WOERNER GMI-A User manual

Operating manual Page 1 of 32 B0102
GMI / GML / SAB / GOI
Delivery pump GMI-A / GML-A
Injection unit SAB-C
OL-mini aggregate GOI-A
Translation of the
original operation manual
Version EN 12/2018

Operating manual Page 2 of 32 B0102
GMI / GML / SAB / GOI
Translation
When delivery is made into EEC countries, this operation manual
needs to be translated into the user’s country language accordingly.
In case that any inconsistency in the translated text occurs, the
original (German) operation manual should be referred to for
clarification or the manufacturer contacted.
Copyright
Unless permitted explicitly, the dissemination, reproduction, and
utilisation of this document as well as the communication of its
contents are prohibited. Any violation of this stipulation shall involve
the obligation to compensate damage.
All rights reserved.

Operating manual Page 3 of 32 B0102
GMI / GML / SAB / GOI
Table of Contents
1. Important notes on this operation manual.....................................................................5
1.1 Users......................................................................................................................5
1.2 Obligation to read...................................................................................................5
1.3 What to do in case of questions..............................................................................5
1.4 Operation manual...................................................................................................5
1.4.1 Applicability............................................................................................................5
1.4.2 Content and purpose..............................................................................................5
1.4.3 Location .................................................................................................................6
1.4.4 Meanings of safety notes and safety symbols ........................................................6
2. Identification....................................................................................................................7
2.1 Product brand and type designation.......................................................................7
2.2 Product version ......................................................................................................7
2.3 Product marking.....................................................................................................7
2.4 Manufacturer and contact address .........................................................................7
2.5 Conformity..............................................................................................................7
3. Product description.........................................................................................................8
3.1 Purpose of use.......................................................................................................8
3.2 Limits of use...........................................................................................................8
3.3 Ambient conditions.................................................................................................8
3.4 Conventional usage................................................................................................9
3.5 Technical data........................................................................................................9
3.5.1 Assemblies.............................................................................................................9
3.5.2 Dimensions ..........................................................................................................10
3.5.3 Technical data......................................................................................................13
4. Functional description ..................................................................................................14
4.1 Drive.....................................................................................................................14
4.2 Operation GMI-A, GML-A and SAB-C ..................................................................15
4.3 Operation GOI-A ..................................................................................................15
4.4 Function control (optional)....................................................................................16
5. Safety notes...................................................................................................................17
5.1 Basic principle......................................................................................................17
5.2 Requirements on user training..............................................................................17
5.3 Safety facilities .....................................................................................................17
5.4 Accident prevention..............................................................................................18
5.5 Residual risks.......................................................................................................18
5.6 Incorrect applications ...........................................................................................18
5.7 General safety regulations and duties ..................................................................18
5.8 Disclaimer ............................................................................................................19
6. Transportation, installation, commissioning and shutdown transport......................19
6.1 Transportation......................................................................................................19
6.2 Unpacking............................................................................................................19
6.3 Installation............................................................................................................20
6.4 Power supply and switch-on.................................................................................20
6.5 Commissioning.....................................................................................................21
6.6 Shutdown.............................................................................................................22
7. Operation .......................................................................................................................23
7.1 Troubleshooting, fault remedy..............................................................................23
7.2 Refilling the reservoir............................................................................................23
7.3 Adjustment of the OL-flow (only GOI-A) ...............................................................23
7.4 Switch-off .............................................................................................................23

Operating manual Page 4 of 32 B0102
GMI / GML / SAB / GOI
8. Cleaning, servicing, fault remedy, and repair..............................................................24
8.1 Cleaning...............................................................................................................24
8.2 Servicing ..............................................................................................................24
8.3 Inspection schedule..............................................................................................25
8.4 Repair ..................................................................................................................25
8.5 List of spare parts.................................................................................................25
8.6 Accessories..........................................................................................................26
9. Return shipment to factory...........................................................................................27
10. Disposal.......................................................................................................................29
11. Appendix......................................................................................................................29
11.1 Content of the declaration of conformity...............................................................29
11.2 Declaration of conformity......................................................................................30
11.3 GML-A special version Art.-Nr. 75239670............................................................31

Operating manual Page 5 of 32 B0102
GMI / GML / SAB / GOI
1. Important notes on this operation manual
This operation manual forms part of the machine and must be available
to the operation and maintenance personnel at any time.
The safety notes contained herein need to be observed. When reselling
the machine, this operation manual must be handed over in any case as
well.
In addition to this operation manual, always be careful to observe the
laws and regulations being applicable in the country of use.
1.1 Users
This operation manual is intended for technically qualified users, who have been instructed
or trained in the operation of the pump unit.
1.2 Obligation to read
As an operator and user of the pump unit, you are obliged to read and understand this
operation manual and, in particular, its section „Safety regulations“. It is your safety that is at
stake! Should you have any question or uncertainty, contact WOERNER, please.
1.3 What to do in case of questions
In case of questions that you cannot solve by means of this operation manual, WOERNER
will help you. In such situations it is indispensable that you provide us with a precise
description of the problem at stake.
1.4 Operation manual
1.4.1 Applicability
This operation manual is applicable to the series versions of the GMI-A, GML-A, SAB-C and
GOI-A units. Should any part thereof be related to particular versions only, special reference
will be made.
1.4.2 Content and purpose
This operation manual contains the relevant information for the commissioning, operation
and maintenance of the pump unit. It is designed to help you in using the pump unit properly,
efficiently and safely.

Operating manual Page 6 of 32 B0102
GMI / GML / SAB / GOI
1.4.3 Location
This operation manual must always be available to the users at their places of work.
1.4.4 Meanings of safety notes and safety symbols
Safety notes
In this operation manual, the pictograms and key words for safety instructions, precautions,
and notes have the following meanings:
Danger! Any danger threatening immediately and capable of causing
serious personal injuries.
Warning! Any possibly dangerous situation capable of causing serious
personal injuries.
Caution! Any possibly dangerous situation that might cause minor
personal injuries.
Caution! Warning about property damage.
Note! Any possibly harmful situation in which the product itself or an
object in its close vicinity might be damaged.
Important! Notes on application and other useful information facilitating the
proper usage of the product.
Danger! Any danger threatening immediately due to the presence of
electric current that may cause serious personal injuries.

Operating manual Page 7 of 32 B0102
GMI / GML / SAB / GOI
2. Identification
2.1 Product brand and type designation
Piston pump unit manufactured by Eugen Woerner GmbH & Co. KG
Product type: GMI-A
GML-A
SAB-C
GOI-A
2.2 Product version
Version as of model year 2015
2.3 Product marking
The type label is located at the side of the pump body and contains information as follows:
Manufacturer:
Type (e.g. GMI-A)
No.:<order number> (e.g. 612345/1)
Model year
2.4 Manufacturer and contact address
Eugen Woerner GmbH & Co. KG
Hafenstrasse 2
DE-97877 Wertheim
Phone +49 9342 803-0
Facsimile +49 9342 803-202
Net www.woerner.de
E-Mail info@woerner.de
2.5 Conformity
The pump unit is in conformity with the EC directive on machinery (2006/42/EG).
For the content of the declaration of conformity see the appendix (sub-section 11)

Operating manual Page 8 of 32 B0102
GMI / GML / SAB / GOI
3. Product description
3.1 Purpose of use
The unit GMI, SAB and GOI is designed for the delivery of lube oils as of
10 mm²/s exclusively.
The delivery pump GML-A is designed for the delivery of lube greases up
to NLGI class 2 exclusively.
3.2 Limits of use
The application area of the pump unit’s components is restricted as follows:
Temperature range: -10 …+50 °C
Depending on the version, these limits of use may be restricted further. Such further
restrictions are dealth with in this operation manual later on.
Besides, the unit’s area of application is determined by the medium to be delivered. Hence,
when determining the area of application, you also need to refer to the technical data sheets
for the medium to be used.
3.3 Ambient conditions
Unit operation in an aggressive atmosphere (solvent vapours, acids,
lyes, salt water mist, etc.) may cause damage to or corrosion of
components and, thus, failure of the system and endangerment due to
leaking lubricant!
Ambient temperature range
Lower temperature limit: -10 °C
Upper temperature limit: +50 °C
Relative humidity: 70% at max.
Noise level : <70 dB(A)
Physical environment
In heights as of 1.000 metres above sea level, the system should be operated after
consultation with the manufacturer only.

Operating manual Page 9 of 32 B0102
GMI / GML / SAB / GOI
3.4 Conventional usage
The unit is exclusively designed for the delivery of lubricating oils (GMI, SAB, GOI) or
lubricating greases (GML) in central lubrication systems. Conventional usage also includes:
the observance of the safety notes and adherence to the safety regulations contained
in this operation manual,
the adherence to the maintenance and servicing instructions given in this operation
manual.
Any usage contrary hereto or going beyond the conventional one may
cause serious personal and property damage.
The delivery of gases, liquefied gases, gases dissolved under pressure,
vapours, and liquids the vapour pressure of which exceeds, at the permissible
maximum temperature, the normal atmospheric pressure (1013 mbar) by
more than 0,5 bar, as well as that of highly inflammable or explosive media
and foodstuff is prohibited!
Important! Please also note the safety data sheets pertaining to the
materials used!
3.5 Technical data
3.5.1 Assemblies
The unit consists of up to two assemblies the different versions of which may vary:
Pump body with drive
Reservoir with level switch monitoring

Operating manual Page 10 of 32 B0102
GMI / GML / SAB / GOI
3.5.2 Dimensions
GMI-A and SAB-C:
Weight:
with reservoir 1,40 kg
without reservoir 1,15 kg
see also data sheet P0655 (GMI-A) or P0643 (SAB-C)
2-4-point
1-point
Version without
reservoir:
1-point
2-4-point
View X
for connection
thread G 1/8
for pipe
AD4
1-point
Function control
1-point impossible!
2-point
3-point
4-point
Function control
Coil and socket
rotatable in steps of 90°

Operating manual Page 11 of 32 B0102
GMI / GML / SAB / GOI
GML-A:
Weight:
with reservoir 1,85 kg
without reservoir 1,15 kg
see also data sheet P0102
Special versions see appendix.
Delivery pump
1-point: 1
Delivery pump
multi-digit: 2, 3, 4, 2A
Version
without reservoir:
View X
1-point
2-point
3-point
4-point
2-point (2A)
Function control
Coil and box
turnable in 90°
steps
1= Outlets for pipe-AD4 or G 1/8
2= Vent plug
2-4-point
2-4-point
1-point
1-point

Operating manual Page 12 of 32 B0102
GMI / GML / SAB / GOI
GOI-A:
Version without reservoir:
Weight:
with reservoir 1,65 kg
without reservoir 1,40 kg
see also data sheet P0657
appr.
Air connector
G 1/8
Throttle screw for
adjusting the air flow
Outlet
G 1/8
View X
Function control
1-point impossible
2-point
Function control
1-point
1-point
2-point
appr.
appr.
appr.
appr.
appr.
appr.
appr.
2-point
1-point

Operating manual Page 13 of 32 B0102
GMI / GML / SAB / GOI
Build-in level switch: (GMI / SAB / GOI)
3.5.3 Technical data
In its basic version, the unit comprises the pump body with magnet exciter and a reservoir
mounted on. The technical data of this unit is as follows:
Unit:
GMI-A
GML-A
SAB-C
GOI-A
Delivery volume per
stroke and outlet
30 mm³
30 mm³
15 mm³
15 mm³
Number of strokes
at max.
approx.
100 min-1
approx.
250 min-1
approx.
250 min-1
Number of outlets
1 … 4
1 …4
1 …4
1 or 2
Actuation time at
min.
approx. 0,1 s
approx. 0,1 s
approx. 0,1 s
approx. 0,1 s
Medium
Oil
11 …1900 cP
Grease
up to NLGI-Kl. 2
Oil
11 …1900 cP
Oil
11 …1900 cP
Temperature range
-10 …+50 °C
-10 …+ 50 °C
-10 …+50 °C
-10 …+50 °C
Reservoir capacity
0,7 l
Cartridge 400 g
DIN 1284
0,7 l
0,7 l
Air pressure at max
-
-
-
6 bar
Material
pump body
Aluminium
Aluminium
Aluminium
Aluminium
Material reservoir
Polyethylene
Steel
Polyethylene
Polyethylene
Material
gaskets
FPM
FPM
FPM
FPM

Operating manual Page 14 of 32 B0102
GMI / GML / SAB / GOI
Electric magnet:
Rated power Variant "A" 30 W
Variant "C" 165 W
Switch-on duration Variant "A" 100%
Variant "C" 15%
Current at 24 VDC Variant "A" 1,27 A
Current at 230 VAC Variant "A" 0,15 A
Variant "C" 0,59 A
Protection type DIN EN 60529 IP65
Insulation class F
Plug-in connection DIN EN 175301-803, shape A
Level switch:
Switching power 10 W / 30 VA
Switching current max. 0,5 A
Switching voltage max. 230 VUC
Protection type DIN EN 60529 IP65
Plug-in connection DIN EN 175301-803, shape A
Function control:
Voltage 10 …30 VDC
Load current ≤200 mA
Protection type DIN EN 60529 IP67
Connection Plug-in connection M8x1, 3-pin
Output PNP NO function
When connecting inductive or capacitive loads, the relevant sup-
pressor circuits (diode, RC element, varistor) need to be provided for!
4. Functional description
4.1 Drive
The unit is driven by a d.c. solenoid actuator, which is laterally screwed on the pump casing.
The solenoid actuator is energised by externally switching the voltage supply. For that
purpose, an external controller is required.

Operating manual Page 15 of 32 B0102
GMI / GML / SAB / GOI
4.2 Operation GMI-A, GML-A and SAB-C
Suction phase
Function scheme:
Pressure phase
Suction connection
(reservoir)
Check valve
The delivery pump consits of a piston pump, an electric magnet and an oil reservoir.
Suction phase:
The pistons are reset by spring force with the lubricant being sucked in from the reservoir by
virtue of the vacuum generated.
Compression phase:
Upon electric magnet actuation, the pistons start to deliver to lubricant through the nozzles to
the lubricating points.
4.3 Operation GOI-A
Suction phase Pressure phase
Suction connector (reservoir) Suction connector (reservoir)
The aggregate consits of a one- or two-digit piston pump, an electric magnet, a control unit
and an oil reservoir.
Suction phase:
The piston is put back by means of spring tension. Due to the negative pressure generated,
the medium will be sucked out of the reservoir.
Pressure phase:
The magnet actuated piston delivers the medium into the airflow. By virtue of the airflow
preset via the throttle valves the resulting oil film will be continuously transported to the
friction and lubrication points.

Operating manual Page 16 of 32 B0102
GMI / GML / SAB / GOI
4.4 Function control (optional)
Functional description:
The function control is basing on an inductive proximity switch, which monitors the piston
movement of the supply pump. When the supply pump fails, the function control immediately
detects that condition. Switch output open at idle position.
Replacing the proximity switch
(damped type)
Replacing the proximity switch
(non-damped type)
Pull off the plug from the proximity switch.
Loosen the locknut. Unscrew anticlockwise
the proximity switch out of the plastic insert.
Screw clockwise the new proximity switch by
hand force into the plastic case to bottom
stop. Slightly tighten the locknut on the
plastic case and mount the plug on the
proximity switch.
Pull off the plug from the proximity switch.
Loosen the locknut. Unscrew anticlockwise
the proximity switch out of the pump case.
Energise the electric magnet (consider the
duty cycle), to make shure that the pistons
has moved out. Screw clockwise the new
proximity switch into the pump case to
bottom stop and turn it back anticlockwise by
half a turn, then. Slightly tighten the locknut
on the pump case and mount the plug on the
proximity switch.
Technical data: Proximity switch
Sensing distance: 2,5 mm
(not flush with surface)
Residual ripple: ≤10%
Connecting diagram:
Technical data: Proximity switch
Sensing distance: 1.5 mm
(flush with surface)
Residual ripple: ≤10%
Connecting diagram:
Spare part order number: 913.900-65
Spare part order number: 913.900-66
Fault elimination guide in case of faults:
Check the plug for tight contact, check the distance of the proximity switch related to the
supply piston and inspect the cable for damage (cable break).

Operating manual Page 17 of 32 B0102
GMI / GML / SAB / GOI
5. Safety notes
5.1 Basic principle
The unit leaves the factory in flawless condition and ensures high technical safety.
The unit is in conformity with the rules of technology and the applicable safety and health
regulations. Nevertheless, in case of incorrect operation or misuse, risks are threatening to
the:
lives and bodies of the users or third parties,
unit or other operator assets,
efficient use of the unit.
5.2 Requirements on user training
Any person getting to work on the unit must be authorised and trained for that purpose by
the operator. They must be able to recognise and avoid potential risks. This also includes
knowledge in the accident prevention regulations, first-aid measures, and local rescue
facilities.
The unit may be inspected, maintained and repaired by technically skilled
personnel with product-specific training only.
Work on electric facilities may be performed by skilled electricians in
conformity with DIN VDE 1000-10 only.
5.3 Safety facilities
Mechanically, the unit is built intrinsically safe.
The unit may not be operated unless the reservoir lid is closed.

Operating manual Page 18 of 32 B0102
GMI / GML / SAB / GOI
5.4 Accident prevention
For accident prevention, take these measures:
Prevent unauthorised persons from accessing the unit.
Keep foreign persons away from the areas and places of risk.
Inform present foreign persons about residual risks repeatedly. Inform yourself about
such risks in the "Residual risks" section.
5.5 Residual risks
When using the unit properly and adhering to the maintenance and repair cycles and
measures prescribed, there are no residual risks to persons and objects within the unit’s
area.
5.6 Incorrect applications
Any usage contrary hereto or going beyond the conventional one may cause
serious personal and property damage.
As experience shows, possible incorrect applications include, for instance, the following:
the delivery of highly inflammable or explosive media,
the delivery of media being capable of reacting with the materials used for the unit,
the delivery of foodstuff.
5.7 General safety regulations and duties
Basically, the following safety regulations and duties are applicable to the use
of the pump unit:
The generally accepted rules for work safety need to be oserved.
Besides, the basic regulations and rules on work safety and
accident prevention being applicable to the place of use have to
be followed.
When using the unit inside vehicles, the generally accepted
traffic law-related rules need to be observed.
The user is obliged to observe the regulations pertaining to the
use of working appliances.
The unit must be operated in flawless and clean condition only.

Operating manual Page 19 of 32 B0102
GMI / GML / SAB / GOI
It is prohibited to remove, modify, bridge or bypass any and all
protection, safety or monitoring facilities.
It is prohibited to reconstruct or modify the unit.
The operator should be notified of any fault or damage
immediately.
For repair, no others than original spare parts may be used.
The operator is required to regularly check and maintain all
protection, safety, and monitoring facilities.
After every repair, the flawless condition of the unit must be
ensured by means of a test run.
5.8 Disclaimer
Should any damage be caused to persons, objects, the environment and/or property due to
the non-observance of this operation manual, no matter whether intentionally or
unintentionally, WOERNER shall be held harmless thereof. Besides, all warranty claims will
be rejected. The same also applies to any and all consequential damage.
6. Transportation, installation, commissioning and shutdown transport
6.1 Transportation
Transport the unit to its destination carefully and by using suitable aids.
6.2 Unpacking
Lift the unit out of its packaging carefully and put it on a stable and plane base.
Note! The unit and the components attached in accordance with the
scope of delivery may still contain residues of blue-dyed test oil.

Operating manual Page 20 of 32 B0102
GMI / GML / SAB / GOI
6.3 Installation
The unit is ready for wall-mounting. It is to be secured by means of two M5 screws. The
mounting surface must be sufficiently stable in order to be capable of carrying the pump
unit’s weight including the filled reservoir. Besides, it needs to be ensured that the
mounting surface is vertical and plane.
Drill scheme:
6.4 Power supply and switch-on
Important! Be careful to compare the data of the local voltage supply with
that given under "Technical data".
Important! Lay the power supply cable such that it cannot be torn off
inadvertently.
Important! Work on electric facilities may only be performed by skilled
electricians in conformity with DIN VDE 1000-10.
Connect the unit to the voltage supply and control.
Check the electric connections for correct installation prior to commissioning.
Caution!
Work on electric facilities implies danger to life!
Electrical connection diagrams
Solenoid
A/W1 and C/W1 A/G1 Level switch Function control 1
Alternating voltage Direct voltage NO contact NC contact
30
This manual suits for next models
3
Table of contents
Other WOERNER Lubrication System manuals
Popular Lubrication System manuals by other brands
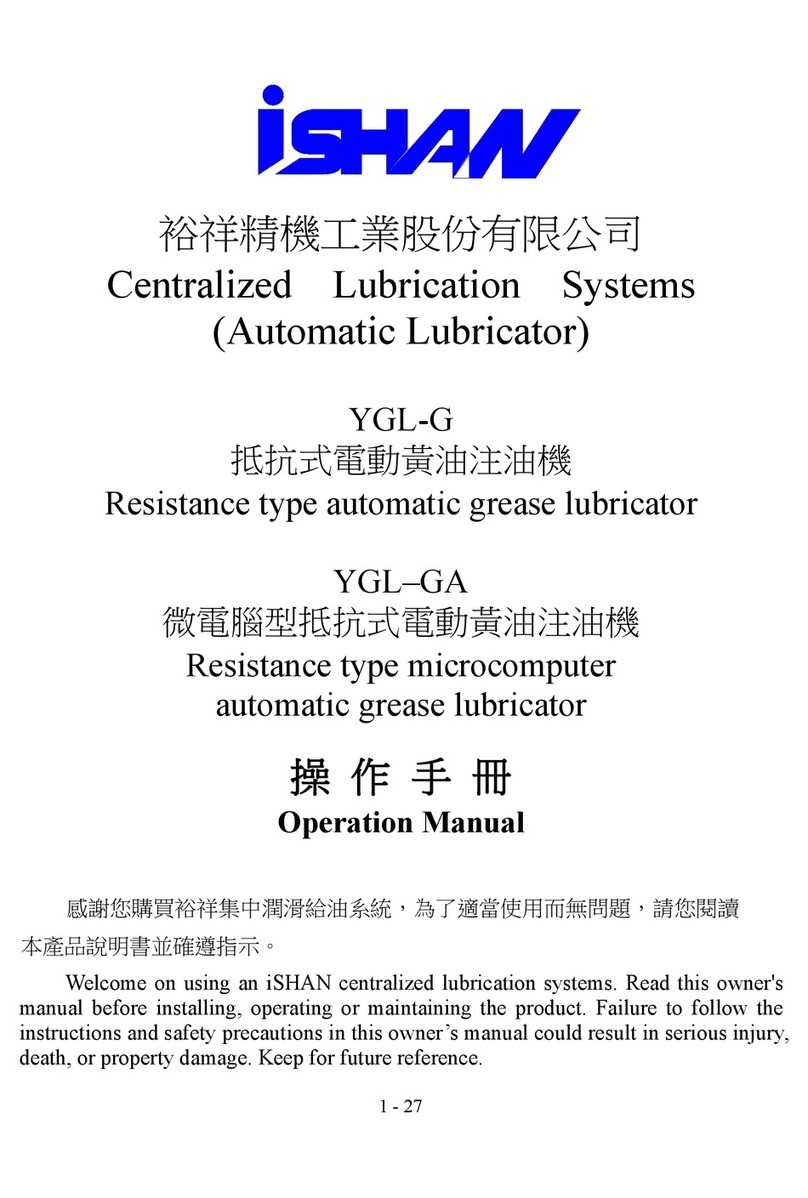
iSHAN
iSHAN YGL-G Operation manual
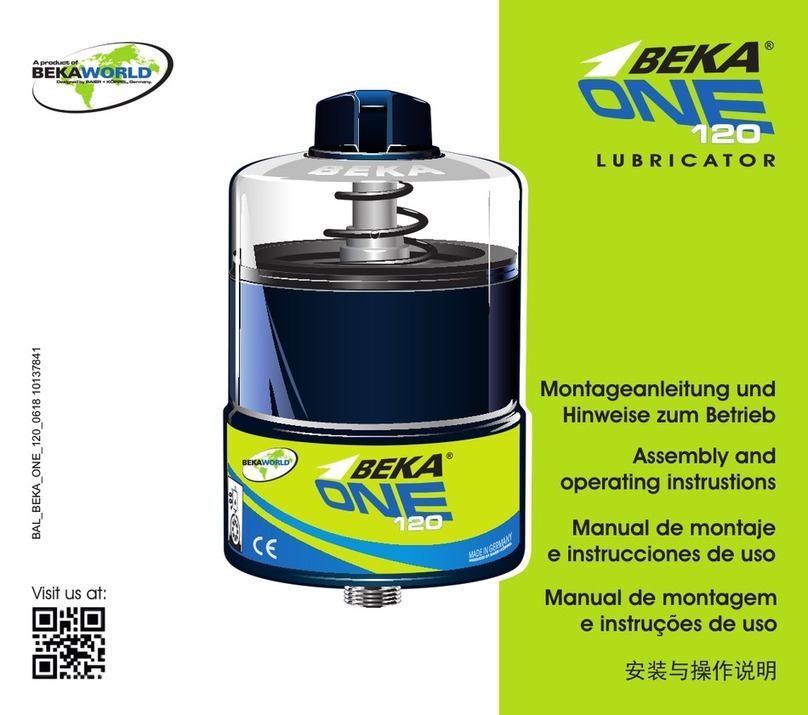
BEKA
BEKA ONE 120 Assembly and operating instrustions

RelaDyne
RelaDyne LUBRIMATE Installation & operation manual
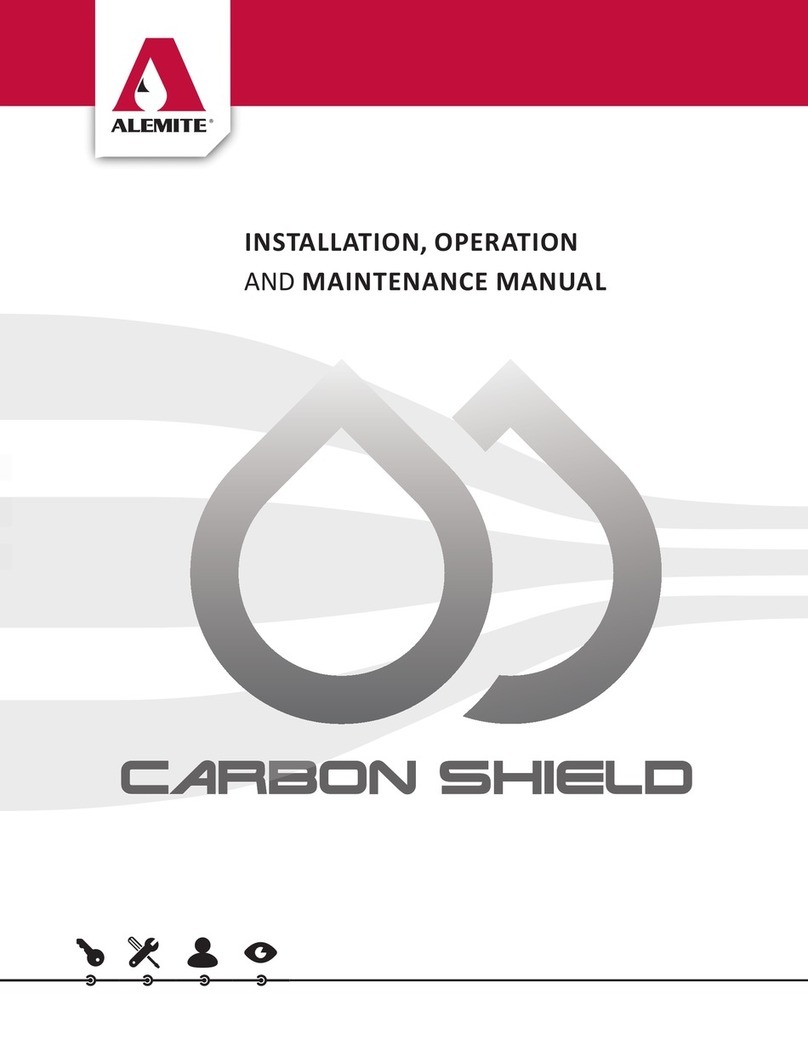
Alemite
Alemite Carbon Shield Installation, operation and maintenance manual

Wilkerson
Wilkerson B18 Installation & service instructions

DLS
DLS FlexxPump 125 B quick start