Tamson Instruments TLV25 User manual

Tamson Instruments bv, van 't Hoffstraat 12, 2665 JL Bleiswijk, Netherlands . +31(0)10 – 522 43 73 Fax. +31(0)10 – 521 19 41
\\word\manuals\tlv25\\mantlv25.doc Date 09-2010 Rev. 1.31 UK
pag. 1 / 26
MANUAL
TLV25
KV40
KV80

Tamson Instruments bv, van 't Hoffstraat 12, 2665 JL Bleiswijk, Netherlands . +31(0)10 – 522 43 73 Fax. +31(0)10 – 521 19 41
\\word\manuals\tlv25\\mantlv25.doc Date 09-2010 Rev. 1.31 UK
pag. 2 / 26
Safety and Warnings
Make sure you read and understand all instructions and safety precautions listed in this manual, before
installing or operating the equipment. If there are any questions concerning the operation of the equipment or
about the information in this manual please contact your local dealer or our sales department first.
Performance of installation, operation or maintenance other than those described in this manual may result in
a hazardous situation and may void the manufacturers warranty.
Never operate equipment that is not correctly installed. Unqualified personnel must not operate the
equipment. Avoid damage to the equipment, or its accessories, caused by incorrect operation.
Important:
-When performing service, maintenance or moving the apparatus, always disconnect the line cord of
the apparatus,
-Proper skilled and trained personel is only allowed to operate this equipment,
-Take notice of warning labels and do not remove them,
-Refer service and repairs to qualified technician,
-If a problem persists, call your supplier or Tamson Instruments bv
Warranty
Tamson Instruments bv warrants that all equipment manufactured by it shall be free from defects in material
and workmanship, which might impair its usefulness. Tamson Instruments bv. does not warranty that the
equipment is fit for any particular use. The manufacturer is only responsible for the security, reliability and
performance of the equipment, if the unit is operated in accordance with the operating instructions,
extensions, adjustments, and when changes or repair is performed by Tamson Instruments bv or authorized
persons only. This warranty is limited to one year from date of invoicing. All equipment and materials are
further subject to tolerances and variations consistent with the usage of the trade.

Tamson Instruments bv, van 't Hoffstraat 12, 2665 JL Bleiswijk, Netherlands . +31(0)10 – 522 43 73 Fax. +31(0)10 – 521 19 41
\\word\manuals\tlv25\\mantlv25.doc Date 09-2010 Rev. 1.31 UK
pag. 3 / 26
Contents
SAFETY AND WARNINGS.......................................................................................2
Warranty .................................................................................................................................................. 2
VISCOMETER BATH TLV25 ....................................................................................5
EC declaration of conformity TLV25......................................................................................................... 5
Delivery checklist ..................................................................................................................................... 6
The TLV25, general ................................................................................................................................. 7
Installation ............................................................................................................................................... 8
Filling and Bath liquids ............................................................................................................................. 8
Cooling .................................................................................................................................................... 9
Heating .................................................................................................................................................... 9
Operating the controller ........................................................................................................................... 9
Operation .......................................................................................................................................... 10
Quick start......................................................................................................................................... 10
What is tuning ................................................................................................................................... 11
Automatic tuning................................................................................................................................ 12
Manual tuning.................................................................................................................................... 13
Manual tuning by Ziegler-Nichols ...................................................................................................... 13
Setting the cutback values................................................................................................................. 14
Faultfinding ............................................................................................................................................ 15
Technical Specs TLV25 ......................................................................................................................... 16
Spare part list TLV25 ............................................................................................................................. 17
Part number........................................................................................................................................... 17
115 Volts................................................................................................................................................ 17
CRYOSTAT KV-SERIES ........................................................................................18
EC declaration of conformity cryostat..................................................................................................... 18
Cryostat, Installation and use................................................................................................................. 19
Cryostat fails to operate ......................................................................................................................... 19
KV40 Cryostat........................................................................................................................................ 20
Technical Specs KV40 ...................................................................................................................... 21
Using the KV for other cooling purposes ........................................................................................... 21
Ordering codes KV40 ........................................................................................................................ 22
Spare part list KV40 .......................................................................................................................... 22
Part numbers ......................................................................................................................................... 22
Principal diagram KV40..................................................................................................................... 22
KV80 Cryostat........................................................................................................................................ 22
KV80 Cryostat........................................................................................................................................ 23
Technical Specs KV80 ...................................................................................................................... 23
Using the KV for other cooling purposes ........................................................................................... 23
Ordering codes KV80 ........................................................................................................................ 24
Spare part list KV80 .......................................................................................................................... 25
Part numbers ......................................................................................................................................... 25
Principal diagram KV80..................................................................................................................... 26
DISCLAIMER..........................................................................................................26

Tamson Instruments bv, van 't Hoffstraat 12, 2665 JL Bleiswijk, Netherlands . +31(0)10 – 522 43 73 Fax. +31(0)10 – 521 19 41
\\word\manuals\tlv25\\mantlv25.doc Date 09-2010 Rev. 1.31 UK
pag. 4 / 26
Tamson Instruments bv
van 't Hoffstraat 12
2665 JL BLEISWIJK
The Netherlands
We wish to thank you for the purchase of this Tamson Thermostatic Bath.
You have bought an instrument with the latest technology.
For a fast settlement of the one-year warranty, please return this warranty certificate as soon as possible to
the following fax number +31 10 521 19 41 or the above mentioned address.
Model Thermostatic bath : ………………………………………………………….
Name of your company : ………………………………………………………….
Name of user : ………………………………………………………….
Address : ………………………………………………………….
……….………………………………………………….
……….………………………………………………….
……….………………………………………………….
Tel. nr. : ……….………………………………………………….
Serial number : ……………………………….
Mains voltage: …………….. Mains Freq.: …………………Hz
Date of delivery : ……………..
Name of dealer: ……….………………………………………………….
……….………………………………………………….
………………………………….……………………….
Signature: …...………………………

Tamson Instruments bv, van 't Hoffstraat 12, 2665 JL Bleiswijk, Netherlands . +31(0)10 – 522 43 73 Fax. +31(0)10 – 521 19 41
\\word\manuals\tlv25\\mantlv25.doc Date 09-2010 Rev. 1.31 UK
pag. 5 / 26
Viscometer bath TLV25
EC declaration of conformity TLV25
Manufacturer: Tamson Instruments bv
van 't Hoffstraat 12
2665 JL Bleiswijk
The Netherlands
Product: Constant temperature bath
Model: Tamson TLV25
The products to which this statement relates, is manufactured and dully carried out in compliance with the
provisions of Directive 89/336/EEC on the approximation of the laws of the Member States relating to
electromagnetic compatibility.
The products are in conformity with the following specification:
EN 50081-1 : 1992
EN 50082-2 : 1995
EN 61000-3-2 : 1995
EN 61000-3-3 : 1995
and distracted from the test certificate of the Tamson TLC3 system
Tamson Instruments bv, The Netherlands
Ing. R.C. van Hall
Director

Tamson Instruments bv, van 't Hoffstraat 12, 2665 JL Bleiswijk, Netherlands . +31(0)10 – 522 43 73 Fax. +31(0)10 – 521 19 41
\\word\manuals\tlv25\\mantlv25.doc Date 09-2010 Rev. 1.31 UK
pag. 6 / 26
Delivery checklist
TESTING DATE
TEST TEMPERATURE
READING WITH CALIBRATED THERMOMETER
°C
TEST LIQUID
REGULATOR TYPE
POWER SUPPLY DURING TEST 230 V 115V
50 Hz 60 Hz
SAFETY CUT-OUT TESTED "DYNAMIC"
WIRING SECURED WITH TY-WRAP'S
MOTORFUSE TESTED
CONDITION MOTOR
The undersigned declares that the figures and test results mentioned in this
delivery checklist are the same as mentioned in the production checklist which
was filled-in during the assembly and testing of the bath mentioned above.
For sign please check separate calibration certificate.

Tamson Instruments bv, van 't Hoffstraat 12, 2665 JL Bleiswijk, Netherlands . +31(0)10 – 522 43 73 Fax. +31(0)10 – 521 19 41
\\word\manuals\tlv25\\mantlv25.doc Date 09-2010 Rev. 1.31 UK
pag. 7 / 26
Cooling TLV25 with KV40 and KV80
[Ref
TLV25_15.XLS]
-70.000
-60.000
-50.000
-40.000
-30.000
-20.000
-10.000
0
10.000
20.000
30.000
0:00
0:30
1:00
1:25
2:00
2:30
3:00
3:30
4:00
4:30
5:00
5:30
6:00
6:30
7:00
7:30
8:00
Time [hrs]
Temp °C
KV80
KV40
The TLV25, general
The Tamson model TLV25, low temperature viscometer bath is designed to perform a variety of accurate
temperature controls for e.g. low temperature viscosity measurements.
The TLV25 system contains a 25 liter Dewar flask. The fluid in the flask must permanently be cooled by an
external cryostat. The temperature set point is maintained via a microprocessor controlled heating element.
Depending on the type of cryostat used, minimum end temperatures of minus 30°, -60°C or -80°C can be
reached. Temperatures are measured in 25 liters of Methanol with the KV40 and KV80 cryostats. At these
minimum temperatures still enough energy is provided to maintain stable temperature when glas work is
placed in the bath. The system accuracy conforms to ASTM D445 and ISO 3103 description. The bath is
inside illuminated by a fluorescent light build-in behind the Dewar flask.
The cryostat is a separate apparatus and must have enough capacity to cool 25 ltrs of liquid. It is further
important that the cooling power supplied by the cryostat is very stable. It is for these reasons that we
strongly recommend a combination of the TLV25 with the KV40 or KV80.
Span
Depending on the used cryostat:
- Minus 30°C with KV40
- Minus 60°C with KV80
-Minus 80°C with KV80S
-Lower temperatures on request
Accuracy
The set point can be set in steps of 0,1°C
from - 90°C up to plus 70°C. Overall
system accuracy is better than ±0,04°C.
Read-out is on a 4 digit, 7 segment LED
display in 0.1 °C. On request read-oud
also is available in °F.
Safety thermostat
To prevent problems caused by a
malfunctioning of the heating element the
bath is equiped with a safety thermostat.
This thermostat can not be adjusted, and
has a fixed preset value of 125°C. When for
any reason the temperature of the bath will raise to this limit

Tamson Instruments bv, van 't Hoffstraat 12, 2665 JL Bleiswijk, Netherlands . +31(0)10 – 522 43 73 Fax. +31(0)10 – 521 19 41
\\word\manuals\tlv25\\mantlv25.doc Date 09-2010 Rev. 1.31 UK
pag. 8 / 26
the safety thermostat will cut the mains supply
Circulation pumping device
The bath is equipped with a special stirrer-pump combination which ensures a good uniformity.
Condensation prevention
To prevent build up of condesat onto the cold surface of the window, surface heaters have been installed
around the window.
A temperature sensor on the window keeps the surface temperature of the window just above the dew-point
under ambient conditions of up to 40 °C and 85% RH.
Illumination
An illuminator providing diffused fluorescent light for background lighting is mounted on the roar of the bath. It
can be switched on and off with the switch-lamp on the control panel.
Top plate
The bath is supplied with a round lid with 3 holes 50 mm diameter to accept 3 capillary type viscometers in
holders. Behind each viscometer position there is an opaque glass plate for easy reading of viscometer.
Installation
Tamson baths are carefully packed when they leave the factory to avoid damage during transport.
Check the packing for any external damage and make a note on the shipping documents if any damage is
found. Always retain the cartons and packing material until the bath has been tested and found in good
condition, because transport companies generally will not honour a claim for damages if the respective
box(es) is (are) not available for examination.
- Clean inner bath thoroughly of any loose packing materials etc.
- Place the bath in a level position.
- Check operating voltage (230 V or 115 V) and connect the bath to appropriate mains supply. The bath has
to be filled with a liquid suitable for operating temperature.
WARNING: Never operate the bath without fluid !!!!
Filling and Bath liquids
Fill the bath up to 5 -10 mm below the lid. At no time should the bath level be allowed to fall 60 mm of the top
plate. Depending on the bath temperature we advise the use of methanol as bath fluid.
Use a mains supply that is well earthened and clean o inter erens and can carry
the load o the bath. Be sure to check the power requirements (230V / 115V)
marked on the tag plate at the back side o the bath.
When using a Cryostat KV80 or KV40, the use o the mixture water
and ethyleneglycol is not recommended because o the high capacity o the cooler.
(ice will grow on the evaporator causing poor heat exchange and unstable
temperature control
)

Tamson Instruments bv, van 't Hoffstraat 12, 2665 JL Bleiswijk, Netherlands . +31(0)10 – 522 43 73 Fax. +31(0)10 – 521 19 41
\\word\manuals\tlv25\\mantlv25.doc Date 09-2010 Rev. 1.31 UK
pag. 9 / 26
Cooling
Low temperatures are reached with the use of a cryostat (immersion cooler). The top-plate
of the bath provides a hole of 50 mm diameter to accept the evaporator of
the immersion cooler. To reach temperature stability which conforms ASTM D445 only use the KV40 or KV80
as cryostat.
Heating
To reduce temperature fluctuations the cryostat provides stable cooling. To settle the bath temperature at a
fixed set point a microprocessor controlled stainless steel heater regulates the temperature.
Operating the controller
The front panel layout of the controller is drawn below.
Model 2216 front panel layout
Number Description
1 Output 1
2 N.A.
3 Set point active
4 N.A.
5 N.A.
6 Page button
7 Scroll button
8 Down button
9 Up button
10 Set point rate limit active
11 Lower readout
12 Upper readout
When the controller is activating the heater the indicator on the controller "OP1" will blink.
2216
OP1
OP2
SP2
REM
RUN
MAN
1
4
3
2
5
6 7 8 9
10
11
12

Tamson Instruments bv, van 't Hoffstraat 12, 2665 JL Bleiswijk, Netherlands . +31(0)10 – 522 43 73 Fax. +31(0)10 – 521 19 41
\\word\manuals\tlv25\\mantlv25.doc Date 09-2010 Rev. 1.31 UK
pag. 10 / 26
Operation
The front panel layout shows following 4 operating keys:
Page
List
Down
Up
The “Page” Key offers following:
•
Temperature readout in °C,
•
Temperature set point in °C, value between –90 and +60°C,
•
Tuning the bath (“Atune”),
•
Changing the tuning (PID) parameters,
•
The ”List” Key will list the P, I, D, High Cutback and Low Cutback options,
•
Changing the temperature calibration offset,
•Programming the bath(ACCS).
*
This menu item has only been build in for servicing purpose and should
not be used by users.
Up and Down keys allow changing the listed value. All changed values like set point and PID parameters will
be kept in memory even after switching of the power supply.
Quick start
To start operating the bath in a quick way do following:
•Fill the bath with fluid until the level reaches 10 to 20 mm under the top plate,
•
Place the power plug,
•Place cold finger/cryostat,
•Switch the bath on with the mains switch,
•
Choose a working temperature (set point) with and ,
•Switch on the cryostat.
•Wait until the bath has reached its set point and choose ATUNE by pressing ,
•Now press and the display shows ”tune”,
•Press to choose “ON”,
•Press and together, the display will now alternate the values “tune” and the actual temperature,
•After a short period, depending on the set point temperature, the blinking of “tune” will stop and the bath
is ready for use.

Tamson Instruments bv, van 't Hoffstraat 12, 2665 JL Bleiswijk, Netherlands . +31(0)10 – 522 43 73 Fax. +31(0)10 – 521 19 41
\\word\manuals\tlv25\\mantlv25.doc Date 09-2010 Rev. 1.31 UK
pag. 11 / 26
What is tuning
The temperature control of the bath is based on a digital PID system. Due to the use of different fluids in the
bath with their own heat capacity, the use of external cooling and external connected processes(circulation),
the PID parameters have to be optimized after changes to the system. Tuning of the bath results in:
•Stable temperature control of the bath,
•No over- or undershoot of the temperature set point,
•Quick response to deviations from the set point caused by external disturbances.
Tuning can be done automatically or manually. The Parameters mentioned in Table 1 will influence the
control of the bath.
Parameter Description Display
Proportional band The bandwith in display-units over which the output power is
proportional between minimum and maximum
Pb
Integration time Determines the time taken by the controller to remove stady state
error signals
Ti
Derivative time Determines the time taken by the controller to react on error
signals.
Td
Low cutback The number of degrees below set point at which the controller
will cutback the output power in order to prevent overshoot on
heat up.
Lcb
High cutback The number of degrees above set point at which the controller
will cutback the output power in order to prevent undershoot on
cool down, important when working below 20°C.
Hcb
Relative offset Offset only shown for PD, or P control (I = off). [degrees] rES
Table 1 Parameters influencing the temperature control
A TLV25 system filled with methanol combined with a KV40 cryostat will give result following in table 2.
Please note that values to your system can differ extremely due to ambient and system tolerances.
Set point
temperature °
°°
°C
Pb – values Ti – values[s]
Td – values[s]
- 10 1,7 340 55
- 20 1,8 444 74
- 30 1,7 340 55
Table 2 PID values for a TLV25 with KV40
A TLV25 system filled with methanol and KV80 will give following results
Set point
temperature °
°°
°C
Pb – values Ti – values[s]
Td – values[s]
- 10 1,8 520 85
- 20 1,7 501 83
- 30 1,9 573 95
- 40 1,8 500 85
- 50 1,8 478 79
Table 3 PID values for a TLV25 with KV80

Tamson Instruments bv, van 't Hoffstraat 12, 2665 JL Bleiswijk, Netherlands . +31(0)10 – 522 43 73 Fax. +31(0)10 – 521 19 41
\\word\manuals\tlv25\\mantlv25.doc Date 09-2010 Rev. 1.31 UK
pag. 12 / 26
Automatic tuning
•Chose desired set point,
•Wait until the bath has reached the set point temperature,
•Choose with key Atune,
•Press key option “Tune”,
•Choose with key “on”,
•Press key and simultaneous, the display will show alternating the word “tune”.
The controller will shortly oscillate the temperature in the bath and from the reaction of the bath it will
calculate the “P”, “I” and “D” parameter. It will store these parameters and returns to its controlling function.
The bath will show its actual temperature on the display. The tuning parameters are kept in memory after
power has been shut off.
The time needed for auto tuning the system depends mainly on the cool-down time of the bath. Due to
thermo dynamic law the tuning time behaves like an exponential function of the bath temperature.
Auto tuning should in all cases give you an optimal result. There are cases in which you want to tune by hand
and set the PID parameters yourself. Following will describe how to manage that.
•Choose set point temperature,
•Wait until the bath has reached its set point temperature,
•Choose key to show PID,
•Press for Ti or Td parameter,
•Change the value or press enough times so that the display shows “Off”,
•Choose with Atune,
•Press to show “Tune”,
•Press for “on”,
•Press and to confirm tuning and display will alternate “tune” and bath temperature,
If PI or P control has been chosen, the reached end temperature in the bath will always deviate from the set
point temperature. To eliminate this error, the value off the error has to be appointed to the rES parameter in
the PID menu. This parameter will only be visible when P or PI control is activated.
To eliminate the error offset do following:
•Choose PID with ,
•Press for rES,
Tip. To allow optimal temperature control o the bath luid, the bath has to be tunded
a ter ollowing changes:
-Other type o luid used in the bath,
-Change o luid level
-Setoint which deviates more than 5°
°°
° o previous tuning set point,

Tamson Instruments bv, van 't Hoffstraat 12, 2665 JL Bleiswijk, Netherlands . +31(0)10 – 522 43 73 Fax. +31(0)10 – 521 19 41
\\word\manuals\tlv25\\mantlv25.doc Date 09-2010 Rev. 1.31 UK
pag. 13 / 26
•Adjust value to eliminate offset with and ,
•Press and at the same time to confirm and show bath temperature reading.
Manual tuning
The parameters for the PID control can also be changed manually. Again this procedure is only to be
followed when automatic tuning is not functioning.
PID parameters can be accessed by pressing:
•Key for 3 times, display shows “PID”,
•Key , display shows PD which is the proportional value,
•Change PD value with and ,
•Key , display shows Ti which is the integrator value in seconds,
•Change Ti value with and ,
•Key , display shows Td which is derivate value in seconds,
•Change Td value with and ,
•Key , display shows Lcb,
•Do not change “auto” value,
•Key , display shows Hcb,
•Press and at the same time to confirm and show bath temperature reading.
The control also allows to set the I and D values to zero. The bath will then function as a proportional system.
The “P” parameter can than be varied to an optimal value by trial and error. A higher P will stabilize the
system when I and D are off. The PID parameters can also be determined with the use of the Ziegler Nichols
method described below.
Manual tuning by Ziegler-Nichols
With the process at its normal running temperature:
1 Set the integral time “Ti” and the derivate Time “Td” to off
2 Check if the Lcb and Hcb are set to auto
3 Ignore the fact that the temperature may not settle precisely at the set point
4 If the temperature is stable, reduce the proportional band Pb so that the temperature just starts to
oscillate. If the temperature is already oscillating, increase the proportional band until it starts
oscillating. Allow enough time between each adjustment for the loop to stabilize. Make a note of the
proportional band value “B” and the period of oscillation “T” Set the Pb, Ti and Td parameter values
according to the calculations given in the table below
Type of control Proportional band “Pb” Integral time “Ti” Derivative time “Td”
Proportional only 2*B Off Off
P + I control 2,2*B 0,8*T Off
P + I + D control 1,7*B 0,5*T 0,12*T

Tamson Instruments bv, van 't Hoffstraat 12, 2665 JL Bleiswijk, Netherlands . +31(0)10 – 522 43 73 Fax. +31(0)10 – 521 19 41
\\word\manuals\tlv25\\mantlv25.doc Date 09-2010 Rev. 1.31 UK
pag. 14 / 26
Overshoot
Time
T
Undershoot
Time
T
Setting the cutback values
The above procedure sets up the parameters for optimum stady state control, If unacceptable levels of
overshoot or undershoot occur during start-up for large step changes in temperature, then manually set the
cutback parameters Lcb and Hcb.
Set the low and high cutback values to three times the proportional bandwith (That is to say, Lcb = Hcb = 3 *
Pb)
See the examples in drawing 2 and 3 for over- and undershoot.
Drawing 2 Drawing 3
Set point Set point

Tamson Instruments bv, van 't Hoffstraat 12, 2665 JL Bleiswijk, Netherlands . +31(0)10 – 522 43 73 Fax. +31(0)10 – 521 19 41
\\word\manuals\tlv25\\mantlv25.doc Date 09-2010 Rev. 1.31 UK
pag. 15 / 26
Faultfinding
The motor is not running and the lamps are not on.
Check the main voltage and all electrical connections, including switches.
Mechanical over temperature cut-out +70 °C is de-activated and can be reset by pressing the reset button on
the back panel near the power supply cable.
Mechanical max. current protection ( 16A ) is de-activated. This fuse is located on the back panel of the
TLV25
Motor is not running, lamps and electronics operate and the motor turns freely by hand.
Motor fuse has deactivated motor. Reset fuse by pushing button on panel.
Motor overloaded. The motor protection may trip because of mechanical overloading of the pump.
The 7 µF capacitor is faulty. Replace motor capacitor located behind the front panel.
Loose connection is possible. Check wiring at rear of motor cover.
Minimum temperature is not reached
There are three possible causes:
1) The KV80 is defective
2) There is a lot of ice forming around the KV80 probe
3) The methanol used is very poluted with water due to condensat and ice forming
Ad 1)The KV80 can only be tested on performance when the TLV25 is completely free of ice and the
methanol used is fresch. The cooling down period of the KV80/TLV25 combination is indicated in the manual
see chapter “The TLV25, general”, page 7.
If the minimum temperature is not reached the filling of the refrigerant inside the KV80 is not ok. The unit
should be repaired. This is a tecnical proces only specialized companies can perform.
Ad 2+3) Free all ice from the TLV25 and KVprobe and hose. Let the unit dry in ambient and make sure there
is no moisture absorbed in the tubing of the KV80. The combination KV80/TLV25 needs good maintenance.
Refresh the methanol in teh TLV25. It's preferred to keep the unit in a moisture free environment and prevent
ice from growing on the machine. Regularly remove ice if neccessary.

Tamson Instruments bv, van 't Hoffstraat 12, 2665 JL Bleiswijk, Netherlands . +31(0)10 – 522 43 73 Fax. +31(0)10 – 521 19 41
\\word\manuals\tlv25\\mantlv25.doc Date 09-2010 Rev. 1.31 UK
pag. 16 / 26
Technical Specs TLV25
Item Unit TLV25
Window [mm] 148*213
Setting ± [°C] 0,1
Stability [°C] ±0,03
Heating [W] 780
Heaters
1
Bath volume [L] 25
Opening [mm] 162(diameter)
Depth [mm] 400
Length [mm] 570
Width [mm] 410
Heigth [mm] 540
Opening Cold
Finger
[mm]
Diameter: 50 * Length
240
Weight [kg] 55
Power [Watt] 920
Voltage [Volt] 230/115

Tamson Instruments bv, van 't Hoffstraat 12, 2665 JL Bleiswijk, Netherlands . +31(0)10 – 522 43 73 Fax. +31(0)10 – 521 19 41
\\word\manuals\tlv25\\mantlv25.doc Date 09-2010 Rev. 1.31 UK
pag. 17 / 26
Spare part list TLV25
TLV25 115 and 230 volts
Part number
230 Volts 115 Volts
Description
04T0100 04T0200 Pump assembly with motor
24T3300 n.a. Capacitor 7uF
n.a. 24T3330 Capacitor 25uF
24T8080 n.a. Motorfuse 0.6 Amps
n.a. 24T8090 Motorfuse 1.3 Amps
05T1160 05T1180 Stainless steel heater
24T9180 24T9190 Heater – on – lamp
28T3015 28T3015 Temperature controller 85..250V
24T8540 Mains Switch
25T2320 PT-100 115 mm
24T7080 Wall socket
24T9250 Fluorescent lamp
06T0377 PCB window heating
25T0140 Window heating 40W
2 Placed parallel @ 115V
2 placed in series @ 230V
28T0091 Sensor + wires preprogrammed for TLV25
window heating
06T0385 PCB with mains FILTER
06T1870 PCB filter for temperature controller
24T8420 Solid state
24T8585 Thermostat
26T1420 Dewar flask

Tamson Instruments bv, van 't Hoffstraat 12, 2665 JL Bleiswijk, Netherlands . +31(0)10 – 522 43 73 Fax. +31(0)10 – 521 19 41
\\word\manuals\tlv25\\mantlv25.doc Date 09-2010 Rev. 1.31 UK
pag. 18 / 26
CRYOSTAT KV-Series
EC declaration of conformity cryostat
Manufacturer: Tamson Instruments B.V.
van 't Hoffstraat 12
2665 JL Bleiswijk
The Netherlands
Product: Cryostat Immersion Cooler
Model: Tamson KV40 and KV80
The products to which this statement relates, are manufactured and dully carried out in compliance with
following CE norms:
- EN 292
- Pr EN 378
- EN 60204
- RLK. 97.
Maximum working pressure level of 30 bar is confirmed.
The equipment conforms with all the specifications and norms in this regard.
The equipment conforms without any further notice.
On each apparatus following pressure and leak tests have been carried out with positive result
- Low pressure side 20 bar
- High pressure side 30 bar
Zoetermeer, The Netherlands
Ing. R.C. van Hall
Director

Tamson Instruments bv, van 't Hoffstraat 12, 2665 JL Bleiswijk, Netherlands . +31(0)10 – 522 43 73 Fax. +31(0)10 – 521 19 41
\\word\manuals\tlv25\\mantlv25.doc Date 09-2010 Rev. 1.31 UK
pag. 19 / 26
Cryostat, Installation and use
Put the unit in its proper place. Leave enough room around the cryostat for sufficient air circulation. Place the
unit in a clean working environment and keep away from dust. When air can not circulate well the cryostat
will overheat itself resulting in irreversible and severe mechanical damage. Dust will block the condensor and
might also cause overheating of the system. Overheating will cause severe damage to the compressor.
The cold finger can be placed in the TLV25 holder, next to the three opening lids for the viscosity meter
holders. When the TLV25 is fully filled with methanol the cryostat can be switched on. In all cases water is
not recommended to use in combination with a cryostat. Water will freeze very quick around the cooling coil
preventing proper energy exchange between the cold finger and the bath fluid.
It is possible to cool down other processes with the cold finger i.e. rapidly lower temperature in hot fluids. It is
not recommended to permanently cool fluids with a temperature above 80°C. Pressure inside the evaporator
circuit will be extremely high and can causing severe thermal damage to the compressor.
Regularly check:
The apparatus to see if airflow is not blocked around apparatus,
Apparatus and condensor are free from dust,
Hose is not mechanically damaged.
Cryostat fails to operate
Check if apparatus is switched on and power is on mains. Check mains fuse. The KV40 has no fuse build in,
the KV80 has a fuse on the front panel next to the power switch.
•Fan does not function
Check wiring inside apparatus and see if nothing is blocking the fan
•Ventilator makes noise
Open apparatus and check blocking of the fan. After several years bearings can be worn out. replace fan.
•Ice forming on cold finger
Water vapour in the air condensates on the top of the cold finger. In time this ice will grow, forming a block of
ice. Turning of the cryostat and let the ice melt, or prevent air from forming condensate by insulating the cold
finger.
•Bad cooling due to forming of ice (crystals).
Do not use water or water glycerine mixture as a bath medium. Instead use methanol.
It is advised not to move the refrigeration hose at low temperatures. Only move the
apparatus
and hose when switched off and cold finger at room temperature.

Tamson Instruments bv, van 't Hoffstraat 12, 2665 JL Bleiswijk, Netherlands . +31(0)10 – 522 43 73 Fax. +31(0)10 – 521 19 41
\\word\manuals\tlv25\\mantlv25.doc Date 09-2010 Rev. 1.31 UK
pag. 20 / 26
Cooling 40 litres of oil down from different
temperatures with KV40 (a,b,d,f) and without
(c,e,g)
[Ref. TV40_30A.XLS]
20.000
30.000
40.000
50.000
60.000
70.000
80.000
90.000
100.000
110.000
120.000
130.000
140.000
150.000
160.000
170.000
0:00
2:00
4:00
6:00
8:00
10:0
12:0
14:0
16:0
17:0
20:0
Time [hrs]
Temperature [°C]
a
b
c
d
e
f
g
KV40 Cryostat
The KV40 is designed for cooling down fluid in viscometer
baths. The combination of the KV40 and our low
temperature viscosity measurement bath TLV25, allows
stable viscosity measurements at temperatures with a
minimum of minus 30°C.
To work at different temperatures, a microprocessor
controlled heating element inside the TLV25 system heats
the fluid against the constant cooling capacity of the KV40
cryostat.
Stable regulation of the KV40 / TLV25 combination is guaranteed for all working temperatures with a
minimum of approximately 2 degrees above the combinations’ minimum temperature. This minimum
temperature of –32’C is reached when the TLV25-heating is fully off.
The cooling probe of the system is formed by a stainless steel coil at the top of a flexible hose. This probe
can be immersed in the cooling fluid.
The KV40 - cooling power is measured in a Dewar flask containing 10 litres of methanol. All measured values
are based on a TLV25 system filled with 25 litres methanol.
The KV-system is guaranteed CFK/HCFK free.
Cooling power KV40
[Ref 40&80_2.XLS]
0
50
100
150
200
250
300
350
400
450
-40 -30 -20 -10 0 10 20 30
Temperature[°C]
Power [Watt]
This manual suits for next models
2
Table of contents
Other Tamson Instruments Laboratory Equipment manuals
Popular Laboratory Equipment manuals by other brands
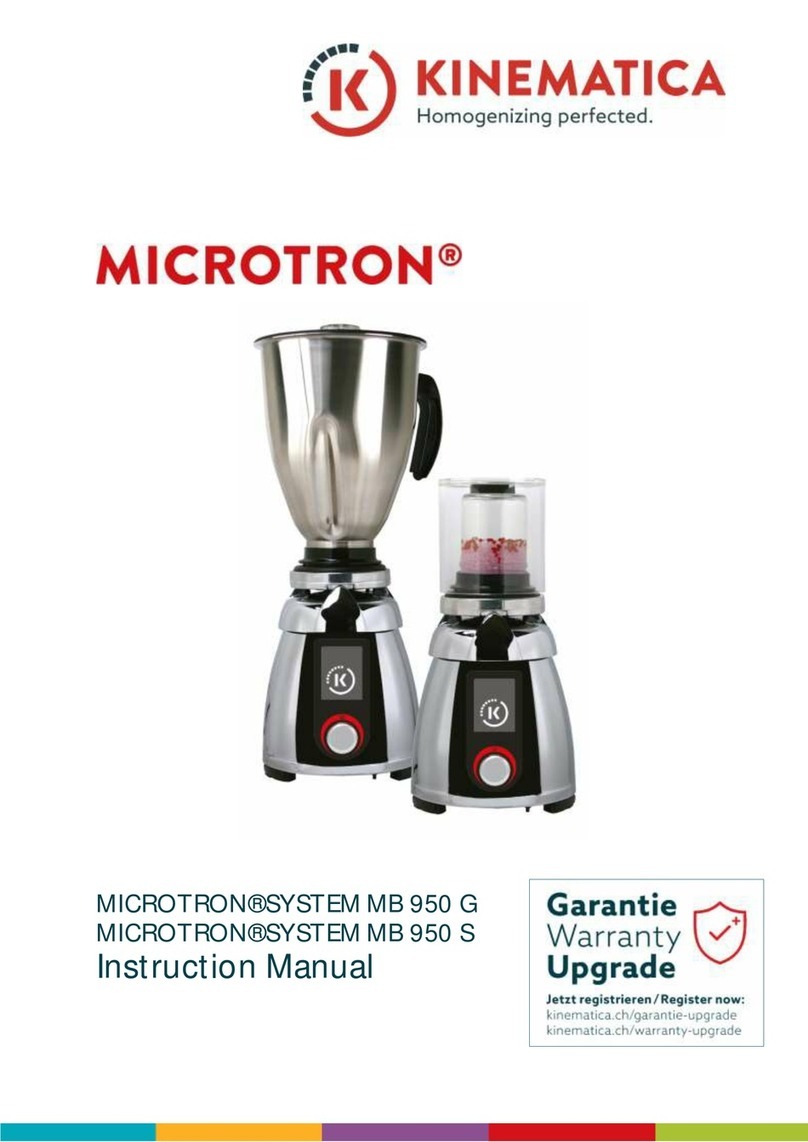
Kinematica
Kinematica MICROTON SYSTEM MB 950 G instruction manual
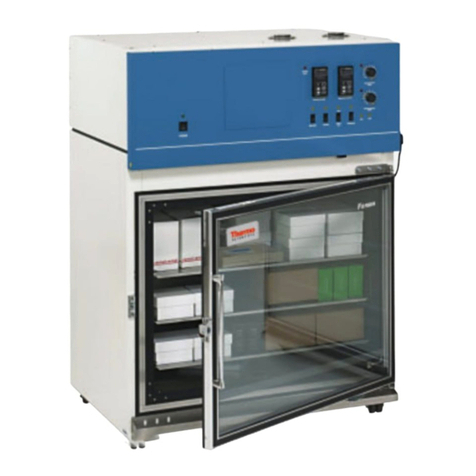
Thermo Scientific
Thermo Scientific 3911 operating manual

Bruker
Bruker Ascend 400'89 user manual
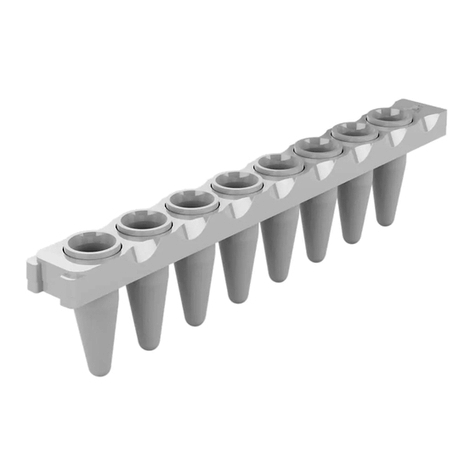
Covaris
Covaris AFA-TUBE 520292 quick start guide
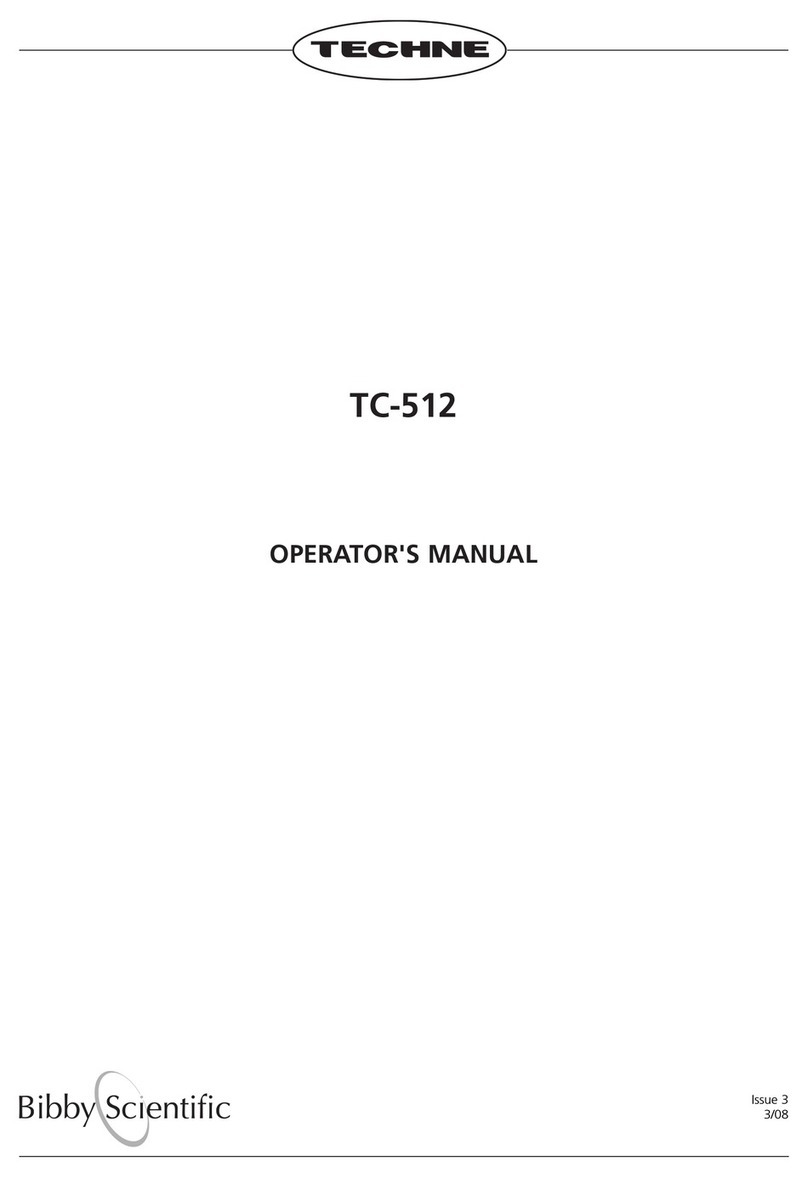
Bibby Sterilin
Bibby Sterilin Techne TC-512 Operator's manual
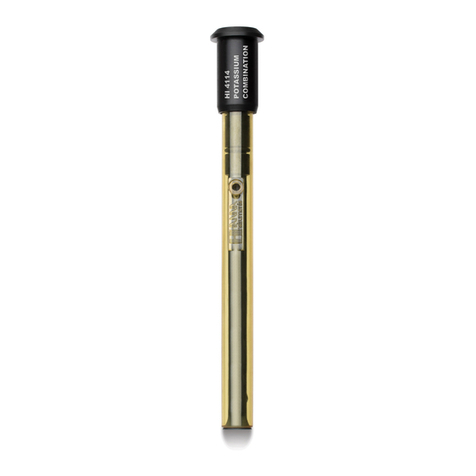
Hanna Instruments
Hanna Instruments HI 4114 instruction manual