Twinno T6500 User manual

T6500
249 mV
pH / ORP
2020-03-05 12:05:33
4.001pH
twinno
上海淳业仪表科技有限公司
Shanghai Chunye Instrument Technology Co.,Ltd
T6500 On-line pH/ORP Meter
Operating Manual


Perface
Features
Specifications
Installations
Instrument connection
Keypad descriptions
Display description
Menu structure
Calibration
Curve query
1
2
3
4
4
5
6
7
8
10
12
13
20
21
21
22
23
Contents
wall-mounted
MODBUS RTU General Information
pH buffer and temperature values
Daily Maintance
Package set
Warranty
Notes

1
Preface
Thank you for your support. Please read this manual carefully before use.The correct use
will maximize the performance and advantages of the product, and bring you a good
experience.
When receiving the instrument, please open the package carefully, check whether the
instrument and accessories are damaged by transportation and whether the accessories
are complete. If any abnormalities are found, please contact our after-sales service
department or regional customer service center, and keep the package for return
processing.
This instrument is an analytical measurement and control instrument with highly
precision.Only skilled,trained or authorized person should carry out installation, setup and
operation of the instrument.Ensure that the power cable is physically separated from the
power supply when connection or repair.Once the safety problem occurs, make sure that
the power to the instrument is off and disconnected.
For example, it may insecurity when the following situations occur:
1) Apparent damage to the analyzer
2) The analyzer does not work properly or provides specified measurements.
3) The analyzer has been stored for a long time in an environment where the
temperature exceeds 70 °C.

Features
The instrument with different types of pH electrode or ORP electrode is widely used in power plant,
petrochemical industry, metallurgical electronics, mining industry, paper industry
Biological fermentation engineering, medicine, food and beverage, environmental water treatment,
aquaculture, modern agricultural planting and other industries.
In aqueous solution's pH value, ORP value and temperature value were continuously monitored and
controlled.
●Large LCD color LIQUID crystal display
●Intelligent menu operation
●Data recording & Curve display
●Various automatic calibration functions
●Differential signal measurement mode, stable and reliable
●Manual and automatic temperature compensation
●Three sets of relay control switches
●High limit, low limit and hysteresis control
●Various output modes of 4-20mA&RS485
●The same interface displays pH/ORP, temperature, current, etc
●Password protection can be set to prevent non-staff misoperation.
2

Specifications
Measuring range
Measure Unit
Resolution
Basic error
Temperature
Temperature resolution
Temperature basic error
Woring temperature
Temperature compensation
Stability
Current output
Communication output
Other functions
Relay control contacts
Optional power supply
Working environment
Ambient temperature
Relative humidity
Protection level
Instrument Weight
Dimensions
Installation
-2։16.00pH2000։2000mV
pHծmV
0.001pH1mV
±0.01pH±1mV
-10։150.0˫(it is basesd on the electrode)
0.1˫
±0.3˫
0։150˫
Automatic or manual
pH:≤0.01pH/24hORP: ≤1mV/24h
3 Rd 4։20mA,20։4mA,0։20mA
RS485 Modbus RTU
Data record/curve display/data upload
3 Group:5A 250VAC5A 30VDC
85։265VAC,9։36VDCPower:≤3W
There is no strong magnetic interference besides the earth
-10։60˫
No more than 90%
IP65
1.5kg
235×185×120mm
Wall mounted
3

Installations
Installation size
Installation completion drawingFix the fixed piece of the instrument
185 mm
35 mm
235 mm
190 mm
4
120 mm
Instrument shape, wall - mounted fixed piece size
Hole:8*12.5mm

5
Instrument connection
The connection between the instrument and the sensor: the power supply, output signal, relay alarm contact and the
connection between the sensor and the instrument are all inside the instrument, and the wiring is as shown above. The
length of the cable lead fixed by the electrode is usually 5-10 Meters, insert the corresponding label or color wire on the
sensor into the corresponding terminal inside the instrument and tighten it.
RLY1 RLY2 RLY3
G,L,N
V+,V-,RX,TX
V+,V-,A,B
V+,V-,A,B
A1,B1
+,-
3 groups of relay
G-groundwire, L-live, N-neutral
RS232 communication output
Digital input channel 1
Digital input channel 2
RS485 communication output
DC power supply
EC1,EC2,EC3,EC4
T+,T-
INPUT
REF
S+,S-
CE,RE,WE
I1,G,I2
I3,G,I4
Electrical conductivity/resistivity wiring
Temperature connection
pH/ORP/lon measure
pH/ORP/lon reference
Membrane dissolved oxygen, FCL
Constant voltage residual chlorine/
chlorine dioxide/ozone
Output current
Input current
Tips: If the user dials the wire by himself, lengthens the cable or shortens
the cable,
Take care to remove the black conductive skin outside the transparent
wire.
To prevent short circuit from the reference end of the electrode, please
use a multimeter to check
Use the pH dedicated cable connection.
RLY1 RLY2 RLY3
G N L
AC220V
EC1 EC2 EC3 EC4 T+ T- INPUT REF S+ S- WE RE CE I1 G I2 I3 G I4
COND
V+ V- RX TX
RS232
V+ V- A B
SENSOR1
V+ V- A B A1 B1 + -
SENSOR2 485
DC24
pH
DO/FCL
FCL/DOZ
mA1 mA2 mA3 mA4
TEMP

Keypad descriptions
Keypad operation tips:
Short Press: Short Press means to release the key immediately after pressing. ((Default to
short presses if not indicated below)
Long Press: Long Press is to press the button for 3 seconds and then release it.
6
Enter menu setting mode
Return measurements
Two modes switching
Enter standard solution calibration mode
Calibrated: check the calibration status
Re-calibration: press “ENT” again
Return to
previous menu
Confirmation
options
Menu setting mode:
press this key to loop
down the menu options
Menu setting mode:
press this key to
rotate menu options
Press the key in
measurement mode to
display the trend chart
In measurement mode,
press this button to set
parameters for browsing

Display descriptions
All pipe connections and electrical connections should be checked before use.
After the power is switched on, the meter will display as follows.
Setting modeMeasurement mode
Trend Chart DisplayCalibration mode
2019-01-09 12:53:17
235 mV
25.0 °C
pH / ORP
14.51 mA
C1
SP1 SP2 SP3
2019-01-09 12:53:17
pH / ORP
2019-01-09 12:53:17
pH / ORP
7.00
4.01
10.01
-5 mV
170 mV
-5 mV
98 %
Done
Calibrating
Error
offset:
Slope:
7
20
16
12
8
4
050 100 150 200 250 300 350 400
2019-01-09 12:53:17
14.001 25.0 °C
2019-01-09 12:53:17
pH / ORP
25.0 °C
4.001 pH
2019-01-09 12:53:17
pH/ORP
Main Value+ Unit Year/Month/Day
Clean
Instrument type
Time:Minutes:Senconds
Relay 1
[blue is off
and red is on]
Relay 2
[blue is off
and red is on]
Relay 3
[blue is off
and red is on]
Current 1
Current 2
Switch display
Automatic
temp. comp.
Temp. + Unit
Configure
Calibration
Set Points
Output
Data Log
System

Menu structure
The following is the menu structure of this instrument
Type
Unit
Temperature
Temperature Offset
Temperature Input
Temperature Unit
USA: 7.00, 4.01, 10.01
NIST: 6.86, 4.01, 9.18
ORP Standard Calibration
Correction
Field calibration
Offset adjustment
Slope adjustment
Status
High/Low Alarm
Limit Value
Hysteresis
Sensor
Temperature
Standard
Calibration
Field
Calibration
Relay 1
Relay 2
Relay 3
Configure
Calibration
Alarm
PH
ORP
pH
mV
NTC2.252 kΩ
NTC10 kΩ
Pt100
Pt1000
0.0000
Automatic
Manual
°C
°F
Automatic identification of standard
solution, calibration of midpoint first
235mV (Default)
Offset correction 1
Slope correction 1
Offset correction 2
Slope correction 2
On
Off
High Alarm
Low Alarm
Clean
(Continuous opening time)
(The interval between the last opening and closing and the next opening)
8
-under cleaning status
-under cleaning status
Status
High/Low Alarm
Limit Value
Hysteresis
Off
High Alarm
Low Alarm
Clean
(Continuous opening time)
(The interval between the last opening and closing and the next opening)
-under cleaning status
-under cleaning status
Status
High/Low Alarm
Limit Value
Hysteresis
Off
High Alarm
Low Alarm
Clean
(Continuous opening time)
(The interval between the last opening and closing and the next opening)
-under cleaning status
-under cleaning status
On
On

9
Channel
Output Option
Upper Limit
Lower Limit
Channel
Output Option
Upper Limit
Lower Limit
Baud Rate
Parity Check
Stop Bit
Network Node
Interval/point
1h/point
12h/point
24h/point
year/month/day
7.5s
90s
180s
176932point
Chinese
English
Year-Month-Day
Hour-Minute-Second
Display Speed
Backlight
Soft Version
Password Settings
Serial Number
No
Yes
Current 1 4mA
Current 1 20mA
Current 2 4mA
Current 2 20mA
Relay 1
Relay 2
Relay 3
Current 1
Current 2
RS485
Graphic Trend
(trend chart)
Data Query
Interval
Data Output
Memory information
Language
Date/Time
Display
Soft Version
Factory Default
Terminal Current
Tuning
Relay Test
Output
Data Log
System
Main
Temperature
4-20mA
0-20mA
20-4mA
Main
Temperature
4-20mA
0-20mA
20-4mA
4800BPS
9600BPS
19200BPS
None
Odd
Even
1 Bit
2 Bit
001+
Low
Standard
Medium
High
Saving
Bright
19-1.0
0000
(The positive and negative ends of the
ammeter are connected to the current
1 or current 2 output terminals of the
instrument respectively, press 【▼】key
to adjust the current to 4 mA or 20mA
,press【ENT】key to confirm.)
(Select three groups of relays and hear
the sound of two switches, the relay is
normal.)

USA: 7.00, 4.01, 10.01
NIST: 6.86, 4.01, 9.18
ORP Standard Calibration
Field Calibration
Offset Adjustment
Slope Adjustment
Standard
Calibration
Field
Calibration
Calibration Automatic identification of standard
solution, calibration of midpoint first
235mV (Default)
Standard Calibration
Choose the two groupUSA: 7.00, 4.01, 10.01&NIST: 6.86, 4.01, 9.18,
After the selection is completed, press the [MENU] key to return to the measurement screen and press the [CAL] key to enter the
standard liquid calibration mode.
When there is no need to modify the standard liquid group, the standard liquid can be calibrated by pressing the [CAL] key.
If the machine has been calibrated, press [CAL] to view the calibration state, and recalibration is needed. In this state, press
[ENT] again to enter recalibration.
If the monitor prompts you for a calibration security password, press [▼] or to set the calibration security password and then
press [ENT] to confirm the calibration security password.
pH calibration: after entering the calibration mode, the instrument display is as follows.
The picture above,
The instrument automatically identifies the standard solution, calibrates the midpoint (example 7.00pH) first, then calibrates 4.01 pH
or 10.01 pH.
The corresponding mV value will be displayed on the left side of the screen.
After calibration, deviation and slope will be displayed on the right side of the screen.
If you only need two points to calibrate, then press [MENU] to exit.
During the calibration process, when the standard liquid is wrong, the screen will be prompted with Error.
Calibration results: glass electrode slope ≥0.90 is qualified, metallic antimony electrode slope ≥0.80 is qualified.
ORP calibration: press [MENU] to enter the setting mode, select ORP standard liquid calibration, and enter the known value of
standard liquid (default: 235mV).
Press the [MENU] key to return to the measurement screen, and press the [CAL] key to enter the standard liquid calibration mode.
This setting is omitted if the value does not need to be modified.
Press [CAL] to calibrate the standard liquid.
After entering the calibration mode, the instrument will be displayed as the figure above on the right, and the corresponding mV value
will be displayed on the left side of the screen.
After calibration, the slope will be displayed on the right side of the screen.
If the machine has been calibrated, press [CAL]to view the calibration state, and recalibration is needed. In this state, press [ENT]
again to enter recalibration.
The pH of the buffer is measured at 25 °C.
To calibrate the instrument using the automatic identification buffer, you need a standard pH buffer that matches any of these values
Fluid.
Before using automatic calibration, select the correct buffer table (see Buffer Table).
Before the calibration, the electrode can be activated in pH immersion solution to ensure the stability and accuracy of the calibration
and monitoring values.
2019-01-09 12:53:17
pH / ORP
235 98 %Done Slope:
228 mV
2019-01-09 12:53:17
pH / ORP
7.00
4.01
10.01
-5 mV
170 mV
-5 mV
98 %
Done
Calibrating
Error
offset:
Slope:
pH Calibration ORP Calibration
10
Calibration
Press [MENU] to enter the setting mode and select the calibration

pH / ORP
pH: 00.000
mV: -1298.2
Temp: 0.0 °C
2019-01-09 12:53:17
pH / ORP
Field calibration
11
Slope: 1.000
Calibrating
Field calibration
Field Calibration
Select on-site calibration methods:Field calibration, Offset adjustment, linear adjustment.
Field Calibration
When the data from laboratory or portable instrument are input into this item, the instrument will
automatically correct the data.
Use [Ӟ] [Ӝ] key to input concentration data, press [ENT] key to start calibration, Calibrating icon in calibration is
displayed below the value, calibration is completed, after that, the [Done] icon is displayed.
Then press [ESC] to exit.
Offset adjustment
Compare the data of laboratory or portable instrument with the data of instrument measurement, if there
are errors, the error data can be modified by this function.
Linear adjustment
Linear values after "field calibration" are stored in this item, with factory data of 1.00.

12
Press the
[MENU]
button returns to the measurement screen. Press the
[
Ӝ/TREND
]
button in the
measurement mode to view the trend chart of the saved data directly. There are 480 sets of data
record per screen, and the interval time of each record can be selected [7.5s, 90s, 180s],
corresponding to the data displayed in [1h, 12h, 24h] per screen.
In the current mode, press the [ENT
]
key to move the data display line to the left and right (green),
and display the data in left and right circles.Long pressing of the [ENT
]
key can accelerates
displacement. (When the bottom icon is green, [ENT
]
key is displacement direction,press
[Ӝ/TREND]key to switch the direction of displacement )
20
16
12
8
4
050 100 150 200 250 300 350 400
2019-01-09 12:53:17
2019-01-09 12:53:17
14.001 25.0 °C
Fluorescence Dissolved Oxygen
Interval/point
1h/point
12h/point
24h/point
year/month/day
7.5s
90s
180s
Curve
query
(trend chart)
Data Query
Interval
Data Log
Graphic Trend(Trend Chart)
PressսMenuվkey to enter the setting mode,set the recording interval, and the instrument will
400 points per screen,displays the most recent
data trend graph according to interval Settings
400 points per screen, display trend chart of
the last 16 days of data
400 points per screen, display trend chart of
the last 200 days of data
400 points per screen, display trend chart of
the last 400 days of data
Year/month/day time: minute: second value unit
Store data every 7.5 seconds
Store data every 90 seconds
Store data every 180 seconds

13
MODBUS RTU General Information
Overview
The hardware version number of this document is V2.0; the software version number is V5.9 and
above. This document describes the MODBUS RTU interface in details and the target object is a
software programmer.
MODBUS command structure
Data format description in this document;
Binary display, suffix B, for example: 10001B
- decimal display, without any prefix or suffix, for example: 256
Hexadecimal display, prefix 0x, for example: 0x2A
ASCII character or ASCII string display, for example: "YL0114010022"
Command Structure
The MODBUS application protocol defines the Simple Protocol Data Unit (PDU), which is
independent of the underlying communication layer.
Figure 1: MODBUS Protocol Data Unit
MODBUS protocol mapping on a specific bus or network introduces additional fields of protocol
data units. The client that initiates the MODBUS exchange creates the MODBUS PDU, and then
adds the domain to establish the correct communication PDU.
MODBUS PDU
Figure 2: MODBUS architecture for serial communication
On the MODBUS serial line, the address domain contains only the slave instrument address. Tips:
The device address range is 1...247
Set the device address of the slave in the address field of the request frame sent by the host.
When the slave instrument responds, it places its instrument address in the address area of the
response frame so that the master station knows which slave is responding.
Function codes indicate the type of operation performed by the server.
CRC domain is the result of the “ redundancy check” calculation, which is executed according to
the information content.
Function Code Data
Address Domain Function Code Data CRC
MODBUS SERIAL LINE PDU

14
MODBUS RTU Transmission Mode
When the instrument uses RTU (Remote Terminal Unit) mode for MODBUS serial communication, each
8-bit byte of information contains two 4-bit hexadecimal characters. The main advantages of this
mode are greater character density and better data throughput than the ASCII mode with the same
baud rate. Each message must be transmitted as a continuous string.
The format of each byte in RTU mode (11 bits):
Coding system: 8-bit binary
Each 8-bit byte in a message contains two 4-bit hexadecimal characters (0-9, A-F)
Bits in each byte: 1 starting bit
8 data bits, the first minimum valid bits without parity check bits
2 stop bits
Baud rate: 9600 BPS
How characters are transmitted serially:
Each character or byte is sent in this order (from left to right) the least significant bit (LSB)... Maximum
Significant Bit (MSB)
Figure 3: RTU pattern bit sequence
Check Domain Structure: Cyclic Redundancy Check (CRC16)
Structure description:
Figure 4: RTU information structure
The maximum frame size of MODBUS is 256 bytes
MODBUS RTU Information Frame
In RTU mode, message frames are distinguished by idle intervals of at least 3.5 character times, which
are called t3.5 in subsequent sections.
Figure 5: RTU message frame
The entire message frame must be sent in a continuous character stream.
When the pause time interval between two characters exceeds 1.5 characters, the information frame
is considered incomplete and the receiver does not receive the information frame.
MODBUS RTU CRC Check
The RTU mode contains an error-detection domain based on a cyclic redundancy check (CRC)
algorithm that performs on all message contents. The CRC domain checks the contents of the entire
message and performs this check regardless of whether the message has a random parity check. The
CRC domain contains a 16-bit value consisting of two 8-bit bytes. CRC16 check is adopted..Low bytes
precede, high bytes precede.
Start bit 2 3 4 5 6 7 Stop bit1 8 Stop bit
Slave Instrument
Address
Function Code
1 byte
Data
0…252 byte
CRC
2 byte
CRC Low byte CRCHigh byte
Starting
≥3.5 characters
Address
8 bit
Function code
8 bit
Data
Nx8 bit
CRC check
16 bit
End
≥3.5 characters
At least 3.5 characters At least 3.5 characters
Frame 1 Frame 2 Frame 3
4.5 characters
3.5 characters
Frame 1 normal
≤1.5 characters >1.5 characters
Frame 2 failure

15
Implementation of MODBUS RTU in Instrument
According to the official MODBUS definition, the command starts with a 3.5 character interval
triggering command, and the end of the command is also represented by a 3.5 character interval.
The device address and MODBUS function code have 8 bits. The data string contains n*8 bits, and the
data string contains the starting address of the register and the number of read/write registers. CRC
check is 16 bits.
Figure 7: MODBUS definition of data transmission
Instrument MODBUS RTU function code
The instrument only uses two MODBUS function codes:
0x03: Read-and-hold register
0x10: Write multiple registers
MODBUS Function Code 0x03: Read-and-hold Register
This function code is used to read the continuous block content of the holding register of the remote
device. Request the PDU to specify the start register address and the number of registers. Address
registers from zero. Therefore, the addressing register 1-16 is 0-15. The register data in the response
information is packaged in two bytes per register. For each register, the first byte contains high bits and
the second byte contains low bits.
Request
Figure 8: Read-and-hold register request frame
Response
N = Register number
Figure 9: Read-and-hold register response frame
The following illustrates the request frame and response frame with the read and hold register 108-110
as an example. (The contents of register 108 are read-only, with two byte values of 0X022B, and the
contents of register 109-110 are 0X0000 and 0X0064)
Value
Byte
Start
No signal bytes
during 3.5
characters
3.5
Device address
1-247
1
Function
Function codes
conforming to
MODBUS
specification
1
Data
Data conforming
to MODBUS
specification
n
Summary Check
CRCL
1
End
No signal
bytes during
3.5 characters
3.5
CRCL
1
Function code
Start Address
Read register number
1 byte
2 byte
2 byte
0x03
0x0000….0xfffff
1…125
Function code
number of bytes
Register values
1 byte
1 byte
N×2 byte
0x03
N×2
Request Frame
Number Systems
Function code
Start address (high byte)
Start address (low byte)
Number of Read Registers (High Bytes)
Number of Read Registers (Low Bytes)
(Hexadecimal)
0x03
0x06
0x02
0x2B
0x00
0x00
0x00
0x64
(Hexadecimal)
0x03
0x00
0x6B
0x00
0x03
Response Frame
Number Systems
Function code
Byte count
Register Value (High Bytes) (108)
Register Value (Low Bytes)(108)
Register Value (High Bytes) (109)
Register Value (Low Bytes) (109)
Register Value (High Bytes)(110)
Register Value (Low Bytes) (110)
Figure 10: Examples of read and hold register request and response frames

16
MODBUS function code 0x10: write multiple registers
This function code is used to write continuous registers to remote devices (1... 123 registers) block
that specifies the value of the registers written in the request data frame. Data is packaged in two
bytes per register. Response frame return function code, start address and number of registers
written.
Request
N = Register number
Figure11:Write multiple register request frames
Response
N = Register number
Figure 12: write multiple register response frames
The request frame and response frame are illustrated below in two registers that write the values
0x000A and 0x0102 to the start address of 2.
Function code
Start Address
Number of input registers
number of bytes
Register values
1 byte
2 byte
2 byte
1 byte
N×2 byte
0x10
2 byte
2 byte
1 byte
N×2 byte
Request Frame
Number Systems
Function code
Start address (high byte)
Start address (low byte)
Input register number (high bytes)
Input register number (low bytes)
number of bytes
Register value (high byte)
Register value (low byte)
Register value (high byte)
Register value (low byte)
(Hexadecimal)
0x10
0x00
0x01
0x00
0x02
0x04
0x00
0x0A
0x01
0x02
Response Frame
Number Systems
Function code
Start address (high byte)
Start address (low byte)
Input register number (high bytes)
Input register number (low bytes)
(Hexadecimal)
0x10
0x00
0x01
0x00
0x02
Function code
Start Address
Register number
1 byte
2 byte
2 byte
0x10
0x0000….0xffff
1…123(0x7B)
Figure 13: Examples of writing multiple register request and response frames

17
Data format in instrument
Overview
Floating Point
Definition: Floating point, conforming to IEEE 754 (single precision)
Figure 14: floating point single-precision definition (4 bytes, 2 MODBUS registers)
Example: Compile decimal 17.625 to binary
Step 1: Converting 17.625 in decimal form to a floating-point number in binary form, first finding the
binary representation of the integer part
17decimal= 16 + 1 = 1×24+ 0×23+ 0×22+ 0×21+ 1×20
The binary representation of integer part 17 is 10001B
then the binary representation of decimal part is obtained
0.625= 0.5 + 0.125 = 1×2−1+ 0×2−2+ 1×2−3
The binary representation of decimal part 0.625 is 0.101B.
So the binary floating point number of 17.625 in decimal form is 10001.101B
Step 2: Shift to find the exponent.
Move 10001.101B to the left until there is only one decimal point, resulting in 1.0001101B, and
10001.101B = 1.0001101 B× 24 . So the exponential part is 4, plus 127, it becomes 131, and its binary
representation is 10000011B.
Step 3: Calculate the tail number
After removing 1 before the decimal point of 1.0001101B, the final number is 0001101B (because
before the decimal point must be 1, so IEEE stipulates that only the decimal point behind can be
recorded). For the important explanation of 23-bit mantissa, the first (i.e. hidden bit) is not compiled.
Hidden bits are bits on the left side of the separator, which are usually set to 1 and suppressed.
Step 4: Symbol bit definition
The sign bit of positive number is 0, and the sign bit of negative number is 1, so the sign bit of 17.625 is 0.
Step 5: Convert to floating point number
1 bit symbol + 8 bit index + 23-bit mantissa
0 10000011 00011010000000000000000B (the hexadecimal system is shown as
0 x418d0000 )
Reference code:
1. If the compiler used by the user has a library function that implements this function, the library
function can be called directly, for example, using
C language, then you can directly call the C library function memcpy to obtain an integer
representation of the floating-point storage format in memory.
For example: float floatdata; // converted floating point number
void* outdata; memcpy(outdata,&floatdata,4);
Suppose floatdata = 17.625
If it is a small-end storage mode, after executing the above statement,
the data stored in the address unit outdata is 0x00.
Outdata + 1 stores data as 0x00
address unit (outdata + 2) stores data as 0x8D
address unit (outdata + 3) stores data as 0x41
Description
Bit
Index Deviation
Symbol
3
Index
30…23
Mantissa
22…0
SUM
22…0
127
Table of contents
Other Twinno Measuring Instrument manuals

Twinno
Twinno T4046 User manual
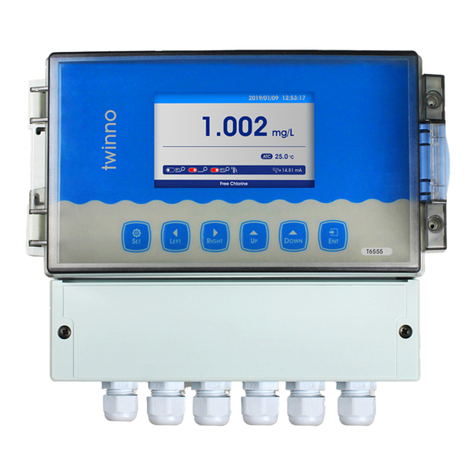
Twinno
Twinno T6555 User manual
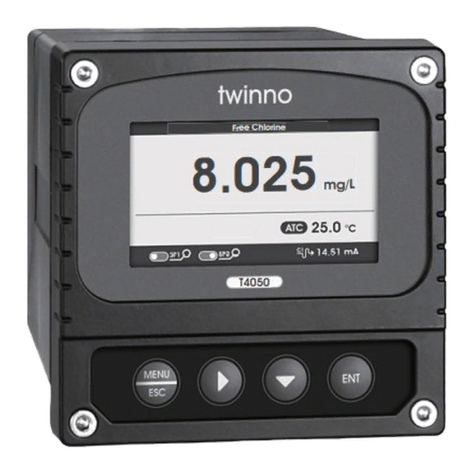
Twinno
Twinno T4050 User manual
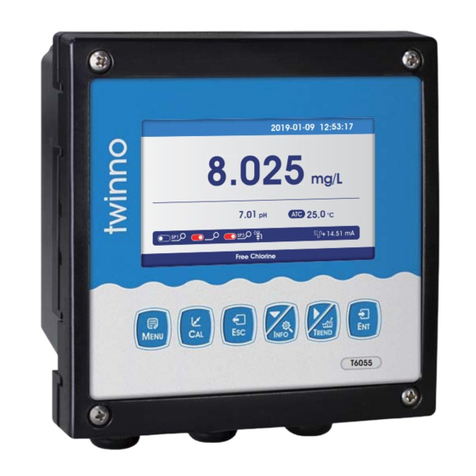
Twinno
Twinno T6055 User manual
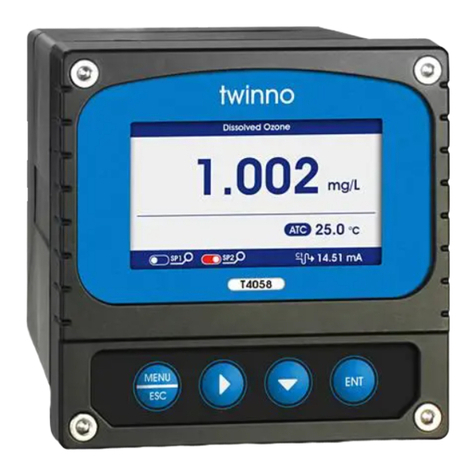
Twinno
Twinno T4058 User manual

Twinno
Twinno T6075 User manual

Twinno
Twinno RM785 User manual
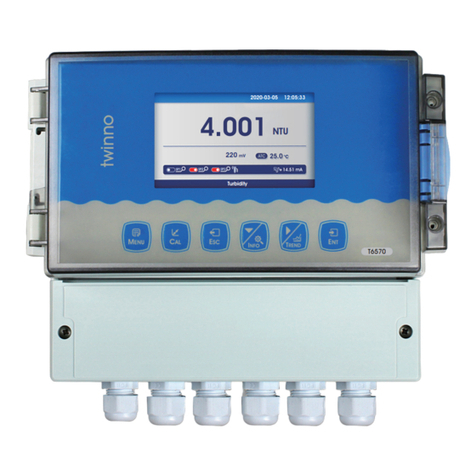
Twinno
Twinno T6570 User manual

Twinno
Twinno T4055 User manual
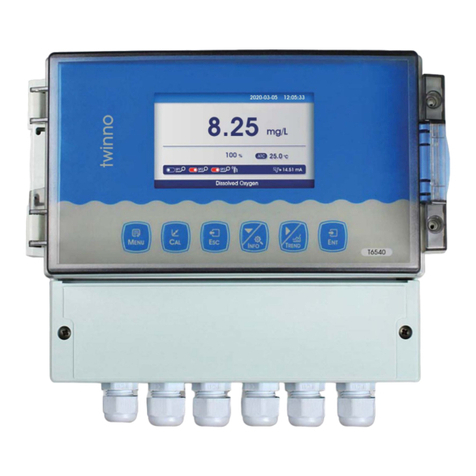
Twinno
Twinno 16540 User manual
Popular Measuring Instrument manuals by other brands
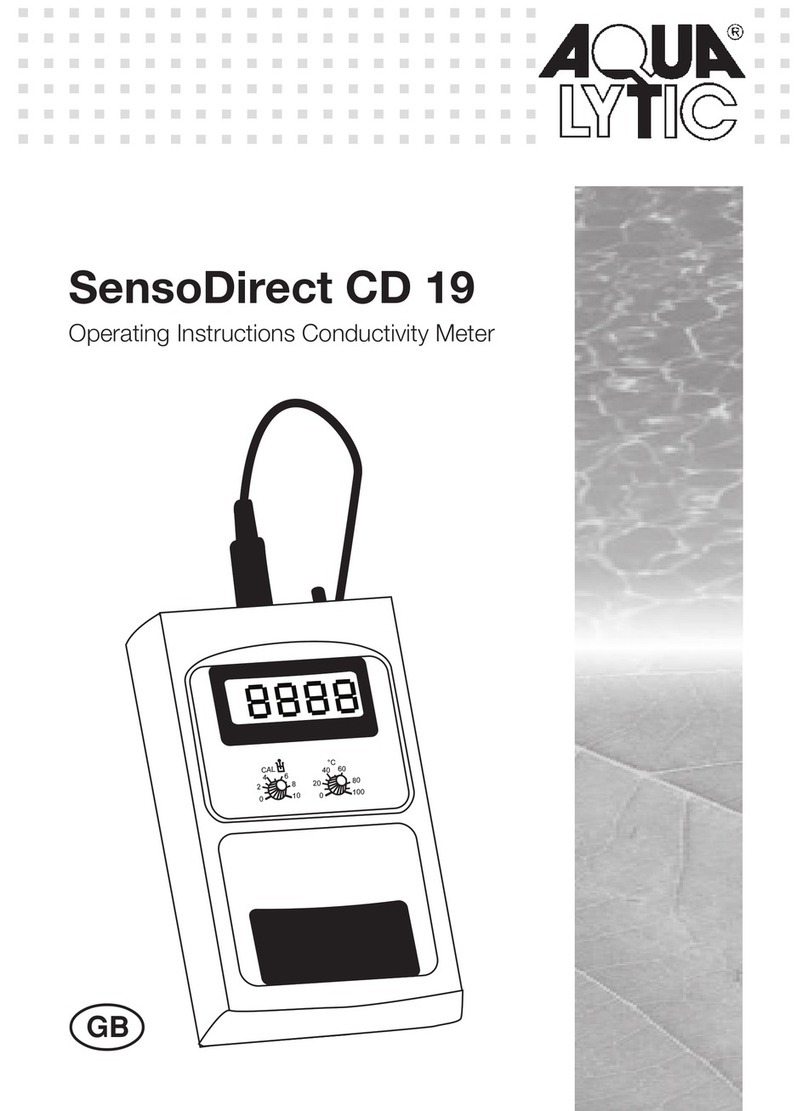
Aqualytic
Aqualytic SensoDirect CD 19 operating instructions
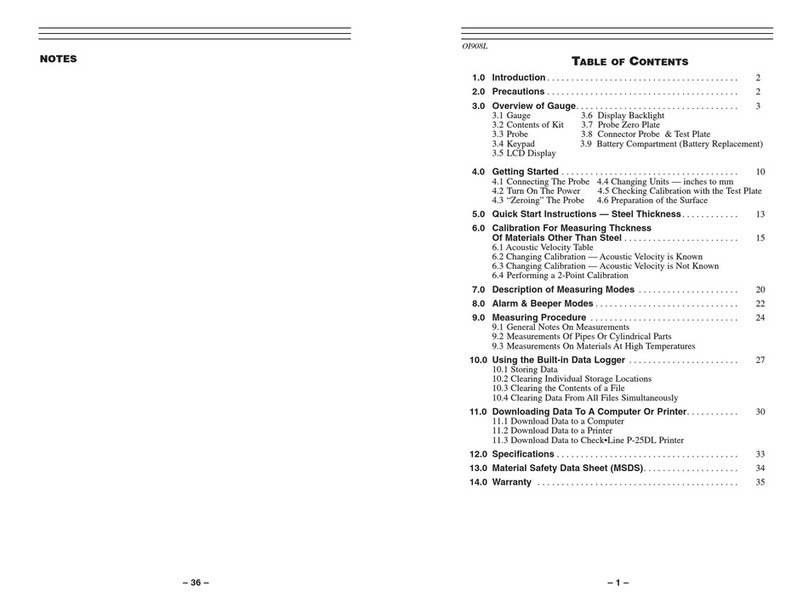
Check-line
Check-line TI-25DL user manual
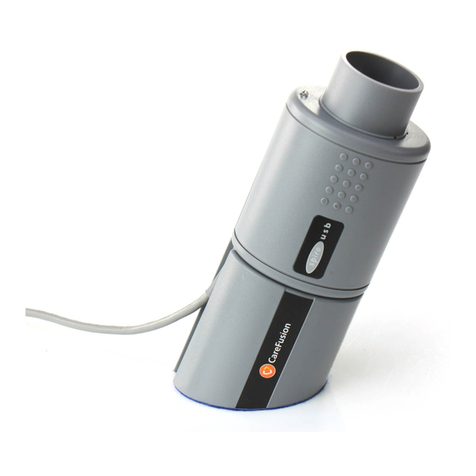
Micro Direct
Micro Direct SpiroUSB operating manual
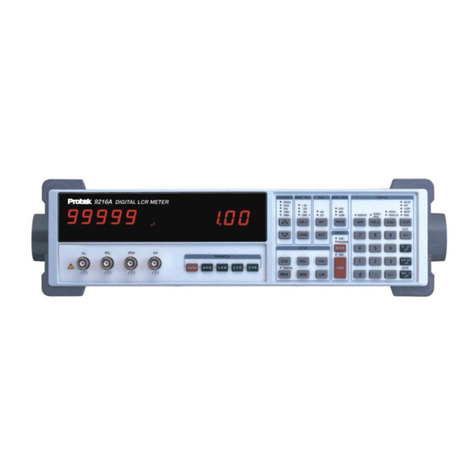
PRO-TEK
PRO-TEK 9216A user manual
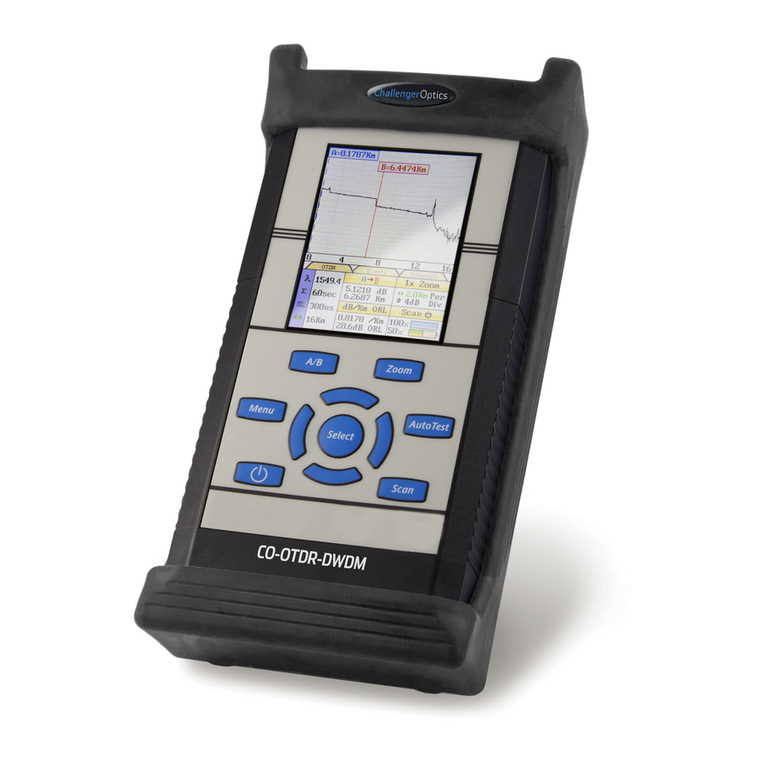
Challenger Optics
Challenger Optics CO-OTDR-DWDM operating manual
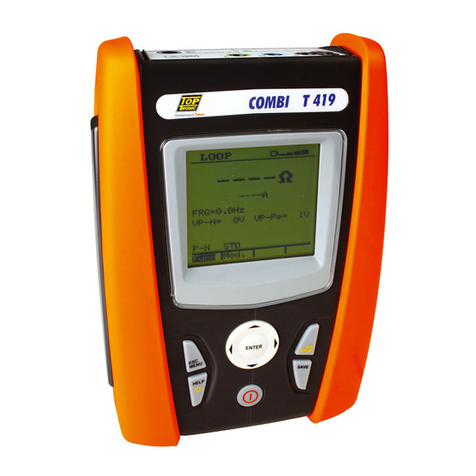
Hellermann Tyton
Hellermann Tyton ACADEMY TCTRP Questions and answers