Tryax TY30-VS User manual

Tryax Limited Jubilee Trade Centre,Jubilee Road,Letchworth Garden City,Herts,SG6 1SP,UK
Phone +44(0) 1462-481295 Fax +44 (0) 1462-685275 www.tryax.com
TRYAX
Vertical Diamond Cut Alloy Wheel Lathe
Operation Manual USA
Model:
TY30-VS

Tryax Limited Jubilee Trade Centre,Jubilee Road,Letchworth Garden City,Herts,SG6 1SP,UK
Phone +44(0) 1462-481295 Fax +44 (0) 1462-685275 www.tryax.com
Table of Contents
1. Safety Notes...........................................................................................................3
1.1 Safety Specification ........................................................................................................3
1.2 General Safety Notes......................................................................................................3
1.3 Notes after Operation Stops ..........................................................................................4
1.4 Notes on Handling Abnormal Status............................................................................4
1.5 Maintenance Safety Notes .............................................................................................4
1.5.1 Routine Maintenance.......................................................................................4
1.6 Noise ................................................................................................................................5
2. Machine Brief Introduction.................................................................................6
2.1 Mechanical Specification...............................................................................................6
Machinery Outline Scheme Diagram.............................................................................
2.3 Assembly Drawing & Machine list ...............................................................................8
2.4 Foundation Plan .............................................................................................................9
2.5 Mechanical Coordinate System ..................................................................................10
2.6 Jaw Chuck size .............................................................................................................10
2.7 Tool Holder Dimension Drawing ................................................................................11
3. Move, Store and Install the Machine................................................................ 11
3.1 Pre-installation Work
3.2 Unload and Moving the Machine ...............................................................................13
3.3 Installation & Levelling
3.3.1 Machine Installation and Leveling...................................................................
3.3.2 Install the Peripherals ...................................................................................16
3.4 Power Requirement .....................................................................................................17
3.5 Compressed Air Source ...............................................................................................18
3.6 Other Objects ...............................................................................................................18
4. Pre-boot Preparation Works .............................................................................19
4.1 Pre-boot Check .............................................................................................................19
4.2 Oil-feed and Oil Types .................................................................................................20
4.2.1 Machine’s Oil-feed Points .............................................................................20
4.2.2 Referenced Machine Oils ..............................................................................20
4.3 Chips Conveyor System...............................................................................................21
5. Machine Maintenance and Tuning ...................................................................22
5.1 Maintenance Period .....................................................................................................22
5.1.1 Maintenance Interpretation..........................................................................22
5.1.2 Machine Regular Maintenance Frequency List..........................................22
5.1.3 Maintenance Check Sheet .............................................................................24
5.2 Soft jaw chuck Mechanism..........................................................................................26
5.3 Forced Auto Lubricator...............................................................................................26
6. Troubleshooting ..................................................................................................29
6.1 Machine Troubleshooting ............................................................................................29
6.2 Quick-Wear Part List ..................................................................................................30
7. Machine Parts List .............................................................................................31

3
1. Safety Notes
1.1 Safety Specification
This machine is equipped with safety devices designed to protect operators from being hurt
or the machine being damaged. Operators should thoroughly read this Manual as well as
undergo the compulsory training programme before operating this Machine.
Ensure there is sufficient space around the Machine to open the electrical-box door for
maintenance/repair and space to allow normal access to and from the machine. Assign
qualified electrical personnel to wire this Machine from the plant power supply.
Do not operate the machine if any safety devices have been damaged or removed.
.
1.2General Safety Notes
1. If you have any safety queries – do not operate the machine.
2. All maintenance and repairs must be undertaken by skilled and trained personnel..
3. Operator should wear appropriate clothing during operation. Do not wear loose fitting
clothing and remove or cover rings and watches.
4. Operators must use approved personal safety equipment.
5. Do not allow other personnel to stand around the machine while it is operating.
6. Ensure the work area around the machine is free from obstruction.
7. When cleaning the machine or removing machined parts do not climb into the
machine.
8. Keep the work area clean and dry.
9. Do not store or keep flammable or hazardous substances near the machine.
10. Do not try to modify this Machine or method of operation.
11. Keep the observation window clean.
12. This Machine is equipped with three-colour alarm light to indicate the alarm status
(red-danger (push the emergency-stop button), amber-warning (abnormal occurs), and
green-normal in operation).
13. Do not attempt to machine oversize work pieces.
14. Do not leave any article or tool within the work chamber.

4
1.3Notes after Machining Operation Stops
1. Before opening the Access Doors, be sure that the chuck has stopped turning.
2. After the dry-cutting process is complete and before removing the workpiece, be sure
to put on safety gloves (to avoid skin-burn).
1.4Notes on Handling Abnormal Status
1. Once an abnormal status occurs, press the emergency stop button immediately.
2. Before accessing Machine’s inner space, be sure that the main power supply is off and
the machine is stationary.
3. If in doubt, press the Emergency Stop Button and seek advice.
1.5Maintenance Safety Notes
1. Before performing maintenance works, shut down main power supply and lock off.
2. Do not leave the machine in an exposed condition and un- attended..
3. After work is completed, do not leave any tool or part in the Machine or on the
operation panel.
4. Clean up the chip tank regularly and wear the correct hand-protection to prevent
allergy or cuts.
5. Keep the observation window clean. If the transparency is blurred, replace it
immediately.
1.5.1 Routine Maintenance
(1) Keep the Machine bed clean.
(2) Tune the indicating gauges (pneumatic and lube oil) to correct positions.
(3) Ensure that lube oil reaches the guide-way.

5
1.6Noise
Per ISO/DIS 230-5 Standard, noise of Machine either at stationary or running status should
be lower than 80 dBA. If over this level, inform us immediately to correct the Machine. The
inspection positions are shown in the figure below.
Measurement standard: according to Machinery Directive 98/38/CE Annex I article 1.7.4(f)
specification.
Spindle speed: 80% of the maximum speed value.
Measuring distance: 1m from the machine housing.
Measurement height: 1.6m from the ground

6
2. Machine Brief Introduction
2.1 Mechanical Specification
Standard accessories:
1. Digitising Probe
2. Diamond Cutter
3. USB & Etherent Ports
4. Halogen Work Light
5. Auto Lube
6. Way Covers
7. Chip Tray
8. Tools & Tool Box
9. Four Way Tool Post
TY30-VS SPECIFICATION
Model
Unit
VTL30
Control
Control System
BECKHOFF
Travel
X-axis Travel
mm(inch)
508(20")
Z-axis Travel
mm(inch)
457(18")
Max.Turning Diameter
mm(inch)
762(30")
Table
Jaw Chuck(Manual)with Soft Jaw
inch
16" - 3
Distance
Distance from Spindle end to Table
mm(inch)
0-457(0~18")
Spindle Nose Taper / Tool
A2-6
Spindle
Spindle Speed
rpm
60~1000
Spindle Type
Belt Drive
Spindle Motor
KW(HP)
7.6(10HP)/4P
2 axes Servo Motors (X/Z)
KW
1.3
Feed
X-axis Rapid Traverse
M/min
10 / Direct
Drive
Z-axis Rapid Traverse
M/min
10 / Direct
Drive
Cutting Feedrate
M/min
10
Min. Input Unit
mm/min
0.001
Installation
Requirements
Weight (about)
t
2

7
2.2 Machinery Outline Scheme Diagram

8
2.3Assembly Drawing & Machine list

9
2.4Foundation Plan

10
2.5Mechanical Coordinate System
Axis-definitions are expressed in below:
X-axis: X-axis is the direction that tool post moves right/left; (+) for right movement and (-)
for left one.
Z-axis: Z-axis is the direction that tool post moves up/down; (+) for up movement and (-)
for down one. tool post

11
2.6Jaw Chuck size
2.7Tool Holder Dimension Drawing

12
3. Move, Store and Install the Machine
3.1 Pre-installation Preparation Works
1. Power source: required power supply specification:
Power
Voltage
Frequency
Phase
Specification
220V
60 HZ
3+Neutral+Earth
2. Pneumatic - air pressure used to clean up spindle, cool down cutting is 5 ~ 7 KG/CM2,
at least 90 NL/min of supply.
3. Oils: feed in required oils before starting this Machine:
Purpose
Product name
Viscosity (40°C)
Capacity
Remark
Lube oil
Guide-way oil
61.2 ~ 74.8
2L
ISO VG68,R-68, K68
4. Precision measuring equipment:
1. 0.02mm/M level meter, at least two pieces.
2. Gauge-carried magnetic seat 1/100, 2/1000mm, one or more set each.
3. One granite right-angle ruler.
5. Space requirement:
To plan for Machine layout space, reserve sufficient space for the
operation/maintenance and access to and from the machine.

13
3.2Unload and Moving the Machine
1. Unload the Machine package: (refer to the pictures below)
The Machine is mounted on a stillage, use forklift to unload the package from
container.
Unload the Machine as shown in the pictures:

14
(2) Removing the machine from the pallet:
a. Remove the 2- covers in front of X axis cover.
Insert a steel bar inside the machine base. (See the figure below)
b. Pass a chain through the 2 openings and loop the chain around the steel bar
from both side of the machine.
c. Then the machine can be lifted.
d. Suitable protection should be used to prevent the chains damaging the paint
Finish of the machine.
.

15
3.3 Installation and Levelling
3.3.1.Machine leveling adjustment
(1) Use the leveler 0.02 mm/m on the center of the chuck,fix the leveler on the X
axis direction and manualy turn the chuck, adjust the level of X axis until the air
bubble in the leveler is centered. Repeat for Z axis.

16
3.3.2 Install the Peripherals
Installing steps of peripherals
No.
Steps
Explanation
1
Compressed air
source
Connect air supply to input point.
2
Filling track
lubricants
Fill lubrication system..
3
Remove the mount
block
Remove the mount blocks in X- & Z-axis; don’t remove the
wooden block that supports the spindle head.
4
Mount and install
the wiring lines
Follow the wire numbers connecting and mounting the
dismantled wires/pipes.
5
Electric control
After checking the electric control lines, connect them.
6
Turn on power to
make test run
a. Certify the correctness of power phases.
b. Certify the correctness of motor turning direction.
c. Check if pipe connectors are connected correctly and
locked tight; mechanism locations are correct
(mechanism should be located at respective location
normally).
d. Lift the tool post head; take out the supporting pads.
7
Certify track
lubrication
Check if the lube system feeds lube oil? Are two lube oils
distributed properly?
8
Clean
Clean the anti-rust oil on jaw chuck & tool post; clean up
dust on Machine and wipe it clean.
9
Commissioning
a. First, manually return Machine’s three axes back to
HOME point manually in slow speed.
b. Return the two axes back to HOME point by 100% fast
speed; certify if the HOME points are same.
c. Check if stroke of each axis follows the set one? If
over-stroke is effective?
d. Follow the attached parameter table to check if
controller’s display meets the parameter table or not?
e. Are the spinning directions and speed of positive/reverse
turns normal?
10
Warm-up run
During running, follow the precision inspection table to
make commissioning run.

17
3.4Power Requirement
.Power and ground
Main power input 3 phase 415V with Neutral and earth
32 Amps per phase
Single Phase Not Required
7. Notes on installing power source and grounding work
(1) Do not co-use power cable with other machines. Provide an independent power
line for this Machine.
(4) Power cable’s external terminals must be protected by a fuse or breaker.
(5) The grounding resistance should be less than 50Ω.
(6) Grounding line color is yellow-green.
Graphic demonstration of machine grounding:
Fig. 1: Single set grounding
Fig. 2: Multi sets grounding
Machine 1
Machine 2
Machine 3
Machine 1
Machine 2
Machine 3

18
3.5Compressed Air Source
1. Use clean air source.
2. Confirm that the air source can provide necessary air flow-rate.
3. Air pressure should exceed 6 kg/cm2.
4. Arrangement of reserved pipelines:
(1) Compressed air must be filtered and be clean and dry (dew point, 6 kgf/cm2,
10°C).
(2) Supply or compressed air must satisfy Machine’s consumption requirement (1-hp
air compressor that supplies 9 0NL/min is approx. enough).
(3) Refer to the drawing below for the input points of compressed air and power
supply.
The compressed air fast-connector size is 9.525 mm (3/8 in.).
.
3.6Other Objects
Clean Utensils Requirement Table
Name
Specification/Quantity
Remark
Kerosene
1L
Used to clean the Machine
Non-volatile cleaning agents
0.5L
Used to clean the Machine
Rag
10 pieces
Used to clean the Machine
Fur brush
1 piece
Used to clean the Machine

19
4. Pre-boot Preparation Works
4.1 Pre-boot Check
In order to ensure the safety of operators and Machine, check the following items before
booting
.
1. Check if oil in the lube oil tank is sufficient?
2. Ensure that space around the Machine and control system is clear.
3. Ensure that every panel and door is closed.
4. Ensure that all control switches are at good condition.
5. Is there anyone in the Machine’s danger area?
6. Does operator wear suitable clothing and correct personal protection equipment
7. Clean up residual water in the air pressure regulators filter.
8.. Check if compressed air, lubrication, hydraulic and cooling system pipelines are
secure.
9. Check and make sure that all safety devices are operating.
14. Certify that toolsand workpiece is secure..

20
4.2Oil-feed and Oil Types
1. The Machine two axis guide-ways and ball screw are under forced-lubrication
operation with auto oil-feeding.
2. Prior to booting, check if lube oil is sufficient.
3. Always use the correct lube oil; incorrect oil will reduce Machine’s lifetime and may
cause malfunction.
4. Lube oil flow-rate is adjusted prior to delivery. Unless the loop is clogged or faulty, do
not adjust it.
4.2.1 Machine’s Oil-feed Points
The following diagram presents the Machine’s oil-feed points. While feeding or replacing
oil, do it at the specified oil-feed points (see the recommended oil list shown in next page).
4.2.2 Referenced Machine Oils
Recommended oil list:
Position
Spot-check/oil-change
cycle
Method
Oil tank
capacity
(Unit: L)
Recommended oil
specification
Oil-feeder
Daily spot-check
When lube-oil-low
alarm appears
Renew it once per
every six months
Feed oil to the upper
limit of oil gauge
2
ISO VG68
MOBIL, DTE 26
SHELL, TELLUS 68
ESSO, TERESSO 68
CASTROL, ALPHASP 68
Table of contents
Popular Lathe manuals by other brands
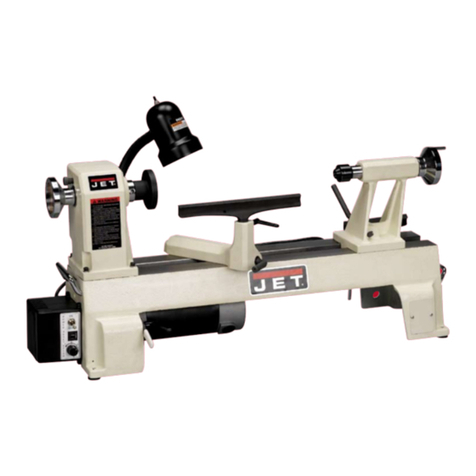
Jet
Jet JWL-1220 brochure
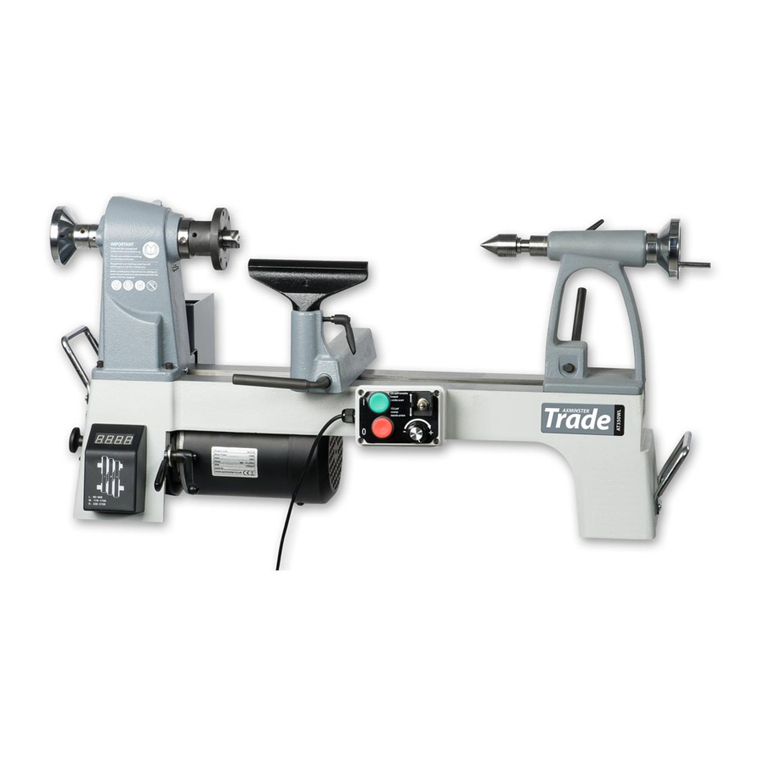
Axminster Trade
Axminster Trade AT350WL Original instructions
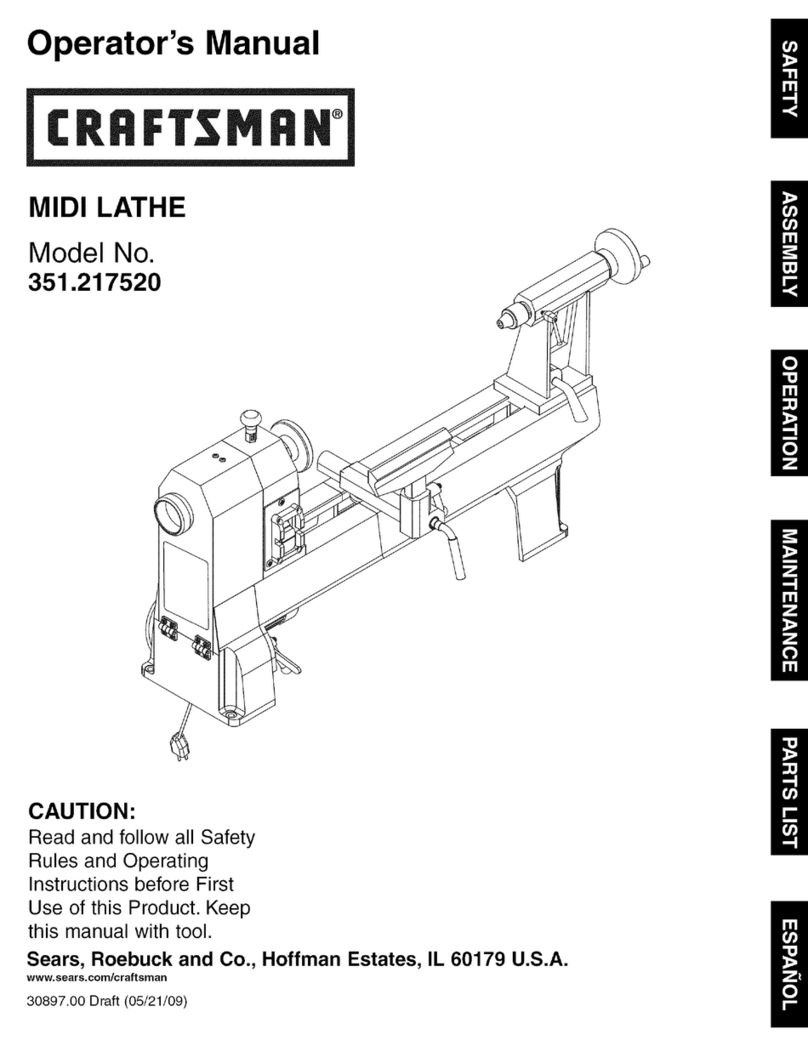
Craftsman
Craftsman 351.217520 Operator's manual
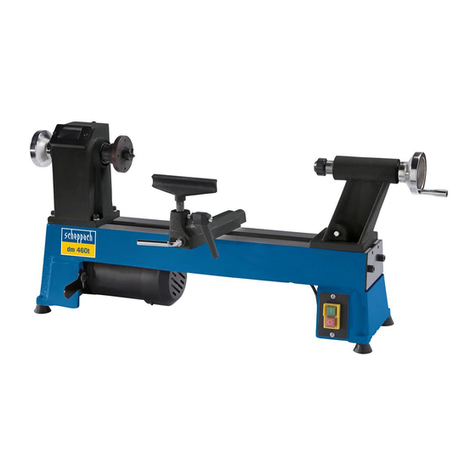
Scheppach
Scheppach DM460T Translation from the original instruction manual
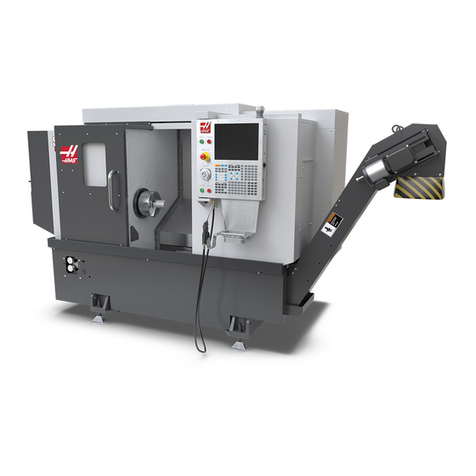
Haas
Haas ST-10/30 troubleshooting guide

HOLZMANN MASCHINEN
HOLZMANN MASCHINEN ED 400FD user manual
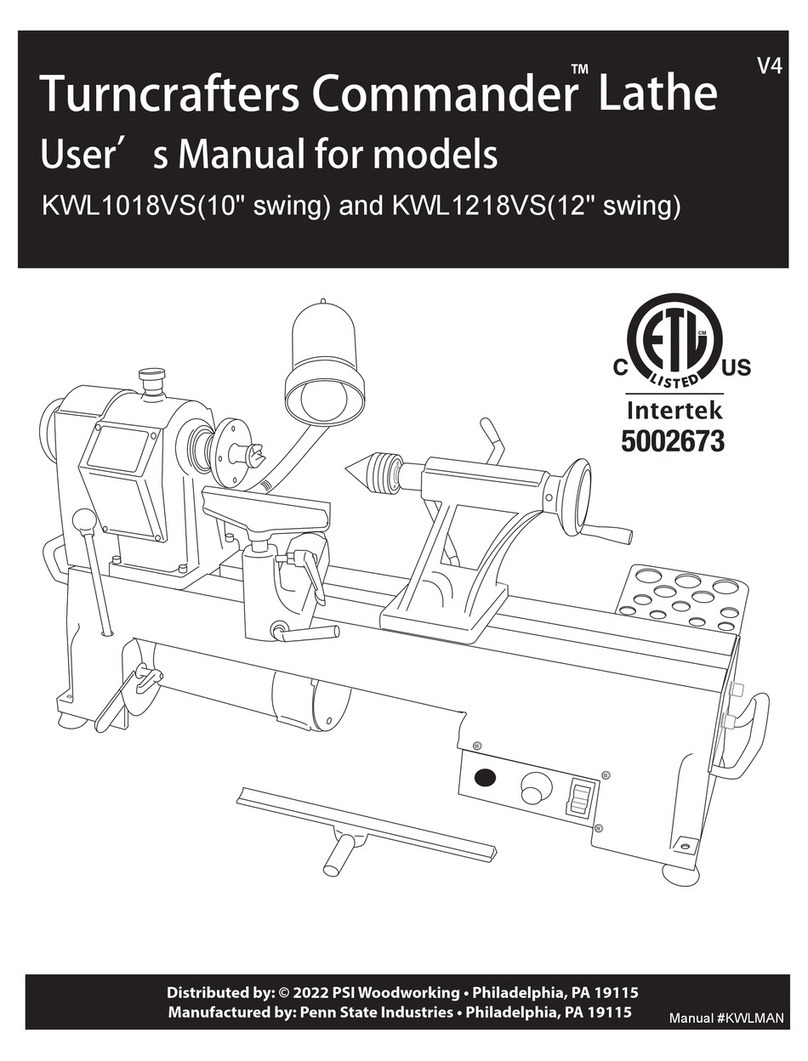
PSI Woodworking
PSI Woodworking Turncrafters Commander KWL1018VS user manual
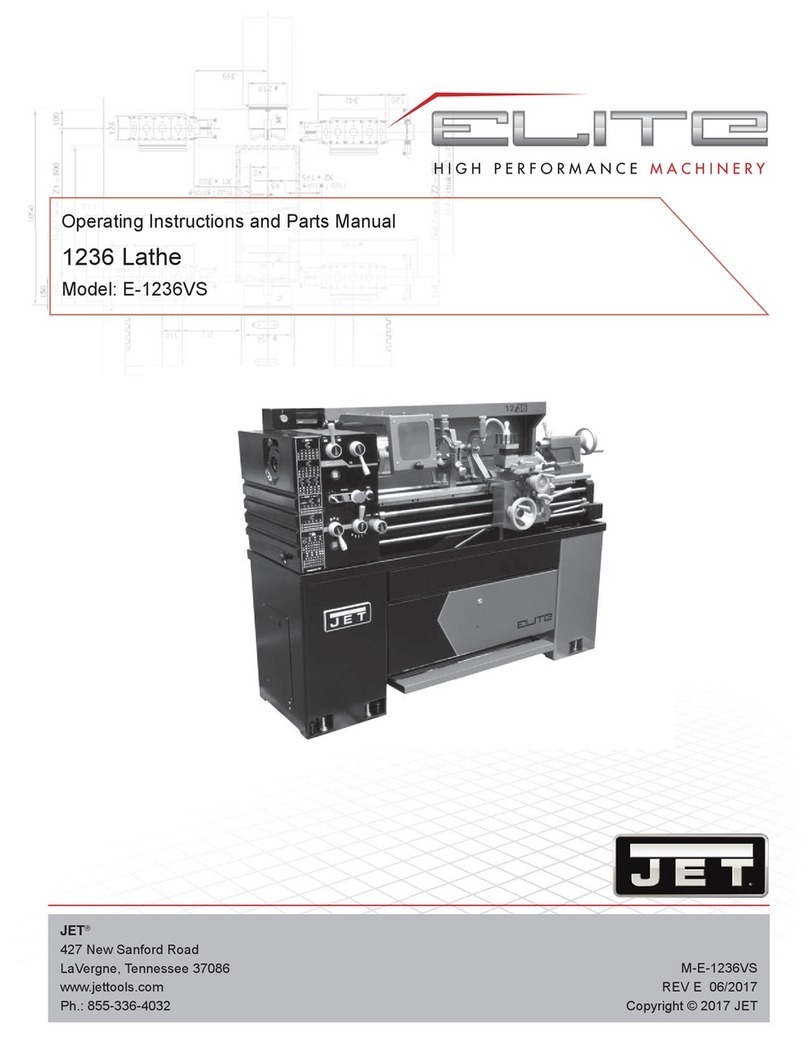
Jet
Jet Elite E-1236VS Operating instructions and parts manual
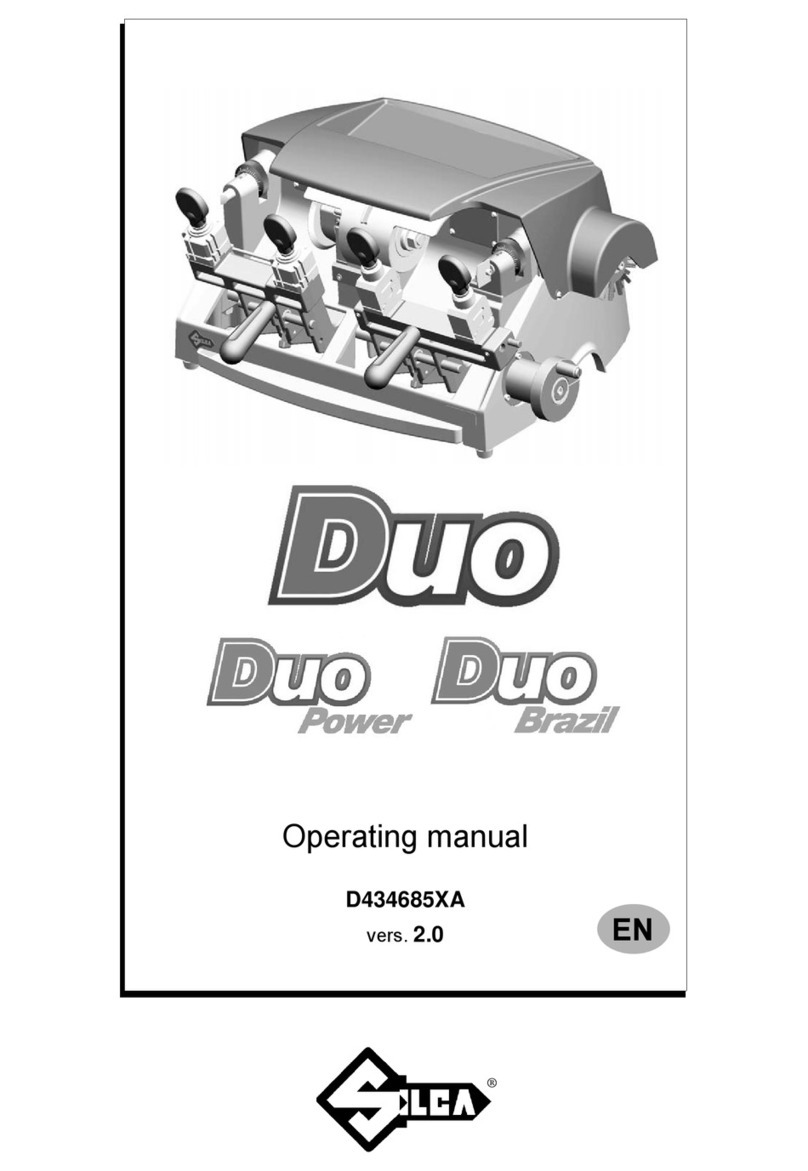
Silca
Silca DUO POWER operating manual
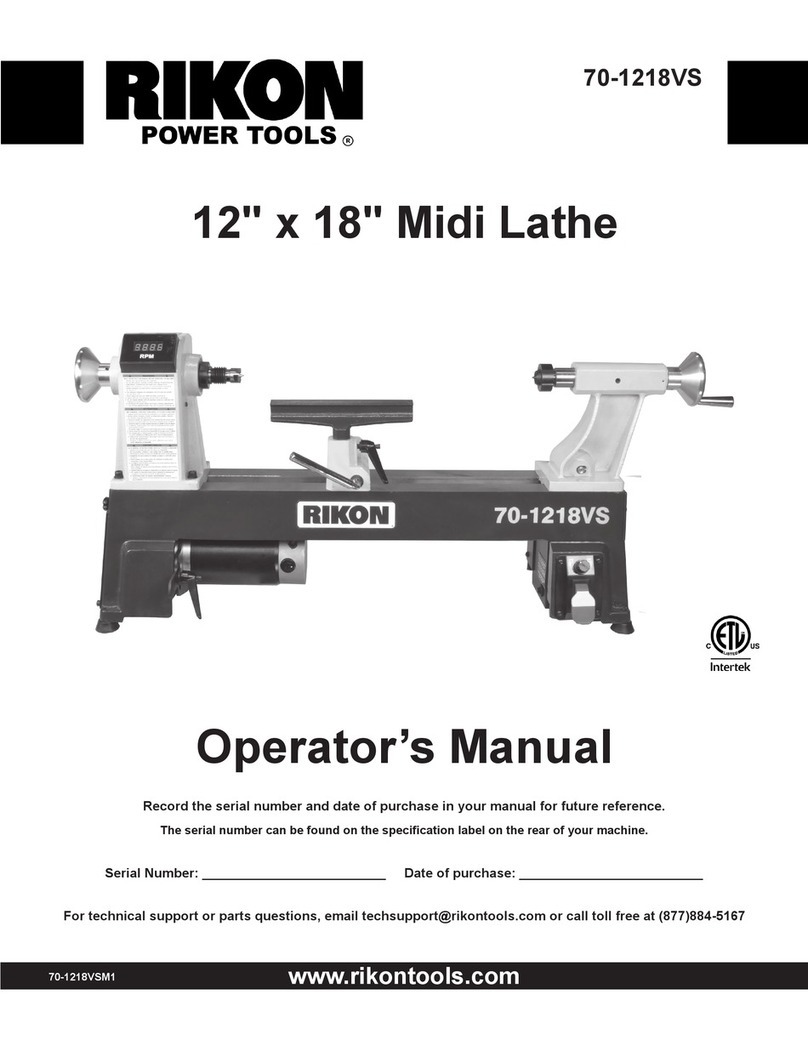
Rikon Power Tools
Rikon Power Tools 70-1218VS Operator's manual
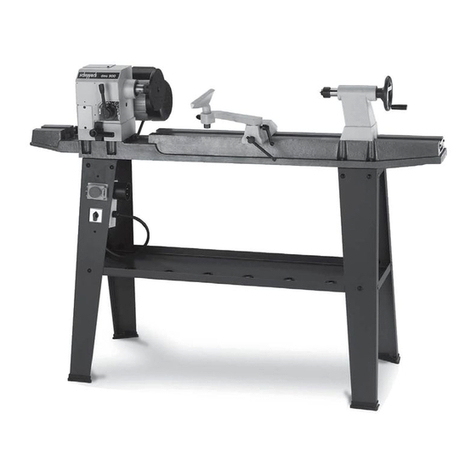
Scheppach
Scheppach dms 900 Translation from the original instruction manual

CHESTER
CHESTER 920 manual