NI roboRIO 2.0 User manual

NI roboRIO 2.0 Embedded Controller for FRC User Manual2023-04-04

NI roboRIO 2.0 Embedded Controller for FRC
User Manual
IntroductionThe NI roboRIO 2.0 is a portable reconfigurable I/O (RIO) device that is used to
design control, robotics, and mechatronics systems.
This document contains pinouts, connectivity information, dimensions, and
mounting instructions for the NI roboRIO 2.0.
Physical FeaturesThe NI roboRIO 2.0 provides the I/O shown in the following figure and connects to a
host computer over USB and 10/100 Ethernet. © National Instruments3NI roboRIO 2.0 Embedded Controller for FRC User Manual

Figure 1. Features
5 V
S6 V
S
4 5 8 96 70 1 2 3
USERRESET
X
Z
Y
ACCELEROMETER
COPI
3.3 V
CIPO
CS
LK
5 V
CS 3
CS 2
C S1
C S0
R EV
4589 67 0123
32103
33 1
21
5 V S
S
0
FWD
SD
INPUT
7-16 V
45 W MAX
L (GRN)
3.3 V SDA
SCL
TXD
RXD
RS-232
DIO
RSL RELAY
PWM
ANALOG IN
I²C
H (YEL)
CAN
RSL
MODE
COMM
RADIO
STATUS
POW
ER
SPI
roboRIO 2.0
1. Digital input and output
(DIO) port
2. RS-232 port 3. I2C port
4. CAN port 5. Power connector 6. USB Device port
7. microSD card slot 8. USB Host ports 9. Ethernet port
10. Serial peripheral interface
bus (SPI) port
11. LEDs 12. Pulse-width modulation
(PWM) port
13. myRIO Expansion Port
(MXP)
14. MXP retention mount 15. User and Reset buttons
16. Analog input (AI) port 17. Relay port 18. Robot signal light (RSL) port
Physical DimensionsThe following figures describe the physical dimensions of the NI roboRIO 2.0
enclosure and its features.
ni.com4NI roboRIO 2.0 Embedded Controller for FRC User Manual

Figure 2. Dimensions, Primary Side
POWERED BYPOWERED BY
POWERPOWER
STATUS
STATUS
RADIO
RADIO
SPISPI
CS0CS0
CS1
CS1
5V
5V
CS2
CS2
CS3
CS3
SCLK
SCLK
COPI
COPI
CANCAN
L (GRN)L (GRN)
H (YEL)
H (YEL)
II2
2C
C
SCLSCL
3.3V SDA3.3V SDA
RS-232RS-232
TXDTXD
RXD
RXD
RSLRSL
CIPOCIPO
3.3V
3.3V
COMMCOMM
MODE
MODE
RSL
RSL
RELAYRELAY
0
011
FWDFWD
5V5V SS
S
S
REVREV
22330011
1
13333
2
233
332
2110
0
7
799886
6554
4
4455667
78899
0
0112
23
3
ANALOG INANALOG IN RESET
RESET
ACCELEROMETERACCELEROMETER
PWMPWM
DIODIO
YY
Z
ZX
X
USERUSER
SS
5V5V
SS6V
6V
INPUTINPUT
7-16V7-16V
45W MAX45W MAX
137.72 mm (5.422 in.)
128.01 mm (5.040 in.)
117.85 mm (4.64 in.)
101.01 mm (3.977 in.)
93.39 mm (3.677 in.)
85.77 mm (3.377 in.)
78.15 mm (3.077 in.)
73.08 mm (2.877 in.)
68.00 mm (2.677 in.)
60.38 mm (2.377 in.)
52.76 mm (2.077 in.)
45.14 mm (1.777 in.)
22.26 mm (0.876 in.)
8.44 mm (0.332 in.)
0.0 mm (0 in.)
0.0 mm (0 in.)
7.16 mm (0.282 in.)
8.42 mm (0.332 in.)
19.52 mm (0.769 in.)
135.47 mm (5.333 in.)
132.61 mm (5.221 in.)
130.72 mm (5.147 in.)
123.43 mm (4.860 in.)
110.96 mm (4.368 in.)
99.54 mm (3.919 in.)
88.10 mm (3.469 in.)
80.48 mm (3.169 in.)
72.86 mm (2.869 in.)
65.24 mm (2.569 in.)
57.62 mm (2.269 in.)
50.00 mm (1.969 in.)
42.38 mm (1.669 in.)
34.76 mm (1.369 in.)
27.14 mm (1.069 in.)
129.83 mm (5.111 in.)
116.64 mm (4.592 in.)
94.67 mm (3.727 in.)
74.55 mm (2.935 in.)
49.45 mm (1.947 in.)
29.58 mm (1.164 in.)
9.71 mm (0.382 in.)
8.93 mm (0.352 in.)
8.44 mm (0.332 in.)
129.21 mm (5.087 in.)
126.94 mm (4.998 in.)
88.50 mm (3.484 in.)
80.88 mm (3.184 in.)
74.70 mm (2.941 in.)
65.64 mm (2.584 in.)
58.02 mm (2.284 in.)
54.40 mm (1.984 in.)
42.78 mm (1.684 in.)
42.58 mm (1.677 in.)
35.16 mm (1.384 in.)
27.54 mm (1.084 in.)
19.92 mm (0.784 in.)
8.09 mm (0.319 in.)
© National Instruments5NI roboRIO 2.0 Embedded Controller for FRC User Manual

Figure 3. Dimensions, Primary Side LEDs
POWERED BYPOWERED BY
POWERPOWER
STATUS
STATUS
RADIO
RADIO
SPISPI
CS0CS0
CS1
CS1
5V
5V
CS2
CS2
CS3
CS3
SCLK
SCLK
COPI
COPI
CANCAN
L (GRN)L (GRN)
H (YEL)
H (YEL)
II2
2C
C
SCLSCL
3.3V SDA3.3V SDA
RS-232RS-232
TXDTXD
RXD
RXD
RSLRSL
CIPOCIPO
3.3V
3.3V
COMMCOMM
MODE
MODE
RSL
RSL
RELAYRELAY
0
011
FWDFWD
SS
S
S
REVREV
22330011
1
13333
2
233
332
2110
0
7
7998866554
4
4455667
78899
0
0112
23
3
ANALOG INANALOG IN RESET
RESET
ACCELEROMETERACCELEROMETER
PWMPWM
DIODIO
YY
Z
ZX
X
USERUSER
SS
SS
5V5V
5V5V
6V6V
INPUTINPUT
7-16V7-16V
45W MAX45W MAX
146.15 mm (5.754 in.)
0.0 mm (0 in.)
0.0 mm (0 in.)
143.18 mm (5.637 in.)
128.51 mm (5.059 in.)
143.68 (5.657 in.)
123.51 mm (4.862 in.)
116.01 mm (4.567 in.)
111.01 mm (4.370 in.)
106.01 mm (4.173 in.)
98.51 mm (3.878 in.)
ni.com6NI roboRIO 2.0 Embedded Controller for FRC User Manual

Figure 4. Dimensions, Secondary Side
22.28 mm (0.877 in.)
0.0 mm (0 in.)
123.88 mm (4.877 in.)
122.39 mm (4.819 in.)
20.79 mm (0.819 in.)
135.09 mm (5.319 in.)
8.09 mm (0.319 in.)
0.0 mm (0 in.)
3.84 mm (0.151 in.)
142.31 mm (5.603 in.)
4-40 Screw Insert
Figure 5. Dimensions, Side
5.71 mm (0.225 in.)
129.59 mm (5.102 in.)
122.39 mm (4.819 in.)
20.79 mm (0.819 in.)
13.59 mm (0.535 in.)
0.0 mm (0 in.)
0.0 mm (0 in.)
6.03 mm (0.238 in.)
20.91 mm (0.823 in.)
22.76 mm (0.896 in.)
34.43 mm (1.355 in.)
32.19 mm (1.267a in.)
Mounting the NI roboRIO 2.0You can mount the NI roboRIO 2.0 in the following ways: © National Instruments7NI roboRIO 2.0 Embedded Controller for FRC User Manual

■Using cable ties to secure one edge of the NI roboRIO 2.0 to perfboard with
6.35 mm (0.25 in.) diameter holes on 12.7 mm (0.5 in.) straight centers, such as
AndyMark part number am-0836.
■Using cable ties to secure one corner of the NI roboRIO 2.0 to perfboard.
■Using screws to secure the bottom of the NI roboRIO 2.0 to a metal plate.
Method One: Using Cable Ties to Secure One Edge of the NI roboRIO 2.0 to
Perfboard
The following figures show how to secure one edge of the NI roboRIO 2.0 to
perfboard.
Figure 6. Step 1 to Secure One Edge of the Device
Figure 7. Step 2 to Secure One Edge of the Device
ni.com8NI roboRIO 2.0 Embedded Controller for FRC User Manual

Figure 8. Step 3 to Secure One Edge of the Device
Figure 9. Step 4 to Secure One Edge of the Device
Method Two: Using Cable Ties to Secure One Corner of the NI roboRIO 2.0
to Perfboard
The following figures show how to secure one corner of the NI roboRIO 2.0 to
perfboard. © National Instruments9NI roboRIO 2.0 Embedded Controller for FRC User Manual

Figure 10. Step 1 to Secure One Corner of the Device
Figure 11. Step 2 to Secure One Corner of the Device
ni.com10NI roboRIO 2.0 Embedded Controller for FRC User Manual

Figure 12. Step 3 to Secure One Corner of the Device
Figure 13. Step 4 to Secure One Corner of the Device © National Instruments11NI roboRIO 2.0 Embedded Controller for FRC User Manual

Figure 14. Step 5 to Secure One Corner of the Device
Method Three: Using Screws to Secure the Bottom of the NI roboRIO 2.0
to a Metal Plate
The following figure shows how to secure the bottom of the NI roboRIO 2.0 to a
metal plate using the built-in 4-40 screw holes. The length of the screws required
depends on the thickness of the plate you use. For example, if the plate is 4.76 mm
(0.188 in.) thick, the recommended screw length is 7.94 mm (0.313 in.).
Figure 15. Mounting NI roboRIO 2.0 Using Screws
2
1
ni.com12NI roboRIO 2.0 Embedded Controller for FRC User Manual

1. Metal Mounting Plate 2. 4-40 Screws x 4
Compatible USB and Ethernet CablesThe following table lists the USB and Ethernet cables available from NI that you can
use with the NI roboRIO 2.0.
Table 1. Compatible USB and Ethernet Cables Available from NI
Cable Description NI Part Number
USB cable USB 2.0 A/B, black, 1 m 192256A-01
Peripheral USB cable USB 2.0 A/A, locking, black, 2 m 152166A-02
Ethernet cable CAT-5E, thin profile, 2 m 151733A-02
Caution To ensure the specified EMC performance, the maximum length
for DIO, RS-232, I2C, CAN, SPI, PWM, AI, Relay, and RSL signal wires is 2.0
m (6.56 ). The maximum length for USB cables is 5.0 m (16.40 ). The
maximum length for Ethernet cables is 30.0 m (98.43 ).
Setting Up the NI roboRIO 2.0Connecting to Power
The NI roboRIO 2.0 requires an external power supply that meets the specifications
in the Power Requirements section of the NI roboRIO 2.0 Specifications. The
NI roboRIO 2.0 filters and regulates the supplied power and provides power for all
of the I/O and user voltage. The NI roboRIO 2.0 has one layer of reverse-voltage
protection.
Complete the following steps to connect a power supply to the chassis.
1. Ensure that the power supply is turned o.
Caution Do not install or remove the power connector from the
front panel of the NI roboRIO 2.0 while power is applied.
© National Instruments13NI roboRIO 2.0 Embedded Controller for FRC User Manual

2. Connect the positive lead of the power supply to the V terminal of the
COMBICON power connector shipped with the NI roboRIO 2.0, and tighten the
terminal screw. The following figure shows the terminal screws, which secure
the wires in the screw terminals, and the connector screws, which secure the
power connector on the front panel.
Figure 16. COMBICON Power Connector
C
V
2
2
1
1. Terminal Screws
2. Connector Screws
3. Connect the negative lead of the power supply to the C terminal of the power
connector and tighten the terminal screw.
4. Install the power connector on the front panel of the NI roboRIO 2.0 and
tighten the connector screws.
5. Turn on the power supply.
Powering On the Device
The NI roboRIO 2.0 runs a power-on self test (POST) when you apply power to the
device. During the POST, the Power and Status LEDs turn on. When the Status LED
turns o, the POST is complete. If the LEDs do not behave in this way when the
system powers on, refer to the LED Indications section.
Connecting to a Network
Connect the NI roboRIO 2.0 to an Ethernet network using the Ethernet port. Use
a standard Category 5 (CAT-5) or better shielded, twisted-pair Ethernet cable to
connect the NI roboRIO 2.0 to an Ethernet hub, router, or directly to a computer.
Caution To prevent data loss and to maintain the integrity of your
Ethernet installation, do not use a cable longer than 30 m.
ni.com14NI roboRIO 2.0 Embedded Controller for FRC User Manual

The first time you power up the chassis, it attempts to initiate a DHCP network
connection. If the chassis is unable to initiate a DHCP connection, it connects to the
network with a link-local IP address with the form 169.254.x.x.
User Power
The following table describes the user voltage rails for powering external sensors
and peripherals. The rails are independent from the power supplies of internal
systems, such as the processor and memory.
Table 2. Voltage Rails
Voltage Rail Description
+6 V Power from PWM ports for use with servos.
+5 V Power for DIO and AI ports for sensors, and
power for the MXP for powering expansion
circuits.
+3.3 V Power for I2C, SPI, and the MXP.
Input Voltage Brownout Behavior
The input voltage range on the NI roboRIO 2.0 is 7 V to 16 V. Operation below 7 V is
allowed for short periods of time but is not recommended for continuous operation.
The brownout threshold voltage on the NI roboRIO 2.0 can be user-configured. By
default, the threshold is 7 V.
The input voltage monitoring circuit monitors the voltage on the input voltage pin.
When the input voltage drops to the brownout threshold voltage, the NI roboRIO 2.0
enters brownout mode with a staged response, as the following table describes.
Table 3. Input Voltage Brownout Behavior
Stage Input Voltage Range Behavior
1 4.5 V to brownout threshold
voltage
The NI roboRIO 2.0 enters a
brownout fault condition and
© National Instruments15NI roboRIO 2.0 Embedded Controller for FRC User Manual

Stage Input Voltage Range Behavior
the following precautions are
taken:
■+6 V voltage rail is
disabled
■All PWM generation
stops at the conclusion of
the current cycle.
■GPIOs configured as
outputs go to High-Z.
■Relay control outputs
are driven low.
■CAN-based motor
controllers become
disabled.
The following systems continue
to function normally with valid
data and communication:
■FPGA, processor, RAM,
disk, and user code
■+5 V and +3.3 V voltage
rails
■USB power and
communication
■Radio, if powered by
USB
■Ethernet
■CAN
■AI and AO
■I2C
■SPI
■RS-232 serial
■LED and RSL status
lights
Stage 1 continues until
the input voltage rises to
ni.com16NI roboRIO 2.0 Embedded Controller for FRC User Manual

Stage Input Voltage Range Behavior
greater than the brownout
threshold voltage+hysteresis
(default 7.85 V) or drops to less
than 4.5 V.
2 Less than 4.5 V All controller functions cease
and the controller state is
lost. This condition continues
until the input voltage rises to
greater than 4.65 V, at which
point the controller starts the
normal booting sequence.
At startup, the controller
remains in Stage 1 until the
input voltage rises to greater
than the brownout threshold
voltage.
Hardware Block DiagramThe following figure shows the arrangement and functions of NI roboRIO 2.0
components. © National Instruments17NI roboRIO 2.0 Embedded Controller for FRC User Manual

Figure 17. NI roboRIO 2.0 Hardware Block Diagram
CAN
Port
Xilinx Zynq-7020
Processor/FPGA
(LabVIEW RT)
USB
Device
Port
USB
Host
Ports
10/100
Ethernet
Port
Status LED
Comm LED
Radio LED
Mode LED
RSL LED
Power LED
+3.3 V
+5.0 V
16 16
2
4
UART
DIO
Analog Out
Analog In
myRIO
Expansion
Port (MXP)
User
Button
Reset
Button
PWM
Port
10
10
+6.0 V
PWM
SPI
SPI Port
+5.0 V
+3.3 V
7
7
2
RS-232
RS-232
Port
2
I
2
C
I2C
Port
2
+3.3 V
DIO
Port
DIO
10 10
+5.0 V
Watchdog
Nonvolatile
Memory
DDR3
Acceler-
ometer
RSL
RSL
Port
Relay
8
8
RELAY
Port
4
+5.0 V
AI
ANALOG IN
Port
microSD
Card
PinoutsThe following describe the pins and signals on the NI roboRIO 2.0 ports.
MXP
The following figure and table describe the MXP pins and signals. Note that some
pins carry both primary and secondary functions.
ni.com18NI roboRIO 2.0 Embedded Controller for FRC User Manual

Figure 18. MXP Pinout
AO0
AO1
AGND
DGND
UART.RX
DGND
UART.TX
DGND
DIO11 / ENC.A
DGND
DIO12 / ENC.B
DGND
DIO13
DGND
DGND
DIO14 / I2C.SCL
DIO15 / I2C.SDA
+5V
AI1
AI3
AI2
DIO1
DIO2
DIO3
DIO4
AI0
DIO0
DIO5 / SPI.CLK
DIO6 / SPI.CIPO
DIO7 / SPI.COPI
DIO8 / PWM0
DIO9 / PWM1
DIO10 / PWM2
+3.3V
34
33
32
31
30
29
28
27
26
25
24
23
22
21
20
19
18
17
16
15
14
13
12
11
10
9
8
7
6
5
4
3
2
1
133
Table 4. MXP Signal Descriptions
Signal Name Reference Direction Description
+5V DGND Output +5 V power output.
AI <0..3> AGND Input 0 V to 5 V, referenced,
single-ended AI
channels. Refer to the
AI Channels section for
more information.
AO <0..1> AGND Output 0 V to 5 V referenced,
single-ended AO. Refer
to the AO Channels
section for more
information.
AGND — — Reference for AI and
AO.
+3.3V DGND Output +3.3 V power output.
DIO <0..15> DGND Input or Output General-purpose
digital lines with 3.3
V output, 3.3 V-/5 V-
compatible input. Refer
to the DIO, PWM, and
Relay Lines section for
more information.
UART.RX DGND Input UART receive input.
UART lines are
© National Instruments19NI roboRIO 2.0 Embedded Controller for FRC User Manual
Table of contents
Other NI Controllers manuals
Popular Controllers manuals by other brands
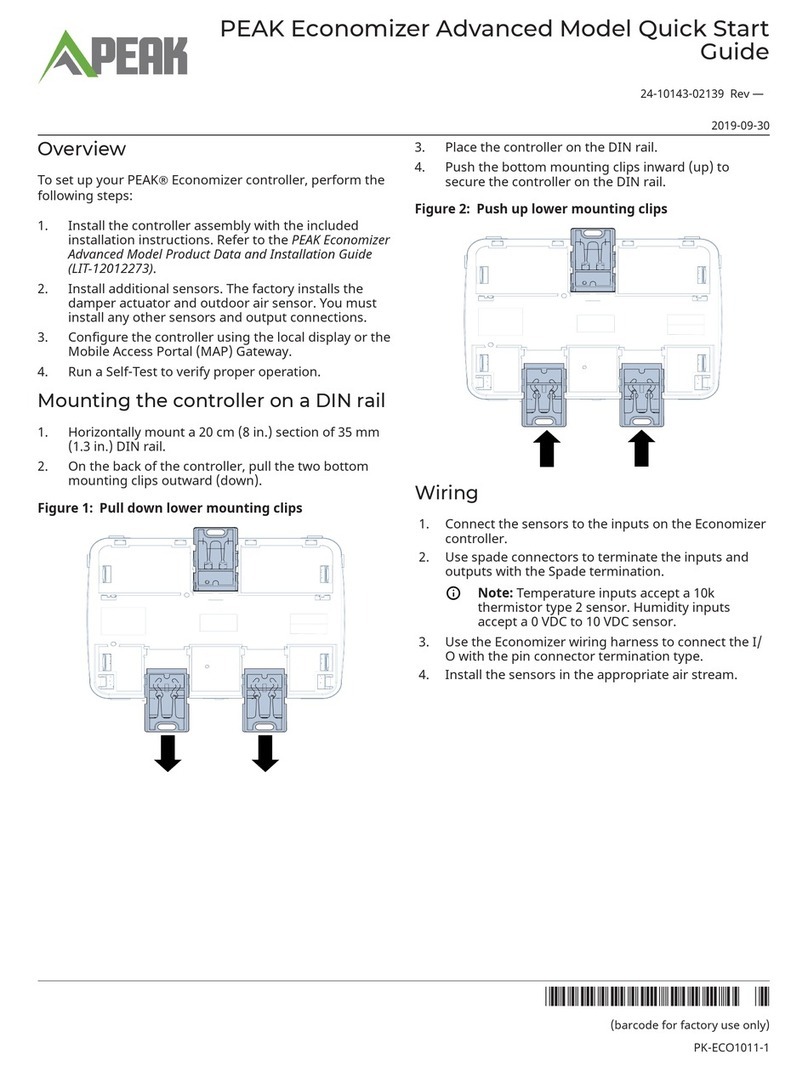
Peak
Peak Economizer Advanced PK-ECO1011-1 quick start guide
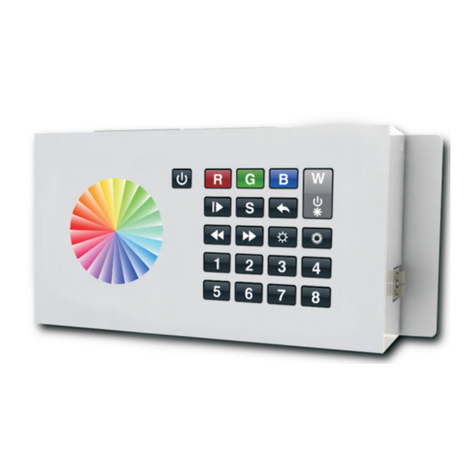
Sunricher
Sunricher SR-2816 user manual
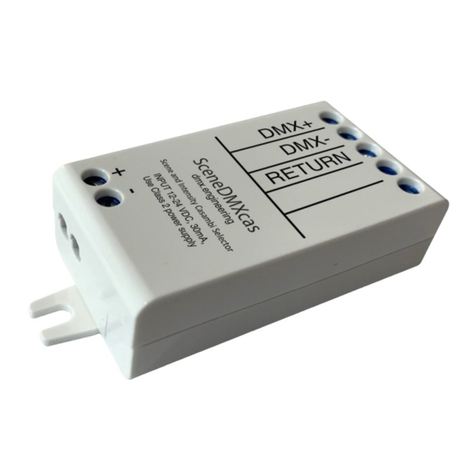
DMX
DMX Casambi SceneDMXcas Installation

Unitronics
Unitronics US5-B10-RA28 installation guide
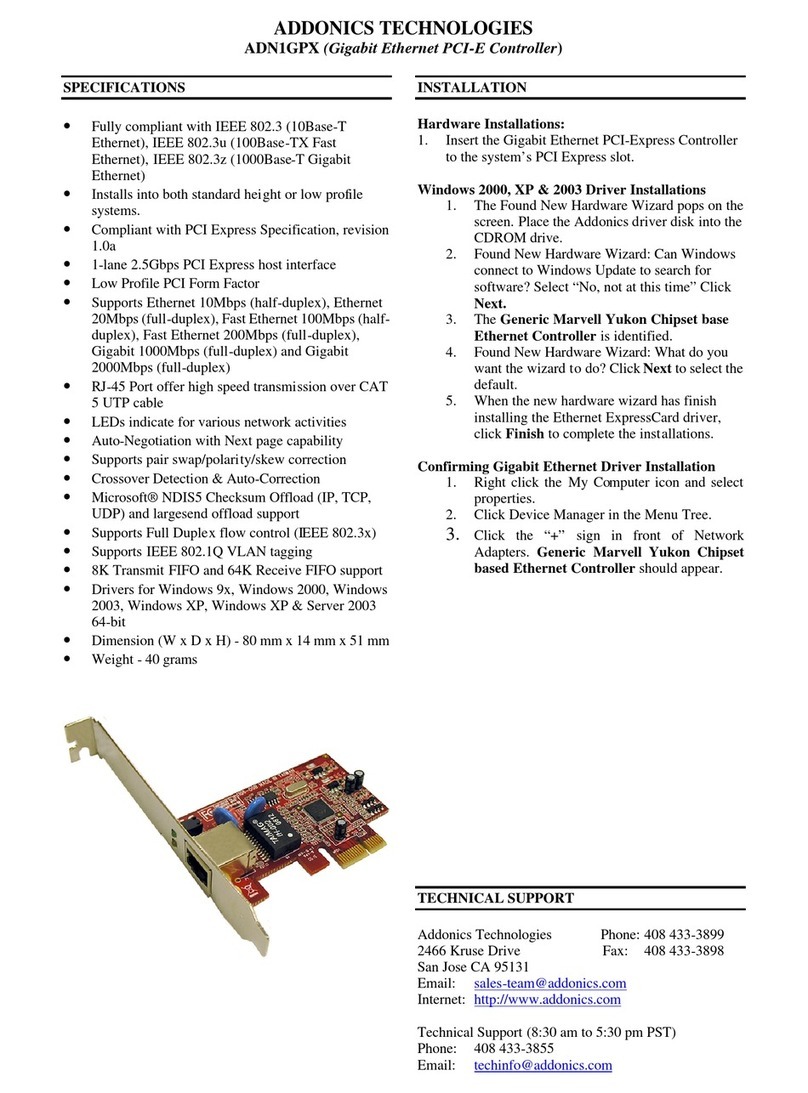
Addonics Technologies
Addonics Technologies ADN1GPX Specification & installation guide
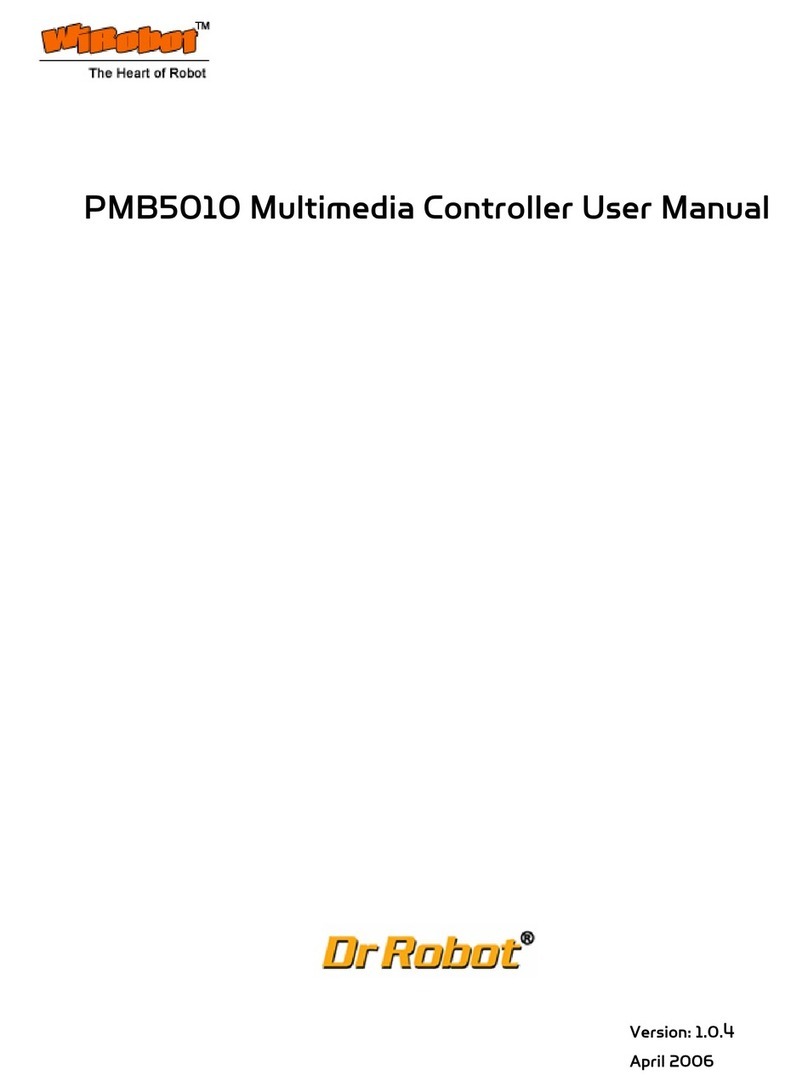
WiRobot
WiRobot DrRobot PMB5010 user manual