Sun Yeh Electrical S Series User manual

Spring Return Fail-safe Electric Valve Actuator【S Series】Sun Yeh Ele. Ind. Co., Ltd. | 2021.06
S Series
Spring Return Fail-safe
Electric Valve Actuator
Operation Manual
SY02-C001F-EN

Spring Return Fail-safe Electric Valve Actuator【S Series】Sun Yeh Ele. Ind. Co., Ltd. | 2021.06
Contents
Contents.....................................................................................................................................................2
1. General Information.............................................................................................................................1
1.1 Safety Instructions.....................................................................................................................1
1.2 Installation Notices....................................................................................................................1
1.3 Inspection, Storage, Transport...................................................................................................2
2. Product Overview.................................................................................................................................3
2.1 Features......................................................................................................................................3
3. Product Mechanical Data.....................................................................................................................3
3.1 Parts Identification.....................................................................................................................3
3.2 Technical Information................................................................................................................4
3.3 Mounting Base Details ..............................................................................................................4
3.4 Sizing.........................................................................................................................................5
3.5 Duty Cycle –IEC.......................................................................................................................5
4. Mounting and Setup .............................................................................................................................7
4.1 Manual Device Installation........................................................................................................7
4.2 Valve Mounting Instructions......................................................................................................8
4.3 Wiring Instructions ....................................................................................................................9
4.4 Actuator Set-up........................................................................................................................10
5. On-off Control and Floating Control Board Adjustment ...................................................................17
5.1 On-off Control Board Surface .................................................................................................17
5.2 Troubleshooting of On-off Controller .....................................................................................18
5.3 Floating Control Board Surface...............................................................................................19
5.4 Troubleshooting of Floating Controller...................................................................................20
6. Modulating Control Board Adjustment..............................................................................................22
6.1 Modulating Control Board Surface .........................................................................................22
6.2 Programming ...........................................................................................................................22
6.3 Dip Switch Setting (SW1).......................................................................................................23
6.4 P4 Terminal..............................................................................................................................25
6.5 Sensitivity Switch Setting (SW2)............................................................................................26
6.6 Signal Settings for OPEN and CLOSE Position......................................................................27
6.7 Troubleshooting of modulating controller...............................................................................28
7. Troubleshooting..................................................................................................................................30
8. Actuator Options ................................................................................................................................32
9. Warranty.............................................................................................................................................33
10.Disposal..............................................................................................................................................33

Spring Return Fail-safe Electric Valve Actuators【S Series】Sun Yeh Ele. Ind. Co., Ltd. | 2021.06
1
1. General Information
Failure to follow safety instructions may cause serious injury, equipment damage, or
voided warranty.
1.1 Safety Instructions
Installation, maintenance and repair works must be performed by trained personnel.
The handling shall follow the safety and warning instruction contained in this manual.
The user should read and follow instructions contained in this operation manual included
with the product. Failure to do this may result in damages and void warranty. Sun Yeh will
not be liable for damages caused by operator negligence or misuse.
Local health and safety legislation shall be complied with.
In a few cases, the surface temperature may exceed 60 °C (140 °F). Please check the
surface temperature before operation, using an appropriate thermometer and wearing
protective gloves before operation.
1.2 Installation Notices
Operating by handwheel:
Do not use any tools to increase force on handwheel for operating as this can
damage the actuator or valve.
The standard spring return actuator rotates counter-clockwise with power (spring
compressed) and rotates clockwise with spring released (fully-closed or fully-open) when
power outage.
Please read operation manual and wiring diagram carefully before installation.
Verify that supply voltage is in accordance with the data on nameplate to prevent short
circuit or electrical/electronic parts damage caused by incorrect power input.
Turn power off before wiring or maintenance.
Connect the ground wire to PE point inside the electric actuator.
To avoid functional failure caused by static, do not touch any components on the PCBA
with metal tools or bare hands.
Do not parallel wire multiple actuators together without using an extra relay.
Use proper techniques when installing conduit and properly seal the connection. Do not
mount the actuator with conduit entries in upright position to prevent condensation from
entering the unit.
After manual operation, the actuator shall be returned to its spring released position by
handwheel before electrical operation of the actuator.

Spring Return Fail-safe Electric Valve Actuator【S Series】Sun Yeh Ele. Ind. Co., Ltd. | 2021.06
2
Actuator should be installed in an upright or horizontal position. Do not mount upside
down or below a horizontal position.
These units are not designed to operate in vacuum spaces or where an explosive
atmosphere exists.
Periodically inspect actuator enclosure to prevent dust from accumulating
1.3 Inspection, Storage, Transport
1.3.1 Receiving / Inspection
Carefully inspect the package for any damages resulting from shipping and
report all damages to the freight carrier and seller.
After unpacking the product and information packet, please keep the cartons
and any packing materials in case of product return or replacement. Verify that
the items listed in packing slip or in bill of lading are the same as what were
ordered. If there is any discrepancy, please contact the seller.
Verify that the technical data on nameplate is in accordance with what was
ordered.
1.3.2 Storage
The actuator should be stored in a dry area with relative humidity of less than
90 % (20 ± 5 °C) and at temperatures between - 20 °C to + 40 °C (- 4 °F to +
104 °F).
The product shall be stored with suitable protection from corrosive substance
that can damage the metal and insulating parts.
The red conduit plug for temporary protection should not be removed until the
actuator is ready to be cabled. Use suitable cable glands to ensure IP rated
protection when installing.
1.3.3 Transport
Attach ropes or hooks for the purpose of lifting by hoist only to housing and not
to handwheel.
Actuators packaged in cartons can stand up to land, sea, or air transportation.
Packaged actuators shall avoid of violent impact and strong vibrations and be
protected from rain or snow.
1.3.4 Lubrication
The gear train has been sufficiently lubricated at the factory. No additional
lubrication is required.

Spring Return Fail-safe Electric Valve Actuator【S Series】Sun Yeh Ele. Ind. Co., Ltd. | 2021.06
3
2. Product Overview
S series spring return fail-safe electric actuators offer torque ranges from 50 Nm to 360 Nm
(445 inlb to 3185 inlb) and are designed for fail-safe positioning of valves or dampers upon loss of
supply voltage, which include On/Off control, floating control and modulating control. A rack and
pinion spring mechanism is used to position the controlled device to either fully OPEN or fully
CLOSED position without any external power source. For On/Off type, a mechanical BUFFER is
used at the end of the spring stroke to reduce the hammer-blow effects in pipes. A clutch-less manual
override is optional to provide manual positioning of the controlled device.
2.1 Features
Controls: On/Off, floating (optional), modulating (optional).
Clutch-less manual override (optional).
Dry-powder coated aluminum alloy enclosure conforms to C3, NEMA 4X, 5 & IP 68
outdoor use.
ISO 5211 mounting flange.
Domed position indicator.
Built-in motor thermal protection.
3. Product Mechanical Data
3.1 Parts Identification
Top Cover Screw
Nameplate
Warning Nameplate
Conduit Entries
Manual Override Gearbox
(Optional)
Actuator Top Cover
Position Indicator
Spring Side Cover
Handwheel
Position Indicator for Manual Override

Spring Return Fail-safe Electric Valve Actuator【S Series】Sun Yeh Ele. Ind. Co., Ltd. | 2021.06
4
3.2 Technical Information
3.3 Mounting Base Details
Model
Torque
Motor Power
Weight
Standard
w / Manual Override
Nm
inlb
Watt
kg
lb
kg
lb
S-500
50
445
50
27
59
37
81
S-1300
130
1150
130
57.5
127
74.5
164
S-2000
200
1770
130
95
209
135
297
S-2600
260
2300
130
95
209
135
297
S-3600
360
3185
130
108
238
156
344
Model
Mounting Flange
Shaft (A)
Depth of Shaft (B)
ISO 5211
mm
inch
mm
inch
S-500
F07
17
0.669
30
1.181
S-1300
F10
22
0.866
41
1.614
S-2000
F12
27
1.063
45
1.772
S-2600
F12
27
1.063
45
1.772
S-3600
F12
36
1.417
46
1.811

Spring Return Fail-safe Electric Valve Actuator【S Series】Sun Yeh Ele. Ind. Co., Ltd. | 2021.06
5
3.4 Sizing
For safety reasons, do not remove or inspect the SPRING STRUCTURE. Proper tools
must be used, or serious injury will occur.
The actuator shall be sized to ensure that its torque output meets the load
requirements of valve. (As a MINIMUM, a 30% safety factor is suggested
for the calculation of torque requirement).
If the maximum torque of 5”valve is 80Nm 80× 1.3 = 104Nm
104 Nm < 130 Nm (S-1300) OK!
104 Nm > 50 Nm (S-500) Not OK!
3.5 Duty Cycle –IEC
The duty cycle is the relationship between the running time and resting time. It is
calculated as below:
Duty Cycle = x 100 %
Rest Time (Sec) =
If the motor running time is 10 sec, spring return time is 5 sec, 50% duty cycle, the
rest (off) time shall be calculated as below:
Motor running time 10 sec× (1 - 50 %) / 50 % = 10, rest time is 10 sec.
Spring return time 5 sec × (1 - 50 %) / 50 % = 5, rest time is 5 sec.
One cycle consists of open-rest-close-rest.
Arest time is required after spring returned because the gear train and motor
are driven during spring release.
Running Time (Sec)
Running Time (Sec) +Rest Time (Sec)
Running Time (Sec) x ( 1 - Duty Cycle)
Duty Cycle

Spring Return Fail-safe Electric Valve Actuator【S Series】Sun Yeh Ele. Ind. Co., Ltd. | 2021.06
6
Ambient temperature and rated duty cycle :
Standard :
Optional (-40℃) :
Model
Duty Cycle
Ambient Temperature
S-500 to S-3600
50%
- 30℃to + 40℃( - 22 °F ~ + 104 °F )
30%
+ 41℃to + 65℃( 106 °F ~ + 149 °F )
Model
Duty Cycle
Ambient Temperature
S-500 to S-3600
50%
- 40℃to + 40℃( - 40 °F ~ + 104 °F )
30%
+ 41℃to + 65℃( 106 °F ~ + 149 °F )

Spring Return Fail-safe Electric Valve Actuator【S Series】Sun Yeh Ele. Ind. Co., Ltd. | 2021.06
7
4. Mounting and Setup
4.1 Manual Device Installation
a. Slide fixing screw through washers and handwheel and secure them to override shaft as
shown in the figure below.
Turn off power when installing handwheel.
b. Assembly completed as shown in the figure below.

Spring Return Fail-safe Electric Valve Actuator【S Series】Sun Yeh Ele. Ind. Co., Ltd. | 2021.06
8
4.2 Valve Mounting Instructions
a. The spring return actuator is shipped in spring return position (spring released) with the
configuration of spring clockwise and fully-closed when power outage unless specified.
Refer to section 8 to ensure actuator selected meets the application.
b. The valve or damper must be rotated to fully-closed position before mounting with
actuator if FAIL POSTION is fully-closed and vice versa.
c. Remove all of valve handle parts, for example, the handle or open/close mechanical stops
so as to not interfere with the actuator.
Do not remove packing gland or other parts necessary for operation from valve.
d. Check again that the valve and actuator are in the same position (fully-open or
fully-closed).
e. Once mounted together, either directly or with a mounting kit, ensure that they are properly
secured together and all fasteners are tightened.
f. Remove the conduit entry plug to relieve the pressure inside the actuator for the ease of the
top cover removal and gently remove the cover.
The power must be off before removing the cover.
g. Refer to section 4.3 for wiring notices and connect the wires according to the wiring
diagram labeled inside the cover of actuator.
h. Supply power to actuator.
Care must be taken at all times as there are live circuits present that may cause
electrical shock.
i. Re-calibration may be required for the end positions, refer to section 4.4 (P.10 to 16) for
further instructions.
j. Assemble the cover and secure cover screws firmly after setting.
Please ensure that the O-ring seal is in good condition prior to cover installation.

Spring Return Fail-safe Electric Valve Actuator【S Series】Sun Yeh Ele. Ind. Co., Ltd. | 2021.06
9
4.3 Wiring Instructions
Turn power off before making the electrical connection!
Connect the ground wire to PE point placed on middle metal plate inside the electric
actuator (a green screw).
Each actuator is attached with a black water-proof plug and a temporary red dust-proof
plug to conduit entries.
Use correct size of fittings so as to not damage the threads.
Verify the supply power is in accordance with the data on the nameplate to prevent a short
circuit and an electrical shock.
Do not apply power to actuator before wiring, otherwise it can cause an electrical
shock or damage components of the actuator.
Use proper sealant to seal the conduit connection after wiring procedure to prevent dust or
water from entering the actuator.
The red plastic dust-proof plug is not meant for long-term use. Replace with
suitable water-proof connector to ensure the enclosure protection rating.

Spring Return Fail-safe Electric Valve Actuator【S Series】Sun Yeh Ele. Ind. Co., Ltd. | 2021.06
10
End Stop
Or
Buffer
Hex Nut
O-ring
Protection Cover
4.4 Actuator Set-up
If the actuator is equipped with a manual override, rotate the handwheel to return
the actuator to its spring released position before the power is supplied.
Securely tighten the conduit fittings to ensure the enclosure protection rating.
The spring return actuator provides fail-safe positioning and the end stop position of
spring return is determined by either buffer or end stop (On/Off by the buffer, floating or
modulating limited by end stop). When the actuator is motorized, the end position is
determined by limit switches.
The actuator has been set and calibrated at the factory. Most of products will not require
recalibration of these settings. However these are general settings. After valve and actuator are
bolted together, apply power to drive the actuator to its fully-open (spring compressed). Then
remove power to let the rack and pinion spring mechanism drive back to its fully-closed
position. If the OPEN or CLOSE stop point are not aligned with valve or damper correctly, its
end positions must be adjusted. Please follow steps below:
For modulating unit, ensure to loosen the sector gear of potentiometer first before
adjusting the following settings.

Spring Return Fail-safe Electric Valve Actuator【S Series】Sun Yeh Ele. Ind. Co., Ltd. | 2021.06
11
4.4.1 Adjustment procedure for spring-return actuator in the fail-closed position upon loss
of supply voltage.
Adjust FULLY-CLOSED (spring released) stop point as steps below:
a. Turn power off and loosen the protection cover using a 5 mm hex key.
b. Loosen the hex nut of the buffer or end stop using a 17 mm hex wrench. Hold the
hex nut and turn the buffer or end stop using a 10 mm hex wrench to adjust end
position
c. Turn the buffer or end stop to adjust the fully-closed stop point.
S-500 : One turn = 2.3 degrees
S-1300 to S-3600 : One turn = 1.4 degrees
d. Once completed, tighten the hex nut, replace the protection cover and tighten all
screws.
If the buffer or end stop is adjusted, TC2 must be reset in accordance with
the buffer or the end stop.
e. Loosen the M3 cap screw of cam TC2 with a 2.5 mm hex key.
f. Rotate the cam TC2 counter-clockwise until a light click is heard, and then slowly
rotate the cam TC2clockwise until a light click is heard, so that LS2 is not triggered.
g. Tighten the cap screw of cam TC2.
Spring released 0°
Clockwise (CW)
Counter-clockwise (CCW)
Spring compressed 90°
Desired Position
Original Position
TC4
TC3
TC2
TC1
TC4
TC3
TC2
TC1

Spring Return Fail-safe Electric Valve Actuator【S Series】Sun Yeh Ele. Ind. Co., Ltd. | 2021.06
12
Adjust FULLY-OPEN (spring compressed) stop point as steps below:
a. Apply power to drive the actuator to its fully-open (spring compressed) position. If
the open stop point is not aligned with the valve or damper properly, then it must be
adjusted.
b. Remove power to let spring system to drive back to its fully-closed (spring released)
position.
c. If it is required to adjust, loosen the cap screw of cam TC1 with a 2.5 mm hex key.
To increase the opening angle, turn the cam clockwise.
To decrease the opening angle, turn the cam counter-clockwise.
【S-500】【S-1300 to S-3600】
d. After adjusting the cam, apply power to drive the actuator to the fully-open position.
e. Verify that it is in the correct fully-open position.
If it is in correct position, remove power and lock the cap screw of cam TC1.
If it is not in correct position, repeat step C until the correct position is reached.
f. If auxiliary switches will be used for feedback, cams TC3 and TC4 need to be
calibrated.
Adjust cam TC3 so it trips just before cam TC1 does.
Adjust cam TC4 so it trips just before cam TC2 does.
增加角度
Decrease the
opening angle
Increase the opening
angle
Decrease the
opening angle
Increase the opening
angle

Spring Return Fail-safe Electric Valve Actuator【S Series】Sun Yeh Ele. Ind. Co., Ltd. | 2021.06
13
4.4.2 Adjustment procedure for spring-return actuator in the fail-open position upon loss
of supply voltage.
Adjust FULLY-OPEN (spring released) stop point as steps below:
a. Turn power off and loosen the protection cover using a 5 mm hex key..
b. Loosen the hex nut of the buffer or end stop using a 17 mm hex wrench. Hold the
hex nut and turn the buffer or end stop using a 10 mm hex wrench to adjust end
position.
c. Turn the buffer or end stop to adjust the fully-open stop point.
S-500 : One turn = 2.3 degrees
S-1300 to S-3600 : One turn = 1.4 degrees
d. Once completed, tighten the hex nut, replace the protection cover and tighten all
screws.
If the buffer or end stop is adjusted, TC2 must be reset in accordance with
the buffer or the end stop.
e. Loosen the M3 cap screw of cam TC2 with a 2.5 mm hex key.
f. Rotate the cam TC2 counter-clockwise until a light click is heard, and then slowly
rotate the cam TC2clockwise until a light click is heard, so that LS2 is not triggered.
g. Tighten the cap screw of cam TC2.
Spring released 90°
Clockwise (CW)
Counter-clockwise (CCW)
Spring compressed 0°
Desired Position
Original Position
TC4
TC3
TC2
TC1
TC4
TC3
TC2
TC1

Spring Return Fail-safe Electric Valve Actuator【S Series】Sun Yeh Ele. Ind. Co., Ltd. | 2021.06
14
Adjust FULLY-CLOSED (spring compressed) stop point as steps below:
a. Apply power to drive the actuator to its fully-closed (spring compressed) position. If
the close stop point is not aligned with the valve or damper properly, then it must be
adjusted.
b. Remove power to let spring system to drive back to its fully-open (spring released)
position.
c. If it is required to adjust, loosen the cap screw of cam TC1 with a 2.5 mm hex key.
To increase the opening angle, turn the cam clockwise.
To decrease the opening angle, turn the cam counter-clockwise.
【S-500】【S-1300 to S-3600】
d. After adjusting the cam, apply power to drive the actuator to the fully-closed
position.
e. Verify that it is in the correct fully-closed position.
If it is in correct position, remove power and lock the cap screw of cam TC1.
If it is not in correct position, repeat step C until the correct position is reached.
f. If auxiliary switches will be used for feedback, cams TC3 and TC4 need to be
calibrated.
Adjust cam TC3 so it trips just before cam TC1 does
Adjust cam TC4 so it trips just before cam TC2 does.
增加角度
Decrease the
opening angle
Increase the opening
angle
Decrease the
opening angle
Increase the opening
angle

Spring Return Fail-safe Electric Valve Actuator【S Series】Sun Yeh Ele. Ind. Co., Ltd. | 2021.06
15
4.4.3 For modulating actuators, after completing the calibration, turn the actuator to
fully-closed or fully-open position (spring released) and follow the procedure below:
Fail clockwise (CW) rotation
a. Loosen M5 set screw.
b. Rotate sector gear clockwise to the position shown in figure below.
Ensure that round gear and sector gear are engaged properly.
c. Tighten M5 set screw.
TC2 is utilized for sensing fully-closed stop point. Once the spring mechanism has
been released when power outage, the actuator will not drive under power again until it has
reached its fail stop position and TC2 is not triggering LS2.
TC1 ”OPEN ”Clockwise: increase opening degree.
Counter-clockwise: decrease opening degree.
Note:
LS2 shall trip while TC2 reaches the end stop point.
TC3 & TC4 are optional, refer to P.12 & P.14 section 4.4.1 (f.) and 4.4.2 (f.)
for calibration.

Spring Return Fail-safe Electric Valve Actuator【S Series】Sun Yeh Ele. Ind. Co., Ltd. | 2021.06
16
Fail counter-clockwise (CCW) rotation
a. Loosen M5 set screw.
b. Rotate sector gear counter-clockwise to the position shown in figure below.
Ensure that round gear and sector gear are engaged properly.
c. Tighten M5 set screw.
TC2 is utilized for sensing fully-closed stop point. Once the spring mechanism has
been released when power outage, the actuator will not drive under power again until it has
reached its fail stop position and TC2 is not trigger LS2.
TC1 ”OPEN ”Clockwise: decrease opening degree.
Counter-clockwise: increase opening degree.
Note:
LS2 shall trip while TC2 reaches the end stop point.
TC3 & TC4 are optional, refer to P.12 & P.14 section 4.4.1 (f.) and 4.4.2 (f.)
for calibration.

Spring Return Fail-safe Electric Valve Actuator【S Series】Sun Yeh Ele. Ind. Co., Ltd. | 2021.06
17
5. On-off Control and Floating Control Board Adjustment
5.1 On-off Control Board Surface
Indicator Lamp
Lamp No.
Status
LED1
Power
LED2
Operating
LED3
Motor Brake
LED4
Alerting Signal
The layout is based on 110/220V voltage.
1
2
3
4
LED2
LED4
LED1
LED3
LS1
LS2
BRAKE

Spring Return Fail-safe Electric Valve Actuator【S Series】Sun Yeh Ele. Ind. Co., Ltd. | 2021.06
18
5.2 Troubleshooting of On-off Controller
Status of LEDs
Possible problems
Solution
LED4 goes on
a. LS1and LS2 terminals
loose or poor contact.
b. Incorrect connection of
the terminal LS1 or LS2.
c. The input power failure
time is more than 150ms.
d. Abnormal setting of limit
switches and cams.
e. Supply the power again
during spring release.
f. LS1and LS2 failed.
g. Actuator overload cause it
can not returned to spring
released position and
restart.
h. Abnormal setting of cam
TC and cause the contact
of LS2 can not be
released.
a. When the terminals loosen, please
refer to the wiring diagram for wiring.
If it is damaged, please replace new
terminals.
b. Verify the actuator is wire properly as
per wiring diagram.
c. Please provide an independent power
supply to actuator to avoid unstable
power supply and cause the actuator
enter to self-protection.
d. Please refer to 4.4 (P.10 to P.16)
Actuator set-up.
e. Power off until the actuator return to
spring released positon and then
supply power again.
f. Replace new limit switches.
g. Please refer to 3.4 (P.5) Sizing.
h. Please refer to 4.4 (P.10 to P.16)
Actuator set-up.
LED1 does not
go on
a. Wrong supply voltage.
b. Blown fuse.
c. PCB failed.
a. Check the power supply is according to
the actuator rated voltage.
b. Replace a new fuse.
c. Replace a new PCB.
LED2 does not
go on
a. Abnormal Setting for LS1
and LS2.
b. PCB failed.。
a. Check the LED 4, if the LED4 lights
please refer to the troubleshooting for
LED4.
b. Replace a new PCB.
LED3 does not
go on
a. PCB failed.
a. Replace a new PCB.
In case LED1 to LED3 does not light or LED4 lights when the actuators are
motorized, please refer to steps below for basic troubleshooting.
This manual suits for next models
5
Table of contents
Other Sun Yeh Electrical Controllers manuals
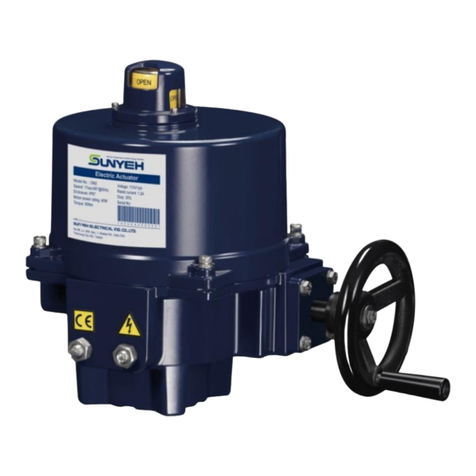
Sun Yeh Electrical
Sun Yeh Electrical OM Series User manual

Sun Yeh Electrical
Sun Yeh Electrical OME Series User manual
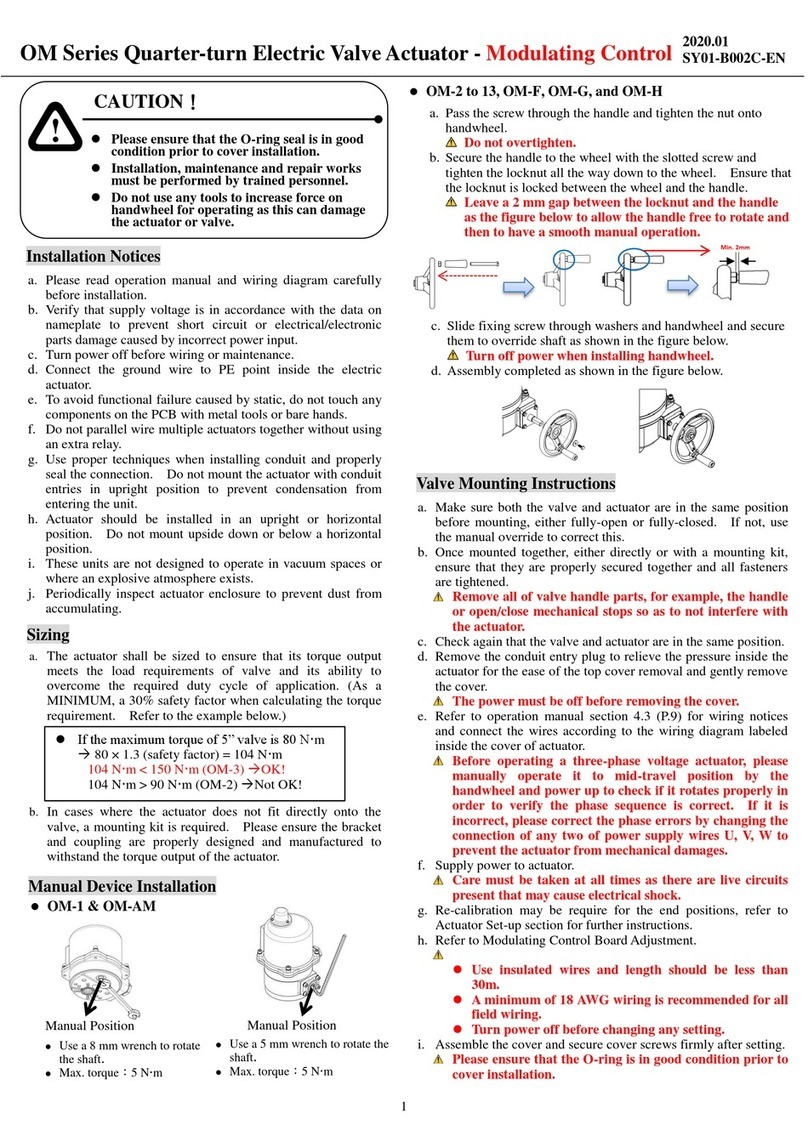
Sun Yeh Electrical
Sun Yeh Electrical OM Series User manual
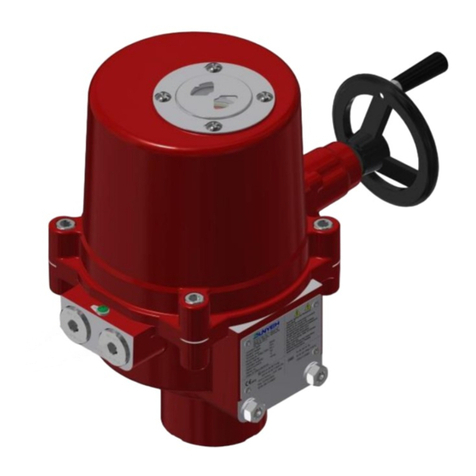
Sun Yeh Electrical
Sun Yeh Electrical OME Series User manual

Sun Yeh Electrical
Sun Yeh Electrical M Series User manual
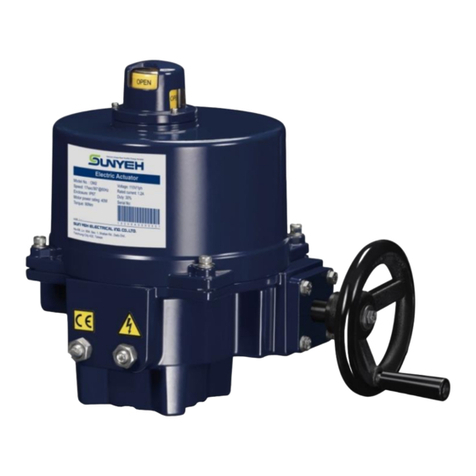
Sun Yeh Electrical
Sun Yeh Electrical OM Series User manual
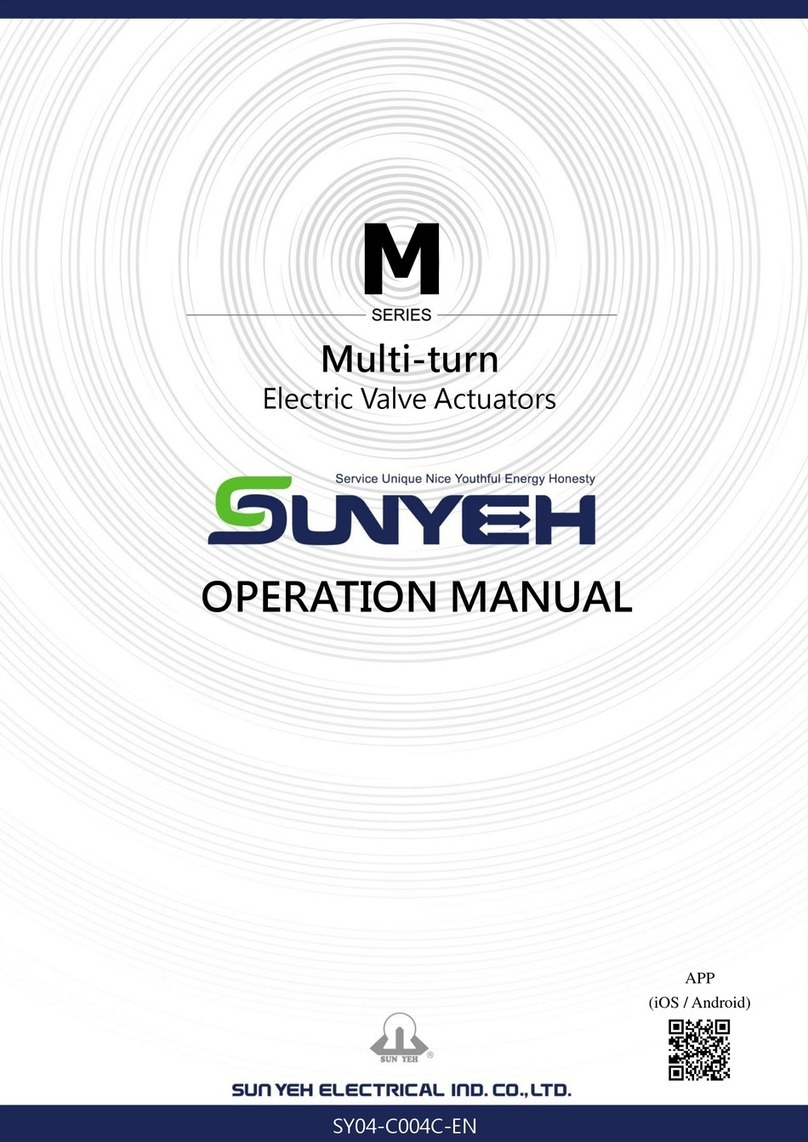
Sun Yeh Electrical
Sun Yeh Electrical M Series User manual