Promag TR515 User manual

TR515 Time Recorder
V1.00

Attention! Firmware Management mode (FMM)
The TR515 has two different modes of operation. Normal mode provides
regular device functionality. Firmware Management mode (FMM) is provided for
internal firmware checkup and upgrades (see Section 5).
The Normal mode is entered by powering the TR515 up while not pressing
the IN button. Switching the TR515 on while holding the IN button or both IN
and OUT buttons down forces the unit into the FMM. The FMM mode of
operation cannot be exited other than by switching the TR515 off and back on
again.
Contents
Attention! Firmware Management mode (FMM)..................
Contents...............................................................................
1. Installing the TR515.......................................................1
2. Using the TR515............................................................7
3. Communications protocol ..............................................8
4. Registers......................................................................16
5. Firmware Management mode......................................20
6. Test mode....................................................................23
Appendix A. Possible Errors ............................................25
Appendix B. Interface connector pin assignment.............25
Appendix C. Cable...........................................................26
Appendix D. Specifications ..............................................28
Appendix E. Ordering Information....................................28
Appendix F. Software Installation …………………………29

TR515 User’s Manual
1
1. Installing the TR515
DC Jack Comm. Port Magnetic/ barcode
head on this side
IN button & LEDOUT button & LED
Comm. Status Bell Control
Wall-mount and desktop operation
The TR515 can be used either as a wall-mount (default, see Figure above)
or desktop device. Machine needs to be rotated 180 degrees when used on a
desk. For this reason, the TR515 comes with two different LED plates (with their
artworks rotated 180 degrees with respect to each other). Machine’s LED can
also display time and other data in a “normal” (wall-mount), or desktop fashion.
There is an orientation setting provided that allows you to select display mode
(see Section 4).
1. RS-232/485 Interface Versions
The TR515 supports two different interfaces: RS232 for single-terminal
communications, and RS485 for multi-terminal communications. Only one
TR515 can be attached to the PC’s serial port using the RS232 interface. Up to
32 units can be interconnected using the multi-terminal RS485
communications.`
RS232 arrangement is simple: just plug the RS232 cable (supplied) into the
TR515 and connect the other side to the PC’s serial port.
Using RS485 requires a special adaptor- CON485 (must be purchased
separately). CON485 is a “smart” RS232!RS485 converter that allows for
higher data transfer rates between the PC and TR515s.

TR515 User’s Manual
2
The RS485 network is of “bus” type- all TR515s are connected in parallel on
a so-called twisted pair bus. The most suitable cable for the bus is the one
normally used for Ethernet communications (twisted pair Cat. III or V). You only
need to use one twisted pair of wires inside the cable.
Note: depending on the cable type, up to 4 twisted pairs may be available, it
doesn’t matter which one you use, just make sure that you are using both wires
of the same wire pair.
To connect the TR515 to the twisted pair bus, cut the RS232 cable supplied
with each TR515 and locate 2 wires inside: Orange and Green. Attach each
wire to one of the wires on the twisted pair bus. Mind the polarity! Orange and
Green wires cannot be switched. It is recommended that you keep the length of
each “bus stem” (i.e. the cable that is used to attach a certain TR515 to the bus)
as short as possible, ideally under 10 cm (see the drawing below).
120
<10cm
485-
Blue
CON485
485- Blue
#4
#3
485+
Green
485+ Green
One side of the bus must be attached to the CON485: Orange connects to
pin #3, Green connects to pin #4.
Another side of the twisted pair bus must be properly terminated. This is
especially important for long buses. Standard termination resistor value is 120
Ohm.
Note: It is not always necessary to have the termination resistor. It
really depends on the actual wiring and connection circumstances.
Before testing the network, make sure that all Terminals and the CON485
are powered and that the CON485’s baudrate selector is in the 19200 position
(selector must be set prior to powering the CON485 up).
TR515RX’s interface connector pin assignment can be found in Appendix B.

TR515 User’s Manual
3
2. Ethernet Interface Versions
The TR515EX is designed to attach directly to the RJ45 10BaseT Ethernet
connector. Standard magnetics circuitry (YCL part 20F001N) has been included
onboard to provide a “glueless” interface to the Ethernet network.
Most Ethernet installations require cables of substantial and variable length,
so you will probably need to make your own cables. For testing purposes
PROMAG supplies two kinds of Ethernet cables: device-to-hub (WAS-1499) for
connections through a standard Ethernet hub, and device-to-device (WAS-1498)
for connections without a hub (i.e. directly from one Ethernet device to another).
TR515 to HUB TR515 to PC
HUB
WAS-1499 WAS-1498
Summary of Status LED signals
In the Serial Programming mode Green and Red LEDs are blinking (Green-Red-Green...)

TR515 User’s Manual
4
Red Led Green Led
POWER
JACK
BELL
CONNECTOR
10BaseT Port
TR515 CONNECTOR AND STATUS
TR515EX’s interface connector pin assignment can be found in Appendix B.
3. Wireless Interface Versions
The TR515WX designed to operate in the 433MHz ISM (Industrial, Scientific
and Medical) frequency band. It features Frequency Shift Keying (FSK)
modulation and demodulation capability.
You must purchase a Master station RDL401A to connect with PC
Wireless Communication
RDL401A

TR515 User’s Manual
5
Understanding machine numbers
For single-terminal RS232 communications, you needn’t specify your
TR515’s machine number.
For multi-terminal RS485 communications you must make sure that all
Terminals on the network have unique machines numbers. Machine number is
a network address that uniquely identifies the Terminal on the network. Having
two different Terminals on the network set up to the same machine number will
result in the inability to communicate with both Terminals.
Machine number can be in the 0 to 255 range (00-FF Hex). 0 is a universal
machine number- any Terminal responds to it regardless of this Terminal’s
actual machine number setting. Machine number of 0 can be used for RS232
communications- you only have a single Terminal in this case, so you can
address it with the universal number.
For multi-terminal RS485 communications, you’ll need to assign a unique
(and non-zero!) machine number to each Terminal on the network.
Assigning machine numbers
The TR515 offers a fast and convenient way of assigning machine numbers
in the range from 0 to 10. To assign a new machine number:
• Power the Terminal down (unplug the power cord)
• Press and hold the OUT button
• Power the Terminal up while continuing to hold down the OUT button
• After 2-3 seconds, the Terminal will beep and display its current
machine number, for example:
• While still keeping the OUT button pressed, push the IN button
(several times if necessary) to change the machine number to the
desired value
• When the desired machine number is displayed, release the OUT
button- the Terminal will resume normal operation
This method allows you to set the numbers in the 0-10 range only (which
would actually cover most of the actual installation requirements). If you need to
set the machine number to, say, 25, then you will have to follow this procedure:
• Connect the TR515 to the PC using the RS232 cable
• Launch the TR515 Control Center software and select the Terminal

TR515 User’s Manual
6
#0 (i.e. use the universal machine number to address the Terminal)
• Use the “Set M#” button to set the new machine number for this
Terminal
• Unplug the RS232 cable and put the Terminal back on the RS485
network.
Note: machine number is displayed briefly at the Terminal power-up (even if
you don’t push the OUT button).
Bell relay
The TR515 features a built-in bell relay. The relay is capable of controlling a
low-power external bell. A daily bell schedule of up to 32 different bell times can
be defined.
NCCOMNO
Relay connector is located under the metal back plate. Figure above shows
connector position and pin assignment. Both Normally Closed (N.C.) and
Normally Opened (N.O.) contacts are provided.
Locking event selection (IN or OUT)
By default, the TR515 allows the User to choose the desired event (IN or
OUT) prior to reading the ID-card. There is a setting provided that allows event
selection to be fixed either at IN or OUT (see Section 4). This arrangement may
be desirable in case several TR515s are used, with some machines installed at
the entrance and serving for registering IN events, and some machines installed
at the exit and serving for OUT registration only. Fixing the event prevents the
User from choosing an alternative event at the moment of reading ID-card.

TR515 User’s Manual
7
2. Using the TR515
Clocking in and out
To register an event (IN or OUT), push the appropriate button and read your
ID-card. For the TR515R (RFID version), the card is read by bringing it close to
the reader (< 8 cm). For the TR515M, TR515B, and TR515F (Magnetic, Visible
Barcode and IR Barcode respectively), the card is read by swiping it in either
direction along the reader slot. For the machine orientation shown on figure of
page 3, magnetic (barcode) stripe of the ID-card must face downwards.
Note: the TR515 can be programmed to fix event selection to IN or OUT
only- in this case event selection won’t work!
The last four digits of the ID-cards ID-code are displayed on the LED when
the ID-card is read. Four dashes are displayed in case of read error (only
applicable to the TR515M):
Memory full status
When the database memory is full, new records cannot be added. Reading
an ID-card will produce a long beep and a “FULL” message:
Error conditions
The TR515 can detect and notify you of a number of different error conditions.
Please refer to Appendix A for complete list of all possible errors.
Normal operation of the TR515 is suspended upon encountering an error
condition other than “card read error”. New records cannot be added to the
database in this situation. Communications with the TR515 from the PC side is
still possible, however. This gives you an opportunity to access the TR515
online and attempt to correct the problem.

TR515 User’s Manual
8
3. Communications protocol
The TR515 communications protocol is based on the GNET protocol
specification. Communications parameters are 19200-8-N-1.
Communications between the TR515 and the PC takes place in the form of
commands sent by the PC and replies from the TR515. Commands and replies
are packets of data. Each packet begins with an STX (02H) character and ends
with CR (0DH) character. Selected commands and replies include a checksum
field as an additional safety measure. All characters between the STX and the
CR characters must be in the 20H...7FH range.
The STX character of a command packets is followed by a one-character
command code. The STX character of a reply packet is followed by a one-
character reply code. Both command and reply packets may contain some
relevant data after the command (reply) character:
STX C1 C2 CR
02H Cmd/Rpl
code Data (if any) Checksum* 0DH
*Checksum field is not included into certain commands and replies
All available commands are described later in this Section. Of reply codes,
only two are possible: ‘A’ (completed successfully) and ‘N’ (some error was
encountered). Depending on the command given to the TR515, reply packets
with reply code ‘A’ may contain some data (as shown on the Figure above).
Reply packets with the reply code ‘N’ always contain a 2-digit error code that
can be used to analyze the source of a problem.
The checksum is an 8-bit sum of all characters between the STX and CR,
represented as a 2-character HEX string. For an example packet below, the
checksum is calculated as follows. The data part of the packet is “A1XYZ”. The
sum of these character codes is: 41H+31H+58H+59H+5AH=17DH. Eight least
significant bits contain 7DH. The string representation of this value is “7D” (i.e. 2
ASCII characters- ‘7’ and ‘D’).
STX A 1 X Y Z 7 D CR
02H 41H 31H 58H 59H 5AH 37H 44H 0DH
Packet portion the checksum is calculated on Checksum

TR515 User’s Manual
9
Table below lists all possible error codes:
04 Illegal (invalid) command (command code or data is wrong)
06 Record number is out of range (requested record doesn’t exist)
07 Command failed (hardware problem or invalid internal data)
Summarized below are all supported commands. Command characters are
found in the “CC” column, their corresponding ASCII codes- in “Hex”. “CS” lists
commands that require the checksum in the command packet (“C”) or reply
packet (“R”). “Error code” column lists errors that may result from each
command execution:
CS Errors
C.
C. Hex Description C R 4 6 7
‘D’ 44H Select designated terminal Note 1
‘I’ 49H Set new machine number + +
‘Y’ 59H Get machine number +
‘S’ 53H Set date/time + +
‘T’ 54H Get date/time +
‘V’ 56H Get firmware version
‘R’ 52H Initialize the terminal
‘C’ 43H Set register (see next table) + +
‘B’ 42H Get register (see next table) + + +
‘N’ 4EH Get number of records + +
‘G’ 47H Get specified record + + + +
‘E’ 45H Initialize the database
‘M’ 4DH Prepare for database recovery
‘Z’ 5AH Perform self-test** Note 2
Note 1. D-command never returns error message even if the data supplied in the
command packet is incorrect. Invalid command packet makes it impossible to determine
which terminal is being addressed and, therefore, which one should reply with an error code.
Note 2. Z-command is never replied to.
Follows is the detailed command description. Command and reply packets
are shown without STX, Checksum and CR characters.

TR515 User’s Manual
10
Select designated terminal (‘D’, 44H)
Possible error codes: none
Command DNN
Reply ANN,TR515
NN is a machine (terminal) number in Hex form (00H-FFH), 00H is a
“universal” number (see below for details).
‘D’ is a special command. It is used to select a particular TR515 terminal.
All terminals power up in a “deselected” state. Each terminal ignores all
incoming commands until it receives the D-command whose machine number is
either equal to the machine number of this terminal, or 00. After that, the
terminal switches into “selected” state and responds to all subsequent
commands until new D-command with a different machine number is issued.
Thus, the D-command should always be used to initiate communications
between the host and the designated TR515.
Note: the TR515 never returns any error codes in reply to this command.
This holds true for both “Illegal command” error and “Command failed” error.
The former is not responded to, because when there is some discrepancy in the
format of the D-command issued by the Host (which can only be in the Machine
Number field), no particular terminal can be “sure” that it is being addressed.
Therefore, no terminal on the network assumes responsibility for sending a
reply. “Command failed” situation can only arise because of incorrect machine
number setting value in the TR515 memory. In this case, the terminal will be
unable to compare its internal machine number with the one supplied in the D-
command. Hence, the Terminal will not be able to make sure that it is being
addressed.
Since 00 is a universal machine number, it works with any terminal. Use it
only when you have a single terminal connected to the host. Universal machine
number also comes handy during initial terminal setup (to assign a unique
machine number to the terminal prior to placing it on a multi-terminal network).
The terminal replies with its actual machine number even if you address it
using 00. The only exception is when the terminal is unable to retrieve its own
machine number due to some internal malfunction. Reply will contain 00 instead
of an actual machine number in this case.

TR515 User’s Manual
11
Set new machine number (‘I’, 49H)
Possible error codes: 04, 07
Command INN
Reply A
NN- machine number in Hex form (00H-FFH), 00 should never be used on a
multi-terminal network because this is a universal number (see D-command
description for details).
This command is used to assign a new machine number to the terminal.
Machine numbers provide a way to distinguish between the terminals on a
multi-terminal network. See D-command description for more details.
Get machine number (‘Y’, 59H)
Possible error codes: 07
Command Y
Reply ANN
NN- machine number in Hex form (00H-FFH)
This command is used to retrieve the terminal’s machine number. Machine
numbers provide a way to distinguish between the terminals on a multi-terminal
network. See D-command description for more details.
Set date/time (‘S’, 53H)
Possible error codes: 04, 07
Command SYYYYMMDDhhmmss
Reply A
YYYY-year, MM- month, DD-date, hh-hour, mm-minutes, ss- seconds
This command is used to set the TR515’s internal clock. Date/time supplied
must be valid. Incorrect data (like 31st of February) will be rejected (error 04).

TR515 User’s Manual
12
Get date/time (‘T’, 54H)
Possible error codes: 07
Command T
Reply AYYYYMMDDhhmmss
YYYY-year, MM- month, DD-date, hh-hour, mm-minutes, ss- seconds
This command is used to get the TR515’s current date and time.
Get firmware version (‘V’, 56H)
Possible error codes: none
Command V
Reply Aversion_string
Version_string length is guaranteed to not exceed 61 character, all
character codes are guaranteed to be in the 20H…7FH range
This command can be used to verify the TR515’s internal firmware version.
Although version string can be any ASCII string, the following format is adopted:
“VX.X cc…….c”, where “VX.X” is a version number (i.e. “V1.0”) and “cc…c”
is a comment string. Comment string is separated from the version number by a
single space character. Version number will never have any spaces in it.
Initialize the terminal (‘R’, 52H)
Possible error codes: none
Command R
Reply A
This command is used to initialize the TR515. Initialization takes place on
the next power-up, not immediately. Upon initialization, all setting values are
restored to their factory defaults. TR515’s internal date and time are also
checked and, if contained garbage, initialized to 1999/01/01 and 00:00:00
respectively. The database data is not erased, this must be done using the E-
command.

TR515 User’s Manual
13
Set register (‘C’, 43H)
Possible error codes: 04, 07
Command CRR,reg_data
Reply A
RR- register number (00H…FFH); reg_data- the data for the register to be
set
This command is used to set one of the TR515 “registers”. Registers are
actually functioning parameters (Settings). Complete description of all available
registers can be found in Section 4.
Get register (‘B’, 42H)
Possible error codes: 04, 07
Command BRR
Reply Areg_datacc
RR- register number (00H…FFH), reg_data is the data stored in the register,
cc- checksum
This command is used to retrieve the data contained in the designated
“register”. Registers are actually functioning parameters (settings). Complete
description of all available registers can be found in Section 4.
Get number of records (‘N’, 4EH)
Possible error codes: 07
Command N
Reply ANNNNcc
NNNN- number of records in Hex form; cc- checksum
This command can be used to retrieve the number of records currently
found in the database. Leading zeroes are not omitted, so reply string length is
always the same.

TR515 User’s Manual
14
Get specified record (‘G’, 47H)
Possible error codes: 04, 06, 07
Command GNNNN
Reply ANNNN,ccc…c,E,YYYY/MM/DD,hh:mm:sscc
NNNN- record number (starting from 0000) in Hex form, ccc…c- ID-code, E-
event (0: OUT, 1: IN), YYYY- year, MM-month, DD-date, hh-hour, mm- minute,
ss- second, cc- checksum
This command is used to retrieve the database record with a specified
number. Record number must be supplied in Hex format, leading zeroes must
be preserved or error 04 will be returned. Record numbers start from 0000.
Specifying record number beyond N-1 (where N is the number of records in the
database returned by the N-command) will cause error 06.
Returned data string contains the record number, ID-code of the ID-card
that was used to create this record, event code (i.e. which button was pressed),
and the date and time of record creation.
The TR515 verifies all database records before sending them out to the PC.
This is done because the FLASH memory may actually contain a garbage data.
There is a special M-command that lets you initialize the database in such a
way that it appears to be 100% full (you can “recover” entire database memory
contents then). Naturally, some database records may turn out to contain
invalid data.
Database record validity is verified on a field-by-field basis. Should the field
turn out to be invalid, its contents are substituted for a “safe” default data:
• ID-code. If ID-code turns out to contain illegal characters (i.e. with
codes outside of 20H-7FH range), then these characters are
substituted for “_”. If ID-code length is outside of valid margins (<1 or
>40) then entire ID-code is substituted for the following code:
“0000000000” (ten ‘0’ characters)
• Date. If the date is invalid (i.e. December, 32nd) then default date
(1999/01/01) is used
• Time. If the time is invalid (i.e. 24:00:00) then default time is used
• Event. if Event code exceeds 1, then this field is substituted for “0”.

TR515 User’s Manual
15
Initialize the database (‘E’, 45H)
Possible error codes: none
Command E
Reply A
Executing this commands initializes the database. This command can be
used to delete all database data and restore the database functionality in case
of database malfunction.
E-command doesn’t really delete the data itself- just some internal database
housekeeping is initialized. The data can still be (partially) recovered using an
M-command.
Prepare for database recovery (‘M’, 4DH)
Possible error codes: none
Command M
Reply A
This command alters the database in such a way that it appears to be 100%
full. The M-command, therefore, can be used for data recovery purposes. For
example, if E-command is executed accidentally while TR515 had some useful
data inside, then M-command can be used to download entire database
memory contents. Naturally, this recovered data may not be consistent. Some
records may contain “garbage” data (more on this in G-command description),
newer records may overlap older ones, etc.
Perform self-test (‘Z’, 5AH)
Possible error codes: none
Command Z
Reply This command is never replied to
This command is used to force the TR515 into a special Test mode. No
reply is issued by the TR515 upon receiving this command. Details of TR515’s

TR515 User’s Manual
16
operation in the Test mode are provided in Section 6. Note, that Test mode
destroys database memory contents in such a way that the data cannot be
recovered even with the M-command.
.
4. Registers
The TR515 features a number of programmable “registers”. Basically,
registers are the TR515’s functioning parameters (Settings). Registers can be
written to using the C-command, and read from using the B-command (see
Section 3 for details).
Table below lists all available registers:
00H LED display mode (0: wall-mount, 1:desktop)
01H Bell duration in seconds (00H-FFH)
02H-21H Bell table, times (total of 32 registers)
22H-41H Bell table, enable/disable (total of 32 registers)
42H Event selection mode, free (IN or OUT)/IN only/OUT only
LED display mode (register 00)
Set Possible error codes: 04, 07
Command C00,MM
Reply A
Get Possible error codes: 04, 07
Command B00
Reply AMMcc
MM- display mode (00: wall-mount operation, 01: desktop operation), cc-
checksum
This register is used to set the LED display mode. Because TR515 can be
used both as a wall-mount and as a desktop device, the LED data must be
displayed in either orientation. Setting register to 00 (default) adjusts LED
picture for wall-mount operation. Setting the register to 01 rotates the image so
that it appears correctly when operating as a desktop device. Note: the mode

TR515 User’s Manual
17
parameter must be supplied as a 2-digit number, i.e. “00” or “01”. Supplying just
one digit will generate error 04.

TR515 User’s Manual
18
Bell duration (register 01)
Set Possible error codes: 04, 07
Command C01,DD
Reply A
Get Possible error codes: 04, 07
Command B01
Reply ADDcc
DD- Bell duration in seconds, in Hex format (00H-FFH), cc- checksum
The TR515 features a relay that can be used for external bell control. Bell
schedule can be programmed using bell table registers (02H-21H, 22H-41H).
This register specifies the number of seconds the bell will be activated for each
time it is enabled.
Note: the DD parameter must always be a 2-digit number (i.e. “3A”).
Supplying just one digit will generate error 04.
Bell table, times
Set Possible error codes:04, 07
Command CRR,hhmm
Reply A
Get Possible error codes: 04, 07
Command BRR
Reply Ahhmmcc
RR- register number in Hex form (02-21H), hh- hour, mm-minutes, cc-
checksum
The TR515 features a relay that can be used for external bell control. Up to
32 different ring times can be specified for which the bell will be activated. Each
bell table entry consists of two fields: time field (set through these 32 registers)
and a corresponding enable/disable field (set through registers 22H-41H).
Table of contents
Other Promag Measuring Instrument manuals
Popular Measuring Instrument manuals by other brands
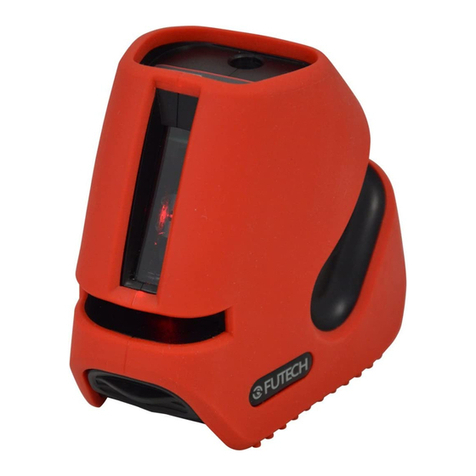
Futech
Futech TERACROSS manual

MKS
MKS Ophir Nova user manual
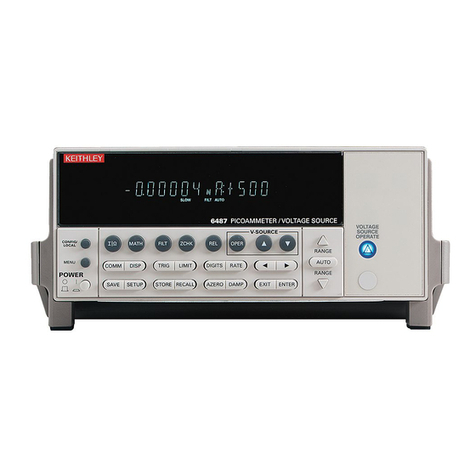
Electro-Tech systems
Electro-Tech systems 863 Basic operating instructions

POSITECTOR
POSITECTOR Powder Checker instructions
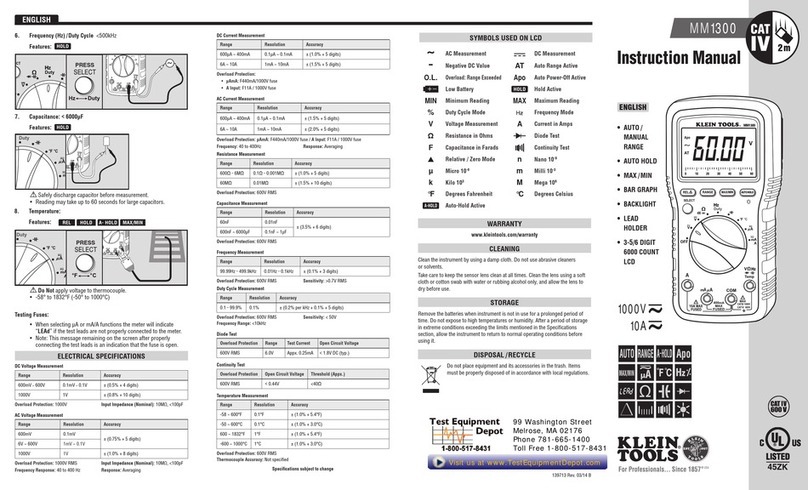
Klein Tools
Klein Tools MM1300 instruction manual
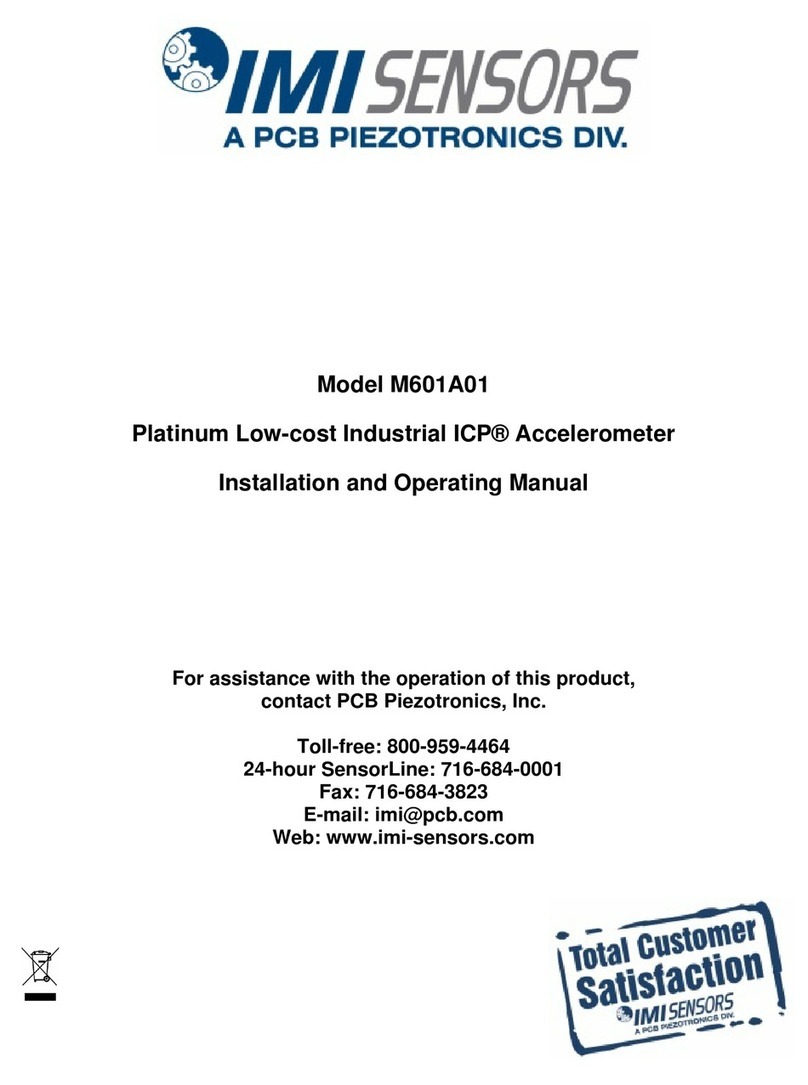
PCB Piezotronics
PCB Piezotronics IMI SENSORS ICP M601A01 Installation and operating manual