Vega vegaflex 83 User manual

Operating Instructions
TDR sensor for continuous level and
interface measurement of liquids
VEGAFLEX 83
Modbus and Levelmaster protocol
Converter version in second chamber
Polished rod probe
Document ID: 41843

2
Contents
VEGAFLEX 83 • Modbus and Levelmaster protocol
41843-EN-210914
Contents
1 About this document ............................................................................................................... 4
1.1 Function ........................................................................................................................... 4
1.2 Target group ..................................................................................................................... 4
1.3 Symbols used................................................................................................................... 4
2 For your safety ......................................................................................................................... 5
2.1 Authorised personnel ....................................................................................................... 5
2.2 Appropriate use................................................................................................................ 5
2.3 Warning about incorrect use............................................................................................. 5
2.4 General safety instructions............................................................................................... 5
2.5 EU conformity................................................................................................................... 5
2.6 NAMUR recommendations .............................................................................................. 6
2.7 Installation and operation in the USA and Canada ........................................................... 6
2.8 Environmental instructions ............................................................................................... 6
3 Product description ................................................................................................................. 7
3.1 Conguration.................................................................................................................... 7
3.2 Principle of operation........................................................................................................ 9
3.3 Packaging, transport and storage................................................................................... 11
3.4 Accessories.................................................................................................................... 11
4 Mounting................................................................................................................................. 13
4.1 General instructions ....................................................................................................... 13
4.2 Mounting instructions ..................................................................................................... 14
5 Connecting to power supply and bus system .................................................................... 19
5.1 Preparing the connection ............................................................................................... 19
5.2 Connecting..................................................................................................................... 20
5.3 Wiring plan ..................................................................................................................... 22
5.4 Double chamber housing with VEGADIS-Adapter.......................................................... 23
5.5 Switch-on phase............................................................................................................. 24
6 Set up the sensor with the display and adjustment module............................................. 25
6.1 Adjustment volume......................................................................................................... 25
6.2 Insert display and adjustment module............................................................................ 25
6.3 Adjustment system......................................................................................................... 26
6.4 Parameter adjustment - Quick setup .............................................................................. 27
6.5 Parameter adjustment - Extended adjustment................................................................ 27
6.6 Saving the parameterisation data................................................................................... 45
7 Setting up sensor and Modbus interface with PACTware.................................................. 46
7.1 Connect the PC.............................................................................................................. 46
7.2 Parameter adjustment with PACTware............................................................................ 47
7.3 Set instrument address .................................................................................................. 48
7.4 Set up with the quick setup............................................................................................. 49
7.5 Saving the parameterisation data................................................................................... 51
8 Diagnostics and servicing .................................................................................................... 52
8.1 Maintenance .................................................................................................................. 52
8.2 Diagnosis memory ......................................................................................................... 52
8.3 Status messages............................................................................................................ 53
8.4 Rectify faults................................................................................................................... 56

3
Contents
VEGAFLEX 83 • Modbus and Levelmaster protocol
41843-EN-210914
8.5 Exchanging the electronics module................................................................................ 59
8.6 Exchanging the rod ........................................................................................................ 60
8.7 Exchanging the seal....................................................................................................... 60
8.8 Software update ............................................................................................................. 62
8.9 How to proceed if a repair is necessary.......................................................................... 63
9 Dismount................................................................................................................................. 64
9.1 Dismounting steps.......................................................................................................... 64
9.2 Disposal ......................................................................................................................... 64
10 Supplement ............................................................................................................................ 65
10.1 Technical data ................................................................................................................ 65
10.2 Device communication Modbus ..................................................................................... 72
10.3 Modbus register ............................................................................................................. 72
10.4 Modbus RTU commands ............................................................................................... 75
10.5 Levelmaster commands ................................................................................................. 77
10.6 CongurationoftypicalModbushosts ........................................................................... 80
10.7 Dimensions .................................................................................................................... 81
10.8 Industrial property rights................................................................................................. 85
10.9 Trademark ...................................................................................................................... 85
Safety instructions for Ex areas
TakenoteoftheExspecicsafetyinstructionsforExapplications.
These instructions are attached as documents to each instrument
with Ex approval and are part of the operating instructions.
Editing status: 2021-08-19

4
1 About this document
VEGAFLEX 83 • Modbus and Levelmaster protocol
41843-EN-210914
1 About this document
1.1 Function
This instruction provides all the information you need for mounting,
connection and setup as well as important instructions for mainte-
nance,faultrectication,theexchangeofpartsandthesafetyofthe
user. Please read this information before putting the instrument into
operation and keep this manual accessible in the immediate vicinity
of the device.
1.2 Target group
This operating instructions manual is directed to trained personnel.
Thecontentsofthismanualmustbemadeavailabletothequalied
personnel and implemented.
1.3 Symbols used
Document ID
This symbol on the front page of this instruction refers to the Docu-
ment ID. By entering the Document ID on www.vega.com you will
reach the document download.
Information, note, tip: This symbol indicates helpful additional infor-
mation and tips for successful work.
Note: This symbol indicates notes to prevent failures, malfunctions,
damage to devices or plants.
Caution: Non-observance of the information marked with this symbol
may result in personal injury.
Warning: Non-observance of the information marked with this symbol
may result in serious or fatal personal injury.
Danger: Non-observance of the information marked with this symbol
results in serious or fatal personal injury.
Ex applications
This symbol indicates special instructions for Ex applications.
• List
The dot set in front indicates a list with no implied sequence.
1 Sequence of actions
Numbers set in front indicate successive steps in a procedure.
Battery disposal
This symbol indicates special information about the disposal of bat-
teries and accumulators.

5
2 For your safety
VEGAFLEX 83 • Modbus and Levelmaster protocol
41843-EN-210914
2 For your safety
2.1 Authorised personnel
All operations described in this documentation must be carried out
onlybytrained,qualiedpersonnelauthorisedbytheplantoperator.
During work on and with the device, the required personal protective
equipment must always be worn.
2.2 Appropriate use
VEGAFLEX 83 is a sensor for continuous level measurement.
Youcannddetailedinformationabouttheareaofapplicationin
chapter "Product description".
Operational reliability is ensured only if the instrument is properly
usedaccordingtothespecicationsintheoperatinginstructions
manual as well as possible supplementary instructions.
2.3 Warning about incorrect use
Inappropriate or incorrect use of this product can give rise to applica-
tion-specichazards,e.g.vesseloverllthroughincorrectmounting
or adjustment. Damage to property and persons or environmental
contamination can result. Also, the protective characteristics of the
instrument can be impaired.
2.4 General safety instructions
This is a state-of-the-art instrument complying with all prevailing
regulations and directives. The instrument must only be operated in a
technicallyawlessandreliablecondition.Theoperatorisresponsi-
ble for the trouble-free operation of the instrument. When measuring
aggressive or corrosive media that can cause a dangerous situation
if the instrument malfunctions, the operator has to implement suitable
measures to make sure the instrument is functioning properly.
The safety instructions in this operating instructions manual, the na-
tional installation standards as well as the valid safety regulations and
accident prevention rules must be observed by the user.
For safety and warranty reasons, any invasive work on the device
beyond that described in the operating instructions manual may be
carried out only by personnel authorised by the manufacturer. Arbi-
traryconversionsormodicationsareexplicitlyforbidden.Forsafety
reasons,onlytheaccessoryspeciedbythemanufacturermustbe
used.
To avoid any danger, the safety approval markings and safety tips on
the device must also be observed.
2.5 EU conformity
ThedevicefullsthelegalrequirementsoftheapplicableEUdirec-
tives.ByaxingtheCEmarking,weconrmtheconformityofthe
instrument with these directives.
The EU conformity declaration can be found on our homepage.

6
2 For your safety
VEGAFLEX 83 • Modbus and Levelmaster protocol
41843-EN-210914
Electromagnetic compatibility
Instruments in four-wire or Ex-d-ia version are designed for use in an
industrial environment. Nevertheless, electromagnetic interference
from electrical conductors and radiated emissions must be taken into
account, as is usual with class A instruments according to EN 61326-
1.Iftheinstrumentisusedinadierentenvironment,theelectromag-
netic compatibility to other instruments must be ensured by suitable
measures.
2.6 NAMUR recommendations
NAMUR is the automation technology user association in the process
industry in Germany. The published NAMUR recommendations are
acceptedasthestandardineldinstrumentation.
ThedevicefullstherequirementsofthefollowingNAMURrecom-
mendations:
• NE 21 – Electromagnetic compatibility of equipment
• NE53–Compatibilityofelddevicesanddisplay/adjustment
components
• NE107–Self-monitoringanddiagnosisofelddevices
For further information see www.namur.de.
2.7 Installation and operation in the USA and
Canada
This information is only valid for USA and Canada. Hence the follow-
ing text is only available in the English language.
Installations in the US shall comply with the relevant requirements of
theNationalElectricalCode(ANSI/NFPA70).
Installations in Canada shall comply with the relevant requirements of
the Canadian Electrical Code.
2.8 Environmental instructions
Protection of the environment is one of our most important duties.
That is why we have introduced an environment management system
with the goal of continuously improving company environmental pro-
tection.Theenvironmentmanagementsystemiscertiedaccording
to DIN EN ISO 14001.
Pleasehelpusfullthisobligationbyobservingtheenvironmental
instructions in this manual:
• Chapter "Packaging, transport and storage"
• Chapter "Disposal"

7
3 Product description
VEGAFLEX 83 • Modbus and Levelmaster protocol
41843-EN-210914
3 Product description
3.1 Conguration
The scope of delivery encompasses:
• Sensor VEGAFLEX 83
• Optional accessory
• Optionally integrated Bluetooth module
The further scope of delivery encompasses:
• Documentation
– Quick setup guide VEGAFLEX 83
– Instructions for optional instrument features
– Ex-specic"Safety instructions"(withExversions)
– Ifnecessary,furthercerticates
Information:
Optional instrument features are also described in this operating
instructions manual. The respective scope of delivery results from the
orderspecication.
This operating instructions manual applies to the following instrument
versions:
• Hardware from 1.0.0
• Software from 1.3.0
• OnlyforinstrumentversionswithoutSILqualication
Thetypelabelcontainsthemostimportantdataforidenticationand
use of the instrument:
Scope of delivery
Scope of this operating
instructions
Type label

8
3 Product description
VEGAFLEX 83 • Modbus and Levelmaster protocol
41843-EN-210914
2
1
12
13
14
15
11
10
5
3
6
4
7
8
9
Fig. 1: Layout of the type label (example)
1 Instrument type
2 Product code
3 Approvals
4 Power supply and signal output, electronics
5 Protection rating
6 Probe length (measurement accuracy optional)
7 Process and ambient temperature, process pressure
8 Material wetted parts
9 Order number
10 Serial number of the instrument
11 Symbol of the device protection class
12 ID numbers, instrument documentation
13 Reminder to observe the instrument documentation
14 NotiedauthorityforCEmarking
15 Approval directives
The type label contains the serial number of the instrument. With it
youcanndthefollowinginstrumentdataonourhomepage:
• Productcode(HTML)
• Deliverydate(HTML)
• Order-specicinstrumentfeatures(HTML)
• Operating instructions and quick setup guide at the time of ship-
ment(PDF)
• Order-specicsensordataforanelectronicsexchange(XML)
• Testcerticate(PDF)-optional
Move to "www.vega.com"andenterinthesearcheldtheserial
number of your instrument.
Alternatively, you can access the data via your smartphone:
• Download the VEGA Tools app from the "Apple App Store" or the
"Google Play Store"
• Scan the QR-code on the type label of the device or
• Enter the serial number manually in the app
Theinstrumentcontainstwodierentelectronicsinitshousingcham-
bers:
Serial number - Instru-
ment search
Electronics design

9
3 Product description
VEGAFLEX 83 • Modbus and Levelmaster protocol
41843-EN-210914
• The Modbus electronics for power supply and communication with
the Modbus-RTU
• The sensor electronics for the actual measuring tasks
2
1
Fig. 2: Position of Modbus and sensor electronics
1 Modbus electronics
2 Sensor electronics
3.2 Principle of operation
The VEGAFLEX 83 is a level sensor with polished rod probe for
continuous level or interface measurement, particularly suitable for
applications in the food processing and pharmaceutical industry.
Optionally an autoclaved version with separable housing is available.
High frequency microwave pulses are guided along a steel cable or
a rod. Upon reaching the medium surface, the microwave pulses are
reected.Therunningtimeisevaluatedbytheinstrumentandoutput
as level.
d
h
1
Fig. 3: Level measurement
1 Sensorreferenceplane(sealsurfaceoftheprocesstting)
d Distance to the level
h Height - Level
High frequency microwave impulses are guided along a steel cable or
rod. Upon reaching the medium surface, a part of the microwave im-
pulsesisreected.Theotherpartpassesthroughtheupperproduct
Application area
Functional principle -
level measurement
Functional principle - in-
terface measurement

10
3 Product description
VEGAFLEX 83 • Modbus and Levelmaster protocol
41843-EN-210914
andisreectedbytheinterface.Therunningtimestothetwoproduct
layers are processed by the instrument.
TS
d1
h1
h2
d2
1
L2
L1
L3
Fig. 4: Interface measurement
1 Sensorreferenceplane(sealsurfaceoftheprocesstting)
d1 Distance to the interface
d2 Distance to the level
TS Thickness of the upper medium (d1 - d2)
h1 Height - Interface
h2 Height - Level
L1 Lower medium
L2 Upper medium
L3 Gas phase
Upper medium (L2)
• The upper medium must not be conductive
• The dielectric constant of the upper medium or the actual distance
totheinterfacemustbeknown(inputrequired).Min.dielectriccon-
stant:1.6.Youcanndalistofdielectricconstantsonourhome
page: www.vega.com.
• The composition of the upper medium must be stable, no varying
products or mixtures
• Theuppermediummustbehomogeneous,nostratications
within the medium
• Min.thicknessoftheuppermedium50mm(1.97in)
• Clear separation from the lower medium, emulsion phase or detri-
tuslayermax.50mm(1.97in)
• If possible, no foam on the surface
Lower medium (L1)
• The dielectric constant must be 10 higher than the dielectric
constant of the upper medium, preferably electrically conductive.
Example: upper medium dielectric constant 2, lower medium at
least dielectric constant 12.
Gas phase (L3)
• Air or gas mixture
Prerequisites for inter-
face measurement

11
3 Product description
VEGAFLEX 83 • Modbus and Levelmaster protocol
41843-EN-210914
• Gas phase - dependent on the application, gas phase does not
alwaysexist(d2=0)
The instrument is always preset to the application "Level measure-
ment".
For the interface measurement, you can select the requested output
signal with the setup.
3.3 Packaging, transport and storage
Your instrument was protected by packaging during transport. Its
capacity to handle normal loads during transport is assured by a test
based on ISO 4180.
The packaging consists of environment-friendly, recyclable card-
board. For special versions, PE foam or PE foil is also used. Dispose
of the packaging material via specialised recycling companies.
Transport must be carried out in due consideration of the notes on the
transport packaging. Nonobservance of these instructions can cause
damage to the device.
The delivery must be checked for completeness and possible transit
damage immediately at receipt. Ascertained transit damage or con-
cealed defects must be appropriately dealt with.
Up to the time of installation, the packages must be left closed and
stored according to the orientation and storage markings on the
outside.
Unless otherwise indicated, the packages must be stored only under
the following conditions:
• Not in the open
• Dry and dust free
• Not exposed to corrosive media
• Protected against solar radiation
• Avoiding mechanical shock and vibration
• Storage and transport temperature see chapter "Supplement -
Technical data - Ambient conditions"
• Relative humidity 20 … 85 %
Withinstrumentweightsofmorethan18kg(39.68lbs)suitableand
approved equipment must be used for lifting and carrying.
3.4 Accessories
The instructions for the listed accessories can be found in the down-
load area on our homepage.
The display and adjustment module is used for measured value indi-
cation, adjustment and diagnosis.
TheintegratedBluetoothmodule(optional)enableswirelessadjust-
ment via standard adjustment devices.
Output signal
Packaging
Transport
Transport inspection
Storage
Storage and transport
temperature
Lifting and carrying
PLICSCOM

12
3 Product description
VEGAFLEX 83 • Modbus and Levelmaster protocol
41843-EN-210914
The interface adapter VEGACONNECT enables the connection of
communication-capable instruments to the USB interface of a PC.
The VEGADIS 81 is an external display and adjustment unit for VEGA
plics®sensors.
The VEGADIS adapter is an accessory part for sensors with double
chamber housings. It enables the connection of VEGADIS 81 to the
sensor housing via an M12 x 1 plug.
The protective cover protects the sensor housing against soiling and
intense heat from solar radiation.
Screwedangesareavailableindierentversionsaccordingtothe
following standards: DIN 2501, EN 1092-1, BS 10, ASME B 16.5,
JIS B 2210-1984, GOST 12821-80.
The display and adjustment module can be optionally replaced by a
display and adjustment module with heating function.
You can use this display and adjustment module in an ambient tem-
perature range of -40 … +70 °C.
If the standard sensor housing is too big or in case of strong vibra-
tions, an external housing can be used.
Then the sensor housing is made of stainless steel. The electronics is
located in the external housing which can be mounted in a distance of
upto10m(32.8ft)tothesensorbyusingaconnectioncable.
If you are using an instrument with rod version, you can extend the
rodprobeindividuallywithrodextensionsofdierentlengthsorseg-
mentitfordicultinstallationsituations.
Allextensionsusedmustnotexceedatotallengthof4m(13.12ft).
The extensions are available in the following lengths:
Rod ø 8 mm (0.315 in)
• Basicsegment:450mm(17.72in)
• Rodsegments:450…480mm(17.72…18.9in)
• Endsegment:26…480mm(1.02…18.9in)
If you mount the VEGAFLEX 83 in a bypass tube or standpipe, you
have to avoid contact to the bypass tube by using a spacer at the
probe end.
VEGACONNECT
VEGADIS 81
VEGADIS adapter
Protective cover
Flanges
Display and adjustment
module with heating
External housing
Rod components
Centering

13
4 Mounting
VEGAFLEX 83 • Modbus and Levelmaster protocol
41843-EN-210914
4 Mounting
4.1 General instructions
Protect your instrument against moisture ingress through the following
measures:
• Use a suitable connection cable (see chapter "Connectingto
power supply")
• Tighten the cable gland or plug connector
• Lead the connection cable downward in front of the cable entry or
plug connector
This applies mainly to outdoor installations, in areas where high
humidityisexpected(e.g.throughcleaningprocesses)andoncooled
or heated vessels.
Note:
Make sure that during installation or maintenance no moisture or dirt
can get inside the instrument.
To maintain the housing protection, make sure that the housing lid is
closed during operation and locked, if necessary.
Metric threads
In the case of instrument housings with metric thread, the cable
glands are screwed in at the factory. They are sealed with plastic
plugs as transport protection.
You have to remove these plugs before electrical connection.
NPT thread
In the case of instrument housings with self-sealing NPT threads, it is
not possible to have the cable entries screwed in at the factory. The
free openings for the cable glands are therefore covered with red dust
protection caps as transport protection.The dust protection caps do
notprovidesucientprotectionagainstmoisture.
Prior to setup you have to replace these protective caps with ap-
proved cable glands or close the openings with suitable blind plugs.
Note:
For safety reasons, the instrument must only be operated within the
permissibleprocessconditions.Youcannddetailedinformationon
the process conditions in chapter "Technical data" of the operating
instructions or on the type label.
Hence make sure before mounting that all parts of the instrument ex-
posed to the process are suitable for the existing process conditions.
These are mainly:
• Active measuring component
• Processtting
• Process seal
Process conditions in particular are:
• Process pressure
• Process temperature
Protection against mois-
ture
Cable glands
Process conditions

14
4 Mounting
VEGAFLEX 83 • Modbus and Levelmaster protocol
41843-EN-210914
• Chemical properties of the medium
• Abrasionandmechanicalinuences
4.2 Mounting instructions
Mount the device in such a way that the distance to vessel installa-
tionsortothevesselwallisatleast300mm(12in).Innon-metallic
vessels, the distance to the vessel wall should be at least 500 mm
(19.7in).
During operation, the probe must not touch any installations or the
vessel wall. If necessary, fasten the probe end.
In vessels with conical bottom it can be advantageous to mount the
device in the center of the vessel, as measurement is then possible
nearly down to the lowest point of the bottom. Keep in mind that
measurement all the way down to the tip of the probe may not be pos-
sible.Theexactvalueofthemin.distance(lowerblockingdistance)is
stated in chapter "Technical data" of the operating instructions.
Fig. 5: Vessel with conical bottom
Plastic vessel/Glass vessel
The guided microwave principle requires a metallic surface on the
processtting.Therefore,inplasticvessels,etc.,useaninstru-
mentversionwithange(fromDN50)orplaceametalsheet
(ø>200mm/8in)beneaththeprocessttingwhenscrewingitin.
Makesurethattheplatehasdirectcontactwiththeprocesstting.
When mounting rod or cable probes in vessels without metal walls,
e.g.inplasticvessels,themeasuredvaluecanbeinuencedby
strongelectromagneticelds(emittedinterferenceaccordingto
EN61326:classA).Inthiscase,useaprobewithcoaxialversion.
Installation position
Type of vessel

15
4 Mounting
VEGAFLEX 83 • Modbus and Levelmaster protocol
41843-EN-210914
1 2
Fig. 6: Mounting in non-metallic vessel
1 Flange
2 Metal sheet
Ifpossible,avoidnozzles.Mountthesensorushwiththevesseltop.
Ifthisisnotpossible,useshortnozzleswithsmalldiameter.
Highernozzlesornozzleswithabiggerdiametercangenerallybe
used. They can, however, increase the upper blocking distance.
Check if this is relevant for your measurement.
In such cases, always carry out a false signal suppression after
mounting.Youcanndfurtherinformationunder"Setup procedure".
h
d
dh
DN25 ...DN150 ≤ 150 mm (5.91")
≤ 100 mm (3.94")> DN150 ...DN200
Fig. 7: Mounting socket
Whenweldingthenozzle,makesurethatthenozzleisushwiththe
vessel top.
Nozzle

16
4 Mounting
VEGAFLEX 83 • Modbus and Levelmaster protocol
41843-EN-210914
1 2
Fig.8:Nozzlemustbeinstalledush
1 Unfavourable mounting
2 Nozzleush-optimummounting
Before beginning the welding work, remove the electronics module
from the sensor. By doing this, you avoid damage to the electronics
through inductive coupling.
Donotmounttheinstrumentsinorabovethellingstream.Makesure
thatyoudetectthemediumsurface,nottheinowingproduct.
Fig.9:Mountingofthesensorwithinowingmedium
The reference plane for the measuring range of the sensors is the
sealingsurfaceofthethreadorange.
Keep in mind that a min. distance must be maintained below the
reference plane and possibly also at the end of the probe - measure-
mentintheseareasisnotpossible(blockingdistance).Thelength
of the cable can be used all the way to the end only when measuring
Welding work
Inowingmedium
Measuring range

17
4 Mounting
VEGAFLEX 83 • Modbus and Levelmaster protocol
41843-EN-210914
conductiveproducts.Theseblockingdistancesfordierentmediums
are listed in chapter "Technical data". Keep in mind for the adjustment
that the default setting for the measuring range refers to water.
Theprocessttingmustbesealedifthereisgaugeorlowpressure
in the vessel. Before use, check if the sealing material is resistant
against the measured product and the process temperature.
Themax.permissiblepressureisspeciedinchapter"Technical
data" or on the type label of the sensor.
Incaseofdicultinstallationconditions,theprobecanalsobe
mounted laterally. For this, adapt the rod with rod extensions or
angled segments.
To compensate for the resulting changes in signal runtime, let the
instrument determine the probe length automatically.
The determined probe length can deviate from the actual probe
length when using curved or angled segments.
If internal installations such as struts, ladders, etc. are present on the
vessel wall, the measuring probe should be mounted at least 300 mm
(11.81in)awayfromthevesselwall.
Youcanndfurtherinformationinthesupplementaryinstructionsof
the rod extension.
Incaseofdicultinstallationconditions,forexampleinanozzle,the
probe can be suitably adapted with a rod extension.
To compensate for the resulting changes in signal runtime, let the
instrument determine the probe length automatically.
Youcanndfurtherinformationinthesupplementaryinstructionsof
the rod and cable components.
Foruseinanautoclave,e.g.forsterilization,theVEGAFLEX83is
available as autoclaved version.
Henceyoucanseparatethehousingfromtheprocesstting.
Under very harsh ambient conditions, the autoclavable version can be
optionally also combined with an external housing.
Open the slotted nut with a hook wrench and remove the housing in
an upward direction.
Thesideoftheprocessttingmustbecoveredwithalidafterthe
housing is removed. Screw the enclosed lid with slotted nut onto the
instrumentsideoftheprocessttingandtightenthenutwithatorque
of 20 Nm.
Make sure that no liquid or contamination penetrates into the housing
or the process side.
Afterautoclaving,screwthelidoagainandplacethehousingverti-
callyonthesideoftheprocesstting.Tightentheslottednutwitha
torque of 20 Nm.
Pressure
Lateral installation
Rod extension
Autoclaved version

18
4 Mounting
VEGAFLEX 83 • Modbus and Levelmaster protocol
41843-EN-210914
112 mm
(4.84")
DIN DN25, DN32, DN40 / 1", 1½"
L
ø 54 mm
(2.13")
ø w
183 mm
(7.20")
65,3 mm
(2.57")
ø w
ø 50,5
DIN DN50 / 2" ø 64
ø 91DIN DN65 / 3"
21
3
Fig. 10: Autoclaved version
1 Groove nut
2 Processtting
3 Coverwithgroovenut

19
5 Connecting to power supply and bus system
VEGAFLEX 83 • Modbus and Levelmaster protocol
41843-EN-210914
5 Connecting to power supply and bus
system
5.1 Preparing the connection
Always keep in mind the following safety instructions:
• Carryoutelectricalconnectionbytrained,qualiedpersonnel
authorised by the plant operator
• If overvoltage surges are expected, overvoltage arresters should
be installed
Warning:
Onlyconnectordisconnectinde-energizedstate.
The operating voltage and the digital bus signal are routed via sepa-
rate two-wire connection cables.
Thedataforpowersupplyarespeciedinchapter"Technical data".
Note:
Powertheinstrumentviaanenergy-limitedcircuit(powermax.100W)
acc. to IEC 61010-1, e.g.
• Class2powersupplyunit(acc.toUL1310)
• SELVpowersupplyunit(safetyextra-lowvoltage)withsuitable
internal or external limitation of the output current
The instrument is connected with standard two-wire, twisted cable
suitable for RS 485. If electromagnetic interference is expected which
is above the test values of EN 61326 for industrial areas, shielded
cable should be used.
Use cable with round cross section for instruments with housing and
cable gland. Use a cable gland suitable for the cable diameter to
ensurethesealeectofthecablegland(IPprotectionrating).
Make sure that the entire installation is carried out according to the
Fieldbusspecication.Inparticular,makesurethatthebusistermi-
nated with suitable terminating resistors.
Metric threads
In the case of instrument housings with metric thread, the cable
glands are screwed in at the factory. They are sealed with plastic
plugs as transport protection.
Note:
You have to remove these plugs before electrical connection.
NPT thread
In the case of instrument housings with self-sealing NPT threads, it is
not possible to have the cable entries screwed in at the factory. The
free openings for the cable glands are therefore covered with red dust
protection caps as transport protection.
Safety instructions
Voltage supply
Connection cable
Cable glands

20
5 Connecting to power supply and bus system
VEGAFLEX 83 • Modbus and Levelmaster protocol
41843-EN-210914
Note:
Prior to setup you have to replace these protective caps with ap-
proved cable glands or close the openings with suitable blind plugs.
On plastic housings, the NPT cable gland or the Conduit steel tube
must be screwed into the threaded insert without grease.
Max. torque for all housings, see chapter "Technical data".
Make sure that the cable screen and grounding are carried out ac-
cordingtoFieldbusspecication.Werecommendtoconnectthe
cable screening to ground potential on both ends.
In systems with potential equalisation, connect the cable screening
directly to ground potential at the power supply unit and the sensor.
The cable screening in the sensor must be connected directly to the
internal ground terminal. The ground terminal outside on the housing
mustbeconnectedtothepotentialequalisation(lowimpedance).
5.2 Connecting
The voltage supply and signal output are connected via the spring-
loaded terminals in the housing.
Connection to the display and adjustment module or to the interface
adapter is carried out via contact pins in the housing.
Information:
The terminal block is pluggable and can be removed from the
electronics.To do this, lift the terminal block with a small screwdriver
and pull it out. When reinserting the terminal block, you should hear it
snap in.
Proceed as follows:
1. Unscrew the housing lid
2. Loosen compression nut of the cable gland and remove blind
plug
3. Removeapprox.10cm(4in)ofthecablemantle(signaloutput),
stripapprox.1cm(0.4in)insulationfromtheendsoftheindi-
vidual wires
4. Insert the cable into the sensor through the cable entry
Cable screening and
grounding
Connection technology
Connection procedure
Other manuals for vegaflex 83
11
Table of contents
Other Vega Measuring Instrument manuals

Vega
Vega VEGAPULS 62 User manual

Vega
Vega VEGACAL 62 User manual

Vega
Vega VEGAFLEX 81 User manual
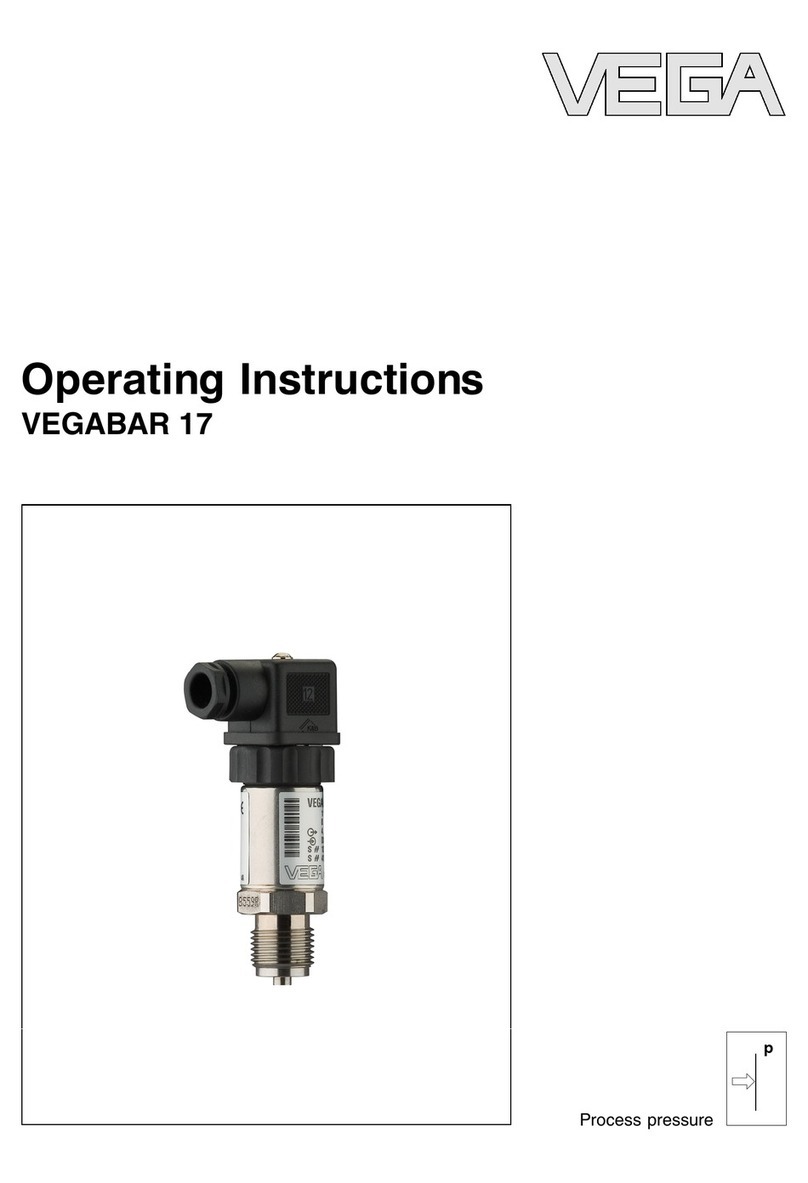
Vega
Vega VEGABAR 17 User manual

Vega
Vega VEGAPULS WL 61 User manual

Vega
Vega VEGAPULS 66 User manual

Vega
Vega VEGAPULS 63 User manual

Vega
Vega VEGAPULS 65 User manual
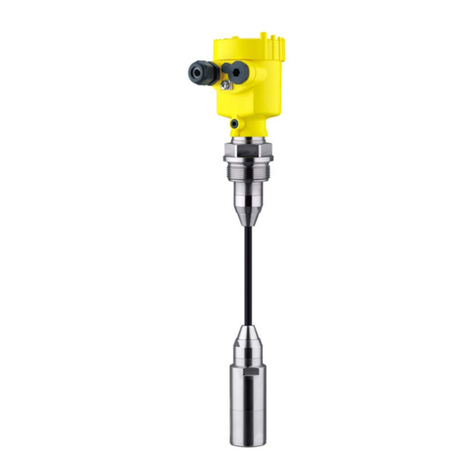
Vega
Vega VEGABAR 86 User manual

Vega
Vega VEGACAP 63 User manual
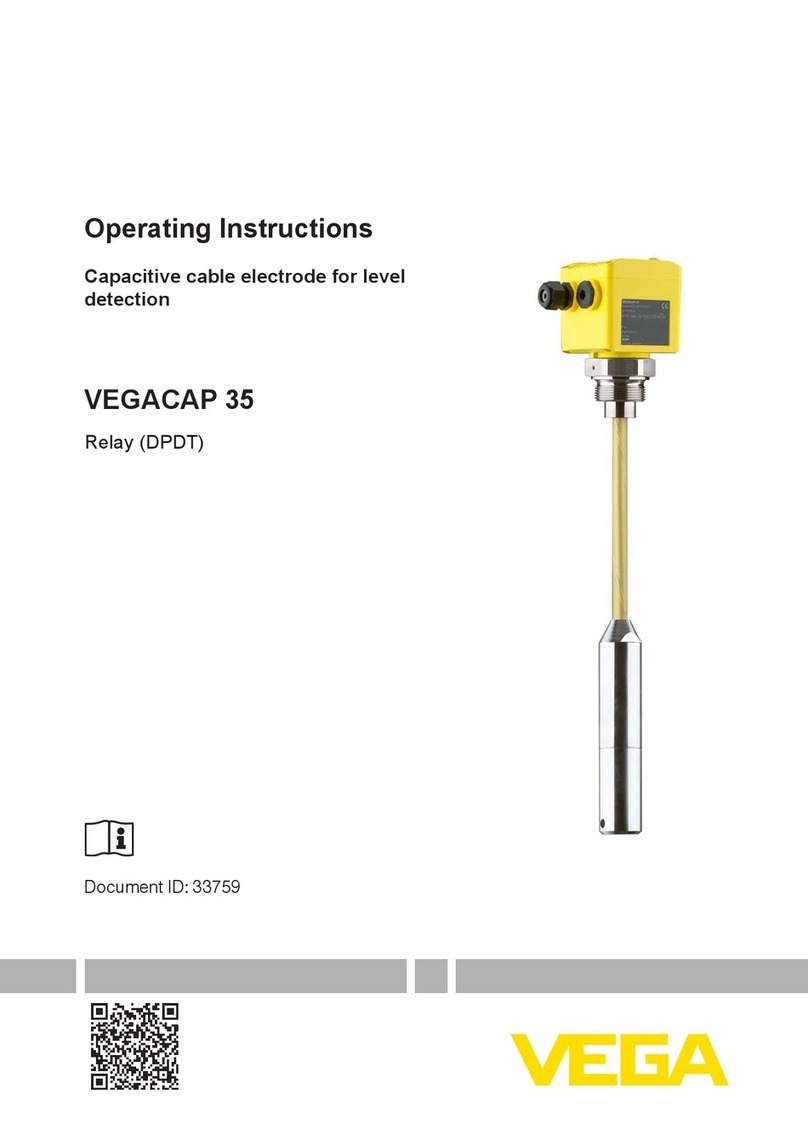
Vega
Vega VEGACAP 35 User manual
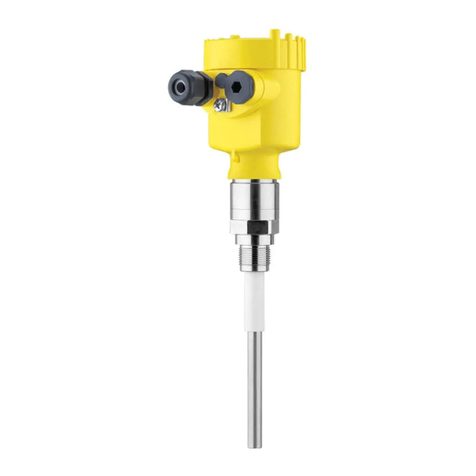
Vega
Vega vegacap 62 User manual
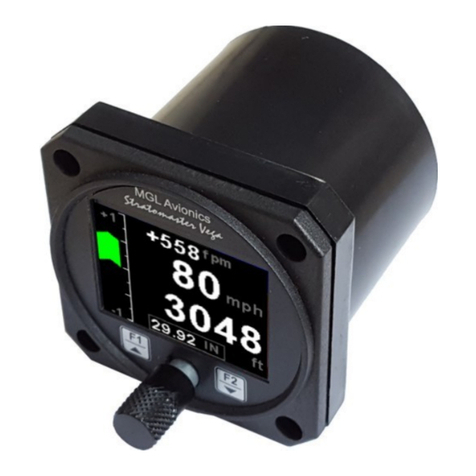
Vega
Vega ASV-1 User manual

Vega
Vega VEGASON 61 User manual
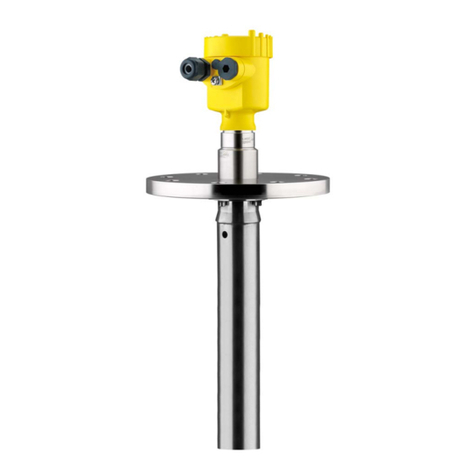
Vega
Vega VEGAPULS 66 User manual

Vega
Vega VEGAPULS 61 User manual

Vega
Vega VEGAPULS 67 User manual
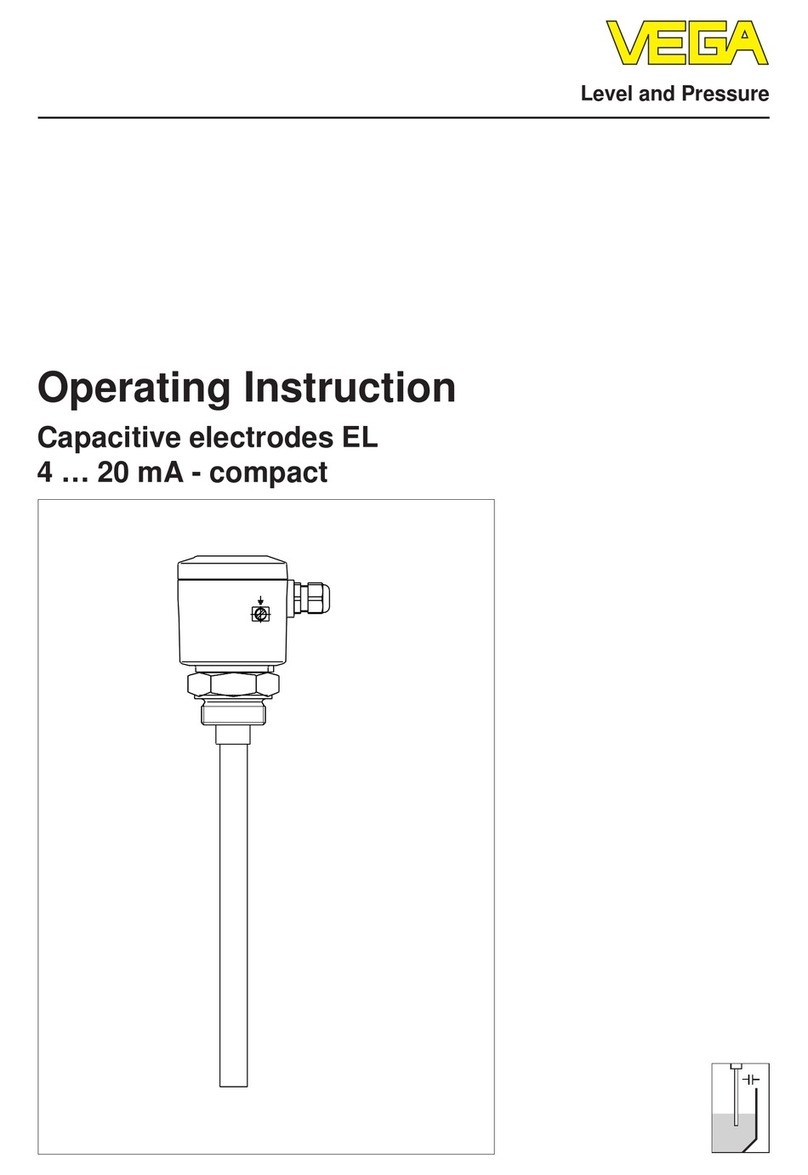
Vega
Vega EL 11 User manual
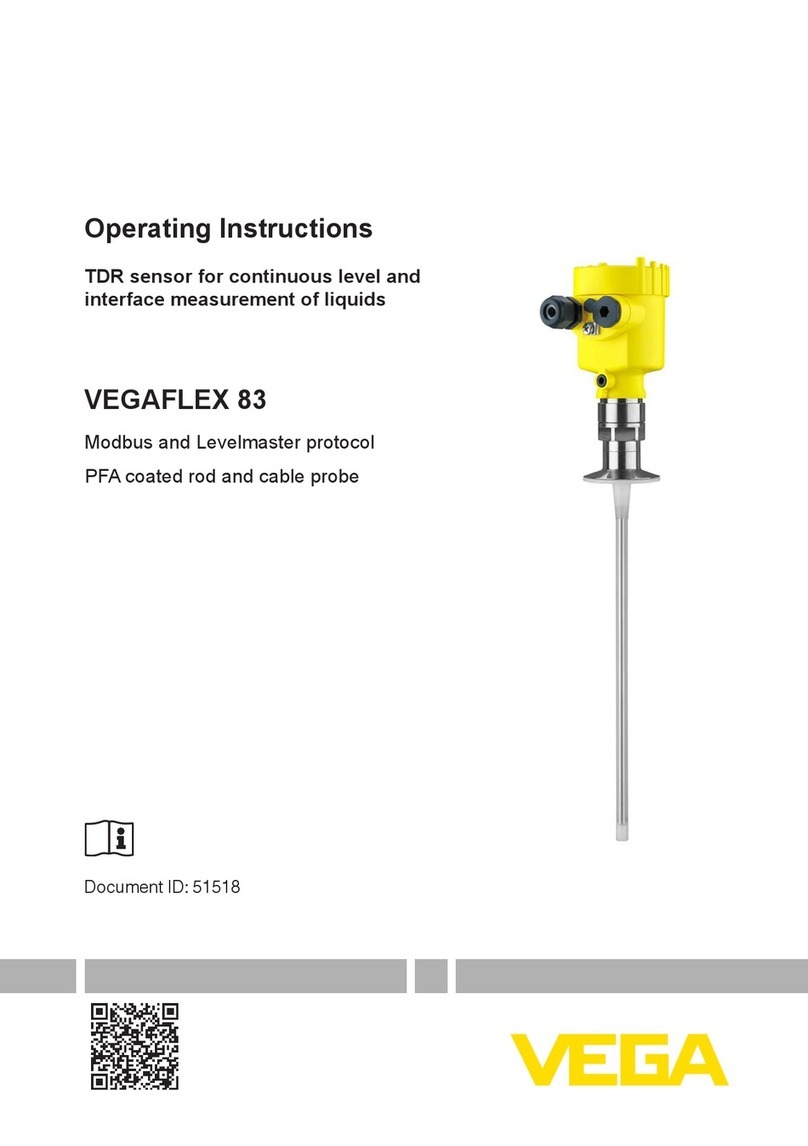
Vega
Vega vegaflex 83 User manual

Vega
Vega VEGASWING 61 User manual