Rhymebus RM6E1 Series User manual

1
http://www.rhymebus.com.tw
2020.08.28 Edition
Thank you for using RHYMEBUS RM6E1 series drive.
For proper operations and safety purposes, please read complete manual carefully (enclose
CD inside the box) or visit RHYMEBUS website: http://www.rhymebus.com.tw to download
the operation manual. To prevent any possible dangers ,only the qualified personnel may
proceed with the installation. Please pay attention to the safety precautions marked with
“DANGER” or “CAUTION” in complete manual before installation.
DANGER
User may cause the casualty or serious damages if user does not abide by the
instructions of the manual to execute the tasks.
CAUTION
User may cause injuries to the people or damage the equipment if user does not
abide by the instructions of the manual to execute the tasks.
※Although the “ ” mark may indicate minor damages, serious damages or injuries may be possibly
incurred if the caution is not under user’s attention.
Type
Symbol
Function
Description
Power
Source
R/L1,S/L2,T/L3
AC power source input
terminals
Three-phase; sinusoidal power source input
terminal. For the single-phase power source
110/220V, please connect only R/L1,S/L2
terminals.
Motor
U/T1,VT2,W/T3
Drive outputs to motor
terminals
The terminals output three phase variable
frequency and voltage to motor.
Power
and Brake
P⊕,NΘ
Dynamic braking unit
connecting terminal
The terminals between P⊕and NΘconnect
dynamic braking unit (option).
P⊕,PR
External braking resistor
connectingterminal
The terminals between P⊕and PR connect
external braking resistor (option).
Grounding
Grounding terminal
Ground the drive in compliance with the NEC
standard or local electrical code.
RM6E1 Series
Simple Version
Operation Manual
Terminals of Main Circuit
XB200161

2
Three-phase,
50/60Hz
AC power input:
(Single Phase-Only
R/L1, S/L2 Terminals) RM6E1
VR 1kΩ, 1/4W
Multi-function Input 1
Induction Motor
Multi-function Outputs (Relay Type)
AC250/0.2A COSθ=0.3
Braking Resistor (option)
R/L1
S/L2
T/L3
R/L1
S/L2
T/L3
X1
X2
X3
X4
COM
IM
U/T1
V/T2
W/T3
PR P N
Ta
Tc
PP
V+
AI
GND
I V
Multi-function Input 2
Multi-function Input 3
Multi-function Input 4
FM
GND
Analog Output
DC0~10V(0~20mA)
DC2~10V(4~20mA)
Analog Inputs
DC0~10V(0~20mA)
DC2~10V(4~20mA)
Shielded Wire
Twisted-Pair Shielded Wire
P
ON
DSW1
JP1
JP2
FMI FMV
JP3
KP-601/
Modbus Port
SINK SOURCE
24V 12V
JP4
Multi-function Input 5
Multi-function Input 6 X5
X6
Tb
※JP1: I/V; AI signal selection
“I” position: AI-GND terminal is inputted with the current signal.
“V” position: AI-GND terminal is inputted with the voltage signal.
※JP2: SINK / SOURCE selection
The signal input selection of multi-function input terminal.
※JP3: FMI / FMV; FM signal selection
“FMI” position: Output current signal.
“FMV” position: Output voltage signal.
※JP4: 12V / 24V; V+ signal selection
“12V” position: Output DC12V between V+ and GND terminals.
“24V” position: Output DC24V between V+ and GND terminals.
※DSW1: The terminal resistor selection of Modbus
communication(the internal resistance is 100Ω).
Control Terminal Mapping
ON
1
DSW1
X4 Tc
Ta
JP1
JP2
JP3
TB1 TB2
X3 COM X2 X1 FM GND AI V+
JP4
X5
X6 Tb
Description of Control Terminals
Type
Symbol
Function
Description
Control circuit terminal
Control
power
V+
*Note 3
Power terminal for
analog input control
DC+12V position: Maximum supplied current is 20mA.
DC+24V position: Maximum supplied current is 50mA.
GND
Common terminal for
analog input control
Common terminal for control power (12V/24V) and analog input
terminal (AI).
AI
*Note 1
Analog signal input
terminal
The function is set by F5.01(default: frequency command)
DC 0~10V / 2~10V (20kΩ);DC 0~20mA / 4~20mA (250Ω)
Input terminals
X1
Multi-function input
terminal 1
Short the terminal of X1 with COM and set the function F5.19.
(default: forward command)
X2
Multi-function input
terminal 2
Short the terminal of X2 with COM and set the function F5.20.
(default: reverse command)
X3
Multi-function input
terminal 3
Short the terminal of X3 with COM and set the function F5.21.
(default: jog command)
X4
Multi-function input
terminal 4
Short the terminal of X4 with COM and set the function F5.22.
(default: reset command)
Descriptions of Terminal and Wiring Diagram
Control Terminals

3
Type
Symbol
Function
Description
Control circuit terminal
Control
power
X5
Multi-function input
terminal 5
Short the terminal of X5 with COM and set the function F5.23.
(default: disable)
X6
Multi-function input
terminal 6
Short the terminal of X6 with COM and set the function F5.24.
(default: disable)
COM
Input/output
common terminal
The common terminal of input control signal.
Output terminals
FM
*Note 2
Analog signal output
terminal
The function is set by F5.12. (default: output frequency)
DC 0~10V / 2~10V (1mAMax);DC 0~20mA / 4~20mA
(500ΩMax)
Ta
Multi-function output
terminals
(default:fault
detection)
N.O (normally open contact; a contact)
The function is set by F5.26,
(capacity: AC250V, 0.2AMax, cosθ=0.3)
Tb
N.C (normally closed contact; b contact)
The function is set by F5.26
(capacity: AC250V, 0.2AMax, cosθ=0.3)
Tc
Common terminal for Ta,Tb
Note 1: I/V selection is set by JP1(default: V);
Note 2: FMI/FMV selection is set by JP3 (default: FMV);
Note 3: 24V/12V selection is set by JP4 (default: 12V);
Func.
Name
Descriptions
Range of
Setting
Unit
Default
F0.00
Drive
Information
0: Software version
1: Drive model number
2: Drive rated current
3: Drive running hours
4: Drive supply power
time
5: Software checksum
code
─
─
─
F0.01
Parameter Lock
0: Parameters are changeable
1: Parameters are locked
0, 1
─
0
F0.02
Parameter
Password Setting
Set the password for the parameter protection
0~9999
1
0
F0.03
Parameter
Password Unlock
Unlock the passwords for the parameters
0~9999
1
─
F0.05
Power Source
The value of setting according to the actual
power source
100.0~120.0
*Note 3
0.1V
110.0
*Note 3
190.0~240.0
*Note 4
220.0
*Note 4
340.0~480.0
*Note 5
380.0
*Note 5
F0.08
~
F0.13
Fault Record 1
~
Fault Record 6
0: Fault code
1: Output current at drive fault
2: DC bus voltage at drive fault
3: Output frequency at drive fault
─
─
─
F0.18
Parameter
Display Selection
of Password lock
1: Paramerter cannot be changed after F0.18
locked, but it can display the setting value.
2: Paramerter cannot be changed after F0.18
locked, but it cannot display the setting value.
0~1
0
F0.20
Default Setting
0: Disable
─
─
0
CLF: Clear fault records
dF60: Default the factory setting of 60Hz
dF50: Default the factory setting of 50Hz
SAv: Store setting
rES: Resume setting
rdEE: Read the parameters from drive to digital
keypad
UrEE: Write the parameters from digital keypad
to drive
Parameter List [ F0 System Parameter ]

4
Func.
Name
Descriptions
Range of
Setting
Unit
Default
F1.00
Start Command
Selection
Start command
Rotation direction
0~11
─
3
0
FWD or REV command
FWD or REV command
1
FWD command
REV command
2
Operation panel
FWD, REV command
3
Forward
4
Reverse
5
Reverse command
6~7
Reserved
Reserved
8
Communication control
Communication control
9
Communication control
Reverse command
10
Forward command
Communication control
11
Operation panel
Communication control
F1.01
Primary
Frequency
Command
Selection
0: Frequency command by analog input selection
1: Frequency command by operation panel.
2: Motor rotation speed setting by operation panel.
3: Machine speed setting by operation panel.
4: Frequency command by multi-function input terminal as
UP/DOWN command.
5: Frequency command by communication terminal.
0~5
─
1
F1.02
Secondary
Frequency
Command
Selection
0: Frequency command by analog input selection(F1.03).
1: Frequency command by operation panel.
2: Frequency command by multi-function input terminal as
UP/DOWN command.
0~2
─
0
F1.03
Analog
Input
Selection
0: Pot knob+ AI
1: Pot knob –AI
2: AI –Pot knob
3: Pot knob or AI
(switch by multi-function
input terminal)
4: Pot knob
5: AI
0~5
─
0
F1.04
“Pot knob”
Command
Source Selection
0: From drive’s operation panel.
1: From external keypad(KP-601).
0, 1
─
0
F1.05
Validity of STOP
of the Operation
Panel
0: Start command from the terminal, STOP key disabled.
1: Start command from the terminal, STOP key enabled.
0, 1
─
1
F1.06
Frequency
Command
Selection
(operation panel)
0: In the monitor mode, frequencycommand cannot be
changed.
1: In the monitor mode, frequency command is changeable.
0, 1
─
1
F1.07
Frequency
Command
Auto-Storing
(operation panel)
0: In the monitor mode, the frequency command cannot be
stored.
1: In the monitor mode, the frequency
command can be stored
automatically after 3 minutes.
0, 1
─
1
F1.08
Main Display
Selection
Control panel have 8 display option
1~8
─
1
1: Output frequency
2:Frequency command
3: Output voltage
4: DC bus voltage
5: Output current
6: Display mode 6(F1.09)
7: Display mode 7(F1.10)
8: Display mode 8(F1.11)
F1.09
Display
Mode 6
0: Terminal status
1: Temperature of heatsink
2: Motor rotation
speed(RPM)
3: Machine speed(MPM)
4: The sector of sequential
operation control
5: The cycle of sequential
operation control
6: Counting value
7: Current limit level
8: Primary frequency command
9: Secondary frequency
command
10: PID command
11: PID feedback
0~11
─
0
F1.10
Display
Mode 7
0~11
─
1
F1.11
Display
Mode 8
0~11
─
2
Parameter List [ F1 Operation Parameter ]

5
Func.
Name
Descriptions
Range of
Setting
Unit
Default
F1.12
Number of Motor
Poles
Determination of RPM display value.
2~10
2P
4P
F1.13
Machine Speed
Ratio
Set the ratio of machine speed. This function determines
MPM display value.
0.00~500.00
0.01
20.00
F1.14
Digits of Decimal
Value
(MachineSpeed)
Select the digits of decimal values displaying the machine
speed.
0~3
─
0
F1.14
Digits of
DecimalValue
(MachineSpeed)
Select the digits of decimal values displaying the machine
speed.
0~3
─
0
F1.17
SPEC Key
Setting
Same function as multi-function input
-28 ~ +28
*Note 7
─
0
F1.18
SPEC Key
Self-Holding
Function
0: Disable
1: Enable
0,1
─
0
F1.19
Stop Mode
0: Ramp to stop + DC braking
1: Coast to stop
2: Coast to stop+ DC braking
0~2
─
0
F1.20
Reverse
Prohibition
0: Reverse rotation allowed
1: Reversal rotation NOT allowed
0,1
─
0
F1.21
Switching
Frequency
The setting value is higher and the motor noise is lower.
0~6
─
2
*Note 8
F1.22
Overload
Decrease
Switching
Frequency
0:The switching frequency will not be adjusted by the load
of current.
1:The swithching frequency will be auto-adjusted
according to the load of current.
0,1
─
1
F1.23
Number of
Tolerance to
Drive Fault
Set the number of tolerance to drive fault conditions when
OC, faults are occurred during the certain time period.
0~16
1
0
Func.
Name
Descriptions
Range of
Setting
Unit
Default
F2.00
Primary Speed
(Preset Speed 1)
Multi-speed
level 4
command
Multi-speed
level 3
command
Multi-speed
level 2
command
Multi-speed
level 1
command
0.00~
400.00
0.01Hz
50.00
*Note 1
OFF
OFF
OFF
OFF
60.00
*Note 2
F2.01
Preset Speed 2
OFF
OFF
OFF
ON
10.00
F2.02
Preset Speed 3
OFF
OFF
ON
OFF
20.00
F2.03
Preset Speed 4
OFF
OFF
ON
ON
30.00
F2.04
Preset Speed 5
OFF
ON
OFF
OFF
0.00
F2.05
Preset Speed 6
OFF
ON
OFF
ON
0.00
F2.06
Preset Speed 7
OFF
ON
ON
OFF
0.00
F2.07
Preset Speed 8
OFF
ON
ON
ON
0.00
F2.08
Preset Speed 9
ON
OFF
OFF
OFF
0.00
F2.09
Preset Speed 10
ON
OFF
OFF
ON
0.00
F2.10
Preset Speed 11
ON
OFF
ON
OFF
0.00
F2.11
Preset Speed 12
ON
OFF
ON
ON
0.00
F2.12
Preset Speed 13
ON
ON
OFF
OFF
0.00
F2.13
Preset Speed 14
ON
ON
OFF
ON
0.00
F2.14
Preset Speed 15
ON
ON
ON
OFF
0.00
F2.15
Preset Speed 16
ON
ON
ON
ON
0.00
F2.16
Jog Speed
Jog speed
6.00
F2.17
Reference
Frequency of
Accel/Decel Time
The frequency corresponding to accel/decel time.
0.01~
400.00
0.01Hz
50.00
*Note1
60.00
*Note2
F2.18
Primary
Acceleration Time
The acceleration time of primary speed, preset speed
5~16, and jog speed.
0.0~
3200.0
0.1
sec
5.0
Parameter List [ F2 Operation Parameter ]

6
Func.
Name
Descriptions
Range of
Setting
Unit
Default
F2.19
Primary
DecelerationTime
The deceleration time of primary speed, preset speed
5~16, and jog speed.
0.0~
3200.0
0.1
sec
5.0
F2.20
Acceleration Time
of Preset Speed 2
Acceleration time of preset speed 2
0.0~
3200.0
0.1
sec
5.0
F2.21
Deceleration Time
of Preset Speed 2
Deceleration time of preset speed 2
0.0~
3200.0
0.1
sec
5.0
F2.22
Acceleration Time
of Preset Speed 3
Acceleration time of preset speed 3
0.0~
3200.0
0.1
sec
5.0
F2.23
Deceleration Time
of Preset Speed 3
Deceleration time of preset speed 3
0.0~
3200.0
0.1
sec
5.0
F2.24
Acceleration Time
of Preset Speed 4
Acceleration time of preset speed 4
0.0~
3200.0
0.1
sec
5.0
F2.25
Deceleration Time
of Preset Speed 4
Deceleration time of preset speed 4
0.0~
3200.0
0.1
sec
5.0
F2.26
Secondary
Acceleration Time
Multi-function input terminals select the secondary
acceleration time.
0.0~
3200.0
0.1
sec
5.0
F2.27
Secondary
Deceleration Time
Multi-function input terminals select the secondary
deceleration time.
0.0~
3200.0
0.1
sec
5.0
F2.28
Set S-curve for
Accel/Decel Time
Set S-curve to slow the acceleration and deceleration
at start and stop.
0.0~5.0
0.1
sec
0.0
F2.30
Limitation of Output
Voltage
0: Output voltage of V/F pattern is not limited.
1: Output voltage of V/F pattern is limited
(voltage compensation disabled).
0,1
─
0
F2.31
V/F Pattern
Selection
0: Linear
1: Energy saving mode
(auto-adjust V/F according
to the loads)
2: Square curve
3: 1.7th power curve
4: 1.5th power curve
0~4
─
0
F2.32
Maximum Output
Frequency
Maximum output frequency of drive
0.1~400.00
0.1Hz
50.0
*Note1
60.0
*Note2
F2.33
Starting Frequency
Starting frequency of drive’s output frequency.
0.1~10.0
0.1Hz
0.5
F2.34
Starting Voltage
The voltage corresponds to the output starting
frequency.
0.1~50.0
*Note3,4
0.1Vac
8.0
*Note3,4
0.1~100.0
*Note5
12.0
*Note5
F2.35
Base Frequency
The frequency corresponds to the base xvoltage in V/F
pattern.
0.1~400.00
0.1Hz
50.0
*Note1
60.0
*Note2
F2.36
Base Voltage
The voltage corresponds to the base frequency in V/F
pattern.
0.1~255.0
*Note3,4
0.1Vac
220.0
*Note3,4
0.1~510.0
*Note5
380.0
*Note5
F2.37
V/F Frequency1
Frequency at the first point of V/F pattern
0.0~399.9
0.1Hz
0.0
F2.38
V/F
Voltage 1
Voltage at the first point of V/F pattern
0.0~255.0
*Note3,4
0.1Vac
0.0
0.0~510.0
*Note5
F2.39
V/F Frequency 2
Frequency at the second point of V/F pattern.
0.0~399.9
0.1Hz
0.0
F2.40
V/F
Voltage 2
Voltage at the second point of V/F pattern.
0.0~255.0
*Note3,4
0.1Vac
0.0
0.0~510.0
*Note5
F2.42
Jump Frequency 1
Avoid mechanical resonance point 1.
0.0~400.00
0.1Hz
0.0
F2.43
Jump Frequency 2
Avoid mechanical resonance point 2.
0.0~400.00
0.1Hz
0.0
F2.44
Jump Frequency 3
Avoid mechanical resonance point 3.
0.0~400.00
0.1Hz
0.0
F2.45
Jump Frequency
Range
Set the range of the jump frequency 1, 2, 3.
0.0~25.5
0.1Hz
0.0
F2.47
Frequency Upper
Limit
The upper limit of output frequency (1.00=maximum
output frequency)
0.00~1.00
0.01
1.00
F2.48
Frequency Lower
Limit
The lower limit of output frequency (1.00=maximum
output frequency)
0.00~1.00
0.01
0.00

7
Func.
Name
Descriptions
Range of
Setting
Unit
Default
F3.00
Holding Frequency
The drive accelerate to the holding frequency and
running at constant speed.
0.0~400.00
0.1Hz
0.5
F3.01
Holding Time Interval
The drive runs at holding frequency by constant
speed and running the time interval.
0.0~360.0
0.1sec
0.0
F3.03
Stall Prevention Level
at the Acceleration
If stall is occurred during acceleration, the motor
keeps running at the constant speed(200%: Off).
30%~200%
of drive rated
current
1%
170
F3.04
Stall Prevention Level
at the Constant
Speed
If stall is occurred at constant speed running, the
motor speed is decreased(200%: Off).
30%~200%
of drive rated
current
1%
160
F3.05
Acceleration Time for
Stall Prevention at the
Constant Speed
Set the acceleration time for the stall prevention of
the constant speed.
0.1~3200.0
0.1sec
5.0
F3.06
Deceleration Time for
Stall Prevention at the
Constant Speed
Set the deceleration time at the stall prevention of
the constant speed.
0.1~3200.0
0.1sec
5.0
F3.07
Deceleration Stall
Prevention
0: Deceleration stall prevention: Disabled
1: Deceleration stall prevention: Enabled
0,1
─
1
F3.10
Frequency Response
Time of Motor Slip
Compensation
Set the frequency response time of motor slip
compensation. Unit: 5ms
1~255
1
40
F3.12
Automatic Boost
Voltage Range
According to the load condition, adjust the output
voltage of the V/F Pattern (0.0: Off).
0.0~25.5
0.1
1.0
F3.13
Response Time of
Automatic Boost
Voltage
Set the response time of automatic boost voltage
range.
1~255
1ms
60
F3.15
Voltage
Compensation for
Current Oscillation
Adjust the voltage according to the current
oscillation.
0.00~2.55
0.01
0.10
F3.16
Response Time of
Voltage
Compensation for
Current Oscillation
Adjust the response time of voltage compensation
according to current oscillation
(0: Off).
0~250
1
10
F3.18
Automatic Voltage
Regulation(AVR)
0: Disable
1: Enable
0, 1
─
1
F3.19
Response Time
of AVR
Set the response time of automatic voltage
regulation.
0~255
1ms
50
F3.21
DC Braking Level
Set the current level of DC braking
0~150%
of drive
rated current
1%
50
F3.22
DC Braking
Response Time
Adjust the response time according to DC braking.
1~255
1ms
10
F3.23
Time Interval of DC
Braking at Start
Set the time interval for DC braking before drive
starts.
0.0~60.0
0.1sec
0.0
F3.24
Time Interval of DC
Braking at Stop
Set the time interval for DC braking at drive stops.
0.0~60.0
0.1sec
0.5
F3.25
DC Braking
Frequency at Stop
Active frequency level of DC braking at stop.
0.1~60.0
0.1Hz
0.5
F3.27
Active Level
of Dynamic Brake
Dynamic brake activates when the DC bus voltage
is over the setting.
Function disable setting:
100/200V series: 410
400V series: 820
350~410
*Note3,4
1Vdc
390
*Note3,4
700~820
*Note5
780
*Note5
F3.28
Pulse Setting of
BrakingTransistor
Set the pulse width of drive baking signal.
10~90
1%
50
F3.30
Operation Selection at
Instantaneous Power
Failure
0: Drive cannot be restarted
1: Drive can be restarted
2: Ramp to stop (please refer to theF3.31~F3.35)
3: When the power is restored during
the ramp to stop interval, the drive
re-accelerates again
0~3
─
0
Parameter List [ F3 Control Parameter ]

8
Func.
Name
Descriptions
Range of
Setting
Unit
Default
F3.31
The Voltage Level
Setting at Power
Failure
Set the voltage level of power source for ramp to
stop. When the voltage of power input is lower than
the setting level, drive ramps to stop.
75.0~96.0
*Note 3
0.1V
87.5
*Note 3
150.0~192.0
*Note 4
175.0
*Note 4
300.0~384.0
*Note 5
320.0
*Note 5
F3.32
Subtracted Frequency
of Deceleration at
Power Failure
When the power failure, the output frequency =
drive’s original output frequency - subtracted
frequency.
0.0~20.0
0.1Hz
3.0
F3.33
Deceleration Time 1
at Power Failure
Set a deceleration time down to the turning
frequency set in (F3.35).
0.0~3200.0
0.1sec
5.0
F3.34
Deceleration Time 2
at Power Failure
Set a deceleration time below the turning frequency
set in (F3.35).
0.0~3200.0
0.1sec
5.0
F3.35
Turning Frequency at
Power Failure
Set the turning frequency level at power failure that
the deceleration time is switched from the F3.33
setting to the F3.34 setting.
0.0~400.00
0.1Hz
0.0
F3.37
The Current Level of
Speed Tracing
When the current large than the tracing current, the
output frequency is tracing downward.
0~200%
of drive
rated current
1%
150
F3.38
Delay Time for Speed
Tracing
Set the output delay time before the speed tracing.
0.1~60.0
0.1sec
0.5
F3.39
The V/F Pattern of
Speed Tracing
Set the percentage of V/F output voltage at the
speed tracing.
0~100%
1%
100
Func.
Name
Descriptions
Range of
Setting
Unit
Default
F4.00
Grounding Fault
Protection (GF)
0: Disable
1: Enable(GF)
0,1
─
1
F4.01
Grounding Detection
Level
Detecting if the unbalanced current is over the
setting level
30~100%
of drive
rated current
1%
70
F4.02
Grounding Detection
Sensitivity
Detect the sensitivity of grounding.
1~255
1 time
10
F4.05
Accumulating
Number of
Over-Current
Limitation at 200%
Limitation
When the accumulating numbers of drive over
current are over the accumulating numbers of
current limits (F4.05), drive trips to OL2 protection.
Unit: 250 times (0: disable)
0~255
1 time
0
F4.07
Motor 1 Overload
Protection (OL)
0: Motor overload protection: Disabled
1: Motor overload protection:Enabled(OL)
2: Motor overload protection of
independent cooling fans: Enabled(OL)
0~2
─
1
F4.08
Motor 1 Rated
Current
Current setting according to the motor rated current.
10%~150%
of drive
rated current
0.1A
According
to the
rated
current of
motor
F4.09
Motor 1 No-Load
Current
Current setting according to the motor’s no-load
condition
0~ motor
rated current
0.1A
1/3 motor
rated
current
F4.10
Trip Time of Motor 1
Overload
Set the tripped time of motor when motor is
overload(150% of Motor rated current).
0.5~10.0
0.1min
5.0
F4.12
Protection Level of
Drive Overheat
Set the tripped level of drive when drive is overheat.
85~115
1℃
90
*Note 6
F4.13
Drive Overheat
Pre-alarm Selection
0: Disable
1: Warning (OHt): Continuous operation
(relay terminal outputs)
2: Warning (OHt): Reduce switching
frequency operation
(relay terminal outputs)
3: Warning (OHt): Stop operation
(relay terminal outputs)
0~3
─
2
Parameter List [F4 Protection Parameters ]

9
Func.
Name
Descriptions
Range of
Setting
Unit
Default
F4.14
Drive Overheat
Pre-alarm Level
Set the temperature level of warning alarm.
45~105
1℃
70
F4.15
Drive Overheat Dead
Band
Set the temperature dead band of temperature
warning and fan active level.
0.1~10.0
0.1℃
3.0
F4.17
Fan Control Selection
0: Forced air: Start the fan at power on.
1: Operation air: Start the fan at operation.
2: Temperature control: Fan activation according to
temperature level
0~2
─
1
F4.18
Temperature Level of
Fan Activation
Set the temperature level of fan activation.
25~60
1℃
50
F4.19
Minimum Operation
Time of Fan
Set the minimum operation time of
fans when the fan control is stopped.
0.1~25.0
0.1min
0.5
F4.21
PTC Overheat
Warning Level
(Motor Overheat
Protection)
Set the temperature warning
level(OH1) of PTC
0.0~10.0
0.1Vdc
1.2
F4.22
PTC Overheat
Warning Disposal
0: Warning (OH1): Continue operation
(relay terminal outputs)
1: Warning (OH1): Stop operation
(relay terminal outputs)
0,1
─
0
F4.23
PTC Overheat Trip
Level
Set the overheat trip level of PTC
0.0~10.0
0.1V
2.4
F4.25
System Overload
Detection (OLO)
0: Disable 1: Enable(OLO)
0,1
─
0
F4.26
System Overload
Detection Status
0: Detection during the constant speed only
1: Detection during the running only
0,1
─
0
F4.27
Output Setting of
System Overload
0: Drive is still running when the
overload is detected
1: Drive is tripped when the overload is detected
0,1
─
0
F4.28
System Overload
Detection Level
Set the level of the current for
overload detection
30%~200%
of drive
rated current
1%
160
F4.29
System Overload
Detection Time
The output current is larger than the setting F4.28
and exceeds the time interval of the overload
detection
0.1~300.0
0.1sec
0.1
F4.36
Current Limit (I-limit)
Current over F4.36
the rated current of drive
during operation, the drive may adjust PWM ouput
and limit output current.
30%~200%
of drive
rated current
1%
180
F4.37
Gain of I-limit
The gain of the current limitation response (P).
0.00~1.00
0.01
0.10
F4.38
Integration Time of
I-limit
Lower integration time I setting value will result the
current limitation response more fast but lower
setting value would cause the effect of oscillating
current.
0~10.0
0.1
0.6
F4.39
Selection of Current
Limitation
0:Disable 1:Enable
0,1
─
0
F4.41
Motor 2 Overload
Protection (OL)
0: Motor overload protection: Disabled
1: Motor overload protection: Enabled(OL)
2: Motor overload protection of
independent cooling fans: Enabled(OL)
0~2
─
1
F4.42
Motor 2
Rated Current
Current setting according to the motor rated current.
10%~150%
of drive
rated current
0.1A
According
to the
rated
current of
motor
F4.43
Motor 2 No-Load
Current
Current setting according to the motor’s no-load
condition
10%~150%
of drive
rated current
0.1A
According
to the
rated
current of
motor
F4.44
Trip Time of Motor 2
Overload
Set the tripped time of motor when motor is
overload(150% of Motor rated current).
0.5~10.0
0.1min
5.0

10
Func.
Name
Descriptions
Range of
Setting
Unit
Default
F4.45
PID Feedback High
Detection Setting
0: Disable
1: Warning, drive continuous operation.
2: Error, drive trip to stop.
0~2
─
0
F4.46
PID Feedback High
Detection Level
Detect if the PID feedbackis higher than setting level
0~100
1%
100
F4.47
PID Feedback High
Detection Time
Feedback signal is higher than setting level and
reach the detection time, the drive will be activated.
0.0~25.5
0.1sec
2.0
F4.48
PID Feedback Low
Detection Setting
0: Disable
1: Warning, drive continuous operation.
2: Error, drive trip to stop.
0~2
─
0
F4.49
PID Feedback Low
Detection Level
Detect if the PID feedback is lower than setting level
0~100
1%
0
F4.50
PID Feedback Low
Detection Time
If feedback signal is lower than setting level and
reach the detection time, the drive will be activated.
0.0~25.5
0.1sec
10.0
Func.
Name
Descriptions
Range of
Setting
Unit
Default
F5.00
“Pot knob”
Selection
(Analog Input)
0: Analog input gain
1: Frequency command
2: Current limit
3: Variable voltage of V/F pattern
0~3
─
1
F5.01
AI Selection
(Analog Input)
0: Analog input gain
1:Frequencycommand
2: Current limit
3: Variable voltage of V/F
pattern
4: PTC temperature
5: PID feedback
0~5
─
1
F5.02
AI Input Source
Selection
0:DC 4~20mA (2~10V)
1:DC 0~20 mA (0~10V)
0, 1
─
1
F5.03
Pot Gain
(Analog Input)
Analog input of “Pot knob”gain
0.00~2.00
0.01
1.00
F5.04
“Pot knob”Bias
(Analog Input)
Analog input of “Pot knob”bias
-1.00~1.00
0.01
0.00
F5.05
AI Gain
(Analog Input)
Analog input of AI gain
0.00~2.00
0.01
1.00
F5.06
AI Bias
(Analog Input)
Analog input of AI bias
-1.00~1.00
0.01
0.00
F5.07
Filter Setting of
AnalogFrequency
Filter the signal based on analog input setting.
0~255
─
20
F5.08
AnalogFrequency
Dead Band
When signal noise is large, appropriately increase the
dead band to stabilize the frequency. But this will reduce
the tuning linearity.
0.00~2.55
0.01Hz
0.00
F5.09
Acceleration
Time of V
Set the acceleration time of the variable voltage of V/F
pattern.
0.0~3200.0
0.1sec
5.0
F5.10
Deceleration
Time of V
Set the deceleration time of the variable voltage of V/F
pattern.
0.0~3200.0
0.1sec
5.0
F5.12
FM Analog
Output Signal
Selection
0: Output frequency
(before slip compensation)
1: Output frequency
(after slip compensation)
2: Frequency command
3: Output voltage
4: Output current
5: DC bus voltage
6: “Pot knob”analog input
signal
7: AI analog input signal
8: PID command
9: PID feedback signal
0~9
─
0
F5.13
FM Analog
Output Gain
Analog output adjustment ratio.
0.00~2.00
0.01
1.00
F5.14
FM Analog
Output Bias
Analog output adjustment offset.
-1.00~1.00
0.01
0.00
Parameter List [ F5 Multi-function Parameter ]

11
Func.
Name
Descriptions
Range of
Setting
Unit
Default
F5.15
FM Range
Option
0:DC 4~20mA (2~10V)
1:DC 0~20 mA (0~10V)
0, 1
─
1
F5.19
Multi-function
Input Terminal
X1
0: Disable
±1: Jog command
±2: Secondary accel/decel
command switching
±3: Multi-speed level 1
command
±4: Multi-speed level 2
command
±5: Multi-speed level 3
command
±6: Multi-speed level 4
command
±7: Reset command
±8: External fault
command(EF)
±9: Interruption of output
command(bb)
±10: Coast to stop
command(Fr)
±11: Speed search from
the maximum frequency
±12: Speed search from
the frequency setting
±13: Holding command
±14: UP command
±15: DOWN command
±16: Clean UP/DOWN
frequency command
±17: UP/DOWN command
enter key
±18: Analog input source
selection(Pot knob/AI)
±19: Primary and secondary
frequency command option
±20: Start command of
sequential operation control
±21: Pause command of
sequential operation control
±22: Forward command
±23: Reverse command
±24: Stop command with
3-wire start/stop circuit
±25: DC braking enable(Stop)
±26: Counter input
±27: Counter clear
±28: Current limit enable
±29: Selection for motor
switching
±30: PIDswitching
(open-loopselection)
±31: PID integrator reset
-31 ~ +31
*Note 7
─
22
F5.20
Multi-function
Input Terminal
X2
-31 ~ +31
*Note 7
─
23
F5.21
Multi-function
Input Terminal
X3
-31 ~ +31
*Note 7
─
1
F5.22
Multi-function
Input Terminal
X4
-31 ~ +31
*Note 7
─
7
F5.23
Multi-function
Input Terminal
X5
-31 ~ +31
*Note 7
─
0
F5.24
Multi-function
Input Terminal
X6
-31 ~ +31
*Note 7
─
0
F5.25
Digital Input
Response Time
When the input signal is under the setting time, program
will not be activated.
1~255
1ms
10
F5.26
Multi-function
Output Setting of
Ta/Tb/Tc
Terminals
0: Disable
±1: Running detection
±2: Constant speed
detection
±3: Zero speed detection
±4: Frequency detection
±5: Overload Detection
(OLO)
±6: Stall prevention
detection
±7: Low voltage detection
(LE)
±8: Braking transistor is
active detection(db)
±9: Restart after
instantaneous power
failure detection
±10: Restart after fault
condition detection
±11: Fault detection
±12: Start detection of
sequential operation control
±13: One complete operation
sector detection of sequential
operation control
±14: One complete operation
cycle detection of sequential
operation control
±15: Pause command
detection of sequential
operation control
±16: Detection of counter
value1
±17: Detection of counter
value2
±18: Reverse detection
±19: NTC temperature
warning
detection (OHt)
±20: Fan operation detection
±21: PTC temperature
warning
detection (OH1)
±22: Feedback high detection
±23: Feedback low detection
-23~+23
*Note 7
─
11
F5.30
UP/DOWN
Memory
Selection
0: Erase UP/DOWN frequency command when power
off
1: Store UP/DOWN frequency command when power off
0, 1
─
0
F5.31
UP/DOWN
Frequency
Calibration
0: 0.01Hz
1~8: ×0.05Hz
9: 0.5Hz
10~250: ×0.1Hz
0~250
─
0

12
Func.
Name
Descriptions
Range of
Setting
Unit
Default
F5.32
UP/DOWN
Calibrating Time
1~5: Terminal adjust the response time. Continuous
acceleration or deceleration when over the
setting time
6: Edge trigger
1~6
─
1
F5.33
UP/DOWN
Frequency
Adjustment
Adjust UP/DOWN frequency on keypad directly
0.00~400.00
0.01Hz
0.00
F5.35
Counting Mode
0: Up counting mode
1: Down counting mode
0, 1
─
0
F5.36
Counter Value 1
Set counter value 1 for sequential operation control cycle
0~9999
1
0
F5.37
Counter Value 2
Set counter value 2 for sequential operation control cycle
0~9999
1
0
F5.39
Constant Speed
Detection Range
Set the bandwidth of constant speed detection range
0.0~10.0
0.1Hz
2.0
F5.40
Frequency
Detection Range
Set the bandwidth of frequency detection range
0.0~10.0
0.1Hz
2.0
F5.41
Frequency
Detection Level
Set the frequency detection level of multi-function
terminal
0.0~400.00
0.1Hz
0.0
Func.
Name
Descriptions
Range of
Setting
Unit
Default
F6.00
Operation Mode
for Sequential
Operation Control
0: Sequential operation
control disable.
1: Sequential operation
controloperates one
cycle and stops.
2: Sequential operation
control operates in
circulation.
3: Sequential operation
control operates one cycle
and stops (by STOP key on
the operation panel).
4: Sequential operation
control operates in
circulation (by STOP key
on the operation panel).
0~4
─
0
F6.01
Cycle Times
for Sequential
Operation Control
1~9998: The number of cycle times of sequential
operation control circulation.
9999: Infinite cycles of sequential operation
control circulation.
1~9999
─
5
F6.02
Sequence of One
Operation Cycle
for Sequential
Operation Control
0: Single direction
1: Dual direction
0, 1
─
0
F6.04
Hold Time Unit
for Sequential
Operation Control
0: Second
1: Minute
2: Hour
0~2
─
0
F6.05
Accel/Decel
Timeof Sector 1
of Sequential
Operation Control
Set the accel/decel time of sector 1 of sequential
operation control.
0.0~360.0
0.1sec
0.0
F6.06
Hold Time of Sector
1of Sequential
Operation Control
Set the hold time of sector 1 of sequential operation
control.
0.0~360.0
0.1sec
0.0
F6.07
Accel/Decel
Timeof Sector 2
of Sequential
Operation Control
Set the accel/decel time of sector 2 of sequential
operation control.
0.0~360.0
0.1sec
0.0
F6.08
Hold Time of Sector
2 of Sequential
Operation Control
Set the hold time of sector 2 of sequential operation
control.
0.0~360.0
0.1sec
0.0
F6.09
Accel/Decel
Timeof Sector 3
of Sequential
Operation Control
Set the accel/decel time of sector 3 of sequential
operation control.
0.0~360.0
0.1sec
0.0
F6.10
Hold Time
of Sector 3
of Sequential
Operation Control
Set the hold time of sector 3 of sequential operation
control.
0.0~360.0
0.1sec
0.0
Parameter List [ F6 Special Parameters ]

13
Func.
Name
Descriptions
Range of
Setting
Unit
Default
F6.11
Accel/Decel
Time of Sector 4
of Sequential
Operation Control
Set the accel/decel time of sector 4 of sequential
operation control.
0.0~360.0
0.1sec
0.0
F6.12
Hold Time
of Sector 4
of Sequential
Operation Control
Set the hold time of sector 4 of sequential operation
control.
0.0~360.0
0.1sec
0.0
F6.13
Accel/Decel
Timeof Sector 5
of Sequential
Operation Control
Set the accel/decel time of sector 5 of sequential
operation control.
0.0~360.0
0.1sec
0.0
F6.14
Hold Time
of Sector 5
of Sequential
Operation Control
Set the hold time of sector 5 of sequential operation
control.
0.0~360.0
0.1sec
0.0
F6.15
Accel/Decel
Timeof Sector 6
of Sequential
Operation Control
Set the accel/decel time of sector 6 of sequential
operation control.
0.0~360.0
0.1sec
0.0
F6.16
Hold Time
of Sector 6
of Sequential
Operation Control
Set the hold time of sector 6 of sequential operation
control.
0.0~360.0
0.1sec
0.0
F6.17
Accel/Decel
Timeof Sector 7
of Sequential
Operation Control
Set the accel/decel time of sector 7 of sequential
operation control.
0.0~360.0
0.1sec
0.0
F6.18
Hold Time
of Sector 7
of Sequential
Operation Control
Set the hold time of sector 7 of sequential operation
control.
0.0~360.0
0.1sec
0.0
F6.19
Accel/Decel
Timeof Sector 8
of Sequential
Operation Control
Set the accel/decel time of sector 8 of sequential
operation control.
0.0~360.0
0.1sec
0.0
F6.20
Hold Time
of Sector 8
of Sequential
Operation Control
Set the hold time of sector 8 of sequential operation
control.
0.0~360.0
0.1sec
0.0
F6.21
Accel/Decel
Time of Sector 9
of Sequential
Operation Control
Set the accel/decel time of sector 9 of sequential
operation control.
0.0~360.0
0.1sec
0.0
F6.22
Hold Time
of Sector 9
of Sequential
Operation Control
Set the hold time of sector 9 of sequential operation
control.
0.0~360.0
0.1sec
0.0
F6.23
Accel/Decel
Time of Sector 10
of Sequential
Operation Control
Set the accel/decel time of sector 10 of sequential
operation control.
0.0~360.0
0.1sec
0.0
F6.24
Hold Time
of Sector 10
of Sequential
Operation Control
Set the hold time of sector 10 of sequential operation
control.
0.0~360.0
0.1sec
0.0
F6.25
Accel/Decel
Timeof Sector 11
of Sequential
Operation Control
Set the accel/decel time of sector 11of sequential
operation control.
0.0~360.0
0.1sec
0.0
F6.26
Hold Time of
Sector 11
of Sequential
Operation Control
Set the hold time of sector 11 of sequential operation
control.
0.0~360.0
0.1sec
0.0

14
Func.
Name
Descriptions
Range of
Setting
Unit
Default
F6.27
Accel/Decel
Time of Sector 12 of
Sequential
Operation Control
Set the accel/decel time of sector 12 of sequential
operation control.
0.0~360.0
0.1sec
0.0
F6.28
Hold Time
of Sector 12
of Sequential
Operation Control
Set the hold time of sector 12 of sequential operation
control.
0.0~360.0
0.1sec
0.0
F6.29
Accel/Decel
Timeof Sector 13
of Sequential
OperationControl
Set the accel/decel time of sector 13 of sequential
operation control.
0.0~360.0
0.1sec
0.0
F6.30
Hold Time
of Sector 13
of Sequential
OperationControl
Set the hold time of sector 13 of sequential operation
control.
0.0~360.0
0.1sec
0.0
F6.31
Accel/Decel
Time of Sector 14
of Sequential
OperationControl
Set the accel/decel time of sector 14 of sequential
operation control.
0.0~360.0
0.1sec
0.0
F6.32
Hold Time
of Sector 14
of Sequential
OperationControl
Set the hold time of sector 14 of sequential operation
control.
0.0~360.0
0.1sec
0.0
F6.33
Accel/Decel
Time of Sector 15
of Sequential
OperationControl
Set the accel/decel time of sector 15 of sequential
operation control.
0.0~360.0
0.1sec
0.0
F6.34
Hold Time
of Sector 15
of Sequential
OperationControl
Set the hold time of sector 15 of sequential operation
control.
0.0~360.0
0.1sec
0.0
F6.35
Accel/Decel
Timeof Sector 16
of Sequential
OperationControl
Set the accel/decel time of sector 16 of sequential
operation control.
0.0~360.0
0.1sec
0.0
F6.36
Hold Time
of Sector 16
of Sequential
Operation Control
Set the hold time of sector 16 of sequential operation
control.
0.0~360.0
0.1sec
0.0
F6.37
Direction Control of
Sequential
Operation Control
Sequential operation control direction is defined with
binary format.
X16~X1(Xn=0: forward;Xn=1: reverse)
Xn: Nth operation direction
0~FFFF
─
0
F6.40
PID Control
Selection
0: PID control disable
1: Forward control, D postposition
2: Reverse control, D postposition
3: Forward control, D preposition
4: Reverse control, D preposition
0~4
─
0
F6.41
Feedback Signal
Detection
0: Open loop detection disable
1: Open loop detection enable (noFb)
0,1
─
1
F6.42
Feedback Signal
Filter
Filter the feedback signal.
0~255
─
10
F6.43
PID Buffer Space
Set the buffer space of PID output value.
0~255
─
2
F6.44
Proportional
Gain(P)
Set the gain value for discrepancy. (0.0: P control
disabled).
0.0~25.0
0.1
1.0
F6.45
Integration Time(I)
Set the integration time for discrepancy.
(0.0: I control disabled)
0.0~100.0
0.1sec
1.2
F6.46
Derivative Time(D)
Set the derivative time for discrepancy.
(0.0: D control disabled)
0.00~2.50
0.01sec
0.00
F6.47
Integration Upper
Limitation
Set the upper limitation value of integrator.
0~200%of
maximum
frequency
1%
100

15
Func.
Name
Descriptions
Range of
Setting
Unit
Default
F6.48
Integration Lower
Limitation
Set the lower limitation value of integrator.
-100~100%of
maximum
frequency
1%
0
F6.49
Integrator
Initialized Value
Set the initial value of the integrator before PID
starts.
-100~100%
of maximum
frequency
1%
0
F6.50
PID Output Upper
Limit
Set the PID control output frequency
0.00~1.00
0.01
1.00
F6.51
PID Compensation
Gain
(PID command –PID feedback)*F6.51
0.1~8.0
─
1.00
F6.52
Propotional Gain(P)
Selection
0: postposition P
1: preposition P
0~1
─
1
F6.53
Feedback Signal
Selection
0: Direct signal
1: Reverse signal
0~1
─
0
F6.54
Derivative Time of
Feedback
Set the derivative time for feedback signal.
0.00~2.50
0.01sec
0.00
F6.55
Communication
Address
The host uses the address to send and receive
messages from the drive (0: Disable)
0~254
─
0
F6.56
Baud Rate
0: 4800bps
1: 9600bps
2: 19200bps
3: 38400bps
0~3
─
1
F6.57
Communication
Protocol
0: 8,N,2
1: 8,E,1
2: 8,O,1
3: 8,N,1
0~2
─
1
F6.58
Communication
Overtime (Cot)
When the data transmission during communication
transmission is interrupted, has no data transmitting,
or delays, drive displays “Cot” message (0.0:
Communication overtime disable)
0.0~100.0
0.1sec
0.0
F6.59
Communication
Overtime Disposal
0: Warning (Cot): Continue operation.
1: Warning (Cot): Ramp to stop
2: Warning (Cot): Coast to stop
0~2
─
0
F6.60
Multi-Function
Input Selection
0: Multi-function inputs from
multi-function terminals
1: Multi-function inputs from
communication control
0, 1
─
0
F6.61
PID Sleep Selection
0:Disable 1:Enable
0~1
─
0
F6.62
PID Wakeup
Initial Frequency
Setting the frequency for PID Wakeup
Process(1.00=max.output frequency)
0.00~1.00
0.01
0.00
F6.63
PID Wakeup Delay
Time
Setting the time for PID Wakeup Process
250
1sec
0
F6.64
PID Sleep
Initial Frequency
Setting the frequency for PID Sleep Process
(1.00=max.output frequency)
0.00~1.00
0.01
0.00
F6.65
PID Sleep
Delay Time
Setting the time for PID Sleep Process
0~250
1sec
0
F6.66
PID Output lower
limit
PID control for output frequency
0.00~1.00
0.01
0.00
The color as means function can be set during the operation.
(Note):
1. The default setting of 50Hz
2. The default setting of 60Hz
3. Specifications of 100V series
4. Specifications of 200V series
5. Specifications of 400V series
6. The default value is “105”for 2003B3/4005B3 models and the default value is “90”for remained models.
7. + : Represents a contact (Normal open), ─ : Represents b contact (Normal close)
UP/DOWN control wiring must not exceed over 20m when multi-function terminals are used for UP/DOWN
control.
8. When the setting value of switching frequency(F1.21) exceeds “4”, the drive must be de-rating for usage or
selecting the higher capacity of drive.

16
Error Trip Messages of Drive
Display
Description
Display
Description
Fot
IGBT module error
noFb
PID feedback signal error
GF
Grounding fault
AdEr
A/D converter error
OC
Drive over current
EF
External fault
OL
Motor overload
PAdF
Keypad interruption
during copy
OL1
Drive overload
EEr
EEPROM error
OL2
Drive current limit
EEr1
Internal memory error
OL3
Braking transistor overload
EEr2
Internal memory error
OLO
System overload
ntcF
Thermal sensor fault
OE
Over voltage
OH
Drive overheat
LE1
Under voltage during
operation
OH2
Motor overheat
Warning Messages of Drive
Display
Description
Display
Description
OLO
System overload
Fr
Coast to stop
Hv
Power source
over voltage
dtF
Forwad/reverse
command input
simultaneously
db
Braking transistor is active
WrF
Different software
version inter-copy
LE
Power source under
voltage
Cot
Modbus
communication
overtime
OHt
Drive overheat
Err 00
Keypad cable trip
before connecting
OH1
Motor overheat
Err 01
Keypad cable trip
during operation
bb
Drive output interruption
Fault Displays
Other manuals for RM6E1 Series
1
Table of contents
Other Rhymebus DC Drive manuals
Popular DC Drive manuals by other brands
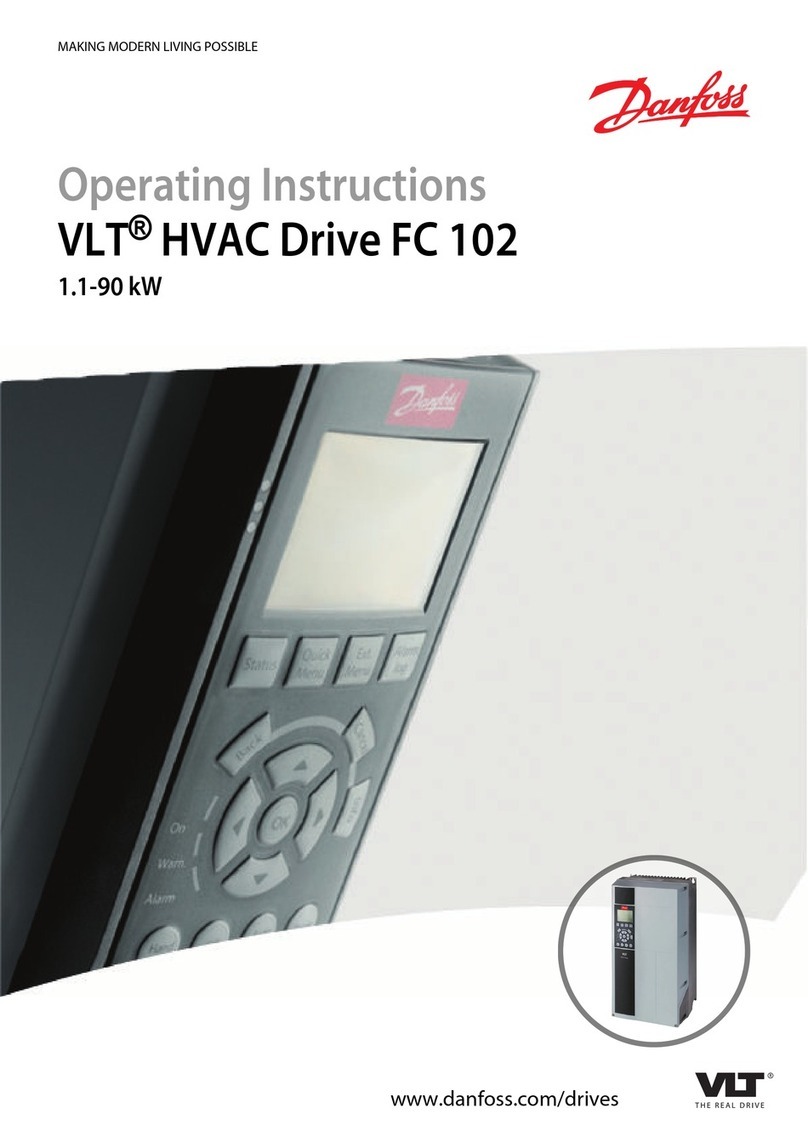
Danfoss
Danfoss VLT HVAC Drive FC 102 operating instructions
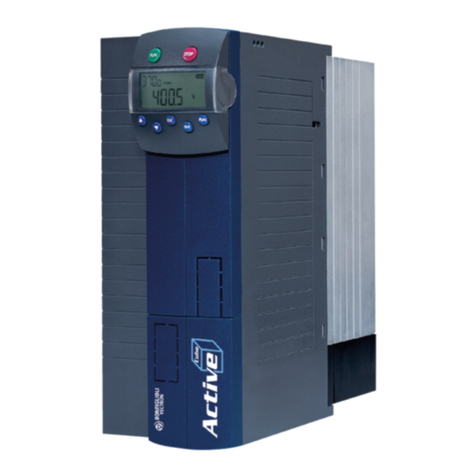
BONFIGLIOLI Vectron
BONFIGLIOLI Vectron ACTIVE CUBE manual
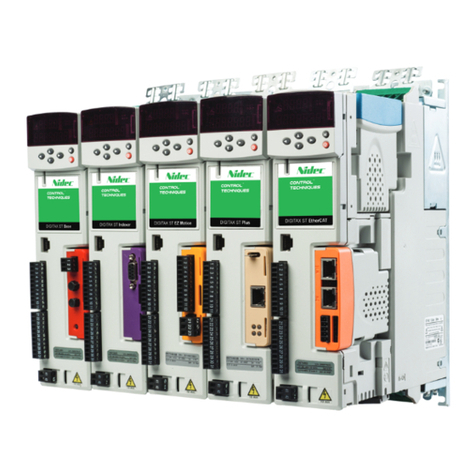
Nidec
Nidec Digitax ST Series installation guide

Hitachi
Hitachi DKC710I-CBXA Maintenance manual

Regal
Regal MD100H Series quick start

Invertek Drives
Invertek Drives OPTIDRIVE E3 user manual