Thermo Scientific STD5000 User manual

STD5000 & STD6000
Current to Pressure Transducers
User Guide
P/N MA45-5600-00
Revision &


© 2005 Thermo Fisher Scientific Inc. All rights reserved.
“Dow Corning” is a registered trademark of Dow Corning Corporation.
All other trademarks are the property of Thermo Fisher Scientific Inc. and its subsidiaries.
Thermo Fisher Scientific Inc. (Thermo Fisher) makes every effort to ensure the accuracy and completeness of this
manual. However, we cannot be responsible for errors, omissions, or any loss of data as the result of errors or
omissions. Thermo Fisher reserves the right to make changes to the manual or improvements to the product at
any time without notice.
The material in this manual is proprietary and cannot be reproduced in any form without express written consent
from Thermo Fisher.

This page intentionally left blank.

Thermo Fisher Scientific STD5000 & STD6000 User Guide v
Revision History
Revision Level Date Comments
5F -- --
A 06-05 Revised per ECO 4882.
B 06-06 Revised per ECO 5219.
C 10-07 Revised per ECO 5720.
D 08-08 Revised per ECO 6521.
E 04-09 Revised per ECO 6869.

This page intentionally left blank.

Thermo Fisher Scientific STD5000 & STD6000 User Guide vii
Contents
Chapter 1 Product Overview ............................................................................................. 1-1
Installation & Wiring........................................................................................ 2-1
Chapter 2
Requirements ...................................................................................... 2-1
Mounting............................................................................................ 2-2
Pneumatic Connections ...................................................................... 2-3
Electrical Connections......................................................................... 2-4
Chapter 3 Operation ............................................................................................................ 3-1
General ............................................................................................... 3-1
Programming ...................................................................................... 3-1
Chapter 4 The E-Pi Plug-In Module ................................................................................. 4-1
General ............................................................................................... 4-1
Replacing the E-Pi .............................................................................. 4-2
Fixed Orifice Replacement .................................................................. 4-3
Cleaning & Repair .............................................................................. 4-4
Calibration & the Test Jack............................................................................ 5-1
Chapter 5
Calibration.......................................................................................... 5-1
The Test Jack...................................................................................... 5-1
Calibration & Operation.................................................................. 5-1
Monitoring ...................................................................................... 5-2
Troubleshooting & Support............................................................................. 6-1
Chapter 6
External Filtration............................................................................... 6-1
Supply Pressure Regulation ................................................................. 6-1
Replacing the CCB ............................................................................. 6-2
Troubleshooting Guide....................................................................... 6-3
Contact Information ........................................................................... 6-4
Warranty............................................................................................. 6-4
Toxic & Hazardous Substances Tables....................................................... A-1
Appendix A
Appendix B Ordering Information....................................................................................... B-1
Specifications....................................................................................................C-1
Appendix C

This page intentionally left blank.

Chapter 1
Product Overview
Thermo Fisher Scientific’s STD5000 and STD6000 current to pressure
(I/P) transducers represent the highest standard in I/P technology. The
rugged NEMA 4X housing, compact size, and plug-in E-Pi module
coupled with Thermo Fisher’s field proven technology make them the most
accurate, reliable, and simplest I/P transducers to install, operate, and
maintain in the industry.
Thermo Fisher’s solid state current-to-pressure converter (E-Pi) technology
uses minimal electrical energy and air consumption to convert an electronic
input signal (4–20 or 10–50 mA) to a proportional pneumatic output
signal (3–15 psig, 0.2–1 bar, etc.). The E-Pi transducer utilizes a virtually
weightless membrane that is electromagnetically positioned over a nozzle to
precisely modulate the pneumatic (backpressure) output. The low mass
membrane is held in a continuously balanced position, providing an output
that is unaffected by shock, vibration, or mounting position. The output of
the E-Pi is then fed into an integral volume booster to deliver a pneumatic
output signal with an output capacity of 4.0 standard cubic feet per minute
(scfm).
The overall performance, accuracy, and repeatability are enhanced by
employing an internal feedback network whose speed and resolution enable
the transducer to quickly respond to input changes. The balanced supply
and exhaust dynamics enhance control stability, while delivering accuracies
of ± 0.15 to ± 0.25 percent of span.
Thermo Fisher Scientific STD5000 & STD6000 User Guide 1-1

Product Overview
Requirements
1-2 STD5000 & STD6000 User Guide Thermo Fisher Scientific
Figure 1–1. Operation flow chart

Chapter 2
Installation & Wiring
Requirementsequirements 1. Temperature: Ambient temperature must match specifications.
2. Mounting/Attitude: No restrictions.
3. Electrical input: Either a 4–20 or 10–50 mA dc current source.
Shielded cable should be used and shield should be grounded to unit
and earth ground. If cable contains shield and drain wire and metal
conduit is NOT used, ground shield. If used, metal conduit should be
grounded to earth ground. Refer to Figure 2–4 for location of ground
screw.
4. Air supply: Clean, dry, oil-free instrument air within acceptable
pressure range for calibrated output.
a. Standard supply pressure should be 20 ±2 psi for 3–15 psig output
and 35 ±2 psi for 3–27, 6–30, or 1–17 psig outputs.
b. Supply pressure for standard high pressure configurations should be
35–100 psig (2.4–6.9 bar).
Note The air line should be purged of all debris, oil, and water. Thermo
Fisher strongly recommends using a coalescent external filter. Failures
attributed to instrument air supply contamination are not covered by the
warranty. ▲
Note If supply pressure is not within acceptable range, a regulator should
be installed (contact Thermo Fisher). ▲
Caution The instrument vents to atmosphere. The use of supply gas other
than air can create a hazardous environment. ▲
Thermo Fisher Scientific STD5000 & STD6000 User Guide 2-1

Installation & Wiring
Mounting
Mounting Refer to the dimensional drawings below (Figures 2–1 through 2–3) and
the following:
●Instrument housing is designed for mounting to a standard valve yoke
(2¼-inch bolt spacing) or a 2½-inch pipe.
●A valve mount kit consists of bolts and washers for mounting to the
valve yoke.
●A pipe mount adapter accessory is available from Thermo Fisher.
Figure 2–1.
Figure 2–2.
2-2 STD5000 & STD6000 User Guide Thermo Fisher Scientific

Installation & Wiring
Pneumatic Connections
Figure 2–3.
Pneumatic
Connections
neumatic
Connections
Note Note the following PRIOR TO making any pneumatic connections:
●Blow out lines thoroughly.
●Soap test all joints and fittings for leaks.
●Do not use pipe thread tapes on pneumatic piping. ▲
Refer to the dimensional drawings and the following:
1. One ¼-inch FNPT port is provided for supply air connections. Each
unit has a filter screen installed in this port.
2. Two ¼-inch FNPT ports are provided for pneumatic output
connections. Either port may be used and one may be used for the
mounting of an output gauge. Plug the unused port with the pipe plug
included with the unit. Note that the pipe plugs are certified and
suitable for the maintenance of the product’s certification rating and
protection concept.
Thermo Fisher Scientific STD5000 & STD6000 User Guide 2-3

Installation & Wiring
Electrical Connections
2-4 STD5000 & STD6000 User Guide Thermo Fisher Scientific
Electrical
Connections
lectrical
Connections
Warning All wiring must be made in accordance with all local and
national codes appropriate to the area in which the instrument is
installed. ▲
Note Observe polarity: Reverse polarity will not damage the unit but will
prevent it from operating. ▲
Refer to the dimensional drawings and the following figure and
instructions:
1. The instrument is supplied with two ½-inch FNPT electrical conduit
connections. Insert a ½-inch FNPT pipe plug into the unused
connection. Note that the pipe plugs are certified and suitable for the
maintenance of the product’s certification rating and protection
concept.
2. A two-position “Barrier Type” terminal block with wire-ready #6-32
screws is supplied for 12–22 AWG wire. The terminal blocks accept
spade lugs or stripped wire. Strip wire approximately ¼-inch before
insertion. The terminals are labeled + and - on the E-Pi label.
3. The earth ground wire, connected to the ground screw, must be
terminated using a spade lug for proper installation.
Figure 2–4. PCB connections

Chapter 3
Operation
Generalneral Operation is outlined in the flow chart displayed in Figure 1–1. The
electric to pneumatic conversion takes place in the E-Pi valve. A
conditioned 4–20 mA input signal provides an electric current to the E-Pi
coil, creating a magnetic field that magnetizes the valve. The magnetization
is proportional to the input current signal and positions the membrane
relative to the valve seat. The pneumatic output is modulated relative to the
input current. Further conditioning of the pneumatic output is achieved
with a volume booster.
Final conditioning of the boosted pneumatic output signal occurs by
measuring the output with a pressure sensor. This signal is then compared
with the current to the E-Pi, resulting in exact pneumatic output relative to
the input signal.
ProgrammingProgramming Programming is selectable via internal jumpers located on the circuit board.
A label on the E-Pi module shows the location and position of these
jumpers (shown in Figure 3–1).
To select the operating mode, plug in the jumpers according to the
following table. The table also displays the part number of the E-Pi module
required to achieve the desired outputs and the necessary supply pressure.
Note We recommend that you select the mode PRIOR TO final
installation. ▲
Note When switched from direct to reverse or into split range, the span
remains within ±1%. ▲
Thermo Fisher Scientific STD5000 & STD6000 User Guide 3-1

Operation
Programming
Figure 3–1. Jumper selection
Table 3–1.
Uses this Supply pressure Jumper select switch position
Output E-Pi Input (mA) Standard High
pressure
Direct Reverse Range
1:1
Range
1:2
Adjust
3–15 psig
3–15 psig
3–15 psig
SA45-1502-15
SA45-1502-15
SA45-1502-15
4–20 or 10–50
4–20 or 10–30
12–20 or 30–50
20 psig
20 psig
20 psig
35–100 psig
35–100 psig
35–100 psig
x
x
x
x
x
x
Zero
Zero
Zero
15–3 psig
15–3 psig
15–3 psig
SA45-1502-15
SA45-1502-15
SA45-1502-15
4–20 or 10–50
4–12 or 10–30
12–20 or 30–50
20 psig
20 psig
20 psig
35–100 psig
35–100 psig
35–100 psig
x
x
x
x
x
x
Zero
Zero
Zero
3–27 psig1,2
27–3 psig
SA45-1502-27
SA45-1502-27
4–20 or 10–50
4–20 or 10–50
35 psig
35 psig
N/A
N/A
x
x
x
x
Zero
Zero
6–30 psig1,3
30–6 psig
SA45-1502-30
SA45-1502-30
4–20 or 10–50
4–20 or 10–50
35 psig
35 psig
N/A
N/A
x
x
x
x
Zero
Zero
1–17 psig
1–17 psig
1–17 psig
SA45-1502-17
SA45-1502-17
SA45-1502-17
4–20 or 10–50
4–12 or 10–30
12–20 or 30–50
35 psig
35 psig
35 psig
N/A
N/A
N/A
x
x
x
x
x
x
Zero
Zero
Zero
17–1 psig
17–1 psig
17–1 psig
SA45-1502-17
SA45-1502-17
SA45-1502-17
4–20 or 10–50
4–12 or 10–30
12–20 or 30–50
35 psig
35 psig
35 psig
N/A
N/A
N/A
x
x
x
x
x
x
Zero
Zero
Zero
1Units with output ranges of 3–27 or 6–30 psig are programmed for 1:2 mode to achieve output range.
2Units factory calibrated for 3–27 psig can be converted to a 3–15 psig output range by changing mode selection from 1:2 to 1:1 and recalibrating.
However, reducing supply pressure to 20 psig may cause the pneumatic zero to drop; attempt to use the unit at 35 psig supply first.
3Units factory calibrated for 6–30 psig may have a pneumatic zero too high to recalibrate to 3–15. You can attempt to recalibrate by changing mode
selection from 1:2 to 1:1. If this does not work, send the unit to Thermo Fisher for recalibration or replace the 6–30 psig E-Pi module with a 3–15 psig
module.
3-2 STD5000 & STD6000 User Guide Thermo Fisher Scientific

Operation
Programming
Thermo Fisher Scientific STD5000 & STD6000 User Guide 3-3
There is adequate adjustment of span and zero to put a dead spot in the
output and thus prevent valve operation overlap in split range. Table 3–2
shows these values. Also note that there is adequate adjustment of span and
zero to provide a margin of overlap, if desired.
Table 3–2.
Mode Input (mA) Output (psig) Adjustment
Direct 1:2 4–11 3–15 Zero, Span
Direct 1:2 13–20 3–15 Zero, Span
Reverse 1:2 4–11 15–3 Zero, Span
Reverse 1:2 13–20 15–3 Zero, Span

This page intentionally left blank.

Chapter 4
The E-Pi Plug-In Module
Generaleneral ●Once removed, the E-Pi can be discarded or refurbished and used as a
spare part.
●In both standard and high pressure units, it is not necessary to shut off
the air supply to the unit. However, be aware that the output signal is
lost during the replacement process.
●High pressure E-Pi modules come supplied with a stiffening bracket
mounted under the mounting screw.
●Ensure the E-Pi you are installing matches the range of the unit.
●If the replacement E-Pi has been in storage for a long period of time, it
may be necessary to apply a lubricant (Dow Corningor equivalent)
to the O-rings.
Caution When removing or installing the E-Pi plug-in module, always pull
straight out or push straight in. Damage or breakage may occur if the
module is pulled out at an angle. ▲
Caution Removing the E-Pi with the air supply still operating creates a
situation where particles that may have accumulated from a contaminated
air supply can be blown out. ▲
Warning Do not remove the cover when the instrument is powered unless
the area is known to be non-hazardous. ▲
Thermo Fisher Scientific STD5000 & STD6000 User Guide 4-1

The E-Pi Plug-In Module
Replacing the E-Pi
Figure 4–1. E-Pi plug-in module
Replacing the
E-Pi
1. Remove the cover.
2. Locate and loosen the module retaining captive screw from the
manifold. Note that the module is designed so that the screw does not
need to be removed from the plastic piece.
3. Grab the module firmly and pull it straight out.
4. Align the replacement module with the pneumatic and electrical
connections. Press straight down into the manifold, and tighten the
retaining screw.
5. Electrical connections are a two-point contact system. The first contact
occurs when the connector is pushed onto the PCB male pin. The
second occurs as the barrel of the connector is pushed further onto the
pin. It may be necessary to use needle nose pliers to make the second
connection. If this is the case, grip the connector firmly above the
barrel section and push straight down. Refer to Figure 4–2.
The unit should operate without requiring calibration.
4-2 STD5000 & STD6000 User Guide Thermo Fisher Scientific
This manual suits for next models
1
Table of contents
Popular Transducer manuals by other brands
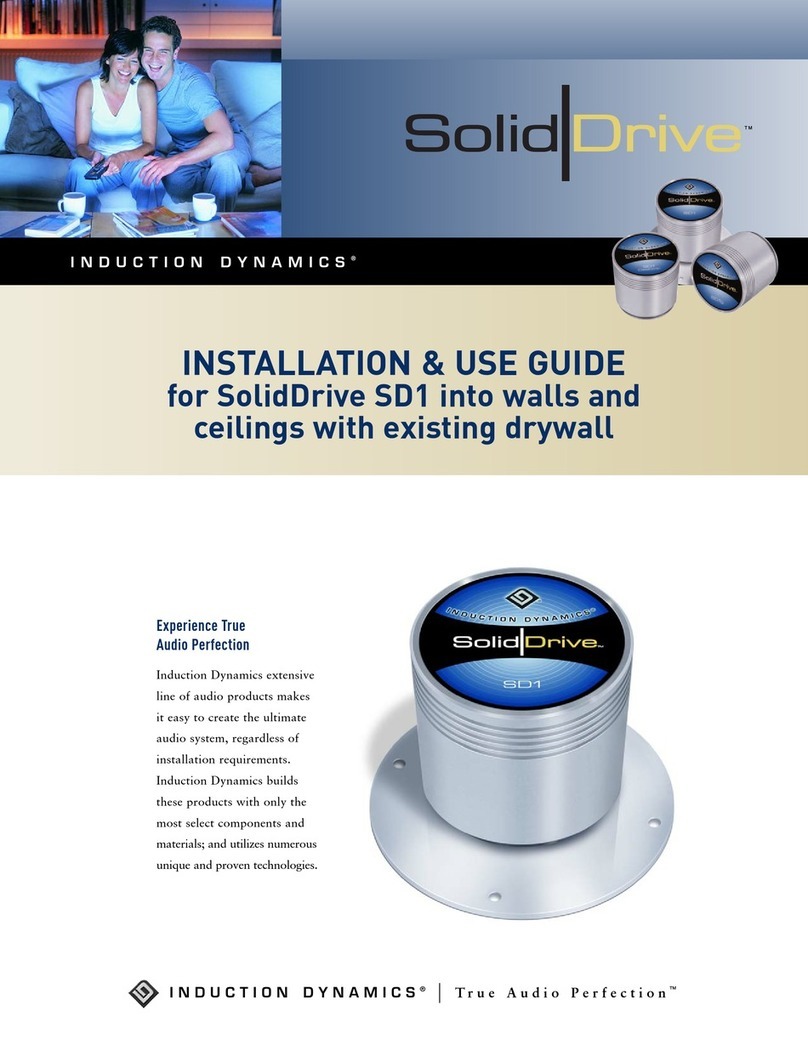
SOLIDDRIVE
SOLIDDRIVE SD1 Installation & use guide
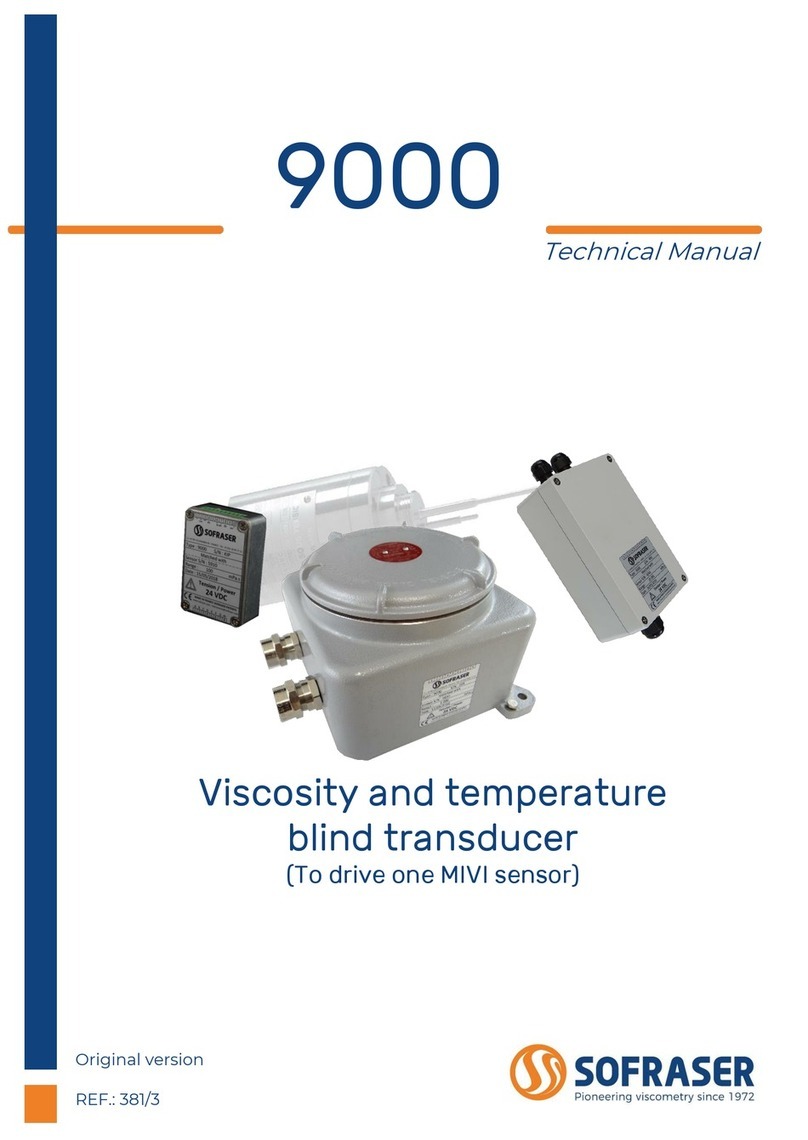
Sofraser
Sofraser 9000 Technical manual
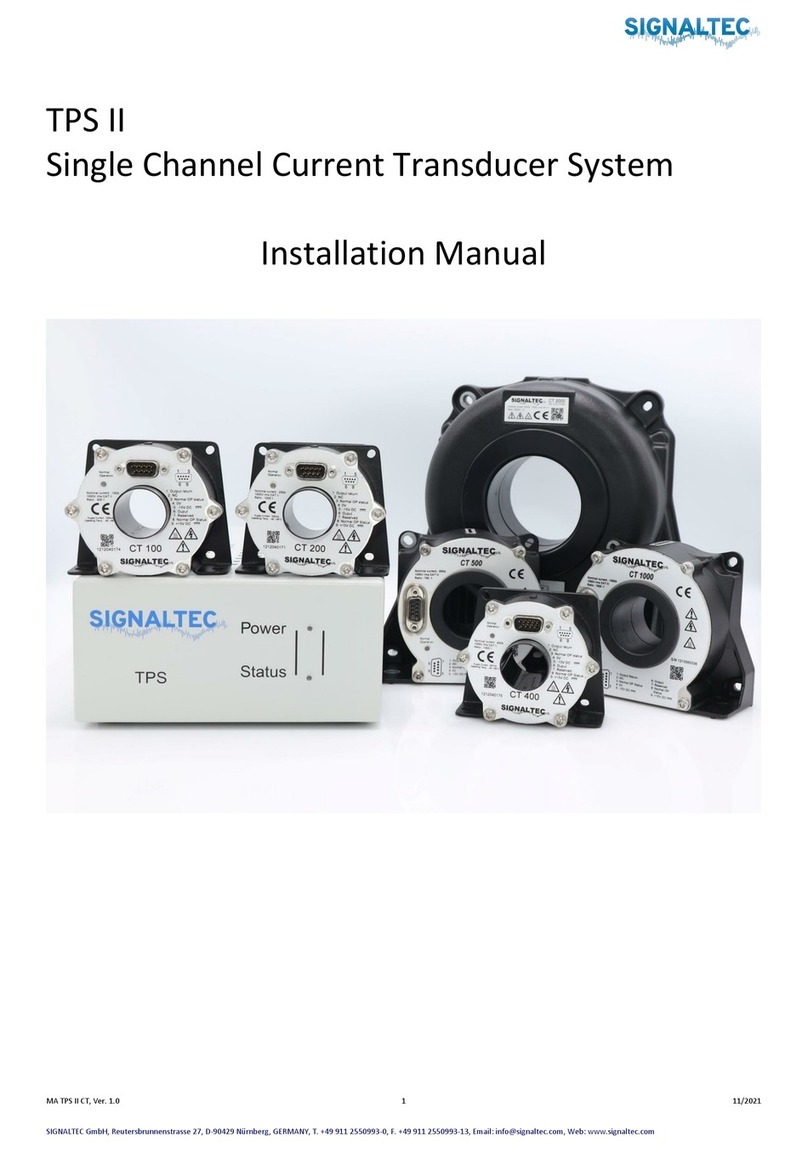
Signaltec
Signaltec TPS II installation manual
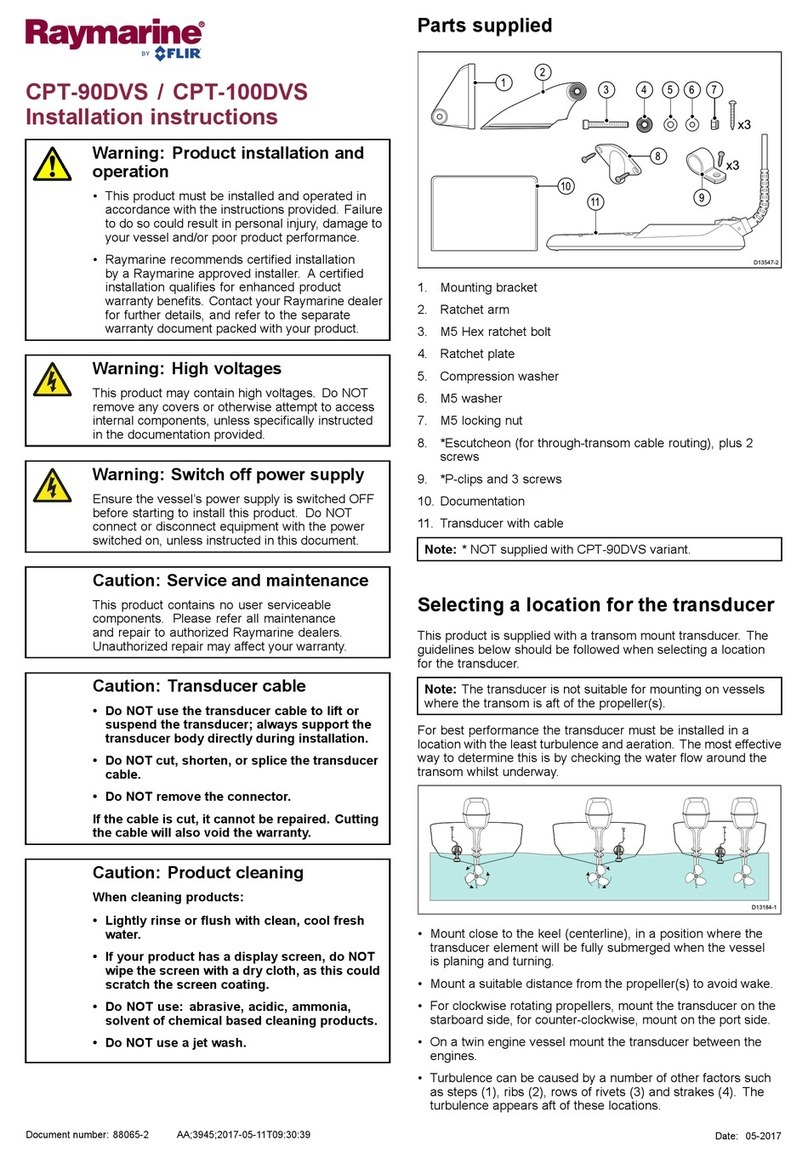
FLIR
FLIR Raymarine CPT-90DVS installation instructions

LEI accessories
LEI accessories FISHSTRIKE HS-WS Installation and operation instructions

Daiichi Electronics
Daiichi Electronics PTT2-92A-12 instruction manual