Task Force Tips 125 Nozzle Series Manual








Other Task Force Tips Firefighting Equipment manuals
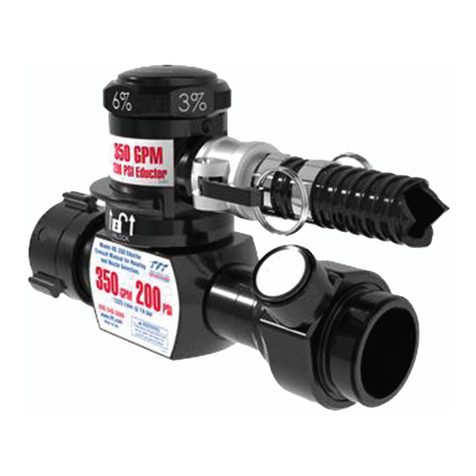
Task Force Tips
Task Force Tips 350 Series User manual
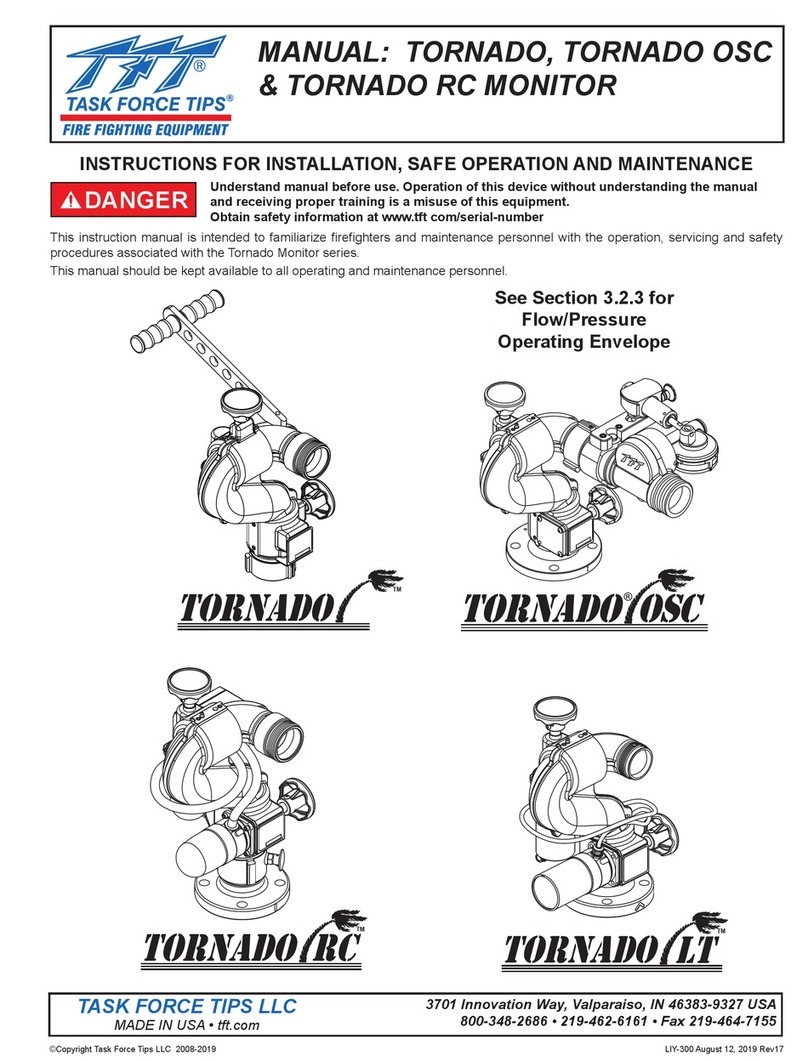
Task Force Tips
Task Force Tips TORNADO User manual
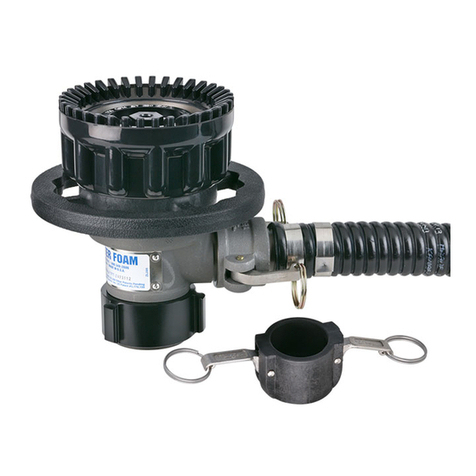
Task Force Tips
Task Force Tips Master Foam Series Programming manual
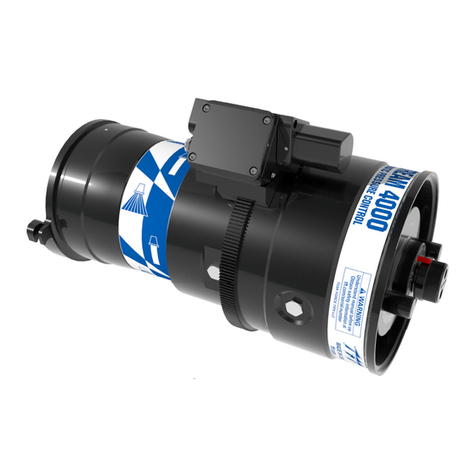
Task Force Tips
Task Force Tips Masterstream 4000 ER Automatic Quick guide
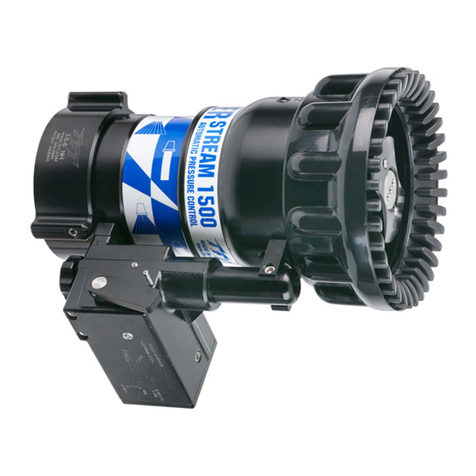
Task Force Tips
Task Force Tips Masterstream Series Programming manual
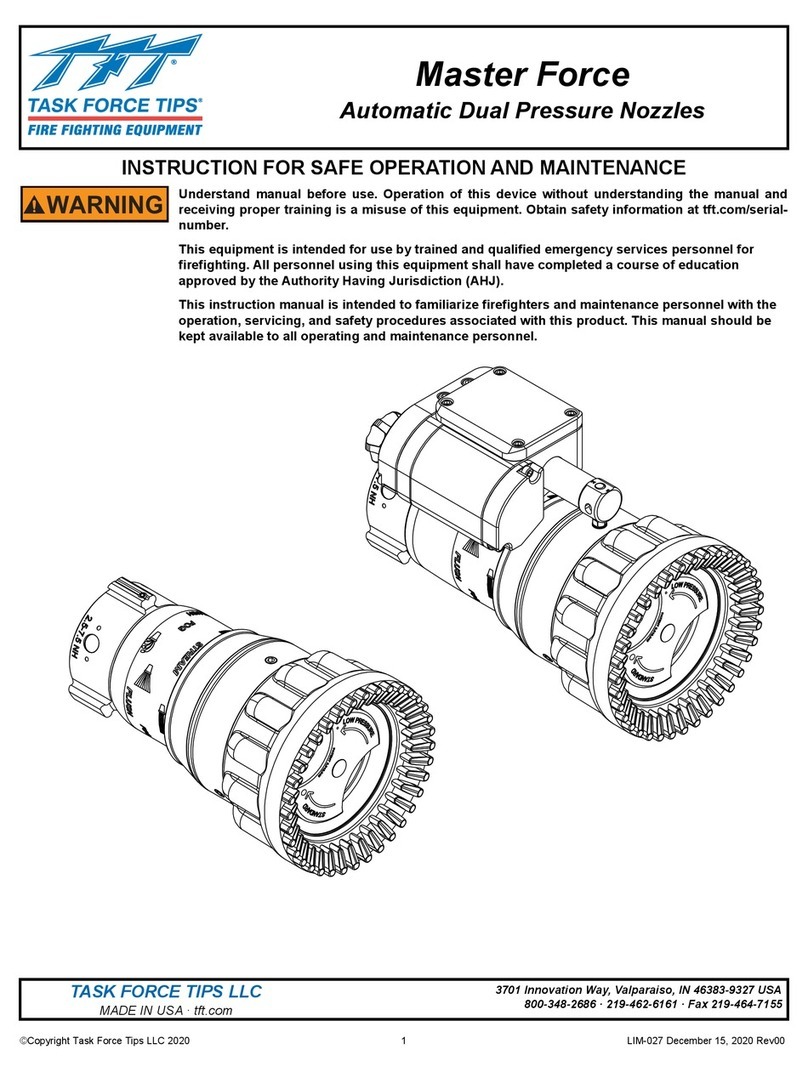
Task Force Tips
Task Force Tips Master Force Series Quick guide
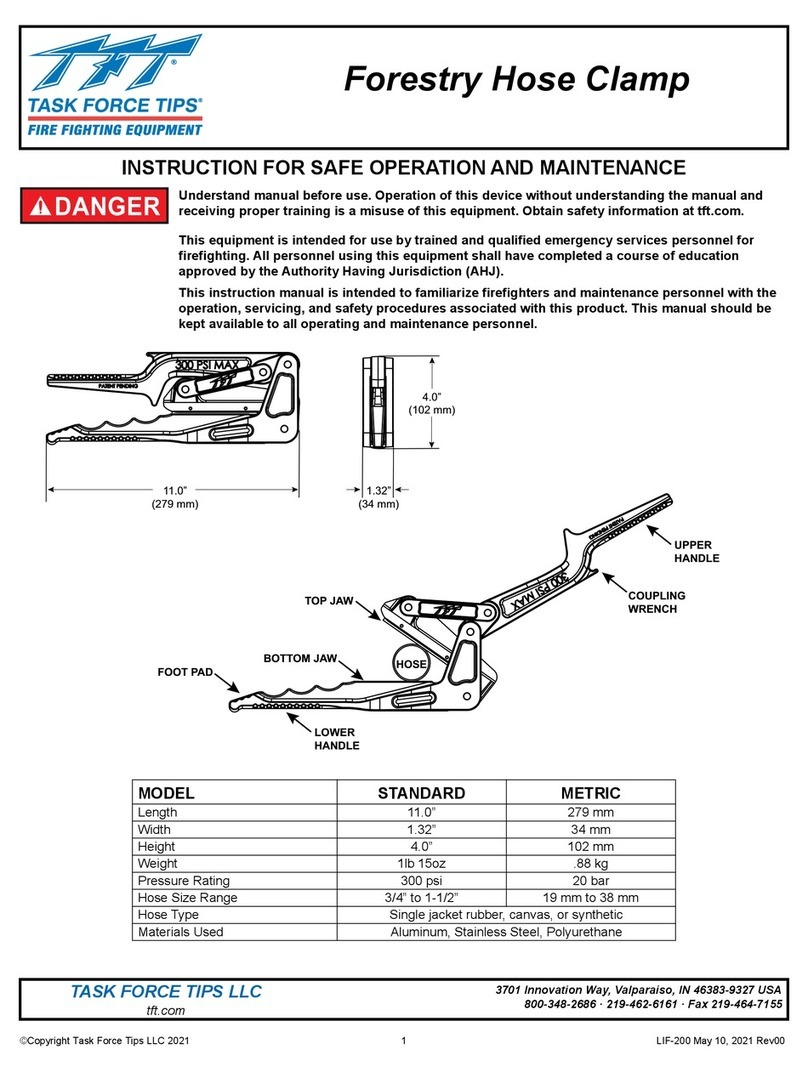
Task Force Tips
Task Force Tips STANDARD Quick guide

Task Force Tips
Task Force Tips BlitzForce Portable Monitor Programming manual
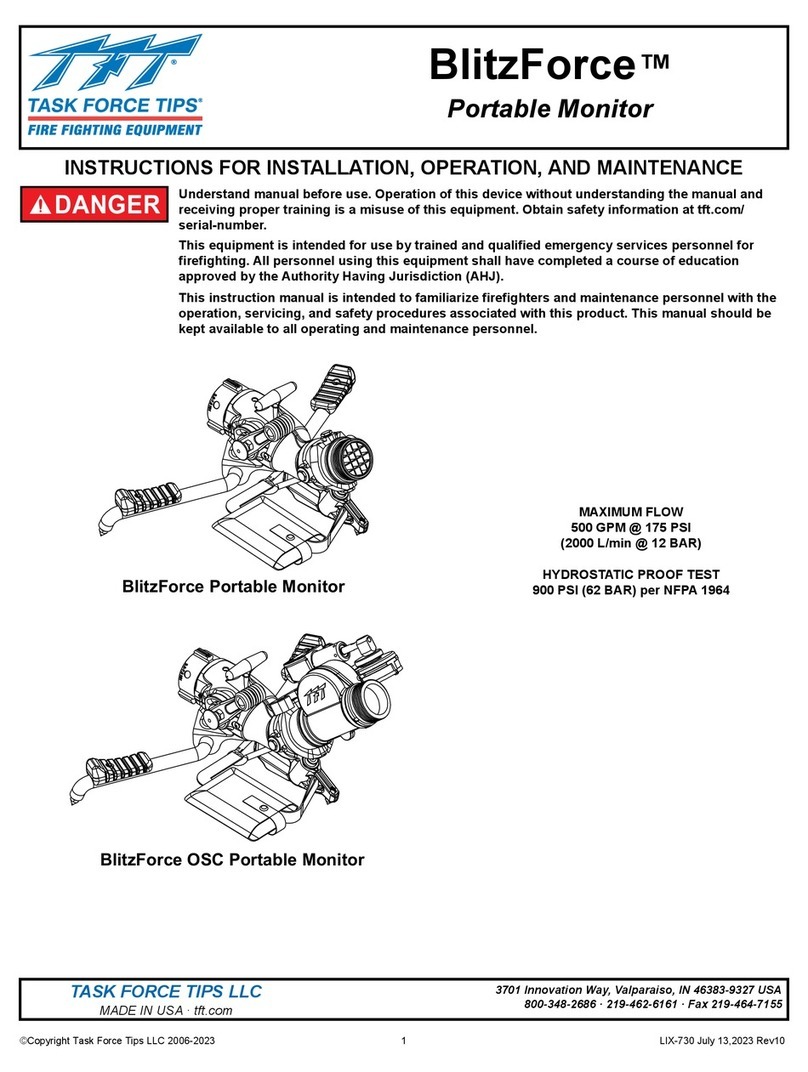
Task Force Tips
Task Force Tips BlitzForce XXLC-33-NH1 Programming manual
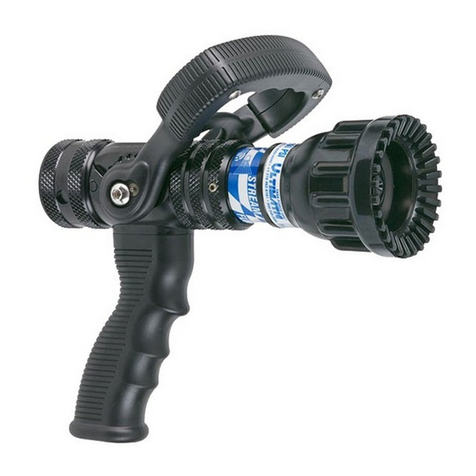
Task Force Tips
Task Force Tips Ultimatic Programming manual
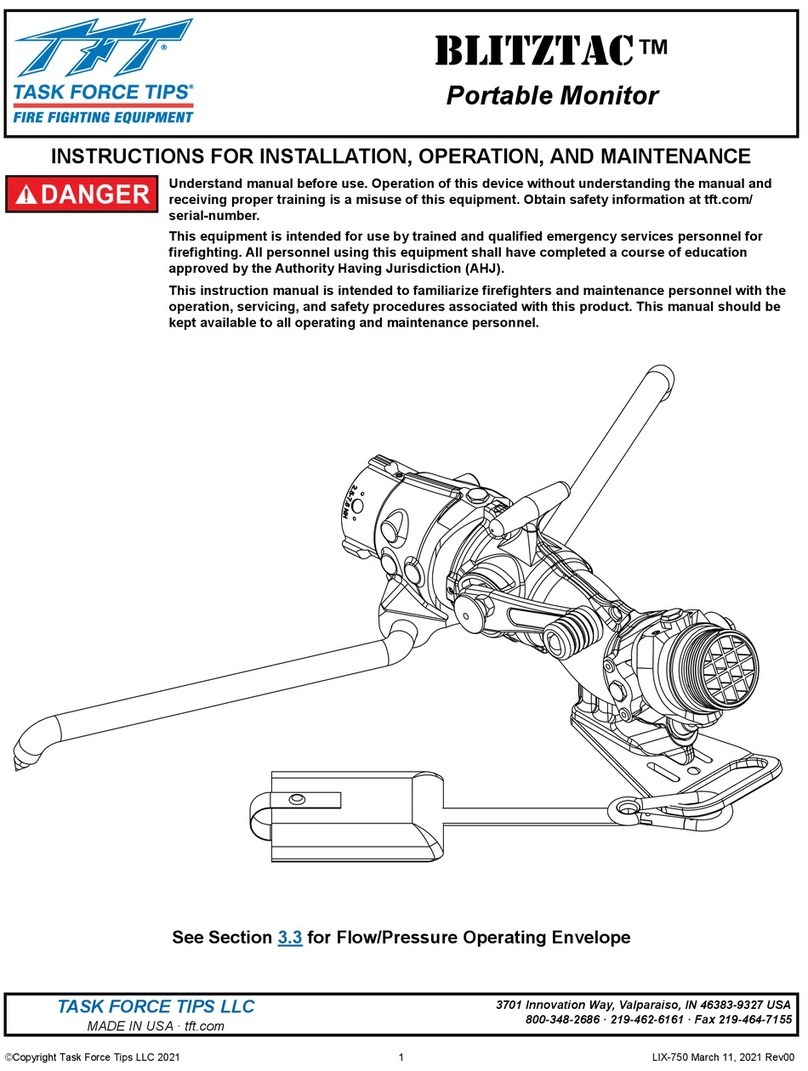
Task Force Tips
Task Force Tips BLITZTAC Portable Monitor Programming manual
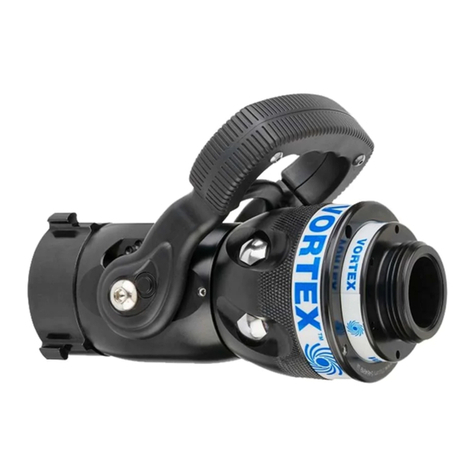
Task Force Tips
Task Force Tips Vortex 1.5" User manual
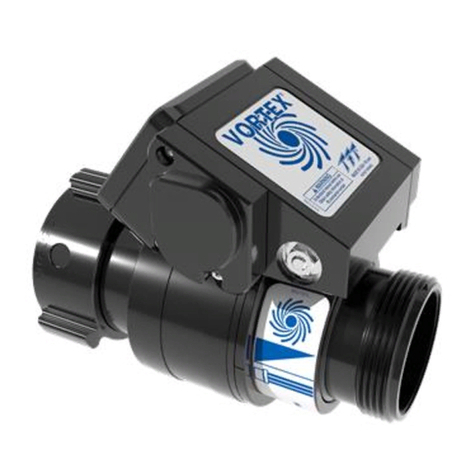
Task Force Tips
Task Force Tips VORTEX 2 ER User manual
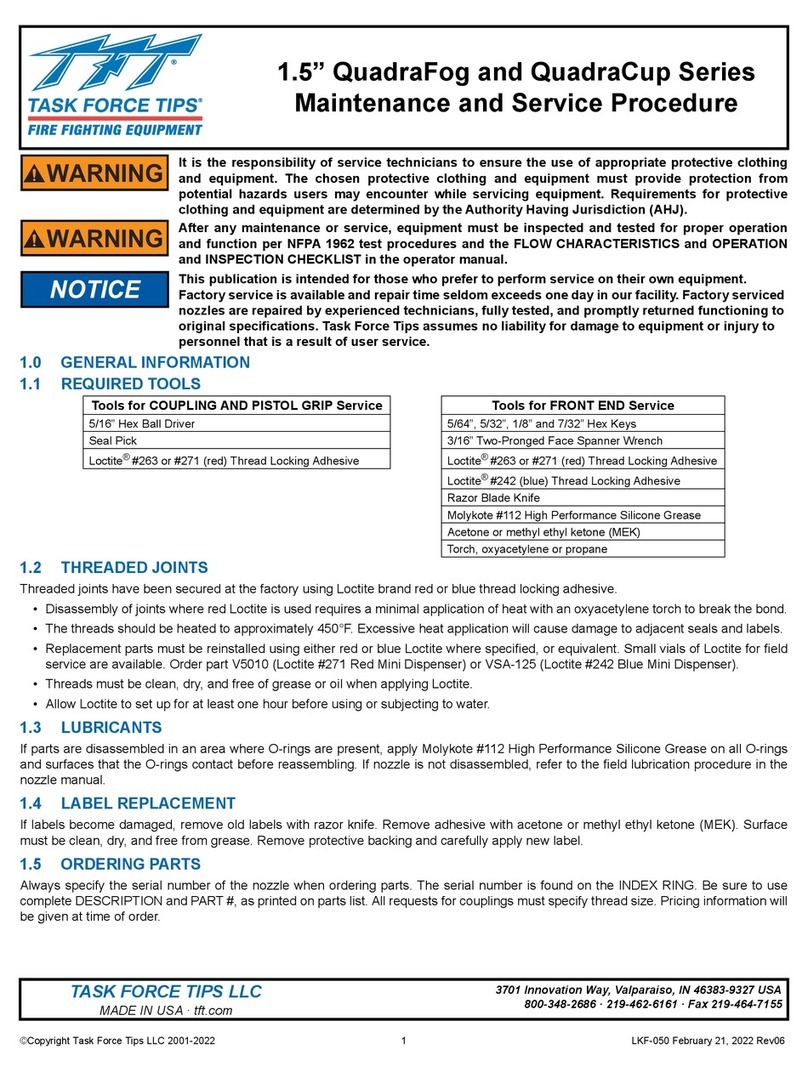
Task Force Tips
Task Force Tips QuadraFog series Manual
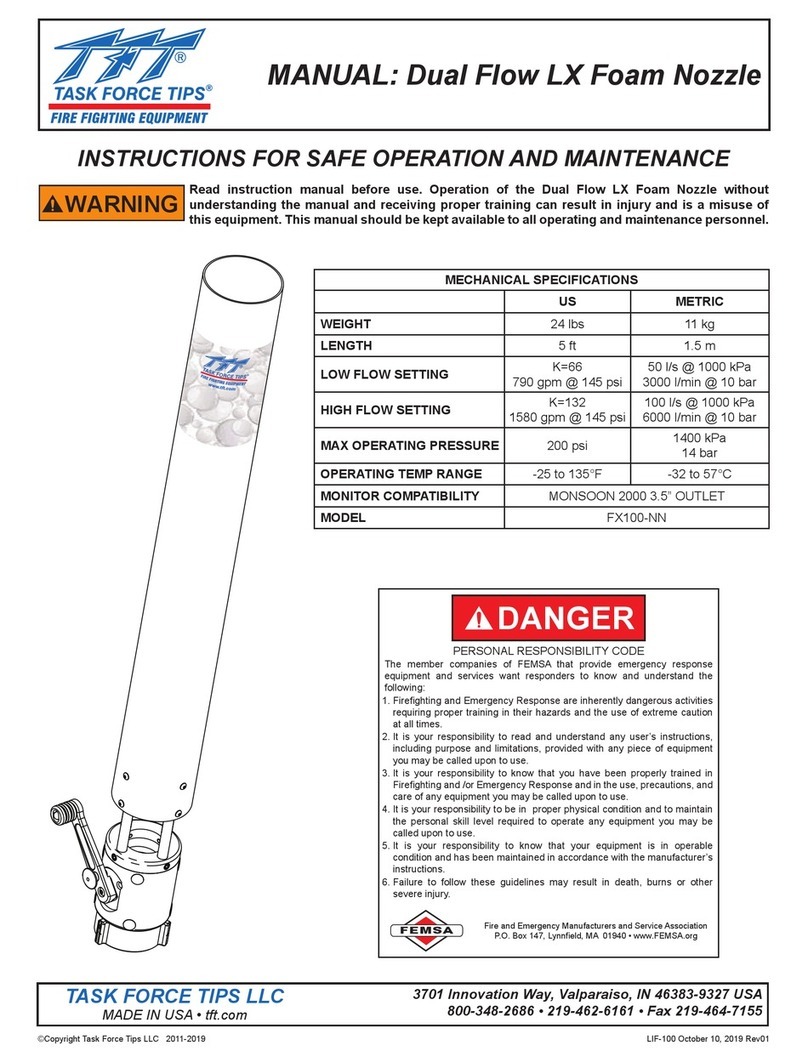
Task Force Tips
Task Force Tips FX100-NN User manual
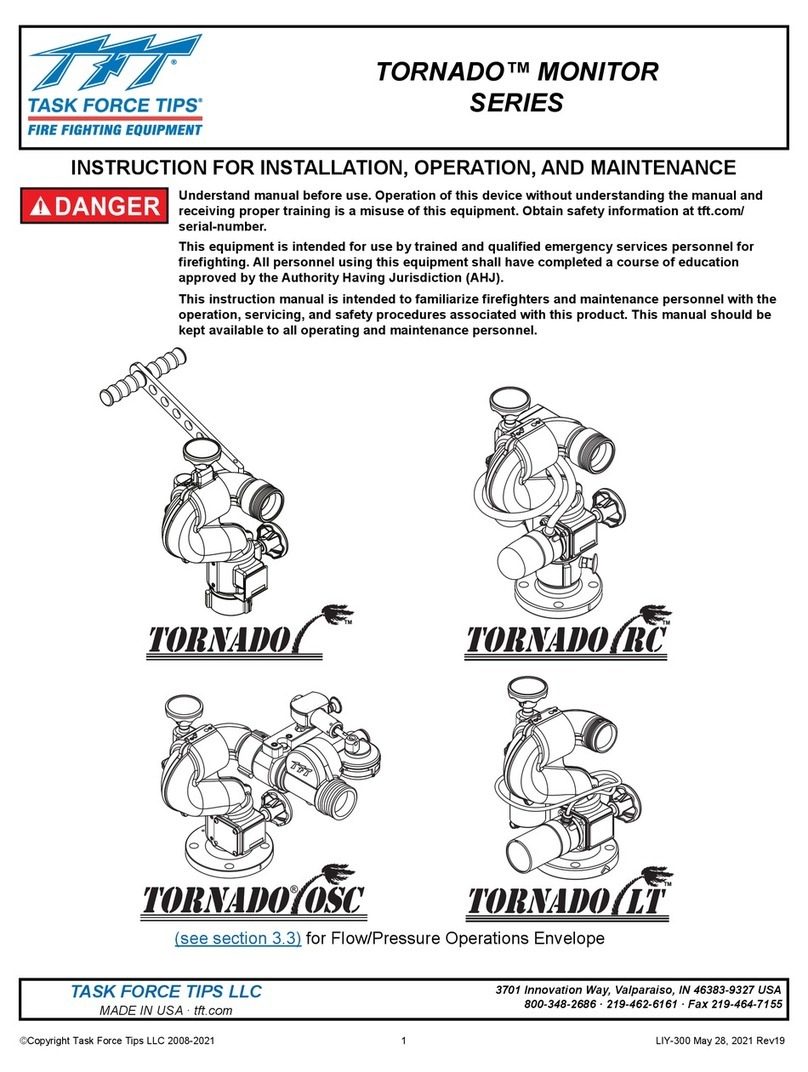
Task Force Tips
Task Force Tips TORNADO Programming manual
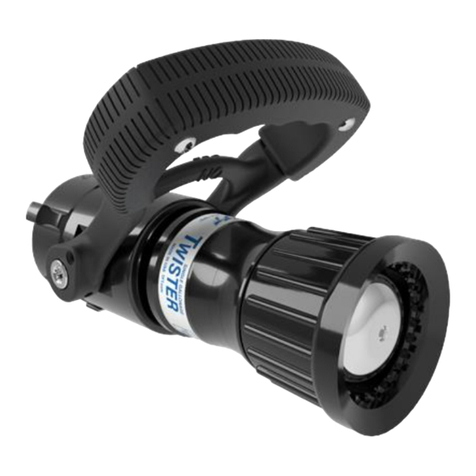
Task Force Tips
Task Force Tips Twister Series Installation instructions
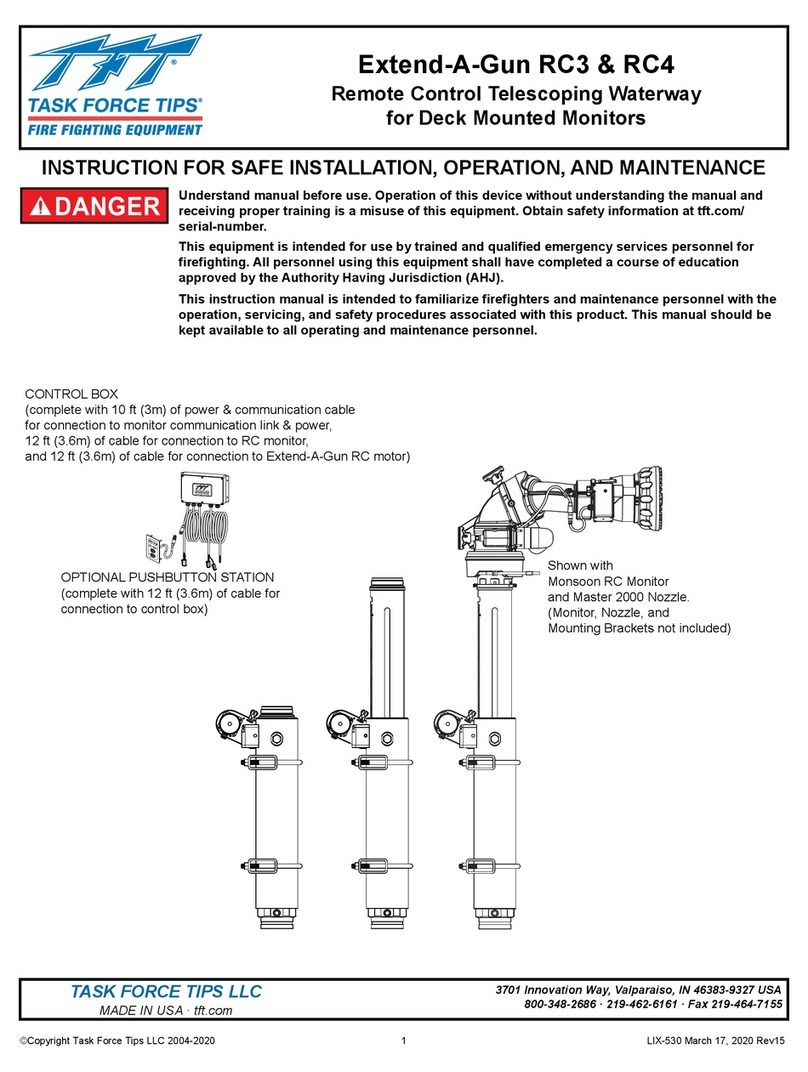
Task Force Tips
Task Force Tips Extend-A-Gun RC3 Owner's manual
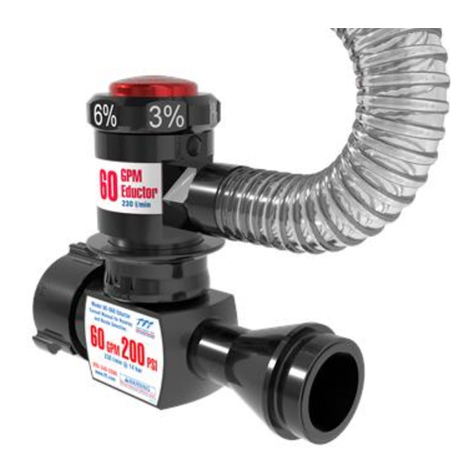
Task Force Tips
Task Force Tips EDUCTOR 125 Series Programming manual
Popular Firefighting Equipment manuals by other brands
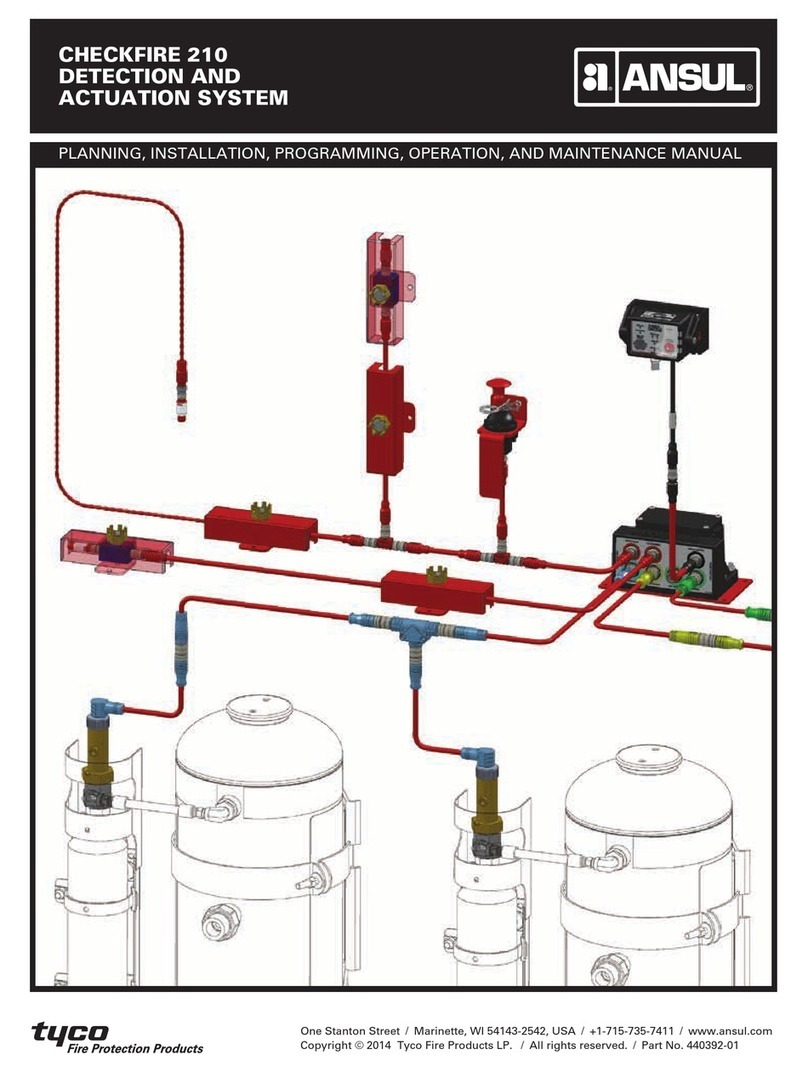
Tyco Fire Protection Products
Tyco Fire Protection Products ANSUL CHECKFIRE 210 PLANNING, INSTALLATION, PROGRAMMING, OPERATION, AND MAINTENANCE MANUAL
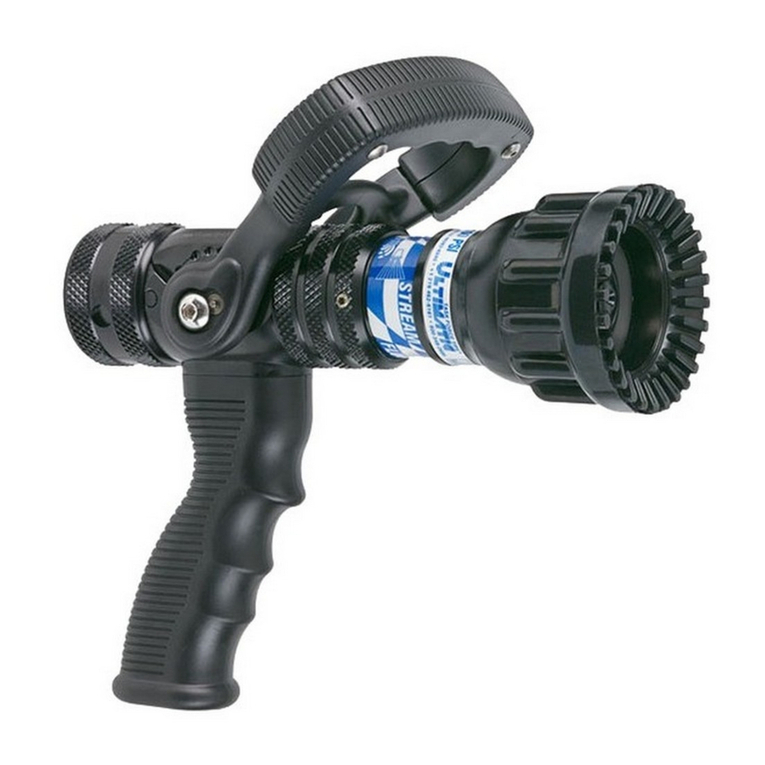
TFT
TFT ULTIMATIC Instructions for installation, operation and maintenance
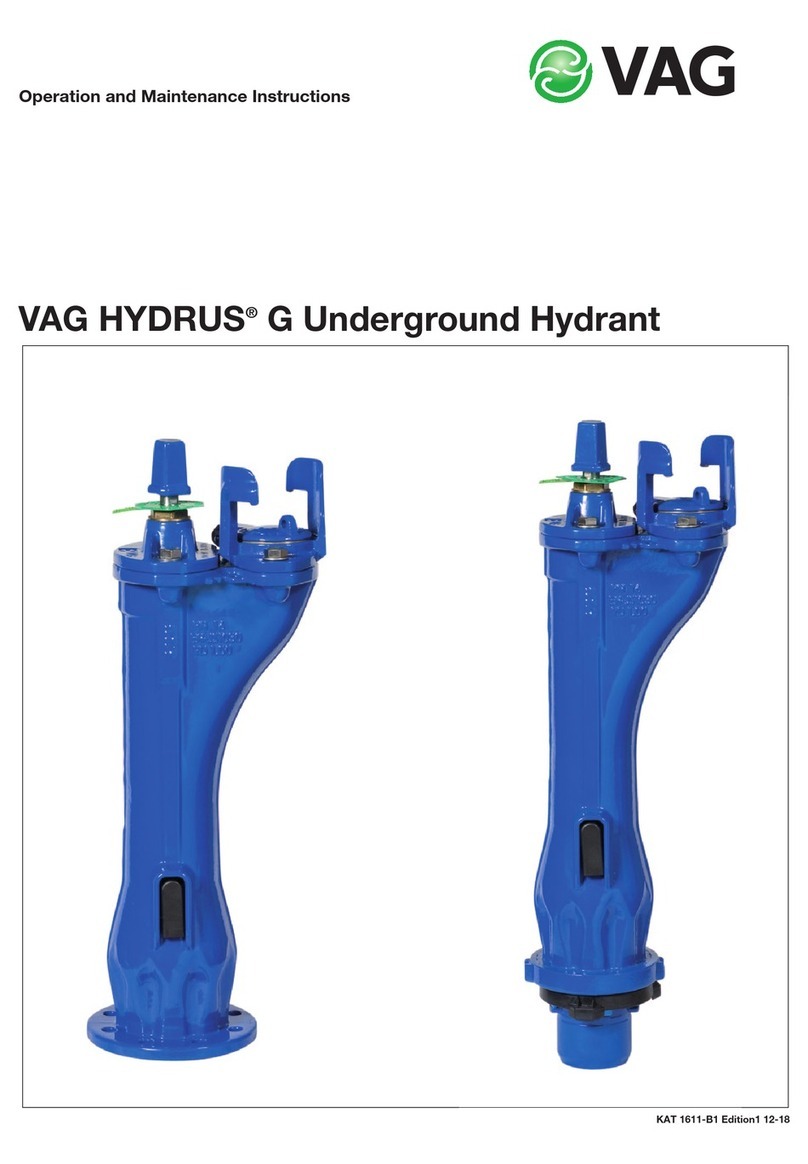
Vag
Vag HYDRUS G Operation and maintenance instruction

Waterous
Waterous 80-P Operation and maintenance instructions
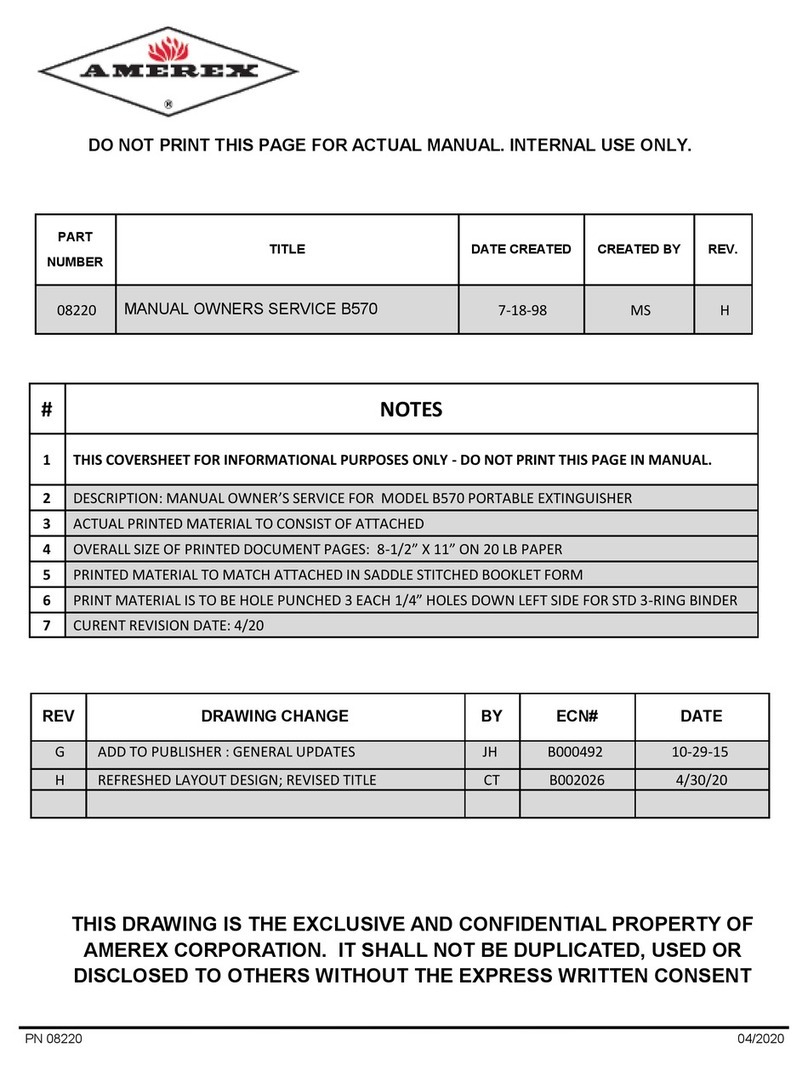
Amerex
Amerex 570 Owner's service manual

SEI Industries
SEI Industries BAMBI MAX Series Operation manual