NSK MEGATORQUE MOTOR SYSTEM User manual

MEGATORQUE®MOTOR SYSTEM
User’s Manual
(EDC Driver Unit CC-Link Option)
Document Number: C20157-02
M-E099DC0C2-157

Limited Warranty
NSK Ltd. warrants its products to be free from defects in material and/or workmanship which NSK
Ltd. is notified of in writing within, which comes first, one (1) year of shipment or 2400 total
operation hours. NSK Ltd., at its option, and with transportation charges prepaid by the claimant,
will repair or replace any product which has been proved to the satisfaction of NSK Ltd. to have a
defect in material and/or workmanship.
This warranty is the sole and exclusive remedy available, and under no circumstances shall NSK
Ltd. be liable for any consequential damages, loss of profits and/or personal injury as a result of
claim arising under this limited warranty. NSK Ltd. makes no other warranty express or implied,
and disclaims any warranties for fitness for a particular purpose or merchantability.
Copyright 2011 by NSK Ltd., Tokyo, Japan
All rights reserved.
No part of this publication may be reproduced in any
form or by any means without permission in writing
from NSK Ltd.
NSK Ltd. reserves the right to make changes to any
products herein to improve reliability, function or design
without prior notice and without any obligation.
NSK Ltd. does not assume any liability arising out of the
application or use of any product described herein;
neither does it convey any license under its present
patent nor the rights of others.
Patents issued and patents pending.
“MEGATORQUE” is a registered trademark of NSK Ltd. in
Japan and that of NSK Corp. in the United States of
America.

— i —
Contents
1. Introduction -----------------------------------1-1
1.1.Notes for Users -------------------------------------------1-2
1.1.1. Notes for Safety------------------------------------1-2
2. Specifications ---------------------------------2-1
2.1. General Specifications-----------------------------------2-1
2.2. Specifications of Hardware Interface-----------------2-1
2.2.1. External Dimensions------------------------------2-1
2.2.2. CN2: Control Input/Output Signal Connector
2.2.2.1. CN2 Pin-Out --------------------------------2-4
2.2.2.2. CN2 Signal List ----------------------------2-5
2.2.3. CN6: Interface Connector ----------------------2-6
2.2.3.1. C6 Pin-Out ----------------------------------2-6
2.2.4. SW1 • SW2: Station Number Switch --------2-7
2.2.5. SW3: Baud Rate Setting Switch --------------2-7
2.2.6. SW4: Terminal Resistor Switch ----------------2-7
2.2.7. LED Status Monitor (SD, RD, RUN and ERR)
----------------------------------------------------------2-8
2.2.8. Wiring Example-------------------------------------2-9
2.3. Software Interface Specification -------------------2-10
2.3.1. Remote Input/Output----------------------------2-10
2.3.2. Remote Register---------------------------------2-12
3. Operation -------------------------------------3-1
3.1. Operation Mode and Input/Output -------------------3-1
3.2. Change of Operation Mode ---------------------------3-2
3.3. Servo-on in the Maintenance Mode -----------------3-2
3.4. Monitoring Control Input/Output ---------------------3-4
3.4.1. Monitoring the State of Remote Inputs/Outputs:
Monitor IO4 ------------------------------------------3-5
3.4.2. Monitoring State of the CC-Link Interface:
Monitor BS--------------------------------------------3-6
3.5. Function Assignment of Control Inputs/Outputs---3-7
3.5.1. Function of Conrol Inputs------------------------3-8
3.5.2. Function of Control Outputs -----------------3-10
3.5.3. Editing Coptrol Inputs/Outputs --------------3-12
3.5.3.1. Editing Contorl Inputs ------------------3-12
3.5.3.2. Editing Control Outputs ----------------3-15
3.5.3.3. Masking the Function of Control
Inputs/Outputs ---------------------------3-18
3.5.3.4. Forcible Change in Setting Control
Output Port Function ---------------------3-19
4. Alarm and Warning--------------------------4-1
4.1. Cause and Rmedy of Alarm and Remedy -------- 4-1
4.1.1. C4: Fieldbus Error -------------------------------- 4-1
4.1.2. C5: Fieldbus Warning -------------------------- 4-2

— ii —
(Blank Page)

1. Introduction
— 1-1 —
1. Introduction
This manual describes an option of the Megatorque Motor System that consists of the EDC
Driver Unit CC-Link option. Please refer to the user’s manual of the Megatorque Motor System
(EDC Driver Unit System) for other details.
Connection of the optional EDC Driver Unit to the CC-Link network will make you utilize its
control Input/Output functions through the master station.
For your safety, please be sure to read the user’s manual thoroughly before operating the
Megatorque Motor System.
1.1. Notes for Users
1.1.1. Notes for Safety
For your safety, you should read this manual thoroughly and understand the contents before
operating the Megatorque Motor System.
The following notices are added to give particular emphasis on the safety precautions in this
manual.
!Danger : A matter that might cause serious injuries.
!Warning : A matter that might result in injuries.
!Caution : A matter that might result in the breakdown of equipment into which the
Motor is installed or the break down of the mechanism surrounding the
Motor.

1. Introduction
— 1-2 —
(Blank Page)

2. Specification
— 2-1 —
2. Specifications
2.1. General Specifications
Table 2-1: General specifications
Item Description
Protocol CC–Link Ver.1.10
Number of slave stations
(Type of station) 2 Remote device stations
Number of addressable
remote input ports 17 16 ports are available for any function
assignment
Number of addressable
remote output ports 8
7 ports are available for any function
assignment
Remote register output 2 words Enables to configure the contents of output
2.2. Specifications of Hardware Interface
2.2.1. External Dimensions
Fig. 2-1: EDC Driver Unit compatible with CC-Link Network
( Motor type: PS1006, PS1012, PS1018, PS3015 and PS3030)

2. Specification
— 2-2 —
Fig. 2-2: EDC Driver Unit compatible with CC-Link Network
(Motor type: PS3060 and PS3090)

2. Specification
— 2-3 —
2.2.2. CN2: Control Input/Output Signal Connector
The table below shows the connectors for CN2.
Table 2-2: Connector list
Connector of Driver Unit DDK Ltd. DHF-RAA10-233NB-FA or equivalent
Mating connector DDK Ltd DHF-PDA10-3-A01-FA or equivalent
◊ An optional cable set (M-E011DCCN1-001) with the mating connector to the CN2 I/O
connector of the Driver Unit is available (Sold separately).
The followings are wiring precautions for the connector CN2.
1) Use a shielded cable for wiring of the CN2 connector.
2) These cables should be laid separately from the main power line.
3) Connect the one end of the shielded cable to the frame ground.
!Caution : Check for a wiring mistake in the polarity of external power supply, and
a shorting between connector pins.
!Caution : Never connect the idle pins that are insntructed as “Do not connect.”
Do not make them idle at the master controller (PLC, etc) side, after
you have connected all pins at the CN2 connector side.
• Connection of an idle pin that is instructed not to connect may make the
Driver Unit easily affected by external noise, and thus likely causing its
malfunction or breakdown.

2. Specification
— 2-4 —
2.2.2.1. CN2 Pin-Out
Figure 2-3 below shows the shipping set of the pin-out arrangement of the CN2 connector.
You may change the function assignment of each signal port.
(Except some ports that are dedicated to a certain function)
◊ Change to an extended capability port.
◊ Transfer an assigned function to other port.
◊ Mask the function of unused port.
The each port of the CN2 connector is assigned to the same port name as the remote
Input/Output of the CN6 interface connector, and the ports of both connectors are corresponsing
each other.
!Caution : A change of function assignment of a port of the CN2 connector forces the
function change to the remote Output/Input of the corresponding port.
Fig. 2.3: CN2 pin-out
1
DC24
6
PI3
(OTM)
2
-
7
-
3
PI0
EMST
8
PO0
(DRDY)
4
PI1
(ACLR)
9
-
5
PI2
(OTP)
10
COM
Note: Functions in brackets is the shipping set.
: The pins with hyphones “-“ are prophibited
connection.
EMST: Emargency stop
Input dedicated to the safety functions
DRDY: Driver Unit ready
NRM :Normal
Output dedicated to the safety functions
EMST : Emergency stop
A
CLR : Alarm clear
OTP : Travel limit, + direction
OTM : Travel limit, - direction
SVON : Servo ON
RUN : Positioning start
STP : Stop
PRG0 - 7: Internal program chanel
selection 0 to 7
JOG : Jogging
DIR : Jogging direction
HLD : Hold
ORD : Velocity override
IOFF : Integration OFF
HOS : Home Return start
HLS : Home position limit
General Input
PI0 and PO0 ports are dedicated to the safety function Input and Output. They have following
restrictions respectively.
◊ You cannot change the function of the port PI0 (Pin number 3: Input EMST
(Emergency stop)). You may only set the input port and the stability timer to it.
◊ You can only exchange the function of the PO0(Pin number 8: Output DRDY (Drive
Unit ready) with the function Output NRM (Normal). You cannot set the output logic
and the stability timer to it.

2. Specification
— 2-5 —
2.2.2.2. CN2 Signal List
Table 2-3: Signal name and function (shipping set)
Pin
No.
Port
code
Signal
code
Contact
logic Signal function Function
1 - DC24 -- 24 VDC external power
supply External power supply for input signal
2 - - - Do not connect -
3 PI0 EMST Normaly
closed Emergency stop Interrupts the positioning and stops with the dynamic
brake
4 PI1 ACLR Normaly
open Alarm clear Clears warning
5 PI2 OTP Normaly
closed Travel limit, + direction If OTP input goes active, the Motor servo is locked in
the CW only
6 PI3 OTM Normaly
closed Travel limit, - direction If OTM input goes active, the Motor servo is locked in
the CCW only
7 - --Do not connect -
8 PO0 DRDY Positive Driver Unit ready Reports that the Motor is ready to rotate (Those pins
open when Motor is not ready, or an alarm occurs)
9 - --Do not connect -
10 - COM -Output signal COMMON Common for output signal
!Caution : Be sure to follow the operation manual when your Megatorque Motor
System is a custom-made version and the function of Input/Output signals
are specially arranged.
!Caution : Never connect the pins indicated as “Do not connect” Be sure to connect
these pins of the master controller (PLC, etc) side after you have connected
all pins of the CN2 connector. Otherwise, it may result in a malfunction or
breakdown of the system.

2. Specification
— 2-6 —
2.2.3. CN6: Interface Connector
The CN6 connector interfaces with the CC-Link network.
The followings are the reference for the connectors that are used for the CN6 connector.
Table 2-4: CN6 mating connectors
Connector, Driver Unit side Phoenix Contact Gmbh, & Co. MSTB2,5/5-GF-5,08AU or
equivalent
Mating connector Phoenix Contact Gmbh, & Co. MSTB2,5/5-STF-5,08AU or
equivalent
Table 2-5 below shows the reference data for the mating connectors.
Table 2-5: Reference data of the mating connector
Item Specification
Cable to be used (single connection) 0.2 to 2.5 [mm2] (twisted) (AWG24 to 12)
Cable to be used (double connection) 0.2 to 1.5 [mm2] (twisted)
Removed coat length 7 [mm]
Machine screws to be used M3
Tightning torque 0.5 to 0.6 [N·m]
2.2.3.1. CN6 Pin-Out
Table 2-6: CN6 pin-out
Pin
No.
Signal
code Function Description
1 FG Frame ground Connect the frame ground
2 SLD Shield Connect the shielded cable (Frame ground cable)
3 DA Data A Connect the data A cable
4 DB Data B Connect the data B cable
1: FG
Top of the Driver Unit
2: SLD
3: DA
4: DB
5: DG
5 DG Data ground Connect the data ground cable

2. Specification
— 2-7 —
2.2.4. SW1•SW2: Station Number Switch
These rotary switches set the station number from 1 to 64.
The SW1sets the tens place of the number, while the SW2 switch sets the ones place.
Table 2-7: Station number switch
SW1 SW2 Station number
0 0 (Never set)
0 1 1 (Shipping set)
…
…
…
Driver U nit’s upper side
SW2: ×1
SW 1: ×10
5 0
1
23
4
6
7 8
9
5 0
1
23
4
6
7 8
9
6 4 64
2.2.5. SW3: Baud Rate Setting Switch
The switch sets the baud rate.
Table 2-8: Baud rate setting switch
SW3 Baud rate[bps]
0 156k
1 625k
2 2.5M
3 5M
4 10M (Shipping set)
5 0
1
23
4
6
7 8
9
Driver Unit’s upper side
5 - 9 Never set
2.2.6. SW4: Terminal Resistor Switch
Set the terminal resistor when connecting the Driver Unit to the end of the network.
◊ Select the resistor value in accordance with the characteristic impedance of the cable.
Be sure to turn off the power of the Driver Unit when setting the terminal resistor.
Table 2-9: Terminal resistor setting switch
SW4 Terminating
resistance Description
Up 130 [Ω] • The terminal resistor is on
(When the characteristic impedance of the cable is 130 [Ω])
Neutral None • The terminal resistor is off (Shipping set)
Driver Unit’s upper side
130Ω
11 0Ω
O
FF
Down 110 [Ω] • The terminal resistor is on
(When the characteristic impedance of the cable is 110 [Ω])

2. Specification
— 2-8 —
2.2.7. LED Status Monitor (SD, RD, RUN and ERR)
The monitor indicates the status of conection and communicatoin with the network.
When the communication status is nomal, the indicators RUN, RD and SD are on, and that of
ERR is off (In some baud rate, the RD and SD indicators seem like blinking).
Table 2-10: LED status monitor
Indicator Color Description
SD On: In the middle of tarnsmitting data
RD On: In the middle of receiving data
RUN
Green
On: Executing the data link. The unit is normal
Off: Not linked to the network. Caririer detection NG, Time-Over, Resetting
Driver Unit’s upper side
SD
RD
RUN
ERR
ERR Red
On:CRC error, SW1and 2 (Station number) setting error, or SW3 (Baud rate)
setting error
Off: Communicating normally or Resetting hardware
Blinking: The switch setting (SW1, 2 and 3 ) is altered
Table 2-11: Monitoring pattern
SD RD RUN ERR Status
✷●●○Communicating normally
✷●●✷Communicating normaly, with occasional CRC error
✷●●✷*
Baud rate and/or station number setting are alterd at the time of power
on.
*LED flickers at intervals of every 0.4 [s]
○●●✷Transferred data become “CRC Error” and thus unable to responsd
○●●○No data transmission to the Driver Unit
✷●○✷Though the polling is responding, the refresh receiving has a CRC error
○●○✷Cannnot respond as the data to the Driver Unit has a CRC error
✷●○○The communication link is not active
○●○○No data sent to the Driver Unit, or impossible to receive the data
○○○○Impossible to receive the data. Power shutdown, or the hardware is in
the middle of resetting
○●/○ ○●Setting error on the baud rate or station number
●: On ✷: Blinking ○: Off
The SD monitor is blinking quickly, and thus it occasionally seemes like as if it is on depending
on the communication state.

2. Specification
— 2-9 —
2.2.8. Wiring Example
Refer to “Figure 2-4: Wiring example” below for wiring the Drive Unit to the CC-Link.
◊ Be sure to use a cable dedicated to the CC-Link.
◊ The wiring order is not necessarily the same order of station numbers.
Fig. 2-4: Wiring example
DA
DB
DG
SLD
FG
DA
DB
DG
SLD
FG
DA
DB
DG
SLD
FG
Terminating
resistor
Terminating
resistor
CC-Link dedicated cable CC-Link dedicated cable
Master station
Remote station
(EDC Driver Unit) Local station
When the EDC Driver
Unit is the terminating
unit, the SW4 switch
may be used for the
function of terminating
resistor.
When the grounding terminal of the Driver Unit (Heat sink) is
grounded, grounding of the FG terminal of the CN6 connector
is not necessary.
Connect the shielded wire of the CC-Link dedicated cable to the SLD terminal of CN6 connector.
The SLD terminal is connected to the housing of the Driver Unit through the FG terminal and
thus, the shielded wire is grounded through the gorunding terminal of the Driver Unit (Heatsink).
Connect the terminating resistor between the DA and DB terminal of the both end units of the
network .
◊ The SW4 switch sets the terminating resistor for the EDC Driver Unit.

2. Specification
— 2-10 —
2.3. Software Interface Specification
2.3.1. Remote Input/Output
Table 2-12 “Remote Input/Output” on the next page shows the function of Input/Output of the
CN6 interface connector (Shipping set).
Excluding some ports, you may change the function assignment to the remote Input/Outpu ports.
Please refer to “3.5 Function Assignment of Control Input/Output” for the details of
Input/Output signal logic and the function that can be assigned to each Input/Output port.
◊ Replaces an assigned function with an extended function.
◊ A previously assigned function may be set to other port.
◊ Masks a unused port.
The same port name of the CN2 control I/O connector is assigned to the corresponding port of
the remote I/O connector and the I/O function of each port is also corresponding each other.
!Caution : Pay special attention when changing the function assignment of Remote
Input/Output port because that of the corresponding port of the CN2 signal
connector changes its function also.

2. Specification
— 2-11 —
Table 2-12: Remote Input/Output (m: A register number derived from the top station number)
Output Port
code
Signal
code Function Input
Port
code
Signal
code Function
RXm0 PO0 DRDY
Reports that the Motor is
ready for the operation RYm0 PI0 EMST
Interrupts the positioning
and stops with the dynamic
brake
RXm1 PO1 WRN
Alerts warning. RYm1 PI1 ACLR
Clears warning
RXm2 PO2 OTPA
Over travel limit (+) (Soft and
hard ware limit switch) RYm2 PI2 -Reserved *1
RXm3 PO3 OTMA
Over travel limit (-) (Soft and
hard ware limit switch) RYm3 PI3 -Reserved *1
RXm4 PO4 SVST
Reports the state of the servo RYm4 PI4 SVON
Turns the servo on
RXm5 PO5 BUSY
Reports the operation state RYm5 PI5 RUN
Starts the program operation
specified by the PRG input
RXm6 PO6 IPOS
Reports the conditions in
position error and positioning RYm6 PI6 STP
Stops positioning operation
RXm7 PO7 NEARA
Reports that the Motor is
approaching the target position RYm7 PI7 PRG0
RXm8 --(Reserved) RYm8 PI8 PRG1
RXm9 --(Reserved) RYm9 PI9 PRG2
RXmA --(Reserved) RYmA PI10 PRG3
RXmB --(Reserved) RYmB PI11 PRG4
RXmC --(Reserved) RYmC PI12 PRG5
RXmD --(Reserved) RYmD PI13 PRG6
RXmE --(Reserved) RYmE PI14 PRG7
A combination of 1 and 0
(ON/OFF) of the“Internal
program channel selection”
selects a channel to be
executed (Channel 0 -255)
RXmF --(Reserved) RYmF PI15 JOG
Starts and stops a jog
operation
RX(m+1)0 --(Reserved) RY(m+1)0 PI16 DIR
Specifies the direction of a
jog operation
RX(m+1)1
to
RX(m+2)F
--
(Reserved) RY(m+1)1
to
RY(m+2)F
--(Reserved)
RX(m+3)0
to
RX(m+3)7
--
(Reserved) RY(m+3)0
to
RY(m+3)7
--(Reserved)
RX(m+3)8 -Flag for processsing an initial data
(Not used) RY(m+3)8 -Flag for completion of initial data
processing. (Not used)
RX(m+3)9 -Flag for “End of initial data setting”
(Not used) RY(m+3)9 -Flag for initial data setting (Not used)
RX(m+3)A -Flag for positioning state (Not used) RY(m+3)A -Flag for requesting error reset (Not
used)
RX(m+3)B -The remote station is ready RY(m+3)B --(Reserved)
RX(m+3)C
to
RX(m+3)F
--(Reserved)
RY(m+3)C
to
RY(m+3)F
--(Resrved)
*1: The shipping set of PI2 and PI3 ports is assigned to signals of OTP and OTM respectively. These are the dedicated input signals from
the CN2: control I/O connector. An input from the CC-Link to these OTP and OTM function ports shall become invalid.
The PI0 and PO0 are dedicated ports for the signals fundamental to the safety function. There are
following restrictions respectively.
◊ You cannot change the function EMST(Emaergency stop) assigned to the Port PI0 (RYm0).
◊ The Output DRDY (Driver Unit Ready) assigned to the Port PO0 (RXm0) is only
interchangeable with the function of NRM(Normal).
Refer to “3.5 Function Assignment of Control Input/Output” for the logic of each function.

2. Specification
— 2-12 —
2.3.2. Remote Register
Table 2-13 “Remoto Register” shows the functon of remote register of the CN6 : interface
connector.
Remote register outputs data monitoring, such as a coordinate data, using two words of remote
register RWr.
◊ The data consists of 32 bit integer with the sign.
Table 2-13: Remote Register
m: A register number derived from the top station number
Output Function Input Function
RWrm+0 RWwm+0
RWrm+1
Monitor data set by the POD parameter
(LSW)
to
(MSW)
RWwm+1
RWrm+2 RWwm+2
RWrm+3 RWwm+3
RWrm+4 RWwm+4
RWrm+5 RWwm+5
RWrm+6 RWwm+6
RWrm+7
(Reserved)
RWwm+7
(Reserved)
The output is set by the parameter POD (Polling data).
◊ The parameter POD must accompany the name of monitor that is outputting data.
Table 2-14: Parameter related to the remote register output
Parameter Function Default Domain
POD Polling data TP Set POD + Monitor name

2. Specification
— 2-13 —
The following show an example to output the data of current velocity to the CC-Link.
1) Monitor TV (Current velocity readout) reports the current velocity of the Motor.
Set “Monitor TV” to the parameter POD (Polling data) to output to the CC-Link.
#
P
ODTV
#_
T
O DP ENT
V
2) Monitor TV reports the current velocity in units of a thousandth of [s -1 ] as described in
the “Megatorque Motor System User’s Manual ( EDC Driver Unit System)”.
◊ The current velocity is given in the units of a thusandth as –5.000 when the Motor is rotating to
the minus direction at the velocity of 5 [S-1].
Fig. 2-5: Description of “Monitor TV” (Megatorque Motor System User’s Manual [EDC Driver Unit System])
3) The decimal point is abbreviated when outputting to the CC-Link.
When the Motor is rotating at -5.000, -5000 (FFFF EC78h in hexadecimal number)
will be outputted. Table 2-15 below shows an example of the relation between the
register address and the contents of an output.
Table 2-15: Output example of the remote register (When outputting -5000)
m: A register number derived from the top station number
Output Function Input Function
RWrm+0 EC78h RWwm+0
RWrm+1 FFFFh RWwm+1
RWrm+2 RWwm+2
RWrm+3 RWwm+3
RWrm+4 RWwm+4
RWrm+5 RWwm+5
RWrm+6 RWwm+6
RWrm+7
(Reserved)
RWwm+7
(Reserved)

2. Specification
— 2-14 —
(Blank Page)
Other manuals for MEGATORQUE MOTOR SYSTEM
1
Table of contents
Other NSK Engine manuals
Popular Engine manuals by other brands
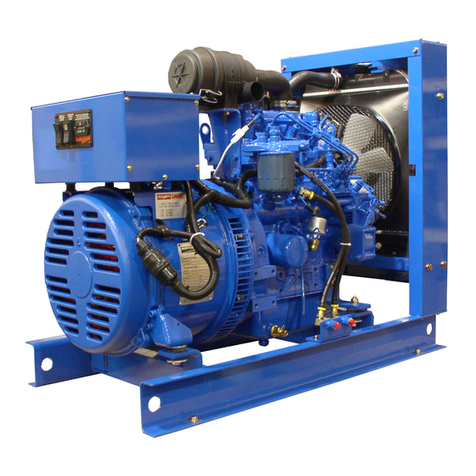
Northern Lights
Northern Lights NL773LW4 Operator's manual
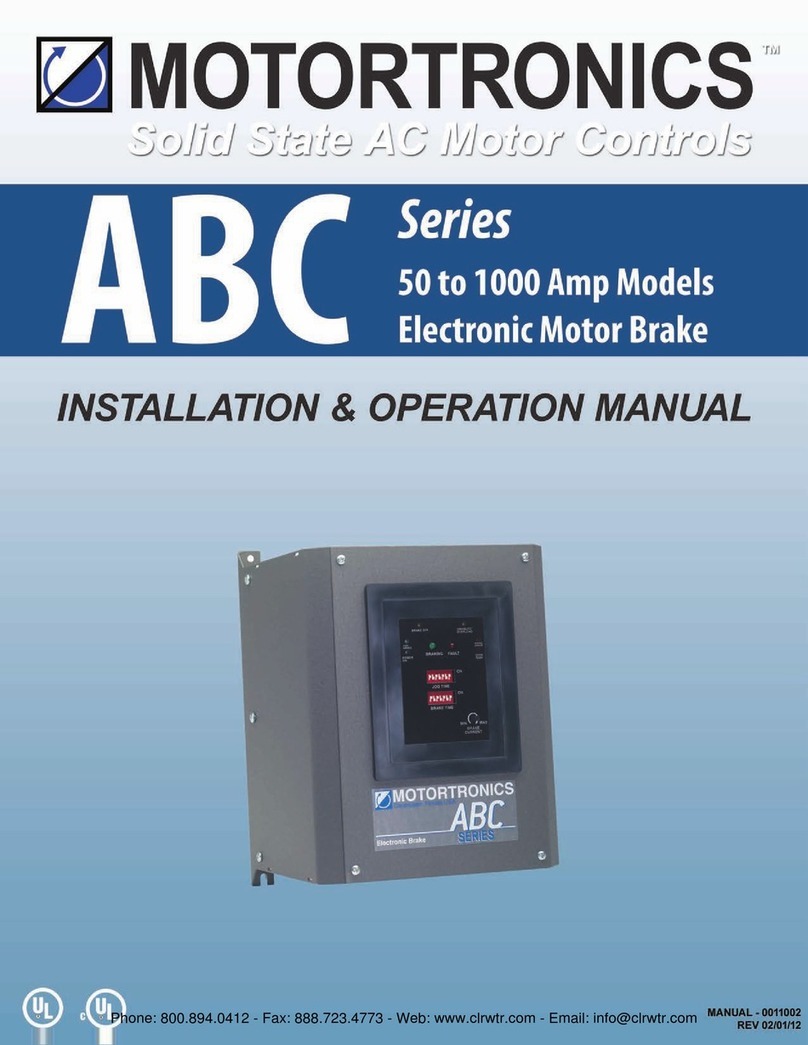
motortronics
motortronics ABC-100 Installation & operation manual

Schellenberg
Schellenberg ROLLODRIVE 65 PREMIUM manual
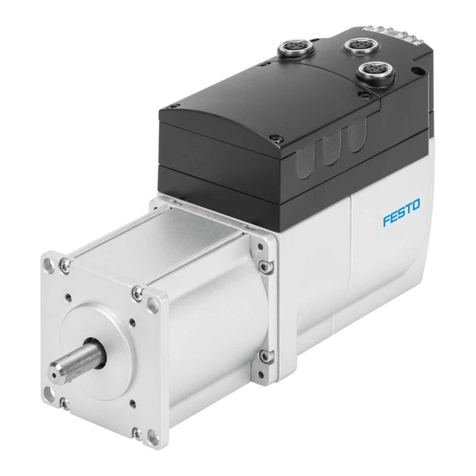
Festo
Festo EMCA-EC-67 CO Series instruction manual
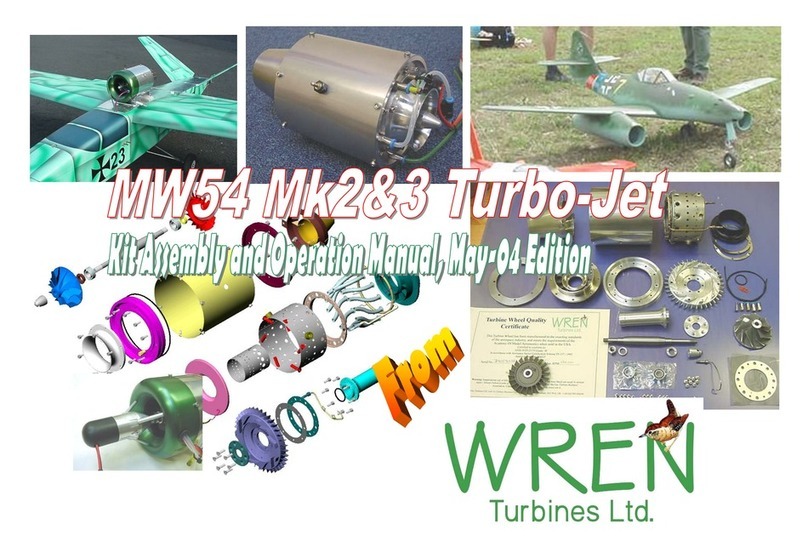
Wren Turbines
Wren Turbines MW54 Mk2 Kit assembly and instruction manual
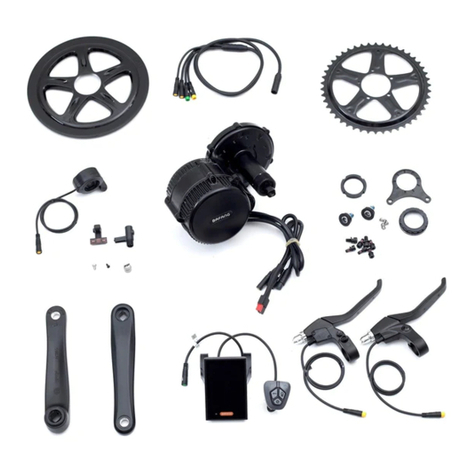
PIREZ
PIREZ BBS01 installation manual