PIETRO FIORENTINI MODUS Series User manual

MT339-I Rev.0.3 08/04/2022
1 - 25
Document classified as: 2 - Company Confidential
Modus
Electronics
TECHNICAL MANUAL

MT339-I Rev.0.3 08/04/2022
2 - 25
Document classified as: 2 - Company Confidential
DISCLAIMER
All rights reserved. No part of this publication may be reproduced, distributed, translated into any
language, or transmitted by any electronic or mechanical means, including photocopying, recording, or
any other means of storage and retrieval, for other purpose other than the purchaser's personal use,
without prior written permission of the Manufacturer.
The Manufacturer is by no means liable for the consequences of operations not performed in
compliance with this manual.

MT339-I Rev.0.3 08/04/2022
3 - 25
Document classified as: 2 - Company Confidential
1Features............................................................................ 4
1.1 Conversion coefficient.............................................................................5
1.2 Energy......................................................................................................5
2Certifications .................................................................... 6
2.1 ATEX 2014/34/UE directive ....................................................................6
2.2 MID 2014/32/UE directive......................................................................6
3Suitability of the equipment for the installation place..... 7
4Power Supply.................................................................... 8
4.1 Batteries (MODUS version A) ..................................................................8
4.2 External power supply (MODUS version T) .............................................9
5User’s Menu ....................................................................10
5.1 Diagnostic..............................................................................................13
5.2 Events....................................................................................................13
5.3 Reasons for closing previous billing period...........................................13
5.4 Factory Reset.........................................................................................13
6Installation .....................................................................14
6.1 MODUS clamps ......................................................................................14
6.2 Prescaler................................................................................................15
6.3 M-Power Clamps....................................................................................15
6.4 Correction channels...............................................................................18
6.5 Metrological unlock Button ...................................................................18
7Metrological sealing .......................................................19
7.2 Non metrological sealings .....................................................................20
8Identification.................................................................. 21
9Maintenance ...................................................................21
10 Verification .....................................................................21
11 Technical specifications.................................................. 22
11.1 I/O characteristic parameters...............................................................23
11.2 Power supply line characteristic parameters ........................................24
12 Disposal ..........................................................................25

MT339-I Rev.0.3 08/04/2022
4 - 25
Document classified as: 2 - Company Confidential
1Features
MODUS is a type 1 gas volume converter with two conversion channels
1
with integrated data-logger.
For each channel, the impulses from the volume meter, the pressure and the temperature of the gas are
acquired and the compressibility factor K and the conversion coefficient C at the reference
thermodynamic conditions are calculated.
If not specified as parameter MODUS calculates the heat of combustion Hs.
Communication with the SAC takes place via the GPRS / GSM network.
Data download, configuration setting and firmware update are possible both remotely and via local
connection
An optical interface compliant with CEI EN 62056-21 is available for local communication with the
equipment
The human-machine interface consists of a liquid crystal display and a keyboard through which it is
possible to navigate through the data presentation menus.
The equipment has the following interface channels towards the field:
3 Pressure inputs (Absolute/relative) from integrated transducers
2 Temperature input from a two wires PT1000 sensor
2 Auxiliary analog inputs with 0÷5 Volt input range
10 Digital inputs
4 Digital outputs
1 RS485 Expansion line
MODUS has been designed to ensure maximum installation versatility and to be powered by a
continuous 12VDC power supply via a dedicated M-POWER power supply, as well as a battery.
Three different versions are available: A, B, T.
MODUS A is equipped with a GSM/GPRS integrated modem and is battery powered.
MODUS B is not equipped with an integrated modem.
It is designed for the use of the M-POWER remote power supply (installed in a safe area) to
which it is possible to communicate the acquired data via an RS485 serial line.
MODUS T is equipped with an integrated GSM/GPRS modem (different from the one for MODUS
A). It is designed for the use of the M-POWER remote power supply (installed in a safe area) to
which it is possible to communicate the acquired data via an RS485 serial line.
1
Second conversion channel can only be viewed through the LCD user interface, and are therefore not available
local data interface (optical interface, RS485) or remote (GSM / GPRS modem) communication.

MT339-I Rev.0.3 08/04/2022
5 - 25
Document classified as: 2 - Company Confidential
1.1 Conversion coefficient
The PTZ corrector performs the acquisition of the pulses emitted by the counter meter and calculates
the equivalent cubic meters base conditions according to the formula:
Symbols
Represented quantity
Measuring unit
Vb
Volume at base conditions
m³
Vm
Volume at measurement conditions
m³
P
Absolute pressure at measurement conditions
bar
Pb
Absolute pressure at base conditions
bar
T
Temperature at measurement conditions
K
Tb
Temperature at measurement conditions
K
Z
Compressibility factor at measurement conditions
-
Zb
Compressibility factor at base conditions
-
C
Conversion factor
-
The compressibility factor takes into account the deviation of behaviour between real and ideal gas. The
calculation method can be configured.
The flow-meter calculates the Z values according to the following standards:
•UNI EN ISO 12213-2 (AGA8-DC92)
•UNI EN ISO 12213-3 (SGERG88)
•AGA-NX19
The conversion factor is calculated according the formula specified into standard UNI EN ISO 12405-1.
1.2 Energy
The device calculates the energy of gas flown according the standard UNI EN 12405-2:2012.
Symbols
Represented quantity
Measuring unit
Vb
Volume at base conditions
m³
E
Energy
J
Hs
Superior calorific value
J/m³
If the compressibility factor configured is AGA8-DC92, the Superior Calorific Value is calculated according
the standard UNI EN ISO 6976:2008, otherwise must be configured by user.
The data-logger processes the metric data according to UNI / TS 11291-3 / 4 and makes them available
to the central acquisition system (SAC) via GSM / GPRS.

MT339-I Rev.0.3 08/04/2022
6 - 25
Document classified as: 2 - Company Confidential
2Certifications
2.1 ATEX 2014/34/UE directive
The MODUS series is certified according to 2014/34 / EU (ATEX) directive both as intrinsically safe
equipment for use in applications in potentially explosive atmospheres and as associated equipment.
Certificate: 0425 ATEX 004371 X
Marking as intrinsically safe equipment:
A version:
II 1 G Ex ia IIA T3 Ga Tamb = -25°C ÷ +60 °C
B version:
II 1 G Ex ia IIB T3 Ga Tamb = -25°C ÷ +60 °C
T version:
II 1 G Ex ia IIA T3 Ga Tamb = -25°C ÷ +60 °C
Marking as associated equipment:
All versions: II (1) G [Ex ia Ga] IIB
Versions MODUS A and MODUS T can only be used with gas from the group IIA while the
version MODUS B can also be used with gas from the group IIB.
EXPLOSION RISK: Installation must be carried out in compliance with the prescriptions
contained in this manual
2.2 MID 2014/32/UE directive
MODUS has been approved MID according to EN12405-1:2005+A2:2010.
Certificate: IT-025-21-MI002-2213

MT339-I Rev.0.3 08/04/2022
7 - 25
Document classified as: 2 - Company Confidential
3Suitability of the equipment for the installation place
In the case of use in areas with danger of explosion, it must be verified that the type of equipment
provided is suitable for the classification of the area and any flammable substances present.
The essential safety requirements against the risk of explosion in classified areas are established by
Directive 2014/34 / EU of the European Parliament and of the Council of 26 February 2014 (as regards
equipment) and 1999/92 / EC of 16 December 1999 (as regards the plants).
The criteria for the classification of areas with risk of explosion are given by the EN60079-10 standard.
The technical requirements of electrical systems in classified areas are given by the EN60079-14
standard.
The following table shows the legend of the marking for use in a hazardous area:
II 1 G
Equipment for surface systems with the presence of gas or vapours, category 1 suitable for zone 0
and with redundancy for zones 1 and 2
Ex ia
Intrinsically safe equipment, category ia
IIA
Equipment of group IIA suitable for substances (gases) of groups IIA.
IIB
(Version B only) Group IIB equipment suitable for substances (gases) of groups IIB.
T3
Equipment temperature class (maximum surface temperature)
Ga
Equipment protection level
Conformity marking to applicable European directives
Marking of conformity to 2014/34 / EU directive and related technical standards
0425 ATEX 004371 X
0425 Number of the laboratory that issued the CE certificate
ATEX Reference directive
004371 Certificate number.
Xindicates that there are particular conditions of use which are indicated in the manual with safety
instructions.
1370
Number of the Notified Body (Bureau Veritas) which carries out the surveillance of the production
system.
Tamb
Ambient operating temperature of the equipment
Equipment with temperature class T3 are also suitable for substances with higher temperature class (T2,
T1)
The following table shows the legend of the marking for use in a safe area as associated equipment.
II (1) G
Associated equipment of category (1), to be installed in a safe area, for surface installations.
[Ex ia Ga]
Associated equipment of category ia with EPL Ga
IIB
Equipment of group IIB suitable for substances (gases) of groups IIB.
Conformity marking to applicable European directives
Marking of conformity to 2014/34 / EU directive and related technical standards
0425 ATEX 004371 X
0425 Number of the laboratory that issued the CE certificate
ATEX Reference directive
004371 Certificate number.
Xindicates that there are particular conditions of use which are indicated in the manual with
safety instructions.
1370
Number of the Notified Body (Bureau Veritas) which carries out the surveillance of the
production system.
Tamb
Ambient operating temperature of the equipment

MT339-I Rev.0.3 08/04/2022
8 - 25
Document classified as: 2 - Company Confidential
Figure 1: CPU Battery
Figure 2: Modem Battery
4Power Supply
4.1 Batteries (MODUS version A)
MODUS Acan use different battery models:
BATTERY CODE
FUNCTION
BATTERY TYPE
DESCRIPTION
HP2 –BP
Modem Power supply
Lithium
Standard
LE-BP
CPU Power supply
Lithium
Standard
HP1-BP2
Modem Power supply
Lithium
Optional
The battery packs have been approved by the Notified Body which issued the ATEX type certificate
and it is therefore absolutely mandatory to use only the model provided.
EXPLOSION RISK
Do not short circuit. Do not heat or incinerate. Do not disassemble. Do not immerse in water. Do
not recharge.
Do not use the BU-BP battery pack for the M-LOG PLUS versions A and B. Use exclusively with the
T version.
Exhausted batteries contain substances that are hazardous to the environment
and are subject to mandatory separate collection: dispose of in accordance with
the laws in force to allow for recycling. CER code 160605.
4.1.1 Replacement
Battery packs must always be replaced in the absence of an explosive atmosphere. Check the
operating conditions with suitable instruments before proceeding.
La Replacing a battery pack involves removing the NON-metrological hardware seals.
It is not possible to insert two LE-BP batteries permanently
After replacing a battery, it is necessary to realign the residual autonomy indicators
To minimize the risk of data loss, two LE - BP batteries can be temporarily connected together on the
CPU board. Before extracting the exhausted battery, connect the new one to the free battery connector
(BT2A or BT2B).
To replace an HP2 - BP or HP1-BP battery, simply extract the exhausted pack and replace it with a
new one.
2
It is possible to equip the HP1-BP equivalent battery as an alternative to the standard HP2-BP.

MT339-I Rev.0.3 08/04/2022
9 - 25
Document classified as: 2 - Company Confidential
4.2 External power supply (MODUS version T)
EXPLOSION RISK: the installation of the remote power supply must be carried out in accordance with
the requirements contained in the MT342-I M-POWER User Manual. Never use models other than the
one provided.
It is NOT allowed to use the external power supply and a battery pack other than BU-BP at the
same time.
MODUS is powered by an external device, the M-POWER.
The remote power supply is available both for solar panel source (PP version) and for mains power
supply with 12Vdc output (INS version).
Both versions are available in the version for DIN rail or wall installation.
To ensure continuity of service in case of interruption of the primary power source, a backup battery
must be considered, the capacity of which must be determined according to the requirements of the
specific use case. The backup battery ensures full system functionality during a power failure.
It is possible to use as a secondary backup an optional lithium battery (BU-BP) capable of keeping only
the conversion function active in case of the main battery failure
It is NOT allowed to simultaneously use the external power supply and a battery pack other than BU-
BP.
The sizing of the mains power supply, the solar panel controller and the backup batteries must be
carried out considering the requirements of the specific application.
Figure 4: M-POWER wall version
Figure 3: M-POWER DIN rail version

MT339-I Rev.0.3 08/04/2022
10 - 25
Document classified as: 2 - Company Confidential
5User’s Menu
Under normal operating conditions MODUS keeps the display off.
To access the main menu, press the OK button.
You can navigate in the menu using the keys . the keyallows you to access the submenus if
available. The key allows you to return to the previous menu.
The menu can only be used to view quantities already configured in the equipment or to force
predefined actions. It is not possible to edit the configurations set.
The Flowmeter menu can show in the first line one or both of the following special characters listed
below
•σ : Metrical sealing temporary unlocked
The metrological release button was pressed. The symbol is shown as long as the display remains
lit.
•β :Volume conversion stopped
Volume conversion is inhibited. The reasons can be different: pressure out of range, temperature
out of range, wrong gas parameters etc
FLOWMETER
Vb 1
Volume Counter at base conditions–channel 1
Vm 1
Volume Counter at measurement conditions–channel 1
Ve 1
Volume Counter at measurement conditions when conversion is
stopped –channel 1
Energy 1
Energy counter–channel 1
Vb2
Volume Counter at base conditions–channel 2
Vm 2
Volume Counter at measurement conditions–channel 2
Ve 2
Volume Counter at measurement conditions when conversion is
stopped –channel 2
Energy 2
Energy counter–channel 2
Measures
→
Press. 1
Absolute pressure at the measurement conditions–channel 1
Temp. 1
Absolute temperature at measurement conditions–channel 1
Zb/Z 1
Gas compression factor at the measurement conditions–channel 1
Zb 1
Gas compression factor at base conditions–channel 1
C 1
Volume conversion factor–channel 1
Press. 2
Absolute pressure at the measurement conditions–channel 2
Temp. 2
Absolute temperature at measurement conditions–channel 2
Zb/Z 2
Gas compression factor at the measurement conditions–channel 2
Zb 2
Gas compression factor at base conditions–channel 2
C 2
Volume conversion factor–channel 2
Parameters
→
Channel 1
→
Composition
See table 2
Channel 2
→
Composition
See table 2
State
→
Diagn.
See table 3
Alarms
Display of any active alarms
Residual
Battery
Percentage of residual flowmeter battery
Contat. Att.
Display of weight and pulse divider
Sistema
→
S/N Conv.
Display of the flowmeter serial number
S/N Press. 1
Display of the serial number of the pressure transducer–channel 1
S/N Temp. 1
Display of the serial number of the temperature transducer–channel 1

MT339-I Rev.0.3 08/04/2022
11 - 25
Document classified as: 2 - Company Confidential
S/N Press. 2
Display of the serial number of the pressure transducer–channel 2
S/N Temp. 2
Display of the serial number of the temperature transducer–channel 2
Vers. FW
Firmware version
Crc FW
Display of the flowmeter firmware CRC
Events
Buffer
→
In queue
→
Events List
Number and list of events with datecode
Abs Counter
Absolute Event counter
Reset
See chapter "Machine reset"
Date & Time
→
Display of the current date and time
Table 1: Flowmeter Menu
Pb
Reference pressure
Tb
Reference temperature
Tcb
PCS combustion temperature
Tpcs
Reference temperature of the PCS measurement
HS
Higher Caloric Power
CO2
Current CO2 concentration
H2
Current H2 concentration
N2
Current N2 (Nitrogen) concentration
CH4
Current CH4 (Methane) concentration
C2H6
Current C2H6 (Ethane) concentration
C3H8
Current C3H8 (Propane) concentration
H20
Current H2O (water) concentration
H2S
Current H2S (Hydrogen sulfide) concentration
CO
Current CO (carbon monoxide) concentration
O2
Current O2 (Oxygen) concentration
iC4
Current Isobutan concentration
nC4
Current Neobutan concentration
iC5
Current Isopentane concentration
nC5
Current neopentane concentration
nC6
Current Neo-C6 concentration
nC7
Current Neo-C7 concentration
nC8
Current Neo-C8 concentration
nC9
Current Neo-C9 concentration
nC10
Current Neo-C10 concentration
He
Current helium concentration
Ar
Current Argon concentration
Table 2: Gaz composition and conversion parameters
NOT CONFIGURED
Factory condition. The machine is NOT operational.
CALIBRATION
Non-operating machine update functions can be performed
NORMAL
Standard operating condition
MAINTENANCE
The equipment is operational but does not store data or events
Table 3: Possible states for the flowmeter section

MT339-I Rev.0.3 08/04/2022
12 - 25
Document classified as: 2 - Company Confidential
DATALOGGER
Id (PDR)
Redelivery point identifier
Per. Fatt.
→
Current
→
ID PT
Rate plan identifier
Vb
Cubic meters counter at standard conditions
Vb F1
Cubic meters counter at standard conditions F1
Vb F2
Cubic meters counter at standard conditions F2
Vb F3
Cubic meters counter at standard conditions F3
Vm
Cubic meters counter at the measurement conditions
Vm F1
Cubic meters counter at the measurement conditions F1
Vm F2
Cubic meters counter at the measurement conditions F2
Vm F3
Cubic meters counter at the measurement conditions F3
Vme
Cubic meters counter in error
Vme F1
Cubic meters counter in error F1
Vme F2
Cubic meters counter in error F2
Vme F3
Cubic meters counter in error F3
→
Previous
→
ID PT
Rate plan identifier
Reason
Reason for period closure - see table 6
Vb
Cubic meters counter at standard conditions
Vb F1
Cubic meters counter at standard conditions F1
Vb F2
Cubic meters counter at standard conditions F2
Vb F3
Cubic meters counter at standard conditions F3
Vm
Cubic meters counter at the measurement conditions
Vm F1
Cubic meters counter at the measurement conditions F1
Vm F2
Cubic meters counter at the measurement conditions F2
Vm F3
Cubic meters counter at the measurement conditions F3
Vme
Cubic meters counter in error
Vme F1
Cubic meters counter in error F1
Vme F2
Cubic meters counter in error F2
Vme F3
Cubic meters counter in error F3
Matr. Cont.
→
Mechanical counter serial number
Modem
→
Call SAC
Force call to the configured remote management centre
SMS Test SAC
Force sending test SMS
Turn on GSM Data
Force power on modem in GSM data mode
Turn on GPRS
Force modem power on in GPRS data mode
Gprs DCE IP
Displays the last IP assigned by the network
GSM Field
Displays the intensity of the GSM field
Local echo modem
Enable modem echo on local serial port
Last connection
Date and time of the last connection occurred
Message SAC
→
P0
Text message from SAC profile 0
P1
Text message from SAC profile 1
P2
Text message from SAC profile 2
P3
Text message from SAC profile 3
P4
Text message from SAC profile 4
Table 4: Datalogger menu

MT339-I Rev.0.3 08/04/2022
13 - 25
Document classified as: 2 - Company Confidential
5.1 Diagnostic
The diagnostic information shown on the display reports the status of each diagnostic bit in
hexadecimal format. Each bit equal to 1 indicates a specific anomaly.
1
2
3
4
5
6
7
8
9
10
11
12
13
14
15
16
17
18
19
20
21
22
23
24
25
26
27
28
29
30
31
32
0 - 4
0 - F
0
0
0 - 2
0 - 3
0 - F
0 - E
VISUALIZZAZIONE A DISPLAY
FUNCTION
BIT
FUNCTION
BIT
FUNCTION
BIT
FUNCTION
BIT
GENERAL ALARM
1
RISERVATO
9
RISERVATO
17
CONVERSION STOPPED
25
STATUS NOT NORMAL
2
RISERVATO
10
RISERVATO
18
UNALIGNED CLOCK
26
PRESSURE ERROR
3
RISERVATO
11
RISERVATO
19
EVENT QUEUE FULL
27
TEMPERATURE ERROR
4
RISERVATO
12
RISERVATO
20
TAMPER ALARM
28
ERR. Z CALCULATION
5
RISERVATO
13
RISERVATO
21
GENERIC ALARM
29
ERR. CONFIGURATION
6
RISERVATO
14
Q OUT OF RANGE
22
EVENT QUEUE 90%
30
PRESS. UNCALIBRATED
7
RISERVATO
15
PRESS. OUT OF RANGE
23
LOW BATTERY
31
TEMP. UNCALIBRATED
8
RISERVATO
16
TEMP. OUT OF RANGE
24
RESERVED
32
Table 4: Flowmeter diagnostic section
5.2 Events
N
DISPLAY
DESCRIPTION
N
DISPLAY
DESCRIPTION
1
GENERIC
Generic Event
14
PROG.DST
Changed DST Setting.
2
OUT OF LIMIT
Out Of Limit
15
EVT FULL
Event Queue Full
3
OUT OF RANGE
Out Of Range
16
CONF BILLING
Changed Billing Period
4
MOD. PARAM.
Modified CTR Object
17
START BILLING
Start New Billing Period
5
FAILURE
Generic Failure
18
CONF SW
New Firmware Downloaded
6
NO SUPPLY
No 230V
19
START SW
New Firmware Active
7
LOW BATT
Low Battery
20
REBOOT
Reboot
8
MOD. DATE
Date and Time Mod.
21
STATUS NOR.
Status Changed to NORMAL
9
CALC ERROR
Calculation Error
22
STATUS UNCO
Status Changed to UNCONFIGURED
10
RESET MEM
Factory Reset
23
STATUS MNT
Status Changed to MAINTENANCE
11
UNLOCKED SEAL
Unlocked Software Seal
24
SEAL MOD.
Password Changed
12
SYNC ERR.
Date or Time Error
25
BATT.REPL.
Battery Replaced
13
EVT RESET
Event Queue Reset
Table 6: Events
5.3 Reasons for closing previous billing period
Code
Description
1
Changed provider
2
New contract
3
New user
4
Changer distributor
5
End of billing period
6
New billing period
Table 7: Reasons for closing billing period
5.4 Factory Reset
It is possible to restore the RTU to its original factory conditions.
1. Disconnect the LE –BP battery pack;
2. Wait for 5 seconds;
3. Holding down the keys Reconnect the battery pack; wait for the message RESET HW to
appear on the display;
4. Wait for the RTU to restart.

MT339-I Rev.0.3 08/04/2022
14 - 25
Document classified as: 2 - Company Confidential
6Installation
It is NOT sufficient for a device to be intrinsically safe for it to be connected to associated equipment. It is
necessary that a qualified technician or a body in charge proceed with the verification of the system and
issue of suitable certification proving the compatibility between the electrical safety parameters possessed by both
devices.
The essential safety requirements against the risk of explosion in classified areas are established by the European
Directives 2014/34 / EU of 26 February 2014 (for equipment) and 1999/92 / EC of 16 December 1999 (for plants).
The criteria for the classification of areas with risk of explosion are given by the EN60079-10 standard.
The technical requirements of electrical systems in classified areas are given by the EN60079-14 standard.
6.1 MODUS clamps
The replacement of the pressure or temperature transducer is not allowed.
Opening the lid removes the metric seals.
Refer to chapter 8 for the characteristic parameters of intrinsically safe circuits.
Figure 5: MODUS clamps
Auxiliary inputs AIN1, AIN2 accept analog signals from galvanically isolated instruments. Refer to Chapter
8 for safety parameters for electrical coordination.
The digital inputs from number 1 to number 8 provide for the application of a voltage-free signal, inputs
DI9 and DI10 can also accept a voltage signal.
The RS485 expansion line can be used for connection to a galvanically isolated equipment.
The digital outputs provide four open collector channels. The devices to which the connection is made
must be galvanically isolated.
Clamp.
DEN.
FUNCTION
Clamp.
DEN.
FUNCTION
Clamp.
DEN.
FUNCTION
M3
GND
Ground
M4
GND
Ground
M3
DO1+
Digital Output 1 - positive
GND
Ground
V CPU
CPU Power Supply
DO1-
Digital Output 1 –negative
DI1
Digital Input 1
V MDM
GSM Modem Power
Supply
DO2+
Digital Output 2 - positive
DI2
Digital Input 2
485 +
RS485 LINE+
DO2-
Digital Output 2 - negative
DI3
Digital Input 3
485 -
RS485 LINE-
DO3+
Digital Output 3 - positive
DI4
Digital Input 4
DO3-
Digital Output 3 - negative
DI5
Digital Input 5
DO4+
Digital Output 4 - positive
DI6
Digital Input 6
DO4-
Digital Output 4 - negative
DI7
Digital Input 7
DI8
Digital Input 8
DI9
Digital Input 9
DI10
Digital Input 10
Table 8: Description of the available clamps

MT339-I Rev.0.3 08/04/2022
15 - 25
Document classified as: 2 - Company Confidential
6.2 Prescaler
Clamps DI9 and DI10 (M3-11, M3-12) have two independent prescalers that can be enabled via selector
LK3 and LK2 respectively.
In this mode the frequency of the input pulses is divided by a configurable factor from 8 to 4096, this
allows to extend the range of input pulse frequencies up to 12KHz.
The prescalers are configured by the LK4 and LK5 selectors; the available options are shown in Tables 9
and 10.
Figure 6: Selectors for enabling and configuring the prescalers for digital inputs DI9 and DI10
LK3
LK5
Prescaler
Frequency
Max
LK2
LK4
Prescaler
Frequency
Max
A-B
-
-
3 Hz
A-B
-
-
3 Hz
B-C
A
1
3 Hz
B-C
A
1
3 Hz
B
8
24 Hz
B
8
24 Hz
C
64
192 Hz
C
64
192 Hz
D
512
1.5 KHz
D
512
1.5 KHz
E
4096
5 KHz
E
4096
5 KHz
Table 9 - DI9 Configuration Table 10 - DI10 Configuration
6.3 M-Power Clamps
6.3.1 Main Board
CLAMP.
DEN.
FUNCTION
M1
Vin+
Power Supply Input - Positive
Vin-
Power Supply Input - Negative
M2
RS485 A
RS485 EXPANSION LINE+
RS485 B
RS485 EXPANSION LINE-
M3
RS485 A
RS485 LINE+
RS485 B
RS485 LINE-
M4
LOW BATT +
Low battery Digital Output –Positive
LOW BATT -
Low battery Digital Output - Negative
M5
V MODEM+
Modem Power Supply Output - Positive
V MODEM-
Modem Power Supply Output - Negative
M6
V CPU+
CPU Power Supply Output - Positive
V CPU-
CPU Power Supply Output - Negative

MT339-I Rev.0.3 08/04/2022
16 - 25
Document classified as: 2 - Company Confidential
Table 11: M-Power Clamps
6.3.2 Namur inputs expansion
Figure 8:5 NAMUR inputs expansion Table 12:Namur Clamp
6.3.3 Digital/Analog inputs expansion
Table 13: Analog/Digital inputs
expansion Link configuration
CLAMP.
DEN.
FUNCTION
M201
OUT1+
Transducer connection NAMUR 1 - positive
OUT1-
Transducer connection NAMUR 1 - negative
OUT2+
Transducer connection NAMUR 2 - positive
OUT2-
Transducer connection NAMUR 2 - negative
M202
IN1+
Repetition NAMUR 1 –positive
IN1-
Repetition NAMUR 1 –negative
IN2+
Repetition NAMUR 2 –positive
IN2-
Repetition NAMUR 3 - negative
LINK
POS.
FUNCTION
LK1
1 –2
AIN3 +-5V FS o 4-
20mA (LK3)
2 –3
AIN3 0 +- 20V FS
Open
AIN3 Open
LK2
Open
AIN0 Voltage
Closed
AIN0 Current
LK3
Open
AIN3 Voltage
Closed
AIN3 Current
LK4
Open
AIN2 Voltage
Closed
AIN2 Current
LK5
Open
AIN1 Voltage
Closed
AIN1 Current
Figure 9:6 Exapansion I/O

MT339-I Rev.0.3 08/04/2022
17 - 25
Document classified as: 2 - Company Confidential
DIN RAIL M-POWER INPUTS IP 67 M-POWER INPUTS
CLAMP
DEN
FUNCTION
CLAMP.
DEN
FUNCTION
M1A
GND
Ground
M1
GND
Ground
DI1
Digital input 1
DI1
Digital input 1
DI2
Digital input 2
DI2
Digital input 2
DI3
Digital input 3
DI3
Digital input 3
DI4
Digital input 4
DI4
Digital input 4
GND
Ground
GND
Ground
GND
Ground
M1B
AIN1
Analog input 1
AIN1
Analog input 1
AIN2
Analog input 2
AIN2
Analog input 2
AIN3
Analog input 3
AIN3
Analog input 3
AIN4
Analog input 4
AIN4
Analog input 4
DO1+
Digital output 1 –positive
DO1+
Digital output 1 –positive
DO1-
Digital output 1 –negative
DO1-
Digital output 1 –negative
DO2+
Digital output 2 –positive
DO2+
Digital output 2 –positive
DO2-
Digital output 2 –negative
DO2-
Digital output 2 –negative
Table 13: DIN RAIL inputs Table 14: IP 67 inputs

MT339-I Rev.0.3 08/04/2022
18 - 25
Document classified as: 2 - Company Confidential
6.4 Correction channels
MODUS has two independent correction channels PTZ1 and PTZ2.
The PTZ2 channel has a prescaler for extending the frequency range of the impulse arriving from the
counter.
The following table shows the wiring and configuration diagram of the two channels. The number and
characteristics of the correction channels actually available depend on the order code used to purchase
the specific machine.
Channel
Clamps
Prescaler
Max
Frequency
Pressure
M2
Temperature
M1
Pulse
M3
Activation
LK2
Configuration
LK4
PTZ 1
VP1+
VS1+
VS1-
PSW1
PTA+
PTA-
D1
GND
-
-
3 Hz
PTZ 2
VP2+
VS2+
VS2-
PSW2
PTB+
PTB-
D10
GND
A-B
-
3 Hz
B-C
A
3 Hz
B
24 Hz
C
192 Hz
D
1.5 KHz
E
5 KHz
6.5 Metrological unlock Button
The Metrological unlock button is accessed removing main cover, protected by Metrological seals.
After pressing Metrological Unlock Button the software Metrological seals are unlocked and Metrological
parameters can be modified. The software Metrological seals return to locked status when display switch
off after 30 seconds of keyboard activity.
During the period the Metrological seals are unlocked the display shows symbol σas first character of
first line
When the Metrological seal is unlocked the following parameters, can be modified:
•Vm –Volume at measure conditions
•Vb –Volume at base conditions
•Ve –Volume in error conditions
•Energy
•Pulse configuration
•Device Status
•Erase Events Queue
The activation and deactivation of the metrological unlock and the modification of the parameters are
recorded as events.

MT339-I Rev.0.3 08/04/2022
19 - 25
Document classified as: 2 - Company Confidential
Figure 9 –Metrological unlock Button
7Metrological sealing
Sealing takes place by affixing two different types of seals: type A seals (adhesives), type B seals (lead).
Type A seals protect:
•The programming button, which is pressed to reprogram some parameters of metrological
significance (sealing A-1, figure 10)
•Motherboard and components (sealing A-2, figure 10)
•Clamps (sealing A-3 e A-4, figure 10)
Figure 10: Type A sealings within the MODUS
Type B sealings protect:
•The connection of pressure transducer / transducers to the system (sealing B-1, figure 11)
•The connection of temperature transducer / transducers to the system (sealing B-2, figure 12)
•The connection between the device and the volume counter (sealing B-3, figure 13)
•The lid of M-Power, if available (sealing B-4, figure 14)
The change of the metrological parameters of the device is protected by a programming button (PROG,
see par.
“Metrological Unlock Button”
), when pressed allows you to reprogram some parameters of
metrological relevance.
Figure 11: Type B sealing for pressure transducer Figure 12: Type B sealing for temperature transducer

MT339-I Rev.0.3 08/04/2022
20 - 25
Document classified as: 2 - Company Confidential
Figure 13: Type B sealing for pulse acquisition Figure 14: Type B sealing for MPOWER lid
7.1.1 Metrological Software sealings
The device provides programming of meteorologically relevant parameters through the optical interface,
which access is restricted by a password and can only be accessed by authorized personnel.
Implemented as requested by the point 6.1.3 of the EN 12405-1:2005 + A2:2010:
1. Restricted access by Password (Changeable);
2. Registration, with date and time, of at least the last intervention carried out;
3. Possibility to access the events recorded in the memory. The events are shown on the display
with the following sequence:
•Press the key 'OK' to turn on the display;
•Press again the key 'OK' to enter the menu;
•Scroll through the menu items using the 'DOWN ARROW' key until selecting 'Event Log';
•Press the key ‘OK' to get in the menu 'Events Buffer'.
The device is equipped with software seals required by the protocol UNI EN 12213.
7.2 Non metrological sealings
A non-metrological seal is provided on the MODUS lid to protect it from unauthorized opening. The figure
below shows an example of sealing:
Figure 15: Non-metrological hardware seal on the MODUS lid
This manual suits for next models
3
Table of contents
Other PIETRO FIORENTINI Measuring Instrument manuals
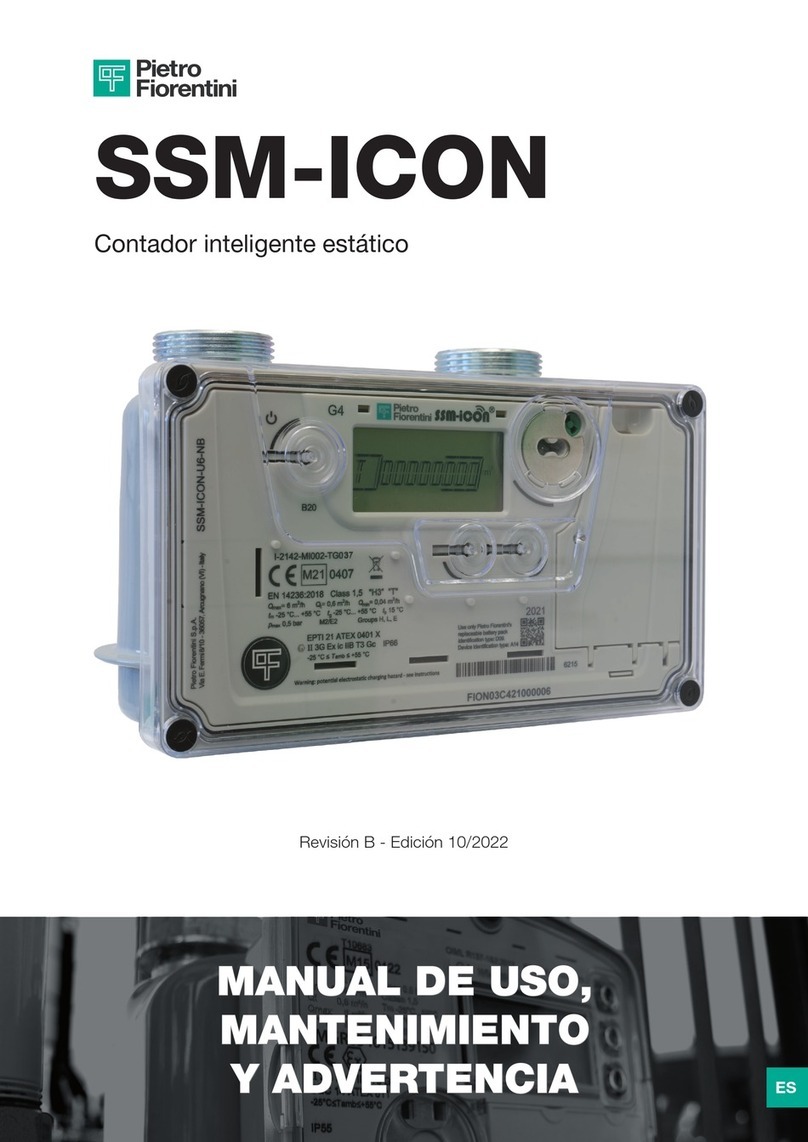
PIETRO FIORENTINI
PIETRO FIORENTINI SSM-ICON User manual
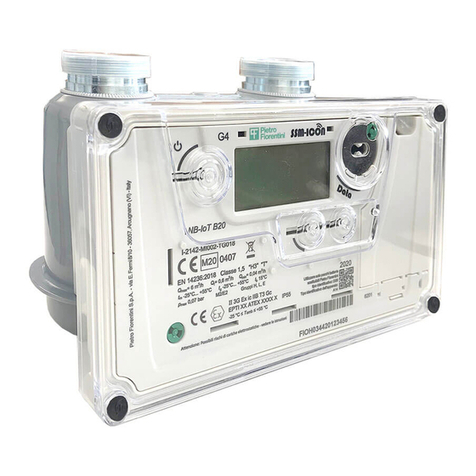
PIETRO FIORENTINI
PIETRO FIORENTINI SSM-ICON User manual
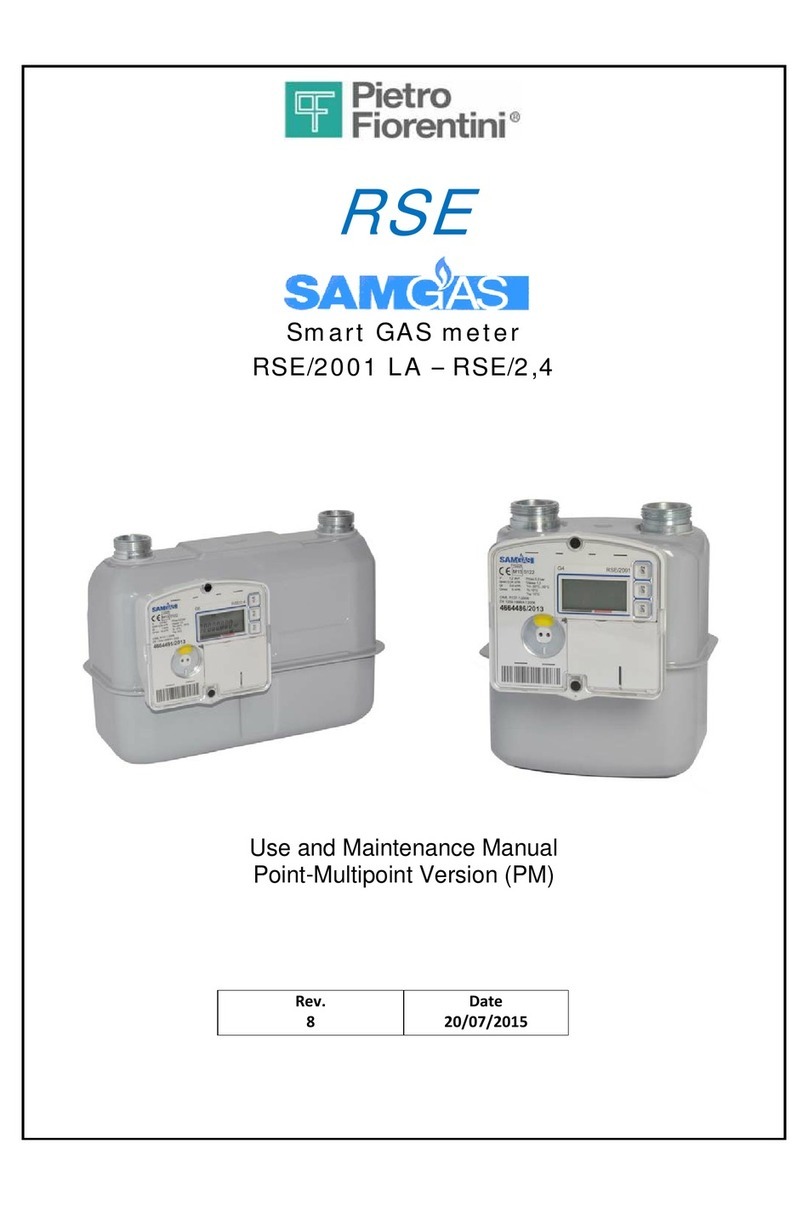
PIETRO FIORENTINI
PIETRO FIORENTINI RSE/2,4 User manual

PIETRO FIORENTINI
PIETRO FIORENTINI SSM-AQUO User manual

PIETRO FIORENTINI
PIETRO FIORENTINI M-LOG Plus User manual
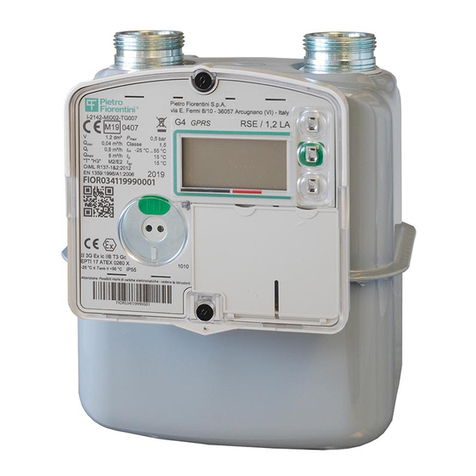
PIETRO FIORENTINI
PIETRO FIORENTINI RSE 1,2 LA N1 User manual
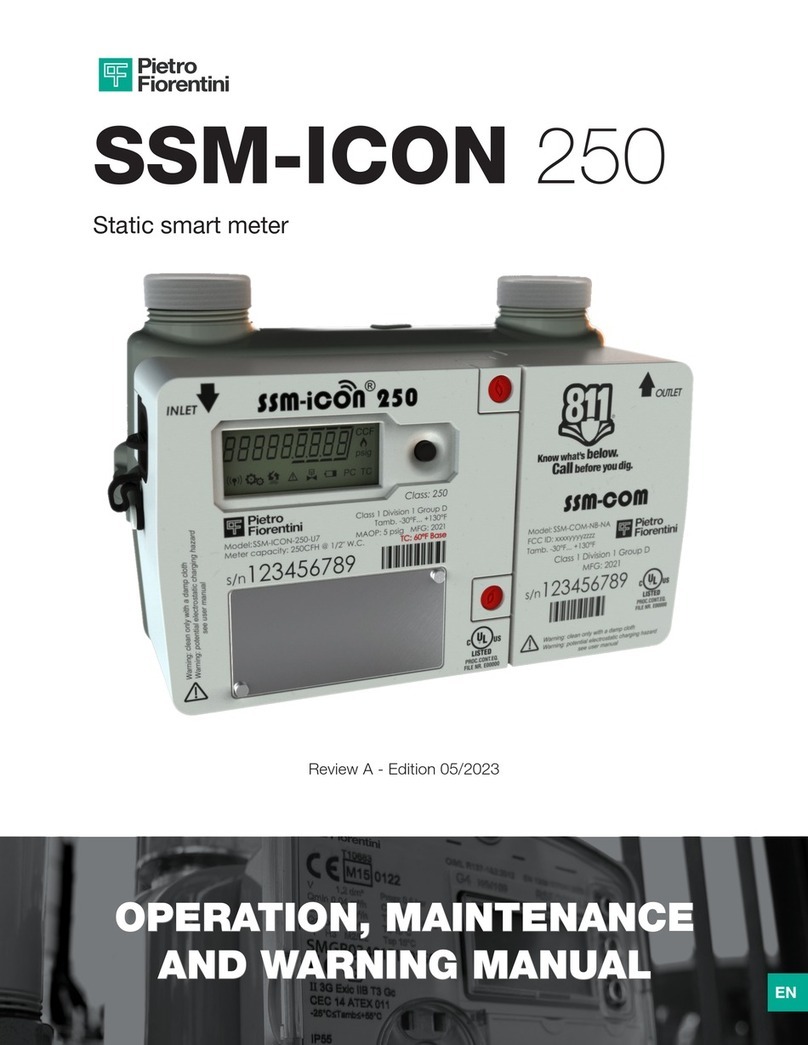
PIETRO FIORENTINI
PIETRO FIORENTINI SSM-ICON 250 User manual
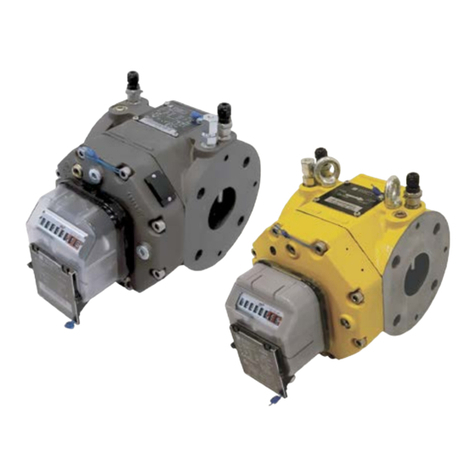
PIETRO FIORENTINI
PIETRO FIORENTINI IM-RM G10 User manual