Origin live ALLIANCE User manual

Notes:
You should not be unsettled if there seems to be
“play” in the bearings - this is deliberate and you
should not adjust or rotate the bearing end caps to try
and “correct” this. The bearings are high quality and
devoid of play, however the bearing housings are
carefully dimensioned to allow a loose fit, thus
“floating” the arm.
hen lowering the arm onto a record, it is best not to
jam down the arm lever completely but rather, just let
it fall under its own weight.
The sound of new arms will improve significantly over the
first 2 weeks as items bed down and arm wires burn in.
Give special attention to underlined text in these
instructions.
Mounting the arm
If possible, refer also to the mounting instructions
from your turntable manufacturer.
HOLE DIMENSIONS
Many decks come with an arm mount hole position
intended for arms with “Rega” geometry. If this is the
case with your deck then the Origin Live arm will fit
perfectly as it shares the same geometry as Rega.
However if this is not the case then mount your arm
using the following dimensions :
Centre of platter to centre of arm hole is approx
222mm ( 295.6mm for 12 inch versions ) plus or
minus 1.5mm tolerance. The hole diameter for the
arm is 23mm to 25 mm. If you need to modify your
existing arm board to enable the arm to fit, please
refer to our web site tonearm pages and see side
menu for “fitting guidance”.
DIAGRAM OF ARM MOUNTED
Insert the arm through the arm-board hole and fit the
cork washer underneath followed by the large
clamping nut. Turn the nut to finger tight as hard as
you can (see above diagram).
Leave final height adjustment till later.
For decks that differ from the illustration, you may
need to contact the turntable manufacturer for
instructions or parts to enable you to fit your OL arm
- Ask how to fit an “old style Rega geometry,
threaded base mounting” and they should understand
Owner Manual for
ALLIANCE, ONYX, SILVER Mk3A
& ZEPHYR ARMS
I n s t r u c t i o n s b y O r i g i n l i v e ©
LOOSE PARTS LIST
Counterweight
Side Bias eight and clamp
ire loop angle diagram
1.5mm A/F Allen key for wire loop
Large clamping nut
Cork asher
Cable clip
Alignment gauge
ire loop
Side Bias clamping ball
Side Bias rod
Bearing end caps
VTA Adjuster Ring
Lift Lower device
Counterweight
Yoke
Lift lever
Side Bias
weight
Arm plate
Headshell
Arm Clip

your requirement as all Origin Live arms are drop in
replacements for all Rega arms.
Connecting the arm
FI T C A BLE CL I P
For best performance, fit the arm cable through a
cable clip attached to the plinth. Leave a slight droop
in the cable so that it isn’t “tight”. Clipping the cable
helps prevent vibration feeding into the arm.
CONNECT ARM TO PHONO STAGE / AMPLIFIER
Plug the phono plugs into the amp or phono stage.
In rare cases the plug may be too loose or too tight.
This is because gold plating thickness varies on plugs
and sockets so you may need to bend the plug flanges
fractionally using a pair of long nosed pliers.
Connect the arm earth lead to the earth of your phono
stage, pre-amplifier or amplifier. This earth lead is
best separated slightly from the arm signal leads so
do not wind it around them for best performance.
Avoid pulling the external wires at the base of the
arm as they can become detached if excessive force is
used to manipulate them.
Always remove phono plugs by holding their body
rather than the cable. This avoids potential cable
failures.
If you have XLR plugs, see our web site for fitting
instructions- see top navigation bar, click support /
owner manuals / tonearms.
Cartridge set up
If you are not familiar with fitting cartridges and
encounter any problems then it may help to read the
section at the end of this manual.
Carry out the following cartridge set up procedure
without deviating from the sequence, as each step
affects the next.
M O U N T I N G
Loosely mount the cartridge in the headshell keeping
the stylus guard on of possible. The headshell bolts
should initially be fitted, such that the cartridge is just
free enough to move it's position in the headshell.
Be especially careful when the stylus guard is off, as
cartridges have a strong magnetic field. Sometimes
metal tools get dragged out of control and cause
damage to the stylus cantilever. The best precaution
is to keep tools well away from the cantilever, and
use a non-ferrous screwdriver.
SET TRACKING FORCE
Find the recommended tracking force for your
cartridge from the manufacturers instructions.
For Origin Live arms you will need a stylus force
gauge (stylus balance). At this stage setting the force
to the nearest 0.3 grams of recommendation is fine as
you will need to re-set it again later.
The tracking force is adjusted by sliding the
counterweight along the rear stub. The friction fit of
the weight on the stub can sometimes be a little tight.
The trick is to rotate the counterweight as you are
pulling or pushing it in the desired direction. This
may require considerable force but the human hand
will not damage Origin Live arm bearings. Tightness
may not be convenient but it increases performance.
A spot of Vaselene can help the weight slide more
easily.
USE OF STYLUS FORCE GAUGE
Most stylus force gauges work on the same principle
as a set of scales or balances. For example with the
Ortofon Stylus Force Gauge, first place the stylus on
the inscribed or graduated portion of the scales. Try
the stylus at different points till you find the point
where the beam “balances” freely in a roughly level
position. You can now read the force being exerted
( 1 gram = 10 mN if the scale is in mN). From this
number you can assess whether you need to increase
the tracking force or vica-versa. Move the tonearm
counterweight accordingly and re-measure the
tracking force. Repeat this procedure until the correct
tracking force is obtained. A digital force gauge
works slightly differently so follow the
manufacturer’s instructions.
SET TANGENCY ALIGNMENT (LATERAL TRACKING
ANGLE)
First set the cartridge overhang, which is 17mm for
all standard 9.5 inch Origin Live and Rega arms
( 13.2mm for 12 inch versions ).
The overhang is measured by positioning the arm
tube such that it’s centre line is directly over the
centre of the spindle. Now measure the distance
between the stylus tip and the centre of the spindle.
This is the overhang.
Follow the instructions on the Origin Live alignment
gauge. After the cartridge body or cantilever is nicely
aligned with the gauge markings, recheck that the
overhang is still correct. If not, repeat the above
procedure till all is as it should be.
hen adjustments are correct, carefully tighten the
cartridge mounting bolts till they are tight. Stainless
steel allen bolts are best but aluminium or brass are
OK. Avoid steel bolts as they are magnetic and
degrade your cartridge magnets.

hen tightening it helps to keep a firm grip on the
cartridge and headshell together so nothing shifts.
Slightly tighten each screw in turn, then repeat until
tight. However careful you’ve been, always check the
alignment and overhang again after tightening.
Ensure the headshell wires are gently bent so that
they are clear of the record surface. VTA
ADJUSTMENT
You now need to adjust the height of the arm base to its
correct position using the threaded VTA adjuster ring (as
shown above).
Rotating the VTA ring clockwise raises the arm, anti-
clockwise lowers it. Once the desired height is achieved,
tighten the large nut to finger tight thus clamping
everything in position.
You do not need to clamp the arm very tightly -
finger tight followed by a light nip with a pair of
pliers should be sufficient as hard tightening is
slightly detrimental to performance - if in doubt, just
listen to different tensions and use the one that gives
best results.
The correct arm height is achieved by placing the
stylus on a flat record. Now adjust the rear height of
the arm till the arm tube is dead parallel with the
surface of the record – It helps to use the parallel
lines on the alignment gauge it to check this by
holding the card vertically behind the arm tube as you
look at it from the side.
TUNING IN VTA BY EAR
It is always best to experiment with varying the VTA
height and listening to the results till you have found
the optimum position. This is necessary because of
variations in stylus angle tolerances.
If the sound is a little hard and bright, with thin bass,
edgy highs, and harsh midrange then the arm
probably needs to be lowered at the arm pillar.
Raise the arm when the sound is dull, the highs
rolled off, and lacking definition. This also sounds a
lot like the effects of changes in tracking force (too
light is edgy, too heavy is heavy and dull). Start with
the arm a little low and very gradually raise it, first to
where it is parallel to the record, and then so the back
of the cartridge is tilting up. Keep track of your
settings so you can return to the one you like best
where everything snaps into focus. The range of
adjustments can be quite broad, as much as 1/2” (at
the arm pivot). Play with the full range so you know
what it sounds like and don’t be diffident.
ANTI-SKATE FORCE (SIDE BIAS)
Side Bias applies an opposing force to balance the
natural inward drag of a pivoting arm while playing.
If left uncontrolled, the stylus would push up against
the inner groove wall, causing slight distortion both
from mis-tracking and a cantilever skewed in relation
to the cartridge generator.
To set side bias carry out the following.
Carefully twist the wire loop to the correct angle
relative to the arm base. This is easy using the
enclosed paper template which shows a plan view of
the arm – the angle only needs to be approximate –
the wire loop is held in place by a set screw in the
arm plate – this can be re tightened if necessary using
the allen key supplied.
Carefully unpack the side bias weight and clamping
ball connected by a joining thread. Fit the sliding ball
clamp onto the side bias rod which protrudes from
the rear of the yoke. You may need to undo the
clamping screw to fit the ball. Also ensure the thread
is pulled slightly as you slide the ball over the rod.
Thread the thin nylon filament line through the small
gap of the wire “eye” to allow the ball weight to
hang freely as shown in photo on first page. The side
bias force is adjusted by moving the clamping ball
along the rodwhich is then clamped in position using
the 1.5mm Allen key to lightly tighten the set screw
in the side of the ball.
The side bias cylinder clamp is initially best
positioned about 5mm away from the yoke – this is
approx the correct position for most cartridges. If
you wish to increase the side bias force then unclamp
the ball and move it further outwards. To decrease the
side force go in the opposite direction.
Checking side bias
Ideally you need a test record with a track for
checking side bias, not all do, so check before you
buy. The Ultimate Analogue Test LP is one that we
recommend as it has an Anti-skating test; 315Hz
amplitude sweep to +12dbu (Lateral). Also the Hi Fi
News test record also has an anti-skate/bias setting
track.
In the absence of a side bias test track, the following
method is better than nothing. Find a record with
approx 10mm of blank vinyl between the end of the

lead out groove and the record label. Lower the stylus
needle on the blank uncut vinyl and observe whether
the needle skates inwards towards the centre of the
record or outwards. Increase anti-skate until the arm
starts to slowly drift inward towards the label. Also,
watch the stylus when you set it into a groove. Does
it move to the right or left relative to the cartridge
body? This indicates too much or too little anti-
skating.
FINE TUNING (option l)
You now have three adjustments approximated,
tracking force, VTA, and azimuth. It’s a matter of
reiteration to optimise the sound. The change in
sound with each of these individual adjustments can
be similar. It’s therefore necessary, in optimising all
three, to experimentally move from one type of
adjustment to the next, then to the next, in order to
balance the optimisation for all three. It’s helpful to
listen to female vocals as you proceed. Firstly try
deviating from the cartridge’s recommended tracking
force by small increments - about 0.2 of a gram
deviation above and below the manufacturer’s basic
recommendations. Don’t worry about record damage
from heavy tracking as most record damage is
actually caused by mistracking in the middle-to-high
frequencies with too little tracking force rather than
with too heavy. If you’re getting mistracking at the
low (lightest) end of the range and yet the low range
is generally sounding the best (and on moderate
signals, not heavy passages), then chances are you
have either a dirty stylus, a bad record, an
accumulation of crud in your cartridge, or a cartridge
that’s getting old. Changes in tracking force can
change how you want VTA adjusted.
WARRANTY
e guarantee arms supplied by ourselves to be free
from fault for 2 years and will undertake remedial
work, providing the arm has not been modified by
any party other than ourselves and has not received
maltreatment of any kind.
Additional Notes
Please note that the occasional rewired arm can make
a slight “rustling noise” through the speakers when
it is lifted across the record. This should not be a
cause for concern as it is only caused by microphony
of the internal litz cable - under normal playing
conditions this is inaudible.
You can speed up the process of “burning in” the
tonearm wires by ordering one of our burn in cables.
Now that all the hard work is over you can settle back
and hear the results - we wish you many hours of
enjoyable music and rediscovering your record
collection.
Solving roblems
Almost all possible issues that can arise with
tonearms are answered on our web site “solving
problems section”. Before contacting us please visit
this area from the top navigation bar and see -
Support / Solving problems / Tonearms
If Ar lift is at wrong height – Please see the web
site video on how to correct this. From top navigation
bar go to Support / owner manuals / tonearms
If the ar “sticks” in playing a record, then check
that the curved arm rest is not fouling on the yoke. To
see this, hold the arm finger lift and check that the
arm can be traversed by hand above the surface of the
whole record. This will identify the position of the
“stick”, The remedy is simply to rotate the curved
arm rest till it no longer fouls – this can usually be
carried out without loosening the arm rest grub screw.
If the wire loop fouls your lid then it should be
gently and permanently bent downwards till clear.
You may need to increase the curvature of the bend if
you find that the ball weight stops at the wire loop
when the arm is at the end of a record. The wire loop
is checked at factory but they sometimes get
deformed in transit.
Hi-Fi cartridges explained
Optional
reading for less experienced
users
G E N E R A L N O T E S
As Origin Live supply most makes of hi-fi cartridge
we get asked questions from time to time about
various issues regarding set up and care. To help
newcomers to this area we have published the
following notes. These guidelines are of a general
nature - we publish them only to be of help and
although widely accepted they are not formally
authoritative - we cannot accept liability if you
choose to use them and neither do we encourage the
time consuming occupation of answering queries
surrounding the procedures outlined - these are best
referred to the manufacturer of your specific hi-fi
cartridge.
For those new or inexperienced to fitting hi-fi
cartridges we would state that this is NOT difficult
and much of the detail and perfectionism outlined
below is for those who like to experiment. e
ourselves do not normally check azimuth, or vary
tracking forces from the manufacturers
recommendations - neither would we worry if the
arm was up to 2mm away from the recommended
distance from the spindle - although all these details

are audible they are generally of a relatively low
order, however tracking force and VTA in particular
are worth fine tuning should you feel anything is
lacking. If things seem complicated we would
encourage you not to be put off as it all becomes
clear once you get started.
Before fine tuning the set up as described below you
should allow the cartridge to “run in” properly - at
least 40 hours for some cartridges.
I M P O R TA N C E O F S E T U P
Hi-Fi cartridges travel like a bobsleigh through the
groove of a record, even though the groove is only a
few thousandths of an inch wide. You hear groove
displacements of the order of a few millionths of an
inch. (That’s like splitting a hair into one thousand
pieces.) Every motion or vibration allowed at this
level can be heard enormously amplified through
your speakers. For this reason it is good to set up the
turntable and arm correctly so that the audio cartridge
can do it’s job properly. For instance a turntable out
of level can produce side forces on the pickup
cartridge tip that will wear it more on one side than
the other. It also has a slightly degrading effect on
the wear of your records.
LEVELNESS
hen a turntable goes out of level, the platter bearing
performance and the arm’s dynamics, specifically
anti-skate, are negatively affected. So be sure your
turntable platter and tonearm mounting board are
level - use a spirit level. If the platter is out of level,
first adjust the surface that the deck stands on. The
suspension (in the case of a suspended sub-chassis
design) may also need levelling if it has subsided
over time. If the arm board is not level (which means
the arm pivot is not vertical), either return it to your
dealer for repair or re-level it yourself by shimming
between the mounting board and it’s support.
HI-FI CAR RIDGES ALIGNMEN
Alignment for hi-fi cartridges needs to be optimised
in three different planes. However, it cannot be
perfect in all three planes, so it must be optimised for
an overall best balance or compromise. The final
authority should always be your ears and preferably
over an extended period of listening. Bear in mind
that each record is cut slightly differently. Here again,
optimise for an overall balance of good sound over a
wide range of records. The three alignment planes are
as follows. (Please note that it is the stylus, not the
cartridge that is being aligned.)
Lateral tracking angle
Viewed from above, the cartridge arcing movement
across the record must maintain the stylus in the same
relation to the groove as that of the cutting stylus’s
straight-line tracking; this is Lateral Tracking Angle
or Tangency. Apart from linear tracking arms this is
always a matter of the best compromise.
Azimuth
Viewed from head on, the stylus must be
perpendicular in the groove so as not to favour one
groove wall, and therefore one channel, over the
other wall/channel; this is Azimuth.
Vertical tracking angle (V A)
Viewed from the side, the stylus must sit correctly in
the groove, at the same angle as the original cutter;
this is Vertical Tracking/Stylus Rake Angle. (VTA,
however, varies from record to record due to their
varying thicknesses. Therefore, this alignment must
be set by ear, even more than is the case with the
other adjustments).
HI-FI CAR RIDGE ALIGNING OOLS
Tools required are an alignment gauge, a ruler, a
tracking force gauge, a FLAT record, a screwdriver or
Allen keys of the right size (usually 2mm), a good
light may also be helpful. Small needle-nose pliers
and a magnifying glass all help. It also helps to have
the hi-fi news test record. Treat the arm with care as
some parts are fragile. To this end ensure that
tightening of any bolts is carried out gently and
without causing undue strain.
Tonearm wiring uses a standard colour code for
channel and polarity identification: hite = L Hot,
Blue = L Ground, Red = R Hot, and Green = R
Ground. If the cartridge pins aren’t color-coded the
same way, they will have letter identifications next to
them. Make sure that the arm’s wires, wire clips, and
solder joints are in very good condition. At minimum,
clean the contact between cartridge pins and wire
clips by removing and replacing each clip. Holding
the clips with needle-nose pliers can make this easier,
but be careful that you don’t strain the wires where
they join the clip. Check the clips for a proper fit on
the cartridge pins, and adjust them if necessary.
“Proper” means snug but not tight. To check clip size,
hold the cartridge tail-up close to the head wires,
grasp a clip firmly right behind its tubular part with
the tweezers, line it up with the cartridge pin, and
press. If it does not slide on with moderate force, the
clip needs opening-up. If it slides on easily but flops
around when attached, it needs tightening. Re-sizing
is the operation most likely to detach a clip. The trick
is to avoid bending the wire at its attachment point or
putting too much tension on it. To avoid either,
always hold the clip with its wire slightly slack-
looped behind it while adjusting. For opening a clip,
hold it firmly with the tweezers or needle-noses, right
behind its tubular section, and press the tip of the

jeweller’s screwdriver into the open end of its
longitudinal slot until you see this widen very
slightly. (Here’s where you’ll probably need the
headband magnifier or reading glasses.) You’re
dealing with thousandths of an inch here, so a barely
visible spreading may be all that’s needed. Try it for
fit, and repeat until it does. For tightening a clip,
press a toothpick inside it as far as it will go, then use
the needle-nose pliers to gently squeeze together the
sides of the clip near its free end, while watching the
slot for any change. (Attempting to squeeze a clip
without the toothpick inside it will flatten its sides.)
Try it for size, and re-squeeze if necessary until the fit
is correct. hen it is, close up the middle section of
the tube to match the end
roper care and maintenance
of cartridges & records
C A R E O F C A R T R I D G E S
Replace your cartridge when due - hi-fi cartridges
have a lifespan for their cantilever suspensions and
stylus needles. This will vary from manufacturer and
type of cartridge as well as other factors like the
cleanliness of your record and the care you take of
the cartridge. It is wise to enquire on the expected life
of your cartridge to the manufacturer so that when the
time comes it is replaced accordingly - most
importantly this will preserve your records as well as
enable you to enjoy the best performance.
If there is a build-up of dust and dirt where the needle
enters the cartridge body you should use a small soft
brush to brush the debris out. Always brush from the
direction of the cantilever to the stylus or you may do
damage.
Care of stylus - One well known method of cleaning
stylus is the Linn green stuff which is a very fine
abrasive paper - this may just be OK on some
cartridges which do not have fine stylus tips and
fragile cantilever mechanisms. However there is a
danger of causing fractures or chips on your diamond
stylus on certain fineline tips. This method can also
strain the cantilever mechanism.
There are a number of fluids on the market that
increase stylus life and help to clean gunge from the
needle - a word of caution though - some of these can
loosen the stylus glue on the cantilever over time -
some fluids can also attack the cantilever or coil
material itself or harden the suspension - consult your
cartridge manufacturer over this. One key factor is to
use the liquid very sparingly on a cotton bud such
that it is just damp (not running with fluid) - this
minimises the fluid which can run up inside the
cartridge.
R E CO R D C AR E A ND CL E A NI N G
The stylus itself does a pretty good job of cleaning
the grooves and should itself therefore be kept clean.
The proprietary brushes etc. for cleaning records will
often do little more than brush dirt deeper into the
record grooves and are best avoided if possible. Also
keep records in high quality non-scratch record
sleeves - preferably good ones.
A record cleaning machine is really the only answer
for cleaning records properly as they suck out the
debris and dust in the record grooves using a
powerful vacuum. Tests using a microscope prove
that this does the job with 100% success. The
performance improvement is also very noticeable
when it comes to even new records being played. e
supply and highly recommend the Moth record
cleaning machine as this is very effective from
personal experience and comes with many glowing
endorsements – see our web site for details and
reviews.
Other manuals for ALLIANCE
1
This manual suits for next models
3
Table of contents
Other Origin live Turntable manuals
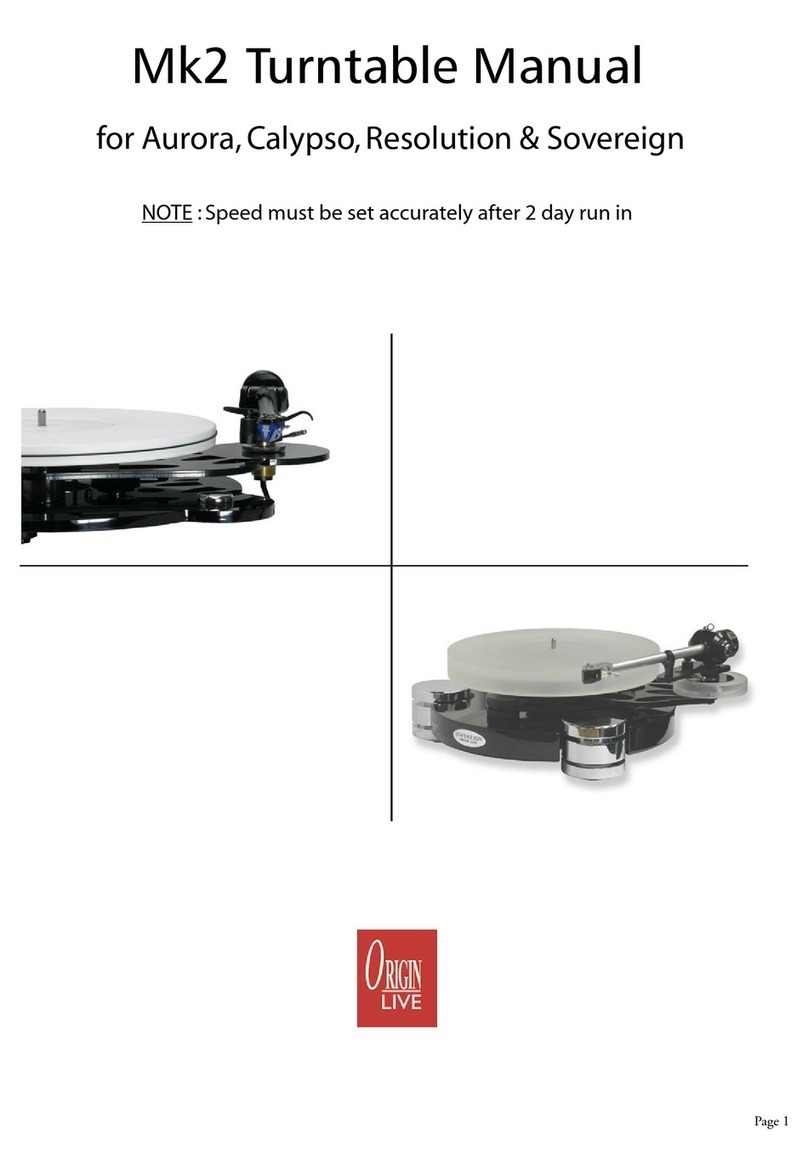
Origin live
Origin live Aurora Mk2 User manual
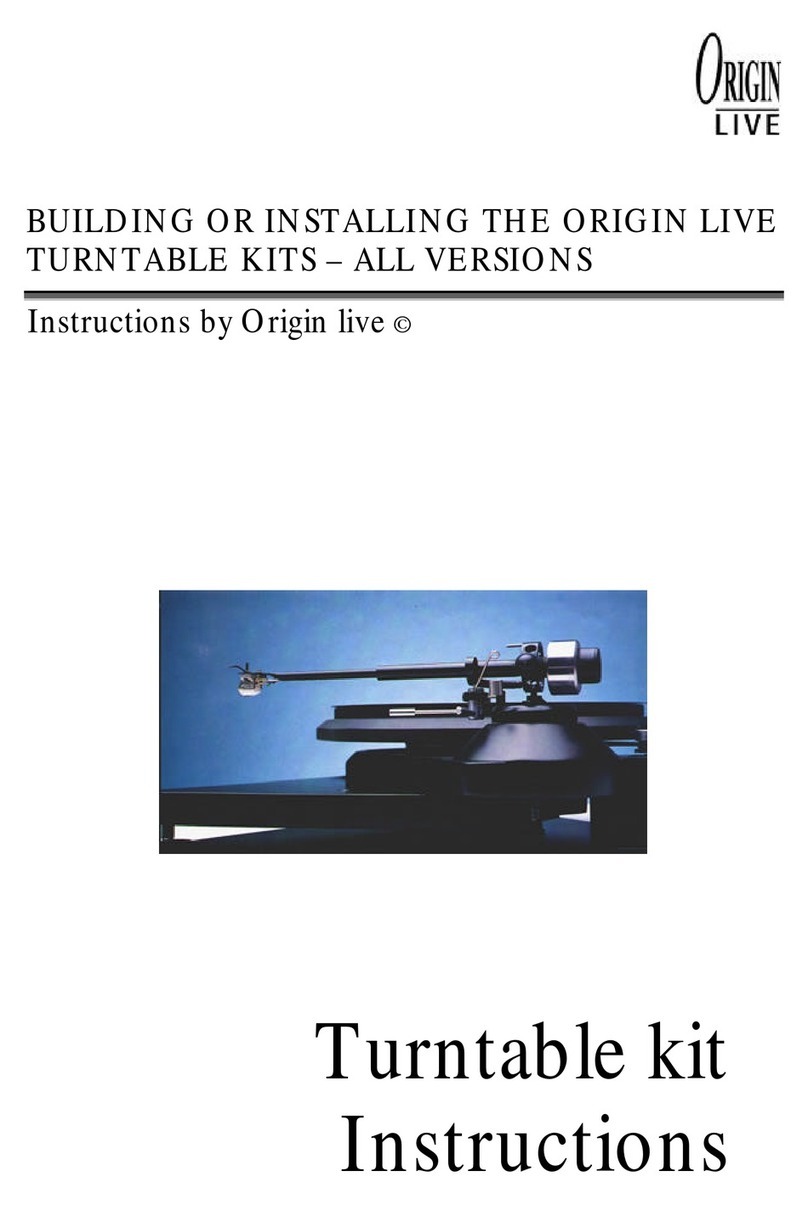
Origin live
Origin live Turntable kit ALL VERSIONS User manual
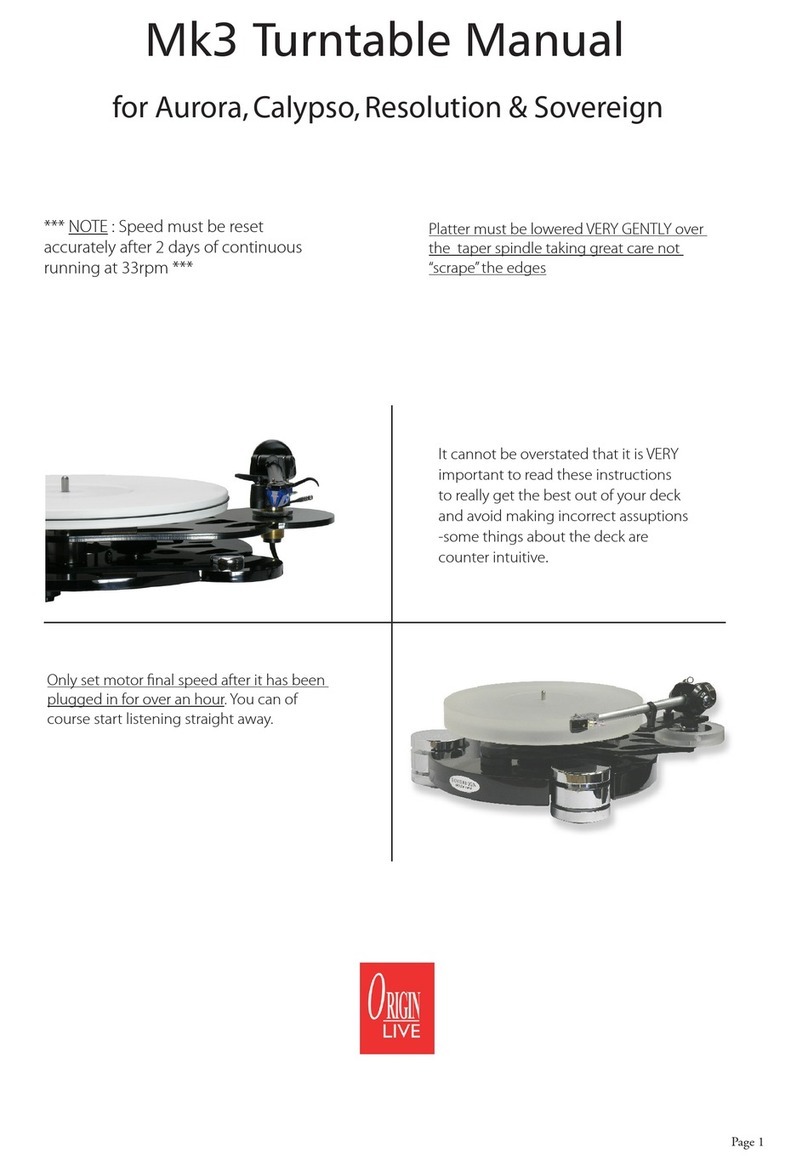
Origin live
Origin live Aurora Mk3 User manual

Origin live
Origin live THE RESOLUTION CLASSIC User manual
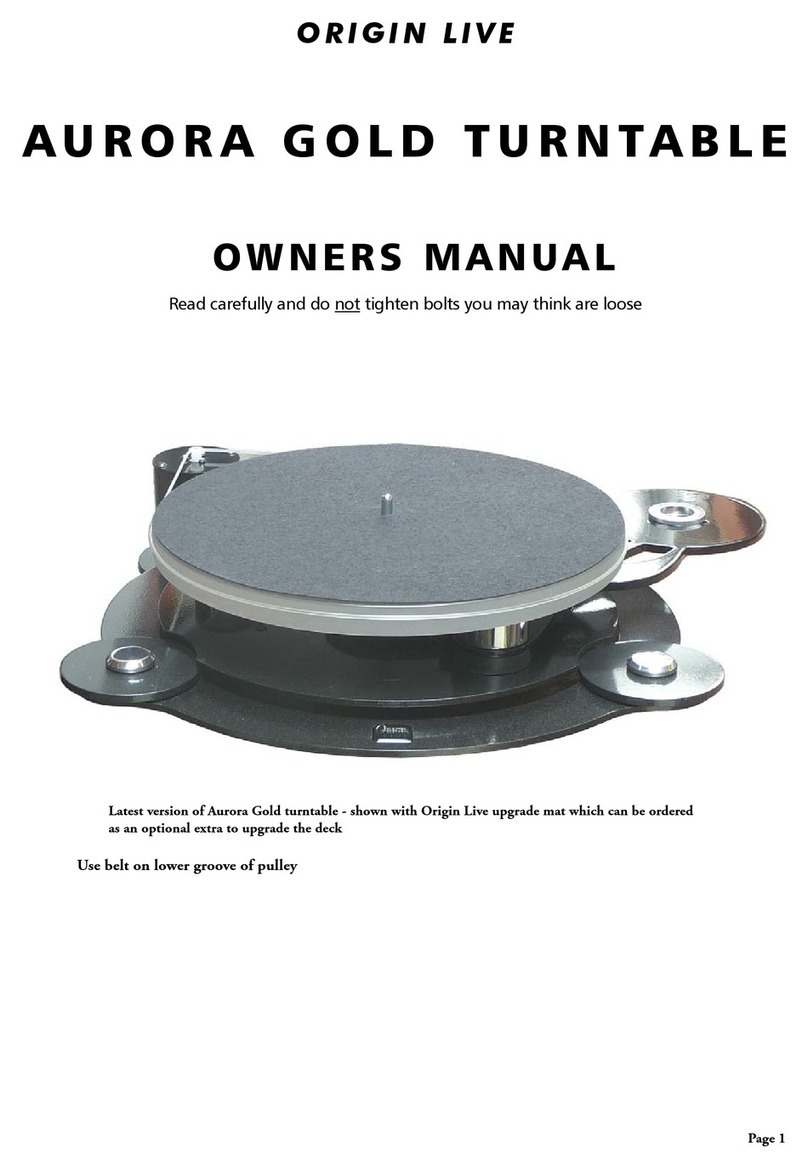
Origin live
Origin live AURORA GOLD User manual

Origin live
Origin live Calypso MKII User manual
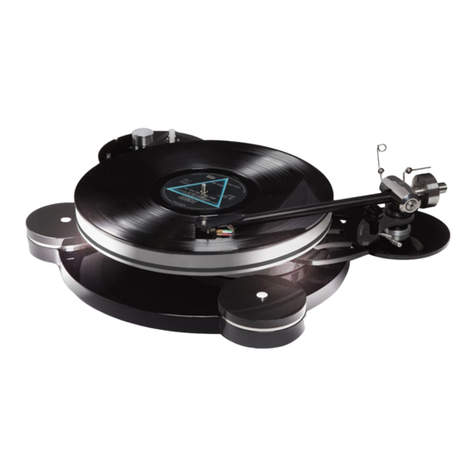
Origin live
Origin live Aurora MK4 User manual
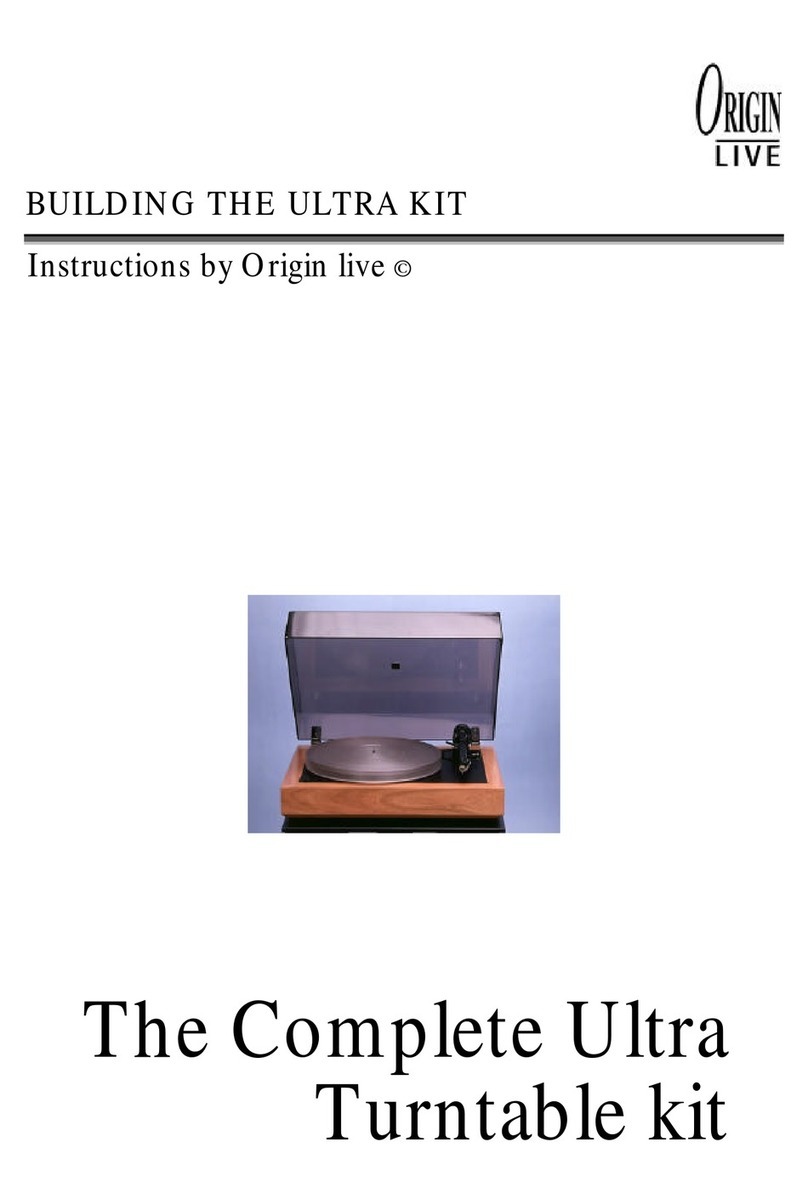
Origin live
Origin live The Complete Ultra Turntable kit User manual
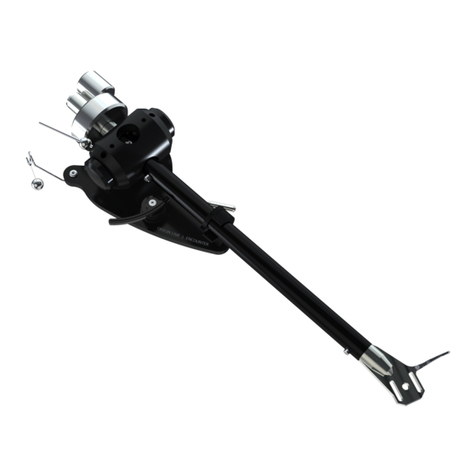
Origin live
Origin live ENCOUNTER User manual
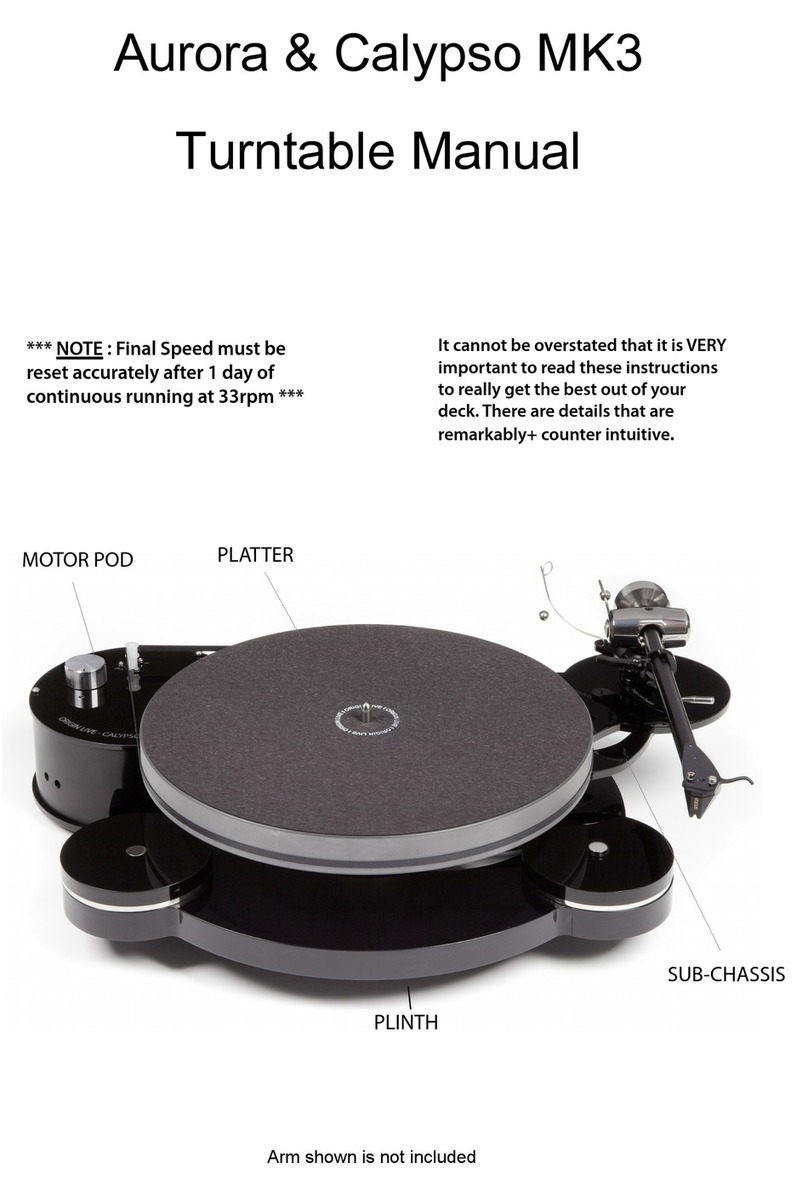
Origin live
Origin live Calypso MK3 User manual