Moore Industries DCA S User manual

DCA
Direct Current Alarm
USER’S MANUAL
May 2016
No. 192-701-00 K
© 2012 by Moore Industries-International, Inc.

Moore Industries’ STAR Center has a
wide variety of quality instrumentation
in stock and ready to ship.
• Signal Transmitters
• Temperature Transmitters
• P/I and I/P Converters
• Isolators and Converters
• Indicators and Displays
• Alarm Trips
• Integrators and Totalizers
• Power Transducers
• Instrument Power Supplies
• Racks, Rails and Enclosures
Most instruments can be customized
to meet your needs. Even then, you’ll
never have to wait more than a few days.
*Support,TechnicalAssistance,andRepair(ourQuick-ShipFacility)
Moore Industries
CENTER
United States/Canada
TOLL FREE
1-800-999-2900
United Kingdom
FREE PHONE
0800 525107
Australia
TOLL FREE
008 251928
16650 Schoenborn Street
Sepulveda, California 91343, U.S.A.
Tel: (818) 894-7111 • Tlx: 65-1322
FAX: (818) 891-2816
CONNECT (MacNet): MIISEPULVEDA
3/18 Resolution Drive, Caringbah
New South Wales 2229, Australia
Tel: (02) 525-9177 • Tlx: 790-75914
FAX: (02) 525-7296
1 Lloyds Court, Manor Royal, Crawley
W. Sussex RH10-2QU, United Kingdom
Tel: 0293 514488 • Tlx: 87667
FAX: 0293 536852
Ask for the STAR Center
*
DELIVERY
48
HR.
Table of Contents
Introduction 1
Description 1
Calibration 4
Installation 19
Maintenance 22

DCA
Page 1
Introduction
Moore Industries’ Direct Current Alarm (DCA) is a
highly versatile, fully adjustable device that is factory-
configured to accept either current or voltage input.
The unit’s internal relays are tripped when input
deviates from a customer-set “safe” range defined by
adjustable trip points. The DCA is ideal for use in an
alarm system, where it may be used to activate a
warning device, or to drive an analog indicator.
This manual provides a brief description of the DCA,
including its physical characteristics and options; a
table of performance and operating specifications; a
set of procedures for calibrating the unit; instructions
for installation, including physical mounting and
electrical connections; and finally, information on
basic maintenance and troubleshooting.
Notes, Cautions, and Warnings are included as a
means of identifying those practices that may present
unnecessary inconveniences (notes), result in dam-
age to the unit (cautions), or cause injury (warnings).
Description
The DCA comes in either Moore Industries’ standard
(STD) or plug-in card (PC) housing.
The STD unit can be used with a variety of mounting
options, including those suitable for use with explo-
sion-proof and NEMA enclosures.
PC-style DCA’s are designed for use with Moore
Industries’ multi-position card racks; the surface
mounted SMR, or the rack mounted RMR.
Both STD and PC DCA’s are available with either
single or dual alarm configurations. The relays used
are single-pole/double-throw, form C. There are a
number of input ranges and alternate relay ratings
available.
Operationally, the unit can be ordered with any com-
bination of single, dual, high, low, fail-safe, or non-fail-
safe alarm relays. The following paragraphs describe
each of these configurations.
High Alarm/Low Alarm. A DCA configured as a high
alarm is tripped when the input increases, and
reaches a customer-set trip point. A low alarm unit is
tripped by a decreasing input that drops below a
customer-set trip point.
Figure 1 illustrates the concept.
Fail-safe/Non-fail-safe. A fail-safe unit’s relay is
energized when input is within a “safe” range, i.e. is
normal, or not in an alarm condition. When the input
goes into an alarm condition, reaching a trip point or
losing power, the relay of a fail-safe DCA is de-
energized.
Conversely, a non-fail-safe unit’s relay is de-energized
when input is within the customer-specified “safe”
range, and is energized when the input reaches the
trip point setting.
Figure 1 also depicts the action of fail-safe relays.
Controls and Indicators
Every type and configuration of DCA comes with
potentiometers (pots) to set the alarm trip points of
each installed relay. Additional pots for controlling
unit dead band are available as an option, and preci-
sion ten-turn vernier scales can be used instead of
the standard pots.
Trip point pots afford full 0- to 100-percent adjustabil-
ity over the unit’s specified span.
Each installed relay is wired to a front panel LED,
which lights when the relay is energized. Depending
upon the type of relay ordered, i.e. fail-safe/non-fail-
safe, a lit LED can indicate either an “alarm” or a “non-
alarm” input condition.
Table 1 summarizes the alarm type/LED status
options for the available types of DCA.

DCA
Page 2
Figure 1. High - and Low-alarm Relay Configurations
Table 1. DCA Alarm Types
NOTES: 1. Older DCA’s may use X1 for H1, X2 for H2, X3 for L1, and X4 for L2.
2. The “UPPER” and “LOWER” labeling on the DCA front panel is for reference only.
Configurations where “LOWER” terminals and pots pertain to the unit’s high alarm, for
example, are quite possible.
3. Relays in fail-safe alarms are DE-energized in the event of power loss to the unit.
Model Number
Designator This Unit is... This Unit signals an
“Alarm” condition when... Its LED will be... Relay(s)
S Single Alarm - - Only one relay installed
D Dual Alarm - - Two relays are installed
H1 High Fail-Safe Input increases, and exceeds
Trip Point. (See Note 2).
OFF in alarm
ON in Non-alarm
DE-energized in alarm
Energized in Non-alarm
H2 High NON-Fail-Safe Input increases, and exceeds
Trip Point. (See Note 2).
ON in Alarm,
OFF in Non-alarm
Energized in Alarm,
DE-energized in Non-alarm
L1 Low Fail-Safe Input decreases, and drops
below Trip Point
(See Note 2)
OFF in alarm
ON in Non-alarm
DE-energized in alarm
Energized in Non-alarm
L2 Low NON-Fail-Safe Input decreases, and drops
below Trip Point
(See Note 2)
ON in Alarm,
OFF in Non-alarm
Energized in Alarm,
DE-energized in Non-alarm
FAIL-SAFE RELAY ENERGIZED, LED ON
FAIL-SAFE RELAY DE-ENERGIZED, LED OFF
TIME
TRIP POINT
RESET
LOW-ALARM DCA
100 %
0 %
DEAD BAND
ANALOG
INPUT
VALUE
TRIP POINT
RESET
TIME
HIGH-ALARM DCA
100 %
0 %
DEAD BAND
ANALOG
INPUT
VALUE

DCA
Page 3
Table 2 lists the performance and operational specifi-
cations for the unit. Options
Each DCA is configured according to customer
requirements. The paragraphs on the following pages
highlight some of the options available.
Table 2. DCA Performance and Operational Specifications
Characteristic
Input
Output
Power
Performance
Environmental
Ratings
Specifications
Current: 1-5 mA @ 200Ωnominal input impedance
4-20 mA @ 50Ωnominal input impedance
10-50 mA @ 20Ωnominal input impedance
Selectable Current (SC) comes with three load resistors for selecting1-5, 4-20, or
10-50 mA (See Note 1)
Voltage: 0.25-1.25 V @ 1MΩ, minimum (See Note 2)
1-5 V @ 1MΩ, minimum
Consult factory for dual input and special range options.
Factory-configured with one (Single DCA) or two (Dual DCA) single pole/double throw
(SPDT), form C, mechanical relays rated for 5 A @ 117 Vac non-inductive, or 28 Vdc.
User selects Normally Open (NO), Normally Closed (NC), or any combination of NO/NC
configurations during installation. Fail-safe/Non-fail-safe configuration factory-set. Refer to
table 1 for available combinations.
Double pole/double throw (DPDT), form 2C and 7.5 A relays available as options.
(See Note 3)
24 or 45 Vdc ±10%, 5 watts nominal
100, 117, 200, 220, or 240 Vac ±10%, 50/60 Hz
AC power inputs not available with PC-style housing
Repeatability: Trip point settings repeat within ±0.1% of span.
Dead Band: 1% of span, standard. Adjustable Dead Band Option available.
Alarm Response: 50 milliseconds for step change of 1% of span.
Line Voltage Effect: ±0.005% per 1% line voltage change (ac or dc).
Isolation: No galvanic path between input, output, and power.
Accuracy: Front panel potentiometers capable of setting trip points from 0 to 100% of
span. Lockable, scaled vernier dials optional.
Effect of Ambient Temperature on Performance: Less than ±0.018% per °C through the
specified range (Less than ±0.01% per °F)
Ambient Operating Temperature: –18 to 65 °C (0 to 150 °F)
NOTES: 1. One of the available resistors MUST be installed.
2. Requires extra engineering when used with some option combinations.
3. DPDT not available with some enclosures and option combinations.

DCA
Page 4
For a complete list of available options, and for
information on other housings, mounting hardware,
and enclosures, contact your Moore Industries Sales
Representative.
AD Option —
Externally-adjustable Dead Band.
Front panel potentiometers vary dead band 1- to 20-
percent of span (nominal), 1- to 50-percent of span
(AD50), or 1- to 100-percent (AD100) of span. (AD
Option not available with some option combinations).
AR Option —
Response Time Delay. Set by the
factory for output delays of 1 to 5, 10, 15, 20, 25, or
30 seconds, according to customer specification.
DA Option —
Deviation Input. Unit signals alarm
condition when the difference between two inputs
exceeds adjustable percent of full span. Requires DI
Option or 2X input. (Not available with some option
combinations.)
DI Option —
Dual Input. Configures dual-alarm DCA
to operate as two, single-alarm units. Standard DI
unit provides a high alarm for one input and a low
alarm for the other. (DI Option not available with
some option combinations).
DPDT Option —
Double Pole, Double Throw/Form 2C
Relays. Contact 5 amps at 28 Vdc, or 117 Vac non-
inductive. (DPDT Option not available with some
option combinations).
FU Option
— Power Fuse. 400 mA rated fuse on
PC-style unit. Use of the FU Option with the STD
housing requires special engineering.
HS Option
— Hermetically Sealed Relays. Rated 1A
@ 117 Vac non-inductive, 2A @ 28 Vdc. Meets
requirements for installation in Class I, Division 2
locations.
MR Option —
Manual Reset. External reset push
button for single- and dual-alarm units. In place of
dead band, MR-equipped units return to normal only
when the process input returns to non-alarm state
and
the external reset push button is pressed.
TT Option —
Lockable Vernier Dial. Front panel,
multiturn potentiometers for setting and locking trip
points. Includes front panel ZERO potentiometer for
appropriate offsets.
TX Option
— Two-wire Transmitter Excitation. Rated
at 30 Vdc @ 25 mA.
7.5A Option —
7.5 amp Relay(s). Rated by CSA and
UL at 7.5 amps, 28 Vdc or 120 Vac.
Model/Serial Number. Moore Industries uses a
system of unit model and serial numbers to keep
track of factory configuration and options for each
DCA shipped and serviced.
The example outlines the significance of each field of
information in a typical DCA model number. Refer to
table 1 for an explanation of the relay configuration
codes used.
If service information or assistance for a DCA is
needed, make a note of the unit’s model and serial
number before contacting Moore Industries’ Customer
Service Department. Our highly skilled technicians
will be happy to assist you.
STD units’ serial and model numbers are located on
an L-shaped metal tag at the top of the connection
terminal strips. On PC DCA’s, the numbers are
located on an adhesive label affixed to the side of the
front panel.
Calibration
Every DCA shipped from the factory is manufactured
and tested according to Moore Industries’ exacting
standards for product quality. A bench check of basic
unit operations is recommended, however, in order to
identify any damage to the unit that may have oc-
curred during shipping. This also allows the user to
effect operational adjustments to trip point settings
and unit dead band, if available.
It is recommended that the procedures in this section
be carried out at a technician’s bench or in a similar
lab environment. This is the safest means of making
adjustments to trip point values; isolated from the
intended DCA application.
The calibration of the DCA consists basically of
setting trip points and dead bands based on the
resistance across the unit contact-closure terminals
as measured by an ohmmeter. With relay contacts
closed, resistance is negligible. With relay contacts
open, resistance is infinite.

DCA
Page 5
Equipment Specifications
Voltage
or
Current Source
Calibrated, adjustable unit, capable of output at discrete levels in the
appropriate range, with the rated impedance for the unit being calibrated.
EDC Models MV105, MV155, or equivalent.
Power Source AC or dc power input appropriate for the type of DCA being calibrated.
Refer to table 2, earlier in this manual.
Ohmmeter Accuracy of ±1%, minimum.
Screwdriver Slotted-tip with head width no greater than 2.54 mm (0.01 in).
Wire Jumpers
(required for
AR-equipped
DCA’s ONLY)
Temporary jumper wiring suitable for shorting AR Option diodes so that the
alarm delay may be defeated while adjusting the unit’s trip point settings.
Extender Card
(optional for use
with PC-style
DCA’s ONLY)
Moore Industries’ part number 350-513-00.
Unit Type
Input
Relay Configuration
Power
Options(s)
Housing
DCA / 4-20MA / DH1L1 / 117AC / -AD [STD]
EXAMPLE
Basic Calibration Setup
The equipment listed in table 3 is needed for calibrat-
ing the DCA. These items are not supplied with the
unit, but should be available in most testing labs.
Be sure to use calibrated test equipment when
performing the bench check and calibration of the
DCA. The use of inaccurate test equipment may
result in unreliable settings for the unit’s trip point(s),
etc.
Table 3. DCA Calibration Equipment
Voltage or
Current Source

DCA
Page 6
Setup for the STD DCA. Figure 2 shows the labeling
used on the front panel of the STD DCA. Figure 3
shows the terminals on a unit equipped with DPDT
relays.
To access the connection terminals for a DCA in the
basic extruded housing (STD, AB, etc.), use a screw
driver to remove the securing screw from the protec-
tive plastic cover on the unit front panel. With the
screw removed, the cover can be removed by hand,
revealing the terminals and the labels depicted in the
illustrations in this manual.
Figure 2. STD DCA Terminal Locations
NOTES: 1. Each unit is factor y-configured for ac or dc power.
2. Each unit is factor y-configured for specific current or voltage input.
+IN — CURRENT OR VOLTAGE +INPUT
UPPER RELAY NORMALLY
CLOSED — UNC
UPPER RELAY NORMALLY
OPEN — UNO
COMMON — COM
LNO —
LOW ER RELAY NORMALLY OPEN
COM — COMMON
LNC —
LOWER RELAY NORMALLY CLOSED
ACC — –DC
AC — +DC
GND
OPTION — +TX FOR TRANSMITTER
EXCITATION, +REF FOR DEVIATION ALARM
-IN — CURRENT OR VOLTAGE -INPUT
UPPER LOW ER
CDC URRENT
ALARM
D EAD BAN D
LOWER
U PPER
ZERO
DCA

DCA
Page 7
Figure 3. STD DCA w/DPDT Option Terminal Locations
WARNING
To guard against accidental electric
shock, it is recommended that the protec-
tive plastic cover be re-installed over the
terminal strip of the STD DCA before
applying power to the calibration setup.
Figure 4 shows the labeling for a STD DCA equipped
with the DI Option. Note that both inputs share the “–
IN” terminal.
UPPER RELAY #1 NORMALLY
CLOSED — UNC1
+IN — CURRENT
OR VOLTAGE +INPUT
-IN — CURRENT
OR VOLTAGE -INPUT
LNO1 — LOWER RELAY #1
NORMALLY OPEN
COM — COMMON
LNC1 — LOWER RELAY #1
NORMALLY CLOSED
LNO2 — LOWER RELAY #2
NORMALLY OPEN
COM — COMMON
LNC2 — LOWER RELAY #2
NORMALLY CLOSED
UNO2 — UPPER RELAY #2
NORMALLY OPEN
COM — COMMON
UNO2 — UPPER RELAY
#2 NORMALLY CLOSED
UPPER LOW ER
DC CURRENT
ALARM
D EAD BAN D
LOWER
U PPER
ZERO
COMMON — COM
ACC — –DC
AC — +DC
GND
UPPER RELAY #1 NORMALLY
OPEN — UNO1
OPTION — +TX FOR
TRANSMITTER EXCITATION,
+REF FOR DEVIATION ALARM
DCA

DCA
Page 8
Setup for the PC DCA. There are two methods of
carrying out the calibration setup connections on the
PC DCA. Most often the unit is installed in one of
Moore Industries’ card racks, and the calibration
equipment is connected to the appropriate rack
terminal strip.
Figure 5 illustrates the PC DCA installed in the
surface mounted card rack, the SMR. Figure 6 shows
the terminal strip labeling for rack units when the DCA
is equipped with the DI Option.
As an alternative to using the card rack, individual PC
DCA’s can be checked with Moore Industries’ Pro-
cess Power Supply, the PPS, equipped with its CT
Option. The CT-equipped PPS accepts the connec-
tion strip of the PC DCA in a connector built into its
side panel. The PPS front panel provides access to
terminal strips similar to those used on the card
racks.
Whether using the card rack or the PPS/CT combina-
tion, note that the DC power connections are not
made directly to the unit, but to the terminal strips of
either the card rack or the PPS. DC power is supplied
to the DCA at its pins 8 and 9
NOTE
The “UPPER” and “LOWER” labeling used
on the DCA is for reference purposes only.
The trip point pots allow for adjustments through 100-
percent of span. It is therefore possible for the
connections to the “LOWER” labeled alarm section to
be configured as a “high alarm”, and the “UPPER”
section to be configured as a “low alarm”.
NOTE
The LED’s DO NOT always indicate an
alarm condition; rather, they light to show
that their complimentary relay is ener-
gized. It is possible for a DCA to be
configured such that the LED’s are lit
when input is in a “non-alarm” state.
Figure 4. STD DCA with DI Option Terminal Locations
LNO —
LOWER RELAY NORMALLY OPEN
LNC —
LOWER RELAY NORMALLY CLOSED
+IN LOW — LOW ER
CURRENT/VOLTAGE +INPUT
-IN — NEGATIVE INPUT
+IN UP — UPPER
CURRENT/VOLTAGE +INPUT
COM — COMMON
ACC — –DC
AC — +DC
GND

DCA
Page 9
Figure 5. Terminals Labeling, the PC DCA in the SMR
INTERNAL RACK SLOT
AND CONNECTOR
MOUNTING
FLANGES
PC DCA
1
15
7LNO - LOWER RELAY NORMALLY OPEN
4LNC - LOWER RELAY NORMALLY CLOSED
2
5
3+IN — CURRENT OR VOLTAGE + INPUT
10 -IN — CURRENT OR VOLTAGE - INPUT
13
1
15 COM - COMMON
UNC - UPPER RELAY NORMALLY CLOSED
COM - COMMON
UNO - UPPER RELAY NORMALLY OPEN
ONE TERMINAL
STRIP PER
CARD POSITION
NOTES :
Power is not applied to each PC connector strip, but to the r ack term inal strip.
Power is supplied to the PC DCA at its pins 8 (-DC) and 9 (+DC).
Rack is shown with protective cover s removed.1.
2.
SMR
PC DCA
COMPONENT SIDE
-DC
+DC
GND
ONE POWER
CONNECTION
PER RACK
OPTION — +TX, +REF

DCA
Page 10
Figure 6. PC DCA with DI Option Terminal Locations
Setup of DCA’s in Explosion-proof Enclosures.
The DCA in an explosion-proof enclosure (EX) in-
corporates a modification of the STD housing where
the connection terminals are replaced with pins on the
unit bottom panel. These pins are inserted in a
terminal block permanently mounted inside the base
of the explosion-proof enclosure.
To effect the calibration connections, unscrew the top
of the enclosure and pull the DCA up and out of the
enclosure base, exposing the terminal block. Figure 7
shows the block and its labeling. Figure 8 shows the
labeling used for units equipped with the DI Option.
Use the appropriate terminal locations figure to
connect the calibration equipment to the terminal
block in the enclosure base. Then re-connect the
DCA by aligning the pins on the bottom of the unit
housing with the holes in the terminal block. Press
down until the unit is seated firmly in the enclosure
base.
CAUTION
The EX DCA housing fits into the terminal
block in its correct orientation only. Note
the position of the connection “key”.
Attempting to “force” the unit in when the
pins are not aligned with the correct holes
will bend the pins.
Basic Calibration Hookup. Use the terminal loca-
tions figure that is appropriate for the type of DCA
being checked, and connect the equipment described
in the calibration equipment table as shown in the
calibration hookup diagram, figure 9.
Set all low alarm pots fully counterclockwise. DCA
pots are equipped with slip clutches to prevent
damage in the event of over-turning. A slight change
in torque may be felt when a wiper stop is reached. If
unable to sense the stop, set pot 15 turns counter-
clockwise.
7LNO - LOWER RELAY NORMALLY OPEN
4LNC - LOWER RELAY NORMALLY CLOSED
2
5
3+IN — LOWER ALARM CURRENT OR VOLTAGE + INPUT
10 -IN — CURRENT OR VOLTAGE - INPUT
13
1
15 COM - COMMON
UNC - UPPER RELAY NORMALLY CLOSED
COM - COMMON
+IN — UPPER ALARM CURENT OR VOLTAGE +INPUT
UNO - UPPER RELAY NORMALLY OPEN
ONE TERMINAL
STRIP PER
CARD POSITION

DCA
Page 11
Figure 7. DCA in an Explosion-proof Enclosure Terminal Locations
Figure 8. DCA with DI Option in an Explosion-proof Enclosure Terminal Locations
7
8
9
10
11
12
6
5
4
3
2
1
`
GND
+DC — AC
–DC — ACC
UNC — UPPER RELAY
NORMALLY CLOSED
COM — COMMON
UNO — UPPER RELAY
NORMALLY OPEN
LOWER RELAY
NORMALLY OPEN — LNO
COMMON — COM
LOWER RELAY
NORMALLY CLOSED — LNC
CURRENT OR VOLTAGE
+INPUT — +IN
CURRENT OR VOLTAGE
-INPUT — -IN
OPTION — +TX FOR TRANSMITTER
EXCITATION, +REF FOR DEVIATION ALARM
7
8
9
10
11
12
6
5
4
3
2
1
GND
+DC — AC
–DC — ACC
UNC — UPPER RELAY
NORMALLY CLOSED
COM — COMMON
UNO — UPPER RELAY
NORMALLY OPEN
LOWER RELAY
NORMALLY OPEN — LNO
COMMON — COM
LOWER RELAY
NORMALLY CLOSED — LNC
CURRENT OR VOLTAGE
-INPUT — -IN
UPPER ALARM CURRENT OR
VOLTAGE +INPUT — +IN UPP
LOWER ALARM CURRENT OR
VOLTAGE -INPUT — +IN LOW

DCA
Page 12
APPROPRIATE
CALIBRATED
ADJUSTABLE
CURRENT
OR
VOLTAGE SOURCE
+
(SEE NOTE 1)
DCA
+IN
–IN
VDC or VAC
POWER SOURCE
+–
+–
NOTES: Check unit model number for appr opiate input source.
Check unit model number for appropr iate power source.
X = U for upper or L for lower. Connect ohmm eter to "NO" for terminals of norm ally open relay, to
NC for normally closed. “#” is used in DPDT-equipped units to refer to the number of the alarm
output, as in UNO1 and LNC2.
1.
2.
3.
(SEE NOTE 2)
COM
XNO#
XNC#
OHMMETER
(SEE NOTE 3)
–
Figure 9. The DCA Calibration Setup
Special Considerations for AR-equipped DCA’s.
Units equipped with the AR Option are factory-set for
specific alarm delay times ranging from 1 to 30
seconds (refer to Options listing). The AR is set and
fully calibrated according to customer requirements
before unit shipment.
The delay in an AR-equipped DCA’s transition from
normal to alarm condition makes the calibration of trip
points difficult, and a temporary disabling of the option
is therefore recommended during the calibration
procedures.
To defeat the AR Option, diodes on PC1 of the DCA
must be shorted. There is a diode for each installed
relay.
DCA’s in the STD housing must be partially disas-
sembled to access the AR diode(s). See figure10.
Figures 11 and 12 show the location of the diodes on
the various types of AR-equipped DCA.
Access to the AR diode(s) on PC-style DCA’s may be
difficult if the unit being calibrated is already installed
in its rack. Moore Industries offers an Extender Card
accessory for calibrating units under these circum-
stances.
The Extender, P/N 350-513-00, mates with the
connector on the PC-style DCA, and then plugs in to
the rack so that the unit is clear of the rack front,
allowing for access to the diode(s).
Calibration Procedures
Before beginning the actual calibration of the DCA,
check the unit’s model number to verify that the
correct power supply and input simulator is being
used. Make sure that the appropriate connections are
made as shown in the figures of the preceding
section.
Using the Calibration Procedures. The Calibration
Procedures section is divided into subsections that
describe first low alarm, then high alarm trip point
setting. The procedure for calibrating the DCA dead
band, for units equipped with the AD Option, should
be conducted after the trip points are set.
If the DCA to be calibrated is equipped with the TT
Option, skip to and complete the procedure in the
section entitled “Calibrating DCA’s Equipped with the
TT Option”.

DCA
Page 13
Figure 10. STD DCA Disassembly
RELAY RELAY
FOR SINGLE-ALARM
PC DCA SHORT AROUND
THIS DIODE
CONNECTOR
PINS
FRONT PANEL
FOR DUAL-ALARM
PC DCA SHORT AROUND
THESE DIODES
Figure 11. AR Option Diodes on the PC DCA

DCA
Page 14
Setting Low-Alarm Trip Points. Remember that the
“UPPER” and “LOWER” labeling on the DCA is for
reference purposes only. The DCA can be ordered
without low alarms, as in a “high/high” configuration.
Dual alarm units can be ordered with either one or
both relays configured as low alarms, and DPDT-
equipped DCA’s may be configured with any combina-
tion of high/low alarms.
Refer to the unit’s model number to determine the
alarm configuration, and perform the following proce-
dure for each installed low alarm.
1. Check model number to verify correct power
input, and apply 117 or 240 Vac; 24 or 45 Vdc, as
appropriate.
2. Make sure that ohmmeter in calibration setup is
connected to appropriate -NO or -NC terminals, as
desired.
3. Apply 100% of application’s input span (current or
voltage, as appropriate) to DCA.
If low alarm is configured as fail-safe, L1 in model
number, verify that appropriate LED for that alarm
is lit. LED for non-fail-safe low alarm, L2 in model
number, will not be lit.
4. Note ohmmeter reading.
In a low alarm, 100% input is a non-alarm condi-
tion. If connected to
X
NO and COM terminals (
X
= U or L, UPP or LOW; NO = normally open),
Resistance across the terminals in a fail-safe
alarm is zero. In a non-fail-safe alarm resis-
tance will be near infinite.
If connected to
X
NC and COM terminals, resis-
tance is infinite in fail-safe, zero in non-fail-safe
alarms.
RELAY RELAY FOR SINGLE ALARM
STD DCA SHORT
AROUND THIS DIODE
FOR DUAL ALARM STD
DCA SHORT AROUND
THESE DIODES
PC2
PC1
LED’S
Figure 12. AR Option Diodes on PC1 of the STD DCA

DCA
Page 15
5. Set input to desired low alarm trip point level.
6. Turn appropriate low alarm adjustment pot (may
be labeled “UPPER” or “LOWER”) slowly clock-
wise. Observe LED and ohmmeter, and stop
turning at exact point where relay changes state.
Vary pot setting slightly above and below trip
point to “zero in” on exact setting.
If low alarm is configured as fail-safe, L1 in model
number, verify that appropriate LED for low alarm
is not lit. LED for non-fail-safe low alarm, L2 in
model number, will be lit.
7. Verify desired setting by varying input above and
below trip point level (from step 6) and observing
both LED and ohmmeter to confirm change of
relay state at, and below trip point setting.
NOTE
Units equipped with any Manual Reset
Option have external push buttons that
must be pressed to reset the relays once
they have been tripped.
Setting High-Alarm Trip Points. Remember that the
“UPPER” and “LOWER” labeling on the DCA is for
reference purposes only. The DCA can be ordered
without high alarms, as in a “low/low” configuration.
Dual alarm units, on the other hand, can be ordered
with either one or both relays configured as high
alarms.
Refer to the unit’s model number to determine the
alarm configuration, and perform the following proce-
dure for each installed high alarm.
1. Check model number to verify correct power
input, and apply 117 or 240 Vac; 24 or 45 Vdc, as
appropriate.
2. Make sure that ohmmeter in calibration setup is
connected to appropriate -NO or -NC terminals, as
desired.
3. Apply 0% of application’s input span (current or
voltage, as appropriate) to DCA.
If high alarm is configured as fail-safe, H1 in
model number, verify that appropriate LED for that
alarm is lit. LED for non-fail-safe low alarm, H2 in
model number, will not be lit.
4. Note ohmmeter reading.
In a high alarm, 0% input is a non-alarm condi-
tion. If connected to
X
NO and COM terminals
(
X
= U or L, UPP or LOW; NO = normally open),
Resistance across the terminals in a fail-safe
alarm is zero. In a non-fail-safe alarm resis-
tance will be near infinite.
If connected to
X
NC and COM terminals, resis-
tance is infinite in fail-safe, zero in non-fail-safe
alarms.
5. Set input to desired high alarm trip point level.
6. Turn appropriate high alarm adjustment pot (may
be labeled “UPPER” or “LOWER”) slowly clock-
wise. Observe LED and ohmmeter, and stop
turning at exact point where relay changes state.
Vary pot setting slightly above and below trip
point to “zero in” on exact setting.
If high alarm is configured as fail-safe, H1 in
model number, verify that appropriate LED for that
alarm is not lit. LED for non-fail-safe high alarm,
H2 in model number, will be lit.
7. Verify desired setting by varying input above and
below trip point level (from step 6) and observing
both LED and ohmmeter to confirm change of
relay state at, or above trip point setting.
NOTE
Units equipped with any Manual Reset
Option have external push buttons that
must be pressed to reset the relays once
they have been tripped.

DCA
Page 16
Setting the Dead Band. See figure 1 for a graphic
representation of the DCA dead band. The dead band
may be thought of as an “area” around a trip point in
which the alarm will not reset.
In a scenario using a high-alarm DCA as an example,
the unit will signal an alarm at its trip point, and will
continue to signal an alarm as long as the input is
above that point.
Without an adjustable dead band, the relay will reset
when the input drops below the trip point. When
equipped with the AD Option, however, no reset will
occur until the input continues to drop to the dead
band setting, presumably some percentage of span
below the trip point.
To set the DCA dead band:
1. Make sure dead band pots are turned fully
counterclockwise. Set trip points for installed
alarms as described in preceding section. Con-
nect ohmmeter to UPPER alarm section to set
UPPER dead band, or to LOWER section for
setting LOWER dead band.
2. Apply input at the dead band setting level.
Typically, this will be lower than trip point for high
alarms, or higher than trip point for low alarms.
3. Turn appropriate dead band pot slowly clockwise,
observing LED and ohmmeter.
4. Set pot (stop turning) at exact point at which relay
changes state.
5. Verify desired setting by varying input above and
below trip point, observing both LED and ohmme-
ter to confirm appropriate change of relay state.
Unit will “trip” at trip point setting, and will not
reset until input returns past dead band setting.
The DCA dead band can be expressed as a percent-
age of the unit’s factory-configured span.
For Example
:
A single, high-alarm DCA rated for 4-20 mA input is
required to have a 25% dead band around its 14 mA
trip point setting. To calculate the input level needed
to set the desired dead band, subtract 25% of 16 mA
(span) from 14 mA:
Trip point setting in mA = 14
– 25% of input span in mA = 16(0.25)
14 – 4 = 10
The result, 10 mA, is the level of input to be applied in
step 2. The DCA in this example will signal an alarm
condition when the input reaches or exceeds 14 mA,
but will not reset until the input drops below 10 mA.
Calibrating TT-equipped Units. Lockable, multiturn
trip point adjustment pots on the front panel of each
TT-equipped DCA are set at the factory so that “0.00”
on the dial is equal to 0% of the application’s rated
input span. “10.00” is equal to 100% of span. The
accuracy of these settings is ±0.5% of the rated
span.
Calibration of DCA’s with this option consists of two
procedures. First, the internal, Full-Scale Adjust
(FSA) potentiometer(s) must be set (this involves
some disassembly of the STD DCA). Then, the unit
zero, trip points, and dead band (if so-equipped), must
be set.
Figure 13 shows the location of the STD DCA FSA
potentiometers. Figure 14 shows the location of the
pots on the PC-style unit. Refer to figure 10 when
disassembling the unit in STD housing, and refer to
figures 13 or 14 while executing the procedure.
NOTE
The following procedure assumes that the
DCA being calibrated has its “UPPER”
alarm section configured as a high alarm,
and its “LOWER” alarm section configured
as a low alarm. If this is not the case for
your DCA, interchange references to
“UPPER” and “LOWER”, as appropriate.

DCA
Page 17
RELAY RELAY
PC1
LED’S
LOWER FULL-SCALE
ADJUSTMENT POT
(DUAL ALARMS ONLY)
UPPER FULL-SCALE
ADJUSTMENT POT
Figure 13. Location of the FSA Potentiometers on the STD DCA PC1
UPPER FULL-SCALE
ADJUSTMENT
(DUAL ALARM ONLY)
CONNECTOR
PINS
FRONT PANEL
FULL-SCALE ADJUSTMENT
(SINGLE ALARM ONLY) LOW ER FULL-SCALE
ADJUSTMENT (DUAL ALARM ONLY)
Figure 14. Location of the FSA Potentiometers on the PC DCA

DCA
Page 18
1. With the hookup described in the Calibration
Setup Section complete, disable AR Option as
described in section titled “Calibrating AR-
equipped DCA’s”. Connect ohmmeter to “UP-
PER” alarm terminals first.
2. Verify that all pots are set fully counterclockwise,
to 0.00.
NOTE
Steps 3 through 10 apply to high alarms.
Skip to step 11 to calibrate the ten-turn
dials on low alarms.
3. Apply 0% of appropriate input from application.
Refer to unit’s model number and specifications
listing in table 2.
4. Turn ZERO pot clockwise until both “UPPER” and
“LOWER” alarms trip.
5. Apply 100% input to setup.
6. Turn “UPPER” and “LOWER” pots clockwise to
10.0 setting.
7. Turn internal FSA pots fully counterclockwise.
High alarm will change state. Disregard low alarm
at this time.
8. Turn FSA pot for “UPPER” alarm slowly clock-
wise, observing ohmmeter and appropriate front
panel LED.
9. Set FSA pot (stop turning) at exact point at which
high alarm is tripped. If high alarm is configured
as fail-safe, H1 in the unit model number, verify
that appropriate LED for high alarm is not lit. The
LED for a non-fail-safe high alarm, H2 in the
model number, will be lit.
10. Disconnect ohmmeter, and reconnect it to
“LOWER” alarm section of DCA.
11. With input at 100%, and ohmmeter connected to
“LOWER” alarm section of unit, turn appropriate
“LOWER” FSA pot fully clockwise. Note that low
alarm trips.
12. Turn “LOWER” FSA pot slowly clockwise, observ-
ing ohmmeter and appropriate front panel LED.
13. Set FSA pot (stop turning) at exact point at which
low alarm is tripped.
If low alarm is configured as fail-safe, L1 in the
unit model number, verify that appropriate LED for
low alarm is not lit.
The LED for a non-fail-safe low alarm, L2 in the
model number, will be lit.
14. Alternate the input between its rated 0 and 100%
level, verifying the setting of the unit’s front panel
pots (0.00 at 0% input, 10.00 at 100% input).
Readjust both FSA pots as necessary.
Calibrating DA -equipped Units. If ordered, the
Deviation Alarm Option allows the user to set alarm
trip points based on the difference between two
inputs. This difference is expressed as a percentage
of total input span, and unit relays are “tripped”
whenever process input varies, more than (high alarm)
or less than (low alarm) the set percentage.
To calibrate DA-equipped DCA’s, a second input
source will be needed. Refer to table 3, and use two
of the appropriate sources as specified.
Refer to figures 2 through 8 as appropriate, to deter-
mine which of the unit terminals is used for the
second, reference input connection.
Finally, refer to the setup shown in figure 9, and add
the connection for the second input source as follows:
“+REF” is used for positive reference input, and the
negative connection for both inputs is common, the “–
IN”.
To calibrate DA-equipped DCA’s:
1. With setup complete as described in preceding
paragraph, and all pots set fully counterclockwise,
determine percentage of rated input span that is
to serve as difference between reference input
and input #2.
2. Set reference input to 50% of rated span.
This manual suits for next models
5
Table of contents
Other Moore Industries Security System manuals
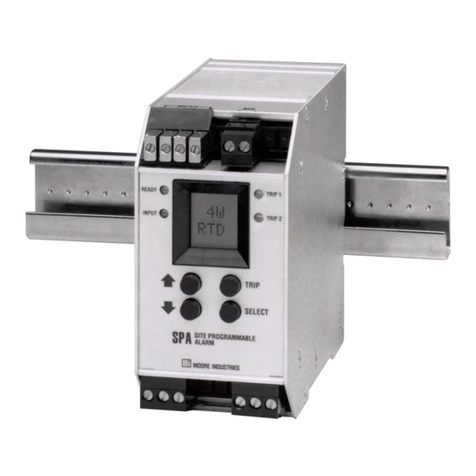
Moore Industries
Moore Industries SPA TPRG User manual
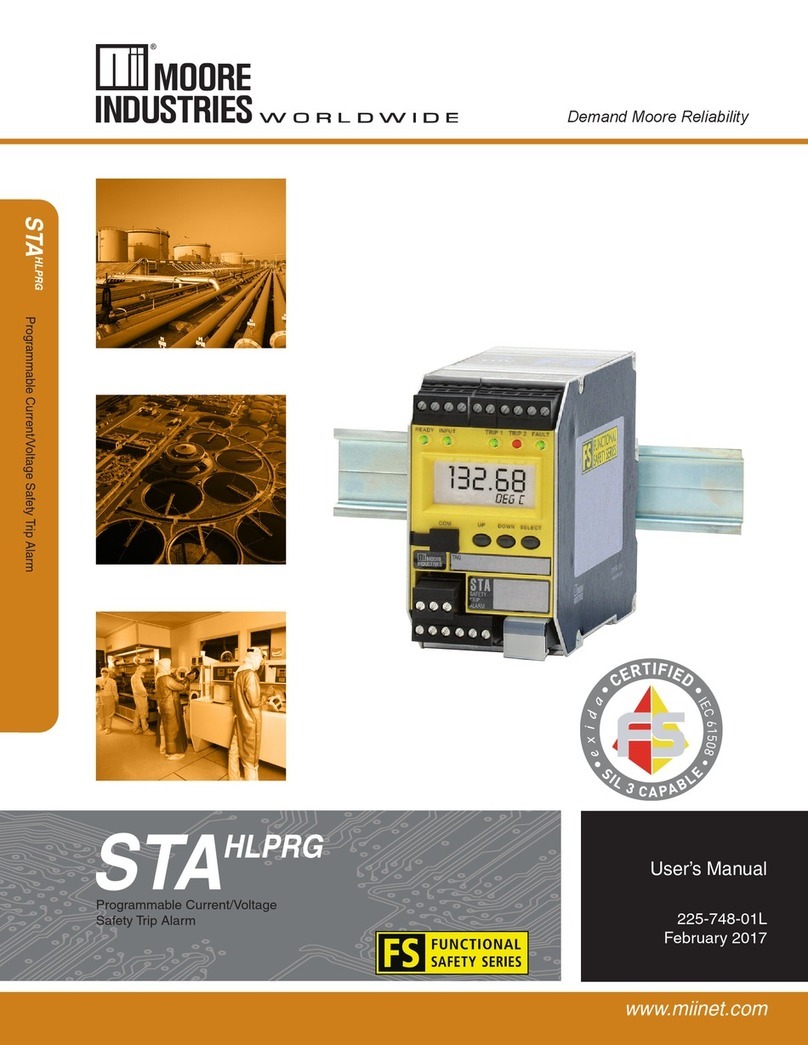
Moore Industries
Moore Industries STA HLPRG User manual
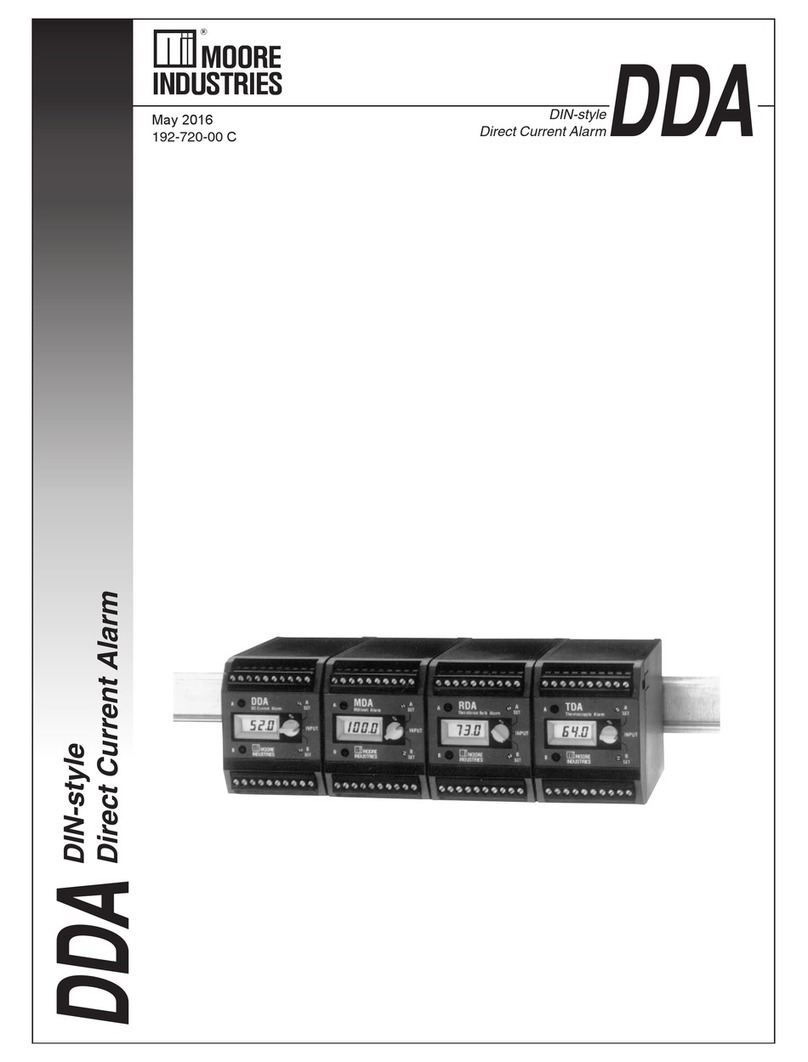
Moore Industries
Moore Industries DDA Series User manual

Moore Industries
Moore Industries SPA HLPRG User manual
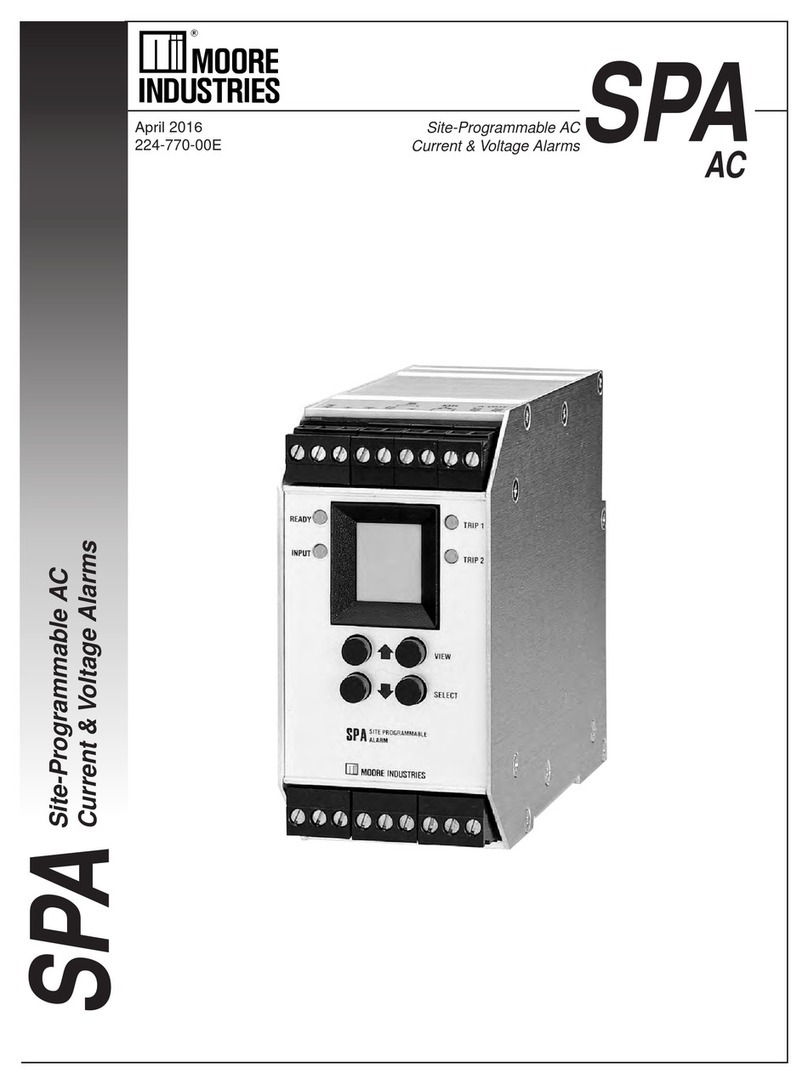
Moore Industries
Moore Industries SPA User manual

Moore Industries
Moore Industries SPA2 TPRG User manual
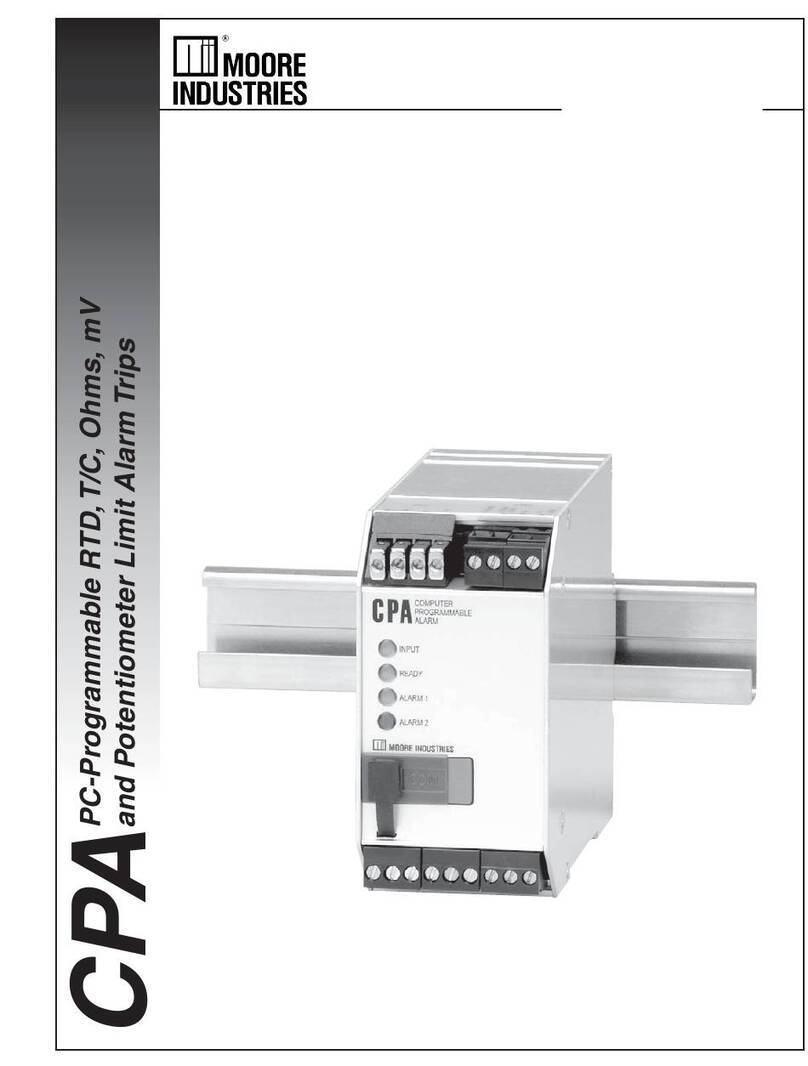
Moore Industries
Moore Industries CPA User manual