System air Access V4.X Instruction sheet

Access V4.X Configuration manual
EN
Document in original language | 153830 · A001

Version
Document
Preliminary 003
Access V4.X Configuration manual
1 (33) 2019-05-13
Contents
1. About the manual .................................................................................................................................3
Basic settings.............................................................................................................................................3
Access levels..........................................................................................................................................3
Date and time .......................................................................................................................................3
Preference unit settings........................................................................................................................3
Communication.........................................................................................................................................4
Terminals...............................................................................................................................................4
Software connectors.............................................................................................................................4
Port function .........................................................................................................................................5
Communication devices........................................................................................................................6
2. Configuration ........................................................................................................................................8
Configuration steps...................................................................................................................................8
Temperature control.................................................................................................................................9
Temperature control types...................................................................................................................9
Heating/Cooling sequences ................................................................................................................10
Step controller ....................................................................................................................................18
Changover settings..............................................................................................................................19
Support control...................................................................................................................................19
Free cooling.........................................................................................................................................21
Pretreatment ......................................................................................................................................22
Summer/winter mode ........................................................................................................................22
Cooling recovery mode.......................................................................................................................23
Extra controller ...................................................................................................................................23
External setpoint device .....................................................................................................................24
Fan control..............................................................................................................................................25
Fan control type..................................................................................................................................25
Fan configuration................................................................................................................................26
Fan levels.............................................................................................................................................27
Fan compensation...............................................................................................................................27
Extra fan motor control.......................................................................................................................28
Humidity control.....................................................................................................................................29
Humidification.....................................................................................................................................29
Dehumidification.................................................................................................................................29

Version
Document
Preliminary 003
Access V4.X Configuration manual
2 (33) 2019-05-13
CO2 control.............................................................................................................................................30
Fan start/stop......................................................................................................................................30
Mixing damper function......................................................................................................................30
Enthalpy control......................................................................................................................................31
Dampers..................................................................................................................................................31
I/O allocation settings.............................................................................................................................31
Starting up and stopping the unit...............................................................................................................32
Schedule..................................................................................................................................................32
Extended running....................................................................................................................................33
External stop ...........................................................................................................................................33

Version
Document
Preliminary 003
Access V4.X Configuration manual
3 (33) 2019-05-13
1. About the manual
This manual is intended to guide while configuring basic functions of the Access controller. It also gives a
general overview of the software and interface.
1.1 Basic settings
Access levels
The controller has four user access levels. The active user access level is indicated by icon.
End user
When logged out
Read /write —Home page.
Possible actions in end user mode are to stop the air
handling unit for maintenance (e.g. filter exchange),
change the time for extended run and change the
temperature setpoint.
Operator mode
(Log in with 1111)
Read and write privileges (except Configuration).
Service mode
(Log in with 0612)
Full read and write privileges.
Date and time
ACCESS controller has a year-base clock function. The clock has an automatic summertime/wintertime
change-over.
Date and time can be set
Time settings > Date / Time
Preference unit settings
Preferred units for temperature, flow and pressure can be set
Configuration > System settings > Preference unit settings
Save and restore
Commissioning settings can be stored in a local memory.

Version
Document
Preliminary 003
Access V4.X Configuration manual
4 (33) 2019-05-13
Configuration > System Settings > Save and restore settings >
Save commissioning settings –saves all recently made changes.
Restore to commissioning settings –restores to last saved commissioning settings.
Restore to factory settings –resets settings to state of delivered unit.
1.2 Communication
Terminals
The Access controller contains dedicated terminals for Ethernet, HMI and EFX display and four terminals
for internal and external bus communications.
Int-link 1 and Int-link 2 are parallel and designated for internal bus communication.
Int-link 1 and Int-link 2 terminals correspond to “Port 3” in the menu.
BMS terminal corresponds to “Port 2” in the menu.
Ext-link terminal corresponds to “Port 1” in the menu.
Ethernet –for connecting to local TCP/IP network
HMI –for connecting NaviPad. This connector support PoE (Power over Ethernet) therefore no
additional power source for NaviPad is needed.
EFX –connector for E3-DSP external display unit.
Software connectors
Configuration > System settings > Communication >

Version
Document
Preliminary 003
Access V4.X Configuration manual
5 (33) 2019-05-13
The communication ports in the Access controller Port 1 (Ext-link), Port 2 (BMS) and Port 3 (Int-link 1|2)
can be configured for particular function.
Port function
These ports can operate as follows:
EXOline slave –Connection to EXO SCADA system and application tool;
EXOline master –Connection to expansion units and Pressigo pressure transmitters;
Modbus slave –Connection to BMS via Modbus RTU;
Modbus master –Bus communication to components inside AHU;
BACnet MSTP slave - Connection to BMS via BACnet MSTP;
External display –Connection to touch display;
EFX master –communication to expansion units via EFX protocol.
Message format
For proper communication, the right message format needs to be configured. Available formats and
description
Baud rate
Description
9k6 bps
9600bps
14k4 bps
14400bps
19k2 bps
19200bps

Version
Document
Preliminary 003
Access V4.X Configuration manual
6 (33) 2019-05-13
28k8 bps
28800bps
38k4 bps
38400bps
57k6 bps
57600bps
76k8 bps
76800bps
115k2 bps
115200bps
Cloud
Cloud function must be enabled if the controller shall access “Systemair Connect” cloud service. The
provided serial number is unique identification of the controller and must be entered upon request
while registering at “Systemair Connect”.
Configuration > System settings > Communication > Cloud >
BACnet
BACnet/IP shall be enabled if controller is connected to BMS via this protocol. The following entries
include device name and BACnet communication related settings.
Communication devices
Configuration > System settings > Communication devices >
The Access controller supports up to 20 devices connected via communication BUS (Modbus and
EXOline).
Only limited number of predefined device models is supported.
List of supported brands and models:
Device
type
Fan / FC
(Modbus)
Rotary
exchanger
(Modbus)
Pressure transmitter
(Modbus / EXOline)
Actuator
(Modbus)
Expansion unit
(EXOline)
Model
Vacon
RHC200
PDTxxC (Modbus)
Belimo
E8
Lenze
IBC VariMax
PDTxxC-2 (Modbus)
Emerson
HK DPT-Dual-MOD-
2500 (Modbus)
LS iG5A
PDTxxC (EXOline)
E15
LS iS7
PDTxxC-2 (EXOline)
E28
EBM-PAPST
DANFOSS FC101
ABB ACSxxx
Ziehl blue
Configuration > System Settings > Communication devices > Device (n) > Address >
Modbus devices on the bus must have unique address assigned. The address shall be the same as set in
the device. The device shall also hold the same message format and baud rate settings as the port it is
connected to (see port function).
Function

Version
Document
Preliminary 003
Access V4.X Configuration manual
7 (33) 2019-05-13
Configuration > System Settings > Communication devices > Device (n) > Function >
Every device on the bus must have function assigned. Different functions are available in dependence on
device type:
Device
type
Fan
(Modbus)
Rotary
Exchanger (Modbus)
*1
Pressure
transmitter
Damper
(Modbus)
Expansion
unit
(EXOline)
Functio
n
Supply air
fan
Heating *1
Exp1
Heating *1
Exp1
Exhaust air
fan
Exchanger*1
Exp2
Exchanger*1
Exp2
Cooling *1
Exp3
Cooling *1
Exp3
Recirculation 1 *1
Exp4
Recirculation 1 *1
Exp4
Recirculation 2 *1
Exp5
Recirculation 2 *1
Exp5
Fan heating/cooling *1
Exp6
Fan heating/cooling
*1
Exp6
Heating 2 *1
Exp7
Heating 2 *1
Exp7
Cooling 2 *1
Exp8
Cooling 2 *1
Exp8
Exchanger extract *1
Exp9
Exchanger extract *1
Exp9
Extra heating/cooling
capacity *1
Exp10
Extra
heating/cooling
capacity *1
Exp10
Recirculation air
Outdoor air
Exhaust air
*1 Only active sequence are selectable
Name
Configuration > System Settings > Communication devices > Device (n) > Name >
Enter a unique device name.
This name will be used in Device “drop down list” when you select Device under I/O allocation.

Version
Document
Preliminary 003
Access V4.X Configuration manual
8 (33) 2019-05-13
2. Configuration
2.1 Configuration steps
The configuration of controller shall start with activation of functions to be used.
Configuration order of control system and menu
Description
Flow
The navigation path
Select function to activate:
e.g. Heater 2, cooler 2,
Support control, Free cooling, fire
function etc.
Activation
Configuration ►Functions ►
Function Activation
How the function should be designed:
e.g. Electric, water, frost protection, fire
damper etc.
Configuration
Configuration ►Functions
Select I/Os for activated function:
e.g. AO2, DI4, DO6, UI4
Allocation
Configuration ►I/O allocation
How the function will work:
e.g. Min limit value, max limit value,
setpoint etc.
Operation settings
Data & Settings

Version
Document
Preliminary 003
Access V4.X Configuration manual
9 (33) 2019-05-13
2.2 Temperature control
Temperature controller is a closed loop system which includes measurement, processing and
adjustment.
Temperature control types
To maintain comfort temperature the controller constantly adjusts supply air temperature. It can be set
constant or variable depending on parameters of choice. Several temperature control types are
available:
Configuration > Functions > Function activation > Temperature control type >
Supply air
The supply air temperature is kept at the setpoint value by controlling the output signals. The controller
is reverse acting, i e. the output will increase for decreasing temperature.
Supply air outdoor compensated
The supply air temperature setpoint is outdoor temperature compensated using a control curve with 4
node points.
Room cascade
Cascade control of room temperature and supply air temperature to achieve a constant, settable room
temperature. The room controller output signal generates the supply air controller’s setpoint value. The
room controller uses an own PI loops.
1..4 room sensors can be connected. The average value of selected sensors is used in the control loop.
Extract air cascade
Cascade control of extract air temperature and supply air temperature to achieve a constant, settable
room temperature. The extract air controller output signal generates the supply air controller’s setpoint
value. The extract controller used an own PI loop.
Room (summer) else supply air
Outdoor temperature dependent switching between supply air temperature control and room
temperature control.
When the outdoor temperature is lower than a settable limit (winter), outdoor compensated supply air
temperature control will be active, otherwise (summer) cascaded room temperature control as in room
cascade type.
Extract air (summer) else supply air
Outdoor temperature dependent switching between supply air temperature control and extract air
temperature control.
When the outdoor temperature is lower than a settable limit (winter), outdoor compensated supply air
temperature control will be active, otherwise (summer) cascaded extract air temperature control as in
extract air cascade type.

Version
Document
Preliminary 003
Access V4.X Configuration manual
10 (33) 2019-05-13
Room outdoor compensated
The room temperature can be compensated when the outdoor temperature increases. One can, for
instance, imagine accepting a slightly higher room temperature if it is warm outside or, conversely, a
slightly lower temperature if it is chilly. This function is included to conserve energy.
Extract air outdoor compensated
The extract air temperature can be compensated when the outdoor temperature increases. One can, for
instance, imagine accepting a slightly higher extract air temperature if it is warm outside or, conversely,
a slightly lower extract air temperature if it is chilly. This function is included to conserve energy.
Extract air dependent supply air
A difference between extract air temperature and supply air temperature can be configured to maintain
the supply air temperature setpoint to follow extract air temperature with this difference (+10°C to -
10°C). Supply air temperature setpoint = extract air temperature + difference.
Heating/Cooling sequences
The supply air temperature is adjusted by controlling the output signals for AHU’s components by
regulating corresponding sequences. Up to 10 sequences with separate PID control settings can be used.
Each sequence can be set for Heating, Cooling, Exchanger, Damper, Pressure/flow compensation or set
as Not used.
For standardization all 10 sequences have predefined names to cover the most frequent configurations
of AHUs. The sequences are also identified by letter A to J.
The order of sequence activation is set by assigning order number for heating and cooling. As in
configuration example bellow in case of heating demand, the Exchanger (SEQ-B) will start first and
Heating (SEQ-A) will follow second.
In case of cooling demand, the Exchanger (SEQ-B) will start first and the Cooling (SEQ-C) will follow
second.
Configuration > Functions > Function activation > Heating/Cooling sequences >
Position
Heating
Cooling
Start
Heating
Start
Cooling
Name
SEQ-A
2
Off
0%
0%
Heating
SEQ-B
1
1
0%
0%
Exchanger
SEQ-C
Off
2
0%
0%
Cooling
SEQ-D
Off
Off
0%
0%
Recirculation 1
SEQ-E
Off
Off
0%
0%
Recirculation 2
SEQ-F
Off
Off
0%
0%
Fan heating/cooling
SEQ-G
Off
Off
0%
0%
Heating 2
SEQ-H
Off
Off
0%
0%
Cooling 2
SEQ-I
Off
Off
0%
0%
Exchanger extract
SEQ-J
Off
Off
0%
0%
Extra heating/cooling capacity

Version
Document
Preliminary 003
Access V4.X Configuration manual
11 (33) 2019-05-13
If required sequence overlapping or dead band can be set by adjusting “Start Heating” and “Start
Cooling” sequence parameters. Adjustable range is -100% .. +100%. Negative starting point will create
sequence overlap while positive starting point will delay start of the selected sequence.
Position
Heating
Cooling
Start
Heating
Start
Cooling
Name
SEQ-A
2
Off
50% 0%
0%
Heating
SEQ-B
1
1
0%
0%
Exchanger
SEQ-C
Off
2
0%
-25% 0%
Cooling
SEQ-D
Off
Off
0%
0%
Recirculation 1
SEQ-E
Off
Off
0%
0%
Recirculation 2
SEQ-F
Off
Off
0%
0%
Fan heating/cooling
SEQ-G
Off
Off
0%
0%
Heating 2
SEQ-H
Off
Off
0%
0%
Cooling 2
SEQ-I
Off
Off
0%
0%
Exchanger extract
SEQ-J
Off
Off
0%
0%
Extra heating/cooling capacity

Version
Document
Preliminary 003
Access V4.X Configuration manual
12 (33) 2019-05-13
Sequence type
Each active sequence has to be defined for control of specific device type. Selecting device type reveals
relevant settings (e.g. if water heating is selected, then pump control and frost protection options will be
available).
Configured sequences (for electric heating and DX cooling) can be used as input for step controllers.
Configuration > Functions > Function activation > Heating/Cooling sequence setup > Step
controller
For combined heating/cooling –changeover option for connecting two sequences can be configured.
Configuration > Functions > Function activation > Heating/Cooling sequence setup >
Changeover settings
Heating
Water heating
When the unit is in running mode the heating valve is controlled by the analogue output and digital
output (“SEQ-A pump”) for pump control and/or signal (“SEQ-A start”) for start heating.
Pump indication
A feedback from pump (“Feedback SEQ-A”) can be used, “running indication or alarm indication.
Frost protection temperature sensor

Version
Document
Preliminary 003
Access V4.X Configuration manual
13 (33) 2019-05-13
The heater return water temperature is measured using the analogue input (”Frost protection sensor”).
Low temperatures will generate an internal, proportional signal that is used to force the heating valve
open thereby preventing freeze-up of the heater.
The internal signal will begin to rise as the frost protection temperature falls below “Alarm limitation
running mode” + “P-band running mode” in order to reach 100 % output when the signal has fallen to
“Alarm limitation running mode”.
Frost guard
When ”Internal signal” reaches 100 % or the digital input (”Defrost switch”) is activated, the unit is shut
down, the heating output is set to completely open mode and an alarm is activated. The unit is restarted
when the alarm has been acknowledged and the temperature for the frost protection sensor has risen
above “Alarm limit frost” + “P-Band”.
The frost protection alarm limits is set in the:
Settings: Data & settings > Temperature control > Heating and/or Heating 2.
Standby mode
If frost protection is activated, the controller will go into ”Standby mode” when the running mode
switches to ”Off”. The “Standby mode” will control the heating output to maintain a constant settable
temperature at the frost protection sensor “Setpoint Standby mode”.
Electric heating
Control
The heating is controlled using the analogue output and/or signal for start heating or step controller to
control 1..4 digital output steps.
Overheat protection
On Activate of the digital input “Overheated electric heater” the unit will be shut down, either according
to the stop sequence described in section Start/stop of unit or as an emergency shutdown. The unit will
restart after the alarm has been acknowledged and “Electric heating is overheated” has reset.
Flow switch
Note that activation of the input signal “Flow switch” will also stop the unit. Note: It is important that
the high temperature thermostat is hardwired to disconnect the power to the heater. That is to ensure
that the heating is shut down when the thermostat is activated even if the Access controller should be
faulty.
Fast stop on overheating
If the function "Fast stop on overheating" is active, the fans will be immediately stopped when there is
an overheating alarm, regardless of the set cool-down time.
Step controller heating
Activation: By configuring the electrical heater the step switch will be activated in the menu.

Version
Document
Preliminary 003
Access V4.X Configuration manual
14 (33) 2019-05-13
Configuration: Configuration > Functions > Function activation > Heating/Cooling sequence setup >
Step controller 1 (Step controller 2)
Cooling
Water cooling
Control
When the unit is in running mode the heating valve is controlled by the analogue output and digital
output for pump control and/or signal for start heating.
Pump indication
A feedback from pump can be used, running indication or alarm indication.
DX cooling
Step controller Heating / DX cooling
As alternative or complement to the above mentioned analogue control, heating and cooling can be
activated in steps. The internal signal is then used to activate digital outputs for control of the
heaters/chillers. Up to four heater outputs and three cooler outputs can be configured. There are two
possible modes:
Sequential control
Each output step has individually settable on and off values in percent of the control signal. The number
of steps is equal to the number of heater/chiller groups. Minimum on and off times can be set, i.e. the
minimum time the step has to be inactive or active for a change to occur.
Binary control
The heater power outputs should be binary weighted (1:2:4:8). The number of loads to be controlled is
set. Thereafter the program will automatically calculate the individual Activate levels. Switching
differential and minimum on/off times can be set.
DX cooler modes
DX cooling with room or extract air control
If DX cooling is used in conjunction with room temperature control or extract air temperature control,
there are two Configure alternatives, DX cooling or DX cooling with exchanger control.
DX cooling without exchanger control
When running cascade control, the supply air controller setpoint is normally controlled by the
room/extract air controller output signal.
When DX cooling is activated, the supply air controller setpoint is lowered to five degrees (adjustable)
below the setpoint given by the room/extract air controller. This prevents the DX cooling from being
activated/deactivated too often.
DX cooling with exchanger control

Version
Document
Preliminary 003
Access V4.X Configuration manual
15 (33) 2019-05-13
When running cascade control, the supply air controller setpoint is normally controlled by the
room/extract air controller output signal.
When DX cooling is activated, the supply air controller setpoint is lowered to five degrees (adjustable)
below the setpoint given by the room/extract air controller. This prevents the DX cooling from being
activated/deactivated too often. If the supply air temperature falls below the setpoint given by the
room/extract air controller, the heat exchanger output will be activated in order to try to maintain the
supply air setpoint given by the room/extract air controller. The output uses P-control with a P-band of
half the setpoint lowering (adjustable, 2.5°C as default). The setpoint given by the room/extract air
controller cannot drop below the set min limit. When there is no longer a cooling demand, the supply air
controller setpoint will return to the value given by the room/extract air controller.
Note: The function cannot be used if the exchanger signal controls a mixing damper.
Example:
The room controller gives a supply air setpoint of 16°C. If there is a cooling demand, the supply air
controller setpoint is lowered to 11°C (16 –5) and DX cooling is activated. Should the supply air
temperature fall below 16°C, the exchanger output will be activated and reach 100 % output when the
supply air temperature has fallen to 13.5°C (16 - 2.5).
Blocking of DX cooling at low outdoor temperature
DX cooling can be blocked when the outdoor temperature is low. It is possible to block the three cooling
steps individually or to block all DX cooling. The temperature limits are adjustable (+13°C default) and
have a fixed one degree hysteresis.
When two DX cooling steps are used with binary function, the cooling effect is divided into three steps.
The desired blocking level can be set individually for each of these steps.
When three DX cooling steps are used with binary function, the cooling effect is divided into seven
steps. However, the controller still only has three blocking level settings. Therefore, Blocking step 1 will
apply to binary steps 1 and 2, Blocking step 2 to binary steps 3 and 4, and Blocking step 3 to binary steps
5, 6..etc.
Blocking of DX cooling at low supply air fan speed
When DX cooling is used in conjunction with pressure controlled or flow controlled fans it is possible to
block DX cooling if the supply air fan control signal falls below a preset values. For sequential control,
the blocking level is individually settable for each DX cooling step.
When two DX cooling steps are used with binary function, the cooling effect is divided into three steps.
The desired blocking level can be set individually for each of these steps.
When three DX cooling steps are used with binary function, the cooling effect is divided into seven
steps. However, the controller still only has three blocking level settings. Therefore, Blocking step 1 will
apply to binary steps 1 and 2, Blocking step 2 to binary steps 3 and 4, and Blocking step 3 to binary steps
5, 6 and 7.
Blocking of DX cooling on cooling pump alarm Access can be configured to block DX cooling on cooling
pump alarm. In- and outputs

Version
Document
Preliminary 003
Access V4.X Configuration manual
16 (33) 2019-05-13
Override of reduced speed for DX cooling
Override to normal quantity of air for DX cooling when the unit runs on reduced quantity of air. The fans
can be set to normal operation when cooling is required at high outdoor temperatures (e.g. >14°C, the
same temperature limit as for blocking of DX cooling).
Step controller
Activate: By configuring Cooler DX, the step switch will be activated in the menu.
Configuration > Functions > Function Activation> Heating/Cooling sequence setup > Step controller 1
(Step controller 2)
DX with exchanger control
Exchanger
Rotary
Control
Rotational speed is controlled by the analogue signal ”Exchanger”. A rotary controller alarm feedback
can be connected to the digital input ”Rotary exchanger alarm”. An alarm is generated if this input is
activated.
Function to prevent the heat exchanger from frost:
A temperature sensor, exhaust air, outdoor air or extra controller sensor can be used as a prevention
sensor. It is possible to set a starting temperature. This represents both the minimum time that the
function should be active, the supply air fan and extract air fan compensation, as well as the minimum
time before the next prevention cycle should begin. While the cycle is active, “Defrosting” is shown in
the NaviPad.
Plate
Control
The airflow through the exchanger is controlled by a shut-off damper and a by-pass damper. Both
dampers are controlled by the same analogue output ”Exchanger”.
Defrosting temperature monitoring
Configuration > Functions > Temerature control > Defrosting temperature monitoring >
Defrosting is activated either when the digital signal ”Defrosting” is activated or when the value of the
analogue input ”Defrosting temperature” falls below the defrosting limit (-3°C), or when the analogue
signal ”Exchanger extract air pressure sensor” rises above the set value for the current pressure. It is
deactivated when the digital signal is reset, or alternatively when the analogue signal exceeds/falls
below the limit value plus a settable differential.
When defrosting:
A PID-controller compares the defrosting setpoint with the signal ”Defrosting exchanger”. The smallest
of the output signal from this controller and the output from the ordinary controller is used as output to
the dampers.

Version
Document
Preliminary 003
Access V4.X Configuration manual
17 (33) 2019-05-13
Defrosting pressure monitoring
Configuration > Functions > Temerature control > Defrosting pressure monitoring >
Defrosting is activated by measuring the pressure difference over the exchangers extract/exhaust side.
The differential pressure transmitter is auto calibrated by the system to obtain the correct pressure in
relation to the airflow.
Manual calibration is possible, e. g. after cleaning of exchanger. Defrosting is possible with by-pass or
stop defrosting, adjustable in the display.
Defrosting is stopped when the desired, adjustable decrease in pressure over the heat exchanger is
obtained.
If the decrease of pressure does not happen during defrost cycle, the air handling unit is stopped and an
alarm is shown in the display.
Sectional defrosting
Configuration > Functions > Temerature control > Sectional defrosting >
Demand for defrosting is monitored by differential pressure drop over Extract and Exhaust sides of the
plate heat exchanger.
The airflow through heat exchanger is controlled by separate controller (Section Defrosting Module =
SDM) and dampers dividing the exchanger into sections. Maximum of 5 damper configuration (4
(exchanger) +1 (bypass)) can be implemented.
The SDM is controlled by the main controller’s signals Digital output (Defrosting start) and Analog
output (Exchanger control). If defrosting is required, a digital output on the main controller is activated.
The function ends if differential pressure drop decreases below preset limit.
Liquid
Control
A mixing valve in the exchanger circulation system is controlled by the analogue signal ”Exchanger” and
digital output (“SEQ-A pump”) for pump control and/or signal (“SEQ-A start”) for start heating.
Defrosting temperature monitoring
Deicing is activated either when the digital input sensor ”Defrosting temperature” is activated, when the
value falls below the deicing limit (-3°C). It is deactivated when the digital input is reset or the analogue
input rises above the limit value plus a settable differential.
On deicing: A PI-controller compares the deicing setpoint with the signal ”Defrosting Exchanger”. The
lesser of the output signal from this controller and the output from the ordinary controller is used as
output to the actuator.
Pump indication
A feedback from pump (“Pump SEQ-B”) can be used, running indication or alarm indication (“Feedback
SEQ-B”).

Version
Document
Preliminary 003
Access V4.X Configuration manual
18 (33) 2019-05-13
Efficiency presentation
Defrosting
Damper
Fan setpoint compensation
It is possible to select whether the compensation (0...10000) should increase or decrease the fan
setpoint. The 0...10000 compensation follows the current control quantity for the fans.
Configuration > Functions > Function Activation> Heating/Cooling sequence setup > Fan
heating/cooling
Data & Settings > Temperature control > Fan heating/cooling
Step controller
Two step controllers are available if electric heater, DX cooler or change-over is used for heating or
cooling. The internal signal is then used to activate digital outputs for control of the heaters/chillers.
In order to get acces to step controller settings the Heating or Cooling sequences have to be configured
first.
Configuration > Functions > Function activation > Heating/Cooling sequence setup >
The configured sequence now can be used by step controller
Configuration > Functions > Function activation > Heating/Cooling sequence setup > Step
controller
Two operation modes for step controllers are available:
Sequential control
Each output step has individually settable on and off values in percent of the control signal. The number
of steps is equal to the number of heater/chiller groups. Minimum on and off times can be set, i.e. the
minimum time the step has to be inactive or active for a change to occur.
Binary control
The heater power outputs should be binary weighted (1:2:4:8 for 4 step controller). The number of loads
to be controlled is set. Thereafter the program will automatically calculate the individual activation
levels. Switching differential and minimum on/off times can be set. The number of heating steps will be:
2no. of groups-1. In binary mode, the analogue output signal may be used to fill out between the steps.
The signal will go 0…100 % between the activation of each step. The load connected to the analogue
signal should have the same size as the smallest of the binary groups. In the example below there are 4
heater groups (1:1:2:4) and the total number of heating steps is eight.

Version
Document
Preliminary 003
Access V4.X Configuration manual
19 (33) 2019-05-13
Changover settings
Configuration > Function Configure
Changeover 1 sequence for heating Heater
Changeover 1 sequence for cooling Cooler
Changeover 2 sequence for heating disable
Changeover 2 sequence for cooling disable
Data & Settings > In-/output status > Digital input (Analogue output)(digital output)*1
Change-over is a function for installations with 2-pipe systems. It makes it possible to use the same pipe
for both heating and cooling, depending on whether heating or cooling is required.
A special analogue output signal, "Changeover 1 (2)*2", is used for Change-over control. Switching
between heating and cooling can be done in two ways. A digital Change-over input signal
“Cooling/(heating) changeover 1(2) is normally used. Open contact gives heating control and closed
contact gives cooling control. If the input has not been configured, change-over is handled by the
internal controller signal. The output signal (AO “changeover 1(2)” and DO “changeover 1(2)”) will follow
the two regular output signals "Heating" and "Cooling". For heating control, the digital outputs Heating
“SEQ-A start” or “SEQ-A pump” are active. For cooling control the digital outputs Cooling “SEQ-C start”
or “SEQ-C pump” are activate.
If frost protection sensor has been configured, it will function in the usual way when heating is active.
However, when cooling is active, it will only be used for indicating temperature.
*1 Digital input (Analogue output)(digital output) = Digital input, Analogue outputs and Digital outputs
*2 Changeover 1(2) = Changeover 1 and Changeover 2
Support control
Activation: Configuration > Functions > Function activation > Support control > “Yes”
Configuration: Configuration > Functions > Support control >
Table of contents
Popular IP Access Controllers manuals by other brands
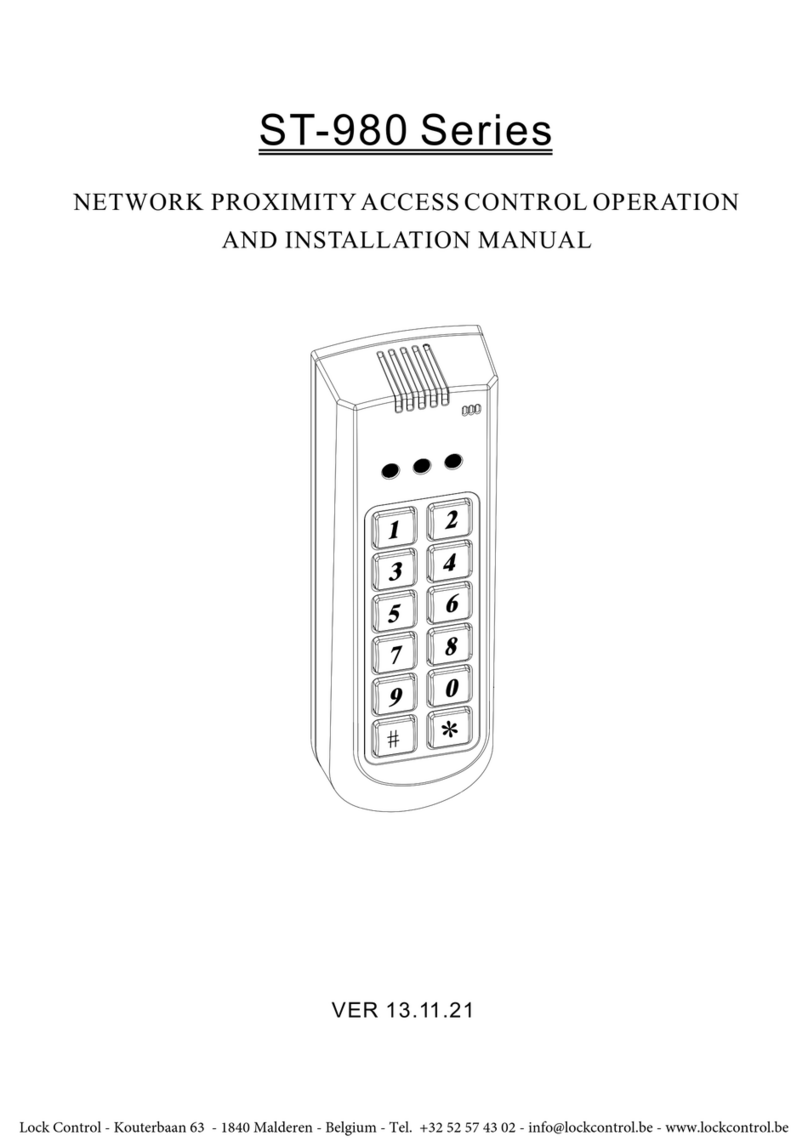
Lock Control
Lock Control ST-980 Series Operation and installation manual
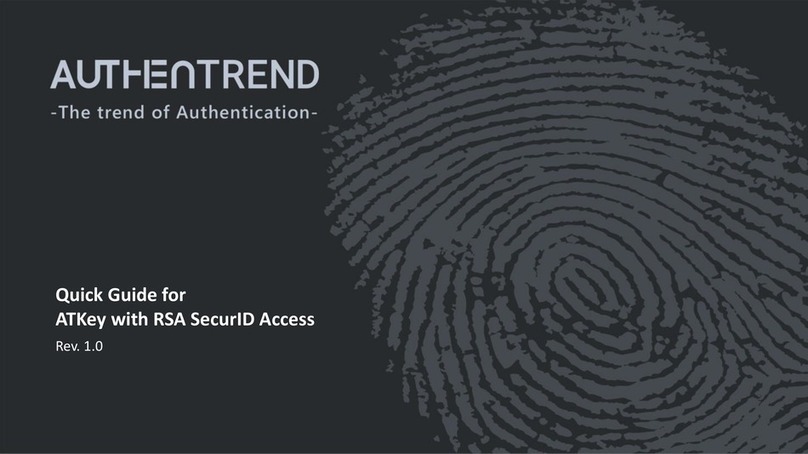
AuthenTrend
AuthenTrend ATKey quick guide
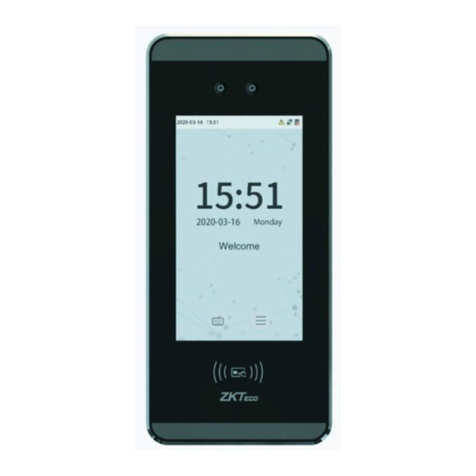
ZKTeco
ZKTeco MiniAC Plus user manual
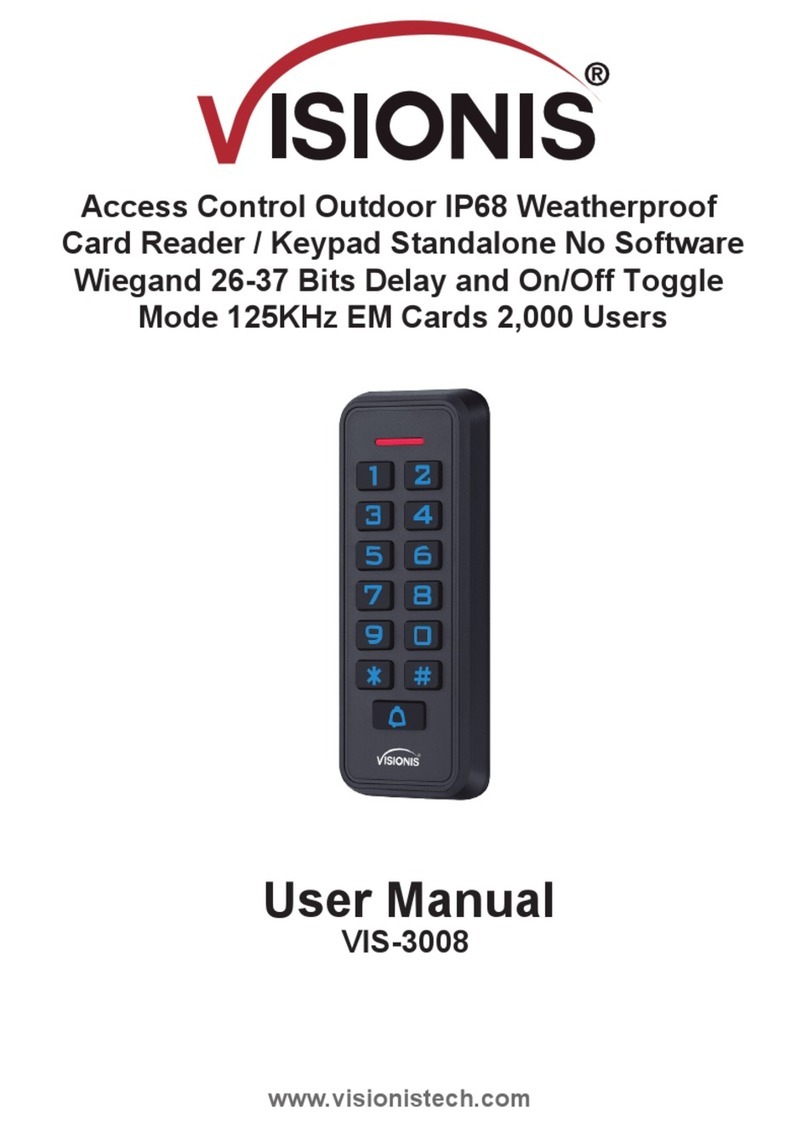
Visionis
Visionis VIS-3008 user manual
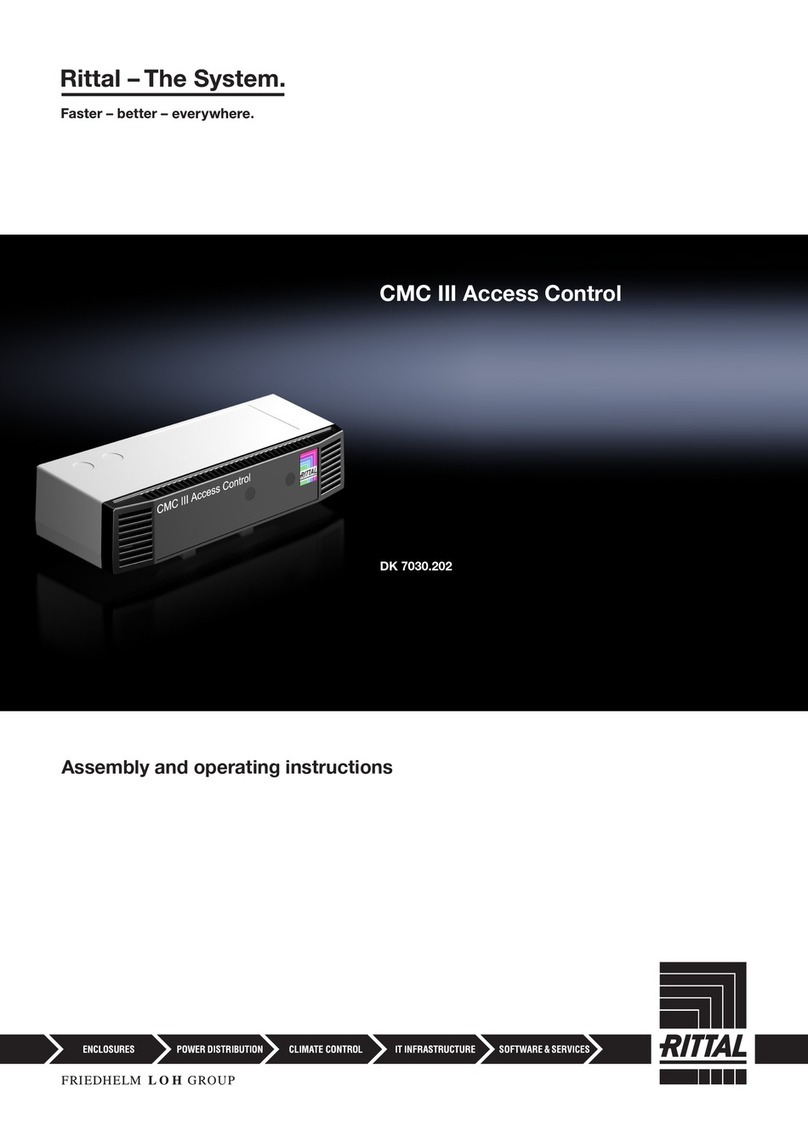
FRIEDHELM LOH
FRIEDHELM LOH Rittal CMC III DK 7030.202 Assembly and operating instructions
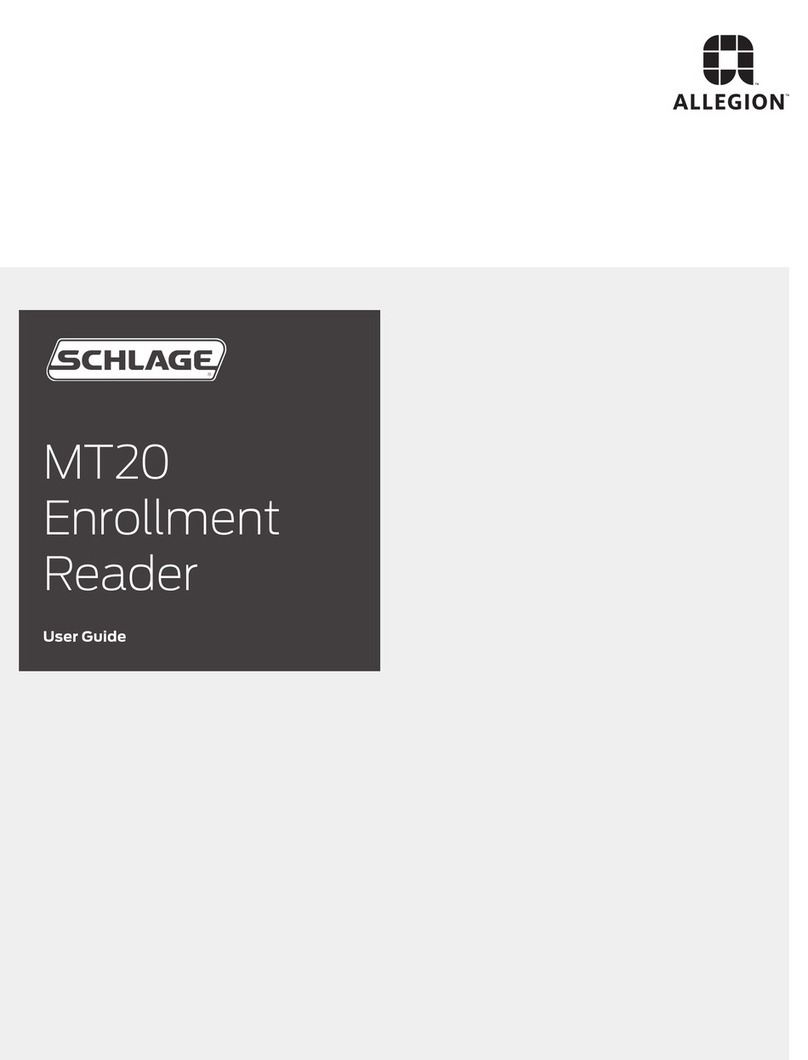
Schlage
Schlage MT20 user guide