SICK ReLy TIME1 User manual

OPERATING INSTRUCTIONS
ReLy TIME1
Safety relay

Described product
ReLy TIME1
Manufacturer
SICK AG
Erwin-Sick-Str. 1
79183 Waldkirch
Germany
Legal information
This work is protected by copyright. Any rights derived from the copyright shall be
reserved for SICK AG. Reproduction of this document or parts of this document is only
permissible within the limits of the legal determination of Copyright Law. Any modifica‐
tion, abridgment or translation of this document is prohibited without the express writ‐
ten permission of SICK AG.
The trademarks stated in this document are the property of their respective owner.
© SICK AG. All rights reserved.
Original document
This document is an original document of SICK AG.
2O P E R A T I N G I N S T R U C T I O N S | ReLy TIME1 8024303/2019-12-18 | SICK
Subject to change without notice

Contents
1 About this document........................................................................ 5
1.1 Purpose of this document........................................................................ 5
1.2 Scope......................................................................................................... 5
1.3 Target groups and structure of these operating instructions................ 5
1.4 Additional information.............................................................................. 5
1.5 Symbols and document conventions...................................................... 6
2 Safety information............................................................................ 7
2.1 General safety notes................................................................................ 7
2.2 Intended use............................................................................................. 7
2.3 Improper use............................................................................................. 7
2.4 Requirements for the qualification of personnel.................................... 8
3 Product description........................................................................... 9
3.1 Construction and function........................................................................ 9
3.2 Product characteristics............................................................................ 9
3.2.1 Device overview....................................................................... 9
3.2.2 Interfaces................................................................................. 9
3.2.3 Compatible sensor types......................................................... 10
3.2.4 Release-delayed enabling current paths................................ 10
3.2.5 Restart interlock...................................................................... 10
3.2.6 External device monitoring...................................................... 10
3.2.7 Cross-circuit detection............................................................. 10
3.2.8 Status indicators...................................................................... 10
4 Project planning................................................................................ 12
4.1 Manufacturer of the machine.................................................................. 12
4.2 Operating entity of the machine.............................................................. 12
4.3 Design........................................................................................................ 12
4.4 Electrical integration................................................................................. 13
4.4.1 Enabling current paths............................................................ 13
4.4.2 Application diagnostic output................................................. 13
4.4.3 Restart interlock...................................................................... 14
4.4.4 External device monitoring (EDM).......................................... 14
4.4.5 Connection diagrams.............................................................. 15
4.5 Testing plan............................................................................................... 15
4.5.1 Minimum requirements for the regular thorough check....... 15
5 Mounting............................................................................................. 16
5.1 Safety......................................................................................................... 16
5.2 Mounting procedure................................................................................. 16
5.3 Disassembly.............................................................................................. 17
5.4 Module exchange...................................................................................... 17
6 Electrical installation........................................................................ 19
CONTENTS
8024303/2019-12-18 | SICK O P E R A T I N G I N S T R U C T I O N S | ReLy TIME1 3
Subject to change without notice

6.1 Device connection.................................................................................... 19
7 Configuration..................................................................................... 22
7.1 DIP switch.................................................................................................. 22
7.2 Configuring release delay......................................................................... 22
7.3 Configuring sensor type........................................................................... 23
7.4 Activating configuration............................................................................ 24
7.5 Resetting the configuration...................................................................... 24
8 Commissioning.................................................................................. 25
8.1 Safety......................................................................................................... 25
8.2 Thorough check........................................................................................ 25
9 Troubleshooting................................................................................. 26
9.1 Safety......................................................................................................... 26
9.2 Status indicator (LED)............................................................................... 26
10 Decommissioning............................................................................. 28
10.1 Disposal..................................................................................................... 28
11 Technical data.................................................................................... 29
11.1 Data sheet................................................................................................. 29
11.2 Dimensional drawings.............................................................................. 35
11.3 Internal circuitry........................................................................................ 35
12 Ordering information........................................................................ 36
12.1 Ordering information for ReLy.................................................................. 36
13 Annex.................................................................................................. 37
13.1 Compliance with EU directives................................................................. 37
14 List of figures..................................................................................... 38
15 List of tables....................................................................................... 39
CONTENTS
4O P E R A T I N G I N S T R U C T I O N S | ReLy TIME1 8024303/2019-12-18 | SICK
Subject to change without notice

1 About this document
1.1 Purpose of this document
These operating instructions contain the information required during the life cycle of the
safety relay.
These operating instructions must be made available to everyone who works with the
safety relay.
1.2 Scope
This document only applies to a ReLy safety relay with the following type label entries in
the Operating Instructions field:
•8024299
1.3 Target groups and structure of these operating instructions
These operating instructions are intended for the following target groups: project devel‐
opers (planners, developers, designers), installers, electricians, safety experts (such as
CE authorized representatives, compliance officers, people who test and approve the
application), operators, and maintenance personnel.
These operating instructions are organized by the life phases of the device: project
planning, mounting, electrical installation, commissioning, operation and maintenance.
The table below shows the target groups and how – for many applications – these are
typically divided up between the manufacturer and the entity operating the machine in
which the device is to be integrated:
Area of responsibility Target group Specific chapters of these operating instruc‐
tions 1)
Manufacturer Project developers
(planners, developers,
designers)
"Project planning", page 12
"Technical data", page 29
Installers "Mounting", page 16
Electricians "Electrical installation", page 19
Safety experts "Project planning", page 12
"Commissioning", page 25
"Technical data", page 29
Operating entity Operators "Troubleshooting", page 26
Maintenance person‐
nel
"Troubleshooting", page 26
"Ordering information", page 36
1) Chapters not listed here are intended for all target groups. All target groups must follow all of the safety
and warning instructions in all chapters of the operating instructions!
In other applications, the operating organization is also the manufacturer of the equip‐
ment with the corresponding allocation of the target groups.
1.4 Additional information
www.sick.com
The following information is available on the Internet:
•This document in other languages
•Data sheets and application examples
•CAD data and dimensional drawings
ABOUT THIS DOCUMENT 1
8024303/2019-12-18 | SICK O P E R A T I N G I N S T R U C T I O N S | ReLy TIME1 5
Subject to change without notice

•Certificates (e.g. EU declaration of conformity)
•Guide for Safe Machinery Six steps to a safe machine
1.5 Symbols and document conventions
The following symbols and conventions are used in this document:
Safety notes and other notes
DANGER
Indicates a situation presenting imminent danger, which will lead to death or serious
injuries if not prevented.
WARNING
Indicates a situation presenting possible danger, which may lead to death or serious
injuries if not prevented.
CAUTION
Indicates a situation presenting possible danger, which may lead to moderate or minor
injuries if not prevented.
NOTICE
Indicates a situation presenting possible danger, which may lead to property damage if
not prevented.
NOTE
Indicates useful tips and recommendations.
Instructions to action
bThe arrow denotes instructions to action.
1. The sequence of instructions for action is numbered.
2. Follow the order in which the numbered instructions are given.
✓The check mark denotes the result of an instruction.
LED symbols
These symbols indicate the status of an LED:
oThe LED is off.
ÖThe LED is flashing.
OThe LED is illuminated continuously.
1 ABOUT THIS DOCUMENT
6O P E R A T I N G I N S T R U C T I O N S | ReLy TIME1 8024303/2019-12-18 | SICK
Subject to change without notice

2 Safety information
2.1 General safety notes
DANGER
If the safety component is integrated incorrectly, the dangerous state may be ended to
late.
bPlan the integration of the safety component in accordance with the machine
requirements, see "Project planning", page 12.
DANGER
Hazard due to lack of effectiveness of the protective device
In the case of non-compliance, it is possible that the dangerous state of the machine
may not be stopped or not stopped in a timely manner.
bPlease read this document carefully and make sure that you understand the con‐
tent fully before working with the device.
bFollow all safety notes in this document.
Improper installation or manipulation can lead to serious injuries.
2.2 Intended use
The safety relay is an evaluation unit device for switching safety-related circuits on and
off for the following sensor types:
•Emergency stop pushbutton
•Safety switches
•Sensors with OSSDs
•Safety devices with OSSDs
The safety relay complies with class A, group 1 as per EN 55011. Group 1 encom‐
passes all ISM devices in which intentionally generated and/or used conductor-bound
RF energy that is required for the inner function of the device itself occurs.
The safety relay must only be used within the limits of the prescribed and specified
technical data and operating conditions at all times.
Incorrect use, improper modification or manipulation of the safety relay will invalidate
any warranty from SICK; in addition, any responsibility and liability of SICK for damage
and secondary damage caused by this is excluded.
UL/CSA applications
If the product is being used in accordance with UL 508 or CSA C22.2 No. 14, the follow‐
ing conditions must also be met:
•To protect the device’s 24-volt voltage supply, use a fuse with a maximum voltage
of 4 A and a minimum of 30 V DC in accordance with UL 248.
NOTE
The safety functions have not be evaluated by UL. Authorization is in accordance with
UL 508, general applications.
2.3 Improper use
The safety relay is not suitable for the following applications (this list is not exhaustive):
SAFETY INFORMATION 2
8024303/2019-12-18 | SICK O P E R A T I N G I N S T R U C T I O N S | ReLy TIME1 7
Subject to change without notice

•At altitudes of over 4,000 m above sea level
•In explosion-hazardous areas
2.4 Requirements for the qualification of personnel
The protective device must be configured, installed, connected, commissioned, and ser‐
viced by qualified safety personnel only.
Project planning
For project planning, a person is considered competent when he/she has expertise and
experience in the selection and use of protective devices on machines and is familiar
with the relevant technical rules and national work safety regulations.
Mechanical mounting, electrical installation, and commissioning
For the task, a person is considered qualified when he/she has the expertise and expe‐
rience in the relevant field and is sufficiently familiar with the application of the protec‐
tive device on the machine to be able to assess whether it is in an operationally safe
state.
Operation and maintenance
For operation and maintenance, a person is considered competent when he/she has
the expertise and experience in the relevant field and is sufficiently familiar with the
application of the protective device on the machine and has been instructed by the
machine operator in its operation.
2 SAFETY INFORMATION
8O P E R A T I N G I N S T R U C T I O N S | ReLy TIME1 8024303/2019-12-18 | SICK
Subject to change without notice

3 Product description
3.1 Construction and function
The safety relay ReLy TIME1 is an electrical switching device with inputs and outputs.
The safety capable inputs of the safety relay are connected to safety sensors or safety
switches.
2 safety capable inputs control the internal relays, which are used to reliably switch the
enabling current paths.
The enabling current paths close only when the two safety capable inputs close within
3 s of one another.
Actuators with positively guided contacts are connected to the enabling current paths.
Opening the input circuit causes the two enabling current paths to open immediately
and for the release-delayed enabling current path to open after a delay. The delay time
is adjustable.
3.2 Product characteristics
3.2.1 Device overview
RELY
PWR
OUT
13
23
I1
Y1
14
24
I2
Y2
A2
S1
37
A1
38
X1 X2
R1
1
2
3
4
Figure 1: Device overview
1Device unlocking
2LEDs
3Front connector unlocking
4Front connector
3.2.2 Interfaces
Inputs
•2 safety capable inputs
•Input for reset pushbutton or external device monitoring
Outputs
•2 enabling current paths (safe)
•1 enabling current path for stop category 1 applications (safe)
PRODUCT DESCRIPTION 3
8024303/2019-12-18 | SICK O P E R A T I N G I N S T R U C T I O N S | ReLy TIME1 9
Subject to change without notice

•2 application diagnostic outputs (not safe)
•3 test outputs (not safe)
3.2.3 Compatible sensor types
The safety relay is suitable for:
•Safety sensors and safety switches with volt-free output contacts (EMSS), e.g.:
Dual-channel safety command devices (emergency stop pushbuttons, rope pull
switches, etc.), dual-channel contact-based interlocking devices (safety locking
devices and safety switches) and dual-channel magnetic safety switches with reed
contacts
•Safety sensors and safety switches with OSSD output, e.g.: Electro-sensitive pro‐
tective equipment (ESPE) with a single-channel or dual-channel monitored active
switching output with cross-circuit detection (OSSD)
3.2.4 Release-delayed enabling current paths
The release-delayed enabling current path opens with a set delay time.
3.2.5 Restart interlock
A restart interlock can be implemented with a reset pushbutton.
3.2.6 External device monitoring
Permanent external device monitoring can be implemented using external wiring.
3.2.7 Cross-circuit detection
A cross-circuit is detected on the safety capable inputs if the “Contacts” sensor type is
configured.
3.2.8 Status indicators
LEDs
RELY
PWR
OUT
13
23
I1
Y1
14
24
I2
Y2
A2
S1
37
A1
38
X1 X2
R1
PWR
OUT
13
23
I1
Y1
14
24
I2
Y2
A2
R1
A1
S1
X1 X2
TIME1
1100688
RELY
37 38
Figure 2: LEDs
The labeled positions are only partially assigned LEDs. The positions and their labeling
(except for the upper 2 lines) also show the pin assignment of the terminals on the front
connector.
3 PRODUCT DESCRIPTION
10 O P E R A T I N G I N S T R U C T I O N S | ReLy TIME1 8024303/2019-12-18 | SICK
Subject to change without notice

Table 1: Safety relay indicators
Labeling Color Function
PWR Green/Red Voltage supply
OUT Green Enabling current paths
I1 Green Safety capable input
I2 Green Safety capable input
S1 Green Reset pushbutton input, exter‐
nal device monitoring (EDM)
Y1 Green Application diagnostic output
Y2 Green Application diagnostic output
(reset required)
Further topics
•"Status indicator (LED)", page 26
PRODUCT DESCRIPTION 3
8024303/2019-12-18 | SICK O P E R A T I N G I N S T R U C T I O N S | ReLy TIME1 11
Subject to change without notice

4 Project planning
4.1 Manufacturer of the machine
DANGER
Failure to comply with manufacturer’s obligations
Hazard due to lack of effectiveness of the protective device
bCarry out a risk assessment before using the safety relay.
bDo not manipulate, open or modify the components of the safety relay.
bMake sure the safety relay is only repaired by the manufacturer or by someone
authorized by the manufacturer. Improper repair can lead to a loss of the protec‐
tive function.
4.2 Operating entity of the machine
DANGER
Failure to observe operator obligations
Hazard due to lack of effectiveness of the protective device
bChanges to the machine and changes to the mechanical mounting of the safety
relay necessitate a new risk assessment. The results of this risk assessment may
require the entity operating the machine to meet the obligations of a manufac‐
turer.
bApart from the procedures described in this document, the components of the
safety relay must not be opened or modified.
bDo not carry out any repair work on components. Improper repair of the safety
relay can lead to a loss of the protective function.
4.3 Design
The safety relay must be installed in a control cabinet with an enclosure rating of IP54
or higher.
The safety relay must be installed on a mounting rail (35 mm) in accordance with IEC
60715.
Space requirements in the control cabinet
To ensure sufficient air circulation and cooling, sufficient distance must be kept in the
control cabinet above and below the safety relay.
Sufficient distance must be kept for the connected cables before the module (front
side).
4 PROJECT PLANNING
12 O P E R A T I N G I N S T R U C T I O N S | ReLy TIME1 8024303/2019-12-18 | SICK
Subject to change without notice

≥ 50≥ 50
≥ 25
Figure 3: Distances in control cabinet
Required distance:
•Above and below the module: ≥ 50 mm
•In front of the module: ≥ 25 mm
4.4 Electrical integration
Important information
DANGER
Hazard due to lack of effectiveness of the protective device
In the case of non-compliance, it is possible that the dangerous state of the machine
may not be stopped or not stopped in a timely manner.
bEnsure the safety relay is supplied with supply voltage in all operating statuses.
bEnsure that the supply voltage of the safety relay is not connected via safety sen‐
sors or safety switches in order to switch the enabling current paths.
4.4.1 Enabling current paths
DANGER
Hazard due to lack of effectiveness of the protective device
bEnsure the enabling current paths are supplied by the same voltage supply.
4.4.2 Application diagnostic output
Application diagnostic output Y1
The signal of the Y1 application diagnostic output changes as soon as the enabling cur‐
rent paths switch. The application diagnostic output is not safe.
Application diagnostic output Y1 is based on the push-pull principle, meaning it can
both absorb and apply current.
PROJECT PLANNING 4
8024303/2019-12-18 | SICK O P E R A T I N G I N S T R U C T I O N S | ReLy TIME1 13
Subject to change without notice

Table 2: Switching behavior of application diagnostic output Y1
State of enabling current paths State of application diagnostic output Y1
Closed 0 V (NPN)
Open 24 V (PNP)
Application diagnostic output Y2
Application diagnostic output Y2 outputs the “Reset required” signal with a frequency of
1 Hz, e.g. for the connection of a signal lamp.
Application diagnostic output Y2 is based on the push-pull principle, meaning it can
both absorb and apply current.
Table 3: Switching behavior of application diagnostic output Y2
State of enabling current paths State of application diagnostic output Y2
Closed 0 V (NPN)
Open 24 V (PNP)
4.4.3 Restart interlock
Important information
DANGER
Hazard due to unexpected starting of the machine
Death or severe injury
bIf you connect the safety relay to an emergency stop pushbutton, you must use the
restart interlock.
Restart interlock
A reset pushbutton must be connected to allow the restart interlock to be used. The
reset pushbutton must be attached outside of the hazardous area. It must not be possi‐
ble to access the reset pushbutton from inside the hazardous area. The entire haz‐
ardous area must be highly visible for all operators from the reset pushbutton.
Further topics
•"Device connection", page 19
4.4.4 External device monitoring (EDM)
External device monitoring (EDM)
With static external device monitoring, the safety relay tests whether the controlled
actuators (contactors) have dropped out when the device is switched on.
Further topics
•"Device connection", page 19
4 PROJECT PLANNING
14 O P E R A T I N G I N S T R U C T I O N S | ReLy TIME1 8024303/2019-12-18 | SICK
Subject to change without notice

4.4.5 Connection diagrams
+24 V DC
0 V
k2
k1
F0
E254877/00/2019-10-28
X1 Y1 Y2 14X2 A2 3824
I1 I2 S1 A1R1 1323 37
RLY3-TIME1
K1
K2
Reset
RESState
3 2 4
1 5
STR1
ENABLE
NO ERROR
M
3
M
3
Figure 4: ReLy TIME1 connection diagram
4.5 Testing plan
The safety relay must be thoroughly checked by appropriately qualified safety personnel
during commissioning, after modifications, and at regular intervals, see "Thorough
check", page 25.
The regular thorough checks serve to assess the effectiveness of the safety relay and to
identify defects as a result of modifications or other influences (e.g., damage or manip‐
ulation).
The manufacturer and user must define the type and frequency of the thorough checks
on the machine on the basis of the application conditions and the risk assessment.
Determination of the thorough checks must be documented in a traceable manner.
4.5.1 Minimum requirements for the regular thorough check
The following thorough checks must be carried out at regular intervals:
•Thorough check of the housing for damage
•Thorough check of the cables for damage
•Thorough check of the safety relay for signs of misuse or manipulation
•Thorough check of the safety function
The required interval for performing these thorough checks depends on the applicable
safety capability of the overall application, see table 6, page 29.
PROJECT PLANNING 4
8024303/2019-12-18 | SICK O P E R A T I N G I N S T R U C T I O N S | ReLy TIME1 15
Subject to change without notice

5 Mounting
5.1 Safety
DANGER
Hazard due to unexpected starting of the machine
Hazard due to electrical voltage
bMake sure that the outputs of the safety relay have no effect on the machine dur‐
ing mounting and electrical installation.
bMake sure that the safety relay and the connected components are isolated from
all voltage sources during mounting and electrical installation of the device and
during mounting/dismantling of the front connector.
NOTICE
Enclosure rating IP20 only applies if the front connector is mounted.
5.2 Mounting procedure
Prerequisites
•Mounting is done in accordance with EN 50274 and electrical installation in
accordance with IEC 60204-1 in the control cabinet with enclosure rating IP54.
•Mounting must be done on a non-flammable base.
•Mounting is done on a 35 mm mounting rail (IEC 60715).
•The mounting rail is connected to the functional earth.
•The module is installed in a vertical orientation (on a horizontal mounting rail).
•There is at least 50 mm of space for air circulation above and below the module.
•There is at least 25 mm of space in front of the module (front side). More space
may be needed depending on the connections.
Approach
Click
Figure 5: Mounting
bAttach module to mounting rail.
5 MOUNTING
16 O P E R A T I N G I N S T R U C T I O N S | ReLy TIME1 8024303/2019-12-18 | SICK
Subject to change without notice

5.3 Disassembly
Prerequisites
•Electrician screwdriver (slotted screwdriver)
Approach
Figure 6: Disassembly
1. Press the unlocking mechanism on the upper side of the module towards the back
using the electrician screwdriver.
2. Loosen module from the mounting rail.
5.4 Module exchange
Approach
1. Disconnect module and the connected components from all voltage sources.
2. Take front connector with connected cables off the defective device: Press the
unlocking mechanism of the front connector downwards and pull out the front con‐
nector.
Figure 7: Dismantle front connector
MOUNTING 5
8024303/2019-12-18 | SICK O P E R A T I N G I N S T R U C T I O N S | ReLy TIME1 17
Subject to change without notice

3. Dismantle the defective module.
4. Mount new module.
5. Mount front connector with connected cables to the new module: First mount in
the module with bent hook and then engage in the housing.
Click
Figure 8: Mount the front connector
✓The front connector engages with an audible click.
5 MOUNTING
18 O P E R A T I N G I N S T R U C T I O N S | ReLy TIME1 8024303/2019-12-18 | SICK
Subject to change without notice

6 Electrical installation
6.1 Device connection
Important information
DANGER
Hazard due to lack of effectiveness of the protective device
In the case of non-compliance, it is possible that the dangerous state of the machine
may not be stopped or not stopped in a timely manner.
bEnsure the safety relay is supplied with supply voltage in all operating statuses.
bEnsure that the supply voltage of the safety relay is not connected via safety sen‐
sors or safety switches in order to switch the enabling current paths.
DANGER
Hazard due to unexpected starting of the machine
Hazard due to electrical voltage
bMake sure that the outputs of the safety relay have no effect on the machine dur‐
ing mounting and electrical installation.
bMake sure that the safety relay and the connected components are isolated from
all voltage sources during mounting and electrical installation of the device and
during mounting/dismantling of the front connector.
NOTICE
Enclosure rating IP20 only applies if the front connector is mounted.
Prerequisites
•Electrical installation is done in conformity with IEC 60204-1.
•The mounting rail is connected to the functional earth.
•The voltage supply and connected signals meet the requirements for SELV/PELV
(EN 61140) or NEC Class 2 (UL 1310).
•The external voltage supply must be capable of bridging a brief power failure of
20 ms as specified in IEC 60204-1. Suitable power supply units are available as
accessories from SICK.
•The safety outputs and external device monitoring (EDM) must be wired within the
control cabinet.
•When using the safety relay with voltages larger than the safety extra-low voltage:
The N/C contacts of the controlled contactors must be safely isolated from the
other contactor contacts.
•Contact fuse with safety fuse gG or circuit breaker C: 6 A, maximum short-circuit
current I ≤ 400 A
•The ground connection of all connected devices must have the same potential as
A2.
•All connected devices and the reset pushbutton comply with the required category
in accordance with ISO 13849-1 and SILCL in accordance with IEC 62061 (e.g.
shielded single sheathed cables, separate installation).
ELECTRICAL INSTALLATION 6
8024303/2019-12-18 | SICK O P E R A T I N G I N S T R U C T I O N S | ReLy TIME1 19
Subject to change without notice

Pin assignment
14
24
Y2
A2
13
23
S1
Y1
A1
1
3
7
9
11
13
15
17
2
4
8
10
12
14
16
18
I2I1
X2X1
R1
3837
Figure 9: Terminals on front connector
Table 4: Pin assignment of the terminals
Terminal Description
13, 14 1) 2) Enabling current path
23, 24 1) 2) Enabling current path
37, 38 1) 3) Enabling current path, release-delayed
I1 4) Safety capable input
I2 4) Safety capable input 3)
S1 2) 5) Reset pushbutton input, external device monitoring (EDM)
R1 Test pulse output
X1 4) Test pulse output
X2 4) Test pulse output
Y1 Application diagnostic output (NC)
Y2 Application diagnostic output (reset required)
A1 Voltage supply 24 V DC
A2 Voltage supply 0 V DC
1) The enabling current paths must be supplied by the same voltage supply.
2) The enabling current path and external device monitoring (EDM) must be wired within the control cabinet.
3) With single-channel base device: Connect jumper between I1 and I2.
4) Connect dual-channel switching elements of the safety sensors between X1 and I1 or X2 and I2.
5) •Use with restart interlock, with external device monitoring (EDM): Connect the N/C contacts of the
actuators between voltage supply Uv, the N/O contact of the reset pushbutton and S1.
•Use with restart interlock, without external device monitoring (EDM): Connect the N/O contact of
the reset pushbutton between S1 and voltage supply UV.
•Use without restart interlock, with external device monitoring (EDM): Connect the N/C contacts of
the actuators between R1 and S1.
•Use without restart interlock, without external device monitoring (EDM): Connect R1 and S1 with a
wire jumper.
6 ELECTRICAL INSTALLATION
20 O P E R A T I N G I N S T R U C T I O N S | ReLy TIME1 8024303/2019-12-18 | SICK
Subject to change without notice
Other manuals for ReLy TIME1
1
Table of contents
Other SICK Relay manuals
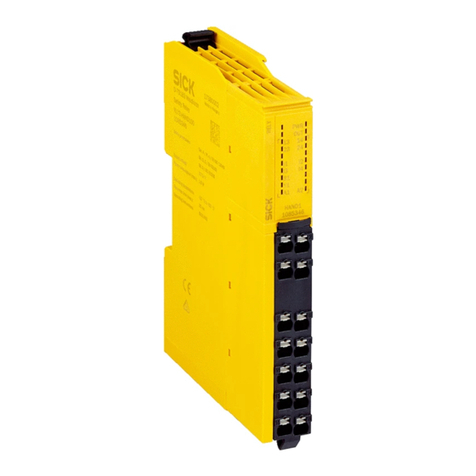
SICK
SICK ReLy HAND1 User manual
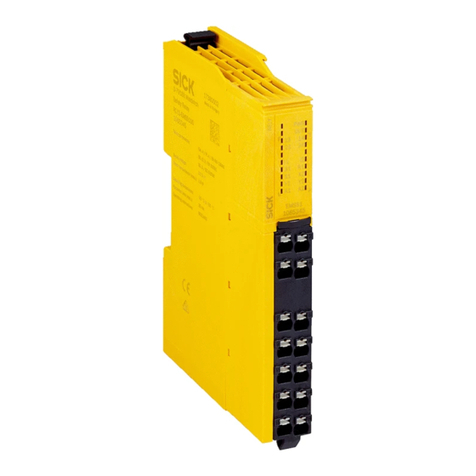
SICK
SICK ReLy EMSS1 User manual
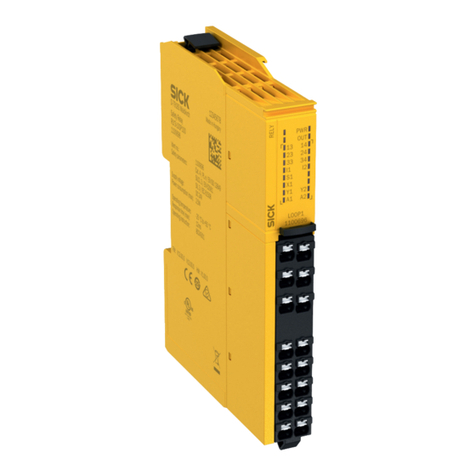
SICK
SICK ReLy LOOP1 User manual
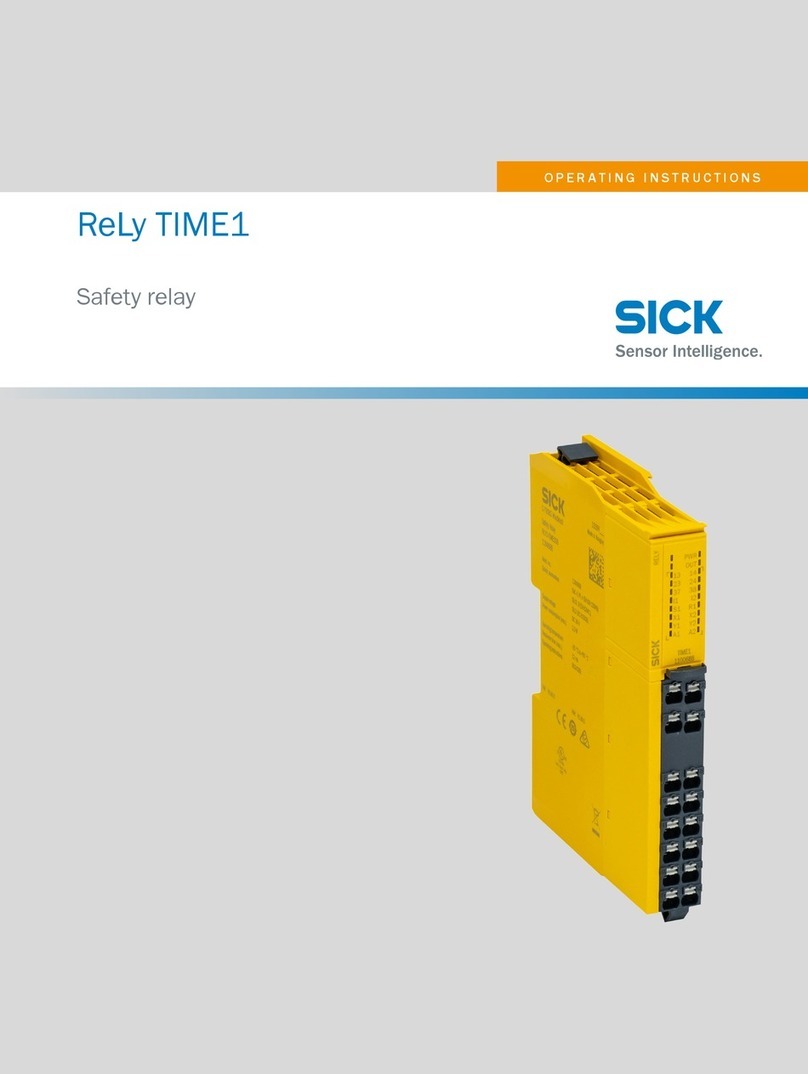
SICK
SICK ReLy TIME1 User manual
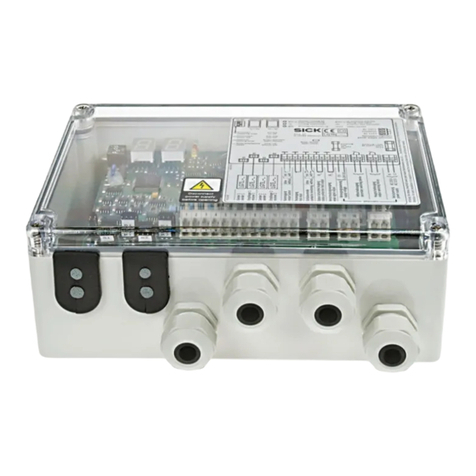
SICK
SICK LGT 015 Parts list manual

SICK
SICK ReLy HAND1 User manual
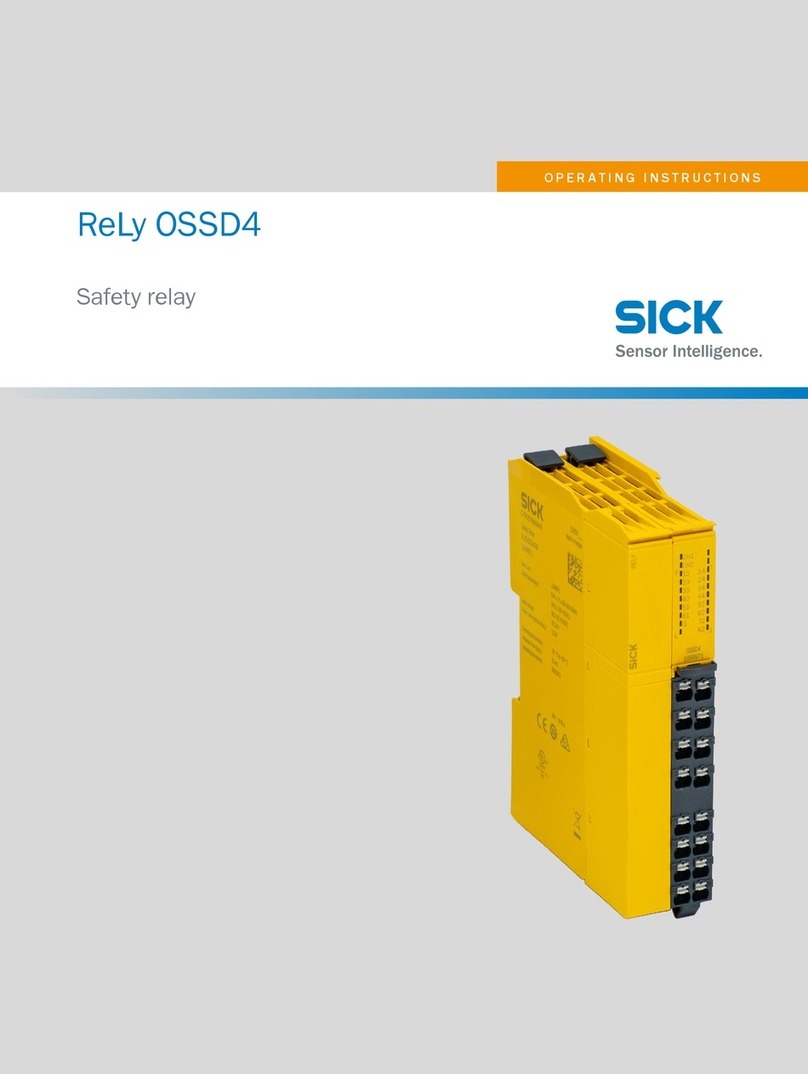
SICK
SICK ReLy OSSD4 User manual
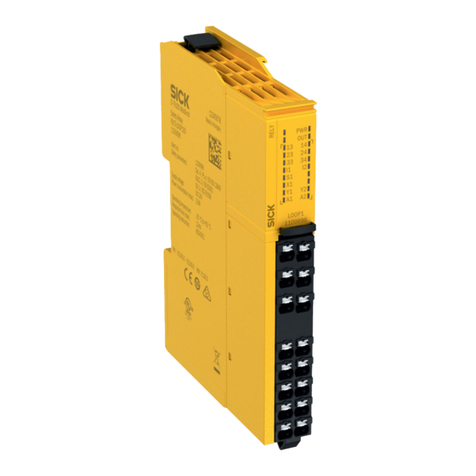
SICK
SICK ReLy LOOP1 User manual
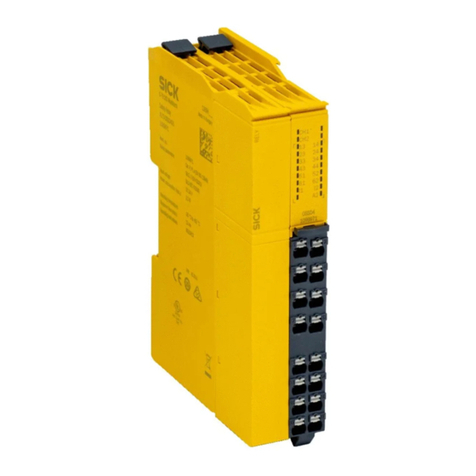
SICK
SICK ReLy OSSD4 User manual
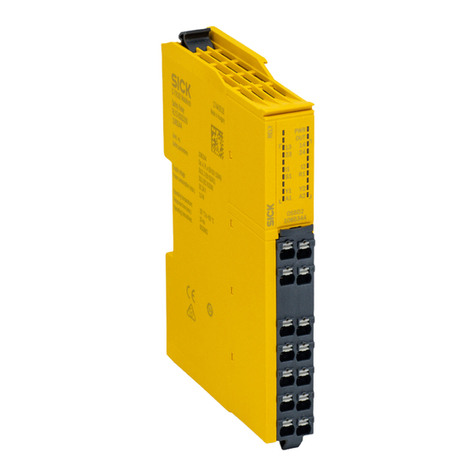
SICK
SICK ReLy OSSD2 User manual