Starrett AVR200 User manual

AVR200 and AVR300
Automatic Video Metrology Systems
User Guide
Copyright © 2020 Starrett Kinemetric Engineering
All rights reserved
AVR200 and AVR300 are registered trademarks of Starrett Kinemetric Engineering
www.starrettkinemetric.com
September 2020
6106 Revision D

The information contained herein is subject to change without notice. Revisions may be issued to advise
of such changes and/or additions.
Correspondence regarding this publication should be forward to Starrett Kinemetric Engineering by
addressing remarks to Technical Support Starrett Kinemetric Engineering, 26052 Merit Circle, Suite 103
Laguna Hills CA 92653, USA. Comments about documentation can also be sent through our service
website at: https://www.ske-service.com/service-request.
Starrett Kinemetric Engineering is an ISO 9001:2015 registered company.

AVR200 and AVR300 User Guide
3 6106 Revision D
Table of Contents
1. About This Guide..................................................................................................................................5
1.1 Purpose........................................................................................................................................5
1.2 Scope...........................................................................................................................................5
1.3 Audience......................................................................................................................................5
1.4 Prerequisites................................................................................................................................5
1.5 Conventions.................................................................................................................................5
1.6 Warranty ......................................................................................................................................6
1.7 Disclaimer of Liabilities................................................................................................................6
1.8 Copyright and Trademark Information.........................................................................................6
1.9 Related Production Information...................................................................................................6
2. Regulatory and Environment Standards............................................................................................7
2.1 Regulatory Compliance ...............................................................................................................7
2.2 Environmental Conditions............................................................................................................8
2.3 Safety Considerations..................................................................................................................8
3. The AVR200 and AVR300 Systems...................................................................................................11
3.1 Overview....................................................................................................................................11
3.2
Features and Capabilities
........................................................................................................11
3.3 AVR Configurations and Options...............................................................................................12
3.4 AVR System Components.........................................................................................................13
3.4.1 X-Y Stage..........................................................................................................................13
3.4.2 Z-Column ..........................................................................................................................13
3.4.3 Motorized Z-Track.............................................................................................................13
3.4.4 MetLogix M3 Metrology Software .....................................................................................14
3.4.5 Lens Options.....................................................................................................................15
3.4.6 Lighting Control.................................................................................................................16
3.4.7 Touch Probe Option..........................................................................................................17
3.4.8 Rotary Stage Options........................................................................................................18
3.4.9 Operator Controls and Interfaces......................................................................................19
3.4.10 Workstation .......................................................................................................................19
4. System Specifications .......................................................................................................................21
4.1 Performance Specifications.......................................................................................................21
4.2 Hardware and Mechanical Specifications..................................................................................21
4.3
Electrical Specifications
...........................................................................................................23
4.3.1 Electrical Power ................................................................................................................23
4.4
Optical Specifications
...............................................................................................................24
4.5 Computer and Software Specifications .....................................................................................25
4.6 Touch Probe Specifications.......................................................................................................25
4.7 Rotary Stage Specifications.......................................................................................................27
4.8 Workstation Specifications.........................................................................................................29
5. Installation and Setup ........................................................................................................................31
5.1 Planning the Placement of Equipment ......................................................................................31
5.2 Moving the Equipment...............................................................................................................31
5.3 Uncrating the Equipment...........................................................................................................32
5.4 Removing Shipping Retainers...................................................................................................33
5.5
Setting Up the System
..............................................................................................................35
5.6 On-Site Installation, Calibration and Training............................................................................36

AVR200 and AVR300 User Guide
4 6106 Revision D
6. System Operations.............................................................................................................................39
6.1 Powering On the System...........................................................................................................39
6.2 Manually Controlling the System...............................................................................................40
6.3 Verifying Basic M3 Software Operations...................................................................................41
6.4 Fixturing Parts............................................................................................................................42
6.5 Accessing System Electronics...................................................................................................44
7. Understanding Measurement Strategy ............................................................................................45
7.1 Zoom Optics Measurement Strategy.........................................................................................45
7.2 Telecentric Lens Measurement Strategy...................................................................................45
7.3 Illumination Strategy ..................................................................................................................46
7.4 Focus Strategy...........................................................................................................................46
7.5 Verifying the Setup of the System .............................................................................................46
8. Maintaining the System .....................................................................................................................49
8.1 Performing Daily Inspections.....................................................................................................49
8.2 Weekly Inspections....................................................................................................................49
8.3 Monthly Zoom Optics Alignment Verification.............................................................................49
8.3.1
Zoom Optics Parfocality and Focus
................................................................................50
8.3.2
Zoom
Optics
Parcentricity
................................................................................................50
8.3.3
Zoom
Optics
Squareness
................................................................................................51
8.4 Monthly Calibration Verification.................................................................................................52
8.5 Cleaning.....................................................................................................................................53
8.5.1
Cleaning External Surfaces
.............................................................................................54
8.5.2
Cleaning Optics
................................................................................................................54
8.5.3
Cleaning
Critical Mechanical Parts
..................................................................................55
8.6
Spare Parts and Accessories
...................................................................................................55
9. Glossary ..............................................................................................................................................57

AVR200 and AVR300 User Guide
5 6106 Revision D
1. About This Guide
1.1 Purpose
This guide provides instructions on how to install, operate and maintain the AVR200 and
AVR300 automatic digital video systems. This guide also provides information on the various
options and features available with the system.
1.2 Scope
This guide provides detailed information about components, features, and specifications of
the AVR systems. This guide also includes operating and maintenance information for the
system. High-level information is provided on unpacking and installation. AVR systems are
intended to be installed by SKE Technical Service specialists, Authorized Service Partners, or
qualified third-party personnel.
1.3 Audience
This guide is intended for end-user customers, SKE Technical Services specialists, and
Authorized Service Partners.
1.4 Prerequisites
You should have some knowledge of vision metrology systems and be familiar with
customary system administration and field service practices.
1.5 Conventions
Information that Requires Special Attention
This guide uses the following three conventions to present information that requires special
attention: a warning, a caution, or a note.
A warning looks like this:
WARNING
Warning information is printed in a box. Warnings direct your attention to
operating or maintenance procedures or practices that must be followed
correctly to prevent personal injury, loss of life and, possible, hardware or
software damage.
A caution looks like this:
Caution
Caution information is printed in a box. Cautions provide information that helps to prevent
accidental hardware or software damage.

AVR200 and AVR300 User Guide
6 6106 Revision D
A note looks like this:
Note
: Pay special attention to the information printed in italics that follows the
Note:
heading. Notes provide additional information that is important to the surrounding
text.
Small Form Factor PC
Throughout this manual, the small form factor PC that is including with the AVR systems will
be referred to as system PC.
1.6 Warranty
Starrett Kinemetric Engineering, Inc. products carry a one-year (from date of purchase)
warranty against defects in material and workmanship (parts and labor) subject to factory
inspection. Parts not manufactured by the Starrett Kinemetric Engineering, Inc. (for example,
computers, monitors, etc.) carry the original manufacturers’ warranty. Starrett might also
process warranty for these parts.
Starrett Kinemetric Engineering, Inc. will repair or replace, at our option, any part or parts,
which we find defective in workmanship or material. We will warranty repaired or replaced
parts for the balance of the original warranty period or 90 days whichever is longer. This
warranty will not apply to defects resulting from modifications made by the customer or
improper use of the system or its components. If applicable, parts returned to the factory will
be repaired at no charge. The customer will pay freight charges to the factory, with return UPS
Ground freight charges to the customer paid by Starrett. Freight other than UPS Ground can
be requested and additional fees may apply.
This warranty does not cover damages from such causes as abuse, accident, neglect, fire,
flood, electrical surge, or freight damage.
1.7 Disclaimer of Liabilities
The L.S. Starrett Company shall have no liability or responsibility to the customer or any other
person or entity with respect to any liability, loss or damage caused or alleged to be caused
directly or indirectly by this documentation, or the hardware and software described in it. This
includes, but is not limited to, any interruption of service, loss of business or anticipatory
profits, or consequential damages resulting from the use or operation of hardware or
equipment.
1.8 Copyright and Trademark Information
AVR200™and AVR300™are trademarks of the L.S. Starrett Company.
M3™is a trademark
of MetLogix, Inc. Windows
®
is a registered trademark of Microsoft Corporation.
1.9 Related Production Information
The following documents provide information that is related to the subject of this guide.
MetLogix M3 Video and FOV Inspection Software User’s Guide
This guide provides detailed information on operating the M3 software that is included with
AVR systems.

AVR200 and AVR300 User Guide
7 6106 Revision D
2. Regulatory and Environment Standards
This section provides the regulatory, environment, and safety information for the AVR
systems.
2.1 Regulatory Compliance
The AVR200 and AVR300 Video Metrology Systems have been
inspected, tested, and evaluated by independent test laboratories
and are declared to comply with Council Directives 2006/42/EC -
Machinery and 2002/95/EC RoHS (by exemption) when installed and
operated in accordance with this manual. Accordingly, these systems
are entitled to bear the CE Mark.
EMC Test Standards
Standard
Description
EN 61326-1:2013
CISPR 11:2003+A1:2004
+A2:2006
Radiated and Conducted Emissions
IEC 61000-4-2:2009
Electrostatic Discharge Immunity
IEC 61000-4-5:2006
Power Line Surge Immunity
IEC 61000-4-4:2012
Electrical Fast Transients Burst Immunity
EN 61000-4-6:2009
RF Common Mode Immunity
IEC 61000-4-3:2006 +A2:2010
Radio Frequency Immunity
IEC 61000-4-8:2010
Power Frequency Magnetic Field Immunity
IEC 61000-4-11:2004
Voltage Dips and Short Interruptions Immunity
Safety Standards
Standard
Description
EN 60204-1:2006+A1:2009
Safety of Machinery, Electrical Equipment of Machines
EN 12100
Safety of Machinery, Principles for Risk Assessment

AVR200 and AVR300 User Guide
8 6106 Revision D
2.2 Environmental Conditions
Operating Conditions
AVR systems can be safely operated under the following environmental conditions:
Environmental Condition
Operational Requirement
Ambient Temperature
20°C ± 3°C (68°F ± 5°F)
Humidity
< 90% RH
If the system is to be operated under environmental conditions that are substantially different
from those in the previous table, the system should be recalibrated under the expected
conditions. Users should also consider the material characteristics of the parts under
inspection, in particular coefficients of thermal expansion. Numerical compensation might be
required when measuring parts under conditions different from those controlling the stated
dimensional specifications for these parts.
Before performing critical parts measurements, allow the system to warm up for 30 minutes
and use the system’s joystick to cycle the X, Y and Z axes ten times.
Factory Calibration Conditions
AVR systems are factory calibrated under the standard laboratory environmental conditions
shown below:
Specification
Calibration Requirement
Ambient Temperature
20°C ± 0.5°C (68°F ± 5°F)
Humidity
40-60% RH
Temperature rate of change
0.5°C (1°F) per hour
2.3 Safety Considerations
General Safety
AVR systems are designed for safety and proper ergonomics during normal use. Exercise
caution when handling or moving the systems to maintain calibration and measurement
performance. Disconnect all power sources prior to moving or working on the equipment.
Consult SKE if you have any question regarding transporting, using, or maintaining the
systems.
Electrical Safety
AVR systems do not contain hazardous AC line voltages, as these are contained on the input
side of the system’s AC adapters, which are UL listed. Even at these low voltages, there is
the potential of electrical component damage caused by accidental short circuits. For
maximum electrical safety and minimal risk to the equipment, adhere to the following
guidelines:

AVR200 and AVR300 User Guide
9 6106 Revision D
•
Ensure that the power receptacles for the AC adapters are properly grounded 3-prong
polarized 100-240VAC for use in North America or appropriate safety-rated receptacles
for use outside of North America.
•
Do not operate the systems with housings open except for service by a factory trained
technician.
•
Keep liquids away from the systems, and do not operate the equipment in excessively
humid conditions, as water can cause short circuits.
•
Keep metal filings away from the systems, as such debris can cause short circuits.
•
Do not operate the equipment around volatile or flammable solvents, as local electrical
heating could cause ignition.
•
Disconnect power, or do not plug in the power cord, if hazardous conditions exist such as
a damaged or frayed power cord, a damaged or improperly grounded power receptacle,
equipment exposure to liquid spills or excessive moisture, or impact damage. Have the
system inspected by authorized personnel before operating.
There are no fuses or user-serviceable items in the systems. Systems should only be opened
by a factory-trained service technician.
Mechanical Safety
•
AVR systems are heavy. To avoid possible back injury, use multiple persons to lift. Bend
your knees, not your back.
•
Only manually lift AVR systems by the two red carrying handles and shipping lift bar. For
more information on lifting the system, refer to “Removing Shipping Retainers” later in this
guide.
•
Motion of the metrology unit is motorized. Motion can be under full computer control or
simply under joystick and trackball control with the computer turned off. There are pinch
points. Do not place your hands or mechanical items at or near pinch points.
Emergency Stop
The AVR systems are equipped with two emergency stops as follows:
•
Red button located on top of the joystick. Refer to the following figure.
•
Emergency stop assembly that includes a switch, cable and DB9 connector. The DB9
connector is connected to the rear of the AVR system. This stop button should be placed
in a highly visible and accessible location in case of emergency. Refer to the following
figure.
When the Emergency Stop is engaged, the M3 software will continue to function as normal,
except in the following scenarios:
•
If the Emergency Stop is engaged during the auto-homing sequence, all motion will
cease, and a dialog box will display the following message:
“An error occurred while auto homing. Measurements will be compromised.”
When the Emergency Stop is disengaged, nothing further will happen. The system should
now resume normal function and the auto-homing sequence will need to be re-run.

AVR200 and AVR300 User Guide
10 6106 Revision D
Figure
1.
Joystick Emergency Stop Button
Figure
2.
Emergency Stop Switch
•
If the Emergency Stop is engaged while a program is running, all motion will cease, and a
dialog box will display the following message:
“The program has been interrupted [SIC] by a hardware error? A CNC E-Stop error
occurred. An E-Stop Error occurred on axis 1. An E-Stop Error occurred on axis 2. An E-
Stop Error occurred on axis 3. “
When the Emergency Stop is disengaged, nothing further will happen. The system should
now resume normal function and the program will need to be re-run from the start. Any data
collected before the Emergency stop was engaged will be saved and can be viewed/exported
as normal.
•
If the user attempts to run the program with the Emergency Stop engaged, all motion will
cease, and a dialog box will display the following message:
“The program has been interrupted [SIC] by a hardware error? A CNC E-Stop error
occurred. An E-Stop Error occurred on axis 1. An E-Stop Error occurred on axis 2. An E-
Stop Error occurred on axis 3. “
When the Emergency Stop is disengaged, nothing further will happen. The system should
now resume normal function.
Emergency
stop switch

AVR200 and AVR300 User Guide
11 6106 Revision D
3. The AVR200 and AVR300 Systems
This section provides the following information:
•
An overview of the AVR systems
•
A description of the features and capabilities of the AVR systems
•
A description of the configuration options
•
A description of the major components of the AVR systems
3.1 Overview
The AVR systems provide a comprehensive CNC metrology solution for dimensional
measurement and inspection applications where high accuracy, extended travel, and a stable
base for multi-sensor measurements are required. The systems are available in two sizes:
the AVR200 with 200 x 100 x 200 millimeters (8 x 4 x 8 inches) of X-Y-Z travel and the
AVR300 with 300 x 200 x 200 millimeters (12 x 8 x 8 inches) of X-Y-Z travel.
3.2 Features and Capabilities
The AVR systems include the following features and capabilities:
•
Includes a granite base for stability, recirculating ball linear guides for smooth and precise
stage motion, and full CNC control.
•
All electronics, other than the PC system, are housed in the Z-column, providing a clean,
integrated system with minimal external wiring. Two high-speed data cables carry all
signals between the metrology unit and PC.
•
Includes the following color video camera options:
•
1.3 megapixel (MP) camera with the standard configuration
•
2 megapixel (MP) camera with the FOV configuration
•
5 megapixel (MP) camera with the 0.14X telecentric lens configuration
•
Metrology performance is provided by linear encoders with 0.1 micron resolution and by
precision optics, which can be 6.5:1 or 12:1 motorized zoom optics, manual 6.5:1 zoom
optics, or numerous telecentric lenses for accurate field-of-view (FOV) measurements.
•
FOV measurements can encompass an entire small part up to 2.00 x 1.50 inches or a
feature of a larger part and be seamlessly integrated with stage motion to measure parts
with a length up to 200 mm (AVR200) or 300 mm (AVR300).
•
24-inch touch screen monitor and small form factor PC (system PC) which runs MetLogix
M3 CNC software under Windows® 10.
•
Ergonomic workstation and easy to use operator controls
•
Optional rotary stage that provides increased workpiece holding versitility.
•
Optional touch probe that is ideal to measure the height of flat surfaces or the lateral
position of vertical surfaces at different heights.

AVR200 and AVR300 User Guide
12 6106 Revision D
•
Optional touch probe changing rack enhances the touch probe option by offering
additional utility.
3.3 AVR Configurations and Options
There are several options available for AVR200 and AVR300 systems. Refer to the following
table for a description of the various options.
System
Options
AVR200 and AVR300 (basic)
•
1.3 megapixel color video camera
•
6.5:1 or 12:1 continuously adjustable motorized zoom
optics. Optics are not interchangeable by the user.
•
Illumination sources including: LED ring light and colli-
mated LED sub-stage lighting (standard), and coaxial
LED lighting
AVR200 FOV and AVR300
FOV
•
2 megapixel color video camera
•
Bayonet lens mount that accepts a 6.5:1 manual
zoom lens
•
Telecentric lenses with the following magnifications:
0.3X, 0.5X, 0.8X, 1.0X, 2.0X, 4.0X
•
Two-channel illumination provided by an LED ring
light, collimated LED sub-stage lighting, and LED
quad ring light
AVR300 FOV 0.14X
•
5 megapixel black and white video camera
•
0.14X telecentric lens
•
Two-channel illumination provided by an LED ring
light and collimated LED sub-stage lighting
Options
•
Auxiliary zooms lenses:
0.5X, 1.5X, 2.0X
•
Touch probe
•
Ergonomic workstation
•
Rotary stage
Accessories
•
Calibration standards
•
Calibration grids
•
Magnification checkers
For more information on available accessories, refer to
“Spare Parts and Accessories” later in Section 8.

AVR200 and AVR300 User Guide
13 6106 Revision D
3.4 AVR System Components
The following information describes the key components of the AVR systems.
Figure
3.
AVR System Components
3.4.1 X-Y Stage
The AVR200 stage offers a measurement range of 200 x 100 x 200 millimeters
(8 x 4 x 8 inches). The AVR300 offers a measurement range of 300 x 200 x 200 millimeters
(12 x 8 x 8 inches). The stage is made from precision machined aluminum on a granite base.
Surface mounting holes allow customer-designed fixtures for part support. Stage motion is by
means of a stepper motor.
3.4.2 Z-Column
A precision aluminum column supports the touch probe (optional), fixed ring light (standard),
coaxial light (optional), and height-adjustable motorized quad ring light (optional). Height
adjustment is 200 millimeters (8 inches) to accommodate tall parts. Motion along the Z-axis is
by means of a stepper motor.
3.4.3 Motorized Z-Track
A motorized Z-track enables height adjustment of the quad ring light. Z-track height is
adjusted through the M3 software. Height adjustment is approximately 15 centimeters
(6 inches).

AVR200 and AVR300 User Guide
14 6106 Revision D
Figure
4.
Motorized Z-Track with Mounted Quad Ring Light
3.4.4 MetLogix M3 Metrology Software
The AVR system includes the MetLogix M3 advanced metrology software. The software
includes the following key features:
•
Advanced Video Probes
: The M3 software includes several probes that provide the
ability to capture complex edges, enable instant feature determination and measurement
with the single click.
•
Field of View Functions
: The field of view Auto Run function plays part programs to
perform measurements quickly without operator intervention. Place one or more identical
parts in the field of view and the system will identify the part, execute the appropriate
program, and report measurement results.
•
Touch Probe Support
: M3 software includes support for multi-sensor video measuring
systems equipped with touch probe modules. Expanded 3-D feature geometries are
supported through touch probe and video measurement of features in the XY, YZ and ZX
planes. Measure planes, cones, cylinders and spheres in 3-D part space and then view
results in the 3-D part view. Part views can be rotated with markups showing feature
measurement results.
•
Multi-Touch Software Control
: In addition to the conventional mouse interface,
expanded MultiTouch logic allows for one-touch feature measurements as well as
versatile panning and zooming of the live video image and the active part view. This
Motorized
Z-Track
with
Mounted
Quad Ring
Light

AVR200 and AVR300 User Guide
15 6106 Revision D
capability increases the efficiency of feature measurements, feature data manipulation,
and reporting tasks with a simple pinch zoom, swipe pan, or double click.
•
Advanced Edge Teach
: This feature provides improved edge detection performance
under a variety of image and lighting conditions. Features with poor edge contrast, or
difficult spacing can be captured in a snap using the M3 software manual teach function.
•
DXF Overlay and FOV Capability
: Using the DXF/FOV option pack, you can import
DXF files for “comparative style” Go/No-Go feature and part inspection. This includes a
live error whisker display for violations of the original DXF tolerance zones. DXF/FOV
option pack features include:
•
Custom DXF crosshair
•
Create feature-based video overlays
•
Import DXF overlay
•
Export features to DXF
•
Pattern teach and recognition
•
Live image “freeze”
For detailed information on the MetLogix M3 software, refer to the
MetLogix M3 Video and
FOV Inspection Software User’s Guide
.
3.4.5 Lens Options
To maximize versatility, the AVR systems provide numerous lens options including 6.5:1 and
12:1 zoom optics and telecentric lens options from 4X to 0.14X.
•
The telecentric lenses that provide micron-level resolution and optical distortion as low as
0.001% across the field of view (depending on the lens) for accurate field-of-view (FOV)
measurements. The 0.14X option enables field-of-view measurements which can
encompass an entire small part up to 60 x 51 millimeters (2.36 x 2.00 inches) or a feature
of a larger part.
•
Zoom optics provide continuous zoom from 0.40X to 4.7X. Utilize zoom optics to measure
large parts which would not fit into a single FOV. Zoom optics are also beneficial for
smaller parts where extremely high magnification is required.
The following figure illustrates the 0.14X telecentric lens option. See “System Specifications”
later in this document for detailed information on lenses.

AVR200 and AVR300 User Guide
16 6106 Revision D
Figure
5.
AVR System with 0.14X Telecentric Lens
3.4.6 Lighting Control
The AVR systems include LED-based lighting control. Light is emitted by ultra-bright LEDs
mounted directly in the ring light, quad ring light, coaxial light, and collimated sub-stage light.
The output of each light source is controlled through and LED controller and the M3 software.
The following information provides additional detail the light source options.
Ring Light
Both zoom and telecentric lenses can include a ring light. The ring light illuminates objects
from the top with even illumination from all sides. The following figure illustrates the ring light.
Figure
6.
Ring Light
Quad Ring Light
The quad ring light enhances the capabilities of the ring light. The quad ring light provides a
total of 96 ultra-bright LEDs in four quadrants. Light intensity for each quadrant can be
adjusted using the M3 software. The height of the quad ring light is also adjustable. In
combination, adjustments of height, direction and light intensity provide very flexible
illumination for edge detection. The following figure illustrates the quad ring light.

AVR200 and AVR300 User Guide
17 6106 Revision D
.
Figure
7.
Quad Right Light
3.4.7 Touch Probe Option
AVR systems are available with an optional touch probe that is fully integrated into the M3
software. The touch probe is ideal to measure the height of flat surfaces or the lateral
position of vertical surfaces at different heights as well as 30 features such as cylinders,
spheres, and cones. The following figure illustrates the touch probe with the ring light and
quad ring light options.
The touch probe kit consists of the following components:
•
Renishaw PH6 probe head
•
TP20 probe body
•
Standard force (SF) probe module
•
TP20 medium force (MF) probe module
•
20 mm long stylus with 2 mm ruby tip
Note: Additional styluses are available from SKE.
Figure
8.
Touch Probe Option

AVR200 and AVR300 User Guide
18 6106 Revision D
3.4.8 Rotary Stage Options
AVR systems include the APT60 rotary stage options. The 60 millimeter rotary fixture
includes the encoder, M3 interface kit, motion amplifier, collet set and right-angle mounting
fixture. The rotary stage includes options for a 25 millimeter or 40 millimeter collet set.
The rotary stage provides the following capabilities:
•
Compatible with MetLogix M3 software
•
Great for positioning small cylindrical parts (shafts, cutting tools, threaded parts)
•
Operates at a maximum speed 10 rpm
•
Includes an axial load rating of 6.0 kilograms (Kg) and a radial load rating of 0.5 Newton
meters (Nm)
•
Includes a 2.25-inch diameter circular face
•
Provides encoder resolution to 0.001 degrees
•
Provides rotational accuracy of ±5 arc minutes
•
Includes options for a 25 millimeter or 40 millimeter collet set:
•
The 25 millimeter collet set holds parts up to 5/8 inches in diameter
•
The 40 millimeter collet set holds parts up to one inch in diameter
•
Includes a 90-degree mounting bracket
The following figure illustrates the rotary stage with the collet set. For detailed specifications
on the rotary stage, refer to “System Specifications” later in this document.
Figure
9.
Rotary Stage Option

AVR200 and AVR300 User Guide
19 6106 Revision D
3.4.9 Operator Controls and Interfaces
The following information provides the controls and interfaces of the AVR systems.
System PC
The AVR systems includes a small form factor PC where the M3 software is preinstalled and
controlled.
Touch-screen monitor
The 24-inch touch screen monitor is used to control the M3 software. The monitor displays a
live video image of the part in addition to software measurement tools and digital readings.
The image of the part can be resized using pan and zoom, and measurements can be taken
by simply tapping a feature on the screen.
Wireless keyboard and mouse
The wireless keyboard and mouse are used to input data to the system PC.
Joystick
The joystick provides position control of the stage in the X, Y, and Z axes. The joystick
includes functionality to stop the system, switch between axis movement, and control speed.
The joystick can be used to operate the system manually for quick individual measurements
and short runs.
For detailed information on operating the joystick, refer to “System Operations” later in this
document.
3.4.10 Workstation
The AVR systems include the option for an ergonomic workstation and workstation extension.
The following figure illustrates the workstation. Refer to “System Specifications” later in this
document for detailed information.
Figure
10.
AVR Workstation Option

AVR200 and AVR300 User Guide
20 6106 Revision D
This manual suits for next models
1
Table of contents
Popular Control System manuals by other brands
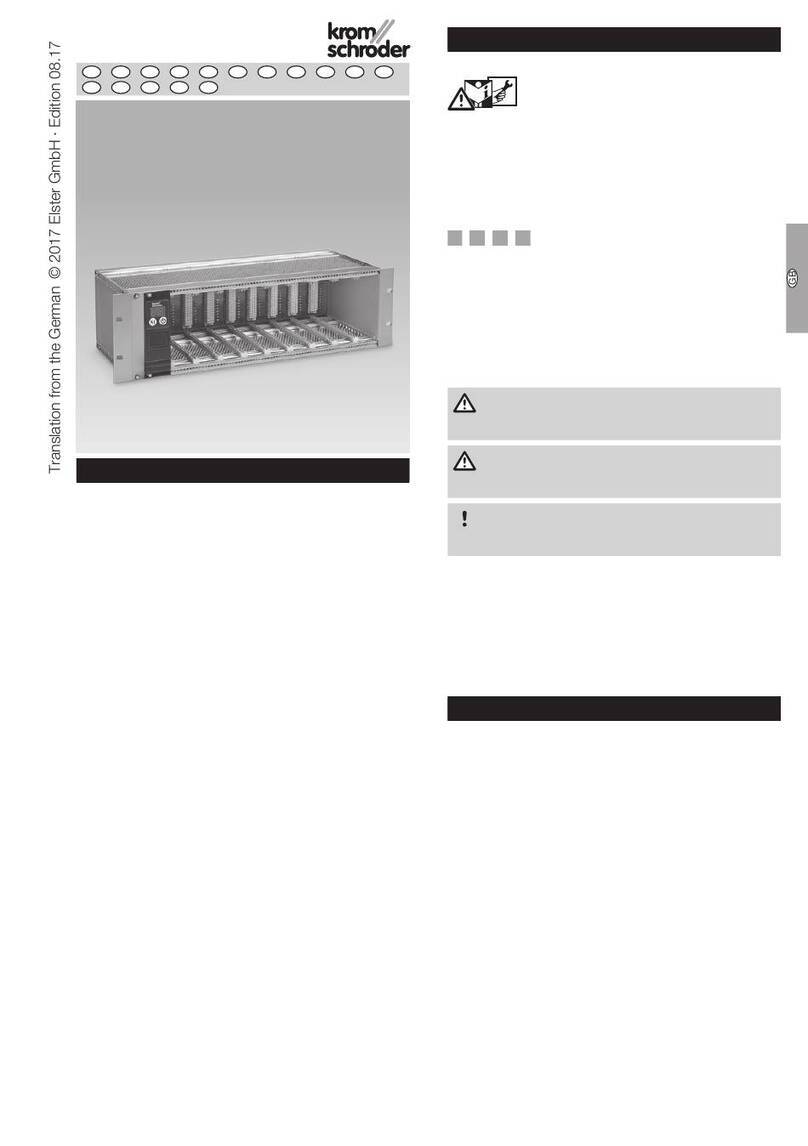
Krom Schroder
Krom Schroder PFA 710 operating instructions

Topline
Topline TEC750A manual

UV-technik
UV-technik UVT 16 Operation manual
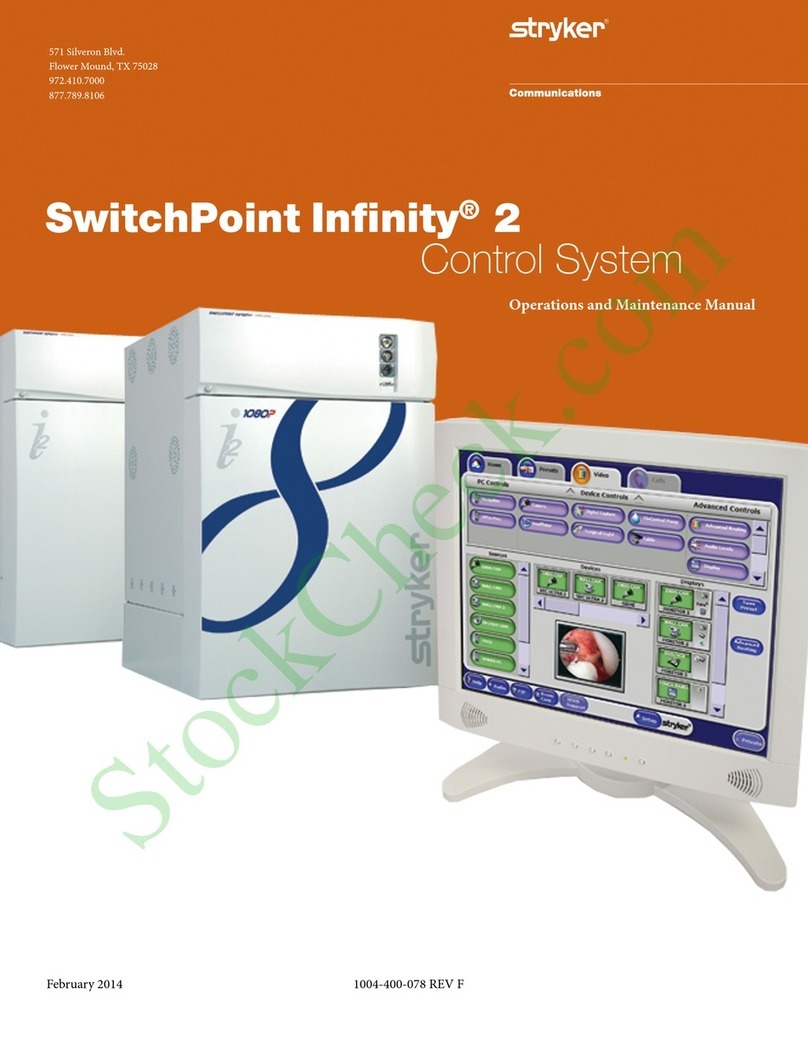
Stryker
Stryker SwitchPoint Infinity 2 Operation and maintenance manual
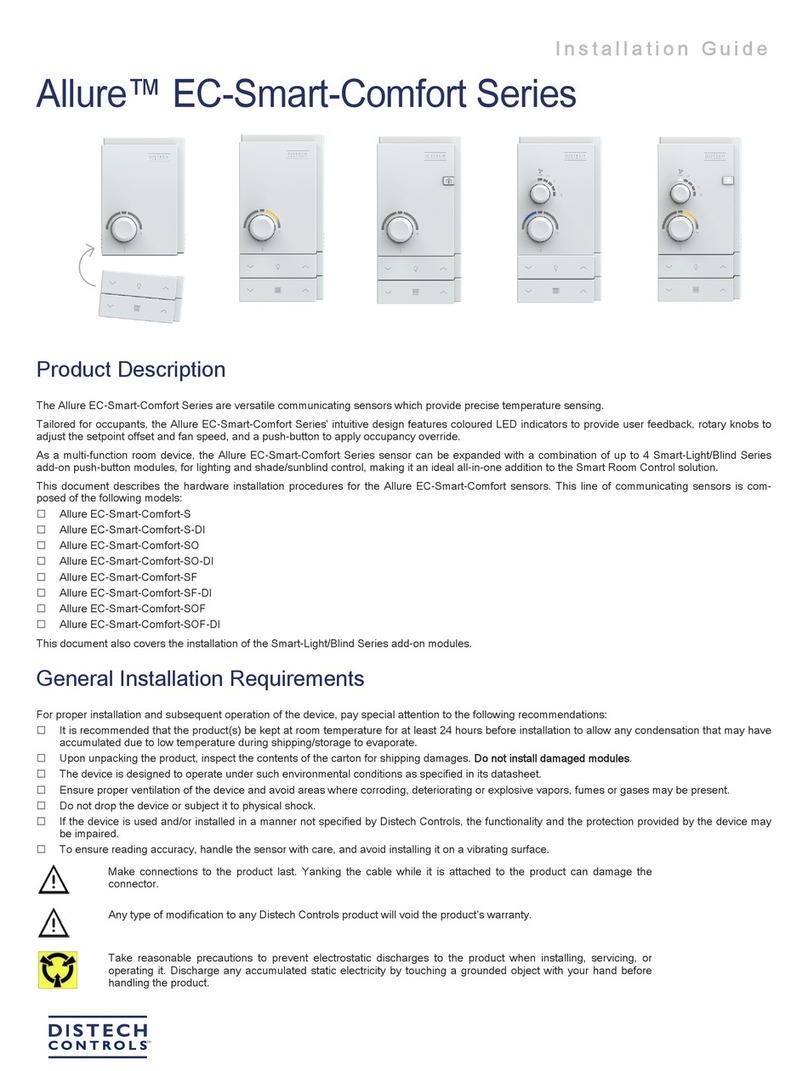
Distech Controls
Distech Controls Allure EC-Smart-Comfort Series installation guide
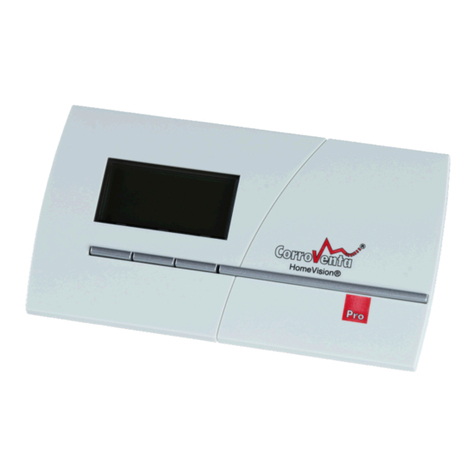
CorroVenta
CorroVenta HomeVision Pro user manual