Solcon HRVS-DN User manual

Instruction Manual
HRVS-DN
Medium Voltage Soft Starters
2300 - 13800V, 60-1200A
September 2006

1
11
1
Safety
•Read this manual carefully before operating the
equipment and follow the instructions.
•Installation, operation and maintenance should be strictly
accordance with this manual, national codes and good
practice. Installation or operation not performed in strict
accordance with these instructions will void
manufacturer’s warranty.
•Disconnect all power inputs before servicing the soft-
starter and/or the motor.
•After installation, check and verify that no parts (bolts,
washers, etc) have fallen into the power Section (IP00).
Attention
1. This product was designed for compliance with IEC 947-4-2 for class A equipment and EN 50178.
2. For further information see Technical Specification
Warnings
•Internal components and P.C.B’s are at main potential
when the HRVS-DN is connected to main voltage. This
voltage is extremely dangerous and will cause death or
severe injury if contacted.
•When HRVS-DN is connected to the main voltage, even
if control voltage is disconnected and motors is stopped,
full voltage may appear on starter’s output and motor’s
terminals.
•Unit must be grounded to ensure correct operation, safety
and prevent damage.
•Check that Power Factor capacitors are not connected to
the output side of the soft starter and confirm that they are
connected upstream to the line contractor.
The company reserves the right to make any improvements Or modifications to its products without prior notice.

2
22
2
Table of Contents
Page Subject
3 Starter Selection
4-5 Installation
6-7 Internal Setting
8-9 Control Terminals
10 Control Terminals – Option Boards
11-12 Control Wiring
13 Wiring Diagrams
14 Wiring Diagrams Diesel Generator
15-16 Wiring Diagrams – Communication
17-18 Start & Stop Parameters
19-20 Motor And Starter Protection
21 Motor And Starter Protection Occurrence Table
22 Standard wiring Diagram
23 Front Panel
24 Display Mode
25-31 Parameter Settings
32 Start-Up Procedure
33-35 Menu Description
36-37 Trouble Shooting
38-39 Technical Specification

Starter Selection
3
33
3
The HRVS-DN is a highly sophisticated and reliable
starter designed for use with standard medium voltage
three-phase, three-wire, squirrel cage induction motors.
It provides the best method of reducing current and
torque during motor starting.
The HRVS-DN starts the motor by supplying a slowly
increasing voltage to the motor, providing soft start and
smooth acceleration, while drawing the minimum
current necessary to start the motor.
The second generation, microprocessor based digital
circuitry provides unique features like pump control,
accurate motor protection and optional analog output.
The optional RS485 Communication with MODBUS,
PROFIBUS and other (consult factory) protocols
enables full control (Start, Stop, Dual Adjust,
command, etc.) and supervision. Up to 32 starters or
other MODBUS slaves can be connected on a shield
twisted pair to a host computer.
Motor Current & Starting Conditions
Select the starter according to motor’s Full Load
Ampere (FLA) – as indicated on its nameplate (even if
the motor is not fully loaded).
The HRVS-DN is designed to operate under the
following conditions:
•Max. ambient temp: 50ºC
•Max. starting current: 400% motor’s FLA
•Max. starting time: 30 sec. (at 400% FLA)
•Max. starts per hour: 2 starts per hour at
maximum conditions.
PIV (Peak Inverse Voltage) Ratings
PIV Rating will be not less than:
System Voltage PIV Ratings
2300V 6900V
3300V 12500V
4160V 12500V
6600V 19500V
11000V 39000V
13800V 41000V
Main Voltage (line to line)
Thyristors PIV rating, internal circuitry and insulation
defines the following voltage levels:
2300V, 3300V, 4160V, 6000V, 6600V, 6900V,
11000V and 13800V.
Each starter is suitable for 50/60Hz.
Control Voltage
The Control voltage operates the electronic circuitry.
The following voltage levels are available:
•220-240V + 10%-15%, 50/60 Hz (standard)
•110-120V + 10%-15%, 50/60 Hz
•110 VDC (optional)
•Consult factory for special voltages.
Control Inputs
Control Input voltage (start, stop, etc.) can be the same
as Control Supply above (standard), or 24-240V AC /
DC (by special order).
Options (see Ordering Information Data)
•Analog card - analog output (option # 5)
•Tachometer feedback (option # T)
•Relays card:
- enable to operate via communication.
- to get an up to speed signal when starting
synchronous motors if the by pass contactor is
close or In < 115% In
•Multi start configuration
•LLOYD’S approval for marine application
•Customized cabinet arrangement.

Installation
4
44
4
Prior to Installation
Check that Motor Full Load Ampere (FLA) is lower
than or equal to the starter Full Load Current (FLC)
and that the Main and Control voltages are as
indicated on the front panel.
Mounting
•The starter must be mounted vertically.
•Do not mount the starter near heat sources.
•Protect the starter from dust and corrosive
atmospheres.
Temperature Range and Relative humidity
The starter is rated to operate within the temperature
range of -10ºC (14ºF) to + 50ºC (122ºF).
Relative humidity inside the enclosure should not
exceed 95% non-condensed.
Do not interchange line and load connections.
Short Circuit Protection
For short circuit protection use M.V. fuses.
Transient Protection
When high transients are expected, external protection
should be used (consult factory).
WARNING
Power factor correction capacitors, if required must
be installed on the line side of the HRVS-DN
Do not connect three phase voltage without starting
the HRVS-DN for more than 30 seconds.
Power Section Connections
•Line to terminals
L1, L2
and
L3
.
•By-pass to terminals
L1b, L2b
and
L3b
.
•Motor to
U, V
and
W
.
•Line and By-pass contactors must be used.
•Power Factor Capacitors, if required, should
be installed on the HRVS-DN line side (not
on the HRVS-DN Load side).
•Main supply must be applied in the correct
phase sequence.
•Bus bars and bypass contactor must be
arrange to maintain current flow through the
bypass after end of acceleration process.
Otherwise, current protection of the soft
starter will not function.
•Interlock the serial contactor - starting relay
with the “Fault relay” of the HRVS-DN.

Internal Settings
5
55
5
Input:
Directly connected
to H.V. bus bars
Control Module for HRVS-DN is identical for all ratings and suitable for mounting in L.V. Compartment
Control Module Connection
•Install the module in the L.V. compartment, which should be fully segregated from the H.V. compartment.
•Ensure that Control Module is properly grounded.
•Connect interposing relays to all HRVS-DN auxiliary contacts, three relays must be incorporated: Run, Fault
and By-pass.
•Fiber-optic technology is used to control the soft-starter’s firing signals. Six fiber optic leads are connected to
the firing boards on the Power Section and should be connected to the Fiber Optic connectors on the Control
Module.
•Follow the fiber optic installation directions carefully and accurately at the end of the commissioning process.
•The leads are marked with numbers from 1-6, insert each lead to its own receptacle.
Fiberoptics Connections
1. Release fiber-optic nut CCW ½ a turn.
2. Remove 25mm fiber-optic lead from the
insertion hole.
3. Identify the numbers for the F/O on the leads.
4. Insert Fiber-optic leads to their maximum
(about 18mm).
5. Tighten fiber-optic nut gently, CW direction, ½
a turn.
Fiberoptics Board
Front view of the fiber-optic board. Fiber-Optic board dip
- switches are located below f/o insertion connector # 5.
Electronic potential transformer (EPT)
Note:
Make sure the wires are connected according
the marked number
Transmitter
Receiver
Fiberoptics
Output:
3 x 120V
Input:
Power supply with
fused connector

Internal Settings
6
66
6
Built-in memory systems
The HRVS-DN incorporates 3 memory systems:
EPROM A read-only, non-volatile memory,
containing factory set parameters
(default) that cannot be changed.
EEPROM A read/write, non-volatile memory,
where field adjusted parameters,
statistical and fault data are saved and
stored.
RAM A read/write memory containing
parameters loaded from the
EEPROM which can be changed
from the keypad. These parameters
are stored only as long as Control
Supply is connected.
Memory system operation
1. When Control Supply is switched on, the
RAM is automatically loaded from the
EEPROM and parameters are displayed on the
LCD.
2. Parameters can now be modified from the
keypad (if starter is in one of the operating
modes and software lock is open – Dip Switch
8 open).
3. Start parameters can be modified during
starting
process and will immediately affect the
operation. Example: if Current Limit is set too
low and motor does not accelerate to full
speed, increasing the Current Limit setting will
immediately affect the start process. This
enables selection of the optimal starting
characteristics.
4. After completion of the adjustments,
parameters should be stored in the EEPROM.
Storing of new parameters is possible at the
end of each Mode Page by pressing Store key
after “Store Enable” is displayed on the LCD.
Test Modes:
Three modes of test are available:
1. Test condition where the soft starter is tested
for correct logical operation without Medium
Voltage connected to it.
2. Firing test requires only control voltage
without main voltage.
Plug to
Power Unit
Control
Transformer
Power Supply
Board
Six Fiber-Optic
Space for
Analogue Board
Dip Switch
Main Board
Communication
Board
Program version
Current Gain
Dip Switche
s
Micro
Controller
End Of Acc. Relay
Fault Relay
Immediate Relay
Firing Relay

Internal Settings
7
77
7
3. Test condition with test harness and four pairs
of dip - switches allowing a 400V motor test.
Dip Switch settings (PC2050)
The Dip Switch module
contains eight separate switches
and located under the front
cover of the Control Module.
Dip Switch
Off
1 2 3 45 6 7 8
When necessary, carefully open the front panel and set
the switches as required.
Note: All switches are factory pre-set in OFF position.
No Switch Function Switch Off Switch On
1 Display Format Minimized Maximized
2 Tacho feedback Disabled Enabled
3 Main / Generator Main Generator
4 Must be Off
5-6 LCD-language
selection See table
7
Special settings –
keep in Off
position
Disabled Enabled
8 Software lock Open Locked
Switch # 1 – Display Modes
For operation convenience there are two display
modes:
Maximized – Display of all possible parameters.
Minimized – Display of pre-selected parameters.
Setting Dip Switch # 1 to Off will minimize the LCD
displays.
Maximized mode
Switch 1 – On
Display only
Main parameters
Start parameters
Stop parameters
Dual adjustment
Fault parameters
I/O programming
Communication parameters
Statistical data
Minimized mode
Switch 1 – Off
Display only
Main parameters
Start parameters
Stop parameters
Statistical data
Switch # 2 – Tacho feedback (Optional)
Set Dip Switch. # 2 to On, when using Incremental
Shaft Encoder or tacho feedback.
Note: To operate tacho feedback – consult factory for
specific settings for each application.
Switch # 3 – Main / Generator control
When starting from a diesel – generator supply,
starting process can sometimes terminate due to
instability of the supply system. To operate generator
mode set Dip Switch # 3 to On and special starting
characteristics, suitable for Diesel Generator supply –
with unstable voltage & frequency become operative.
Closure of Dual Adjustment contact (terminal 8)
operates the special starting characteristics.
When operating from network voltage and alternatively
from diesel generator, set normal starting
characteristics for Main and suitable parameters for the
Diesel Generator (for example, faster acceleration,
lower current limiting, etc.) on Dual Adjustment
setting.
WARNING
When operating in Generator Mode, or with curve
“0” motor must be loaded, otherwise, vibration may
occur during starting and stopping.
Switches # 5, 6 – Language Selection
Language Switch 5 Switch 6
English Off Off
French Off On
German On Off
Spanish On On
Switch # 7 – Special settings – consult factory
WARNING
When using extended Soft-
Starter range, apply
maximum precautio
ns to avoid motor or starter
damage.
Switch # 8 – Software Lock
The software lock prevents undesired parameter
modification.
To verify that parameters are locked, press Store and
or
keys and the LCD displays, “Unauthorized
Access”.

Control Terminals
8
88
8
Control Supply ......................................Terminals 1-3
110-120V or 220-240V, 50/60Hz as indicated on the
front panel is required to power the electronic circuitry.
This voltage can be supply from a grounded or
ungrounded main system. It can be supply by special
order for 110VDC.
Note: It is recommended that terminals 1-3 be
continuously connected to the Control Supply.
Firing Supply Outut .................................. Terminal 2
Output of control voltage (from terminal 1) to energize
the firing transformer. Operates during soft start and
soft stop of the soft starter.
Control Inputs
Incorporating opto - couplers to isolate the micro -
processor circuitry can be the same voltage as Control
Supply above, 110-120 or 220-240V, 50/60Hz.
By special order it can be supply for 24-110VDC.
Note: The HRVS-DN is supplied as standard with the
same voltage for Control Supply & Control
Inputs.
Stop............................................................. Terminal 4
Input from a N.C contact. To stop the motor,
disconnect control voltage from Terminal 4 for at least
250mSec.
Soft stop...................................................... Terminal 5
Input from a N.C contact. To soft stop the motor,
disconnect control voltage from Terminal 5 for at least
250mSecs.
Note: If Soft-Stop is not required, connect a jumper
between terminals 4 and 5.
Start ............................................................ Terminal 6
Input from a N.O contact. To start the motor, connect
control voltage to Terminal 6 for at least 500 mSecs.
Notes:
1. Motor will start only if Stop (4) and Soft Stop
(5) terminals are connected to control voltage.
2. Reset after a fault is not possible for as long as
Start command is present.
3. HRVS-DN ignores start within 3 sec after
stop. Wait at least 3 sec before restarting.
Test / Reset………………………….Terminal 7
Input from a N.O contact. Selection between above
functions is made from the keypad or through the
communication.
a. Test is designed to enable thyristors firing test
without mains. When connected through a
N.O. contact, closing the contact operates
Test.
b. When Reset function is selected, connect
terminal 7 momentarily to control voltage (use
a N.O momentary contact) to reset the starter.
Dual Adjust / Reset .................................... Terminal 8
Input from a N.O contact. Selection between above
functions is made from the keypad or through the
communication (see I/O Programming).
a. Dual Adjustment function is selected by
connecting terminal 8 to control voltage to
operate starter with the Dual Adjustment
characteristic.
Switching between Primary and Dual Adjustment
settings can be done before and during starting. If
a push-button arrangement is used, keep control
voltage connected at least until RUN LED is lit.
Note: When starting from a “small” Diesel Generator
or weak power supply set dip switch # 3 to on
and connect terminal 8 to control voltage to
operate starter with Generator Parameter
settings.
c. When “Reset” function is selected, connect
terminal 8 momentarily to control voltage (use
a N.O momentary contact) to reset the starter.
Common A ................................................. Terminal 9
Common for terminals 4, 5, 6, 7, 8.
Note: When control supply voltage and control input
voltages are from the same source, connect a
jumper between terminals 3 and 9.
1-3 4-9 10-21 22-24
I/O Terminals

Control Terminals
9
99
9
Immediate/Shear-pin Relay.........Terminals 10-11-12
Terminals: 10-N.O. 11-N.C. 12 - Common.
Voltage free 8A, 250VAC max.
Selection between functions is made from the keypad or
through the communication, (see I/O Programming),
Programmable functions:
1. Immediate (after start signal)
2. O/C Shear-pin detection.
1. When Immediate is selected, the contact
changes its position upon start signal. The
contact returns to its original position upon Stop
signal and in case of a fault or control supply
outage.
When Soft Stop is operated, the contact returns to
the original position at the end of the Soft Stop
process.
The contact incorporates On & Off delays within
0 – 60 sec each.
The Immediate Contact can be used to:
•Interlocking with other systems.
•Signaling.
•Delay for opening an upstream contactor at the
end of soft stop thus to allow current decrease
to zero before opening the contactor.
•Switch to / from Dual Adjustment settings with
a time delay from Start signal (see Special
Starting).
2. When O/C Shear-pin is selected, the contact
changes position upon detection of Jam
condition (Starter trip can be delayed within 0-5
sec.)
The O/C Shear-Pin contact can be used to:
•Interlocking with other systems.
•Signaling
•Delay for operating a reversing combination of
contactors when Jam is detected to allow a
clearing of a Jam condition.
Fault Contact................................Terminals 13-14-15
Terminals: 13-N.O. 14-N.C. 15 - Common
Voltage free 8A, 250VAC, 2000VA max. changes its
position on fault. The contact is programmable to
function as Trip or Trip fail safe relay.
a. When Trip function is selected - the relay is
energized upon fault. The contact returns to its
original position after fault has been removed
and starter was reset or upon disconnection of
Control Supply.
b. When Trip-fail safe function is selected - the
relay is energized immediately when Control
Supply is connected and de-energizes upon fault
or control Supply disconnection.
End of Acceleration Contact....... Terminals 16-17-18
Terminals: 16 - N.O. 17 - N.C. 18 - Common
Voltage free 8A, 250VAC, 2000VA max. changes its
position at the end of acceleration with an adjustable
time delay (Contact Delay) of 0 – 120 sec.
The contact returns to its original position on Soft Stop
or Stop signals on fault condition or voltage outage.
The End Of Acceleration contact must be used to close a
by-pass contactor through a pilot (interposing) relay and
can be use to:
•Activate a valve after compressor has reached
full speed.
•Signal, allowing for the loading of a conveyor
after motor reached full speed, etc.
External Fault 1 ...................................... Terminal 19
Input from a N.O contact connected between terminals
19 and 21. The starter will trip 2 seconds after contact
closes.
External Fault 2 ...................................... Terminal 20
Input from a N.O contact connected between terminals
20 and 21. The starter will trip 2 seconds after contact
closes.
Common B................................................ Terminal 21
Common for terminals 19, 20
Notes:
1. When Control Supply voltage and Control Input
voltage are from the same source, connect a
jumper between terminals 3, 9 and 21.
2. If External inputs are not used, leave terminals
19, 20 and 21 open.

Control Terminals – Option Boards
10
1010
10
RS-485 Communication ....................Terminals 23-24
Terminals: 23 (-), 24 (+) and terminal 22 (GND).
Optional RS485, half duplex with MODBUS
protocol, baud rate 1200, 2400, 4800, 9600 BPS.
Twisted shielded pair should be used and shield
connects to ground on the PLC/Computer side.
Terminals 4 & 5 must be wired to control supply
voltage for operation in communication mode (see
Communication Wiring Diagrams).
Profibus
9 pin D-sub connector is available for Profibus.
Analog I/O (option # 5) ....................Terminals 28-32
Terminals 28-29 leave open
Terminal 30 – Ground (leave oopen)
Terminal 31 – Analog output (-)
Terminal 32 – Analog output (+)
The Analog card output incorporates
two functions (Voltage & Current
outputs).
Dip switches allow selection
between:
0-10VDC, 0-20 mA and 4-20 mA
The Analog value is related to the
motor current and can be
programmed to normal or inverted
output. (Default = Normal)
Maximum value (20mA or 10Vdc) is
related to 2 x In.
Dip. Sw. S1
Off
Dip. Sw. S2
Off
Out
(+) (-)
Gnd
32 31 30
29
28
Dip switch No. 4-20 mA* 0-20 mA 0-10VDC
Dip-Switch S1
# 1 On On Off
Dip-Switch S1
# 2 On On Off
Dip-Switch S1
# 3 Off Off On
Dip-Switch S1
# 4 Off Off On
Dip-Switch S2
# 1 On Off Off
Dip-Switch S2
# 2 No use No use No use
* Default
Relays board
The board includes two relays that enable:
1) Operation and control of starter cabinet via
communication.
2) Up to speed relay, which energizes when By Pass
contactor is closed and current reduced below 115% of
FLA. The relay remains latched until motor stopped.
Tacho board
This option is suitable to use with incremental shaft
encoder. Consult factory

Control Wiring
11
1111
11
1
2
3
4
5
6
7
8
9
10
11
12
13
14
15
16
17
18
19
20
21
22
23
24
30
31
32
Fault
Relay
Immediate
/
O
.
C shear
pin Relay
End Of Acceleration
Relay
Stop
Soft Stop
Start
Input #1
-
Test/ Reset
Input #2
-
D. Adjust/ Reset
Common A (of 4..8)
Input #3
-
Ext. Fault 1
Input #4
-
Ext. Fault 2
Common B (of 19..20)
Leave Open
(-) RS 485
(+)
RS
485
Leave Open
(-) Analogue
Outp
ut
(+)
Analogue
Output
N
-
control supply
Firing Supply output
Control supply
Analogue card
Note: One of the cards can be installed.
Relays Board
Notes:
1. Standard control and input voltage are 115 or
230VAC.
DC Supply sources available by special order.
See ordering information and consult our
factory.
2. If External faults are not used leave terminals
19, 20, 21 open.
A 10A fuse must protect control Supply.
It is recommended to use a separate fuse for the
auxiliary circuits.
1
2
3
4
5
6
7
8
9
21
Control Supply and Control
Inputs from the same source.
1
2
3
4
5
6
7
8
9
21
Separate sources for Control
Supply and Control Inputs. If
terminal 19 and 20 are not used,
leave Terminal 21 (Common B)
open.
1
2
3
4
5
6
7
8
9
21
19
20
Three separate sources for:
1. Control Supply
2. Control Inputs
terminals 4-9
3. Control Inputs
terminals 19-21
41
40
42
Insulation
test
Leak
Optional
}
}
Optional
31
32
33
34
35
Comm. Start/ Stop
“Up to speed” relay
Optional
}

Control Wiring
12
1212
12
1. Motor will soft start when
C closes and stop
immediately when C
opens.
1
2
3
4
5
6
7
8
9
L
1
NC
2. Motors will soft start
and soft stop with C.
1
2
3
4
5
6
7
8
9
L
1
N
C
3. Motors will soft start
and soft stop with C.
C
1
act as emergency
stop.
1
2
3
4
5
6
7
8
9
L
1
N
C
C
1

Wiring Diagrams
13
1313
13
1
2
3
4
5
6
7
8
9
10
11
12
13
14
15
16
17
18
19
20
21
N
22
23
24
28
29
30
31
32
M
U
V
W
L1
b
L2
b
L3
b
L1
L2
L3
Start
Stop
C
1
Line
Contactor
Bypass
Contactor
Interposing Relays
To Line
Contactor
Control Circuitry
To By-Pass Contactor
Control Circuitry
Series contactor
•A Line contactor and by-pass contactor must be used
•To incorporate soft stop, use Run contact off delay to “Hold” the Line Contactor.
This system is used mainly when the HRVS-DN is retrofitted into an existing system, thus, reducing modifications in
existing installations. Main power and Start signal are switched on upon closure of the series contactor. The starter will
operate as long as the series contactor is closed.
Notes:
1. It is recommended that terminals 1-3 shall be always connected to Control Supply.
2. Upstream contactor must be opened immediately after soft stopping. The upstream contactor can be
interlocked via the Immediate Contact that changes its position only at the end of soft stop. It is therefore
recommended to delay the opening of the upstream contactor for a few seconds after the completion of soft
stop process (after current reached zero). See Immediate / Shear-pin contacts delay – page 9.
•Ensure that auxiliary contact C
1
closes together with or after the main contactor. The soft-starter provides a
500 mili seconds delay for the start signal. If it close before, Under Voltage fault will occur.
By-pass contactor
End of Acceleration contact is activated after an adjustable time delays “Run Contact Delay” – see page 26 at the end of
start-up period, closing the by-pass contactor.
•By-Pass Open failure will trip the system if the By-pass contactor is connected to L1, L2 and L3 instead to
L1b, L2b and L3b buses. If this type of connection cannot be avoided set By Pass open trip to DISABLE.
Warning: all current protections are lost.
The contact will return to its original position when:
•Soft Stop or Stop signals are initiated.
•Fault conditions occur.
When the by-pass contactor closes, current to the motor will flow through the by-pass. When a Soft Stop signal is given,
the End of Acceleration contacts return to its original position opening the by-pass contactor. Thereafter, the voltage
will gradually ramp down to zero to soft stop the motor.

Wiring Diagrams – Diesel Generator
14
1414
14
FOR STARTING FROM GENERATOR ALWAYS TRY START CURVE 0 FIRST!
1. When starting from a Diesel – Generator, the voltage regulator (especially older type regulators) may be
affected during the starting process and cause a rapid voltage fluctuations. In these rare cases, the voltage
regulator must be upgraded – consult your Diesel-Generator Supplier.
2. When operating from Diesel Generator verify that power factor capacitors are not used.
3. In applications that may start both from generator and from mains, ensure that power factor capacitors, if used,
are disconnected before starting from the generator.
4. Ensure that Diesel Generator size is suitable. It is recommended that Generator KVA is 2.5 times motor KVA
or larger.
WARNING
1. Motor can not run idle and must be loaded when operating in Generator Mode, otherwise vibration may
occur during starting and stopping.
2. When using extended range, use maximum precaution to avoid motor or starter burnout.
3. Disconnect all other loads before starting for the first time to prevent damages due to voltage fluctuations.
4. Disconnect Power Factor capacitors when operating with Diesel Generator

Wiring Diagrams - Communication
15
1515
15
Operation via communication link with Local / Remote selector switch
•Remote: via Communication Link
•Local: Soft-start, soft-stop by maintained contact.
1 2 3 4 5 6 7 8 9 10 11 12 13 14 15 16 17 18 19 20 21
N
22
23
24
25
26
27
M
U V W
L1 L2 L3 28 29 30 31 32
Start Soft Stop
Remote Local
L1
b
L2
b
L3
b
RS485 to
RS232 Adapter
Twisted Shielded Pair
The communication enables remote parameter
settings and readings. For start, stop, soft-stop, dual
adjust, etc. terminals 4 and 5 must be wired as
shown.
Soft-start and soft-stop
•Program the “Serial Link Number” in the communication page according to the protocol manual.
•Disconnect control supply, so the new information will be loaded on the next time you turn it on.
•Connect a communication line (twisted shield pair) with its (+) to HRVS-DN terminal 24 and (-) to terminal
23, on MODBUS, connect the other end to your host computer containing RS-485 communication port with
MODBUS protocol. For other protocols – consult factory
•Connect other HRVS-DN terminals as follows:
1. Terminal 1, 3 and Control Supply
2. Terminal 4 to Control Supply phase
3. Terminal 9 to Common for terminals 4, 5, 6.
4. During operation via communication link, terminal 5 is connected through the “Local-Remote”
selector switch to Control Supply and start-stop commands are controlled through the communication
port.
During operation in Local mode, terminals 5 and 6 are connected to Control Supply through the start/soft-stop
toggle switch.
WARNING
Starter and host computer must be grounded when communicating with HRVS-DN

Wiring Diagrams - Communication
16
1616
16
Soft-start and immediate stop
Same as the explanation for soft-start and soft-stop
except # 4:
4. During operation via communication link, terminals
4 and 5 are connected through the Local / Remote \
Comm. 4 position selector switch to Control Supply
and start-stop commands are controlled through the
communication port.
During operation in Local mode, terminals 4, 5 and
6 are connected to Control Supply through the start-
stop toggle switch.
Soft-start, soft-stop and immediate stop
Same as the explanation for Soft-start and soft-stop
except # 2 and # 4:
2. Connect terminal 4 as described above.
4. During operation via communication link, terminals
4 and 5 are connected through push-buttons to Control
Supply and start / stop commands are controlled
through the communication port.
During normal operation mode, terminals 4, 5 are
connected to Control Supply through the immediate
stop and soft stop push buttons. Soft start command
may be initiated by pressing the start push button.
Notes: The communication (data retrieval and statistics) is active at all time!
If control signals (start, stop, etc.) are required, terminals 4 and 5 have to be wired in accordance with the
appropriate wiring diagram:
1. Maintained soft start and stop.
2. Maintained soft start with immediate stop.
3. Soft start / stop with immediate stop via push-button control.
Relays board
The relay board enables to control the soft starter via communication with MODBUS or PROFIBUS.
Operation via communication link with Local \ Remote \ Communication (Selector switch)
•Local - to soft-start or immediate stop by maintained contact.
•Remote - via PLC link or other remote signal.
•Comm. - Operation via communication link.
Contacts 31-32 control by communication through
the following protocols:
PROFIBUS
1) Operating the contact for Start \ Stop signal.
2) D. Adj. Calibration.
3) Reset the soft starter.
MODBUS
With MODBUS protocol it is possible to calibrate the
parameters as well as operating the unit like with
PROFIBUS protocol
4
5
6
31
32

Start & Stop Parameters
17
1717
17
Pump Control – Start Curves
Induction motors produce peak torque of up to 3 times
the rated torque towards the end of starting process.
In some pump applications, this peak may cause high
pressure in the pipes.
The HRVS-DN incorporates 5 different starting curves:
Start Curve 0 – Basic curve. Uses less feedback
signals.
Use at beginning of commissioning and when other
curves do not give good starting process.
Start Curve 1 – Standard curve (Default). The most
stable and suitable curve for the motor that prevents
prolonged starting and motor overheating.
Start Curves 2, 3, 4 – During acceleration, before
reaching peak torque, the pump control program
automatically controls the voltage ramp-up to reduce
peak torque.
Choice of three pump control acceleration curves
Speed
Time
Torque
Voltage
DOL
1
2
3
4
Start Curve 5
– Torque curve.
Provides linear torque control.
With certain loads, may cause
linear acceleration.
Note:
Normally starts with Start Curve 1. If towards
the end of acceleration, the peak torque is too high
(pressure is too high), proceed to Curve 2 then 3 or 4 if
necessary.
Pulse Start
This feature includes two settings:
Pulse Level [% of FLA]
Pulse Time [sec.]
These settings allow to use the pulse:
•
To start high friction loads,
requiring high starting
torque for a short time.
•
“Pedestal starting” –
holding the current at a
required level for some
time.
time
0 - 10 Sec.
I
Pulse level
time
Pulse time (0 - 10 Sec.)
I
Pulse level
After the end of the pulse time voltage is ramped
down/up to the current determined by the initial
voltage setting.
Note:
Pulse Start has no effect with Start Curve = 0.
Initial Voltage / Current
Determines the motor initial starting torque (the torque
is directly proportional to the square of the voltage).
Range: 10-50% Un (consult factory for extended
range).
This adjustment also determines the inrush current and
mechanical shock. A setting, which is too high, may
cause high initial mechanical shock and high inrush
current (even if current limit is set low as the Initial
Voltage setting overrides Current Limit setting).
A setting that is too low may result
in prolonged time until motor
begins to turn. In general, this
setting should ensure that the motor
begins turning immediately after
start signal.
U%
10%
50%
100%
If the initial voltage value is increased above the max
value, first line message changes to initial current.
Setting range is 100%-400% of motor FLA. When
initial current is set, starter causes current ramp instead
voltage ramp.
Current limit
Determines the motor highest current during starting.
Range 100-400% of FLA setting (consult factory for
extended range). A too high setting will cause greater
current drawn from main voltage and faster
acceleration.
A setting that is too low may
prevent motor from completing
acceleration process and reaching
full speed. In general, this setting
should be set to a high enough
value in order to prevent stalling.
Note:
Current limit is not operating
during Run and soft stop.
I%
400%
100%
Acceleration Time
Determines the motor voltage
ramp-up time from initial to full
voltage. Range 1-30 sec. (consult
factory for extended range). It is
recommended to set acceleration
time to the minimum acceptable
value (approx. 5 sec).
U%
1
100%
30 sec
Notes:
1.
Since current limit overrides acceleration time
when current limit is set low, starting time
will be longer than the preset acceleration
time.
2.
When motor reachs full speed before voltage
reachs nominal voltage, acceleration time
setting is overridden and cause the voltage to
ramp-up quickly to nominal.
3.
Starting curves 1, 2, 3 prevents quick ramp up.
t
T

Start & Stop Parameters
18
1818
18
Maximum Start Time
The maximum allowable starts time from start signal to
the end of acceleration. If voltage does not reach full
voltage during this time (for example, because of low
current limit setting), the starter will trip the motor.
LCD displays “Long Start Time” message.
Range: 1-30 sec (consult factory for extended range).
Contact Delay
Time delay for the End of Acceleration contact after
completion of starting process. Range: 0-120 sec.
Pump Control – Stop curve
Intended to prevent water hammer during stopping.
In pump applications, load torque decreases in square
relation to the speed and reducing the voltage will
reduce torque so motor will smoothly decelerate to
stop.
The following
Stop curves
can be selected:
Stop curve 0 –
Basic curve. See note at page 17.
Stop curve 1 –
Standard default curve – voltage is
linearly reduced from nominal to zero.
Stop curves 2, 3, 4 –
In some pump applications, when
pumping to a high level, a considerable part of the
torque is constant and does not decrease with speed. It
may happen that during soft stop, when voltage
decrease, motor torque quickly falls below load torque
and motor will abruptly stall instead of smoothly
decreasing speed to zero.
Curves 2, 3, 4 designed
to prevent stall condition.
Voltage Deceleratio
n
2
1
3
4
Note:
Normally use stop curve 1. If motor stalls
quickly instead of slowly decreasing its speed,
select stop curve 2, then 3 or 4 if necessary.
Stop Curve 5
– Torque curve.
Provides linear torque control.
With certain loads, may cause
linear deceleration.
Deceleration Time – Soft Stop
Used for controlled deceleration
of high friction loads.
Determines motor voltage ramp
down time.
Range: 0-30 sec. (consult
factory for extended range).
U%
2
100%
30sec
Note:
soft stop initiation opens the End Of
Acceleration contact and opens the by-pass
contactor. Load will be transferred to the
HRVS-DN and voltage begins to ramp down.
Final Torque
Determines torque towards the
end of soft stop. If current is
still flowing after speed is softly
reduced to zero, increase the
final torque setting.
U%
2
100%
30 sec
Dual Adjustment
A secondary set of parameters used for varying loads,
two speed motors, etc. Connecting control supply to
Terminal 8 makes transfer to Dual Adjustment settings.
•
Initial Voltage 10-50% of
Un.
•
Current Limit 100-400% of
motor’s FLA.
•
Acceleration Time 1-30
sec.
•
Deceleration Time 0-30
sec.
•
Motor Full Load Ampere.
U%
100%
sec2- -302- -10
40%
100%
20%
Note:
Consult factory for extended range.
Tacho Feedback, Incremental Shaft Encoder
(Optional)
Provides linear acceleration and
deceleration curves according to
rpm feedback. 12 tacho gain levels
can be selected for closed loop
control starting and stopping.
Note:
Consult factory for additional
information.
Motor Voltagae
+10Vdc
Speed RPM
Un
t
T

Motor & Starter Protection
19
1919
19
Too Many Starts
Combines three parameters:
•Number of Starts
Determines the maximum allowable number of
starts.
Range: Off, 1-10 starts. Default: 1
•Start Period
Time period when number of starts is being
counted. Range: 1-60 min. Default: 20 Min.
•Start inhibit
Determines time period when start signal is
disabled after “Too many starts” trip.
Range: 1-60 min
Note:
Motor can not be started before “Start Inhibit
Time” has elapsed. Trying to start the motor
during this time delay will result in LCD
displaying “Wait Before Restart: ___ MIN.
Long Start Time – (Stall Protection)
Trips the starter if motor does not reach full speed
during “Maximum Start Time”.
Range: 1-30 sec. (consult factory for extended range).
Over Current Shear-pin trip
Operational when starter is energized and has two
functions:
•
Trips the starter when current exceeds 850%
of starter’s FLC setting in 1 cycle or less.
•
850% FLA with delay during start (850%
overrides O\L settings.
•
During run (after RUN LED is on) it trips the
starter if current exceeds set level and time
delay.
Range: 100 - 850% of motor FLA setting
Delay: 0 – 5 sec. (0=up to 200 msec)
Note:
The O/C Shear-Pin trip is not intended to replace
the fast acting fused. It is required to protect the
thyristors (see fuse table in the appendix).
Overload (OL)
Inverse time electronic overload
becomes operational when RUN
LED is on.
The OL circuitry incorporates a
Thermal Memory Register, which
calculates the heat less the
dissipation of the motor. The starter
trips when the register fills up.
The thermal register resets itself 15
minutes after the motor stops.
t
I%
500115
10
1
The value is adjustable within 75-150% of motor FLA
and factory pre-set at 115%.
Tripping time at 500% FLA is adjustable within 1-10
seconds to allow trip curve selection.
ATTENTION
Overload protection is not operative during soft-
start
or soft-stop.
Under Current
Operational when motor is running. Trips the starter
when motor current drops below under current trip
(UCT) set point for a period of time longer than under
current delay (UCD).
Under Current Trip range: 0 = Off, 20-90% of FLA
Under Current Delay range: 1-40 sec.
Auto Reset
A special feature enables auto reset after adjustable
time delay. Range: Off, 10-120 min.
Under Voltage / No Voltage
Operational after start signal. It trips the starter when
main voltage drops below the Under Voltage Trip set
point for a period of time longer than Under Voltage
Delay.
Auto reset can be activated via Fault Parameters. Auto
reset is activated 60 seconds after trip occurred.
Under Voltage Trip range: 50-90% Un (Line to Line)
Under Voltage delay range: 1-10 sec.
Note:
1.
When voltage drops to zero (voltage outage)
the starter will trip immediately, overriding
the delay.
2.
Auto reset can not be activated if start signal
is still connected.
Table of contents
Other Solcon Controllers manuals
Popular Controllers manuals by other brands

Frymaster
Frymaster 3000 quick reference
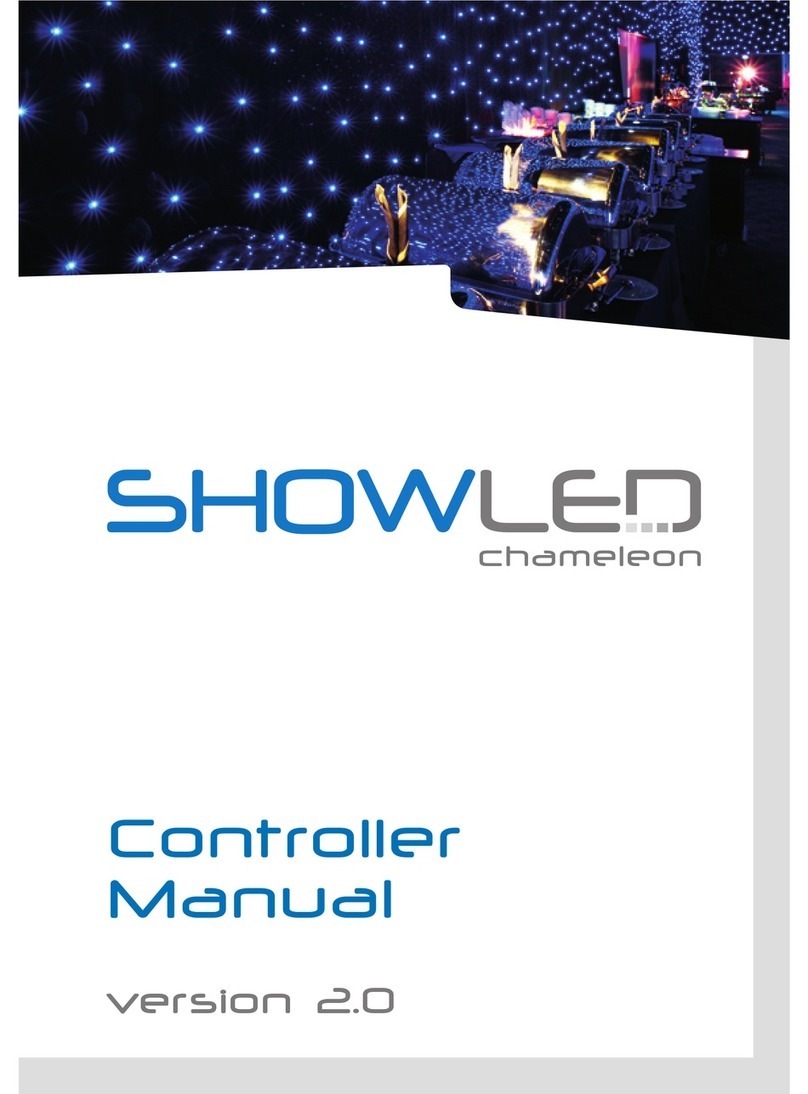
ShowLed
ShowLed Chameleon manual

Mitsubishi
Mitsubishi a2 Series Programming manual

Honeywell
Honeywell CVL4022ASVAV1 Engineering guide
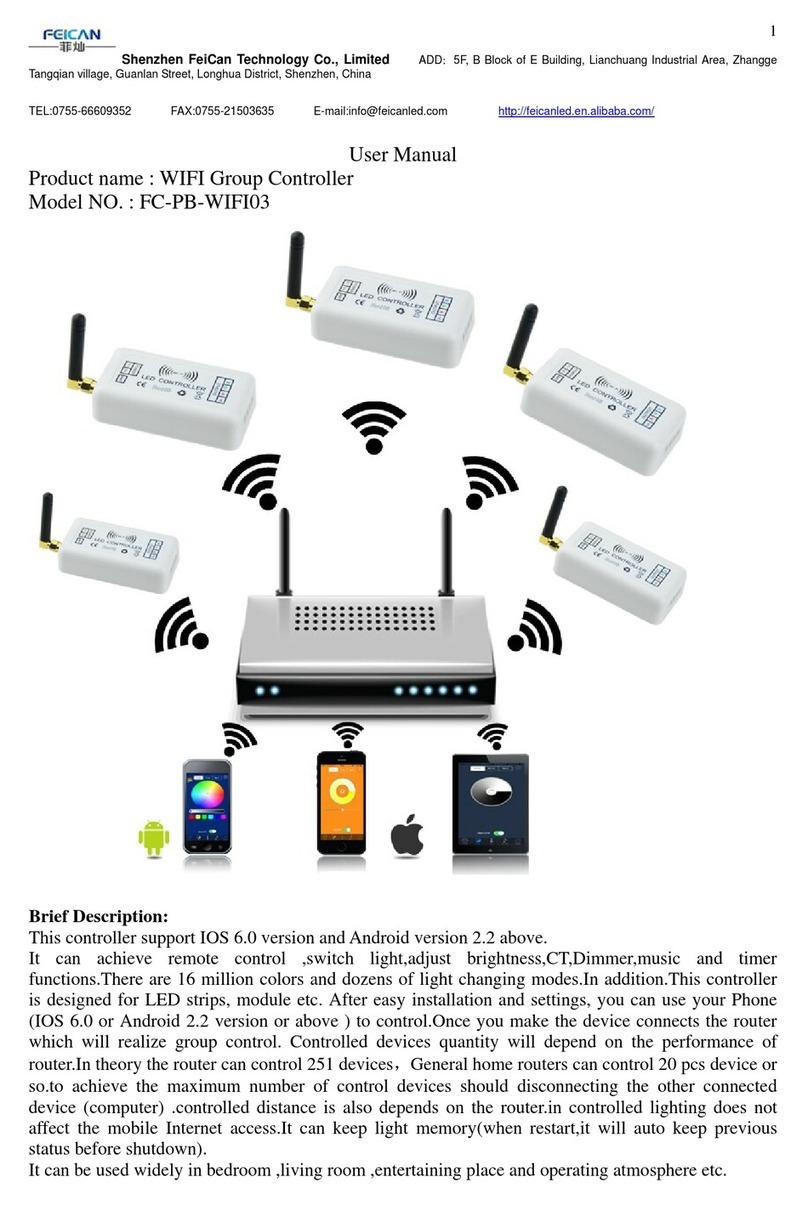
Shenzhen FeiCan Technology Co.
Shenzhen FeiCan Technology Co. FC-PB-WIFI03 user manual
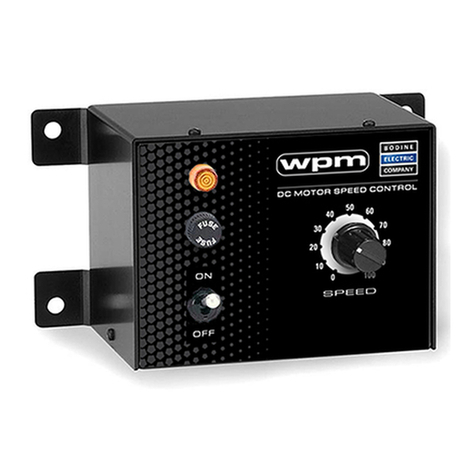
Bodine
Bodine 0790 Instructions for installation and operation
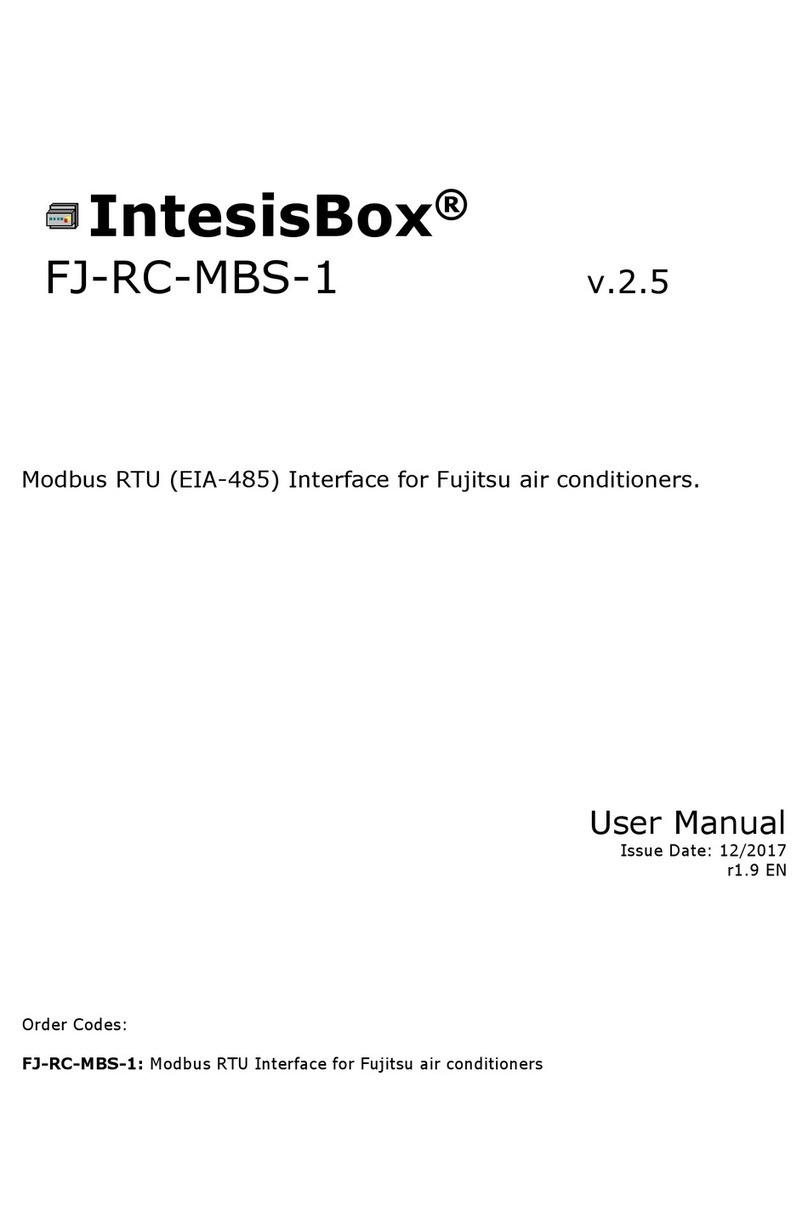
IntesisBox
IntesisBox FJ-RC-MBS-1 user manual
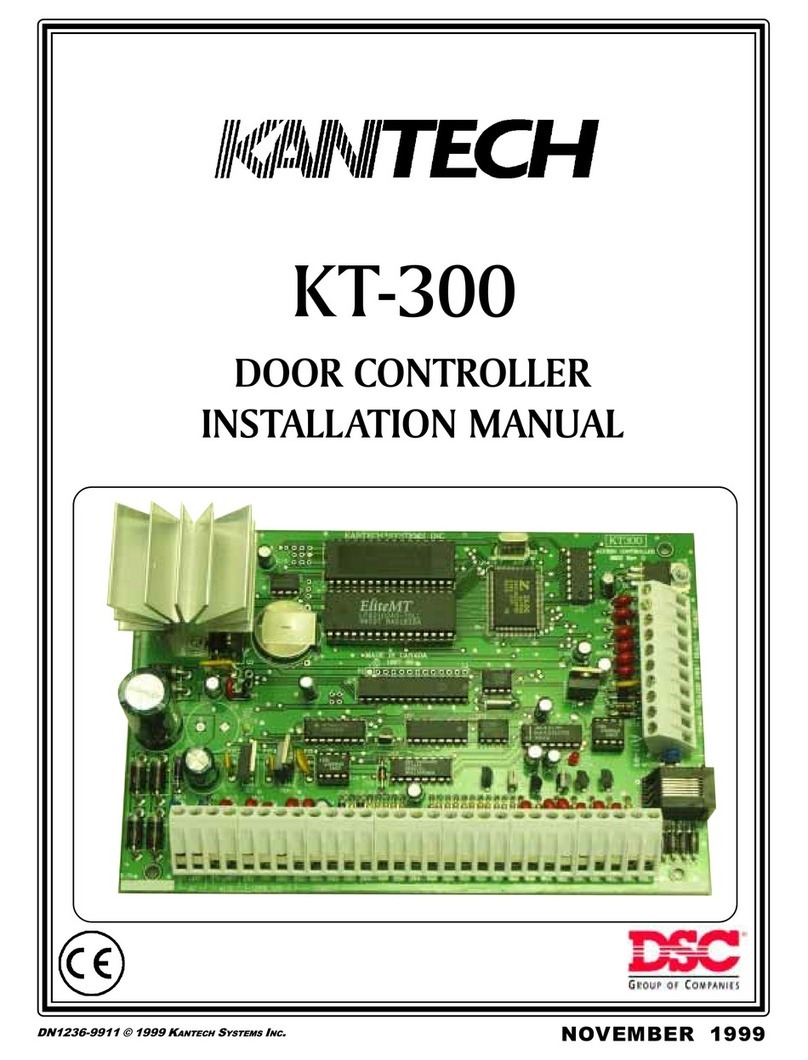
Kantech
Kantech Door Controller Innovative and Powerful... installation manual

AMX
AMX SX16+ Instruction and programming manual
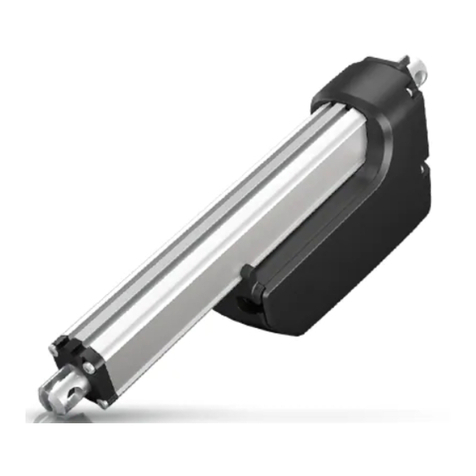
Linak
Linak TECHLINE LA33 user manual
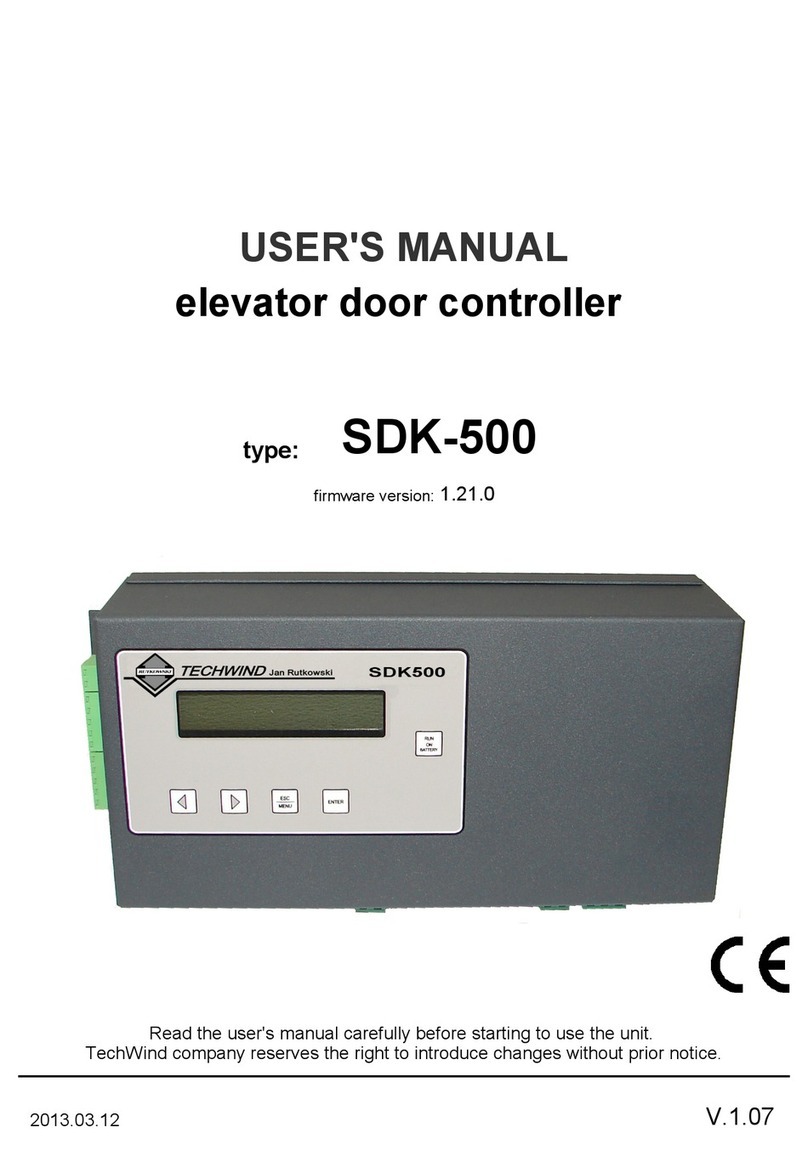
TechWind
TechWind SDK-500 user manual
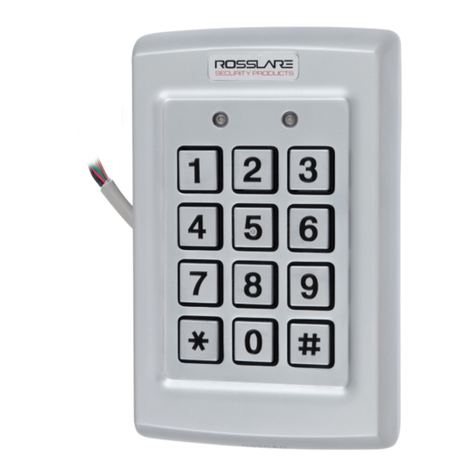
Rosslare
Rosslare AYC-Q54B Installation and programming manual