Murphy DVU Series User manual

Installation 00-02-0483 page 1 of 4
Installation and Operation Manual for
DVU Series Dump Valves
Models: DVU150, DVU175, DVU2105, DVU2115 and DVU2120
00-02-0483
Revised 10-08
Section 15
Please read the following information before installing. A visual inspection of this product for damage during shipping is recommended
before mounting. It is your responsibility to have a qualified person install this unit and make sure it conforms to local codes.
GENERAL INFORMATION
WARNING
BEFORE BEGINNING INSTALLATION OF THIS MURPHY PRODUCT
Disconnect all electrical power to the machine.
Make sure the machine cannot operate during installation.
Follow all safety warnings of the machine manufacturer.
Read and follow all installation instructions.
500
500
10
20
30
40
50
60
70
Vessel Pressure (PSIG)
Minimum Control Pressure (PSIG)
Control Pressure (PSIG)
1000
1000
1500
1500
1800
2000
0
0
20
30
40
45
50
60
Vessel Pressure (PSIG)
Maximum Actuation
Pressure
Minimum Actuation Pressure
DVU2105
DVU2115 DVU2120
DVU150/175
Pressure
Inlet Port
1/8 in.-27 NPT
Manual Valve
Operator
A
B
C
D
E
F
Drain
Connection
Plug Seal
Vent
Union
Weep Hole Valve Open/Closed
Indicator Button
(dimension shown
for reference only)
G
Fig. 2 Dimensions (all models)
Specifications
Operating Temperature: -30 to 250°F (-34.4 to +121°C)
Valve Operating Pressure: Refer to chart, Fig 1.
Maximum Process Pressure:
DVU2120:2000psi (13.8 MPa) [138 bar].
DVU2115:1500psi(10.3MPa) [103bar].
DVU2105:500 psi (3.44 MPa) [34 bar].
DVU150 and DVU175: 1800psi (12.4 MPa) [124 bar].
Flow Characteristics:See chart, page 4 (DVU150/175 models only).
Body Material: Electroless NickelPlated 12L14 Carbon Steel
Internal WettedParts:Plug Seal: 90 Durometer Urethane.
Other: 303stainless steel; Electroless Nickel Plated 12L14 Carbon Steel
Shipping Weights: DVU150 and DVU175: 9 lbs. (4 kg.).
Shipping Weights: DVU2105, DVU2115 and DVU2120:14 lbs. (6.4 kg.).
Shipping Dimensions: 7-1/2 x 7-1/2 x 10-3/4 in. (191 x 191 x 274 mm.).
Fig. 1 Control Pressure vs. Working Pressure
Model
Inlet Outlet Trim Size
DVU2120 2 NPT 1 NPT 0.436 in. (11 mm)
DVU2115 2 NPT 1 NPT 0.576 in. (15 mm)
DVU2105 2 NPT 1 NPT 0.859 in. (22 mm)
DVU1751 NPT 3/4 NPT 0.359in. (9 mm)
DVU1501 NPT 1/2 NPT 0.359in. (9 mm)
Description
The DVU Series models are pneumatically controlled dump valves.
The valves open and close automatically by pneumatic control from a
Murphy L1200NDVOR or similar level controller and dump valve opera-
tor. Diaphragm actuated, the DVU series dump valves operate at 30–70 psi
(207–483 kPa) [2.07–4.83 bar] and up to 2000 psi (13.8 MPa) [138 bar]
vessel pressure (depending on the model).
A key benefit of this design is a hex union that provides the ability
to replace the seat without removing thevalve from piping.
Model A B C D E F G
DVU2120 7.50 (191) 8.0 (203) 2.75 (70) 1.0 (25) 2-11.5 NPT 1-11.5 NPT 1.03
DVU2115 7.50 (191) 8.0 (203) 2.75 (70) 1.0 (25) 2-11.5 NPT 1-11.5 NPT 1.03
DVU2105 7.50 (191) 8.0 (203) 2.75 (70) 1.0 (25) 2-11.5 NPT 1-11.5 NPT 1.03
DVU175 7.50 (191) 6.75 (171) 2.06 (52) 1.0 (25) 1-11.5 NPT 3/4”-14 NPT 1.03
DVU150
7.50 (191) 6.75 (171) 2.06 (52) 1.0 (25)
1-11.5 NPT 1/2”-14 NPT
1.03
NOTE: Dimensions are in inches and (millimeters)

Installation 00-02-0483 page 2of 4
Basic Operation
As condensate rises in the scrubber, the float
on the L1200NDVOR rises and trips its pneu-
matic valve. The valve opens allowing pres-
sure to enter the dump valve pilot chamber.
Once the pressure enters the pilot chamber it
forces the diaphragm and valve stem forward
thus opening the valve seat (valve open/closed
indicator button pops out) and releasing con-
densate through the valve stem and out the
drain. As the condensate level drops, the
L1200NDVOR pneumatic valve closes to shut
off the pressure to the dump valve causing it to
close.
If for any reason the condensate continues to
rise beyond normal dump levels, model L1200
operates the alarm and/or shuts down the
equipment.
The L1200NDVOR Filter/Regulator and the
MURPHYGAGE®help keep the control pres-
sure clean and dry. They also allow the opera-
tor to adjust pressure to recommended levels.
NOTE: Always use clean, dry,
instrument quality gas.
TYPICAL INSTALLATION ON GAS COMPRESSORS
DVU Series Installation
The following describes the “Direct Mounting” method to the
tank wall.
1. Install the valve so the drain connection is on the bottom. Use
pipe thread sealant on all the connections.
2. Be sure the unit is screwed tight and does not leak.
3. Install the piping for the pneumatic input signal into the
1/8 NPT threaded connection of the pressure inlet port (on
top of the diaphragm housing of the DVU).
6. Install a union between the DVU drain connection and the
condensate out line. Use pipe thread sealant on all the con-
nections.
Vessel Wall
Union
UpperAssembly
(removable)
Valve
Union
Pneumatic
Input Signal
Maintenance
Bolt
Valve Indicator
Drain
Connection
WeepHole
Condensate Out
2-Way(Manual Drain)
Shutoff Valve
Fig. 4
Typical
Dump Valve
Installation
CAUTION: ALWAYS USE “NON-SPARKING TOOLS”
WHEN GAS IS KNOWN TO BE PRESENT.
WARNING
WARNING
Fig. 3
Scrubber/Separators
Filter/Regulator &
MURPHYGAGE®
“Instrument
Quality Air/Gas
Supply”
Pneumatic Level Control
Float actuated level snap-acting switch
controls pneumatic pressure to open
and close dump valve.
L1200NDVOR: Dump Valve Operator,
pressure regulator, and pressure indi-
cating MURPHYGAGE.®
Two piece union design with manual valve operator
allows soft plug and hard seat to be replaced with-
out disassembling outlet piping or scrubber pipe
connection. Diaphragm actuated valves operate on
30-70 psi (207-483 kPa; 2-5 bar).
Pneumatic Dump
Valves
See DVU-01069B
for more details.
Control
Panel
High Level Shutdown Switch
Stainless steel float actuated level switches to alarm
and/or shutdown the equipment.
L1200: 2” NPT pipe connection; Rated 2000 psi
(13.7MPa) [137bar]; Class I, Division 1. SPDT
snap-switch standard. DPDT Optional.
All Stainless Steel available.
TThheeMMuurrpphhyyGGaassCCoommpprreessssoorrSSccrruubbbbeerrLLeevveellSSyysstteemm((SSLLSS))
The system provides for liq-
uid control in gas scrubber
applications, by dumping liq-
uids to drain and protecting
compressors with a high liq-
uid level switch. Wetted metal
parts are made to survive
constant use in corrosive
environments.
See Bulletin: SLS-04005B for
more details.
DUMP VALVE INSTALLATION

Installation 00-02-0483 page 3of 4
Suggested Tools
(Sizes listed are wrench openings.
Adjustable crescent wrenches, socket and/or end wrench, pipe
wrenches, flat edge screwdriver with 1/4” blade width, can also
be used .)
Replacing the Plug and Seat
1
. Close the pressure block valves (suction & discharge valves) on the inlet
and outlet of the skid. Lock them closed if possible.
2
. Open the blowdown valve to remove pressure from the unit. Lock the
blowdown valve open if possible.
3
. After taking all possible precautions to insure there is no pressure in the
vessel. (If the condensate line is pressurized, it must also be blocked and
locked.) Open the manual drain valve so it bleeds into the vessel so it
can also be bled down. Disconnect the pneumatic input signal connection
after insuring it also has been de-pressurized.
4
. Using a back-up wrench on the valve body, with a quick "breaking"
action loosen the union nut on the valve. There is a "weep" hole in the
nut. If at any time while loosening and taking off the nut pressure is
escaping through the "weep" hole, immediately stop loosening the nut.
Retighten the nut and check the preceding procedures to ensure the pres-
sure is bled off the vessel. Never remove the assembly if pressure is
coming through the weep hole. See Figure 4 on page 2.
5
. With the upper assembly removed from the vessel the plug and/or seat can
be replaced. Loosen the 9/16” jam nut on the maintenance bolt on top of
the diaphragm cover. Spin the nut up against the head of the bolt. Tighten
the bolt to extend the shaft and plug. DO NOT OVERTIGHTEN.
6
. Using a back-up wrench on the plug, remove the stem nut on the shaft
under the plug. Once the stem nut is broken loose, the 9/16” head main-
tenance bolt and top assembly will keep the stem from turning. The
plug turns freely on the stem once loose. The plug and seat can now be
removed. All soft seals should be replaced. Refer to kit part numbers
under service parts on page 4.
7
. Install the seat and plug. Place the O-ring on the stem, followed by the
washer and stem nut.
8
. Tighten the stem nut. Loosen the 9/16” head maintenance bolt by at least one
turn past the point where it is no longer in contact with the stem. Tighten the
9/16" jam nut holding the 9/16” head maintenance bolt.
9
. Replace the crush washer and the O-ring hidden by the union nut.
NOTE: If pressure or fluid comes out the weep hole of the union nut,
either the O-ring under the union nut is leaking, or the packing could be
leaking through the internal weep hole above that O-ring.
10
. The assembly is ready to be re-installed. Check for relative position of
the pneumatic input signal connections before tightening the union nut.
Washer(s)*
*Number of washers varies depending on the model from 1 to 3.
Stem
Nut O-Ring
Plug
Crush Washer SealSeat butts into here
O-Ring Seals
Against Outlet
Stem
Seat
Stem
Packing
Diaphragm
Assembly
Pressure Inlet
Seal Washer Maintenance
Bolt
1-1/8" or
1" round nut
Backup
Plate
Stem Spring
Diaphragm
Diaphragm
Housing
1/2" Nut
REPAIR PROCEDURE
CAUTION:
THE INSTALLATION AND REPAIR PROCEDURES SHOULD
ONLY BE PERFORMED BY TRAINED, QUALIFIED, AND EXPERIENCED
PERSONNEL. THE TRAINING, QUALIFICATION AND EXPERIENCE
REQUIRED IS FOR WORK AROUND PRESSURE VESSELS, NATURAL GAS, POSSI-
BLY SOUR GAS, OR ANY SUBSTANCE TO BE FOUND IN THE VESSEL. EXTREME
CARE MUST BE TAKEN TO INSURE ANY RESIDUAL OR FULL PRESSURE IS
RELIEVED FROM ALL PARTS OF THE SYSTEM TO BE SERVICED.
WARNING
WARNING
Fig. 5
Fig. 6
Model
Valve Body Union Nut Plug Seal Hex Stem Nut
DVU150/DVU175 2-1/4” 2-1/4” 3/4” 3/8”
DVU2105 3” 3” 1-1/4” 1/2”
DVU2115 3” 3” 1” 1/2”
DVU2120 3” 3” 7/8” 1/2”
Replacing the Diaphragm
6A.If the diaphragm is to be replaced, all preceding steps have to be
done. Additionally, do the following:
6B. Loosen the 9/16” head maintenance bolt, allowing the
diaphragm spring to relax, and the stem to retract. Make align-
ment marks on the top and bottom halves of the diaphragm
assembly for alignment during re-assembly.
6C. Remove the 8, 7/16" bolts/nuts holding the diaphragm housing
together.
6D. Using a straight edge screwdriver, gently separate the 2 halves
of the diaphragm housing, and remove the top, or outside por-
tion.
6E. Lift the diaphragm and support plates far enough for the 1-1/8"
hex or 1” round nut on the bottom of the diaphragm assembly to
be accessible to a wrench and not have the spring interfere. If it
is desired to replace the packing, pull the stem all the way out.
The packing can be easily removed using a small screwdriver to
pry the packing out. The new packing can be simply pressed in,
making sure the orientation of the packing installed is the same
as the orientation of the packing removed. The packing is wider
toward the plug end. You will have to use the seat to hold the
packing in place when re-inserting the stem.
6F.With the 1-1/8" hex or 1” round nut held by a wrench, use a
wrench to loosen and remove the 1/2" nut on top of the
diaphragm. The diaphragm can now be removed and replaced.
6G. With the new diaphragm in place and the 1/2" nut tightened,
place the assembly, diaphragm down on a clean, smooth sturdy
surface.
6H.Have the seat, plug, washers and stem nut handy (if any of these
parts are to be replaced, use the old parts for this procedure).
Press down evenly and smoothly on the bottom of the
diaphragm assembly to cause stem to come up. Place the seat
and plug in place. Then push the bottom of the diaphragm
assembly down far enough to install the washers and stem nut
on the stem. Tighten the stem nut enough to hold against the
diaphragm spring.
6J.Align the diaphragm holes to the bolt holes (bottom half of the
housing). Install the upper diaphragm housing using the align-
ment marks from step 6B. Install the 8, 7/16" bolts and nuts.
Tighten the bolts evenly going from one bolt then 180° around
to the next bolt, then either 120°or 240°around to the next bolt
and so forth until all 8 bolts are evenly tight.
6K. Using the 9/16” head maintenance bolt, tighten, pushing the
stem out until the 9/16"bolt stops – DO NOT OVERTIGHTEN.
6L. Remove the stem nut holding the plug. (If old parts were used,
prepare to install the new parts now.)

Installation 00-02-0483 page 4 of 4
PRESSURE VS. FLOW CHART
5
Flow (gpm)
Pressure (psid)
10 15 20 25 30 35 4540
0
0
50
100
150
200
250
Pressure vs. Flow for DVU150 Dump Valve
Fig. 7
250
200
150
100
50
Pressure vs. Flow for DVU150 and DVU175 models only
SERVICE PARTS
Part No Description
DVU2120
55-00- 0 2 3 7 Seal Kit (includes plug)
55-00- 0 2 3 6 Diaphragm Kit
DVU2115
55-00- 0 2 4 1 Seal Kit (includes plug)
55-00- 0 2 4 0 Diaphragm Kit
DVU2105
55-00- 0 2 4 5 Seal Kit (includes plug)
55-00- 0 2 4 4 Diaphragm Kit
DVU175
55-00- 0 2 3 0 Seal Kit (includes plug)
55-00- 0 2 3 1 Diaphragm Kit
DVU150
55-00- 0 2 3 0 Seal Kit (includes plug)
55-00- 0 2 3 1 Diaphragm Kit
TypicalSeal Kit includes:
Nut, Washer (1 to3), “O” Ring, Plug
and Seal, Seat, Crush Washer.
Typical Diaphragm Repair Kit
i
ncludes:
Diaphragm; Diaphragm Washer (upper),Diaphragm Nut, Diaphragm Plate
(1 or2 pcs.), Packing, “O” Ring, Stem, Seal Washer for Maintenance Bolt.
The DVU Series Valve is included in the
following Scrubber Levels Systems.
(Includes LS200, LS200NDVOR, and DVU valve)
SLS212 0:Includes DVU2120 valve
SLS211 5:Includes DVU2115 valve
SLS210 5:Includes DVU2105 valve
SLS175:Includes DVU175 valve
SLS150:Includes DVU150 valve
-LR:Less Regulator option
Warranty
A limited warranty on materials andworkmanship is given with this FW
Murphy product. A copy of the warranty may be viewedor printed bygoing
to www.fwmurphy.com/support/warranty.htm
Printed in U.S.A.
MurCal
c
CALL MURCAL TO PLACE YOUR ORDER
P:(661)272-4700 F:(661)947-7570
w w w. m u r ca l . c o m e - m a i l : s a l e s @ m u r ca l . c o m
This manual suits for next models
5
Other Murphy Control Unit manuals
Popular Control Unit manuals by other brands
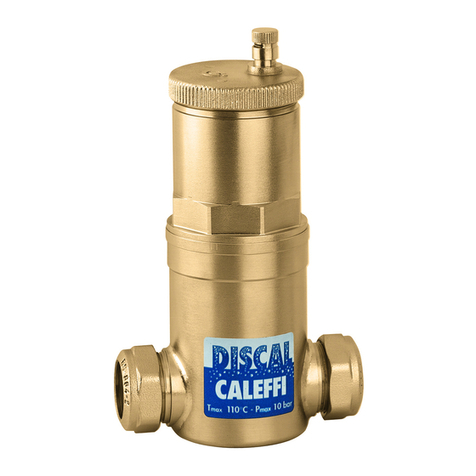
CALEFFI
CALEFFI DISCAL 551 Series manual
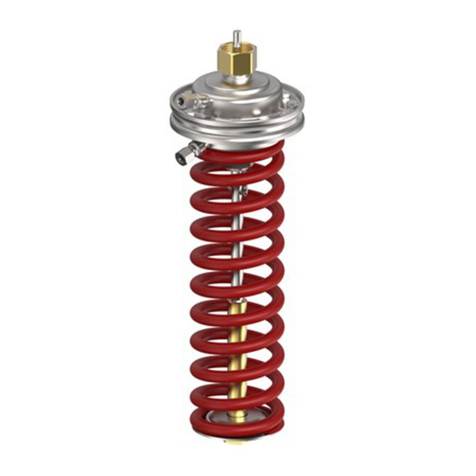
Danfoss
Danfoss PCV-VFGS 2 DN 150-250 installation guide
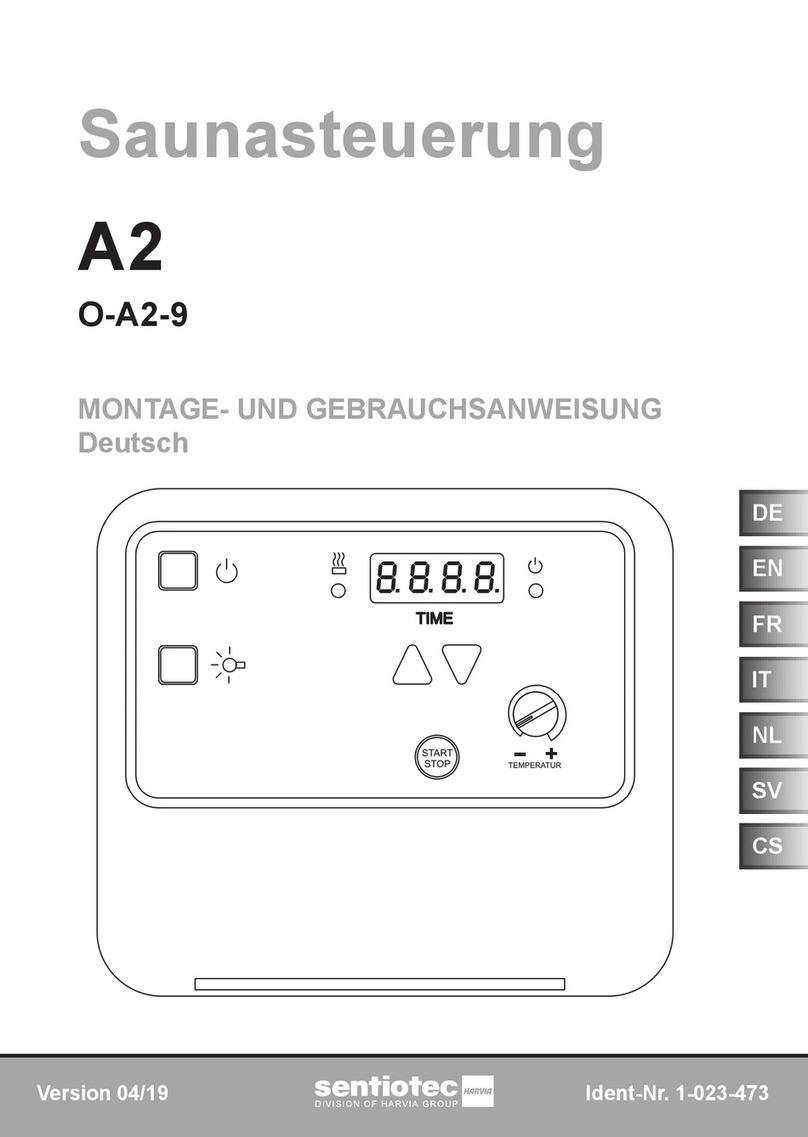
Harvia
Harvia Sentiotec A2 Instructions for installation and use
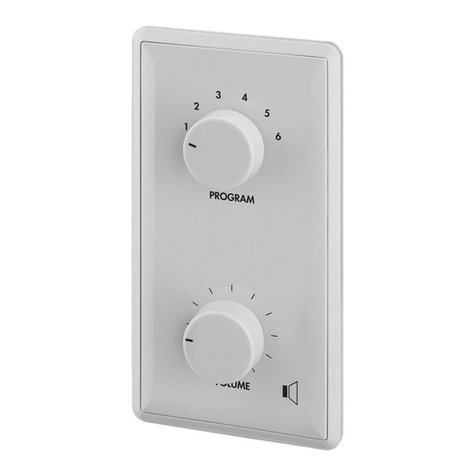
Monacor
Monacor ATT-412PEU instructions

Meinberg
Meinberg IMS-HPS-100 Setup guide
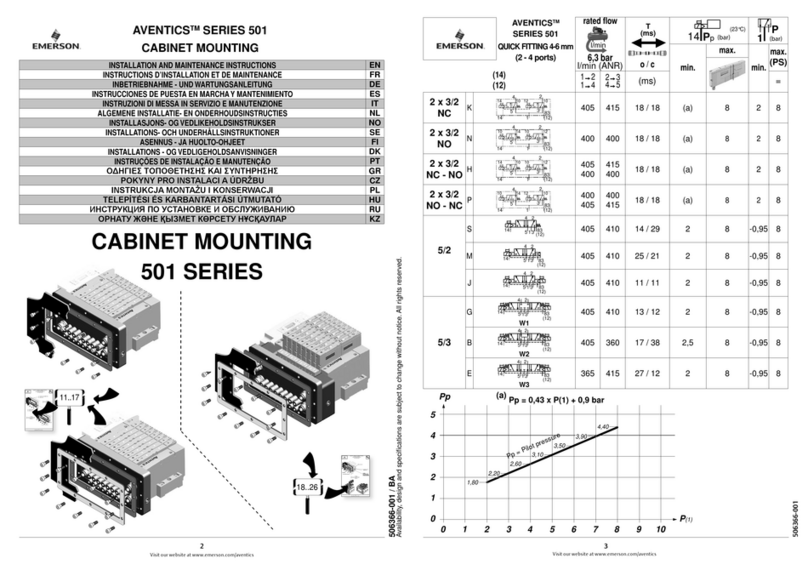
Emerson
Emerson AVENTICS 501 Series Installation and maintenance instructions