Parker Pneumatic V-575P User manual

INSTALLATION/OPERATING INSTRUCTIONS
A Flow Control "Sandwich" controls the flow of air from the valve exhaust
ports to atmosphere. The Sprint valve (4-way) is typically used with a
double acting cylinder alternately pressurizing one end while exhausting
the other. Cylinder speed can be influenced by restricting the exhaust
path.
NOTE: If the complete blockage of air to atmosphere or extremely fine
adjustments are required DO NOT use a Flow Control "Sandwich".
Instead connect Micrometer Flow Control Valves to cylinder ports of
subbase or manifold with the free flow direction pointing away from the
subbase or manifold.
Flow Control "Sandwich" is intended for use with subbase or manifold
mounted Sprint Valves. It is only recommended for use with Common
Port versions of Sandwich Regulators. The Flow Control is to be
assembled between the regulator and the subbase or manifold using the
(3) 1/4-20 X 1-1/4" low head cap screws provided in the kit. If used with
Single Port or Independent Port versions of Sandwich Regulators
functionality is limited as follows:
Flow Control "Sandwich" used in conjunction with Single Port
version of Sandwich Regulator - Adjust speed with the adjusting
screw on the regulator end of the Sandwich Regulator. It adjusts the
speed of exhaust flow from cylinder ports "2" and "4". Independent
speed adjustment is not possible. This could result in different
exhaust speeds for cylinder ports "2" and "4" since line pressure is
supplied to one cylinder port and a regulated pressure is supplied to
the other. The other adjusting screw is non-functional.
Flow Control "Sandwich" used in conjunction with Independent
Port version of Sandwich Regulator - Fully close one adjustment
screw and perform adjustment with the other. Either adjustment
screw controls the speed of exhaust flow from cylinder ports "2" and
"4". Independent speed adjustment is not possible. This could result
in different exhaust speeds for cylinder ports "2" and "4" since a
different regulated pressure is supplied to each cylinder port.
APPLICATION LIMITS
These products are intended for use in general purpose compressed air
systems only.
Operating Pressure Range: PSIG Bar kPa
Minimum 35 2.4 241
Maximum 150 10.4 1034
Operating Temperature Range: 20°F (-7°C) to 140°F (60°C)
Voltage Range: +10% to -15% of Valve Rating
(Applicable only for solenoid operated valves)
NOTE: The above ratings are those of the associated valve.
INSTALLATION
1) Remove the valve from the subbase or manifold (if assembled) by
removing and discarding the three mounting screws.
2) Clean all mating surfaces of valve, subbase or manifold and Flow
Control "Sandwich" of dust and dirt.
3) Apply a light coating of grease (in kit) to gasket and place in gasket
track on bottom of Flow Control "Sandwich".
4) Place Flow Control "Sandwich" on top of subbase or manifold lining
up all three mounting holes. Electrically operated valves also require
pressing down on flow control to seat electrical plug.
5) Apply a light coating of grease (in kit) to valve gasket and place in
gasket track on bottom of valve.
6) Place valve on top of Flow Control "Sandwich" lining up all three
mounting holes. Electrically operated valves also require pressing
down on valve to seat electrical plug.
7) Assemble valve, flow control and subbase or manifold together with
(3) 1/4-20 screws. Tighten to 35-40 in-lbs. (If valve has a black
plastic cover use the (3) 1/4-20 socket head cap screws. If valve
has a gray metal cover use (3) 1/4-20 button head screws, P/N
H09829. Part number H09829 must be ordered separately).
8) Apply pressure to subbase or manifold and check for leakage at
gasket interfaces. If audible leakage or noticeable bubbling (using
soapy water at joints) is present the gasket probably was accidentally
pushed out of the groove during assembly. If this occurs remove
pressure, disassemble and replace gasket.
ADJUSTMENT PROCEDURES
Adjustment screw nearest to junction box cover on subbase or manifold
controls the flow of air from cylinder port 4 to exhaust port5. With a
double solenoid valve this occurs when operator #12 is actuated. With a
single solenoid valve this occurs when operator #14 is not actuated.
Adjustment screw on other end controls air from cylinder port 2 to
exhaust port 3.
1) Turn both adjustment screws clockwise until fully closed and then
counterclockwise slightly.
2) While cycling valve with cylinder adjust clockwise to decrease speed
or counterclockwise to increase speed.
ANSI SYMBOL
Installation Instructions: V-575P
Sprint/AL Sandwich Flow Controls
ISSUED: July, 1999
Supersedes: November, 1998
ECN #9125
Pneumatic Division North America
Richland, MI 49083
!WARNING
To avoid unpredictable system behavior that can cause personal injury
and property damage:
•Disconnect air supply and depressurize all air lines connected to this
product before installation, servicing, or conversion.
•Disconnect electrical supply before installation, servicing or
conversion.
•Operate within the manufacturer's specified pressure, temperature,
voltage and other conditions listed in these instructions.
•Medium must be moisture-free if ambient temperature is below
freezing.
•Service according to procedures listed on service instructions sheets.
•Installation, service and conversion of these products must be
performed by knowledgeable personnel who understand how
pneumatic products are to be applied.
•After installation, servicing, or conversion, air and electrical supplies
should be connected and the product tested for proper function and
leakage. If audible leakage is present, or the product does not operate
properly, do not put into use.
•Warnings and specifications on the product should not be covered by
paint, etc. If masking is not possible, contact your local representative
for replacement labels.
541 2 3
541 2 3

V-575P
EXTRA COPIES OF THESE INSTRUCTIONS ARE AVAILABLE FOR INCLUSION IN EQUIPMENT / MAINTENANCE
INSTRUCTION MANUALS THAT UTILIZE THESE PRODUCTS. CONTACT YOUR LOCAL REPRESENTATIVE.
WARNING!
FAILURE OR IMPROPER SELECTION OR IMPROPER USE OF THE PRODUCTS AND/OR SYSTEMS DESCRIBED HEREIN OR RELATED
ITEMS CAN CAUSE DEATH, PERSONAL INJURY AND PROPERTY DAMAGE.
This document and other information from Parker Hannifin Corporation, its subsidiaries and authorized distributors provide product and/or system options
for further investigation by users having technical expertise. It is important that you analyze all aspects of your application, including consequences of any
failure, and review the information concerning the product or system in the current product catalog. Due to the variety of operating conditions and
applications for these products or systems, the user, through its own analysis and testing, is solely responsible for making the final selection of the
products and systems and assuring that all performance, safety and warning requirements of the application are met.
The products described herein, including without limitation, product features, specifications, designs, availability and pricing, are subject to change by
Parker Hannifin Corporation and its subsidiaries at any time without notice.
Other Parker Pneumatic Controllers manuals
Popular Controllers manuals by other brands

Festo
Festo SEC-AC-305 General instructions
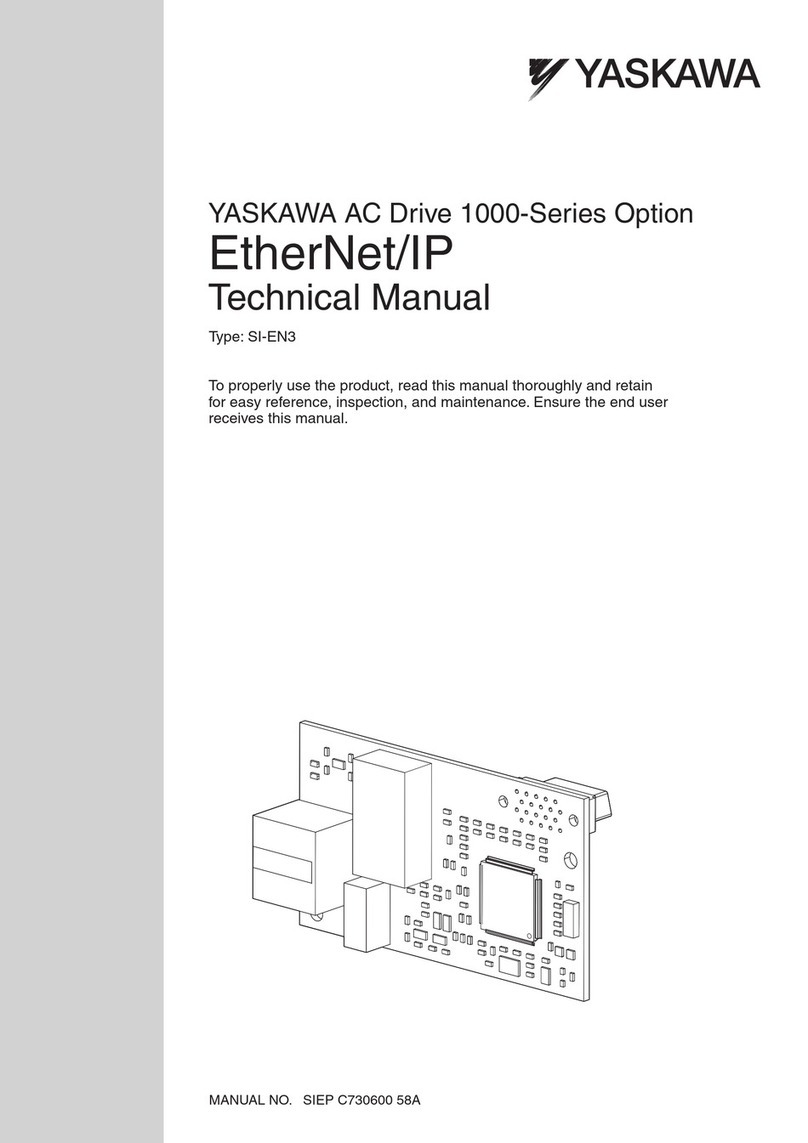
YASKAWA
YASKAWA 1000-Series Technical manual
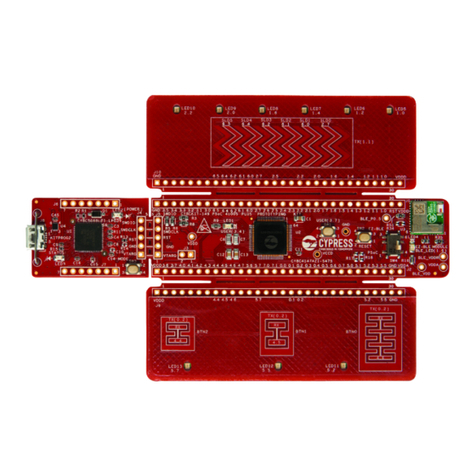
Cypress
Cypress PSoC 4100S Plus manual
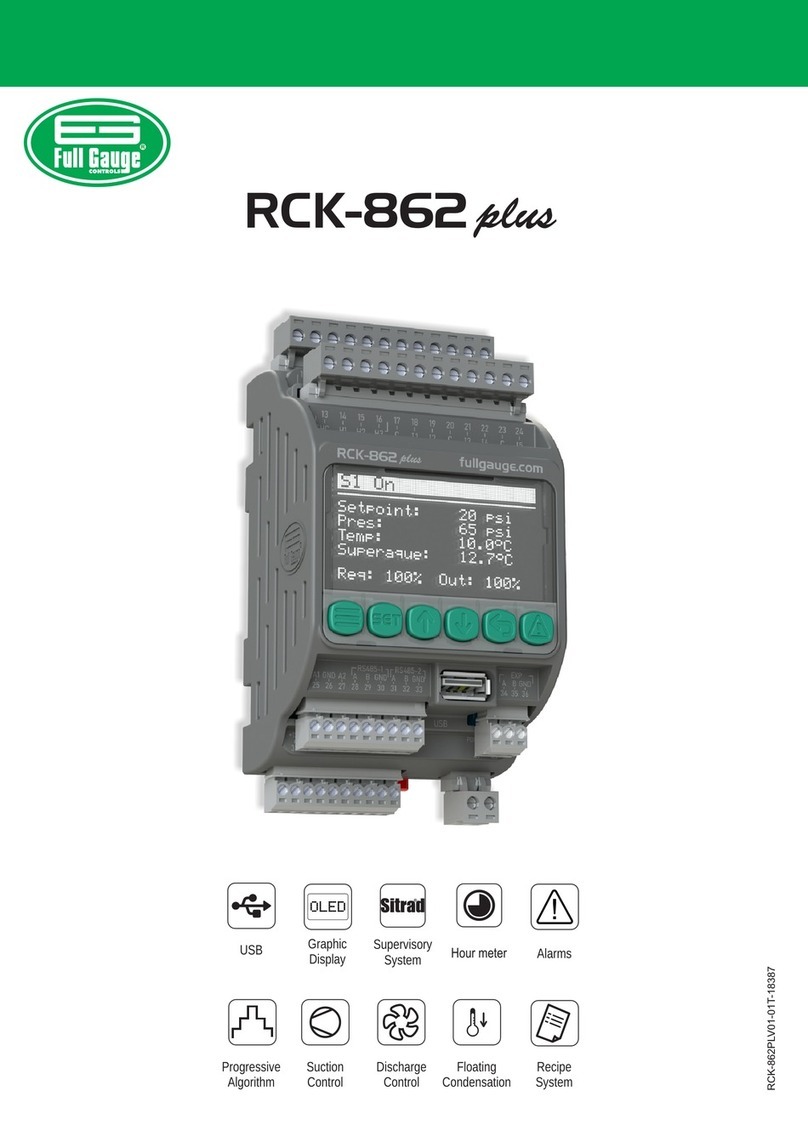
Full Gauge Controls
Full Gauge Controls RCK-862 plus manual
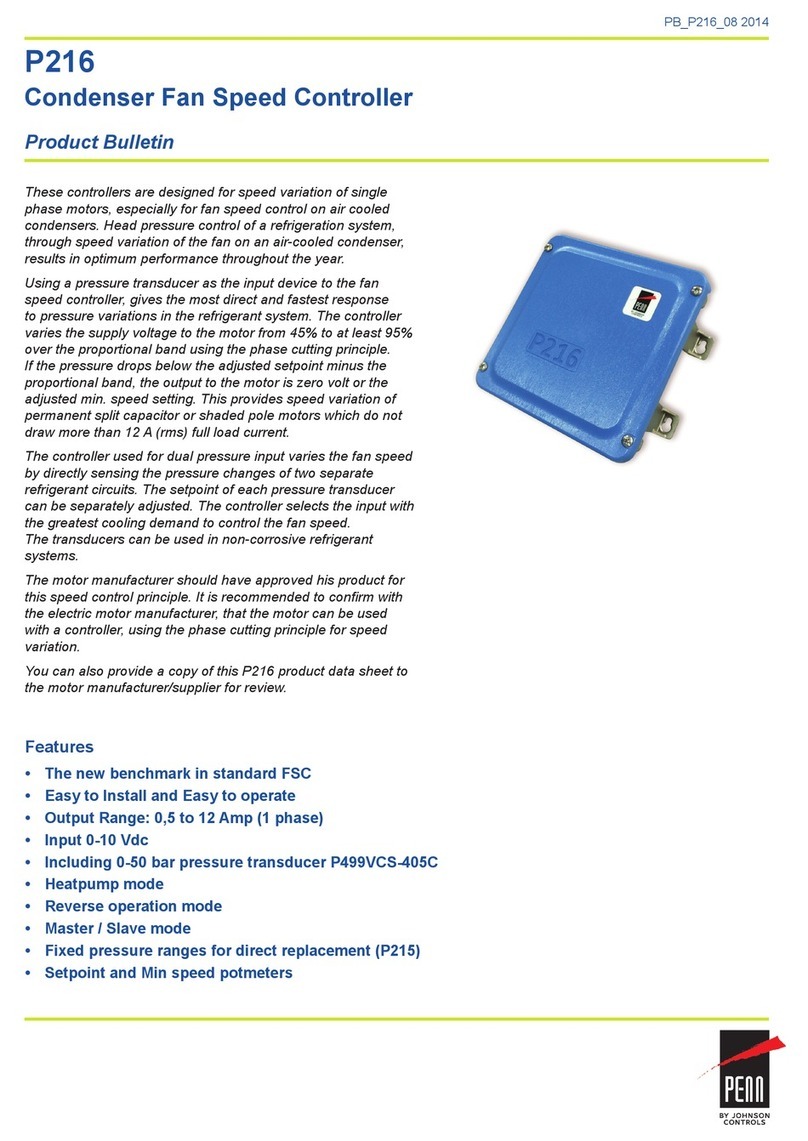
Johnson Controls
Johnson Controls Penn P216 Product bulletin
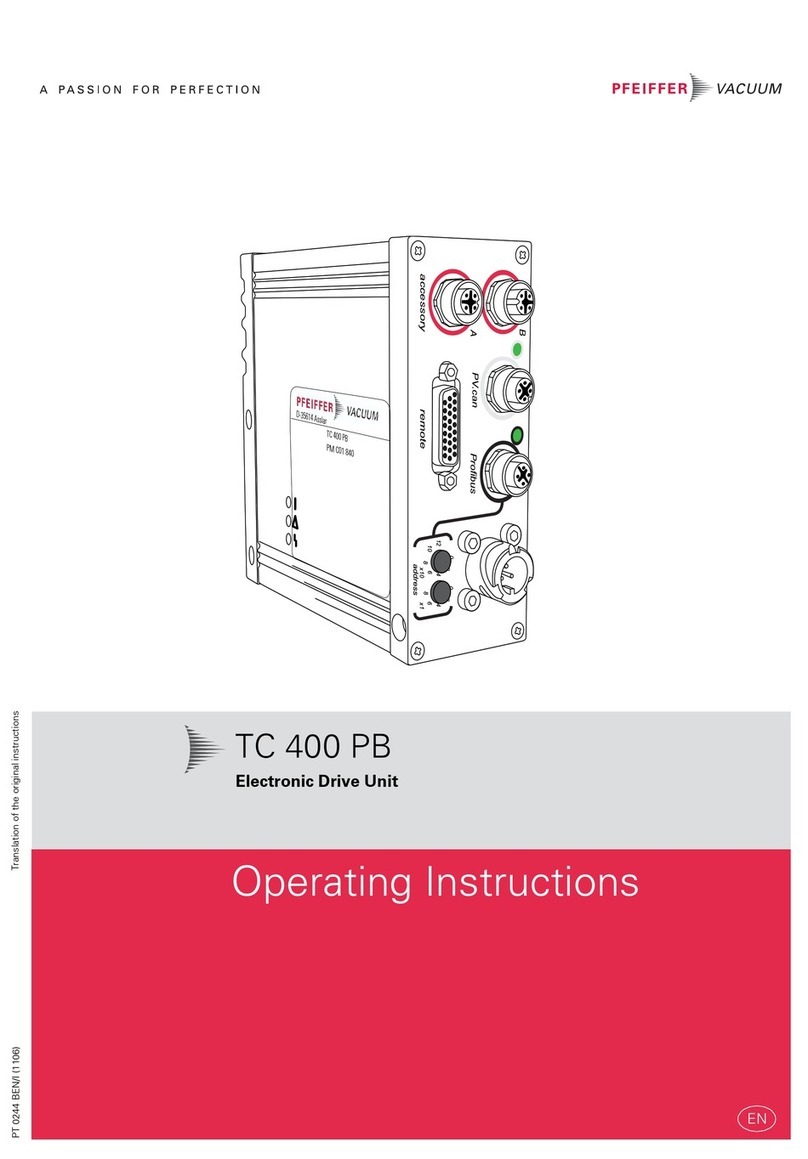
Pfeiffer Vacuum
Pfeiffer Vacuum TC 400 PB operating instructions