Noblelift CG1646 User manual

NOBLELIFT EQUIPMENT
Service & Maintenance Manual
Power Sacker
CG1646
V-CG1646-01.00 Date: 2011-2-10

2
CONTENTS
FOREWORD..............................................................................................................................................3
1. GENERAL...........................................................................................................................................4
1.1 INTRODUCTION – MAINTENANCE SAFETY PRECAUTIONS.............................................. 4
1.2 MEASUREMENT CONVERSIONS ...........................................................................................8
2. SPECIFICATION ..............................................................................................................................13
2.1 LOCATION OF COMPONENTS..............................................................................................13
2.2 SPECIFICATION SHEETS....................................................................................................16
2.2.1 Technical Features..............................................................................................................16
2.2.2 Residual Capacity at different lifting height.....................................................................16
2.3 LUBRICATION ......................................................................................................................16
3ELECTRIC SYSTEM ........................................................................................................................18
3.1 ELECTRIC DIAGRAM.............................................................................................................18
3.2 CABLE SYSTEM………………………………………………………………………………….....20
3.3 DRIVE WHEEL.........................................................................................................................23
3.4 PUMP STATION ......................................................................................................................23
3.5 BATTERY.................................................................................................................................23
3.6 CHARGER ...............................................................................................................................28
3.7 CURTIS CONTROLLER..........................................................................................................33
3.8 BATTERY INDICATOR ...........................................................................................................40
3.9 REPLACE THE ELECTRIC PARTS........................................................................................42
3.10 TOOL FOR REPAIRING THE PIN OF ELECTRIC PLUG ......................................................47
3. HYDRAULIC SYSTEM.....................................................................................................................48
4.1 OPERATION OF PUMP STATION .......................................................................................49
4.2 REPLACE THE CYLINDER ....................................................................................................51
5. DRIVE WHEEL..................................................................................................................................52
5.1 THE DRIVE WHEEL...............................................................................................................52
5.2 REPLACE THE DRIVE WHEEL…………………………………………………………………..52
5.3 REPLACE THE CARBON BRUSH KIT................................................................................56
5.4 REPLACE THE BRAKE........................................................................................................57
5.5 ADJUST THE CLEARANCE OF THE BRAKE ....................................................................57
6. CONTROL HANDLE ........................................................................................................................59
6.1 OPERATION OF THE CONTROL HANDLE.............................................................................61
6.2 OPERATION OF THE AIR SPRING AND MICRO SWITCH..................................................62
7. CASTER WHEEL .............................................................................................................................64
8. OPERATION OF THE INTERNAL MAST........................................................................................64
9. TROUBLE DIAGNOSTICS...............................................................................................................65
9.1 MAINTENANCE LIST..............................................................................................................65
9.2 TROUBLE SHOOT..................................................................................................................66

3
FOREWORD
Proper operation, maintenance, troubleshooting and repairs are necessary to preserve the performance
of the stacker over along period of time and ensure that fault and breakdowns do not occur. The object of
this service manual is to provide the information necessary especially in connection with the
performance of inspections and repairs mainly in the maintenance areas.
The majority of this stacker consists of steel, it can be completely recycled. Waste
material in conjunction with repairs,maintenance, cleaning or scrapping, must be collected and disposed
of in an environment-friendly way and in accordance with the directives of respective countries. Such
work must be carried out in areas intended for this purpose. Recyclable material should be taken care of
by specialized authorities. Environmentally hazardous waste, such as oil filters, batteries and electronics,
will have a negative effect on the environment, or health, if handled incorrectly.
All of the information reported herein is based on data available at the moment of
printing. Our products are constantly being developed and renewed, we reserves the right to modify our
own products at any moment without prior notice and incurring in any sanction. So, it is suggested to
always verify possible updates.

4
1. GENERAL
1.1 INTRODUCTION – MAINTENANCE SAFETY PRECAUTIONS
Careless performing of the easy work may cause injuries. Take care to always perform work safely, at
least observing the following. It is of utmost importance that maintenance personnel pay strict attention
to these warnings and precautions to avoid possible injury to themselves or others, or damage to the
equipment. A maintenance program must be followed to ensure that the machine is safe to operate.
The specific precautions to be observed during maintenance are inserted at the appropriate point in the
manual. These precautions are, for the most parts, those that apply when servicing hydraulic and larger
machine component parts.
MODIFICATION OF THE MACHINE WITHOUT CERTIFICATION BY A
RESPONSIBLE AUTHORITY THAT THE MACHINE IS AT LEAST AS SAFE AS ORIGINALLY
MANUFACTURED, IS A SAFETY VIOLATION.
SINCE THE MACHINE MANUFACTURER HAS NO DIRECT CONTROL OVER THE
FIELD INSPECTION AND MAINTENANCE, SAFETY IN THIS AREA RESPONSIBIUTY OF THE
OWNER OR OPERATOR.
FAILURE TO COMPLY WITH SAFETY PRECAUTIONS LlSTED IN THIS SECTION
MAY RESULT IN MACHINE DAMAGE, PERSONNEL INJURY OR DEATH AND IS A SAFETY
VIOLATION.
When carrying out any operation or maintenance, have trained and experienced personnel carry out
the work.
When carrying out any operation or maintenance, carefully read out Operation and Maintenance
Manual.
Read all the precautions given on the decals which are fixed to the machine.
Be sure you fully understand the contents of the operation. It is important to prepare necessary tools
and parts and to keep the machine.
Your safety, and that of others , is the first consideration when
engaging in the maintenance of equipment. Always be conscious of
weight. Never attempt to move heavy parts without the aid of a
mechanical device. Do not allow heavy objects to rest in an
unstable position. When raising a portion of the equipment, ensure
that adequate support is provided.

5
It should be noted that the machines hydraulic systems operate at
extremely high potentially dangerous pressures. Every effort should
be made to relieve any system pressure prior to disconnecting or
removing any portion of the system. Relieve system pressure by
cycling the applicable cntrol several times with the engine(motor)
stopped and ignition on, to direct any line pressure back into the
reservoir. Pressure feed lines to system components can then be
disconnected with minimal fluid loss.
Remove all ringd, watches and jewelry when performing any maintenance.
Wear well-fitting helmet, safety shoes and working Clothes When
drilling grinding or hammering always. Wear protective goggles.
Always do up safety clothes properly so that they do. Not catch on
protruding parts of machines. Do not wear oily clothes. When
checking, always release battery plug. DO NOT WEAR LONG
HAIR UNRESTRAINED, OR LOOSE-FITTING CLOTHING AND
NECKTIES WHICH ARE APT TO BECOME CAUGHT ON OR
ENTANGLED IN EQUIPMENT.
During maintenance do not allow any unauthorized person, to
stand near the machine.
Flames should never be used instead of lamps. Never use a naked
flame to check leaks or the level of oil or electrolyte.
Immediately remove any oil or grease on the floor of the operator’s
compartment or on the handrail. It is very dangerous if someone slips
while on the machine.
Always use pure oil or grease, and be sure to use clean containers.
Oil is a dangerous substance. Never handle oil, grease or oily
clothes in places where there is any fire or flame. As
preparation for use of fire extinguishers and other fire- fighting
equipment.
Keep the battery away from fire hazards. The generated gases
are explosive.
Store all the oils in a specified place.
Keep the flammable things away from the machine. Do not
smoke int the working site.

6
Battery should always be disconnected during replacement of electrical components.
Always use the grades of grease and oil recommended by NOBLELIFT choose the viscosity
specified for the ambient temperature.
Exhaust gas is dangerous provide ventilation when working in a closed
space.
Avoid breathing dust that may be generated when handling components
containing asbestos fibers. Wear a gas mask if necessary.
When working on top of the machine, be careful not to lose your balance
and fall.
Hand a caution sign in the operator’s compartment (for example “Do not
start” of “Maintenance in progress”). This will prevent anyone from
starting or moving the machine by mistake.
When welding on the machine or working on the electical
system, ALWAYS turn the key switch OFF and remove the
battery plug from the battery. Park the machine on firm, flat
ground. Lower the fork to the min. height and stop the motor.
Sulfuric acid in battery electrolyte is poisonous. Ist is strong
enough to burn skin and eat holes in clothing. If you spill acid
on your clothes or skin, immediately jlush with large quantities
or water.
When working on the battery, wear goggles or safety glasses.
If splashed into the eyes, flush with water and get medical
attention immediately.
Battery terminals touched by metal objects can cause short
circuit and burn you. Keep tools away from the terminals.
Keep sparks, lighted matches, and open flame away from the
top of battery. Battery (hydrogen) gas can explode.
When disassembling and assembling the battery, make sure
that the battery terminals (+, –) are correctly connected.
If water gets into the electrical system, abnormal operation or
failure can result. Do not use water or steam on sensors,
connectors and instruments in the cab.
Do not handle electrical equipment while wearing wet gloves, or in wet places, as this can cause
electric shock.

7
When working with others, choose a group leader and work according to his instructions. Do not
perform any maintenance beyond the agreed work.
Unless you have special instructions to the contrary, maintenance should always be carried out with
the motor stopped. If maintenance is carried out with the motor running, there must be two men
present : one operating the stacker and the other one performing the maintenance. In such a case,
never touch any moving part.
Before making adjustment, lubricating or performing any other maintenance, shut off all power
controls.
When removing parts containing O-ring Gaskets or seal clean the mounting surface and replace
with new sealing parts.
Thoroughly clean the machine. In particular, be careful to clean the grease fittings and the area
around the dipsticks. Be careful not to let any dirt or dust into the system.
Use only approved, nonflammable cleaning solvents.
When changing the oil or fitter, check the drained oil and filter for any signs of excessive metal
particles or other foreign materials.
Always use NOBLELIFT genuine parts for replacement. ENSURE REPLACEMENT PARTS OR
COMPONENTS ARE IDENTICAL OR EQUIVALENT TO ORIGINAL PARTS OR COMPONENTS.
When checking an open gear case, there is a risk of dripping things in. Before removing the covers
to inspect such cases, empty everything from your pockets. Be particularly careful to remove
wrenches and nuts.
Do not allow anyone to stand or walk under the elevated forks or load.
Never use the forks to lift people.

8
1.2 MEASUREMENT CONVERSIONS
Length
Unit cm m km in ft yd mile
cm 1 0.01 0.00001 0.3937 0.03281 0.01094 0.000006
m 100 1 0.001 39.37 3.2808 1.0936 0.00062
km 100000 1000 1 39370.7 3280.8 1093.6 0.62137
in 2.54 0.0254 0.000025 1 0.08333 0.02777 0.000015
ft 30.48 0.3048 0.000304 12 1 0.3333 0.000189
yd 91.44 0.9144 0.000914 36 3 1 0.000568
mile 160930 1609.3 1.6093 63360 5280 1760 1
1mm=0.1cm, 1µm=0.001mm
Area
Unit cm2 m2 km2 a ft2 yd2 in2
cm2 1 0.0001 – 0.000001 0.001076
0.000012 0.155000
m2 10000 1 0.000001 0.01 10.764 1.1958 1550.000
km2 – 1000000 1 10000 1076400 1195800 –
a 0.01 100 0.0001 1 1076.4 119.58 –
ft2 – 0.092903 – 0.000929 1 0.1111 144.000
yd2 – 0.83613 – 0.008361 9 1 1296.00
in2 6.4516 0.000645 – – 0.006943
0.000771 1
1ha=100a, 1mile2=259ha=2.59km2
Volume
Unit cm3 = cc m3 l in3 ft3 yd3
cm3 = m l 1 0.000001 0.001 0.061024 0.000035 0.000001
m3 1000000 1 1000 61024 35.315 1.30796
l 1000 0.001 1 61.024 0.035315 0.001308
in3 16.387 0.000016 0.01638 1 0.000578 0.000021
ft3 28316.8 0.028317 28.317 1728 1 0.03704
yd3 764529.8 0.76453 764.53 46656 27 1
1gal(US)=3785.41 cm3=231 in3=0.83267gal(US)
Weight
Unit g kg t oz lb
g 1 0.001 0.000001 0.03527 0.0022
kg 1000 10 0.001 35.273 2.20459
t 1000000 1000 1 35273 2204.59
oz 28.3495 0.02835 0.000028 1 0.0625
lb 453.592 0.45359 0.000454 16 1
1 tonne(metric)=1.1023 ton(US)=0.9842 ton(UK)

9
Pressure
Unit kgf/cm2 bar Pa=N/m2 kPa lbf/in2 lbf/ft2
kgf/cm2 1 0.98067 98066.5 98.0665 14.2233 2048.16
bar 1.01972 1 100000 100 14.5037 2088.6
Pa=N/m2 0.00001 0.001 1 0.001 0.00015 0.02086
kPa 0.01020 0.01 1000 1 0.14504 20.886
lbf/in2 0.07032 0.0689 6894.76 6.89476 1 144
lbf/ft2 0.00047 0.00047 47.88028 0.04788 0.00694 1
kgf/cm2=735.56 Torr(mmHg)=0.96784atm
Standard tightening torque
The following charts give the standard tightening torques of bolts and nuts.
Exceptions are given in sections of “Disassembly and Assembly”
METER TABLE
Classification 4T, 5T 10T
Bolt type
Bolt size Torque kgf · m (lbf · ft) Torque kgf · m (lbf · ft)
M4 0.2 ± 0.02 0.4 ± 0.04
M5 0.3 ± 0.03 0.8 ± 0.08
M6 0.5 ± 0.05 1.4 ± 0.14
M8 1.2 ± 0.12 3.3 ± 0.3
M10 2.3 ± 0.23 6.5 ± 0.7
M12 4.0 ± 0.4 11.3 ± 1.1
M14 6.4 ± 0.6 17.9 ± 1.8
M16 9.5 ± 0.9 26.7 ± 2.7
M18 13.5 ± 1.4 38.0 ± 3.8
M20 18.6 ± 1.9 52.2 ± 5.2
M22 24.7 ± 2.5 69.4 ± 6.9
M24 32.1 ± 3.2 90.2 ± 9.0
M30 62.6 ± 6.3 176.1 ± 17.6
M36 108.2 ± 10.8 304.3 ± 30.4
M42 171.8 ± 17.2 483.2 ± 48.3
M45 211.3 ± 21.1 594.3 ± 50.4
10.9

10
INCH TABLE
4T, 5T 10T
Classification Bolt type
Bolt size Torque kgf · m (lbf · ft) Torque kgf · m (lbf · ft)
1/4 0.6 ± 0.06 1.7 ± 0.2
5/16 1.2 ± 0.12 3.0 ± 0.3
3/8 2.0 ± 0.20 5.6 ± 0.5
7/16 3.2 ± 0.32 8.9 ± 0.9
1/2 4.7 ± 0.47 13.4 ± 1.3
9/16 6.8 ± 0.68 19.0 ± 1.9
5/8 9.3 ± 0.93 26.1 ± 2.6
3/4 16.0 ± 1.60 45.1 ± 4.5
7/8 25.5 ± 2.55 71.6 ± 7.2
1 38.0 ± 3.80 106.9 ± 10.7
1-1/8 54.1 ± 5.41 152.2 ± 15.2
1-1/4 74.2 ± 7.42 208.9 ± 20.9
1-3/4 98.8 ± 9.88 277.8 ± 27.8
1-1/2 128.2 ± 12.82 360.7 ± 36.1
The torque in above table shall not be applied to the bolts with nylon packings and nonferrous
metal washers, or the ones with specially designated torque and standard.
H Newton meter : 1 N·m = 0.1kgf·m
TIGHTENING TORQUE OF SPLIT FLANGE BOLTS
The following torque shall be applied to the split flange bolts.
Diameter
(mm) Flat width
(mm) Torque
kgf·m N·m
10 14 6.7 ± 0.7 66.7 ± 6.8
12 17 11.5 ± 1 112 ± 9.8
16 22 28.5 ± 3 279 ± 29

11
TIGHTENING TORQUE FOR HYDRAULIC PLUGS WITH O–RING
O – ring Plug
PF THREAD
Thread Torque (kgf·m)
1/8 1.1 ± 0.1
1/4 2.6 ± 0.2
3/8 4.6 ± 0.3
1/2 8.5 ± 0.4
3/4 19 ± 1.0
1 33 ± 2.0
TORQUE FOR SWIVEL NUT WITH O-RING
Connector O – ring Swivel – nut hose
Tube O.D (inch) Thread (in) Torque (kgf·m)
1/2 UN 13/16 - 16 9.5 ± 0.95
3/4 UN 1 3/16 - 12 18 ± 1.8
1 UN 1 7/16 - 12 21 ± 2.1

12
APPROXIMATE CONVERSIONS
SI Conv Non–SI Conv SI
Unit Factor Unit Factor Unit
Torque
newton meter (N·m)
×8.9 = ln·in ×0.113 = N·m
newton
meter (N·m)
×0.74 = lb·ft. ×1.36 = N·m
newton meter (N·m) ×
0.102
= kg·m
×
7.22
= lb·ft.*
Pressure (Pa = N/m
2
)
kilopascal (kPa)
×4.0 = in. H2O ×0.249 = kPa
kilopascal (kPa)
×0.30 = in. Hg ×3.38 = kPa
kilopascal (kPa)
×0.145 = psi ×6.89 = kPa
(bar)
×14.5 = psi ×0.069 = bar*
(kg/cm2
)
×14.22 = psi ×0.070
=
k f/ 2*
newton/mm
2
×145.04 = psi ×0.069 = bar*
megapascal (MPa) ×
145
= psi
×
0.00689
= MPa
(Pa=N·m
2
)
Power r (W = J/s)
kilowatt (kW)
×1.36 = PS (cv) ×0.736 = kW
kilowatt (kW)
×1.34 = HP ×0.746 = kW
kilowatt (kW)
×0.948 = Btu/s ×1.055 = kW
watt (W)
×0.74 = ft·lb/s ×1.36 = W
(W=J/s) Energy (J = N·m)
kilojoule (kJ)
×0.948 = Btu ×1.055 = kJ
joule (J)
×0.239 = calorie ×4.19 = J
(J=N·m) Velocity and Acceleration
meter per sec
2
(m/s
2)
×
3.28
= ft/s
2
×
0.305
= m/s
2
meter per sec (m/s)
×
3.28
= ft/s
×
0.305
= m/s
kilometer per hour (km/h)
×0.62 = mph ×1.61 = km/h
Horse Power/Torque
BHP ×5252 R.P.M. = TQ (lb·ft) TQ Z R.P.M. 5252 = B.H.P.
Temperature
°C = (°F–32) ÷ 1.8 °F= (°C Z 1.8) + 32
Flow Rate
liter/min (dm3
/min)
×
0.264
= US gal/minZ3.785 = l/min
Note : ( ) Non–SI Unit

13
2. SPECIFICATION
2.1 LOCATION OF COMPONENTS
4 3 6 1 2 5 8 7 9 10
1. Control Handle 6. Drive Wheel
2. Start Key Switch 7. Battery
3. Emergency Button 8. Caster Wheel
4. Battery Indicator CURTIS 803 9. Lift Cylinder
5. Pump Station 10. Load Roller
CONTROL HANDLE(Tiller) 1.FWD / BWD Turning Knob: Control the speed of
the stacker and moving direction: forward or
backward
2.Shifting Button for high speed and low speed:
Snail function takes light-touch switch, when touch
the button once, the speed becomes low;Touch the
button once again, the speed recovers to high.
3.Universal Reversing Button: the emergency
directional reverse button
4. RAISE Button
5. LOWER Button
6. Horn Button
peed.

16
2.2 SPECIFICATION SHEETS
2.2.1 Technical Features
Manufacturer`s type
CG1646
Rated load Q(kg) 1600
Load centre distance c(mm)
600
Lift height mm 4600
Travel speed, unladen km/h 5.4
Travel speed, laden km/h 5.1
Gradient performance, laden % 6
Turning radius Wa(mm) 1605
Tyre size, front 250×78
Drive motor rating kw 1.2
Lift motor rating kw 3.0
Sound level at driver`s ear acc.to EN 12053 B(A) 70
2.2.2 Residual Capacity at different lifting height
Up to TOP mm
ACTUAL CAPACITY ( Q ) kg
2500
1600
1000
3700
1000
600
4600
800
500
Load centre distance ( C ) mm
600
700
2.3 LUBRICATION
CG1646
A 2098mm
B 1950mm
C 570 or 695mm
D 1050mm
E 355mm
F 1140mm

17
Hydraulic oil
Hydraulic oil must have anti-wear qualities at least. It is not advisable to mix oils of
different brands or types, as the may not contain the same required additives or be of
comparable viscosities.
Oil and Lubrication
6.5.4 Oil and Lubricant
Lubrication chart
No. Service point Interval/Running hours
500 h 1000 h 2000h
1 Wheel bearings L A
2 Mast beam L B
3 chains L C
4 Hydraulic system C O D
5 bearings L E
6 Drive gear O F
L=Lubrication C=Check O=Oil change
Oil and grease specification
Lubricant Specification
>-15℃<-15℃Application area
A Grease 2# Grease 2# Grease Bearings,Bushings,Joint
B Grease 2# Grease 2# Grease Side shift forks
C Grease 2# Grease 2# Grease Chains and wires
D Hydraulic Oil 40#Hydraulic Oil 30# Hydraulic Oil Hydraulic system
E Grease 2# Grease 2# Grease Steering bearings
F Grease 1# ALVANIA EP 1# ALVANIA EP Gears

18
3 ELECTRIC SYSTEM
3.1 ELECTRIC DIAGRAM
WIRING DIAGRAM

19
CONNECTION DIAGRAM
No.
Code
NL. Drawing No.
Description
Qty.
1
GB
Battery, 280Ah
1
2
FU01
Fuse, 150A
1
3
Mp
Motor for pump, 3.0kw
1
4
KMp
Relay for motor of pump, DC24V
1
5
YV
Lower magnet valve, DC24V
1
6
Mt
Motor for traction, DC24V/1.2kw
1
7
YB
Brake, DC24V
1
8
KM
DQ-3
Main relay C100/120 DC24V
1
9
Et
DQ-13
Controller CURTIS 1243-4220
1
10
VD
DQ-10
Diodes 1N5408
2
11
FU
DQ-9
Fuse,10A
1
12
S
DQ-48
Emergency button ZDK31-250
1
13
SY
DQ-26-1
Lock LKS-101A
1
14
P
DQ-27
Battery Indicator CURTIS 803
1
15
SA
DQ-23
Micro switch Z-15GW2
1
16
K
DQ-14
Relay ARL2F DC24V
1
17
Kr
DQ-2-1
Protect module BD-W135/110
1
18
HA
DQ-22
Horn DC24V
1
20
B
WG-5
Control handle
(
CH-1
1
21
SH
DQ-45
Magnetic switch HWK23
1
22
AP
DQ-53-1
-
1
23
SU
DQ-55
Micro switch Z-15GW22-B
24
FU02
Fuse, 200A
1

20
3.2CABLE SYSTEM
CG1646 Controlling Circuit(TILLER Handle)
Serial No
Part No Description Note
1 30914100030 Cable of Control Circuit
2 30914900016 Cable of Handle
3 30914800037 Cable of Electromagnetic Brake European
Driving Wheel
4 30914800038 Cable of Speed Limiting Switch
5 30914800039 Cable of Micro Switch
6 L2501008 Controlling Cables Circuit Board
A4

21
CG1646 Universal Electric Parts List

22
Serial
No Part No Description Quantity Note
1 30910100006 Charger 1 Asian(English)
1 30910100007 Charger 1 Asian(Chinese)
1 30910100001 Charger 1 European
1 30910100037 Charger 1 American
1 30910100041 Charger 1 Australian
2 30901200004 Battery 280Ah 1
3 30909100009 Connector (Male) 95199-00 1
4 30909100010 Connector (Female) 95342-01 1
5 5010404025C0 Socket Head Screw M4×25 4
6 30906300004 Micro Switch RZ-15GW2-B3 3
7 30906300023 Cover of Micro Switch 2
8 30902700001 Controlling Board CL-0 1
9 5010504020C0 Phillips Screw M4×20 2
10 30911100026 6A Fuse 1
11 30913300001 White Polar 8*10 2
12 30906600006 Horn 125 24V 1
13 503020023 Elastic Washer Φ8 4
14 5010408016C0 Socket Head Screw M8*16 4
15 422420032 Cable Clip 2
16 5010605012CB Phillips Screw M5*12 2
17 30906100001 Power Switch(New Type) 1
18 30913300003 CL Plastic Cable Clip A 2
19 5010406030C0 Socket Head Screw M6*30 4
20 30913300004 CL Plastic Cable Clip B 2
21 5010406016C0 Socket Head Screw M6X16 4
22 30906200003 Key Switch LKS-101A 1
23 30905100028 Battery Indicator 803 1
24 5010504020C0
Phillips Screw 4*20
2
Table of contents
Other Noblelift Lifting System manuals
Popular Lifting System manuals by other brands
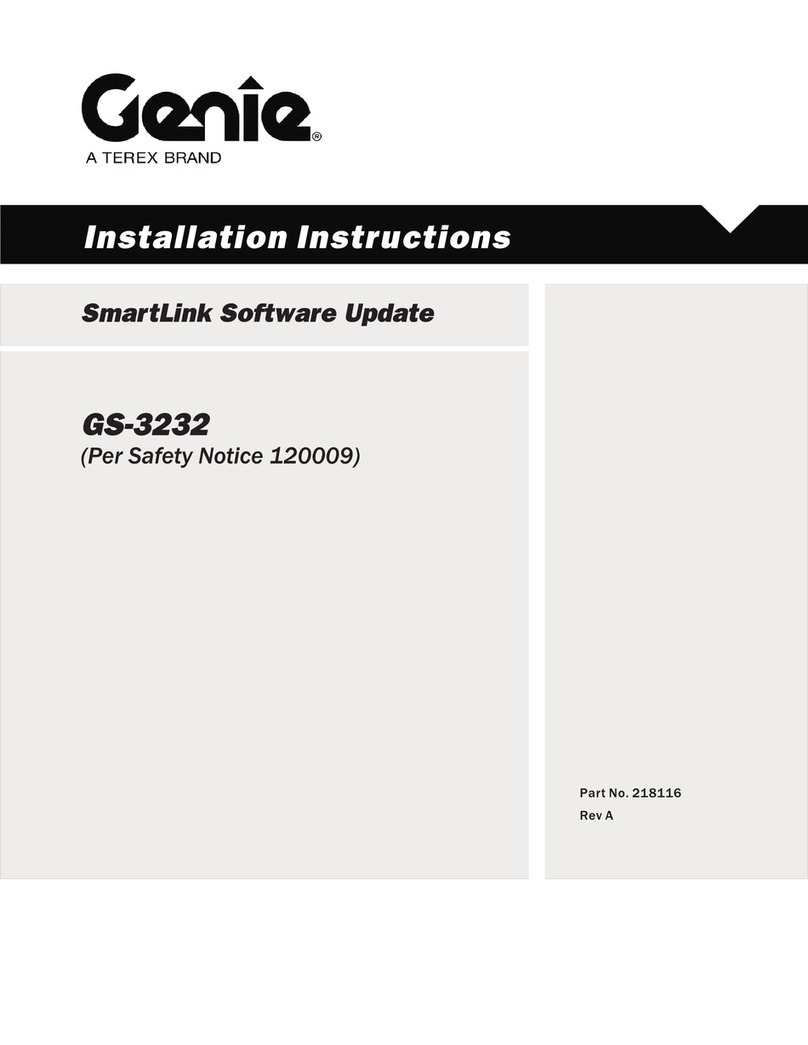
Terex
Terex Genie GS-3232 installation instructions
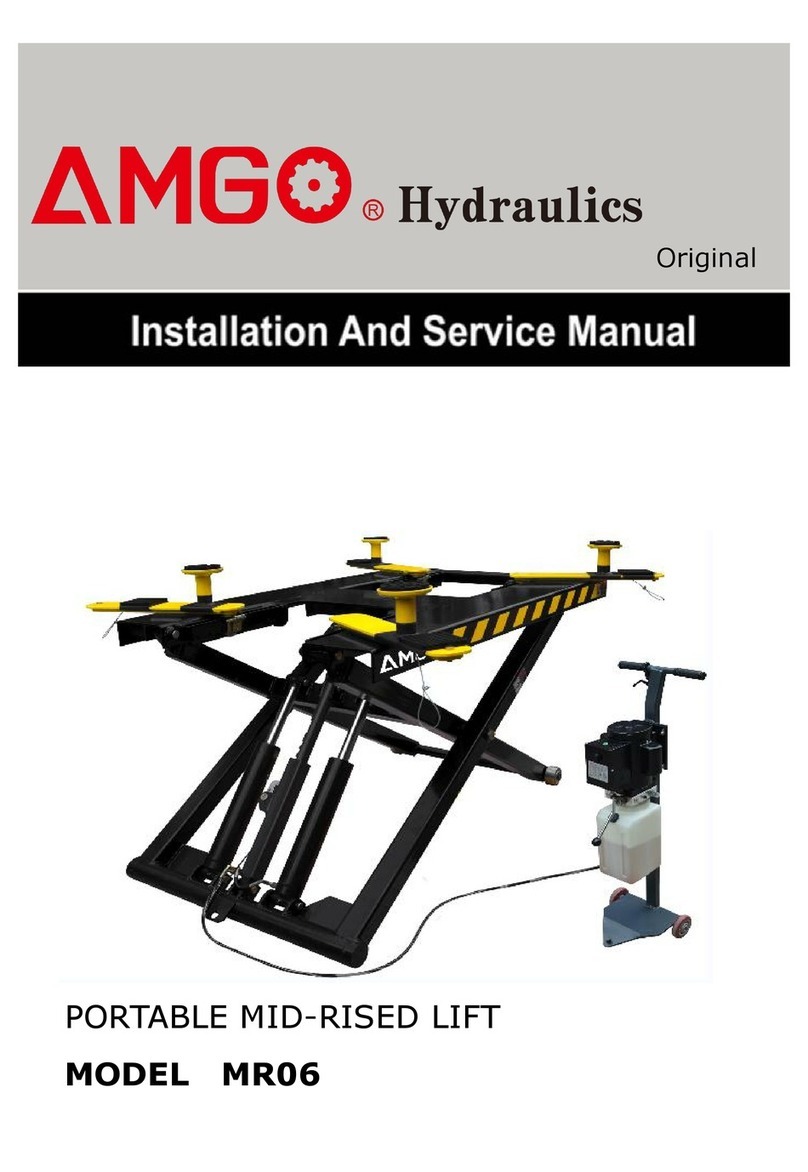
AMGO Hydraulics
AMGO Hydraulics MR06 Installation and service manual

Ergotron
Ergotron StyleView SV22 Assembly instructions
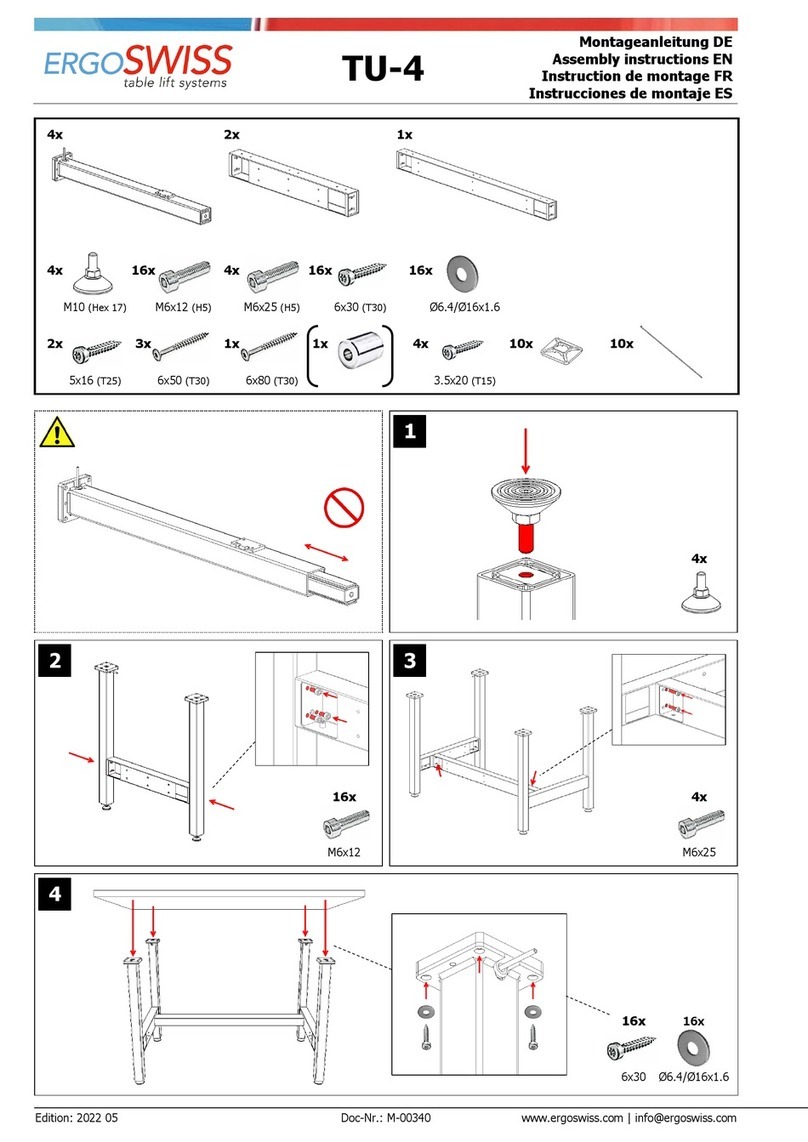
Ergoswiss
Ergoswiss TU-4 Assembly instructions
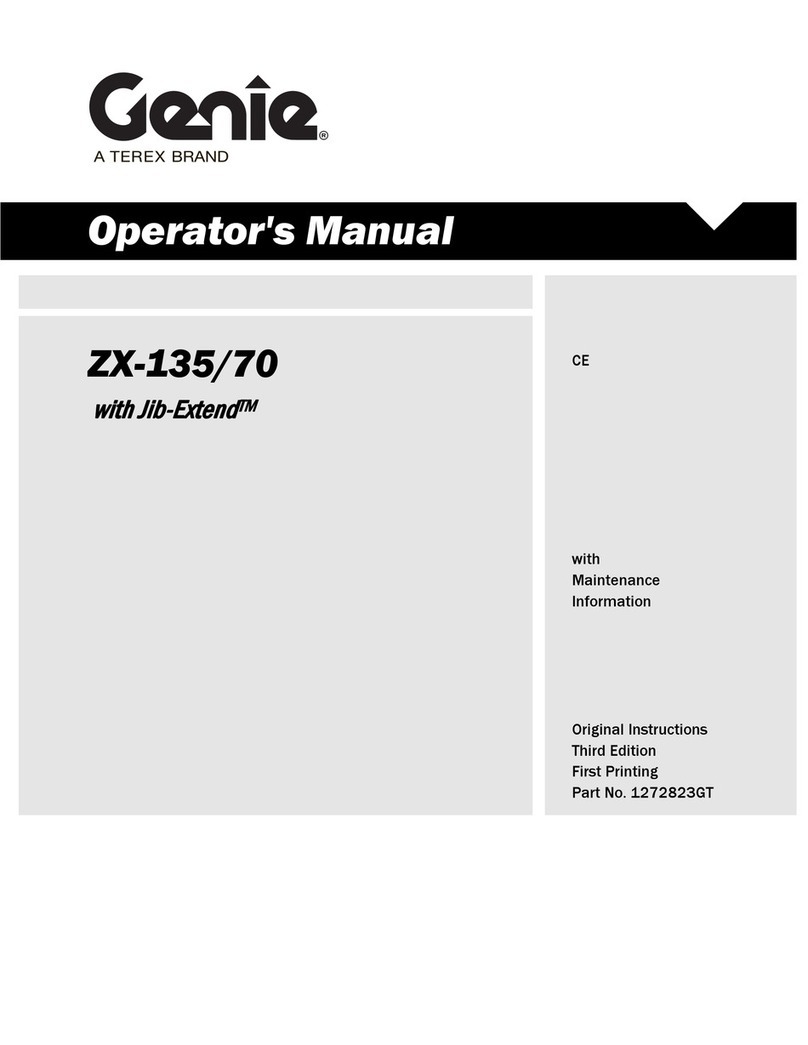
Genie
Genie ZX-135/70 with Jib-Extend Operator's manual
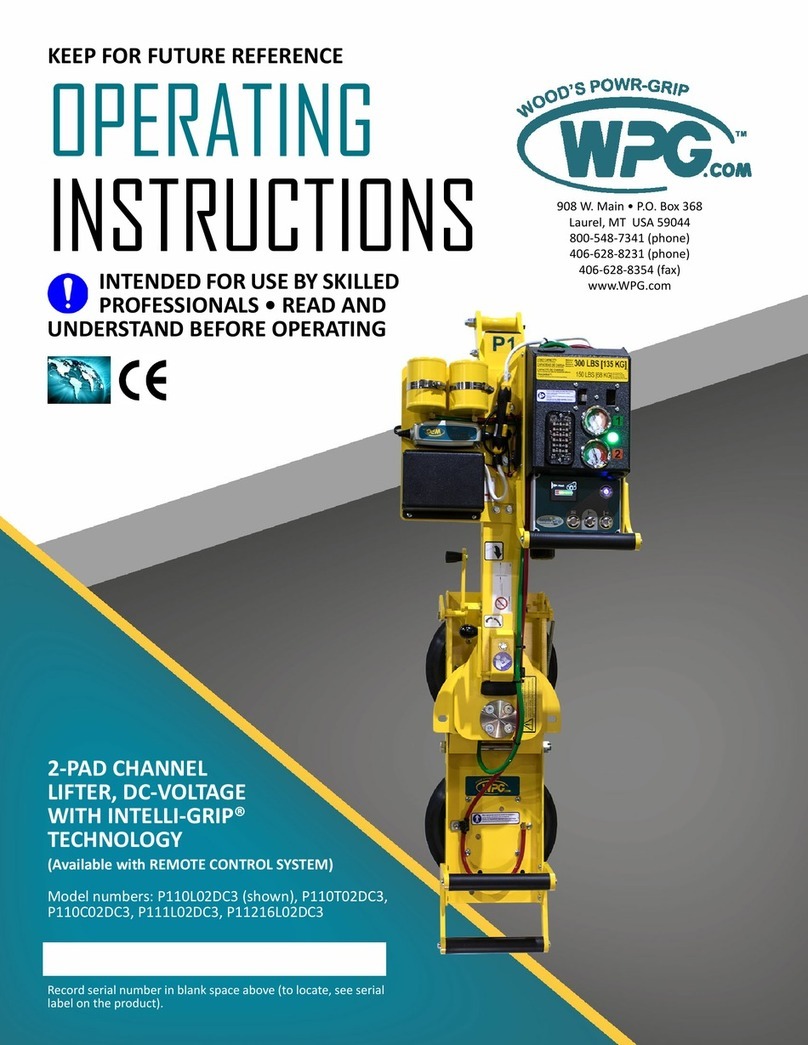
WOOD'S POWR-GRIP
WOOD'S POWR-GRIP P110L02DC3 operating instructions