Nordson MicroCoat MC800 Series User manual

MicroCoat MC800 Series System
Operating Manual
Electronic pdf les of Nordson EFD
manuals are also available at
www.nordsonefd.com
™
Original Instructions

MicroCoat MC800 Series System
2www.nordsonefd.com [email protected] 800-556-3484 Sales and service of Nordson EFD dispensing systems are available worldwide.
You have selected a reliable, high-quality dispensing system from Nordson EFD, the world leader in uid
dispensing. The MicroCoat®MC800 Series system was designed specically for industrial dispensing
and will provide you with years of trouble-free, productive service.
This manual will help you maximize the usefulness of your MicroCoat MC800 Series system.
Please spend a few minutes to become familiar with the controls and features. Follow our recommended
testing procedures. Review the helpful information we have included, which is based on more than
50years of industrial dispensing experience.
Most questions you will have are answered in this manual. However, if you need assistance, please do
not hesitate to contact EFD or your authorized EFD distributor. Detailed contact information is provided
on the last page of this document.
The Nordson EFD Pledge
Thank You!
You have just purchased the world’s nest precision dispensing equipment.
I want you to know that all of us at Nordson EFD value your business and will do everything in our power
to make you a satised customer.
If at any time you are not fully satised with our equipment or the support provided by your Nordson
EFD Product Application Specialist, please contact me personally at 800.556.3484 (US), 401.431.7000
I guarantee that we will resolve any problems to your satisfaction.
Thanks again for choosing Nordson EFD.
Srini Subramanian, General Manager
Srini Subramanian

MicroCoat MC800 Series System
3www.nordsonefd.com [email protected] 800-556-3484 Sales and service of Nordson EFD dispensing systems are available worldwide.
Contents
Contents..........................................................................................................................................................................3
Introduction .....................................................................................................................................................................4
Nordson EFD Product Safety Statement ........................................................................................................................5
Halogenated Hydrocarbon Solvent Hazards ...............................................................................................................6
High Pressure Fluids....................................................................................................................................................6
Qualied Personnel......................................................................................................................................................6
Intended Use ...............................................................................................................................................................7
Regulations and Approvals..........................................................................................................................................7
Personal Safety............................................................................................................................................................7
Fire Safety....................................................................................................................................................................8
Preventive Maintenance ..............................................................................................................................................8
Important Disposable Component Safety Information ................................................................................................9
Action in the Event of a Malfunction............................................................................................................................9
Disposal .......................................................................................................................................................................9
Specications................................................................................................................................................................10
MC800 Controller (7008008)......................................................................................................................................10
MC785M (7008020) & MC785M-WF (7008013) Valves .............................................................................................10
MicroCoat Tank Reservoirs........................................................................................................................................11
4000FLT MC Filter Elements (7017347).....................................................................................................................11
Declaration of Conformity .............................................................................................................................................12
How the System Operates ............................................................................................................................................13
Controller Features........................................................................................................................................................14
Tank Reservoir Features................................................................................................................................................16
System Assembly..........................................................................................................................................................17
Mount the Spray Valves.............................................................................................................................................17
Spray Area Coverage.................................................................................................................................................17
Installation / Removal of Flow Control / Block-off Plug from Manifold .....................................................................18
Set Up the Controller.................................................................................................................................................18
Connect the Press Air Solenoid.................................................................................................................................18
Press Air Solenoid Diagram.......................................................................................................................................19
Connect the Valve Hoses...........................................................................................................................................20
Connect the Tank Reservoir and Lubricant Filter ......................................................................................................20
System Assembly Diagram........................................................................................................................................21
Connect the Emergency Stop Circuit ........................................................................................................................22
System Setup................................................................................................................................................................23
Check All Connections ..............................................................................................................................................23
Fill the Tank Reservoir................................................................................................................................................23
Prime the System ......................................................................................................................................................23
Adjust the Spray ........................................................................................................................................................24
Preventive Maintenance ................................................................................................................................................24
Spray Valve Maintenance ..............................................................................................................................................25
Part Numbers ................................................................................................................................................................26
MicroCoat Spray Valves.............................................................................................................................................26
MicroCoat Fluid Manifolds.........................................................................................................................................26
MicroCoat Tank Reservoirs........................................................................................................................................26
Accessories ...................................................................................................................................................................27
Replacement Parts........................................................................................................................................................28
MC785M Series Spray Valve Part Numbers..............................................................................................................28
MC800 Controller ......................................................................................................................................................29
MC687M 19 Liter Tank Reservoir ..............................................................................................................................30
MC685M and MC686M 3.8 and 7.5Liter Tank Reservoir .........................................................................................30
Troubleshooting.............................................................................................................................................................31
Technical Data ...............................................................................................................................................................32
Controller Air Schematic............................................................................................................................................32
Oil Flow Schematic....................................................................................................................................................32

MicroCoat MC800 Series System
4www.nordsonefd.com [email protected] 800-556-3484 Sales and service of Nordson EFD dispensing systems are available worldwide.
Introduction
The MicroCoat System provides precise lubrication control for
metal stamping operations.
The MC800 controller, MC785M series spray valves and
the MicroCoat tank reservoirs are all produced to exacting
specications and thoroughly tested prior to shipment.
The MC785M series valves are designed for long life without
maintenance when clean lubricant is used.
To obtain the maximum performance from your MicroCoat System,
please read through these instructions carefully.
Our goal is to build not only the nest equipment but also to build
long-term customer relationships founded on superb quality,
service, value and trust.

MicroCoat MC800 Series System
5www.nordsonefd.com [email protected] 800-556-3484 Sales and service of Nordson EFD dispensing systems are available worldwide.
Nordson EFD Product Safety Statement
The safety messages that follow have a CAUTION level hazard.
Failure to comply may result in minor or moderate injury.
CAUTION
READ MANUAL
Read manual for proper use of this equipment. Follow all safety instructions. Task- and equipment-
specic warnings, cautions, and instructions are included in equipment documentation where
appropriate. Make sure these instructions and all other equipment documents are accessible to
persons operating or servicing equipment.
The safety message that follows has a WARNING level hazard.
Failure to comply could result in death or serious injury.
WARNING
ELECTRIC SHOCK
Risk of electric shock. Disconnect power before removing covers and / or disconnect, lock out, and
tag switches before servicing electrical equipment. If you receive even a slight electrical shock, shut
down all equipment immediately. Do not restart the equipment until the problem has been identied
and corrected.
MAXIMUM AIR PRESSURE
Unless otherwise noted in the product manual, the maximum air input pressure is 7.0bar (100psi).
Excessive air input pressure may damage the equipment. Air input pressure is intended to be applied
through an external air pressure regulator rated for 0 to 7.0bar (0 to 100psi).
RELEASE PRESSURE
Release hydraulic and pneumatic pressure before opening, adjusting, or servicing pressurized
systems or components.
BURNS
Hot surfaces! Avoid contact with the hot metal surfaces of heated components. If contact can not be
avoided, wear heat-protective gloves and clothing when working around heated equipment. Failure
to avoid contact with hot metal surfaces can result in personal injury.

MicroCoat MC800 Series System
6www.nordsonefd.com [email protected] 800-556-3484 Sales and service of Nordson EFD dispensing systems are available worldwide.
Nordson EFD Product Safety Statement (continued)
Halogenated Hydrocarbon Solvent Hazards
Do not use halogenated hydrocarbon solvents in a pressurized system that contains aluminum components.
Under pressure, these solvents can react with aluminum and explode, causing injury, death, or property damage.
Halogenated hydrocarbon solvents contain one or more of the following elements.
Element Symbol Prefix
Fluorine F “Fluoro-”
Chlorine Cl “Chloro-”
Bromine Br “Bromo-”
Iodine I “Iodo-”
Check the Safety Data Sheet (SDS) or contact your material supplier for more information. If you must use
halogenated hydrocarbon solvents, contact your EFD representative for compatible EFD components.
High Pressure Fluids
High pressure uids, unless they are safely contained, are extremely hazardous. Always release uid pressure before
adjusting or servicing high pressure equipment. A jet of high pressure uid can cut like a knife and cause serious
bodily injury, amputation, or death. Fluids penetrating the skin can also cause toxic poisoning.
Any injury caused by high pressure liquid can be serious. If you are injured or even suspect an injury:
• Go to an emergency room immediately.
• Tell the doctor that you suspect an injection injury.
• Show the doctor the following note.
• Tell the doctor what kind of material you were dispensing.
WARNING
Medical Alert — Airless Spray Wounds: Note to Physician
Injection in the skin is a serious traumatic injury. It is important to treat the injury surgically as soon as possible. Do
not delay treatment to research toxicity. Toxicity is a concern with some exotic coatings injected directly into the
bloodstream.
Qualified Personnel
Equipment owners are responsible for making sure that EFD equipment is installed, operated, and serviced by
qualied personnel. Qualied personnel are those employees or contractors who are trained to safely perform
their assigned tasks. They are familiar with all relevant safety rules and regulations and are physically capable of
performing their assigned tasks.

MicroCoat MC800 Series System
7www.nordsonefd.com [email protected] 800-556-3484 Sales and service of Nordson EFD dispensing systems are available worldwide.
Intended Use
Use of EFD equipment in ways other than those described in the documentation supplied with the equipment may
result in injury to persons or damage to property. Some examples of unintended use of equipment include:
• Using incompatible materials.
• Making unauthorized modications.
• Removing or bypassing safety guards or interlocks.
• Using incompatible or damaged parts.
• Using unapproved auxiliary equipment.
• Operating equipment in excess of maximum ratings.
• Operating equipment in an explosive atmosphere.
Regulations and Approvals
Make sure all equipment is rated and approved for the environment in which it is used. Any approvals obtained for
Nordson EFD equipment will be voided if instructions for installation, operation, and service are not followed. If the
equipment is used in a manner not specied by Nordson EFD, the protection provided by the equipment may be
impaired.
Personal Safety
To prevent injury, follow these instructions:
• Do not operate or service equipment unless you are qualied.
• Do not operate equipment unless safety guards, doors, and covers are intact and automatic interlocks are
operating properly. Do not bypass or disarm any safety devices.
• Keep clear of moving equipment. Before adjusting or servicing moving equipment, shut off the power supply
and wait until the equipment comes to a complete stop. Lock out power and secure the equipment to prevent
unexpected movement.
• Make sure spray areas and other work areas are adequately ventilated.
• When using a syringe barrel, always keep the dispensing end of the tip pointing towards the work and away
from the body or face. Store syringe barrels with the tip pointing down when they are not in use.
• Obtain and read the Safety Data Sheet (SDS) for all materials used. Follow the manufacturer’s instructions for
safe handling and use of materials and use recommended personal protection devices.
• Be aware of less-obvious dangers in the workplace that often cannot be completely eliminated, such as hot
surfaces, sharp edges, energized electrical circuits, and moving parts that cannot be enclosed or otherwise
guarded for practical reasons.
• Know where emergency stop buttons, shutoff valves, and re extinguishers are located.
• Wear hearing protection to protect against hearing loss that can be caused by exposure to vacuum exhaust port
noise over long periods of time.
Nordson EFD Product Safety Statement (continued)

MicroCoat MC800 Series System
8www.nordsonefd.com [email protected] 800-556-3484 Sales and service of Nordson EFD dispensing systems are available worldwide.
Nordson EFD Product Safety Statement (continued)
Fire Safety
To prevent a re or explosion, follow these instructions:
• Shut down all equipment immediately if you notice static sparking or arcing. Do not restart the equipment until
the cause has been identied and corrected.
• Do not smoke, weld, grind, or use open ames where ammable materials are being used or stored.
• Do not heat materials to temperatures above those recommended by the manufacturer. Make sure heat
monitoring and limiting devices are working properly.
• Provide adequate ventilation to prevent dangerous concentrations of volatile particles or vapors. Refer to local
codes or the SDS for guidance.
• Do not disconnect live electrical circuits when working with ammable materials. Shut off power at a disconnect
switch rst to prevent sparking.
• Know where emergency stop buttons, shutoff valves, and re extinguishers are located.
Preventive Maintenance
As part of maintaining continuous trouble-free use of this product, Nordson EFD recommends the following simple
preventive maintenance checks:
• Periodically inspect tube-to-tting connections for proper t. Secure as necessary.
• Check tubing for cracks and contamination. Replace tubing as necessary.
• Check all wiring connections for looseness. Tighten as necessary.
• Clean: If a front panel requires cleaning, use a clean, soft, damp rag with a mild detergent cleaner. DO NOT USE
strong solvents (MEK, acetone, THF, etc.) as they will damage the front panel material.
• Maintain: Use only a clean, dry air supply to the unit. The equipment does not require any other regular
maintenance.
• Test: Verify the operation of features and the performance of equipment using the appropriate sections of this
manual. Return faulty or defective units to Nordson EFD for replacement.
• Use only replacement parts that are designed for use with the original equipment. Contact your Nordson EFD
representative for information and advice.

MicroCoat MC800 Series System
9www.nordsonefd.com [email protected] 800-556-3484 Sales and service of Nordson EFD dispensing systems are available worldwide.
Nordson EFD Product Safety Statement (continued)
Important Disposable Component Safety Information
All Nordson EFD disposable components, including syringe barrels, cartridges, pistons, tip caps, end caps,
and dispense tips, are precision engineered for one-time use. Attempting to clean and re-use components will
compromise dispensing accuracy and may increase the risk of personal injury.
Always wear appropriate protective equipment and clothing suitable for your dispensing application and adhere to
the following guidelines:
• Do not heat syringe barrels or cartridges to a temperature greater than 38° C (100° F).
• Dispose of components according to local regulations after one-time use.
• Do not clean components with strong solvents (MEK, acetone, THF, etc.).
• Clean cartridge retainer systems and barrel loaders with mild detergents only.
• To prevent uid waste, use Nordson EFD SmoothFlow™pistons.
Action in the Event of a Malfunction
If a system or any equipment in a system malfunctions, shut off the system immediately and perform the following
steps:
1. Disconnect and lock out system electrical power. If using hydraulic and pneumatic shutoff valves, close and
relieve pressure.
2. For Nordson EFD air-powered dispensers, remove the syringe barrel from the adapter assembly. For Nordson
EFD electro-mechanical dispensers, slowly unscrew the barrel retainer and remove the barrel from the actuator.
3. Identify the reason for the malfunction and correct it before restarting the system.
Disposal
Dispose of equipment and materials used in operation and servicing according to local codes.

MicroCoat MC800 Series System
10 www.nordsonefd.com [email protected] 800-556-3484 Sales and service of Nordson EFD dispensing systems are available worldwide.
Specifications
NOTE: Specications and technical details are subject to engineering change without prior notication.
MC800 Controller (7008008)
Item Specification
Cabinet size 14.6Wx 19.1Dx 27.6Hcm (5.8Wx 7.5Dx 10.8H")
Weight 4.8 kg (10.62 lb)
Air input required 4.14bar (60psi) minimum
Tank air pressure regulator 2.07bar (30psi) maximum
Nozzle air regulator 2.07bar (30psi) maximum
Cycle rate Up to 60 per minute
Pressure switch rating 20VA 240V
Approvals CE Compliant
Satises Machinery Directive 98/37/EC, evaluated to EN292-2, Annex 1
MC785M (7008020) & MC785M-WF (7008013) Valves
Item Specification
Size (with ttings) 66.29 mm (2.61")
Length 49.28 mm (1.94") width
Weight 206 g (7.28 oz)
Lubricant chamber Hard-coated aluminum
Return spring 303 stainless steel
Needle and nozzle 303 stainless steel
Air cap 303 stainless steel
Diaphragm Viton®with PTFE coating
Lubricant inlet hole 1/8 NPT mounting, 6 mm tapped hole
Operating frequency Up to 60 per minute
Nozzle diameter 1.17 mm (0.046")
U.S. Patent #D-398, 705

MicroCoat MC800 Series System
11www.nordsonefd.com [email protected] 800-556-3484 Sales and service of Nordson EFD dispensing systems are available worldwide.
MicroCoat Tank Reservoirs
Item Specification
Operating pressure 2.07bar (30psi) maximum
Safety relief pressure 2.76bar (40psi)
Low level switch rating 20VA 240V
Tank Model MC686M (7023846) MC685M (7023843) MC687M (7023849)
MC687M-DFS (7023850)*
Capacity 3.8 L (1 gallon) 7.5 L (2 gallons) 19 L (5 gallons)
Construction Acrylic tank wall, anodized aluminum end caps Type 304 stainless steel
Weight 4.1 kg (9.18 lb) 5.2 kg (11.6 lb) 7.9 kg (17.54 lb)
*Includes two oat switches: mid-level warning indicator,and low level indicator for press shutdown.
4000FLT MC Filter Elements (7017347)
Item Specification
Internal lter element Resin impregnated cellulose media
Micron lter size 10 micron nominal
Specifications (continued)

MicroCoat MC800 Series System
12 www.nordsonefd.com [email protected] 800-556-3484 Sales and service of Nordson EFD dispensing systems are available worldwide.
Declaration of Conformity

MicroCoat MC800 Series System
13www.nordsonefd.com [email protected] 800-556-3484 Sales and service of Nordson EFD dispensing systems are available worldwide.
How the System Operates
The MicroCoat System incorporates up to eight low volume low
pressure (LVLP) spray valves, a lubricant reservoir, and a controller
that regulates air pressure, meters lubricant ow, and controls valve
operation.
Constant air pressure applied to the tank reservoir forces lubricant
through precision uid ow ]controls on the MC800 controller, then out
to the spray valves.
When the press is stamping, a 3-way air solenoid activates the system
and opens the valves.
As the valve opens, LVLP air creates a pressure drop at the nozzle,
causing the lubricant to spray a ne lm onto the stock.
Lubricant ow can be adjusted independently for each valve via ow
controls on the front of the MC800 controller.
Control air (On)
Nozzle air
(On)
Control air (Off)
Nozzle air
(Off)
Lubricant
Open
Closed

MicroCoat MC800 Series System
14 www.nordsonefd.com [email protected] 800-556-3484 Sales and service of Nordson EFD dispensing systems are available worldwide.
Controller Features
1. System Pressure Switch
Turns the system air supply On and Off.
2. Mode Switch
Use Manual/Setup position to prime and test the valves
without running the press.
In the Auto/Run position, the system will spray lubricant
when the press begins stamping.
Press air solenoid must be properly installed to allow
the MicroCoat System to run in Auto/Run mode (refer to
pages 18–19).
3. Tank Air Pressure
Regulates air pressure in the lubricant reservoir. For most
lubricants, 1.03bar (15psi) is a good start.
Minimum setting is 0.83bar (12psi).
4. Nozzle Air
Regulates nozzle air pressure.
Average setting is 0.55 to 0.83bar (8 to 12psi). Higher
pressure provides ner spray.
5. Flow Controls
Provide independent ow control of the lubricant to
each spray valve. Each blue ring on the stem coming
out of the middle of the knob indicates one complete
revolution.
Turn counterclockwise to increase ow.
12
3 4
5

MicroCoat MC800 Series System
15www.nordsonefd.com [email protected] 800-556-3484 Sales and service of Nordson EFD dispensing systems are available worldwide.
6. Low Pressure Switch
Registers low uid pressure. Connects with low level
switch for press protection.
Must be wired to the press Emergency Stop Circuit
to prevent the press from operating without lubricant
pressure (refer to page 22).
WARNING
7. Tank Air
Air from this port pressurizes the lubricant reservoir.
8. Nozzle Air
Air from this port is used to spray the lubricant.
9. Valve Control Air
Air from this port controls the opening and closing of
the spray valves.
10. Fluid Outlet
Pressurized lubricant ows from these ports to the
spray valves.
11. Constant Air Input
The main air supply to the system should be a
minimum of 4.14bar (60psi).
12. Fluid Inlet
Lubricant from the tank reservoir enters the manifold
through this port.
13. Control Air Input from Solenoid
Activates the system when the press begins
stamping. Minimum 4.14bar (60psi) required.
Controller Features (continued)
7
11
8 9
13
12 6
10

MicroCoat MC800 Series System
16 www.nordsonefd.com [email protected] 800-556-3484 Sales and service of Nordson EFD dispensing systems are available worldwide.
Tank Reservoir Features
1. Low Level Switch
Prevents the system from operating without lubricant when
connected to the press Emergency Stop Circuit. Switch opens
when tank level is near empty.
2. Air Pressure Relief Valve
Automatically exhausts air if tank reservoir pressure exceeds
2.76bar (40psi). Also used to manually exhaust air pressure
before relling the tank.
3. Fill Port Cap
Ported threads relieve any residual reservoir air pressure when
cap is loosened.
4. Drain Plug (not shown)
5. Lubricant Inline Filter
6. Bleed Valve
Valve releases air after lter replacement.
1
3
6
5
4
2

MicroCoat MC800 Series System
17www.nordsonefd.com [email protected] 800-556-3484 Sales and service of Nordson EFD dispensing systems are available worldwide.
System Assembly
Mount the Spray Valves
Mount each valve with the mounting clamp (7021742)
provided, or use the 6 mm mounting hole in the valve body to
attach the valve to an alternative mounting bracket.
NOTE: Optional valve mounting xtures provide easy
installation of the valves without the need to drill or fabricate
attachment hardware. See page 27 for further information.
To ensure proper lubrication coverage, mount the MC785M
valve so the tabs on the air cap are in line with the stock as
illustrated. Use the valve alignment tool (7023866) shown on
page 27 for precise valve alignment.
IMPORTANT: If you loosen the air cap retainer nut to
reposition the tabs, be sure to retighten the nut with a wrench
before operating the valve.
The width of spray coverage is determined by the distance
between the valve nozzle and the stock, as shown in the chart
below.
Spray Area Coverage
Spray Valves
Nozzle Distance to Stock
2.54 mm
(0.1")
50.8 mm
(2.00")
76.2 mm
(3.00")
101.6 mm
(4.00")
127.0 mm
(5.00")
152.4 mm
(6.00")
MC785M 25.4 mm
(1.00")
38.1 mm
(1.50")
50.8 mm
(2.00")
63.5 mm
(2.50")
69.9 mm
(2.75")
82.6 mm
(3.25")
MC785M-WF 38.1 mm
(1.50")
63.5 mm
(2.50")
88.9 mm
(3.50")
114.3 mm
(4.50")
139.7 mm
(5.50")
165.1 mm
(6.50")
The MC785M-WF is recommended for spray widths from 2.0" to 6.0".
NOTE: Spray width coverage may vary depending on the viscosity and surface tension of the uid.
Air cap
Metal
stock
Valve mounted
perpendicular
Nozzle distance
Valve mounted
at 45˚ angle
Nozzle distance

MicroCoat MC800 Series System
18 www.nordsonefd.com [email protected] 800-556-3484 Sales and service of Nordson EFD dispensing systems are available worldwide.
Installation / Removal of Flow
Control / Block-off Plug from
Manifold
Turn the system pressure off and conrm that tank
pressure is at zero before performing maintenance
on the system.
CAUTION
To remove a block-off plug or ow control, loosen the
set screw on the bottom of the uid manifold block and
pull the block-off or ow control out of the manifold.
NOTE: To loosen / release the block-off and / or the
ow control from the manifold, it may help to rotate
them clockwise while you pull. This will help free the
0-ring seal. The ow control needs to be fully closed
before the body will turn within the manifold.
System Assembly (continued)
To install a new ow control, lubricate the 0-rings on the
ow control with your stamping oil and push the ow
control into the manifold while turning clockwise until
the ow control slides into place. Continue turning until
the zero on the knob is lined up with the zero reference
on the ow control manifold. Tighten the manifold
setscrew rmly.
Set screw
on bottom of manifold
Set Up the Controller
1. Place the controller and tank reservoir away from trafc areas and position the tank to allow for convenient
relling.
2. Set the controller System Pressure to the Off position and the mode switch to the Auto/Run position.
3. Refer to the diagram on page 19 and connect a ve-micron lter / regulator to the plant air supply. Using the
black and white 8 mm hoses supplied with the controller, connect to the color-coded Constant Air Input (black,
8 mm) and Control Air Input from Solenoid (white, 8 mm) ttings at the back of the controller.
Connect the Press Air Solenoid
IMPORTANT: When the press is stamping, the solenoid must be open continuously to allow constant spray from the
MicroCoat system. This can be accomplished by wiring the solenoid into the press clutch / run circuit.
To provide proper air distribution and control, a press air solenoid must be installed in-line with the white hose going
to the Control Air Input from Solenoid Fitting.
1. Select the appropriate 3-way solenoid. Flow must meet or exceed 0.06 m3/min (2.0 cfm) at 4.14bar (60psi).
2. Cut the control air hose at a convenient location and install the solenoid as shown.
3. Connect the solenoid wires to the press control circuit.

MicroCoat MC800 Series System
19www.nordsonefd.com [email protected] 800-556-3484 Sales and service of Nordson EFD dispensing systems are available worldwide.
System Assembly (continued)
Press Air Solenoid Diagram
Review with Plant
Electrician
Fitting, 1/4 MPT x 8 mm elbow
#7022191
Operating air pressure:
Set regulator to 4.14bar (60psi)
Fitting, 1/4 NPT x (2) 8 mm elbow
#7022193
8 mm, black
#7022180
Constant air
connector
Control air
connector
Connect to
press control circuit
3-way press air solenoid
is continuously open when
the press is stamping
Flow requirement:
0.06 m3/min (2.0 cfm)
at 4.14bar (60psi)
Five-micron lter / regulator,
optional — order separately
#7022158
Compressed air input
4.14–8.62bar
(60–125psi)
8 mm, white
#7022181
MC800 Controller
EFD MicroCoat Solenoids
Part # Description
7008014 24 volt DC solenoid
7022162 24 volt AC solenoid
7022159 100 volt AC solenoid
7022160 120 volt AC solenoid
7022161 220 volt AC solenoid
EFD MicroCoat Solenoid Cord Sets
Part # Description
7016694 AC solenoid cord set
7008016 DC solenoid cord set

MicroCoat MC800 Series System
20 www.nordsonefd.com [email protected] 800-556-3484 Sales and service of Nordson EFD dispensing systems are available worldwide.
Connect the Valve Hoses
NOTE: Refer to the diagram on page 21.
1. Find a suitable location and mount the two air manifolds. One manifold is
for the white Control Air hose and the other is for the black Nozzle Air hose.
2. Connect a suitable length of black 6 mm tubing between the valve controller
Nozzle Air outlet tting and the air manifold inlet which has black push-in
ttings.
3. Connect a suitable length of white 6 mm tubing between the valve controller
Control Air outlet tting and the air manifold inlet which has white push-in
ttings.
4. Using the black and white 4 mm tubing, connect each color-coded valve
tting to the appropriate colored manifold tting, cutting the tubing to the
appropriate length as you proceed.
5. Using the clear 4 mm tubing, connect the appropriate length of tubing to
the uid manifold at the back of the controller using the compression nut
provided and connect the opposite end to the appropriate spray valve inlet
push-in tting.
6. Using the spiral wrap supplied, group and wrap each valve tri-hose to
provide a neat installation and prevent damage due to loose hoses.
System Assembly (continued)
Connect the Tank Reservoir and Lubricant Filter
NOTE: Refer to the diagram on page 21.
The tank reservoir is supplied with a lubricant lter, uid hose, air hose and low
level switch cable.
Connect the tank to the controller as follows:
1. Connect the grey air hose to the Tank Air tting on the back of the controller.
Connect the opposite end of the hose to the Tank Air Inlet tting on top of
the tank.
2. Mount the lter adapter to the tank reservoir or MicroCoat stand using the
hardware provided.
3. Connect the clear uid hose to the Fluid Inlet connector on the manifold at
the back of the controller. Then connect the opposite end of the uid hose
to the outlet tting at the bottom of the tank reservoir.
4. Cut the clear uid hose from the tank to the controller so the end of the
hose coming from the tank can be installed into the “IN” port of the lter
adapter.
5. Connect the uid hose from the controller to the “OUT” port on the lter
adapter.
6. Lubricate the lter gasket and screw the lter onto the adapter until the
gasket makes contact and then tighten an additional 3/4 turn.
7. Refer to page 22 to wire the press Emergency Stop Circuit and to
connect the low level switch cable to the controller.
Table of contents
Popular Lubrication System manuals by other brands
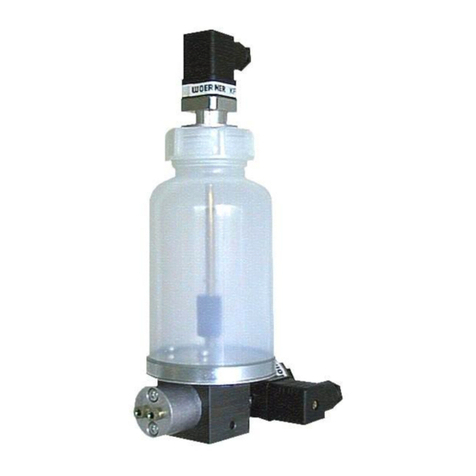
WOERNER
WOERNER GMI-A Translation of the original operation manual

DLS
DLS DLS-47 Series user manual
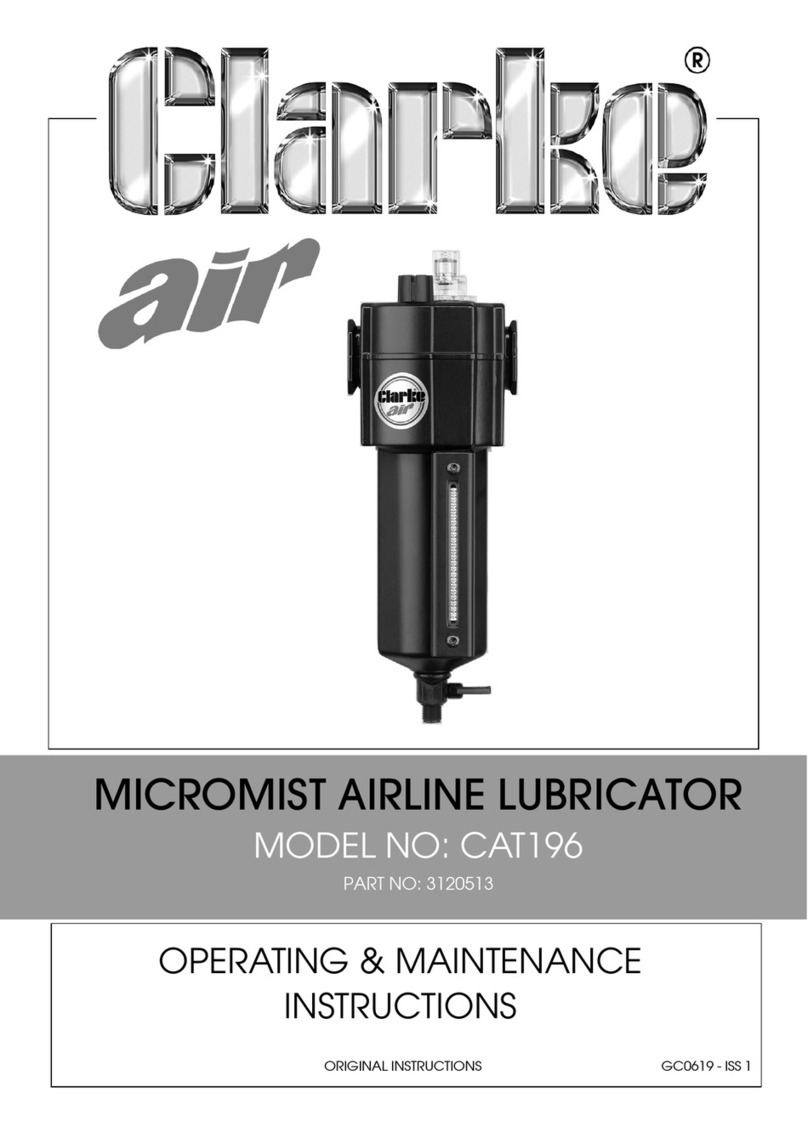
Clarke
Clarke CAT196 Operating & maintenance instructions
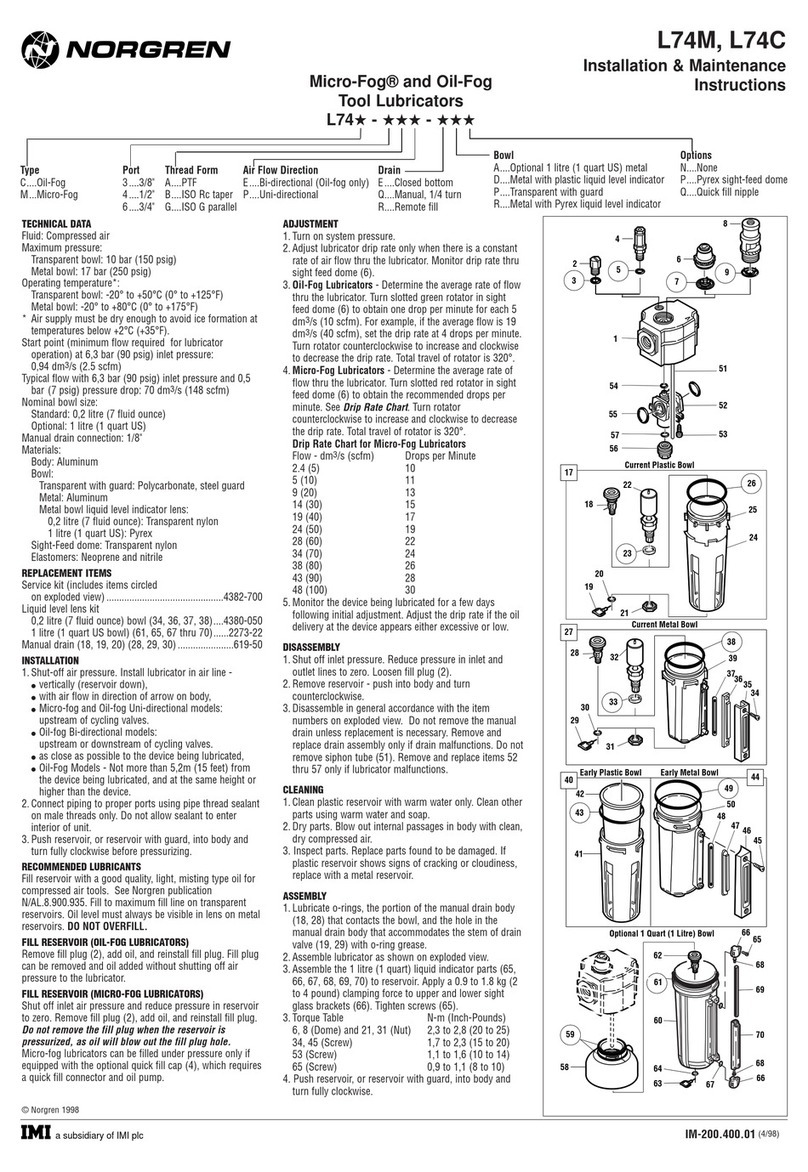
Norgren
Norgren L74M Installation & maintenance instructions
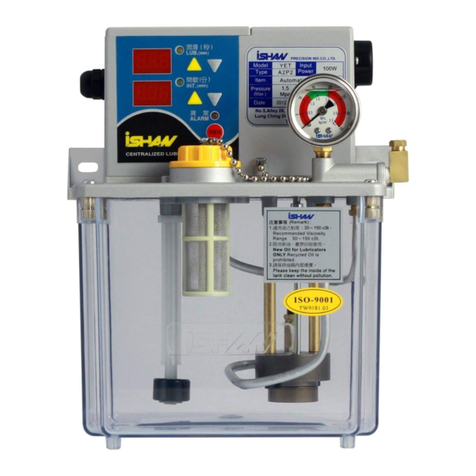
iSHAN
iSHAN YET-A1 Operation manual
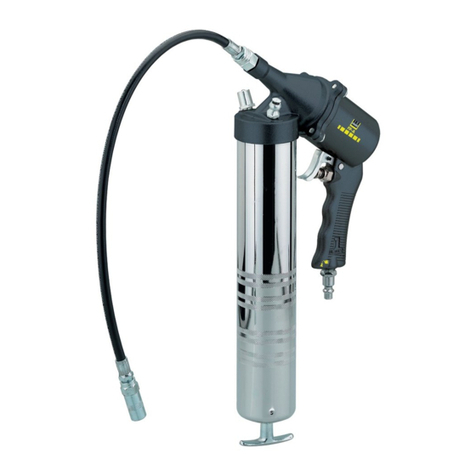
Schneider Airsystems
Schneider Airsystems FP-M Original operating manual