New lift ECO User manual

Home lift control system acc. to EN81-41
MANUAL

ECO manual
Manufacturer NEW LIFT Service Center GmbH
Ruwerstraße 16
54427 Kell am See
Tel +49 6589 – 919 540
Fax +49 6589 – 919 540 – 300
E-Mail [email protected]
www.newlift.de
Service line Tel +49 89 – 898 66 – 110
Mail [email protected]
First version 17.03.2016
Author JW
Last change 07.09.2017 DU / EP
Release 11.09.2017 HW
Hardware version Processor module: 9-00-30-ECO-PRZ
Display module: 9-00-30-ECO-BAZ
Preselection module: 9-01-30-ECO-VST
Software version ECO-01 V18
Doc. No. hb_eco_2017-09_en
Copyright © NEW LIFT Steuerungsbau GmbH, 2017.
This manual is protected by copyright. All rights, including those of copying, of
reproduction, of translation and of modification, in whole or in part, are reserved by
the publisher.
No part of this description may be reproduced in any form or copied with an
electronic replication system without written permission.
Although great care has been taken in the production of texts and figures, we
cannot be held legally liable for possible mistakes and their consequences.

Product overview
ECO processor module
ECO pre-control module
Power supply
UPS
Motor contactors K1, K2
Maintenance socket
Control cabinet lighting
Main switch
Frequency inverter

ECO manual
4
Content
1 Information on this manual 6
1.1 Abbreviations, characters and symbols used 6
1.2 Further information 7
1.3 How to contact us 7
2 General safety regulations 8
2.1 Applicable standards and guidelines 8
2.2 Electromagnetic compatibility (EMC) 8
2.3 Handling electronic assemblies 8
2.4 General 8
2.4.1 Qualifications of the installing engineer 8
2.4.2 Residual dangers 9
2.4.3 Safety regulations 9
3 About the ECO 11
3.1 Purpose 11
3.2 Pin assignment 12
3.2.1 Pin assignment ECO 12
3.2.2 Terminal assignment of terminal strip in control cabinet 14
3.2.3 Jumper/DIP switches in ECO processor module 15
3.2.4 Terminal assignment of car top box 16
4 Installation 18
4.1 Delivery contents 18
4.2 Checking the delivery contents 18
4.3 Claiming damages during transport 18
4.4 Reordering ECO components 19
4.5 Installing the control cabinet 19
4.6 Connecting the control cabinet 20
4.7 Installing and connecting the travelling cable 20
4.8 Meaning of the display indicator of the ECO 21
5 Description of the functions available 22
5.1 Orientation drive after switching on. 22
5.2 Normal drive 22
5.2.1 ECO basic 22
5.2.2 ECO premium 22
5.3 Light curtain test (ECO basic) 23
5.4 Safely accessing the shaft pit 23
5.5 Safely accessing the car roof 23
5.6 Auxiliary mode control in the control cabinet 24
5.7 Inspection control on the car roof 24
5.8 Emergency evacuation (passenger evacuation) 25
5.9 Function of control panel buttons 26

ECO manual
5
5.10 Online configuration 27
5.11 Functions for free I/O ports 28
6 Monitoring functions of ECO 30
6.1 Description of the functions available 30
6.2 Activation of individual monitoring functions 31
7 Activation of special options 32

Information on this manual
Abbreviations, characters and symbols used
ECO manual
6
1 Information on this manual
The ECO was specially designed for platform lifts in accordance with EN81-41. It is precongured for max. 6
oors and is available in two variants:
- ECO basic: platform lift without car door with dead man control
- ECO premium: platform lift with car door and self-driving control system
Please read this manual carefully before installing and commissioning the ECO. Also see Chapter 2 „General
safety regulations“.
This manual will help you during installation and commissioning of the ECO and its components. This manual
contains important information for safe and proper installation and commissioning of the ECO controller.
Following these instructions will help to:
- prevent danger
- avoid repair costs and downtime
- increase the reliability and service life of the ECO and the platform lift.
Local, national and on-site regulations regarding health and safety and protection of the environment must be
taken into account in addition to this manual.
This manual only describes the assemblies of the platform lift delivered by NEW LIFT. For information on
components that were not manufactured and supplied by NEW LIFT, please refer to the respective user infor-
mation supplied by the manufacturer or supplier.
1.1 Abbreviations, characters and symbols used
Symbol/
abbrevia-
tion
Meaning
ECO ECO home lift control system
IInput
OOutput
I/O Input/output
Delivery condition
Settings that are supplied as standard are marked with
an asterisk .
►
Operational instructions
Perform the tasks that follow this symbol in the specied
order.
Safety information
This symbol is located in front of safety-relevant
information.
Information notice
This symbol is located in front of relevant information.

Information on this manual
Further information
7
ECO manual
1.2 Further information
The following documents, among others, are available for the ECO and its components:
› Function description of the ECO home lift control system
› Wiring diagram example: ECO basic/premium
1.3 How to contact us
Should you require support, our service line is there for you:
Tel +49 6589 – 919 540
Mail [email protected]
Mon. - Thurs.: 8:00 a.m. – 12:00 p.m. and 1:00 p.m. – 5:00 p.m.
Fr: 8:00 a.m. – 3:00 p.m.
This and other current manuals can be found in the download area of our
website under "Service": http://www.newlift.de/en/service/download

General safety regulations
Applicable standards and guidelines
ECO manual
8
2 General safety regulations
The ECO may only be operated in perfect working condition in a proper manner, safely and in compliance with
the manual, the valid accident prevention regulations and the guidelines of the local power company.
The safety guidelines of all NEW LIFT control system series apply for this product.
2.1 Applicable standards and guidelines
The ECO complies with ...
›DIN EN 81 - 41: safety rules for the construction and installation of vertical lifting platforms intended for persons
with impaired mobility,
›DIN VDE 0100:conditions for the erection of high voltage installations with nominal voltages up to 1 kV,
›VDE 0106:the contact protection measures in the machine room,
›Data sheet ZH 1/312: safety measures for the installation, maintenance and commissioning of lift systems.
› The new EC machinery directive 2006/42/EC
2.2 Electromagnetic compatibility (EMC)
The HST and its components were inspected by an accredited inspection authority in accordance with the limit
values and severity levels stated in EN 12015/1995 and EN 12016/1995.
The HST and its components are...
› immune to electrostatic discharge (EN 61000-4-2/1995)
› immune to electrostatic elds (EN 61000-4-3/1997)
› immune to fast transient disturbances (EN 61000-4-4/1995)
The electromagnetic disturbance eld strengths created by the HST and its components do not exceed the
permissible thresholds (EN 55011/1997).
2.3 Handling electronic assemblies
› Keep the electronic assembly in its original packaging until installation to prevent damage.
› Before opening the original packaging, a static discharge must be performed!
To do this, touch a grounded piece of metal.
› During work on electronic assemblies, periodically repeat this discharge procedure!
› Equip all bus inputs/outputs not in use with a terminal resistor (terminator) to prevent malfunctions.
2.4 General
2.4.1 Qualifications of the installing engineer
All persons performing installation and commissioning work on the ECO must read this chapter and follow its
regulations.
Laws, regulations, guidelines and standards that apply in the country of operation must be followed in addition
to the safety regulations mentioned in this manual.

General safety regulations
General
9
ECO manual
The installing engineer must:
• be over 18 years of age (exception: apprentices who are over 16 years of age and are permanently super-
vised by an engineer qualied for training apprentices).
• have rst aid training.
• have theoretical and practical knowledge of regulations and measures for the prevention of re and explo-
sions in his work area.
• be able to identify, avoid and rectify all dangers that might occur during his work in the lift shaft and in the
operating rooms.
• be able to identify and rectify all irregularities and faults that might occur during installation and operation of
a lift system.
• have theoretical and practical knowledge of operating principles and requirements of electric controls and
drive systems.
All installation and commissioning work on electric and electronic components of the ECO must be performed
by or supervised by a qualied electrician.
A qualied electrician has appropriate training and knowledge of regulations that allow him to judge the quality
of the work performed and identify possible dangers (UVV, VGB 4, §2 (3)).
2.4.2 Residual dangers
• Danger to life! Do not touch live parts while working on electrical equipment
• Danger to life when falling down the lift shaft.
• Risk of injury when lifting or moving the control cabinet if it falls down or tips over.
• Risk of injury for persons in the lift shaft while the car is in motion.
• Risk of injury due to unexpected car movements.
• Destruction of the ECO Controller and its electronic assemblies by short circuits or excessive voltage.
2.4.3 Safety regulations
• The instructions of the lift manufacturer and the instructions in this manual must be followed during installa-
tion and commissioning of the lift system.
• The lift shaft must be secured against unauthorised trespassing during installation and commissioning.
• Assemblies, devices and cables must be installed securely and permanently.
• Loads must be moved with suitable aids (lift trucks, hoisting gear etc.).
• Sharp or pointed tools or other potentially dangerous objects must not be carried in the clothing unless
sufcient protective measures are taken to avoid injuries.
• Alcohol and drugs must not be consumed before and during installation and commissioning.
• A copy of this manual and the order-specic wiring diagrams must be available to the installing engineer at
the time of installing and commissioning the ECO and its components. A copy of this manual and the wiring
diagrams must be kept in the control cabinet at all times after installation.
• The supplied, order-related wiring diagrams of the ECO are binding. Changes must only be made after
consulting NEW LIFT and must be documented in writing on the system.
• The factory test logs of the ECO remain with NEW LIFT.

General safety regulations
General
ECO manual
10
Electricity:
• Regulations for installing and operating electrical equipment (VDE0100) and regulations of local utilities
must be followed.
• The specied distances between different electrical assemblies must be controlled and maintained.
• All installation work must be carried out with the system shut down and off circuit.
• All cables and wires must be installed with sufcient strain relief.
• The neutral and ground wires must be routed separately.
Working in the lift shaft:
• If the car is used as an assembly platform, the regulations from VGB 35: “building elevators” apply for the
entire lift system.
• Any work in the lift shaft requires perfect and permanent communication between the supervisor on the
ECO and the workers in the shaft.
• Parts in the lift shaft must be located and secured in a way that persons entering the lift shaft for inspection,
maintenance or repair are not in danger. (AufzV, appendix 2.1.5)
• The maximum load of the lift system must not be exceeded.
• The specied overruns of the emergency end switches in relation to the speed must be observed.
• The emergency installations must not be activated during normal operation.
• All emergency installations and braking systems must be checked for troublefree operation at the begin-
ning of each shift.
• During breaks, the car is to be moved to the lowest rest position, the controller must be switched off and
the power supply must be interrupted.
• Installation and operation are prohibited if other persons could be in danger.
• Workers must be secured against falling.
Personal protective equipment of the installing engineer
• Eye protection
• Safety boots
• Protective helmet
• Safety harness
• Clothing suitable to the ambient conditions of the installation location
• Jewellery, watches or similar objects must not be worn
Waste disposal
• All packaging material must be disposed of in an environmentally acceptable manner.
• Paper, plastic, metal and electronic assemblies must be recycled.
• Adhesive residues must be disposed of in an environmentally acceptable manner in accordance with the
governing laws and regulations.

About the ECO
Purpose
11
ECO manual
3 About the ECO
3.1 Purpose
The term “home lift” or “platform lift” refers to a simple type-tested passenger lift in accordance with EN81-41
with frequency-regulated cable drive (open loop) or hydraulic drive (star/delta or soft-start) and xed speed of
v=0.15 m/s for use in private residences. This lift can serve up to six oors and requires a standard 230V AC
1-phase supply. The ECO home lift control system is available in two variants:
ECO BASIC:
- up to six oors in button-control mode (single-call mode)
- landing call acknowledgement is used as ‘Lift Here’ display
- no car door; monitored safety curtain used as guard
- manual shaft swing doors with xed retiring cam and zone switching
- 24 V DC safety circuit, contactor and runtime monitoring
- landing calls are processed automatically
- car calls are processed in dead man mode
- magnetic positioning with level switch and correction switch (BC)
- zone switching with zone magnets for bridging the xed retiring cam
- landing calls via at cable
- monitoring of shaft doors, shaft pit and car roof
- 10 freely programmable I/O ports
- four controls:
- cable drive with two speeds (GEFRAN frequency inverter)
- cable drive with two speeds (GEFRAN frequency inverter) + readjustment
- hydraulic drive with FAST-valve
- hydraulic drive with star/delta or soft start and FAST-valve
ECO PREMIUM:
- all features of the ECO BASIC
- landing calls via LON bus with ADM-3 or EAZ-256/64 or EAZ-TFT.110 position indicator possible
- car calls via LON bus with EAZ-TFT.110 position indicator possible
- position indicators can be switched off after an adjustable time
- voice message via SAM speech computer or integrated in EAZ-TFT.110 position indicator possible
- control of an automatic car door
- automatic sliding landing doors or manual doors
On delivery, the ECO is precongured so that no parameter changes are necessary during installation and
commissioning.
Technical data
General
Description Value
Supply voltage 230 V AC ±10% / N / PE
Typical power consumption 500 mA – 6000 mA
Outputs Short circuit-proof to 40V
Installation dimensions WxHxD = 500x750x175 mm
Weight 55 kg
Temperature range:
Storage & transport / operation -20 – +70 °C / ±0 – +60 °C
Relative humidity:
Storage & transport / operation (non-condensing) +5 – +95 % / +15 – +85 %

About the ECO
Pin assignment
ECO manual
12
3.2 Pin assignment
3.2.1 Pin assignment ECO
ECO processor module:
Terminal I/O Function
X0.1 O Remote trigger of arrest +24V
X0.2 ORemote trigger of arrest +0V
X0.5 O Drive-motor brake +24V
X0.6 ODrive-motor brake +0V
X1.1 O Analogue load weighing +24V (potentiometer)
X1.2 O Analogue load weighing +0V (potentiometer)
X1.3 I Analogue signal for load weighing (potentiometer)
X1.5 O Overload (digital)
X1.6 I Overload (digital)
X2.1 O Motor contactor K1.A1 (coil)
X2.2 O Motor contactor K2.A1 (coil)
X2.3 O Motor contactors K1/K2.A2 (coils)
X2.4 O Motor contactors K1.13 and K1.11 (+24V for contact evaluation)
X2.5 I Motor contactor K2.14 (NO normally open contacts)
X2.6 I Motor contactor K2.12 (NC normally closed contacts - contactor monitoring)
X2.8 O FU_M01 (frequency-inverter reference potential)
X2.9 I FU_MCM (brake signal - lowside switch)
X2.10 O FU_MI1 (direction of travel UP)
X2.11 O FU_MI2 (direction of travel DOWN)
X2.12 O FU_MI6 (SHK STOP)
X2.13 OFU_V=0.05 (slow)
X2.14 I FU_COM (common contact in frequency inverter)
X3.1 I +24VDC supply voltage
X3.2 I+0 V supply voltage
X4/5.1 I/O LON_TXD
X4/5.2 I/O LON_RXD
X4/5.3 I+0 V supply voltage
X4/5.4 I +24 V supply voltage
X11.1/2 O +24V
X11.3 OCar Here - oor 0
X11.4 O Car Here - oor 1
X11.5 OCar Here - oor 2
X11.6 OCar Here - oor 3
X11.7 OCar Here - oor 4
X11.8 O Car Here - oor 5
X11.12 I/O Travelling cable - replacement cable (connected with X24.13 on pre-control
module)
X11.13/14 O0V
X12.1/2 O +24V
X12.3 I/O Free I/O PORT 0
X12.4 I/O Free I/O PORT 1
X12.5 I/O Free I/O PORT 2
X12.6 I/O Free I/O PORT 3
X12.7 I/O Free I/O PORT 4
X12.8 I/O Free I/O PORT 5
X12.9 I/O Free I/O PORT 6
X12.10 I/O Free I/O PORT 7
X12.11 I/O Free I/O PORT 8
X12.12 I/O Free I/O PORT 9

About the ECO
Pin assignment
13
ECO manual
Terminal I/O Function
X12.13/14 O0V
X13.1 ILanding call - oor 0 (oor button)
X13.2 ILanding call - oor 1
X13.3 ILanding call - oor 2
X13.4 ILanding call - oor 3
X13.5 ILanding call - oor 4
X13.6 ILanding call - oor 5
X13.7 I/O Free I/O PORT 8
X13.8 I/O Free I/O PORT 9
X13.9 O0V
X13.10 O +24V
X14.1 O Extension SPI_CS_EN
X14.2 O Extension SPI_CS
X14.3/8/12 OExtension 0V
X14.4/11 O Extension +24V
X14.5 OExtension SPI_SDO
X14.6 IExtension SPI_SDI
X14.7 OExtension SPI_SCK
X14.9 O Extension +5V
X14.10 I/O Extension reset
ECO pre-control module:
Terminal I/O LED
X21.1 I 230VAC supply
X21.2 O 230VAC mains supply
X21.3 I230VAC supply - car lighting
X21.4 I N supply
X22.1 O Travelling cable - N supply automatic door
X22.2 O Travelling cable - 230VAC supply automatic door
X22.3 OTravelling cable - 230VAC car lighting
X23.1 O Travelling cable - +24V
X23.2 OTravelling cable - 0V
X23.3 O Travelling cable - +24V supply (occupied)
X23.4 I/O Travelling cable - SHK from emergency stop circuit
X23.5 I/O Travelling cable - SHK to folding support
X23.6 I/O Travelling cable - SHK from emergency stop
X23.7 I/O Travelling cable - SHK to light curtain
X23.8 I/O Travelling cable - SHK from light curtain
X23.9 ITravelling cable - Zone A
X23.10 ITravelling cable - Zone B
X23.11 I Travelling cable - correction downward (end switch)
X23.12 I Travelling cable - levelled position 1 (end switch)
X23.13 ITravelling cable - levelled position 2 (end switch: only with hydraulic drive)
X23.14 I/O Travelling cable - connected to X24.14
X24.1 I Travelling cable - car call oor 0
X24.2 I Travelling cable - car call oor 1
X24.3 ITravelling cable - car call oor 2
X24.4 I Travelling cable - car call oor 3
X24.5 ITravelling cable - car call oor 4
X24.6 ITravelling cable - car call oor 5
X24.7 I Travelling cable - emergency call button
X24.8 I Travelling cable - door open button
X24.9 O Travelling cable - horn - overload/emergency call
X24.10 O Travelling cable - automatic door OPEN

About the ECO
Pin assignment
ECO manual
14
Terminal I/O LED
X24.11 O Travelling cable - automatic door CLOSED
X24.12 I Travelling cable - automatic door COM
X24.13 I/O Travelling cable - replacement cable (connected to X11.12 on processor
module)
X24.14 I/O Travelling cable - connected to X23.14
X31 I/O SHK - FU_RB/RC
X32 I/O SHK - emergency stop
X33 I/O SHK - slack rope
X34 I/O SHK - shaft-pit folding support
X35 I/O SHK - locking
X36 I/O SHK - top emergency limit point
X37 I/O SHK - bottom emergency limit point
X38 I/O SHK - speed limiter
X25.1 I +24V supply
X25.2 I+0V supply
X26.1 O Horn - overload/emergency call +24V
X26.2 OHorn - overload/emergency call 0V
X41-46.1 O SHK - manual door (NC)
X41-46.2 I SHK - manual door (NC)
X41-46.3 O SHK - lock (NC)
X41-46.4 I SHK - lock (NC)
X41-46.5 I Monitoring of door emergency release (NC)
X41-46.6 O Monitoring of door emergency release (NC)
3.2.2 Terminal assignment of terminal strip in control cabinet
ATTENTION!
Potential equalisation must be carried out in accordance with applicable
regulations and guidelines (VDE, DIN, EN and ISO) depending on the
power rating. The neutral and ground wires must be routed separately!
All cables and wires must be secured with sufficient strain relief.
Fig. 3.1: Terminal strip in control cabinet
Terminal strip X1 (supply):
Terminal I/O Description
X1.1 I Supply L1 230VAC +-10% (fuse-protection of 16A to be provided by the
customer)
X1.2 I Supply N
X1.3 I Supply PE
X1.11 O Drive motor PE of the motor cable
X1.12 O Drive motor U
X1.13 O Drive motor V
X1.14 O Drive motor W
X1.PE O Drive motor shielding of the motor cable (only with cable lift)
X1.15 O Drive motor U2 (only with hydraulic lift)

About the ECO
Pin assignment
15
ECO manual
Terminal I/O Description
X1.16 O Drive motor V2 (only with hydraulic lift)
X1.17 O Drive motor W2 (only with hydraulic lift)
Terminal strip X2 (only with hydraulic lift):
Terminal I/O Description
X2.1/2 O Valve - DOWN
X2.3/4 O Valve - UP
X2.5/6 O Valve - slow/fast
X2.7/8 O Valve - emergency lowering/locking
Terminal strip X40 (peripherals):
Terminal I/O Description
X40.1/2 O PTC resistor - motor (only with cable lift)
X40.3/4 O Motor brake (only with cable lift)
X40.5/6 I Smoke detector (optional)
X40.7-9 I Door CLOSE button - landing (optional)
X40.10/11 I Temperature sensor - drive motor (only with hydraulic lift)
X40.12 OEmergency call lter - changeover contact (12)
X40.13 OEmergency call lter - changeover contact (11)
X40.14 OEmergency call lter - changeover contact (14)
X40.15 O Collective fault - changeover contact (12)
X40.16 O Collective fault - changeover contact (11)
X40.17 O Collective fault - changeover contact (14)
X40.18 O Locking solenoid - changeover contact (12)
X40.19 O Locking solenoid - changeover contact (11)
X40.20 O Locking solenoid - changeover contact (14)
3.2.3 Jumper/DIP switches in ECO processor module
J1: Basic: switch off dead man control for car calls
Premium: car calls as dead man control
J2: manual changeover to ECO premium
J3: ECO premium with manual doors
DIP-1: auxiliary mode/inspection, slow only
DIP-2: homing drive also with cable drive
DIP-3,4 00 - cable drive with GEFRAN frequency inverter
01 - cable drive with GEFRAN frequency inverter + readjustment
10 - hydraulic drive with FAST valve
11 - hydraulic drive with soft- or star/delta-start and FAST valve
DIP 5-8: reserved (for development)

About the ECO
Pin assignment
ECO manual
16
3.2.4 Terminal assignment of car top box
Fig. 3.2: ECO car top box
Terminal strip X29 (travelling cable - 230V car):
Terminal I/O Description
X29.1 O Travelling cable - power supply N
X29.2 O Travelling cable - power supply - car door 230V
X29.3 OTravelling cable - power supply - car lighting 230V
X29.PE O Travelling cable PE
Terminal strip X30 (travelling cable - safety circuit, zone, end switch):
Terminal I/O Description
X30.1 O Travelling cable - +24V
X30.2 OTravelling cable - 0V
X30.3 O Travelling cable - +24V supply (occupied)
X30.4 I/O Travelling cable - SHK from emergency stop circuit
X30.5 I/O Travelling cable - SHK to folding support
X30.6 I/O Travelling cable - SHK from emergency stop
X30.7 I/O Travelling cable - SHK to light curtain
X30.8 I/O Travelling cable - SHK from light curtain
X30.9 ITravelling cable - Zone A
X30.10 ITravelling cable - Zone B
X30.11 I Travelling cable - correction downward (end switch)
X30.12 I Travelling cable - levelled position 1
X30.13 I Travelling cable - levelled position 2 (only with hydraulic drive)
X30.14 I/O Travelling cable - connected to X24.14
Terminal strip X31 (travelling cable - calls, door):
Terminal I/O Description
X31.1 ITravelling cable - car call oor 0
X31.2 ITravelling cable - car call oor 1
X31.3 ITravelling cable - car call oor 2
X31.4 ITravelling cable - car call oor 3

About the ECO
Pin assignment
17
ECO manual
Terminal I/O Description
X31.5 ITravelling cable - car call oor 4
X31.6 ITravelling cable - car call oor 5
X31.7 I Travelling cable - emergency call button
X31.8 I Travelling cable - door open button
X31.9 O Travelling cable - horn - overload/emergency call
X31.10 O Travelling cable - automatic door OPEN
X31.11 O Travelling cable - automatic door CLOSED
X31.12 I Travelling cable - automatic door COM
X31.13 I/O Travelling cable - replacement cable (connected to X11.12 on processor
module)
X31.14 I/O Travelling cable - connected to X23.14
Terminal strip X100 (safety circuit):
Terminal I/O Description
X100.11 O Arrest switch (11)
X100.12 I Arrest switch (12)
X100.13 O Slack rope switch (11)
X100.14 I Slack rope switch (12)
X100.15 O Emergency stop - car roof (11)
X100.16 I Emergency stop - car roof (12)
X100.17 O Emergency stop - car (11) - only with ECO basic with manual doors
X100.18 I Emergency stop - car (12) - only with ECO basic with manual doors
X100.19 O Car door (11) - only with automatic doors
X100.20 I Car door (12) - only with automatic doors
X100.21 O Light curtain 1 (gn) - only with ECO basic with manual doors
X100.21a I Light curtain 1 (gr) - only with ECO basic with manual doors
X100.21b O Light curtain 2 (gn) - only with ECO basic with manual doors
X100.21c I Light curtain 2 (gr) - only with ECO basic with manual doors
X100.21d OLight curtain 3 (gn) - only with ECO basic with manual doors
X100.22 ILight curtain 3 (gr) - only with ECO basic with manual doors
X100.23 O Folding support - car roof - NC (11)
X100.24 I Folding support - car roof - NC (12)
X100.25 OFolding support - car roof - NO (13)
X100.26 I Folding support - car roof - NO (14)
Terminal strip X101 (24V supply):
Terminal I/O Description
X101.1-3 O +24V supply
X101.4-6 O+0V supply
Floor adapter A140 (car calls / Lift Here):
Terminal I/O Description
1 I/O Travelling cable - car call / Lift Here - oor 00
2 I/O Travelling cable - car call / Lift Here - oor 01
3I/O Travelling cable - car call / Lift Here - oor 02
4 I/O Travelling cable - car call / Lift Here - oor 03
5I/O Travelling cable - car call / Lift Here - oor 04
6I/O Travelling cable - car call / Lift Here - oor 05
7I/O Travelling cable - door OPEN button
8 I/O Travelling cable - emergency call button - NO
9 O Travelling cable - power supply - car calls / Lift Here GND
10 O Travelling cable - power supply - car calls / Lift Here +24 V

Installation
Delivery contents
ECO manual
18
4 Installation
All important information on the installation procedure, installation conditions and settings for the ECO com-
ponents are described in this section. Special circumstances at the installation site may require an installation
procedure that differs from the one recommended here.
4.1 Delivery contents
ECO components and documentation:
› Control cabinet HST WxHxD = 500x750x175 mm
› Control-cabinet fastening set
› Wiring diagram
› ECO operating instructions (this manual)
› Frequency inverter operating instructions
› Brake resistor - inverter
› ECO car top box as sheet-metal box with terminal blocks and car call adapter
› Magnet switch (incl. connection cable, 2 m)
› Magnets
› Travelling cable for all 24V and 230V signals, prefabricated
› Travelling cable holder set
› Cable, Ölex, 5 x 1 mm² - for car door drives and car installation
› Cable, Ölex, 3 x 1 mm² - for car light and car installation
› Motor cable, 4 x 2.5 mm², shielded
› Cable, 3 x 1 mm², shielded for brake and motor thermistor
› Cable, Ölex, 6 x 0.75 mm², for shaft doors
› Cable, Ölex, 4 x 1 mm² - for safety circuit switch - shaft and monitoring switch of shaft doors
› EMERGENCY-OFF palm button for shaft pit
› Cable duct, 60 x 40 mm for shaft (delivered in two-metre rods)
› Car operating panel
› Call button AT33RM for shaft door frame (incl. 30 m at cable and plug)
4.2 Checking the delivery contents
►Use the shipping note, the system drawing and the wiring diagram to check the delivered ECO components
for completeness
►Visually inspect the delivery for damage
► When unpacking the delivery, check:
- whether there is any visible mechanical damage on the ECO components
- whether the labelling of the ECO components matches the designation in the wiring diagram
- whether the supplied cables are of sufcient length and quantity
4.3 Claiming damages during transport
If any damage occurred during transport, it must immediately be reported to the carrier.

Installation
Reordering ECO components
19
ECO manual
4.4 Reordering ECO components
If any ECO components or cables are missing, contact the NEW LIFT hotline immediately. We will need the
following information in order to help you as quickly as possible:
› 8-digit NEW LIFT factory number, e.g.: EP140181 (can be found in the wiring diagram)
› Designation of the missing component (can be found in the wiring diagram)
› Type and length of missing cable
› Your phone/fax number or e-mail address so we can contact you if necessary
4.5 Installing the control cabinet
►Transport the control cabinet to the planned installation location and install it there
►The type of mounting brackets to be used depends on the installation location and the weight of the control
cabinet and is to be selected by the installing engineer.
►Install the supplied mounting bracket
►Mount the control cabinet with the upper edge in the installed mounting bracket
►Mark the cable entry through the opening in the mounting plate on the shaft wall
►Dismount the control cabinet again and make an opening into the shaft through the marked entry
►After you have again mounted the control cabinet, secure the control cabinet with an additional screw in the
lower hole of the mounting plate
► The planned installation location can only be changed in exceptional cases, as the prefabricated cables
might not be adequate. Please inform the NEW LIFT hotline so a solution can be found.
Fig. 4.1: Control cabinet installation

Installation
Connecting the control cabinet
ECO manual
20
4.6 Connecting the control cabinet
ATTENTION!
Potential equalisation must be carried out in accordance with applicable
regulations and guidelines (VDE, DIN, EN and ISO) depending on the
power rating. The neutral and ground wires must be routed separately!
All cables and wires must be secured with sufficient strain relief.
Customer wiring is shown in dashed lines in the wiring diagrams,
factory wiring is shown in solid lines
ATTENTION!
The 230 V AC mains supply line at the installation site must be equipped
with a protective device (fuse) for isolating the entire control system!
The tripping current of this protective device should be 16A!
The use of residual current devices (RCD) is not recommended.
Before commissioning the control cabinet, the following connections must be made according to the wiring
diagram:
› Supply
› Drive
› Light
› Safety circuit
4.7 Installing and connecting the travelling cable
►Install the suspension brackets for the travelling cable in the shaft and on the car at a suitable location and
hang the travelling cable.
The turning point of the travelling cable lies at approximately half the shaft height.
The minimum bending radius of the travelling cable is 225 mm.
Note:
- the turning point of the at trailing cable lies at half the
shaft height
- the installation direction of the at trailing cable
On the NEW LIFT components, the at trailing cable is plugged into the car and the control system (see “Car
top box” on page 16).
Table of contents
Other New lift Control System manuals
Popular Control System manuals by other brands
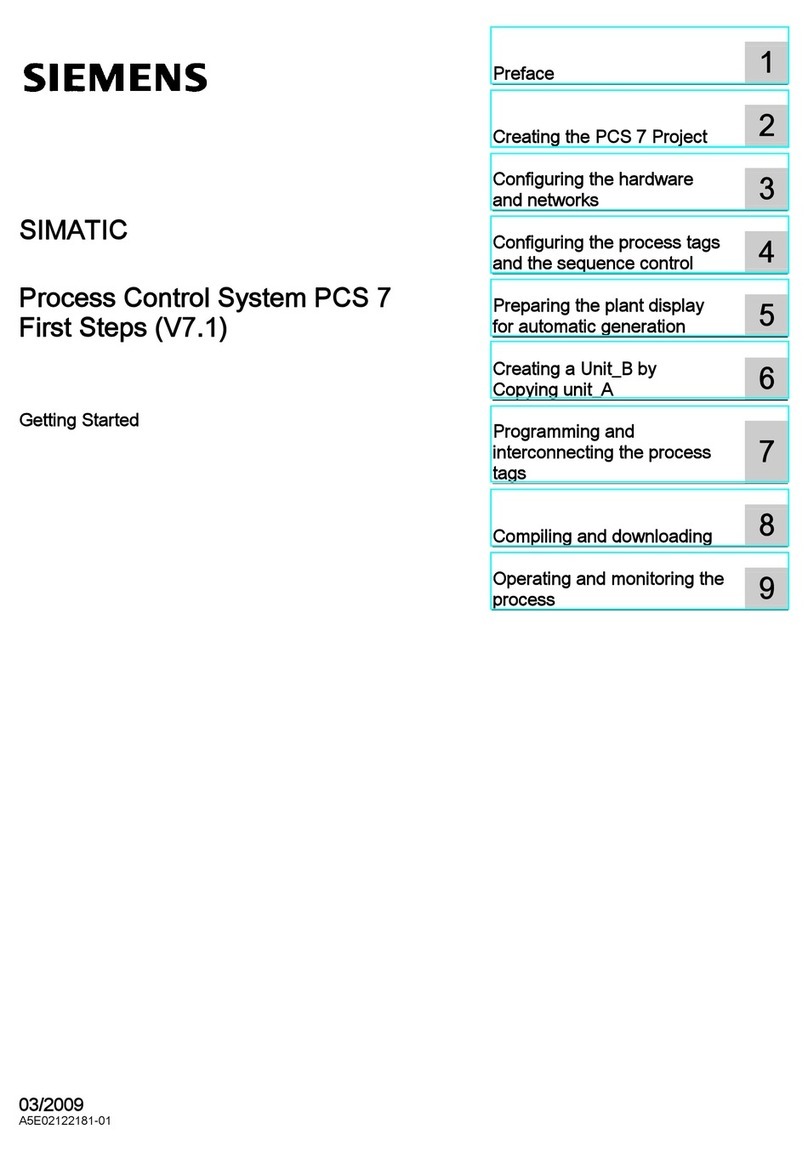
Siemens
Siemens SIMATIC PCS 7 Getting started
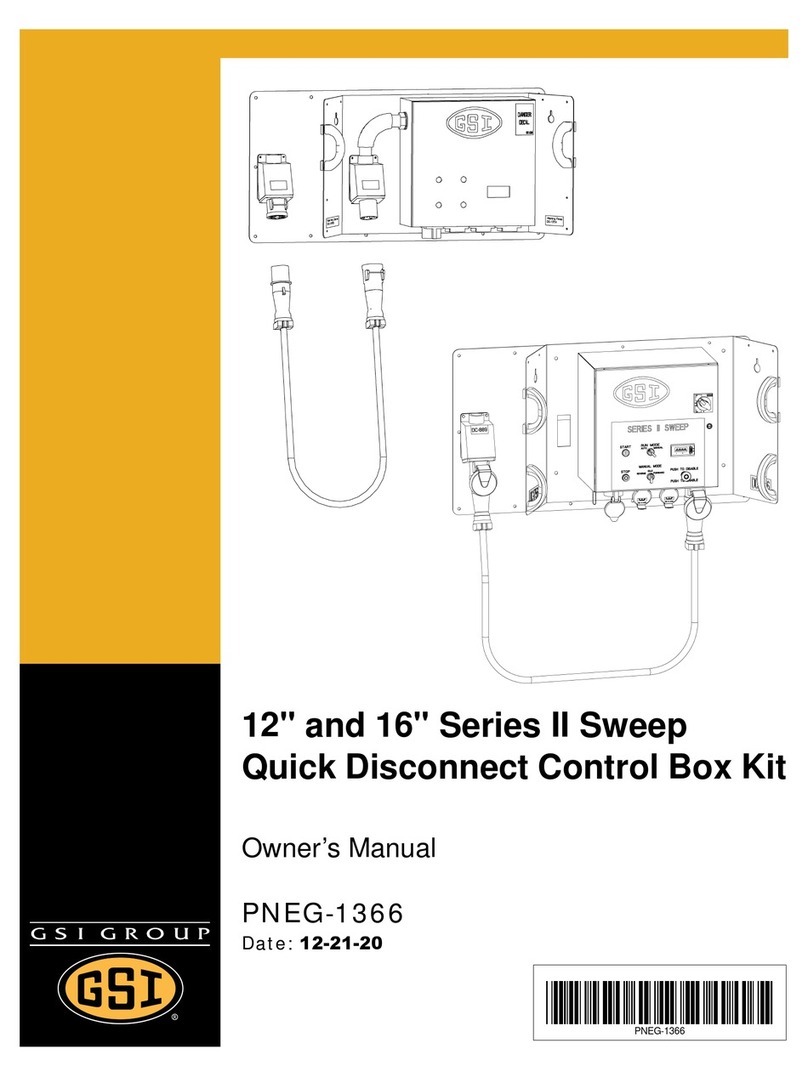
GSI Group
GSI Group II Sweep Series owner's manual
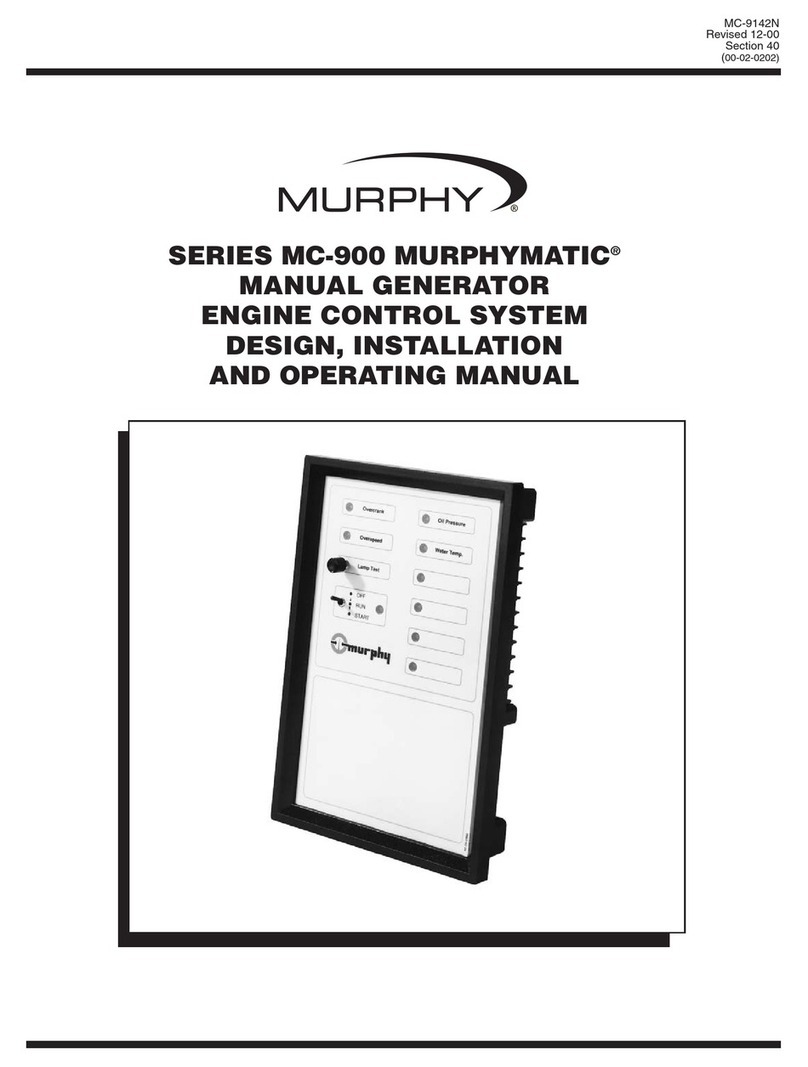
Murphy
Murphy MURPHYMATIC MC-900 Series Installation and operating manual
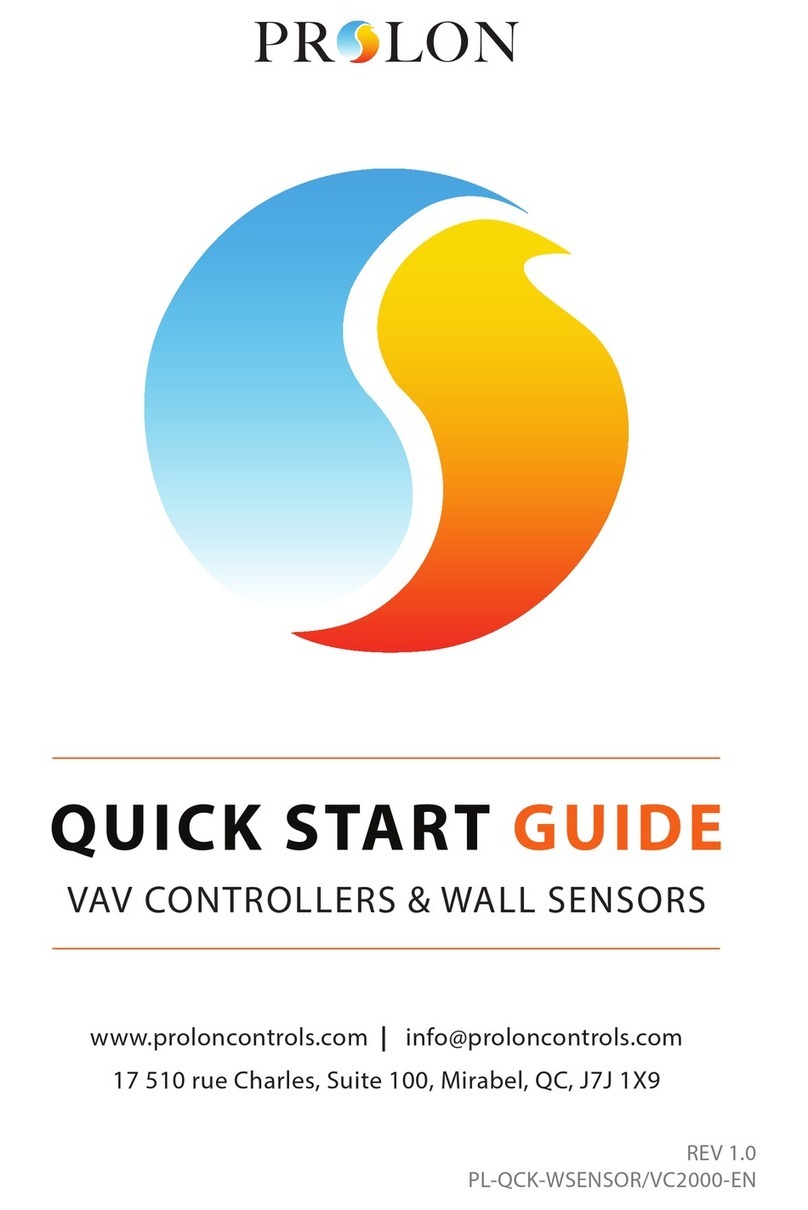
Prolon
Prolon PL-RS quick start guide
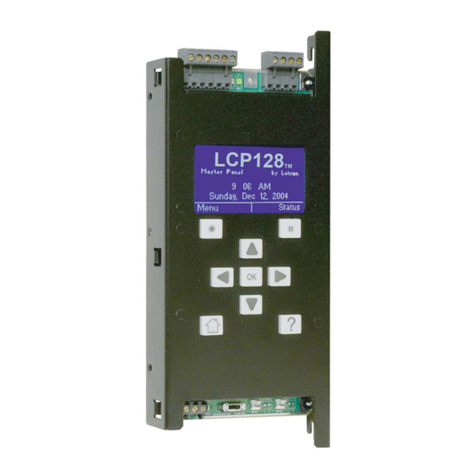
Lutron Electronics
Lutron Electronics LCP128 installation guide
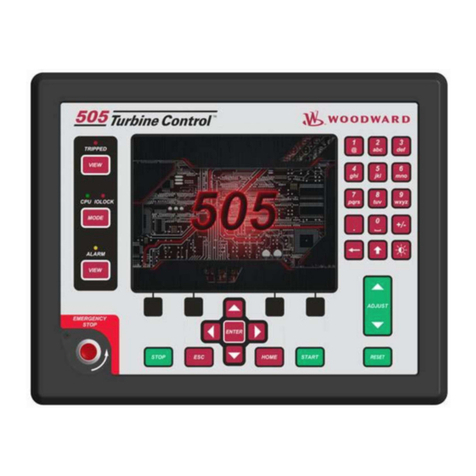
Woodward
Woodward 505HT Installation and operation manual