SICK ReLy OSSD4 User manual

OPERATING INSTRUCTIONS
ReLy OSSD4
Safety relay

Described product
ReLy OSSD4
Manufacturer
SICK AG
Erwin-Sick-Str. 1
79183 Waldkirch
Germany
Legal information
This work is protected by copyright. Any rights derived from the copyright shall be
reserved for SICK AG. Reproduction of this document or parts of this document is
only permissible within the limits of the legal determination of Copyright Law. Any modi‐
fication, abridgment or translation of this document is prohibited without the express
written permission of SICK AG.
The trademarks stated in this document are the property of their respective owner.
© SICK AG. All rights reserved.
Original document
This document is an original document of SICK AG.
2O P E R A T I N G I N S T R U C T I O N S | ReLy OSSD4 8023931/1FH0/2022-10-27 | SICK
Subject to change without notice

Contents
1 About this document........................................................................ 5
1.1 Purpose of this document........................................................................ 5
1.2 Scope......................................................................................................... 5
1.3 Target groups of these operating instructions........................................ 5
1.4 Additional information.............................................................................. 5
1.5 Symbols and document conventions...................................................... 5
2 Safety information............................................................................ 7
2.1 General safety notes................................................................................ 7
2.2 Intended use............................................................................................. 7
2.3 Inappropriate use..................................................................................... 7
2.4 Requirements for the qualification of personnel.................................... 8
3 Product description........................................................................... 9
3.1 Device overview........................................................................................ 9
3.2 Structure and function............................................................................. 9
3.3 Product characteristics............................................................................ 9
3.3.1 Interfaces................................................................................. 9
3.3.2 Compatible sensor types......................................................... 10
3.3.3 External device monitoring...................................................... 10
3.3.4 Status indicators...................................................................... 10
4 Project planning................................................................................ 11
4.1 Manufacturer of the machine.................................................................. 11
4.2 Operating entity of the machine.............................................................. 11
4.3 Design........................................................................................................ 11
4.4 Electrical integration................................................................................. 12
4.4.1 Voltage supply.......................................................................... 12
4.4.2 Enabling current paths............................................................ 13
4.4.3 Feedback current path............................................................ 13
4.4.4 Signaling current path............................................................. 13
4.4.5 Connection diagrams.............................................................. 14
4.5 Testing plan............................................................................................... 14
4.5.1 Planning the thorough check during commissioning and in
certain situations..................................................................... 14
4.5.2 Planning the regular thorough check..................................... 15
5 Mounting............................................................................................. 16
5.1 Mounting procedure................................................................................. 16
5.2 Disassembly.............................................................................................. 17
5.3 Module exchange...................................................................................... 17
6 Electrical installation........................................................................ 19
6.1 Device connection.................................................................................... 19
CONTENTS
8023931/1FH0/2022-10-27 | SICK O P E R A T I N G I N S T R U C T I O N S | ReLy OSSD4 3
Subject to change without notice

7 Commissioning.................................................................................. 21
7.1 Safety......................................................................................................... 21
7.2 Check during commissioning and modifications.................................... 21
8 Troubleshooting................................................................................. 22
8.1 Safety......................................................................................................... 22
8.2 Status indicator (LED)............................................................................... 22
9 Decommissioning............................................................................. 23
9.1 Disposal..................................................................................................... 23
10 Technical data.................................................................................... 24
10.1 Data sheet................................................................................................. 24
10.2 Dimensional drawings.............................................................................. 29
10.3 Internal circuitry........................................................................................ 29
11 Ordering information........................................................................ 30
11.1 Ordering information for ReLy.................................................................. 30
12 Annex.................................................................................................. 31
12.1 Conformities and certificates................................................................... 31
12.1.1 EU declaration of conformity................................................... 31
13 List of figures..................................................................................... 32
14 List of tables....................................................................................... 33
CONTENTS
4O P E R A T I N G I N S T R U C T I O N S | ReLy OSSD4 8023931/1FH0/2022-10-27 | SICK
Subject to change without notice

1 About this document
1.1 Purpose of this document
These operating instructions contain the information required during the life cycle of the
safety relay.
These operating instructions must be made available to everyone who works with the
safety relay.
1.2 Scope
Product
This document applies to the following products:
•Product code: ReLy OSSD4
•“Operating instructions” type label entry: 8023913
Document identification
Document part number:
•This document: 8023931
•Available language versions of this document: 8023913
You can find the current version of all documents at www.sick.com.
1.3 Target groups of these operating instructions
Some sections of these operating instructions are intended for certain target groups.
However, the entire operating instructions are relevant for intended use of the product.
Table 1: Target groups and selected sections of these operating instructions
Target group Sections of these operating instructions
Project developers (planners, developers,
designers)
"Project planning", page 11
"Technical data", page 24
Installers "Mounting", page 16
Electricians "Electrical installation", page 19
Safety experts (such as CE authorized repre‐
sentatives, compliance officers, people who
test and approve the application)
"Project planning", page 11
"Commissioning", page 21
"Technical data", page 24
Operators "Troubleshooting", page 22
Maintenance personnel "Troubleshooting", page 22
1.4 Additional information
www.sick.com
The following information is available on the Internet:
•Data sheets and application examples
•CAD data and dimensional drawings
•Certificates (e.g. EU declaration of conformity)
•Guide for Safe Machinery Six steps to a safe machine
1.5 Symbols and document conventions
The following symbols and conventions are used in this document:
ABOUT THIS DOCUMENT 1
8023931/1FH0/2022-10-27 | SICK O P E R A T I N G I N S T R U C T I O N S | ReLy OSSD4 5
Subject to change without notice

Safety notes and other notes
DANGER
Indicates a situation presenting imminent danger, which will lead to death or serious
injuries if not prevented.
WARNING
Indicates a situation presenting possible danger, which may lead to death or serious
injuries if not prevented.
CAUTION
Indicates a situation presenting possible danger, which may lead to moderate or minor
injuries if not prevented.
NOTICE
Indicates a situation presenting possible danger, which may lead to property damage if
not prevented.
NOTE
Indicates useful tips and recommendations.
Instructions to action
bThe arrow denotes instructions to action.
1. The sequence of instructions for action is numbered.
2. Follow the order in which the numbered instructions are given.
✓The check mark denotes the result of an instruction.
LED symbols
These symbols indicate the status of an LED:
oThe LED is off.
ÖThe LED is flashing.
OThe LED is illuminated continuously.
1 ABOUT THIS DOCUMENT
6O P E R A T I N G I N S T R U C T I O N S | ReLy OSSD4 8023931/1FH0/2022-10-27 | SICK
Subject to change without notice

2 Safety information
2.1 General safety notes
Product integration
DANGER
The product can not offer the expected protection if it is integrated incorrectly.
bPlan the integration of the product in accordance with the machine requirements
(project planning).
bImplement the integration of the product in accordance with the project planning.
Mounting and electrical installation
DANGER
Death or severe injury due to electrical voltage and/or an unexpected startup of the
machine
bMake sure that the machine is (and remains) disconnected from the voltage
supply during mounting and electrical installation.
bMake sure that the dangerous state of the machine is and remains switched off.
Repairs and modifications
DANGER
Improper work on the product
A modified product may not offer the expected protection if it is integrated incorrectly.
bApart from the procedures described in this document, do not repair, open, manip‐
ulate or otherwise modify the product.
2.2 Intended use
The safety relay is an expansion module for sensors or safety devices with OSSDs for
switching safety-related circuits on and off.
The safety relay complies with class A, group 1 as per EN 55011. Group 1 encom‐
passes all ISM devices in which intentionally generated and/or used conductor-bound
RF energy that is required for the inner function of the device itself occurs.
The product may be used in safety functions.
The product must only be used within the limits of the prescribed and specified techni‐
cal specifications and operating conditions at all times.
Incorrect use, improper modification or manipulation of the product will invalidate any
warranty from SICK; in addition, any responsibility and liability of SICK for damage and
secondary damage caused by this is excluded.
2.3 Inappropriate use
The safety relay is not suitable for the following applications (this list is not exhaustive):
•At altitudes of over 4,000m above sea level
•In explosion-hazardous areas
SAFETY INFORMATION 2
8023931/1FH0/2022-10-27 | SICK O P E R A T I N G I N S T R U C T I O N S | ReLy OSSD4 7
Subject to change without notice

2.4 Requirements for the qualification of personnel
The product must be configured, installed, connected, commissioned, and serviced by
qualified safety personnel only.
Project planning
You need safety expertise to implement safety functions and select suitable products
for that purpose. You need expert knowledge of the applicable standards and regula‐
tions.
Mounting, electrical installation and commissioning
You need suitable expertise and experience. You must be able to assess if the machine
is operating safely.
Operation and maintenance
You need suitable expertise and experience. You must be instructed in machine oper‐
ation by the machine operator. For maintenance, you must be able to assess if the
machine is operating safely.
2 SAFETY INFORMATION
8O P E R A T I N G I N S T R U C T I O N S | ReLy OSSD4 8023931/1FH0/2022-10-27 | SICK
Subject to change without notice

3 Product description
3.1 Device overview
RELY
1
2
3
4
CH1
CH2
13
23
43
I1
14
24
44
I2
A2
51
33
52
34
6162
Figure 1: Device overview
1Device unlocking
2LEDs
3Front connector unlocking
4Front connector
3.2 Structure and function
The safety relay ReLy OSSD4 is an electrical switching device with inputs and outputs.
The safety capable inputs of the safety relay are connected to safety sensors.
2 safety capable inputs control the internal relays, which are used to reliably switch the
enabling current paths.
At the enabling current paths it is possible to connect, for example, actuators with
positively guided contacts.
3.3 Product characteristics
3.3.1 Interfaces
Inputs
•2 safety capable inputs
Outputs
•4 enabling current paths (safe)
•Feedback current path (for use as external device monitoring, not safe)
•Signaling current path (non-safety)
PRODUCT DESCRIPTION 3
8023931/1FH0/2022-10-27 | SICK O P E R A T I N G I N S T R U C T I O N S | ReLy OSSD4 9
Subject to change without notice

3.3.2 Compatible sensor types
Table 2: Compatible sensor types
Sensor type Description Examples
Safety sensors with
monitored semiconduc‐
tor output (OSSD)
Safety sensors with dual-channel
cross-circuit monitored semi-con‐
ductor outputs
Safety controllers with monitored
semi-conductor outputs
•Transponder safety switch
e.g., Sistra
•Safety light curtains, e.g.
deTec4
•Safety laser scanner, e.g.,
microScan3, nanoScan3
3.3.3 External device monitoring
The feedback current path is used as external device monitoring for the monitoring by
the base device.
3.3.4 Status indicators
LEDs
RELY
CH1
CH2
13
23
43
I1
14
24
44
I2
A2
51
33
52
34
6162
RELY
CH1
CH2
13
23
43
I1
14
24
44
I2
A2
5251
61 62
OSSD4
1099971
23 24
Figure 2: LEDs
The labeled positions are only partially assigned LEDs. The positions and their labels
(except the top 2 lines) also indicate the assignment of the terminals on the front connec‐
tor.
Table 3: Safety relay indicators
Labeling Color Function
CH1 Green OSSD1 safety capable input
CH2 Green Safety input OSSD2
Further topics
•"Status indicator (LED)", page 22
3 PRODUCT DESCRIPTION
10 O P E R A T I N G I N S T R U C T I O N S | ReLy OSSD4 8023931/1FH0/2022-10-27 | SICK
Subject to change without notice

4 Project planning
4.1 Manufacturer of the machine
The manufacturer of the machinery must carry out a risk assessment and apply appro‐
priate protective measures. Further protective measures may be required in addition to
the product.
The product must not be tampered with or changed, except for the procedures descri‐
bed in this document.
The product must only be repaired by the manufacturer of the product or by someone
authorized by the manufacturer. Improper repair can result in the product not providing
the expected protection.
4.2 Operating entity of the machine
Changes to the electrical integration of the product in the machine controller and
changes to the mechanical mounting of the product necessitate a new risk assess‐
ment. The results of this risk assessment may require the entity operating the machine
to meet the obligations of a manufacturer.
After each change to the configuration, it is necessary to check whether the protective
measure provides the necessary protection. The person making the change is responsi‐
ble for ensuring that the protection measure provides the necessary protection.
The product must not be tampered with or changed, except for the procedures descri‐
bed in this document.
The product must only be repaired by the manufacturer of the product or by someone
authorized by the manufacturer. Improper repair can result in the product not providing
the expected protection.
4.3 Design
Installation site
The safety relay must be installed in a control cabinet with an enclosure rating of IP54
or higher.
The safety relay must be installed on a mounting rail (35mm) in accordance with IEC
60715.
Space requirements in the control cabinet
To ensure sufficient air circulation and cooling, sufficient distance must be kept in the
control cabinet above and below the safety relay.
Sufficient distance must be kept for the connected cables before the module (front
side).
PROJECT PLANNING 4
8023931/1FH0/2022-10-27 | SICK O P E R A T I N G I N S T R U C T I O N S | ReLy OSSD4 11
Subject to change without notice

≥ 50≥ 50
≥ 25
Figure 3: Distances in control cabinet
Required distance:
•Above and below the module: ≥50mm
•In front of the module: ≥25mm
4.4 Electrical integration
Important information
NOTE
The device achieves overvoltage category III if feedback current path 31/32 is supplied
by the same voltage supply as the upstream OSSDs (safety extra-low voltage). Con‐
nected devices must be also have overvoltage category III.
4.4.1 Voltage supply
Prerequisites
•The power supply unit is able to jumper a brief power failure of 20ms as specified
in IEC60204-1.
•The voltage supply and connected signals meet the requirements for SELV/PELV
(EN61140) or NECClass2 (UL1310).
•The electrical voltage supply has a suitable electrical fuse.
Further topics
•"Data sheet", page 24
4 PROJECT PLANNING
12 O P E R A T I N G I N S T R U C T I O N S | ReLy OSSD4 8023931/1FH0/2022-10-27 | SICK
Subject to change without notice

4.4.2 Enabling current paths
Important information
DANGER
Hazard due to lack of effectiveness of the protective device
bEnsure the enabling current paths are supplied by the same voltage supply.
Cross-circuits
Cross-circuits between the enabling current paths or with other signals may not be
detected and can put the machine in a dangerous state.
Measures:
bLay the cables in a protected manner or separately (e.g., within the control cabinet
as per IEC60204-1).
bTake other necessary measures to achieve the required safety-related characteris‐
tic values.
4.4.3 Feedback current path
The feedback current path is used as external device monitoring for the monitoring by
the base device.
The status of the feedback current path (61, 62) changes as soon as the safe enabling
current paths (13, 14, 23, 24, 33, 34, 43, 44) switch. The feedback current path is not
safe.
Table 4: Switching behavior of feedback current path
State of enabling current paths State of feedback current path
Closed Open
Open Closed
4.4.4 Signaling current path
The purpose of the signaling current path is to indicate the status of the safety relay.
The status of the signaling current path (51, 52) changes as soon as the safe enabling
current paths (13, 14, 23, 24, 33, 34, 43, 44) switch. The signaling current path is not
safe.
PROJECT PLANNING 4
8023931/1FH0/2022-10-27 | SICK O P E R A T I N G I N S T R U C T I O N S | ReLy OSSD4 13
Subject to change without notice

4.4.5 Connection diagrams
3) PELV
F2 F1F4 F3
+24 V DC
0 V DC
E243849/02/2021-10-05
System connection
System connection
+24 V DC
deTec4 SP1
2
1
3
5
6
4
7
8
r
RES
ADO
OSSD 1
OSSD 2
EDM
0 V DC
MFP 1
s
+24 V DC
n.c
In 2
In 1
n.c.
0 V DC
MFP 1
n.c.
2
3
4
5
6
1
7
8
2)
F0
L+
L–
1)
k2k1
x1
x1
y1
y1
k4k3
x2
x2
y2
y2
k4
k3
z2
z2
k2
k1
z1
z1
H1 K4 K3 K2 K1
34445262A2 24
61 334351I1 I2 23
14
13
RLY3-OSSD4
Figure 4: ReLy OSSD4 connection diagram
1) Output circuits: These contacts must be incorporated into the control such that the
dangerous state is brought to an end if the output circuit is open. For categories 4 and 3,
they must be incorporated on dual-channels (x, y paths). Type 2 devices are suitable for
use up to PL c. Single-channel incorporation into the control (z path) is only possible with
a single-channel control and taking the risk analysis into account.
2) To indicate the status on both sides, the MFP1 connections from the sender and receiver
must be connected to each other in the control cabinet (optional)
3) SELV/PELV safety extra-low voltage.
4.5 Testing plan
The manufacturer of the machine and the operating entity must define all required
thorough checks. The definition must be based on the application conditions and the
risk assessment and must be documented in a traceable manner.
The following tests must be planned:
•A thorough check must be carried out during commissioning and following modifi‐
cations.
•The regular tests of the device must fulfill certain minimum requirements.
4.5.1 Planning the thorough check during commissioning and in certain situations
Overview
Before commissioning the machine and after making changes, you must check whether
the safety functions are fulfilling their planned purpose and whether persons are being
adequately protected.
Minimum requirements
The device and its application must be thoroughly checked in the following situations:
•Before commissioning
•After changes to the configuration or the safety function
•After changes to the mounting or the electrical installation
•After exceptional events, such as after manipulation has been detected, after
modification of the machine, or after replacing components
4 PROJECT PLANNING
14 O P E R A T I N G I N S T R U C T I O N S | ReLy OSSD4 8023931/1FH0/2022-10-27 | SICK
Subject to change without notice

The thorough check ensures the following:
•All relevant regulations are complied with and the device is effective in all of the
machine’s operating modes.
•The documentation accurately reflects the state/condition of the machine, includ‐
ing the protective device.
The thorough checks must be carried out by qualified safety personnel or specially
qualified and authorized personnel, and must be documented in a traceable manner.
4.5.2 Planning the regular thorough check
Overview
The purpose of regular tests is to identify any defects due to changes or external
influences (e.g. damage or manipulation) and to ensure that the protective measure
provides the necessary protection.
Minimum requirements
The following thorough checks must be carried out at regular intervals:
•Thorough check of the housing for damage
•Thorough check of the cables for damage
•Check the device for signs of misuse or manipulation
•Thorough check of the safety function
The required interval for performing these thorough checks depends on the applicable
safety capability of the overall application, see table 7, page 24.
PROJECT PLANNING 4
8023931/1FH0/2022-10-27 | SICK O P E R A T I N G I N S T R U C T I O N S | ReLy OSSD4 15
Subject to change without notice

5 Mounting
5.1 Mounting procedure
Prerequisites
•Mounting is done in accordance with EN 50274 and electrical installation in
accordance with IEC 60204-1 in the control cabinet with enclosure rating IP54.
•Mounting must be done on a non-flammable base.
•Mounting is done on a 35mm mounting rail (IEC60715).
•The mounting rail is connected to the functional earth.
•The module is installed with a vertical orientation (on a horizontal mounting rail).
•There is at least 50mm of space for air circulation above and below the module.
•There is at least 25mm of space in front of the module (front side). More space
may be needed depending on the connections.
Approach
1. Attach module to mounting rail.
Click
Figure 5: Mounting
✓The module engages with an audible click.
2. Attach the end clamps on the mounting rail on the left and right of the module.
Figure 6: Mounting the end clamps
5 MOUNTING
16 O P E R A T I N G I N S T R U C T I O N S | ReLy OSSD4 8023931/1FH0/2022-10-27 | SICK
Subject to change without notice

5.2 Disassembly
Prerequisites
•Electrician screwdriver (slotted screwdriver)
Approach
2 x
Figure 7: Disassembly
1. Press the unlocking mechanisms on the upper side of the safety relay towards the
back using the electrician screwdriver.
2. Loosen module from the mounting rail.
5.3 Module exchange
Approach
1. Disconnect module and the connected components from all voltage sources.
2. Take front connector with connected cables off the defective device: Press the
unlocking mechanism of the front connector downwards and pull out the front
connector.
Figure 8: Removing the plug
MOUNTING 5
8023931/1FH0/2022-10-27 | SICK O P E R A T I N G I N S T R U C T I O N S | ReLy OSSD4 17
Subject to change without notice

3. Dismantle the defective module.
4. Mount new module.
5. Mount front connector with connected cables to the new module: First mount in
the module with bent hook and then engage in the housing.
Click
Figure 9: Mount the front connector
✓The front connector engages with an audible click.
5 MOUNTING
18 O P E R A T I N G I N S T R U C T I O N S | ReLy OSSD4 8023931/1FH0/2022-10-27 | SICK
Subject to change without notice

6 Electrical installation
6.1 Device connection
Important information
Prerequisites
•Electrical installation is carried out according to the project planning.
•Dangerous condition of the machine is and remains off during the electrical instal‐
lation.
•Electrical installation is done in conformity with IEC60204-1.
•The mounting rail is connected to the functional earth.
•The safety outputs and external device monitoring (EDM) must be wired within the
control cabinet.
•When using the safety relay with voltages larger than the safety extra-low voltage:
The N/C contacts of the controlled contactors must be safely isolated from the
other contactor contacts.
•Enabling current paths are safely isolated from the other terminals. There is a
basic insulation between the enabling current paths.
•The ground connection of all connected devices must have the same potential as
A2.
•All connected devices and the reset pushbutton comply with the required category
in accordance with ISO 13849-1 and SIL in accordance with IEC 62061 (e.g.
shielded single sheathed cables, separate installation).
Pin assignment
14
24
34
52
62
I2
A2
44
13
23
33
43
51
61
I1
1
3
5
7
11
13
15
17
2
4
6
8
12
14
16
18
1
Figure 10: Terminals on front connector
1Safe isolation of the enabling current paths from the other terminals
Table 5: Pin assignment of the terminals
Terminal Description
13, 14 Enabling current path
23, 24 Enabling current path
ELECTRICAL INSTALLATION 6
8023931/1FH0/2022-10-27 | SICK O P E R A T I N G I N S T R U C T I O N S | ReLy OSSD4 19
Subject to change without notice

Terminal Description
33, 34 Enabling current path
43, 44 Enabling current path
51, 52 Signaling current path
61 Feedback current path, 24V DC
62 Feedback current path, for connection to the EDM input of
the basic device
I11) CH1 input (safety input for OSSD1)
I21) CH2 input (safety input for OSSD2)
A2 Voltage supply 0VDC
1) For a single-channel base device, connect a jumper between I1 and I2.
Complementary information
To protect and increase the service life of contact outputs, equip all connected loads
with varistors or RC elements. The response times will increase depending on the
suppressor used.
Further topics
•"Connection diagrams", page 14
•"Data sheet", page 24
•"Electrical integration", page 12
6 ELECTRICAL INSTALLATION
20 O P E R A T I N G I N S T R U C T I O N S | ReLy OSSD4 8023931/1FH0/2022-10-27 | SICK
Subject to change without notice
Other manuals for ReLy OSSD4
1
Table of contents
Other SICK Relay manuals
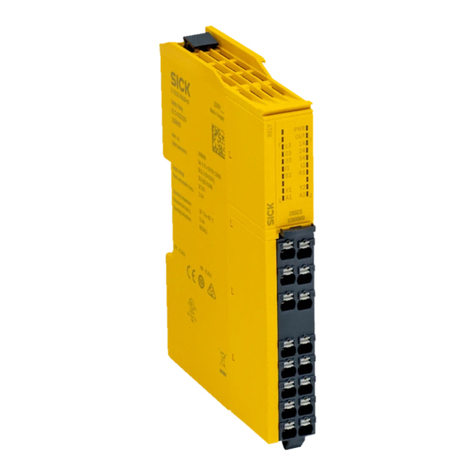
SICK
SICK ReLy OSSD3 User manual
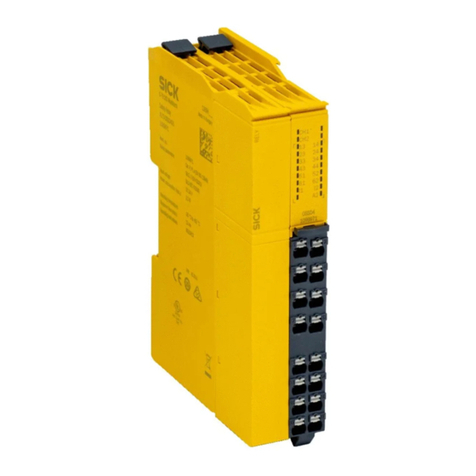
SICK
SICK ReLy OSSD4 User manual
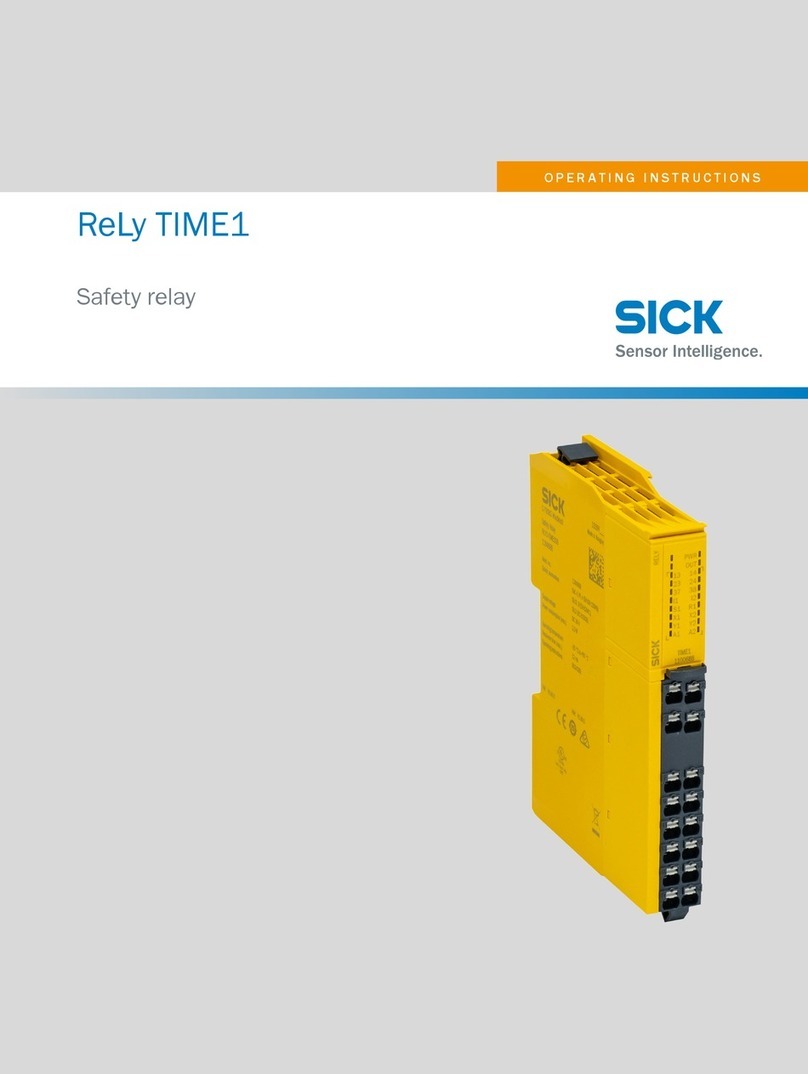
SICK
SICK ReLy TIME1 User manual
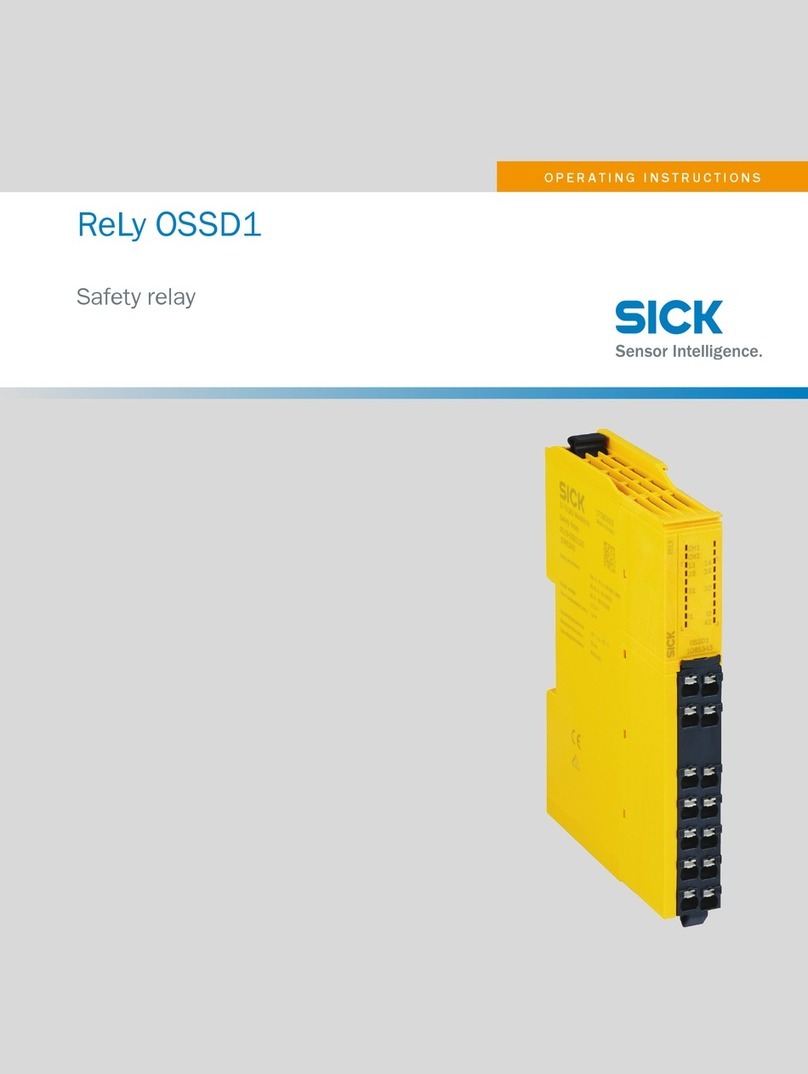
SICK
SICK ReLy OSSD1 User manual
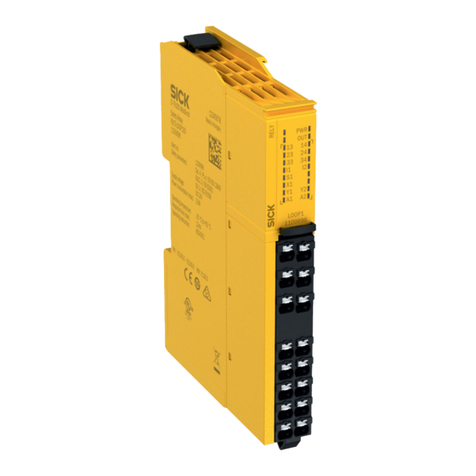
SICK
SICK ReLy LOOP1 User manual

SICK
SICK ReLy HAND1 User manual
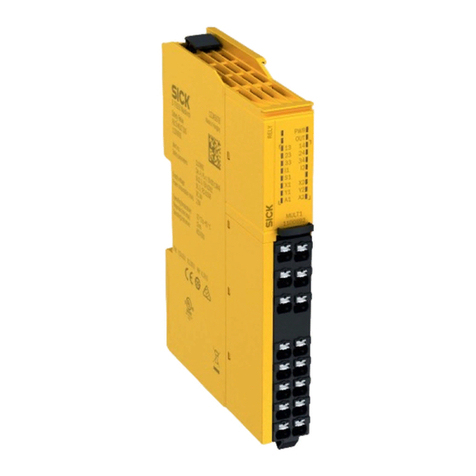
SICK
SICK ReLy MULT1 User manual
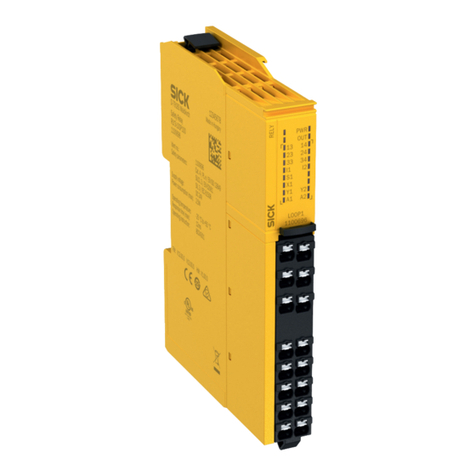
SICK
SICK ReLy LOOP1 User manual
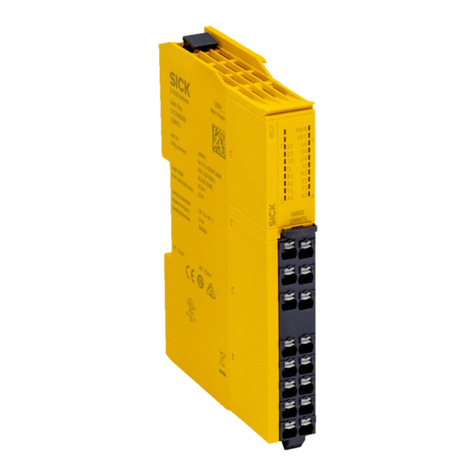
SICK
SICK ReLy EMSS3 User manual
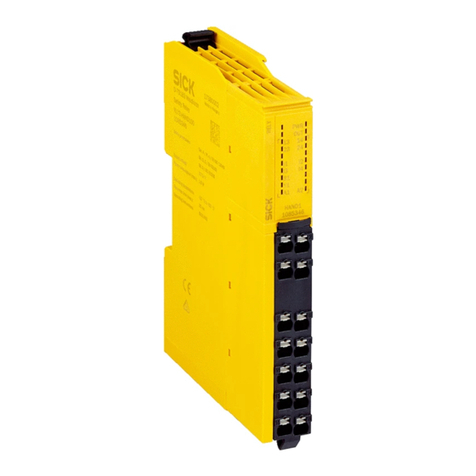
SICK
SICK ReLy HAND1 User manual
Popular Relay manuals by other brands

Woodward
Woodward WIC1 Series Original Technical Manual
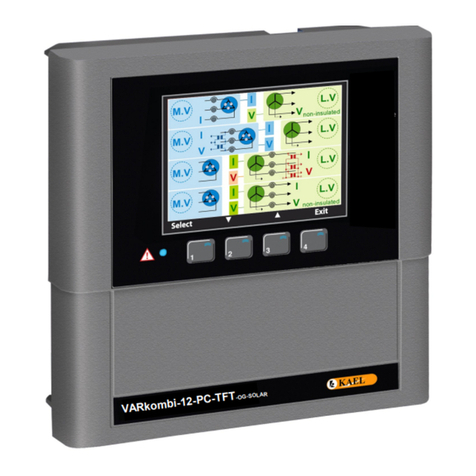
KAEL Muhendislik Elektronik
KAEL Muhendislik Elektronik VARkombi-12-PC-TFT-OG-SOLAR manual
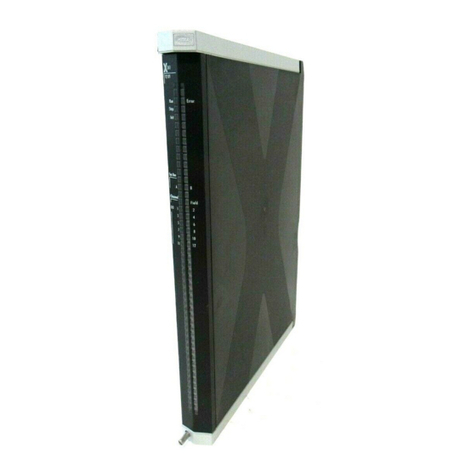
HIMA
HIMA HIMax X-DO 12 01 manual

Westinghouse
Westinghouse CO instructions
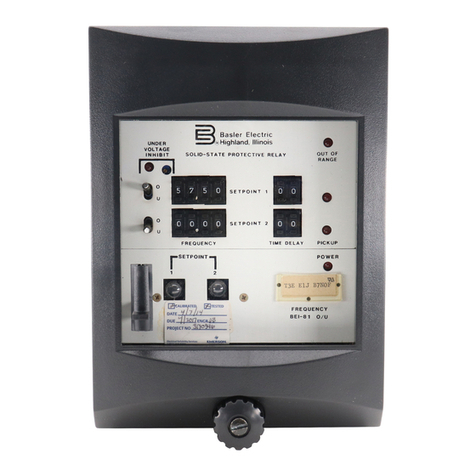
Basler
Basler BE1-81O/U instruction manual
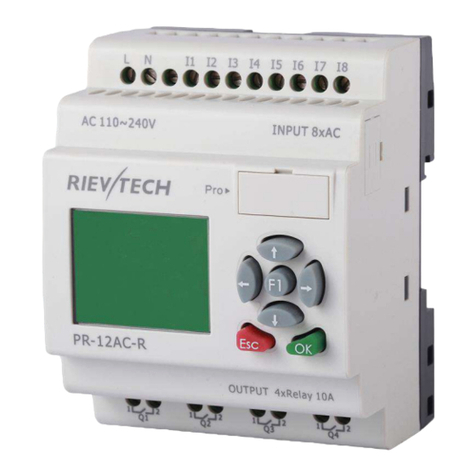
Rievtech
Rievtech xLogic ELC Series user manual