PICOLAS LDP-C 120-40 NG User manual

User Manual
-preliminary-
LDP-C/CW 120-40 NG
LDP
-
C/CW 80
-
40
NG
PicoLAS GmbH
Burgstrasse 2
52146 Würselen
Phone: +49 (0) 2405-64594-60
Fax: +49 (0) 2405-64594-61
E-Mail: [email protected]
Web:
www.picolas.de

Rev. 01/2021
1
Table of Contents
Product Family Overview and Parameters.................................................................................................................. 2
Please pay attention to all safety warnings! ............................................................................................................... 3
How to use the Manual ....................................................................................................................................................... 4
How to get started (refer to drawings on next 2 pages) ......................................................................................... 5
Connecting and Interfacing ............................................................................................................................................... 6
Interface Specifications ..................................................................................................................................................... 8
Settings and Readings ...................................................................................................................................................... 10
Functional Description ...................................................................................................................................................... 11
Dos and Don’ts .....................................................................................................................................................................13
Test Load .............................................................................................................................................................................. 14
Power Supply ...................................................................................................................................................................... 14
Cooling ................................................................................................................................................................................... 14
Overtemperature Shutdown ........................................................................................................................................... 15
Soft Start ............................................................................................................................................................................... 15
LED Blink Codes .................................................................................................................................................................. 16
Trigger Modes ...................................................................................................................................................................... 17
Mechanical Dimensions ................................................................................................................................................... 18
Power on Self Test ............................................................................................................................................................ 18
Controlling the Driver using a PLB-21 ........................................................................................................................ 20
Menu Structure ................................................................................................................................................................... 20
Pulse Parameters ............................................................................................................................................................... 21
Trigger .................................................................................................................................................................................... 21
Config ...................................................................................................................................................................................... 21
Defaults ................................................................................................................................................................................. 22
Temperature ........................................................................................................................................................................ 22
Measurement ...................................................................................................................................................................... 22
If an Error Occurs .............................................................................................................................................................. 23
Controlling the Driver via PC ......................................................................................................................................... 24
Introduction .......................................................................................................................................................................... 24
Available protocols ............................................................................................................................................................ 24
Description of the RS232 Interface .............................................................................................................................. 24
Description of the Ethernet Interface .......................................................................................................................... 25
The Serial Text Interface .................................................................................................................................................. 26
Structure ............................................................................................................................................................................... 26
Commands for the LDP-C / CW..................................................................................................................................... 27
The PicoLAS Protocol ....................................................................................................................................................... 30
Structure ............................................................................................................................................................................... 30
General Commands ............................................................................................................................................................31
Commands for the Driver ................................................................................................................................................ 32
Register Description ......................................................................................................................................................... 35
Description of the LSTAT Register ............................................................................................................................... 35
Description of the ERROR Register .............................................................................................................................. 37
Impressum ............................................................................................................................................................................ 39

Rev. 01/2021
2
Product Family Overview and Parameters
LDP-C/CW 120-40 LDP-C/CW 80-40
Load Current
Range
10 .. 120 A 10 .. 80 A
Compliance
Voltage
40 V 40 V
Max. Output
Power
4800 W 3200 W
Ripple < 1 A < 1 A
Current
Overshoot
< 1% < 1%
Analog
Modulation
(60 A peak-
peak)
< 4 kHz * < 4 kHz *
Current Setting
Time
(0 .. 100%)
< 100 µs < 100 µs
Current Setpoint
(external)
0 .. 2.4 V (50 A/V) 0 .. 2.0 V (50 A/V)
LD Current
sensing
50 A/V ** 50 A/V **
LD Voltage
sensing
0.1 V/V ** 0.1 V/V **
Inputs LDP-C BOB, PLB-21
LDP-C BOB, PLB-21
Supply 24 .. 48 V,
min. 2 V above LD voltage
24 .. 48 V
min. 2 V above LD voltage
Max. Power
Dissipation
@ 120 A / 12 V
out
175 W abs. max. 175 W abs. max.
Dimensions in
mm
100 x 180 x 74 100 x 180 x 74
Weight 1510 g 1510 g
Operating
Temperature
0 .. +55 °C, non condensing 0 .. +55 °C, non condensing

Rev. 01/2021
3
Please pay attention to all safety warnings!
Change Notes
Rev 01/2021:
- Initial release
Valuable information, remark
Do not
Please pay special attention
Risk of electrical hazard

Rev. 01/2021
4
How to use the Manual
Remark: The LDP-C/CW described in this manual are baseplate cooled devices.
Improper cooling may cause an internal overtemperature shutdown. The two fans in one side
of the unit prevent local thermal hot spots inside the unit. They can not compensate a
baseplate cooling. The air inside an enclosure within an OEM application is usually enough to
yield enough air flow.
Baseplate cooling: Depending on the final application and operation regime, this unit may
stay non-cooled or must be assembled onto a heat sink.
No general rule value can be given. It depends on the (electrical) power used by your diode –
and thus the power dissipation (about 5% of this) in the driver.
You may use a passively or an actively air/water cooled device.
Housing: All units are delivered with housing. Changes are possible the units can be delivered
without housing upon request.
Before powering on your unit, read this manual thoroughly and make sure your understood
everything.
Please pay attention to all safety warnings.
If you have any doubt or suggestion, please do not hesitate to contact us!

Rev. 01/2021
5
How to get started (refer to drawings on next 2 pages)
Step
What to do Check
1 Unpack your device and place it in front
of you as shown on the next page.
2 Connect a load (for example your laser
diode) to the output.
Make sure to use both anode
and cathode connectors in
parallel.
3 The following connectors refer always to
the BOB connector (vertical PWB).
Set pin 8 (master enable) to high
(+ 5 V). In order to do this, you
may connect pin 8 to pin 2 (+5 V).
This master enable feature is used
for the safety shutdown of the
laser.
4 If you do not use your driver as a stand
alone module, please connect it to the
PLB or PC.
Use the Ethernet or the PLB-21
connector.
5 Set pin 7 (enable/disable driver) to low
(0 V)
For start up this input must be
low.
6 Connect the input power supply. Make
sure that polarity is correct. The supply
voltage must be at least 12 V and about 4
V above your diode’s compliance voltage.
If the red LED (on the upper right of the
vertical board – see next side) flashes 4
times, it indicates that the supply voltage
is too low.
Make sure that your power
supply does not have any
voltage overshoots when switching
on or off. Do not exceed the
maximum permitted voltage of
48V
7 Set the required current.
If you use the plain driver, apply a voltage
to pin 10 (input analog).
If you use a PLB or a PC, set the current
via the corresponding commands.
The conversion scale is 50 A/V. So
in order to set a current of 25 A,
you would apply a voltage of
0.5 V.
8 Set pin 7 (enable driver) to high. This starts the driver operation.
9 If you use a pulsed trigger mode (default),
apply your trigger pulses to input pin 6.
Input impedance is 10 kΩ
For pulse parameters see
corresponding datasheets.
10 Monitor the output current with an
oscilloscope on pin 9 or the compliance
voltage on pin 4.
Use pin 3 or pin 5 for ground.
Scales:
50 A/V for current (pin 9)
0.1 V/V for voltage (pin 4)
11 Verify that pin 1 is on 0 V. No internal error, unit works fine.

Rev. 01/2021
6
Connecting and Interfacing
The baseplate is internally not connected to GND to avoid GND loop currents.
The chassis / baseplate must be grounded by the user!
The maximum voltage between GND and chassis is 48 V. Exceeding this
voltage will damage the driver and / or will cause communication errors.
This is not covered by warranty!
Strictly avoid ground loop currents through the controlling interface!
Front view
Serial sticker
Indicating product type,
hardware version (HW)
and software version (SW)
Indicating LEDs
Positive supply
voltage
GND
(supply return)
Ethernet
interface Analog interface
Connect e.g.
BOB here!

Rev. 01/2021
7
Rear view
Digital interface for PLB-21
(RS-232)
LD +
(Anode)
LD –
(Cathode)
LD anode and cathode must be floated and must have no contact to GND!
The drawing shows all connections which are available to the user.
LDP-C BOB
Connector
See section “Interface Specifications” for detailed information. (Breakout
board connector.)
PLB Connector for PLB-21 human interface device (protected against polarity
reversal).
Vin Supply voltage must be about 4 V above laser diode compliance voltage but
at least +12 V. Do not exceed the limits listed in the datasheets. (24 V and
48 V respectively).
GND Supply ground
LD+ Positive laser diode output (anode). It is highly recommended to use both
connectors parallel, especially for high currents.
LD- Negative laser diode output (cathode). Do not connect to ground. It is highly

Rev. 01/2021
8
recommended to use both connectors parallel, especially for high currents.
Ethernet Ethernet connector for linking the driver to a network.
For a more convenient use of the driver (e.g. in laboratory use) we recommend the optional
available product accessories LDP-C BOB or the PLB-21. Please see LDP-C BOB and
PLB-21 manual for further details.
Interface Specifications
The following figure shows the input and output signals of the external analog BOB
connector. This connector can be found on the perpendicular circuit board on the right side as
shown on the previous page.
The BOB (Breakout board) is recommended for easy testing of the driver. It will be replaced
in the application by your machine interface. The PLB-21 is a human interface device that
allows for full control of all relevant device parameters.
Functional Description of the analog Connector Interface
The PLB-21 interface is a standard RS-232 interface connection. It can be used to connect
either the PLB-21 or a PC to the driver.

Rev. 01/2021
9

Rev. 01/2021
10
Settings and Readings
Isetpoint (Pin 10)
This input signal is used to provide an analog setpoint value (amplitude modulation). In order
to use the analog setpoint, it must be configured in the PC via USB or the PLB-21. Please
apply a voltage corresponding to the desired current settings. The scaling is 50 A/V. For
analog modulation the best results are obtained when modulating between 50 and 100% of the
maximum values.
Analog modulation for LDP-CW series Analog modulation for LDP-C series
Idiode (Pin 9)
This signal is used as an output signal of the internal current shunt. It provides near real time
measurement of the output current. Connect your scope and take into account the following
scaling: 50 A/V
Udiode (Pin 4)
This signal is used to determine the compliance voltage of the connected load. It provides
near real time measurement. Connect your scope and take into account the following scaling:
0.1 V/V
Master Enable (MEN) (Pin 8)
The Master Enable provides a safety interlock that disables the driver when pulled low.
This signal must be pulled high by the user for the driver to start up. If the signal is low when
the driver is powered on, it will not work properly.
It is recommended that the user also disables the ENABLE after disabling MEN. Otherwise
there will be a current overshoot on the connected load. When no safety interlock is needed
this signal can be connected to pin 2 of the BOB connector.
Enable (Pin 7)
The ENABLE signal enables / disables the driver during normal operation. The ENABLE
signal must be pulled low by the user in order for the driver to start up. If the signal is high
when the driver is powered on it will not work properly.
After the user applies the ENABLE signal, the internal current regulator ramps the current
flow to the configured setpoint in a configured amount of time (soft start).
Pulse (Pin 6)
This signal is only used by the LDP-C. It provides fast access to the output stage and can be
used to pulse the output current. Its actual usage depends on the configured trigger mode.
Please see section “Trigger Modes” for more details.

Rev. 01/2021
11
Pulser OK (Pin 1)
This signal informs the user about any error condition. It is pulled low by the driver when no
internal error is detected (remark: The word “pulser” here refers to the “driver” itself).
Functional Description
The driver operates with four parallel buck converters (S1, S2, D1, D2, L1; S3, S4, D3, D4,
L2; S5, S6, D5, D6, L3; S7, S8, D7, D8, L4). Every single converter has an independent
control loop with a current sensor (Imeas1, Imeas2, Imeas3 and Imeas4). The setpoint current
that is defined by the user is evenly spread over all four converters. The current through the
laser diode is measured directly at the output pins with the help of a shunt resistor.
Inductor current (additional current of all three phases), laser diode current and compliance
voltage are pre-processed and then fed into to the external BOB connector. An enable input as
well as a status output is available.
Several security features protect the laser diode and driver from damage. D10 protects the
laser diode from reverse currents, S9 could short the output pins and the bypass diode D9
protects the driver in case of a load failure. To protect the laser diode during start-up of the
driver, S0 remains opened until the supply voltage has reached a stable level. In case of a
failure, the control unit disables the driver. A soft start mechanism slowly rises the current
after an over temperature shutdown or at start-up.
Operation principle of the LDP-C/CW driver family

Rev. 01/2021
12
Element Function
S0 Security switch
C1, S1, S2, S3, S4, S5, S6, S7,
S8, D1, D2, D3, D4, D5,
D6,D7 L1, L2, L3, L4
Buck converter
C0 Input buffer capacitor
S9 Shunt MosFETs short output
D9, D10 Laser diode and driver protection diodes
Shunt LD current monitor

Rev. 01/2021
13
Dos and Don’ts
Never ground any output connector. This may result in an incorrect current regulation!
Never use any grounded probes at the output.
Do not connect your oscilloscope to the output!
This will immediately destroy the driver and the probe!
For measuring current and voltage you connect the scope to pin 9 or pin 4 respectively.
Do not shorten the output. This will not do any harm to the laser driver but will result
in an incorrect current measurement.
Keep connecting cables between power supply and driver as well as the connection between
driver and laser diode as short as possible.
Mount the driver on an appropriate heat sink!
Please be aware that there might be hot surfaces, be careful not to touch them!
Do never connect the oscilloscope to the output connectors!!!
(Please note: the picture above shows another but similar PicoLAS driver)

Rev. 01/2021
14
Test Load
A common method to test the driver is to connect a regular silicon rectifier diode to the
driver output. Attention has to be paid to the junction capacitance of the diode. Only fast
recovery diodes (or similar) have as low a parasitic capacitance as laser diodes have. To
achieve reasonable test results, the parasitic elements of the test diode and the connection
must be very similar to a laser diode. Regular silicon rectifier diodes have a junction
capacitance of several microfarads and are not a suitable test load! The use of these diodes
will result in incorrect current measurement at the pulse edges!
Power Supply
To obtain a good pulsing performance with the driver, it requires an appropriate power
supply unit (PSU). The PSU has to supply not only the power that is delivered to the laser
diode but also the power to compensate for the losses in the driver itself. Please take into
account that the laser diode power varies strongly when the output current is modulated.
Although the driver is equipped with a large input capacitance of 12 mF to buffer these
power peaks, the power supply has to deliver the required power fast enough to avoid input
voltage drops. For excessive modulation of the output current, the PSU output impedance as
well as the line impedance between PSU and diode driver has to be as low as possible.
When the input voltage drops below 20.0 V the driver shuts down automatically. To remove
this condition the enable line has to be toggled (switched off and on again).
Cooling
The driver produces up to 220 W of losses. Thus, the baseplate has to be mounted on a heat
sink to ensure proper operation and prevent an overtemperature shutdown. If working with
high currents above 90 A, it is recommended to cool the power inductors as well. This can be
achieved easily by placing the diode driver with its heat sink in the air flow of a fan.

Rev. 01/2021
15
Power dissipation as a function of output current
Overtemperature Shutdown
To protect the laser diode and the driver the unit automatically disables itself if its
temperature rises above the configured shutdown temperature. This condition is latched and
the diode driver will not start working until temperature drops five degrees below the
shutdown temperature and the ENABLE pin is toggled. During the overtemperature
shutdown, the PULSER_OK output (pin 1 of the BOB connector) is pulled low. The
shutdown temperature can be modified using a PLB-21 or via the USB connector.
Soft Start
The driver implements a soft start mechanism, which is activated every time the output is
enabled via the ENABLE pin or the L_ON bit in the LSTAT register. This mechanism ramps
up the current output from zero the setpoint.
0
20
40
60
80
100
120
140
20 40
60
80
100
120
I_out [A]
P_loss [W]
power dissipation

Rev. 01/2021
16
LED Blink Codes
The driver has two status LEDs located above the BOB connector. The green LED indicates
the readiness and the red LED an error condition of the driver. The following table shows the
meaning of the different blink codes:
Nr. Green LED Red LED Meaning Solution
1
on
off
N
ormal operation
--
2
blink 1x
off
S
tand by
--
3
blink 2x
off
Master enable not given
--
4 off off Driver has no power
supply
Switch power on
5 off on When self test has been
completed:
P
ower self test failed
Contact your distributor
6 off on When driver was on
before:
Overtemperature
shutdown
Set ENABLE low and wait
until the driver cooled down
7
off
blink 1x
T
emperature warning

Rev. 01/2021
17
Trigger Modes
The driver can be configured by the user for internal, external or cw trigger.
CW
When the cw mode is configured the LDP-C behaves like the LDP-CW series. See above for
more details.
External
The output stage is controlled by the PULSE signal. Like the cw mode, the current regulator
is controlled by the ENABLE signal and L_ON bit, but the output stage is controlled
separately. Hence, the user can enable the internal current flow, but wait for the soft start to
be finished before enabling the output stage. This will lead to a very low rise time compared
to the soft start. The actual rise time can be configured using the digital control.
Please see sections “Soft Start” and “Timing Diagram” for more details.
Internal
The output stage is controlled by an internal pulse generator which can be enabled / disabled
using the L_ON bit in the LSTAT register. The PULS input is not used. The values for pulse
width and repetition rate can be configured via USB or the PLB-21.
Please see sections “Soft Start” and “Timing Diagram” for more details.

Rev. 01/2021
18
Mechanical Dimensions
All dimensions in mm
Over all height: 69.0 mm

Rev. 01/2021
19
Power on Self Test
Each time the driver is powered on, it performs a test of its internal safety features.
The MEN pin (pin 8, Master Enable) has to be HIGH, while the ENABLE pin
(pin 7) has to be LOW for the self test to work properly.
Changing either of the signals during the self test will result in a failure. The driver cannot be
enabled until a self test has been performed successfully. The PULSER_OK signal will be
pulled high when the test has been successful. (“PULSER” here stands for “diode driver)
The test will take less than 5 seconds, but can take up to 15 seconds due to internal time outs
if any failure is detected. The following diagram shows the individual tests and the
approximate time it will take:
This manual suits for next models
3
Table of contents
Popular DC Drive manuals by other brands
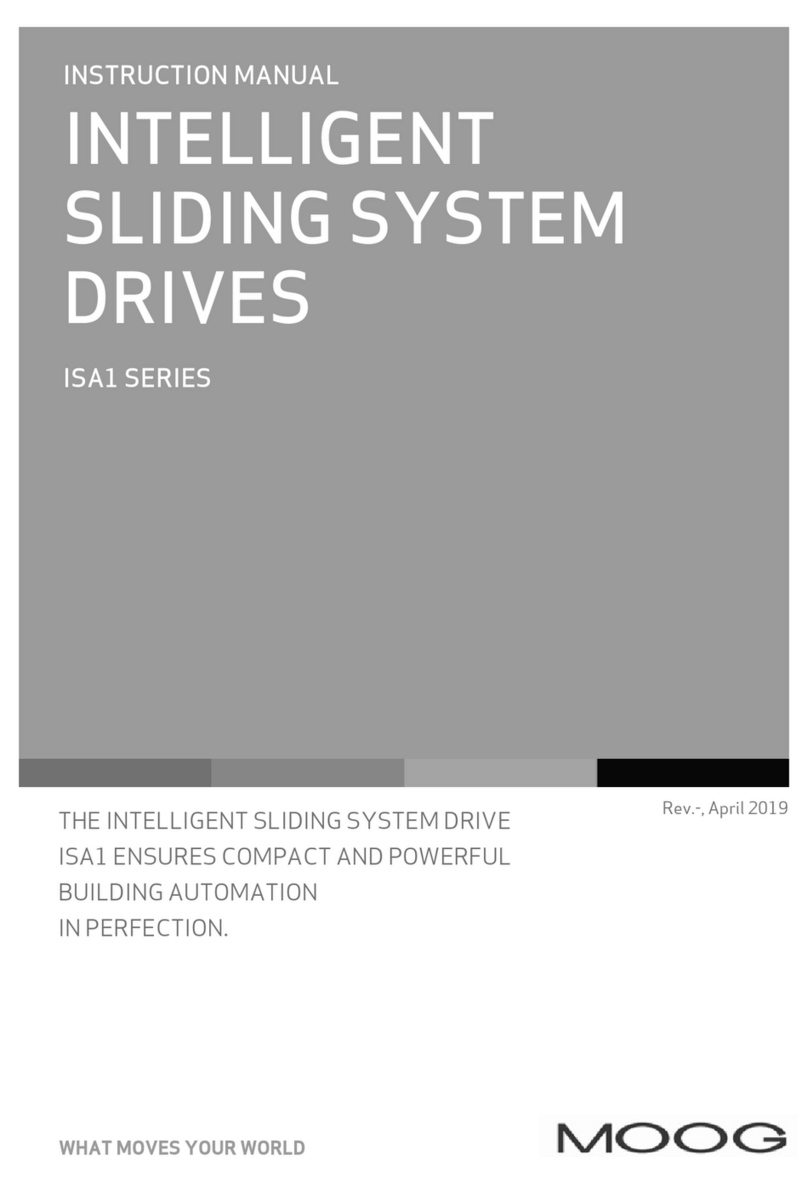
Moog
Moog ISA1 Series instruction manual

ABB
ABB ACS180 Quick installation and start-up guide
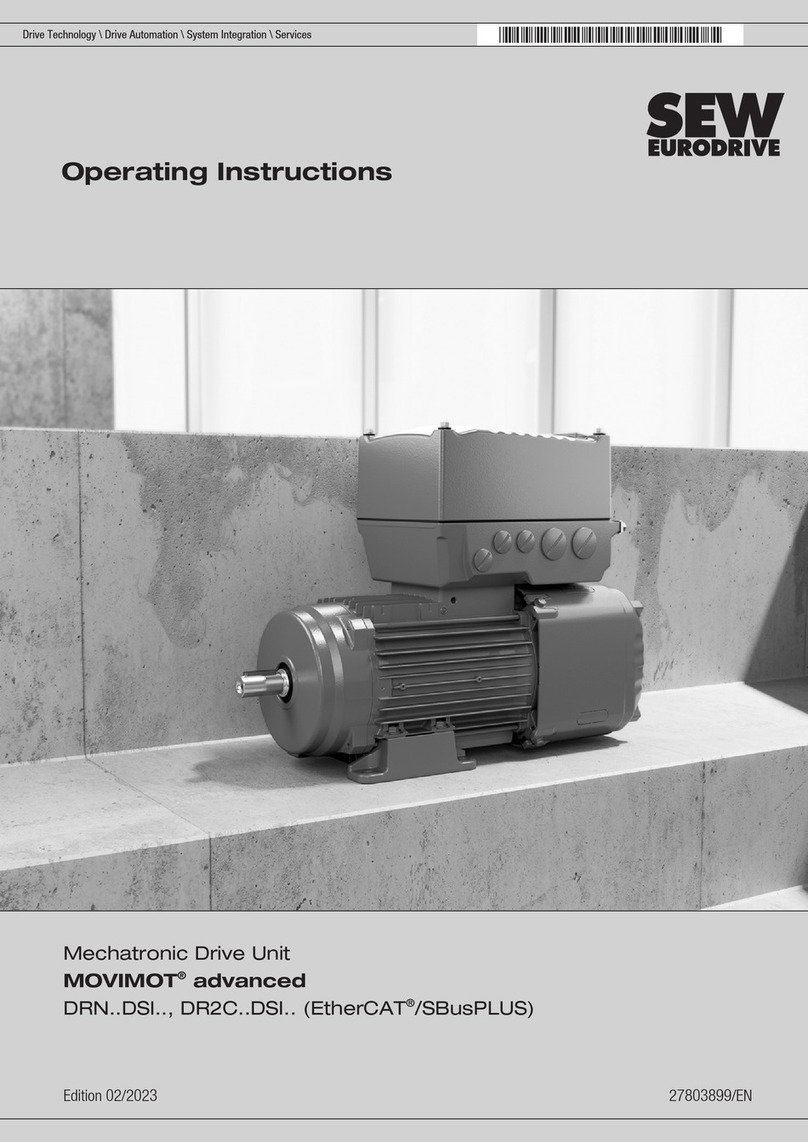
SEW-Eurodrive
SEW-Eurodrive MOVIMOT DRN DSI Series operating instructions
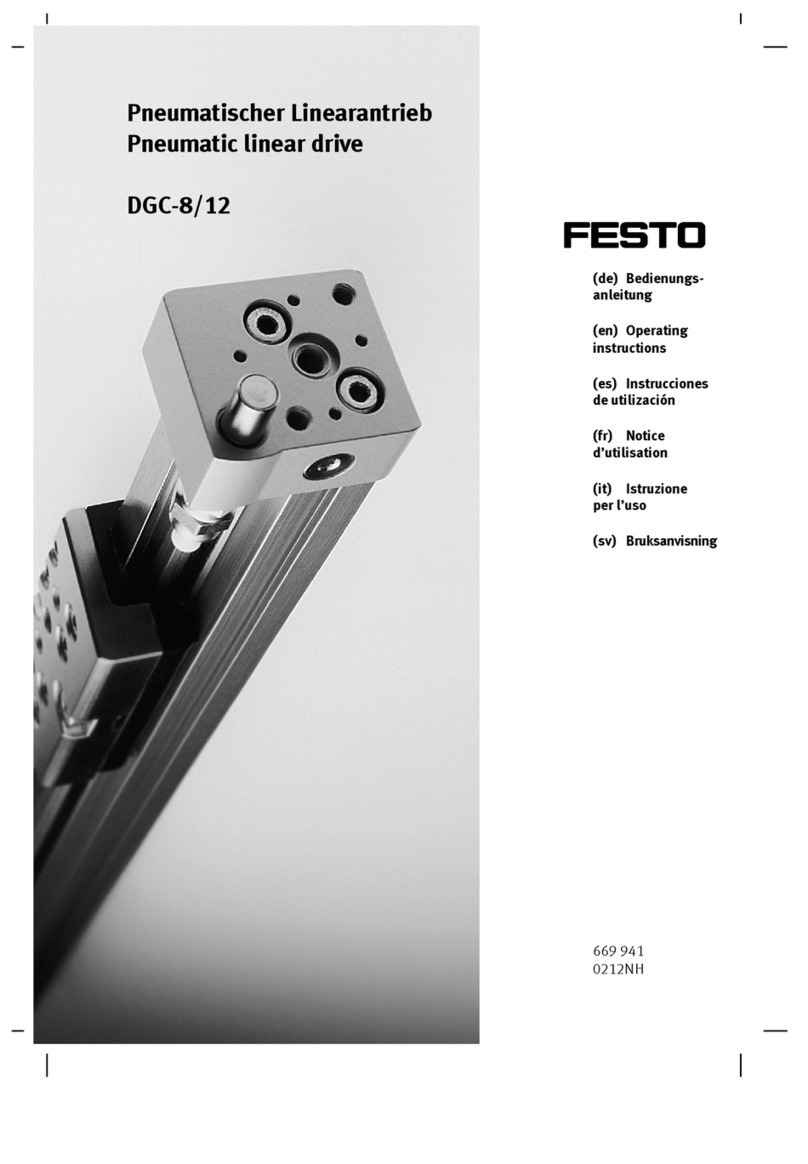
Festo
Festo DGC-8 Series operating instructions
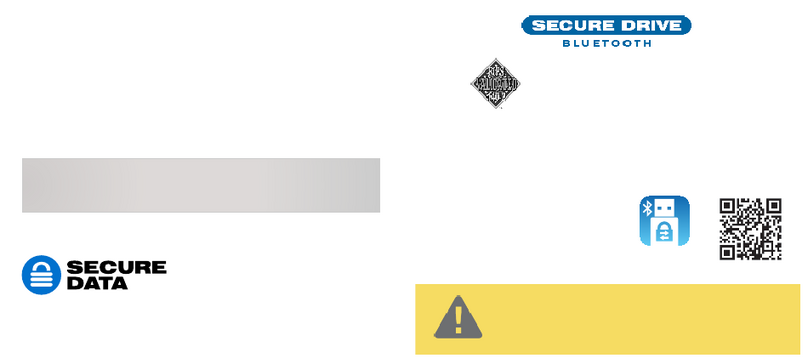
SecureData
SecureData SecureDrive BT quick start guide

KEBCO
KEBCO COMBIVERT Series Getting started