Oki OKIPAGE 8c Plus User manual

Colour Guide

2OKIPAGE 8c
Brilliant Colour from Oki
Thank you for choosing the OKIPAGE 8c Colour Page Printer.
The OKIPAGE 8c offers brilliant colour printing at a fast 8
pages per minute on plain paper and 6 pages per minute on
transparencies - the OKIPAGE 8c is the perfect workgroup
printer for a wide range of business applications.
The following pages have been conceived to provide the
reader with a broad overview of the issues related to colour
printing, in order that the best use of colour be made in the
applications chosen. The text is designed to describe the
technical issues in a manner that can be understood by anyone
involved in the preparation of colour documents.
Please also familiarize yourself with the Operator
documentation provided – this describes specific operational
details of the OKIPAGE 8c set-up and configuration for
specific options.
We are sure that you will find the OKIPAGE 8c an excellent
part of your departmental printing soloution. If you have any
comments with regard to the content of this document, then
please let us know through your local Oki representative.

Colour Guide 3
English
Contents
Brilliant Colour from Oki ............................................ 2
The use of colour ......................................................... 4
Colour perception ........................................................ 5
The electromagnetic spectrum.................................... 6
Primary and secondary colours .................................. 7
Additive and subtractive primaries ....................... 7
Additive primaries.............................................. 8
Subtractive primaries ......................................... 8
Neutral Colours ............................................................ 9
Colour Complements ................................................... 9
Colour wheel .............................................................. 10
The problems with using colour ............................... 11
Colour management systems................................ 11
Specifying colour....................................................... 12
Printing colour....................................................... 14
Colour registration................................................ 14
Colour adjustments ............................................... 15
The OKIPAGE 8c printer driver ........................... 16
Print Modes....................................................... 16
Halftone Settings .............................................. 17
Image Colour Matching ................................... 17
Colour Settings ................................................. 18
Manual Adjustment .......................................... 18
Glossary ...................................................................... 19
Index ........................................................................... 23

4OKIPAGE 8c
The use of colour
Recent advances have brought colour to the desktop in a way
that could not have been imagined a decade ago. It has been
shown that using colour in print can increase memory
retention by up to 65% and readership by as much as 40%,
not to mention the added impact that it provides. As colour
becomes more and more accessible it is essential to
understand the importance of colour and how best to use it.
People use colour for different reasons; it has become a very
important tool and is used widely in marketing to grab
attention and communicate ideas, and when used effectively
can alter the viewer’s perception.
Colour can be used in text documents as well as for graphics.
It can be used to emphasise headings or particular words
which would otherwise be lost in the vast array of black and
white. Colour adds impetus to a company logo and can be as
important as the design itself. The use of colour also makes a
document easier to comprehend and can convey information
at a glance. For example, using red to highlight negative
figures in a spreadsheet.
The use of colour should be considered an integral part of
any presentation or document and not added at the end as an
afterthought.

Colour Guide 5
English
The following examples list some widely used colours and
their significance:
Thisisaverypowerful andpassionatecolour.Thepowerandpassion
thatitportrayshasmadeitafavouriteformanyexoticsportscars.
Unlikered,green is a very calming and ‘natural’colour.It signifies
trees,grassandplantlifeingeneral.Itissoothingandperhapsassociated
withastrollinafield.Aswellasthecalmingsideofgreen,itisalsothe
colourof envy.
Acool and refreshing colour. Itis the colour of summer skies and a
clearblueseawhichproducesacalmingeffect.Darkbluesareassociated
withwealthanddignityandalsohavenamesthatsuggestthesevirtues
–Royalblue,Navyblue,etc.
Thisisreallyanabsenceofcolourandthecontrastthatitprovideswith
othercolourshasmadeitoneofthemostwidelyused.Blackisusually
associatedwithnightanddarkness
The colour of pure snow and in itself suggests purity. It is used in
hospitalstoportrayanairofcleanlinessandsterility.Likeblack,white
canbepairedwithmost colours and is therefore verypopular.
In short, colours can be used effectively to send their own
message, regardless of the message that they are supporting.
The colours used within a message are seen and automatically
decoded before the message itself has been read. This
underlines the importance and effectiveness of using colour.
Colour perception
Colour does not exist by itself but is dependent on the
presence of:
• alightsource
• anobject
• anobserver
Our perception of colour involves light from a source being
reflected off, or transmitted through, an object and entering
the eye.

6OKIPAGE 8c
Light interacts with an object and what we see is the final
result of that interaction. An object can reflect, transmit or
emit light. A reflective object absorbs some sections of the
visible spectrum and reflects the rest. What we see is the
reflected portion. An object removing wavelengths at the ultra
violet end for example, will appear red in hue. A transmissive
object allows light to pass through it and may absorb a section.
The colour of the object in this case, will depend upon the
wavelengths of light that are allowed to pass through. An
emissive object emits light and the appearance of the light
will depend on the wavelengths emitted. In short, the
composition of the light and its interaction with the object
will define the colour we see.
The electromagnetic spectrum
All colours we can see fall into what is the visible part of the
electromagnetic (EM) spectrum. The visible portion of the
EM spectrum is minute and although we are ‘blind’ to the
rest, the part we can see has a significant effect on our
perception of everything around us.
If light containing all visible wavelengths in balanced
quantities is detected, then white light is seen. If there is an
absence of all wavelengths then black is perceived. The
infinite combination of different wavelengths give rise to what
we perceive as colour. So colour is light.
When our eyes receive information containing a strong
content of a particular wavelength then we interpret that as a
colour. A strong content around 700nm (0.0007mm
wavelength) is interpreted as red and at the other end of the
scale, 400nm is interpreted as violet.
1 micrometre = 1×10-6metre (0·001mm)
1 nanometre = 1×10-9metre (0·000001mm)
1picometre = 1×10-12metre (0·000000001mm)
1 fentometre = 1×10-15metre (0·000000000001mm)

Colour Guide 7
English
Primary and secondary colours
In theory, all colours can be made up from a very small group
of ‘colour elements’. There are three primary colours, and
all other colours can, in theory, be obtained by mixing the
primary colours in varying proportions. Mixing two primary
colours in equal proportions produces what is known as a
secondary colour.
Additive and subtractive primaries
Primary colours can be split into two categories which are
termed additive and subtractive. It is important to note the
difference between mixing additive primaries and subtractive
primaries. For example mixing red and green inks will
produce a ‘muddy’ brown, whilst red and green light mixes
to give yellow. So in which way do the two models differ ?
RED
YELLOW
GREEN
CYAN
BLUE MAGENTA

8OKIPAGE 8c
Additive primaries
Video technology such as computer monitors and television
screens use the additive model. The additive primaries are
Red, Green and Blue (RGB). Starting from black (lack of
colour) and adding red, green and blue in equal quantities
will generate shades of grey with white being generated with
full, balanced intensities of all three. Mixing the three colours
in different quantities will generate intermediate colours.
Subtractive primaries
Cyan, Magenta and Yellow (CMY) are known as the
subtractive primaries and are commonly used in printing
processes. In this case we start with a white background
(usually paper) and add translucent inks of cyan, magenta
and yellow to subtract certain wavelengths of light. For
example, cyan ink on a page appears to be this colour because
the ink removes components of red light and reflects green
and blue, which we perceive as cyan.
standarddot display Trinitron™ display
Traditional CMYK print

Colour Guide 9
English
In theory, a combination of the three subtractive primaries
will produce black. In practice however, pigments used in
inks are not perfect and usually give rise to a dark green/
brown. For this reason, in many colour output devices, a
separate black ink is used to produce greys and black (in
shadows and black text for example). This is the CMYK
model and is the method most widely used in the colour
printing and printer industry. The OKIPAGE 8c uses separate
cartridges of cyan, magenta, yellow and black toner to
generate high definition colour images for the workgroup or
networked environment.
Neutral Colours
Although the term ‘colour’ is applied, neutral colours do not
have properties of hue or saturation. They are described in
terms of lightness only. The neutral colours are black and
white and all shades of grey in between. A balanced mix of
cyan, magenta and yellow yields a neutral colour or black
(in theory). The same effect can be achieved with the additive
primaries by having an equal mix of red, green and blue light.
Colour Complements
Complements are pairs of colours that combine to produce a
neutral colour. It can be seen from the above that balanced
quantities of all three primaries produce a neutral. Mixing
two primaries produces a secondary colour. Mixing this
secondary colour with the remaining primary colour produces
a neutral colour. For example:
CYAN + MAGENTA + YELLOW = NEUTRAL
—red (magenta + yellow) + cyan = NEUTRAL
—green (yellow + cyan) + magenta = NEUTRAL
—blue (cyan + magenta) + yellow = NEUTRAL
This relationship can be applied to all colours and is shown
in more detail in the following section.

10 OKIPAGE 8c
Colour wheel
The relationship between colours can be best shown on what
is known as a colour wheel. The hue value of a particular
colour is expressed in degrees. Red for example is at 0° and
green and blue are located at 120° and 240° respectively.
The subtractive primaries, yellow, cyan and magenta are
located at mid points between these.
The colour wheel shows the following relationships:
• theadditiveprimariesare displaced by120°fromeachother.
• thesubtractive primariesaredisplacedby120°fromeachother.
• eachcolourisasecondarycolourofthetwocolourseithersideofit.
e.g.mixingequal quantitiesofyellowandmagentawillproducered.
• acolouris directly oppositeitscomplement.
We can continue to mix neighbouring colours on the colour
wheel to produce further, intermediate colours. The number
of colours on the colour wheel now doubles to twelve (as
shown below). Repeating the procedure a number of times
produces a colour wheel with subtle changes of hue from
neighbour to neighbour.
Colour Wheel
showingRGB(circles),CMY(squares)andtheir
firstsetofintermediatecolours.

Colour Guide 11
English
The problems with using colour
As already explained, a computer monitor, where an image is
first viewed, and a printer which produces the final document
use different methods to generate colours. Indeed they are based
around a different set of primaries (RGB for monitors, CMYK
for printers). Monitors do not generate a full range of perfect
colours and neither do printers. There is a limit on how many
colours a monitor or printer can generate. This is known as a
device’s colour gamut. Some colours can be reproduced by
both devices, while others can be displayed on a monitor but
cannot be printed or vice versa. This in practice may lead to a
colour print not resembling the original on-screen image. So
what has happened?
Images (graphics and text) can be captured through scans or
digital photography, or input directly into the PC via
applications programs. However the original image is
obtained, it will be displayed and manipulated in RGB colour
space (on-screen) and finally converted to CMYK for print.
Each of these processes requires data conversion/
manipulation. An image seen on a computer monitor relies on
the monitor’s ability to reproduce the image and represent
colours within it. Adjustments such as brightness, colour and
contrast also tailor the image to the preference of the viewer
rather than a display of true colour. The data sent to the printer
may not be adjusted to allow for imperfections in the inks used.
Colour management systems
Colour Management Systems (CMS) such as those found in
the OKIPAGE 8c printer driver, allow for any mismatches that
may occur between the RGB and CMYK conversion process.
Colour matching systems go a long way to ensuring a better
match between the input data and printed result but cannot
always allow for monitor adjustment or a variation in paper
stock. Paper can sometimes appear blue or cream in hue which
will have an effect on the light reflected from the page and
therefore change the appearance of some colours. The texture
of the paper used will affect the way that light is scattered and
may also result in patches of light or dense colour. It is therefore
best to find and adopt a paper that provides you with the best
results. This of course may be a process of trial and error, but
some recommendations are given in the User’s Guide.

12 OKIPAGE 8c
Although colour has its obvious benefits, it has also created
a whole new set of problems that need to be dealt with:
• Itisimportantnot to gooverboardand add dashes ofcolourwithout
thoughtasthiswillundoubtedly have a negativeeffectonthe whole
purposeof usingcolour.
• Usingcolourswhichareconsideredgarishwillalso affect the way in
whichyourdocumentorpresentationisperceived.
• Theproximity of colours is alsoan important factor and itis bestto
considertheresult whencertaincoloursarepaired.
To minimize any problems it is important to use colour with
pre-planning and a great deal of care. If specific colours are
of paramount importance (such as those in a company logo)
then it is best to print these colours beforehand and note the
composition that gives the closest match to the required
colour. Then use the component amounts regardless of what
is displayed on the monitor.
Specifying colour
There are many different ways to specify colour and there
are many different models to cater for this. The colour wheel
as already shown, is a two-dimensional view of the HSL
model which is based on Hue, Saturation and Lightness as
components for specifying colour. The third dimension in
this case is lightness and describes the tendency towards
black or white.
Commonly used models are:
• HSL • HSB
• CMY(K) • RGB
• CIE,CIELab,CIELuv • YCC
HUE
SATURATION
LIGHTNESS

Colour Guide 13
English
The printout from this set of numbers should produce a
colour close to the original. Due to the variation in printer
inks however, it may be necessary to make minor adjustments
until the right combination is found. Once a colour match is
obtained, the RGB components should be entered regardless
of the colours displayed on-screen. To maintain colour
consistency it is recommended that OKI original consumables
are used as they are specifically manufactured for the
OKIPAGE 8c.
Each of the models have their benefits and disadvantages
and are useful in particular situations. Most applications will
have support for the RGB model which (along with CMYK)
is perhaps the simplest to use. This model is used to specify
colours by varying the proportions and levels of the red, green
and blue components.
The amount of red, green and blue present in a colour is usually
expressed as a number from 0 to 255. Less commonly it may
also be expressed as number between 0 and 65535 or as a
percentage. Converting between the systems is straight
forward and a few examples are given below:
Example: To achieve a colour that is described as 100% red,
50% Green and 40% blue…
255 Colour scale: 100/100 × 255 = 255 red
50/100 × 255 = 128 green
40/100 × 255 = 102 blue
65535 Colour scale: 100/100 × 65535 = 65535 red
50/100 × 65535 = 32768 green
40/100 × 65535 = 26214 blue

14 OKIPAGE 8c
Printing colour
No matter how colours are specified, the printer is only able
to use a combination of three colours plus black to generate
an image on paper. To achieve this the printer uses processes
known as halftoning and dithering. Each addressable picture
element (pixel) on a monitor screen or printed output
contributes to what we see in the final image. The pixels are
placed in close proximity so the eye is unable to resolve
individual dots. Colours of adjacent pixels appear to merge
and produce a new colour. Using dot patterns of a given set
of colours to generate new colours is known as dithering.
Shades of grey can be generated by using a similar technique
of black dot placement. This technique is known as halftoning
and gives rise to what we perceive as a continuous tone
image. Examples of dither and halftone are shown below:
Colour registration
The CMYK printing process, as already stated, uses
overlapping inks of cyan, magenta and yellow. To produce
the best possible output, the colours must print in specific
positions so that overlaps and dithering are accurate. If the
colours are not aligned, the resulting print will have colour
shifts (colours produced where incorrect colours overlap to
produce an undesired colour) or appear blurred. Using black
to print grey and also black in text eliminates the problem in
these instances but not when colour is constructed from two
or more of the process primaries. The print below shows how
registration problems can cause undesired effects:
dither pattern halftone pattern
The entire printing area is split into sections known as cells
(much like a grid). The patterns within the cell are then altered
to obtain the required amount of greyscale. An area of an
image containing 50% grey will contain cells that have half
of the dots within the cell printed with black and the other
half left empty.
If your OKIPAGE 8c shows problems as described above then
refer to your User’s Guide in the section entitled “Adjusting
Colour Registration”.

Colour Guide 15
English
Colour adjustments
Certain images such as bitmaps, sometimes print with a
strong hint of a particular colour. Images that appear fine
when viewed on a monitor may not necessarily print that way
due to the reasons described previously. The colour that
appears to dominate the picture will vary depending on
factors such as the scanner (or other input device) having a
bias towards a particular colour, or the monitor’s ability to
represent certain colours on-screen. To compensate for this,
the OKIPAGE 8c has a colour adjustment system that can
reduce the amount of any of the process colours put on the
page in relation to the others. If you run Windows on your
computer, the printer drivers supplied with your printer
provide these adjustments. These are outlined in this manual
and explained in more detail in the driver’s on-line help. (Click
the Help button in any driver dialogue box.). For other
operating systems or drivers, the printer’s Operator Panel
menus provide similar adjustments, detailed in the
OKIPAGE 8c User’s Guide.
This is useful if, for example, you find that all of your
graphics have a tendency to contain too much blue. To
compensate for this, you could reduce the amount of cyan or
magenta as it is these two colours that combine to produce
blue. Bear in mind that other colours containing cyan or
magenta will also be affected. An alternative would be to
increase the amount of yellow. This has the advantage of
increasing colour saturation while balancing the image.
Another method of decreasing strong colours is to increase
the lightness setting in the printer driver. To compensate for
this, the saturation setting must be stepped down accordingly.
As a rule, the saturation should be set down an equal number
of steps to the level that the lightness has been stepped up.

16 OKIPAGE 8c
The OKIPAGE 8c printer driver
There are various features designed to allow you to achieve
the best results with your OKIPAGE 8c. The Colour Options
tab within the printer driver provides a list of colour matching
techniques and adjustments which can be applied to your
graphics and text to provide the optimum balance of colour
on your document. The options and adjustments that can be
made are described below. Clicking on the properties button
after a print request has been made and then selecting the
colour options tab will display the following:
Print Modes
Colour Matching
Thisoption,whenselected,allowstheprinterdrivertoadjustoutputdata
tospecifyhow colours in thedocumentwillmatchthoseprinted.
Monochrome Printing
Allprint data is sent as monochrome (black and white) with colours
beingoutputasgreyscale.Onlytheblacktonercartridgeisusedinthis
instance.
Manual Colour Adjustment
Thisleaves details suchassettings forhalftone,colour, lightness and
saturation to the user. This allows maximum flexibility but requires
thoughtandpre-planning beforeuse.
The colour matching option is set by default, as is the ‘Device
Best’ halftone setting and ‘OKI Unique Matching’. These
settings will produce the best results from your OKIPAGE 8c
in most situations. It is sometimes necessary to use other
settings to allow a certain effect to be achieved. The
selectable items are:

Colour Guide 17
English
Halftone Settings
Device Best
Thisselectsoptimum dithering formostprintjobs.
Cluster Dither
Thedriverselectsfixedsizehalftonecellswhichareusefulwhenprinting
charts,graphs orotherbusinessgraphics.
Error Diffusion
This is only found under the bitmap tab and prints pixels as close as
possibletothespecifieddensity.Anyvariationfromthedataspecifiedis
takenintoaccount when printingneighbouringpixels.Neighbouring
pixelswillbeprintedlighterordarkertocompensateforthevariationof
theoriginalpixel. This methodproducessmooth transitions ofcolour
withinan image.
Image Colour Matching
OKI Unique Matching
Thiscolourmatching technique usesOKIcolourmatchingtechnology
to match colours in the document to those printed. This matching
techniqueisoptimizedfortheOKIPAGE 8candreplacestheonenormally
performedbyWindows.
Windows Image Colour Matching (ICM)
ThisallowsWindowstohandlethecolourmatchingoperation,butmay
notprovidesatisfactoryresultsasitisnotspecifictoyourOKIPAGE 8c.
Afurtherdropdownlistallowsyoutoselectthecolourrenderingintent.
Matching Off
Nocolourmatchingisperformed.Thismeansthatprintedcolours will
notnecessarily matchthosespecifiedwithinthe document.

18 OKIPAGE 8c
Colour Settings
Vivid Colour
Coloursareprintedas brightly and vividlyaspossible, i.e. colours are
moresaturated andvibrant.
Screen Match
Coloursareprintedsothattheyresemblethoseon-screen.Thismaynot
workin practice becausebrightness, chromaand contrast settings on
eachindividualmonitorcannotbeallowedfor.
Unadjusted Colour
Nocolourmatching isperformed anddataissentdirectlytotheprinter.
Printedcoloursmay notmatchthosespecifiedwithinthedocument.
Monochrome
Allcolourdataisconvertedto greyscaleandsenttotheprinter as black
andwhite withhalftone.
Manual Adjustment
Lightness
Thisallowsthe imagebrightnesstobeadjustedsothatcolours withinit
tendtoappearclosertoblack(negativeadjustment or darker) or white
(positiveadjustmentorlighter).
Saturation
Thisadjustsallcolourswithintheimagesothattheyappeardull(negative
adjustment)orvivid (positive adjustment).

Colour Guide 19
English
Glossary
Brightness
Alongwithhue,andsaturation,brightnessisoneofthethreedimensions
ofcolour.Itisthepropertythatdescribes the intensity of light reflected
ortransmittedbyan object or source, independentofhueorsaturation.
Cluster-dot screening
Thisisahalftoningmethodthatusesmultiplepixelsthatvaryfromsmall
tolargerdotsasthecolour getsdarker.Itischaracterizedbyapolka-dot
look.
Colour gamut
Therange of coloursthat adevice can produce is knownas itscolour
gamut.Devicesareunabletoproduceallcoloursthat occurinnatureso
theircolourgamutisasubset of this.
Colour Management System (CMS)
Asystem used tocommunicate colour fidelityacross devices suchas
input,displayandoutputtoensurethatthebestcolourrenditionpossible
isgivenat all times.
Colour mapping
Thisisthetranslationofcolourrepresentationfromonedevice(orsystem)
toanother.
Colour models
Acolourmodelisasystemthatallowscolourstobearrangedoridentified.
Therearevariousmodelsinexistence,withsomemoresuitabletospecific
applicationsthan others.
RGB
Computermonitorsforexample,usered,green and blue phosphors to
displayimages andcoloursarespecifiedusingtheRGBmodel.
CMY(K)
Cyan,magenta, yellow and black are the inks used in the four colour
print process and there is a model used to describe this. Due to the
imperfectionsinprintinginks, black isaddedrather than producedby
mixingtheotherthreeinks.Blackisidentifiedas‘K’toavoidconfusion
withothercolourssuchasblue.
HSL
Coloursare definedbyhue,saturationandlightness.
HSB
Coloursaredefinedbyhue,saturationandbrightness. The dimensions
aresimilartotheHSLmodelbutthe HSB model is relatedtotheRGB
system.

20 OKIPAGE 8c
YCC
Thissystemwasdeveloped by Kodakforencoding colour images for
displayon video monitors. RGBvaluesareconverted to a luminance
component(Y) andchromaticcomponents(C1)and(C2).
CIE
In1931theCommissionInternationaledel’Eclairage(CIE)deviseda
colour system based on the human visual system and is an accepted
standard.Thissystemis not linear and difficulttointerpret.Therehave
beenmodifications tothe systemthat havegiven rise to CIELab and
CIELuv.
Colour separations
Eachoftheprocesscoloursareprintedseparatelyandmustthereforebe
specifiedindividually,asthecolouris needed. Imagedataistherefore
splitintotheprimarycolours(plusspotcolours)beforeprinting.
Colour space
Thisisamethodofdescribingcolour.Somesystemsaredevice-dependent
suchasRGBandCMYK.TheCIEsystemisadeviceindependentcolour
space.Note that all colour models are notcolour spaces in their own
right.
Colourants
Thesearethecoloursused by adeviceto reproduce colour.Aprinting
pressusestheCMYKcolourants.
Density
Inthiscontext,thereisnorelationtothemass andvolumeoftheobject,
butistheabilityoftheobject to absorb light.Themorelightabsorbed,
thehigherthe objectdensity.
Dithering
Atechniquewherepixelsofdifferentcoloursareplacedincloseproximity
togivetheillusionofanother colour as perceived bythehumanvisual
system.
Dot gain
Duringtheprintingprocess,inksmayspreadcausingdotsonapageto
printlargerthanintended.Thisresults in darker tones and colours. The
problemcan becompensatedforbycarefuladjustment.
Error diffusion
Thisisusuallyassociatedwithhalftoningbutcanalsobeusedwithdither.
Theerrorbetweenapixelanditsintendedvalueispropagatedtoadjacent
pixelstoproduceabalancedoveralleffect.Resultsmaysometimesappear
grainy.
Other manuals for OKIPAGE 8c Plus
4
Table of contents
Other Oki Printer manuals
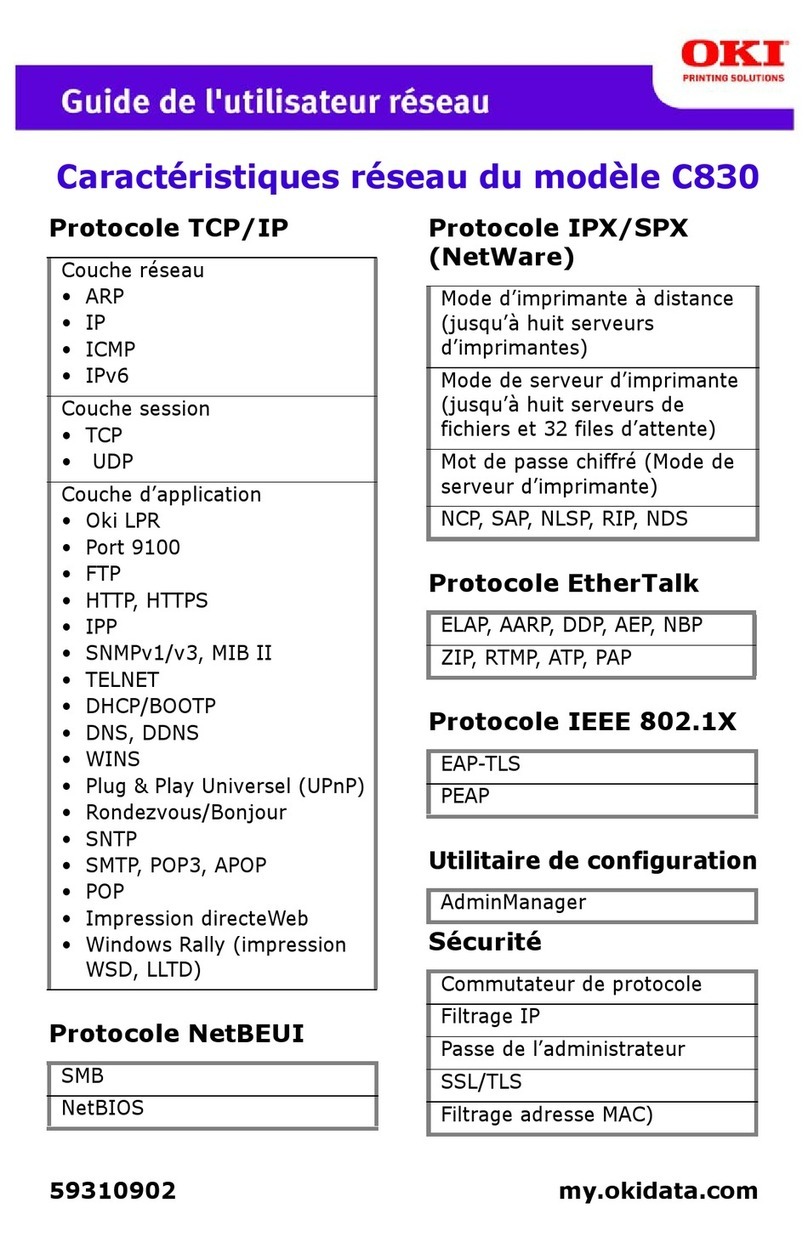
Oki
Oki C810n Quick start guide

Oki
Oki B4100 User manual
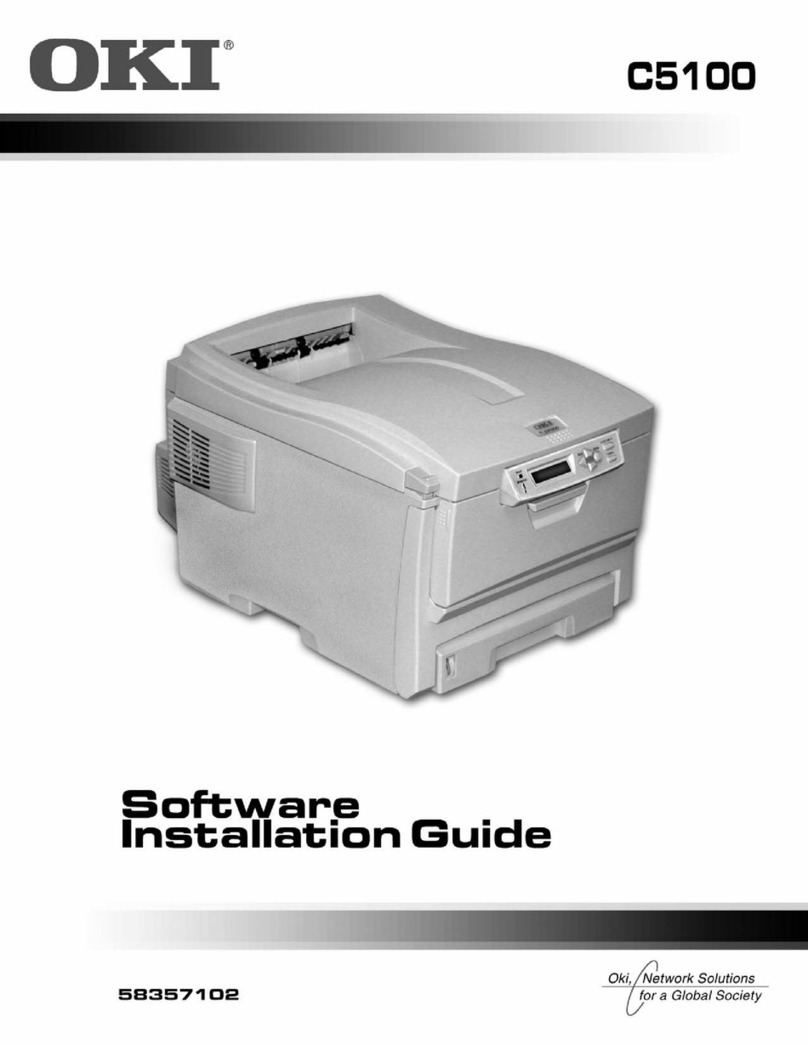
Oki
Oki C5100n Firmware update
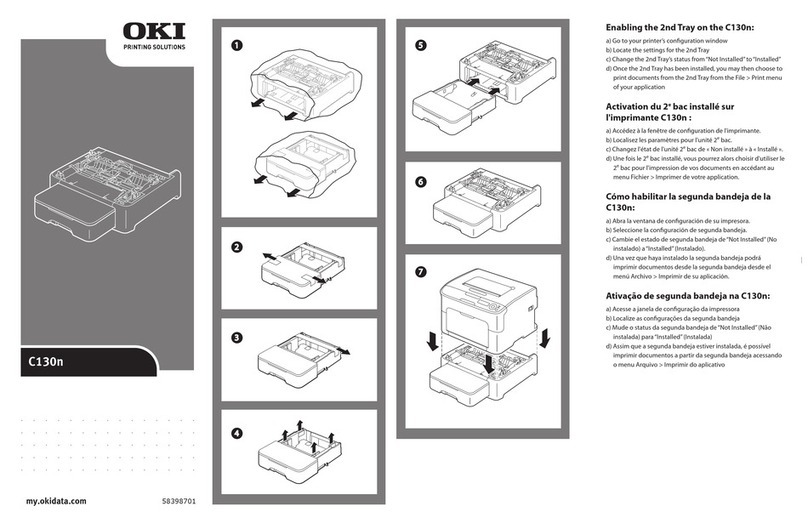
Oki
Oki C130n User manual
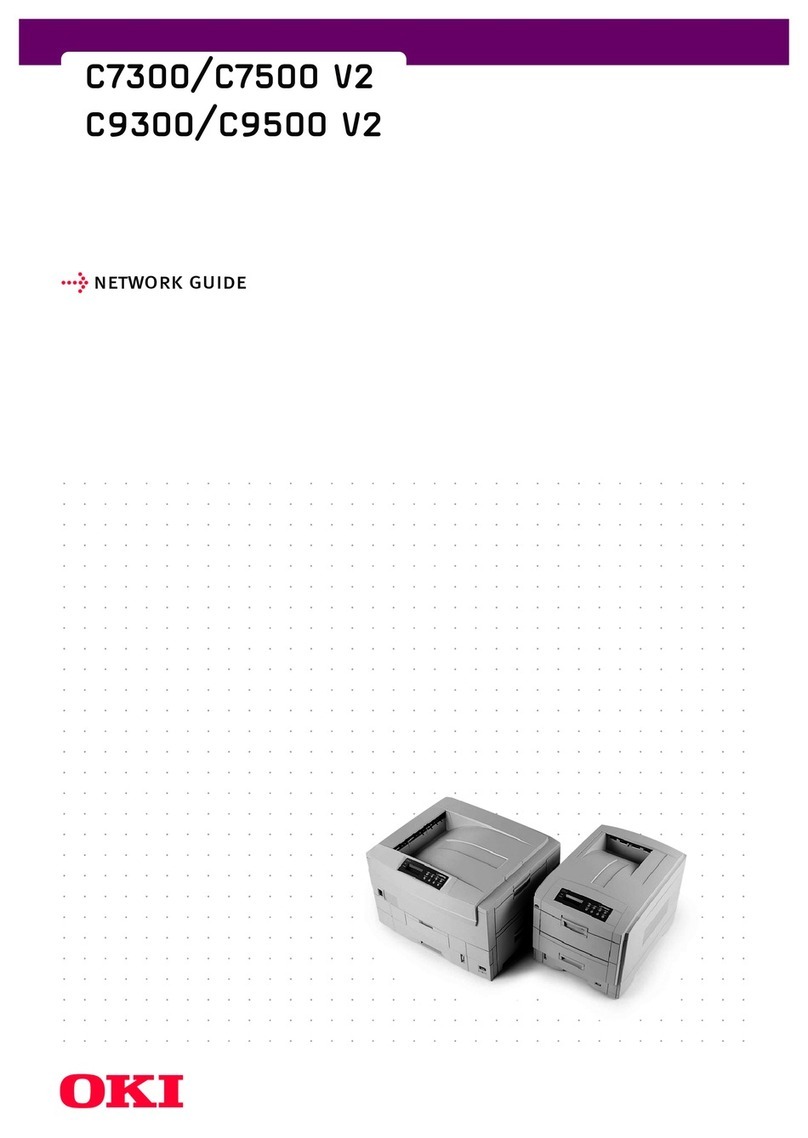
Oki
Oki C7500 V2 Installation and maintenance instructions

Oki
Oki B710n Quick start guide
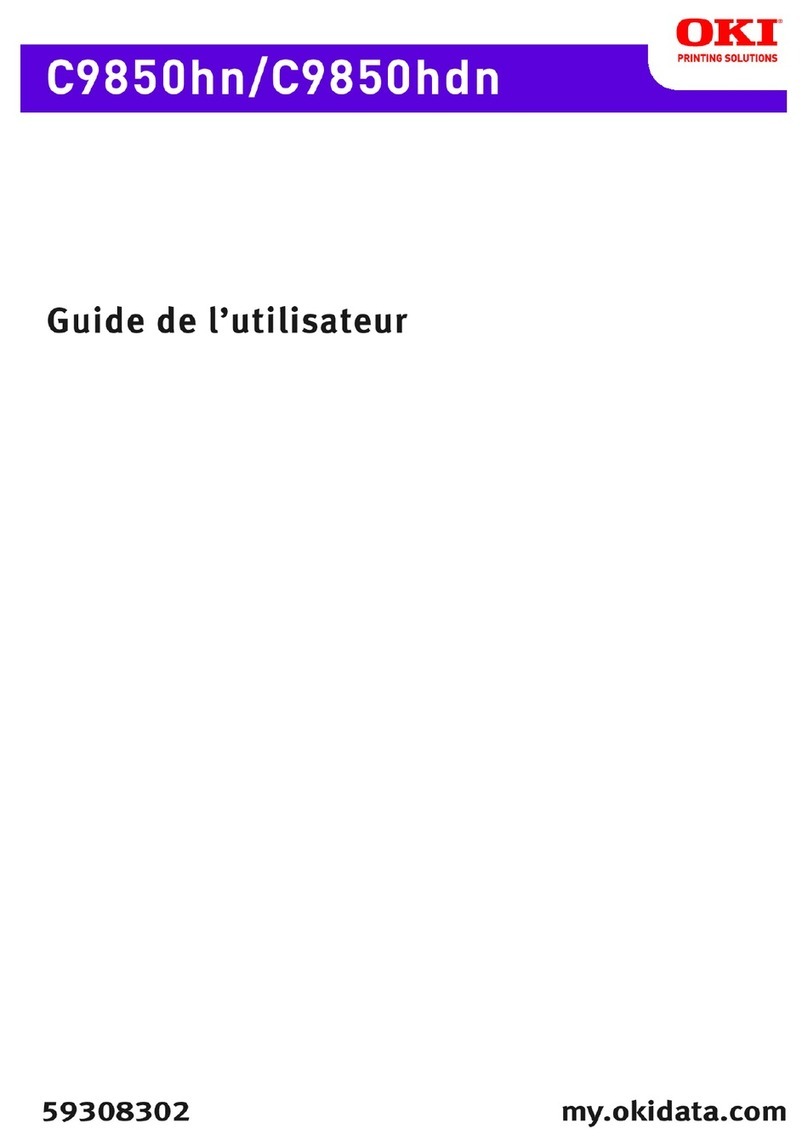
Oki
Oki C9850hdn Quick start guide
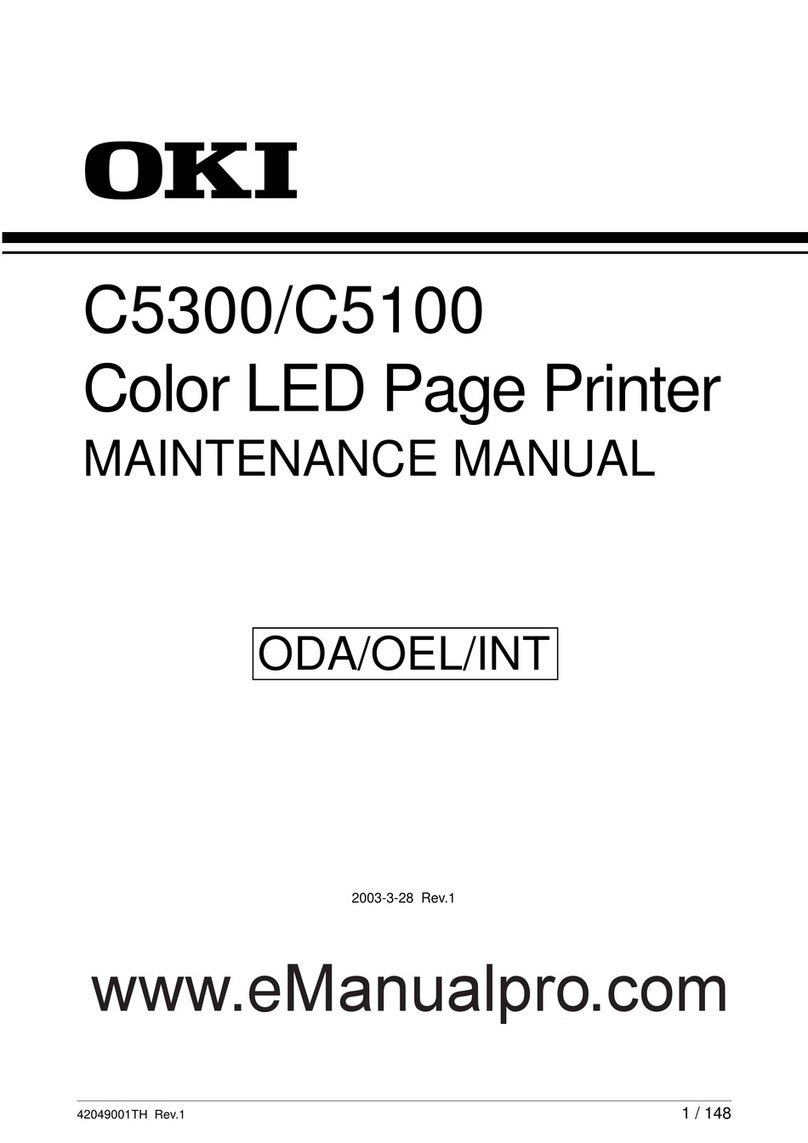
Oki
Oki C5100 User manual
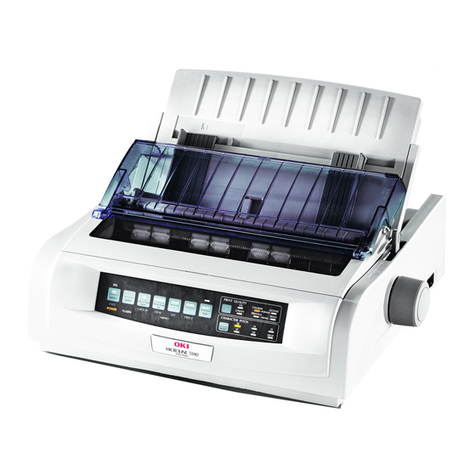
Oki
Oki ML5521 User manual
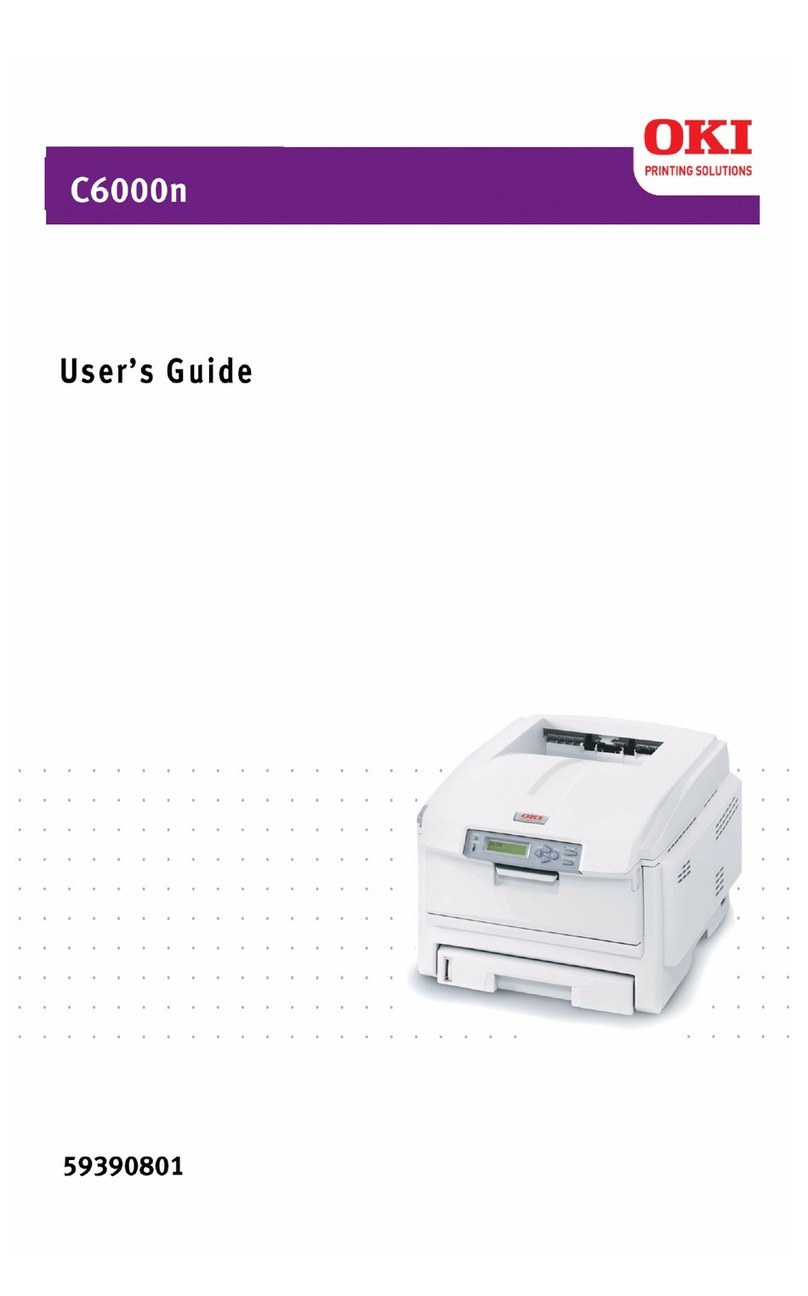
Oki
Oki C6000n User manual