Tyco Xtralis VESDA VLC-800MX User guide

© 2008 Tyco Safety Products PAGE 1 of 18
VLC-800MX
17A-03-VLC
4 12/08
Registered Company: Thorn Security Ltd. Registered Office: Dunhams Lane Letchworth Garden City Hertfordshire SG6 1BE
EQUIPMENT:
PUBLICATION:
ISSUE No. & DATE:
Xtralis VESDA VLC-800MX
INSTALLATION, COMMISSIONING AND SERVICING INSTRUCTIONS
LIST OF CONTENTS
1 TECHNICAL SPECIFICATION 2
2 INTRODUCTION 3
2.1 SCOPE OF THIS DOCUMENT 4
3 OPERATION 4
3.1 LED OPERATION 4
4 SAMPLING PIPEWORK 5
4.1 PRIMARY SAMPLING (OF AIR
HANDLING UNIT RETURN GRILLES): 5
4.2 SECONDARY SAMPLING
(ROOM OR VOID PROTECTION) 5
4.3 PRE-ENGINEERED SOLUTIONS
FOR SECONDARY SAMPLING 5
4.4 CAPILLARY SAMPLING 7
4.5 PIPEWORK INSTALLATION 7
5 MOUNTING THE DETECTOR BRACKET 8
6 EXTERNAL POWER SUPPLY 9
7 REMOTE LED AND RELAY OPTIONS 9
8 WIRING NOTES (FIG. 10 REFERS) 9
9 COMMISSIONING 10
9.1 OVERVIEW 10
9.2 PRECAUTIONS PRIOR TO POWER-UP 10
9.3 SETTING THE MX ADDRESS 10
9.4 CONFIGURING THE MX PANEL
USING MX CONSYS 10
9.5 POWER-UP SEQUENCE 10
9.6 TESTING COMMUNICATION 11
9.7 CONNECTING A PC RUNNING
VConfig PRO 11
9.8 NORMALISING THE FLOW 11
9.9 SELECTING SMOKE THRESHOLDS 11
9.10 PRE-ALRM AND ALARM DELAYS 12
9.11 USING AUTOLEARN 12
9.12 SETTING FLOW THRESHOLDS 13
9.13 COMMISSIONING TESTS 13
10 MAINTENANCE 14
10.1 OVERVIEW 14
10.2 SCHEDULE 14
10.3 CHANGING THE AIR FILTER
CARTRIDGE 14
10.4 REPLACING THE ASPIRATOR 15
10.4.1 REMOVING THE ASPIRATOR 15
10.4.2 ASSEMBLY 15
11 TROUBLE SHOOTING 16
11.1 INTERROGATING FAULT CONDITIONS 16
12 ORDERING INFORMATION 17
13 APPROVALS 17

VLC-800MX
17A-03-VLC
4 12/08
PAG E 2 of 18
Fig. 1 Xtralis Vesda VLC-800MX
WARNING:
The Xtralis VESDA VLC incorporates a
Laser device and is classified as a Class 1
Laser product which complies with FDA
Regulations 21 CFR 1040.10 and 1040.11.
The laser is housed in a sealed Detector
chamber and contains no serviceable
parts. This laser emits invisible light and
can be hazardous if viewed with the naked
eye. Under no circumstances should this
chamber be opened. There is a safety label
on the chamber as shown in Fig. 2.
Fig. 2 Laser Warning Label
1. TECHNICAL SPECIFICATION
Type Identification Value: 179
System Compatibility: Use only with MX Fire
Alarm Controllers
Environment: Indoor Application only
IP Rating: IP30
Operating Temperature:
Detector Ambient: -10°C to +39°C
Sampled Air: -20°C to +60°C
Relative Humidity: 10-95% non-condensing
Dimensions:
Height: 225mm
Width: 225mm
Depth: 85mm
Weight:1.9kg
Sampling Network:
Maximum Area Coverage: 800m2
Maximum Pipe length: 80m with up to 15* holes,
or 2 x 50m with up to 9*
holes per pipe
Pipe Size: ID15 - 21mm
OD 25mm
‘*’ more holes may be used on networks designed using the
VESDA ASPIRE II pipe modelling software.

VLC-800MX
17A-03-VLC
412/08
© 2008 Tyco Safety Products PAGE 3 of 18
Registered Company: Thorn Security Ltd. Registered Office: Dunhams Lane Letchworth Garden City Hertfordshire SG6 1BE
EQUIPMENT:
PUBLICATION:
ISSUE No. & DATE:
Electrical Characteristics:
External 24V dc:
Supply Voltage: 18 to 30V dc
Current Consumption:
Standby: 225mA
Alarm: 245mA
Battery Requirements Addressable Loop:
Standby: 300μA
Non operational (VLC off): 300μA
Alarm: 300μA
Alarm with external relay: dependant on the relay
Alarm with external LED: 3.3mA
Fire relay: rated 2A @ 30V dc
Electromagnetic Compatibility:
The VLC-800MX complies with the following:
Product standard EN 54-20:2006, Fire detection and fire
alarm systems Part 20: Aspirating Smoke Detectors.
Product family standard EN50130-4/A1/A2:2003 in
respect of EMC immunity
Generic standard EN 61000-6-3:2007 in respect of EMC
emissions
2. INTRODUCTION
The VLC-800MX is a derivative of the standard Xtralis
VESDA product family, with the primary difference being
that it communicates directly on the MX loop.
VESDA VLC detectors provide Very Early Warning of
potential fire conditions by drawing air samples through
25mm pipe up to 80m long. Smoke is sampled through
holes in the pipe and transported to the detector by an
integrated aspirator or fan. Holes are positioned according
to the application and often follow the spacing of standard
conventional point detectors. Where necessary, sampling
points can be constructed using capillary extensions. See
Section 4, Sampling Pipework for more information.
The MX version of the VESDA VLC acts as a smoke sensor
on the Tyco MX loop and reports directly to the MX
controller.
PC PROGRAMMING
SOCKET
TERMINATION
CARD
LCD CARD
CONNECTOR
ASPIRATOR
CONNECTOR
AIR FILTER
CARTRIDGE
FILTER RELEASE SCREW AIR EXHAUST PORT
ASPIRATOR
FUSE 1.6A
ANTI TAMPER
SCREW
CABLE ENTRY PORTS
AIR INLET PORT
CABLE TERMINAL
STRIP
VLC -800
PROGRAMMING
PORT
Fig. 3 VLC-800MX Component Location

VLC-800MX
17A-03-VLC
4 12/08
PAG E 4 of 18
2.1 SCOPE OF THIS DOCUMENT
This manual provides instructions on how to install,
commission and operate the VESDA VLC-800MX. It outlines
the standard pipe configurations permissible, power supply
requirements, and some installation tips. It does not provide
information on how to design and verify customised pipe work
configurations using the VESDA ASPIRE II pipe modelling
software and does not include detailed step-by-step installation
instructions.
This document provides brief details on how VSC (VESDA
System Configurator) is used to configure the detector. It does
not describe how to use VESDA VSC PC based software to
configure custom alarm thresholds, interrogate event logs and
smoke trends stored in the detector, set the internal clock and
generally access the extensive features of the LaserCOMPACT
detector.
This document is intended for proficient installation engineers
who are familiar with the commissioning of an MX Fire
Detection System but have limited experience with the
installation of VESDA Aspirating Smoke Detectors.
3. OPERATION
In normal operation, the VLC-800MX is polled every 5
seconds for the current smoke reading. This is scaled such that
a zero reading is reported as 12 and a measurement equating
the Fire threshold configured in the VLC is reported as 112. If
the value exceeds 112 for three consecutive polls, the MX
panel reports the condition as an alarm and commands the Fire
LED on the VLC to illuminate. A value exceeding 82 may be
reported as a Pre-alarm condition by the MX panel. In addition
to the poll every 5 seconds, the MX panel also polls the VLC
for its fault status every 20 seconds.
3.1 LED OPERATION
Fig. 4 refers.
LaserCOMPACT
VLC-800 MX
tyco
FILTER
OK
FAULT
SERVICE
FIRE
MX TECHNOLOGY
Fig. 4
Red FIRE LED: Indicates that a fire condition
has been detected. Also, when
configured to flash-when-polled1,
it will normally flash once
every 5 seconds with a double
flash every 20 seconds
reflecting the polling
for smoke and fault.
Yel low SERVICE LED:Indicates that all the fault
conditions present are
likely to be resolved by a
technician with the aid of
VSC. If this LED is not
illuminated when the Fault
LED is, then it is likely that the
fault present will require a
change of component and it is
therefore recommended that the
Technician responding to the
call carries a spare detector with
him. The intention of this LED
is to eliminate the need for a
double service visit.
Yel low FAULT LED: Indicates that there is a fault
condition present which may
impair the detector’s ability to
detect smoke. Urgent attention
is required.
Note: Note that if the Service LED is also illuminated
then all the faults present are likely to be resolved
by a technician with the aid of VSC.
Green OK LED: Indicates that the operation is
normal. However, when the unit
is normalizing airflow this LED
flashes twice and when running
Autolearn this LED flashes
three times.
Yel low FILTER LED: Indicates that there is a problem
with the filter. It is
recommended that technicians
responding to such a fault carry
a spare filter cartridge.
1Some approvals bodies - notably VdS and SSL do not allow
the flash-when-polled option

VLC-800MX
17A-03-VLC
412/08
© 2008 Tyco Safety Products PAGE 5 of 18
Registered Company: Thorn Security Ltd. Registered Office: Dunhams Lane Letchworth Garden City Hertfordshire SG6 1BE
EQUIPMENT:
PUBLICATION:
ISSUE No. & DATE:
Fig. 5 Sampling an AHU
4. SAMPLING PIPEWORK
This document does not cover the design and installation of
Aspirating pipework in detail. For complex or customised
designs please contact a VESDA approved agent who can
use the ASPIRE II pipework modelling programme to
verify non-standard designs.
Note:
1) The following standard designs are provided
for ease of installation in the majority of
applications. The limitations specified are
conservative and the VLC is fully capable of
being successfully applied beyond the limits
stated when the design and installation of the
pipework is directed by a VESDA approved
agent.
2) The following standard designs are Class B
under EN 54-20 when used with the default
alarm threshold of 0.2% obscuration/m.
4.1 PRIMARY SAMPLING (OF AIR
HANDLING UNIT RETURN GRILLES)
VESDA VLC detectors are ideally suited to protecting large
areas (up to 500m2) with high airflows by arranging
sampling pipe across the return grille of Air Handling Units.
Up to 2 identical Air Handling Units may be covered as long
as they are not independently controlled or unusually large
(eg, > 30kW or >10,000m3/hr).
Pipework across the grille should be arranged to ensure that
the flow into the grille is adequately sampled. Generally
Xtralis suggests a maximum coverage of 0.2m2per
sampling hole. For example, a grille measuring 1.5m x
0.8m would need 6 sampling holes (see Fig. 5). When
sampling across a grille the sampling holes should generally
face into the flow, as such slight rotations of the pipe during
commissioning may improve performance. Consideration
should be given to any maintenance requirements for the Air
Handling Unit. For example, it may be necessary to allow
for convenient removal of the VESDA pipework to allow
easy access to filters in the AHU.
4.2 SECONDARY SAMPLING (ROOM OR
VOID PROTECTION)
VESDA VLC detectors may be used to protect open areas
up to 800m2. This is generally achieved by positioning
sampling holes according to the standards relating to
conventional point detectors.
The following pre-engineered pipework solutions may be
used without verifying their performance using the ASPIRE
II pipe modelling software. These pre-engineered solutions
are compliant with the European standard EN54-20 and
achieve a transport time of less than 90 seconds. Each
sampling hole has an individual sensitivity of better than
4.5% obscuration/m and so the systems are Class B systems
under VESDA approvals to EN 54-20. and sensitivity
performance is significantly better than the requirements of
EN54-7 (or EN54-20:Class C) where the sensitivity of
individual sampling points must be better than 10%
obscuration/m. However, where specific performance
requirements are specified (eg, a Class A system or
transport times of <60 seconds) or where practical
considerations fall outside the following pre-engineered
designs, the performance of the sampling system shall be
modelled on the ASPIRE II software by personnel with
suitable training.

VLC-800MX
17A-03-VLC
4 12/08
PAG E 6 of 18
MAXIMUM PIPE LENGTH 80m
4mm END HOLE
3-15 OFF 2.5mm SAMPLING HOLES
2 OFF 4MM END HOLES
MAXIMUM PIPE LENGTH 50m
2-9 OFF 3mm SAMPLING HOLES (PER PIPE)
Fig. 6 Pre-engineered Pipework Configurations
4.3 PRE-ENGINEERED SOLUTIONS FOR
SECONDARY SAMPLING
In single pipe system, pipe lengths of up to 80m may be
used, between 3 and 15 sampling holes may be used; each
having a diameter of 2.5mm with an end cap drilled with a
4mm hole:
In branched pipe systems with two branches (ie, 2 x 50m)
within 4m of the detector, each branch is capable of having
between 2 - 9 sampling holes of 3mm diameter plus an end
cap of 4mm.
Sampling holes should be evenly spaced (within ±20%) but
may be bunched towards the end cap end if required. Equal
numbers of sampling holes should be used on each pipe
unless supported by an ASPIRE II model.
Sharp elbows in the pipe should be avoided - use “slow
bends”.
The drilled openings should be de-burred but NOT
chamfered for proper functioning of the system.
These systems are EN 54-20 Class B systems when using
the default Fire alarm threshold of 0.2%obscuration/m
Using ASPIRE II (V 2.01.00 or later) it is possible to
determine the Class of many different configurations of
holes and pipework. It is also possible to estimate the Class
by considering the additional information relating to the
configuration of the systems tested during the evaluation to
EN54-20.
Where the VESDA detector is located remote from the
protected area (for example in a corridor outside the room)
then consideration must be given to returning the detector
exhaust to the protected area to balance the pressure
differences that may exist between the areas. In the majority
of applications, this is not necessary as pressure differences
are minimal. Where a small pressure difference is present
but it is not practical to return the exhaust, the VLC-800MX
may still be deployed but it may be necessary to remove the
pipe while the aspirator is off during flow normalization
(see section 9.8) to prevent residual flows corrupting the
normalization process and to ensure that flow monitor
operates correctly.
Where pressure differences may exceed 50Pa the pre-
engineered solutions presented in this manual may not be
reliable and it is recommended that the design is verified by
a suitably qualified installer using ASPIRE II.
Note: When transport times of <60 seconds are
specifically required, the maximum pipe length
for the pre-engineered systems is
65m. Transport times of <60 seconds can be
achieved with pipe lengths of up to 70m on
custom systems designed using Aspire II.

VLC-800MX
17A-03-VLC
412/08
© 2008 Tyco Safety Products PAGE 7 of 18
Registered Company: Thorn Security Ltd. Registered Office: Dunhams Lane Letchworth Garden City Hertfordshire SG6 1BE
EQUIPMENT:
PUBLICATION:
ISSUE No. & DATE:
Fig. 7 Capillary Sampling
4.4 CAPILLARY SAMPLING
Capillary sampling consists of 8mm OD flexible tubes up to
2m long, running from the main pipework in place of
standard sampling holes. Longer capillary tubes (up to 8m
long) may be used but system performance must be verified
using the ASPIRE II pipe modelling software.
Fig. 7 illustrates capillary sampling.
4.5 PIPEWORK INSTALLATION
The following points should be considered when installing
the sampling pipe:
•Aspirating Pipe should only be installed by a
competent contractor.
•Various pipe materials and colours may be
used but the most common is 25mm PVC or
ABS in red or white. Smooth bore tube is
preferable.
•All pipe runs must be adequately supported
with appropriate clips.
•Avoid the use of sharp elbows - use “slow”
bends for 90 degrees.
•Where pipe must be removable for
maintenance access (e.g. in front of an Air
Return Grille), use appropriate socket
unions.
•In environments with large temperature
variations expansion and contraction of the
pipe should be considered. The pipework
layout and clips must be able to
accommodate any likely movement. For
example ABS pipe expands by 0.1% with
every 10°C increase in temperature.
•All joints must be airtight - this is typically
achieved on plastic pipe using suitable
adapters and adhesives.
Note: DO NOT USE ADHESIVE ON THE PIPE
JOINT ENTERING THE DETECTOR
•Allow sufficient movement in the pipe at the
detector to facilitate removal for
maintenance. A tapering of the air inlet port
prevents the pipe from being inserted
beyond 15mm (5/8in).
•All pipe should be clearly marked as
‘Aspirating Detector’ or equivalent.
•All sampling holes should be clearly
marked. It is advisable to do this as each
hole is drilled to avoid any
misunderstandings.
•Ensure that swarf and installation debris is
cleared from the pipework before
connecting the pipe to the detector. This can
be achieved by using an industrial vacuum
cleaner prior to making the connection.
•On installations where the detector is in the
inverted orientation there may be a risk of
objects falling into the exhaust port. It may
be prudent to install a short length of
exhaust pipe to eliminate the risk.
WARNING:
THE PERFORMANCE OF THIS SYSTEM IS
DEPENDENT UPON THE PIPE
NETWORK. ANY EXTENSIONS OR
MODIFICATIONS TO THE DESIGNED
INSTALLATION MAY CAUSE IMPROPER
OPERATION. OPERATIONAL EFFECTS OF
SUCH CHANGES SHALL BE VERIFIED. A
DESIGN TOOL IS AVAILABLE FROM THE
MANUFACTURER.

VLC-800MX
17A-03-VLC
4 12/08
PAG E 8 of 18
E
112. 5
112. 5
205
95
225
225
MOUNTING
BRACKET
E = CABLE ENTRY POINT ON REAR OF ENCLOSURE
8mm FIXING HOLES
Fig. 8 VLC-800 Mounting Bracket
5. MOUNTING THE DETECTOR
BRACKET
Refer to Fig. 8. Mount the detector bracket (supplied) in
the specified location using suitable wall plugs and screws
(fixing holes 8mm). Ensure that the hooks on the bracket
point up.
Mount the detector to the bracket in the orientation
specified in the system drawing (see Fig. 8).
When positioning the detector ensure that sufficient space
is allowed for pipe and cable conduit connections. Xtralis
suggests that there is at least 150mm of clear space around
the air inlet pipe and cable entry points to allow for pipe and
conduit entry.
The front cover is simply removed by unscrewing two
Philips head screws. It is retained on the main enclosure
with a plastic tie but can be removed completely by
disconnecting the lead to the LED display card and twisting
the plastic tie through 90 degrees. If the detector is to be
installed in the inverted orientation then the cover must be
removed, rotated through 180 degrees and replaced. See
Fig. 9.

VLC-800MX
17A-03-VLC
412/08
© 2008 Tyco Safety Products PAGE 9 of 18
Registered Company: Thorn Security Ltd. Registered Office: Dunhams Lane Letchworth Garden City Hertfordshire SG6 1BE
EQUIPMENT:
PUBLICATION:
ISSUE No. & DATE:
CABLE ENTRY (ONE
ENTRY ON REAR OF
ENCLOSURE NOT SHOWN)
AIR INLET PORT AIR EXHAUST
PORT
CABLE ENTRY
AIR EXHAUST PORT
Fig. 9 Detector Orientation (the backbox shows the generic termination card)
In order to prevent the detector being removed from the
bracket once installed, an anti- tamper screw is provided as
shown in Fig. 3. This locks the detector to one of the hooks.
Ensure that it is screwed out before sliding the detector onto
the mounting brackets and screw it home once the detector
is in place.
6. EXTERNAL POWER SUPPLY
The VESDA VLC-800MX requires a 24V dc power supply.
This is generally provided by an EN54-4 compliant supply
(eg, PSM800 with APM800) with back up batteries and
fault indications. For 24hr backup with 0.5hr alarm the
LaserCOMPACT requires 7Ah batteries or larger.
If a supply other than a PSM800 is used, the fault relay from
the power supply should be connected to the Power Supply
Monitor input (PSM) terminals on the VLC-800MX in
order to inform the Tyco Panel of any faults. This input is
monitored and requires a 47k End-of-Line resistor. The
VLC-800MX records a PSU fault and reports a general fault
to the MX panel when a short circuit or open circuit is
detected on these terminals.
7. REMOTE LED AND RELAY
OPTIONS
The VESDA VLC-800MX provides connection for a
remote LED (terminals R+ and R-). This output has a 3K6
series resistor and is designed to power an LED directly
(powered by the loop). For it to be illuminated on Fire, the
appropriate configuration setting must be made in MX
Consys.
The VLC-800MX also provides an onboard relay (NO, C
and NC terminals) and an additional output to drive an
external relay (REL+ and REL- terminals). The onboard
relay is rated 2A @ 30Vdc and the additional output has a
27K resistor in series and is designed to power the external
relay from the loop. For the relay(s) to operate, the
appropriate configuration setting must be made in MX
Consys which relates to both the onboard relay and the
external relay output.
Note: MX Consys does not allow simultaneous
configuration of both the remote LED and the
onboard/external relay (only the relay can be
configured).
8. WIRING NOTES (FIG. 10 REFERS)
a) All wiring must conform to the current
edition of IEE Wiring Regulations and
BS5839 Part 1.
b) All conductors must be free of earths.
c) Remove the required push out plugs for
cable entry.
d) Run all cables and gland off as necessary.
e) If a power supply other than a PSM800 with
APM800 is used, connect the power supply
fault relay to the PSM+ and PSM- terminals
with a 47k EOL.
f) If a remote LED is required, connect to the
R+ and R- terminals.
g) If the onboard relay, is required connect to
the NO, C and NC terminals.
If an external relay is required, connect to
REL+ and REL- terminals.
h) Verify the correct polarity of wiring before
connecting the VLC-800MX to the
addressable loop and external power supply.

VLC-800MX
17A-03-VLC
4 12/08
PAGE 10 of 18
RS232 PORT FOR
VCONFIG PRO
CONNECTION
VLC800 TERMINATION CARD
L-
L+
L-
L+
R-
R+
REL-
REL+
PSM-
PSM+
0V
+24V
N.O
C
N.C
OV
+24V
EXTERNAL
24V SUPPLY
EXTERNAL SUPPLY
FAULT RELAY
47k
EOL
FROM CONTROLLER
OR PREVIOUS DEVICE
TO NEXT DEVICE
OR CONTROLLER
REMOTE LED
ONBOARD
RELAY
SUPPLY FOR
FURTHER DEVICES
EXTERNAL RELAY
DRIVE
EXTERNAL RELAY
}
FRONT PANEL
LED CONNECTOR
ASPIRATOR
CONNECTOR
PROGRAMMING
PORT
Fig. 10 Simplified Wiring Diagram
9. COMMISSIONING
9.1 OVERVIEW
Configuration of a VLC-800MX is a simple task for the
majority of installations and may be performed easily with
VSC software which is downloadable from
www.vesda.com. However, in some circumstances, custom
thresholds must be set by a VESDA approved agent.
Custom commissioning of the system is not covered in this
manual. Please refer to VESDA literature for further
information.
Commissioning requires the following essential steps:
1) Pipework checks and power up.
2) Configuration of the MX controller via MX
Consys.
3) Setting the MX address using the MX
programmer.
4) Commissioning of the Laser.COMPACT.
5) Performance tests.
9.2 PRECAUTIONS PRIOR TO POWER-UP
•Check that the supply is 24VDC and has the
capacity to power the VESDA.
•Ensure that the polarity is correct.
•Check that Loop, PSU monitoring and
external relay connections are correct.
•Ensure that the exhaust bung has been
removed.
•Ensure that the pipework is properly
installed and all joints are airtight.
•Ensure that sampling holes have been
drilled in the specified positions.
9.3 SETTING THE MX ADDRESS
The MX address is programmed using the standard MX
handheld programmer (801AP Service Tool) which is
connected to the VLC-800MX using the standard cable that
connects to all MX ancillary devices.
Note: The MX address may be programmed while
the VLC-800MX is not powered (24V dc). It
may also be programmed when the VLC-
800MX is powered and wired into the MX loop.
9.4 CONFIGURING THE MX PANEL
USING MX CONSYS
MX Consys Version 2.1 or later supports the VLC-800MX.
9.5 POWER-UP SEQUENCE
All LEDs should operate during the power on sequence –
any failures should be investigated. The aspirator starts after
several seconds and (assuming no previous commissioning)
an airflow fault will be reported within two minutes because
the flow has not been “normalised”.

VLC-800MX
17A-03-VLC
412/08
© 2008 Tyco Safety Products PAGE 11 of 18
Registered Company: Thorn Security Ltd. Registered Office: Dunhams Lane Letchworth Garden City Hertfordshire SG6 1BE
EQUIPMENT:
PUBLICATION:
ISSUE No. & DATE:
Fig. 11 Normalise Airflow
9.6 TESTING COMMUNICATION
When the MX controller has been configured and the VLC-
800MX is powered, the MX controller should automatically
detect the VLC-800MX if it does not then a ‘NO
RESPONSE’ message is generated.
If this does not happen then wiring diagnostics is required.
Note: It is most likely that the VLC-800MX will also be
reporting an urgent airflow fault at this stage.
9.7 CONNECTING A PC RUNNING VSC
To commission the VLC-800MX, it is necessary to connect
it to a PC running VSC software (V2.05.02 or later) via a
serial extension lead.
The following Sections (9.7 to 9.13) relate to the
commissioning of the VLC-800MX using VSC.
The connection is made using a cable with a 9-way ‘D’
(male) to 9-way ‘D’ type (female) with straight through
connections, ie, 1-1, 2-2, 9-9 etc.
When logged on, check that the detector clock (reported as
“Device time” on the Summary Status Tab - behind the
bargraph - see Figure 11) is correct. If it is not, then select
Set System Date and time from the Device menu to
synchronise the detector clock with the time and date of the
PC (which is assumed to be correct).
9.8 NORMALISING THE FLOW
The VLC-800MX will need to normalise the amount of air
which flows through the detector. This may be achieved
through VSC by running “Normalize Air Flow” from the
Device menu (see Fig. 11). Normalisation takes
approximately 11 minutes. For approximately the first 5
minutes the detector measures the normal flow to allow for
future monitoring of flow variations from this norm. For
approximately the last 5 minutes the aspirator is turned off
and the residual flow, due to any pressure differences, is
measured. If this is too large or if the normal flow is too
small a “normalisation failed” fault (fault 75) is reported.
Note: The VLC-800MX should respond by
continually blinking the OK LED with two
flashes while it is normalising.
9.9 SELECTING SMOKE THRESHOLDS
Smoke thresholds can be set in one of three ways.
1) The default Fire threshold of 0.2% obscuration/m
may be used for all standard design
configurations as each hole has a sensitivity better
than 4.5% obscuration/m (and provide EN54-
20:Class B sensitivity). However, this may not
achieve the optimum levels of protection possible.
2) The system can be set in AutoLearn to achieve
optimum levels of protection. This learning
algorithm runs for a maximum of 14 days and
monitors the background levels, setting the alarm
threshold at an appropriate level above the normal
background. See Section 9.11.

VLC-800MX
17A-03-VLC
4 12/08
PAGE 12 of 18
3) Customised thresholds can be set using a
PC running VLC.
Customised thresholds may be appropriate in particular
circumstances but should be used with caution. For
example, the default alarm threshold of 0.2% may be
inappropriate for a system protecting a small area (using
fewer holes than the maximum allowed) with a background
level around 0.15% obscuration/m. In this situation a Fire
threshold > 0.2% obscuration/m may be appropriate.
However, as a general rule, the maximum Alarm threshold
needed to ensure a given EN54-20 sensitivity Class is given
by the following expression:
Class C threshold < 6/ N % obscuration/m
Class B threshold < 3 / N % obscuration/m
Class A threshold < 1 / N % obscuration/m
(where N = total number of holes; sampling holes +
endcap)
Note: These rule of thumb expressions are only
relevant to the Pre-engineered designs
presented in this manual. They are not
relevant to pipe configurations designed by an
approved VESDA agent and verified using the
Aspire pipe modelling software.
9.10 PRE-ALRM AND ALARM DELAYS
The VLC-800MX supports Pre-alarm processing such that
if the analogue reading exceeds 82 for two consecutive
polls, the MX panel will report a pre-alarm condition. If
the analogue reading exceeds 112 for three consecutive
polls, then an alarm condition is reported. Any additional
delays to signalling or acting on the alarm condition may be
configured in MX Consys. There are no configurable
delays specific to the VLC-800MX.
9.11 USING AutoLearn
See Fig. 12. When using AutoLearn it is essential that the
protected area is operating in normal conditions. For
example, all building work should be complete and air
conditioning operational (if present). AutoLearn can be
started via VSC by selecting the “Start AutoLearn Smoke”
tab from the device menu. From this form you can set the
duration of AutoLearn (to a maximum of 14 days). Click
OK to accept and the VLC-800MX should respond by
continually blinking the OK LED with three flashes.
During Autolearn, the detector is fully active and uses the
alarm thresholds in place when Autolearn was started. At
the end of the Autolearn period the “learnt” thresholds are
automatically applied and become active. If an alarm
condition is detected during the Autolearn period then
autolearn is aborted.
Notes:
1) The VLC-800MX should respond by
continually blinking the OK LED with three
flashes while it is in Autolearn mode.
2) Early releases of VSC (version3.01.00 and
earlier) do not support Autolearn on the VLC-
800MX - please upgrade to the latest version
of VSC which is available on www.vesda.com
Fig. 12 AutoLearn

VLC-800MX
17A-03-VLC
412/08
© 2008 Tyco Safety Products PAGE 13 of 18
Registered Company: Thorn Security Ltd. Registered Office: Dunhams Lane Letchworth Garden City Hertfordshire SG6 1BE
EQUIPMENT:
PUBLICATION:
ISSUE No. & DATE:
Fig. 13 Flow Threshold Setting
9.12 SETTING FLOW THRESHOLDS
See Fig. 13. This can be selected from the configuration
tabs which are accessed by double clicking on the device
Device/View Configuration menu and selecting the Flow
Threshold Tab. The default is Medium thresholds. Only
Medium and Narrow thresholds comply with EN54-20
which requires detection of +/-20% change in flow. When
setting custom thresholds the low urgent and high urgent
thresholds should tighter than 80% and 120% respectively
for compliance with EN54-20.
9.13 COMMISSIONING TESTS
There are two alternative approaches to commissioning
tests. The first is simply a check to ensure that the system
responds to smoke and is appropriate on systems designed
for compliance with local codes and standards. The second
approach is a performance based test which is often used to
demonstrate the superior performance capabilities of the
VESDA technology.
It is beyond the scope of this manual to discuss the details
of performance based testing as details of the tests are
particular to each application. However, guidance may be
found in VdS rules or British Standards (eg, BS6266)
which provides good information on some standard
commissioning tests. The FIA (UK Fire Industry Association)
Code of Practise for Aspirating Smoke Detections is also a
good source of information on performance based testing.
(available from www.FIA.uk.com).
Performance to appropriate standards and codes (such as the
EN54 series) is assured if the detector has been installed in
accordance with this manual. This is based on compliance
testing of this product against the standard EN54 fire tests with
only one sampling hole exposed to the test fire and the
remaining holes drawing clean air. However, to ensure the
integrity of the pipework the following tests must be
performed:
1) From the controller set the VLC-800MX into
walk test. (Faults will still be reported).
2) Introduce a sample of smoke into the end cap(s)
– with a concentration equivalent to that used
for routine testing of point detectors.
3) Check that an Alarm is reported within 90
seconds. Response times over 90 seconds
indicate that the pipework may not be installed
to specification and should be investigated.
4) Reset the Alarm from the controller.

VLC-800MX
17A-03-VLC
4 12/08
PAGE 14 of 18
Action Frequency Details
Check Power supplies Every month Test according to suppliers instructions. Note: Where the
condition of the battery is regularly checked automatically, less
frequent manual checks may be applicable.
Check the pipework Every 6 months Check that all pipe runs are intact, that pipe supports and joints are
firm and that the sampling holes are free of dirt.
Check air flows Every year Check logs to verify that no airflow faults have occurred. Where
possible use VConfig to read the airflow readings (including the
raw airflow readings). Any sign of drift should be investigated.
Check Filter Every year Check that there are no filter faults (where possible use VConfig
Pro to read the current filter counts).
Change Filter Every 2 years Fit a new filter cartridge regularly depending on the relative
cleanliness of the protected environment. Eg, every 2 years in a
normal environment, up to 5 years in a clean, air conditioned
computer room or every year or less in an area exposed to a dusty
or smokey atmosphere.
Smoke test Every year Set the detector into Walk Test mode and introduce smoke into the
end cap (see commissioning). Compare response times with those
previously recorded and investigate any discrepancies.
Flush sampling points Every 2 years Isolate the detector, remove pipe from the inlet port and connect a
vacuum cleaner. Run the cleaner for several minutes.
Clean sampling points As necessary If flushing does not clear the sampling points then they must be
physically cleared.
Table. 1 Maintenance Schedule
5) Carefully check each sampling hole (using
field glasses if necessary). Introduce smoke
into any that cannot be inspected and into at
least 10% of the holes. Check that an Alarm
is reported at the VLC-800MX in each case.
6) Record all results for future reference –
particularly the response time from the end
cap(s) and the raw flow reading.
10. MAINTENANCE
10.1 OVERVIEW
The VESDA VLC-800MX requires little regular
maintenance as the majority of potential failures are
monitored.
There are only two serviceable items; the filter cartridge and
the aspirator.
On no account should the rear cover of the detector be
removed as this may invalidate the warranty.
10.2 SCHEDULE
Table 1 details the maintenance schedule necessary to
maintain the VESDA VLC-800MX in peak working order
in the majority of applications.
10.3 CHANGING THE AIR FILTER
CARTRIDGE
See Fig. 14. The filter cartridge is retained by a recessed
Philips head filter screw. Ensure that the screw driver is
properly located in the screw before applying any torque to
avoid damage to the cartridge.
A switch operates when the filter is removed and the fault
“filter removed” is reported. It is necessary to acknowledge
the filter as being replaced, and this is performed by the
“Reset Filter Settings” function in VSC (see Fig. 15).
Fig. 14 Air Filter Change

VLC-800MX
17A-03-VLC
412/08
© 2008 Tyco Safety Products PAGE 15 of 18
Registered Company: Thorn Security Ltd. Registered Office: Dunhams Lane Letchworth Garden City Hertfordshire SG6 1BE
EQUIPMENT:
PUBLICATION:
ISSUE No. & DATE:
Fig. 15
10.4 REPLACING THE ASPIRATOR
10.4.1 REMOVING THE ASPIRATOR
1) Remove the four screws (A) securing the
termination card.
2) Disconnect the aspirator cable loom from
the connector on the aspirator.
3) Gently pull out termination card (B) from
interface card (connected behind).
4) Be careful not to dislodge any wires
connected to the termination card.
5) Leave the termination card suspended by its
wires.
6) Pull off the air hose from aspirator pipe (D).
7) Undo three Philips head screws securing
aspirator (E). Screws are captive and do not
come off the aspirator.
8) Turn aspirator anti-clockwise (F) using the
exhaust port as the pivot point.
9) Push aspirator upward (G) and remove.
10.4.2 ASSEMBLY
1) Check the new aspirator has a gasket on the
inlet flange and three attached screws.
2) Wipe manifold outlet flange surface if dirty.
3) Do the reverse of disassembly.
4) Secure aspirator with three screws (E).
5) Connect removed air hose to pipe on
aspirator. Ensure a tight fit over the pipe.
6) Insert Termination Card (B) into interface
card (C).
7) Secure the termination card with four
screws (A).
8) Connect aspirator cable connector to socket
on aspirator. Connector is polarised and can
only be inserted one way.
9) Check all wires are secured to its connectors
or terminals.
10)Power ON the detector and check the
aspirator is running.
11)Close up the detector.

VLC-800MX
17A-03-VLC
4 12/08
PAGE 16 of 18
Fig. 16 Removal/Replacement of Aspirator Assembly
11. TROUBLE SHOOTING
11.1 INTERROGATING FAULT CONDITIONS
The VLC-800MX fault status is communicated via the MX
loop and more implicitly on the LEDs on the front of the unit.
See below for a description of LED behaviour:
Service LED: If this LED is lit fault(s) on the detector
are serviceable by a field technician
without the need to replace components.
However, if the Fault LED is lit and this
LED is not lit, then it is possible that the
faults present will require component
replacement.
Fault LED: If this LED is lit, the fault(s) present
require urgent attention.
Filter LED: If this LED is lit, filter replacement will be
necessary.

VLC-800MX
17A-03-VLC
412/08
© 2008 Tyco Safety Products PAGE 17 of 18
Registered Company: Thorn Security Ltd. Registered Office: Dunhams Lane Letchworth Garden City Hertfordshire SG6 1BE
EQUIPMENT:
PUBLICATION:
ISSUE No. & DATE:
Fault
No. Description
Fault
Solution
Service
able
Urgent
Fault Filter
0 Aspirator failed YES Check the cable. If okay, contact your supplier for
a replacement aspirator.
2 Comms fault on Port A YES Check MX loop connections and that the panel is
operational.
3 Detector PIC failure YES Contact your supplier for a replacement detector.
4 Filter removed YES YES Replace the filter. If problem persists, check filter
switch.
7 Software fault found YES Contact VESDA.
8 Aspirator speed control failure YES Contact VESDA.
11 Filter approaching capacity YES YES Replace Filter.
12 Zone setup = factory defaults YES Use VConfig PRO to “accept the factory defaults”
and recommission the detector.
14 Flow sensors = factory defaults YES Contact VESDA.
15 AC mains failure YES YES Check the external Power Supply (monitored on
the PSM monitoring input, see Fig. 10).
22 Flow sensor failure pipe 1 YES Contact VESDA.
23 Laser signal too low YES Contact your supplier for a replacement detector.
27 AutoLearn aborted YES Inspect the Smoke Trends using VConfig PRO.
Investigate and eliminate the causes and re-run
AutoLearn (or set the alarm thresholds manually).
29 Manufacturer setup corrupted YES Contact your supplier for a replacement detector.
33 User list = factory defaults YES Use VConfig PRO to “accept the factory defaults”
and recommission the detector.
34 Detector setup = factory defaults YES Contact your supplier for a replacement detector
36 Event Log Corrupt YES Under ‘DST’ access, “clear the event log”.
Contact VESDA if fault persists.
37 Detector cal = factory defaults YES Contact VESDA.
38 Detector EEPROM failure YES Contact VESDA.
51 Urgent high airflow pipe 1 YES YES Inspect pipework for breakage’s or leaks and
rectify. Re-normalise if necessary.
52 Minor high airflow pipe 1 YES Investigate reasons for drift in flow reading.
53 Minor low airflow pipe 1 YES Investigate reasons for drift in flow reading.
54 Urgent low airflow pipe 1 YES YES Inspect pipework for blockages and rectify. Re-
normalise if necessary.
56 Clock failed YES Contact VESDA.
59 Fault test YES
65 Incompatible SW version detected YES Contact VESDA.
73 Filter clogging YES YES YES Replace filter urgently.
74 Raw flow too high YES Eliminate excessive positive pressure assisting the
flow and/or reduce the number/size of sampling
holes.
75 Normalisation has failed YES Investigate - are the sampling holes drilled?, has
the exhaust plug been removed.
76 Filter replaced but not
acknowledged
YES YES Use VConfig Pro to acknowledge that a new filter
has been fitted (or old one removed).
77 Normalising YES
80 No factory flow calibration YES Contact VESDA.

VLC-800MX
17A-03-VLC
4 12/08
PAGE 18 of 18
12. ORDERING INFORMATION
VLC-800MX VESDA Laser COMPACT: 516.018.012
Air Filter Cartridge: 516.018.504 Xtralis: VSP-005
Aspirator Fan: 516.018.515 Xtralis: VSP-015
VESDA 24V dc 2A Power Supply: 516.018.407 Xtralis: VSP-220
13. APPROVALS
The VLC-800MX is CE marked to the Construction Products Directive (CPD) supported by an EC Certificate of Conformity
(0832-CPD-0770 issued by BRE Global) to EN 54-20. The VLC-800MX is approved by LPCB and VdS to EN 54-20 under
Xtralis AG certificate numbers 305b issue 8 and G203026 repectively.
JM/jm
3rd December 2008
Table of contents
Other Tyco Smoke Alarm manuals
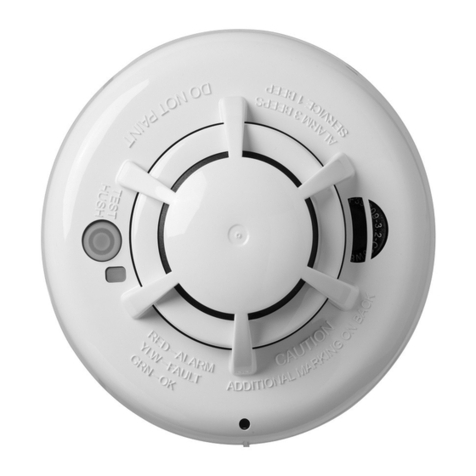
Tyco
Tyco Visonic SMD-429 PG2 Series User manual

Tyco
Tyco MR601TEx User manual
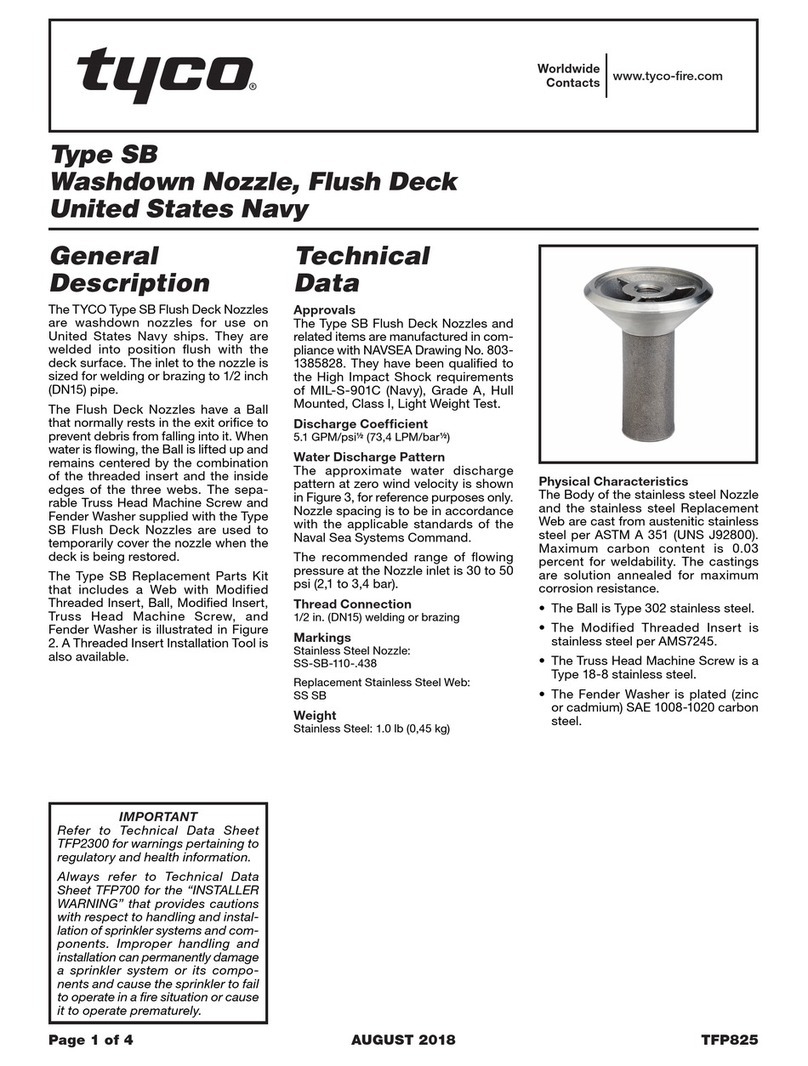
Tyco
Tyco SB User manual
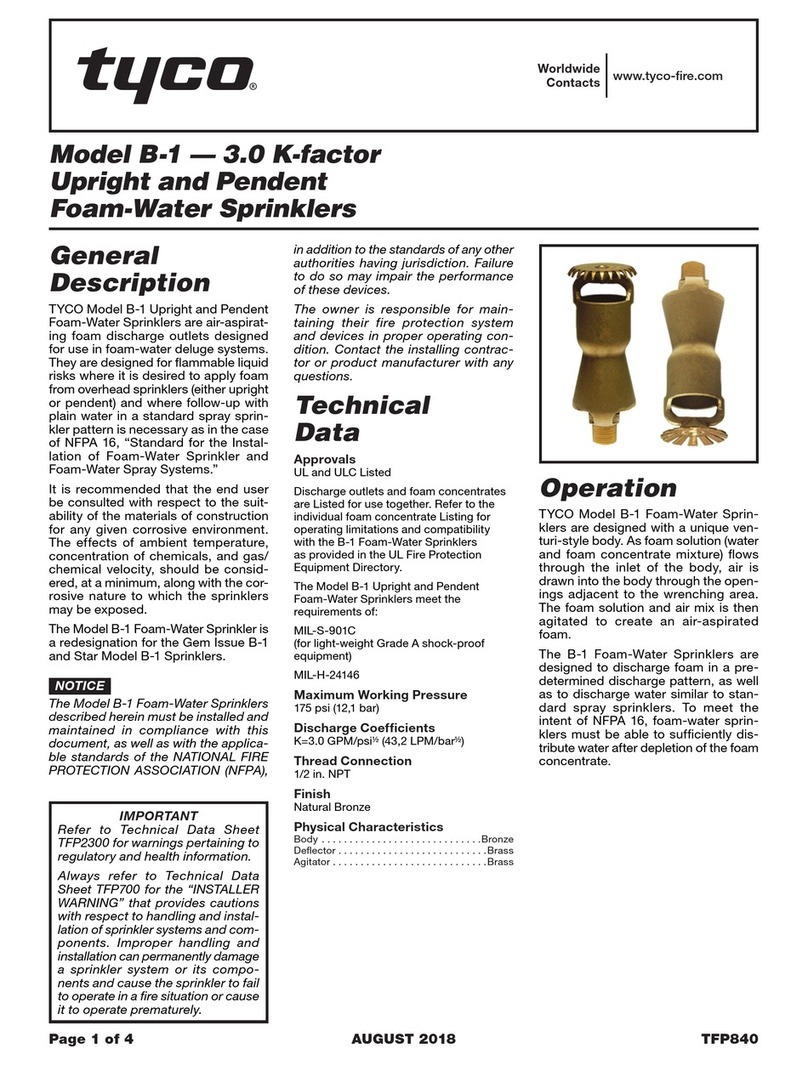
Tyco
Tyco B-1 User manual
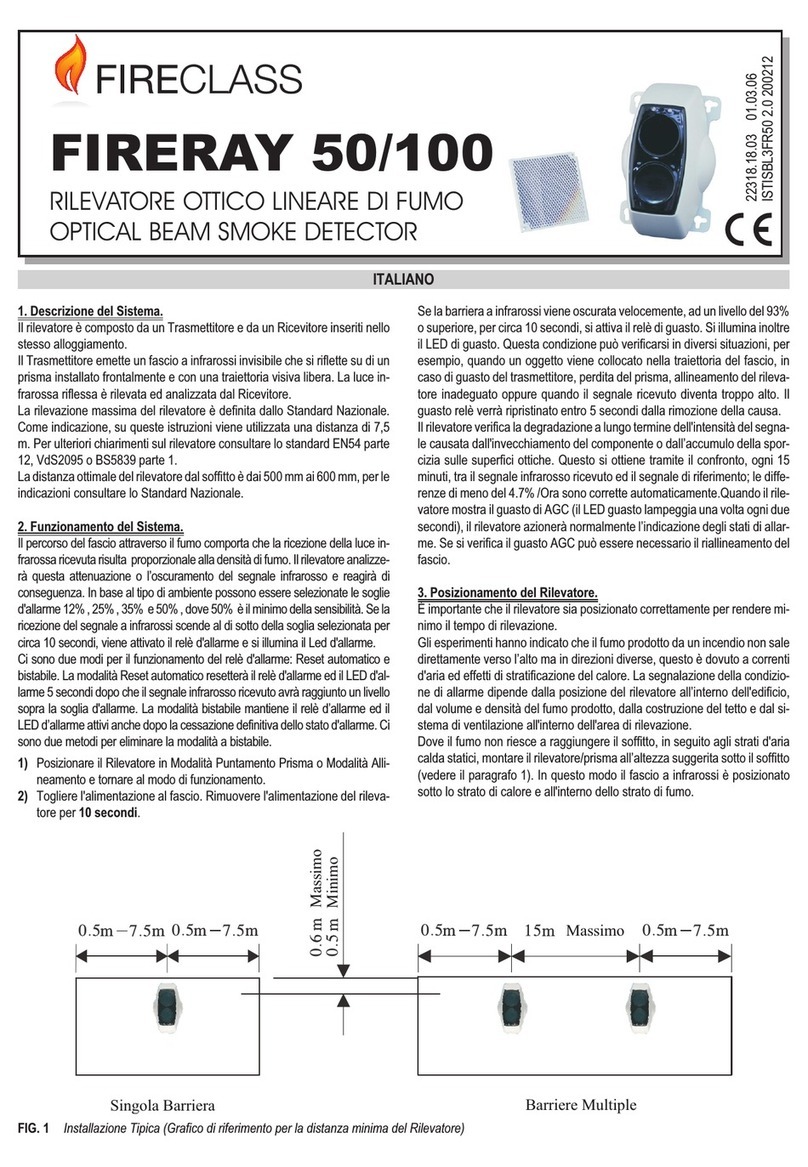
Tyco
Tyco FireClass FIRERAY 50 User manual

Tyco
Tyco 601PH User manual
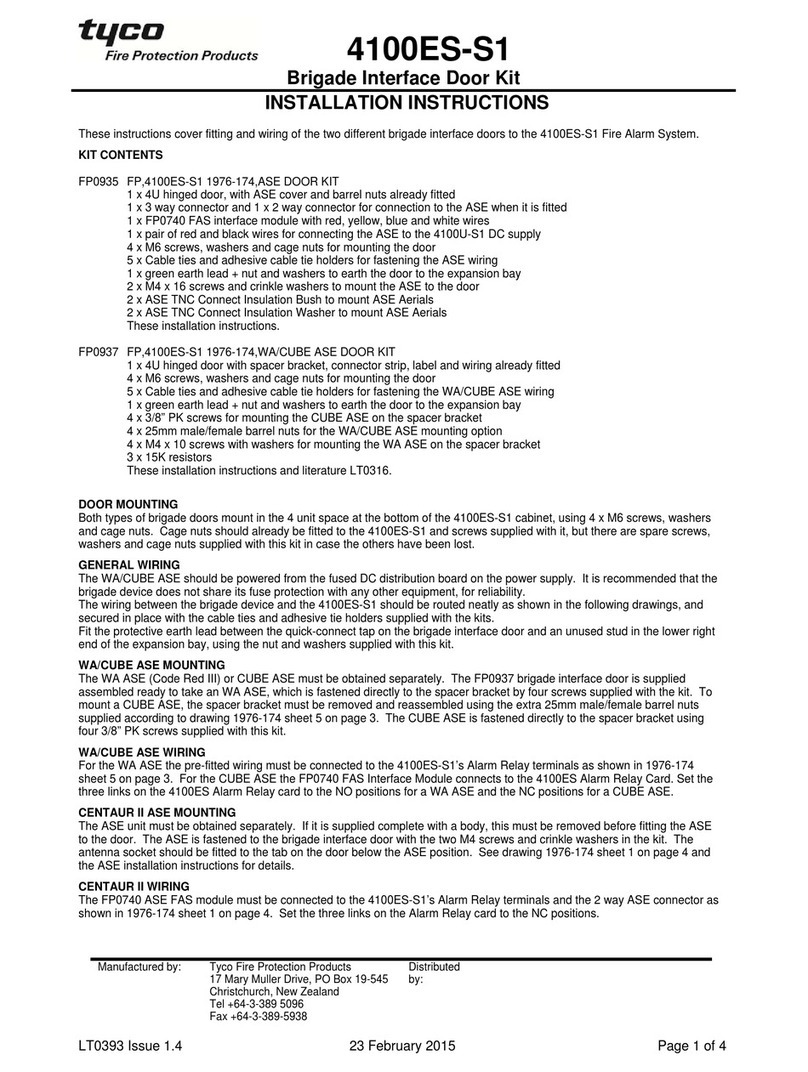
Tyco
Tyco 4100ES-S1 User manual
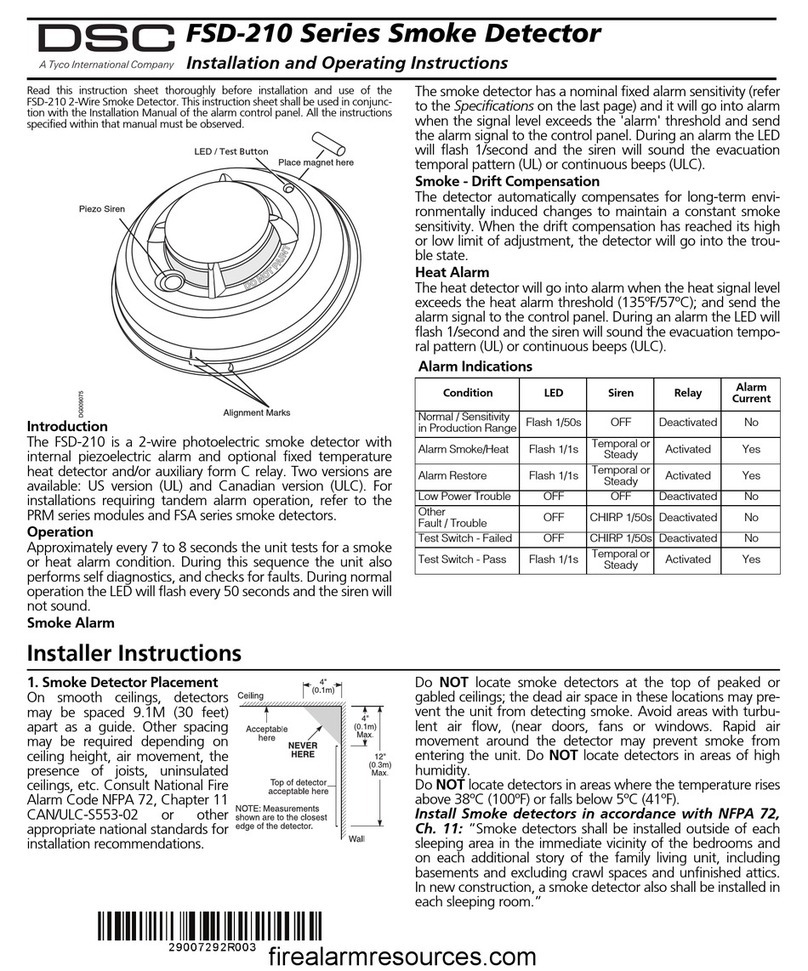
Tyco
Tyco DSC FSD-210 Series User manual
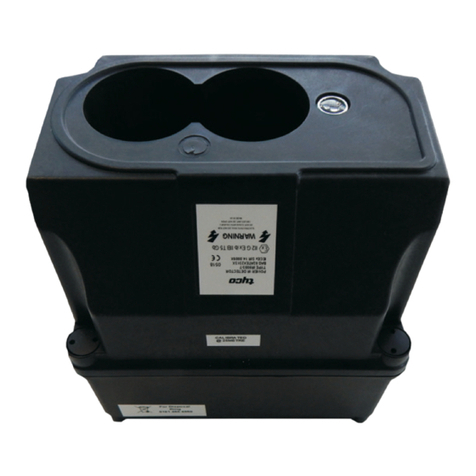
Tyco
Tyco IR6003/7 Specification sheet

Tyco
Tyco Fire Alarm User guide