Victron energy VE.Bus BMS V2 User manual

Table of Contents
1. General description .................................................................................................................. 1
2. Safety precautions ................................................................................................................... 3
3. Installation ............................................................................................................................. 4
3.1. What's in the box? ........................................................................................................... 4
3.2. Basic installation ............................................................................................................. 5
3.2.1. Minimal VE.Bus firmware ......................................................................................... 5
3.2.2. Battery BMS cable connections ................................................................................. 6
3.2.3. Mains detector ..................................................................................................... 7
3.3. Controlling DC loads and chargers ........................................................................................ 8
3.3.1. DC load control .................................................................................................... 8
3.3.2. DC charge control ................................................................................................. 8
3.3.3. Controlling inverter/chargers, solar chargers and other battery chargers .................................. 8
3.3.4. DVCC operation with VE.Bus BMS V2 ......................................................................... 9
3.3.5. Charger control via Charge disconnect ......................................................................... 9
3.3.6. Charging with an alternator ...................................................................................... 9
3.4. Remote on/off terminal .................................................................................................... 10
3.5. GX device .................................................................................................................. 11
3.6. Connecting a Digital Multi Control or a VE.Bus Smart dongle ....................................................... 12
4. System examples .................................................................................................................. 13
4.1. System with a GX device, on/off switch and pre-alarm circuit ........................................................ 13
4.2. System with a SmartShunt, BatteryProtect and solar charger ....................................................... 14
4.3. Basic system ............................................................................................................... 15
4.4. System with an alternator ................................................................................................ 16
4.5. Three-phase system with a Digital Multi Control ....................................................................... 17
5. Operation ............................................................................................................................ 18
5.1. Important warning ......................................................................................................... 18
5.2. LED indications ............................................................................................................ 18
6. Frequently asked questions ...................................................................................................... 19
7. Technical specifications VE.Bus BMS V2 ..................................................................................... 20
8. Appendix ............................................................................................................................. 21
8.1. Dimensions VE.Bus BMS V2 ............................................................................................ 21
8.2. VE.Bus BMS V2 compared to VE.Bus BMS V1 ....................................................................... 22
VE.Bus BMS V2

1. General description
Protects each individual cell of a Victron Lithium Battery Smart (LiFePO₄) battery
Each individual cell of a LiFePO₄ battery must be protected against under- and overvoltage, as well as low and high temperature.
This is exactly what the VE.Bus BMS V2 does in combination with the battery's BTV module, which provides appropriate signals
to the BMS.
The Victron Lithium Battery 12.8V & 25.6V Smart have integrated Balancing, Temperature and Voltage control (acronym: BTV)
and connect to the VE.Bus BMS V2 with two M8 circular connector cord sets. The BTVs of several batteries can be daisy
chained. Please see our Lithium Battery Smart product page for details.
Depending on the signals from the battery, the BMS will:
• Generate a pre-alarm signal to warn of an imminent cell undervoltage.
• Shut down or disconnect loads in case of cell undervoltage.
• Turn off the inverter of VE.Bus inverter/chargers in case of cell undervoltage.
• Reduce the charge current in case of cell overvoltage or overtemperature of VE.Bus inverter/chargers or VE.Bus inverters.
• Shut down or disconnect battery chargers in case of cell overvoltage or overtemperature.
Pre-alarm
The pre-alarm output is normally free floating and becomes high in case of imminent cell undervoltage. It is set by default at 3.1V
per cell and is adjustable on the battery between 2.85V and 3.15V per cell. The minimum delay between pre-alarm and load
disconnect is 30 seconds. Note that the pre-alarm does not generate a notification on the GX device and therefore not on VRM
either.
Load disconnect
The Load disconnect output is normally high and becomes free floating in case of cell undervoltage. The Load disconnect output
can be used to control:
• The remote on/off terminal of a load.
• The remote on/off terminal of an electronic load switch like a BatteryProtect (preferred low power consumption solution).
Charge disconnect
The Charge disconnect output is normally high and becomes free floating in case of cell over voltage or over temperature. The
Charge disconnect output can be used to control:
• The remote on/off terminal of a charger, like an AC charger, DC-DC charger or solar charger.
• A Cyrix-Li-Charge relay.
• A Cyrix-Li-ct Battery Combiner.
LED indicators
The BMS has the following LED indications:
•Status LED (blue): Lights once every 10 seconds when the Multi is switched on to indicate BMS info frames are being sent.
When the Multi is off, either due to a low cell/remote off or just switched off by means off the front panel switch, the BMS goes
into low power mode but continues to send BMS info frames (with a slightly longer interval between them). In this mode the
BMS status led does not light up to conserve energy. If the BMS is stuck in the bootloader, the status LED will flash rapidly. This
can happen, for example, after an interrupted firmware update (to fix this, restart the update on VictronConnect or via VRM).
• Cell voltage above 4V LED (red): Lights when the Charge disconnect output is low because of cell overvoltage or
overtemperature.
• Cell voltage above 2.8V LED (blue): Lights when the Load disconnect output is high and the battery cell voltages are above
2.8V.
VE.Bus BMS V2
Page 1 General description

Connectivity and communication with GX device
• On/off/charger-only control of VE.Bus products via a GX device.
• GX DVCC control of solar chargers. There is no need to install an BatteryProtect or Cyrix-Li-Charge to control solar chargers
via the BMS like the VE.Bus BMS V1 does.
Has separate power input and output connections for GX devices
• The GX-Pow output supplies GX power from either the battery or from the Aux-In input, whichever voltage is higher.
• An AC-DC adapter (not included) or other power supply connected to the Aux-In input will ensure that the GX device is
powered as long as that Aux power is available, even if the battery is low, for example, due to an error the battery is in under
voltage and the inverter/charger is switched off. This allows the system to be diagnosed remotely (assuming the Internet is still
available), even when (almost) everything else is turned off. See the Technical specifications [20] for the required power rating
of an AC-DC adapter.
True remote on/off terminal
• The VE.Bus BMS V2 needs to remain connected to the battery positive in order to be able to keep the Multi in low power mode
even when AC input on the Multi is available (Multi will stop inverting/charging, close the transfer switch and indicate a low
battery error on the status LEDs). In comparison, disconnecting the battery positive of the VE.Bus BMS V1 only really turns the
Multi off when no AC input is available.
VE.Bus BMS V2
Page 2 General description

2. Safety precautions
• Installation must strictly follow the national safety regulations in compliance with the enclosure, installation,
creepage, clearance, casualty, markings and segregation requirements of the end-use application.
• Installation must be performed by qualified and trained installers only.
• Switch off the system and check for hazardous voltages before altering any connection.
• Do not open the lithium battery.
• Do not discharge a new lithium battery before it has been fully charged first.
• Charge a lithium battery only within the specified limits.
• Do not mount the lithium battery upside down or on its sides.
• Check if the Li-Ion battery has been damaged during transport.
VE.Bus BMS V2
Page 3 Safety precautions

3. Installation
3.1. What's in the box?
The following items are in the box:
• 1x VE.Bus BMS V2
• 1x Mains detector
• 1x 0.3m RJ45 UTP cable
• Piece of Velcro adhesive hook and loop tape
Note that the DC power cable to power the BMS is not included. Use any 1-wire cable with at least 0.75mm2 (AWG 16) and a 1A
inline fuse.
What's in the box
VE.Bus BMS V2
Page 4 Installation

3.2. Basic installation
1. Connect the battery BMS cables to the BMS. For multiple batteries, see the Battery BMS cable connections [6] chapter.
2. Connect the inverter/charger or inverter positive and negative cables to the battery. Make sure it has been updated to the
most recent firmware version. For more information, see the Minimal VE.Bus firmware [5] chapter.
3. Connect the battery positive via the red power cable with the fuse to the BMS "Battery+" terminal.
4. Connect the VE.Bus port of the Inverter/charger or inverter to the "MultiPlus/Quattro" port of the BMS via an RJ45 cable (not
included).
5. In case of a non-new style MultiPlus 12/1600/70 and MultiPlus 12/2000/80, non-MultiPlus-II or non-Quattro-II, install the
mains detector. For more information, see the Mains detector [7] chapter.
Basic BMS connections
Note that the BMS does not have a battery negative connection. This is because the BMS obtains battery
negative from the VE.Bus. As such, the BMS cannot be used without a VE.Bus Inverter/charger or a VE.Bus
inverter.
3.2.1. Minimal VE.Bus firmware
Before connecting the BMS to the system, the VE.Bus firmware of all inverter/chargers or inverters used in the system needs to
be updated to the latest firmware version (version xxxx489 or above).
If the inverter/charger firmware is between version xxxx415 and xxxx489, the "VE.Bus BMS" or "ESS" assistant must be installed
in the inverter/charger.
If the inverter/chargers or inverters have a VE.Bus firmware version below xxxx415, the BMS will generate a VE.Bus error 15
(VE.Bus combination error). This error indicates that the VE.Bus products or firmware versions cannot be combined. If it is not
possible to update the inverter/chargers or inverters to a VE.Bus firmware version xxxx415 or higher the VE.Bus BMS V2 cannot
be used.
VE.Bus BMS V2
Page 5 Installation

3.2.2. Battery BMS cable connections
In the case of several batteries in parallel and/or series configuration, the BMS cables should be connected in series (daisy-
chained), and the first and last BMS cable should be connected to the BMS.
If the BMS cables are too short, they can be extended with extension cables, the M8 circular connector Male/Female 3 pole
cables.
Left: Connecting a single battery. Right: connecting multiple batteries.
VE.Bus BMS V2
Page 6 Installation

3.2.3. Mains detector
The mains detector is not required for the new style MultiPlus 12/1600/70 and MultiPlus 12/2000/80,
MultiPlus-II, Quattro-II and inverter models. In this case this chapters can be skipped and the mains detector
should be disposed of.
The purpose of the mains detector is to restart the inverter/charger when the AC supply becomes available in case the BMS has
shut down the inverter/charger due to low cell voltage (so that it can recharge the battery).
In systems consisting of several units configured for parallel, three-phase, or split-phase operation, the mains detector should be
wired in the master or leader unit only.
In the case of a MultiPlus, only use one AC wire pair, and in the case of a Quattro, use both wire pairs.
AC detector wiring example.
# Description
1 AC grid or generator
2 AC circuit breaker and RCD
3 Mains detector
4 Inverter/charger
5 VE.Bus BMS V2
6 Lithium Battery Smart
VE.Bus BMS V2
Page 7 Installation

3.3. Controlling DC loads and chargers
3.3.1. DC load control
DC loads with remote on/off terminals:
DC loads must be switched off or disconnected to prevent cell undervoltage. The Load disconnect output of the BMS can be used
for this purpose. The Load disconnect output is normally high (= battery voltage). It becomes free-floating (= open circuit) in case
of an impending cell undervoltage (no internal pull down to limit residual current consumption in case of low cell voltage).
DC loads with a remote on/off terminal that switches the load on when the terminal is pulled high (to battery plus) and switches it
off when the terminal is left free-floating, can be controlled directly with the BMS Load disconnect output.
DC loads with a remote on/off terminal that switches the load on when the terminal is pulled low (to battery minus) and switches
it off when the terminal is left free-floating, can be controlled with the BMS Load disconnect output via an Inverting remote on/off
cable.
Note: please check the residual current of the load when in the off state. After low cell voltage shutdown, a
capacity reserve of approximately 1Ah per 100Ah battery capacity is left in the battery. For example, a residual
current of 10mA can already damage a 200Ah battery if the system is left in a discharged state for more than
eight days.
Disconnecting a DC load via a BatteryProtect:
Use a BatteryProtect for DC loads that do not have a remote on/off terminal or for switching groups of DC loads off.
A BatteryProtect will disconnect the DC load when:
• Its input voltage (= battery voltage) has decreased below a preset value.
• Its remote on/off H terminal becomes free floating (usually high). This signal is provided by the Load disconnect output
(wired to the remote on/off H terminal of the BatteryProtect) of the VE.Bus BMS V2. See the wiring example System with a
BatteryProtect and a solar charger [14].
3.3.2. DC charge control
3.3.3. Controlling inverter/chargers, solar chargers and other battery chargers
In the event of high cell voltage or low temperature, battery charging must be stopped to protect the battery cells. Depending
on the system, chargers are either controlled via DVCC or must be controlled via their remote on/off terminals and the Charge
disconnect output of the VE.Bus BMS V2.
• In systems with a GX device, you must enable DVCC to ensure that the solar chargers and other DVCC-compatible devices
only charge when they should. See DVCC operation with VE.Bus BMS V2 [9] for details.
• In systems without a GX device, the BMS Charge disconnect output must control the solar charger and other chargers, either
via remote on/off, a BatteryProtect or a Cyrix-Li-Charge. See Charger control via Charge disconnect [9] for details.
VE.Bus BMS V2
Page 8 Installation

3.3.4. DVCC operation with VE.Bus BMS V2
DVCC (Distributed Voltage and Current Control) allows a GX device to control compatible devices such as solar chargers,
Inverter RS, Multi RS or Multis.
In order for the GX device to control the solar chargers, Inverter RS or Multi RS in a system with a VE.Bus BMS V2, DVCC
must be enabled. These chargers are controlled by setting their maximum charge current limit to zero when the VE.Bus BMS V2
requests that charging should stop.
Note that the presence of a VE.Bus BMS V2 does not control the charge voltage of the solar chargers, Inverter RS, Multi RS or a
Multi.
• In an ESS system, the Multi controls the charging voltage of the solar chargers, Inverter RS and Multi RS using the
configuration made with VE.Configure or VictronConnect. In other words: The charge algorythm must be configured in the
Multi.
• In a non-ESS (off-grid) system, the solar chargers, Inverter RS, Multi RS and Multi follow their own internal charge algorithm.
Here, all devices must be set to the appropriate lithium charge algorithm.
AC chargers and smaller Phoenix inverters are not (yet) controlled by the GX device, and therefore you still need to wire signal
wiring (via ATC aka Charge disconnect) to control such devices.
3.3.5. Charger control via Charge disconnect
Chargers that are not DVCC compatible or installed in systems without a GX device can be controlled via the VE.Bus BMS V2
Charge disconnect output, provided the chargers have a remote on/off port.
The Charge disconnect output, normally high (equal to battery voltage), must be connected to the H terminal of the charger's
remote on/off connector. At high cell voltage or low temperature, the Charge disconnect output becomes free-floating and pulls
the charger's remote on/off H terminal low (to battery minus), stopping the charge.
For battery chargers with a remote terminal that activates the charger when the terminal is pulled low (to battery minus) and
deactivates when the terminal is left free floating, the Inverting remote on-off cable can be used.
Alternatively, a Cyrix-Li-Charge relay can be used. The Cyrix-Li-Charge relay is a unidirectional combiner that inserts between
a battery charger and the lithium battery. It will engage only when charge voltage from a battery charger is present on its
charge-side terminal. A control terminal connects to the Charge disconnect output of the BMS.
3.3.6. Charging with an alternator
Alternator charging can be controlled either with a DC-DC charger such as the Orion-Tr Smart, or with a SolidSwitch 104 when
controlling an external alternator regulator like the Balmar MC-614.
Both devices are then also controlled by the BMS Charge disconnect output wired to the Orion-Tr Smart or SolidSwitch 104
remote on/off H terminal. See System with an alternator [16]
VE.Bus BMS V2
Page 9 Installation

3.4. Remote on/off terminal
The BMS remote on/off terminal can be used to turn the entire system on and off while the BMS remains connected to battery
positive, which keeps the inverter in low power (discharging and charging not allowed) mode even if it is still connected to AC In.
The remote H and L terminals switch the system on when:
• Contact is made between the remote H terminal and L terminal, for example, via the wire bridge or a switch.
• Contact is made between the remote connector H terminal and battery positive.
• Contact is made between the remote connector L terminal and battery negative.
A typical application is switching off the system when a predetermined state of charge (SoC) is reached in a BMV. Its relay then
operates the remote on/off terminal of the BMS. Note that at least the wire loop between pins L and H must be plugged in, so that
the VE.Bus BMS V2 can switch on.
VE.Bus BMS V2
Page 10 Installation

3.5. GX device
For solar chargers, Inverter RS, Multi RS or Multis to be controlled by the BMS via a GX device, the following requirements
should be met:
• The GX device Venus OS firmware must be version 2.80 or above.
Installation:
1. Connect the GX device VE.Bus port to the Remote panel port on the BMS via an RJ45 cable (not included). Note that this is
different from the former VE.Bus BMS V1, which allowed only the connection of a Digital Multi Control. The VE.Bus BMS V2
allows to connect a GX device, a VE.Bus Smart dongle or a Digital Multi Control.
2. Connect the GX device "power +" terminal to the GX-Pow terminal of the BMS and connect the GX device "power -" terminal
to the negative terminal of the battery.
3. Connect the positive wire of an (optional) AC-DC power supply to the AUX-in terminal of the BMS and connect the negative
wire to the negative battery terminal. Note that the AC-DC power supply is optional and most likely not needed in off-grid
installations such as boats or RVs.
4. Perform a VE.Bus re-detect system action on the GX device. This action is available in the inverter/charger menu on the GX
device.
GX device connections
The functionality of the GX-Pow and Aux-In terminals:
• The GX-Pow output supplies GX power from either the battery or from the Aux-In input, whichever voltage is higher.
• An AC-DC adapter (not supplied) or other power supply connected to the Aux-In input ensures that the GX device is also
powered during a low cell state as long as that aux power is available.
The GX device is powered by the GX-Pow terminal. The GX-Pow terminal is normally battery powered via the Battery+ terminal.
In the event of a low cell voltage, this connection would not be available, leaving the GX device without power. However, when
another power supply (i.e. a grid connected AC-DC power supply) is connected to the Aux-In, the GX-Pow connection will
continue to power the GX device, allowing the system to remain accessible despite low cell voltage, for example, to remotely
diagnosis the system.
VE.Bus BMS V2
Page 11 Installation

3.6. Connecting a Digital Multi Control or a VE.Bus Smart dongle
A VE.Bus Smart dongle or Digital Multi Control (DMC) must be connected to the Remote panel port of the BMS. Both have
on/off/charger-only control of the inverter/charger.
Note that in systems containing a Digital Multi Control and a GX device or a VE.Bus Smart dongle at the same time, on/off/
charger-only control of the inverter/charger is only possible via the Digital Multi Control.
For example, the VE.Bus Smart dongle, Digital Multi Control and the GX device can all be connected simultaneously to the
Remote panel port. However, in this scenario, on/off/charger-only control of the inverter/charger via the GX device and VE.Bus
dongle is disabled. Since inverter/charger control is disabled, the GX device or VE.Bus Smart dongle can also be connected to
the MultiPlus/Quattro port of the BMS for easy wiring.
Left: System with a Digital Multi Control Panel - Right: System with a VE.Bus Smart dongle
# Description
1 Digital Multi Control
2 VE.Bus Smart dongle
3 MultiPlus-II Inverter/charger
4 VE.Bus BMS V2
The VE.Bus Smart dongle needs to measure the battery voltage. Therefore its Battery+ terminal must be connected
to the positive battery terminal. Be aware that the VE.Bus Smart dongle will not be turned off by the BMS in case of a
low cell warning and will continue to draw current (up to 9mA - see the VE.Bus Smart dongle specifications for details)
from the battery.
5 Lithium Battery Smart or battery which can consist of multiple batteries to form a 12V, 24V or 48V battery.
VE.Bus BMS V2
Page 12 Installation

4. System examples
4.1. System with a GX device, on/off switch and pre-alarm circuit
AC/DC
power
supply
Pre-alarm
warning
circuit
On
Off
12 3
5
4
8
7
6
9
# Description
1 AC source, grid or generator
2 Circuit breaker
3 MultiPlus-II Inverter/charger
4 Remote on/off switch
5 VE.Bus BMS V2
6 Cerbo GX
7 AC-DC power supply, providing backup power to the Cerbo GX should the battery be too far discharged
8 Pre-alarm warning circuit, giving an advanced warning in case of an imminent system shutdown due to a too far
discharged battery
9 Lithium Battery Smart or battery consisting of multiple batteries creating a 12V, 24V or 48V battery bank
VE.Bus BMS V2
Page 13 System examples

4.2. System with a SmartShunt, BatteryProtect and solar charger
1
2
3
4
5
8
6
7
DC
loads
9
10
# Description
1 AC source, grid or generator
2 Circuit breaker
3 MultiPlus-II Inverter/charger
4 Solar charger
5VE.Direct non-inverting remote on/off cable connects between the solar charger VE.Direct port and the BMS
Charge disconnect terminal
6 VE.Bus BMS V2
7 Lithium Battery Smart or battery consisting of multiple batteries creating a 12V, 24V or 48V battery bank.
8 BatteryProtect
9 DC loads
10 SmartShunt
VE.Bus BMS V2
Page 14 System examples

4.3. Basic system
1
2
3
# Description
1 MultiPlus-II Inverter/charger
2 VE.Bus BMS V2
3 Lithium Battery Smart or battery consisting of multiple batteries creating a 12V, 24V or 48V battery bank
VE.Bus BMS V2
Page 15 System examples

4.4. System with an alternator
1
2
3 4
5
6
8
7
9
# Description
1 AC source, grid or generator
2 Circuit breaker
3 Orion DC-DC charger, the remote H terminal is connected to the Charge disconnect terminal on the VE.Bus V2 BMS
4 VE.Bus BMS V2
5 MultiPlus-II Inverter/charger
6 Starter monitor and alternator
7 12V starter battery
8 Lithium Battery Smart or battery consisting of multiple batteries creating a 12V or 24V battery bank
9 SmartShunt
VE.Bus BMS V2
Page 16 System examples

4.5. Three-phase system with a Digital Multi Control
# Description
1 Digital Multi Control
2 MultiPlus-II Inverter/charger installed and configured as a 3-phase system
3 VE.Bus BMS V2
4 Lithium Battery Smart or battery consisting of multiple batteries creating a 12V, 24V or 48V battery bank
VE.Bus BMS V2
Page 17 System examples

5. Operation
5.1. Important warning
Lithium batteries are expensive and can be damaged due to over discharge or over charge. Damage due to over discharge can
occur if small loads (such as: alarm systems, relays, standby current of certain loads, back current drain of battery chargers
or charge regulators) slowly discharge the battery when the system is not in use. In case of any doubt about possible residual
current draw, isolate the battery by opening the battery switch, pulling the battery fuse(s) or disconnecting the battery plus when
the system is not in use.
A residual discharge current is especially dangerous if the system has been discharged completely and a low cell voltage
shutdown has occurred. After shutdown due to low cell voltage, a capacity reserve of approximately 1Ah per 100Ah battery
capacity is left in the battery. The battery will be damaged if the remaining capacity reserve is drawn from the battery. A residual
current of 10mA for example may damage a 200Ah battery if the system is left in discharged state for more than 8 days.
The shutdown due to low cell voltage by the BMS should always be used as a last resort to be on the safe side at all times. We
recommend not letting it get that far in the first place and instead shutting down the system automatically based on a defined state
of charge so that there is enough reserve capacity in the battery. For an inverter/charger, for example, this can be done via the
VE.Configure setting 'shut-down on SoC'. It is even easier with a BMV, whose relay can control the remote on/off port of the BMS
via an adjustable SoC value.
5.2. LED indications
LED Colour Behaviour Meaning
Status Blue
Off BMS is off
Lights shortly
approximately once
every 10 seconds.
BMS is operating normally.
Flashes rapidly at
approximately 15 times
per second.
The BMS is stuck in boot loader mode due to a faulty application.
Cell > 2.8V Blue
Off
Low cell voltage.
The BMS has switched the DC loads and the inverter off.
Charge the battery or connect an AC supply to the inverter/charger.
Once the battery voltage has increased sufficiently, the DC loads
and inverter will be switched on again.
On Cell voltage within normal range.
Cell > 4V Red
Off Cell voltage and temperature within normal range.
On
High cell voltage or high temperature.
The BMS has switched off the chargers.
Check for a faulty charger and/or reduce battery temperature.
Once the battery voltage and/or temperature have been sufficiently
reduced, the BMS will switch the chargers back on.
VE.Bus BMS V2
Page 18 Operation
Other manuals for VE.Bus BMS V2
1
Table of contents
Other Victron energy Control Unit manuals
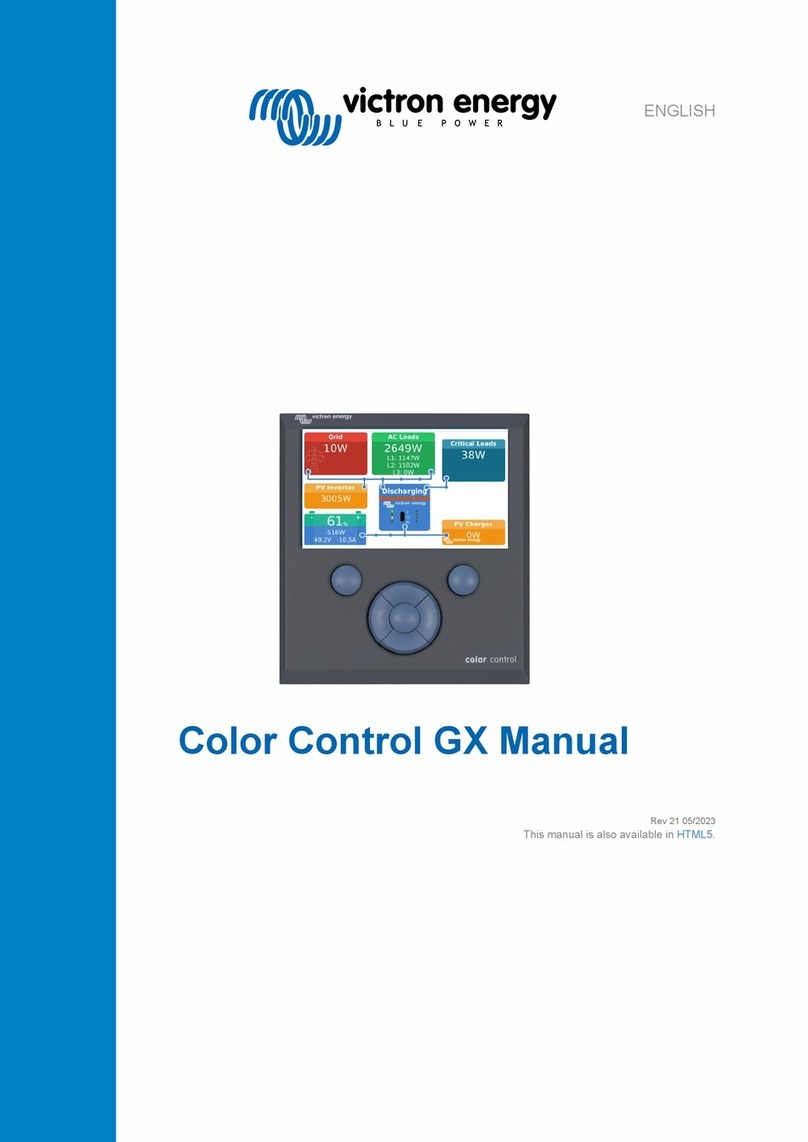
Victron energy
Victron energy Color Control GX User manual
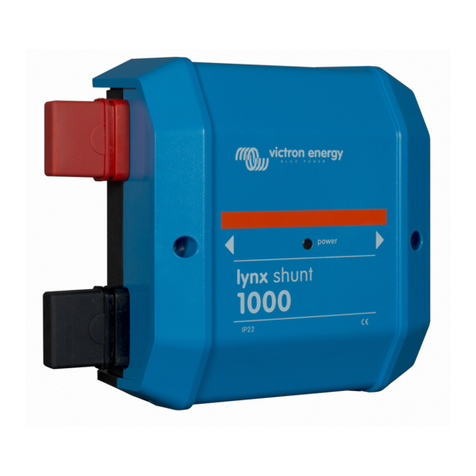
Victron energy
Victron energy Lynx Shunt VE.Can User manual
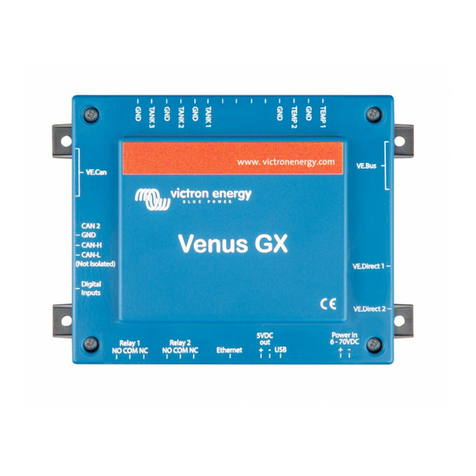
Victron energy
Victron energy Venus GX User manual

Victron energy
Victron energy GlobalLink 520 User manual
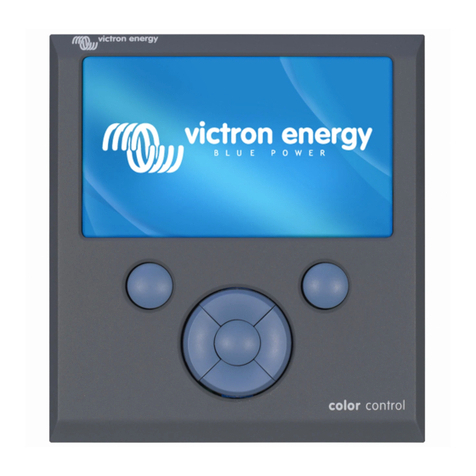
Victron energy
Victron energy Color Control GX User manual
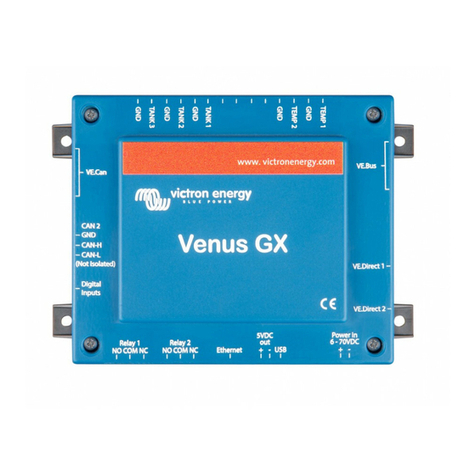
Victron energy
Victron energy Venus GX User manual
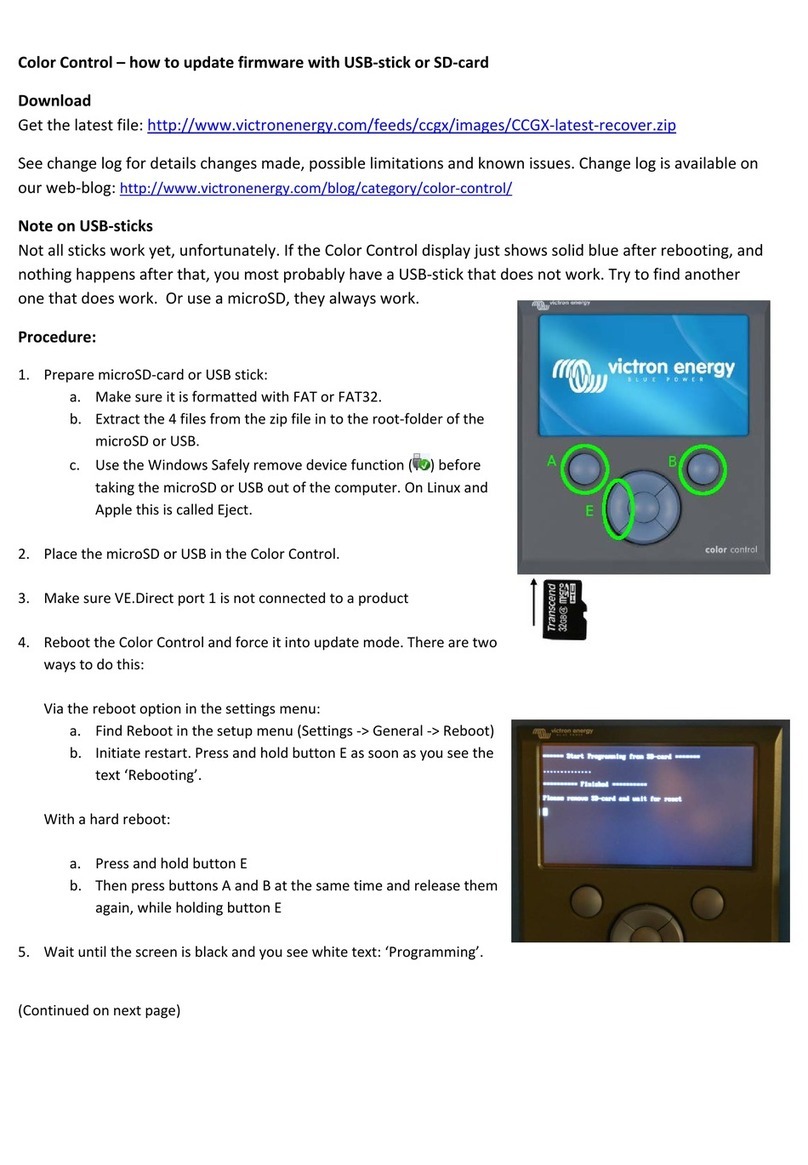
Victron energy
Victron energy Color Control Use and care manual
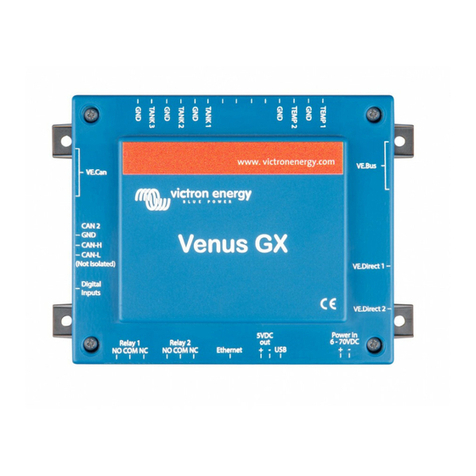
Victron energy
Victron energy Venus GX User manual

Victron energy
Victron energy BlueSolar Pro User manual
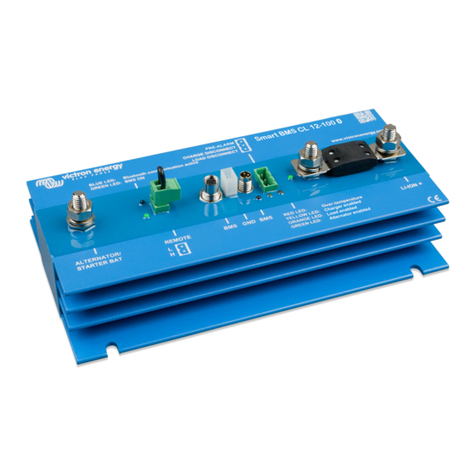
Victron energy
Victron energy Smart BMS CL 12/100 User manual