Rheodyne 8125 User manual

1.0 DESCRIPTION
Model 8125 is a six-port micro-scale
sample injector with a built-in needle port in
the handle for sample loading. Model 8126 is
the pneumatic version. The actuator of
Model 8126 is built around the injector and
allows both manual and automatic operation.
Five of the stator ports have a dual-size port
design and accommodate both 0.5 mm
(0.020") and 1/16" OD tubing. Port 3 only
accommodates 1/16" OD tubing and allows
the tubing to bottom out in the port for low
dispersion connections.
2.0 SUPPLIED WITH THE VALVE
Supplied with the valve in a separate bag
are RheFlex®Stainless Steel fitting sets for
all ports and the following items. A 5 µL
sample loop comes standard with the valve.
•HexKeys
• Wrench
• Needle Port Cleaner
• Vent Tubes
• Mounting Screws
• Needle Adapter Assembly
(Model 8126 only)
The #22 gauge needle supplied in the valve
should be removed from the needle port
before using the valve.
3.0 SPECIFICATIONS
• Maximum Operating Pressure: 48 MPa
(483 bar, 7000 psi)
• Maximum Operating Temperature:
Model 8125 - 80°C
Model 8126 - 50°C
• Flow Passage Diameters: 0.3 mm
(0.013") and 0.3 mm (0.012")
• Wetted Surfaces: stainless steel and an
inert polymer
• Gas Supply for Pneumatic Actuator: 0.4
MPa (4.1 bar, 60 psi) to 0.7 MPa (6.9 bar,
100 psi)
• Built-in position sensing switch
4.0 IMPORTANT SAFETY NOTICES
4.1 Warning: When using sample loops
larger than 100 µL, shield yourself from
mobile phase coming out of the needle port
when the valve is turned from INJECT to
LOAD. Example, 1 mL loop ejects 20 µL
upon decompression from 19 MPa (200 bar,
2898 psi).
4.2 Warning: When using the Needle Port
Cleaner, empty the syringe slowly to prevent
solvent from squirting back at you.
4.3 Caution: Rinse the valve after using
buffer solutions to prevent crystals from
forming, which can cause damage to the
rotor seal and stator face assembly.
5.0 USING PROPER NEEDLES AND
TUBING SIZES
5.1 SYRINGE NEEDLES
Use syringes with #22 gauge needles
without electrotaper and 90° (square cut)
point style. The wrong needle tip can cause
damage to the valve.
5.2 TUBING SIZES
Figure 2A shows how 0.5 mm (0.020") and
1/16" OD tubing can connect to five of the
valve ports in Models 8125 and 8126. For
low dispersion, use the 0.5 mm (0.020") OD
tubing for the sample loop. Since Port 3 is
positioned differently in the stator and the
internal geometry allows 1/16" OD tubing to
bottom out in the port, no cavity forms in the
stator port (see Figure 2B). Using 1/16" OD
tubing for the column connection will not
increase dispersion.
1/16" OD tubing can be used in the pump
port and the vent line ports. 1/16" OD tubing
can also be used for sample loops when
using sample volumes larger than 50 µL.
There is a negligible effect on overall
dispersion for these sample sizes.
6.0 INSTALLATION
a) To mount the valve on a panel, remove
the handle by loosening the two handle set
screws. Use the two set screws supplied to
fasten the valve to a panel.
b) Replace the handle by tightening the two
set screws on the two flats of the shaft.
c) Connect the two vent tubes supplied to
Ports 5 and 6. The outlet ends of both vent
tubes should be at the same horizontal level
as that of the needle port to avoid siphoning.
d) Connect the pump to Port 2 and the
column to Port 3. Leave the column
disconnected from the valve during initial
flushing.
Operating Instructions
Models 8125 and 8126
Manual and Pneumatic Micro-Scale Sample Injectors
Fig. 1. Flow diagram of Models 8125 and 8126.
ste
Waste
Position A (L
O
AD)
4
Need e Port
S
am
p
le Loo
p
P
um
p
Position B (INJE
C
T)
eed e
Po
r
t
P
u
m
Column
o
l
um
le Loo
p
Column
u
u
u
u
u
u
u
u
u
u
u
u
Fig. 2B. Port 3 design.
0.020” OD
0.5 mm Ferrule
1/16” OD
Cavity Volume = 1.9 µL
1/16” Ferrule
1/16” OD
1/16” Ferrule
#7010-010
Fig. 2A. Dual-size port design of five of the
stator ports.
Page 1 of 4
2320667A
9/99
Rheodyne LLC • A Unit of IDEX Corporation • 600 Park Court, Rohnert Park, CA 94928 • (707) 588-2000 • Fax (707) 588-2020
www.rheodyne.com

7.0 OPERATION
7.1 PNEUMATIC CONNECTIONS FOR
8126
Automatic operation requires a gas (air or
nitrogen) supply of 0.4 MPa (4.1 bar, 60 psi)
to 0.7 MPa (6.9 bar, 100 psi). Figure 3 shows
the suggested pneumatic and electrical
connections using a Model 7163 Solenoid
Valve.
7.2 CONNECTING THE NEEDLE
ADAPTER TO 8126
Use the Needle Adapter for automatic
unattended operation. Refer to Figure 4 and
proceed as follows:
a) Insert the Needle Adapter into the needle
port.
b) Push the Adapter to the bottom.
c) Insert screw through the holes in the
knob and Adapter walls and tighten to
fingertight.
d) Refer to Loading By Suction (Section
7.5.3) to use the Needle Adapter.
7.3 POSITION SENSING SWITCH IN
MODEL 8126
The position sensing switch in Model 8126
is recessed into the side of the actuator body.
The switch starts an external action such as
an event mark or a computer run.
The SPDT (single pole double throw)
switch has three electrical connections (see
Figure 5). One electrical wire will connect to
the C (common) terminal. If you want to
make contact when turning from LOAD to
INJECT, then connect the second electrical
wire to the NC (normally closed) terminal. If
you want to make contact when turning from
INJECT to LOAD, then connect the wire to
the NO (normally open) terminal.
The switch is rated for 125/250 VAC and 5A.
7.4 FLUSHING THE INJECTOR
In the INJECT position, flush the needle port
with about 1 mL of mobile phase using the
Needle Port Cleaner as shown in Figure 6.
At this time, the pump flushes the loop. See
Caution 4.2.
7.5 MANUAL LOOP LOADING
7.5.1 COMPLETE LOOP FILLING
In complete-filling, the volume of sample
injected is set by the volume of the loop (this
includes the valve passages). This method
produces the highest precision.
Overfill the loop with at least two to five
loop volumes of sample. Six to ten loop
volumes will provide even better precision.
An excess of sample is needed because
mobile phase near the wall of the loop is
displaced slowly due to the laminar flow
effect shown in Figure 7.
To completely fill the loop:
a) See Warning 4.1 and turn to LOAD.
b) Insert the syringe into the needle port.
You will feel tightness during the last 2-3
mm of travel as the needle passes through the
needle seal and then stops against the stator
face.
c) Load the sample.
d) Leave the syringe in and turn to INJECT.
7.5.2 PARTIAL LOOP FILLING
If you only have a small quantity of sample,
this is the method of choice. In the partial-
filling method the volume of sample injected
is set by the syringe. In this method, no more
than half a loop volume of sample should be
loaded into the loop. For example, load no
more than 10 µL into a 20 µL loop. With
larger than half the loop volume, some of the
sample is lost out Vent Line 6. This is
because sample flows down the center of the
loop at twice the average velocity due to the
laminar flow effect shown in Figure 7.
To partially load the loop:
a) In INJECT, use the Needle Port Cleaner
to flush out the needle port with about 1 mL
of mobile phase. This will flush out
contamination from the earlier injection.
This liquid will exit out Vent Line 5.
b) Follow steps a-d in Section 7.5.1.
7.5.3 LOADING BY SUCTION
Refer to Figure 8 and proceed as follows:
a) In LOAD, dip the tube attached to Port 6
into the sample.
b) Connect an empty syringe to the Needle
Adapter assembly and suck up sample into
the loop. Use of this assembly is shown in
Figure 8.
c) Leave the syringe in position and turn to
INJECT.
The syringe can be used many times before
it needs to be emptied.
Page 2 of 4
2320667A
9/99
Fig. 3. Pneumatic and electrical connections with
Model 8126.
Fig. 5. Location and detail of Position Sensing
Switch on Model 8126.
Fig. 4. Installation of Needle Adapter assembly.
Gas Supply
Controller
Needle
Suction Needle Adapter
8-32 x 11⁄4Screw
Syringe Barrel
Needle Port Cleaner
Handle Assembly
Needle Guide
Fig. 6. Use of Needle Port Cleaner.
Fig. 7. Laminar flow effect.
Flow
Sample
Tube Wall
Mobile Phase
Rheodyne LLC • A Unit of IDEX Corporation • 600 Park Court, Rohnert Park, CA 94928 • (707) 588-2000 • Fax (707) 588-2020
www.rheodyne.com

To load the loop with all of the available
sample, the loop should be at least four times
the volume of sample loaded. The loop is
first filled with mobile phase via the dip tube,
then the whole sample is drawn into the dip
tube and loop, followed by more mobile
phase. The sample is now sandwiched
between two zones of mobile phase in the
loop.
8.0 ADJUSTING FOR LEAKAGE OR
HIGHER PRESSURE OPERATION
There is a single pressure adjusting screw at
the handle end of the valve body. The handle
assembly is designed to be used as a tool for
adjusting this screw. If you need operation up
to a higher pressure or if there is a leak
between the stator and stator ring, loosen the
two set screws so that the handle slips down
the shaft and the two protrusions fit into the
slots on the adjusting screw. Tighten the
adjusting screw about 1/20th turn. If there is
still leakage at this new setting, repeat the
process. Replace the rotor seal if the leak
continues.
Note:When the valve is not panel mounted,
the adjusting screw can be hard to turn. In
this case, loosen the three stator screws 1/4
turn prior to adjusting the screw. Retighten
the stator screws before testing for leaks.
Replace the handle and tighten the two set
screws on the two flats of the shaft. Confirm
that the handle protrusions are out of the
slots in the adjusting screw before tightening
the set screws. This step is important. If the
handle engages the pressure adjusting screw
the shaft will not rotate between LOAD and
INJECT. See Figure 9.
Note: If the vent lines from Ports 5
and 6 do not have their outlet ends at
the same horizontal level as the
needle port, siphoning can result,
which is often misinterpreted as a leak.
A siphoning leak will stop when the vent
lines and needle port tube are empty. A leak
due to a damaged rotor seal will continue.
9.0 MAINTENANCE
The only parts that may need eventual
replacement are the rotor seal, isolation seal,
and stator face assembly.
The main causes of early failure are:
a) The wrong needle tip can damage the
stator face, which then causes deep
scratching of the rotor seal surface.
b) Abrasive particles in the sample can
scratch the rotor seal surface.
Genuine Rheodyne parts are easily replaced
by the following instructions. See Section
11.0.
9.1 MODEL 8125
9.1.1 DISASSEMBLY
To disassemble Model 8125, refer to Figure
10 and proceed as follows:
a) Remove the handle assembly.
b) Remove the three stator screws.
c) Remove the stator, stator face assembly,
and stator ring from the body (the stator face
assembly usually remains on the stator).
d) Pull the rotor seal off the pins.
e) Pull the isolation seal off the shaft
assembly.
9.1.2 REASSEMBLY
To reassemble Model 8125, refer to Figures
9, 10, and 11 and proceed as follows:
a) Slip the new isolation seal (open side
facing the handle) onto the stator end of the
shaft assembly next to the bearing ring.
b) Line up the new rotor seal as shown in
Figure 11. The rotor seal grooves face the
stator.
c) Replace the stator ring (with black gap
ring in place) so that the rotor pin falls
between the two milled flat surfaces of the
stator ring and the body locating pin enters
the mating hole in the body.
d) Place the pins in the new stator face
assembly into the mating holes in the stator.
e) Replace the stator and stator face
assembly on the valve so that the pin in the
stator ring enters the mating hole in the
stator.
f) Add the three stator screws. Tighten each
screw a 1/2 turn past fingertight.
g) Replace the handle and tighten the two
set screws on the two flats of the shaft.
Confirm that the handle protrusions are out
of the slots in the body before tightening the
set screws. This step is important. If the
handle engages the pressure adjusting screw
the shaft will not rotate between LOAD and
INJECT. See Figure 9.
9.2 MODEL 8126
9.2.1 DISASSEMBLY
To disassemble Model 8126, refer to
Figures 11, 12, 13, and 14, and proceed as
follows:
a) Remove the handle assembly.
b) Remove the three stator screws.
c) Remove the stator and stator face
assembly from the stator ring (the stator face
assembly usually remains on the stator).
Fig. 9. Valve handle acting as wrench to adjust
valve pressure adjusting screw.
Fig. 8. Loading by suction using the Needle
Adapter assembly.
Fig. 10. Exploded view of Model 8125.
Fig. 11. Correct position of rotor seal (grooves
face the stator).
Handle Assembly
Handle Set Screws
Needle Guide
Pressure Adjusting Screw
Body
Thrust Bearing
Spring Washers
Needle Port Tube Assembly
Bearing Ring
Isolation Seal
Rotor Seal
Body Locating Pin
Gap Ring
Position Sensing Switch
Stator Ring
Stator Locating Pin
Stator Face Assemby
Stator
Stator Screws (3)
Page 3 of 4
2320667A
9/99
Shaft Assembly *
* Shaft Assembly includes Rotor, Shaft, and Pins.
Rheodyne LLC • A Unit of IDEX Corporation • 600 Park Court, Rohnert Park, CA 94928 • (707) 588-2000 • Fax (707) 588-2020
www.rheodyne.com

d) Remove the two hex screws in the stator
ring. To make it easier to pull the stator ring
off, screw the two hex screws into two of the
three stator screw holes. Take the stator ring
off by pulling on the two hex screws while
rocking the stator ring back and forth (see
Figure 13). Pull the rotor seal off the four
pins.
Note: If the shaft assembly comes out with
the stator ring, ensure that the gear goes back
into the actuator body and lines up correctly
with the two racks on either side. The racks
can be moved up and down to align the
punch marks on the racks with the punch
marks on the gear (see Figure 14).
e) Remove the isolation seal (it may have
come off with the stator ring).
9.2.2 REASSEMBLY
To reassemble Model 8126, refer to Figures
11, 12, 13, and 14 and proceed as follows:
a) Mount the new isolation seal with the
open side facing the handle.
b) Line up the new rotor seal as shown in
Figure 11. The rotor seal grooves face the
stator. The notch on the rotor seal's metal
band is at 12 o'clock.
c) Replace the stator ring so that the two
pins in the stator ring enter the mating holes
in the actuator body. The two drain slots on
the stator ring must be in the down position.
Replace the two hex screws in the stator ring.
d) Follow steps d-g from Section 9.1.2.
9.3 POSITION SENSING SWITCH IN
MODEL 8125
The position sensing switch is standard in
Model 8125. The switch is a magnetic reed
switch actuated by a magnet sealed inside the
shaft. The switch is rated for 100 V at 200
mA.
To replace or remove the switch:
a) Remove the handle assembly.
b) Remove the three stator screws.
c) Remove the stator, stator ring, and stop
ring.
d) Pull the switch out of the stop ring.
e) Replace with new switch, or leave the
hole empty if the switch is not needed.
f) Follow the steps in Section 9.1.2 to
reassemble.
10.0 OPERATING SUGGESTIONS AND
TROUBLESHOOTING
10.1 LEAKAGE
If you see liquid between the stator and
stator ring, or from the needle port or a vent
tube, tighten the pressure adjusting screw as
explained in Section 8.0. If this fails to stop
the leak then replace the rotor seal and/or
stator face assembly.
10.2 NEEDLE SEAL LEAKAGE
Since the outside diameter of syringe
needles can vary, the needle seal (Teflon1
sleeve in the rotor seal) may not seal
correctly around a needle that is smaller than
average. This will result in the loss of
accuracy in loading the sample. To make a
good seal, remove the needle from the needle
port and push in on the plastic needle guide
with the eraser end of a pencil. Repeat if
necessary.
10.3 USE OF AQUEOUS BUFFERS OR
SALT SOLUTIONS
To prevent the formation of salt crystals in
the valve which can scratch the rotor seal,
flush out the flow passages and the needle
port with water after using salt solutions.
10.4 USE OF HIGH pH SOLUTIONS
The standard rotor seal in Models 8125 and
8126 is Vespel1, a polyimide with good wear
resistance. Vespel is sensitive to alkaline
attack when exposed to solutions having a
pH of 10 or more. Use a PEEK or Tefzel1
rotor seal for alkaline solutions.
10.5 ACCURACY OF SAMPLE LOOPS
Sample loop sizes are not actual values.
Actual volumes can differ by ± 10% for a 20
µL loop. Smaller loops show greater
differences. For actual injection volume, use
the partial-filling manual sample loading
method.
11.0 RECOMMENDED SPARE PARTS
Rheodyne offers a RheBuild™ Kit for
maintaining the quality performance of your
valve. The kit includes all the necessary
parts, tools, and instructions.
8125-999 RheBuild Kit for 8125 and 8126
12.0 WARRANTY
All Rheodyne products are warranted
against defects in materials and
workmanship for a period of one year
following the date of shipment by Rheodyne.
Rheodyne will repair or replace any
Rheodyne product that fails during the
warranty period due to a defect in materials
or workmanship at no charge to the
customer. The product must be returned to
Rheodyne’s factory in original packaging or
equivalent, transportation prepaid. Damage
occurring in transit is not covered by the
warranty. This limited warranty is
Rheodyne’s sole warranty of its products,
and all other warranties of merchantability or
fitness for any particular purpose are hereby
disclaimed. Under no circumstances will
Rheodyne be liable for any consequential or
incidental damages attributable to a claimed
failure of a Rheodyne product, even if
Rheodyne has been placed on notice of
possibility of such damages.
Fig. 13. Removing the stator ring with two hex
screws.
Set Screws (2)
Needle Guide
Handle Assembly
Shaft Assembly*
* Shaft Assembly includes Rotor, Shaft, and Pins.
Seal Pins (4)
Needle Port Tube
Rotor Seal
Stator Face Assembly
Drain Slots
Stator Ring
Stator Stator Screws
Isolation SealNotch
Fig. 12. Exploded view of Model 8126.
Page 4 of 4
2320667A
9/99
1Vespel, Tefzel, and Teflon are trademarks of E.I. DuPont.
Fig. 14. Alignment of punch marks.
Four Punch Marks
in Line
Correct Meshing of Gear
and Rack Teeth
Rheodyne LLC • A Unit of IDEX Corporation • 600 Park Court, Rohnert Park, CA 94928 • (707) 588-2000 • Fax (707) 588-2020
www.rheodyne.com
This manual suits for next models
1
Other Rheodyne Laboratory Equipment manuals
Popular Laboratory Equipment manuals by other brands
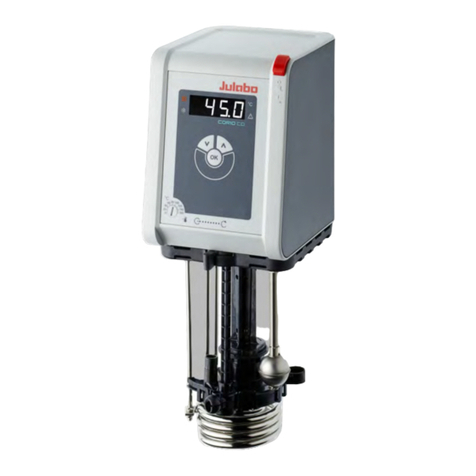
Julabo
Julabo CORIO CD operating instructions

MELAG
MELAG Cliniclave 45 D Technical manual

Beckman Coulter
Beckman Coulter JA-25.50 Instructions for use
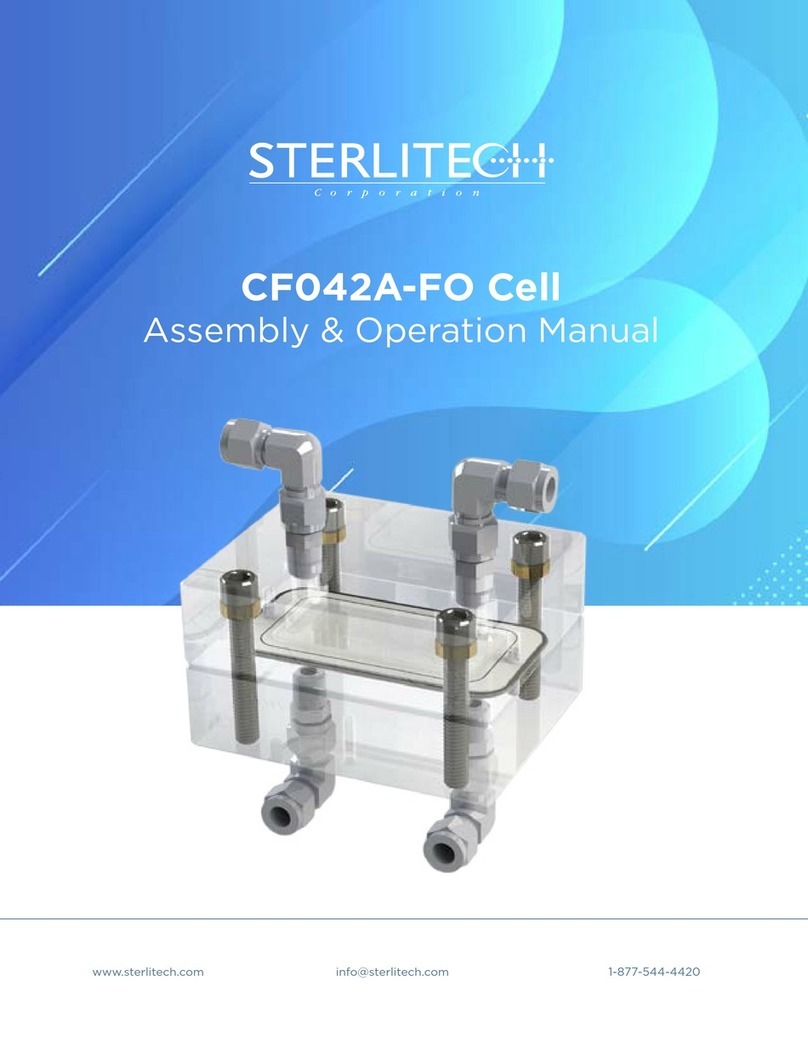
Sterlitech
Sterlitech CF042A-FO Cell Assembly & operation manual
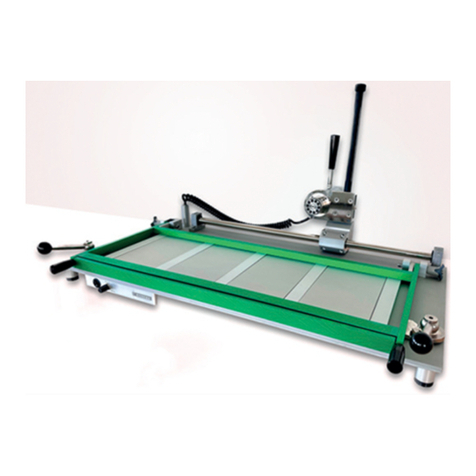
Bioreba
Bioreba HOMEX 7 user guide
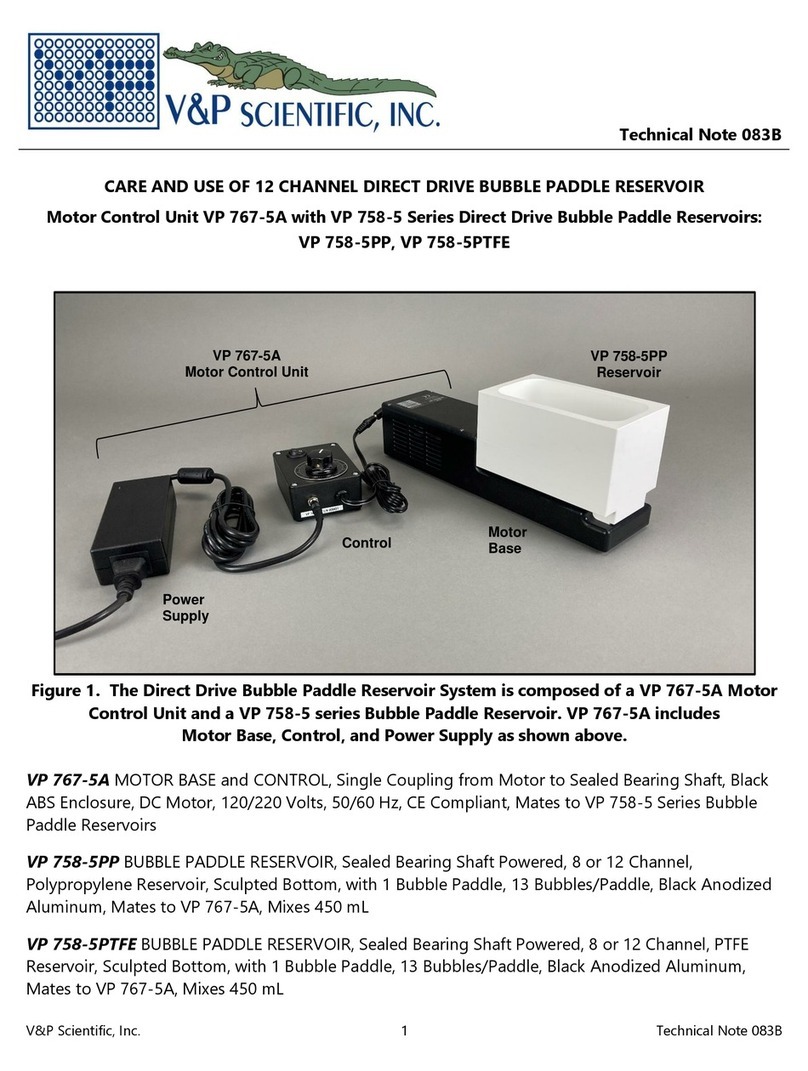
V&P Scientific
V&P Scientific VP 767-5A Series Technical notes