Signal POWER STATION 4 User manual

www.signal-group.com P a g e | 1of 26
Raising gas analysis to new levels

Series 4 Operating Manual - Nebula Issue 1.00
www.signal-group.com P a g e | 2of 26
DOCUMENT HISTORY
ISSUE
AMENDMENT
DATE
1.00
FIRST RELEASE
05/08/21
Table 1 : Document history table
© Signal Group Ltd.
All rights reserved. No part of this manual may be reproduced, stored in a retrieval system or
transmitted in any form or by any means - electronic, mechanical, photocopying, recording or
otherwise - without the prior written permission of Signal Group Ltd.
While we believe that the information and guidance given in this manual is correct, all parties must
rely upon their own skill and judgment when making use of it. Signal Group Ltd. will not assume any
liability to anyone for any loss or damage caused by any error or omission in the manual, whether
such error or omission is the result of negligence or any other cause. Any and all such liability is
disclaimed.
The information contained within this document is subject to change without notice.

Series 4 Operating Manual - Nebula Issue 1.00
www.signal-group.com P a g e | 3of 26
Contents
1What’s in the box ........................................................................................................... 4
2Important safety instructions .......................................................................................... 6
2.1 Wiring and Installation............................................................................................. 6
2.2 Handling and Storing Pressurised Gases................................................................ 6
2.3 Operation and Maintenance.................................................................................... 7
2.4 Competent Personnel ............................................................................................. 8
3Quick-start ..................................................................................................................... 9
4Introduction.................................................................................................................. 11
5The Principle of Tunable Diode Laser Spectrometry .................................................... 12
5.1 Sample System..................................................................................................... 12
6Operation..................................................................................................................... 13
6.1 Services................................................................................................................ 13
6.2 Start...................................................................................................................... 14
6.3 Control.................................................................................................................. 16
6.3-1 Calibration ..................................................................................................... 16
6.4 Remote Control..................................................................................................... 18
6.5 Connectivity .......................................................................................................... 18
7Routine Maintenance ................................................................................................... 23
7.1 Introduction........................................................................................................... 23
7.2 Sample Filter......................................................................................................... 23
8Routine Servicing......................................................................................................... 25
8.1 Schedule............................................................................................................... 25
8.2 Service Manual ..................................................................................................... 25
9Table of Figures........................................................................................................... 26
10 Table of Tables......................................................................................................... 26

Series 4 Operating Manual - Nebula Issue 1.00
www.signal-group.com P a g e | 4of 26
1 What’s in the box
‒Signal Series 4 Nebula analyser
‒Signal Series 4 Wireless Tablet (Optional)
‒Signal USB Drive containing:
•Operating Manual
•S4i installation (Optional)
•Datasheet
•Test Reports
‒Shipping kit containing –Signal Part No. 9000/396010:
•2m Mains lead cable
•Sample filter key (MC/318011)
•9/16” Wrench
•7/16” Wrench
•USB drive with related documents
‒Analogue output connection cable –Signal Part No. MI/995 (Optional)
‒Relay output connection cable –Signal Part No. MI/1020 (Optional)

Series 4 Operating Manual - Nebula Issue 1.00
www.signal-group.com P a g e | 5of 26
Read This First
Signal Group Ltd designs, manufactures and tests its products to meet many national and
international standards. Because these instruments are sophisticated technical products, you
MUST properly install, use, and maintain them to ensure they continue to operate within their
normal specifications. The following instructions MUST be adhered to and integrated into your
safety program when installing, using and maintaining Signal Group Ltd products. Failure to
follow the proper instructions may cause any one of the following situations to occur: Loss of
life; personal injury; property damage; damage to this instrument; and warranty invalidation.
‒Read all instructions prior to installing, operating, and servicing the product.
‒If you do not understand any of the instructions, contact your Signal Group Ltd
representative for clarification.
‒Follow all warnings, cautions, and instructions marked on and supplied with the product.
‒Inform and educate your personnel in the proper installation, operation, and maintenance
of the product.
‒Install your equipment as specified in the Installation Instructions of the appropriate
Instruction Manual and per applicable local and national codes. Connect all products to the
proper electrical and pressure sources.
‒To ensure proper performance, use qualified personnel to install, operate, update, program,
and maintain the product.
‒When replacement parts are required, ensure that qualified people use replacement parts
specified by Signal Group Ltd. Unauthorised parts and procedures can affect the product’s
performance, place the safe operation of your process at risk, and VOID YOUR
WARRANTY. Substitutions may result in fire, electrical hazards, or improper operation.
‒Ensure that all equipment doors are closed, and protective covers are in place, except
when maintenance is being performed by qualified persons, to prevent electrical shock and
personal injury.

Series 4 Operating Manual - Nebula Issue 1.00
www.signal-group.com P a g e | 6of 26
2 Important safety instructions
2.1 Wiring and Installation
The following safety instructions apply to all EU member states and should be followed
according to Low Voltage Directive. It is recommended that non-EU areas should also comply
with these instructions unless superseded by other local or national standards.
‒It is essential that suitable grounding connections be made at all connectors provided for
this purpose.
‒All safety covers and grounding connections must be properly reinstated after maintenance
or troubleshooting. The integrity of all earth terminals must always be maintained.
‒To ensure safe operation of this equipment, connection to the mains supply should be made
through a circuit breaker which will disconnect all circuits carrying conductors in the case
of a fault. These circuit breakers should comply with a recognised standard such as
IEC947. All wiring must conform to any local or national standards.
2.2 Handling and Storing Pressurised Gases
This instrument requires pressurised gases for use. Some general safety precautions are
outlined below; however, it is advisable that operators are properly trained in the handling and
storage of pressurised gas containers:
‒Never drop cylinders or permit them to strike each other violently.
‒Cylinders may be stored in the open, but in such cases should be protected against
extremes of weather and, to prevent rusting, from the dampness of the ground. Cylinders
should be stored in the shade when located in areas where extreme temperatures are likely.
‒The valve protection cap should be left on each cylinder until it has been safely secured
against a wall or other solid structure or placed is dedicated cylinder stand.
‒Avoid dragging, rolling or sliding cylinders, even for a short distance –they should be
moved using a suitable transportation device (e.g. bottle trolley).
‒Never tamper with the safety devices in valves or cylinders.
‒Avoid storage of full and empty cylinders together. Serious suck-back can occur when
empty cylinders are attached to pressurised systems.
‒No part of a cylinder should be exposed to a temperature higher than 52°C (125°F), or a
naked flame or incandescent material.
‒Do not place cylinders where they could become part of an electric circuit.

Series 4 Operating Manual - Nebula Issue 1.00
www.signal-group.com P a g e | 7of 26
2.3 Operation and Maintenance
On leaving the Signal Group Ltd factory, this product conformed to all applicable safety
directives. The operator must take care to follow the instructions given in this manual to
preserve this condition.
Before switching on the instrument, ensure that the local supply voltage is within the limits
indicated in this manual.
Any interruption of the protective earth connections, whether inside or outside of the unit, or
removal or interruption of its ground line connection, may result in reduced instrument
performance and exposure to the risk of electrocution. It is therefore strictly forbidden to
deliberately disconnect the protective earth.
The removal of covers and panels may expose electrical components. Connectors may also
be energised even if no mating connector is present. The unit should therefore be
disconnected from all electrical supplies before any kind of maintenance or repair is carried
out. Only trained personnel who are aware of the risk are permitted to energise an open unit.
Fuses may only be replaced with identical items. It is forbidden to use repaired fuses or to
bypass fuses.
Substances hazardous to health may escape from the unit’s gas outlets. It is advisable to
exhaust the gas outlets to a safely ventilated area.
The safety of the personnel operating this equipment is paramount. All efforts should be taken
to ensure their protection.
Our analysers are checked and tested using state of the art equipment and techniques.
Despite this, an element of risk remains to the user when using any gas analyser. Even when
operated as intended and observing all applicable safety instructions and standards, some
risks remain, including but not limited to the following:
‒An accidental interruption of the protective earth line, e.g. In an extension cable, may result
in a risk to the user;
‒Electrically live components may be exposed if operating the instrument with covers
removed;
‒The emission of hazardous gases may be possible even if all connections have been made
correctly and according to the manufacturers’ instructions.
Avoid exposure to the dangers of these residual risks by taking care when installing, operating,
maintaining and servicing the analyser.
If unsure about anything in this manual, please contact your local Signal Group Ltd
representative for further guidance.

Series 4 Operating Manual - Nebula Issue 1.00
www.signal-group.com P a g e | 8of 26
2.4 Competent Personnel
Specialist knowledge of this instrumentation is a necessity for working with and on the unit.
Authorised personnel for installing, operating, servicing, and maintaining the analyser are
instructed and trained personnel of the operating company, Signal Group Ltd or their local
representatives.
‒It is the responsibility of the operating company to:
‒Ensure their staff have adequate training.
‒Observe safety regulations.
‒Follow this instruction manual.
‒Operators must:
‒Have been properly trained.
‒Have read and understood all relevant sections of the instruction manual before
commencing use of the instrument.
‒Know all the applicable safety mechanisms and regulations.
To avoid personal injury and loss of property, do not install, operate, maintain or service this
instrument before reading and understanding this manual and receiving appropriate training.
Do not dispose of this instruction manual.

Series 4 Operating Manual - Nebula Issue 1.00
www.signal-group.com P a g e | 9of 26
3 Quick-start
Please read all safety instructions before operating the analyser
This section is intended as a quick guide for trained personnel. See the Operation section for
detailed instructions.
‒Connect your power supply to the mains IEC connector on the rear panel (for standard AC
operation);
‒Connect your gases to the rear panel at the following pressures, using tubing as indicated
below:
Gas
Tube
Pressure
SAMPLE
1/4ʺPTFE or similar
0.75 ± 0.15 Bar
SPAN (NH3)
1/8ʺPTFE or similar
1.0 ± 0.2 Bar
ZERO (Clean Air or N2)
1/8ʺPTFE or similar
1.0 ± 0.2 Bar
Table 2 : Quick-start setup
‒Switch on the power using the switch on the rear panel (AC operation only). At this stage
you should see a solid blue LED on the front panel, indicating that the unit is in Sleep mode.
An internal fan may also be audible;
‒Your instrument is now powered up and ready for general use. The various internal heated
components require time to warm up. For the NEBULA it is imperative you wait at least 30
minutes for all components’ temperature to stabilize after every power off. Use your chosen
operating interface (front panel display or S4i. See the appropriate user guide for detailed
information) to proceed and initiate the warmup procedure;
‒The following options will initiate warmup:
Standby –the unit will go to a state ready for measurement. No gas valves will be open.
Zero –the unit will automatically open the zero valve to begin measuring zero gas.
Span –the unit will automatically open the span valve to begin measuring span gas.
Sample –as Zero & Span but the unit will begin measuring Sample gas.
Pause –Span, Zero and Sample Solenoids will all be closed.

Series 4 Operating Manual - Nebula Issue 1.00
www.signal-group.com P a g e | 10 of 26
‒For optimal performance you need to calibrate your instrument. (It is recommended to do
this daily) You can calibrate from the following modes:
Zero –calibration in this mode will adjust the zero offset only.
Span –calibration in this mode will adjust the span coefficient only.
Sample –calibration in this mode will adjust the zero offset, followed by the span coefficient.
NOTE –it is advisable to leave your instrument on for at least an hour before first
calibration to allow the detector to stabilise.
Further details regarding calibration can be found in Section 6 (Including calibration
through the sample port).
‒Once calibrated and stable, your instrument is ready for accurate measurement. Use the
relevant user interface guide for further information regarding instrument features such as
analogue outputs and data logging, and how to configure and use them.
Front Panel Light codes
Light
Status
Red Blink
Heating
Purple
Loading Config File
Yellow
Standby
Yellow Blink
Purge
Green
Measurement Mode
White
No Config
Red/Blue
Alarm
Blue
Sleep

Series 4 Operating Manual - Nebula Issue 1.00
www.signal-group.com P a g e | 11 of 26
4 Introduction
The Signal NEBULA range of gas analysers uses reference-method Tunable Diode Laser
Spectrometry (TDLS) technology to determine the Ammonia (NH3) content of gas samples.
Specifically designed to be versatile and reliable, the Nebula can be used in a multitude of
applications. These include Process control (incineration & combustion), emission monitoring
and environmental safety (leak detection, toxicity etc.). Proprietary digital flow and
temperature control, together with Signal’s world-class Series 4 electronics package, provides
superior performance across the board.
•Standard NEBULA analysers allow optional:
•Measurement ranges as low as 1ppm NH3equivalent up to as high as 1% NH3
equivalent;
•Full internal heating (to 191°C);
•Fully automated calibration;
•Continuous measurement of Ammonia (NH3);
•10 user-programmable analogue outputs for monitoring concentrations, ranges,
pressures and/or temperatures;
•Up to 35 user-programmable relay outputs for alarm or external valve operation;
•Remote control and data logging over Ethernet or RS232;
•On-board data logging;
•24VDC power supply.
Signal is renowned for its ability to create instruments for special applications, so if the options
above do not cover your specific requirements, then contact Signal or one of their local
representatives to discuss your application further.

Series 4 Operating Manual - Nebula Issue 1.00
www.signal-group.com P a g e | 12 of 26
5 The Principle of Tunable Diode Laser Spectrometry
Tunable Diode Laser Spectrometry is an infrared absorption measurement which utilizes the
interaction of infrared light with gas molecules to determine the concentration of a target gas.
The absorption of infrared light by the gas molecules causes a decrease in IR radiation
intensity on the detector/photo diode.
A standard TDLS setup consists of a laser diode, optical lens, gas sample cell and a photo
detector. The optical lens in the system collimates the laser light to ensure the light is
perpendicular as it hits the photo diode. The laser diode in the detector is tuned to the
characteristic absorption lines of a material in a sample gas. Therefore, one laser/detector will
be used to measure one gas with little to no chance of any cross-sensitivity with other species
in the sample.
5.1 Sample System
The compact 3U 19" rack unit includes a 191 °C heated sample handling module which houses
a sample particulate filter, a sample selection solenoid, and connections to the zero and span
selection valves.
The sample handling module allows the connection of a heated sample line directly to the rear
panel preventing cold spots where sample condensation may occur. This is particularly
dangerous for this application as Ammonia is such a toxic gas. The NEBULA uses an internal
heated inlet line to maintain the temperature from the sample handling module to the detector
to prevent condensation forming on the inlet pipe. It also has a heated exhaust pipe so that
moisture build up does not occur and form aqueous ammonia in the outlet line.

Series 4 Operating Manual - Nebula Issue 1.00
www.signal-group.com P a g e | 13 of 26
6 Operation
6.1 Services
Signal Group Ltd assumes that the user has a certain level of understanding of gas analysers.
Some aspects of gas analysis can be dangerous without proper training and understanding.
Signal and its representatives are able to provide full analyser training on request. Contact
your local representative for further information.
To use your NEBULA analyser, you will need the following services:
‒Power: NEBULA’s standard universal power supply allows operation from 100Vac to
250Vac at 50 to 60Hz. 600W maximum.
24DC operation is available on request. Please ask for details.
‒Zero: Depending on your chosen options, you may need zero-grade compressed air. For
applications where accuracy under 1ppm CH4-equivalent are required, you should use
zero-grade air or an external air purifier such as Signal’s model AS80 air purifier.
‒Calibration Gases: Only NH3may be used. Signal recommends a gas concentration close
to the expected measurement level. The NEBULA’s TDLS detector is manufactured to
measure a specific level of concentration. Do not attempt to measure over your analyser’s
measurement range as you will not get reliable results and may over saturate.
‒Humidity: In most cases, the analyser will only read a sample which has more than 5%
H2O in the sample gas. If you intend to analyse gases under this level of humidity you will
need to contact Signal Group LTD to configure the analyser for this, as it will not read
accurately.
CAUTION: If you suspect your gas may have dust load, it is imperative you use the
filtered SAMPLE line to avoid cell contamination. Always use clean, particulate-free
gases for calibration as there is no filter on the Zero/Span inlets.

Series 4 Operating Manual - Nebula Issue 1.00
www.signal-group.com P a g e | 14 of 26
6.2 Start
‒Ensure that the analyser is resting on a stable surface or fixed into a rack, or on a wall if
the wall-mount option has been chosen;
‒Connect the included (or equivalent) power cable to the rear panel IEC power socket,
ensuring the supply voltage is within the operational limits of the instrument;
Figure 1: NEBULA rear panel
‒Ensure that the correct fuses are in place within the integrated IEC socket on the rear panel.
‒Figure 2 below shows the rear panel layout of the NEBULA;
Figure 2: NEBULA pneumatic connections
1/4” SAMPLE
INLET
1/8ʺSPAN
INLET
1/8ʺZERO
INLET
EXHAUST

Series 4 Operating Manual - Nebula Issue 1.00
www.signal-group.com P a g e | 15 of 26
‒ZERO: Ensure that the correct air supply is available for your chosen option: -
‒For flushing out the system, pressurised air or N2 is required, at 1.0±0.2bar (100±20kPa,
14.5±3psi).
‒Zero-grade air is recommended for accurate readings and sufficient cleansing. Some
applications may require an external air purifier to achieve best performance. Consult
your local Signal Group Ltd representative for further advice.
‒Connect your chosen air supply to the ZERO port on the rear panel.
‒SPAN
‒Connect your chosen concentration of span calibration gas to the SPAN port on the rear
of the analyser at 1.0 Bar ± 0.2 Bar. It is recommended that the concentration value of
your span gas should be between 40% and 80% of your chosen measurement range.
‒SAMPLE
‒Connect your sample supply to the SAMPLE/FILTER port on the rear panel at 0.75 Bar
± 0.15 Bar.
‒It is recommended that the sample gas temperature be maintained at a level above the
dew point of the measurand(s), e.g. 191°C, using a heated sample line obtainable from
Signal Group Ltd.
‒EXHAUST
‒Connect the exhaust to a well-ventilated area, ensuring that the connection is free from
obstruction that could cause restrictions. Ensure that the connection tubing remains at
a downward angle to avoid moisture build up in the tubing.
CAUTION: The gases emitted from the EXHAUST will be hot and contain sample
gas. Care must be taken to avoid risk of burning or local build-up of sample gases.
‒If desired, attach your chosen output cables (analogue/relays/etc) now. Preassembled
cables can be purchased separately from Signal Group Ltd. Contact your local
representative for details. Alternatively, see the Output Wiring section of this manual for
connection information.
‒When all the fittings and cables are secure, you may apply power to the unit by using the
switch on the rear panel (this applies to units powered by mains AC only. 24VDC units
should use an external switch capable of carrying up to 25Amps if switching 24VDC, 3.15
Amps (for 230VAC) or 6.5Amps (for 115VAC), if switching the primary side of an AC-DC
transformer.
‒The front panel Status LED should now be illuminated solid blue. This indicates that the
unit is in Sleep mode.

Series 4 Operating Manual - Nebula Issue 1.00
www.signal-group.com P a g e | 16 of 26
6.3 Control
Once the analyser is powered on it may be controlled using either the wireless tables or
optional S4i for computer use. (See the appropriate User Guides provided for further
information).
6.3-1 Calibration
Calibration Requirements
The TDLS detector within the analyser will reliably measure a sample gas with 5% or more
H2O present. Therefore, for accurate calibration, anhydrous NH3of a known PPM value is
required to be mixed with humidified air/zero gas. The diagram below is the recommended
experimental setup for doing this:
Figure 3: Nebula Calibration Schematic
Signal Group LTD provide an external calibration unit with humidifying capabilities that will aid
this process. Please contact the Sales team if this is something you require.
Zero/Span Calibration
‒The procedures for calibration of the zero offset and span coefficient are fully automated.
The process is as follows:
‒Enter the span gas bottle concentration values as described in your chosen interface
guide
‒Select Calibrate while the unit is lit and stable to initiate the process. The analyser will
start by choosing the correct gas path (if not already selected), to allow the calibration
gas to flow.
‒It will then monitor the measurements to determine the point at which they have become
stable enough to use as a reference for calibration.

Series 4 Operating Manual - Nebula Issue 1.00
www.signal-group.com P a g e | 17 of 26
‒Once stability is achieved, the unit will monitor the measurements for a short period
before setting the correct values.
‒Before attempting any calibration, ensure that the correct gases are connected.
‒Before attempting a Span calibration, ensure that the span gas table is complete with the
correct gas values, as described on the gas cylinder certificate. Failure to do this may result
in large errors in measurement and/or unexpected readings.
‒Each measurement range has its own individual zero offset and span coefficient. Select
Apply Calib. to All Ranges before any calibration if you wish to use the same offset and
coefficient for all ranges.
‒You may begin a Calibration from any of the following modes:
‒ZERO: only the zero offset is adjusted.
‒SPAN: only the span coefficient is adjusted.
‒SAMPLE: First the zero-gas path is automatically selected and the zero-offset adjusted,
then the adjustment of the span coefficient is performed with the span gas path selected.
Calibration Through Sample Port
‒If required, the analyser may be configured so that calibration is performed through the
SAMPLE port instead of the separate SPAN and ZERO ports.
‒In this case the procedure is the same, ZERO and SPAN modes can still be selected but
when calibration starts, the sample solenoid will open.
‒If calibration is selected in SAMPLE mode a zero and span calibration will still be performed
consecutively but the gases must be switched over manually.
Calibration Failure
‒The calibration routine automatically waits for a stable reading before applying the results.
If a stable reading cannot be found within the built-in time limit, then the calibration will fail,
and an alarm will be activated.
‒There are many reasons that a stable reading would not be found. It is advisable to contact
your local Signal Service representative for advice if this occurs.
Measurement
‒Once the unit is stable and fully calibrated, accurate measurements can be taken.
‒Select Sample mode to energise the heated internal sample valve and allow sample gas
to flow.
‒You may check the calibration at any time by switching to Zero or Span gas paths and
monitoring the measurements.

Series 4 Operating Manual - Nebula Issue 1.00
www.signal-group.com P a g e | 18 of 26
Ranges
‒The instrument has a single hardware range, allowing accurate measurement from zero to
full scale of the instrument at all times, regardless of selected user range. However, it is
standard practice (and often dictated by regulations) to choose a suitable range for
measurement. For this reason, consult your local regulations for further guidance on the
use of ranges.
‒To enable compliance with various regulations, 5 ranges are provided, together with an
auto range facility. Each of these ranges is programmable by the user, apart from the
maximum range which is fixed.
‒Four of the five ranges are standard 0-n type, with a fixed lower end, but the fifth is m-n,
which means that it has a programmable lower end allowing the expansion of the specific
range of measurement. For example, if the expected range of measurement is 11 to 18ppm,
an instrument range of 5 to 25ppm may be chosen. The main benefit of this facility is that
it allows for greater resolution on the analogue outputs.
‒NOTE: Each range uses separate calibration curves and coefficients. Ensure that all the
ranges that will be in use are properly calibrated before taking measurements.
‒NOTE: Due to the capability of separate calibrations for each range, it may appear that
one range measures differently to another. In this case it is necessary to recalibrate in
order to realign the measurements. Always apply the calibration to all ranges to avoid
inter-range differences.
6.4 Remote Control
Consult the S4i User Guide or Tablet Software User Guide (if applicable) for detailed remote-
control operational guidance.
6.5 Connectivity
Relays
‒The Analyser can be fitted with up to 35 contact closure output relays which can be
configured to operate when in alarm states, or to actuate valves for a particular detector,
range and gas path.
‒The following output relays are available depending on your selected option:
•Standard IO –3 (non-configurable)
•Extended IO –23 (20 configurable)
•Special Extended IO –35 (32 configurable)

Series 4 Operating Manual - Nebula Issue 1.00
www.signal-group.com P a g e | 19 of 26
‒I/O cables, MI/1020 can be ordered separately to connect to the Relay outputs. (Previously,
MI/996)
Relay specification
•Load: Resistive load (cosφ = 1)
•Rated Load: 0.5 A at 125 VAC; 1 A at 24 VDC
•Contact Material: Ag (Au alloy)
•Rated Carry Current: 2 A
•Max. switching voltage: 125 VAC, 60 VDC
•Max. switching current: 1 A
•Max. switching power: 62.5 VA, 30 W
•Failure rate (reference value): 1 mA at 5 VDC
‒P level: λ60 = 0.1 x 10-6/operation. This value was measured at a switching frequency of
120 operations/min and the criterion of contact resistance is 100. This value may vary
depending on the operating environment. Always double-check relay suitability under
actual operating conditions

Series 4 Operating Manual - Nebula Issue 1.00
www.signal-group.com P a g e | 20 of 26
MI/1020
Relay
No/Digital
IO
Pin
Colour
Relay No/Digital
IO
Pin
Colour
1
1
Brown
18
18
LightGreen
68
White/Red
51
Pink/Black
2
2
Brown/Green
19
19
LightGreen/Brown
67
Purple/Green
50
White/Black
3
3
Red
20
20
LightBlue
66
LightBlue/Gray
49
Gray/Green
4
4
Orange
22
21
Green/White
65
Pink/Gray
48
Gray/Black
5
5
Orange/Brown
GLB ALB23 (NO)
22
Yellow/Red
64
Purple/Yellow
GLB ALA23 (Com)
47
Purple/White
6
6
Yellow
GLB ALC23 (NC)
23
Blue/Red
63
Yellow/Gray
GND Power
46
Purple/Black
7
7
Green
+24V Fused
Output
24
LightBlue/Red
62
Green/Brown
TTL Sleep
45
Blue/Black
8
8
Pink/Green
NC
25
Green/Red
61
Yellow/White
TTL CAL
44
LightBlue/Yellow
9
9
Blue/Green
GND POWER
26
Green/Orange
60
Orange/White
GND POWER
43
Pink/Blue
10
10
Green/Yellow
DIO1
27
yellow/Gray
59
Red/White
DIO9
42
Pink/Red
11
11
Blue
DIO2
28
LightGreen/Green
58
LightBlue/Green
DIO10
41
Green/Black
12
12
Purple
DIO3
29
Yellow/Brown
57
Blue/Orange
DIO11
40
Yellow/Black
13
13
Purple/Red
DIO4
30
Brown/Yellow
56
Yellow/Blue
DIO12
39
Orange/Gray
14
14
Gray
DIO5
31
Brown/Pink
55
Blue/White
DIO13
38
Orange/Black
15
15
Gray/Red
DIO6
32
LighBlue/Brown
54
LightBlue/Black
DIO14
37
Red/Black
16
16
White
DIO7
33
Gray/Brown
53
LightGreen/Gray
DIO15
36
Brown/White
17
17
Pink
DIO8
34
Black
52
LightGreen/Black
DIO16
35
Brown/Black
Table 3 : Relay wiring table - Colours refer to Signal output cable MI/1020
Other manuals for POWER STATION 4
1
Table of contents
Other Signal Measuring Instrument manuals
Popular Measuring Instrument manuals by other brands

Hornady
Hornady LOCK-N-LOAD BLACKPOWDER Product instructions

Arcteq
Arcteq AQ-P215 instruction manual
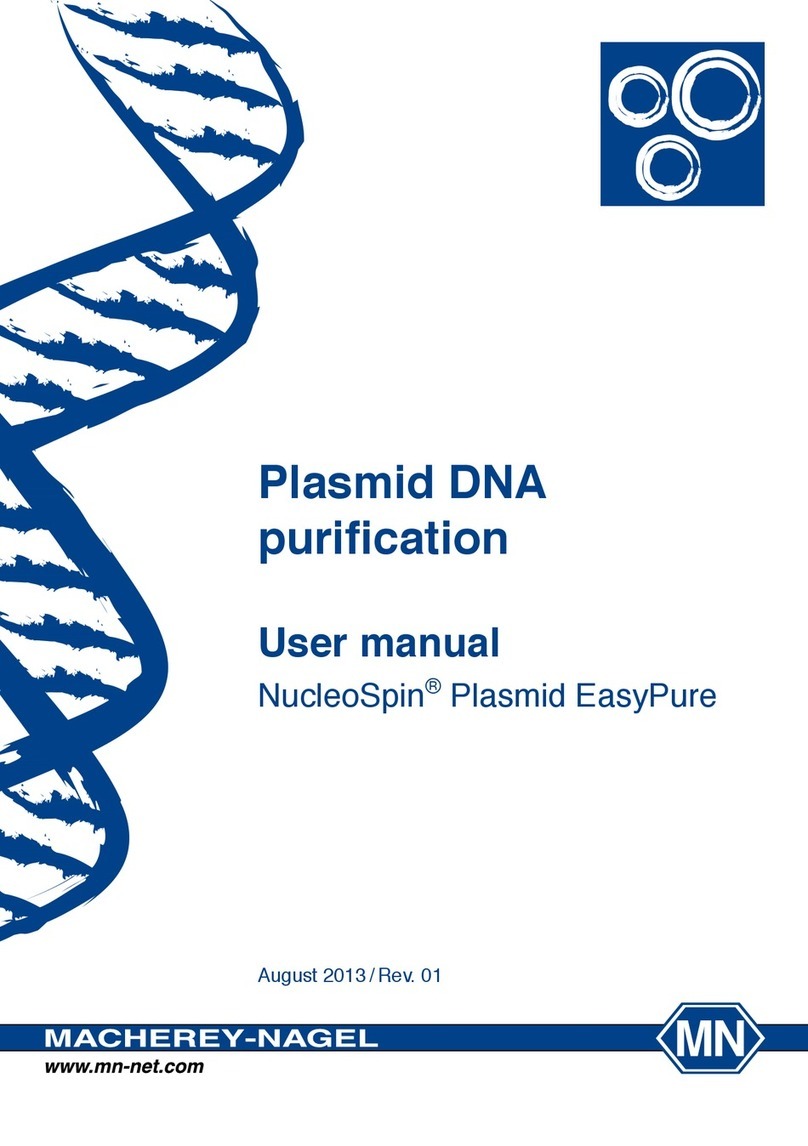
Macherey-Nagel
Macherey-Nagel NucleoSpin 740727.10 user manual
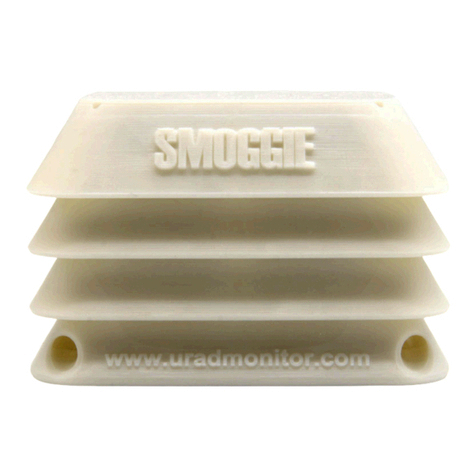
uRADMonitor
uRADMonitor SMOGGIE quick start guide
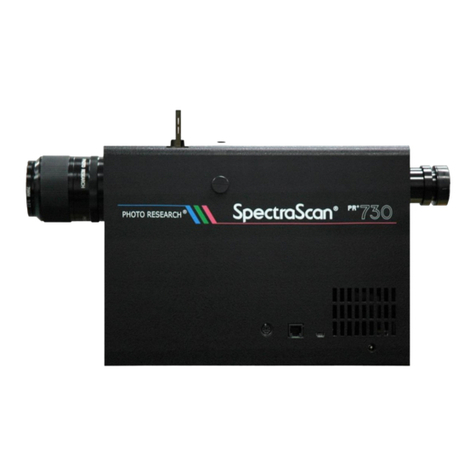
Jadak
Jadak Photo Research SpectraScan PR-7 Series user manual

REED
REED SD-4023 instruction manual
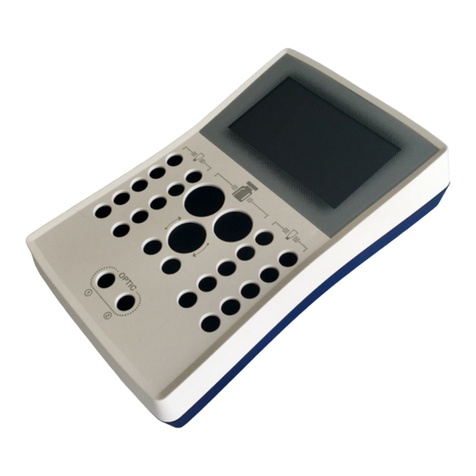
DIALAB
DIALAB DIAcheck C1 Operation manual
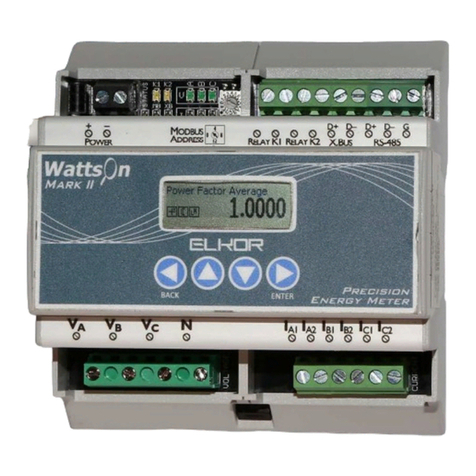
ELKOR
ELKOR WattsOn-Mark II Installation and commissioning guide
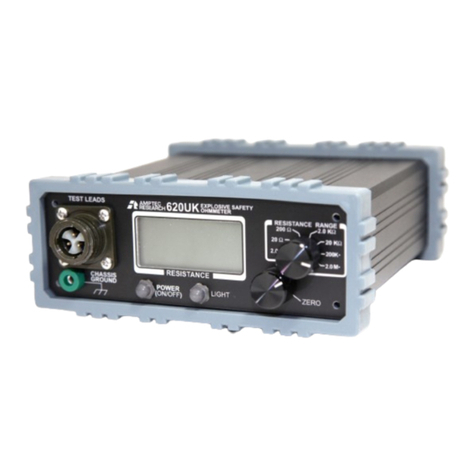
Amptec Research
Amptec Research 620UK-4 MAINTENANCE and Operation manual
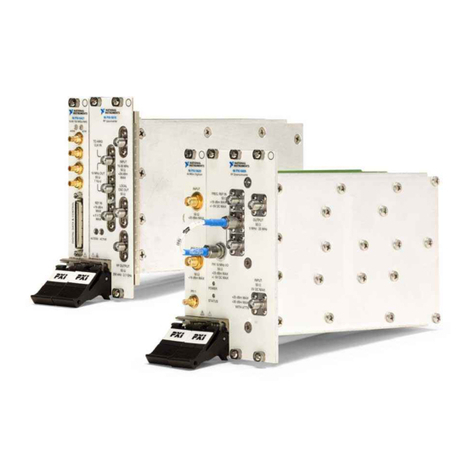
National Instruments
National Instruments PXI-5660 Getting started guide

Siemens
Siemens FS720 Series Mounting & installation
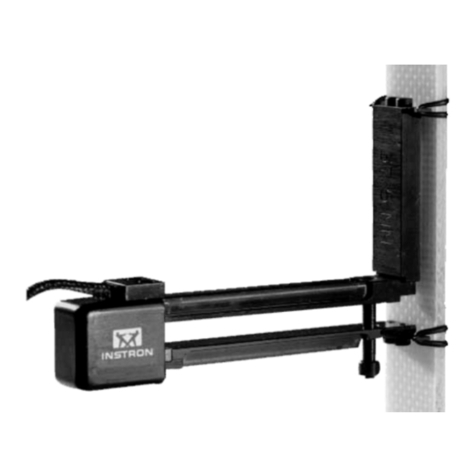
Instron
Instron 2620-600 Series Reference manual