Power Electronics V2 Series User manual

User's Manual
SOFTSTARTER

V2
ELECTRONICS SOFT-STARTER
User’s Manual V2MT01II Rev. I
POWER ELECTRONICS ESPAÑ
A
C/ Leonardo da Vinci, 24 - 26
46980 · PARQUE TECNOLÓGICO
PATERNA · VALENCIA · ESPAÑA
Tel. +34 96 136 65 57 · Fax. +34 96 131 82 01
Atención al Cliente: 902 40 20 70
www.power-electronics.com

2 | POWER ELECTRONICS User’s Manual V2 V2MT01II

ELECTRONIC SOFT-STARTER
IMPORTANT NOTES
RECEPTION
•V2 soft-starters are carefully tested and perfectly packed before leaving the factory.
ESPAÑOLDEUTSCH
•In case of transport damage, notify it to transport agency and to POWER ELECTRONICS
(+34 96 136 65 57), not later than 24hrs from delivery date.
UNPACKING
•Make sure model and serial number of the soft starter are the same in the box, delivery
note and unit.
•Position 1: V2 soft starter.
•Position 2: V2 Technical Manual.
SAFETY
•It is electrician's responsibility to ensure the configuration and installation of the V2
meets the requirements of any site specific, local and national electrical regulations.
•The V2 operates from HIGH VOLTAGE, HIGH ENERGY ELECTRICAL SUPPLIES.
Always isolate before servicing.
•Service only by qualified personnel. For any question or enquiry please contact POWER
ELECTRONICS Technical Department or with your local distributor.
•The V2 contains static sensitive printed circuit boards. Use static safe procedures when
handling these boards.
ENGLISH
POWER ELECTRONICS User’s Manual V2 V2MT01II | 3

REVISIONS
Date Revision Description
September 2006 I Installation regulations.
June 2005 H General update.
New power and control wiring.
March 2004 G Add new dimensions for 60 and 75A (IP54)
Change DT0048D (Page 11).
March 2003 F IP54 new range release.
October 2002 D Jumper 7: Default value Freewheel Stop.
July 2002 B PCB Change. 00016B.
Modify the jumper 9.
4 | POWER ELECTRONICS User’s Manual V2 V2MT01II

ELECTRONIC SOFT-STARTER
INDEX
1. MOUNTING AND WIRING................................................................................................... 6
ESPAÑOLDEUTSCH
1.1. Environmental conditions.
1.2. IEC Protection.
1.3. Mounting.
1.4. Power loss dissipation.
1.5. Power wiring.
1.6. Control wiring.
1.7. Checks before Commissioning.
2. ELECTRICAL SPECIFICATIONS........................................................................................ 11
3. DIMENSIONS AND STANDARD RATINGS........................................................................ 12
4. CONTROL INPUTS.............................................................................................................. 13
4.1. Control terminals.
4.2. Terminal descriptions.
5. LED INDICATIONS..............................................................................................................15
6. POWER PCB JUMPER CONFIGURATION........................................................................ 17
7. POTENTIOMETER COMMISSIONING................................................................................ 20
8. APPLICATIONS................................................................................................................... 24
9. DECLARATION OF CONFORMITY CE................................................................................ 26
ENGLISH
POWER ELECTRONICS User’s Manual V2 V2MT01II | 5

1. MOUNTING AND WIRING.
1.1 ENVIRONMENTAL CONDITIONS
1.1.1 IP00 MODEL
The maximum V2 ambient/working temperature is 40ºC. It is possible to be operated up to higher
temperature of 50ºC, by over sizing the soft starter 2% per extra degree.
Example: Motor 15kW, 380V, 30A
Working temperature 50ºC.
Soft-Starter required: At 40ºC the soft starter required should be a V2030 (30Amps), but at 50ºC the
soft starter should be oversized a 2% per extra ºC. Thus,
Temperature: 10°C; 2% x 10ºC means a 20% oversize:
I motor x 20% = 30 x 1.2 = 36 Amp
Then the soft starter required is a V2045 (@50ºC).
1.1.2 IP54 MODEL
The maximum V2 ambient/working temperature is 50ºC.
1.2 IEC PROTECTION
The V2 soft-starter ingress protection is IP00 and IP54.
1.3 MOUNTING
To improve heat dissipation, it is recommended to mount the soft starter over a metal plate.
Minimum safe 30mm side distance and 150mm top and button distance is to be kept between soft
starters.
Do not install V2 above any heat source, unless heat airflow is driven out of the cabinet.
DT0055
30mm
Avisosobre/subcarga
OL/UL w ar n ing
Überlast warnung
Sobrecarga
Overload
Überlast
Listo
Ready
Fertig
Marcha
Run
Läuft
Übertemperature
So br et e m p e ra t u ra
Overtemperature
Fa ll o gen er al
Generalfault
Fehler
Avisosobre/subcarga
OL/ULwa rning
Überlast warnung
Sobrecarga
Overload
Übe rl a s t
Lis to
Ready
Fertig
Marcha
Run
Läuft
Übertemperature
Sobretemperatura
Overtemperature
Fallogeneral
Generalfault
Fehler
Avis o s o br e/ s ub c ar ga
OL/ULwa rning
Überlast warnung
Sob r e c ar ga
Overl o ad
Überlast
Listo
Ready
Fertig
Marcha
Run
Läuft
Übertemperature
Sobretemperatura
Over tem per at u re
Fallogeneral
Generalfault
Fehler
150mm
Fig. 1: Vertical mounting.
6 | POWER ELECTRONICS User’s Manual V2 V2MT01II

ELECTRONIC SOFT-STARTER
1.3.1 IP00 MODEL
The V2 IP00 soft starter is designed to be mounted vertically inside an electrical cabinet with forced air-
cooling.
1.3.2 IP54 MODEL
IP54 Model can be mounted within a sealed cabinet if its internal temperature does not exceed 50ºC
and limiting the number of starts according to its technical specifications.
ESPAÑOLDEUTSCH
1.4 POWER LOSS DISSIPATION
1.4.1 IP00 MODEL
The V2 has a power loss of 3 watt per amp, this means that a V2045 has a power loss of 135 Watts at
full load.
1) Without forced cooling:
Practical example:
Ambient temperature is 30ºC.
Maximum working temperature of the V2 is 40ºC.
Power losses of the soft starter are 3 watts per amp at full load and 6 watts per amp during the start
(only with more than 6 starts per hour).
If the V2017 is going to be drawing constantly 15A, our power loss must be:
P= Im x Loss = 15 x 3 = 45 watts
This is the worst case assuming a duty cycle of 100% at full load (45W). You have also to take the
losses of switches, contactors, relays into account (20Watts).
Ploss= 45 + 20 = 65 watts
The heat transfer coefficient of metals and polyester must be known:
Polyester: 3.5 W / m²K°
Metal: 5.5 W / m²K°
The total surface required without forced cooling should be:
Area = Ploss/ k (Tr-Ta)
Area = 65 / 5.5 x (40 - 30) = 1.181m²
Chosen an 800 x 600 x 400 cabinet, the total area of dissipation is:
Area = Door + 2 (side) + Top Covers
Area = (0.8 x 0.6) + 2(0.8 x 0.4)+ (0.6 x 0.4) = 1.36m2
ENGLISH
The area of the cabinet is high enough to dissipate the total power loss.
NOTE: When you place cabinets in parallel, just take one side (for the total area) into account for thermal calculations.
2) With forced cooling:
The power loss dissipated is the same as without forced cooling, but now you have to calculate the air
flow required to get the desired differential temperature between the inside and the outside of the
cabinet.
We have a V2017 working at 30ºC ambient temperature. We want the air inside the cabinet less than
40ºC.
POWER ELECTRONICS User’s Manual V2 V2MT01II | 7

PLoss = Total power loss dissipated.
Tr = Maximum temperature inside the cabinet.
Ta = Ambient temperature.
Ø = Airflow required in m3/min.
Ø = PLoss / 20 x (Tr-Ta)
Ø = 65 / 20 x (40-30) 0.325 m3/min
NOTE: Using filters at the air intake/exhaust of the cabinet should protect the V2 from dust.
1.4.2 IP54 MODEL
IP54 range V2 do not need forced cooling as no heat is produced during nominal operation, only start
and stop heat is dissipated, thus number of starts is limited to 6 per hour and provided 50ºC as
maximum working temperature.
1.5 POWER WIRING
Most electrical wiring regulations require a mains isolator on solid-state equipment. The V2 soft-starter
falls to this category. This is to ensure there is an air break in the circuit, as semiconductors cannot be
relied upon to be safe isolation. There are many choices, the most common are using a magnethermic
protection with a trip coil, and the other is placing a contactor.
DT0045C
M
3~
U1 V1 W1
PE
UVW
L1 L2 L3
PE
N
L1
L2
L3
PE
PE
V2
LN.C.N
F1*
230Vac
PE 1
2
N
L1
L2
L3
PE
Q0
Fig. 2: V2 Power wiring configuration.
Note: Minimum recommended protection 1A for F1.
It is absolutely necessary that the installer guaranties the correct observance of the law and the regulations
that are in force in those countries or areas where this device is going to be installed.
8 | POWER ELECTRONICS User’s Manual V2 V2MT01II

ELECTRONIC SOFT-STARTER
Magnetic protection is required to protect the V2 soft-starter from damage due to a short circuit within
the V2 or on the output cabling or motor. When a faster protection was needed, it is recommended ultra
fast fuses. The fuses should be mounted as close to the V2 soft-starter as possible. Power factor
correction capacitors must not be connected after the fuses or on the output of the V2.
The V2 protects the motor with electronic overload sensing, so an external overload relay is not
necessary. If multiple motors are connected separate, overloads are required for each motor.
ESPAÑOLDEUTSCH
An isolator can be fitted after the V2 but is recommended for off load use only. A motor isolator is not
necessary for the operation of the V2 soft-starter but site standards or electrical wiring regulations may
require an isolator near the motor.
If a contactor is to be fitted, an output relay of the soft starter can energize it on receiving the start
signal.
1. 6 CONTROL WIRING
NOTE: Wiring distance.
Control wiring shouldn't run in parallel with power input or output cables to the motor. Space
at least 300mm away, and cross at right angles.
Control terminals:
The control terminals do need to be screened when running in parallel with power cables.
(Terminals 7 to 13)
Start/Stop wiring:
Wiring options with push buttons or selector (switch) according to Selection 4.2.
L
N
1234567 89101112
INSTANT
RELAY
FAULT
RELAY
13
DT0038E
230Vac
DIGITAL INPUTS
DIGITAL OUTPUTS
ENGLISH
Fig. 3: V2 Control Wiring.
POWER ELECTRONICS User’s Manual V2 V2MT01II | 9

1. 7 CHECKS BEFORE COMMISSIONING
1. Check for foreign objects in the V2 cabinet that may be left from installation.
2. Check the control board main supply (T1-T2, 230Vca +/-10%) is connected.
3. Check the mains connection is connected to terminals L1, L2, L3 and the motor is connected to
terminals U, V, W. Confirm the mains supply is within V2 specifications and motor nameplate matches
to V2 rated nameplate.
4. Check control wiring and ensure the installation is electrically safe and it is safe to run the motor.
10 | POWER ELECTRONICS User’s Manual V2 V2MT01II

ELECTRONIC SOFT-STARTER
2. ELECTRICAL SPECIFICATIONS.
INPUT
Input voltage: 230-400V(~3 phases), ±10%
ESPAÑOLDEUTSCH
Supply frequency: 47-62 Hz
Control Voltage: 230V +/-10%, others under demand
OUTPUT
Output voltage: 0 -100% Supply Voltage
Output frequency: 47-60 Hz
Efficiency (at full load): > 99%
ENVIRONMENTAL CONDITIONS
Ambient temperature: Operating: 0 to +40ºC
Storage: -10ºC to +70ºC
Altitude losses: >1000m 1% each 100m, maximum 3000m
Humidity: 95%@ 40ºC non-condensation
Protection degree: IP00
Cooling: Natural
PROTECTIONS Input phase loss
Starting current limit
Rotor locked
Motor overload (thermal model)
Underload
Phase unbalance
V2 PROTECTIONS General fault
V2 over temperature
SETTINGS Initial torque
Acceleration ramp
Deceleration ramp
Overload: 0.8 to 1.2 In
Overload curve
Underload: 0.2 to 0.6 In
Underload curve
Current limit: 1 to 5 In
NOTE: V2 IP54 number of starts per hour is limited to 5
OUTPUT SIGNALS 2 changeover relays (5A 230Vac non inductive)
· Fault: It opens in case of any fault condition
· Instantaneous: Its position changes when starting and stopping
LED’S INDICATIONS LED 1 Run
LED 2 Ready
ENGLISH
LED 3 Overload warning / Underload fault
LED 4 Overload Fault
LED 5 Over temperature
LED 6 General fault
POWER ELECTRONICS User’s Manual V2 V2MT01II | 11

3. DIMENSIONS AND STANDARD RATINGS.
IP00 – IP54 IP54
V2009 – V2075 V2060B – V2075B
Fig. 4: V2 Dimensions.
REFERENCE A 220V
KW
380V
KW
DIMENSIONS
(mm)
IP
PROTECTION
V2009 9 2.2 4 350x157x132 IP00
V2017 17 4 7,5 350x157x132 IP00
V2030 30 9 15 350x157x132 IP00
V2045 45 15 22 350x157x132 IP00
V2060* 60 18.5 30 350x157x132 IP00
V2075* 75 22 37 350x157x132 IP00
V2009B* 9 2.2 4 350x157x132 IP54
V2017B* 17 4 7,5 350x157x132 IP54
V2030B* 30 9 15 350x157x132 IP54
V2045B* 45 15 22 350x157x132 IP54
V2060B* 60 18.5 30 410x157x132 IP54
V2075B* 75 22 37 410x157x132 IP54
* All types signed with “*” do have an integrated BYPASS function. The Motor protection is operating
all the time.
Table 1: V2 standard ratings.
12 | POWER ELECTRONICS User’s Manual V2 V2MT01II

ELECTRONIC SOFT-STARTER
4. CONTROL INPUTS.
The next figure provides the electrical specification of all V2 control inputs. Each input is individually
described below.
ESPAÑOLDEUTSCH
4.1 C
ONTROL TERMINALS
Fig. 5: V2 Control Terminals.
4.2 TERMINAL DESCRIPTIONS
Control voltage terminals.
Input terminal for control board voltage supply (230V +/-10%). Other voltage rates are also available on
demand.
Between 1 and 2 there is an empty terminal with no se to secure electrical isolation.
Terminals 1-6 Output relays
Fault: It switches in case of any fault condition.
Instantaneous: It switches when starting/ stopping
Fig. 6: Output relay.
ct 5A at 230V.
L
N
1234567 89101112
INSTANT
RELAY
FAULT
RELAY
13
DT0038E
230Vac
DIGITAL INPUTS
DIGITAL OUTPUTS
u
.
A1
A2
A1
A2
DT0048F
INSTANT
RELAY
FAULT
RELAY
1
2
3
4
5
6
ENGLISH
NOTE: Maximum current per conta
POWER ELECTRONICS User’s Manual V2 V2MT01II | 13

Terminals 7-9: Inputs
Start/stop pushbutton configuration:
Fig. 7: 3-wire configuration.
NOTE: T minals 10 - 11 only reset.
Start/stop switch configuration:
Start/stop contact configuration.
OTE: Terminals 10 - 11
Terminal 10-11: Inputs
Remote r set configuration
Fig. 9: Reset configuration.
OTE: If re is not usin
Terminal 12-13: Inputs
Start pul pushbutton configuration.
For variable load applications (different material mixing, etc.), where sometimes a higher torque is
required, torque pulse pushbutton inputs are provided.
er
Fig. 8:
N
stop/reset.
s
e
Nset g terminals 10 and 11 must be linked.
s
se
a
Fig. 10: Start pulse configuration.
DT0049C
Stop
Start
7
8
9
7
8
Start/Stop
9
DT0050C
10
11
DT0051C
Reset
12
13
DT0052C
lseStart Pu
14 | POWER ELECTRONICS User’s Manual V2 V2MT01II

ELECTRONIC SOFT-STARTER
ESPAÑOLDEUTSCH
ENGLISH
5. LEDS INDICATIONS.
DT0039E
1xIn 5xIn
MIN MAX0.2xIn 0.6xInMIN MAX
0.8xIn 1.2xIn2S. 15S.MIN MAX
PAR INICIAL
INIT. TORQUE
INITIAL. STARTM.
ACELER.
ACC.
HOCHLAUF
DECELER.
DEC.
RÜCKLAUF
SOBRECARGA
OVERLOAD
ÜBERLAST
CURVA SOBRC.
O/L CURVE
ÜBERLASTKURVE
SUBCARG.
UNDERLOAD
UNTERLAST
TIEMPO SUB.
U/L TIME
UNTERLASTZEIT
LIMITE I.
I. LIMIT
STROMBEGRENZ
MIN MAX
LED1
LED2
LED3
LED4
LED5
LED6
Sobrecarga
Sobretemperatura
Fallo General
Overload
Overtemperature
General Fault
Überlast
Übertemperature
Fehler
Marcha
A
U
viso sobrecarga/
Fallo subcarga
Ready
Run
OL warning/
L fault
Fertig
Läuft
Überlast Warnung/
Unterlast Fehler
Listo
Fig. 11: Led and potentiometer PCB
LED 1 READY STATUS
It shows 230V is applied to control board.
LED 2 RUN STATUS
It blinks during acceleration and deceleration ramp.
It is steadily on after acceleration ramp when running at nominal current.
LED 3 OVERLOAD WARNING & UNDERLOAD FAULT
Blinking light: UNDERLOAD FAULT
Description Motor Underload.
Possible Cause Motor working with no load.
POWER ELECTRONICS User’s Manual V2 V2MT01II | 15

Wrong
Action In case
setting of Underload conditions.
of pump application, check there is no air inside the pipe network and
that the pump suction is not obstructed.
Increase Underload potentiometer.
Steady light: OVERLOAD WARNING
Description Motor overload warning before the soft-starter will trip on overload fault.
LED 4 OVERLOAD FAULT
Description Adjusted motor overload has reached an unacceptable level.
Trip is produced during start:
Possible Cause Motor overload due to mechanical or load problems and wrong settings.
Action Check mechanical conditions.
Check there is not a power input supply voltage drop lower than a 10%.
Increase acceleration ramp (high inertia applications).
Increase Overload curve potentiometer.
Increase current limit.
Trip is produced at nominal speed:
Possible Cause Wrong Overload potentiometer setting or load conditions change.
Action Check working conditions of motor.
Check load.
Increases overload potentiometer.
LED 5 V2 OVER TEMPERATURE
Description Heat sink too hot (>85ºC).
Sense level (> 85°C).
Possible Cause Insufficient cooling.
Fan failure.
Ambient temperature too high, >40ºC for IP00 model and >50ºC for IP54 model.
The actual current is higher than the nominal.
Action Check the ambient temperature during normal operation doesn't exceed 40ºC
for IP00 model and 50ºC for IP54.
Check that actual motor current is the same or smaller than the V2 nominal current.
LED 6 GENERAL FAULT
Description Phase or PCB fault.
Possible Cause Phase loss.
Phase unbalance.
Thyristor fau
Action Check supply, all cables, mo r.
sts, call to POWER ELECTRONICS or an authorized distributor.
lt.
to
If the problem persi
16 | POWER ELECTRONICS User’s Manual V2 V2MT01II

ELECTRONIC SOFT-STARTER
ESPAÑOLDEUTSCH
ENGLISH
ER CB JUM
6. POW PER CONFIGURATION.P
T tarte be damaged by setting the jumpers dhe Soft-s r could uring operation. For safety reasons, the
mpers are located underneath the potentiometer and LED PCB. This PCB must be removed only
umper drawing.
R'S UNCTIO
JP1-JP6 MOTOR SUPPLY VOLTAGE
Description Rated (Nameplate) Motor Voltage
Default Value 400V (No jumper required)
Function Adjust nominal motor voltage.
Adjust Position 1: 400V
Position 2: 230V (to introduce 6 jumpers according to drawing).
Add or remove 6 jumpers (2 per phase) according to input voltage at the soft
starter input. Make sure this value is related to rated (Nameplate) motor voltage.
ju
when control and power supply is off.
DT0043B
JP1 - JP6
JP7
JP8
JP9
B JFig. 12: Power PC
J F N
UMPE
POWER ELECTRONICS User’s Manual V2 V2MT01II | 17

Fig. 13: JP1-JP6: Motor supply voltage jumper selection.
JP7 FREEWHEEL STOP
Description Enable/disable deceleration ramp.
Default value Position 1: Freewheel stop
Function Set the type of stop required. The stop could be controlled through a ramp down
voltage or uncontrolled where the stop depends on the load torque (freewheel
stop).
Adjust Position 1(default): Freewheel stop. Deceleration ramp disabled.
Position 2: Deceleration ramp is enabled.
op selection jumper.
lue
djust
Position 1: 400V supply Position 2: 230V supply
No jumper With jumper
DT0047D
JP7
Fig. 14: JP7: Freewheel st
JP8 SUPPLY FREQUENCY
n
Descriptio Supply frequency
va
Default Position 1: 50Hz
unction
F Set the mains frequency.
A Where the mains frequency is known as 50Hz, leave as default. Where the
mains frequency is 60Hz set jumper to Position 2.
Position 1: Freewheel stop Position 2: Deceleration ramp
ble
ena
DT0044F
18 | POWER ELECTRONICS User’s Manual V2 V2MT01II

ELECTRONIC SOFT-STARTER
ESPAÑOLDEUTSCH
ENGLISH
escription rent.
efault Value Position 1: Underload protection disabled.
unction
Adjust
rrent selection jumper.
osition 2: 60Hz supply
JP8
Position 1: 50Hz supply P
Fig. 15: JP8: Supply frequency selection jumper.
DT0046D
JP9 UNDERLOAD PROTECTION
D Underload cur
D
F Set underload protection.
Position 1 (default): Underload protection is disabled.
Position 2: Underload protection is enabled.
JP9
1: Desable u/l protection Position 2: Enable u/l protection
Position
DT0057D
Fig. 16: JP9: Underload cu
POWER ELECTRONICS User’s Manual V2 V2MT01II | 19
This manual suits for next models
1
Table of contents
Other Power Electronics Controllers manuals
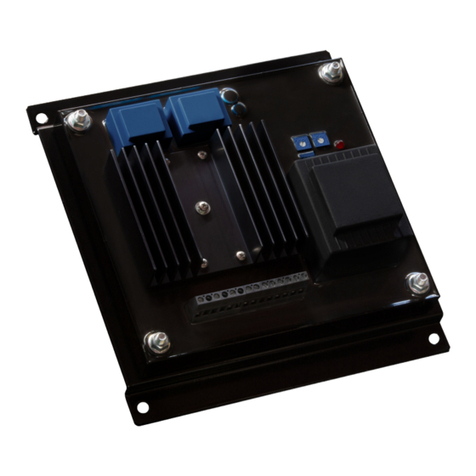
Power Electronics
Power Electronics TAIYO ASC-62-4 User manual
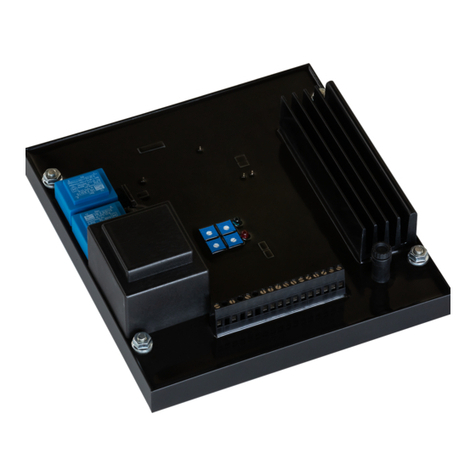
Power Electronics
Power Electronics NISHISHIBA VZKUP-4B COMPATIBLE User manual
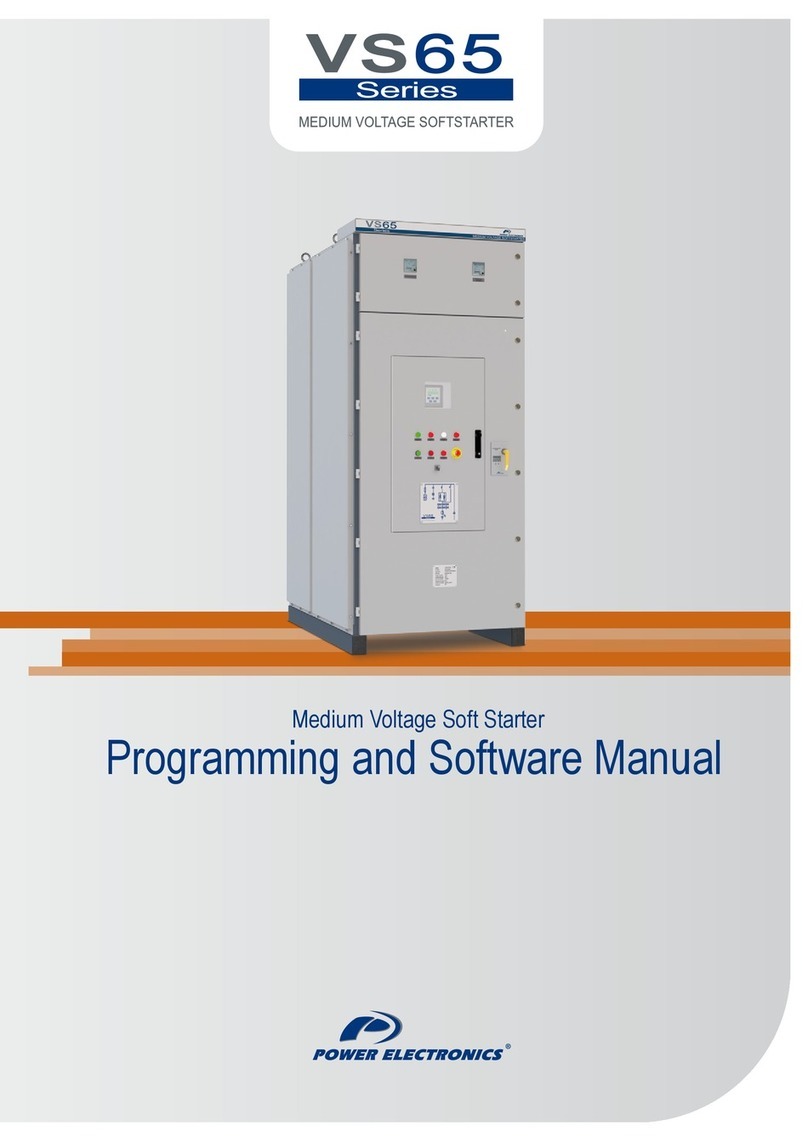
Power Electronics
Power Electronics VS65 Series Mounting instructions
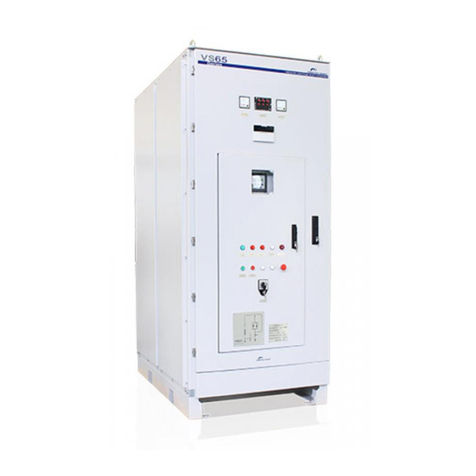
Power Electronics
Power Electronics VS65 Series User manual
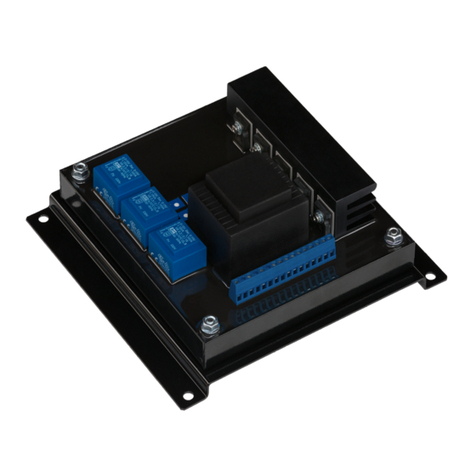
Power Electronics
Power Electronics TAIYO ASC 12-4Z3 User manual
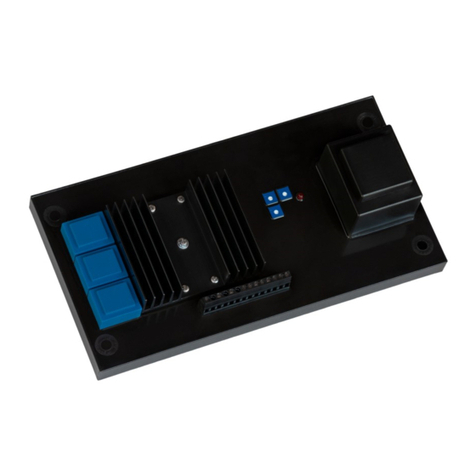
Power Electronics
Power Electronics NISHISHIBA VZRAB-1S User manual
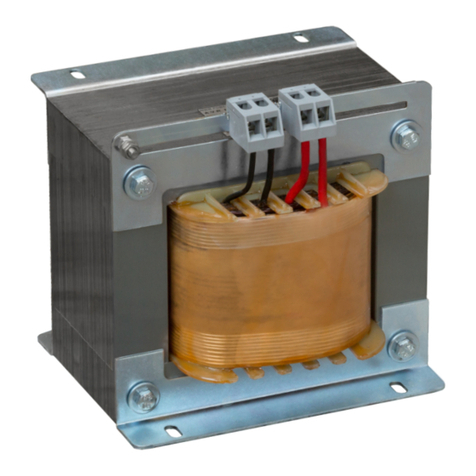
Power Electronics
Power Electronics SE-4LH15 User manual
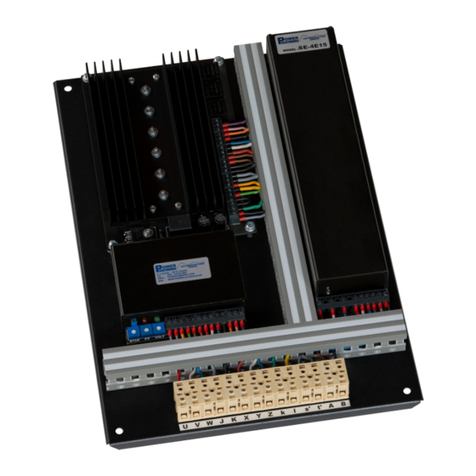
Power Electronics
Power Electronics SE-4E15 User manual
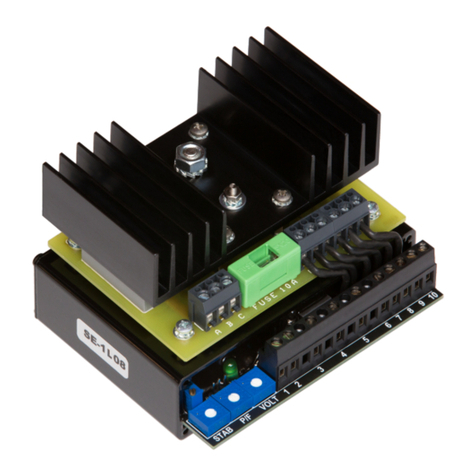
Power Electronics
Power Electronics SE-1L08 User manual
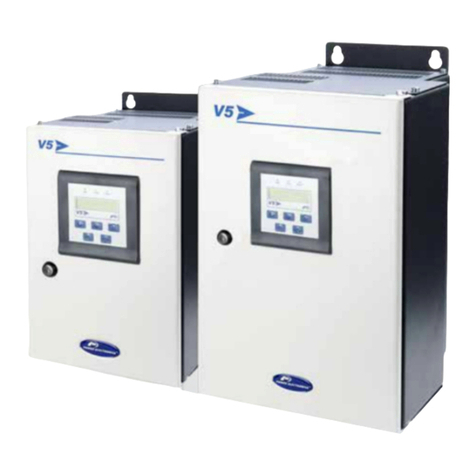
Power Electronics
Power Electronics V5 Series Parts list manual