UniData Communication Systems Starflow QSD User manual

Manual
Starflow QSD Model 6527B and 6537A
This equipment has been tested and found to comply with the limits for a Class A digital device,
pursuant to Part 15 of the FCC Rules in the U.S.A. These limits are designed to provide reasonable
protection against harmful interference when the equipment is operated in a commercial environment.
This equipment generates, uses, and can radiate radio frequency energy and, if not installed and used
in accordance with the instruction manual, may cause harmful interference to radio communications.
Operation of this equipment in a residential area is likely to cause harmful interference in which case
the user will be required to correct the interference at their own expense.
This equipment has been tested for compliance with European regulations as follows:
Application of Council Directive:
2004/108/EC
Standards to which Conformity is declared:
EN-61000-6-1:2001
EN-61000-4-2:1995
EN-61000-4-3:1995
EN-61000-4-4:1995
EN-61000-4-6:1996
ENV-50204:1995
Any changes or modifications to this equipment not expressly approved by the manufacturer Unidata
Pty Ltd could void the user’s authority to operate this equipment.
Revision History
File name / Revision Date
Authors & Change
Details
Checked/
Approved
Unidata Manual - 6537A Starflow QSD SDI-12 User Manual 27 05 2019.docx
27 05 2019
IM First Draft
MS
Unidata Manual - 6537A Starflow QSD User Manual 21 06 2019
21 06 2019
RDS, PD
MS
Unidata Manual - 6537A Starflow QSD User Manual 04 07 2019.doc
04 07 2019
CB
KC
Unidata Manual - 6537A Starflow QSD User Manual 12 07 2019.doc
12 07 2019
KC
MS
Unidata Manual - 6537A Starflow QSD User Manual 17 07 2019
17 07 2019
KC MS
MS
Unidata Manual - 6537A Starflow QSD User Manual 28 10 2019.doc
28 10 2019
CB
PD
Unidata Manual - 6527B and 6537A Starflow QSD User Manual 27 11 2019.doc
27 11 2019
IM
CB
Unidata Manual - 6527B and 6537A Starflow QSD User Manual 17 01 2020.docx
17 01 20
IM Update EC Specs
DM
Streamline Measurement Ltd
Streamline Measurement Ltd
Streamline Measurement Ltd, 01457-864334, sales@streamlinemeasurement.co.uk, www.streamlinemeasurement.co.uk

Manual – Starflow QSD Model 6527B and 6537A
Unidata Manual - 6527B and 6537A Starflow QSD User Manual 17 01 2020.docx Contents 1
TABLE OF CONTENTS
1.0 Introduction ........................................................................................................................1
2.0 Specifications.....................................................................................................................3
3.0 Operating Principles & Measured Parameters ................................................................5
3.1 Flow Velocity Measurement .................................................................................. 5
3.2 Water Depth Measurement – Ultrasonic ............................................................... 6
3.3 Water Depth Measurement - Pressure.................................................................. 6
3.4 Temperature.......................................................................................................... 6
3.5 Electrical Conductivity (EC) – 6537A Only ............................................................ 6
3.6 Accelerometer ....................................................................................................... 7
3.7 Power Supply Voltage ........................................................................................... 7
3.8 Signal Spread........................................................................................................ 7
3.9 Received Signal Strength Indicator (RSSI) ........................................................... 7
4.0 Taking Measurements From The Instrument ..........................................................................8
4.1 SDI-12 Operation ........................................................................................................ 8
4.2 Modbus RS485 Operation......................................................................................... 12
5.0 Installation ................................................................................................................................16
5.1 Site Considerations................................................................................................... 16
5.2 Instrument Mounting ................................................................................................. 17
6.0 Configuration - Using The sonic configuration software.....................................................19
6.1 Setup – Connection to Starflow QSD........................................................................ 19
6.2 Settings Starflow QSD .............................................................................................. 21
6.3 Configuration – Configuring Sonic ............................................................................ 25
6.4 Tools – Starflow QSD................................................................................................ 27
7.0 Instrument maintenance .........................................................................................................30
Apendix A - Factors Affecting Flow Measurement Accuracy....................................................31
Alignment with Flow and Depth....................................................................................... 31
Instantaneous Versus “Averaged” Velocity..................................................................... 31
Conversion of Logged to Mean Velocity ......................................................................... 31
The Speed of Sound in Water......................................................................................... 32

Manual – Starflow QSD Model 6527B and 6537A
Unidata Manual - 6527B and 6537A Starflow QSD User Manual 17 01 2020.docx
Page 1
1.0 INTRODUCTION
The 1st generation 6527 Starflow QSD Instrument measures water Velocity, Depth (ultrasonic) and
Temperature. The Starflow QSD – 2nd generation has been enhanced to include Depth using the
Pressure – Hydrostatic method (6527B Starflow QSD) and Electrical Conductivity (6537A Starflow
QSD) as well as Tilt. These models come standard with both SDI-12 and RS-485 (Modbus RTU)
interfaces.
The capacity of the instrument to measure the water conductivity is unique and allows the instrument
to determine not only the water velocity, flow and volume but also an indication of the water quality.
The conductivity measurement can also be used where existing techniques for measuring water
quality are unsuitable or too expensive.
By using Digital Signal Processing (DSP) techniques, the Starflow QSD is able to perform in a wide
range of environments. It is used to measure flows and water conductivity (6537A) in pipes, channels
and small streams. It can operate in a range of water qualities from fresh streams to primary sewage
channels.
Electrical conductivity feature of 6537A instrument empower the user to detect unusual waste
dumping / agriculture runoff which is not visible using current flow sensors. The pressure depth
sensor allow the instrument to be placed in an angled position on the wall of irregularly shaped
drainage canals or on the sides of channels in which is difficult or impossible to place it on the
channel floor.
The Tilt parameter is measured by an internal accelerometer and represents the pitch and roll of the
instrument body as it is installed and its measurement is in degrees angle.This provides user with
useful information of the sensor after mounted under water or during a post installation inspection.
Starflow QSD system consists of:
Model 6527B or 6537A Starflow QSD instrument
Model 6527M Stainless Steel Mounting Bracket
6527B
6537A

Manual – Starflow QSD Model 6527B and 6537A
Unidata Manual - 6527B and 6537A Starflow QSD User Manual 17 01 2020.docx
Page 2
Hardware Accessories:
The following accessories should be purchased according to your application requirements.
Model 6907B-14 12V, 14Ah Sealed Lead Acid Battery
Model 6904I-10 10W Solar Recharge Panel & Mount
Model 6904I-20 20W Solar Recharge Panel & Mount
Model 6702S Starflow QSD Weatherproof Enclosure
Model 6705A Small Expanding Clamp SS expanding turn-buckle and band clips
100mm wide, 100mm long, 50mm expansion
Use in pipes up to 600mm (24") in diameter
Model 6705B Large Expanding Clamp SS expanding turn-buckle and band clips.
100mm wide, 150mm long, 100mm expansion
Use in pipes over 600mm (24") in diameter
Model 6705D 1800mm Band Segment 100mm wide, 0.6mm Stainless Steel band
With 50mm spaced locating holes at both ends
Model 6705F Band Joiner Stainless Steel joiner
Instrument Accessories:
Model 6515A QSD Barometric Reference for pressure depth reading compensation
Software Accessories:
Sonic Software A software utility enabling advanced access to configuration parameters

Manual – Starflow QSD Model 6527B and 6537A
Unidata Manual - 6527B and 6537A Starflow QSD User Manual 17 01 2020.docx
Page 3
2.0 SPECIFICATIONS
Velocity (Continuous Beam):
Range
20mm/sec to 0.8 m/sec
20mm/sec to 1.6 m/sec (default)
20mm/sec to 3.2 m/sec
20mm/sec to 13.2 m/sec
Bidirectional velocity capability, set using configuration tools
Accuracy Typical ±1%
Resolution 1 mm/s
Depth (Ultrasonic)
Range 20mm to 5000mm (5m)
Accuracy ± 1% of full scale
Resolution 1 mm
Depth (Pressure)
Range 0mm to 10m
Accuracy Typical ±0.19% for 0m to 5m range
Typical ±0.38% for 0m to 10m range
Resolution 1 mm
Temperature
Range 0°C to 60°C
Accuracy ±0.5°C
Resolution 0.1°C
Electrical Conductivity (EC) – 6537A ONLY
Range 0 to 200,000 µS/cm, typically ±1% of measurement
Resolution ±1 µS/cm
May be recorded as a 16-bit value (0 to 65,535 µS/cm) or
a 32-bit value (0 to 262,143 µS/cm)
Tilt (accelerometer)
Range ±70° in roll and pitch axes.
Accuracy ±1° for angles less than 45°
Power Requirements
Voltage range 12 to 24 V DC
Supply current 50uA standby, 100mA active for 1 second @12V
Power source 12V DC - typically an external batter
Communications
SDI-12 SDI-12 v1.3
Connection Single cable up to 50 metres long (standard fitment is 15m)
Maximum cable 60m defined by SDI12.org
RS-485 Modbus RTU
Connection Single cable up to 300 metres long (standard fitment is 15m)
Baud rate and parity Configurable

Manual – Starflow QSD Model 6527B and 6537A
Unidata Manual - 6527B and 6537A Starflow QSD User Manual 17 01 2020.docx
Page 4
Environmental
Operating 0°C to 60°C (water temperature)
Storage -20°C to 60°C
Humidity up to 100 % RH
Physical
Dimensions Approximately L 135 mm, W 55 mm, H 22 mm
Material Epoxy-sealed body, stainless steel mount
Weight 1kg with 15m of Cable
Cable 15 metre
Cable options User-specified, up to 50 metres
Instrument Wiring Table
Variants for Wiring are detailed below
Brown Wire Variant
Starflow QSD / Wire Colour Function / Signal Name
White
SDI-12
Brown
Power
Green
Ground
Yellow
A- (Modbus)
Pink
B+ (Modbus)
Grey
One-Wire *
Red Wire Variant
Starflow QSD / Wire Colour Function / Signal Name
White
SDI-12
Red
Power
Yellow
Ground
Blue
A- (Modbus)
Orange
B+ (Modbus)
Grey
One-Wire *
* Use with Unidata 6515A QSD Barometric Reference Module
When Unidata 6515A QSD Barometric Reference module is connected, the instrument will
automatically handle the barometric correction and will report actual water level instead of water head
plus atmospheric pressure.
If your data logger has a barometric sensor, the data logger program must perform the barometric
correction OR the user can perform a post processing method to correct for barometric changes by
using barometric pressure data from a trusted source such as a weather department or another
barometer close by.
The 6515A QSD Barometer Reference module should be:
a) Mounted in an enclosure near to the data logger in a position protected from the elements.
b) The enclosure should be vented to allow the barometer sensor to be exposed to atmospheric
pressure variations.

Manual – Starflow QSD Model 6527B and 6537A
Unidata Manual - 6527B and 6537A Starflow QSD User Manual 17 01 2020.docx
Page 5
3.0 OPERATING PRINCIPLES & MEASURED PARAMETERS
The 6527B and 6537A Starflow QSD measure:
•Flow velocity
•Depth (ultrasonic)
•Temperature
•Depth (Pressure)
•Electrical Conductivity (EC) – 6537A Only
•Tilt ( the angular orientation of the instrument)
The Starflow QSD performs data processing and analysis each time a measurement is made.
This can include rolling averaging and outlier/filter functions for Depth (ultrasonic), Velocity, Depth
(Pressure) and Conductivity (6537A). The function parameters can be configured via SDI-12
eXtended command or Sonic software.
3.1 Flow Velocity Measurement
For Velocity the Starflow QSD uses Continuous Mode Doppler. To detect water velocity, an
ultrasonic signal is transmitted into the water flow and echoes (reflections) returned from particles
suspended in the water flow are received and analysed to extract the Doppler shift (velocity). The
transmission is continuous and simultaneous with the returned signal reception.
During a measurement cycle the Starflow QSD emits a continuous signal and measures signals
returning from scatterers anywhere and everywhere along the beam. These are resolved to a
mean velocity that can be related to a channel flow velocity at suitable sites.
The receiver in the instrument detects reflected signals and those signals are analysed using
digital signal processing techniques.
Internally the instrument auto scales over these ranges if the range is manually set in the
settings: Bidirectional velocity capability is a supported option.
20mm / s to 0.8 m sec
20mm / s to 1.6m/s (default)
20mm / s to 3.2 m/s
20mm / s to 13.2 m/s

Manual – Starflow QSD Model 6527B and 6537A
Unidata Manual - 6527B and 6537A Starflow QSD User Manual 17 01 2020.docx
Page 6
3.2 Water Depth Measurement – Ultrasonic
For Depth measurement the Starflow QSD uses Time-of-Flight (ToF) Ranging. This involves
transmitting a burst of ultrasonic signal upwards to the surface of the water and measuring the time
taken for the echo from the surface to be received by the instrument. The distance (water depth) is
proportional to the transit time and the speed of sound in water (corrected for temperature and
density). The maximum ultrasonic depth measurement is limited to 5m.
3.3 Water Depth Measurement - Pressure
Sites where the water contains large amounts of debris or air bubbles may be unsuited for ultrasonic
depth measurement. These sites are better suited to using pressure to determine the water depth.
Pressure based depth measurement may also be applicable to sites where the instrument cannot be
located on the floor of the flow channel or it cannot be mounted horizontally.
The Starflow QSD is fitted with a 2 bars absolute pressure sensor. The sensor is located on the
bottom face of the instrument and utilises a temperature compensated digital pressure sensing
element.
Where depth pressure sensors are used the atmospheric pressure variation will cause errors in the
indicated depth. This is corrected by subtracting the atmospheric pressure from the measured depth
pressure. A barometric pressure sensor is required to do this.
If the data logger used to read the Starflow QSD does not incorporate a barometric pressure sensor
then the One Wire Bus 6515A Reference Barometer option should be purchased. This mounts near to
the logger and is read by the Starflow QSD instrument which will then automatically compensate for
the atmospheric pressure variations ensuring an accurate depth measurement is achieved. This
enables Starflow QSD to report actual water depth (pressure) instead of barometric pressure plus
water head.
3.4 Temperature
A solid state temperature sensor is used to measure the water temperature. The speed of sound in
water and its conductivity is affected by temperature. The instrument uses the measured temperature
to automatically compensate for this variation.
3.5 Electrical Conductivity (EC) – 6537A Only
The 6537A Starflow QSD is equipped with the capacity to measure the conductivity of the water. A
linear four electrode configuration is used to make the measurement. A small current is passed
through the water and the voltage developed by this current is measured. The instrument uses these
values to calculate the raw uncorrected conductivity.
Conductivity is dependent on the temperature of the water. The instrument uses the measured
temperature to compensate the returned conductivity value. Both raw or temperature compensated
conductivity values are available.

Manual – Starflow QSD Model 6527B and 6537A
Unidata Manual - 6527B and 6537A Starflow QSD User Manual 17 01 2020.docx
Page 7
3.6 Accelerometer
The Starflow QSD has an integral accelerometer sensor to measure the inclination of the instrument.
The sensor returns the roll and pitch angle of the sensor (in degrees). This information can be useful
in ensuring the installation position of the sensor is correct and for determining if the instrument has
moved (bumped or washed away) during post installation inspection.
3.7 Power Supply Voltage
The instruments internal power supply voltage is readable as a measurement parameter. The
operating range of the power supply is 12 to 24V DC. If the supply voltage falls below defined limits
the instrument stop taking measurements to ensure only quality data is measured.
3.8 Signal Spread
This can be used to determine the amount of “turbulence” affecting the signal quality and used to
reject the measurement if the spread (turbulence) is too great. A good flow would return a spread
value of around 50, anything above 100 would be considered poor.
10 Excellent SPREAD
20 Very good SPREAD
30 Good SPREAD in dirty river water
40 Good SPREAD in clean river water (Typical)
60 Average SPREAD
80 Poor SPREAD
90 Bad SPREAD (Poor site selection)
100 Above 100 gives unreliable velocity data.
3.9 Received Signal Strength Indicator (RSSI)
The RSSI channel is the measurement of the received signal power. RSSI values may change
significantly each measurement because of the number of reflectors in the water at that time
RSSI Channel Interpretation
0 Threshold signal at Analog.Gain=5 (default)
1 Useable Signals
5 Good signal
10
20 Typical signal in clean river water
40
1000 Saturated signal
Therefore in very laminar flow situations (perfect conditions) the RSSI value should be very low,
between 1-10. In typical river situations RSSI will be between the 1 and 30.
}

Manual – Starflow QSD Model 6527B and 6537A
Unidata Manual - 6527B and 6537A Starflow QSD User Manual 17 01 2020.docx
Page 8
4.0 TAKING MEASUREMENTS FROM THE INSTRUMENT
The Starflow QSD instrument has both SDI-12 and RS485 (Modbus RTU) Interfaces. The following
sections describe them in detail. If you are a user of Unidata NRL loggers you can simply add the
Starflow QSD as an instrument within the logging scheme as a SDI-12 instrument
4.1 SDI-12 Operation
The Starflow QSD can be operated as a standard SDI-12 (V1.3) sensor.
Measurement commands (M! & C!) returns atttn(n) response with ttt indicating the delay until
measurements are ready and n(n) indicates the number of parameters return.
A Service Request is sent.
The R! command returns an acknowledge response a<CR><LF>
The D! command returns the measured data values.
SDI-12 Command Notes:
1. Change Address aAb! is supported
2. Start Verification aV! returns an acknowledge response
3. Extended Command aX is supported (see below for details)
4. D/R1…9! Commands operate the same as a D/R0! command
5. M/C1...9! Commands operate the same as an M/C! command
6. MC, CC & RC commands requesting CRC are supported
4.1.1 Measure Parameters
Measured parameters – 6527B/6537A Starflow QSD measures several parameters and these are
available for collection by a data logger. Up to 16 parameters are supported and the default
configuration only returns 9 parameters. The parameters are associated with the instrument internal
Channels. The parameters can be configured to return in any sequence (see extended commands
below). The default sequence parameters are listed below:
Parameter
Description
Units
Example
Meaning
1 Water Temperature 1/10 ºC +152 15.2ºC
2 Battery Voltage 1/100 Volts +1302 13.02Volts
3 Ultrasonic Depth mm +123 123mm
4
CW Water Velocity
+/- mm/s
-234
234mm/s -ve flow
5
RSSI (signal level)
no units
+66
66 (no units)
6
Signal Spread
no units
+45
45 (no units)
7
Conductivity (TC)
µS/cm
+2350
2350µS/cm
8
Pressure Depth
+/- mm
+123
123mm
9
Barometric Reference
+ mm
+10120
10120mm

Manual – Starflow QSD Model 6527B and 6537A
Unidata Manual - 6527B and 6537A Starflow QSD User Manual 17 01 2020.docx
Page 9
4.1.2 Channels Table
These Channels are data registers within the instrument. That the SDI-12 parameters are assigned to
the Channels and their order of return can be configured using the Sonic software utility and SDI-12
eXtended command.
Channel
Description
Units
Example
Meaning
0
Water Temperature
1/10 ºC
+152
15.2ºC
1
Battery Voltage
1/100 Volts
+1302
13.02Volts
2
Ultrasonic Depth
mm
+123
123mm
3
CW Water Velocity
+/- mm/s
-234
234mm/s -ve flow
4 RSSI (signal level) no units +66 66 (no units)
5 Signal Spread no units +45 45 (no units)
10 X-Axis Tilt +/- deg -9 9 deg left tilt
11
Y-Axis Tilt
+/- deg
7
7 deg forward tilt
12
Pressure Depth
+/- mm
+123
123mm
13
Barometric Reference
+ mm
+10120
10120mm
70
Conductivity (UC)
µS/cm
+2350
2350µS/cm
72
Conductivity (TC)
µS/cm
+2350
2350µS/cm
Default SDI-12 Parameters and Channels assignment are listed below
Parameter
Channel
Description
Units
1
0
Water Temperature
1/10 ºC
2
1
Battery Voltage
1/100 Volts
3
2
Ultrasonic Depth
mm
4
3
CW Water Velocity
+/- mm/s
5
4
RSSI (signal level)
no units
6
5
Signal Spread
no units
7
72 Conductivity (TC) µS/cm
8
12 Pressure Depth +/- mm
9
13 Barometric Reference + mm
10
unassigned
11
unassigned
12
unassigned
13
unassigned
14
unassigned
15
unassigned
16
unassigned

Manual – Starflow QSD Model 6527B and 6537A
Unidata Manual - 6527B and 6537A Starflow QSD User Manual 17 01 2020.docx
Page 10
4.1.3 Extended Commands
To enable various settings and adjustments to be made to the Starflow QSD using SDI-12 eXtended
command aX!. The extended command format is:
Command Response
Examine setting aXn! a<values><CR><LF>
Change setting aXn<values>! a<values><CR><LF>
Where n = setting number to examine or change
0 – Sensor address in ASCII (aX0b! is the same as aAb! Command)
1 – Number of measurements returned by aD0! or aR0! Commands and the Sequence (order) of
returned measurements (parameter addresses)
2 – Min Battery (in 1/100s of Volts), below which water measurements are not made
+ Min Water Depth (in mm) below which Velocity will not be measured
+ Min RSSI (signal level) below which Velocity will not be measured
+ Max Signal Spread above which Velocity will not be measured
3 – Velocity Ripple Filter (in 0.75mm/s units) below which Velocity will be attenuated
+ Velocity Gain
+ Velocity Pre-Filter (0=none, 1= 33, 2=83, 3=167 mm/s) below which Velocity is attenuated
4 – Outlier Filter and Moving Average setting for Depth (Ultrasonic), CW Velocity, Conductivity and Depth
(Pressure)
5 – Set (+ve) and Reset (-ve) QSD 32 Options (0…31)
6 – Conductivity Temperature Correction Coefficient
7 – Pressure Depth zero Offset (for barometric compensation)
# - Restore Factory Default Settings
<values> = integer(s) with ± sign (no decimal point) or ASCII string (no ± sign)
Hint: If the Sensor has an unknown address, use the “?” wild card address along with the A or X0
command to reset a known address (e.g. ?A0! or ?X00! to reset the address to “0”)

Manual – Starflow QSD Model 6527B and 6537A
Unidata Manual - 6527B and 6537A Starflow QSD User Manual 17 01 2020.docx
Page 11
4.1.4 Starflow QSD - SET/RESET Option Settings (aX5)
To alter the operation of QSD, there are 32 option settings numbered 0 to 31. These affect QSD’s
performance so must be changed “wisely”. The aX5 eXtended command is used and several options
adjustments (set and/or reset) can be made using a single aX5 command. A SET option is a
<+value> and RESET a <-value>. The <value> is the option number 0..31. Undefined options MUST
NOT be changed.
Option No. SET Meaning RESET Meaning
<value> < + value> < - value>
04 Enable Pressure Depth Disable Pressure Depth
05 Zero P.Depth on Fail Retain last P.Depth
06 Enable Barometric Ref Disable Barometric Ref.
07 Show –ve P.Depth P.Depth +ve only
08 Enable Electrical Conductivity (EC) Disable Electrical Conductivity (EC=0)
16 Enable Depth Measurement Disable Depth Measurement (Depth = 0)
17 Depth = 0 if < Min Operating Level Retain last measurement
18 Enable Depth Drive 1 Disable Depth Drive 1
19 Enable Depth Drive 2 Disable Depth Drive 2
20 Enable Depth Drive 3 Disable Depth Drive 3
21 Enable Depth Drive 4 Disable Depth Drive 4
22 Use MEDIAN value for Depth Use MAXIMUM value for Depth
24 Enable CW Velocity Measurement Disable CW Velocity (Velocity = 0)
25 CW Velocity = 0 if < MIN RSSI Retain last measurement
26 Enable -ve CW Velocity +ve Velocity regardless of direction
27 Enable SOS Temp Corr. Don’t correct for SOS
31 Velocity = 0 if > MAX SPREAD Retain last measurement
Examples:
Command Response Meaning
aX03! a3<CR><LF> Sensor address was “a” and now “3” **
aX1! a+9+0+1+2+3+4+5+72+12 aD0/R0! will return 9 measurements
+13+0+0+0+0+0+0+0<CR><LF> from Channel Nos. listed
aX1+6! a+6+0+1+2+3+4+5+72+12<CR><LF>>Now will return 6 measurements (max 16)
+13+0+0+0+0+0+0+0<CR><LF> from 1st to 6th Channel Nos. listed
aX2! a +1150+40+4+5000<CR><LF> Low battery limit is 11.50 Volts
Depth>40mm, RSSI>4,Spread>5000
aX2+1200! a+1200+25+1+300<CR><LF> Low battery limit changed to 12.00 Volts
aX4! a+3+0+3+0+3+0+3+0+3+0<CR><LF> Examine Outlier filter & Average setting
aX4+3+2! a+3+2+3+0+3+0+3+0+3+0<CR><LF> Change Moving Average from 0 to 2
aX5! a+1+16+17+18+19+20+22+24+27+30 Default SET Options***
aX5-18+21 a+1+16+17+19+20+21+22+24+27+30 Disable drive level 1, enable 4
aX7-33! a-33<CR><LF> Pressure Depth Offset = –33 mm of water
aX#! a+nnnnn<CR><LF> Restore Factory Defaults nnnnn=QSD Serial#
Notes: ** The Sensor address is an ASCII value so DOES NOT use a ± sign.
*** Only SET Options are displayed. Change order is not important.
**** Except for aX5, the order of changed parameters IS important. You MUST
re-enter all parameters occurring prior to the parameter you wish to change.

Manual – Starflow QSD Model 6527B and 6537A
Unidata Manual - 6527B and 6537A Starflow QSD User Manual 17 01 2020.docx
Page 12
4.2 Modbus RS485 Operation
The Starflow QSD can be operated as a Modbus RTU Slave sensor. The Baud rate and parity
selected must be configured prior to using the instrument. The instrument supports configurable Baud
rates for the RS-485 Communication Port (the SDI-12 Port is fixed to 1200/9600 as per the SDI-12
standard). There are two configuration parameters (baud rate & parity) and these may be changed via
the Sonic configuration utility (via Modbus).
When changing these, the new settings come into effect AFTER the response has been sent to the
SONIC/Modbus PC utility. To continue communicating via RS-485, the PC utility’s baud rate settings
MUST then be changed to match that of the Starflow QSD.
Use the “SETTINGS/Configure SONIC” menu to change baud rate settings, and then click
"CONNECT" to re-connect.
Note 1: SONIC ALWAYS starts in 9600,8,N,1 when launched in Windows.
Note 2: If a HARD FIRMWARE UPDATE (QSD Serial# set to zero) is performed over RS-485 at a
baud rate other than 9600, the update will succeed, but indicate failure because the existing RS-485
baud rate settings are not preserved across a hard update and have been reset to the default 9600.
RS485 Baud rate and Parity setting options can be configured using PC SONIC utility via Unidata
6603W FTDI programming cable OR using a USB to RS485 Converter Cable.
RS-485 Baud Rate Settings (0..4)
0 = 9600 Default
1 = 19200
2 = 38400
3 = 57600
4 = 115200
RS-485 Parity Settings (0..5)
0 = 8,N,1 Default
1 = 8,0,1
2 = 8,E,1
3 = 8,N,2
4 = 8,0,2
5 = 8,E,2
4.2.1 Reading the measured parameters via Modbus
Physical links requirement: RS485 - low power, 2V, three wire (A/B signals & ground), differential, half
duplex; at 9600bps (support up to 1000m cable, at 19200bps up to 500m cable, at 115Kkps up to
100m cable) and it supports PP, MD & MP protocols.
Protocol requirement: MODBUS (Modicon) - variable speed (9600 & 19200), MD over RS485. For PC
configuration, an USB to RS485 converter is required. The instrument has to be powered via 12V and
ground; A- and B+ signals will need to be connected as per wiring table in specifications section 2.0.
The instrument supports the Modbus RTU communication protocol; this is the format of choice for
serial communications such as RS485/RS232 as it is the most efficient.
The general message structure will consist of device address, function code, data payload and the
checksum.

Manual – Starflow QSD Model 6527B and 6537A
Unidata Manual - 6527B and 6537A Starflow QSD User Manual 17 01 2020.docx
Page 13
4.2.2 Master Format
Device Address
Function Code
Data Payload
CRC
Device address – 1 byte field ranging from 1 to 247. Broadcast address 0
Function code – 1 byte field with a value range 1-127 representing the standard or extended
function code
Data payload – 0-N bytes with response data from the device. Error response will be a 1 byte
value 1-255.
CRC – 2 bytes computed mathematically
4.2.3 Slave Response Format
Device Address
Function Code
Data Payload
CRC
Device Address – Echo of device address sent in master message to the device
Function code – Echo of function code sent in master message to the device
Data payload – 0-N bytes with response from device.
CRC-2 bytes with a value computed mathematically
4.2.4 Standard Message Format
Read Holding Registers is used to retrieve measurements
Message
Response
Address
1 byte
1-247
Address
1 byte
1-247
Function Code
1 byte
0x03
Function Code
1 byte
0x03
Data Address
2 bytes
0 to 0xFFFF
Byte Count
1 byte
Register Count
2 bytes
Data Payload
N bytes
CRC
2 bytes
CRC
2 bytes
*Byte count = 2*Register Count
Write Single Register is used to configure instrument settings
To set a single register in a device:
Message
Response
Address
1 byte
1-247
Address
1 byte
1-247
Function Code
1 byte
0x06
Function Code
1 byte
0x06
Data Address
2 bytes
0 to 0xFFFF
Byte Count
1 byte
0 to 0xFFFF
Register Count
2 bytes
0 to 0xFFFF
Data Payload
N bytes
0 to 0xFFFF
CRC
2 bytes
CRC
2 bytes

Manual – Starflow QSD Model 6527B and 6537A
Unidata Manual - 6527B and 6537A Starflow QSD User Manual 17 01 2020.docx
Page 14
RS485 Settings
Baud rates – Support Baud rates from 9600 to 115200
Data Bits – 8 data bits (7 data bits is not valid setting for Modbus RTU)
Parity Bits – Even, Odd and None
Stop Bits – 1 or 2
Default settings will be 9600,8,N,1.
4.2.5 Modbus Registers
The below list of parameters will all be located in the holding registers.
Sensor Common Registers: Registers Numbered 0001 to nnnn have Data Addresses 0000 to nnnn-1
Register
XXXX
Size
(Reg)
Mode/Access
Data
Type
Description
0001
1
Read only
ushort
Water Temperature * 0.1 DegC
0002
1
Read only
ushort
Battery Voltage * 0.01 Volts
0003
1
Read only
ushort
Water Depth (Ultrasonic) mm
0004
1
Read only
sshort
CW Water Velocity mm/s
0005
1
Read only
ushort
RSSI
0006
1
Read only
ushort
Signal Spread
0007
1
Read only
ushort
EC Conductivity Un-Corrected
0008
1
Read only
ushort
EC Hi-Resolution Un-Corrected
0009
1
Read only
ushort
EC Conductivity Temperature Corrected
0010
1
Read only
ushort
EC Hi-Resolution Temperature Corrected
0011
1
Read only
sshort
Accelerometer X +/- 90 deg
0012
1
Read only
sshort
Accelerometer Y +/- 90 deg
0013
1
Read only
sshort
Water Depth (Pressure) mm
0014
1
Read only
ushort
OWB Barometric Reference mm
0015
1
Read only
sshort
PW Velocity in +/- mm/s
0101
1
Read/Write
ushort
Auto Refresh rate in seconds
0102
1
Read/Write
ushort
Low Level Battery threshold *.001 Volts
0103
1
Read/Write
ushort
Minimum Operating Depth (MoD) mm
0104
1
Read/Write
ushort
Minimum RSSI
0105
1
Read/Write
ushort
Maximum Signal Spread
0106
1
Read/Write
ushort
Analogue Gain
0107
1
Read/Write
ushort
Depth Median Outlier Filter
0108
1
Read/Write
ushort
Depth Moving Average
0109
1
Read/Write
ushort
Velocity range (OSR)
0110
1
Read/Write
sshort
Pressure depth offset (mm)
0201
1
Read only
ushort
Unused LOGGER Start on Power-up (if Scheme loaded)
0202
1
Read only
ushort
Unused LOGGER ON/OFF
0203
1
Read only
ushort
Unused
0204
1
Read only
ushort
Unused
0205
1
Read/Write
ushort
P.Depth ON/OFF

Manual – Starflow QSD Model 6527B and 6537A
Unidata Manual - 6527B and 6537A Starflow QSD User Manual 17 01 2020.docx
Page 15
0206
1
Read/Write
ushort
P.Depth = zero if sensor fails
0207
1
Read/Write
ushort
Barometric reference ON/OFF
0208
1
Read/Write
ushort
Show -ve P.Depth
0209
1
Read/Write
ushort
Conductivity ON/OFF
0210
1
Read only
ushort
Unused
0211
1
Read only
ushort
Unused
0212
1
Read only
ushort
Unused
0213
1
Read/Write
ushort
PW Doppler ON/OFF
0214
1
Read only
ushort
Unused
0215
1
Read only
ushort
Unused
0216
1
Read only
ushort
Unused
0217
1
Read/Write
ushort
U.Depth Measurement ON/OFF
0218
1
Read/Write
ushort
U.Depth zero/hold - Below MoD
0219
1
Read/Write
ushort
Enable U.Depth Drive 1/Not used
0220
1
Read/Write
ushort
Enable U.Depth Drive 2/Not used
0221
1
Read/Write
ushort
Enable U.Depth Drive 3/Not used
0222
1
Read/Write
ushort
Enable U.Depth Drive 4/Not used
0223
1
Read/Write
ushort
U.Depth Median Filter ON/OFF
0224
1
Read only
ushort
Unused
0225
1
Read/Write
ushort
CW.Velocity ON/OFF
0226
1
Read/Write
ushort
CW.Velocity zero below RSSI
0227
1
Read/Write
ushort
Enable negative CW.Velocity
0228
1
Read/Write
ushort
Enable SOS Temp. Correction
0229
1
Read only
ushort
Unused
0230
1
Read only
ushort
Unused
0231
1
Read/Write
ushort
CW.Velocity use half power point
0232
1
Read/Write
ushort
CW.Velocity zero above Spread
Device Information and Communications Registers
Register
XXXX
Size
(Reg)
Mode/Access
Data
Type
Description
0301
0302
1
1
Read only
Read only
ushort
ushort
Serial Number (lower 16 bits)
Serial Number (upper 16 bits)
0303
1
Read only
ushort
Firmware Version
0304
1
Read only
ushort
Hardware Version
0305
1
Read only
ushort
SDI-12 Address in ASCII
0306
1
Read/Write
ushort
Modbus Device Address (1-247)
0307
1
Read/Write
ushort
Modbus Baud Rate ID
0308
1
Read/Write
ushort
Modbus Parity and Stop Bits
0401
1
Read/Write
sshort
** Modbus Request Measurement (0M!) sec
** Request Measurement Register
Writing this register acts like the SDI-12 command aM0!
Reading this register returns the # of seconds since the last Refresh (i.e. the age of Data Available).
Note that immediately after a Manual Refresh to register 401, a Read returns a negative number
indicating the # of seconds to wait for new data.
SDI-12 Mode and Modbus Mode Operation setting
In Modbus mode - Auto Refresh = nn secs (Modbus register 0101)
Write any value to Modbus register 401 will returns zero (0). Data Available
In SDI-12 Mode, Auto Refresh = 0 secs (Modbus register 0101 OR Set via PC Utility SONIC)Velocity Trace
To implement current TTL serial function over RS485 using same command and same data format.

Manual – Starflow QSD Model 6527B and 6537A
Unidata Manual - 6527B and 6537A Starflow QSD User Manual 17 01 2020.docx
Page 16
5.0 INSTALLATION
5.1 Site Considerations
The Doppler signal received, and the accuracy of the computed velocity, is related to the flow and
cross-section characteristics of the site. A suitable site has the following features:
Feature Description
Flows are laminar and the velocity measured
by the transducer can be related to the mean
velocity of the channel.
Velocity is measured from a limited path in front
of and above the acoustic sensors. This area
varies with the amount of suspended material in
the water and the channel characteristics. The
user has to determine the relationship between
the measured and mean velocity.
The channel cross section is stable.
The relationship between water level and the
cross-sectional area is used as part of the flow
computation.
Velocities are greater than 20 mm / second.
The transducer does not process velocities
slower than this. The maximum velocity is 5
metres / second. The transducer will measure
velocities in both directions.
Reflectors are present in the water.
Generally the more material in the water the
better. Starflow QSD generally works well in
clean natural streams but problems may be
encountered in extremely clean water.
No excessive aeration.
Bubbles are good scatterers and occasional
small bubbles will enhance the signal. However
the speed of sound can be affected if there are
excessive amounts of air entrapped in the flow.
The bed is stable and Starflow QSD will not
be buried by deposits.
Some coating and partial burying has little effect
on the measured velocity but it should be
avoided. Any burying or sediment covering the
depth transducer will affect the depth reading
results.
Starflow QSD Pointing Upstream or
Downstream?
Pointing the sensor end downstream will stop it
accumulating debris; however in some channels
the sensor body may disturb the velocity
distribution unacceptably. The velocity reading
will be positive when pointing upstream and
negative when pointing downstream. The
Starflow QSD may be configured to only read
positive velocities regardless of water flow
direction.
Starflow QSD Depth sensor not situated
parallel to the surface?
If Depth sensor is not parallel to the surface (~
±10 °) the readings could be compromised
Corrugated Pipes
In general the Starflow QSD is not suited to
installation in corrugated pipes.

Manual – Starflow QSD Model 6527B and 6537A
Unidata Manual - 6527B and 6537A Starflow QSD User Manual 17 01 2020.docx
Page 17
5.2 Instrument Mounting
A typical installation is in a pipe or culvert with diameters between 150mm and 2000 mm. The
Starflow QSD should be located near the downstream end of a straight and clean culvert, where non-
turbulent flow conditions are maximised. The mounting should ensure the unit sits right on the bottom
to avoid debris catching beneath it.
It is recommended that in open pipe situations that the instrument is situated 5 times the diameter
from the opening or discharge. This will allow instrument to measure the best possible laminar flow.
Keep the instrument away from pipe joints. Corrugated culverts are not suitable for Starflow QSD
instruments.
Diagram showing instrument 5 diameters in from pipe opening
In culverts the sensor can be mounted on a stainless steel band that is slipped inside the pipe and
expanded to lock it in position. In open channels special mounting brackets may be required.
The Model 6705 Expanding Band kit allows you to install a Starflow QSD instrument into a pipe.
Kit design is modular, allowing it to fit into any size pipe. The band is flexible enough to fit irregular
shapes, such as ovoid (egg shaped) sections.
All components are made from stainless steel and the band fittings are 100mm wide to fit the
standard Starflow QSD mount.
Although pipes come in standard diameters, their dimensions are not always accurate. This means
that an expanding band system must allow the installer to make adjustments on site. To achieve this,
the Model 6705 system is made so that general assembly can be done in the workshop, whilst
adjustments can be made in the field with hand tools. An expanding turn-buckle locks the band into
the pipe.
To determine what installation hardware is needed for a pipe installation the pipe diameter needs to
be known.
Pipe Diameter Clamp Bands Joiners
Up to 600mm 6705A 6705D -
600 - 1200mm 6705B 2 x 6705D 1
1200 - 1800mm 6705B 3 x 6705D 2

Manual – Starflow QSD Model 6527B and 6537A
Unidata Manual - 6527B and 6537A Starflow QSD User Manual 17 01 2020.docx
Page 18
Note: Pipes less than 150mm diameter are NOT RECOMMENDED for Starflow QSD installation due
to the instrument’s size. Do the following:
1. If the inside circumference of the pipe is ACCURATELY known, then cut the band assembly to
this length LESS 25mm for fitting clearance. Circumference (length) = Diameter x 3.14
2. Arrange the clamp, band(s) and joiner(s) so that Starflow QSD unit will be positioned at the
bottom (invert) of the pipe and an Expanding Clamp at the top (obvert) of pipe (see diagram).
3. Drill 4 x 5mm holes, 85mm spaced in the centre of the band to locate the instrument. Use the
Starflow QSD mounting clamp 6527M as a guide.
Use a small pilot drill bit (about 2mm) then finish with the 5mm bit. When drilling stainless steel
use a slow speed and high pressure. Avoid stopping as the material will work harden making it
more difficult to drill.
4. Use M3 x 12mm stainless steel machine screws and M3 nylock nuts (supplied) to connect all
parts. (If pop rivets and the pop rivet gun are available they can be used as the replacement for
the screws and nuts sets)
Note: the band length must be measured to include the Expanding Clamp (fully closed), bands
and joiners all together as shown.
5. Position and tighten Starflow QSD and band, the bolt the Starflow QSD mount to the band
6. Fold the band into a circle to easily fit inside the pipe and position into place inside the pipe
7. Slip the loose end of the band into the expanding clamp
8. Adjust clamp until band is tight inside pipe (use spanner if necessary)
This manual suits for next models
2
Table of contents
Other UniData Communication Systems Measuring Instrument manuals
Popular Measuring Instrument manuals by other brands

Rosemount
Rosemount TankRadar Pro Technical description
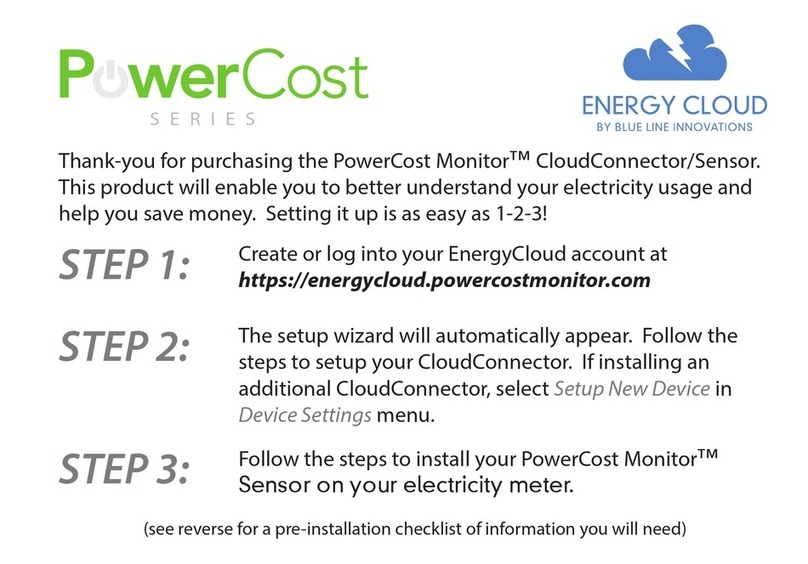
Energy cloud
Energy cloud PowerCost series Monitor Sensor installation manual
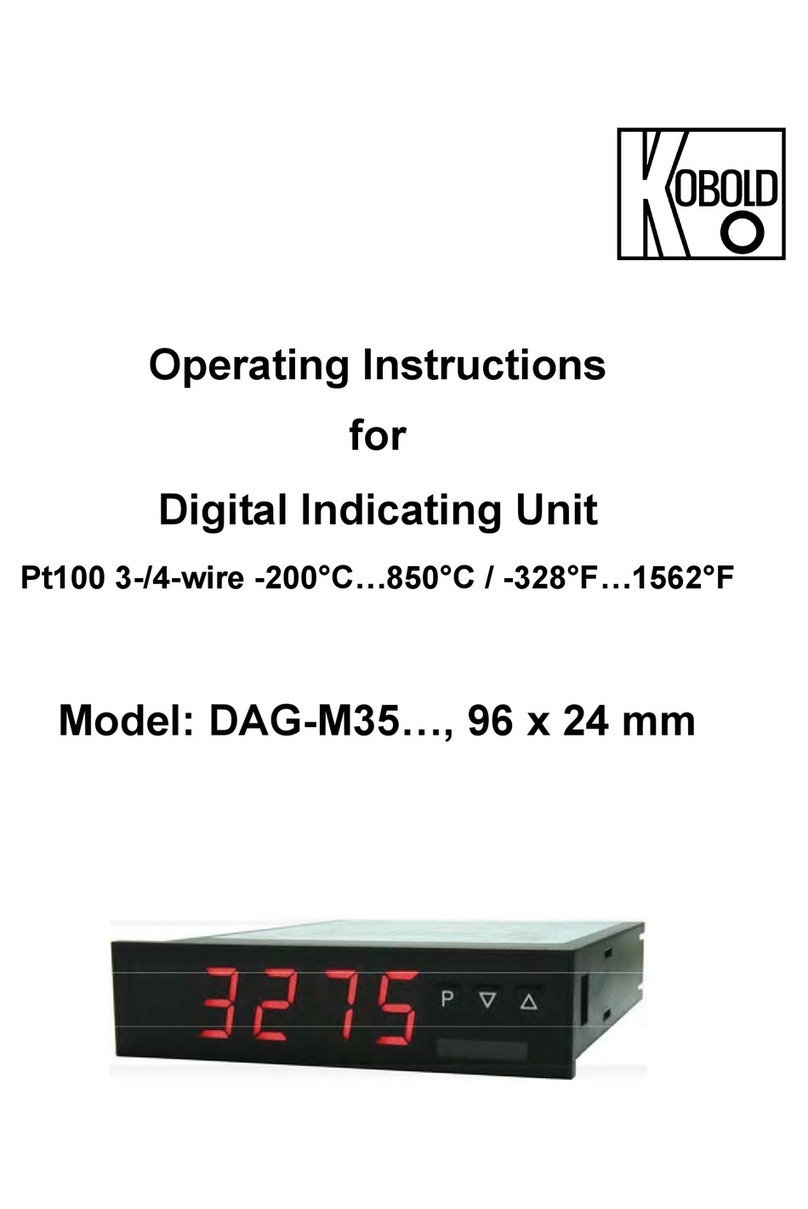
Kobold
Kobold DAG-M35 Series operating instructions

DAKOTA ULTRASONICS
DAKOTA ULTRASONICS MMX-6 Operation manual
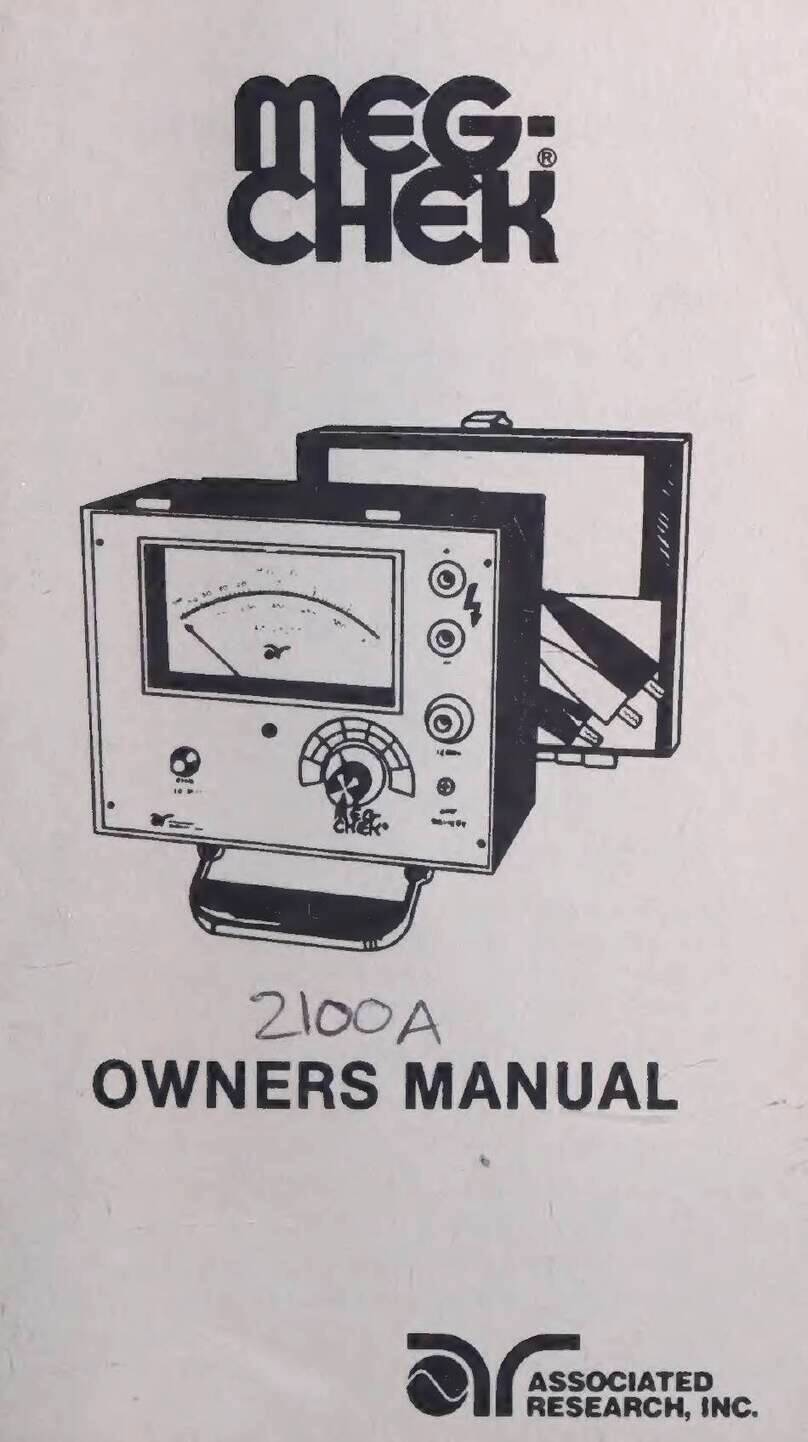
Associated Research
Associated Research MEG CHEK 2100 owner's manual
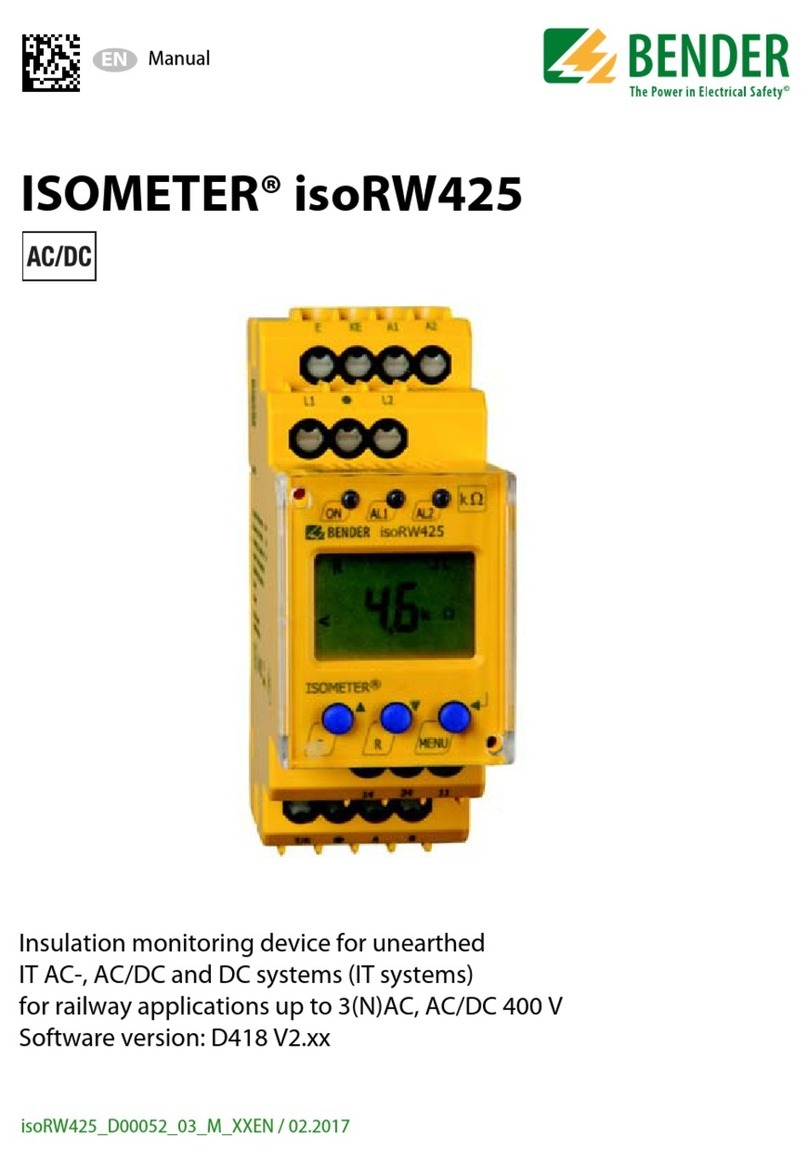
Bender
Bender ISOMETER isoRW425 manual