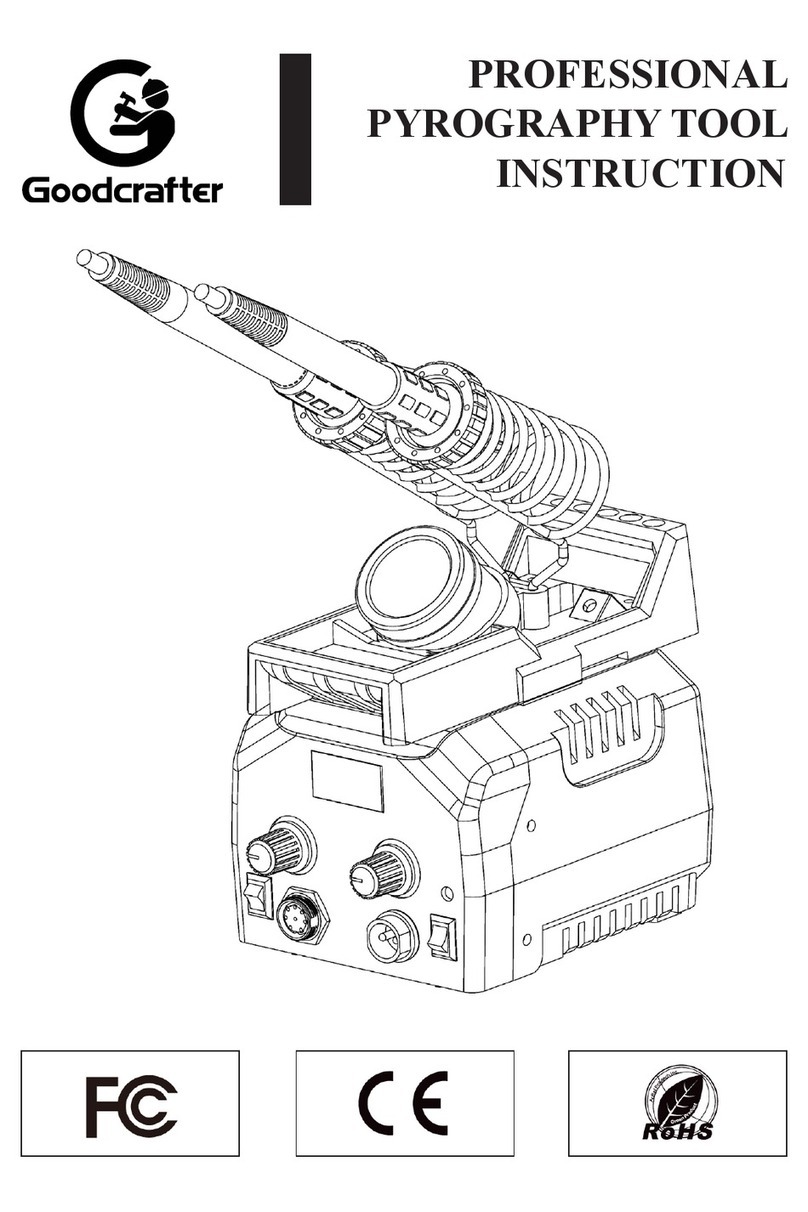
Goodcrafter
Goodcrafter 939D II instructions
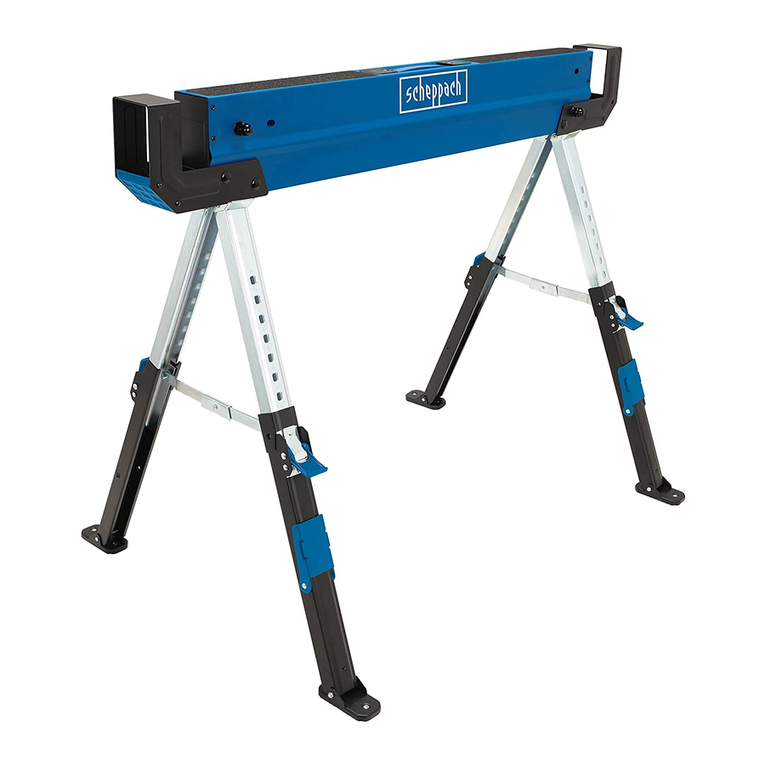
Scheppach
Scheppach MWB600 Translation of original operating manual