ROGUE MPT-3024 User manual

1
MPT-3024
30A - 12/24VDC MPPT
Photovoltaic Charge Controller
Installation Guide
and
Owner’s Manual
Rogue Power Technologies, Ashland, OR 97520
www.roguepowertech.com
© Copyright 2011, Revision C1, 05/18/11

2
Warranty and Liability Information
Rogue Power Technologies (hereafter RPT) warrants the MPT-3024 to
be free from defects in materials and workmanship for a period of five
(5) years from date of purchase. Warranty applies only to the original
purchaser. RPT will, at its option, either repair or replace a unit found
to be defective under the terms of this warranty. RPT’s sole liability
shall be said repair or replacement of a defective unit. RPT shall not be
held liable for incidental or consequential damages, or injury, arising
from the installation or use of this unit, nor shall RPT provide reim-
bursement for labor, removal or installation, shipping charges, or other
expenses not directly related to the terms of this warranty. RPT does not
warrant the workmanship of any persons installing this unit.
Conditions that will invalidate this warranty:
• Operation or installation contrary to the instructions provided in this
guide, including but not limited to: damage caused by reverse battery
connection, installation in an unapproved location, improper wiring,
etc.
• Damage caused by lightning or electrostatic discharge.
• Damage caused by abuse, neglect, or accident.
• Any unit which has been modified or repaired by anyone other than
RPT.
• Damage cause by natural disaster, shipping, transportation, or any
other circumstances outside of RPT’s control.
• Damage caused by another component of the power system.
• Any unit that has had its serial number or identification tag removed
or altered.
• Damage resulting from moisture or other environmental elements.
• Cosmetic damage, including scratches, scuffs, dents.
Before returning a unit for warranty service, please verify that the unit
is in fact defective. Shipping must be prepaid and insurance must be
purchased on any unit sent in for warranty service. RPT will pay return
shipping and insurance on units after the validity of the warranty claim
has been confirmed. Units sent in that are outside of their warranty
period, or units that do not qualify for warranty service based on the
above terms, will be returned at the expense of the sender. Units in need
of warranty service should be sent to: Rogue Power Technologies,
15975 Baldy Creek Rd., Ashland, OR 97520. Include a copy of the
original receipt and a detailed description of the problem.

3
Table of Contents
1. Introduction and Overview...................................................................................
2. Safety Information...............................................................................................
2.1 General safety precautions................................................................
3. Front Panel and LCD Display...............................................................................
4. System design considerations.............................................................................
4.1 Distance of wire runs.........................................................................
4.2 Wire size..........................................................................................
4.3 Optimal PV array voltage..................................................................
4.4 Optimal PV array power....................................................................
4.5 PV array location..............................................................................
4.6 Matching array modules....................................................................
5. Lead-Acid Battery Charging.................................................................................
5.1 Charging basics................................................................................
5.2 Charging modes................................................................................
6. Maximum Power Point Tracking...........................................................................
7. Remote Battery Temperature Sensor...................................................................
8. Remote Battery Voltage Sense............................................................................
9. Auxiliary Output / Relay.......................................................................................
10. RE-CONN Communications Port.........................................................................
11. Installation........................................................................................................
11.1 Mounting and thermal considerations..............................................
11.2 Wiring.............................................................................................
11.3 Grounding......................................................................................
11.4 Disconnects and overcurrent protection..........................................
11.5 External surge protection................................................................
11.6 External noise filtering....................................................................
11.7 Remote temperature sensor installation...........................................
11.8 Remote battery voltage sense connection........................................
11.9 Auxiliary output / relay connection...................................................
11.10 RE-CONN communication port connection......................................
11.11 Final Assembly..............................................................................
12. Setup and Configuration....................................................................................
12.1 Initialization....................................................................................
12.2 Setpoint adjustments.......................................................................
13. Operation.........................................................................................................
13.1 Backlight and autoexit features.......................................................
14. Data Logging....................................................................................................
15. Battery Equalization..........................................................................................
16. Use of Multiple/Other Charging Sources............................................................
17. Fault Messages.................................................................................................
18. Troubleshooting...............................................................................................
19. Specifications...................................................................................................
5
6
6
8
9
9
9
11
12
13
14
14
14
15
18
24
25
25
25
26
26
28
30
31
31
31
31
32
33
33
34
34
34
35
38
38
38
40
43
44
44
46

4
Tables, Graphs, and Diagrams
Tables
4.1.1. Copper wire resistance & power loss vs. gauge.............................
4.2.1. Wire distance vs. gauge & voltage drop for 12V............................
4.2.2. Wire distance vs. gauge & voltage drop for 24V............................
4.3.1. Typical voltage drop and power loss.............................................
4.4.1. Maximum PV array input...............................................................
12.2.1. Default values for setpoints........................................................
17.1.1. Fault messages..........................................................................
Graphs
5.2.1. Typical day of operation...............................................................
6.1.1. Typical PV array power curve........................................................
6.1.2. Efficiency......................................................................................
Diagrams
11.2.2. Wiring diagram...........................................................................
11.9.1. Auxiliary output wiring................................................................
12.1.1. Operational flowchart.................................................................
9
10
10
11
13
37
45
19
20
23
29
33
36

5
1. Introduction and Overview
The Rogue MPT-3024 is a highly efficient 30 amp photovoltaic charge
controller that features a proprietary maximum power point tracking algorithm
for peak performance under a variety of atmospheric conditions. The MPT-
3024 constantly monitors the PV array’s output and automatically readjusts it
as necessary to extract the most power available from it at any given moment.
The array is never disconnected from the battery to make measurements, nor
are periodic sweeps of the array conducted while the controller is operating in
the power tracking stage. Either of these methods can result in more downtime
and less power being delivered to the batteries. Boost of over 40% may be
achieved with the MPT-3024 when the batteries are in a low state of charge,
the PV array is cold, and the sun is bright.
The MPT-3024 is based on a DC-DC buck converter topology. As such, it’s
capable of operating with a PV array input voltage that is higher than the
voltage of the battery it’s charging. The MPT-3024 will accommodate a 24-volt
nominal PV array with either a 12-volt or 24-volt battery bank, or a 12-volt
nominal PV array with a 12-volt battery bank. It will not operate with a PV array
that generates less voltage than that of the battery it’s charging. Output
current is electronically limited to 30 amps.
The MPT-3024 has been designed and built using only the highest quality,
most reliable components available, including ultra-low resistance MOSFETS;
long life, high-temperature capacitors; a 40-MHz microprocessor; and a
heavy-gauge, low resistance inductor. Additionally, the MPT-3024 senses
current without the use of resistive shunts. This results in an output gain of at
least 3 watts over conventional current shunt technology.
The MPT-3024 utilizes an advanced six-stage charge routine to ensure that
batteries are maintained properly for long life and minimal maintenance. All
setpoints are fully adjustable from the front panel and are stored in a
non-volatile memory that retains information even when the power is removed.
Setpoints may be retrieved, viewed, and altered on the LCD display at any time
during normal operation. Also included with the unit is a remote temperature
sensor that will alter the programmed setpoints based on the temperature of
the batteries being charged. This prevents overcharging when the batteries are
warmer, and undercharging when the batteries are cooler.

6
The MPT-3024 features remote battery voltage sensing, which results in more
accurate charging. Additionally, it offers an auxiliary output relay that can be set
to turn on at a specific battery voltage. A RS-485 communication port is also
standard on the MPT-3024. It may be connected to a PC through the optional
DCV-0001data converter, and may also be directly connected to remote
monitoring and interface devices that may be available from Rogue.
Thirty days worth of data logging is kept in non-volatile memory. The data log
is retrievable during both normal operation and after the controller has entered
sleep mode. It can be erased at any time.
2. Safety Information
Please take a moment to read this manual and become better acquainted with
the features of the MPT-3024. As you read you will notice the following
symbols. They are meant to alert you of potential hazards, cautions, or
information that will require your attention as you install and use the MPT-
3024. Read the notations accompanying them carefully and understand their
content before continuing.
FPotential hazard to health, life, or property.
!Potential damage to charge controller or other ancillary equipment
if instructions are not followed.
SInformation that is useful in obtaining maximum performance from
the charge controller.
2.1 General safety precautions
1) This charger is intended for use only with lead-acid battery chemistries of
12- or 24-volt nominal system voltage. It may be suitable for other types of
batteries; consult your battery manufacturer for more information.
2) Lead-acid batteries produce small amounts of flammable hydrogen gas
during charging. Always work with batteries in a well-ventilated area and never
allow flames, sparks, or other sources of ignition within the vicinity of batteries
being charged.

7
3) Lead-acid batteries contain an electrolytic mixture of water and sulfuric acid.
Wear suitable eye and skin protection while working with batteries. Make sure
you have access to running water and a supply of baking soda nearby to
neutralize any spilled or splashed acid. Should acid contact eyes, wash
immediately with running water for at least ten minutes and get medical
attention.
4) Batteries are capable of producing an extremely large current under short
circuit conditions. This current can generate enough heat to weld metal and
cause severe burns. Be careful when using metal tools around batteries and
remove all metal jewelry before commencing work.
5) Never attempt to move or relocate a battery without first disconnecting it
completely from its circuit.
6) Never charge a frozen battery.
7) Always ensure that the battery’s electrolyte is filled to the level recom-
mended by the manufacturer. Failure to do so may cause permanent damage
to the battery.
8) The electricity generated by a PV array may be of sufficient voltage to cause
electric shock or electrocution. Practice industry-standard safety techniques at
all times when working around electricity and always disconnect electricity
before you begin work on a circuit.

8
1 - Array voltage (volts)
2 - Array current (amps)
3 - Array power (watts)
4 - Battery voltage (volts)
5 - Battery current (amps)
6 - Charger operating mode
• MPPT - bulk power tracking mode
• ABSB - absorb mode
• FULL - battery full
• FLOT - float mode
• EQLZ - equalize mode
7 - Accumulated PV Watt-hours (kWh if greater than 999Wh)
8 - Accumulated Amp-hours (as delivered to BATTERY)
9 - Battery temperature (if sensor is connected)
10-13 - Keypad legend
• BKLT - press for backlight on/off
• DATA - press for data log
• EQLZ - press to invoke equalize routine
• SETUP - press to view and alter setpoints
14 - Keypad
3. Front Panel and LCD Display

9
4. System Design Considerations
Whether you are planning and installing your energy system for the first time
or retrofitting an existing system, you’ll obtain the best performance if you
follow a few simple guidelines.
4.1 Minimize the distance of wire runs
Place the PV array and battery bank as close as practical to the MPT-3024.
This will limit the power loss associated with long wire runs. Longer lengths of
wire will cause an increase in power loss, especially at higher currents. See
Table 4.1.1 to determine the resistance of selected wire gauges versus wire
length.
4.2 Maximize wire size
The wire used to connect the PV array and battery bank to the MPT-3024
should be of a heavy enough gauge so as not to introduce excessive voltage
drops and/or current limitations. At higher currents, light gauge wire may
introduce a large voltage drop from the PV array, causing an extreme loss of
power and erratic operation of the MPT-3024. Wire of insufficient size may
also constrain charging current to the battery (which is charging at a relatively
constant voltage at any given point in time). The effects of wire size may not
be evident at lower charging currents; they may gradually appear and get
worse as current increases.
Table 4.1.1. Copper wire resistance and power loss versus wire gauge.
Wire Gauge
(copper)
Resistance
(ohms/ft at 25oC)
Power Loss @ 30A (watts/
ft)
#12 0.00162 1.46
#10 0.00102 0.92
#8 0.00064 0.58
#6 0.00040 0.36
#4 0.00025 0.23
#2 0.00016 0.14

10
NEC 310-15 restricts the minimum wire size for a 30-amp circuit to 10-gauge.
12-gauge may be used for installations of 20 amps or less, provided that the
length of the wire does not cause a significant voltage drop. Ideally the voltage
drop in any of your wiring runs should be 2% or less of the system voltage: for
example, this would be approximately 0.24 volts for a 12-volt system, or 0.48
volts for a 24-volt system. Refer to Tables 4.2.1 and 4.2.2 for help in
determining the proper gauge of wire when factoring in voltage drop and
distance.
#12 #10 #8 #6 #4 #2
5A 30 47 75 119 190 302
10A 15 24 37 60 95 151
15A 10 16 25 40 63 101
20A 7 1219304775
25A — 9 15 24 38 60
30A — 8 12 20 32 50
Table 4.2.1. Maximum distance (in feet) for wire at a specific gauge and cur-
rent, which will result in no more than a 0.24v (2%) voltage drop when used
with a 12-VOLT nominal system. Divide these distances in half for a round-trip
(both positive and negative) wire run.
#12 #10 #8 #6 #4 #2
5A 59 94 150 238 379 604
10A 30 47 75 119 190 302
15A 20 31 50 79 126 201
20A 15 24 37 60 95 151
25A —19304876121
30A —16254063101
Table 4.2.2. Maximum distance (in feet) for wire at a specific gauge and cur-
rent, which will result in no more than a 0.48v (2%) voltage drop when used
with a 24-VOLT nominal system. Divide these distances in half for a round-trip
(both positive and negative) wire run.

11
S Each connection to the terminal block of the MPT-3024 will accept
up to 4-gauge wire; however, for ease of installation and compliance with
code, it’s best to use wire no larger than 6-gauge within the enclosure. If it
is determined that a size of wire larger than 6-gauge is required to meet
the maximum voltage drop, a junction box may be used, in which a short
run of 6-gauge wire from the MPT-3024 is terminated at the larger gauge
wire.
4.3 Select the optimal PV array voltage
In most situations it’s best to wire your PV array for 24-volt nominal output. A
24-volt array is preferable because it will provide the same amount of power as
a 12-volt array of identical power output, but at half the current. Since power
loss in a wire is directly dependent on current, less current flowing through a
wire will result in less of a voltage drop across it. Using a 24-volt array instead
of a 12-volt array of the same power output will result one-fourth of the power
loss for any given wire gauge or distance. See Table 4.3.1 for an example of
24-volt versus 12-volt losses. The MPT-3024 will charge either a 12-volt or a
24-volt battery bank from a 24-volt array. Please note that some modules that
are labeled for 24-volt use actually exhibit a Vmp that is less than the typical
float voltage of a 24-volt battery. These types of modules must be used with a
12-volt battery bank to ensure satisfactory operation.
It can also be seen that as a PV array heats up, the voltage at which it
produces its maximum power output (Vmp)drops. This results in little or no gain
to be had by tracking the array’s maximum power point when charging a
battery bank of the same nominal voltage as the PV array.
PV Watts PV Volts
(nominal)
PV Amps Vdrop for 30ft
of 6ga
Ploss for 30ft
of 6ga
300W 12.0V 25.0A 0.30V 7.500W
300W 24.0V 12.5A 0.15V 1.875W
Table 4.3.1. Example of voltage drop and power losses for a given length of
wire when used with 300 watt, 12-volt and 24-volt systems. Notice that the
voltage drop in the 24-volt system is half that of the 12-volt, and that the
power loss drops by a factor of four.

12
! The MPT-3024 is designed to operate with 12-volt and 24-volt
nominal PV arrays. The absolute maximum input voltage is 60 volts. A
24-volt nominal array, which may produce more than 45 volts open-circuit
on a cold sunny day, is the maximum recommended standard array
configuration to be used with this controller. A 36-volt nominal array will
normally have an open-circuit voltage of greater than 60 volts, which will
exceed the operating voltage of the MPT-3024. Use of arrays greater than
24 volts nominal is therefore not recommended. Above the 60-volt limit,
damage to the controller may result, which is not covered by warranty.
4.4 Optimize PV array power
A match between your PV array’s output and your battery bank is important for
proper maintenance of your batteries. Your PV array’s output, and also the
storage capacity of your battery bank, will be determined by several factors,
including the average amount of sun available to your site and the demand that
your loads present. Consult a system installer or an appropriate text for help in
calculating your needs.
The MPT-3024 will charge battery banks given any amount of current provided
(up to the maximum of 30 amps), but may not reach setpoints regularly, and
may not equalize properly, if current is constantly insufficient. Conversely, an
array that is oversized will consistently push the MPT-3024 to its maximum limit
of 30A. At and beyond this limit the power from the array is constrained and the
MPPT algorithm is overridden so that the controller does not exceed its
maximum current output. To avoid wasting available power, follow the guide-
lines given in Table 4.4.1 when sizing your array.
NEC 690-8 requires that the maximum PV short-circuit current (Isc.) used with
the MPT-3024 be limited to 24 amps. This means that the maximum array
power is limited to about 835 watts for a 24-volt array with a voltage of 34.8
volts at its maximum power point connected to a 24-volt battery, 418 watts for
a 12-volt array with a Vmp of 17.4 volts connected to a 12-volt battery, and 418
watts for a 24-volt array with a Vmp of 34.8 volts connected to a 12-volt battery.
The maximum usable PV array power when taking into consideration system
losses may be approximately calculated using the following formula, where Vb
is the battery voltage: PV(watts) = (30 x Vb) / 0.90

13
4.5 Choose PV array location
Choose a location for your PV array, if possible, that will allow it full and
unobstructed access to the sun. This will dramatically increase its output and
will improve the tracking accuracy of its maximum power point.
A partially shaded array, especially an array that has panels wired in series, will
result in substantially less output and less-than-optimal tracking of the maxi-
mum power point. If your PV array experiences partial shading for much of the
day, and you are unable to relocate it to a better site, it is best to wire your
modules in parallel so that those modules which may be receiving full illumina-
tion will not be hampered by shaded modules.
PV Watts PV Volts
Vmp
PV Amps
Isc
Battery
Amps
Battery
Volts
Nominal
PV/Bat
1864 34.8 25 30** 28.8 24 / 24
2835 34.8 24* 29 28.8 24 / 24
3660 34.8 19 30** 22.0 24 / 24
4432 34.8 12.4 30** 14.4 24 / 12
5330 34.8 9.5 30** 11.0 24 / 12
6432 17.4 25 30** 14.4 12 / 12
7418 17.4 24* 29 14.4 12 / 12
8330 17.4 19 30** 11.0 12 / 12
Table 4.4.1. Maximum PV array input versus battery arrangement and state of
charge. * = PV input limited by NEC 690-8. ** = PV input limited by maxi-
mum 30A output of MPT-3024. Rows 1 and 6 suggest the maximum array
sizes that are feasible without regard to NEC 690-8, using maximum 30A out-
put limit for constraint. None of these values take into account losses from
wiring and converter efficiency, so in reality you could use a slightly larger ar-
ray than those shown to compensate for any system inefficiencies. Use of an
array much larger than suggested will result in wasted power beyond the 30
amp limit of the MPT-3024.

14
4.6 Match the modules of an array
Although the individual PV modules of an array need not necessarily be of the
same make or model, you will achieve better tracking performance from an
array in which all of the modules have the same maximum power point (Vmp).
This is best accomplished by choosing modules of the same make and model.
Even if modules are not identical, be sure that they each have the same
number of cells. While it is possible to wire modules together with varying
numbers of cells, this will degrade the output of the entire array.
5. Lead-Acid Battery Charging
5.1 Charging basics
It’s possible to charge a lead-acid battery by any one of several different
methods. Low-end chargers are typically on/off devices, where the charger
cycles between full on and full off depending on the terminal voltage of the
battery. These chargers may over- or undercharge a battery and provide no
means of maintaining a battery’s state once it has been completely charged.
More advanced chargers utilize a multi-stage approach that closely monitors
the battery’s voltage and the current being drawn by the battery during the
charging process. These chargers select a charging mode which best suits the
condition of the battery at any given time, resulting in optimal charging, less
maintenance, and extended battery life.
A lead-acid battery which is discharged generally begins charging at a rate
equal to its capacity in amp-hours divided by a value of five to twenty (C/5 to
C/20). C/10 is a good rate, which allows for fairly rapid, well-controlled
charging. A charger operating at this rate is in the BULK mode. A charge
controller operating from a PV array that is properly matched to its battery
bank seldom produces more than the C/10 rate, so it will usually charge a
battery in the bulk mode with all available power from the PV array.
A multi-stage charge controller will constantly monitor the terminal voltage at
the batteries during the BULK mode. The battery will be considered nearly full
once it reaches its absorption voltage (which is around 14.3 - 14.7 volts for
most lead-acid batteries). At this voltage, the BULK mode will terminate and the
charger will begin charging the battery at a constant voltage equal to its

15
absorption voltage. This is the ABSORB mode. As the battery reaches full
charge the charging current will gradually diminish because the battery voltage
is being held steady. Ideally, the ABSORB mode will terminate once the
charging current to the battery falls below a predetermined value (typically
equal to the battery capacity in Ah divided by 100). In some situations (external
loading), battery charging current cannot be accurately determined and so a
timer may be used instead to limit the amount of time that the charger spends
in this mode.
The battery is considered to be fully charged once the ABSORB mode is
terminated. Upon completion of this mode, the controller will initiate the FLOAT
mode, which charges the battery at a constant, predetermined voltage (usually
around 13.4 - 13.6 volts). The charging current will slowly rise as this voltage
is held steady and will eventually taper off to a steady value. The FLOAT mode
will persist indefinitely unless external factors (such as attached loads or a
change in the available input power) force the controller to revert to a previous
mode because the battery voltage begins to fall below the float setpoint.
Loads that are being powered during the charging procedure will cause power
that would otherwise be used for charging to be diverted. This will greatly
influence both the duration and sequence of the various charging modes.
Moderate to heavy loading will often prevent the battery from becoming fully
charged, and so the controller will remain in the BULK mode.
See the following section (5.2) for a more detailed explanation of each mode as
it pertains to the MPT-3024.
5.2 Charging modes
The MPT-3024 employs six distinct modes of charger operation.
1) MPPT: This is the default charging mode, also called the BULK mode, which
commences when the controller first has power applied and when it first wakes
up after sleeping. In this mode, the controller determines the voltage (Vmp) at
which the PV array produces the most power (see the discussion of maximum
power point tracking in Section 6 to understand how this works). While
operating in the MPPT mode, the controller will find this point and constantly
track it as it changes with array temperature and insolation. The result of this
operation is maximum power delivered to the batteries when they are less than

16
fully charged. As the charger operates in this mode, battery voltage will
gradually rise until it equals the absorb setpoint, at which point the batteries
are typically within 25% or less of being fully charged. PV voltage will be
maintained at its Vmp during this mode.
2) ABSORB: The controller will transition to this mode from the MPPT mode
when the battery voltage equals the absorb setpoint. The batteries will then be
charged at this constant voltage and a timer will begin counting down based on
the value of the FLOTM setpoint. The charger will remain in this mode until one
of these two conditions are met: A) The battery charging current eventually
decreases to the value defined by the FLOTR setpoint, or B) The time defined
by the FLOTM setpoint has elapsed. In general, if the charger is supplying
current to loads as well as charging batteries in this mode, the FLOTR setpoint
will never be met because the loads will almost always be demanding a current
greater than that of the FLOTR setpoint. The timer will instead elapse and force
a transition to the full state. If the controller cannot maintain the battery voltage
within 0.2 volts of the absorb setpoint (because of insufficient current from the
PV array and/or excessive loads), it will revert back to the MPPT mode and will
once more begin charging up to the absorb setpoint. The absorb timer will be
reset and will begin counting down again when the controller next enters the
absorb mode. This transition between MPPT and ABSORB modes may occur
back and forth a number of times when the battery voltage is near the absorb
setpoint on partly cloudy days. The absorb mode may be disabled by setting
the FLOTM setpoint to its minimum value of zero minutes. If absorb is disabled,
the controller will transition immediately to full upon reaching the absorb
setpoint voltage, and will remain in this mode indefinitely unless triggered back
into the MPPT mode, as described above. Note that if both the absorb mode
and the float mode have been disabled, the charger will remain in the absorb
mode indefinitely. The absorb mode will be re-enabled (FLOTM will be reset to
its default of 180 minutes or 3 hours) if power is disconnected from the
MPT-3024 while absorb is disabled.
3) FULL: In this mode, the charger has been turned off so that no power is
being supplied to the batteries. The controller will transition to this mode upon
completion of the ABSORB mode, or any time the battery charging current
drops to zero while the controller is in float mode (as may happen if the float
setpoint is lowered while the controller is in float mode). It will remain in this
mode until the battery voltage drops to about 0.05 volt below the value defined
by the float setpoint and the batteries begin drawing current.

17
4) FLOAT: This mode commences after the batteries have become fully
charged, when they once again begin to draw current. A battery in good
condition will typically draw less than 0.5A of current per 100Ah of battery
capacity once float has stabilized. The charger will remain in this constant
voltage mode indefinitely and will maintain the batteries in the full state,
compensating for self-discharge. The PV voltage will often be very near the
array’s Voc during float mode. If the controller cannot maintain the battery
voltage within 0.2 volts of the float setpoint (because of insufficient current
from the PV array and/or excessive loads), it will revert back to the MPPT mode
and the charge routine starts over. As the sun sets at the end of the day and/or
the PV array becomes shaded, the controller will exit float mode and will return
to MPPT mode, where it will remain until the PV array is unable to provide at
least 100mA of current to the charger. At less than 100mA, the controller will
enter sleep mode. The float mode may be disabled by increasing the float
setpoint beyond its maximum value, until the display reads “DSABL.” If float
mode is disabled, the charger will remain in absorb mode indefinitely upon
reaching the absorb setpoint voltage, unless triggered back into MPPT mode as
described above. Float cannot be disabled while the charger is presently
operating in float mode.
5) SLEEP: The controller will enter sleep mode when the PV array is unable to
provide at least 100mA of current. Upon entering this mode, the batteries are
no longer receiving a charge, the PV array is disconnected, the microprocessor
operates at a reduced speed, and only essential circuit elements continue to
receive power. These measures ensure that the MPT-3024 consumes minimal
power while sleeping. In this mode the controller will check the open-circuit
voltage (Voc) of the PV array every five minutes. If the array’s Voc is at least 2.0
volts above the battery voltage, the controller will wake up, enter MPPT mode,
and attempt to charge the batteries. The PV array must be able to provide at
least 100mA of current at this point, or the controller will resume sleeping, and
will try again in another five minutes. The controller may wake up and go back
to sleep several times in the morning and evening before finally settling in a
steady state. Sleep mode may also occasionally be invoked due to adverse
weather conditions, such as snow or heavy clouds. The sleep mode consumes
about 53mW of power (approximately 2.2mA of current with a 24-volt battery
bank).
6) EQUALIZE: This mode is not one of the routine modes of normal charger
operation and must be initiated manually by pressing the EQLZ key during

18
normal charger operation (see Section 15 for instructions). Upon selecting this
mode the controller will resume operation in the MPPT mode (if it’s presently in
any other mode, it will exit that mode and enter MPPT mode), and will begin an
attempt to charge the batteries until their voltage reaches the value determined
by the EQLZ setpoint. Once the equalize setpoint has been met, the controller
will transition to the equalize mode and will try to maintain the battery voltage
at the equalize setpoint for the amount of time specified by the user. The
controller will remain in this mode until either the timer has elapsed, the user
aborts the operation, or the controller enters the sleep mode. If the controller
enters the sleep mode before the equalize setpoint has been met, or before
the timer has fully elapsed, it will display an error when it reawakens and will not
attempt to resume operation in the equalize mode. For safety reasons,
equalize must always be initiated (or re-initiated) manually.
See Figure 5.2.1 for mode transitions during a typical day of operation.
6. Maximum Power Point Tracking
A PV array, for the most part, delivers a constant current over a wide range of
voltages. For this reason, it’s usually thought of as a
constant
current
source.
By contrast, a battery will provide a relatively constant voltage over a wide
range of currents; it’s called a
constant voltage
source.
An array that is sold for 12-volt use, for example, actually generates anywhere
from zero to about 21 volts, depending on the load it’s connected to and the
number of individual cells comprising the array. A PV array will develop its
highest voltage without a load; this is the open-circuit condition, and the
voltage measured at this point is called Voc. Since there is no load in the
open-circuit condition, the resistance of the load is essentially infinite, and
therefore the array will produce no current at Voc. With no current flowing, and
because power equals voltage multiplied by current (P=VxI) the power being
produce by the array will be zero watts.
At the other extreme, the load connected to the array can be a short circuit, the
resistance of which is zero ohms. Under this condition the array will produce the
maximum amount of current of which it’s capable, called Isc. Since the load
under this condition (ideally) offers no resistance, there can be no voltage
across it. The array under a short circuit therefore generates no voltage, and
like the open-circuited array, produces no power.

19
Figure 5.2.1. A typical day of operation for the MPT-3024 with 24-volt nominal array
and 12-volt battery bank.

20
Between the open circuit and short circuit conditions, there is a point at which
the array’s voltage and current will come together to produce the maximum
amount of power. This is called the
maximum power point
of the array, with a
voltage of Vmp (Figure 6.1.1).
The direct connection of a battery to a PV array causes the array to operate at
the voltage of the battery. This is generally well below the Vmp of the array. Take,
for example, a battery that is being charged at 12.0 volts. The Vmp of the array
to which the battery is connected is 17.4 volts., which is 5.4 volts above the
battery voltage. The array, producing a nearly constant current of, say, 4.0
amps, will generate 69.6 watts (17.4 x 4.0) of power at its maximum power
point of 17.4 volts. If connected directly to a battery being charged at 12.0
volts, the array is able to produce only 48.0 watts (12.0 x 4.0) – a 21.6 watt
loss.
The MPT-3024 is capable of operating the array at its maximum power point
voltage while charging a battery of substantially less voltage. It does this by
rapidly switching on and off (many thousands of times per second) the
connection between the array and the battery. The on-time (the pulse width) of
this switching may be varied according to PV output and the state of charge of
the battery. The energy from the PV array is stored in an inductor during the
on-time, released during the off-time, and the output filtered. The result is a
nearly lossless power converter. It’s able to take a higher input voltage at a
Figure 6.1.1. Typical PV array
power curve. Notice that the maxi-
mum power point (Vmp) changes
with the amount, intensity, and
type of sunlight received. Partial
shading (B) may cause a second,
lesser peak to appear on the
curve, which can result in a loss of
tracking efficiency and a signifi-
cant loss in output from the array.
The curve flattens out as light
intensity drops (C). At very low
light levels, the power curve will
have have no discernable Vmp to
track.
Table of contents
Popular Controllers manuals by other brands

Altronic
Altronic EPC-250 Installation and operating instructions
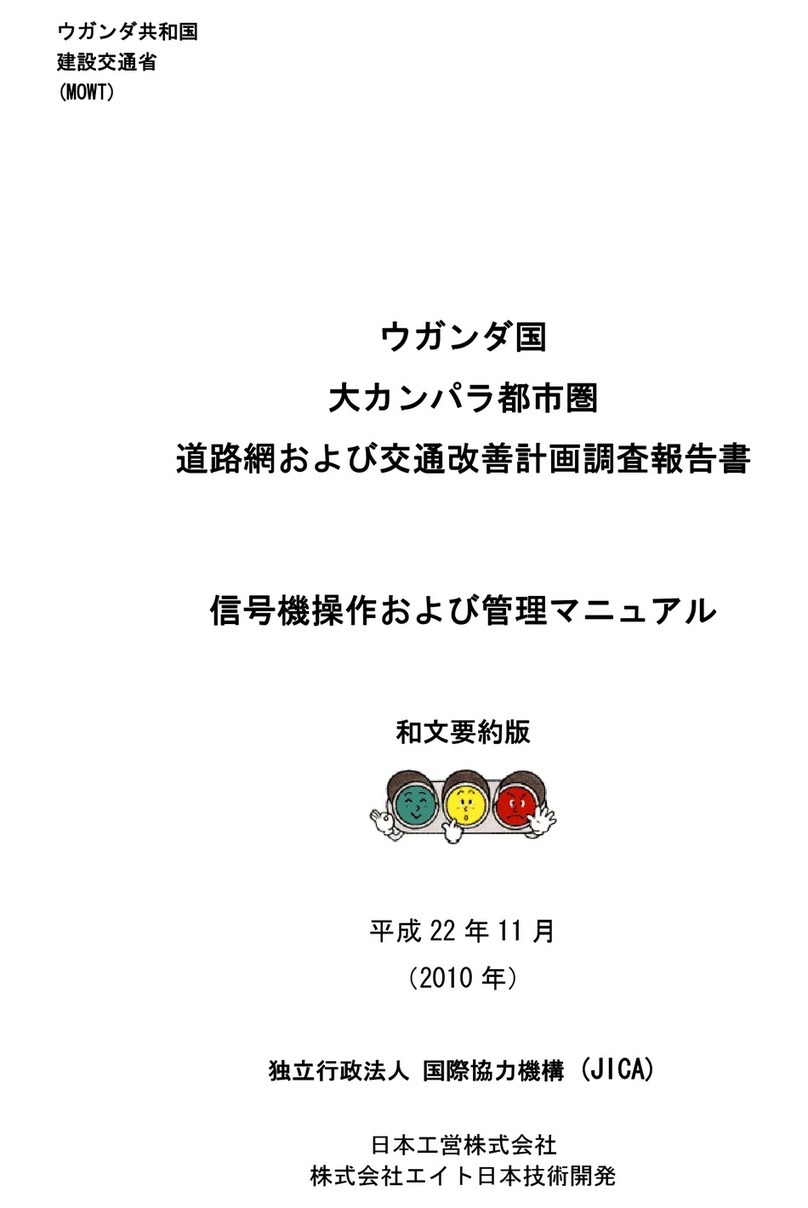
Matsunaga
Matsunaga TSA-1030-CJ operating instructions
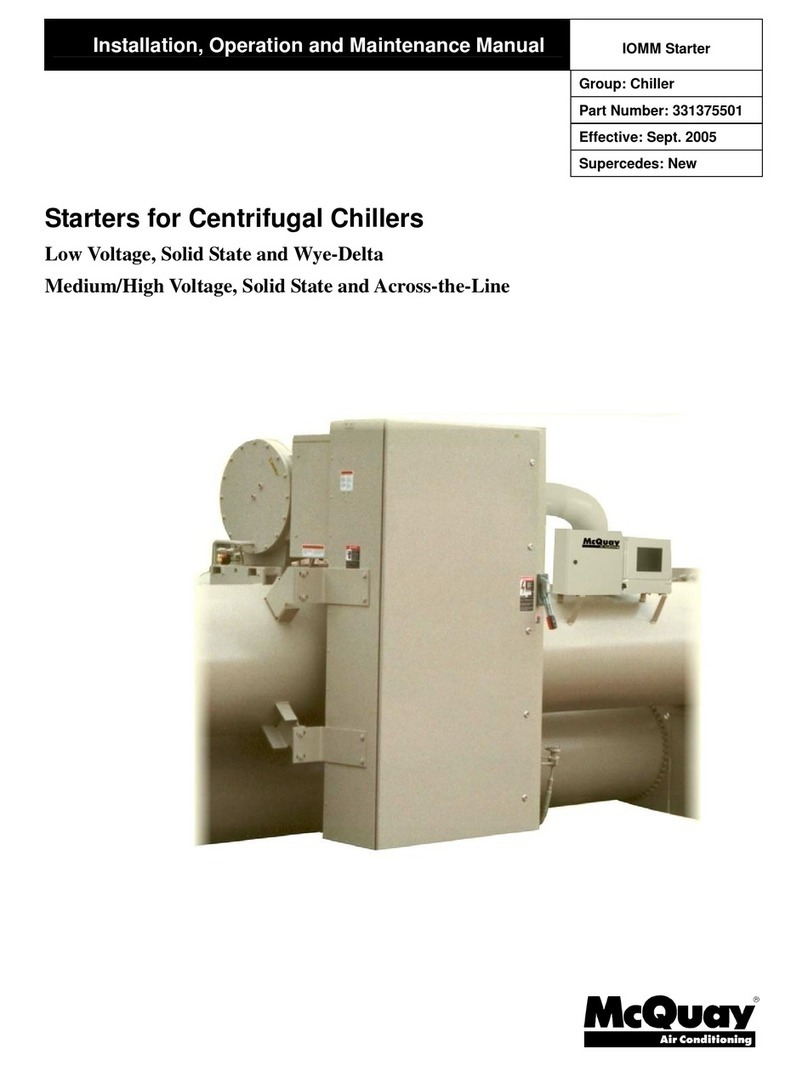
McQuay
McQuay RVSS14 Installation, operation and maintenance manual
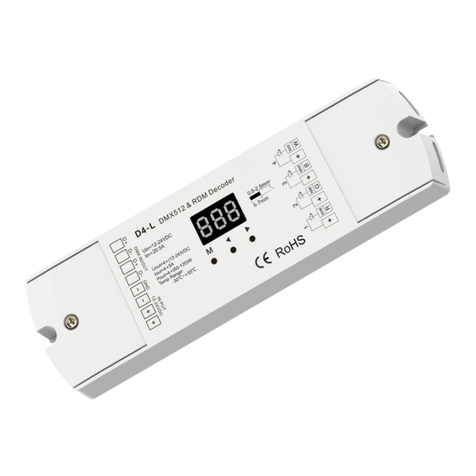
SKYDANCE
SKYDANCE RGBW user guide
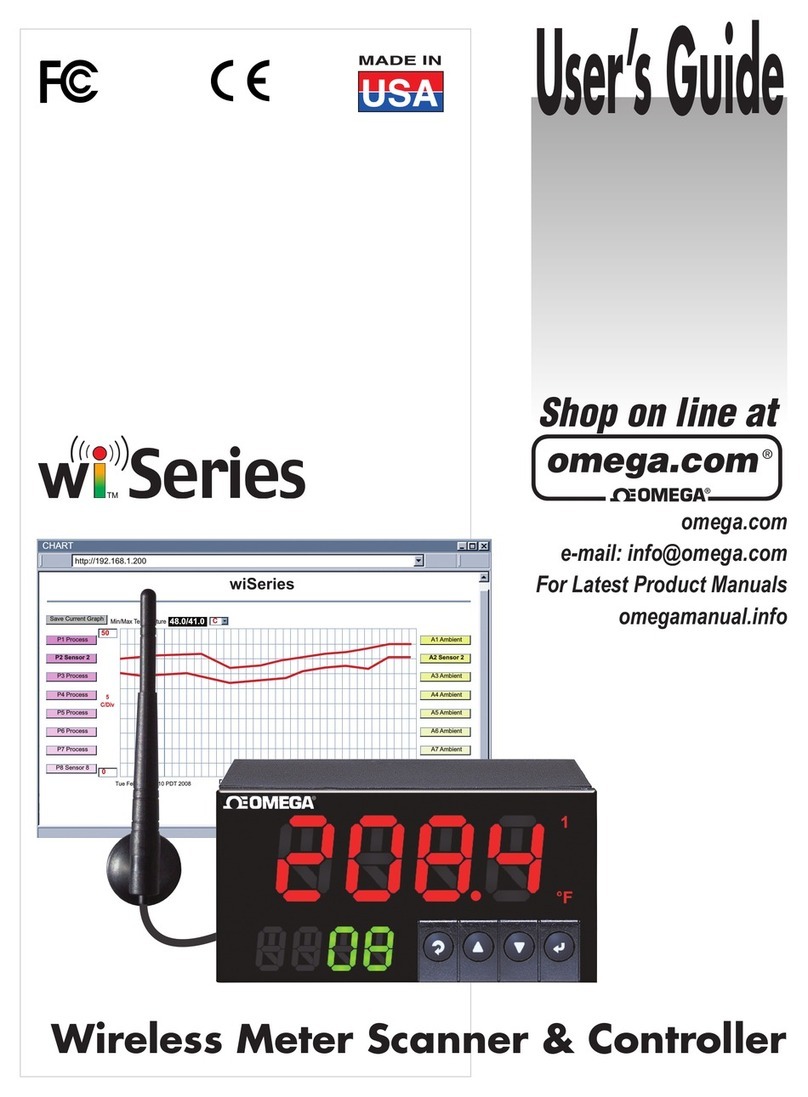
Omega Engineering
Omega Engineering Wireless Meter Scanner & Controller wi... user guide
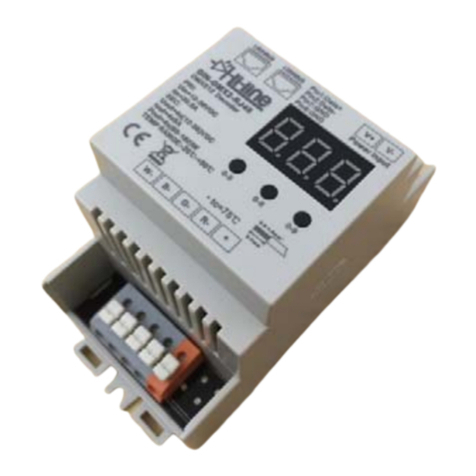
Hi-Line
Hi-Line DIN-DMX2-RJ45 Settings guide