Pavone Systems MC 353 User manual

Pavone Sistemi
pesatura elettronica industriale
Rev. 201301
TECHNICAL MANUAL
MC 353 Flow Rate Controller for belt weigher
Software version 1.9

Pag. 2
MC 353 software 1.9 ENG
SYMBOLS
Following are the symbols used throughout the manual to call reader’s attention:
Further details.
Warning! Electric shock risk
Warning! This operation shall be carried out by qualified staff.
Pay special attention to the following points.
WARNINGS
This manual provides texts and pictures to inform the operator about all prescriptions and criteria ne-
cessary for installing and using this instrument.
The equipment shall be installed only by qualified personnel that must have read this manual. With
the expression “qualified personnel” is meant the personnel that has been trained and thus expressly
authorised to carry out the installation by the person in charge for the system safety.
Power the instrument with a voltage value within the limits specified in the features.
The user must make sure that the installation is carried out in compliance with the relevant rules in force.
Please contact the nearest Assistance Centre for every fault you find. Any attempt of disassembly or
change that has not been previously authorised will null and void the warranty and will release the
Manufacturer from any responsibility.
The purchased instrument has been designed and produced to be used in the weighing and metering
processes thus any improper use will release the Manufacturer from any responsibility.

Pag. 3
MC 353 software 1.9 ENG
Table of conTenTs
SYMBOLS ..................................................................................................... 2
WARNINGS.................................................................................................. 2
CE DECLARATION OF CONFORMITY - ............................................................ 5
1 - INTRODUCTION....................................................................................... 6
1.1 - OTHER FUNCTIONS OF MC353............................................................. 8
1.2 - TECHNICAL FEATURES ........................................................................... 9
2 - MC353 INSTALLATION............................................................................ 12
2.1 - INSTALLATION WARNINGS AND INDICATIONS .................................... 12
2.2 - INSTRUCTIONS FOR A CORRECT INSTALLATION ................................... 13
2.3 - ELECTRIC CONNECTIONS ................................................................... 14
3 - MC353 STRUCTURE AND PARAMETERS ................................................... 25
3.1 - PARAMETERING GENERAL FEATURES.................................................... 25
3.2 - MC353 DISPLAYS ................................................................................ 27
3.3 - SET-UP MENU LEVELS ........................................................................... 31
3.4 - PARAMETERS TABLES............................................................................ 33
3.5 - LIST OF PARAMETERS TO BE SET ........................................................... 36
3.6 - LIST OF PARAMETERS PRIOR TO COMMISSIONING ............................... 42
4 - INSTRUMENT PROCEDURE ...................................................................... 45
4.1 - INSTRUMENT COMMISSIONING PROCEDURE ...................................... 45
4.2 - IN-OUT TEST PROCEDURE .................................................................... 46
4.3 - SIMULATION PROCEDURE .................................................................... 46
4.4 - MACHINE TEST PROCEDURE ................................................................ 47
5 - SYSTEM CALIBRATION ............................................................................ 48
5.1 - BELT HOMING DYNAMIC PROCEDURE ................................................. 48
5.2 - BELT CALIBRATION DYNAMIC PROCEDURE ........................................... 49
5.3 - ZERO STATIC CALIBRATION AND WITH SAMPLE WEIGHT ...................... 50
5.4 - MC353 OPERATION ALARMS............................................................... 51
6 - ADDITIONAL FUNCTIONS OF MC353 ..................................................... 53
6.1 - DATA LOGGER .................................................................................... 53
6.2 - SAVE AND LOAD SET-UP ...................................................................... 53

Pag. 4
MC 353 software 1.9 ENG
6.2 - FILE LOADING..................................................................................... 54
6.3 - RECEIPT PRINT..................................................................................... 55
7 - SERIAL COMMUNICATION AND PROTOCOLS.......................................... 56
7.1 - ASCII COMMUNICATION PROTOCOL .................................................. 56
7.2 - MODBUS COMMUNICATION PROTOCOL ............................................ 61
7.3 - PROFIBUS-DP COMMUNICATION PROTOCOL ....................................... 62
7.4 - SUPERVISION FUNCTIONS .................................................................. 71
7.5 - MASTER / SLAVE COMMUNICATION PROTOCOL.................................. 71
7.6 - REPETITOR TRANSMISSION PROTOCOL ................................................ 72
8 - TROUBLESHOOTING ............................................................................. 73
8.1 - TROUBLESHOOTING ........................................................................... 73
CONFIGURATION AND TEST FORM ............................................................. 76

Pag. 5
MC 353 software 1.9 ENG
- CE DECLARATION OF CONFORMITY -
· ELECTROMAGNETIC COMPATIBILITY DIRECTIVE
2004/108/EC
· EN61000-6-2, EN61000-6-3, EN61010-1, EN45501 STANDARDS
MANUFACTURER
Electronic commercial denomination: “Metering control electronic instrument”
Model: “MC353”
Protection class: “IP 65”
It is forbidden to start-up the electronic equipment provided with certication before
the electric panel it is going to be integrated or assembled has been declared conforming
with the Directives requirements.
CERTIFICATION
WE, THE UNDERSIGNED OF THIS DOCUMENT, DECLARE UNDER OUR OWN
RESPONSIBILITY THAT THE CONCERNED ELECTRONIC EQUIPMENT IS
CONFORMINGWITHTHE ITALIAN LAWANDTHUSWITHTHE ELECTROMAGNETIC
COMPATIBILITY DIRECTIVE 2004/108/EC AS WELL AS THE EN61000-6-2, EN61000-
6-3, EN61010-1, EN45501 STANDARDS.
NAME: POSITION:
ISSUE DATE: SIGNATURE:
ELECTRONIC IDENTIFICATION
Pavone Sistemi S.r.l.
Via Dei Chiosi, 18
20873 Cavenago Brianza (MB) - ITALY
Tel. +39.02.95339165 - Fax +39.02.9501252
pavone@pavonesistemi.it - www.pavonesistemi.it
Donato Di Reda sole director
03/02/2012

Pag. 6
MC 353 software 1.9 ENG
1
Inverter
Encoder Flow Rate
Motor
Load Cells
MC 353
PLC / PC
MC 353
Inverter
MotorLoad Cells
Weighing Belt
Encoder
PC / PLC
1 - InTRoDUcTIon
The picture shows how the instrument controls the system adjustment ring.
The MC353 can operate as follows according to its set-up:
FLOW RATE TRANSMITTER
The instrument, thanks to the weight (load cells) and the speed (encoder) signal when it receives the run
input, calculates an instantaneous flow rate which is then transmitted externally through a configurable
analogue output (0÷10 V, 0÷5 V, 0÷20 mA, 4÷20 mA).
It is also possible to receive the following outputs:
- Weight totalization output;
- Conveyed weight preset output;
- Conveyed weight set output;
- Serial communication protocol, Ethernet included.
- Generic alarm output;
- Flow rate equal to 0 output;
- Conveyed weight reset input;
- USB device communication port;
- Optional USB HOST port with USB pen drive interface.
FLOW RATE CONTROLLER
The MC 353 control unit is configured with P.I. (instantaneous flow rate) regulator; it processes the weight
and speed variables to get the instantaneous hourly flow rate and the totalized weight. Furthermore it
acts as flow rate self-regulator.

Pag. 7
MC 353 software 1.9 ENG
1
The external supervisor transmits the work set-up (that can be set also through the keyboard) through
the serial communication to the MC353 control unit; the latter, according to the calculated flow rate
value, controls directly (through analogue output) the inverter frequency of the motor where the weighing
system has been installed.
The MC353 control unit has the following features:
- Weight totalization output;
- Conveyed weight total preset and set output;
- Generic alarm output;
- Flow rate out of tolerance alarm output;
- Flow rate output equal to 0;
- Retroaction analogue output (0÷10V;0÷5V, 0÷20 mA; 4÷20 mA);
- Flow rate proportional optional analogue output;
- Optional analogue input for setting-up the flow rate;
- Inputs for the selection of 15 preset set points;
- Conveyed weight reset input;
- Selection of the instrument state from manual to automatic and vice versa by means of the keyboard,
from the instrument rear side through external contact, and by means of serial communi-
cation protocol;
- Serial communication protocol, Ethernet included;
- Optional USB HOST port with USB pen drive interface.

Pag. 8
MC 353 software 1.9 ENG
1
1.1 - OTHER FUNCTIONS OF MC353
MASTER-SLAVE OPERATION
This instrument can operate as slave, thus acquiring the flow rate setpoint in continuous duty, through
analogue input (0÷10V / 4÷20mA) or digital input (RS485). The flow rate setpoint is updated accor-
ding to the current input: the flow rate setpoint is divided and it represents the input scale end (100%).
In case the current setpoint is set to 0, the setpoint will correspond to the input percentage value of the
system maximum flow rate.
The instrument can also operate as master by transmitting the instantaneous flow rate through the op-
tional analogue output or digital transmission (RS485) for the direct connection to instruments in SLAVE
operation.
PARAMETERS THAT CAN BE SET
It is possible to set the operation parameters through the touch screen user interface; all parameters are
organised on 3 levels with independent access criteria.
All parameters that can be set are listed in a table and clearly identified with a numerical code (address).
The parameters reading and writing access is available on the communication port with supervisor
(Rs422 / RS485 / Ethernet, optional), through the ModBus RTU protocol. Furthermore the parameters
reading and setting can be carried out by sharing files in CSV format on the COM2 communication
port (Rs232 or USB) or directly on USB pen drive connected to the USB Host port (optional).
For operation details see the relevant paragraphs.
DATA IMPORT / EXPORT
To facilitate the data set-up and acquisition in a format that can be used with standard informatic systems
the instrument is provided with files transfer functions (TXT or CSV). It features especially a reading/
writing (even partial) of the memory parameters from CSV files and a data logger procedure to acquire
operation parameters.
To customise the instrument it is possible to set the setpoint names, create Help pages and load the
image displayed upon switching-on (BMP file).
If the instrument is provided with a USB Host option, the import and export of the files mentioned above
can occur directly on USB pen drive.

Pag. 9
MC 353 software 1.9 ENG
1
1.2 - TECHNICAL FEATURES
STRUCTURAL FEATURES
Made of aluminium with polycarbonate screen
Protection class: IP 65
Overall dimensions: 196 mm x 105 mm (l x h)
Panel front projection: 5 mm
Built-in panel front.
Drilling template 187 mm x 97 mm (l x h)
Fixing by means of 4 metallic threaded rods
3 mm rubber seal along all perimeter
Stainless steel coating
Overall dimensions: 186 mm x 95 mm (l x h)
Embedding depth: 70 mm (terminal boards included)
5.08 / 7.5 mm pitch screw terminal board
Standard USB connectors (Host / Device)
RJ45 standard Ethernet connector
Front panel
Assembly
Rear panel
Connections
POWER SUPPLY
24 Vdc (± 15 %)
10W
Cat. II
Operation temperature: -10 °C ÷ + 50 °C
(85% humidity without condensate)
Storage temperature: -20 °C ÷ + 60 °C
Power supply
Max. absorption
Installation category
Temperatures
DISPLAY
5.2” LCD (118 mm x 58 mm visual area) (l x h)
Graphic (240x128 pixel)
Monochromatic (b/w) with high contrast
Backlit with white leds, adjustable intensity
4 wires resistive, suitable for use with gloves and buzzer
Display
Touch screen

Pag. 10
MC 353 software 1.9 ENG
1
LOAD CELLS INPUT
2 input channels for load cells. Acquisition at intervals
or simultaneously at low frequency
5 Vdc / 120mA (max. 8 350 Ohm cells in parallel)
Protected against short circuit
0.02 microV min
< 0.01% of the scale end
< 0.0003% of the scale end / °C
24 bit (16.777.216 points)
Up to 600,000 divisions on the flow rate
7.8 mV/V bipolar
From 12.5Hz to 250Hz
Adjustable from 0.2Hz to 50Hz
No. of channels
Cells supply
Input sensitivity
Linearity
Temperature warmup drift
Internal resolution
Weight resolution
Measure field
Acquisition frequency
Digital filter
ANALOGUE I/O
2 opto-isolated analogue outputs (1 optional)
1 analogue input (optional)
Analogue output: 16 bit
Analogue input: 24 bit
Outputs: 0÷5V, 0÷10V, 0÷20mA, 4÷20mA
Input: 0÷5V, 0÷10V, 4÷20mA
Voltage: 10KΩ min, current 300 max
< 0.03% of the Full Scale
< 0.001% of the Full Scale / °C
No. of channels
Resolution
Measure field
Output impedance
Output linearity
Output temperature
warmup drift
1 2-phase incremental encoder input (up-down, A-B).
As an alternative there are 2 pulse-counting inputs
24Vdc (100mA max)
2 KHz max
ENCODER INPUT
No. of channels
Power supply
Acquisition frequency

Pag. 11
MC 353 software 1.9 ENG
1
6 opto-isolated logic outputs (clean contact)
6 opto-isolated logic inputs (PNP)
30 Vdc max / 60 mA each
12 ÷ 24Vdc (external supply)
Up to 4 external modules with 4 in. / 8 out. each
(16 in. / 32 out. in total)
LOGIC I/O
No. of channels
Output power
Input voltage
Additional I/O
3 independent communication ports (not changed-over)
Rs422 / RS485 / Ethernet (option)
Rs232 / RS485 / USB Device (Virtual Com Port)
Rs232 (only transmission for printer or repetitor,
9600 baud).
15 m (Rs232), 1000 m (RS485)
From 1200 m to 115200 bit/sec
TCP/IP, UDP, ARP, ICMP, ModBus/TCP
USB pen drive interface with FAT16/32 file system
management
It can be implemented with an external module
No. of channels
COM1 interfaces
COM2 interfaces
COM3 interfaces
Wire length
Baud rates
Ethernet protocols
USB Host (optional)
DP Profibus (optional)
COMMUNICATION PORTS
Micro-controller
Code memory
Data memory
Clock / calendar
RISC 32 bit, 44 MHz
Flash 256K Bytes, it can be set on-board (Rs232, USB)
1088 Kbytes standards, it can be expanded
up to 2113 Kbytes
Integrated with a rechargeable buffer battery
CPU
EN61000-6-2, EN61000-6-3, EN61010-1, EN45501
CONFORMITY WITH STANDARDS
Standards

Pag. 12
MC 353 software 1.9 ENG
2
mod.
s.n. MC 353
2010/0000
2.1 - INSTALLATION WARNINGS AND INDICATIONS
Upon installation it is necessary to arrange after and near the equipment a main switch for an omnipolar
cut-off with contact minimum opening of 3 mm.
For cleaning the instrument make use of a cloth slightly soaked in pure alcohol for both the container
and the display.
During the cleaning the instrument must be OFF.
Environmental pollution level: 2
INSTRUMENT ASSEMBLY
- Only qualified personnel shall carry out the following procedures.
- All connections shall be made with instrument OFF.
The instrument shall be assembled in an opening with a 187 x 97 mm drilling template and shall be
fixed by means of the 4 threaded tie rods supplied together with the instrument.
- Consider that the instrument depth with extractable terminal blocks fitted is of 70 mm, and it is neces-
sary to keep place enough for all connections.
- Do not install the instrument near power equipment (motors, inverters, contactors, etc.) or any equipment
non-conforming with the Electromagnetic Compatibility EC Standards.
- The load cells connection cable shall have a maximum length of 140 mt/mm2.
- The Rs232 serial line shall have a maximum length of 15 meters (EIA RS-232-C Standards).
- All warnings concerning all peripheral devices connections shall be duly followed.
The installation environment can be subject to strong magnetic fields and electric interferences due to
present machinery; it is thus recommended to take all precautions so as to prevent them from affecting
the typical signals of a precision electronic equipment (filters on remote control switches, diodes on 24
Vdc relays, etc.)
INSTRUMENT IDENTIFICATION PLATE
In case of information or indications request concerning the instrument it is important to report such data
along with the programme number and version that are printed on the manual cover and displayed
upon instrument switching-on.
2 - Mc353 InsTallaTIon
Pavone Sistemi s.r.l.

Pag. 13
MC 353 software 1.9 ENG
2
2.2 - INSTRUCTIONS FOR A CORRECT INSTALLATION OF THE LOAD CELLS AND
THE MICROPROCESSOR SYSTEMS
1. Do not carry out weldings with load cells fitted.
2. Use a copper conductor to connect the load upper support plate with the lower one, then connect
both upper plates with the earth line.
3. Use watertight fittings and sheaths to protect the cells wires.
4. Use a watertight connection box and a terminal board with cable clamp to connect the cells in
parallel.
5. All “shielded” cables for signal amplifiers or cells connection extensions shall be inserted alone in
the cable conduit or in a tube as far away as possible from the power cables.
6. The amplifier or cells cable shall be inserted in the panel from one side or the other and it should be
connected directly to the instrument terminal block without being interrupted by additional terminal
blocks or passing through cable conduits with other wires.
7. Use “RC” filters on the coils of remote control switches and the solenoid valves controlled by the
micro-processor.
8. In case of condensate inside the equipment it is recommended to always keep them powered.
9. The electric panel installer shall provide all instrument electric protections (fuses, door lock switch,
etc.).
10. It is recommended to connect the housing of the instrument to the protective earth (possibility to use
the set screws of the control unit).

Pag. 14
MC 353 software 1.9 ENG
2
Set OUT
Pre-Set OUT
2.3 - ELECTRIC CONNECTIONS
Only qualified personnel shall carry out the procedures described below. All connections shall be
made with instrument OFF.
- The cell cable shall not be inserted together with other cables (for eg. outputs connected with remote
control switches or supply cables), it must be routed in its own path.
- Any cable extension connection shall be carefully shielded, respecting the colour code and using the
cable type supplied by the manufacturer. The extension connections shall be made through welding or
support terminal blocks or connection box supplied as optional.
- The cell cable shall have a number of conductors not higher than those used (4 or 6). In case of a
4-conductors cable connect the reference wires by making a jumper across the relevant poles of the
supply cables.
It is possible to connect up to maximum 8 350 Ohm cells in parallel to the instrument. The cells supply
voltage is of 5 Vdc and is protected against temporary short circuit. The instrument measurement field
foresees the use of load cells with sensitivity from 1 mV/V to 5 mV/V.
TERMINAL BLOCKS DIAGRAM
LOAD CELL CONNECTION (CONTACTS 1÷6 LOwER TERMINAL BLOCk)

Pag. 15
MC 353 software 1.9 ENG
2
The 6 logic inputs are electrically isolated by the instrument through optoisolators.
The logic inputs connection cables must not be inserted together with power or supply cables and you
have to use a cable as short as possible.
The inputs are active when a voltage of 12 / 24 Vdc is applied (PNP logic).
The 6 logic outputs feature a photorelay (clean contact) with a common contact. The capacity of each
contact is of 60 mA / 30Vdc .
6 WIRES CELL CONNECTION
4 WIRES CELL CONNECTION
NUM. Lower terminal block
(pitch 5.08 mm)
1Cell supply -
2Cell supply +
3Reference cell +
4Reference cell -
5Signal cell -
6Signal cell +
LOGIC INPUTS AND OUTPUTS (CONTACTS 9÷22 LOwER TERMINAL BLOCk)
Note: to use the 4-wires technique make a jumper across terminal 3 and terminal 2, terminal 4 and
terminal 1.
The cell cable SHIELD must be connected with terminal 1 ( CELL SUPPLY -).
NUM. Lower terminal block
(pitch 5.08 mm)
9IN 1 - Run
10 IN 2 - Man / Aut
11 IN 3 - BCD1
12 IN 4 - BCD2
13 IN 5 - BCD4 / Auto 0
14 IN 6 - BCD8 / Reset
15 Input common connector
NUM. Lower terminal block
(pitch 5.08 mm)
16 OUT 1 - Set
17 OUT 2 - Pre-Set
18 OUT 3 - Tot. pulse
19 OUT 4 - General alarm
20 OUT 5 - Flow rate alarm
21 OUT 6 - Flow rate = 0
22 Output common connector
SIGNAL -
POWER SUPPLY +
REFERENCE +
SIGNAL +
REFERENCE -
POWER SUPPLY
SIGNAL -
POWER SUPPLY +
REFERENCE +
SIGNAL +
REFERENCE -
POWER SUPPLY

Pag. 16
MC 353 software 1.9 ENG
2
IN1 - Run static input. Close this contact to enable instrument begin and maintain programmed operations
(weighing, flow regulation, alarms etc.). Input must be kept closed during dosing; open the contact to
stop operations.
IN2 - Manual selection (open) / automatic (closed). The selection through the keyboard has the priority
over the selection of this input. When a selection that does not correspond to the input state is changed
through the keyboard, to commutate the selection with this input it is necessary to first set the selection
according to what had been done by the keyboard, and then commutate it in the desired position. For
example: with the input set to AUTO, it is possible to commutate it to MAN through the keyboard. To
restore the automatic operation using the input it is necessary to first set the input to MAN and then to
AUTO.
IN3 - Bit 1 setpoint selection with BCD coding. The selection is shown on the display. When all inputs
are open the system keeps the last selected combination (even if you switch off the instrument).
IN4 - Bit 2 setpoint selection with BCD coding. The selection is shown on the display. When all inputs
are open the system keeps the last selected combination (even if you switch off the instrument).
IN5 - The function of this input can be selected: the input (closed by pulses) can control the belt homing
remote procedure. Otherwise you can have the function combined with inputs 3, 4 and 6 for selec-
ting the setpoint with BCD coding. (inp. 5 = bit 4). To start AUTOZERO procedure, close input 1027
(parameter INPUT FUNCTION 5 = “belt reset mode”); the above procedure can be activated only
when 3028 RUN STATUS is STOP. Then, set 3028 RUN STATUS = RUN and keep it that way during
the whole duration of the procedure. The duration of the procedure depends upon the time settings of
parameter 0132 BELT LAP TIME, so please wait until this time elapse. During this period, if there are
any anomalies, will be indicated by the alarm output. If, during AUTOZERO procedure duration, no
alarm is raised, you can safely assume that the procedure has successfully ended. Now you can set
again 3028 RUN STATUS = STOP.
IN6 - The function of this input can be selected: the input (closed by pulses) can control the conveyed
total reset, with receipt print if the printer is suitably set. Otherwise you can have the function combined
with inputs 3, 4 and 5 for selecting the setpoint with BCD coding. (inp. 6 = bit 8 if inp. 5 = bit 4; inp.
6 = bit 4 if inp. 5 is selected to control the belt homing procedure).
NOTE: inputs are activated only if activation time exceeds 500 msec.

Pag. 17
MC 353 software 1.9 ENG
2
OUT1 - Total Set reached. This output is active when the total conveyed product exceeds the set value,
anticipated of the set flying material. If the set value is zero, this output is never excited.
The output is disabled when the total conveyed product is reset.
OUT2 - Total PreSet reached. This output is active when the total conveyed product exceeds the SET
value - PRESET value. If the set value is zero, this output is never excited. The output is disabled when
the total conveyed product exceeds the SET value - PRESET value. If the set value is zero this output is
not excited. The output is disabled when the total conveyed product is reset.
OUT3 - Totalization pulse. This output is excited by pulses (0.5 sec.) each time that the quantity of pro-
duct that is conveyed is equal to the set value, max. 1 impulse per second (1 Hz)
OUT4 - Functioning alarm. This output is activated when at least one of the scheduled alarms occurs
(except alarm 3). You can program this function. OUT4 is deactivated automatically when function is
one again normal. Output is active during RUN or always according to parameter’s 1030 settings.
OUT 5 - Instantaneous flow rate out of tolerance. During belt’s RUN (only in automatic mode), this ou-
tput is active if instantaneous flow rate exceeds the set limit. OUT5 is deactivated automatically when
function is one again normal, i.e when flow rate is within tolerance. You can program this function.
OUT6 - Null flow rate alarm (Al 3). During the belt movement this output is active when the null flow
rate alarm (minimum weight or encoder signal missing) is triggered according to the conditions defined
by the 1022 parameter selections.

Pag. 18
MC 353 software 1.9 ENG
2
TX
RX
GND
The instrument is supplied by the 2-pole terminal block with 7.5 mm pitch.
The supply cable shall be inserted separately from other supply cables featuring a different voltage,
from the load cell, encoder and logic and analogue input/output cables.
INSTRUMENT POwER SUPPLY (CONTACTS 23-24, LOwER TERMINAL BLOCk)
NUM. Lower terminal block
(pitch 7.5 mm)
23 + 24Vdc
24 GND
POWER SUPPLY: 24Vdc +/-15%
POWER: 10W
WARNING: when using this connection it is not possible to use an RS485 interface and the USB device
port, shared on the same COM2 communication port.
To make a serial connection use a shielded cable having care to connect to earth the screen to only
one of the two sides. In case the cable has more conductors than those used connect the screen to the
free conductors.
The serial connection cable shall have a maximum length of 15 metres (EIA RS-232-C Standards), if it
is longer it is necessary to use the instrument Rs422 interface.
- The cable shall not be inserted together with other cables (for eg. outputs connected with remote control
switches or supply cables), it must be possibly routed in its own path.
The PC used for the connection shall be compliant with the EN 60950 Standard.
Following is the drawing of the connection with 9-pole PC connector:
COM2 - RS232 SERIAL PORT (CONTACTS 1÷3, UPPER TERMINAL BLOCk)
NUM. Upper terminal block
(pitch 5.08 mm)
1
2
3
Data transmission
Data reception
Signal mass
WARNING: when using this connection it is not possible to use an RS485 and RS232 interface, shared
on the same COM2 communication port.
Use this communication port to interface directly with a PC or through a USB port.
For the connection use a USB standard cable.
To connect the instrument through the USB device port it is necessary to install on the PC the suitable
driver for the used operative system. Follow specific instructions for the installation.
COM2 - USB DEVICE PORT (REAR USB FEMALE CONNECTOR)
- Specification 2.0 compliant; full-speed 12Mbps -
Note: verify that GND (pin 24) is grounded

Pag. 19
MC 353 software 1.9 ENG
2
MASTER
RS485
TX+ / RX+ TX+ / RX+
TX- / RX- TX- / RX-
COM3 - RS232 SERIAL PORT (CONTACTS 3÷6, UPPER TERMINAL BLOCk)
NUM. Upper terminal block
(pitch 5.08 mm)
4TX
5cts
3GND
Data transmission
cts
Signal mass
This communication port is only provided with data transmission functions with fixed communication
parameters. The units that can be connected are a repetition printer or display that shall feature an
RS232 serial interface.
Speed: 9600 bps
Word length: 8 bit.
Start bit: 1 bit. Parity bip: 0 bit. Stop bit: 1 bit.
Handshaking: DTR protocol.
Refer to the printer or repetitor manual to select the communication parameters according to the
transmission.
To make a serial connection use a shielded cable having care to connect to earth the screen to only
one of the two sides. In case the cable has more conductors than those used connect the screen to the
free conductors.
The serial connection cable length shall not exceed 15 meters (EIA RS-232-C Standards).
PRINTER -
REPETITOR
COM2 - RS485 SERIAL PORT (CONTACTS 6-7, UPPER TERMINAL BLOCk)
WARNING: when using this connection it is not possible to use an RS232 interface and the USB com-
munication device port, shared on the same COM2 communication port.
Through the RS485 serial interface it is possible to carry out serial connections for long distances.
This type of connection allows to connect more units to one MASTER using one single serial line. The
maximum number of connected units is 32.
The serial connection cable type shall be suitable for RS485 serial communications with 1 twisted pair
and the relevant shielding.
- The cable shall not be inserted together with other cables (for eg. outputs connected with remote control
switches or supply cables), it must be possibly routed in its own path.
Set the terminal line resistors as specified in the following paragraph.
NUM. Upper terminal block
(pitch 5.08 mm)
6
7TX- / RX-
TX+ / RX+

Pag. 20
MC 353 software 1.9 ENG
8
9TXD-
TXD+
10 RXD+
11 RXD-
TXD+
TXD-
RXD-
RXD+ TXD+
TXD-
RXD-
RXD+
MASTER RS422
2
Through the RS422/RS485 serial interface it is possible to carry out serial connections for long distances.
This type of connection allows also to connect more instruments to one MASTER unit (personal computer,
PLC, etc.), using only one serial line and thus just one MASTER serial port.
The maximum number of connected instruments is 32. Obviously also the master unit shall be equipped
with an RS485 or RS422 serial interface, otherwise it can be supplied as optional.
The serial connection cable type shall be suitable for serial communication with 2 conductor twisted
pairs for RS422, or 1 twisted pair for RS485 and the relevant shielding.
- The cable shall not be inserted together with other cables (for eg. outputs connected with remote control
switches or supply cables), it must be possibly routed in its own path.
Set the terminal line resistors as specified in the following paragraph.
NUM. Upper terminal block
(pitch 5.08 mm)
Other instrument
For the RS485 connection connect in parallel TXD + with RXD+ and TXD- with RXD-.
COM1 - RS422/485 SERIAL PORT (CONTACTS 8÷11, UPPER TERMINAL BLOCk)
TERMINAL RESISTORS RS485 AND RS422
Data bus transmission on RS485 / RS422 connection is differential type, i.e. signal is the result of
tension difference between the 2 wires composing the bus.RS485 / RS422 transmitters provide an
output (under load) of ±2-3 V between output A and B; receivers recognize output levels up to ±200
mV as a valid signal.
This technique provides excellent disturb immunity even with long cable runs.
To minimize reflections, transmitter must have the possibility to insert the polarizing resistance while first
and last network line element should be equipped with a terminal line resistor, connected inparallel to
the line.
Typically, terminal line resistors must have resistance values between 120 and 560 ohm.
In case of connections with dou-
ble pairs RS422 and two nodes,
resistances should be near the fur-
ther receiver while value can be
low up to 120 Ohm (see figure)
Table of contents
Popular Controllers manuals by other brands
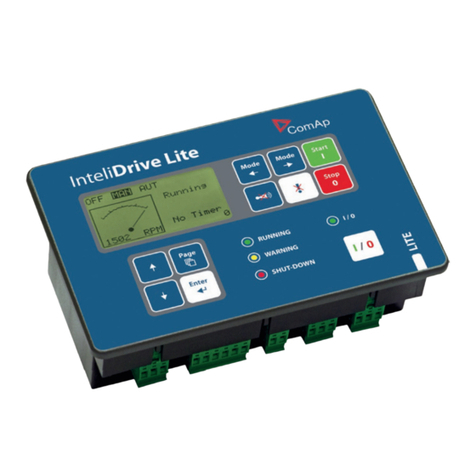
ComAp
ComAp InteliDrive Lite user guide
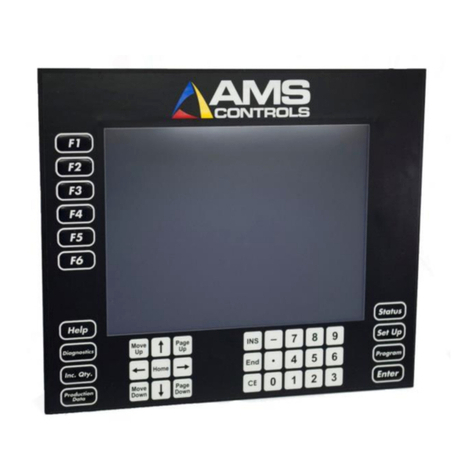
AMS Controls
AMS Controls XL200 ECO 1263 BATTERY REPLACEMENT GUIDE
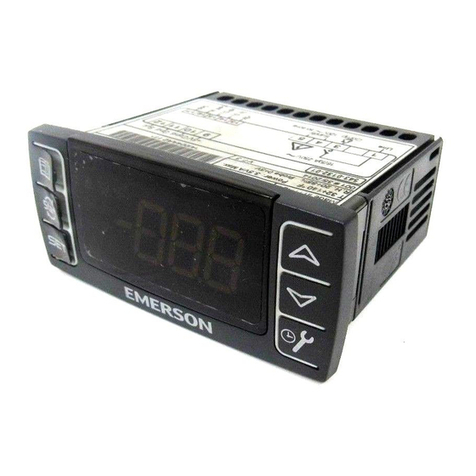
Emerson
Emerson dixell XC10CX Installing and operating instructions
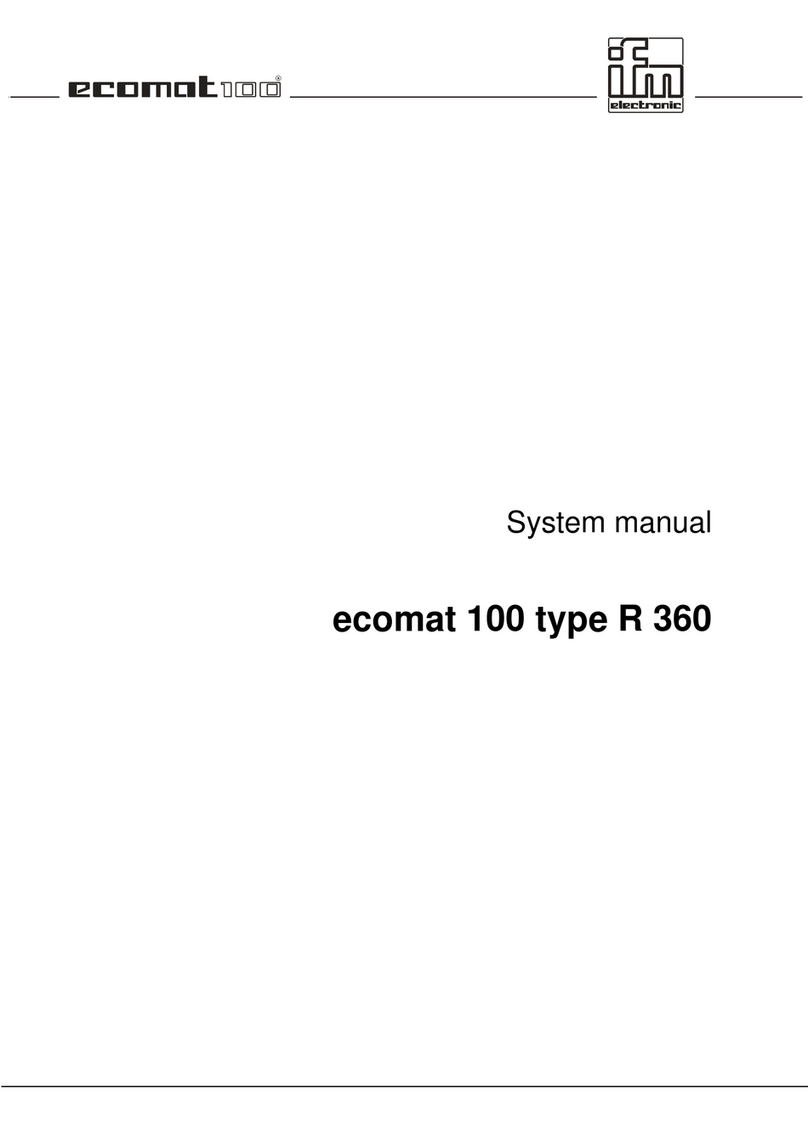
IFM
IFM ecomat 100 R 360 Series System manual
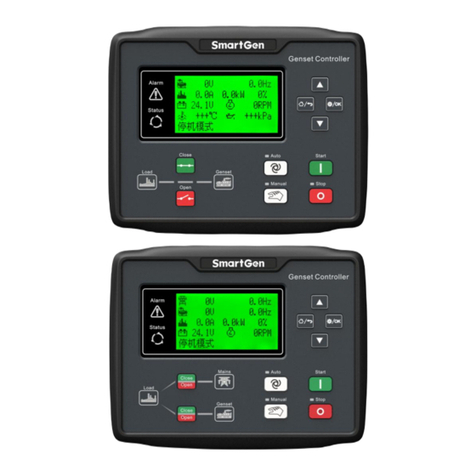
Smartgen
Smartgen HGM6100LT SERIES user manual
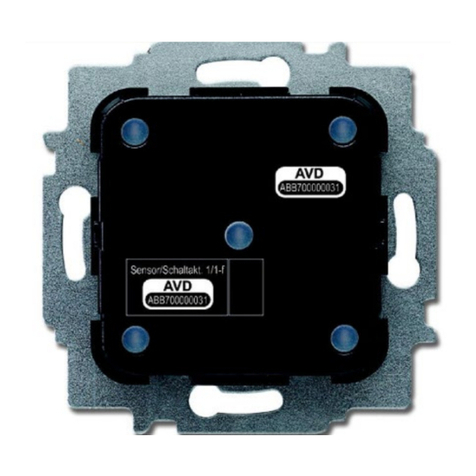
Busch-Jaeger
Busch-Jaeger Busch-free@home 6211/1.1-WL product manual