Vescent Photonics D2-125 User manual

2021/04/17 23:32 1/18 Reconfigurable Laser Servo
Product Manuals - https://www.vescent.com/manuals/
Fig. 1: D2-125
Reconfigurable Laser
Servo
Model No. D2-125
Document Revision: 4.1
Document Last Updated on 2021/03/02 17:06
Please read Limited Warranty and General Warnings
and Cautions prior to operating the D2-125 (web page)
Reconfigurable Servo.
Quick start for D2-125.
D2-125 web page.
Description
The D2-125 Reconfigurable Laser Servo contains a tunable PI2D loop filter for tight locking to an error
signal. The error signal is either an amplified version of the Error Input signal (side-lock mode) or an
amplified version of a demodulated Error Input (optional peak-lock mode). In both modes, a DC Offset
is summed to the error signal, allowing the user to select the zero-crossing and thus the lock point.
The error signal can also be inverted via a front-panel switch. Additionally, the Laser Servo has an
internal ramp generator for sweeping the output and computer control functionality to make and
break lock and directly control the output voltage.
The main component in the Reconfigurable Laser Servo is the PI2D loop filter, which means that the
feedback has standard proportional (P), integral (I), and differential (D) feedback with a second
integral feedback (I) providing the PI2D transfer function. The double integration is used to boost gain
at low frequencies. With integrator frequencies tunable from 2 MHz down to 10 Hz, the Laser Servo
can be optimized to a wide variety of plants and servo loops. With the Peak Lock option, the Laser
Servo can demodulate a provided 4 MHz dither signal to enable slope-detection for locking to signal
minima and maxima. The Laser Servo can be used to lock a laser's current or PZT to an
interferometer or an optical transition. With peak-lock, the Laser Servo can perform Pound-Drever-Hall
(PDH) locking to an optical cavity. The Reconfigurable Laser Servo uses basic voltage inputs and
outputs. As a result, it can be used with lasers or with any voltage-tunable device with an error signal.
The Laser Servo can be unlocked by a computer (via TTL control) to jump the output voltage to a set
voltage difference from the current lock point, or to a specific voltage. This feature can be used to
jump the laser frequency a known distance away and then relock to the original or a new lock point
frequency. This feature can be used for auto-locking or relocking routines.
The Laser Servo has an internal sweep generator to sweep the laser frequency prior to lock.

Last update: 2021/03/02 17:06 d2:laser_servo https://www.vescent.com/manuals/doku.php?id=d2:laser_servo
https://www.vescent.com/manuals/ Printed on 2021/04/17 23:32
Purchase Includes
D2-125 Laser Servo
VPN00465 BNC cable (1ft)1)
VPN00457 Trimpot tweaker (large)
VPN00458 Trimpot tweaker (small)
VPN00456 DB9 Power Cable (1ft)
Options
The D2-125 can be purchased with two options:
-PL: Peak Lock option
-IP-X: Internal Power (where X=100 VAC, 120 VAC, or 230 VAC)
The Peak Lock option generates a 4 MHz dither signal that can be used to modulate the laser current.
The amplitude and phase of this modulation can be adjusted via front panel controls. The Error Signal
input will be demodulated relative to the dither signal which will generate a derivative of the input
Error Signal. This derivative signal will be used to lock the laser to a minima or maxima of the input
Error Signal. This is often referred to as peak-locking. If purchased with the Peak Lock option, the
Laser Servo can still be used in side-lock mode. A front panel switch controls whether the D2-125-PL is
in side-lock or peak-lock mode. When in side-lock mode the modulation / demodulation circuitry is
disabled. In this manual, sections that are only relevant to the Peak Lock option are printed in red.
The Internal Power option removes the 9-pin power connect used to connect power between Vescent
electronics modules and provides power entry module for powering the module via main AC lines. The
input voltage, 100VAC, 120VAC or 230VAC, is specified in the option. Note, with this option, the
D2-125 cannot be powered via the D2-005 Power Supply, the D2-001 break-out or from any other
Vescent electronics modules. Additionally, this module will not be able to power other Vescent
electronics modules; the -IP option makes the Laser Servo completely stand-alone. In this manual,
sections that are only relevant to the Internal Power option are printed in orange.
Absolute Maximum Ratings
Note: All modules designed to be operated in laboratory environment
Parameter Rating
Environmental Temperature >15°C and <30°C
Environmental Humidity <60%
Environmental Dew Points <15°C
When connecting Servo Output to your
plant, always make sure to discharge any
residual voltages, for instance from a PZT.

2021/04/17 23:32 3/18 Reconfigurable Laser Servo
Product Manuals - https://www.vescent.com/manuals/
Specifications
Value Units
Input and Output Impedance 502) Ω
Output Voltage (main and aux) ±10 V
Input Voltage Noise3) <5 nV/√Hz
Max Input Voltage DC Level ±500 mV
Max Input Voltage Signal Amplitude ±500 mV
Bandwidth4) >10 MHz
Proportional Gain (ref to DC Error)
Proportional Gain (ref to Input Error)
-66 to +6
-40 to +32 dB
First Integrator
Off, 10 Hz, 20 Hz, 50 Hz, 100 Hz, 200 Hz,
500 Hz, 1 kHz, 2 kHz, 5 kHz, 10 kHz,
20 kHz, 50 kHz, 100 kHz, 200 kHz
Second Integrator
Off, 100 Hz, 200 Hz, 500 Hz, 1 kHz, 2 kHz,
5 kHz, 10 kHz, 20 kHz, 50 kHz, 100 kHz,
200 kHz, 500 kHz, 1 MHz, 2 MHz
Differential
Off, 500 Hz, 1 kHz, 2 kHz, 5 kHz, 10 kHz,
20 kHz, 50 kHz, 100 kHz, 200 kHz,
500 kHz, 1 MHz, 2 MHz, 5 MHz, 10 MHz
Differential Gain 5 to 15 dB
Auxiliary Servo Output Gain5) Integral: 500 μs to 5 s
Laser Freq. Jump
Jump Time <400 μs
Ramp Amplitude (Max) ±5 V
Ramp Frequency (on main servo output)
Ramp Frequency (on aux servo output)
500
50 Hz
Dither Frequency (-PL only) 4 MHz
RF Output Max Amplitude (-PL only) ±75 mV
RF Output Impedance (-PL only)6) 50 Ω
Ramp Centering Range ±5 V
Inputs, Outputs, and Controls

Last update: 2021/03/02 17:06 d2:laser_servo https://www.vescent.com/manuals/doku.php?id=d2:laser_servo
https://www.vescent.com/manuals/ Printed on 2021/04/17 23:32
Fig. 2: Schematic drawing of the front and back panels of the D2-125
Monitor Section
Located at the top of the front panel, the monitor section contains 6 BNC outputs for monitoring
various signals used by the Laser Servo. The logic of the monitors is shown in figure 3. Open a pdf of
this image .

2021/04/17 23:32 5/18 Reconfigurable Laser Servo
Product Manuals - https://www.vescent.com/manuals/
Fig. 3: Monitor output logic
Error In
The ERROR IN monitor is a buffered and filtered version of the ERROR INPUT. The monitor has a 300
kHz low-pass filter.
DC Error
The signal from ERROR IN (after demodulation if in PEAK LOCK mode) is amplified by 26 dB (x20). The
amplified signal is summed with both the DC OFFSET as set on the front panel and the back-panel DC
OFFSET INPUT. The DC ERROR is passed through a low pass filter with a roll off of 200 kHz, so that
high frequency noise does not obfuscate the signal. The DC level of the DC ERROR sets the lock-point
and can be adjusted with the DC OFFSET knob. When locked, the Laser Servo acts to drive the DC
ERROR to zero.
AC Error
The AC ERROR monitors the same signal as the DC ERROR, except there is no low-pass filter and the
signal is coupled through a high pass filter to remove DC components (< 10 Hz). It is designed for
spectrum analysis and is also useful for coarse estimates of the laser line-width. The bandwidth of the
AC ERROR is limited by the preceding amplifier stages to greater than 20 MHz.
Servo Out
The SERVO OUT monitors the correction signal that is fed back to the laser, SERVO OUTPUT. The
signal is the output from the tunable loop filter.
Ramp Mon
The RAMP MON is a monitor for the actual ramp signal sent to the SERVO OUTPUT when the laser is in
RAMP mode.
Ramp TTL

Last update: 2021/03/02 17:06 d2:laser_servo https://www.vescent.com/manuals/doku.php?id=d2:laser_servo
https://www.vescent.com/manuals/ Printed on 2021/04/17 23:32
The RAMP TTL is a trigger synchronous with the ramp. It is usually used to trigger an oscilloscope
while sweeping the SERVO OUTPUT. The RAMP TTL signal is also available on the back panel as a
dedicated trigger output.
Front Panel
Power (LED indicator)
All electronic modules have a blue LED power indicator on the top right side of the front panel control
section. The LED requires +15V and -15V in order to light.
Lock Mode (two-position switch) -PL only
When set to the PEAK LOCK position, this switch routes the ERROR IN to a FM demodulation circuit
that extracts the error signal, which is then passed to the Loop Filter circuit. In the SIDE LOCK
position, the demodulation circuit is bypassed and the signal is fed directly to the Loop Filter circuit.
Additionally, the RF OUTPUT is disabled in SIDE LOCK.
Ramp Amp (1-turn knob)
The RAMP AMP sets the amplitude of the internal ramp generator.
Phase (25-turn trimpot) -PL only
When purchased as part of a complete laser system, the PHASE control is set at the factory and
generally will not require further adjustment. The PHASE control adjusts the phase between the dither
signal at RF OUTPUT and the local oscillator used to demodulate the signal coming in to ERROR INPUT.
It is used to maximize the demodulated DC ERROR signal while the laser is sweeping across the
desired transition(s) or lock points. The dither frequency is 4 MHz.
Dither Amp (25-turn trimpot) -PL only
The DITHER AMP control is used to set the amplitude of the dither signal at RF OUTPUT. When
purchased as part of a complete laser system, it is set at the factory and generally will not require
further adjustment. When used with the D2-105 Laser Controller, the RF OUTPUT should be connected
to the Laser Controller's RF INPUT to modulate the laser current. The DITHER AMP can range from 0 to
±75 mV (into a 1 MΩ load).
Error Input (BNC)
This is the input for the error signal. In SIDE LOCK mode, the signal is amplified by 26 dB and summed
with the DC OFFSET and DC OFFSET INPUT (back panel). In PEAK LOCK mode, the ERROR INPUT is
demodulated by the dither frequency and is then amplified by 26 dB and summed with the DC
OFFSET and DC OFFSET INPUT (back panel). In both modes the amplified signal can be seen with the
DC ERROR MONITOR and the AC ERROR MONITOR.
RF Output (BNC) -PL only
The RF OUTPUT signal is the 4 MHz dither or FM modulation signal. When used with the D2-105 Laser
Controller, it should be connected to the RF INPUT on the Laser Controller. In SIDE LOCK mode the
dither to the RF OUTPUT is turned off.

2021/04/17 23:32 7/18 Reconfigurable Laser Servo
Product Manuals - https://www.vescent.com/manuals/
Gain Sign (two-position switch)
The GAIN SIGN reverses the sign of the signal input from ERROR INPUT and should be used if the
desired lock-point has the wrong slope (loop is providing positive feedback instead of negative
feedback). Switching GAIN SIGN will invert the pattern seen at DC ERROR. When triggering an O-
scope with the RAMP TTL signal on a positive edge, the Laser Servo locks to a zero crossing with a
positive slope.
Laser State (three-position switch)
The lock switch has three positions. The lowest is the RAMP, which connects the internal ramp to the
SERVO OUTPUT causing the laser to sweep. The amplitude of the sweep is controlled with RAMP AMP
knob. In the center position (UNLOCK) the ramp is disconnected and zero volts is output to SERVO
OUTPUT. In the top position (LOCK) the loop filter is engaged.
DC Offset (10-turn potentiometer)
The DC OFFSET knob adds a DC offset to the DC ERROR MONITOR signal. Since the servo locks to the
point where the DC ERROR MONITOR reads 0V, adjusting the DC OFFSET changes the lock point.
Coarse Gain (seven-position switch)
The COARSE GAIN sets the overall proportional gain of the circuit without changing the location of any
corners or poles in the loop filter transfer function. Relative to the DC ERROR MONITOR, the Coarse
Gain adjusts the gain from 0dB to -60dB.
The overall loop gain (controlled by both the COARSE GAIN and the FINE GAIN) should be set around
the point that minimizes the RMS noise on the DC ERROR MONITOR. This can sometimes result in
setting the gain too high because the DC ERROR MONITOR filters high frequencies and thus hides
some of the gain peaking with high gain. To precisely set the gain, look at the noise with a spectrum
analyzer through the AC ERROR MONITOR.
Fine Gain (1-turn knob)
The FINE GAIN control adjusts the proportional gain by +6 to -6 dB.
Servo Output
When connecting Servo Output to your
plant, always make sure to discharge any
residual voltages, for instance from a PZT.
The SERVO OUTPUT is a voltage output to control the frequency of the laser. When the Laser Servo is
used with the D2-105 Laser Controller, the SERVO OUTPUT is connected to the CURRENT SERVO
INPUT on the Laser Controller. The SERVO OUTPUT is the output from the loop filter when in LOCK
mode, zero volts when in UNLOCK mode, and a DC balanced triangle wave when in RAMP mode. The
ramp can be shifted with respect to 0V using the ramp centering functionality.
Auxiliary Servo Output

Last update: 2021/03/02 17:06 d2:laser_servo https://www.vescent.com/manuals/doku.php?id=d2:laser_servo
https://www.vescent.com/manuals/ Printed on 2021/04/17 23:32
The AUXILIARY SERVO OUTPUT is generated from integrating the SERVO OUTPUT. Its purpose is to
supply a correction signal to drive the SERVO OUTPUT to zero. When used with Vescent DBR lasers
and the D2-105 Laser Controller, the AUXILIARY SERVO OUTPUT can be connected to the TEMP SERVO
IN to adjust the laser diode temperature to keep the feedback laser current constant. Similarly,
AUXILIARY SERVO OUTPUT can drive a PZT on an external-cavity laser diode to keep the laser diode
current constant. See AUXILIARY SERVO: GAIN SIGN and AUXILIARY SERVO: GAIN for information on
setting the gain and gain sign of the AUXILIARY SERVO OUTPUT.
Ramp Offset
The Ramp Offset provides the user with two front-panel knobs to adjust the voltage of the center of
the ramp. When the Ramp Offset is zeroed, the ramp is centered at 0 V and when the servo goes from
unlock mode to lock mode, it engages the integrators starting from 0 V. The user can adjust the Ramp
Offset knobs (coarse and fine) to define the center of the ramp and the initial voltage point from
which the servo begins integrating. The Ramp Offset is typically set to 0 V when Servoing Vescent
DBR lasers as this functionality is redundant with the current adjust knobs on the D2-105 Laser
Controller. Ramp Offset is more useful when servoing PZT-based external cavity lasers where the PZT
amplifier (if used) does not have an offset knob.
Ramp Offset Coarse
Coarse adjust to the center of the ramp signal and the DC Voltage output in UNLOCK mode. Range is
approximately ±5 V.
Ramp Offset Fine
Fine adjust to the center of the ramp signal and the DC Voltage output in UNLOCK mode.
Right Side Panel
Fig. 4: Side panel of D2-125 showing transfer function and
corner adjustments.

2021/04/17 23:32 9/18 Reconfigurable Laser Servo
Product Manuals - https://www.vescent.com/manuals/
Fig. 5: Schematic of the configuration transfer function and
user-controls.
The feedback loop is defined by the Gain vs Frequency plot shown above. ƒI, ƒPI and ƒD define three
corners in the transfer function. ƒI and ƒPI are the frequencies where the first and second integrators
respectively switch from having integral gain to having proportional gain. ƒD is the frequency where
the gain switches from proportional to differential. ƒI, ƒPI and ƒD are controlled by two rotary switches,
where the upper switch is used to select higher frequencies, and the lower switch is used for selecting
the lower frequencies. The upper switch must be in the “low freq” position to engage the lower
switch.
NOTE: Adjusting the loop filter corners while locked may result in loss of lock. If this happens, unlock
laser before adjusting poles and corners and relock laser after adjustment.
NOTE: The triangle embedded in the rounded side of each click switch points to the selected value.
First Integrator (TOP)
Sets the frequency of the first integrator (ƒI). This knob only selects higher-frequency positions (2 kHz -
200 kHz). To set ƒI to lower frequencies, this knob must be placed in the LOW FREQ position.
First Integrator (BOTTOM)
Sets the frequency of the first integrator (ƒI). This knob only selects the lower-frequency positions (10
Hz - 1 kHz) and is only active if the FIRST INTEGRATOR (TOP) knob is in the LOW FREQ position. To
turn off the integrator, this knob must be placed in the OFF position and the FIRST INTEGRATOR (TOP)

Last update: 2021/03/02 17:06 d2:laser_servo https://www.vescent.com/manuals/doku.php?id=d2:laser_servo
https://www.vescent.com/manuals/ Printed on 2021/04/17 23:32
knob must be in the LOW FREQ position.
Second Integrator (TOP)
Sets the frequency of the second integrator (ƒPI). This knob only selects the higher-frequency positions
(20 kHz - 2 MHz). To set ƒPI to lower frequencies, this knob must be placed in the LOW FREQ position.
First Integrator (BOTTOM)
Sets the frequency of the second integrator (ƒPI). This knob only selects the lower-frequency positions
(100 Hz - 10 kHz) and is only active if the SECOND INTEGRATOR (TOP) knob is in the LOW FREQ
position. To turn off the integrator, this knob must be placed in the OFF position and the FIRST
INTEGRATOR (TOP) knob must be in the LOW FREQ position.
Differential (TOP)
Sets the frequency of the differentiator (ƒD). This knob only selects the higher-frequency positions (200
kHz - 10 MHz) and can turn off the differential by placing the switch in the OFF position. To set ƒD to
lower frequencies, this knob must be placed in the LOW FREQ position.
Differential (BOTTOM)
Sets the frequency of the differentiator (ƒD). This knob only selects the lower-frequency positions (500
Hz - 100 kHz) and is only active if the DIFFERENTIAL (TOP) knob is in the LOW FREQ position.
Differential Gain (25-turn trimpot)
Sets the maximum differential gain. 25-turn trimpot adjusts the gain from 5db to 15dB.
Auxiliary Servo: Gain (25-turn trimpot)
This trimpot sets the gain for the AUXILIARY SERVO OUTPUT. The Aux Servo is a pure integrator and
the gain ranges from 500 μs to 5 s. Full ccw sets gain to minimum (5 s), full cw sets gain to maximum
(500 µs).

2021/04/17 23:32 11/18 Reconfigurable Laser Servo
Product Manuals - https://www.vescent.com/manuals/
Fig. 6: Certain rarely used controls are only accessible by
removing the right-side panel, as shown in the figure above.
Fig. 7: VPN00211 board.
Selector DIP Switch Array:
Ramp→Aux / Ramp→Servo (2-position slider switch)
This 2-position slider switch is only accessible by removing the right side panel (see above) and sets
whether the ramp is applied to the SERVO OUTPUT or the AUXILIARY SERVO OUTPUT. It is factory set
in the Ramp→Servo position. When the Ramp→Servo is selected, the ramp is a ~500 Hz triangle wave
and when Ramp→Aux is selected the ramp is ~50 Hz. Additionally, when using The Absolute Jump TTL
or the Relative Jump TTL, the output jump is placed on the same channel as gets the ramp signal. The

Last update: 2021/03/02 17:06 d2:laser_servo https://www.vescent.com/manuals/doku.php?id=d2:laser_servo
https://www.vescent.com/manuals/ Printed on 2021/04/17 23:32
other signal (SERVO OUTPUT or AUXILIARY SERVO OUTPUT) is held at its current value.
Aux Gain: + / Aux Gain - (2-position switch)
This switch is only accessible by removing the right side panel (see above). This switch sets the gain
sign for the AUXILIARY SERVO OUTPUT.
Aux Gain: Low / Aux Gain: High (2-position switch)
This switch is only accessible by removing the right side panel (see above). This switch sets a 40dB
attenuator for the AUXILIARY SERVO OUTPUT loop gain when set to Aux Gain: Low.
Aux: Bipolar / Aux: Unipolar (2-position slider switch)
This 2-position slider switch is only accessible by removing the right side panel (see above) and sets
whether the AUXILIARY OUTPUT SERVO is unipolar or bipolar. It is factory set to be bipolar so the
auxiliary output can range from -10 V to +10 V. For some applications such as driving a PZT, limiting
the voltage range to positive values is necessary. When this switch is in the unipolar mode, the
auxiliary output ranges from -0.5 V to +10 V. Additionally, when in Ramp→Aux mode and Aux:
Unipolar, the ramp is centered at ~3.5V instead of 0V.
Ramp Master / Slave (Jumper)
This jumper is only accessible by removing the right side panel (see above) and sets whether the
ramp input is in master or slave mode. It is factory set to be in MASTER MODE. In SLAVE MODE
(jumper off) the RAMP signal is generated externally and input through the back panel RAMP I/O port.
In MASTER MODE (jumper on) the ramp is generated internally and is sent out to the RAMP I/O port for
driving other D2-125 Laser Servos configured in SLAVE MODE.
The amplitude of the slave ramp is about -5x of the master ramp input (at slave Ramp Amp
maximum). The DC offset is applied after amplification.
Lock Guard
The Lock Guard feature on newer models (roughly post 2014) provides a relocking function that
detects if the primary servo output has changed its value too quickly. If this is detected, the servo
disengages the lock and reengages the lock with the servo output set to its value prior to the unlock
event.
Lock Guard Controls (DIP Switch Array)
Disabled / Enabled
This 2-position slider switch is only accessible by removing the right side panel (see figure 6) and sets
whether the auto-locking routine is engaged or not. When engaged, an AC-coupled (RC ≈ 10 μs)
window comparator monitors the SERVO OUTPUT to detect fast changes in the output. If the servo
output changes too much (as set by R202 / T3, see below) the autolock routine is engaged. The
autolock will set the SERVO OUTPUT to its value immediately before the detected unlock event, wait
for the hold time (see below) and then re-engage the lock. If the SERVO OUTPUT jumps after this
relock attempt, the relock routine will attempt a second relock again, but only after N+1 Relock Time

2021/04/17 23:32 13/18 Reconfigurable Laser Servo
Product Manuals - https://www.vescent.com/manuals/
has passed since the previous relock attempt.
Mode A,B,C
These three 2-position slider switches are only accessible by removing the right side panel (see
above) and sets the Hold Time and N+1 Relock Time described above. The 3 positions, A,B,C form a
binary scale factor given by the table below:
C B A Hold Time N+1 Relock Time
Off Off Off 60 µs 150 µs
Off Off On 125µs 300 µs
Off On Off 250 µs 600 µs
Off On On 500 µs 1.25 ms
On Off Off 1 ms 2.5 ms
On Off On 2 ms 5 ms
On On Off 4 ms 10 ms
On On On 8 ms 20 ms
The ideal delay used will depend on your system and loop bandwidth. Generally, a faster response
and slower delay is ideal, however, sometimes the system needs time to stabilize after a large
correction and these settings enable the user to adjust how long to wait to let the system stabilize
before engaging the lock.
R202 (Trimpot)
The R202 trimpot sets the size of the window comparator described above. The size of the window
can be measured by the voltage on T3. A smaller window means that the servo is more sensitive to
unlock events and detects them quicker, however, if the window is too small the servo may detect
false positives when the system remains locked but the SERVO OUTPUT is moving quickly to respond
to a challenge.
Back-panel Section
Power I/O (9-pin D-sub)
Never connect this device to a power supply that is switched
on and supplying power. Always turn off the power supply,
make connections to this device, and then re-energize the
power supply.
The power to each electronics module is through a 9-pin D-sub connector through either a power
bridge unit or a serial cable with 9-pin D-sub connectors, which is convenient when the unit must be
taken out of line for access to the side panels. The pin outs are shown in the following figure:

Last update: 2021/03/02 17:06 d2:laser_servo https://www.vescent.com/manuals/doku.php?id=d2:laser_servo
https://www.vescent.com/manuals/ Printed on 2021/04/17 23:32
Absolute Jump TTL (BNC)
When asserted HIGH (5V) while in LOCK mode, ABSOLUTE JUMP takes the Laser Servo out of lock and
conveys the negative of the voltage on LASER JUMP AMPLITUDE to the SERVO OUTPUT. Thus, a 1 V
input to LASER JUMP AMPLITUDE applies -1 V to SERVO OUTPUT. ABSOLUTE JUMP is useful when one
wants to control the voltage on the integration stages of the loop filter, or for zeroing the integrators
during auto-locking routines. When returned to LOW (0V), the loop filter is reengaged. Engaging or
disengaging the ABSOLUTE JUMP is achieved in under 400 μs.
When asserted HIGH (5V) while in RAMP mode, ABSOLUTE JUMP applies a DC offset equal to
-1*(LASER JUMP AMPLITUDE) to the ramp signal at SERVO OUTPUT. When asserted LOW while in RAMP
mode, the ramp signal is DC balanced.
When disconnected, ABSOLUTE JUMP is low.
Relative Jump TTL (BNC)
When asserted HIGH (5 V) while in LOCK mode, RELATIVE JUMP engages a sample-and-hold circuit and
takes the Laser Servo out of lock. The voltage on the SERVO OUTPUT is the sample-and-hold value
summed in with the negative of the LASER JUMP AMPLITUDE. For example, if the laser is locked and
the SERVO OUTPUT is -200 mV, then putting +300 mV on the LASER JUMP AMPLITUDE and engaging
the RELATIVE JUMP will set the SERVO OUTPUT to -200 mV + (-300 mV) = -500 mV. This feature is
useful for jumping the laser relative to its current lock point (say +200 MHz from a locked transition).
When returned to LOW (0 V), the loop filter is reengaged, enabling the laser to be relocked to a new
lock point (by asserting the trigger low with the LASER JUMP AMP still at a non-zero value). (See
application note here.) Or the laser can be relocked to its original position (by setting LASER JUMP
AMP to zero before returning the trigger to TTL low). Engaging or disengaging the RELATIVE JUMP is
achieved in under 400 μs.
When asserted HIGH (5V) while in RAMP mode, RELATIVE JUMP applies a DC offset equal to the LASER
JUMP AMPLITUDE to the ramp signal at SERVO OUTPUT. When asserted LOW (0V) while in RAMP mode,
the ramp signal is DC balanced.
When disconnected, RELATIVE JUMP is low.
Ramp TTL
Same as the front panel signal. The RAMP TTL is a trigger synchronous with the ramp. It is used to
trigger an oscilloscope while sweeping the SERVO OUTPUT.

2021/04/17 23:32 15/18 Reconfigurable Laser Servo
Product Manuals - https://www.vescent.com/manuals/
Ramp IN / OUT
The Laser Servo is shipped with the Ramp in MASTER MODE. In this configuration, the RAMP IN / OUT
is an output of the maximum ramp signal, generated internally. Removing the side-panel RAMP
MASTER / SLAVE jumper will put the Laser Servo in slave mode. In this configuration, RAMP IN / OUT is
an input of an external ramp signal. When the LASER STATE is in RAMP MODE, the SERVO OUTPUT is
an attenuated version of the input to RAMP IN / OUT. The attenuation is controlled by the RAMP AMP
knob. If controlling multiple lasers with multiple D2-125's to sync the ramps, one D2-125 must be in
master mode and the rest in slave mode with all the RAMP IN / OUT signals connected. In this way
each laser will sweep off a synced signal and only one oscilloscope trigger is needed for all the lasers.
The Ramp I/O has a bandwidth of roughly 50 kHz.
DC Offset Input
This signal is attenuated by a factor of 10 and summed into the DC ERROR. Inputting a square wave
into the DC OFFSET INPUT jumps the laser lock point and can be used to measure the closed-loop
transfer function of the laser system. It has a bandwidth of about 300 kHz (-3 dB point). The maximum
voltage at this input should be no more than ±10 V (±1 V of DC offset).
Laser Jump Amp (BNC)
The LASER JUMP AMPLITUDE is an analog signal that is used to jump the frequency of the diode laser.
See preceding sections on RELATIVE JUMP and ABSOLUTE JUMP for a full explanation.
Laser Lock Troubleshooting
Most laser locking problems can be attributed to the following:
Gain set too high (or too low). Reduce the coarse and fine gain all the way and try locking.
Increase the coarse gain by one click at a time.
Gain sign wrong (trying to lock to the wrong slope).
Make sure the oscilloscope is triggering to positive slope7).
Make sure oscilloscope is not in inverting mode.
Make sure your desired lock-point has a positive slope.
If all else fails, flip the gain sign and try again.
Note: sometimes the laser will lock even if the slope is wrong because there are legitimate lock-points
nearby. This can fool you into thinking you are locking to the proper spot.
DC OFFSET not adjusted properly.
When monitoring DC ERROR make sure you are not AC coupled on the oscilloscope!
When locking to spectroscopy, ramping fast through the transition can change the DC
value on the scope (due to atom transit time through laser beam coupling to optical
pumping rates). Reduce RAMP AMP towards zero on the desired transition until the DC
value is not affected. Adjust DC OFFSET if necessary.
Loop Filter Too Fast. Try turning off the differential feedback and only use one integrator.
Then try slowing down your integrator. If you get a lock, you can then put back double
integration and the differential feedback.
The ramp center is not located at the center of the oscilloscope. When adjusting the

Last update: 2021/03/02 17:06 d2:laser_servo https://www.vescent.com/manuals/doku.php?id=d2:laser_servo
https://www.vescent.com/manuals/ Printed on 2021/04/17 23:32
RAMP AMP, the oscilloscope signal will expand and contract about a single point. That
“breathing point” should be centered in the middle of the oscilloscope and can be adjusted by
changing the trigger delay of the oscilloscope. When set properly, if the oscilloscope is centered
exactly on an atomic transition or other feature, then that feature will remain centered on the
oscilloscope even when the RAMP AMP is turned all the way up or down.
Magnetic fields are interfering with the spectroscopy signal. If the servo is used with a
spectroscopy module (D2-110), magnetic fields can make locking difficult. When locking to
spectroscopy, even though the spectrum might look okay, strong magnetic fields can affect the
transfer function of the spectroscopy error signal in a negative way, making locking difficult. If
using the D2-110 Spectroscopy Module and a D2-100 laser, make sure the laser module is at
least three inches away from the spectroscopy module. In some cases, strong magnetic fields
can emanate from the optics table (if magnetic clamps are in use).
If you are having problems locking the laser, it is a good idea to not use the AUXILIARY SERVO
OUTPUT as this complicates the system. Once you get the locking to work properly, you can
reconnect this cable.
figure 8 shows and table 1 lists the nominal corner settings for locking the Vescent D2-100 (or a
Photodigm TOSA) to atomic spectroscopy. If all else fails, return to these setting, turn down the gain
and try again.
Fig. 8: Factory settings for locking a D2-100
Corner Value Units
First Integrator (high freq.) low freq.
First Integrator (low freq.) 10 Hz
Second Integrator (high freq.) low freq.
Second Integrator (low freq.) 500 Hz
Differential (high freq.) OFF
Differential (low freq.) 100 kHz

2021/04/17 23:32 17/18 Reconfigurable Laser Servo
Product Manuals - https://www.vescent.com/manuals/
Tab. 1: D2-125 locking D2-100 or TOSA
D2-125 Stand-alone Test
It is possible to “lock the D2-125 to itself” as a self-test. Under the following conditions, the D2-125
should behave as described. Depending on your observations, contact Vescent technical support and
discuss the performance.
Switch to Side Lock Mode1.
Set Ramp to Servo (not Aux)2.
Disconnect the 125 from all input and output3.
Connect the Servo Output to the Error Input4.
Set Gain to about the middle of the course range5.
Set the Ramp Center to the middle of its range6.
Set Ramp Amp to max7.
Set DC Offset to center of its range8.
What voltage do you see on the Servo Out Monitor (into 1 MΩ impedance)9.
In Ramp mode?1.
Should be a ±9-10V triangle wave at 500 Hz1.
In Unlock mode?2.
Should be 0 V (Could be offset by the Ramp Center)1.
In Lock mode?3.
Should be 0 V (Could be offset by either the Ramp Center or DC Offset)1.
If D2-125 rails, return to Unlock mode, switch the Gain Sign from + to - (or vice versa) and retry10.
In Lock mode, turn up gain. At some point, the Servo Out should oscillate at something close to11.
10 MHz, depending on the specific corner settings of the PI2D loop
1)
quantity 2 when PL option ordered
2)
In Peak Lock mode, the 50 Ω to ground is AC-coupled. A measurement of the DC impedance will yield
a higher value.
3)
Referenced to 50Ω load
4)
Oscillation frequency when Laser Servo locked to itself in proportional mode.
5)
Gain referenced to Primary Servo Output.
6)
Into a 1 MΩ load
7)
It is not necessary to trigger the oscilloscope to a positive slope, however, switching the trigger slope
will change whether the servo locks to a positive slope (positive slope trigger on oscilloscope) or
negative slope (negative slope trigger on oscilloscope)

Last update: 2021/03/02 17:06 d2:laser_servo https://www.vescent.com/manuals/doku.php?id=d2:laser_servo
https://www.vescent.com/manuals/ Printed on 2021/04/17 23:32
From:
https://www.vescent.com/manuals/ - Product Manuals
Permanent link:
https://www.vescent.com/manuals/doku.php?id=d2:laser_servo
Last update: 2021/03/02 17:06
Table of contents
Other Vescent Photonics Servo Drive manuals
Popular Servo Drive manuals by other brands
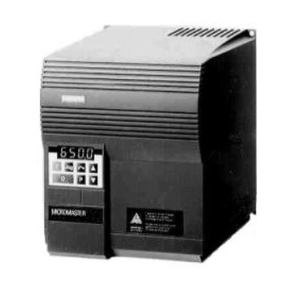
Siemens
Siemens MICROMASTER 6SE92 Getting started
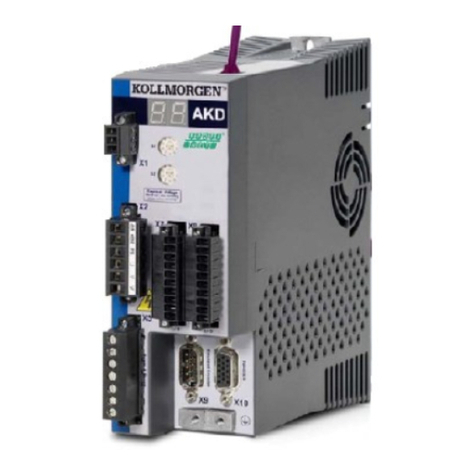
Kollmorgen
Kollmorgen AKD PROFINET RT Communication manual
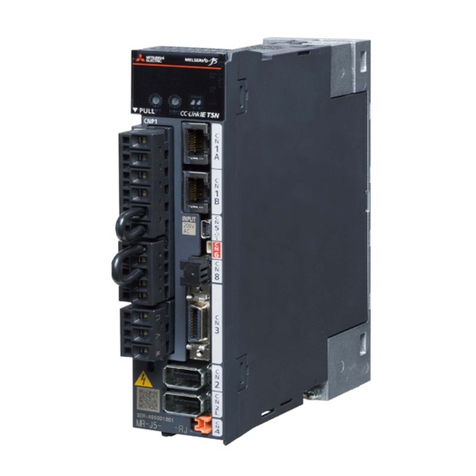
Mitsubishi Electric
Mitsubishi Electric MR-J5 Series user manual
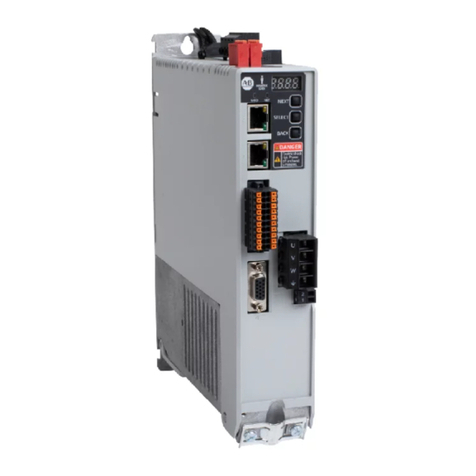
Rockwell Automation
Rockwell Automation Allen-Bradley Kinetix 350 installation instructions
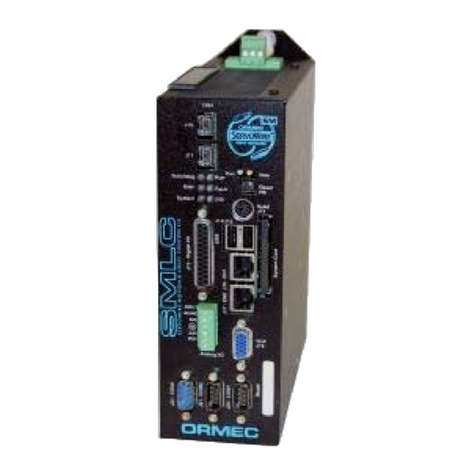
Ormec
Ormec SMLC Programming guide
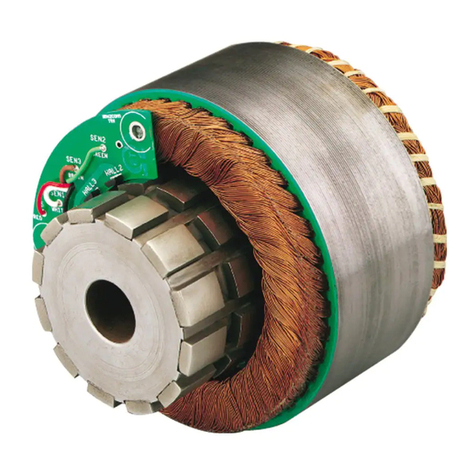
Parker
Parker K Series Technical manual
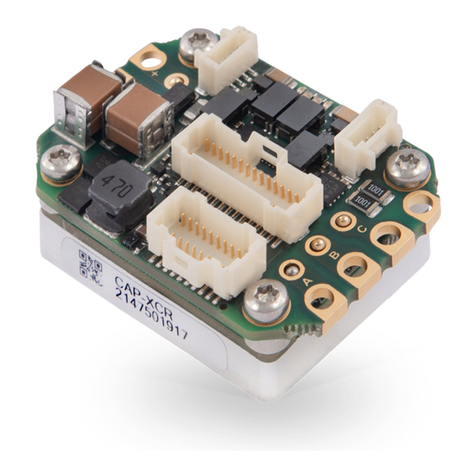
INGENIA
INGENIA Everest XCR product manual
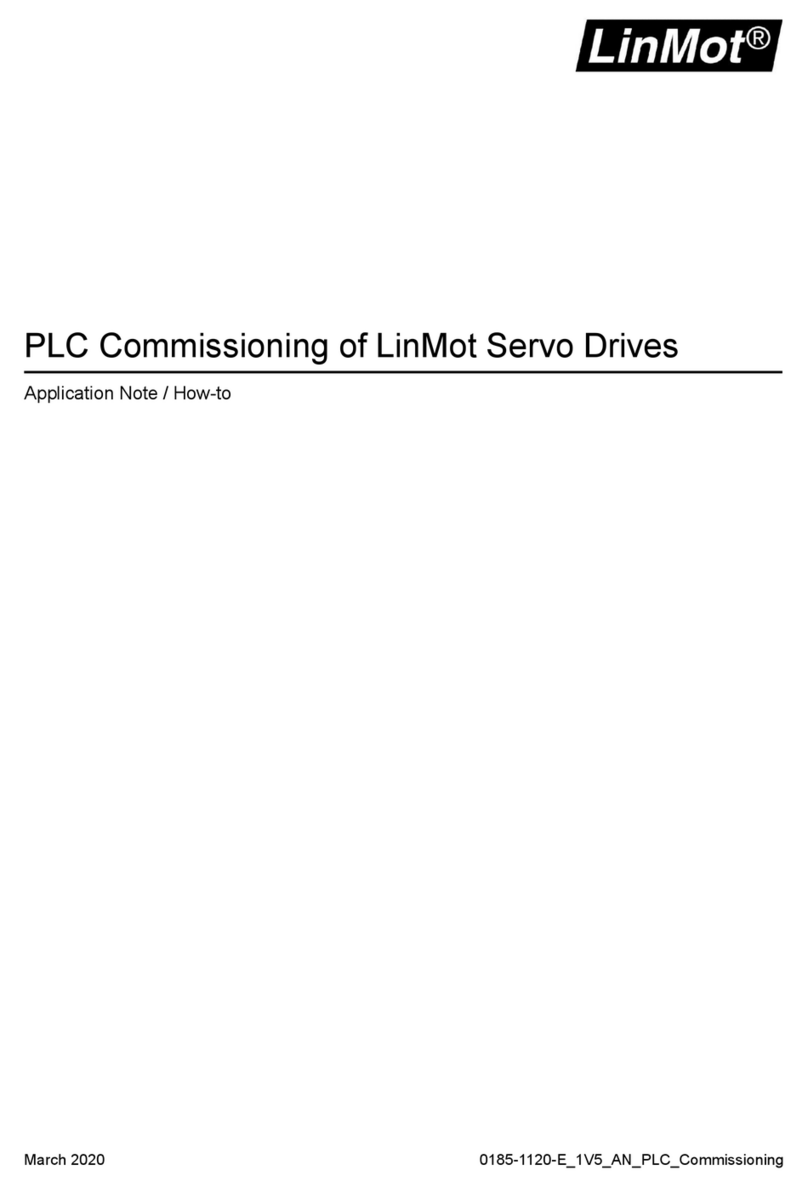
LinMot
LinMot C1250-IP Series Application note
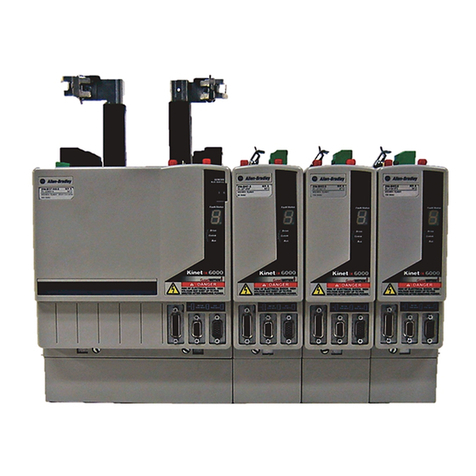
Allen-Bradley
Allen-Bradley 2094-AC05-MP5 user manual
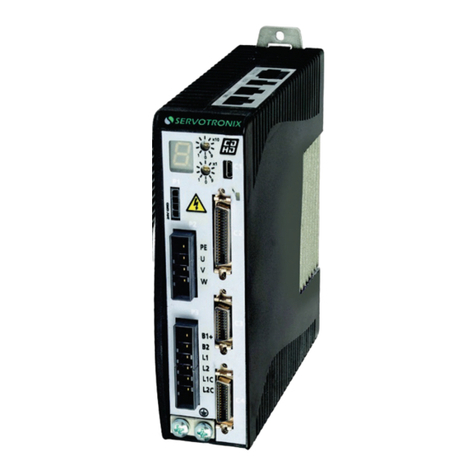
Servotronix
Servotronix CDHD Series Application note
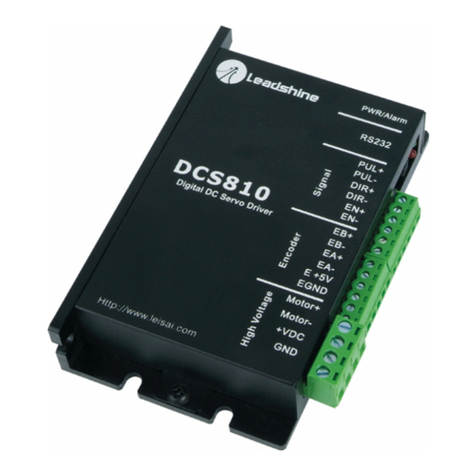
Leadshine Technology
Leadshine Technology DCS810 user manual
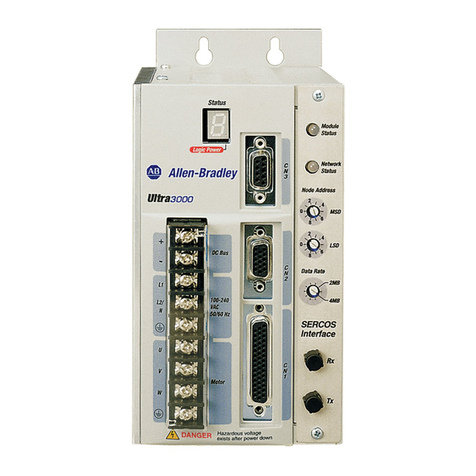
Rockwell Automation
Rockwell Automation Allen-Bradley Ultra3000 Migration guide