Trinity Highway CASS TL3 User manual


TrinityHighway.com 1 Part No. 620289
©2021 Trinity Highway Products, LLC
Revision A November 2021
CASS® C-Channel
CAble Safety System
The CASS® C-Channel CAble Safety System (“CASS®”), 3-cable, has been tested to National
Cooperative Highway Research Program (“NCHRP”) Report 350 criteria and has been deemed eligible
for Federal-aid reimbursement on the National Highway System (“NHS”) by the Federal Highway
Administration (“FHWA”) as a Test Level 3 (“TL-3”) system when installed on slopes which are 6:1 or
flatter.
Product Description
Assembly Manual
15601 Dallas Parkway
Suite 525
Addison, Texas 75001
Warning: The local state/specifying agency, distributors, owners, and contractors
are RESPONSIBLE for the assembly, maintenance, and repair of CASS®. Failure
to fulfill these RESPONSIBILITIES with respect to the assembly, maintenance, and
repair of CASS® could result in serious injury or death.
Important: These instructions are for standard assembly specified by the
state/specifying agency. In the event the specified system assembly, maintenance,
or repair would require a deviation from standard assembly parameters, contact
a Trinity Highway Products, LLC (“Trinity Highway”) representative. This system
has been deemed eligible by the FHWA for use on the NHS under strict criteria utilized
by that state/specifying agency.
This manual must be available to the worker overseeing and/or assembling the product at all
times. For additional copies, contact Trinity Highway at (888) 356-2363 or visit
TrinityHighway.com/Products.
The information contained in this manual supersede all previous versions. The instructions,
illustrations, and specifications are based on the latest CASS® information available to Trinity Highway
at publication. We reserve the right to make changes at any time. Please visit TrinityHighway.com/product-
category/barriers to confirm the latest revision.

TrinityHighway.com 2 Unreleased May 2021
Revision A November 2021
Table of Contents
CASS® Acronyms .......................................................................................................................... 2
Customer Service Contacts ........................................................................................................... 3
Important Introductory Notes ......................................................................................................... 3
Limitation and Warnings ................................................................................................................ 4
General CASS® Information .......................................................................................................... 6
CASS® Components ...................................................................................................................... 6
Recommended Tools .................................................................................................................. 13
Ground Preparation and Barrier Alignment ................................................................................. 14
Line Post Foundation Placement ................................................................................................ 15
CASS® Cable End Treatments .................................................................................................... 17
CCT Line Footings ...................................................................................................................... 19
CCT Posts Assembly .................................................................................................................. 21
Terminal Cables .......................................................................................................................... 22
Line Cables ................................................................................................................................. 23
Laying Out the Cable/Attaching the Cables to the Posts ............................................................ 26
Tensioning and Tension Meter .................................................................................................... 27
Delineation .................................................................................................................................. 28
Repairs ........................................................................................................................................ 29
Emergency Repairs ..................................................................................................................... 30
Cable Tension Inspection Program ............................................................................................. 32
CASS® Assembly/Repair Checklist ............................................................................................. 33
CASS® Routine Inspection Checklist (File with Maintenance Records) ...................................... 34
CASS® C-Channel Temperature/Tension Chart .......................................................................... 35
Tension Log Cable Safety System .............................................................................................. 36
Appendix A: Flare Assemblies 30:1 Flare .................................................................................. 37
Appendix B: Cable Barrier Overlap ............................................................................................ 38
Appendix C: Encountering Rock ................................................................................................ 39
Appendix D: Base Plated Post Assembly ................................................................................... 40
CASS® ACRONYMS
AASHTO American Association of State Highway and Transportation Officials
CASS® The CASS® C-Channel Cable Safety System
CBOD Cable Barrier Overlap Distance
CCA CASS® Cable Anchor
CCT CASS® Cable Terminal
CFR Code of Federal Regulation
CRP Cable Release Post
FHWA Federal Highway Administration
MSC Minimum Strength Concrete
MUTCD Manual on Uniform Traffic Control Devices
NCHRP National Cooperative Highway Research Program
NHS National Highway System
OSHA Occupational Safety & Health Administration
PN Trinity Part Number
PPE Personal Protective Equipment
TL-3 Test Level-3
Trinity Highway Trinity Highway Products, LLC
1V: “x”H Slope Measurement-1 Foot Vertical Distance to “x” Distance

TrinityHighway.com 3 Unreleased May 2021
Revision A November 2021
Customer Service Contacts
Trinity Highway is committed to the highest level of customer service. Feedback regarding CASS®,
its assembly procedures, supporting documentation, and performance is always welcome.
Additional information can be obtained from the contact information below:
Trinity Highway
Telephone
(888) 356-2363 (USA)
+1 214 589 8140 (International)
Contact Link
TrinityHighway.com\Contact
Website:
www.trinityhighway.com
Trinity Highway Products, LLC
15601 Dallas Parkway
Suite 525
Addison, TX 75001
Important Introductory Notes
Proper assembly of CASS® is essential to achieve the performance that has been evaluated and deemed
eligible for federal-aid reimbursement by the FHWA per NCHRP Report 350. These instructions are to be
read in their entirety and understood before assembling CASS®. These instructions are to be used only in
conjunction with standard CASS® assemblies specified by the appropriate state/specifying agency. If you
need additional information, or have questions about CASS®, please contact the state/specifying
agency that has planned and specified this assembly and, if needed, contact Trinity Highway
Customer Service. This product must be assembled in the location specified by the state/specifying
agency. If there are deviations, alterations, or departures from the assembly instructions specified in this
manual, the device may not perform as tested.
Note: The Metric conversion from Imperial in this manual uses a soft conversion.
The state/specifying agency’s careful evaluation of the site layout, vehicle population type and speed, traffic
direction, and visibility are some of the elements that require evaluation in the selection of a highway
product. For example, curbs could cause an untested effect on an impacting vehicle.
A set of product and project shop drawings will be supplied by Trinity Highway. The shop drawings will be
for each section of the assembly. These drawings are to be reviewed and studied thoroughly by a qualified
individual who is skilled in interpreting them.

TrinityHighway.com 4 Unreleased May 2021
Revision A November 2021
Limitations and Warnings
Trinity Highway, in compliance with NCHRP-350,
contracts with ISO 17025 A2LA accredited testing
laboratories to perform crash tests, evaluate tests, and
submit the test results to the FHWA for review.
CASS® has been deemed eligible by FHWA as
meeting the requirements and guidelines of NCHRP
Report 350, Test Level 3 (TL-3). These tests typically
evaluate product performance defined by NCHRP
Report 350 involving a range of vehicles on
roadways, from lightweight cars (approx. 800 kg [1800
lb.]) and full size pickup trucks (approx. 2,000 kg [4,400
lb.]) at 100 kph [62 mph].
CASS® is tested pursuant to the test matrix criteria of
NCHRP Report 350 as designated by FHWA. The
FHWA tests are not intended to represent the
performance of systems when impacted by every
vehicle type or in every impact condition existing on
the roadway. Every departure from the roadway is a
unique event.
Trinity Highway expressly disclaims any warranty or
liability for injury or damage to persons or property
resulting from any impact, collision or harmful contact with
its products, other vehicles, or nearby hazards or objects
by any vehicle, object or person, whether or not the
products were assembled in consultation with Trinity
Highway or by third parties.
CASS® is intended to be assembled, delineated, and
maintained within the state/specifying agency and federal
guidelines. It is important for the state/specifying agency
specifying the use of a highway product to select the most
appropriate product configuration for site specifications.
The state/specifying agency’s careful evaluation of the
site layout, vehicle population type and speed, traffic
direction, and visibility are some of the elements that
require evaluation in the selection of a highway
product. For example, curbs could cause an untested
effect on an impacting vehicle.
After an impact with the system, all debris must be
removed from the area immediately in compliance with the
most applicable state/specifying agency policy. The
specified CASS® System must be evaluated and restored
to its original specified condition or replaced as the
state/specifying agency determines/requires, as soon as
possible. Product selection, approval, proper installation,
and maintenance of any highway product is the sole
responsibility of the state/specifying agency.
Safety Alert Symbols appear throughout this
manual and indicate Danger, Warning, Caution or
Important statements. Failure to read and follow these
warnings could result in serious injury or death in the
event of a vehicle impact with the system.
WARNING: Do not assemble, maintain, or repair
CASS® until you have read this manual thoroughly and
completely understand it. Ensure that all Danger,
Warning, Caution, and
Important
statements within
the manual are completely followed. Please call
Trinity Highway at (888) 356-2363 if you have any
questions about instructions in this manual.
WARNING: Safety measures incorporating
appropriate traffic control devices and personal
protective equipment ("PPE") specified by the
state/specifying agency must be used to protect all
personnel while at the assembly, maintenance, or
repair site.
WARNING: Ensure the assembly site meets all
appropriate Manual on Uniform Traffic Control
Devices (“MUTCD”) and state/specifying agency
standards.
WARNING: Only Trinity Highway parts that are
specified herein can be used for assembly,
maintenance, or repair on CASS®. Do not utilize or
otherwise commingle parts from other systems, even
if those systems are other Trinity Highway systems.
Alternate configurations have not been tested, nor
have they been approved for use.
Assembly,
maintenance or repairs using unspecified parts or
accessories is strictly prohibited. Failure to follow
this warning could result in serious injury or death
in the event of a vehicle impact with such an
UNACCEPTED system.
WARNING: Do NOT modify CASS® in any way.
IMPORTANT: Trinity Highway makes no
recommendation whether use or reuse of any part of
CASS® is appropriate or acceptable after system
impact. It is the responsibility of the state/specifying
agency and its engineers to make that determination.
IMPORTANT: It is the responsibility of the applicable
owner, state/specifying agency, or specifier to inspect
CASS® after assembly is complete to ensure the
instructions provided in this manual have been strictly
followed.

TrinityHighway.com 5 Unreleased May 2021
Revision A November 2021
Danger: It is critical that CASS® posts are placed
in suitable soil that will allow the system to fully
perform in accordance with design specifications.
Should you have any questions about this, please
contact the state/specifying agency that specified
CASS® at this particular location for guidance.
Trinity Highway is available for consultation with
that state/specifying agency.
Warning: Do not allow pedestrians or workers to stand
near this system, when under tension, in
circumstances where the cable may be impacted or
cut. Failure to follow this warning can result in serious
injury or death to the workers, bystanders and/or
pedestrians in the event of a vehicle impact with the
system.
Warning: It is imperative, before assembly, that you
contact a Trinity Highway representative and
state/specifying agency engineer for special criteria for
soils which do not meet or exceed NCHRP Report 350
soil conditions. It is also recommended that you consult
your own geotechnical engineer.
Warning: Be aware of hazards of using compressed
air (small objects may become projectiles). Failure to
follow this warning can result in serious injury or death
to the workers and/or bystanders.
Warning: When drilling rock, it is the responsibility of
the installer to consult Occupational Safety & Health
Administration (“OSHA”) silica respiratory standard 29
Code of Federal Regulation (“CFR”) 1910.134 for
debris removal and ensure compliance.
Warning: Ensure that CASS® and delineation used
meets all federal, state/specifying agency, and local
specifications.
Warning: CASS® shall be placed on a median or
roadside without obstructions, depressions, etc. that
may significantly affect the stability of an errant vehicle.
Grading of the site and/or appropriate fill materials may
be required. The assembler shall “flatten” or “round”
various topographical inconsistencies that could
interfere with the ability to consistently maintain the
design height (in relation to the terrain) of the cables.
To address assembly in rock, see Appendix C:
Encountering Rock.
Note: Based on soil conditions at the site, ANY or ALL
foundations may need larger/deeper concrete footings
or larger soil plates (for driven applications.) as
determined by soil analysis.

TrinityHighway.com 6 Revision A November 2021
General CASS® Information
CASS® is a 3-Cable Barrier that can be used as a TL-3 system on 1V:6H or flatter slopes. CASS®
consists of a 4” wide galvanized steel C-Channel post and three (3) pre-stretched 3/4” [19 mm]
wire rope cables. The posts can be driven, placed in a driven sleeve, placed in a sleeve and
concrete footing, placed in a sleeve in a mow strip, or base plated. One inch [25 mm] or 3/4” [19
mm] fitting hardware can be used.
The post spacing range is 6’-6” [2 m] minimum and 16’-4” [5 m] maximum. The 12” x 30” diameter
[300 mm x 762 mm] minimum depth concrete footing is used for the system with slopes 1V:6H or
flatter. See the Ground Preparation Section for additional placement criteria. The footing
depths/diameters can be increased if the soil characteristics do not meet NCHRP 350 standard
soil. Contact Trinity Highway for these designs.
CASS® can be placed on the roadside in front of slopes 1V:2H or flatter. Use a minimum distance
of 2’ [0.6 m] in front of the hinge point to the center of the post.
All cable height dimensions are approximate from top of grade to center of the cables. Cables
are placed in a slot at the top of the posts at approximate heights of 20.9” [530 mm], 25.2” [640
mm], and 29.5” [750 mm]. Plastic spacers keep the cables positioned at approximately 4” [100
mm] on center from each other. A stainless steel strap is placed around the post below the top
cable.
The post spacing will be in accordance to the contract plans. The barrier is terminated either with
a CCT, or a CCA. Only use the CCA when not on the NHS or when it cannot be impacted in
either direction.
The Minimum Strength Concrete (“MSC”) for all concrete components of CASS® is 3,000
psi [21 MPa] or greater to meet the state/specifying agency’s specifications.
Inspect Shipment
Before assembling the CASS®, carefully unpack and inspect all components for signs of damage.
Check the received parts against the packing list supplied with the system to verify that all parts
were received. If parts are damaged or missing from the shipment or unspecified parts were
part of the shipment, do not attempt to assemble the system; contact Trinity Highway
immediately.
Warning: Use only Trinity Highway parts that are specified by Trinity
Highway for use with the CASS® for assembling, maintaining, or
repairing the CASS®. Do not utilize or otherwise commingle parts from
other systems even if those systems are other Trinity Highway Systems.
CASS® Components
Below is a pictorial of components for the CASS® hardware. Please see Trinity Highway
drawing for specific lists of quantities. All Trinity Part Numbers (“PN”) are provided for standard
parts only.
Note: The following components are not shown to scale.

TrinityHighway.com 7 Revision A November 2021
PN: 3240G
PN:3245G
PN: 3300G
5/16” Flat Washer (F844)
5/16” Hex Nut (A563)
5/8” Flat Washer (F844)
PN: 3310G
PN: 3361G
PN: 3536G
5/8” Lock Washer
5/8” Hex Nut
1” Stud Flattened-LHT
PN: 3537G
PN: 3700G
PN: 3701G
1” Stud Flattened-RHT
3/4” Flat Washer (F844)
3/4” Flat Washer (F436)
PN: 3710G
PN: 3711G
PN: 3908G
3/4” Hex Nut (A563)
3/4” Hex Nut (A194 2H)
1” Heavy Hex Nut
(A563 DH)

TrinityHighway.com 8 Revision A November 2021
PN: 4099G
PN:4190G
PN: 4199B
Torpedo Cable Splice
Cable End Casting
3/4" Cable Wedge (3 x 7)
PN: 4211G
PN: 4779G
PN: 4902G
5/16” x 1 3/4” Hex Bolt (A307)
3/4” x 4 1/2” Hex Bolt (A325)
1” Flat Washer (F436)
PN: 4903G
PN: 4959G
PN: 5225G
1” Hex Nut (A194 2H)
3/4” Heavy Square Nut
5/8” X 7 1/2” HAS SUPER
Rod Chisel Pt (A193 B7)
PN:5403G
PN:5633G
PN: 5634G
3/4” x 5 1/2” Hex Bolt (A325)
1” Cable Splice
3/4” Cable Field Splice Left

TrinityHighway.com 9 Revision A November 2021
PN:5635G
PN: 5698G
PN: 5700B
3/4” Cable Field Splice Right
3/4” Cable Splice
4” Cable Spacer w/o Reflector
PN: 5701B
PN: 5702B
PN: 5709B
4” Cable Reflector Spacer
Yellow
4” Cable Reflector Spacer
White
CASS® Thermometer
PN: 5711G
PN: 5823B
PN: 5824T
3/4” Turnbuckle- Open Body
Sleeve Cover – CASS® Post
Stainless Steel Post Strap
PN: 5825G
PN: 5826G
PN: 5833B
Cable Lock Bolt (A307)
1” Turnbuckle - Closed Body
C Post Sleeve Cap, Bottom

TrinityHighway.com 10 Revision A November 2021
PN: 5836B
PN: 5837B
PN: 5838B
8” Concrete Reinforcing Ring
S3 Sleeve Cap, Bottom
CASS® C Post Cap
PN: 5839B
PN: 5840G
PN: 5850B
S3 Sleeve Cover Terminal
Post
5’-0” Cable Field Repair
Section
CASS® Cable Pulling Tool
PN: 5851B
PN: 5852B
PN: 5878B
Reflector Median (LEFT)
Reflector Roadside (RIGHT)
CASS® Tension Meter
PN: 5909G
PN:5910G
PN: 5919B
1” Cable Field Splice Left
1” Cable Field Splice Right
#4 x 2’-8” Rebar Rod

TrinityHighway.com 11 Revision A November 2021
PN: 6722G
PN: 9021G
PN: 33901G
5/8" X 8" ATR CHSL PT A449
Bearing Angle
C-Shaped Driven Post
PN: 33902G
PN: 33903
PN: 33908G
C-Shaped Post
Driven S3 Terminal Posts
w/Soil Plates-Posts 4-9
Terminal Post Sleeve–S3
Post
PN: 33909G
PN: 33910G
PN: 33912G
CRP-Cable Bracket
S3 Terminal Post – in Sleeve
Splice Post in Sleeve
PN: 33915A
PN: 33916B
PN: 33934A
Base Plated Post
CRP Reinforcing Cage
Bottom CRP (in Concrete)

TrinityHighway.com 12 Revision A November 2021
PN: 33935A
PN: 33936A
PN: 33938G
Top CRP
Bottom CRP (w/Soil Plate)
15” C Post Sleeve
PN: 33950G
PN: 33951A
PN: 33952A
30 3/4” Driven C Post Sleeve
30 3/4” Driven Sleeve w/Soil
Plate (C Post)
Driven Terminal Sleeve w/Soil
Plates- S3 Posts 4-9
PN: 33985G
PN:105204G
PN: 105205G
27” C-Post Sleeve
3/4” Stud Flattened-LHT
3/4” Stud Flattened-RHT
Important: Trinity Highway makes no recommendation whether use or
reuse of any part of the system is appropriate or acceptable following an
impact. It is the sole responsibility of the state/specifying agency and its
engineers to make that determination. It is critical that you inspect this
product after assembly is complete to make certain that the instructions
provided in this manual have been strictly followed.

TrinityHighway.com 13 Revision A November 2021
Recommended Tools
Documentation
• Manufacturer’s CASS® CAble Safety System Assembly Manual
(Current Version).
• CASS® System Drawing(s). Current version of SS-720
Personal Protective Equipment (PPE)
• Eye Protection
• Work Gloves
• Back Protection
• Safety-Toe Shoes
• Reflective Vest
• Apron
Wrenches
• Pipe Wrenches
• Adjustable Spanner
• Adjustable Jaw Wrenches
• Imperial and Metric Wrenches
Concrete equipment
• Concrete Vibrator
• Concrete Tools
Cable/Miscellaneous equipment
• Traffic Control Equipment and Plan per local standards and the MUTCD
• Cable Tension Meter (PN-5878B)
• CASS® Thermometer (Infrared) (PN-5709B)
• Abrasive Cutoff Blade/Saw
• C-Clamps
• CASS® Cable Pulling Tool (PN-5850B)
• Locking Pliers
• Duct tape
• Pry Bars
• Line/String
• Plumb Line
• Straight Edge
• Level
• Drift Pin
• Tape Measure
• Come-along/Lever chain hoist (3 ton minimum capacity)
• Backhoe (optional tensioning device)
• Chain (5 ton minimum capacity) of appropriate length for tensioning equipment
• Marking Paint
• Post Pounder
• Auger
Note: The provided list of tools is a general recommendation and should not be considered
an extensive list. Depending on specific site conditions and the complexity of the
assembly specified by the appropriate state/specifying agency, the required tools may
vary. Decisions as to what tools are needed to perform the job are entirely the
responsibility of the state/specifying agency and the agency’s contractor performing the
assembly of the system at the agency’s specified assembly site.

TrinityHighway.com 14 Revision A November 2021
Ground Preparation and Barrier Alignment
CASS® shall be placed on a median or roadside without obstructions, depressions, etc. that may
significantly affect the stability of an errant vehicle. Grading of the site and/or appropriate fill
materials may be required. The assembler shall “flatten” or “round” various topographical
inconsistencies that could interfere with the ability to consistently maintain the design height (in
relation to the terrain) of the cables. To address assembly in rock, see Appendix C: Encountering
Rock.
Warning: It is imperative, before assembly, that you contact a Trinity Highway
representative and state/specifying agency engineer for special criteria involving
soil conditions not meeting or exceeding NCHRP Report 350 soil conditions. It is
also recommended that you consult your own soils or structural engineer.
Note: Based on soil conditions at the site, ANY or ALL foundations may need larger/deeper
concrete footings or larger soil plates (for driven applications.) as determined by soil analysis.
Ground Preparation
When CASS® is placed in a median, use the following criteria for locating the system:
Ensure that the finished grade (side slope) is 1V:6H or flatter.
FHWA and AASHTO guidance for ANY NCHRP-350 cable system placed on
side slopes steeper than 1V:10H shall not be placed within 1’ to 8’ [0.3m to
2.4m] from the ditch line.
Barrier Alignment
Follow all procedures in the placement of the footing and/or post to ensure proper alignment. It
is suggested that a string line or other means be used to provide a consistent horizontal and
vertical alignment that meets specifications. If assembled on a horizontal curve, a minimum 650
foot [198 m] radius is required. If assembled on a sag vertical curve, the K value is ≥ 100’ [30 m].
See “Assembly on a Curve” Section.
CASS® can be placed on the roadside in front of slopes 1V:2H or flatter. Use a minimum distance
of 2’ [0.6 m] in front of the hinge point to the center of the post.
Use the appropriate state/specifying agency’s guardrail terminal standards for grading and
widening for the CCT.
There may be instances where a break will be required in the cable run. In these circumstances
proper overlap of the terminals is required in order to prevent a vehicle from passing through the
protected area. Depending on the location of the cable with respect to the direction of traffic, there
are two situations which can occur. See Appendix B for recommended overlaps.
Important: A flare rate of 30:1 or flatter is required if the barrier must be flared,
transverse across the median, or if CASS® must have a change in
direction (See Appendix A).

TrinityHighway.com 15 Revision A November 2021
Assembly on a Curve
Horizontal Curve
Complete the following steps to place the posts or post foundations along a curve.
1. When the cable is placed on a curve, post spacing may need to be reduced based
on the radius.
2. Weak soil conditions may necessitate a larger/deeper footing for the line posts,
based on the radius of the curve.
3. When placing posts on a curve, use the table below to adjust the spacing as required:
Curve Radius
Post Spacing
0 to 650’
CASS® is not recommended.
650’ to 1300’ [198 m to 396 m]
10’ [3.05 m] post spacing or less (as specified by the state/specifying
agency)
Greater than 1301’ [396 m]
16’-4” [5 m] post spacing or less (as specified by the state/specifying
agency)
Note: If any of the post spacing for a particular radii grouping is larger than the contract
specifications, use the contract specification post spacing.
Vertical Curve
For a sag vertical curve, the recommended minimum K value is 100’ [30 m]. There is no K value
limit for crest vertical curves.
K= L / (g1-g2)
L = length of vertical curve in feet [meters) between the two tangents
g1 = grade of tangent in
g2 = grade of tangent out
When the minimum sag vertical curve value is not met, the use of intermediate terminals at the
low point of the sag curve is recommended to minimize the cables from rising beyond the
allowable height tolerance relative to grade.
Line Post Foundation Placement
Warning: If the post cannot be placed, pursuant to these assembly
instructions, because of soil conditions, or any other environmental factor,
please contact the state/specifying agency immediately! NEVER attempt to
place posts if these assembly instructions cannot be complied with.
Post Alignment
Lay out the post alignment and post spacing according to the contract specifications.
Maximum post spacing is 16’-4” [5 m].
Driven Foundation Sleeve With and Without Soil Plate
Complete the following steps for a driven foundation sleeve assembly.
1.
Drive the foundation sleeve (PN-33950G) or foundation sleeve with soil plate (PN-
33952A) with an appropriate driving head. During the driving process ensure that the
sleeve is aligned, properly oriented (with interior tabs 15” [375 mm] from the top of the
tube sleeve and the 3” [75 mm] side parallel to the roadway), soil is prevented from
coming up into the sleeve, and the sleeve is not damaged.

TrinityHighway.com 16 Revision A November 2021
Sleeve in Poured Concrete Footing
Complete the following steps for placing a sleeve in a poured concrete footing.
1.
Place a plastic cap (PN-5833) on the bottom of the foundation sleeve (PN-33985G) or
tape the bottom end of the foundation sleeve to prevent the concrete from coming into the
tube.
2.
Punch or auger a minimum 12” [300 mm] diameter x 30” [762 mm] deep hole for the
concrete footing.
3.
Pour the MSC in the hole so the concrete is flush with the finish grade.
4.
Place the foundation sleeve in the poured concrete footing. Ensure that the sleeve is
positioned plumb, flush with the top of the footing, properly oriented (with interior tabs 15”
[375 mm] from the top of the tube sleeve and the 3” [75 mm] side parallel to the roadway),
and in alignment. Consolidate the concrete to remove air pockets in compliance with
applicable state specifications for similar applications.
5.
a minimum of 4” [100 mm] from the edge of the footing, and in alignment.
6.
Place a rebar ring (PN-5836B) around the top of the sleeve 2” to 3” [50 mm to 75 mm]
from the top of the footing.
7.
Smooth off the top of the concrete footing with a slight crown from the sleeve.
8.
Allow the footing to attain the required concrete strength before disturbing the foundations,
including the placement of posts.
Sleeve in Mow Strip
When a mow strip is used that meets the criteria in drawing SS 720, sleeve (PN-33938G) may be
used.
Complete the following steps for placing a sleeve in a mow strip.
Footing utilized with a qualified Mow Strip Assembly
1. Place a plastic cap (PN-5833) on the bottom of the foundation sleeve (PN-33938G) or tape
the bottom end of the foundation sleeve to prevent the concrete from coming into the tube.
Monolithic Pour:
A.
Punch or auger a minimum 12” [300 mm] diameter hole, 24” [600 mm] deep for the
concrete footing. The MCS will be placed in the hole as part of the mow strip poured.
B.
Proceed to step 3 below.
Footings Placed after the Construction of the Mow Strip:
A. Place leave-out material at each footing location in the strip to allow the footing hole to be
augered or punched after the mow strip is constructed.
B. Proceed to step 3 below.
2.
Pour the MSC.
3.
Consolidate the concrete to remove air pockets in compliance with applicable state
specifications for similar applications.
4.
Place the foundation sleeve plumb and in alignment with the string line, ensuring a minimum
of 3” [75 mm] of concrete surrounds the sleeve on all sides, and the top is flush with the top
of the concrete footing.
5.
Smooth off the top of the concrete footing with a slight crown from the sleeve.

TrinityHighway.com 17 Revision A November 2021
6.
Allow the footing to attain the required concrete strength before disturbing the foundations,
including the placement of posts.
Precast Concrete Footings
The precast concrete footings will be fabricated in forms and installed the same as if placed in
an augured or punched hole.
Post Placement
Posts
CASS® posts can be driven, placed in a driven sleeve, placed in a sleeve in a concrete footing
(poured or precast), or mounted to a concrete surface (Base Plated Post-See Appendix C).
All C-Channel Posts shall be alternately rotated 180 degrees as shown in Figure 1, Post
Orientation.
Driven Posts
Complete the following steps for a driven post assembly.
1.
Lay out the post alignment and post spacing according to contract specifications and drive
the post (PN-33901G) with an appropriate driving head equipment.
2.
The height from the finished grade to the top of the post is approximately 2’-8 1/4”
[0.819 m].
Posts in Sleeve
Complete the following steps for a post in the sleeve assembly
1.
Place the post sleeve cover (PN-5823B) on the bottom end of the CASS® post.
2.
Place the post in the sleeve so it rests on the first tab in the sleeve or bottom of the sleeve
and the sleeve cover is located at the top of the sleeve.
3.
The height from the finished grade to the top of the post is approximately 2’-8¼” [0.819m].
Base Plated Post
For Base Plated Post Assembly, see Appendix D.
CASS® Cable End Treatments
CASS® is terminated with either a CCT or a CCA.
CCT
The CCT consists of three (3) CRP (Bottom CRP and Top CRP Post) and six (6) S3 x 5.7# [S75
x 8] terminal line posts. The cables are terminated at the CRP, one at each post. The terminal

TrinityHighway.com 18 Revision A November 2021
line posts are placed with sleeve in a concrete footing, a sleeve with a soil plate, or a driven post
with a soil plate.
See Figure 2 for the footing locations and spacing.
Based on soil conditions at the site, the CCT may need larger/deeper concrete anchors or larger
soil plates (for driven applications) as determined through soil analysis.
Bottom CRP with Concrete Footings
Place the Bottom CRP (PN 33936A) in a minimum 18” [450] diameter x 5’-0” [1.50 m] deep
reinforced MSC footing. The footing is reinforced with a spiral rebar cage.
Complete the following steps for the placement of the Bottom CRP in the concrete footing:
1.
Lay out the three (3) CRP footings.
2.
Punch or auger the appropriate hole for the concrete footing.
3.
Fabricate a rebar cage in accordance with project/shop drawing requirements. A standard
spiral rebar cage that may be applicable is PN-33916B (See Figure 3).
4.
Place the rebar cage in the footing hole, ensuring a minimum of 3” [75 mm] of concrete
surrounds the cage on all sides and the cage is approximately 3” [75 mm] from the top of
the footing (finished grade). Place the Bottom CRP in the center of the spiral rebar cage,
ensuring the top of the post is no more than 4” [100 mm] above the finished grade. See
Figure 3 for the orientation of the post.
5.
Place the MSC in the hole. Consolidate the concrete to remove air pockets in compliance
with applicable state specifications for similar applications.
6.
Smooth off the top of the concrete footing with a slight crown from the sleeve.
7.
Allow the footing to attain the required concrete strength before disturbing the foundations,
including the placement of posts.

TrinityHighway.com 19 Revision A November 2021
N
Bottom CRP with Soil Plate
The Bottom CRP with Soil Plate assembly, size based on soil conditions, can be driven or
placed in an augured hole. The soil plate can be either welded or bolted to the bottom CRP
(See Figure 3).
Complete the following steps for assembling the CCT Bottom CRP with Soil Plate:
1.
Lay out the three footings.
2.
Punch or auger a pilot hole approximately 4’-0” [1.92 m] or deeper for the Bottom CRP
with soil plate if the post is not completely driven. Place the Bottom CRP with soil plate in
the hole. The post is to be aligned with the soil plate on the downstream side of the post.
Drive the post so that the top of the Bottom CRP does not protrude more than 4” [100 mm]
above the finished grade.
3.
Backfill the hole with material in 6" [150 mm] lifts and compact to optimum compaction.
CCT Line Footings
Post Alignment
Lay out the post alignment and post spacing. Starting at post 4, post spacing for posts 4 through
9 is 6’-6” [1.98 m]. The posts will be on the center line of the cable assembly.
Terminal Line Sleeve in a Poured Concrete Footing – Posts 4 through 9
Complete the following steps for placing a line terminal sleeve in a poured concrete footing:
1.
Place the end cap (PN-5837B) on the bottom of the foundation sleeve (PN-33908G) to
prevent the concrete from coming into the tube.
Table of contents
Other Trinity Highway Control System manuals
Popular Control System manuals by other brands
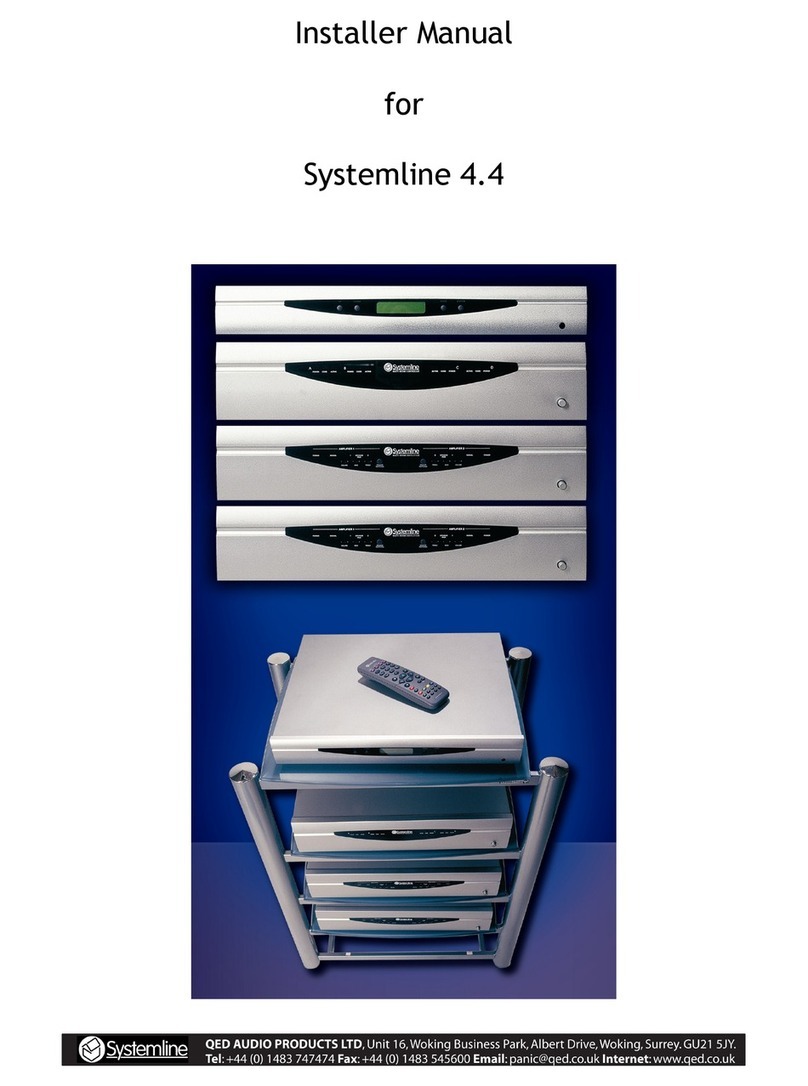
Systemline
Systemline 4.4 Installer manual
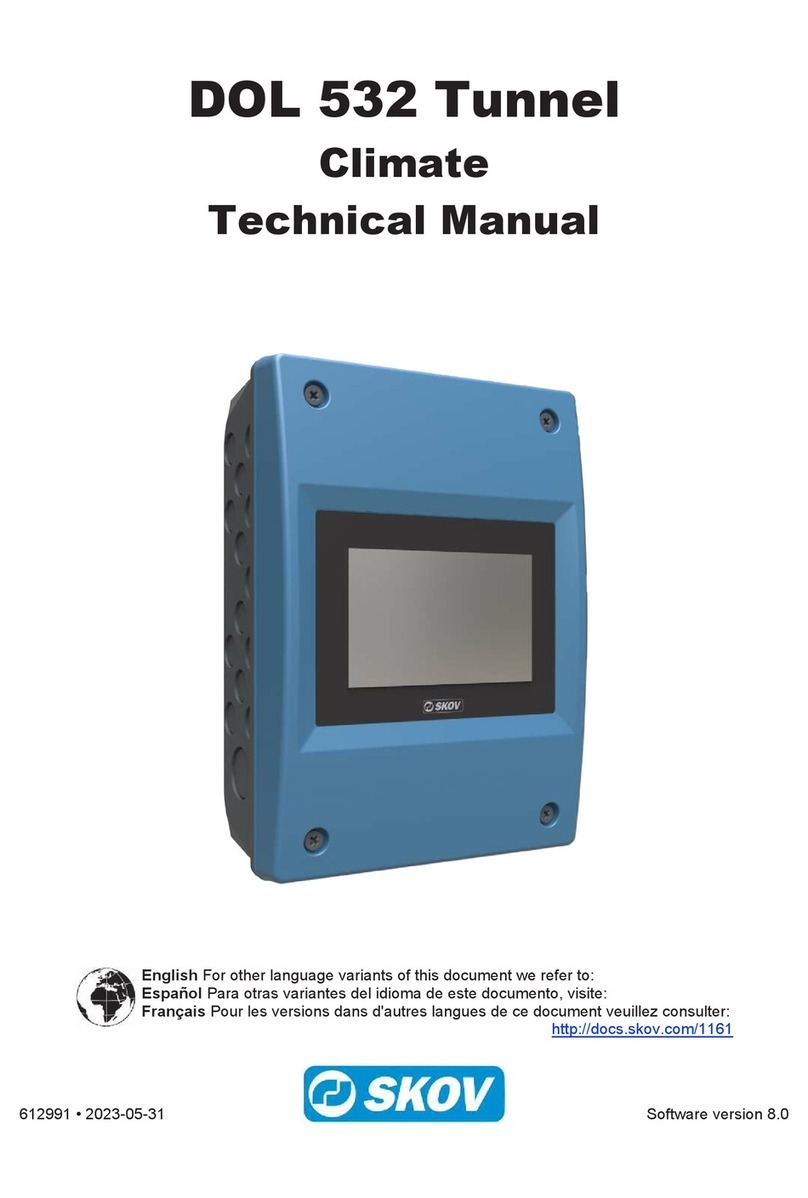
Skov
Skov DOL 532 Tunnel Technical manual
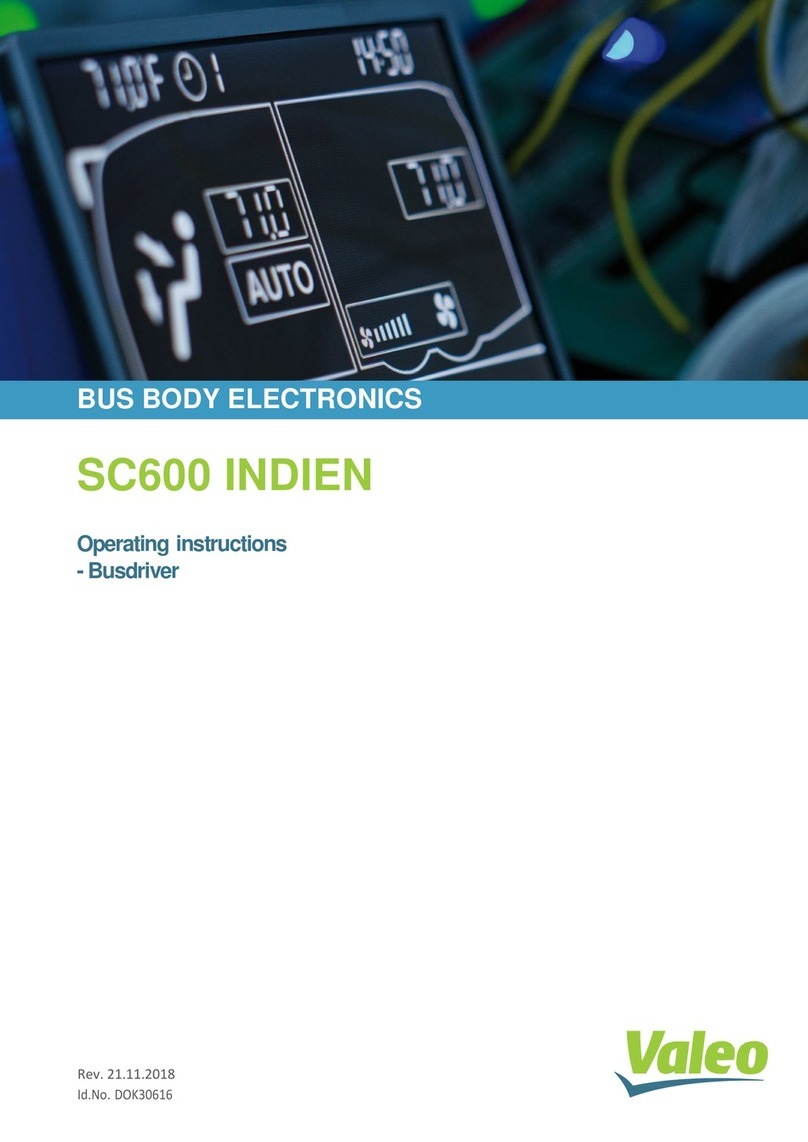
Valeo
Valeo SC600 Indien operating instructions
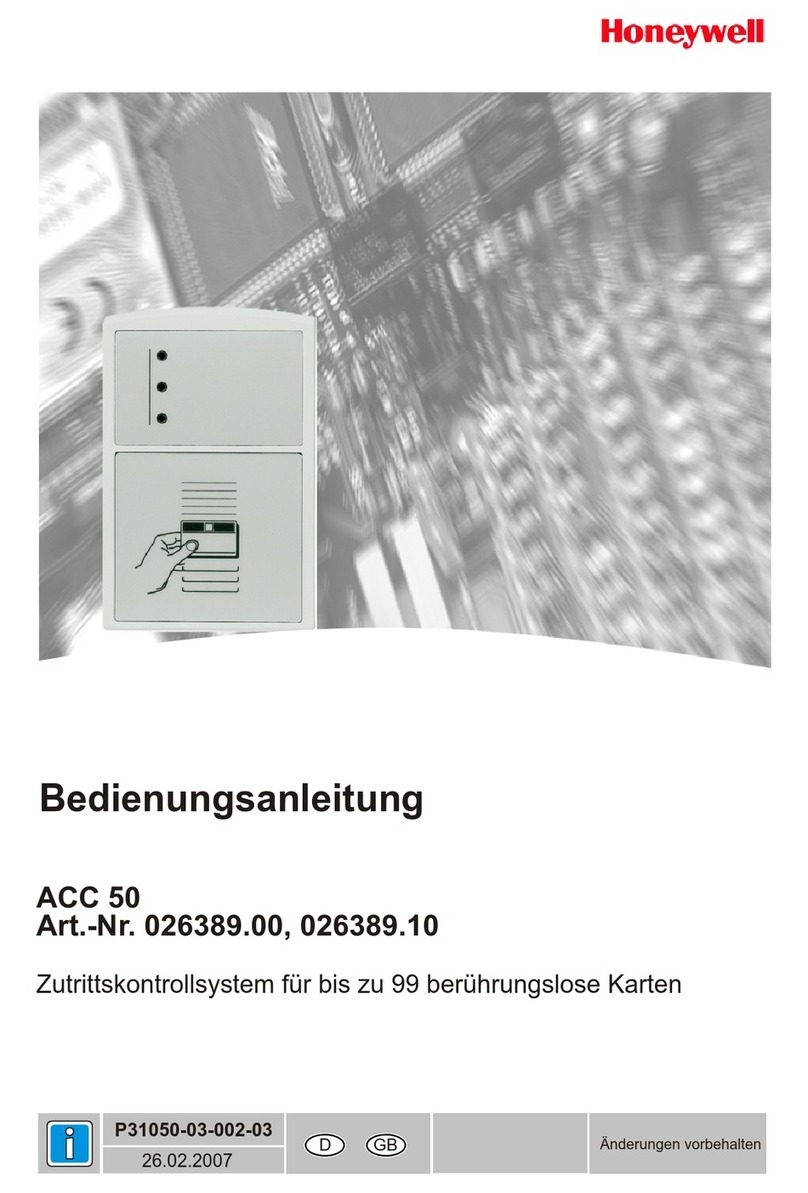
Honeywell
Honeywell ACC 50 operating instructions
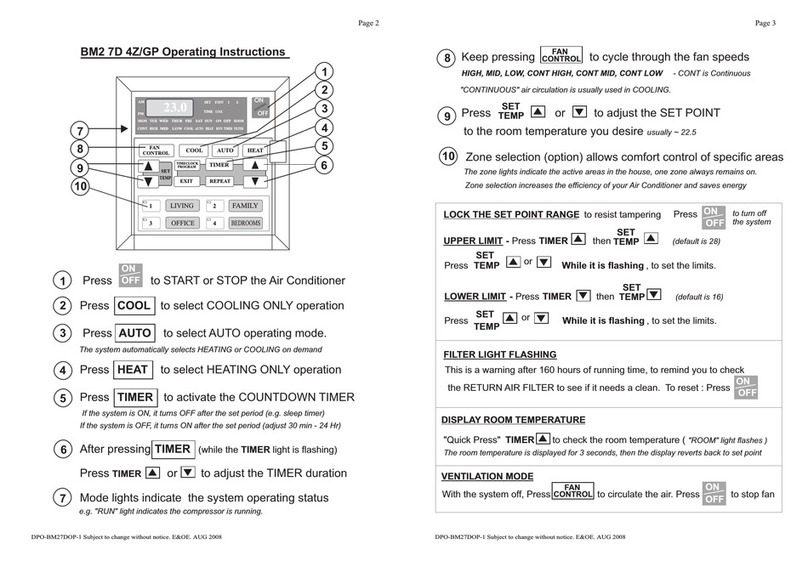
ActronControls
ActronControls Leasam BM2-7D-4Z operating instructions
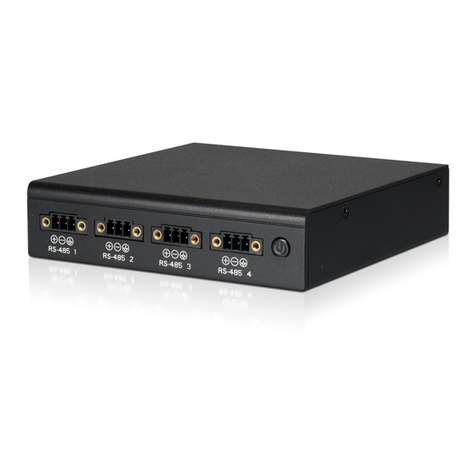
VIA Technologies
VIA Technologies ARTiGO-A600 Development guide