THIEMAN NTEA TVL Series User manual

TVLSerieS
All Aluminum Railgates By THIEMAN
TVL125, TVL125A, TVL16, TVL16A, TVL20, TVL20A
INSTALLATION INSTRUCTIONS
IMPORTANT! KEEP IN VEHICLE!
!
PLEASE READ AND UNDERSTAND THE CONTENTS OF THIS
MANUAL BEFORE OPERATING THE EQUIPMENT.
TAILGATES, INC.
600 East Wayne Street
Celina, Ohio 45822
Phone: 419-586-7727 Fax: 419-586-9724
HIEMAN
NTEA
THE ASSOCIATION FOR THE WORK TRUCK INDUSTRY
TM
MEMBER

ALL ALUMINUM 125/16
2.
ALL ALUMINUM TVL 125/16
ATTENTION INSTALLERS:
Changes are made periodically to the installation procedure to comply with engineering
changes. To ensure proper liftgate operation, it is VERY IMPORTANT to read and understand
the installation instructions before attempting an installation. Installers also MUST read and
understand the liftgate’s Owner’s Manual before installing the liftgate, so they can operate the
liftgate safely as required during different stages of the installation process. NEVER perform
a modification on the liftgate, which is not specifically covered in this manual or which is
unauthorized by Thieman. Modifications may result in failure of the liftgate and may create
hazards for liftgate installers, operators, or maintainers. Serious damage, equipment failure, or
operator injury could result from improper installation. This equipment MUST have all decals
applied properly. FAILURE to apply all decals properly will VOID all warranties! Any installer
with questions or doubts should contact Thieman before proceeding.
NOTES:
1. All maximum mounting dimensions are shown with the vehicle empty; all minimum
mounting dimensions are shown with the vehicle loaded.
2. Check the bed height when vehicle is parked on a level surface.
3. Refer to figure 1 and table 1 for overall dimensions of liftgates and bed height ranges for
different models.
4. The TVL series railgates are all level ride, which means when the vehicle is located on a level
surface; the rails should be perpendicular to the ground. When mounting, consideration
should be given to the platform position with the truck both empty and loaded. See figure 2
and 3.
NOTES:
1. All bed height ranges shown in tables 1 allow installer to provide a minimum of 18" of
ground clearance by cutting off the lower end of the rail as needed unless otherwise stated.
Rails must NOT be cut more than 22" above the ground (Note: 22" measurement must
be made with truck unloaded. See Step 9 of Installation Instructions. On special orders,
consult factory as the allowable trim dimensions may vary from what is shown here).
MODEL
TYPE
TVL125/16/20
TVL125A/16A/20A
TVL125LB/16LB/20LB
RAIL
LENGTH
“A”
83.00
89.00
80.00
FRAME WIDTH
“B”
82, 92, 97, 102
82.00
92.00
97.00
102.00
82, 92, 97, 102
BED HEIGHT
RANGE
33.00-51.00
33.00-37.00
38.00-43.00
33.00-40.00
41.00-43.00
33.00-40.00
41.00-43.00
33.00-40.00
41.00-43.00
33.00-37.00
ABOVE BED
RANGE
NA
16.00
15.00-7.00
16.00
15.00-10.00
16.00
15.00-10.00
16.00
15.00-10.00
16.00
TABLE 1

3.
INSTALLATION INSTRUCTIONS
Step 1 Inspect entire package of your new liftgate for obvious damage. Report any damage to
the freight line that delivered your liftgate. DO NOT REMOVE ANY BANDING!
Step 2 Locate the vehicle on which the liftgate is to be mounted on a dry and level floor and
open the rear door on the vehicle.
Step 3 Raise gate and place it against the rear of the vehicle and remove any obstructions
where possible. If obstruction can not be removed, use 6 aluminum spacers 12" long
x 3" wide by depth of interference and weld to top and bottom of rails. See figure 2. (If
structural angle or tubing is used for spacer, it must have a .25" minimum wall thick-
ness). The depth of the spacers may vary from top to bottom to enable a perpendicu-
lar mounting to the ground. See figure 3.

4.
Step 4 Raise the liftgate once again and square it with the rear sill of the vehicle as shown in
figure 4. Temporary supports as shown in figure 5 may be welded to cylinder housing
to assist in squaring lift to rear sill of vehicle.

5.
Step 5 Once the liftgate is centered on the vehicle, mark and drill the holes through the rear of
the body. Use .38 Grade 5 bolts and a backer plate as shown in figure 6A. Depending
on the body structure, a rear corner backer plate may be needed as shown in figure
6B for additional support. See figure 7 for the vertical spacing of these backer plates.
DO NOT REMOVE THE FORKLIFT OR CRANE UNTIL ALL MOUNTING IS COMPLETE!
Step 6 Review all mounting dimensions and be certain liftgate is square and centered with re-
spect to the body and rails are perpendicular to the ground.

6.
Step 7 If liftgate installation is on a flatbed vehicle, fabricate load bearing support tubes and
diagonal braces as shown in Figure 8. Square the support tubes with the bed and
perpendicular to the ground as shown, and weld braces to vehicle body and support
tubes. Then weld liftgate rails to support tubes on both the inside and outside corners
of each rail.
Step 8 These models have plastic oil reservoirs on their power units. Necessary precautions
must be taken during welding to prevent heat damage to reservoirs on these models.
Re-check all welds and fasteners then remove forklift or crane from liftgate. Remove
the lifting crossbar from the rails.

7.
Step 9 If possible, install diagonal braces from the lower part of the rails to the vehicle body
(see Figure 9). On lower bed heights, the rails may need trimmed to maintain an ad-
equate 18" of ground clearance. NEVER trim the rails more than 22" from the ground
OR so high that lower nylon wear pads drop, EVEN PARTIALLY, out of rails, which may
cause liftgate to jam up or cause damage to liftgate (see Figure 9). This 22" maximum
dimension MUST be measured on an unloaded truck, or this dimension will be ex-
ceeded when the truck is unloaded. (On special orders, consult factory as the allow-
able trim dimensions may vary from what is shown here).
Step 10 Fasten the 150 AMP circuit breaker provided within 2 ft. of the truck battery. Route
battery cable from the pump enclosure toward the 150 AMP breaker. AVOID SHARP
CORNERS AND HIGH HEAT AREAS! Use cable clips provided to secure the cable
to the truck frame every 2 feet. Cut the cable to the desired length and strip .75"
of insulation from the end. Slide the pre-cut heat shrink over the end of the cable.
Secure the cable lug in a vise and apply heat to the connector and insert the cable as
the solder melts. Allow connector to cool and install the heat shrink. Attach this end
to one terminal on the 150 amp breaker. Wire the breaker to the truck battery using
the 2 ft. cable provided. Bolt the grounding cable from the liftgate to the truck frame.
See figure 10.
Step 11 Many late model trucks have battery connections as shown in figure 10. The ground
cable from the battery may be run directly to the engine block with only a light
braided ground strap connecting the block to the chassis. Where this is the case, the
factory installed cable usually does not provide an adequate ground circuit for oper-
ating battery powered liftgates. We recommend that the cables labeled with an “X”
be not less than #2 gauge cable as supplied in the installation kit. Also, due to the
high current draw (Approx. 200A) we recommend that the alternator be a heavy duty
type and the battery must have a 150 AMP minimum reserve capacity.
Step 12 The TVL above bed models are pre-set to travel 10 inches above bed. Depending on
the bed height it may be possible to obtain up to 16 inches above bed. Refer to table
1. To do this some of the lift chain must be removed. This amount is the same as the
additional travel desired. The platform must be completely lowered to the ground and
the cylinder housing cover removed. Remove the jam nuts and tension rods attached
to the chain and cut off the required amount from each chain. Push the cylinder rod
in and re-assemble the tension rods and replace cover. Raise the platform and check
dimensions and adjust as necessary.
Step 13 Platform manual closing torsion assist is preset at the factory, however, if it is neces-
sary to adjust the closing torsion, use the following steps to do so: (See figure 12).
A. Place the platform in the stowed (vertical) position making sure the platform stow
bars are secured in the resting place on both sides of the liftgate.
B. Remove the .62" diameter retention bolt (A) from the center of the tension adjust-
ing bracket.
C. Place a .50" square breaker bar in the square hole of the tension adjusting
bracket.
D. Turn breaker bar counterclockwise to relieve the force on the .38" diameter bolt
(B) and remove bolt (B) noting the position of the tension adjusting bracket at the
initial setting.

8.
E. To increase tension, use the breaker bar to rotate bracket counterclockwise be-
yond its initial setting until the desired tension is reached. Line up a hole in the ad-
justing bracket with one of the two holes in the slider and thread the .38" diameter
bolt (B) through the aligned holes to secure the desired setting.
F. Replace retention bolt (A) and tighten both bolts (A and B) securely.

9.
Step 14 If the liftgate was mounted correctly to the truck, the platform should be parallel to
the ground in its open position, however, if minor adjustments are required, simply
tighten adjusting nuts (A) on U-bolt (B) on platform block (C) to raise the ramp end of
the platform or to lower the ramp end simply loosen nuts (A). See figure 13. Similar
adjustments should be made on both sides of the platform so that both chains see
the same tension when loaded. CAUTION: U-BOLT (B) MUST REMAIN COMPLETELY
THREADED THROUGH NUTS (A).
Step 15 Set adjustment angles on either side of liftgate to hold platform vertical such that
the stow bars on platform are aligned with the resting plate slots. Inspect alignment
with stow bars raised completely out of resting plate slots (See figure 4A). If they are
out of alignment, put the platform in the stored position. Raise platform slightly, so
that stow bars are not sitting on the bottom of the resting plate slot, so there is ten-
sion in chains (See figure 4B). Then, unloosen screws on the adjustment angles and
move angles so they are tight against the vertical platform. Once angles are adjusted,
tighten screws. Be sure to do this for both sides. Repeat inspection of stow bar align-
ment and readjust if necessary. Failure to keep stow bars aligned with resting plate
slots can result in excessive wear of stow bars and resting plates.
Step 16 IF APPLYING A FINISHED COAT OF PAINT, MASK OFF OPENINGS IN VERTICAL
FRAME RAILS so that no paint gets inside, where the I-beam sliders track up and
down. WARNING: OVERSPRAY IN RAILS CAN GET EMBEDDED IN NYLON WEAR
PADS ON SLIDERS, WHICH CAN CAUSE LIFTGATE TO NOT OPERATE SMOOTHLY.
If painting, carefully grease or mask fittings and exposed portion of the piston rod.
Finish paint, if desired, and remove the pre-mask on decals already applied by
Thieman. Apply decals from installation kits in the appropriate locations as shown.
The decals MUST be applied or all warranties are VOID!

10.
INSPECTION AND LOCATION OF DECALS
Inspect all decals listed below to be certain they are in the proper location and are legible.
ALL DECALS MUST BE IN PLACE AND LEGIBLE OR ALL WARRANTIES ARE VOID!
Item Part Name Part Number
1 Warning Decal-center load 4682
2 Fast Idle Decal 4650150
3 Danger Decal-no riding 4609
4 Operating Decal 4650780
5 Capacity Decal 1250# 4650060
5 Capacity Decal 1600# 4650750
6 Caution Decal-pinch point 4650790
7 Caution Decal-cover 4650760
8 Caution Decal-working area 4650770
9 Reflector (3) 5705
10 Thieman Nameplate 4650801
11 Toggle Switch Decal (1) 4650820
12 Wiring Decal 4617
13 Warning Decal - High Pressure 4620
14 Lubrication Instruction Decal 4662
15 Lube Location Decal (4) 4663
16 Urgent Warning Decal 4681
Step 17 Thieman recommends that the installer perform a weight test of the liftgate to check
the welds or mounting bolts and the structural integrity of the body or frame of the
truck or trailer. The load used should be the maximum weight rating of the partciular
liftgate with the weight centrally located on the platform. A minimum of 20 cycles
should be made to insure the integrity of the mounting.
Step 18 Any lights that were removed or obstructed must be replaced or relocated in such
a manner that the completed vehicle must be in compliance with FMVSS 108 (49
CFR 571.108) If the liftgate was ordered with the optional light kit, refer to the light
wiring pictorial for wiring details.

LIGHT WIRING PICTORIAL

Rev. 10/21 • 1M • MP108067
This manual suits for next models
6
Table of contents
Other THIEMAN Lifting System manuals
Popular Lifting System manuals by other brands
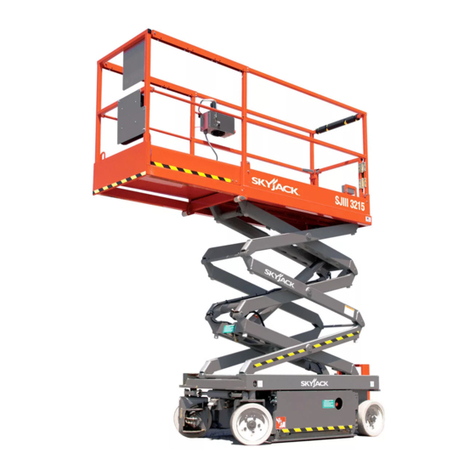
Skyjack
Skyjack SJIII Series operating manual
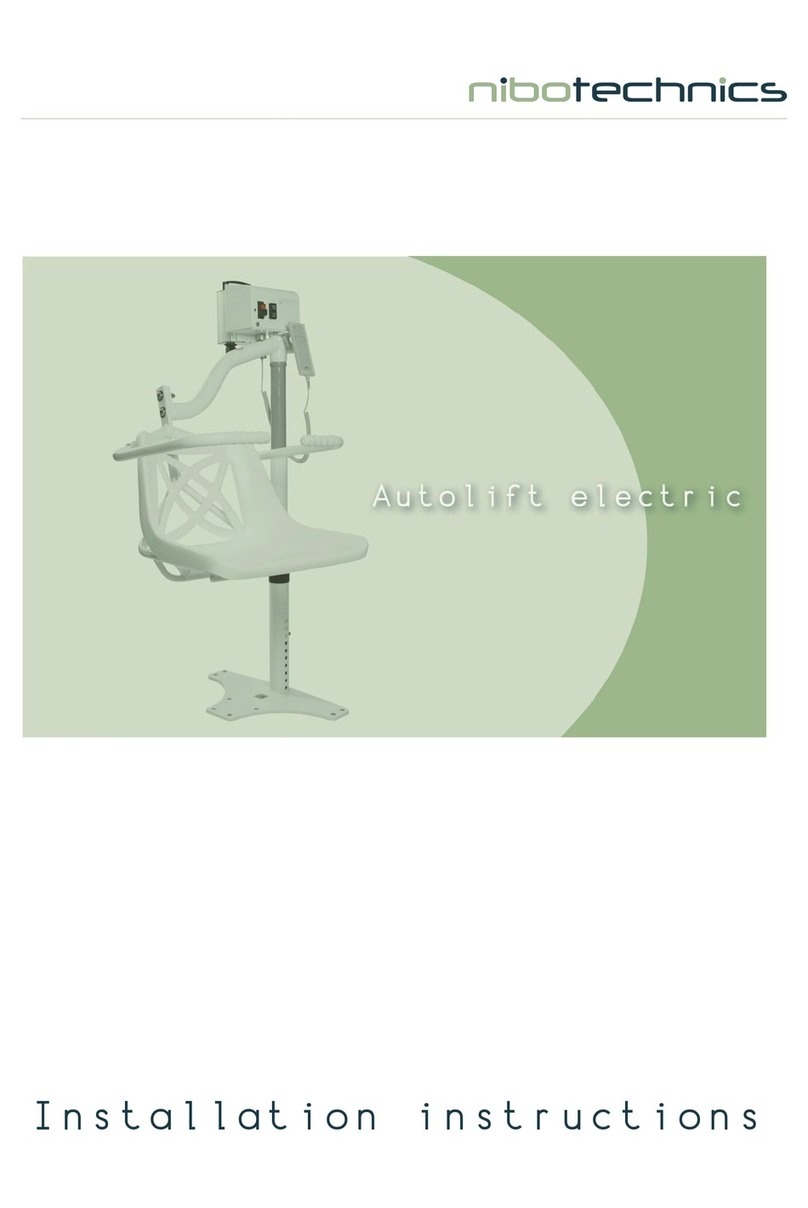
Nibotechnics
Nibotechnics Autolift electric installation instructions
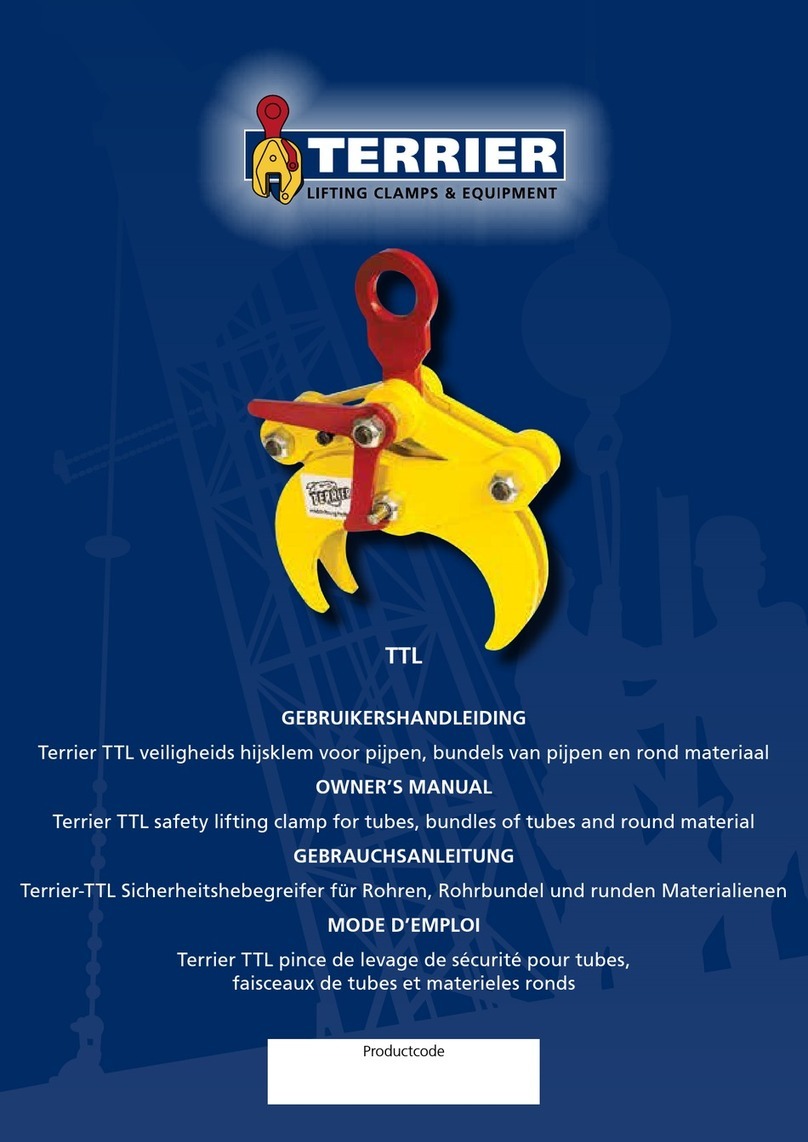
Terrier
Terrier TTL owner's manual
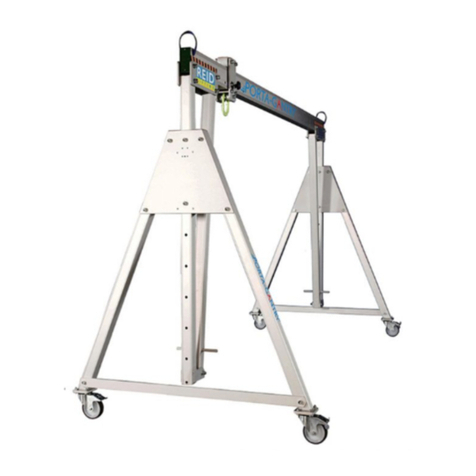
REID LIFTING
REID LIFTING porta-gantry 500 Assembly & operation manual
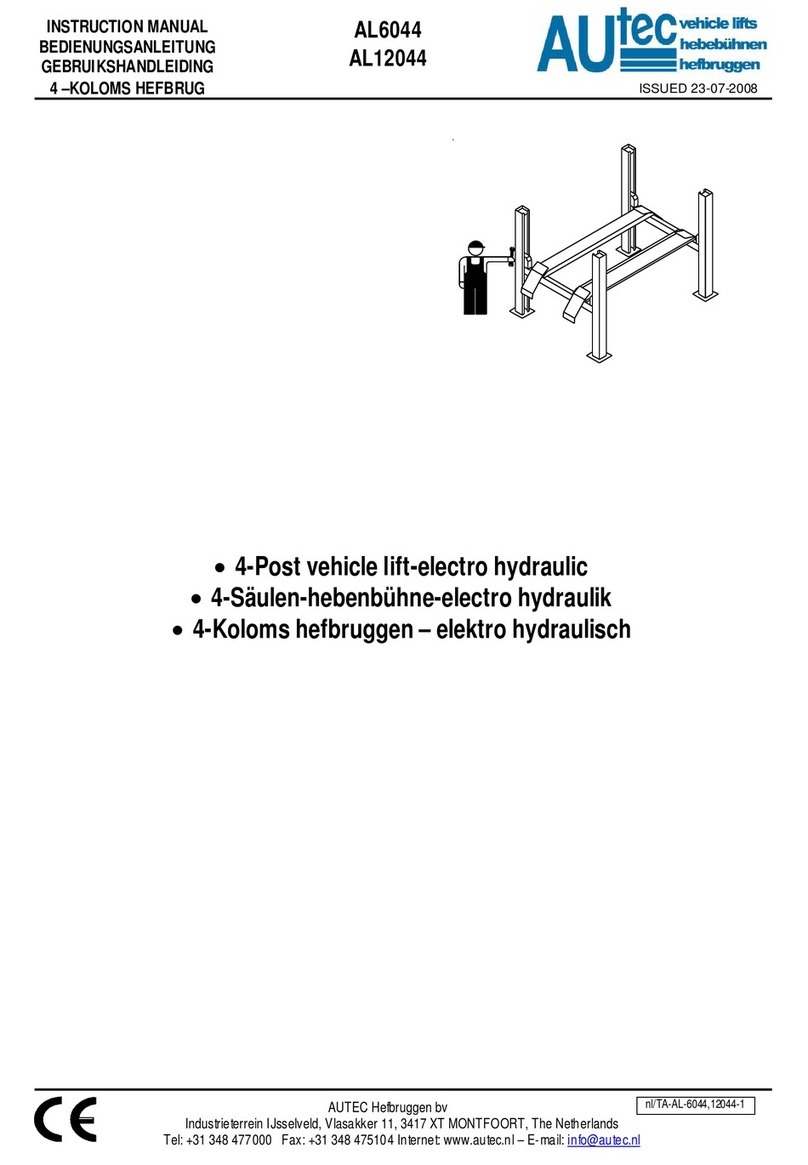
AUTEC
AUTEC AL6044 instruction manual
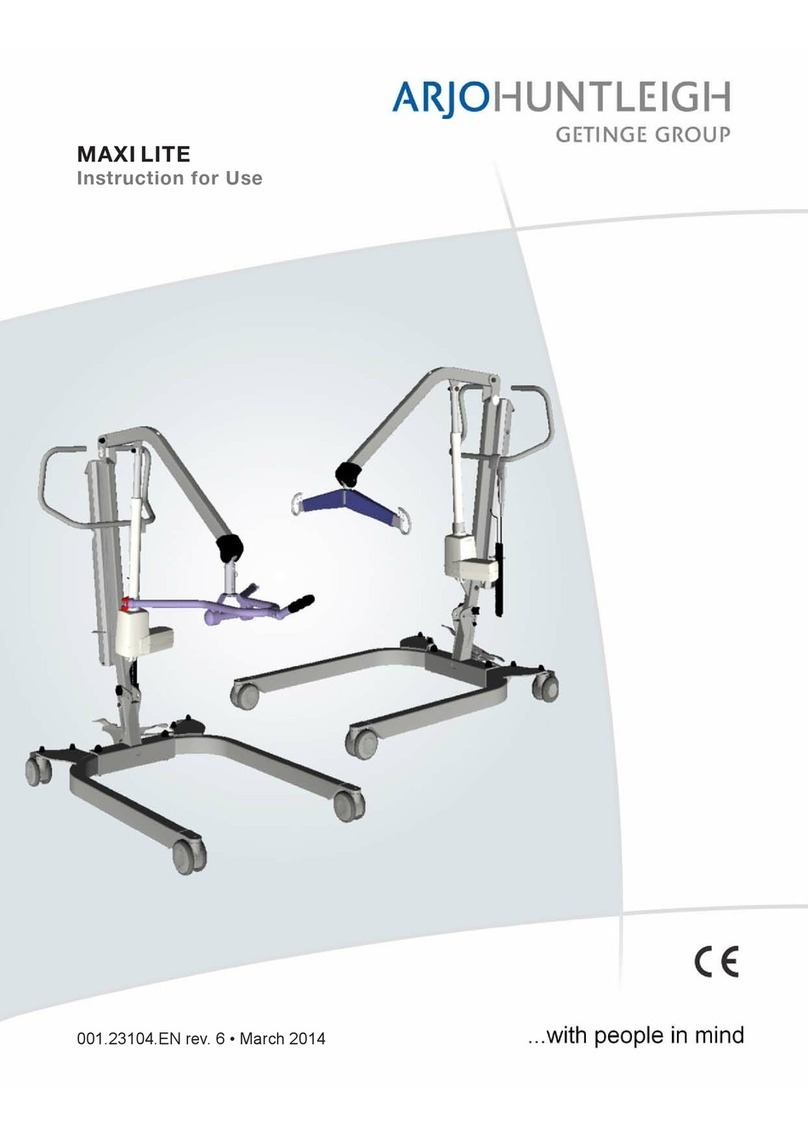
ARJO HUNTLEIGH
ARJO HUNTLEIGH MAXI LITE Instructions for use