Ss Brewtech BREWMASTER User manual

— BREWMASTER EDITION —
Ss BREW KETTLE
Quick Reference Guide

Stainless Steel Prep
Pre-Clean: Prior to rst time use, thoroughly wash all surfaces of the
kettle, including the valve and TC ttings, with Tri-Sodium Phosphate
(TSP) in hot water, mixed to the manufacturer’s recommendations.
Scrub with a soft terry cloth, and after the initial TSP wash, rinse
thoroughly and dry all surfaces.
Passivation: It’s good practice to periodically passivate all stainless
steel equipment with an acid based solution to establish a uniform
passive oxide layer that will maximize corrosion resistance. Following
the pre-clean step, ll the kettle with Star San at a concentration of 1
ounce per gallon at 70-80°F for 30 minutes. Moving forward, for best
stainless performance, passivation should be performed at least
once a year or anytime you believe you may have inadvertently
scratched the surface.
Cleaning and Sanitizing: As part of a regular cleaning regimen both
pre and post-boil/mash, wash the interior surfaces of your kettle with an
alkali cleaner such as PBW at a ratio of 0.75 ounce per gallon.
Kettle Assembly
Once the initial pre-clean step is complete, begin by locating the TC
clamps, gaskets, and caps. We have included caps for the tangential
whirlpool and thermometer ports when these accessories are not in use.
Begin by capping these locations using the included TC ttings to form
a liquid tight seal.
Next, locate the ½” TC sight glass ball valve, and the remaining TC
clamp and gasket. Install the ball valve so that the handle is pointed in
the upright position. Then locate the kettle racking arm, and insert the
arm from the inside of the kettle. As a best practice, use a small amount
What’s in the Box
• Kettle
• Lid
• ½” TC Sight Glass Ball Valve
• Ball Valve Racking Arm
• (3) TC Clamps
• (3) TC Gaskets
• (2) TC Caps

of Star San solution to lubricate the racking arm’s O-rings before
inserting it into the valve. Doing so will extend the life of the O-rings.
Before brewing, its best to align the racking arm with the ball valve’s
handle so that a reference point exists when rotating the valve.
Beginning with the valve pointed upward, there is a full 180 degrees of
rotation in to avoid the pickup of hops or trub during knock out.
Installation of the Optional Thermometer: If they have already been
installed, begin by removing the included TC cap from the thermometer
port. Once removed, locate the TC kettle thermometer and reinstall so
that the temperature marks are clearly visible.

Installation of the Optional Whirlpool Accessories: We have
designed the BME kettle to accept modular TC ttings to divert the
ow of wort and create a uniform whirlpool and trub cone. Equipment
congurations can vary, so we will offer two examples of establishing a
correct whirlpool recirculation loop.
In the rst example the recirculation loop will be left in place without
a ball valve during the length of the boil, this setup is ideal for users
with a dedicated brew kettle pump and want to avoid tying up the use
of the kettle’s main sight glass ball valve. A whirlpool tee tting, TC
thermometer, ½” ID silicone tubing, hose clamps, and ½” TC barb tting
will be required for the install to work correctly.
Begin by installing the optional whirlpool tee tting at the thermometer
port location, and then install the TC thermometer opposite the port
location, so that the thermoprobe extends into the kettle. Then attach
a length of ½” ID silicone tubing from the whirlpool tee tting’s barb to
the pumps inlet. Lastly, run a length of ½” ID silicone tubing from the
pump’s outlet to the ½” TC barb tting and secure that to the kettle’s
tangential inlet.
In the next example, the recirculation loop will utilize two valves to
control the ow of hot wort from the kettle. This setup is ideal for users
utilizing a single pump for their entire brewhouse. This setup also
allows the user to install the recirculation loop temporarily post boil. A ½”
3-piece TC ball valve, ½” ID silicone tubing, hose clamps, and ½” barb
ttings will be required for the install to work correctly.
Begin by running a length of ½” ID silicone tubing from the kettle’s
primary ½” TC sight glass ball valve to the pump’s inlet. Then install the
second ½” 3-piece TC ball valve at the tangential inlet location. Lastly,
run another length of ½” silicone tubing from the pumps outlet, to the
newly installed tangential inlet ball valve.
Once installed, both methods allow for the wort to be picked up from
either the thermometer port or the main ball valve, and recirculate
through the kettles integrated tangential whirlpool port.

Warranty information can be found at www.ssbrewtech.com/warranty
Once cleaned and assembled, your kettle is now ready for use. The
BME kettle was designed with advanced brewing practices in mind, and
purpose-built to suit the needs of a boil kettle or HLT. It is not recom-
mended to use your BME kettle as a mash tun since false bottoms are
not available, however, the kettle is perfectly suited for BIAB brewing.
If you intend to use the vessel primarily as a boil kettle. The rotatable
racking arm and sight glass are key features that will inhibit the transfer
of break material, trub, and hop residue into the fermenter. For best
results, immediately following the boil, create a whirlpool utilizing one of
the methods explained above. The dished bottom and tangential inlet
will assist greatly in fostering a smooth and consistent whirlpool, free of
cavitation.
The effectiveness of the racking arm to avoid trub pickup is dependent
on creating a trub cone in the center of the vessel. Furthermore, nning
agents such as Whirloc or irish moss can also be used to assist in
the process of coagulating break material. This process is especially
important for brewers that typically utilize whole or leaf hops, since they
can easily clog the kettle’s racking arm.
If you plan to utilize a propane or gas burner, take care to insure that the
burner is sized appropriately. Ensure that the kettle is centered directly
over the burner, and for stability, always make sure that the dish bottom
and outer re box skirt are both in contact with the burner’s stand.
Kettle Operation and Best Practices
Direct ame or heat that comes into the contact with the
ball valve or thermometer can cause damage to the ther-
mometer’s and/or ball valve’s interior seals. Always brew
on a at, nonammable surface.

USE THE FOLLOWING WITH CAUTION:
• Stainless steel scrubbing pads or Scotch-Brite pads. If used too
aggressively, abrasive pads can damage the surface and/or nish of
the stainless.
• Oxalic Acid cleaners such as Bar Keeper’s Friend, Kleen King, or
Revere Ware Stainless cleaners on the etched volume markings or
etched logo. They may cause the markings to fade.
NEVER USE THE FOLLOWING:
• Chlorine bleach or chlorine based products. Chlorine can cause pit-
ting of stainless steel, or pin holes through the surface which cannot
be repaired.
• OxiClean or other peroxide cleaners in combination with hard water.
These can cause calcium carbonate to precipitate onto the surface.
If this happens re-passivate your Chronical.
If you have any further questions about your Ss Brewtech gear go to our website and take a look
at our extensive knowledgebase in the FAQ section. Over the years it has become a treasure trove
of information. If after searching our FAQs, you still can’t nd an answer to your specic question,
please email us at [email protected].
During the rst use with your kettle, the outer re box skirt will change in
color due to the high heat of propane or natural gas burner. This should
be considered completely normal and will not affect the operation or
longevity of the vessel.
The BME kettle utilizes a robust stainless dished bottom which has not
been tri-clad, as such it is not compatible with induction burners.
Lastly, while our kettles are designed to be lifted while full, never attempt
to lift a kettle that contains hot liquid due to the risk of injury or scalding
to yourself or others. As a solution, utilize a wort pump to transfer hot
liquids and avoid injury.

— Optional Whirlpool Valve and Thermometer available on www.SsBrewtech.com —

© Ss Brewtech
Table of contents
Other Ss Brewtech Brewing System manuals
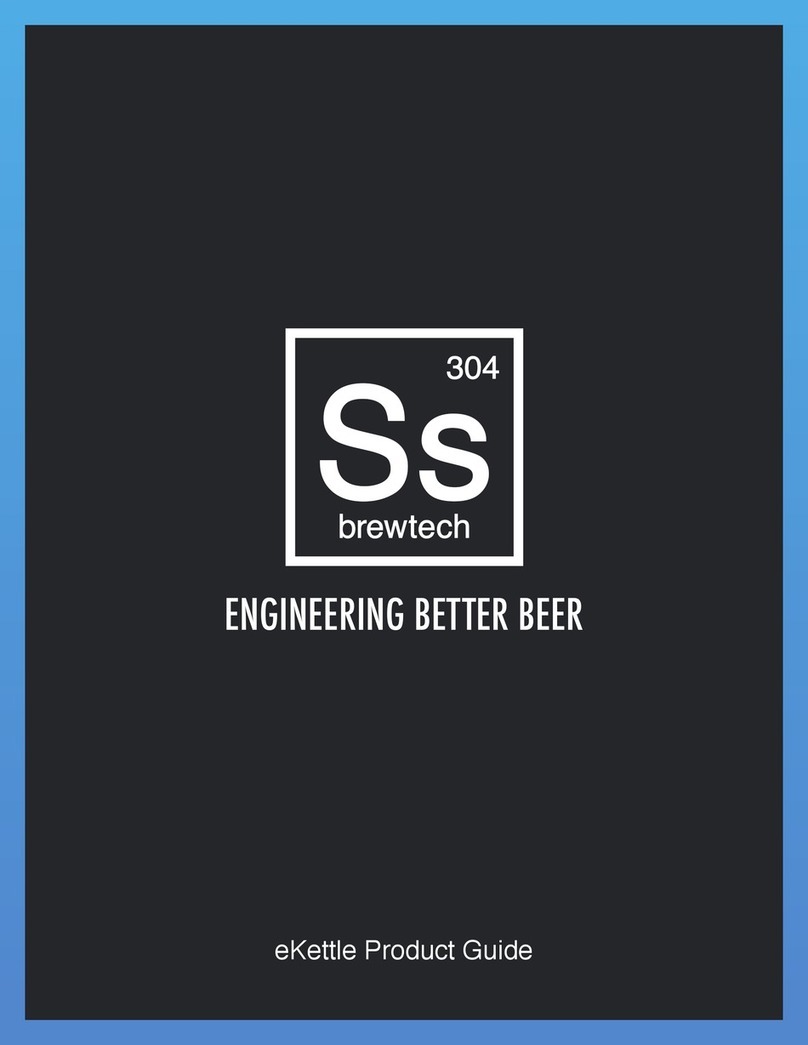
Ss Brewtech
Ss Brewtech E-Kettle 304 User manual
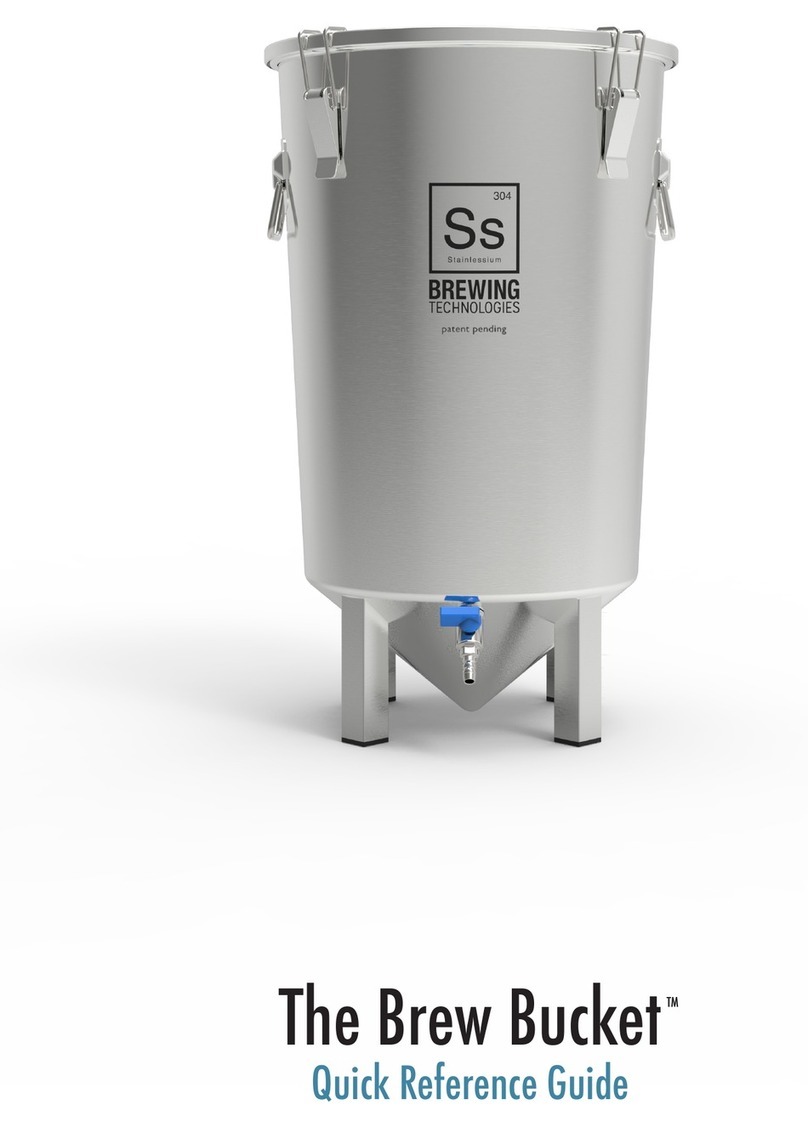
Ss Brewtech
Ss Brewtech The Brew Bucket User manual
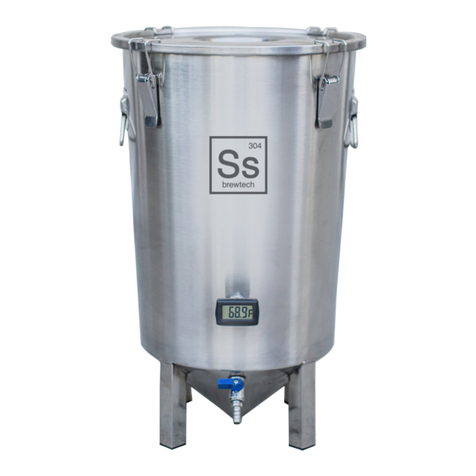
Ss Brewtech
Ss Brewtech E-Kettle 304 User manual
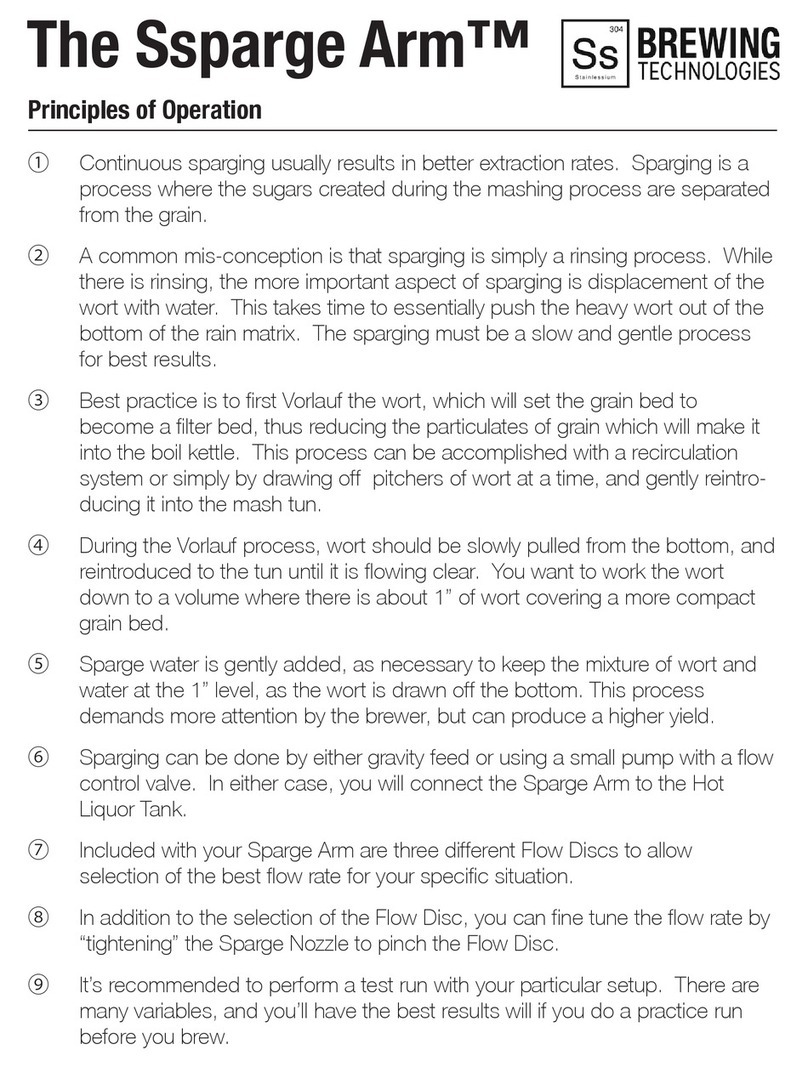
Ss Brewtech
Ss Brewtech Ssparge Arm User manual
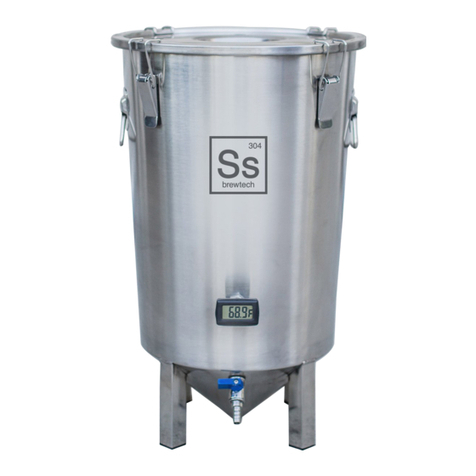
Ss Brewtech
Ss Brewtech E-Kettle 304 User manual
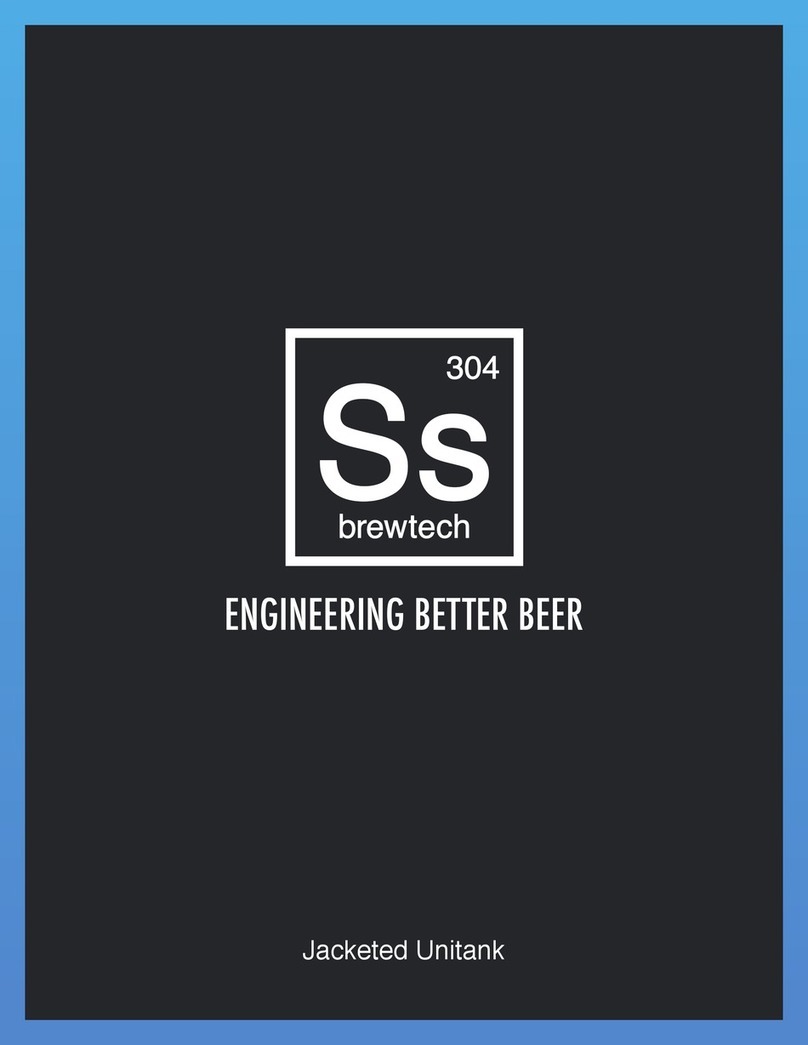
Ss Brewtech
Ss Brewtech Jacketed Unitank User manual
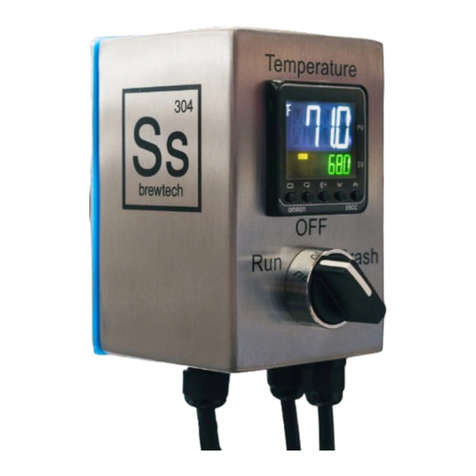
Ss Brewtech
Ss Brewtech FTSs Pro User manual
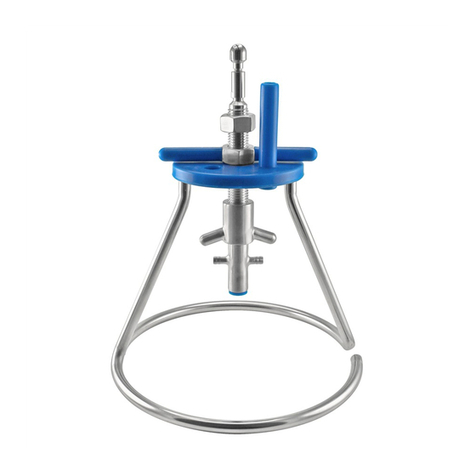
Ss Brewtech
Ss Brewtech Keg WaSsher User manual
Popular Brewing System manuals by other brands

Newco
Newco AKH-TC-A Installation and operation manual
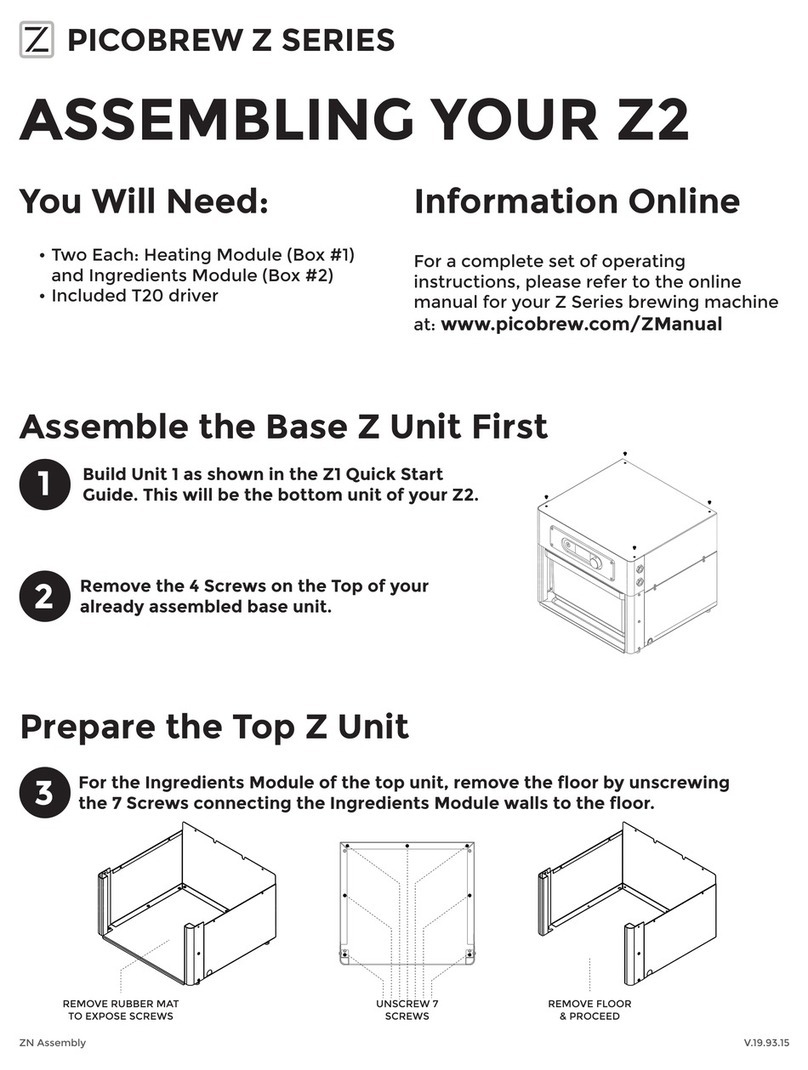
PicoBrew
PicoBrew Z Series Assembly guide
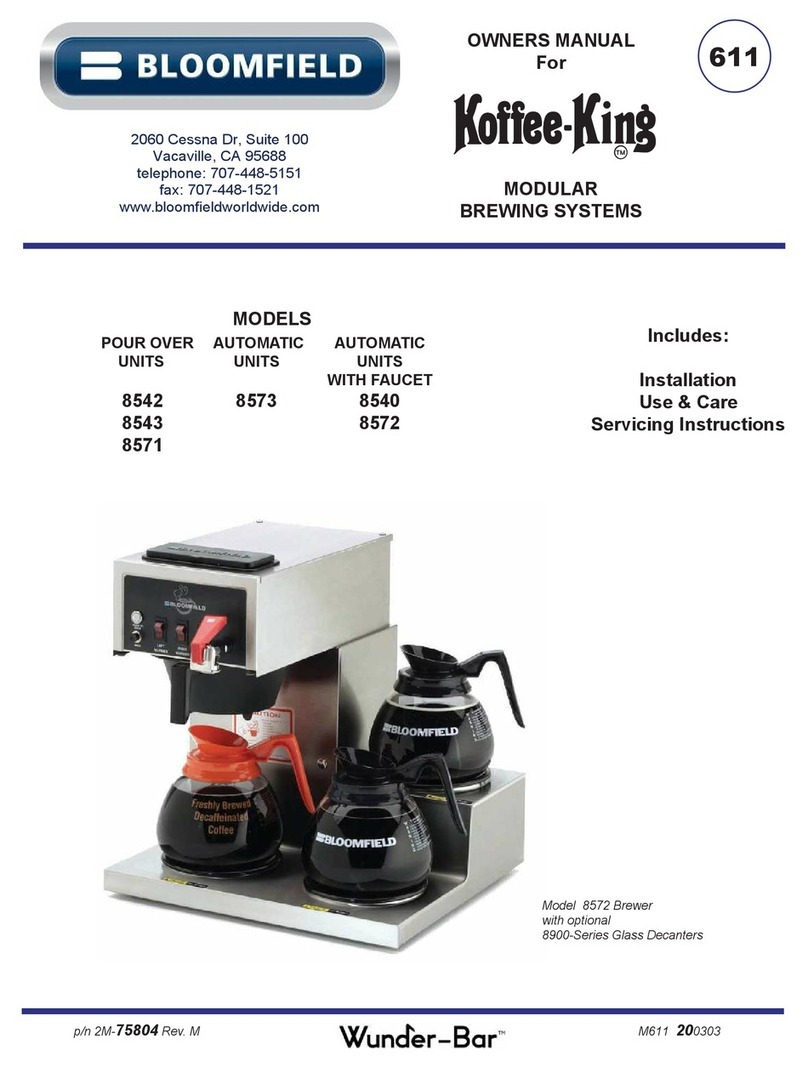
Bloomfield
Bloomfield Koffe-King Wunder-Bar 8573 owner's manual
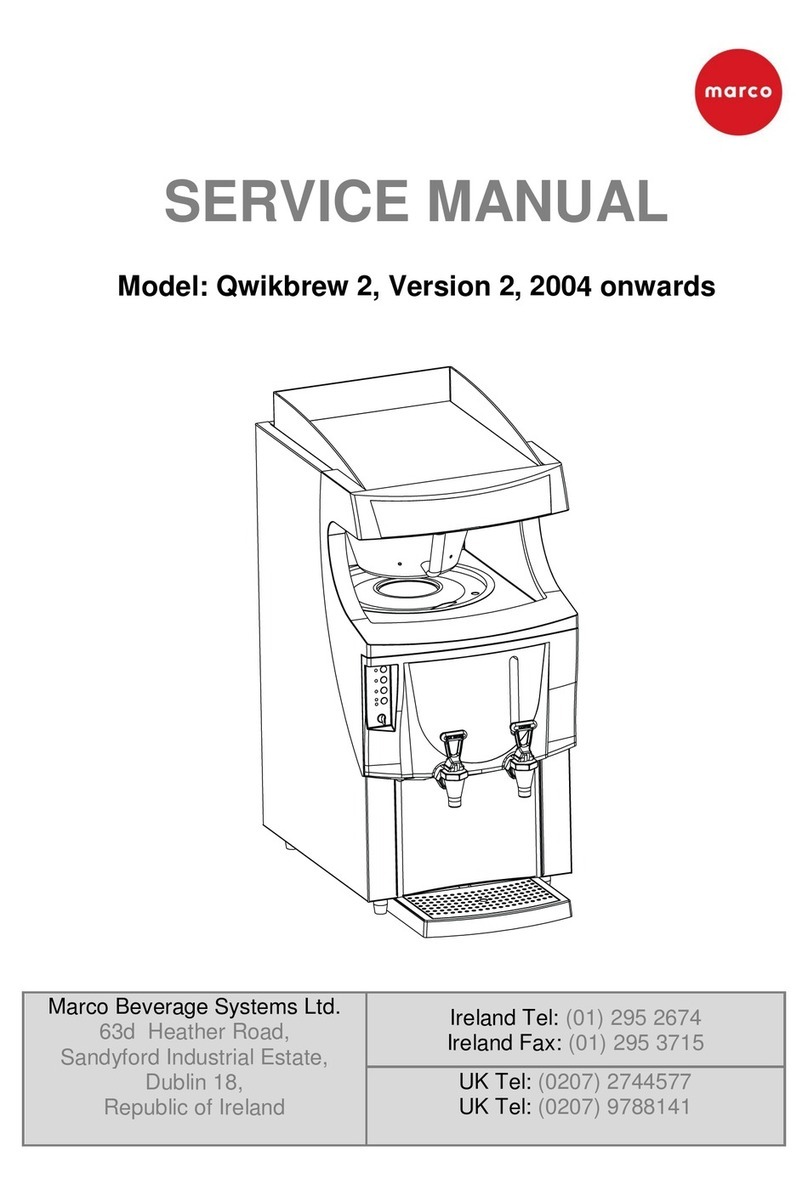
Marco
Marco Qwikbrew 2 Twin Service manual
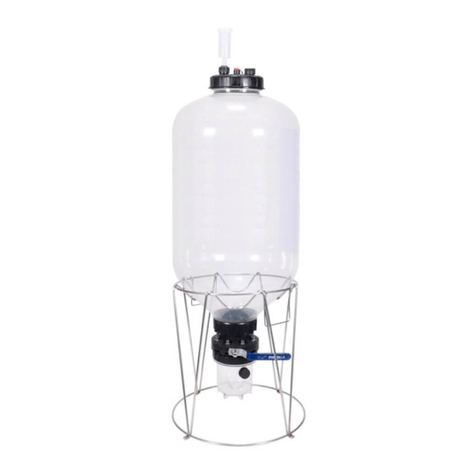
KegLand
KegLand Fermzilla Unitank Series instruction manual
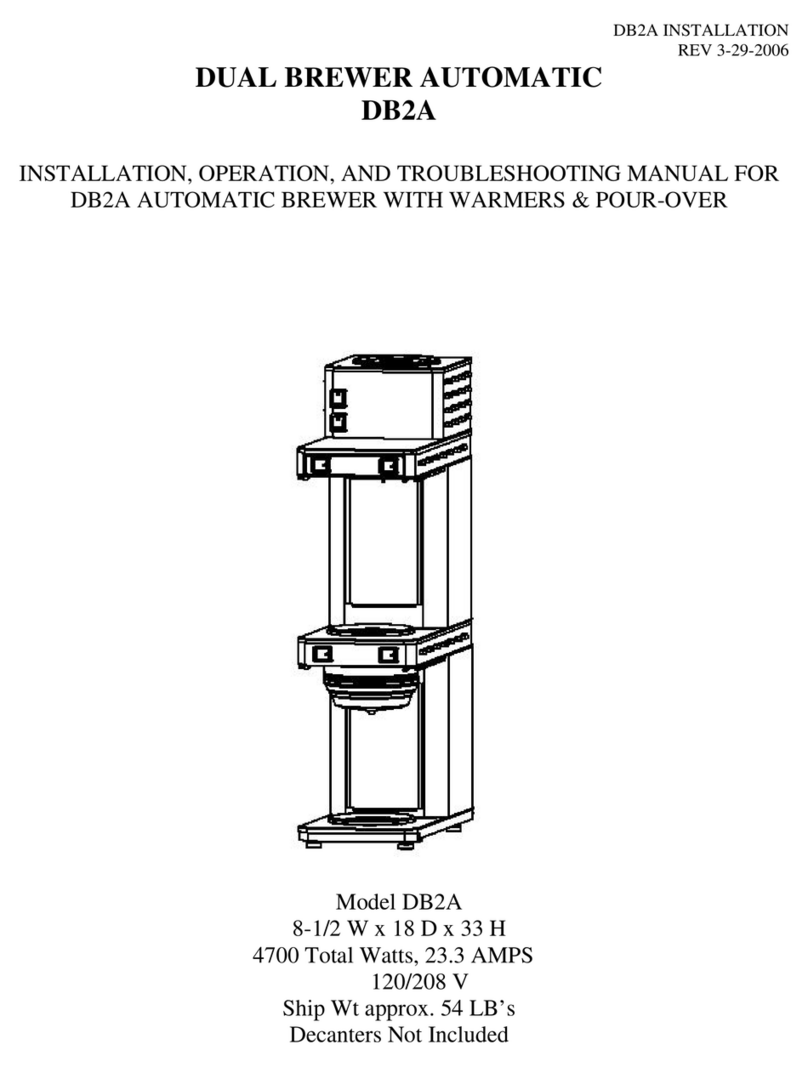
Newco
Newco DB2A Installation & operating manual