Trinity ET Plus 350 User manual

ENERGY ABSORPTION SYSTEMS
ET Plus®
350
Guardrail End
Treatment
Assembly Manual
Part No. 620292B Revised March 2010

www.highwayguardrail.com 1Revised: October 5, 2009
ET-PLUS™ Systems
Guardrail End Treatment
Instructional Manual
Trinity Highway Products, LLC.
2525 Stemmons Freeway
Dallas, Texas 75207
This Manual must be available to the workers at all times. For
additional copies, contact Trinity Highway Products, LLC. at
800-527-6050.
All information, illustrations, and specifications in this Manual are based
on the latest ET-PLUS™ systems information available at the time of
printing. We reserve the right to make changes at any time.
IMPORTANT: These instructions are to be used only in
conjunction with the installation of the ET-PLUS™systems.
These instructions are for standard installations specified by
the appropriate state/specifying agency. In the event the
specified systems installation requires or involves special
circumstances, contact the appropriate state/specifying
agency before proceeding. Trinity Highway Products, LLC.
representative is available for consultation, if required.
Revised: March 2010

www.highwayguardrail.com 2 Revised: March 2010
CUSTOMER SERVICE CONTACTS
Trinity Highway Products, LLC is committed to the highest level of customer
service. Feedback regarding the ET-PLUS™ systems, their installation
procedures, supporting documentation, and performance is always welcome.
Our goal is to enhance highway safety through innovation. Additional
information for materials and product specifications can be obtained by
calling the telephone numbers or writing to the email address below:
TRINITY HIGHWAY PRODUCTS, LLC:
Telephone: 800-644-7976 (U.S. Calls)
+1-214-589-8140 (International)
REGIONAL TELEPHONE CONTACTS:
Dallas, Texas 800-527-6050
Centerville, Utah 800-772-7976
Elizabethtown, Kentucky 800-282-7668
Girard, Ohio 800-321-2755
Orangeburg, South
Carolina 800-835-9307
SUGGESTED SAFETY RULES FOR INSTALLATION
- MAINTENANCE - REPAIR
* IMPORTANT SAFETY INSTRUCTIONS *
Always keep this Manual in a location where it is easily accessed by persons
who install, maintain, or repair the ET-PLUS™ systems.
SAFETY SYMBOLS
Below are the safety symbols that may appear on the ET-PLUS™ systems or
in the documentation. Read the entire Manual for suggested safety,
assembly, installation, maintenance, repair, and service information.
SYMBOL MEANING
SAFETY ALERT SYMBOL
Indicates Danger, Warning, or Caution. Failure to
read and follow the Danger, Warning, and Safety or
Caution indicators could result in serious injury or
death to the workers and/or bystanders.
WARNING – READ MANUAL
Read the Manual(s) and follow all warnings and
safety instructions. Failure to follow this warning
could result in serious injury or death to the workers
and/or bystanders.

www.highwayguardrail.com 3 Revised: March 2010
WARNINGS AND CAUTIONS
Read all warnings, cautions, and instructions before installing/
maintaining/repairing the ET-PLUS™ systems.
IMPORTANT: READ SAFETY INSTRUCTIONS THOROUGHLY
AND FOLLOW THE SAFE OPERATION PRACTICES WHILE
INSTALLING THE ET-PLUS™ systems. Failure to follow this warning
could result in serious injury or death to the workers and/or
bystanders.
WARNING: Read the instructions carefully. Be familiar with the
complete instructions for the ET-PLUS™ systems before installing,
maintaining, or repairing the ET-PLUS™ systems. Failure to follow
this warning could result in serious injury or death in the event of a
collision.
WARNING: Ensure that the necessary traffic control is setup and any
debris that has encroached onto the traveled way or shoulder has
been removed, before beginning installation or repairs. Failure to
follow this warning could result in serious injury or death in the event
of a collision.
WARNING: Be sure adequate time is available for complete
installation, before beginning the installation process. Failure to
follow this warning could result in serious injury or death in the event
of a collision.
WARNING: Do NOT perform installation, maintenance, or repair of
the ET-PLUS™ systems when tired, ill, or under the influence of
alcohol, drugs, or medication. Failure to follow this warning could
result in serious injury or death in the event of a collision.
WARNING: Do not install, maintain, or repair the ET-PLUS™
systems, until you have read this Manual thoroughly. Please call
Trinity Highway Products, LLC at 800-644-7976, if you do not
understand the installation instructions. Failure to follow this warning
could result in serious injury or death in the event of a collision.
WARNING: Use only Trinity Highway Products’ parts on the ET-
PLUS™ systems for installation, maintenance, or repair. The
installation or co-mingling of unauthorized parts is strictly prohibited.
Failure to follow this warning could result in serious injury or death in
the event of a vehicle impact with a system that has not been
accepted by the Federal Highway Administration (“FHWA”). The ET-
PLUS™ systems and its component parts have been accepted for
state use by FHWA. However, a co-mingled system has not been
accepted.
WARNING: Do NOT modify the ET-PLUS™ systems in any way.
Failure to follow this warning could result in serious injury or death in
the event of a collision.
WARNING: Do NOT perform installation, maintenance, or repair, if
the ET-PLUS™ systems site, shoulder, or traveled area is covered or
encroached by road debris. Failure to follow this warning could result
in serious injury or death in the event of a collision.
WARNING: Safety measures, incorporating traffic control devices,
must be used to protect all personnel, while at the installation,
maintenance, or repair site. Failure to follow this warning could result
in serious injury or death to the workers and/or bystanders. .
WARNING: Ensure that the entire work zone site is visible at all
times. Failure to follow this warning could result in serious injury or
death to the workers and/or bystanders.
WARNING: Use caution when working near public roads. Be mindful
of vehicles in motion nearby. Failure to follow this warning could
result in serious injury or death to the workers and/or bystanders.
WARNING: Ensure that all Guardrail products and delineation used
meet all federal, state/specifying agency, and local specifications.
Failure to follow this warning could result in serious injury or death in
the event of a collision.

www.highwayguardrail.com 4Revised: October 5, 2009
WARNING: Ensure that your installation, repair, and maintenance
meet all appropriate Manual on Uniform Traffic Control Devices
(MUTCD) and local standards. Failure to follow this warning could
result in serious injury or death in the event of a collision.
WARNING: Ensure that the Guardrail you install is terminated, as
dictated by the state/specifying agency, pursuant to FHWA
acceptance. Failure to follow this warning could result in serious
injury or death in the event of a collision.
WARNING: Do NOT install SYTP™ at location 1. Failure to
follow this warning could result in serious injury or death in the
event of a collision.
WARNING: Do NOT install 6’0” CRT post at location 1. Failure to
follow this warning could result in serious injury or death in the
event of a collision.
WARNING: Do NOT bolt the rail panel to the post at location 1 in
any of the ET-PLUS™ systems. Failure to follow this warning
could result in serious injury or death in the event of a collision.
WARNING: Do NOT bolt the rail to the HBA™ post at location 2.
Failure to follow this warning could result in serious injury or death
in the event of a collision.
WARNING: Ensure that there is proper site grading for tube and
post placement, as dictated by the state/specifying agency,
pursuant to FHWA acceptance. Failure to follow this warning
could result in serious injury or death in the event of a collision.
WARNING: Ensure that the proper Leaveout (specified area of
open space in the pavement) around the posts is reserved and
filled with state/specifying agency approved backfill material that
will not prevent movement, for any posts installed in rigid
pavement such as any thickness of concrete or asphalt. Failure to
follow this warning could result in serious injury or death in the
event of a collision.
WARNING: Ensure that all of the ET-PLUS™ systems Warnings,
Cautions, and Important statements within the ET-PLUS™
systems Manual are completely followed. Failure to follow this
warning could result in serious injury or death in the event of a
collision.
WARNING: Always use safety precautions when performing
installation, maintenance, repair, mixing chemicals, and/or moving
heavy equipment. Wear steel toe shoes, gloves, safety goggles,
and back protection. Failure to follow this warning could result in
serious injury or death to the workers and/or bystanders.
WARNING: Ensure all wood blocks or composite blocks used with
steel posts are routered. Failure to follow this warning could result
in serious injury or death in the event of a collision.
WARNING: Ensure that this installation conforms with the
guidance provided by the AASHTO Roadside Design Guide,
including, but not limited to, those regarding placement on curbs.
Failure to follow this warning could result in serious injury or death
in the event of a collision.
WARNING: Any grout, backfill, or other materials (such as
concrete, asphalt, or soil) must be low enough so as not to
obstruct, constrain, or otherwise engage the bearing plate. Failure
to eliminate the interaction of soil or materials with the bearing
plate will hinder the performance of the ET-PLUS™ systems and
could result in serious injury or death in the event of a collision.
CAUTION: Ensure before installing, maintaining, or repairing the
ET-PLUS™ systems that no parts are frayed, damaged, or broken.
Failure to follow this warning could result in serious injury to the
workers and/or bystanders.
Revised: March 2010

www.highwayguardrail.com 5Revised: October 5, 2009
KNOW YOUR ET-PLUS™ SYSTEMS
ET- PLUS™ (TL-3)
50' (15.24 m) SYSTEM
For specific installation, maintenance, or repair details,
refer to the state/specifying agency’s standard drawing(s).
(This drawing represents one (1) version of the 50' (15.24 m) systems)
Alternates for Foundation Tubes
At post locations 1 and 2, the alternates to long foundation tube without soil plate
are:
•Hinged Breakaway™ (“HBA™”) post
•Short tube with soil plate
•HBA™ post at location 1, Steel Yielding Terminal Post™
(“SYTP™”) at location 2
•Long foundation at location 1, SYTP™ at location 2
•Short foundation with soil plate at location 1, SYTP™ at
location 2
The alternate to two (2) 12' 6" (3.81 m) long rail elements is one (1)
25’ 0” (7.62 m) long rail element.
For post locations 3 through 8 (50’ (15.24 m) system), alternates
are:
•All short tubes without soil plates and breakaway wood
posts
•All HBA™ posts
•All CRT posts
•All SYTP™
•Any combination of above options, as accepted by the
FHWA and dictated by the state/specifying agency
Revised: March 2010

www.highwayguardrail.com 6Revised: October 5, 2009
ET-PLUS™ (TL-3)
37’ 6" (11.43 m) SYSTEM
For specific installation, maintenance, or repair details,
refer to the state/specifying agency’s standard drawing(s).
(This drawing represents one (1) version of the 37' 6” (11.43 m) systems)
Alternates for Foundation Tubes and Posts
At post locations 1 and 2, the alternates to long foundation tube
without soil plate are:
•HBA™ post
•HBA™ post at location 1 and SYTP™ at location 2
•Long foundation tube or short tube with soil plate at
location 1 and SYTP™ at location 2
For post locations 3 through 7 (37’ 6” (11.43 m) system),
alternates are:
•All short tubes without soil plates and breakaway wood
posts
•All HBA™ posts (HBA™ post required at location 8)
•All CRT posts
•All SYTP™ (SYTP™ required for location 8)
•Any combination of above options, as accepted by the
FHWA and dictated by the state/specifying agency
Revised: March 2010

www.highwayguardrail.com 7Revised: October 5, 2009
ET-PLUS™ (TL-2)
25' (7.62 m) SYSTEM
For specific installation, maintenance, or repair details,
refer to the state/specifying agency’s standard drawing(s).
(This drawing represents one (1) version of the 25' (7.62 m) systems)
Alternates for Foundation Tubes, Rail Panels, and Posts
At post locations 1 and 2, the alternates to long foundation tube
without soil plate are:
•HBA™ post
•HBA™ post at location 1 and SYTP™ at location 2
•Long foundation tube or short tube with soil plate at
location 1 and SYTP™ at location 2
The alternate to two (2) 12' 6" (3.81 m) long rail elements is one (1)
25’ 0” (7.62 m) long rail element.
For post locations 3 through 4 (25’ (7.62 m) system), alternates
are:
•Short steel foundation tubes without soil plates and
breakaway wood posts or SYTP™ in tubes
•All HBA™ posts
•All CRT posts
•All SYTP™
Revised: March 2010

www.highwayguardrail.com 8Revised: October 5, 2009
BILL OF MATERIAL ENGLISH (METRIC)
WARNING: Use only Trinity Highway Products’ parts on the ET-
PLUS™ systems for installation, maintenance, or repair. The
installation or co-mingling of unauthorized parts is strictly
prohibited. Failure to follow this warning could result in serious
injury or death in the event of a vehicle impact with a system that
has not been accepted by the Federal Highway Administration
(“FHWA”). The ET-PLUS™ systems and its component parts have
been accepted for state use by FHWA. However, a co-mingled
system has not been accepted.
ET-PLUS™ SYSTEMS
(For specific materials and quantities, see state/specifying agency’s option(s))
PN Description
9G 12/12.5'/6’ 3"/S (2.67/3.81/1.905/S) (Guardrail)
32G 12/12.5"/6' 3"/S (2.67/3.81/1.905/S) ANC (Guardrail)
60G 12/25'/6' 3"/S (2.67/7.62/1.905/S) (Guardrail)
62G 12/25'/6' 3"/S (2.67/7.62/1.905/S) ANC (Guardrail)
704A Cable Anchor Bracket
705G Pipe Sleeve - 2" STD Pipe x 51/2" (50 STD Pipe x 150
Pipe)
740G* 6" x 8" x 4' 6" x 3/16 (152 x 203 x 1375 x 4.8) Tube Sleeve
749G 6" x 8" x 6' 0" x 3/16 (152 x 203 x 1830 x 4.8 Tube
Sleeve (Alternate to using 740G and 766G)
766G* 18" x 24" x 1/4" (460 x 610 x 16) Soil Plate
782G 8" x 8" x 5/8” (200 x 200 x 16) Bearing Plate
995A ET-PLUS™ Extruder (Head)
3000G Cable (Assembly) 3/4" x 6' 6" (19 x 1981)
3300G 5/8" (16) Round Washer
3340G 5/8" (16) HGR Nut
3360G 5/8" DIA. X 11/4" (16 DIA. x 35) Splice Bolt (HGR)
3478G 5/8" DIA. x 71/2" (16 DIA. x 190) Hex Head Bolt
3497G 5/8" DIA. x 91/2" (16 DIA. x 240) Hex Head Bolt
3500G 5/8" DIA. x 10" (16 DIA. x 255) HGR Post Bolt
3580G 5/8" DIA. x 18" (16 DIA. x 460) HGR Post Bolt
3701G 3/4" (19) Washer
3704G 3/4” (19) HEX Nut
3717G 3/4“ x 21/2" (19 x 75) Hex Head Bolt (High Strength)
3718G 3/4" x 3” (19 x 75) Hex Head Bolt (High Strength)
3900G 1" (25) Round Washer
3910G 1" (25) Hex Nut
4063B Wood Post 6" x 8" x 6' 0" (150 x 200 x 1830) CRT
4075B Wood Block 6" x 8" x 14" (150 x 200 x 360) DR
4076B Wood Block - 6” x 8” x 14” (150 x 200 x 360) DR
4147B Wood Post - 51/2” x 71/2” x 3’ 9" (140 x 190 x 1145)
4254G 3/8” (10) Round Washer
4255G 3/8” (10) Fender Washer 11/2” OD (38)
4258G 3/8” (10) Lockwasher
4261G 3/8” DIA. X 11/2" (10 x 38) Hex Head Bolt
4228B 3/8” x 4" (10 x 100) Lag Screw
4388G 7/16” (11) Hex Nut
4389G 7/16” (11) Round Washer
4390G 7/16” DIA. x 11/2” (11 x 38) GR. 5 Hex Head Bolt
4393G 7/16” (11) Lockwasher
5148G 3/4” DIA. X 91/2” (19 DIA. x 240) Hex Head Bolt (High
Strength)
4699G 3/4” (19) Lockwasher
Revised: March 2010

www.highwayguardrail.com 9Revised: October 5, 2009
PN Description
6321G 3/8” x 2’ (10 x 50) Hex Head Bolt (High Strength)
6405G 3/8” (10) Hex Nut
6907B Polymer Block 4” x 71/2” x 14” (100 x 187 x 350) [King
Block]
14329G#3’ 65/8” SYTP Stub
14578G#6’ Steel Yielding Terminal Post (SYTP)
33871A#ET HBA Post #1 Top
33873A#ET HBA Post #1 and #2 Bottom
33874A#ET HBA Post #3 - #8 Bottom
33877A#ET HBA Post #2 - #8 Top
9852A#Strut (and Yoke Assembly)
33875G#6' 6" (1980) Angle Strut ET HBA
33795G# 6’ 6” (1980) Angle Strut
33730G#6’ 71/2” (1980) Angle Strut
33847G#6’ 91/8” Angle Strut
*Option to the 6’0” Post Sleeve Tube
#Review the state/specifying agency’s standard drawings of these
systems, for details that are specific to the project or site locations.
Delineation Options
PN Description
6206B Right Side 13” x 27 1/2” (325 x 700) Reflective Sheeting
6207B Left Side 13” x 27 1/2” (325 x 700) Reflective Sheeting
6668B Either Side 12” x 12” (305 x 305) Reflective Sheeting
(Typically 2 required)
Revised: March 2010

www.highwayguardrail.com 10 Revised: October 5, 2009
Use Trinity Highway Products’ drawings for the ET-PLUS™ systems with
these instructions. Review the state/specifying agency’s standard
drawings of this system. Details will be specific to the project or site
locations.
WARNING: Use only Trinity Highway Products’ parts on the ET-
PLUS™ systems for installation, maintenance, or repair. The
installation or co-mingling of unauthorized parts is strictly
prohibited. Failure to follow this warning could result in serious
injury or death in the event of a vehicle impact with a system that
has not been accepted by the Federal Highway Administration
(“FHWA”). The ET-PLUS™ systems and its component parts have
been accepted for state use by FHWA. However, a co-mingled
system has not been accepted.
WARNING: Ensure that there is proper site grading for tube and
post placement, as dictated by the state/specifying agency,
pursuant to FHWA acceptance. Failure to follow this warning
could result in serious injury or death in the event of a collision.
WARNING: Ensure that the proper Leaveout (specified area of
open space in the pavement) around the posts is reserved and
filled with state/specifying agency approved backfill material that
will not prevent movement, for any posts installed in rigid
pavement such as any thickness of concrete or asphalt. Failure to
follow this warning could result in serious injury or death in the
event of a collision.
WARNING: Do NOT install 6’0” CRT post at location 1. Failure to
follow this warning could result in serious injury or death in the
event of a collision.
WARNING: Do NOT install SYTP™ at location 1. Failure to
follow this warning could result in serious injury or death in the
event of a collision.
WARNING: Ensure that all Guardrail products and delineation
used meet all federal, state/specifying agency, and local
specifications. Failure to follow this warning could result in serious
injury or death in the event of a collision.
MATERIALS
As packaged, the ET-PLUS™ systems include all materials needed for a
complete installation. This will include either a 50’ (15.24 m) system, 37’
6” (11.43 m) system, or 25’ (7.62 m) system pay limit, unless otherwise
specified in the contract plans. Note that concrete footings or foundations
are not required.
TOOLS REQUIRED
The following list shows recommended tools for installation of the ET-
PLUS™ systems:
•9/16” (14 mm) Socket or Wrench
•15/16” (24 mm) Socket or Wrench
•11/4” (32 mm) Socket or Wrench
•11/2” (38 mm) Socket or Wrench
•Augers
•Post Pounders (commonly used in driving posts)
•Locking Pliers
•Tape Measure
The following list shows recommended tools for the repair of the ET-
PLUS™ systems. However, since repair is directed by the
state/specifying agency, they may have more specific guidelines.
•Acetylene torch to cut off extruded rail
•Heavy-duty chain to remove the ET-PLUS™ Extruder (Head)
•Locking Pliers or channel lock pliers
•Sledge hammer
•Post removal tool and other normal guardrail tools
•Eye bolts connected to heavy duty chain (to remove the posts
from tubes)
•Vehicle to pull the Extruder from the damaged rail
INSTALLING THE ET-PLUS™ SYSTEMS
Revised: March 2010

www.highwayguardrail.com 11 Revised: October 5, 2009
SITE PREPARATION
When the Guardrail is installed in-line with edge of the shoulder (without
any offset), a 25:1 or flatter straight flare over the length of the systems
can be used to position the ET-PLUS™ Extruder (Head) further away
from the edge of the shoulder. Minor site grading may be necessary for
installations beyond the edge of the shoulder, for the proper placement of
the steel tubes and the CRT posts. Use the state/specifying agency’s
standard specifications and drawings for the site grading. Trinity does not
direct grading. Complete all grading before the start of the installation of
the ET-PLUS™ systems. See INSTALLATION OF THE ET-PLUS™
SYSTEMS ON A CURVE section for the layout of the ET-PLUS™
systems on a curve.
WARNING: Ensure that there is proper site grading for tube and
post placement, as dictated by the state/specifying agency,
pursuant to FHWA acceptance. Failure to follow this warning
could result in serious injury or death in the event of a collision.
INSTALLATION
WARNING: Ensure that this installation conforms with the
guidance provided by the AASHTO Roadside Design Guide,
including, but not limited to, those regarding placement on curbs.
Failure to follow this warning could result in serious injury or death
in the event of a collision.
For installation of the ET-PLUS™ systems, see POST INSTALLATION
section. If the systems are installed on a curve, see INSTALLATION OF
THE ET-PLUS™ SYSTEMS ON A CURVE. When installing the ET-
PLUS™ systems outside or inside the curve, the ET must be straight over
the length of the systems. If there are special field conditions
encountered when installing the ET-PLUS™ systems, contact the
state/specifying agency’s engineer. Trinity Highway Products LLC., at 1-
800-644-7976, is available to assist the state/specifying agency, if
needed.
POST INSTALLED IN RIGID MATERIAL
Provide the proper leave out (specified area of open space in the
pavement) around a post when installing the post in any thickness of
concrete or asphalt. The top surfaces of any grout or other backfill
placed in the rigid material “leave out” MUST be low enough so that
it does not engage the anchor cable bearing plate at Post 1 or
otherwise obstruct/constrain the 3/8” shear bolts or the ¾” hinge
bolts of the HBA Post.
For "leave-out" information, please consult the applicable state/specifying
agency. Additional source of "leave-out" information/details can be found
in the U.S. Department of Transportation, Federal Highway
Administration, Memorandum B64-B, dated 3-10-04. Trinity can provide
this FHWA memo upon request.
WARNING: Ensure that the proper Leaveout (specified area of
open space in the pavement) around the posts is reserved and
filled with state/specifying agency approved backfill material that
will not prevent movement, for any posts installed in rigid
pavement such as any thickness of concrete or asphalt.
INSTALLATION OF THE ET-PLUS™ SYSTEMS ON A
CURVE
When the ET-PLUS™ systems are installed on a curve, use the following
layouts. All offsets are measured to the face of the rail. Under no
circumstances shall the guardrail within the ET-PLUS™ pay limit be
curved.
Outside the curve: With the line guardrail installed parallel to the
curve, the terminal end is offset from the curve a distance equal to
the line guardrail offset plus the value in Table 1. (See
state/specifying agency drawings for details.)
•Inside the curve (radius Greater than 1000 feet): With the line
guardrail installed parallel to the curve, the terminal end is offset from
the curve a distance equal to the line guardrail offset plus the value
in Table 1. (See state/specifying agency drawings for details.)
•Inside the curve (radius 1000 feet or Less): With the line guardrail
installed parallel to the curve, the terminal end is offset from the
Revised: March 2010

www.highwayguardrail.com 12 Revised: October 5, 2009
curve a distance equal to the line guardrail offset plus 1 foot
maximum in Table 1. (See state/specifying agency drawings for
details.)
ET™ Length Outside the
Curve Max
Offset
Inside the Curve
With a Radius
Greater Than 1000
Feet Max Offset
Inside the Curve
With a Radius
1000 Feet or
Less Max Offset
50 Feet 2 Feet 2 Feet 1 Foot
37 Feet 6 Inches 1.5 Feet 1.5 Feet 1 Foot
25 Feet 1 Foot 1 Foot 1 Foot
Table 1
POST INSTALLATION
Complete the following steps when installing wood CRT posts, foundation
tubes with wood posts, HBA™ posts, and SYTP™. When installing posts
in rigid pavement, see the POST INSTALLED IN RIGID MATERIAL
section.
WARNING: Ensure that the proper Leaveout (specified area of
open space in the pavement) around the posts is reserved and
filled with state/specifying agency approved backfill material that will
not prevent movement, for any posts installed in rigid pavement
such as any thickness of concrete or asphalt. Failure to follow this
warning could result in serious injury or death in the event of a
collision.
INSTALLING THE WOOD CRT POSTS
Complete the following steps to install the wood CRT posts:
Step Actions
1. Install the wood posts (PN-4063B) at locations required for the
systems, spaced at 6' 3" (1270 mm) apart. Select Option A or
Option B to install the CRT posts.
Option
A
Drive posts into the ground.
Option
B
1. Drill 12” (300 mm) maximum diameter pilot
holes approximately 44" (1120 mm) deep.
2. Insert the 6' 0" (1830 mm) wood posts into these
holes.
3. Backfill the holes with compactable materials in
6" (150 mm) lifts and compact with pneumatic
equipment to optimum compaction.
Note: In either option within Step 1, the bottom of the upper 31/2"
(90 mm) hole in the post is approximately at the finished grade.
WARNING: Do NOT install 6’0” CRT post at location 1.
Failure to follow this warning could result in serious injury
or death in the event of a collision.
WARNING: Ensure that the proper Leaveout (specified
area of open space in the pavement) around the posts is
reserved and filled with state/specifying agency approved
backfill material that will not prevent movement, for any
posts installed in rigid pavement such as any thickness of
concrete or asphalt. Failure to follow this warning could
result in serious injury or death in the event of a collision.
Revised: March 2010

www.highwayguardrail.com 13 Revised: October 5, 2009
PLACING FOUNDATION TUBES FOR WOOD OR SYT™ POSTS
Complete the following steps to install foundation tubes and Wood or
SYT™ posts:
Step Actions
1. Select Option A or Option B for this tube installation.
1. For 6' 0" (1830 mm) Tube without Soil Plate
1. Install the foundation tube (PN-749G), per
Step 2 below.
Option
A
2. For 4’ 6” (1375 mm) Tube without Soil Plate
(locations 3 through 8, locations 3 through 7,
or locations 3 through 4)
1. Install the soil tube (PN-740G), per Step 2
below.
1. For 4' 6" (1375 mm) Tube with Soil Plate
(locations 1 & 2)
1. Assemble the soil tubes and soil plates.
2. Bolt the soil plate (PN-766G) to the
foundation tube (PN-740G) with two 5/8" x
71/2" (16 mm x 190 mm) Hex Head Bolts
(PN-3478G) and 5/8" (16 mm) HGR Nuts
(PN-3340G) (no washers).
3. Install the foundation tube (PN-766G) with
soil plate, per Step 2 below.
Option
B
2. For 4’ 6” (1375 mm) Tube without Soil Plate
(locations 3 through 8, locations 3 through 7, or
locations 3 through 4)
1. Install the soil tube (PN-740G), per Step 2
below.
Note: Do not over tighten the nuts and deform the tubes, this will
complicate post replacement.
WARNING: Ensure that the proper Leaveout (specified
area of open space in the pavement) around the posts is
reserved and filled with state/specifying agency approved
backfill material that will not prevent movement, for any
posts installed in rigid pavement such as any thickness of
concrete or asphalt. Failure to follow this warning could
result in serious injury or death in the event of a collision.
2. Install the foundation tubes at locations 1 and 2. Use the strut
as a guide for the spacing of the tubes. If the soil plate is
utilized, position it on the downstream side of the post (away
from the impact head).
Note: Do not drive tubes with the wood post inserted, this will
complicate post replacement.
INSTALLATION OPTIONS FOR FOUNDATION TUBES FOR
WOOD OR SYT™ POSTS
Complete the following steps to install foundation tubes and Wood or
SYT™ posts:
FOR PERMEABLE SOIL
Step Actions
1. If the soil is permeable (water will drain from the tubes), drive
the tubes (with an appropriate driving head) to the optimum
height, where the top of the tube is 25/8” (67 mm) above the
finished grade.
Note: Take extra care to prevent settlement or lateral
displacement of the tubes, to ensure the posts attach to the
Guardrail, correctly.
2. Ensure that the finished Guardrail height will be approximately
273/4" (706 mm) above the finished grade, or as the state/
specifying agency plans indicate.
3. Ensure that the tubes do not project more than 4" (100 mm)
above the finished grade.
Revised: March 2010

www.highwayguardrail.com 14 Revised: October 5, 2009
WARNING: Ensure that the proper Leaveout (specified area of
open space in the pavement) around the posts is reserved and
filled with state/specifying agency approved backfill material that
will not prevent movement, for any posts installed in rigid
pavement such as any thickness of concrete or asphalt. Failure to
follow this warning could result in serious injury or death in the
event of a collision.
FOR NON-PERMEABLE SOIL
Step Actions
1. Select Option A, Option B, or Option C below, if soil is non-
permeable.
For 6’ Tube Only
1. Drill a 12” (300 mm) maximum diameter pilot
hole approximately 75” (1905 mm) deep.
2. Insert the tube into the hole to the optimum
depth, where the top of the tube is 25/8” (67 mm)
above the finished grade.
For 4’ 6” Tube with Soil Plate
1. Drill a 12” (300 mm) maximum diameter pilot
hole approximately 57” (1450 mm) deep.
2. Insert the soil plate/tube assembly into the hole
by impact or vibratory means with an
appropriate driving head.
3. Insert the tube to the optimum depth of where
the top of the tube is 25/8" (67 mm) of the above
the finished grade.
Option
A
For 4’ 6” Tube without Soil Plate
1. Drill a 12” (300 mm) maximum diameter pilot
hole approximately 57” (1450 mm) deep.
2. Insert the tube into the hole to the optimum
depth, where the top of the tube is 25/8” (67 mm)
above the finished grade.
Option
B
For 4’ 6” Tube with Soil Plate
Cut slots for the soil plates out by hand or by using a
rock bar and then follow all of the steps of Option A
for 4’ 6” tube with soil plate, above.
Option
C
For 4’ 6” Tube with Soil Plate
Drill three adjacent 12” (300 mm) maximum
diameter holes or one 24” (610 mm) maximum
diameter hole to accommodate the soil plate/tube
assembly and then follow all of the steps of Option A
for 4’ 6” tube with soil plate, above.
Note: Take extra care to prevent settlement or lateral
displacement of the tubes, to ensure the posts attach to the
Guardrail, correctly.
WARNING: Ensure that the proper Leaveout (specified
area of open space in the pavement) around the posts is
reserved and filled with state/specifying agency
approved backfill material that will not prevent
movement, for any posts installed in rigid pavement
such as any thickness of concrete or asphalt. Failure to
follow this warning could result in serious injury or death
in the event of a collision.
2. Backfill the hole with compactable materials in 6" (150 mm) lifts
and compact with pneumatic equipment to optimum compaction.
3. Ensure that the finished Guardrail height will be approximately
273/4" (706 mm) above the finished grade, or as the
state/specifying agency plans indicate.
4. Ensure that the tubes do not project more than 4" (100 mm)
above the finished grade.
Revised: March 2010

www.highwayguardrail.com 15 Revised: October 5, 2009
INSTALLING HBA™ BOTTOM POSTS
Complete the following steps to install HBA™ Bottom Posts:
Step Actions
1. Arrange the posts so that the large hole (13/16” [21 mm]) is placed
downstream (away from the impact end of the systems).
2. Adjust the offset to Post 2, if the ET-PLUS™ Extruder (Head)
causes a gap between the rail panel and Post 2.
Note: The rail panel must be within 1/2” (13 mm) of Post 2.
3. Select Option A or Option B for this installation.
Option
A
1. Drive the HBA™ Bottom Posts (PN-33873A,
PN-33874A) with an approved driving head
to the appropriate depths. The appropriate
depth will be approximately 72” (1830 mm)
for post PN-33873A, at Posts 1 and 2 and
44” (1120 mm) for post PN-33874A, at Posts
3 through 8, Posts 3 through 7, or Posts 3
through 4.
For HBA™ Bottom Posts (PN-33873A) at Posts 1
and 2
1. Drill a 12” (300 mm) maximum diameter pilot
hole approximately 72” (1830 mm) deep.
Option
B
For HBA™ Bottom Posts (PN-33874A) at Posts 3
through 8, Posts 3 through 7, or Posts 3 through
4
1. Drill a 12” (300 mm) maximum diameter pilot
hole approximately 44” (1120 mm) deep.
2. Insert the posts to the appropriate depth by
impact or vibratory means with an appropriate
driving head.
3. Backfill the hole with compactable materials in 6"
(150 mm) lifts and compact with pneumatic
equipment to optimum compaction.
Note: In either option, the optimum depth will have the 13/16” (21
mm) hole in the post plates (ears) even with the finished grade.
WARNING: Ensure that the proper Leaveout (specified
area of open space in the pavement) around the posts is
reserved and filled with state/specifying agency approved
backfill material that will not prevent movement, for any
posts installed in rigid pavement such as any thickness of
concrete or asphalt. Failure to follow this warning could
result in serious injury or death in the event of a collision.
INSTALLING FOUNDATION TUBES, HBA™ POSTS, OR SYTP™
WHEN ENCOUNTERING ROCK
Complete the following steps to install foundation tubes, HBA™ posts or
SYTP™ when encountering rock:
Step Actions
1. Select Option A or Option B below when encountering rock,
unless there is a more restrictive state/specifying agency
specification.
Option
A
If rock is encountered with depth of 20" (510
mm) or less
1. Drill a 12" - 16" (300 mm - 400 mm) diameter
hole into the rock.
2. Drill the hole 2" (50 mm) deeper than the
required embedment depth.
3. Place granular material or small pieces of the
drilled rock in the bottom 2" (50 mm) of the hole
for drainage.
Continues on next page.
Revised: March 2010

www.highwayguardrail.com 16 Revised: October 5, 2009
4. Install the tube/post into the hole. Backfill the
hole with compactable materials in 6" (150 mm)
lifts and compact with pneumatic equipment to
optimum compaction.
Note: If compactable, the material removed from
the hole may be used for the backfill.
Option
B
If rock is encountered with depth greater than
20" (510 mm)
1. Drill a 12" - 16" (300 mm - 400 mm) diameter
hole 22" (560 mm) deep into the rock.
2. Cut off the embedded portion of the tube/post so
the Guardrail will be installed at the proper
mounting height.
3. Place granular material or small pieces of the
drilled rock in the bottom 2" (50 mm) of the hole
for drainage.
4. Install the tube/post in the hole. Backfill the hole
with compactable materials in 6" (150 mm) lifts
and compact with pneumatic equipment to
optimum compaction.
Note: If compactable, the material removed from
the hole may be used for the backfill.
WARNING: Ensure that the proper Leaveout (specified
area of open space in the pavement) around the posts is
reserved and filled with state/specifying agency approved
backfill material that will not prevent movement, for any
posts installed in rigid pavement such as any thickness of
concrete or asphalt. Failure to follow this warning could
result in serious injury or death in the event of a collision.
INSTALLING WOOD POSTS IN TUBES
Complete the following steps to install wood posts in tubes:
Step Actions
1. Insert Pipe Sleeve (PN-705G) in post (PN-4147B) and install the
wood post in the steel tube at location 1.
2. Install wood post(s) (PN-4147B) in tubes at locations required
for the systems, as dictated by the state/specifying agency.
3. Insert a 5/8” x 91/2” (16 mm x 240 mm) Hex Head Bolt (PN-
3497G) through the foundation tube and the wood post at all
locations EXCEPT locations 1 and 2.
Note: The bolt must be installed from the embankment side, to
aid in possible post replacement.
4. Place a 5/8” (16 mm) HGR Nut (PN-3340G) on the end of the
inserted bolt.
5. Tighten the nuts to a snug position.
Note: Do not over tighten the bolts and deform the tubes, this
will complicate post replacement.
WARNING: Ensure that the proper Leaveout (specified area of
open space in the pavement) around the posts is reserved and
filled with state/specifying agency approved backfill material that
will not prevent movement, for any posts installed in rigid
pavement such as any thickness of concrete or asphalt. Failure to
follow this warning could result in serious injury or death in the
event of a collision.
INSTALLING HBA™ TOP POSTS
Complete the following steps to install the HBA™ Top Posts, after the
Bottom Posts have been installed:
AT POST 1
Step Actions
1. Install the Top Post (PN-33871A) at Post 1, by aligning the
holes of the post plates (ears) on the Top and Bottom Posts.
Note: The Top Post’s post plates (ears) can be installed on
either side of the Bottom Post’s post plates (ears).
2. Insert a 3/8” (10 mm) diameter x 2” (50 mm) Hex Head High
Strength Bolt (PN-6321G) through the 7/16” (11 mm) holes of the
Revised: March 2010

www.highwayguardrail.com 17 Revised: October 5, 2009
post plates (ears) on the Top and Bottom Posts.
3. Place a 3/8” (10 mm) Washer (PN-4252G) and a 3/8” (10 mm)
Lockwasher (PN-4258G) under a 3/8” (10 mm) Hex Nut (PN-
6405G) on the inserted bolts to secure.
Note: The bolts can be installed so the nuts are on the inside or
outside of the post plates (ears).
4. Tighten the nuts to a snug position. The designer does not
recommend a torque requirement for the HBA field assembly.
5. Insert a 3/4” (19 mm) diameter x 21/2” (63 mm) Hex Head High
Strength Bolt (PN-5148G) in the 13/16” (21 mm) hole of the
HBA™ Post 1 post plates on the side opposite the strut.
Do not install the 3/4” (19 mm) bolt on the strut side of Post 1,
until the strut is ready to be installed.
Note: The bolts can be installed so the nuts are on the inside or
outside of the post plates (ears).
6. Place a 3/4” (19 mm) Washer (PN-3701G) and a 3/4” (19 mm)
Lockwasher (PN-4699G) under a 3/4” (19 mm) Hex Nut on the
inserted bolt to secure.
7. Tighten the nuts to a snug position. The designer does not
recommend a torque requirement for the HBA field assembly.
AT POST 2
Step Actions
1. Install the Top Post (PN-33877A) at Post 2, by aligning the
holes of the post plates (ears) on the Top and Bottom Posts.
2. Insert a 3/8” (10 mm) diameter x 2” (50 mm) Hex Head High
Strength Bolt (PN-6321G) in the 7/16” (11 mm) holes.
Note: For the bolt opposite the strut, install it so the nut is on
either side of the post plates (ears). For the 3/8” (10 mm) bolt that
is on the side of the strut, install the bolt through the post plates
(ears) with the bolt head on the same side as the strut.
3. Place a 3/8” (10 mm) Washer (PN-4251G) and a 3/8” (10 mm)
Lockwasher (PN-4258G) under a 3/8” (10 mm) Hex Nut (PN-
6405G) on the inserted bolts to secure.
4. Tighten the nuts to a snug position. The designer does not
recommend a torque requirement for the HBA field assembly.
5. Insert a 3/4” (19 mm) diameter x 2 ½” (63 mm) Hex Head High
Strength Bolt (PN-5148G) through the 13/16” (21 mm) hole of the
HBA™ Post 2 post plates on the side opposite the strut.
Do not install the 3/4” (19 mm) bolt on the strut side of Post 2,
until the strut is ready to be installed.
Note: The bolts can be installed so the nuts are on the inside or
outside of the post plates (ears).
6. Place a 3/4” (19 mm) Washer (PN-3701G) and a 3/4” (19 mm)
Lockwasher (PN-4699G) under a 3/4” (19 mm) Hex Nut on the
inserted bolt to secure.
7. Tighten the nuts to a snug position. The designer does not
recommend a torque requirement for the HBA field assembly.
AT POSTS 3 THROUGH 8, POSTS 3 THROUGH 7, OR POSTS 3 AND
4
Step Actions
1. Arrange the Top Posts (PN-33877A), for Posts 3 through 8,
Posts 3 through 7, or for Posts 3 through 4, by aligning the
holes of the post plates (ears) on the HBA™ Top and Bottom
Posts, if used.
2. Insert a 3/8” (10 mm) diameter x 2” (50 mm) Hex Head Bolt (PN-
6321G) through in the 7/16” (11 mm) holes of the post plates
(ears).
3. Place a 3/8” (10 mm) washer (PN-4254G) and a 3/8” (10 mm)
Lockwasher (PN-4258G) under a 3/8” (10 mm) Hex Nut (PN-
6405G) on the inserted 3/8” diameter Hex Head Bolt.
4. Insert a 3/4” (19 mm) diameter x 21/2” (63 mm) Hex Head High
Strength Bolt (PN-6321G) through the 13/16” (21 mm) holes.
Note: The bolts can be installed so the nuts are on either side of
the post plates (ears).
Revised: March 2010

www.highwayguardrail.com 18 Revised: October 5, 2009
5. Place a 3/4” (19 mm) Washer (PN-4252G) and a 3/4” (19 mm)
Lockwasher (PN-4258G) under 3/4” (19 mm) Hex Nut on the
inserted 3/4” (19 mm) diameter Hex Head High Strength Bolt to
secure.
6. Tighten the nuts to a snug position. The designer does not
recommend a torque requirement for the HBA field assembly.
INSTALLING THE SYTP™
The SYTP™ can be driven or installed in a tube. For SYTP™ installation
in a tube, see the INSTALLING THE SYTP™ IN TUBES section. The
SYTP™ can be installed at all locations EXCEPT at location 1.
Complete the following step to install the SYTP™:
WARNING: Do NOT install SYTP™ at location 1. Failure to
follow this warning could result in serious injury or death in the
event of a collision.
DRIVING THE 6’ SYTP™
Step Actions
1. Drive all the 6’0” SYTP™ (PN-14578) to the optimum depth,
where the centers of the four (4) yielding holes through the
flange are at the ground line.
WARNING: Do NOT install SYTP™ at location 1.
Failure to follow this warning could result in serious injury
or death in the event of a collision.
WARNING: Ensure that the proper Leaveout (specified
area of open space in the pavement) around the posts is
reserved and filled with state/specifying agency approved
backfill material that will not prevent movement, for any
posts installed in rigid pavement such as any thickness of
concrete or asphalt. Failure to follow this warning could
result in serious injury or death in the event of a collision.
INSTALLING THE SYTP™ IN TUBES
Step Actions
1. Install the 3’ 65/8” SYTP(s) ™ (PN-14329) in tubes,as dictated
by the state/specifying agency.
WARNING: Do NOT install SYTP™ at location 1.
Failure to follow this warning could result in serious injury
or death in the event of a collision.
WARNING: Ensure that the proper Leaveout (specified
area of open space in the pavement) around the posts is
reserved and filled with state/specifying agency approved
backfill material that will not prevent movement, for any
posts installed in rigid pavement such as any thickness of
concrete or asphalt. Failure to follow this warning could
result in serious injury or death in the event of a collision.
2. Follow the instructions in the INSTALLING THE STRUT section,
Step 5.
3. Except at Posts 1 and 2, install the SYTP™ in a tube at
locations required for the systems with the four (4) yielding
holes (through the flange) at the top of the tube.
4. From the embankment side of the tube, insert a 5/8” x 91/2” (16
mm x 240 mm) Hex Head Bolt (PN-3497G) through the tube, the
Spacer (PN-4161), and the SYTP™.
5. Place a 5/8” (16 mm) HGR Nut (PN-3340G) on the inserted bolt,
to secure the SYTP™ to the tube.
Note: Do not over tighten the nut and deform the tube, this will
complicate post replacement.
Revised: March 2010

www.highwayguardrail.com 19 Revised: October 5, 2009
INSTALLING THE STRUT
Complete the following steps when installing the strut:
Note: For All strut installations, the installer must provide a shallow
valley/trough for installation of the strut, since a portion of the angle
strut will be below grade.
INSTALLING THE STRUT WITH HBA™ POSTS/SYTP™
Complete the following steps to install the strut with HBA™
posts/SYTP™:
Step Actions
1. Place the Angle Strut (PN-33875G for HBA™, or PN-33795G for
HBA™/SYTP™) on the outside flanges of the HBA™ posts or
the SYTP™ at locations 1 and 2. (Use PN-33875G with the
HBA™ posts or the HBA™ post/SYTP™ in a tube. Use PN-
33795G with the HBA™ post/SYTP™.)
Note: The strut can be placed with one of the legs flat on the
ground or with the leg edge on the ground. The strut may
be installed either on the traffic side or the field side of
the posts.
2. Install a 3/4” (19 mm) diameter x 2 1/2” (63 mm) Hex Head High
Strength Bolt (PN-3717G) in the 13/16” (21 mm) hole of the
HBA™ Post 1 post plates. Place the bolt through the top and
Bottom Post’s post plates and through the strut.
3. Place a 3/4” (19 mm) Washer (PN-3700G) and a 3/4” (19 mm)
Lockwasher under a 3/4” (19 mm) Hex Nut on the end of the bolt
to secure.
4. Tighten the nuts to a snug position. (The designer does not
recommend a torque requirement.)
5. Select Option A, Option B, or Option C below, for installing the
strut on post 2:
Option
A
For HBA™ post at location 2
1. Insert a 3/4” (19 mm) diameter x 3” (75 mm) Hex
Head High Strength Bolt (PN-3718G) through the
strut, two or three ¾” (19 mm) Washers (PN-
3701G), and the 13/16” (21 mm) holes of the
HBA™ post plates of Post 2. (The two or three
washers allow the strut to pass over the 3/8” (10
mm) bolt head.)
2. Place a 3/4” (19 mm) washer and a 3/4” (19 mm)
Lockwasher (PN-4699G) under a 3/4” (19 mm)
Hex Nut (PN-3704G) on the inserted bolt.
3. Tighten the nuts to a snug position. The designer
does not recommend a torque requirement for
the HBA field assembly.
Option
B
For 6’ SYTP™ only at location 2
1. Place a 7/16” (11 mm) Round Washer (PN-4389G)
on the two (2) 7/16” (11 mm) diameter x 11/2” (38
mm) Hex Head High Strength Bolts (PN-4390G).
2. Place the bolts in the two slotted holes of the strut
and the yielding diameter holes of the SYTP™.
3. Place a Lockwasher (PN-4699G) under a 7/16”
Hex Nut (PN-3704G) on the ends of the inserted
bolts.
4. Tighten the nuts to a snug position. (The designer
does not recommend a torque requirement.)
Option
C
For 3’ 65/8” SYTP™ in tube at location 2
1. Place a 3/4” (19 mm) Washer (PN-3701G) on
diameter x 91/2” (240 mm) Hex Head High
Strength Bolt (PN-3718G).
2. From the embankment side, insert the bolt
through the strut, foundation tube, Spacer (PN-
4161), and the SYTP™.
3. Place a washer under a nut on the end of the
inserted bolt.
4. Tighten the nuts to a snug position. (The designer
does not recommend a torque requirement.)
Note: Do not over tighten the bolts and deform the
tubes, this will complicate post replacement.
Revised: March 2010
Table of contents
Other Trinity Control System manuals
Popular Control System manuals by other brands
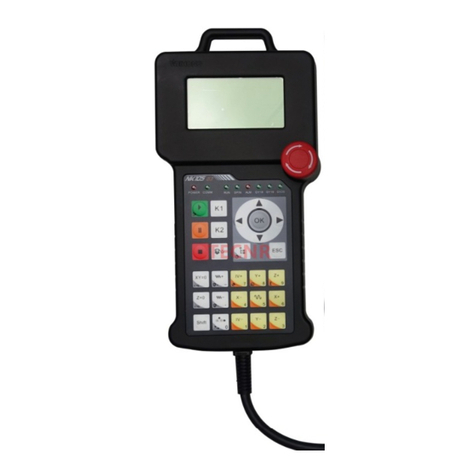
WEIHONG
WEIHONG NK105 Manufacturer's manual
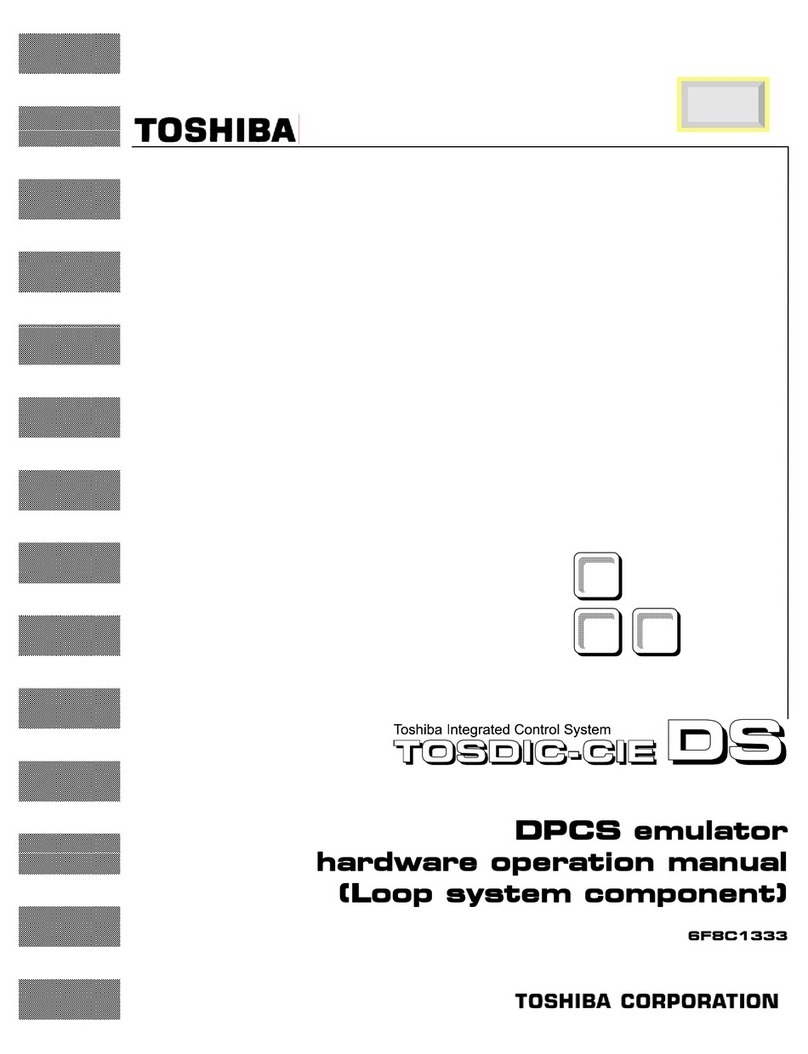
Toshiba
Toshiba TOSDIC-CIE DS Hardware operation manual
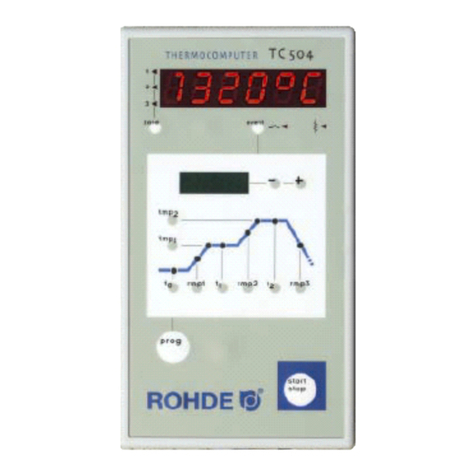
Rohde
Rohde TC 504 instruction manual
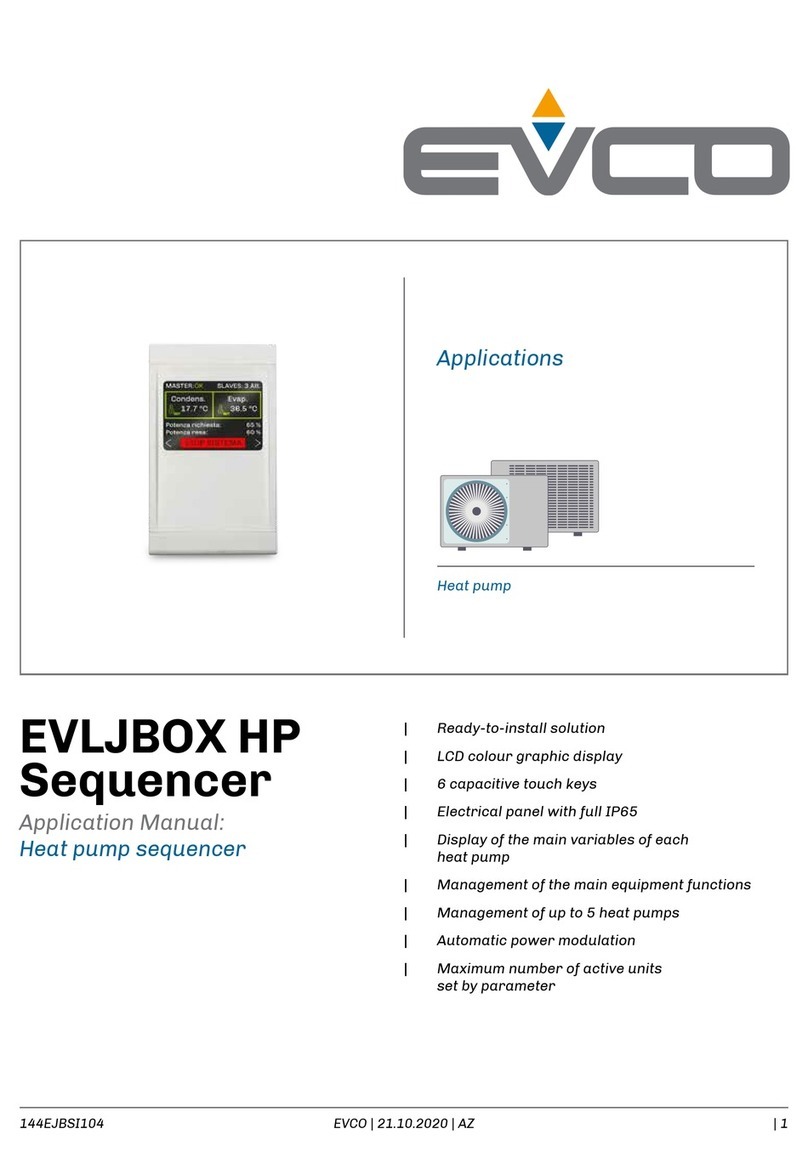
Evco
Evco EVLJBOX HP Sequencer manual

Grunbeck
Grunbeck GENO-CPR-tronic 02 family Operation manual

Intelligent Motion Systems
Intelligent Motion Systems MicroLYNX-4 Quick manual