Rockwell Automation Allen-Bradley iTRAK User manual

iTRAK System
Bulletin Number 2198T-L16
Troubleshooting Guide Original Instructions

2Rockwell Automation Publication 2198T-TG001A-EN-P - October 2020
iTRAK System Troubleshooting Guide
Important User Information
Read this document and the documents listed in the additional resources section about installation, configuration, and
operation of this equipment before you install, configure, operate, or maintain this product. Users are required to familiarize
themselves with installation and wiring instructions in addition to requirements of all applicable codes, laws, and standards.
Activities including installation, adjustments, putting into service, use, assembly, disassembly, and maintenance are required to
be carried out by suitably trained personnel in accordance with applicable code of practice.
If this equipment is used in a manner not specified by the manufacturer, the protection provided by the equipment may be
impaired.
In no event will Rockwell Automation, Inc. be responsible or liable for indirect or consequential damages resulting from the use
or application of this equipment.
The examples and diagrams in this manual are included solely for illustrative purposes. Because of the many variables and
requirements associated with any particular installation, Rockwell Automation, Inc. cannot assume responsibility or liability for
actual use based on the examples and diagrams.
No patent liability is assumed by Rockwell Automation, Inc. with respect to use of information, circuits, equipment, or software
described in this manual.
Reproduction of the contents of this manual, in whole or in part, without written permission of Rockwell Automation, Inc., is
prohibited.
Throughout this manual, when necessary, we use notes to make you aware of safety considerations.
Labels may also be on or inside the equipment to provide specific precautions.
WARNING: Identifies information about practices or circumstances that can cause an explosion in a hazardous environment,
which may lead to personal injury or death, property damage, or economic loss.
ATTENTION: Identifies information about practices or circumstances that can lead to personal injury or death, property
damage, or economic loss. Attentions help you identify a hazard, avoid a hazard, and recognize the consequence.
IMPORTANT Identifies information that is critical for successful application and understanding of the product.
SHOCK HAZARD: Labels may be on or inside the equipment, for example, a drive or motor, to alert people that dangerous
voltage may be present.
BURN HAZARD: Labels may be on or inside the equipment, for example, a drive or motor, to alert people that surfaces may
reach dangerous temperatures.
ARC FLASH HAZARD: Labels may be on or inside the equipment, for example, a motor control center, to alert people to potential
Arc Flash. Arc Flash will cause severe injury or death. Wear proper Personal Protective Equipment (PPE). Follow ALL Regulatory
requirements for safe work practices and for Personal Protective Equipment (PPE).

Rockwell Automation Publication 2198T-TG001A-EN-P - October 2020 3
Table of Contents
Preface
About This Publication . . . . . . . . . . . . . . . . . . . . . . . . . . . . . . . . . . . . . . . . . . . 5
Conventions. . . . . . . . . . . . . . . . . . . . . . . . . . . . . . . . . . . . . . . . . . . . . . . . . . . . . 5
Appropriate Use . . . . . . . . . . . . . . . . . . . . . . . . . . . . . . . . . . . . . . . . . . . . . . . . . 5
Download Firmware, AOP, EDS, and Other Files . . . . . . . . . . . . . . . . . . . . 5
Additional Resources . . . . . . . . . . . . . . . . . . . . . . . . . . . . . . . . . . . . . . . . . . . . . 6
Chapter 1
iTRAK System Hardware Mechanical iTRAK components . . . . . . . . . . . . . . . . . . . . . . . . . . . . . . . . . . . 8
Power supplies. . . . . . . . . . . . . . . . . . . . . . . . . . . . . . . . . . . . . . . . . . . . . . . . . . . 8
Gateway. . . . . . . . . . . . . . . . . . . . . . . . . . . . . . . . . . . . . . . . . . . . . . . . . . . . . . . . . 8
Digital USB I/O . . . . . . . . . . . . . . . . . . . . . . . . . . . . . . . . . . . . . . . . . . . . . . . . . . 9
Chapter 2
Power Up the System Turn Main Power On . . . . . . . . . . . . . . . . . . . . . . . . . . . . . . . . . . . . . . . . . . . . 11
Motor Modules Status LED . . . . . . . . . . . . . . . . . . . . . . . . . . . . . . . . . . . . . . 11
Control Power or Communication LED Off. . . . . . . . . . . . . . . . . . . . . . . . 12
Chapter 3
Connect a Monitor and Key
Board to the Gateway
Check Firmware Revision and Section Type . . . . . . . . . . . . . . . . . . . . . . . 17
Change Incorrect Section Type using Bitvise or Terminal Monitor . . . 17
Chapter 4
Correct Monitor Problems Sections are not Displayed on the Monitor . . . . . . . . . . . . . . . . . . . . . . . . 23
Chapter 5
Retrieve a Log File Log File Retrieval Tool . . . . . . . . . . . . . . . . . . . . . . . . . . . . . . . . . . . . . . . . . . . 25
Gen 1 and Gen 2 Gateway Bitvise . . . . . . . . . . . . . . . . . . . . . . . . . . . . . . . . . 26
Gen 3 Bitvise. . . . . . . . . . . . . . . . . . . . . . . . . . . . . . . . . . . . . . . . . . . . . . . . . . . . 29
Chapter 6
ACD file Loop Update Rates . . . . . . . . . . . . . . . . . . . . . . . . . . . . . . . . . . . . . . . . . . . . . . 31
Configuring with Libraries. . . . . . . . . . . . . . . . . . . . . . . . . . . . . . . . . . . . . . . 39
Chapter 7
Field Use Cases Intermittent Low Voltage Errors . . . . . . . . . . . . . . . . . . . . . . . . . . . . . . . . . 41
Mover Oscillations, Missing Movers, Error 12 . . . . . . . . . . . . . . . . . . . . . . 42
Rough and Choppy Mover Motion in Straights and Curves. . . . . . . . . . 43
Intermittent Error Code 9 . . . . . . . . . . . . . . . . . . . . . . . . . . . . . . . . . . . . . . . 46
Error Code 28 after Power Cycle . . . . . . . . . . . . . . . . . . . . . . . . . . . . . . . . . . 47
Index . . . . . . . . . . . . . . . . . . . . . . . . . . . . . . . . . . . . . . . . . . . . . . . . . . . . . . . .49

4Rockwell Automation Publication 2198T-TG001A-EN-P - October 2020
Table of Contents
Notes:

Rockwell Automation Publication 2198T-TG001A-EN-P - October 2020 5
Preface
About This Publication This manual provides troubleshooting instructions for use in the
commissioning of an iTRAK® system.
This manual is intended for engineers or technicians who are directly involved
in the design, installation, and wiring of the iTRAK system. It is also intended
for programmers who are directly involved in the operation, field
maintenance, and integration of this system with an EtherNet/IP™
communication module or controller.
If you do not understand the basics of the iTRAK system, contact your
Rockwell Automation sales representative for information on available
training courses.
Conventions These conventions are used throughout this manual:
• Bulleted lists provide information, not procedural steps.
• Numbered lists provide steps or hierarchical information.
Appropriate Use Before you use the iTRAK system, read and understand the safety instructions
found in the iTRAK System with TriMax Bearings User Manual, publication
2198T-UM002.
In addition, also follow these guidelines:
• Leave the hardware in its original state; never make structural changes.
• Do not de-compile software or alter source code.
• Do not use damaged or faulty components.
• Use the system in the manner that is described in this manual.
• Operate the system in the ambient conditions that are described in the
iTRAK System Technical Data, publication 2198T-TD001.
Download Firmware, AOP,
EDS, and Other Files
Download firmware, associated files (such as AOP, EDS, and DTM), and access
product release notes from the Product Compatibility and Download Center at
rok.auto/pcdc.
ATTENTION: Incorrect use of the products can cause personal injury
and property damage.

6Rockwell Automation Publication 2198T-TG001A-EN-P - October 2020
Preface
Additional Resources These documents contain additional information concerning related products
from Rockwell Automation.
You can view or download publications at rok.auto/literature.
Resource Description
iTRAK System Technical Data, publication 2198T-TD001 Contains product specifications for iTRAK system components. Includes performance,
environmental, certifications, load force, and dimension drawings.
Kinetix Servo Drives Specifications Technical Data, publication KNX-TD003 Provides product specifications for Kinetix® Integrated Motion over the EtherNet/IP
network, Kinetix 5700 iTRAK Power Supply, Integrated Motion over sercos interface,
EtherNet/IP networking, and component servo drive families.
iTRAK System with TriMax Bearings User Manual, publication 2198-UM002 Provides information on how to install, configure, start, and troubleshoot your iTRAK system
with TriMax bearings.
Kinetix 5700 iTRAK Power Supply and iTRAK Bus Conditioner Installation
Instruction, publication 2198T-IN001 Provides information on how to wire and connect the Kinetix 5700 iTRAK power supply to the
iTRAK system.
iTRAK System Programming Manual, publication 2198T-PM001 Provides information on how to commission and program an iTRAK system.
3D CAD Models of iTRAK Components 2198T-3DCAD.zip.
Motion Analyzer website, https://motionanalyzer.rockwellautomation.com/
Products/iTrak
Provides 2D outline, assembly, and system drawings, STEP files for the movers and motor
modules, and hyperlinks to complete system STEP files.
ControlLogix System User Manual, publication 1756-UM001 Provides details on how to configure, program, and operate a 1756 ControlLogix® system.
Also provides technical specifications
System Design for Control of Electrical Noise Reference Manual,
publication GMC-RM001 Provides information, examples, and techniques that are designed to minimize system
electrical noise failures.
Industrial Automation Wiring and Grounding Guidelines, publication 1770-4.1 Provides general guidelines for installing a Rockwell Automation® industrial system.
Product Certifications website, rok.auto/certifications. Provides declarations of conformity, certificates, and other certification details.

Rockwell Automation Publication 2198T-TG001A-EN-P - October 2020 7
Chapter 1
iTRAK System Hardware
The iTRAK® system is composed of motor modules, mounting plates, bearing
rails, and movers. The motor modules are an integrated drive motor system
with feedback. Mounting plates can be attached to the sides of the motor
modules, and bearing rails can be attached to the mounting plates. Movers
have independent linear motor magnets and bearings, and multiple movers
can be operated on a motor module at any time. Movers can be synchronized
or independently controlled, however they are programmed.
When installing or troubleshooting an iTRAK system, it is important to be
familiar with the components and how they are described in the iTRAK System
with TriMax Bearings User Manual, publication 2198T-UM002.
This document focuses on basic troubleshooting steps to get your iTRAK
system running for the first time, or after a fault has occurred.

8Rockwell Automation Publication 2198T-TG001A-EN-P - October 2020
Chapter 1 iTRAK System Hardware
Mechanical iTRAK
components
An exploded view of the mechanical and servo components of an iTRAK system
is displayed in the following diagram. Familiarize yourself with the
nomenclature and use of each component.
Power supplies The iTRAK system can be powered by using a preconfigured Power Control
Module (PCM) with fixed output wattage or with a scalable Kinetix® 5700
iTRAK power supply as part of a Kinetix 5700 system.
Details and installation instructions on the use of the two power supplies are
covered in the iTRAK System with TriMax Bearings User Manual, publication
2198T-UM002.
Gateway The gateway provides centralized motion processing and communication
between the controller and the motor modules. There are three generations of
gateways, which all provide the same function, however, there are some
differences:
Item Description Item Description
1 Top bearing rail 7 Movers
2 Transverse bearing rail 8 Mover magnets
3 Top frame plate 9 Bottom frame plate
4 Straight motor modules 10 Bottom bearing rail
5 Curved motor modules 11 Spine bars
6 Position magnets 12 Mounting plate
1
4
5
67
8
9
10
11
12
3
2
2
2
2

Rockwell Automation Publication 2198T-TG001A-EN-P - October 2020 9
Chapter 1 iTRAK System Hardware
• Gen 1 and Gen 2 require a loopback connector after the last
communication cable if all ports are not occupied by communication
cable. (Gen 3 doesn’t require a loopback connector)
• The Compact Flash card used on Gen 1 is different than CFast card Gen 2
and Gen 3 utilize therefore they cannot be used interchangeably.
For more information about the gateway, see the iTRAK System with TriMax
Bearings User Manual, publication 2198T-UM002.
Digital USB I/O The digital USB I/O module provides an interface between the power supply
that is used by your system and the gateway. This module is integrated in a
gateway cabinet and must be included in your system when using Kinetix 5700
iTRAK power supply.
For more information about the digital USB I/O module, see the iTRAK System
with TriMax Bearings User Manual, publication 2198T-UM002.

10 Rockwell Automation Publication 2198T-TG001A-EN-P - October 2020
Chapter 1 iTRAK System Hardware
Notes:

Rockwell Automation Publication 2198T-TG001A-EN-P - October 2020 11
Chapter 2
Power Up the System
The following sections describe how to complete initial power up of your
iTRAK® system.
Turn Main Power On When you power up the system, it means that you bring AC power to the
cabinet where all the electronic components, such as power supplies, circuit
breakers, and safety circuitry, are located.
When you use a Kinetix® 5700 iTRAK Power Supply (iPS), the cabinet has been
designed and built by the original equipment manufacturer (OEM).
In the past, Rockwell Automation provided a single cabinet with the electronic
components known as a Power Control Module (PCM), which provided DC
power to the iTRAK motors and gateway. See the iTRAK System with TriMax
Bearings User Manual, publication 2198-UM002,for further information about
the power supplies.
Motor Modules Status LED Once AC power is turned ON, the power supplies send 24V DC to the motor
modules through the power cables. For the Series B motor modules, upon
power up, two out of three LEDs are ON. Control Power is solid green. The
Communication LED flashes green until it has made a connection to the
gateway, at which point the LED turns solid green. Power up and connection
to the gateway takes 3…5 minutes. Observe the behavior of the LEDs after this
time. There are three scenarios that can occur:
1. All motor module Communication LEDs are solid.
This indicates that the system is functioning properly and that all motor
modules have made connection with the gateway. No further action is
necessary.
2. All motor module Communication LEDs are still flashing green.
This indicates that none of the motor modules have properly made a
connection with the gateway. Check all communication cable
connections to the motor module and gateway. If, after checking the
communication cables, the problem persists, proceed to Connect a
Monitor and Key Board to the Gateway on page 15 for further
diagnostics.
3. Most motor modules Communication LEDs are solid, however, one or
more motor modules are flashing.

12 Rockwell Automation Publication 2198T-TG001A-EN-P - October 2020
Chapter 2 Power Up the System
This indicates that there is a problem with the particular section or
sections making a connection with the gateway. Check communication
cable(s) connection to the motor(s) and gateway. If, after checking the
communication cables, the problem persists, proceed to Connect a
Monitor and Key Board to the Gateway on page 15 for further
diagnostics.
The Drive Enabled LED does not turn solid until the iTRAK system has been
energized and has servo power.
Control Power or
Communication LED Off
If you do not have any LED illuminated, including Control Power, this
indicates that you have no power to the iTRAK system or particular motors.
Follow these steps to diagnose power:
1. If the Control Power LED is off, that motor module is not receiving 24V
DC from the power supply. Check the following:
a. Disconnect the two-pin connector from the power supply.
b. Measure the output of the 24V DC power supply. The output should
measure between 18…26V DC.
c. Check the orange power cable for continuity.
d. Make sure the power connector is properly secured at the power
supply end and at the motor module.
e. Remove the power cable from the motor module and use a multimeter
to measure the 24V DC input from the cable.
f. If 24V DC is present at the power cable, it is possible that there is an
internal problem in the module and it may need to be replaced.
2. If the communication LED is Off:
a. Check both ends of the cable at the motor module and the gateway and
ensure that they are connected properly.
b. Each cable is labeled from 00 to the last number of sections in the
system. Make sure the communication cable from motor 00 goes to
port 00 in the gateway, motor 01 to port 01, and so on.
c. The communication cables need to be connected in ascending order in
the gateway, 00, 01, 02,…0x in the counter clockwise direction of the
track.
d. After you verify that the cables are connected properly, and you still see
the communication issue, two scenarios are possible.
• There is a bad port on the gateway.
Connect one section at a time to the gateway until the bad port is
found.

Rockwell Automation Publication 2198T-TG001A-EN-P - October 2020 13
Chapter 2 Power Up the System
• The motor module is faulty
Remove all other communication cables from the gateway. Place the
suspect motor section in port 00 of the gateway (make sure to move
the loopback to port 01 if you use a Gen 1 or Gen 2 gateway), and then
reboot. If the problem persists, the module needs to be replaced.

14 Rockwell Automation Publication 2198T-TG001A-EN-P - October 2020
Chapter 2 Power Up the System
Notes:

Rockwell Automation Publication 2198T-TG001A-EN-P - October 2020 15
Chapter 3
Connect a Monitor and Key Board to the Gateway
The use of a monitor is recommended when troubleshooting iTRAK® issues. All
information for the iTRAK system is in the gateway and can easily be displayed
by using a monitor.
To connect the monitor, complete the following steps:
1. Connect a monitor with a DVI connector to the gateway.
2. If the monitor has a VGA connector, use an adapter VGA to DVI in order
to connect to the gateway.
3. Connect the DVI-A male end from your computer monitor into the DVI
plug on the gateway.

16 Rockwell Automation Publication 2198T-TG001A-EN-P - October 2020
Chapter 3 Connect a Monitor and Key Board to the Gateway
4. Connect a keyboard to any one of the free USB ports in the gateway.
5. Once the gateway has booted up, it asks for a log in. Press Alt + F2.
6. The screen display a screen similar to the one shown.

Rockwell Automation Publication 2198T-TG001A-EN-P - October 2020 17
Chapter 3 Connect a Monitor and Key Board to the Gateway
The numbers represent the movers. If there are more than ten movers on
the track, letters are displayed. The vertical lines represent each section
of the iTRAK. In the following picture, there are two sections and three
movers.
If no motor sections or movers are displayed on the screen, proceed to
Sections are not Displayed on the Monitor.
Check Firmware Revision
and Section Type
You need to verify that the firmware revision of the gateway is the same
revision as the firmware revision of the sections.
To verify the firmware revision, complete the following steps:
1. From the Bitvise terminal screen or keyboard and monitor, press x.
This displays your gateway firmware and section firmware. Make sure
that both are the same
2. Verify that your section types are correct.
There are two different commutation tables for 50mm, 100mm, and
150mm movers. See the table below for section types for optimal current
and optimal force for each mover. Verify that each section type
corresponds to the correct mover size being used and that commutation
tables match.
Change Incorrect Section
Type using Bitvise or
Terminal Monitor
If, in the previous procedure, you find that your section types do not match,
follow these instructions to change the firmware from Bitvise or from the
terminal screen:
1. Press x.
Mover Size Straight Section
Optimal Force
Straight Section
Optimal Current
Curve Section
Optimal Force
Curve Section
Optimal Current
50 mm Type 6 Type 506 Type 108 Type 4608
100 mm Type 5 Type 505 Type 107 Type 4607
150 mm Type 13 Type 513 Type 14 Type 4514

18 Rockwell Automation Publication 2198T-TG001A-EN-P - October 2020
Chapter 3 Connect a Monitor and Key Board to the Gateway
Section 0 has a section type that does not match. Section 0 is type 6 which
is a 50 mm optimal force, while the rest of the track is 100 mm optimal
current.
2. Press Shift + U at the same time.
The system prompts you to enter the number of the section you want to
change. In this example we are changing 0.

Rockwell Automation Publication 2198T-TG001A-EN-P - October 2020 19
Chapter 3 Connect a Monitor and Key Board to the Gateway
3. Type the correct section type for the track.
This example calls for type 505.
The prompt asks: Do you want to download the PWM FW to the section
as well? (y/n).
4. Type y.
The system asks you to confirm the change: You want to change section
number x to type y? (y/n).

20 Rockwell Automation Publication 2198T-TG001A-EN-P - October 2020
Chapter 3 Connect a Monitor and Key Board to the Gateway
5. Type y.
The gateway immediately goes down for a reboot.
After the reboot, the gateway downloads the firmware and begins to burn
the section.
After completion, the gateway reboots again.
Table of contents
Other Rockwell Automation Control System manuals
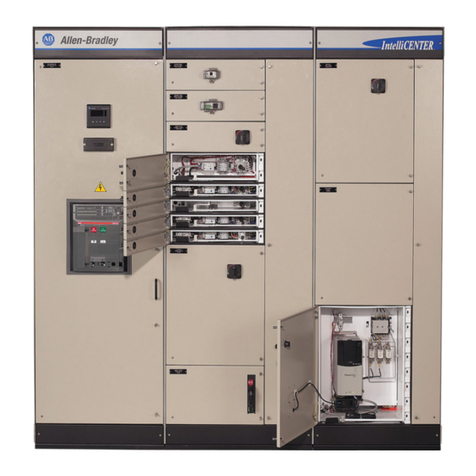
Rockwell Automation
Rockwell Automation Allen-Bradley CENTERLINE 2500 User manual
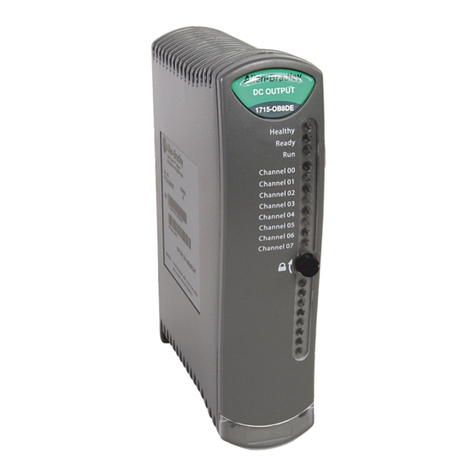
Rockwell Automation
Rockwell Automation Allen-Bradley ControlLogix SIL 2 User manual
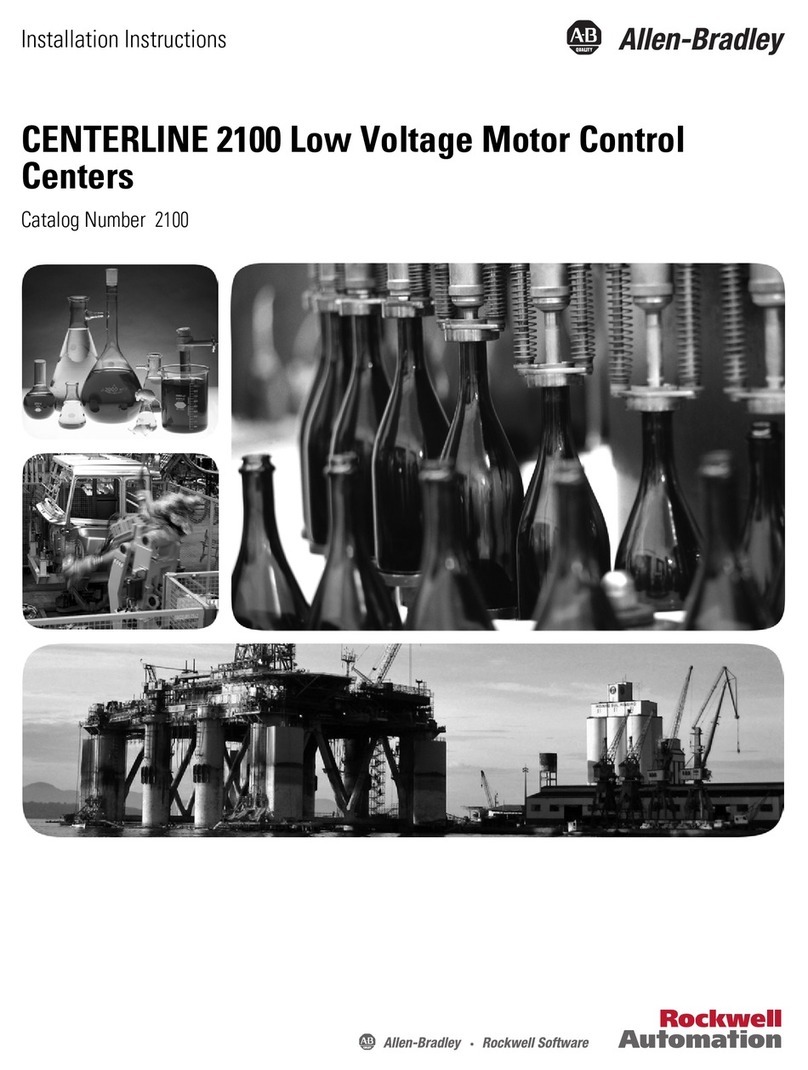
Rockwell Automation
Rockwell Automation Allen-Bradley CENTERLINE 2100 User manual
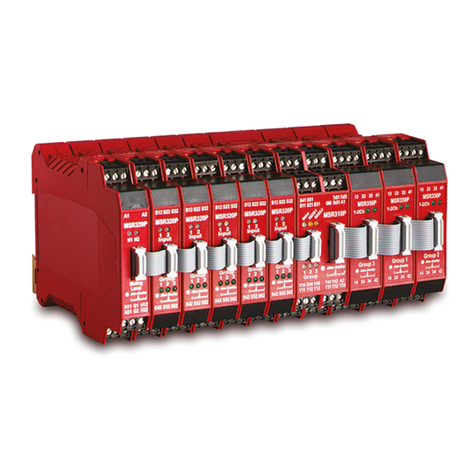
Rockwell Automation
Rockwell Automation MSR300 User manual
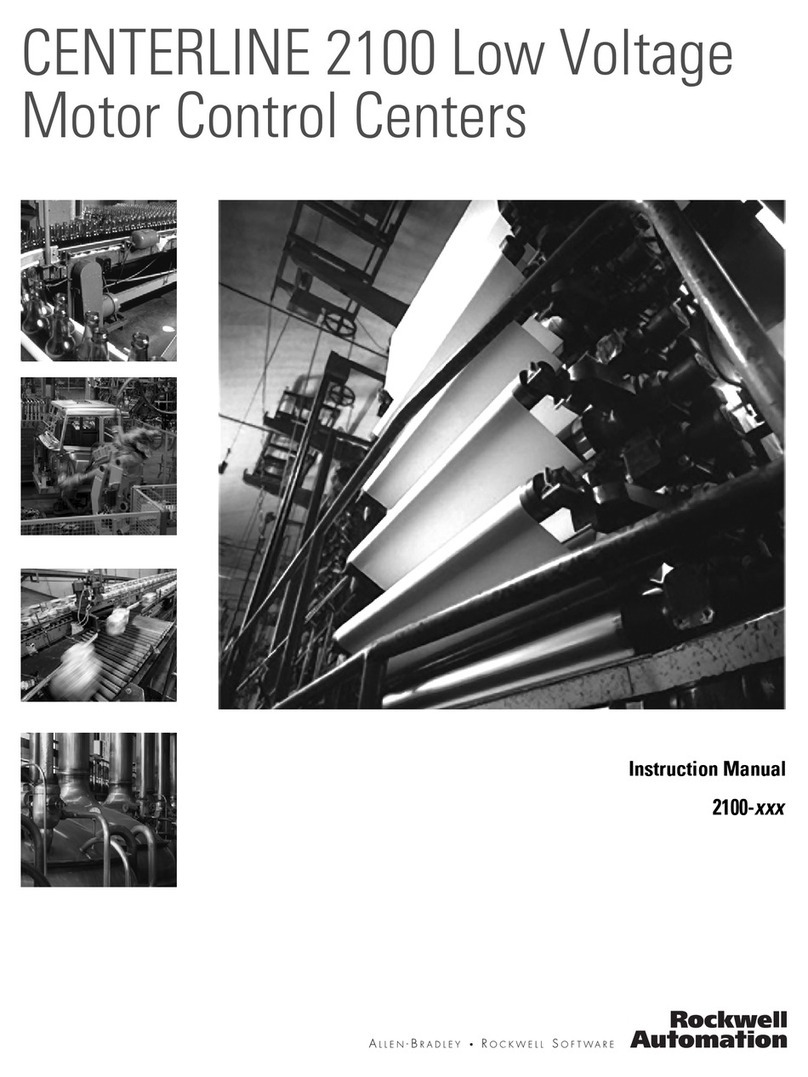
Rockwell Automation
Rockwell Automation CENTERLINE 2100 User manual
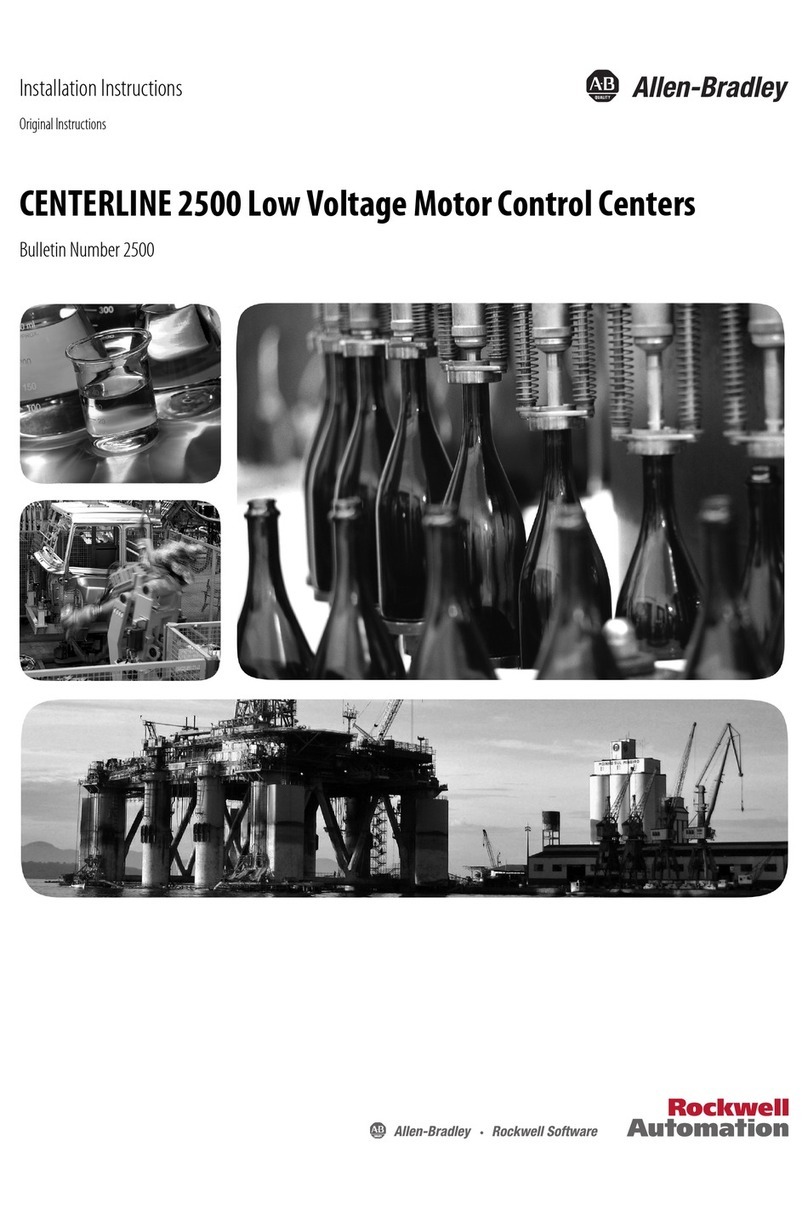
Rockwell Automation
Rockwell Automation Allen-Bradley CENTERLINE 2500 User manual
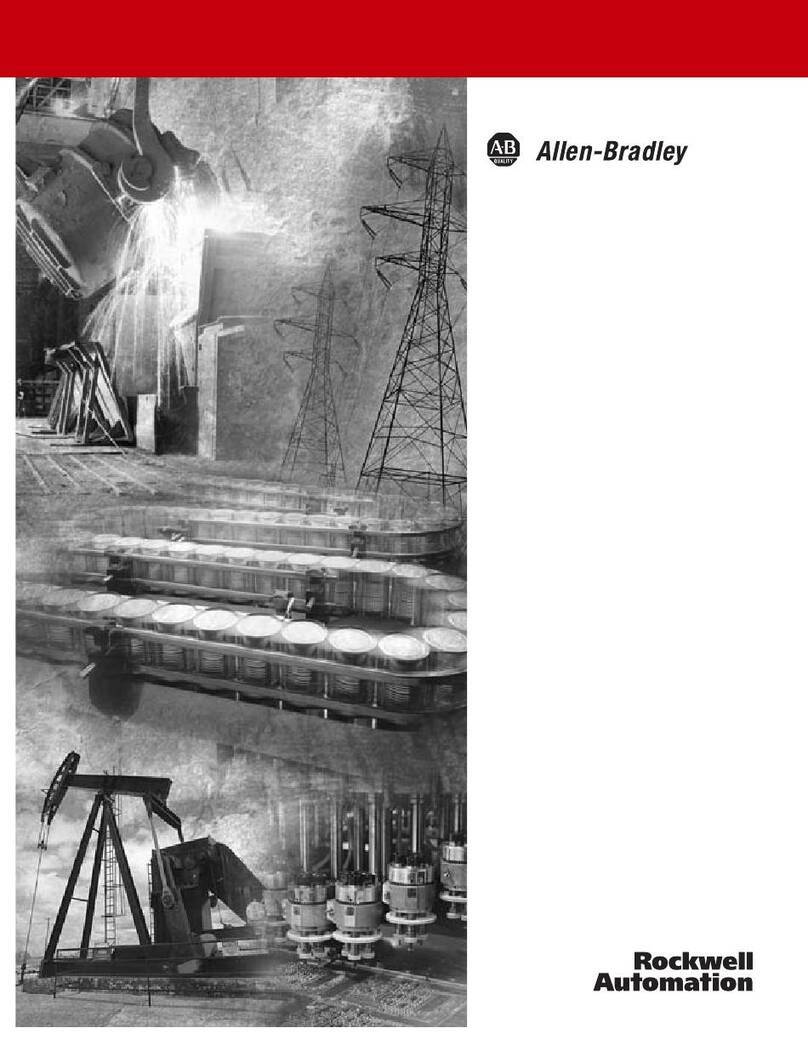
Rockwell Automation
Rockwell Automation Allen-Bradley Ultra5000 User manual
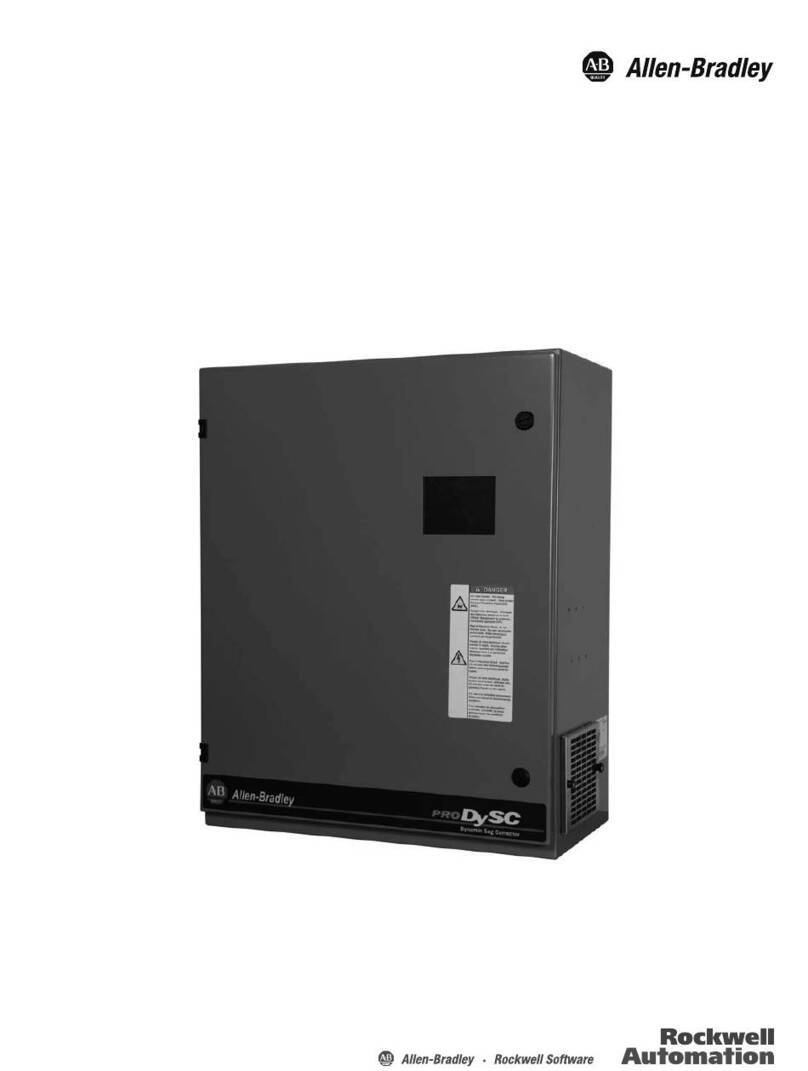
Rockwell Automation
Rockwell Automation AB Quality Allen-Bradley 1608P User manual