QB Robotics SoftHand Industry User manual

Please read carefully these instructions before use. Do not discard: keep for future
reference.
USER GUIDE

www.qbrobotics.com
This page is intentionally left blank

www.qbrobotics.com
Dear customer,
Thank you for purchasing our product.
The present document provides information at best of our knowledge at the time of
publication. This document could present differences from the product and it is subject
to changes without notice: the latest version is available on our webpage
www.qbrobotics.com.
qbrobotics s.r.l. does not assume any responsibility for errors or omissions.
In no case qbrobotics s.r.l. will be responsible for any loss, problems or damages to
persons or property arising from the use of this document.
The qb® logo and qbrobotics® are registered trademarks of qbrobotics s.r.l. The
indications of (R) are omitted.
Manifacturer:
qbrobotics s.r.l.
via Giuntini 13, 56023 Navacchio (PI), Italia
Release 1.0 15/07/2019

1
15 luglio 2019
Summary
1Preface.................................................................................................................... 2
1.1 Using this document ......................................................................................... 2
1.2 Symbols and conventions ................................................................................. 2
2Safety ...................................................................................................................... 3
2.1 Intended use ..................................................................................................... 3
2.2 Safety instructions ............................................................................................ 3
2.3 EC Directives on product safety........................................................................ 4
2.4 Environmental conditions................................................................................. 5
2.5 Environmental safety ........................................................................................ 5
2.6 Personnel qualification ..................................................................................... 6
3Description.............................................................................................................. 6
4Assembly................................................................................................................. 7
4.1 SoftHand Industry mounting ............................................................................ 7
4.2 Cable connections........................................................................................... 10
4.2.1 Set of cables ........................................................................................... 10
4.2.2 Driver ports ............................................................................................ 13
4.2.3 Connection sequence............................................................................. 14
4.2.4 Digital I/Os cable “EC_CBL_26_CRMP24_WIRE_050” (OPTIONAL)........ 17
5Installation ............................................................................................................ 19
6Working with qb SoftHand Industry ..................................................................... 21
7qb SoftHand Industry technical data .................................................................... 24
7.1 Fingers workspace .......................................................................................... 28
7.2 Adjustable wrist .............................................................................................. 29
8Maintenance and warranty .................................................................................. 31
9Appendix............................................................................................................... 33
9.1 Troubleshooting.............................................................................................. 33
10 Certifications......................................................................................................... 34

2
15 luglio 2019
1Preface
1.1 Using this document
The documentation must always be complete and in a perfectly readable
state.
Keep the document accessible to the operating and, if necessary,
maintenance personnel at all times.
Pass the document to any subsequent owner or user of the product.
1.2 Symbols and conventions
WARNING: identifies information about practice or
circumstances that can lead to damages on the
device and to personal injury.
Attentions help you identify a hazard, avoid a
hazard, and recognize the consequence.
Courier text
Identifies file paths, file names and sw functions.

3
15 luglio 2019
2Safety
2.1 Intended use
The product design is intended for grasping objects in the weight range from
1 to 2000 g.
Fragile, sharp or sharp-edged objects shall not be grasped.
Objects having the ratio between the biggest and the smallest dimensions
≥8 and the main dimension greater than 300 mm shall not be grasped.
The product is intended for installation on robotic arms: the safety features
are stablished only for use as described in this document.
The safety of the product cannot be guaranteed in case of inappropriate use.
One, single, inappropriate use can result in a permanent damage to the
safety of the product.
2.2 Safety instructions
WARNING:
•Check that all the content is intact after removing
it from the packaging.
•The device can be used only by specially trained
staff.
•Disconnect the power supply before installation,
cleaning or maintenance operations.
•Make sure that no residual energy remains in the
system.
•Always operate the product within the
specifications defined.
•Keep away from children and pets. Always set off
or unplug when not in use.
•Never use aerosol products, petroleum-based
lubricants or other flammable products on or near
the end-effector.

4
15 luglio 2019
•Do not use any damaged power cable, plug, or
loose outlet. It may cause damages to the product
or injury to people.
•Do not touch electrical components to avoid
damages due to electrostatic charges.
•Make sure the end-effector is properly and
securely bolted in place and cabled.
•Do not use if damaged or defective. Do not
disassemble.
•Do not insert any objects between moving parts
of the fingers.
•Keep head and face outside the reach of the end-
effector.
•Do not wear loose clothing or jewelry when
working with the end-effector.
•Disrespect of these precautions can affect safety
of the device.
2.3 EC Directives on product safety
•The following EC directives on product safety must be observed.
•If the product is being used outside the UE, international, national
and regional directives must be also observed.
Machinery Directive (2006/42/EC)
Because of their small size, no serious threats to life or physical condition
can normally be expected from electric miniature drivers. Therefore, the
Machinery Directive does not apply to our products. The products described
here are not “incomplete machines”, so installation instructions are not
normally issued by qbrobotics.
Low Voltage Directive (2014/35/EU)
The Low Voltage Directive applies for all electrical equipment with a nominal
voltage of 75 to 1500 V DC and 50 to 1000 V AC. The products described in
this device manual do not fall within the scope of this directive, since they
are intended for lower voltages.

5
15 luglio 2019
2.4 Environmental conditions
Wrong environmental and operating conditions can lead to injuries, product
damages and/or significant reduction to the product’s life.
WARNING:
Any use or application deviating from intended use is
deemed to be impermissible misuse. This includes, but is not
limited to:
•Use before performing a risk assessment;
•Use outside the permissible operational conditions
and specifications;
•Use in not low-dust environment;
•Use in places with high temperature or humidity;
•Use in wet places;
•Use in potentially explosive atmospheres;
•Use in medical and life critical applications;
•Use close to a human’s head, face and eye area;
•Use as a climbing aid;
•Use in outdoor applications.
2.5 Environmental safety
The qb SoftHand Industry must be disposed of in accordance with the
applicable national laws, regulations and standards.
All the components of this product have been chosen in accordance with the
EU RoHS directive 2011/65/EU: they are produced with restricted use of
hazardous substances to protect the environment.
Observe national registration requirements for importers according to EU
WEEE Directive 2012/19/EU.

6
15 luglio 2019
2.6 Personnel qualification
If the personnel working with the product is not sufficiently qualified, may
occur serious injuries and damage.
•Observe the national safety regulations and rules and general safety
instructions.
•Before working with the product, the personnel must have read and
understood the complete assembly and operating manual.
•All work may only be performed by qualified personnel.
3Description
qb SoftHand Industry is an anthropomorphic robotic hand based on soft-
robotics technology, flexible, adaptable and able to interact with the
surrounding environment, objects and humans while limiting the risk of
hurting the operators, spoiling the products to be handled, and damaging
the robot itself.
The qb SoftHand is adaptable and can grasp different objects without any
change in the control action, showing an unparalleled level of simplicity and
flexibility.
Thanks to its soft nature the hand by qbrobotics exploits the principles of
synergies in a simple and intrinsically intelligent design that is not only safe
in unexpected human-robot interaction, but also adaptable to grasp
different objects without any change in the control action.
The combination of these innovations results in a flexible prehensile device
that can grasp a wide variety of objects. The single-motor actuation makes
the hand plug-and-play and simple-to-control (one single motor requires
one single control signal to close and open the whole hand) and affordable.

7
15 luglio 2019
4Assembly
The qb SoftHand Industry Kit allows you to connect the device to your robot
arm.
The kit consists of:
•N.1 qb Softhand Industry 24V;
•N.1 external driver “G-DCWHI2.5/100EES”;
•N.1 ethernet cable “EC_CBL_UTP_6_RJ45_BLK_050”;
•N.1 power cable “EC_CBL_22_02_L50_RR_200”;
•N.1 STO cable “EC_CBL_26_CRMP3_WIRE_050”;
•N.1 power line communication bridge with main cable of 3m
“EC_CBL_26_M8FA8_CRIMP_100”;
•N.1 USB pen drive:
oManual;
oDatasheet;
•N.1 cylindrical pin EN ISO 8734 A d6x10 h6;
•N.4 metrical screws EN ISO 10642 M6x10;
•N.1 Allen hex key.
4.1 SoftHand Industry mounting
Use only the screws provided within the package. Longer screws could
damage the robot or the hand. To assemble the hand on the robot arm,
please follow the instructions of Table 4-1:
#
instructions
1
Unlock by a single turn two
knobs (1) and rotate the
robot’s wrist (2).

8
15 luglio 2019
#
instructions
2
Keep (2) as shown in figure,
then tight the two knobs
(1).
3
Insert (3) into the 6 mm
hole on the wrist.
4
Center (2) on the wrist
diameter 63mm,
5
Fasten (2) to the UR wrist by
tightening the four screws
(4).
You need the 4mm
Allen wrench.

9
15 luglio 2019
#
instructions
6
Unlock by one turn two
knobs (1) and rotate the
device until the desired
position.
7
Fix the device by tightening
the 2 knobs (1).
Table 4-1 Installation guidelines of the SoftHand Industry on robot arm. Referring to the
balloons in the pictures: (1) n.2 knobs M4; (2) SoftHand Industry flange ISO9409-1-50-4-M6;
(3) n.1 cylindrical pin EN ISO 8734 A d6x10 h6; (4) n.4 metrical screws EN ISO 10642 M6x12.

10
15 luglio 2019
4.2 Cable connections
To connect the hand to the external driver, please use the provided set of
cables.
4.2.1 Set of cables
The provided cables are:
•Ethernet cable “EC_CBL_UTP_6_RJ45_BLK_050”
Figure 4-1 Ethernet cable.
•Power cable “EC_CBL_22_02_L50_RR_200”
Figure 4-2 Power cable to supply the external driver.

11
15 luglio 2019
•STO cable “EC_CBL_26_CRMP3_WIRE_050”
This cable has a screw terminal block to let the user connect the STO (Safe
Torque Off).
Figure 4-3 Cables with connectors and terminal block to connect the STO.
Figure 4-4 Locking system for external pin.
You can connect the Safe Torque Off in two ways:
Conn. A) Connection to Robot control box. In this way the STO is
managed by the control box and its safety protocols.
Conn. B) External power connection. In this way you can keep the
motor enabled and you have to turn off the external power source
to disable it.

12
15 luglio 2019
•Main cable “EC_CBL_26_M8FA8_CRIMP_100”
The pinning of the female M8 connector, 8 poles, is given below:
Figure 4-5 Pinning and contacts of the M8 8 pin female connector.
Referring to Figure 4-5, the connections are the following:
Pin n.
Wire color
Purpose
1
White
SSI 5 VDC
2
Brown
SSI GND
3
Green
SSI clock +
4
Yellow
SSI clock -
5
Gray
SSI data +
6
Pink
SSI data -
7
Blue
motor phase 1
8
Red
motor phase 2
Table 4-2 Signals and power connections.

13
15 luglio 2019
4.2.2 Driver ports
Figure 4-6 shows the provided external driver with the indication of the
ports; Table 4-3 External Driver ports.indicates the characteristics of each
port.
Figure 4-6 External driver.
Port n.
Type
Function
Pins
1
2.54 mm Pitch Molex
STO
3
2
2.54 mm Pitch Molex
Feedback port C and I/O
24
3
2.54 mm Pitch Molex
Feedback port B
8
4
2.54 mm Pitch Molex
Feedback port A
12
5
Phoenix 3.81 mm Pitch ‘HC’
Auxiliary supply input
2
6
Phoenix 5 mm Pitch ‘HC’
Main Power
3
7
Phoenix 5 mm Pitch ‘HC’
Motor phases
4
8
USB Device Mini-B
USB
5
9
EtherCAT in
RJ-45
8
10
EtherCAT out
RJ-45
8
Table 4-3 External Driver ports.

14
15 luglio 2019
4.2.3 Connection sequence
#
instructions
1
Assembly the motor phases of
the main cable to the 4-pin
connector for the port 7; block
the cables turning clockwise
the two screws.
Make sure to connect the red
cable to the M2 pin and the
blue cable to the M3 pin.
WARNING:
Pay attention to connect
cables in the correct
way.
You need the flathead
screwdriver.
2
Assembly the main cable to
the external driver.
Connect the 12-pin Molex
plug to the port 4and the 4-
pin connector to the port 7.
3
Connect the STO plug to the
external driver port 1.

15
15 luglio 2019
#
instructions
4
Assembly the power cable to
the 3-pin connector for the
port 6; block the cables
turning clockwise the two
screws.
Make sure to connect the
brown cable to the VP+ pin
and the white cable to the PR
pin.
WARNING:
Pay attention to connect
cables in the correct
way.
You need the flathead
screwdriver.
5
Connect the power cable to
the port 6, by the 3-pin
connector.
Driver nominal voltage 24V
(min 12V, max 95V)
6
Connect the Ethernet cable to
the port 9.

16
15 luglio 2019
#
instructions
7
Insert the M8 connector (4) of
the main cable into the
receptacle on the hand wrist
flange. Lock the M8 connector
by manually tightening its
threaded ring on the body of
the receptacle (max
tightening torque= 0.2 Nm).
WARNING:
Be careful to insert the
connector in the right
direction;
Do not rotate the M8
connector when
inserted into the
receptacle;
Minimum curve radius
of the cable (4) = 51mm.
Table 4-4 Assembly sequence of the cables.
Table 4-5 Connection layout for the external driver.

17
15 luglio 2019
4.2.4 Digital I/Os cable “EC_CBL_26_CRMP24_WIRE_050” (OPTIONAL)
This cable has a screw terminal block to let the user connect the 13 pins for
the digital I/Os communication. In the other end there is a Molex 24 pins
connector, for the external driver’s port 2. Figure 4-3 Cables with connectors
and terminal block to connect the STOshows the pin-out of the cable.
Figure 4-7 Cable with connectors and terminal block to connect the digital I/OS pins.
The digital inputs are listed below:
IN_GND: digital inputs ground;
IN1: fully opening at maximum speed;
IN2: fully closing at maximum speed and force;
IN3: fully closing at 25% of speed and maximum force;
IN4: fully closing at maximum speed and 75% of force;
IN5: fully closing at 25% of speed and 75% of force;
IN6: correct termination procedure to use before switching off.
All these states are activated by a pulse of a few tenths of a second on the
respective 24VDC digital input (with respect to the IN_GND which acts as a
ground for digital inputs). If the input remains high, the others can still be
activated, but the high one will not activate until it returns to "0" (0 VDC)
and then again to "1" (24 VDC).
Table of contents
Other QB Robotics Robotics manuals
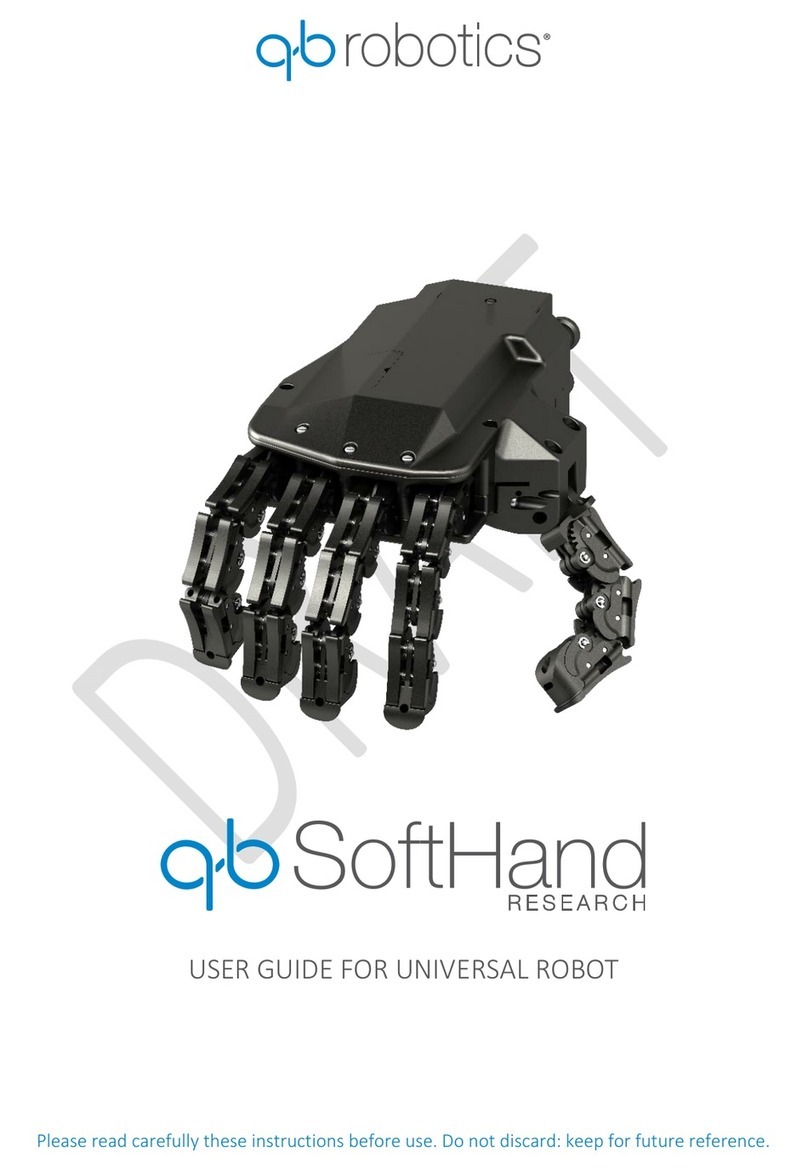
QB Robotics
QB Robotics qb SoftHand RESEARCH User manual
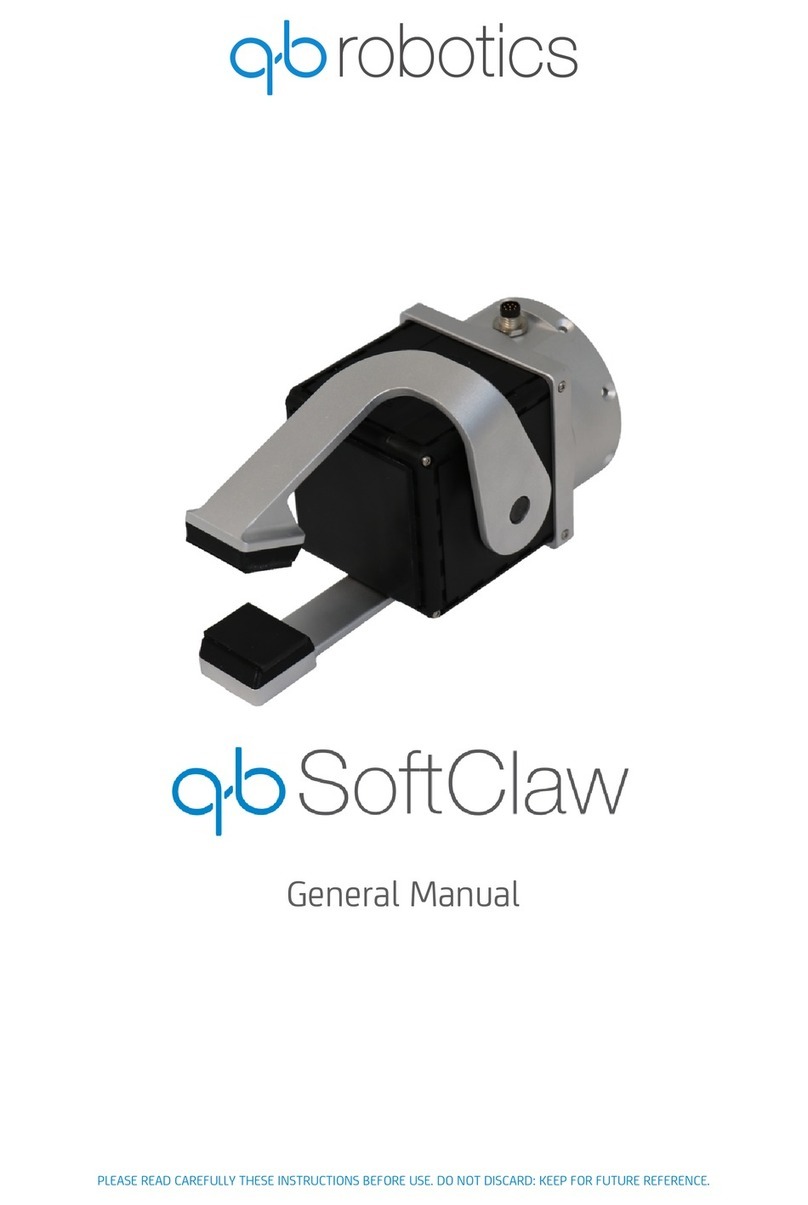
QB Robotics
QB Robotics qb SoftClaw Configuration guide
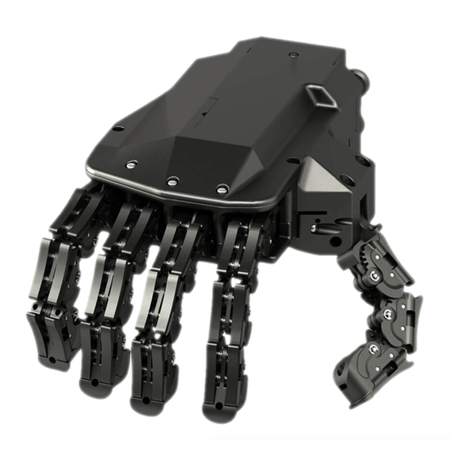
QB Robotics
QB Robotics SoftHand Research User manual
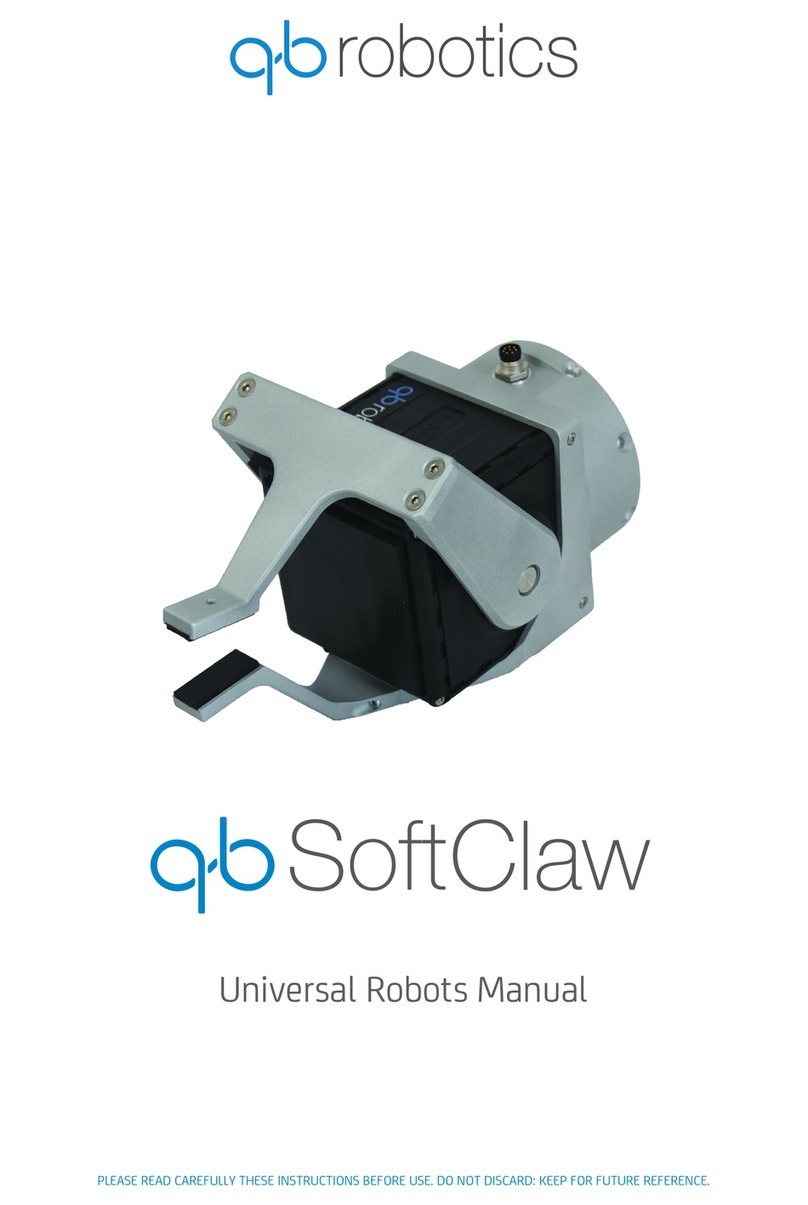
QB Robotics
QB Robotics SoftClaw User manual
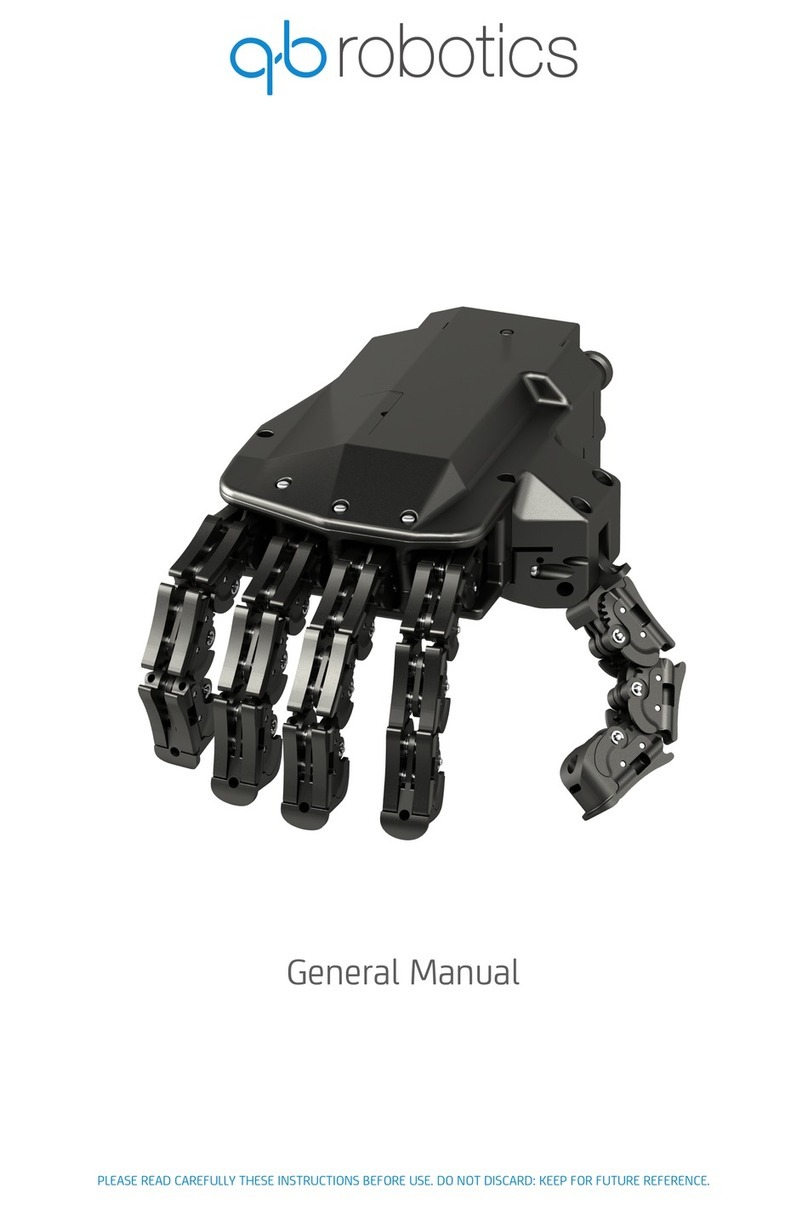
QB Robotics
QB Robotics N.1 qb SoftHand Research 24 V Configuration guide
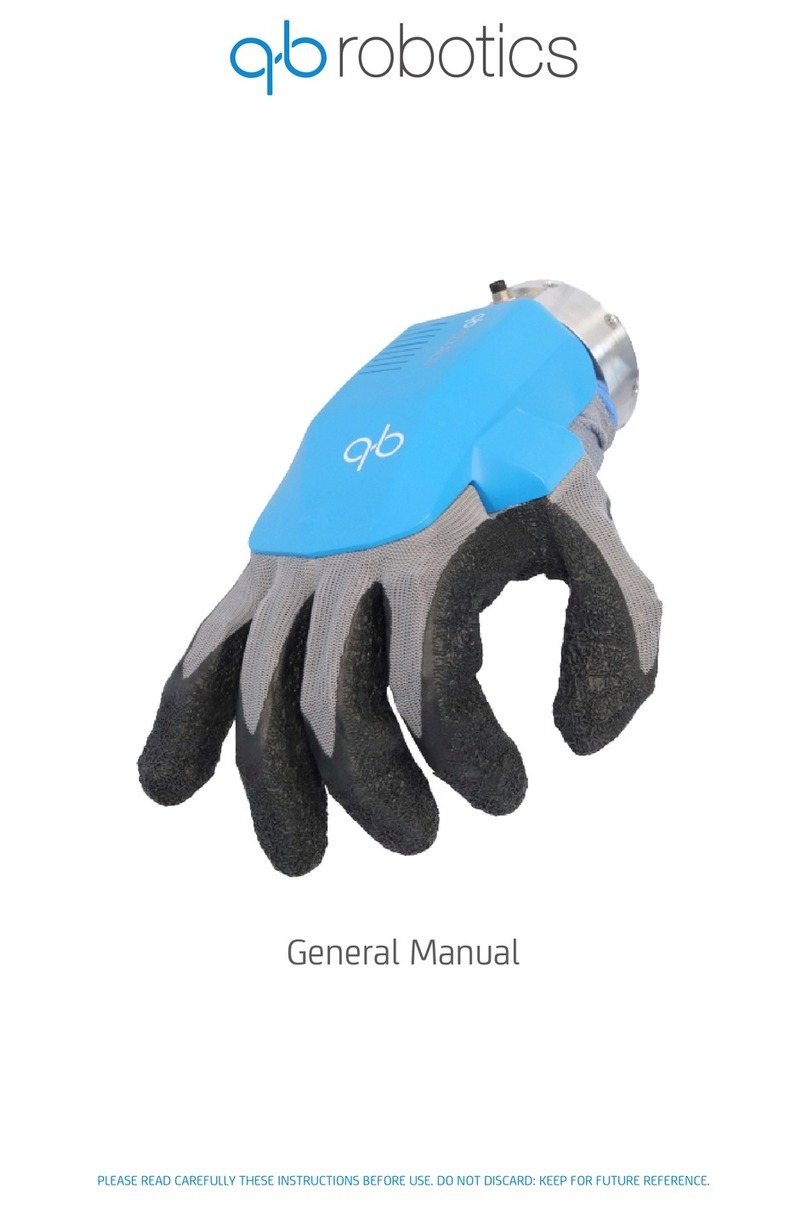
QB Robotics
QB Robotics SoftHand2 Research Configuration guide
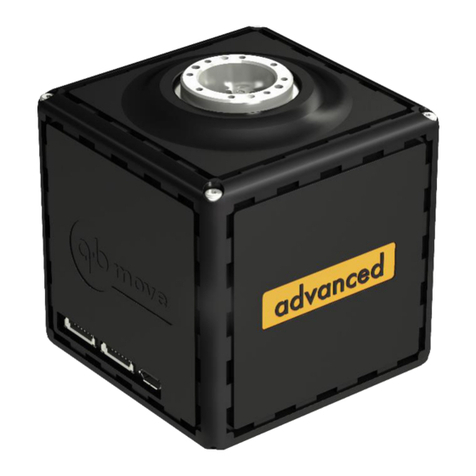
QB Robotics
QB Robotics qbmove Advanced Kit User manual
Popular Robotics manuals by other brands
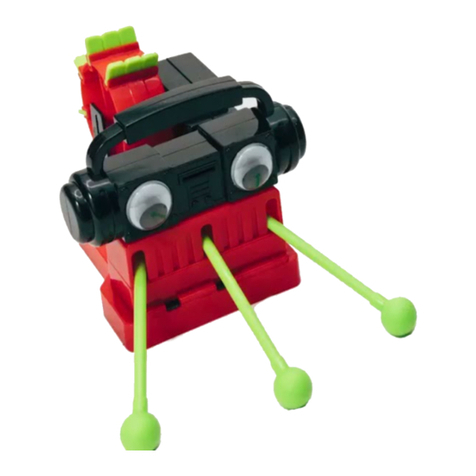
4M
4M KidzRobotix Drummer Robot instruction manual
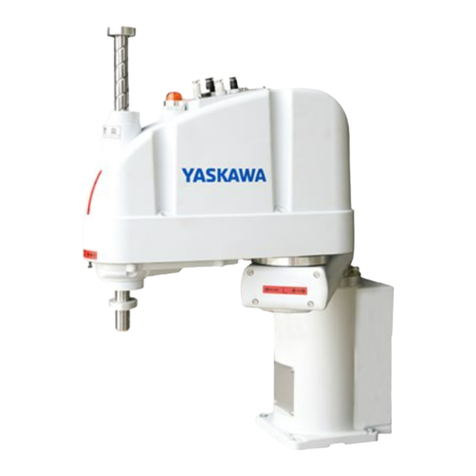
YASKAWA
YASKAWA MOTOMAN MYS450L Operating and maintenance instructions

Artec
Artec Robo 2.0 Fire Fighter manual
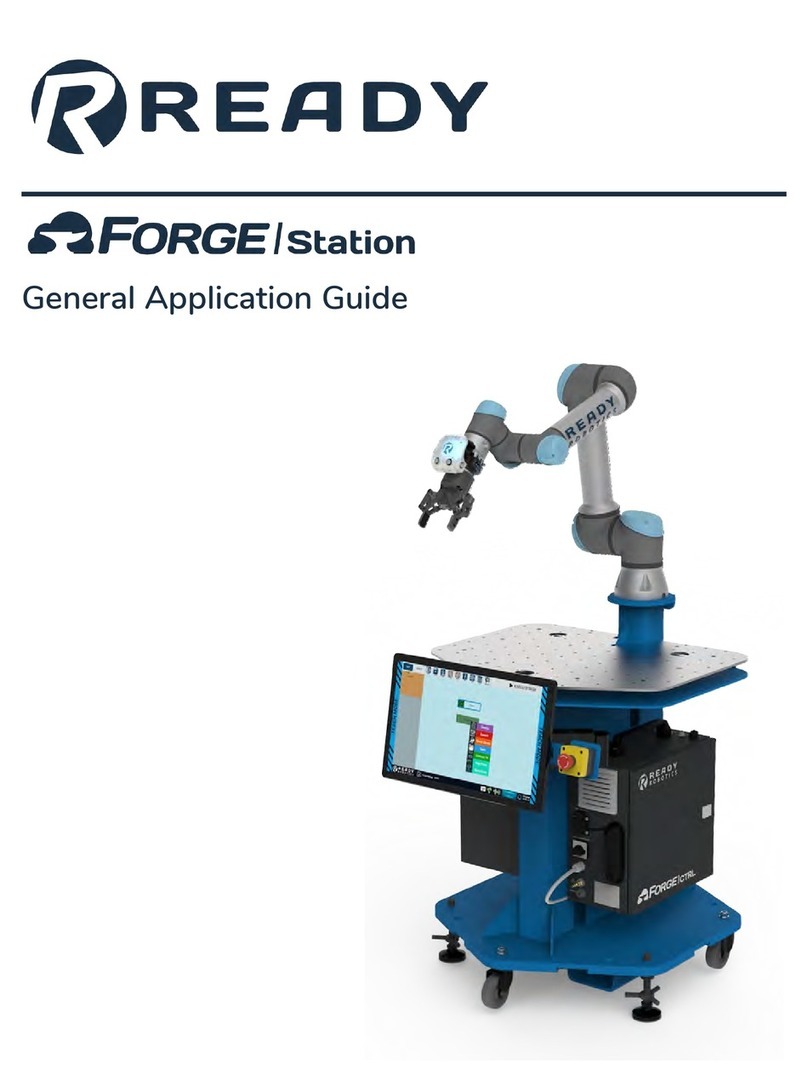
READY
READY FORGE Station General Application Guide
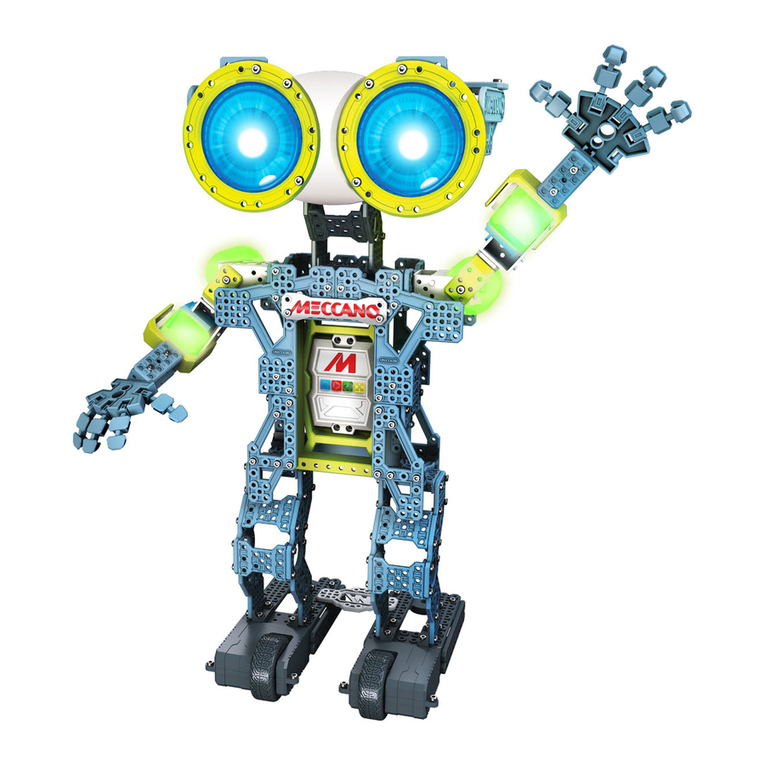
Meccano
Meccano Meccanoid G15 instructions
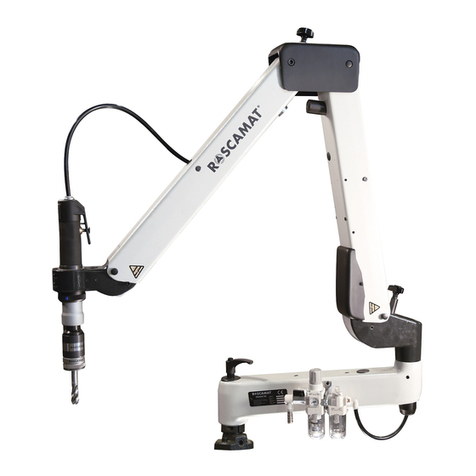
Tecnospiro
Tecnospiro ROSCAMAT-500 Series Operator's manual