RefPlus EK Series User manual

R
LIGHT-INDUSTRIAL WALK-IN
EVAPORATORS
EK-EM-EJ-LM-LJ-DJ
SERIES
INSTALLATION, OPERATION
AND MAINTENANCE
MANUAL
AWEF
REGISTERED

R

R
3
TABLE OF CONTENTS
1. SAFETY CONSIDERATIONS ...................................................................................................... 4
2. INTRODUCTION.......................................................................................................................... 4
3. PRODUCT DESCRIPTION .......................................................................................................... 4
4. NOMENCLATURE ....................................................................................................................... 5
5. HANDLING AND RIGGING.......................................................................................................... 6
5.1 STANDARD UNIT WEIGHTS ................................................................................................................................. 7
5.2 R-448A OPERATING CHARGES (LB.) ................................................................................................................... 8
6. INSTALLATION ............................................................................................................................ 9
6.1 COMPLETE PRE-INSTALLATION INSPECTION ................................................................................................... 9
6.2 INSTALLATION LOCATION .................................................................................................................................... 9
6.3 MOUNTING............................................................................................................................................................. 9
6.4 CONNECTING DRAIN LINE ................................................................................................................................... 11
6.5 CONNECTING REFRIGERANT LINES .................................................................................................................. 11
6.6 CONNECTING THE EXPANSION VALVE .............................................................................................................. 12
6.7 BULB LOCATION AND INSTALLATION.................................................................................................................. 12
6.8 SUCTION LINE CONSTRUCTION ......................................................................................................................... 13
6.9 EXTERNAL EQUALIZER LOCATION ..................................................................................................................... 15
6.10 FIELD WIRING...................................................................................................................................................... 15
7. START UP.................................................................................................................................... 16
7.1 LEAK TESTING AND EVACUATION....................................................................................................................... 16
7.2 FAN MOTORS......................................................................................................................................................... 16
7.3 FAN DELAY DEFROST TERMINATION CONTROL............................................................................................... 16
7.4 FAN DELAY DRAIN PAN CONTROL ...................................................................................................................... 16
7.5 ADJUSTING EVAPORATOR PRESSURE AND SUPERHEAT ............................................................................... 16
8. DEFROST SYSTEM .................................................................................................................... 17
8.1 AIR DEFROST UNITS. ........................................................................................................................................... 17
8.2 ELECTRIC DEFROST UNITS................................................................................................................................. 17
8.3 REVERSE-CYCLE HOT-GAS DEFROST UNITS. .................................................................................................. 17
8.4 THREE-PIPE HOT-GAS DEFROST UNITS............................................................................................................ 17
9. SERVICE ..................................................................................................................................... 18
9.1 INITIAL INSPECTION ............................................................................................................................................. 18
9.2 PERIODIC INSPECTIONS...................................................................................................................................... 18
9.3 CLEANING .............................................................................................................................................................. 18
10. TROUBLESHOOTING CHART.................................................................................................. 19
11. REPLACEMENT PARTS............................................................................................................ 19
12. EVAPORATOR START-UP REPORT FORM ............................................................................. 20
13. WIRING DIAGRAMS.................................................................................................................. 22
13.1 EKA-EMA MODELS - AIR DEFROST (ECM TWIN-SPEED FAN MOTORS)........................................................ 22
13.2 EKE-EME MODELS - ELECTRIC DEFROST (ECM HIGH-SPEED FAN MOTORS) ........................................... 23
13.3
EKR-EKT-EMR-EMT MODELS - HOT-GAS DEFROST (ECM HIGH-SPEED FAN MOTORS)
............................... 24
13.4 ALL LM MODELS - AIR, ELECTRIC & HOT GAS DEFROST............................................................................... 25
13.5 EJA-LJA MODELS - AIR DEFROST (HIGH-SPEED FAN MOTORS (OPTIONAL)) ............................................. 26
13.6 EJA-LJA-DJA MODELS - AIR DEFROST (TWIN-SPEED FAN MOTORS (OPTIONAL)) ..................................... 27
13.7 EJA-LJA-DJA MODELS - AIR DEFROST (LOW-SPEED FAN MOTORS)............................................................ 28
13.8 EJE-LJE-DJE MODELS - ELECTRIC DEFROST (TWIN-SPEED FAN MOTORS (OPTIONAL))......................... 29
13.9 EJE-LJE-DJE MODELS - ELECTRIC DEFROST (HIGH-SPEED FAN MOTORS FOR ROOMS
OF LESS THAN 32OF (0OC) (PILOT DUTY).......................................................................................................... 30
13.10 EJ-LJ-DJ MODELS - HOT-GAS DEFROST (TWIN-SPEED FAN MOTORS) ..................................................... 31
13.11 EJ-LJ-DJ MODELS - HOT-GAS DEFROST (HIGH-SPEED FAN MOTORS FOR ROOMS
OF LESS THAN 32OF (0OC) ................................................................................................................................ 32
13.12 EJ-LJ-DJ MODELS - HOT GAS DEFROST WITH ELECTRIC DRAIN PAN (TWIN-SPEED
FAN MOTORS..................................................................................................................................................... 33
13.13 EJ-LJ-DJ MODELS - HOT-GAS DEFROST WITH ELECTRIC DRAIN HIGH-SPEED
FAN MOTORS FOR ROOMS OF LESS THAN 32OF (0OC) ................................................................................ 34
13.14 EJ-LJ-DJ MODELS (AWEF) ECM BLUE FAN MOTORS.................................................................................... 35
14. PIPING DIAGRAMS............................................................................................................................................. 36
14.1 EK-EM-EJ MODELS - HOT-GAS DEFROST ........................................................................................................ 36
14.2 LM-LJ-DJ MODELS - HOT-GAS DEFROST WITH ELECTRIC DRAIN PAN........................................................ 37
14.3 LM-LJ-DJ MODELS - HOT-GAS DEFROST WITH HOT-GAS DRAIN PAN ......................................................... 38
GENERAL WARRANTY................................................................................................................... 39

R
4
1. SAFETY CONSIDERATIONS
Installing, starting up, and servicing equipment can be
hazardous due to system pressures, electrical components
and equipment location (elevated structures, etc.). Only
trained and qualied installers as well as service technicians
should install, start-up and service this equipment.
When working on the equipment, observe precautions found
in the literature, on the tags, stickers, and labels attached to
the equipment.
Follow all safety codes. Wear safety glasses and work
gloves. Keep quenched cloths and re extinguisher nearby
when brazing. Use care in handling, rigging, and setting
bulky equipment. Units are factory pressurized with dry air at
approximately 40 psig. Be careful when opening the circuit.
If no pressure is present, check for leaks or loose valves.
Work in a well-ventilated location when using refrigerant.
WARNING! Before installation, always check to
make sure main power to systems is OFF.
Electrical shock can cause personal injury or
death.
2. INTRODUCTION
These instructions describe installation, start-up and service
of refrigeration duty, light-industrial evaporator units.
3. PRODUCT DESCRIPTION
EK,EM,EJ,LM,LJ and DJ series are ceiling-mounted
light-industrial walk-in evaporators. All series except the
LM series are AWEF registered. Each unit includes a wiring
diagram that meets the customer’s requirements. The wiring
diagram displays all the components with all the necessary
protections and controls.
EK,EM and EJ series are single-coil construction for an
air distribution towards the centre of the cooler and freezer.
The fans draw air from the evaporator coil and discharge it
through the fan guards at the front of the unit.
LM, LJ and DJ series are dual-coil construction. On the
LM and LJ series, fans draw air from below the unit and
discharge it through the evaporator coils on both sides
of the unit. On the DJ series, the fans draw air from the
evaporator coil and discharge it vertically through the fan
guards underneath the unit.
Coils are manufactured with seamless deoxidized heavy
wall smooth copper tubes and aluminum plate ns. For
a maximum heat transfer, the tubes are mechanically
expanded into self-spaced plate ns with full collar for a
permanent bond.
Connections and bends are brazed with high-temperature
brazing alloy. Coils are factory leak tested at 300 psig and
purged with a -40°F dew point dry air. Coils are ready for
HFC, HFO and CO2 refrigerants and are provided with sweat
type connections (several coating materials are available).
All units are modular design and use a minimum amount of
parts for easy part replacement and availability.
All controls, motors and heaters are factory wired to provide
a fully automatic operation of the unit.
Casing for all models is made from heavy-gauge stucco
aluminum. All units come with stainless steel or plated
hardware for a lightweight and rustproof assembly. Other
optional materials are available.
EM and EJ series are provided with removable
1 1/4” female pipe thread drain tting for easy installation
and cleaning when installed with a drain union. EK, LM, LJ
and DJ series are provided with removable 7/8” female pipe
thread drain ttings.
EK, EM and LM models are equipped with AC standard-
efciency fan motors. EJ, LJ and DJ models are equipped
with 500mm (20") high-efciency cast-aluminum industrial
fans. This exible, economical and environmentally friendly
fan system enables high air side pressures, ideal efciency
and quiet operation. Fans are designed with a polymer
aerodynamic ventury for maximum air-ow dynamics. Seven
sickle-shaped fan blades are made from cast aluminum for
good corrosion resistance, low weight, excellent airow
output and sound power reduction.
All units are provided with an insulated drain pan and
assembled with corrosion-free components.
All standard EKE, EME, EJE, LME, LJE and DJE models
are provided with a defrost termination switch, heater safety
thermostat and fan delay thermostat. All units feature incoloy
low watt density tubular heaters. They are embedded within
the coil for positive defrost and high-energy efciency. This
allows heat gain reduction in coolers and freezers. They are
available for 208-240/3/60, 480/3/60 and 575/3/60. 240/3/60
and 480/3/60 can be used on 200/3/50 and 380/3/50. All
units use proper number of heaters for an even phase
loading. Refer to the wiring diagrams (Section 13) for heater
arrangement.
EMG, EJG, LMG, LJG, DJG, EMH, EJH, LMH, LJH and
DJH models are provided with fan motor contactors, heater
contactors, drain pan heater safety, fan delay and defrost
termination thermostats. These thermostats sense the coil
temperature and control the operation of fans and heaters.
All units feature incoloy low watt density tubular heaters in
the drain pan.
EKT, EMT, EJT, LMT, LJT and DJT models are provided
with fan delay, defrost termination thermostat and hot gas
defrost pan grid.

R
5
4. NOMENCLATURE
OPTIONS #2A
W = Water / glycol mixture
VOLTAGE
1 = 120/1/60
2 = 240/1/60
5 = 208-240/3/60
8 = 575/3/60
9 = 480/3/60
2350 = 235 000 BTU/H
043 = 4300 BTU/H
*Can vary from 2 to 4 digits
MODEL NUMBER / NOMINAL CAPACITY @ 10°FTD
UNIT SERIES
EK = Kompact light-industrial walk-in
EM = Light-industrial walk-in
EJ = Light-industrial walk-in with high efficiency motor(s)
LM = Low velocity light-industrial walk-in
LJ = Low velocity light-industrial walk-in with high efficiency motor(s)
DJ = Down flow light-industrial walk-in with high efficiency motor(s)
DEFROST TYPE
MODEL GENERATION
A = Air defrost
E = Electric defrost
G = Reverse cycle defrost with electric drain pan
H = Three-pipe defrost with electric drain pan
R = Reverse cycle defrost with hot gas drain pan
T = Three-pipe defrost with hot gas drain pan
0-6 = Conventional refrigerant generation
7-9 = CO2generation
OPTIONS
A = AWEF compliant
L = Low speed
J AE 2350 L0 8 W
- -

R
6
5. HANDLING AND RIGGING
Good handling and rigging practices must be followed
to protect units from damage. Having proper handling
equipment at the job site is most important and it should be
planned.
In the US, follow OSHA 1926.251 standard for Rigging
Equipment and Material Handling.
In Canada, follow your province’s requirements for
hoisting and rigging.
Improper rigging of a load or a rigging failure
can expose riggers and other workers nearby to
a variety of potential hazards.
Always lift units secured to the fork lift to
prevent it from slipping off.
Your unit is shipped crated on a pallet. This prevents any
damage to the drain pan underneath. To fasten the unit to
the ceiling, it is recommended to leave it on the pallet in
order to securely lift it up with a motorized or hand-operated
forklift. Do not use a forklift against sheet metal panels or
coils. Make sure forks extend the entire length of the unit
and against a structural part or frame.
On EK models, use the provided support brackets to bolt the
unit to the ceiling, as shown. EM, EJ, LM, LJ and DJ models
must be mounted with steel rod hangers, as shown in Figure
1. Refer to section 6.3 MOUNTING for more information.
LM, LJ and DJ units should be titled so that drain ttings are
on the lower side, to allow proper draining.
This procedure is for reference only. Rigging and handling
procedures will vary from one machine to another and from
one site to another.
Equipment handling and rigging should be
carried out by a certied operator.
EM-EJ-LM
LJ-DJ
EK
LM, LJ & DJ UNITS MUST BE TILTED
TO ALLOW PROPER DRAINING
Figure 1 Securing unit to ceiling
HANDLING AND RIGGING

R
7
STANDARD UNIT WEIGHTS
5.1 STANDARD UNIT WEIGHTS (LB.)
MODEL SHIPPING
WEIGHT MODEL SHIPPING
WEIGHT MODEL SHIPPING
WEIGHT
EKA-1400 100 EKE-1300 110 EK*-1300 108
EKA-1600 110 EKE-1500 121 EK*-1500 118
EKA-1800 153 EKE-1700 168 EK*-1700 165
EKA-2100 167 EKE-2000 184 EK*-2000 180
EKA-2400 196 EKE-2200 216 EK*-2200 211
EKA-3000 214 EKE-2900 235 EK*-2900 230
EKA-3600 243 EKE-3400 267 EK*-3400 261
EKA-4200 264 EKE-4000 290 EK*-4000 284
EKA-5400 313 EKE-5000 344 EK*-5000 337
EKA-6300 361 EKE-6000 397 EK*-6000 388
* EKR/EKT
MODEL SHIPPING
WEIGHT MODEL SHIPPING
WEIGHT MODEL SHIPPING
WEIGHT
EMA-02150 210 EME-02000 255 EM*-02000 230
EMA-02550 225 EME-02400 265 EM*-02400 245
EMA-03000 245 EME-02900 295 EM*-02900 265
EMA-04300 375 EME-04000 455 EM*-04000 405
EMA-05100 400 EME-04800 480 EM*-04800 430
EMA-06000 440 EME-05800 540 EM*-05800 470
EMA-07650 595 EME-07200 720 EM*-07200 630
EMA-09000 640 EME-08700 772 EM*-08700 680
EMA-10200 785 EME-09600 930 EM*-09600 835
EMA-12000 830 EME-11600 989 EM*-11600 900
* EMG/EMH/EMR/EMT
MODEL SHIPPING
WEIGHT MODEL SHIPPING
WEIGHT MODEL SHIPPING
WEIGHT
EJA-02900 370 EJA-02500L 370 EJE-02700 415
EJA-03600 385 EJA-03100L 385 EJE-03500 425
EJA-04500 405 EJA-03700L 405 EJE-04300 455
EJA-05900 595 EJA-05100L 595 EJE-05700 675
EJA-07200 620 EJA-06200L 620 EJE-07100 700
EJA-08900 660 EJA-07400L 660 EJE-08800 760
EJA-10800 875 EJA-09300L 875 EJE-10700 1,000
EJA-13500 920 EJA-11100L 920 EJE-13400 1,052
EJA-14300 1,125 EJA-12300L 1,125 EJE-17600 1,329
EJA-18000 1,170 EJA-14900L 1,170 EJE-22800 1,454
EJA-21800 1,454 EJA-18200L 1,454
EJA-24800 1,600 EJA-19400L 1,600
MODEL SHIPPING
WEIGHT
EJG/EJH/EJR/EJT-02900 390
EJG/EJH/EJR/EJT-03600 405
EJG/EJH/EJR/EJT-04500 425
EJG/EJH/EJR/EJT-05900 625
EJG/EJH/EJR/EJT-07200 650
EJG/EJH/EJR/EJT-08900 690
EJG/EJH/EJR/EJT-10800 910
EJG/EJH/EJR/EJT-13500 960
EJG/EJH/EJR/EJT-14300 1,175
EJG/EJH/EJR/EJT-18000 1,240
EJG/EJH/EJR/EJT-21800 1,454
EJG/EJH/EJR/EJT-24800 1,600
MODEL SHIPPING
WEIGHT MODEL SHIPPING
WEIGHT MODEL SHIPPING
WEIGHT
LMA-02200 221 LME-02200 268 LM*-02200 242
LMA-02800 236 LME-02800 279 LM*-02800 279
LMA-03300 257 LME-03300 310 LM*-03300 279
LMA-04400 394 LME-04400 394 LM*-04400 426
LMA-05600 420 LME-05600 504 LM*-05600 452
LMA-06600 462 LME-06600 567 LM*-06600 494
LMA-08400 625 LME-08400 625 LM*-08400 662
LMA-09900 672 LME-09900 811 LM*-09900 714
LMA-11200 824 LME-11200 977 LM*-11200 877
LMA-13200 872 LME-13200 1,038 LM*-13200 945
* LMG/LMH/LMR/LMT
MODEL SHIPPING
WEIGHT MODEL SHIPPING
WEIGHT MODEL SHIPPING
WEIGHT
LJA-03300L 381 LJE-03200L 421 LJ*-03300L 381
LJA-03900L 396 LJE-03800L 436 LJ*-03900L 396
LJA-04800L 417 LJE-04700L 624 LJ*-04800L 417
LJA-06600L 584 LJE-06400L 624 LJ*-06600L 584
LJA-07900L 640 LJE-07700L 680 LJ*-07900L 640
LJA-09600L 682 LJE-09300L 762 LJ*-09600L 682
LJA-11800L 845 LJE-11500L 905 LJ*-11800L 845
LJA-14400L 892 LJE-14300L 1,012 LJ*-14400L 892
LJA-15800L 1,044 LJE-15800L 1,124 LJ*-15800L 1,044
LJA-19200L 1,092 LJE-19200L 1,252 LJ*-19200L 1,092
LJA-25400L 1,547 LJE-25000L 1,631 LJ*-25400L 1,644
* LJG/LJH/LJR/LJT
MODEL SHIPPING
WEIGHT MODEL SHIPPING
WEIGHT MODEL SHIPPING
WEIGHT
DJA-03300L 381 DJE-03200L 421 DJ*-03300L 381
DJA-03900L 396 DJE-03800L 436 DJ*-03900L 396
DJA-04800L 417 DJE-04700L 624 DJ*-04800L 417
DJA-06600L 584 DJE-06400L 624 DJ*-06600L 584
DJA-07900L 640 DJE-07700L 680 DJ*-07900L 640
DJA-09600L 682 DJE-09300L 762 DJ*-09600L 682
DJA-11800L 845 DJE-11500L 905 DJ*-11800L 845
DJA-14400L 892 DJE-14300L 1,012 DJ*-14400L 892
DJA-15800L 1,044 DJE-15800L 1,124 DJ*-15800L 1,044
DJA-19200L 1,092 DJE-19200L 1,252 DJ*-19200L 1,092
DJA-25400L 1,547 DJE-25000L 1,631 DJ*-25400L 1,631
* DJG/DJH/DJR/DJT

R
8
5.2 R-448A OPERATING CHARGES (LB.)
MODEL OPERATING
CHARGE MODEL OPERATING
CHARGE MODEL OPERATING
CHARGE
EKA-1400 3.48 EKE-1300 5.5 EK*-1300 3.48
EKA-1600 5.24 EKE-1500 8.65 EK*-1500 5.24
EKA-1800 4.24 EKE-1700 6.7 EK*-1700 4.24
EKA-2100 6.38 EKE-2000 10.52 EK*-2000 6.38
EKA-2400 6.14 EKE-2200 9.67 EK*-2200 6.14
EKA-3000 9.21 EKE-2900 15.2 EK*-2900 9.21
EKA-3600 8.01 EKE-3400 12.64 EK*-3400 8.01
EKA-4200 12.03 EKE-4000 19.87 EK*-4000 12.03
EKA-5400 14.86 EKE-5000 24.55 EK*-5000 14.86
EKA-6300 17.71 EKE-6000 29.23 EK*-6000 17.71
* EKR/EKT
MODEL OPERATING
CHARGE MODEL OPERATING
CHARGE MODEL OPERATING
CHARGE
EMA-02150 3.97 EME-02000 6.09 EM*-02000 3.97
EMA-02550 5.31 EME-02400 8.5 EM*-02400 5.31
EMA-03000 7.96 EME-02900 12.57 EM*-02900 7.96
EMA-04300 7.53 EME-04000 11.52 EM*-04000 7.53
EMA-05100 10.03 EME-04800 16.05 EM*-04800 10.03
EMA-06000 15.05 EME-05800 23.72 EM*-05800 15.05
EMA-07650 14.76 EME-07200 23.6 EM*-07200 26.57
EMA-09000 22.11 EME-08700 34.88 EM*-08700 39.87
EMA-10200 20.65 EME-09600 32.22 EM*-09600 37.21
EMA-12000 30.98 EME-11600 48.83 EM*-11600 55.82
* EMG/EMH/EMR/EMT
MODEL OPERATING
CHARGE MODEL OPERATING
CHARGE MODEL SHIPPING
WEIGHT
EJA-02900 6.6 EJA-02500L 6.6 EJE-02700 5.6
EJA-03600 8.79 EJA-03100L 8.79 EJE-03500 7.82
EJA-04500 13.2 EJA-03700L 13.2 EJE-04300 11.54
EJA-05900 12.47 EJA-05100L 12.47 EJE-05700 10.59
EJA-07200 16.63 EJA-06200L 16.63 EJE-07100 14.76
EJA-08900 24.94 EJA-07400L 24.94 EJE-08800 21.82
EJA-10800 24.45 EJA-09300L 24.45 EJE-10700 21.7
EJA-13500 36.68 EJA-11100L 36.68 EJE-13400 32.1
EJA-14300 32.27 EJA-12300L 32.27 EJE-17600 42.35
EJA-18000 48.42 EJA-14900L 48.42 EJE-22800 52.63
EJA-21800 60.16 EJA-18200L 60.16
EJA-24800 80.2 EJA-19400L 80.2
MODEL OPERATING
CHARGE
EJG/EJH/EJR/EJT-02900 6.6
EJG/EJH/EJR/EJT-03600 8.79
EJG/EJH/EJR/EJT-04500 13.2
EJG/EJH/EJR/EJT-05900 12.47
EJG/EJH/EJR/EJT-07200 16.63
EJG/EJH/EJR/EJT-08900 24.94
EJG/EJH/EJR/EJT-10800 24.45
EJG/EJH/EJR/EJT-13500 36.68
EJG/EJH/EJR/EJT-14300 32.27
EJG/EJH/EJR/EJT-18000 48.42
EJG/EJH/EJR/EJT-21800 60.16
EJG/EJH/EJR/EJT-24800 80.2
MODEL OPERATING
CHARGE MODEL OPERATING
CHARGE MODEL SHIPPING
WEIGHT
LMA-02200 3.7 LME-02200 4.77 LM*-02200 3.7
LMA-02800 5.55 LME-02800 8.13 LM*-02800 5.55
LMA-03300 7.45 LME-03300 10.03 LM*-03300 7.45
LMA-04400 7.01 LME-04400 9.06 LM*-04400 7.01
LMA-05600 10.52 LME-05600 15.34 LM*-05600 10.52
LMA-06600 14.03 LME-06600 19 LM*-06600 14.03
LMA-08400 15.49 LME-08400 22.6 LM*-08400 15.49
LMA-09900 20.65 LME-09900 27.91 LM*-09900 20.65
LMA-11200 19.92 LME-11200 26.6 LM*-11200 19.92
LMA-13200 26.55 LME-13200 34.54 LM*-13200 26.55
* LMG/LMH/LMR/LMT
MODEL OPERATING
CHARGE MODEL OPERATING
CHARGE MODEL OPERATING
CHARGE
LJA-03300L 10.57 LJE-03200L 7.94 LJ*-03300L 10.57
LJA-03900L 14.08 LJE-03800L 10.13 LJ*-03900L 14.08
LJA-04800L 21.14 LJE-04700L 15.83 LJ*-04800L 21.14
LJA-06600L 19.97 LJE-06400L 14.95 LJ*-06600L 19.97
LJA-07900L 26.6 LJE-07700L 19.14 LJ*-07900L 26.6
LJA-09600L 39.89 LJE-09300L 29.91 LJ*-09600L 39.89
LJA-11800L 39.11 LJE-11500L 28.11 LJ*-11800L 39.11
LJA-14400L 58.7 LJE-14300L 44.03 LJ*-14400L 58.7
LJA-15800L 51.63 LJE-15800L 37.12 LJ*-15800L 51.63
LJA-19200L 77.45 LJE-19200L 58.11 LJ*-19200L 77.45
LJA-25400L 96.25 LJE-25000L 72.19 LJ*-25400L 96.25
* LJG/LJH/LJR/LJT
MODEL OPERATING
CHARGE MODEL OPERATING
CHARGE MODEL OPERATING
CHARGE
DJA-03300L 10.57 DJE-03200L 7.94 DJ*-03300L 10.57
DJA-03900L 14.08 DJE-03800L 10.13 DJ*-03900L 14.08
DJA-04800L 21.14 DJE-04700L 15.83 DJ*-04800L 21.14
DJA-06600L 19.97 DJE-06400L 14.95 DJ*-06600L 19.97
DJA-07900L 26.6 DJE-07700L 19.14 DJ*-07900L 26.6
DJA-09600L 39.89 DJE-09300L 29.91 DJ*-09600L 39.89
DJA-11800L 39.11 DJE-11500L 28.11 DJ*-11800L 39.11
DJA-14400L 58.7 DJE-14300L 44.03 DJ*-14400L 58.7
DJA-15800L 51.63 DJE-15800L 37.12 DJ*-15800L 51.63
DJA-19200L 77.45 DJE-19200L 58.11 DJ*-19200L 77.45
DJA-25400L 96.25 DJE-25000L 72.19 DJ*-25400L 96.25
* DJG/DJH/DJR/DJT
R-448A OPERATING CHARGES

R
9
6. INSTALLATION
6.1 COMPLETE PRE-INSTALLATION INSPECTION
Check all items against the bill of lading to make sure all
crates and boxes have been received. Check unit for
possible damage incurred during shipment. Check for
concealed damage. If there is any shortage or damage, le
a freight claim immediately with the transport company.
Do not return damaged equipment to the factory without
prior approval. A Return Material Authorization (RMA)
must be obtained in advance. Items returned without an
RMA label will be refused. Also verify that the nameplate
electrical requirements match the available power supply.
All RefPlus units are pressurized with dry air. A lack of
pressure does not indicate a leak. Check the coil for
possible leaks before installing or returning the unit.
The following essential rules should be complied with
when installing the unit:
• All circuits, including controls and safety switches, must
be correctly connected according to the wiring diagram
supplied with the unit and/or found in this manual.
• The factory wiring cannot be modied without RefPlus'
written approval.
• All units and equipment must be installed with the
specied clearances.
• System piping must be in accordance with proper
refrigeration practices.
• Inert gas must be charged into the system piping
during brazing.
6.2 INSTALLATION LOCATION
All units should be installed ush against the ceiling. The
unit must be level in all directions to ensure proper drainage
of condensate. Refer to Figure 2 and Figure 3 for unit
clearance information.
When deciding on the location of the unit, consider the
following:
• Location of aisle racks
• Location relative to compressor for minimum pipe runs
• Location of condensate drains for minimum run
• The air pattern must cover the entire room
• Never locate units over doors or door openings
• Allow sufcient space between rear of unit and wall to
permit free return of air
IMPORTANT: Avoid placement of the unit directly above
doors and door openings where low temperature is being
maintained. Position the unit so the discharge air blows
above the doors. Install a bafe if door extends above the
blower level. Leave space equal to unit height between
bottom of unit and product. Do not stack product in front
of fans.
EK, EM and EJ units should be located in a position where
the air discharge is towards the door.
The coil face on units should be away from the wall by:
• EK, EM & EK models: 1/2 coil unit height minimum -
unit height recommended
• LM models: 6 ft minimum - 40 ft maximum
• LJ & DJ models: 10 ft minimum - 40 ft maximum
NOTE: Units with electric defrost require a minimum
clearance equal to the width (W) of the unit at the left
end when facing the fans to allow removal of defrost
heaters, as shown in Figure 2 and Figure 3.
6.3 MOUNTING
Most units can be mounted with either bolts or steel rod
hangers. When mounting unit to ceiling, use Table 1 below
to determine proper rod or bolt size. Use steel rods with
a minimum 9 Kpsi. This information should be used as
reference only.
STEEL ROD
OR BOLT
SIZE
MAXIMUM WEIGHT PER ANCHOR POINT
5/16" 200 lbs
3/8" 300 lbs
1/2" 550 lbs
Table 1 Bolt and rod size chart
The evaporator must be mounted level for proper condensate
draining. Adequate support must be provided to hold the
weight of the unit.
NOTE: The area above the unit must be sealed or
accessible to facilitate hand cleaning without the use
of tools in order to comply with National Sanitation
Foundation (NSF) Standard 7.
INSTALLATION

R
10
1/2 H min.
1 H recommended
3’ min.
(W for units
w/electric defrost)
(W for units
w/electric defrost)
3’ min.
Air
Flow
6’ min.
40’ max.
10’ min.
40’ max.
3’ min. 3’ min.
W
EK-EM-EJ
LM-LJ-DJ
LM LJ-DJ
Figure 2 Single-evaporator clearance (H=Height of unit - W=Width of unit)
3’ min. 3’ min.
(W for units
w/electric defrost)
(W for units
w/electric defrost)
(W for units
w/electric defrost)
W min.
Air
Flow
Air
Flow
1/2 H min.
1 H recommended
1/2 H min.
1 H recommended
6’ min.
40’ max.
3’ min. 3’ min.
3’ min.
EK-EM-EJ EK-EM-EJ
LM-LJ-DJ LM-LJ-DJ
LM-LJ-DJ LM-LJ-DJ
LM 10’ min.
40’ max.
12’ min.
80’ max.
LM 20’ min.
80’ max.
LJ-DJ
LJ-DJ
W W
Figure 3 Multiple-evaporator clearance (H=Height of unit - W=Width of unit)
INSTALLATION

R
11
6.4 CONNECTING DRAIN LINE
For all evaporators, a drain line union is recommended
for ease of installation and future servicing and should be
located in close proximity to the drain pan.
EK, LM, LJ & DJ: A 7/8" ID removable drain coupling is
supplied with each unit.
EM & EJ are supplied with 1 1/4" FPT connections.
FOR ALL MODELS, connect the drain line as follows:
1. Replace the rubber gasket to prevent condensate
leakage.
2. Locate the union as close to the drain pan as possible.
3. Hand tighten the coupling as shown in Figure 4. DO
NOT use wrench to tighten coupling in place as this
could damage the gasket and cause leaks. Once the
coupling is in place, connect the drain pipe and tighten
pipe using two wrenches as shown. The use of two
wrenches will prevent the coupling from twisting and
damaging the unit.
HAND TIGHTEN ONLY
LOCK COUPLING IN PLACE
WHILE TIGHTENING PIPE
Figure 4 Drain pan coupling
4. Sharply pitch the drain line and exit it through the
cooler with a short run.
5. Insulate and seal the drain line where it passes through
the wall.
6. Locate the drain traps in warm ambient air temperature
to prevent freeze-up.
Drain traps on low temperature units must be outside of
refrigerated enclosures. Properly protected from freezing,
copper or steel pipes should be used. Food approved plastic
can also be used for medium temperature coolers above
35°F (2°C). The drain line must have a minimum of 4’’ per foot
pitch for proper drainage. The unit must be perfectly level in
two directions. The drain line should be at least as large as
the evaporator drain connection. All plumbing connections
should be made in accordance with local plumbing codes.
All condensate drain lines must be trapped and run to an
open drain. They must never be connected directly to the
sewer system. Traps in the drain lines must be in a warm
ambiance.
We recommend a trap on each evaporator. Traps located
outside the building must be insulated and wrapped with a
drain line heater. When installing the heater, be sure to avoid
overlapping. The heater must be permanently energized. A
heat input of at least 20 W per linear foot of drain line for a
0°F (-18°C) room and 30 W per linear foot of drain line for
a -20°F (-29°C) room should be satisfactory. Always trap
drain lines individually to prevent vapour migration.
6.5 CONNECTING REFRIGERANT LINES
All refrigerant system components must be installed in
accordance with applicable local and national codes using
proper engineering practices. Refer to the piping diagrams
on page 36.
Use top quality refrigeration tubing that is internally free of
dirt, humidity or other contaminants. Unsealed tubing should
not be used. Long radius elbows are recommended.
Dry nitrogen must be swept through the lines while joints are
brazed to avoid oxidation and carbon deposits.
IMPORTANT: A calibrated pressure gauge and regulator
must always be used with nitrogen gas cylinders.
All external piping must be well supported. The unit will not
support external piping or valves.
If the condition arises where the suction line must be raised
to a point higher than the suction connection on the unit, a
suction line trap must be installed on the unit.
Horizontal suction lines should slope away from the
evaporator toward the compressor. Leak check and
evacuate the system using a two-stage deep vacuum pump.
Pull and hold for 24 hours a 500 micron vacuum.
INSTALLATION

R
12
6.6 CONNECTING THE EXPANSION VALVE
All units are supplied with a sweat expansion valve
connection. Expansion valves are eld supplied or may have
been installed at the factory (optional).
All units require the use of an externally equalized expansion
valve and are provided with a 1/4" OD equalizer line.
Check the operation of the expansion valve after the system
has reached the desired cooler temperature. If the coil is not
receiving enough refrigerant, reduce the superheat setting
on the expansion valve.
To ensure unit performance, the expansion valve must be
set at the proper superheat and at the lowest temperature in
which the system is expected to operate.
6.7 BULB LOCATION AND INSTALLATION
The location and installation of the bulb is extremely
important to the proper system performance and care
should be taken with its nal location. Accepted principles of
good suction line piping should be followed to provide a bulb
location that will give the best possible valve control.
The bulb should be securely fastened to a clean straight and
horizontal section of the suction line at the evaporator outlet.
This will ensure good thermal contact between the bulb and
the suction line for satisfactory expansion valve control. If
the bulb cannot be located in that manner, it may be located
on a descending vertical line only. The bulb should never
be located in a trap or downstream of a trap in the suction
line. Liquid refrigerant or mixture of liquid refrigerant and oil
boiling out of the trap will falsely inuence the temperature of
the bulb and result in poor valve control.
On suction lines 7/8” OD and larger, the surface temperature
may vary slightly around the circumference of the line. On
these lines, it is generally recommended that the bulb be
installed at 4 or 8 o’clock on the side of the horizontal line,
and parallel with respect to the direction of ow. On smaller
lines the bulb may be mounted at any point around the
circumference, however locating the bulb on the bottom of
the line is not recommended as an oil-refrigerant mixture
is generally present at that point. Figure 5 shows both
installation conguration. Certain conditions, specic to a
particular system, may require a different bulb location than
normally recommended. In these cases, the proper bulb
location may be determined by trial.
BULB ON SMALL SUCTION LINE
BULB ON LARGE SUCTION LINE
7/8” OD AND LARGER
8 o’clock 4 o’clock
Figure 5 Bulb installation
On multiple evaporator installations, the piping should
be arranged so that the ow from any valve cannot affect
the bulb of another, as shown in Figure 6. Approved piping
practices including the proper use of traps ensures individual
control for each valve without the inuence of refrigerant and
oil ow from other evaporators.
The vertical riser extending to the height of the evaporator
prevents refrigerant from draining by gravity into the
compressor during the off-cycle.
ABOVE AND BELOW MAIN SUCTION LINE
FLOW FROM UPPER VALVE
CANNOT AFFECT BULB
OF ANOTHER
INVERTED TRAP TO
AVOID OIL DRAINING
INTO IDLE
EVAPORATOR
FREE DRAINING
Figure 6 Bulb installation on multiple evaporator conguration
INSTALLATION

R
13
6.8 SUCTION LINE CONSTRUCTION
RECOMMENDED VELOCITY FOR GOOD OIL RETURN OF POE WITH HFC - FPM (M/S)
FPM Minimum
Horizontal
Minimum
Vertical Design Maximum
Condensate NA NA ≤ 100 (0.5) 150 (0.8)
Liquid NA NA ≤ 300 (1.5) 300 (1.5)
Suction 500 (2.5) 900 (4.6) 1000 (5.1) - 3000 (15.2) 4000 (20.3)
Discharge 500 (2.5) 900 (4.6) 2000 (10.2) - 3000 (15.2) 3500 (17.8)
HG Defrost 500 (2.5) 900 (4.6) 1000 (5.1) - 2000 (10.2) 3000 (15.2)
Table 2 Recommended velocity for good oil return of POE with HFC - FPM (m/s)
INSTALLATION
IMPORTANT: A calibrated pressure gauge and regulator
must always be used with nitrogen cylinders.
The suction line must be sized to maintain proper line
velocities with a practical line pressure drop. It is usually
equal to 2°F (1.1°C). To ensure proper oil return, all horizontal
lines must be sloped down toward the compressor with a
minimum pitch of 1/4” (6.4 mm) per 10 ft (3 m).
An access tting must be installed (when not part of the
evaporator) on the evaporator suction line to read an
accurate suction pressure for superheat adjustment.
In situations where it is necessary for the suction line to rise,
an oil trap must be installed at the bottom of the riser as
shown in Figure 7, page 13. To ensure oil return through a
riser in the suction line, a velocity of no less than 1000 FPM
(5.1 m/s) is required. When a system has capacity variation
or unloaders, a double riser when at less than 50% capacity
may be necessary to keep the velocity at a minimum of 900
FPM (4.6 m/s). You can drop one size for suction riser to lift
the oil. A trap should be provided for each additional 20 ft
(6 m) of riser. See Figure 8.
Avoid oil and refrigerant migration between active and
inactive evaporators in a common suction system. When
multiple evaporators are connected to a common suction
line, it must enter from the top. The rst evaporator suction
connection should have an inverted trap as shown in Figure
9.
Suction lines should not be exposed to heat or the sun.
The line must be properly insulated if it is necessary to run
suction line outside of the building or through heated areas.
The suction line must be insulated in any situation where the
pipe may sweat or freeze.
If isolation valves are installed on the suction lines, full port
ball valves should be used.
OIL
OIL
SLOPE 1/4”
PER 10 FT.
TOWARD
COMPRESSOR
IMPROPER PROPER PROPER
INSTALL REDUCERS
IN VERTICAL PIPE
INSTALL EXPANDER
IN HORIZONTAL PIPE
Figure 7 Suction oil trap construction

R
14
INSTALLATION
A B A B
SUCTION LINE
TO COMPRESSOR
SUCTION LINE
TO COMPRESSOR
EVAP.
RED TEE RED TEE
U-BEND OR
2 ELLS
45OSTR.
ELLS
90OSTR.
ELLS
EVAP.
Figure 8 Double suction riser
MULTIPLE EVAPORATORS
ON DIFFERENT LEVELS:
COMPRESSOR ABOVE
MULTIPLE EVAPORATORS
STACKED ON SAME LEVEL:
COMPRESSOR ABOVE
(ARRANGEMENT APREFERRED)
MULTIPLE EVAPORATORS ON
SAME LEVEL: COMPRESSOR
BELOW
DOUBLE RISER
WHEN
NECESSARY DOUBLE RISER
WHEN
NECESSARY
MULTIPLE EVAPORATORS ON
SAME LEVEL: COMPRESSOR
ABOVE
A B C D
Figure 9 Multiple evaporator suction line construction

R
15
6.9 EXTERNAL EQUALIZER LOCATION
The purpose of the external equalizer is to sense the
pressure in the suction line at the bulb location and transmit
it to the TEV diaphragm. This usually means installing the
external equalizer immediately downstream from the bulb.
This ensures the correct pressure is signalled to the TEV.
In some situations this “ideal” location may not be possible.
In these cases, an alternate location, such as at B or C (see
Figure 10), could be used. However, the pressure at these
locations must be nearly identical to the pressure in the line
where the bulb is located.
In other words, locations B and C are acceptable as long
as these pressures are essentially the same as A when
the system is operating at full load. In the past, there has
been concern about installing the external equalizer “up-
stream” from the bulb. This was due to the possibility of
refrigerant leaking past the TEV push rods, passing through
the equalizer line and into the suction line, thus falsely
inuencing the TEV bulb temperature.
6.10 FIELD WIRING
WARNING: All system wiring must be done in
accordance with applicable codes and local
ordinances.
All internal wiring of fan motors, tubular heaters and
combination defrost termination fan delay control have been
factory connected. Before operating the unit, always double-
check all wiring connections, including the factory wired
terminals. Factory connections may vibrate loose during
transport.
Wiring diagrams are shown at the end of this manual for
reference only. Always refer to the wiring diagram supplied
with your specic unit.
When eld wiring the unit, consider the following:
• All wiring connections terminate on terminal block(s) in
the wiring compartment and are clearly labeled.
• The serial tag on the unit is identied with the electrical
characteristics for wiring the unit.
• Consult the wiring diagram in the unit for proper
connections.
• Wires should be copper conductor only and of the
proper size in order to handle the connected electrical
load.
• The unit must be grounded.
• For systems with multiple evaporator, the defrost
termination controls should be wired in series. Follow
the wiring diagrams for multiple evaporators carefully.
• Multiple evaporator systems should operate off of one
thermostat.
• If a remote defrost timer is used, the timer should be
located outside the refrigerated space.
INSTALLATION
B
A
C
EVAPORATOR
TEV
COMPRESSOR
Figure 10 Location of TEV external equalizer

R
16
7. START-UP
CAUTION: Before starting unit, be sure wire fan
guards are secured in place over each fan.
7.1 LEAK TESTING AND EVACUATION
Leak testing and evacuation must be done in
accordance with local and national codes.
Once all refrigerant connections are made, leak test all
joints before charging the system with refrigerant. After
leak testing, all moisture and non-condensable gas must
be evacuated from the system. Attach high vacuum line
pump and gauge on both high and low pressure sides of the
system. A minimum vacuum level of 500 micron is required
to effectively remove moisture.
Be sure all valves such as compressor, hot gas, receiver,
and liquid solenoid valves are open. Break the vacuum in
the system with the refrigerant to be used. Always charge
the refrigerant into the system through a new 16 cu. in drier
(eld supplied) in the charging manifold line.
7.2 FAN MOTORS
Fan motors may cycle off on automatic thermal protection if
the coils are frozen or blocked. Check the supply voltage at
the motor leads if motor is inoperable. Also check direction
of rotation of the motors.
AWEF registered EJ, LJ & DJ models are limited to -30oF
room temperature and -40oF suction. Minimum fan speed is
set to 60% of its maximum. For air defrost units, minimum
fan speed is 50%.
IMPORTANT! For units equipped with variable-
speed ECM Blue motors, current provided to fan
motors must be applied at all times, specially
during winter operation. Refer to wiring diagram
13.14 on page 35 for more details.
7.3
FAN DELAY / DEFROST TERMINATION CONTROL
This control is located on the coil plate and senses the coil
temperature. To provide fan delay, the defrost thermostat
must be turned off.
To set the defrost termination / fan delay thermostat:
1. Set the cut-in temperature to approximately 50-60oF. This
will be your high event or the limit defrost temperature.
2. Set the differential temperature to approximately 20-30oF.
This will be your low event or fan cut-in temperature.
The idea is to have your evaporator coil temperature
below 32oF in order to avoid water carry over.
Example:
Cut-in defrost temperature=55oF (End defrost)
Cut-in fan temperature=30oF (Start fans)
Differential= 25oF (55-30=25)
7.4 FAN DELAY DRAIN PAN CONTROL
The fan delay drain pan control senses the general coil
temperature.
• With temperature rise, the fan delay thermostat de-
energizes the fan and energizes the electric pan heaters.
• After defrost cycle, the coil temperature drops below the
freezing point and the fan delay thermostat energizes
the fan motor and de-energizes the heaters.
• Defrost timer must be set long enough to completely
melt the ice in the unit. Set the thermostat at 20 to 25ºF
and the differential at minimum.
IMPORTANT: After correcting a faulty defrost cycle, it is
essential that the coil, drain pan and unit be free and clear of
ice before placing the unit back on automatic operation.
7.5 ADJUSTING EVAPORATOR PRESSURE AND
SUPERHEAT
What is Glide:
Understanding Glide is the key to maintaining the
desired temperature and protecting the compressor.
To reach EPA and Environment Canada's mandated lower
global warming potential (GWP) levels, the commercial
refrigeration industry has increasingly turned to refrigerant
blends. These blends are non-toxic, non-ammable and
operate within the typical commercial refrigeration operating
pressures.
Many technicians are accustomed to using refrigerants that
act as a single component with a boiling temperature that
doesn’t change within the evaporator. But with zeotropic
refrigerant blends, the temperature in the evaporator will be
colder at the start of the coil than at the end. Simply put, the
differences in these temperatures is the Glide.
Refrigerant Blends and Glide:
Refrigerant blends such as R-404A, R-407A, R-407C, R-407F,
R-448A and R-449A are a mixture of components that retain
their individual evaporating and condensing points.
With R-404A, the refrigerant glide is approximately 1oF and
can generally be ignored.
With R-407A, R-407C, R-407F, R-448A and R-449A,
refrigerant glide is much higher (6-10˚F) and yields higher
dew point condensing temperatures in comparison to R-404A
for equivalent performance
Why Glide Matters:
Because different components in a blend boil at different
temperatures, the temperature in the coil will vary as the
mixture boils. If the expansion valve adjustment isn’t made
using the Dew Point, two things can happen. FIRST, the
liquid may not vapourize before reaching the compressor,
which can cause inefciency and lead to compressor damage.
SECOND, the blend may completely boil part way through the
evaporator, leading to a loss of efciency and
required xture
temperature.
START-UP

R
17
Setting Evaporator Pressure:
As an example, let say we want to achieve an average coil
temperature of 20oF ( in Table 3). Using a temperature-
pressure chart as reference such as the example in Table
3, now that we can begin by setting the Pressure to 51 psig
(item ).
Setting Evaporator Superheat:
In order to set the superheat, nd the Dew Point temperature
corresponding to the coil pressure. The evaporator coil
pressure and dew temperature are shown by and in the
chart below. To get superheat, compare the dew temperature
from the chart to the actual temperature of the evaporator
outlet piping. The difference in these two temperatures is
the superheat. In this example, when the pressure is 51
psig and the pipe temperature is 30 degrees, the superheat
will be 30 minus 25, or 5 degrees. As you continue to take
temperature readings, you can adjust the superheat and
pressure as needed until you’ve achieved the desired coil
temperature.
Note: In the absence of specic manufacturer recommendations,
a 4 to 6° F superheat for low temperature and 6 to 8° F for
medium temperature is recommended.
Note: When setting superheat in a system using a refrigerant
with glide, remember that pressure is constant throughout
the evaporator while the temperature will change during
boiling in the evaporator.
Adjusting for Glide:
When adjusting pressure and superheat, your goals are to
achieve the desired temperature, maximize coil efciency,
and protect the compressor for long service life. It all starts
by looking at the Pressure-Temperature (PT) chart included
with your refrigerant or any up-to-date refrigerants PT Chart.
PRESSURE
TEMPERATURE
AVERAGE BUBBLE DEW
(PSIG) OF
45 15 10 20
46 16 11 21
47 17 12 22
48 18 12 23
49 18 13 24
50 19 14 24
151 420 315 225
52 21 16 26
53 22 16 27
54 22 17 28
55 23 18 28
Table 3 Example of pressure-temperature chart
8. DEFROST SYSTEM
8.1 AIR DEFROST UNITS
Fan motors run continuously and a defrost time clock, or
low-pressure setting, stops the compressor when defrost is
required.
NOTE: The unit must not be in operation more than 16
hours per day.
8.2 ELECTRIC DEFROST UNITS
A time clock starts the defrost process by stopping the fan
and energizing the heaters. When the defrost thermostat
resets the time clock, it de-energizes the heaters and re-
starts the fan motors.
8.3 REVERSE-CYCLE HOT-GAS DEFROST UNITS
Reverse-cycle defrost systems introduce compressor
discharge gas through the suction line during defrost. The
amount of gas introduced is controlled by a solenoid bypass
valve and a gas defrost time clock.
Condensed refrigerant is relieved through a check valve.
The check valve bypasses the expansion valve leading to
the liquid line which has reduced pressure. The drain pan is
warmed by the entering hot gas to avoid freezing. Defrost is
initiated and terminated by the time clock.
NOTE: A minimum of 4 evaporators is required for an
efcient operation.
NOTE: The use of a suction to liquid heat exchanger is
recommended.
8.4 THREE-PIPE HOT-GAS DEFROST UNITS
During defrost, compressor discharge gas is introduced in
a separate hot gas line. The amount of gas introduced is
controlled by a solenoid bypass valve and a gas defrost time
clock.
To avoid excessive accumulation of liquid in the suction
accumulator, a heat exchanger is recommended. The drain
pan is warmed by the entering hot gas to avoid freezing. The
time clock cycles fan motors, liquid and hot gas solenoids.
NOTE: A minimum of 3 evaporators is required for an
efcient operation. Special engineering is required
for a 1 or 2 evaporator conguration. Please
contact RefPlus' Sales-Engineering department for
proper selection.
NOTE: A eld-installed pressure regulating valve may
be required on low temperature systems to control
compressor crankcase pressure.
4
1
12
DEFROST SYSTEM

R
18
9. SERVICE
9.1 INITIAL INSPECTION
After the system has been charged and has operated for at
least two hours at normal operating conditions without any
indication of malfunction, it should be allowed to operate
overnight on automatic controls. Then a thorough inspection
of the unit operation should be made as follows:
1. Check for any vibration in the unit.
2. Check liquid line sight glass and proper operation of
expansion valve. If additional refrigerant seems to be
required, leak test all connections. Repair any leaks
before adding refrigerant.
3. Thermostatic expansion valves must be checked for
proper superheat settings. Sensing bulbs must be
in positive contact with the suction line and should
be insulated. Valves set at high superheat will lower
refrigeration capacity. Low superheat may cause liquid
slugging and compressor bearing washout.
4. Check defrost controls for initiation and termination
settings and length of defrost period. Set fail safe at
length of defrost + 25%. Example: 20 minute defrost + 5
minutes = 25 minute fail safe
5. Check drain pan for proper drainage.
9.2 PERIODIC INSPECTIONS
All units should be checked at least once a month for proper
defrosting. It may be necessary to periodically change the
number of defrost cycles or adjust the duration of defrost.
Under normal usage conditions, proper unit maintenance
should be done every six months to include the following:
1. Check all wiring and insulators.
2. Check and tighten all electrical connections.
3. Inspect contactors for proper operation and for worn
contact points.
4. Check all fan motors. Tighten motor mount bolts/nuts
and tighten fan set screws.
5. Clean condenser coil surface.
6. Check refrigerant and oil level in the system.
7. Check operation of the control system ensuring all safety
controls are operating properly.
8. Check all defrost controls are functioning properly.
9. Clean the unit coil surface.
10. Clean the drain pan and check the drain pan drain line
for proper drainage.
11. Check drain line heater for proper operation, cuts and
abrasions.
12. Check and tighten all are connections.
See troubleshooting chart for troubleshooting information.
CAUTION: Before starting unit, be sure wire fan
guards are securely fastened over each fan.
9.3 CLEANING
WARNING! Before carrying out any cleaning or
maintenance of the unit, always check to make
sure main power to systems is OFF.
Electrical shock can cause personal injury or
death.
The unit should be checked periodically for dirt accumulation.
Grease and dust should be removed from the fan, fan
guards, and drain pan.
Occasional cleaning of nned surfaces can be done by
dusting the ns and then cleaning with a mild detergent and
warm water spray.
Always pressure clean in reverse of the air ow.
IMPORTANT: Do not use alkaline or acidic solutions; they
will damage the coils. Remove the fan guards to clean the
inner face of the coil.
SERVICE

R
19
TROUBLESHOOTING CHART
10. TROUBLESHOOTING CHART
PROBLEM POSSIBLE CAUSES POSSIBLE CORRECTIVE STEPS
Fan(s) will not
operate
1. Main switch open.
2. Blown fuses.
3. Defective motor.
4. Defective timer or defrost thermostat.
5. Unit in defrost cycle.
6. Coil does not get cold enough to reset
thermostat.
1. Close switch.
2. Replace fuses. Check for short circuits or
overload conditions.
3. Replace motor.
4. Replace defective component.
5. Wait for completion of cycle.
6. Adjust fan delay setting of thermostat.
Room temperature
too high
1. Room thermostat set too high.
2. Superheat too high.
3. System low on refrigerant.
4. Coil iced-up.
1. Adjust thermostat.
2. Adjust thermal expansion valve.
3. Add refrigerant.
4. Manually defrost coil and check defrost
controls for malfunctions.
Ice accumulating
on ceiling around
evaporator and/or
on fan guards,
venturi, or blades
1. Defrost duration is too long.
2. Fan delay not delaying fans after defrost
period.
3. Defective defrost thermostat or timer.
4. Too many defrosts.
1. Adjust defrost termination thermostat.
2. Defective defrost thermostat or not
adjusted properly.
3. Replace defective component(s).
4. Reduce number of defrost.
Coil not clearing of
frost during defrost
cycle
1. Coil temperature not getting above freezing
point during defrost.
2. Not enough defrost cycles per day.
3. Defrost cycle too short.
4. Defective timer or defrost thermostat.
1. Check heater operation.
2. Adjust timer for more defrost cycles.
3. Adjust defrost thermostat or timer for
longer cycle.
4. Replace defective component.
Ice accumulating in
drain pan
1. Defective heater.
2. Unit not pitched properly.
3. Drain line plugged.
4. Defective drain line heater.
5. Defective timer or thermostat.
1. Replace heater.
2. Check pitch and adjust, if necessary.
3. Clean drain line.
4. Replace heater.
5. Replace defective component.
Uneven coil
frosting
1. Defective heater.
2. Unit located too close to door or opening.
3. Defrost termination set too low.
4. Incorrect or missing distributor nozzle.
1. Replace heater.
2. Relocate unit.
3. Adjust defrost termination setting higher.
4. Add or replace nozzle with appropriate
sized orice for conditions.
11. REPLACEMENT PARTS
Download the parts manual at refplus.com

R
20
EVAPORATOR STARTUP REPORT FORM
12. EVAPORATOR START-UP REPORT FORM
IMPORTANT: This startup report form must be lled out, signed and sent to RefPlus for the warranty to be honoured.
1. GENERAL INFORMATION
JOB LOCATION: _____________________________________________________________________________________________________________________
_____
REFPLUS RJ No: CONTRACTOR NAME:
UNIT COOLER MODEL No.: SERIAL No.:
2. PRE-START-UP (Check each item when completed)
CHECK ALL ELECTRICAL CONNECTIONS AND TERMINALS FOR TIGHTNESS CHECK ALL FAN MOTORS AND MOTOR MOUNTS FOR TIGHTNESS
CHECK DRAIN LINES AND DRAIN PAN FOR PROPER DRAINAGE CHECK DRAIN LINE HEATER FOR PROPER OPERATION
VERIFY THAT ALL DEFROST CONTROLS ARE FUNCTIONING PROPERLY CHECK ALL FLARE CONNECTIONS FOR TIGHTNESS
CHECK ALL MECHANICAL SEALS AND REFRIGERANT PIPING CONNECTIONS FOR TIGHTNESS
CARRY OUT PRESSURE TEST (PRESSURE/DURATION) PRESSURE : PSI DURATION: ____
EVACUATION (DURATION): ________ FINAL MICRON: _
UNIT COOLER DRAIN LINE TRAPPED OUTSIDE OF BOX: YES NO
3. START-UP
REFRIGERANT
REFRIGERANT TYPE (I.E. R448A)
ELECTRICAL
CHECK FAN MOTORS FOR PROPER ROTATION
MAIN POWER (DESIGN): __________V / ________ PH / _______Hz
MAIN POWER (MEASURED): L1-L2 __________V L1-L3 __________V L2-L3 __________V
CONTROL VOLTAGE (MEASURED): __________V
TOTAL UNIT AMPERAGE (MEASURED) __________ AMPS
FAN 1 __________ AMPS (L1) __________ AMPS (L2) _________ AMPS (L3) _________ AMPS (RATED)
FAN 2 __________ AMPS (L1) __________ AMPS (L2) _________ AMPS (L3) _________ AMPS (RATED)
FAN 3 __________ AMPS (L1) __________ AMPS (L2) _________ AMPS (L3) _________ AMPS (RATED)
FAN 4 __________ AMPS (L1) __________ AMPS (L2) _________ AMPS (L3) _________ AMPS (RATED)
FAN 5 __________ AMPS (L1) __________ AMPS (L2) _________ AMPS (L3) _________ AMPS (RATED)
TEMPERATURE START-UP AFTER 24 HOURS OF OPERATION
AMBIENT TEMPERATURE 0F 0F
DESIGN BOX TEMPERATURE 0F 0F
OPERATING BOX TEMPERATURE 0F 0F
SUPERHEAT AT COMPRESSOR 0F 0F
SUCTION LINE TEMP. AT EVAPORATOR 0F 0F
SUPERHEAT AT EVAPORATOR 0F 0F
SUB-COOLING 0F 0F
LIQUID TEMPERATURE 0F 0F
PRESSURES (in cooling mode)
REFRIGERANT SUCTION PSIG TEMP AT COMPRESSOR 0F
REFRIGERANT DISCHARGE PSIG TEMP AT COMPRESSOR 0F
This manual suits for next models
379
Table of contents
Popular Fan manuals by other brands

Beacon Lighting
Beacon Lighting LUCCI AIRFUSION MOTO Installation, operation, maintenance & warranty information

Cumberland
Cumberland G54CBF16GA Installation and operation manual
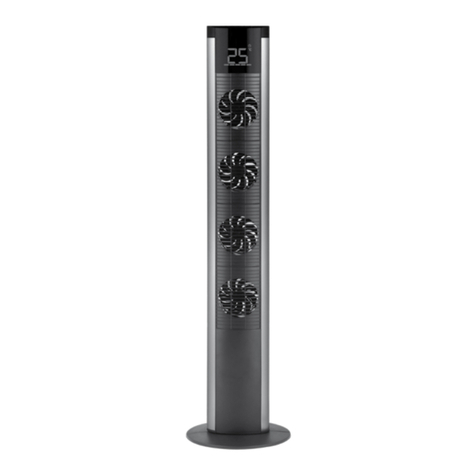
ARDES
ARDES AR5T128R Instructions for use
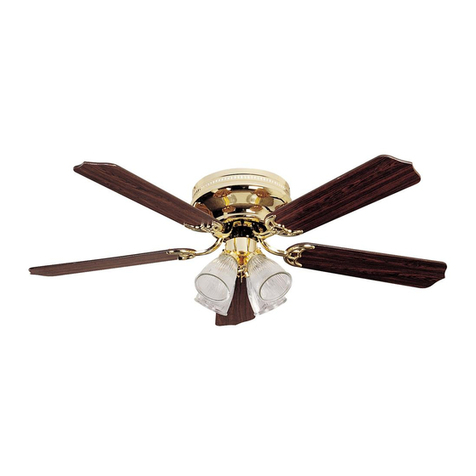
Litex
Litex BRC52AB5C installation guide
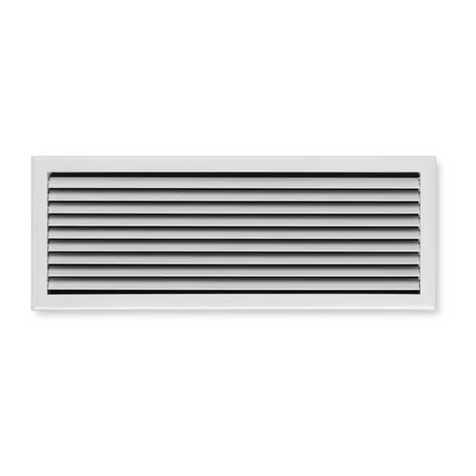
Trox Technik
Trox Technik X-GRILLE installation manual
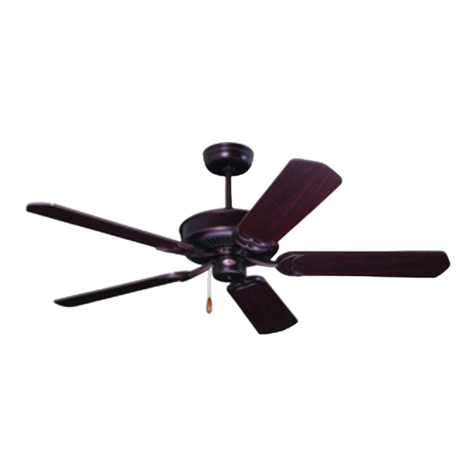
Emerson
Emerson NORTHWIND CF705AB03 owner's manual
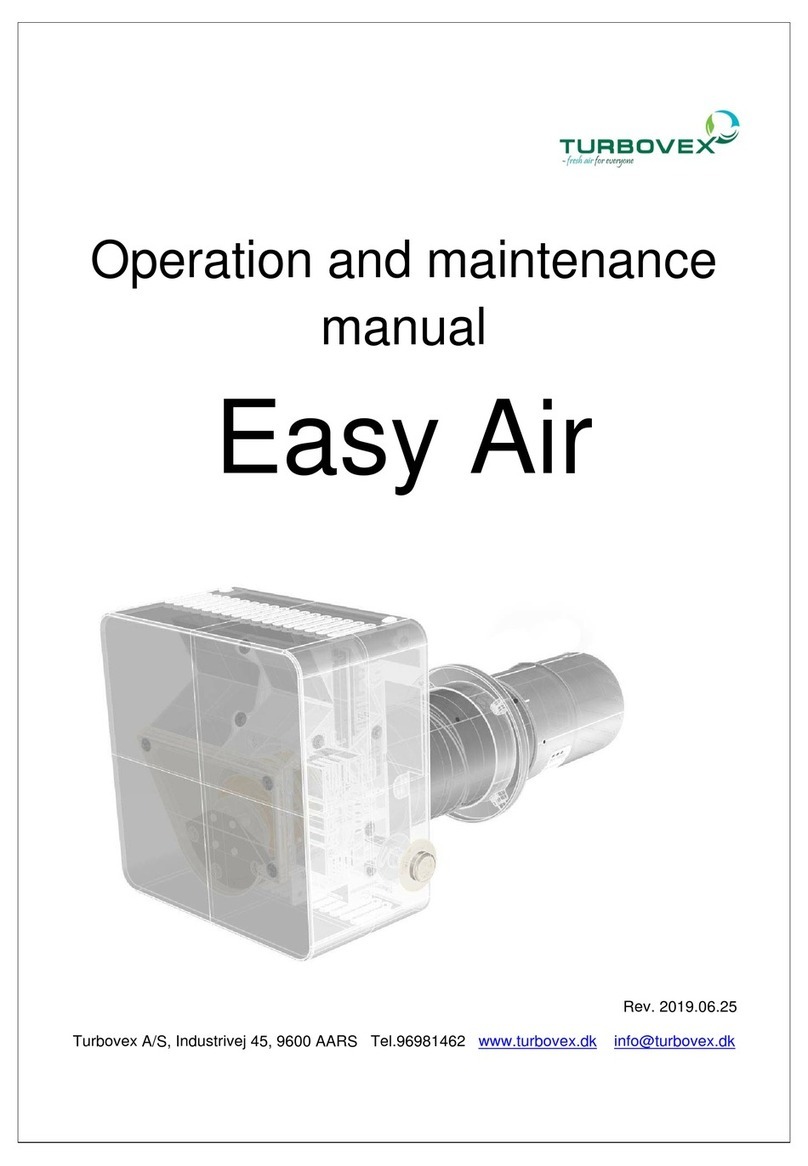
Turbovex
Turbovex Easy Air Operation and maintenance manual
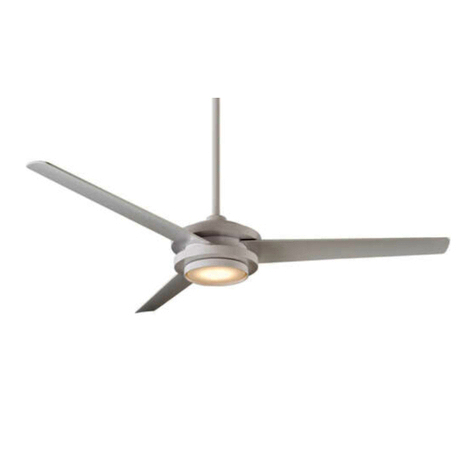
WAC
WAC Geos installation instructions
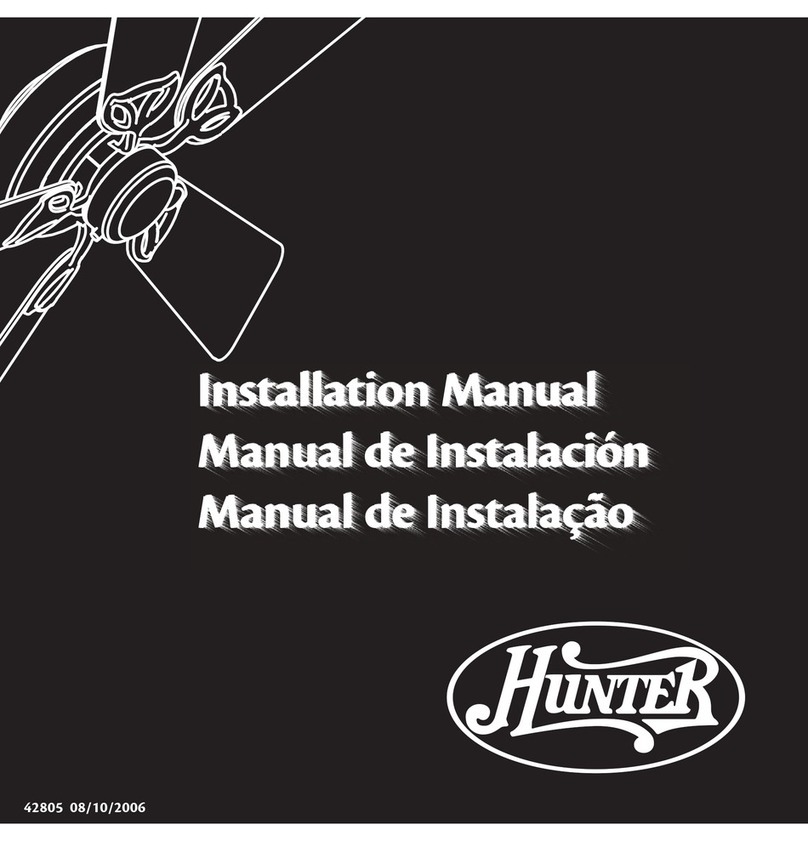
Hunter
Hunter 42805 installation manual

Hunter
Hunter Parkview 50999 installation manual
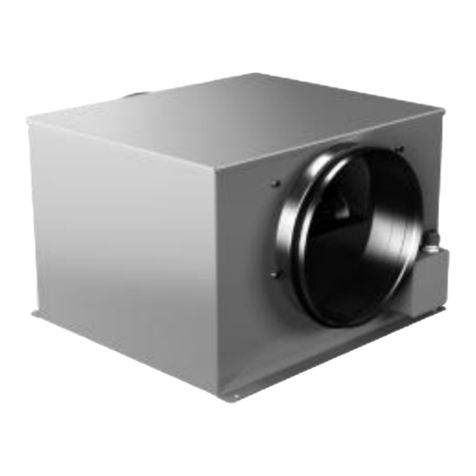
Rosenberg
Rosenberg GKH Series Operating instruction
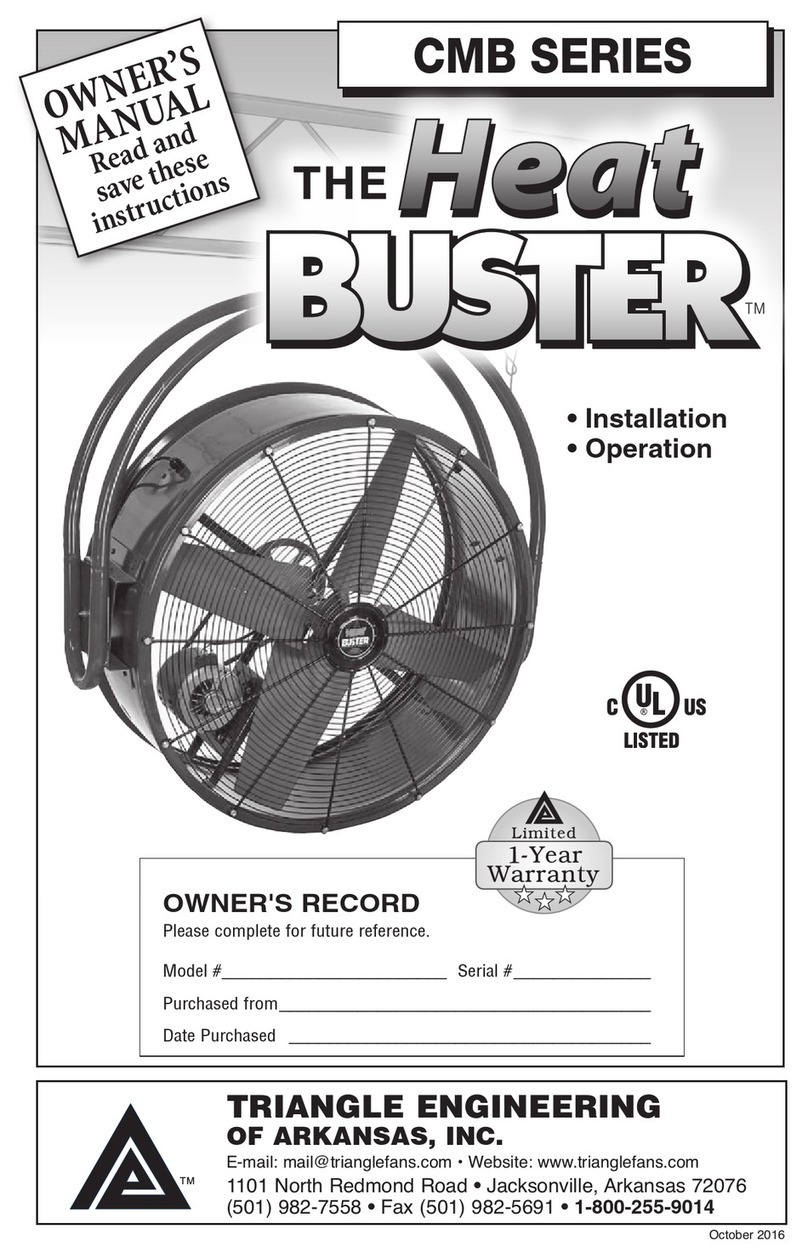
Triangle Engineering of Arkansas
Triangle Engineering of Arkansas Heat BUSTER CMB Series owner's manual